systémy pro rozprašování kovů Specifikace
Obsah
Atomizace kovů je proces používaný k výrobě jemných kovových prášků pro různé aplikace. Zahrnuje tavení kovu a jeho následné rozdělení na jemné kapičky pomocí plynu nebo odstředivé síly. Kapičky rychle ztuhnou na částice prášku. Rozprašovací systémy kovů jsou zařízení používaná k efektivnímu provádění tohoto procesu v průmyslovém měřítku.
Přehled systémů atomizace kovů
Aspekt | Popis |
---|---|
Funkce | Systémy atomizace kovů jsou tahounem výroby jemných kovových prášků. Tyto systémy rozkládají roztavený kov na drobné kapičky pomocí vysokotlakého plynu, vody nebo kombinace obojího. Výsledné částice prášku, které se obvykle pohybují v rozmezí od 5 do 150 mikronů, se mohou pochlubit specifickými vlastnostmi a přesnými velikostmi, které jsou zásadní pro různé průmyslové aplikace. |
Rozdělení procesu | 1. Tání: Proces začíná zvolenou kovovou vsázkou, kterou může být panenský materiál, šrot nebo předem legovaná směs. Tento materiál se taví uvnitř pece, nejčastěji pomocí indukčních nebo obloukových technologií. 2. Atomizace: Proud roztaveného kovu je poté protlačován tryskou. Zde se setkává s vysokorychlostním proudem plynu, vody nebo obojího, v závislosti na požadovaných vlastnostech prášku a typu systému. Vysokotlaký proud narušuje proud kovu a rozbíjí ho na jemné kapičky. 3. Ztuhnutí: Jak atomizované kapičky padají přes vyhrazenou komoru, rychle tuhnou díky své malé velikosti a zvětšené povrchové ploše vystavené chladicímu prostředí. 4. Klasifikace a sběr: Ochlazený kovový prášek se poté klasifikuje, aby se dosáhlo požadovaného rozložení velikosti částic. Nakonec se prášek shromažďuje pro další zpracování nebo skladování. |
Typy systémů | Existují dvě primární kategorie systémů atomizace kovů: plynová atomizace a vodní atomizace. Plynová atomizace využívá inertní plyny jako argon nebo dusík k rozbití proudu taveniny. Tato metoda je ideální pro výrobu vysoce čistých prášků se sférickými tvary, díky čemuž jsou ideální pro aplikace aditivní výroby (AM). Vodní atomizace na druhé straně používá pro atomizaci vysokotlaké vodní trysky. Tato technika je nákladově efektivnější a vede k nepravidelně tvarovaným částicím. Prášky atomizované vodou se běžně používají v procesech práškové metalurgie (PM) pro aplikace, jako jsou ložiska a ozubená kola. |
Klíčové úvahy | Výběr systému atomizace kovů ovlivňuje několik faktorů. Zásadní jsou požadované vlastnosti prášku, jako je velikost částic, tvar a chemické složení. Kromě toho hraje významnou roli typ zpracovávaného kovu a požadavky na objem výroby. Je třeba také zohlednit provozní náklady systému, včetně spotřeby energie a potřeb údržby. |
Výhody | Atomizace kovů nabízí několik výhod oproti tradičním metodám zpracování kovů. Umožňuje vytváření prášků s přizpůsobenými vlastnostmi, což podporuje vývoj nových materiálů a pokročilých výrobních procesů. Atomizace navíc umožňuje výrobu téměř čistého tvaru v AM, což minimalizuje odpad materiálu. Tato technologie navíc usnadňuje recyklaci kovového šrotu zpět na cenné prášky, což podporuje udržitelnost ve výrobním sektoru. |
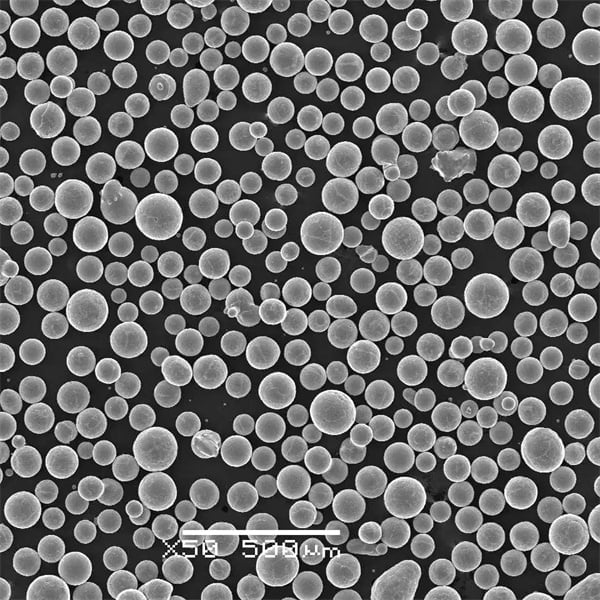
Typy systémů atomizace kovů
Systém | Popis | Výhody | Nevýhody | Aplikace |
---|---|---|---|---|
Atomizace plynu | Inertní plyn (obvykle argon) se používá k rozbití proudu roztaveného kovu na jemné kapičky. | Vyrábí sférické prášky s vysokou tekutostí Nižší obsah kyslíku v prášku Vhodné pro širokou škálu kovů a slitin | Pomalejší výrobní rychlosti ve srovnání s vodní atomizací Vyšší spotřeba energie Omezená kontrola nad distribucí velikosti částic na jemnějším konci | Aditivní výroba (3D tisk) Tepelné stříkání Vstřikování kovů (MIM) |
Atomizace vody | Vysokotlaké vodní trysky rozkládají roztavený kov na kapičky. | Rychlejší výrobní rychlosti a nižší náklady Vhodné pro velkoobjemové aplikace Může dosáhnout jemnějších velikostí částic | Vyšší obsah kyslíku v prášku v důsledku interakce s vodou Nepravidelné tvary prášku s družicemi (připojené kapičky roztaveného kovu) Omezeno na specifické kovy (obvykle hliník a ocel) | Vstřikování kovů (MIM) Tření svařování Díly s nižšími konstrukčními požadavky |
Rotační atomizace | Roztavený kov se nalije na vysokorychlostní rotující kotouč, který vyhazuje kov na kapičky v důsledku odstředivé síly. | Vyrábí téměř sférické prášky s dobrou tekutostí Může dosáhnout širšího rozsahu velikostí částic ve srovnání s plynovou atomizací | Omezeno na kovy s nízkou teplotou tání (obvykle hliník a hořčík) Vyšší spotřeba energie ve srovnání s vodní atomizací Možnost stříkání a bezpečnostní obavy | |
Plazmová atomizace | Inertní plyn je ionizován na plazmu pomocí elektrického oblouku, čímž se vytváří vysokoteplotní a vysokorychlostní proud, který rozbíjí roztavený kov. | Vhodné pro zpracování reaktivních kovů a kovů s vysokou teplotou tání Může dosáhnout velmi jemných a stejnoměrných velikostí částic Nižší obsah kyslíku ve srovnání s vodní atomizací | Vysoké investiční a provozní náklady Komplexní proces vyžadující specializované vybavení a odborné znalosti | Aditivní výroba (3D tisk) pro vysoce výkonné slitiny (např. titan, niklové superslitiny) Součásti plynových turbín Letecké a kosmické díly |
Proces plazmové rotující elektrody (PREP) | Varianta plazmové atomizace, kde se spotřební elektroda taví plazmovým hořákem a roztavený kov je odstředivě vyhazován na kapičky. | Kombinuje výhody plazmové atomizace a rotační atomizace Dosahuje vysokých výtěžků prášku a dobré kontroly nad velikostí a morfologií částic | Extrémně vysoké kapitálové a provozní náklady Omezená komerční dostupnost | Aditivní výroba pro vysoce hodnotné a speciální slitiny |
Konstrukce systému atomizace kovů
Hlavní součásti typického systému plynové atomizace jsou:
Konstrukce systému plynové atomizace
Komponent | Podrobnosti |
---|---|
Tavicí jednotka | Indukční tavicí kelímek, kapacita 50-2000 kg |
Sestava trysek | Více blízko spojených trysek, průměr 2-5 mm |
Přehřátí taveniny | Dusík/argon vstřikovaný pro přehřátí taveniny |
Atomizační komora | Chlazeno vodou, výška 3-5 m |
Zásobování plynem | Dusík/argon, tlak 50-100 barů |
Cyklónové separátory | Více cyklónů v sérii pro sběr prášku |
Závěrečné filtry | Vakový filtr, patronové filtry |
Konstrukce a počet trysek jsou důležité pro dosažení požadovaného rozložení velikosti jemných částic prášku. Výška atomizační komory umožňuje kapičkám ztuhnout před sběrem.
Vysoce kvalitní průmyslové plyny, jako je dusík nebo argon, jsou dodávány z tlakových plynových lahví nebo z generátorů na místě. Jejich tlak a průtok určují velikost kapiček.
Specifikace systému atomizace kovů
Typické specifikace pro průmyslové plynové atomizační systémy jsou:
Specifikace systému atomizace kovů
Parametry | Specifikace |
---|---|
Výrobní kapacita | 10 kg/h až 5000 kg/h |
Velikost částic | 10 - 150 mikronů |
Typy kovů | Slitiny niklu, železa, kobaltu, mědi |
Teplota tání | 1600 °C max. |
Tlak plynu | 10 – 100 bar |
Rychlost chlazení | 104 – 106 K/s |
Čistota prášku | 99.5% |
Konstrukce trysek | Kruhová štěrbina, diskrétní tryska |
Atomizační plyn | Dusík, argon |
Kapacita závisí na velikosti kelímku a pohybuje se od laboratorního/pilotního měřítka 10 kg/h až po systémy ve velkém měřítku 5000 kg/h. Většinou se atomizují slitiny niklu, železa a kobaltu, ale zpracovávají se i další kovy, jako je hliník, slitiny mědi.
Vysoký tlak plynu a rychlé chlazení zajišťují jemné mikroskopické práškové částice v rozsahu velikosti 10-150 mikronů. Lze získat prášky s čistotou 99,5 %.
Aplikace systému atomizéru kovů
Některé hlavní aplikace kovového prášku vyrobeného atomizací zahrnují:
Aplikace kovových prášků
Průmysl | Aplikace |
---|---|
Aerospace | Lopaty turbín, disky |
Automobilový průmysl | Slitované díly, filtry |
Elektronika | Čipové rezistory, vodiče |
Aditivní výroba | Prášky pro 3D tisk |
Chemické | Katalyzátory, pigmenty |
Biomedicína | Implantáty, protetika |
V leteckém průmyslu se prášky ze slitin niklu a titanu používají k výrobě lopatek a disků turbín se složitými tvary práškovou metalurgií. Automobilový průmysl používá atomizované prášky železa a oceli pro slinuté díly, jako jsou ozubená kola.
Jemné měděné a stříbrné prášky slouží jako vodiče a rezistory v mikroelektronických aplikacích. Kovové prášky jsou surovinou pro aditivní výrobní metody, jako je 3D tisk.
Prášky ze speciálních slitin se používají jako chemické katalyzátory a pigmenty. Porézní prášek z nerezové oceli se používá pro ortopedické kostní implantáty v biomedicínské oblasti.
Výhody systémů atomizace kovů
Některé výhody použití atomizace kovů pro výrobu prášku:
Výhody atomizace kovů
Výhody | Podrobnosti |
---|---|
Jemnější prášky | Velikosti v mikrometrech až nanometrech |
Úzké rozdělení velikosti | Přesná kontrola nad velikostí částic |
Vysoká čistota | Zamezení kontaminace broušením |
Nižší náklady | Levnější než mechanické broušení |
Kontrola složení | Slitina možná v tavenině |
Sférické částice | Dobrá tekutost |
Všestranný | Široká škála atomizovaných slitin |
Plynová a odstředivá atomizace může produkovat jemnější kovové prášky až do 10 mikronů ve srovnání s mechanickým mletím. Rozdělení velikosti částic je užší, což dává lepší kontrolu.
Vzhledem k tomu, že nejsou zapojena žádná mlecí média, je čistota prášku vyšší. Kapitálové a provozní náklady jsou nižší než u mechanického mletí.
Slitiny lze přidávat do kelímku, což umožňuje flexibilitu ve složení prášku. Sférické práškové částice poskytují dobrou tekutost, což je důležité pro plnění forem.
Téměř jakákoli slitina od nitinolu po inconel může být atomizována se správnou kontrolou nad parametry procesu.
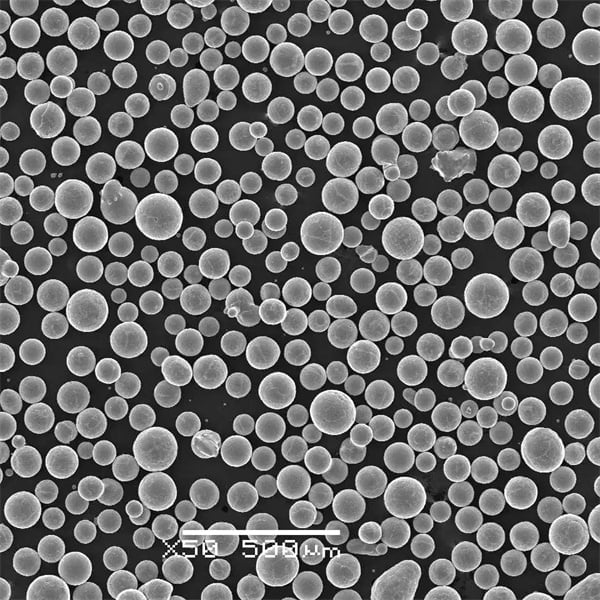
Omezení atomizace kovů
Některé nevýhody systémů atomizace kovů jsou:
Omezení atomizace kovů
Nevýhody | Podrobnosti |
---|---|
Vysoký bod tání | Omezeno na kovy s nižším bodem tání |
Reaktivní kovy | Obtížná atomizace reaktivních kovů, jako je titan, hliník |
Záchyt plynu | Absorbované plyny ovlivňují kvalitu prášku |
Satelitní částice | Vytvořeno několik větších nepravidelných částic |
Vysoké kapitálové náklady | Pro velký systém je nutná velká investice |
Kovy s velmi vysokými body tání nad 1800 °C, jako je wolfram, molybden, se obtížně atomizují kvůli omezením kelímku. Reaktivní kovy, jako je titan, hliník, vyžadují vakuum nebo inertní atmosféru.
Plyny absorbované během procesu atomizace ovlivňují vlastnosti prášku. Během atomizace se spolu se sférickými částicemi tvoří i některé nepravidelně tvarované satelitní částice.
Velké systémy atomizace kovů vyžadují velké kapitálové investice přesahující 2 miliony dolarů. Provozní náklady jsou také relativně vysoké.
Dodavatelé systémů atomizace kovů
Někteří přední globální dodavatelé zařízení pro atomizaci kovů jsou:
Dodavatelé systémů pro atomizaci kovů
Společnost | Umístění | Měřítko |
---|---|---|
Phoenix Scientific | Rockwood, USA | Z laboratoře do průmyslu |
Výroba kovových prášků | Manchester, UK | Z laboratoře do průmyslu |
ASK Chemicals | Hilden, Německo | Z laboratoře do průmyslu |
ZenniZ | Moskva, Rusko | Průmyslový |
ALD Vacuum | Hanau, Německo | Průmyslový |
Tyto společnosti nabízejí plynové, odstředivé a vakuové atomizační systémy v rozsahu od laboratorního/pilotního měřítka 5 kg/h po velké průmyslové kapacity 2000 kg/h. Poskytují se systémy na klíč s jednotkami pro tavení, atomizaci a manipulaci s práškem.
Ceny atomizačních systémů se pohybují od 100 000 USD za laboratorní jednotky do více než 2 milionů USD za průmyslové závody v závislosti na kapacitě a vlastnostech. Na ceny má vliv také umístění, daně, doprava atd.
Instalace systému pro atomizaci kovů
Klíčové kroky při instalaci systému pro atomizaci kovů jsou:
Instalace atomizéru kovů
Fáze | Akce |
---|---|
Příprava stanoviště | Vyrovnání betonové podlahy, instalace inženýrských sítí |
Montáž | Sestavení dílčích jednotek, jako je kelímek, sekce trysky |
Připojení | Připojení plynových vedení, chladicí vody, potrubí |
Uvedení do provozu | Zkušební provoz naprázdno, kontrola těsnosti, zkouška s nízkou kapacitou |
Bezpečnostní kontroly | Instalace nouzového zastavení, protipožární ochrany, alarmů |
Školení personálu | Školení personálu o provozu a údržbě systému |
Zařízení je těžké, takže místo musí mít rovnou, bezvibrační betonovou podlahu. Musí být připojeny inženýrské sítě, jako je chladicí voda, inertní plyn a odtahové potrubí.
Systém se poté sestaví, vyrovná, otestuje těsnost a zpočátku se spustí prázdný před skutečným horkým uvedením do provozu. Bezpečnostní systémy pro nouzové vypnutí, požár nebo únik taveniny musí být funkční.
Důkladné zaškolení obsluhy dodavatelem je nezbytné pro hladký provoz.
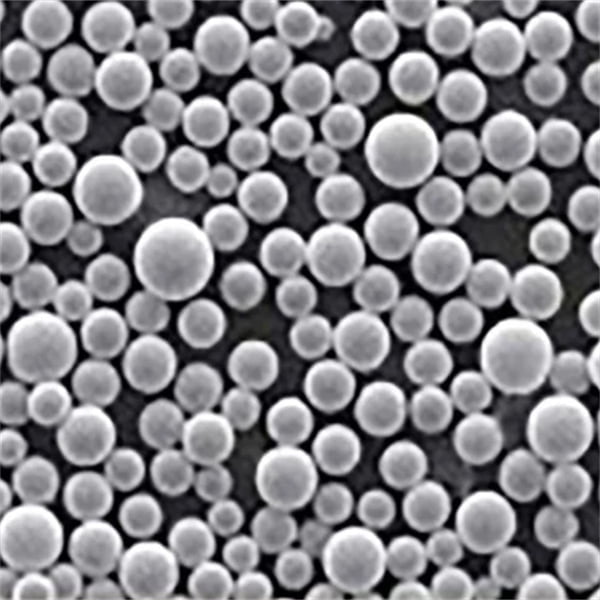
Provoz a údržba atomizéru kovů
Klíčové aspekty provozu systému atomizace kovů zahrnují:
Provoz atomizéru kovů
Aktivity | Podrobnosti |
---|---|
Manipulace se surovinami | Používejte vhodné rukavice, nádoby na vsázku kovu |
Čištění kelímku | Odstraňte zbytky, strusku broušením, mořením kyselinou |
Vložkování kelímku | Zkontrolujte vložku, v případě potřeby znovu natřete/vyměňte |
Parametry procesu | Udržujte správnou teplotu, tlak, průtoky |
Stav trysky | Zkontrolujte trysky, zda nejsou opotřebované, ucpané |
Manipulace s práškem | Zajistěte správné nádoby, postupy přenosu |
Kontrola zařízení | Zkontrolujte těsnění, konektory, bezpečnostní systémy |
Údržba | Naplánujte preventivní údržbu, opravy |
Při manipulaci se surovými kovovými kusy by se měly používat vhodné ochranné prostředky, aby se zabránilo kontaminaci. Tavicí kelímek vyžaduje pravidelné čištění a údržbu žáruvzdorné výstelky.
Důležité je pečlivé sledování procesních parametrů, jako je teplota, tlak a průtok plynu. Trysky, zejména pro atomizaci plynem, vyžadují pravidelnou kontrolu a výměnu.
Jemný prášek, který se vyrábí, vyžaduje pečlivou manipulaci, aby se zabránilo rizikům expozice. Pravidelné kontroly pomáhají odhalit úniky, poškození a zajistit, aby všechny bezpečnostní systémy fungovaly. Preventivní údržba by měla být naplánována, aby se předešlo poruchám.
Výběr dodavatele atomizéru kovového prášku
Klíčové faktory při výběru dodavatele systému atomizace kovů:
Výběr dodavatele atomizéru kovů
Kritéria | Úvahy |
---|---|
Technické znalosti | Zkušenosti, odborný personál |
Rozsah vybavení | Laboratorní, pilotní, průmyslové systémy |
Záznamy | Relevantní případové studie, seznam klientů |
Přizpůsobení | Flexibilita pro specifické požadavky |
Poprodejní servis | Podpora instalace, smlouvy o údržbě |
Cena | Cenové nabídky odpovídající rozpočtu |
Spolehlivost | Kvalita zpracování a osvědčený výkon |
Bezpečnost | Splňuje všechny průmyslové bezpečnostní normy |
Certifikace | Certifikace ISO nebo jiná certifikace kvality |
Hledejte zavedenou společnost se zkušenostmi v oblasti tepelného stříkání nebo práškové metalurgie. Měli by nabízet celou řadu atomizérů od laboratorních prototypů až po velkovýrobu.
Požádejte o reference klientů a případové studie relevantní pro vaši konkrétní aplikaci. Hledejte přizpůsobená řešení pro vaše potřeby kapacity a charakteristiky prášku.
Vyhodnoťte poprodejní servisní podporu, jako je dohled nad instalací, školení obsluhy, smlouvy o údržbě atd. Zvažte cenu, ale upřednostněte výkon, bezpečnost a spolehlivost.
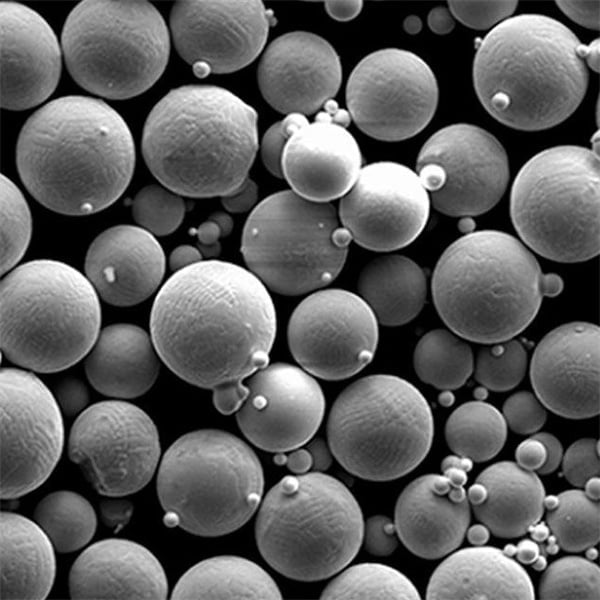
Závěr
Atomizace kovů je účinný proces pro výrobu čistých, sférických jemných kovových prášků z různých slitin pro pokročilé aplikace v letectví, automobilovém průmyslu, aditivní výrobě a dalších průmyslových odvětvích.
Systémy atomizace plynem a odstředivé atomizace se skládají z jednotek pro tavení kovů, tvorbu kapiček a sběr prášku. Pro dosažení požadované velikosti částic a charakteristik prášku je vyžadován pečlivý návrh.
Přední dodavatelé nabízejí standardní a přizpůsobené atomizační systémy v malých až velkých průmyslových kapacitách s vhodnou poprodejní podporou. Výběr správného dodavatele a dodržování správných provozních postupů zajišťuje hladké fungování a maximální produkci prášku.
Nejčastější dotazy
Otázka: Jaký je typický rozsah kapacity systémů atomizace kovů?
Odpověď: Systémy atomizace kovů jsou k dispozici v kapacitách od 10 kg/h pro laboratoře/pilotní měřítko až po více než 5000 kg/h pro velkoobjemovou průmyslovou výrobu. Možné jsou i větší kapacity až do 10 000 kg/h.
Otázka: Která průmyslová odvětví běžně používají atomizaci kovů?
Odpověď: Mezi klíčová průmyslová odvětví využívající atomizaci kovů patří letectví, automobilový průmysl, aditivní výroba, prášková metalurgie, elektronika a chemický průmysl. Jemné, sférické prášky se používají k výrobě kritických součástí.
Otázka: Jak jemná může být velikost částic prášku?
Odpověď: Při atomizaci plynem lze dosáhnout velikosti prášku až 10 mikronů optimálním návrhem trysek, tlaku plynu a průtoků. Odstředivá atomizace obvykle vytváří hrubší prášky o velikosti více než 20 mikronů.
Otázka: Jaké kovy lze atomizovat?
Odpověď: Většina technických kovů s bodem tání pod 1800 °C lze atomizovat. Běžnými příklady jsou slitiny niklu, železa, kobaltu a titanu. Některé reaktivní kovy, jako je hliník a hořčík, lze také atomizovat za kontrolovaných podmínek.
Otázka: Jaké plyny se používají při atomizaci plynem?
Odpověď: Dusík a argon se používají nejrozšířeněji díky své inertnosti a dostupnosti. V některých případech se používá také kyslík nebo vzduch, ale může kontaminovat prášek.
Otázka: Jaké jsou provozní náklady atomizačních systémů?
Odpověď: Provozní náklady jsou vyšší než u mechanického mletí, protože je nutná nepřetržitá dodávka vysokotlakého plynu. K nákladům se navíc přidává elektrická energie pro indukční ohřev a údržbu kelímku/trysky.
Otázka: Jakým bezpečnostním aspektům je třeba věnovat pozornost?
Odpověď: Vysokoteplotní taveniny kovů, inertní plyny pod tlakem, jemné hořlavé prášky vyžadují pečlivou manipulaci a bezpečnostní systémy pro prevenci požáru a výbuchu. Důkladné zaškolení obsluhy je nutností.
Otázka: Jaká údržba je pro zařízení vyžadována?
Odpověď: Kontrola a výměna trysek, oprava/vložkování kelímku, kontrola těsnosti, čištění vzduchových filtrů jsou typické úkoly údržby. Plánovaná preventivní údržba minimalizuje poruchy.
Otázka: Lze atomizovat kovové slitiny?
Odpověď: Ano, kovové slitiny lze snadno atomizovat přidáním legujících prvků, jako je chrom, hliník, titan, do tavicího kelímku v přesných poměrech, aby se získalo požadované složení.
Otázka: Lze atomizaci kovů provádět v malém měřítku?
Odpověď: Ano, dodavatelé nabízejí laboratorní atomizéry s kelímky o kapacitě 1-5 kg pro výrobu prášku v malých dávkách, jako jsou účely výzkumu a vývoje. Provozní náklady na kg jsou však vyšší.
Sdílet na
MET3DP Technology Co., LTD je předním poskytovatelem řešení aditivní výroby se sídlem v Qingdao v Číně. Naše společnost se specializuje na zařízení pro 3D tisk a vysoce výkonné kovové prášky pro průmyslové aplikace.
Dotaz k získání nejlepší ceny a přizpůsobeného řešení pro vaše podnikání!
Související články
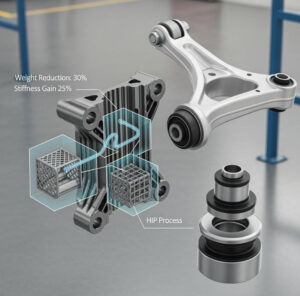
Metal 3D Printed Subframe Connection Mounts and Blocks for EV and Motorsport Chassis
Přečtěte si více "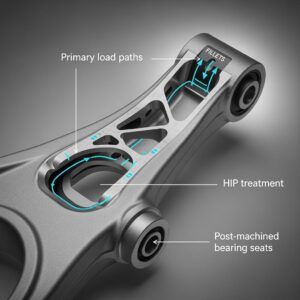
Metal 3D Printing for U.S. Automotive Lightweight Structural Brackets and Suspension Components
Přečtěte si více "O Met3DP
Nedávná aktualizace
Náš produkt
KONTAKTUJTE NÁS
Nějaké otázky? Pošlete nám zprávu hned teď! Po obdržení vaší zprávy obsloužíme vaši žádost s celým týmem.