Vstřikovací prášek
Obsah
Prášek pro vstřikování se vztahuje na typ vstupního materiálu používaného při vstřikování prášku, což je průmyslový výrobní proces pro výrobu složitých a vysoce přesných kovových dílů. Tento prášek je směsí jemných kovových prášků a polymerních pojiv, které lze vstřikovat do složitých dílů s konečným tvarem ve velkém objemu.
Výhody použití prášku pro vstřikování
Výhoda | Popis | Benefit |
---|---|---|
Složité geometrie: IMP umožňuje vytváření složitých tvarů s jemnými prvky, kterých je obtížné nebo nemožné dosáhnout tradičními technikami vstřikování. Tato svoboda designu otevírá dveře pro inovativní komponenty v různých průmyslových odvětvích. | Na rozdíl od tradičních lisovacích materiálů, jako jsou roztavené plasty, používá IMP systém pojiva, který drží částice prášku pohromadě během procesu lisování. To umožňuje vytváření dílů s vnitřními kanály, podříznutími a dalšími složitými geometriemi. | |
Účinnost materiálu: IMP podporuje výrobu téměř čistého tvaru, minimalizuje plýtvání materiálem ve srovnání se subtraktivními technikami, jako je obrábění. To je zvláště výhodné pro drahé nebo vysoce výkonné materiály. | Přesná kontrola distribuce prášku během vstřikování minimalizuje nadměrné použití materiálu. Kromě toho, na rozdíl od tradičních procesů, které generují zmetky během zkušebních běhů, umožňuje IMP rychlejší iterace návrhu s minimálním plýtváním materiálem. | |
Široký výběr materiálů: IMP nabízí širší škálu možností materiálů ve srovnání s tradičním vstřikováním. Tato všestrannost umožňuje vytváření dílů se specifickými vlastnostmi přizpůsobenými aplikaci. | Kromě standardních polymerů používaných při vstřikování může IMP používat kovové prášky, keramiku a dokonce i kompozitní materiály. To otevírá dveře pro vytváření dílů s jedinečnými kombinacemi pevnosti, vodivosti nebo biokompatibility. | |
Vysoce výkonné díly: Schopnost používat kovové a keramické prášky v IMP umožňuje výrobu vysoce výkonných dílů s výjimečnou pevností, tepelnou odolností nebo odolností proti opotřebení. | Komponenty vstřikované kovem (MIM) mohou dosáhnout mechanických vlastností srovnatelných s kovanými (objemovými) kovy, díky čemuž jsou vhodné pro náročné aplikace. Podobně keramické díly IMP nabízejí vynikající odolnost proti opotřebení a vysokoteplotní výkon. | |
Potenciál hromadné výroby: I když se původně používala pro prototypování, technologie IMP dozrála tak, aby umožnila nákladově efektivní sériovou výrobu složitých dílů. | Vysoký stupeň automatizace dosažitelný v procesech IMP umožňuje efektivní výrobu velkého množství dílů s konzistentní kvalitou. Díky tomu je to životaschopná možnost pro aplikace s velkým objemem. | |
Vylepšená povrchová úprava: Ve srovnání s tradičními technikami lití kovů může IMP někdy dosáhnout hladší povrchové úpravy na konečných dílech. | Použití jemných prášků a řízený proces lisování může minimalizovat povrchové nedokonalosti, což může snížit potřebu rozsáhlých kroků následného zpracování, jako je leštění. |
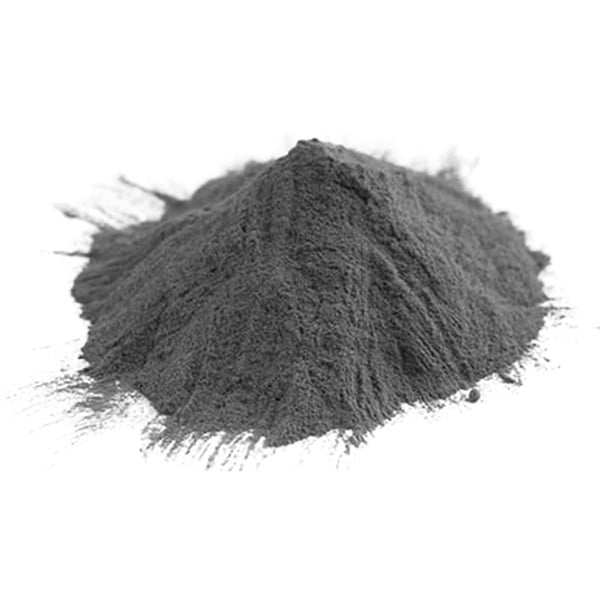
Složení prášku pro vstřikování
Komponent | Popis | Funkce |
---|---|---|
Základní prášky | Ty tvoří primární funkční materiál konečného dílu a lze je rozdělit do tří hlavních typů: Kovové prášky: Jemně rozdělené kovové částice různých slitin, jako je nerezová ocel, nástrojová ocel nebo superslitiny. Ocelové prášky, které nabízejí rovnováhu mezi cenovou dostupností a odolností proti opotřebení, se dodávají v různých třídách, z nichž každá je přizpůsobena pro specifické aplikace. Keramické materiály, jako je oxid hlinitý, oxid zirkoničitý nebo nitrid křemíku ve formě prášku. Polymerní prášky: Termoplastické polymery běžně používané při vstřikování, jako je nylon nebo polypropylen. | Volba základního prášku určuje konečné vlastnosti lisovaného dílu, jako je pevnost, odolnost proti opotřebení nebo tepelný výkon. |
Systém pojiva | Jedná se o zásadní složku, která působí jako dočasné lepidlo a drží částice základního prášku pohromadě během procesu lisování. Systém pojiva se obvykle skládá z: Termoplastický polymer: Termoplastická pryskyřice, která se taví během fáze vstřikování, což umožňuje tekutost a adhezi se základním práškem. * Vosky nebo přísady: Ty mohou zlepšit vlastnosti toku, zlepšit účinnost odstraňování pojiva nebo pomoci při disperzi prášku v pojivu. | Systém pojiva zajišťuje, že se prášek chová jako lisovatelná vsázka během vstřikování a umožňuje vytváření složitých tvarů. |
Tvorby pórů | Jedná se o volitelné přísady, které vytvářejí dočasné póry uvnitř lisovaného dílu. Mohou to být: * Organické materiály: Ty se během odstraňování pojiva vypálí a zanechají síť pórů, které usnadňují odstranění systému pojiva. * Chemická činidla pro loužení: Ty se rozpouštějí ve specifickém rozpouštědle během kroku následného zpracování, čímž se vytváří řízená struktura pórů. | Tvorba pórů umožňuje vytváření porézních struktur v konečné části, což může být výhodné pro aplikace, jako jsou filtry nebo kostní implantáty. |
Charakteristiky použitých kovových prášků
Charakteristický | Popis | Důležitost v MIM |
---|---|---|
Velikost a distribuce částic | Velikost a distribuce částic kovového prášku významně ovlivňují následující aspekty MIM: Plnění formy a zelená pevnost: Jemnější prášky obecně nabízejí lepší hustotu slisování a mohou zlepšit plnění formy během vstřikování. Nadměrně jemné částice však mohou bránit tekutosti a vést k problémům během zpracování. Úzká distribuce velikosti částic zajišťuje konzistentní slisování a minimalizuje dutiny v lisované části, což přispívá k dobré zelené pevnosti (pevnost části před slinováním). Chování při slinování a konečné vlastnosti: Velikost částic ovlivňuje proces slinování, kde se částice spojují a vytvářejí pevnou strukturu. Prášky se širší distribucí velikosti mohou vést k nehomogennímu slinování a potenciálně ovlivnit konečné mechanické vlastnosti dílu. | Pečlivý výběr velikosti a distribuce částic je zásadní pro dosažení dobrého plnění formy, zelené pevnosti a optimálního výkonu v konečné slinuté součásti. |
Morfologie částic | To se týká tvaru částic kovového prášku. Ideálně procesy MIM upřednostňují prášky se sférickou nebo téměř sférickou morfologií. | Sférické částice lépe tečou, což zlepšuje plnění formy a hustotu slisování. Nepravidelně tvarované částice mohou vytvářet dutiny a bránit tekutosti, což může vést k defektům v lisované části. |
Zdánlivá a kohoutková hustota | Tyto vlastnosti představují objemovou hmotnost prášku za různých podmínek. Zdánlivá hustota: Jedná se o hustotu prášku v klidu, přičemž se zohlední mezery mezi částicemi. Hustota kohoutku: To odráží hustší stav dosažený standardizovaným procesem odběru. | Vyšší sypná hustota je obecně v MIM žádoucí pro efektivní využití materiálu a dobrou rozměrovou přesnost v konečné části. Přispívá také ke zlepšenému slisování během lisování a minimalizuje smrštění během slinování. |
Chemické složení | Specifické prvky nebo slitiny použité v kovovém prášku určují konečné vlastnosti slinuté části. | Volba složení kovového prášku umožňuje přizpůsobit vlastnosti, jako je pevnost, odolnost proti korozi nebo odolnost proti opotřebení, aby splňovaly specifické požadavky aplikace. MIM může využívat různé kovové slitiny, včetně nerezové oceli, nástrojové oceli a dokonce i vysoce výkonných slitin, jako je Inconel. |
Tekutost | To se týká snadnosti, s jakou prášek teče působením gravitace nebo aplikovaných sil. | Dobrá tekutost je nezbytná pro rovnoměrné rozložení prášku během vstřikování. Prášky se špatnou tekutostí mohou vést k nesrovnalostem v hustotě slisování a potenciálním defektům v konečné části. |
Normy pro kovové prášky
Použité kovové prášky musí splňovat normy pro složení a zrnitost:
Standardní tělo | Standard | Popis | Důležitost v IMP |
---|---|---|---|
ASTM International (ASTM) | ASTM B930 – Standardní návod pro charakterizaci prášku pro vstřikování kovů (MIM) | Tato norma popisuje různé zkušební metody pro charakterizaci vlastností kovových prášků používaných v MIM. | Poskytuje rámec pro hodnocení faktorů, jako je distribuce velikosti částic, morfologie, tekutost a zdánlivá hustota. To zajišťuje konzistenci a kontrolu kvality kovových prášků používaných pro aplikace IMP. |
** | ** | * ASTM B783 – Standardní specifikace pro prášky z nerezové oceli pro aplikace vstřikování kovů (MIM) | Tato norma definuje specifické požadavky na chemické složení, distribuci velikosti částic a tekutost prášků z nerezové oceli používaných v MIM. |
** | ** | * ASTM D4000 – Standardní klasifikační systém pro specifikaci plastových materiálů | I když se nejedná o výhradní záležitost IMP, tato norma poskytuje klasifikační systém pro různé typy plastových materiálů, včetně těch, které se potenciálně používají jako pojiva v surovinách IMP. |
Mezinárodní organizace pro normalizaci (ISO) | * ISO 3095 – Kovové prášky – Stanovení průtoku pomocí Hallova průtokoměru | Tato norma specifikuje metodu pro měření tekutosti kovových prášků pomocí Hallova průtokoměru. | Poskytuje standardizovaný přístup k hodnocení tekutosti, což je kritická charakteristika pro dosažení dobrého plnění formy a konzistentní kvality dílů v IMP. |
** | ** | * ISO 4497 – Plasty – Stanovení rychlosti toku taveniny (MFR) a rychlosti toku objemu taveniny (MVR) termoplastů | Tato norma popisuje metodu pro měření rychlosti toku taveniny (MFR) termoplastických materiálů, což může být relevantní pro složku pojiva v surovinách IMP. |
Kroky ve výrobním procesu
Výrobní proces se skládá z následujících klíčových kroků:
Krok | Popis | Důležitost |
---|---|---|
1. Příprava a míchání prášku | Základní prášek (kov, keramika nebo polymer) je pečlivě vybrán a předem ošetřen na základě požadovaných konečných vlastností. Mohou být zahrnuty přísady, jako jsou tvůrci pórů nebo maziva. Prášek se poté přesně zváží a smíchá se systémem pojiva za vzniku homogenní suroviny. | Tento krok zakládá základ pro vlastnosti konečné části. Pečlivý výběr a přesné míchání zajišťují konzistentní chování materiálu během zpracování. |
2. Vstřikování | Připravená surovina IMP se zahřeje do polotaveného stavu a vstřikuje se do uzavřené dutiny formy pod vysokým tlakem. Forma replikuje požadovaný tvar konečné části. | Tato fáze definuje geometrii dílu. Konzistentní tok a tlak během vstřikování jsou zásadní pro dosažení přesných rozměrů dílu a minimálních defektů. |
3. Odstraňování pojiva | Lisovaná část, nazývaná také „zelená část“, prochází procesem odstraňování pojiva, aby se odstranil systém pojiva. Toho lze dosáhnout pomocí: * Odstraňování pojiva rozpouštědlem: Část se ponoří do rozpouštědla, které rozpouští pojivo a zanechává strukturu prášku. * Tepelné odstraňování pojiva: Část je vystavena řízenému cyklu ohřevu, kde se pojivo tepelně rozkládá a uniká jako plyn. | Efektivní odstraňování pojiva je kritické pro dosažení konečného požadovaného tvaru a pórovitosti bez poškození jemné struktury prášku. |
4. Slinování | Část zbavená pojiva je vystavena vysokým teplotám v řízené atmosféře (často ve vakuu nebo v inertním plynu). Tento proces podporuje difúzi a spojování mezi částicemi prášku, což má za následek pevnou součást blízkou čistému tvaru. | Slinování určuje konečné mechanické vlastnosti dílu, jako je pevnost, hustota a rozměrová stabilita. Zásadní je přesná regulace teploty a řízení atmosféry. |
5. Post-processing | V závislosti na požadavcích aplikace může slinutá část podstoupit další dokončovací kroky, jako jsou: * Obrábění nebo broušení: Pro dosažení přesných rozměrových tolerancí nebo povrchových úprav. * Tepelné zpracování: Pro zlepšení specifických mechanických vlastností, jako je pevnost nebo tvrdost. * Povlakování nebo infiltrace: Pro zlepšení povrchových vlastností, jako je odolnost proti opotřebení nebo odolnost proti korozi. | Úpravy po zpracování mohou dále zlepšit funkčnost a estetiku konečné části IMP. |
Aplikace vstřikovaných dílů
Prášek pro vstřikování lze použít k výrobě různých složitých a vysoce přesných dílů napříč průmyslovými odvětvími:
Průmysl | Příklady použití | Výhoda vstřikování |
---|---|---|
Automobilový průmysl | Vnitřní komponenty (palubní desky, panely dveří, konzoly) Díly pod kapotou (kryty ventilátorů, sací potrubí) Funkční komponenty (ozubená kola, řetězová kola) | Hromadná výroba složitých tvarů s přesnými prvky. Lehké díly pro zlepšení spotřeby paliva. Široká škála možností materiálů pro různé potřeby výkonu (odolnost, tepelná odolnost). |
Spotřební elektronika | Elektronické kryty (telefony, notebooky, tablety) Konektory a tlačítka Vnitřní komponenty (držáky, ozubená kola) | Hromadná výroba složitých dílů s vysokou rozměrovou přesností. Hladké povrchové úpravy pro estetiku a pohodlí uživatele. Různé barvy a textury dosažitelné výběrem materiálu a technikami lisování. |
Lékařské přístroje | Chirurgické nástroje (rukojeti, úchyty) Protézy (kolenní klouby, zubní implantáty) Jednorázové lékařské komponenty (stříkačky, lahvičky) | Sterilizovatelné materiály pro hygienu a bezpečnost. Biokompatibilní materiály pro použití v lidském těle (některé polymery a kovové slitiny). Složité geometrie pro přesnou funkčnost v lékařských aplikacích. |
Letectví a obrana | Letecké komponenty (potrubí, části podvozku) Satelitní komponenty (držáky, kryty) Obranné vybavení (helmy, součásti zbraní) | Lehké a vysoce pevné materiály pro snížení hmotnosti v leteckých aplikacích. Materiály zpomalující hoření nebo tepelně odolné pro specifické požadavky. Odolné díly pro drsné prostředí a náročné provozní podmínky. |
Spotřební zboží | Hračky a hry Spotřebiče (kryty, knoflíky, číselníky) Sportovní zboží (helmy, části jízdních kol) | Nákladově efektivní výroba pro spotřební produkty s velkým objemem. Široká škála barev a povrchových úprav pro vizuální přitažlivost. Odolné a funkční díly pro každodenní použití. |
Výhody vstřikování pro výrobu dílů
Výhoda | Popis | Benefit |
---|---|---|
Hromadná výroba: Vstřikování vyniká při efektivní výrobě velkého množství identických dílů. Možnosti automatizace a rychlé doby cyklu umožňují nákladově efektivní hromadnou výrobu. | To je zvláště výhodné pro produkty vyžadující miliony kusů, jako je spotřební elektronika nebo automobilové komponenty. Konzistentní kvalita a opakovatelnost jsou zajištěny v průběhu celé výrobní série. | |
Flexibilita designu: Vstřikování může pojmout širokou škálu geometrických složitostí, včetně složitých tvarů, tenkých stěn a vnitřních prvků. Tato svoboda designu umožňuje vytváření funkčních a inovativních dílů. | Na rozdíl od některých subtraktivních výrobních metod není vstřikování omezeno geometrií nástroje. Podřezání, kanály a další složité prvky lze přímo lisovat do dílu. | |
Rozměrová přesnost a opakovatelnost: Přesná kontrola nad konstrukcí formy a parametry vstřikování umožňuje konzistentní a přesné rozměry dílů napříč velkým objemem výroby. | To minimalizuje potřebu kroků následného zpracování pro rozměrovou korekci a zajišťuje zaměnitelné díly pro montáž. Opakovatelnost je zásadní pro udržení konzistentní kvality a funkčnosti produktu. | |
Široký výběr materiálů: Ve vstřikování lze použít širokou škálu materiálů, včetně termoplastů, termosetů, elastomerů a dokonce i některých kovových slitin (prostřednictvím vstřikování kovů – MIM). | Tato všestrannost umožňuje výběr optimálního materiálu na základě požadovaných vlastností, jako je pevnost, tepelná odolnost, chemická odolnost nebo flexibilita. | |
Povrchová úprava a estetika: Vstřikování může produkovat díly s hladkými a vysoce kvalitními povrchovými úpravami, často eliminující potřebu rozsáhlých kroků následného zpracování, jako je leštění. Kromě toho lze během lisování začlenit různé barviva a textury. | To přispívá k vizuální přitažlivosti a funkčnosti konečného produktu. Hladké povrchy mohou být zásadní pro hygienu ve zdravotnických prostředcích nebo pro snadné čištění ve spotřebním zboží. | |
Účinnost materiálu: Vstřikování podporuje výrobu blízkou čistému tvaru, minimalizující plýtvání materiálem ve srovnání se subtraktivními technikami, jako je obrábění. Přebytečný materiál, nazývaný vtok a vtokové kanály, lze často recyklovat a znovu použít v následných výrobních sériích. | To je výhodné z hlediska nákladů a udržitelnosti. Minimalizace odpadu také snižuje dopad výrobního procesu na životní prostředí. | |
Potenciál automatizace: Proces vstřikování může být vysoce automatizovaný, s minimálním zásahem člověka potřebným pro provoz. To umožňuje konzistentní kvalitu výroby a snižuje náklady na pracovní sílu. | Automatizace je zvláště výhodná pro výrobní série s velkým objemem a zajišťuje konzistentní kvalitu produktu bez ohledu na úroveň dovedností ob |
Omezení výrobního procesu
Existují i určitá omezení:
- Hmotnost dílu omezena na < 400 g
- Tloušťka stěny > 0,4 mm
- Sestavy potřebné pro složité geometrie
- Drahé nástroje pro formy
- Rozměrové změny během slinování
Globální dodavatelé surovin
Mnoho mezinárodních společností dodává hotové suroviny pro vstřikování:
Společnost | Umístění | Materiály |
---|---|---|
BASF | Německo | Nerezová ocel 316L, slitiny titanu |
Sandvik | Švédsko | Nerezové oceli, nástrojové oceli |
GKN | Spojené království | Slitiny hliníku a hořčíku |
Rio Tinto | Austrálie | Kovové a keramické vstřikované směsi |
Orientační ceny
Materiál | Cenové rozpětí |
---|---|
Nerezová ocel | $50-70 na kg |
Nástrojová ocel | 45–65 USD za kg |
Těžká slitina wolframu | 130–170 USD za kg |
Ceny závisí na objemu objednávky, potřebách přizpůsobení a ekonomických faktorech.
Výhody a nevýhody používání Prášky pro vstřikování
Výhody | Nevýhody |
---|---|
Složité a komplexní tvary | Omezená velikost a hmotnost |
Užší tolerance | Drahé nástroje a vybavení |
Jemná povrchová úprava | Rozměrové změny během slinování |
Řada materiálů | Často je nutné následné zpracování |
Vysoká produkce, nízké náklady na díl | Křehké materiály mají tendenci praskat |
Snížení množství odpadu | Omezuje výběr materiálu |
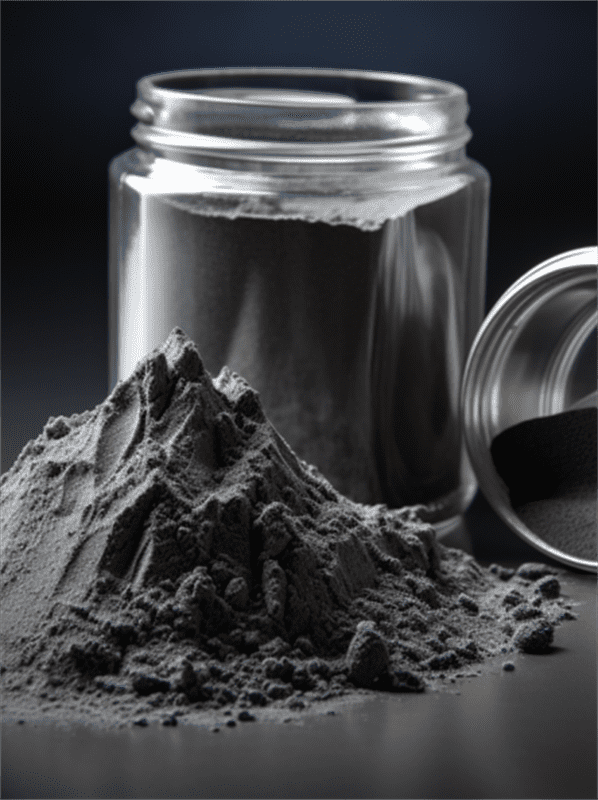
FAQ
Otázka: Jaké je typické složení prášků pro vstřikování?
Odpověď: Obsahují 80–90 % kovového prášku, 8–20 % pojiva a 1–2 % maziv podle hmotnosti. Běžná pojiva jsou vosk, PP, PE a PEG.
Otázka: Jaký rozsah velikostí prášků se používá?
Odpověď: Používají se prášky o velikosti 1–20 mikronů. Jemnější prášek zlepšuje hustotu, ale může být náchylný ke shlukování.
Otázka: Jaké smrštění nastává během slinování?
Odpověď: Během slinování v kapalné fázi dochází k lineárnímu smrštění dílů až o 20 %. V konstrukci nástrojů je třeba s tím počítat.
Otázka: Co způsobuje praskliny ve slinutých kovových dílech vstřikovaných do formy?
Odpověď: Nerovnoměrné zahřívání v pecích, použití rychlého chlazení po slinování, špatné míchání prášku a výběr křehkých slitin.
Otázka: Jaké možnosti materiálů existují pro prášky pro vstřikování?
Odpověď: Nerezové oceli, nástrojové oceli, těžké slitiny wolframu, slitiny mědi, titan a slitiny titanu a další.
Sdílet na
MET3DP Technology Co., LTD je předním poskytovatelem řešení aditivní výroby se sídlem v Qingdao v Číně. Naše společnost se specializuje na zařízení pro 3D tisk a vysoce výkonné kovové prášky pro průmyslové aplikace.
Dotaz k získání nejlepší ceny a přizpůsobeného řešení pro vaše podnikání!
Související články
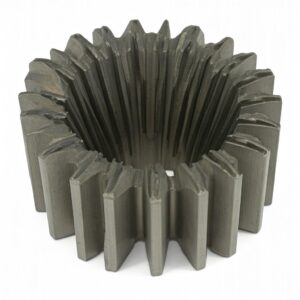
Vysoce výkonné segmenty lopatek trysek: Revoluce v účinnosti turbín díky 3D tisku z kovu
Přečtěte si více "O Met3DP
Nedávná aktualizace
Náš produkt
KONTAKTUJTE NÁS
Nějaké otázky? Pošlete nám zprávu hned teď! Po obdržení vaší zprávy obsloužíme vaši žádost s celým týmem.
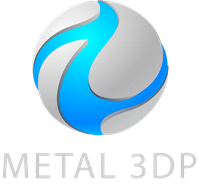
Kovové prášky pro 3D tisk a aditivní výrobu