Izostatické lisování za tepla (HIP)
Obsah
Představte si svět, kde jsou kovové součásti prakticky bezchybné, bez drobných vzduchových kapes a nedokonalostí, které by je mohly oslabit. To není sci-fi, ale realita lisování za tepla (Hot Isostatic Pressing).HIP), což je výkonná technika, která posouvá kovové díly na vyšší úroveň.
V tomto obsáhlém průvodci se ponoříme do fascinujícího světa HIP, prozkoumáme jeho účel, aplikace, výhody a dokonce i některá omezení. Připoutejte se a připravte se na objevování toho, jak teplo a tlak spojují své síly a vytvářejí vynikající materiály!
Účel lisování za tepla (HIP)
Už jste někdy mačkali antistresový míček? To je něco jako HIP, ale na mnohem intenzivnější úrovni. HIP vystavuje součásti extrémní teplo (až 2 000 °C). a rovnoměrný vysokotlaký plyn (až 45 000 psi). ve specializované tlakové nádobě. Představte si ji jako přeplněný tlakový hrnec na kovy a keramiku.
Tato účinná kombinace slouží ke dvěma hlavním účelům:
- Odstranění pórovitosti: Představte si kov jako houbu. Při výrobních procesech se v něm mohou zachytit malé vzduchové kapsy, kterým se říká pórovitost. Tyto kapsy materiál oslabují, takže je náchylnější k prasklinám a únavě. HIP působí jako houba, která tyto vzduchové kapsy sráží a vytváří hustší a pevnější součást.
- Lepení práškových kovů: Slyšeli jste někdy o 3D tisku z kovu? HIP hraje v této technologii klíčovou roli. Kovové prášky se používají k vytváření složitých tvarů, ale tyto tvary mohou být slabé kvůli sypké povaze prášku. HIP tyto částice spojí dohromady, čímž vznikne pevný, vysoce výkonný kovový díl.
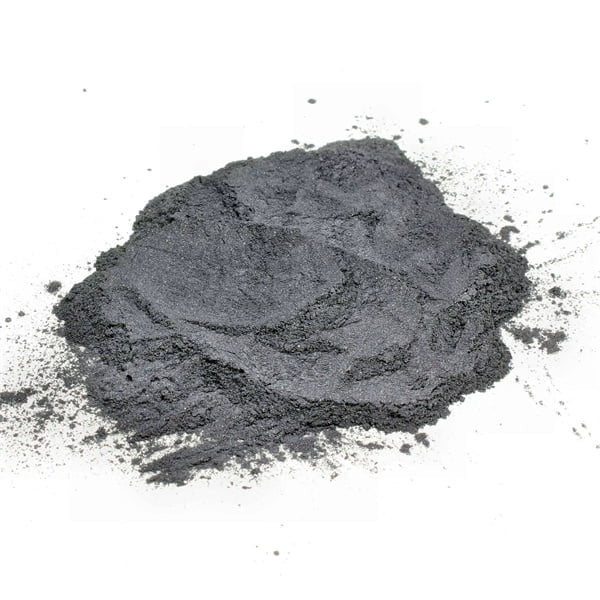
Aplikace izostatického lisování za tepla (HIP)
Služba HIP není jednoúčelová. Jeho schopnost vytvářet superhusté, vysoce integrované materiály z něj činí cenný nástroj v různých průmyslových odvětvích:
- Letectví: Součásti letadel, jako jsou lopatky turbín a podvozky, musí být neuvěřitelně pevné a lehké. HIP zajišťuje, že tyto díly vydrží obrovské namáhání při letu, aniž by byla ohrožena bezpečnost.
- Lékařské přístroje: Umělé kyčelní klouby a další implantáty vyžadují výjimečnou biokompatibilitu a trvanlivost. HIP vytváří díly, které jsou méně náchylné k opotřebení, což vede k delší životnosti implantátů.
- Ropa a plyn: Zařízení pro hlubinné vrty čelí drsným podmínkám. HIP tyto součásti zpevňuje a zabraňuje tak katastrofickým poruchám pod obrovským tlakem.
- Automobilový průmysl: Vysoce výkonné automobilové díly, jako jsou závodní kola a bloky motorů, těží ze schopnosti společnosti HIP vytvářet lehké a přitom neuvěřitelně pevné komponenty.
- Obrana: Vojenské aplikace, jako jsou zbraňové systémy a pancíře, vyžadují výjimečnou pevnost a spolehlivost. HIP zajišťuje, že tyto komponenty mohou bezchybně fungovat v extrémních podmínkách.
To je jen několik příkladů. Od zubních implantátů po součásti tryskových motorů - HIP hraje zásadní roli při vytváření vysoce výkonných materiálů pro náročné aplikace.
Výhody lisování za tepla (HIP)
Proč tedy upřednostnit HIP před tradičními výrobními metodami? Zde je několik pádných důvodů:
- Vynikající mechanické vlastnosti: Eliminací pórovitosti vytváří HIP díly se zvýšenou pevností, únavovou odolností a tažností. To znamená, že součásti snesou větší zatížení a vydrží déle.
- Vylepšená mikrostruktura: Intenzivní tlak během HIP zjemňuje strukturu zrn materiálu, což vede k rovnoměrnější a předvídatelnější mikrostruktuře. To následně zlepšuje celkové vlastnosti materiálu.
- Zvýšená těsnost: HIP vytváří téměř dokonalé těsnění uvnitř komponentů, takže jsou prakticky nepropustné. To má zásadní význam pro aplikace, kde i malá netěsnost může mít katastrofální následky.
- Všestrannost: HIP může pracovat s různými materiály, včetně kovů, keramiky a kompozitů. To z něj činí cenný nástroj pro širokou škálu průmyslových odvětví.
Kromě těchto výhod nabízí HIP také některé praktické výhody:
- Složité geometrie: HIP lze použít u složitých tvarů, které mohou být obtížně dosažitelné tradičními výrobními metodami.
- Zpracování tvaru sítě: V některých případech umožňuje HIP vytvářet téměř hotové díly, což snižuje potřebu rozsáhlého následného zpracování.
Berte HIP jako investici do kvality a výkonnosti. Počáteční náklady mohou být vyšší, ale dlouhodobý přínos v podobě trvanlivosti a spolehlivosti může být významný.
Nevýhody izostatického lisování za tepla (HIP)
Přestože HIP nabízí působivé výhody, není bez omezení:
- Náklady: Složitá zařízení a vysoká spotřeba energie při HIP z něj činí relativně nákladný proces ve srovnání s některými tradičními metodami.
- Omezení velikosti: Velikost a tlak nádob HIP omezují velikost komponent, které lze zpracovávat.
- Materiálová kompatibilita: Ne všechny materiály dobře reagují na intenzivní teplo a tlak při HIP. U některých materiálů může dojít k nežádoucím změnám jejich vlastností.
- Složitost procesu: HIP vyžaduje pečlivý výběr parametrů zpracování (teplota, tlak a čas) pro každý materiál a aplikaci. Nesprávné nastavení může vést k vadám nebo dokonce k poškození součásti.
- Dlouhá doba cyklu: Proces HIP může v závislosti na velikosti a materiálu součásti trvat hodiny nebo i dny. To může být nevýhodou pro velkosériovou výrobu.
Je důležité pečlivě zvážit výhody a nevýhody HIP a určit, zda je to správné řešení pro vaše konkrétní potřeby.
Materiálová hlediska pro izostatické lisování za tepla (HIP)
Ne všechny materiály jsou stejné a jejich vhodnost pro HIP se může lišit. Zde je rozpis některých klíčových faktorů, které je třeba zvážit:
- Bod tání: Teplota tání materiálu musí být výrazně vyšší než teplota zpracování použitá při HIP, aby se zabránilo nežádoucímu tavení nebo degradaci.
- Tažnost: Pro HIP jsou obecně vhodné tvárné materiály, tedy takové, které se mohou pod napětím deformovat, aniž by se porušily. Vysoký tlak může pomoci těmto materiálům proudit a vyplnit případné dutiny.
- Tepelná roztažnost: U materiálů s vysokým koeficientem tepelné roztažnosti může během cyklů ohřevu a chlazení HIP dojít k deformaci nebo zkroucení. U takových materiálů je rozhodující pečlivá kontrola parametrů zpracování.
- Chemická reaktivita: Některé materiály mohou reagovat s tlakovým plynem (obvykle argonem) používaným při HIP. To může vést k nežádoucím povrchovým reakcím nebo vnitřním defektům.
Výběr materiálu pro HIP je zásadním krokem. Konzultace s kvalifikovaným poskytovatelem služeb HIP může pomoci zajistit, že zvolený materiál je kompatibilní s procesem a dosáhne požadovaných výsledků.
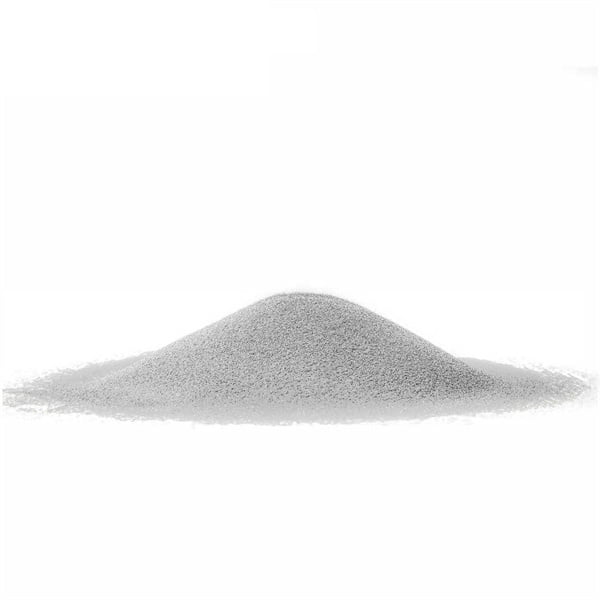
Srovnání HIP s dalšími výrobními technikami
Jak si HIP stojí v porovnání s jinými výrobními technikami? Zde je rychlé srovnání:
- Obsazení: Odlévání je tradiční metoda tvarování kovových tvarů. Odlitky však mohou být náchylné k pórovitosti. HIP lze použít jako následný krok zpracování ke zlepšení hustoty a mechanických vlastností odlitků.
- Kování: Kování spočívá v tvarování kovu kladivem nebo lisováním. Kováním lze sice vytvořit husté díly, ale nemusí být vhodné pro složité geometrie. HIP lze použít ve spojení s kováním k dalšímu zlepšení vlastností kovaných součástí.
- Svařování: Svařováním se spojují jednotlivé kusy kovu. Svarová zóna však může mít v porovnání se základním kovem odlišné vlastnosti. HIP může pomoci zlepšit integritu a rovnoměrnost svarů.
- Prášková metalurgie: Prášková metalurgie zahrnuje tvarování kovových předmětů ze stlačených kovových prášků. HIP se často používá jako závěrečný krok práškové metalurgie k vytvoření zcela hustých dílů s vynikajícími vlastnostmi.
Každá výrobní technika má své silné a slabé stránky. HIP může být cenným nástrojem, který doplňuje a zdokonaluje ostatní metody a vede k výrobě vysoce výkonných součástí.
Jak se HIP používá v různých odvětvích
Pojďme se hlouběji podívat na několik konkrétních příkladů, které ukazují sílu HIP v různých odvětvích:
- Letectví: Lopatky turbíny v proudových motorech pracují za extrémních teplot a tlaků. HIP zajišťuje, že tyto lopatky jsou výjimečně pevné a odolné vůči únavovým trhlinám, což zvyšuje výkon a bezpečnost motoru.
- Lékařské přístroje: Umělé kyčelní a kolenní náhrady vyžadují mimořádnou odolnost proti opotřebení a biokompatibilitu. Společnost HIP vytváří téměř bezchybné implantáty, které mají delší životnost a snižují riziko komplikací.
- Ropa a plyn: Vrtné nástroje používané při průzkumu ložisek ropy a zemního plynu čelí obrovskému tlaku a drsnému prostředí. HIP tyto nástroje zpevňuje a zabraňuje tak poruchám, které mohou být nákladné a škodlivé pro životní prostředí.
- Automobilový průmysl: Vysoce výkonné automobilové komponenty, jako jsou ojnice a lehká kola, těží ze schopnosti společnosti HIP vytvářet pevné a zároveň lehké díly. To se projevuje ve vyšší spotřebě paliva a celkovém výkonu vozidla.
- Obrana: Vojenské aplikace, jako je pancéřování a zbraňové systémy, vyžadují výjimečnou pevnost a spolehlivost. HIP zajišťuje, že tyto součásti vydrží náročné bojové podmínky, aniž by byla ohrožena jejich funkčnost.
To je jen několik příkladů, které však zdůrazňují všestrannost HIP a jeho úlohu při vytváření špičkových materiálů pro náročné aplikace v různých průmyslových odvětvích.
Zde je tabulka shrnující hlavní výhody HIP v různých odvětvích:
Průmysl | Výhody HIP |
---|---|
Aerospace | Zvýšená pevnost a únavová odolnost lopatek turbín a dalších kritických součástí |
Lékařské přístroje | Zvýšená odolnost proti opotřebení a biokompatibilita implantátů |
Ropa a plyn | Zvýšená pevnost a spolehlivost vrtných nástrojů pro hlubinné vrty |
Automobilový průmysl | Lehké, ale pevné komponenty pro lepší výkon a nižší spotřebu paliva |
Obrana | Výjimečná pevnost a spolehlivost pro pancéřování a zbraňové systémy. |
Budeme pokračovat v objevování světa lisování za tepla (HIP) v další části, včetně často kladených otázek a dalších zdrojů.
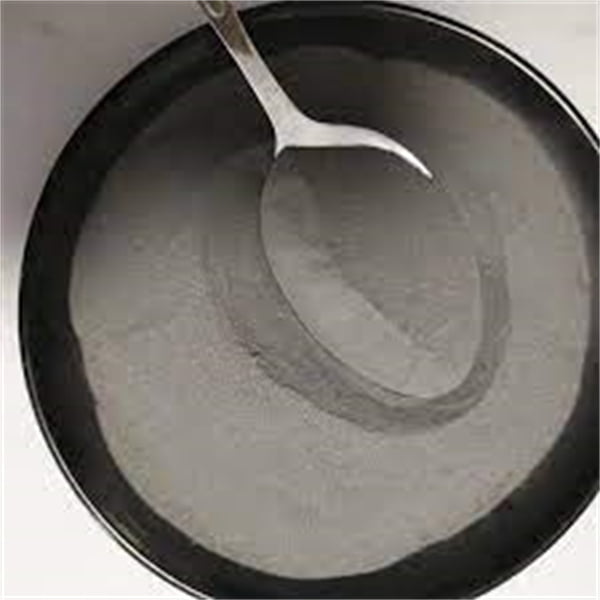
FAQ
Zde jsou některé z nejčastějších otázek týkajících se lisování za tepla (HIP):
Otázka: Jaké materiály lze použít v HIPu?
Odpověď: HIPovat lze širokou škálu materiálů, včetně:
- Kovy (ocel, titan, hliník, slitiny)
- Keramika (nitrid křemíku, oxid hlinitý)
- Kompozity (kompozity s kovovou matricí, kompozity s keramickou matricí)
Vhodnost materiálu pro HIP závisí na faktorech, jako je bod tání, tažnost, tepelná roztažnost a chemická reaktivita. Doporučuje se konzultace s kvalifikovaným poskytovatelem služeb HIP, abyste zjistili, zda je konkrétní materiál s tímto procesem kompatibilní.
Otázka: Jaké jsou typické rozměry součástí, které lze použít pro HIP?
Odpověď: Omezení velikosti nádob HIP omezuje maximální velikost součástí, které lze zpracovávat. Konkrétní velikostní omezení se liší v závislosti na poskytovateli služeb HIP, ale typické rozsahy jsou:
- Průměr: Až několik metrů
- Délka: Až několik metrů
U součástí, které přesahují tato omezení, může být nutné použít alternativní výrobní metody nebo rozdělit součást na menší části pro individuální ošetření HIP.
Otázka: Kolik stojí HIP?
Odpověď: Náklady na HIP se mohou lišit v závislosti na několika faktorech, včetně:
- Velikost a složitost součásti
- Zpracovávaný materiál
- Parametry zpracování (teplota, tlak, čas)
- Objem zpracovávaných dílů
Obecně je HIP ve srovnání s některými tradičními výrobními metodami dražší proces kvůli složitému vybavení a vysoké spotřebě energie. Dlouhodobé přínosy v podobě vyššího výkonu a spolehlivosti však mohou u kritických aplikací převýšit počáteční náklady.
Otázka: Jaké jsou výhody používání poskytovatele služeb HIP ve srovnání s vlastním zařízením HIP?
Odpověď: Zde jsou některé výhody využívání služeb poskytovatele HIP:
- Odborné znalosti: Poskytovatelé služeb HIP mají rozsáhlé zkušenosti a odborné znalosti v oblasti optimalizace procesu pro různé materiály a aplikace.
- Dostupnost zařízení: Investice do vlastního vybavení HIP a jeho údržba mohou být nákladné. Využití poskytovatele služeb umožňuje přístup k modernímu vybavení bez počátečních investic.
- Kontrola kvality: Poskytovatelé služeb HIP zavedli postupy kontroly kvality, aby zajistili konzistentní a spolehlivé výsledky.
- Škálovatelnost: Poskytovatelé služeb mohou v porovnání s vlastními kapacitami pojmout širší škálu velikostí a objemů komponent.
Použití vlastního zařízení HIP však může být vhodnější v situacích, kdy je zapotřebí vysokých objemů výroby, přísné kontroly procesu nebo vlastních aplikací.
Sdílet na
MET3DP Technology Co., LTD je předním poskytovatelem řešení aditivní výroby se sídlem v Qingdao v Číně. Naše společnost se specializuje na zařízení pro 3D tisk a vysoce výkonné kovové prášky pro průmyslové aplikace.
Dotaz k získání nejlepší ceny a přizpůsobeného řešení pro vaše podnikání!
Související články
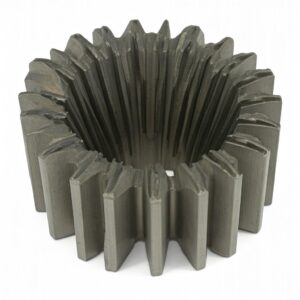
Vysoce výkonné segmenty lopatek trysek: Revoluce v účinnosti turbín díky 3D tisku z kovu
Přečtěte si více "O Met3DP
Nedávná aktualizace
Náš produkt
KONTAKTUJTE NÁS
Nějaké otázky? Pošlete nám zprávu hned teď! Po obdržení vaší zprávy obsloužíme vaši žádost s celým týmem.
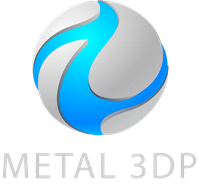
Kovové prášky pro 3D tisk a aditivní výrobu