tryskový roztok kovového pojiva
Obsah
Představte si, že vyrábíte složité kovové předměty s nesrovnatelnou přesností, to vše z digitálního plánu. Toto je kouzlo tryskový roztok kovového pojiva, špičková technologie aditivní výroby (AM), která mění způsob, jakým navrhujeme a vyrábíme složité kovové díly.
Ale jak přesně tento proces funguje? Připoutejte se, protože se noříme hluboko do světa kovového pojiva tryskáním, zkoumáme jeho základní komponenty, aplikace a jedinečné výhody, které nabízí.
Přísady z tryskový roztok kovového pojiva
V srdci tryskání kovových pojiv leží silné trio:
- Kovový prášek: Základ vaší tvorby! Kovové prášky se dodávají v různých jakostech a velikostech v závislosti na požadovaných konečných vlastnostech součásti. Nerezová ocel, Inconel, titan a hliník jsou jen některé příklady běžně používaných kovových prášků.
- Roztok pojiva: Toto funguje jako lepidlo, držící kovové částice pohromadě vrstvu po vrstvě. Pojiva mohou být organická nebo anorganická a jejich výběr významně ovlivňuje požadované kroky následného zpracování.
Představte si to jako stavění z Lega. Kovový prášek představuje kostky Lego a pojivovým roztokem je speciální lepidlo, které je udržuje spojené, aby vytvořily požadovanou strukturu.
- Tiskový systém: Hlavní mozek operace. Tento sofistikovaný systém precizně nanáší roztok pojiva na kovové práškové lože a pečlivě vytváří váš 3D objekt vrstvu po vrstvě.
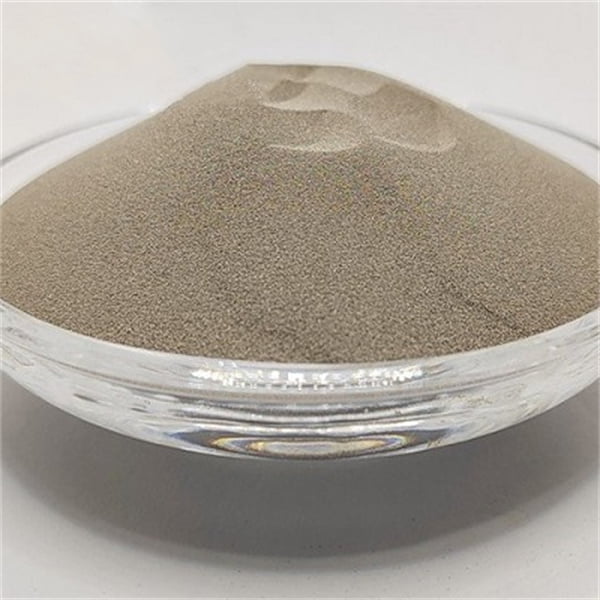
roztok kovového pojiva: Dobrodružství krok za krokem
Nyní se vydejme na cestu krok za krokem, abychom byli svědky toho, jak se rozvíjí kouzlo kovového pojiva:
- Digitální design: Dobrodružství začíná vaší vizí převedenou do 3D modelu počítačem podporovaného navrhování (CAD). Tento plán slouží jako plán pro tisk.
- Roztírání prášku: Tenká vrstva kovového prášku je pečlivě rozprostřena po tiskové platformě, podobně jako položení základu pro vaši tvorbu.
- Binder Jetting v akci: Tisková hlava, stejně jako zkušený umělec se štětcem, přesně nanáší roztok pojiva na konkrétní oblasti práškového lože a přilepuje kovové částice dohromady podle vašeho návrhu CAD.
- Vrstva po vrstvě: Tento fascinující tanec rozprašování prášku a tryskajícího pojiva pokračuje a pečlivě staví váš objekt jednu vrstvu po druhé. Představte si skládání kostek Lego vrstvu po vrstvě, ale s mnohem jemnějším rozlišením!
- Objevuje se zelená část: Po dokončení procesu tisku vám zůstane křehká, nesvázaná struktura nazývaná „zelená část“. Podobá se konečné podobě, ale postrádá pevnost a hustotu hotového kovového předmětu.
- Post-processing Powerhouse: Zde prochází zelená část proměnou. V závislosti na použitém pojivu může zahrnovat proces odstraňování pojiva k odstranění pojivového materiálu. Poté je díl sintrován, což je vysokoteplotní tepelné zpracování, které spojuje kovové částice dohromady a dodává mu konečnou pevnost a hustotu.
Představte si fázi následného zpracování jako transformační komoru pro vaši tvorbu. Stejně jako se superhrdina vynoří ze svého kokonu, vaše kovová část získá svou konečnou sílu a robustnost.
Aplikace tryskový roztok kovového pojiva
Tryskání kovového pojiva není jednoduchý poník. Jeho všestrannost mu umožňuje vyniknout v různých aplikacích:
- Letectví a obrana: Schopnost vyrábět lehké komponenty s vysokou pevností, jako jsou součásti motoru a tepelné štíty, z něj činí cennou výhodu v těchto odvětvích.
- Automobilový průmysl: Prototypování a vytváření složitých dílů pro vozidla je další oblastí, kde se leskne tryskání kovových pojiv.
- Lékařské přístroje: Výroba přizpůsobených implantátů a protetiky, které vyžadují složité geometrie, se pro tuto technologii dokonale hodí.
- Spotřební zboží: Od šperků na míru až po složité hardwarové komponenty, tryskání kovových pojiv otevírá dveře pro inovativní design produktů.
Možnosti jsou opravdu nekonečné! Stejně jako švýcarský armádní nůž může tryskání kovového pojiva řešit širokou škálu problémů v různých průmyslových odvětvích.
Tryskání kovových pojiv vs. jiné technologie Metal AM
Tryskání kovového pojiva není jediným uchazečem v aréně 3D tisku na kovové díly. Srovnejme to s dalšími dvěma populárními technologiemi:
- Laserové selektivní tavení kovů (SLM): Podobnosti: Oba vytvářejí složité kovové díly z digitálního souboru. Rozdíly: SLM taví kovový prášek pomocí vysoce výkonného laseru, výsledkem je hustší a pevnější konečný produkt. SLM je však obvykle pomalejší a dražší ve srovnání s tryskáním pojiva.
Představte si Metal SLM jako vysoce výkonného laserového sochaře, který pečlivě taví kovový prášek a vytváří velmi pevnou a hustou součást. Tento proces tvarování však může být pomalejší a dražší.
- Metal Fused Deposition Modeling (FDM) Oba využívají ke stavbě objektu vrstvený přístup. Rozdíly: FDM používá vlákno z plastu napuštěného kovem, které se taví a nanáší vrstvu po vrstvě. Finální část pak vyžaduje dodatečné dodatečné zpracování pro odstranění pojiva a spékání pro dosažení konečné kovové podoby. Tryskání kovového pojiva na druhé straně používá čistý kovový prášek, což má za následek přímější cestu ke kovovému předmětu.
Představte si Metal FDM jako 3D tiskárnu využívající plastová vlákna napuštěná kovem. I když může nakonec vytvářet kovové části, vyžaduje to další kroky ve srovnání s přímým přístupem k kovovému prášku tryskáním pojiva.
Klíčový závěr: Tryskání kovového pojiva nabízí přesvědčivou rovnováhu mezi rychlostí, hospodárností a schopností vytvářet složité geometrie. Zatímco SLM poskytuje vynikající pevnost a hustotu a FDM nabízí širší škálu materiálů, pojivové tryskání vyniká efektivní výrobou složitých kovových dílů za konkurenceschopnou cenu.
Výhody a úvahy o tryskání kovových pojiv
Tryskání kovového pojiva se může pochlubit několika výhodami, které z něj činí atraktivní volbu pro různé aplikace:
- Rychlost a efektivita: Ve srovnání s jinými kovovými AM technologiemi nabízí pojivo jetting vyšší rychlost tisku, takže je ideální pro velkoobjemové výrobní série.
- Efektivita nákladů: Tento proces využívá méně materiálového odpadu a vyžaduje méně energie ve srovnání s některými metodami metal AM, což vede k nižším výrobním nákladům.
- Svoboda designu: Schopnost vytvářet složité geometrie se složitými vlastnostmi je významnou výhodou pojiva tryskáním. Podříznutí, kanály a další složité detaily lze snadno začlenit do návrhu.
- Všestrannost materiálu: Při tryskání pojiva lze použít širokou škálu kovových prášků, což umožňuje vytvářet díly s různými materiálovými vlastnostmi.
Je však důležité vzít v úvahu některá omezení tryskání kovového pojiva:
- Požadavky na následné zpracování: Kroky odstraňování pojiva a slinování zvyšují složitost procesu ve srovnání s technikami, které poskytují plně hustý finální díl přímo z tiskárny.
- Síla a hustota dílu: Zatímco slinování součást zpevňuje, tryskání kovovým pojivem obvykle vede k mírně nižší hustotě konečné součásti ve srovnání s SLM.
Tryskání kovového pojiva je jako vysoce výkonný, ale ekonomický sportovní vůz. Nabízí rychlost, efektivitu a flexibilitu designu, ale nemusí být tou nejvýkonnější možností, když je nejvyšší prioritou čistá síla.
Odborníci hovoří: Průmyslové poznatky o tryskání kovových pojiv
Zde je to, co přední odborníci v oboru říkají o tryskání kovových pojiv:
- Dr. Sarah Jones, ředitelka AM Research ve společnosti XYZ Inc.: "Jetování kovovým pojivem rychle dospívá a stává se životaschopnější možností pro produkční aplikace. Pokrok v technologii pojiva a technikách následného zpracování posouvá hranice toho, co je s touto technologií dosažitelné."
- Pan David Li, generální ředitel společnosti ABC Metal Printing: "Nákladová efektivita a svoboda designu, které nabízí metalické spojování tryskáním, mění hru v mnoha průmyslových odvětvích. Zaznamenáváme prudký nárůst zájmu ze strany společností, které chtějí vyrábět složité, lehké kovové díly pro různé aplikace."
Tyto expertní posudky zdůrazňují rostoucí uznání potenciálu kovového pojiva tryskáním způsobit revoluci ve výrobě kovů AM.
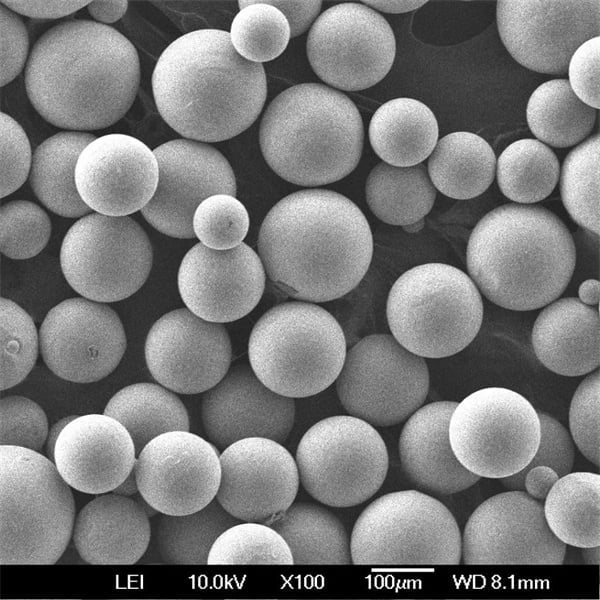
Budoucnost tryskový roztok kovového pojiva
Budoucnost kovového pojiva tryskáním překypuje vzrušujícími možnostmi:
- Pokročilá pojiva: Klíčovou oblastí zájmu je vývoj nových pojivových materiálů, které vyžadují méně složité nebo nízkoteplotní procesy odstraňování pojiva.
- Vylepšené slinovací techniky: Pokračuje výzkum optimalizace parametrů slinování pro dosažení vyšší hustoty finálního dílu, což posouvá hranice možností tryskání kovových pojiv.
- Hybridní AM přístupy: Kombinace tryskání kovového pojiva s dalšími technologiemi AM, jako je tavení laserem, by mohla otevřít nové možnosti pro vytváření dílů s odstupňovanými vlastnostmi nebo integrovanými funkcemi.
Tryskání kovového pojiva je připraveno stát se v nadcházejících letech ještě robustnější a všestrannější technologií. Představte si budoucnost, kde se složité kovové díly budou vyrábět efektivně a levně, s vlastnostmi přizpůsobenými konkrétním aplikacím. To je vzrušující budoucnost, kterou tryskání kovových pojiv slibuje.
FAQ
Otázka: Jaké jsou typické velikosti dílů, které lze vyrobit tryskáním kovového pojiva?
Odpověď: Tryskáním kovového pojiva lze vyrobit díly o velikosti od několika milimetrů do několika centimetrů. Maximální velikost závisí na konkrétních možnostech tiskárny.
Otázka: Je tryskání kovového pojiva vhodné pro kusovou výrobu nebo velké série?
Odpověď: Tryskání kovového pojiva je vhodné pro oba scénáře. Nabízí výhody pro kusovou výrobu díky své rychlosti a konstrukční flexibilitě. Vyniká však také ve velkoobjemových výrobních sériích díky svému efektivnímu procesu a sníženému plýtvání materiálem ve srovnání s některými jinými kovovými AM technikami.
Otázka: Jaká je povrchová úprava kovových dílů tryskaných vstřikováním v porovnání s jinými kovovými AM technologiemi?
Odpověď: Povrchová úprava kovových dílů tryskaných tryskou se může lišit v závislosti na použitém kovovém prášku a použitých technikách následného zpracování. Obecně může být povrchová úprava mírně drsnější ve srovnání s technikami, jako je SLM. Pro dosažení hladšího povrchu však lze použít techniky obrábění nebo leštění, pokud to aplikace vyžaduje.
Otázka: Jaké jsou některé ekologické výhody tryskání kovových pojiv?
A: Tryskání kovového pojiva nabízí několik ekologických výhod:
- Snížení množství materiálového odpadu: Tento proces efektivně využívá nepoužitý kovový prášek, čímž se minimalizuje odpad ve srovnání s tradičními subtraktivními výrobními technikami.
- Nižší spotřeba energie: Tryskání pojiva obvykle vyžaduje méně energie ve srovnání s některými kovovými AM metodami, jako je SLM, což vede ke snížení ekologické stopy.
- Optimalizace designu: Schopnost vytvářet lehké díly se složitou geometrií může přispět ke zvýšení palivové účinnosti v aplikacích, jako je letecký a automobilový průmysl.
Minimalizací odpadu, snížením spotřeby energie a umožněním výroby lehkých dílů přispívá tryskání kovového pojiva k udržitelnějšímu výrobnímu přístupu.
Závěr:
Tryskání kovových pojiv se ukázalo jako silný uchazeč v oblasti výroby kovových přísad. Jeho schopnost vyrábět složité kovové díly s rychlostí, hospodárností a svobodou návrhu z něj činí přesvědčivou volbu pro různé aplikace. Vzhledem k tomu, že se technologie neustále vyvíjí s pokroky v materiálech a procesech, je tryskání kovových pojiv připraveno k revoluci ve způsobu, jakým navrhujeme, prototypujeme a vyrábíme složité kovové součásti v různých průmyslových odvětvích.
Sdílet na
MET3DP Technology Co., LTD je předním poskytovatelem řešení aditivní výroby se sídlem v Qingdao v Číně. Naše společnost se specializuje na zařízení pro 3D tisk a vysoce výkonné kovové prášky pro průmyslové aplikace.
Dotaz k získání nejlepší ceny a přizpůsobeného řešení pro vaše podnikání!
Související články
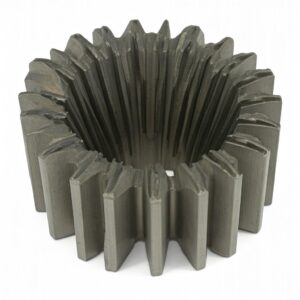
Vysoce výkonné segmenty lopatek trysek: Revoluce v účinnosti turbín díky 3D tisku z kovu
Přečtěte si více "O Met3DP
Nedávná aktualizace
Náš produkt
KONTAKTUJTE NÁS
Nějaké otázky? Pošlete nám zprávu hned teď! Po obdržení vaší zprávy obsloužíme vaši žádost s celým týmem.
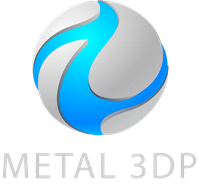
Kovové prášky pro 3D tisk a aditivní výrobu