Characteristics of Plasma Atomized Metal Powder
Obsah
Imagine sculpting intricate objects, layer by layer, with exceptional precision and detail. This is the reality of additive manufacturing (AM), a revolutionary technology rapidly transforming various industries. But the magic behind AM lies not only in the sophisticated printers but also in the powdered metal they utilize.
Among various kovový prášek production methods, atomizace plazmatu stands out for its ability to create high-quality, spherical powders with unique characteristics. This article delves deep into the world of plasma-atomized metal powders, exploring their properties, applications, and specific models, empowering you to understand their potential and make informed decisions.
Co je plazmová atomizace?
Imagine a high-powered torch capable of generating intense heat, exceeding 30,000°C! This is the essence of the plasma atomization process. In this method, a plasma arc melts the metal feedstock, transforming it into a molten liquid. Subsequently, a high-speed gas stream breaks down the molten metal into tiny droplets, which rapidly solidify into spherical metal particles as they fall through a cooling chamber.
This process offers several advantages over traditional methods, including:
- Vysoká čistota: The high temperature and inert atmosphere minimize contamination.
- Kulovitý tvar: This enhances flowability and packing density, crucial for AM processes.
- Velikost jemných částic: Enables the creation of intricate details in printed parts.
- Vlastnosti na míru: Various process parameters can be adjusted to achieve specific powder characteristics.
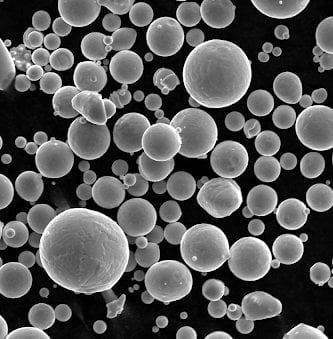
Key Characteristics of Plasma-Atomized Kovové prášky
[Table 1: Key Characteristics of Plasma-Atomized Metal Powders]
Charakteristický | Popis |
---|---|
Particle size & distribution | Typically ranges from 10 to 150 microns, with controlled distribution crucial for consistent packing density. |
Kulovitost | Ideally close to perfect spheres, affecting flowability and packing efficiency. |
Tekutost | Plays a vital role in powder handling and spreading in AM processes. |
Zdánlivá hustota | Measures the mass of powder per unit volume, impacting powder handling and storage. |
Hustota poklepání | Represents the density after tapping the powder, affecting packing efficiency in AM. |
Chemické složení | Closely monitored to ensure consistent material properties in the final product. |
Surface morphology | Refers to the surface texture and presence of oxides, influencing various properties. |
Mikrostruktura | Grain size and distribution impact mechanical properties like strength and ductility. |
Understanding these characteristics empowers manufacturers to select the optimal powder for their specific application, ultimately influencing the quality and performance of the final product.
Exploring the Applications of Plasma-Atomized Metal Powders
Due to their exceptional properties, plasma-atomized metal powders find application in various industries, including:
[Table 2: Applications of Plasma-Atomized Metal Powders]
Průmysl | aplikace | Výhody |
---|---|---|
Additive manufacturing (AM) | 3D printing of complex metal parts | High precision, good surface finish, diverse material options |
Aerospace & defense | Lightweight components, aircraft engine parts, rocket nozzles | High strength-to-weight ratio, excellent mechanical properties |
Automobilový průmysl | Engine parts, gears, lightweight components | Enhanced performance, fuel efficiency, design flexibility |
Biomedicína | Implants, prosthetics, dental applications | Biocompatible materials, customized designs for individual needs |
Elektronika | Chladiče, elektronické obaly | High thermal conductivity, precise component fabrication |
Oil & gas | Drilling tools, wear-resistant components | High wear resistance, corrosion resistance |
The diverse applications of plasma-atomized metal powders highlight their versatility and significant contribution to various technological advancements.
Unveiling Specific Kovový prášek Modely
Metal powders, the building blocks of additive manufacturing (AM), come in a diverse range, each boasting unique properties and catering to specific applications. Delving deeper, let’s explore some specific metal powder models across various materials, highlighting their key characteristics and potential uses:
Model kovového prášku | Materiál | Způsob výroby | Klíčové vlastnosti | Potential Applications |
---|---|---|---|---|
APEX Ti-6Al-4V | Titanium-6 Aluminum-4 Vanadium | Plasma Atomization (PA) | High strength, good ductility, excellent biocompatibility | Aerospace components, biomedical implants, sports equipment |
AMCP AlSi10Mg | Hliník Křemík Hořčík | Atomizace plynu (GA) | Lehká konstrukce, dobrá odolnost proti korozi, vysoká tepelná vodivost | Automotive components (e.g., engine blocks, heat sinks), consumer electronics (e.g., housings), food packaging |
EOS Stainless Steel 316L | Nerezová ocel 316L | PA | High corrosion resistance, biocompatible, good mechanical properties | Medical instruments, chemical processing equipment, jewelry, tools |
Höganäs IN625 | Nickel-62.5% Chromium | PA | Vynikající pevnost při vysokých teplotách, odolnost proti oxidaci | Superalloy components for turbine blades, heat exchangers, other high-temperature applications |
Carpenter Cobalt-Chrome (AM) | Kobalt-chrom | PA | Vysoká odolnost proti opotřebení, biokompatibilní | Hardfacing materials for wear resistance, dental implants, magnetic components |
LPW Maraging Steel 1.2709 | Maraging Steel (1.2709 grade) | PA | High strength-to-weight ratio, good toughness | Aerospace components, tooling applications requiring high strength and toughness |
SLM Solutions Inconel 625 | Inconel 625 (Nickel-Chromium-Molybdenum alloy) | PA | Excellent high-temperature strength, oxidation resistance, corrosion resistance | Lopatky turbín, výměníky tepla, zařízení pro chemické zpracování. |
Renishaw AM260 | Aluminum Magnesium Scandium | PA | Lightweight, high strength, excellent weldability | Aerospace components, high-performance automotive parts |
ExOne Copper PA | Měď | PA | High thermal conductivity, good electrical conductivity | Chladiče, elektrické komponenty, aplikace tepelného managementu |
Desktop Metal 17-4 PH Stainless Steel | 17-4 Precipitation Hardening Stainless Steel | PA | High strength, good corrosion resistance, excellent printability | Medical instruments, tooling applications, aerospace components |
Remember, this table represents just a small selection of the vast array of metal powder models available. Each manufacturer offers various grades and compositions within each material category, catering to specific application requirements and user preferences. By understanding the unique properties and potential applications of these models, users can make informed decisions when selecting the right metal powder for their specific AM needs.
It’s crucial to remember that this list is not exhaustive, and new models are constantly being developed. Each model possesses specific properties tailored for various applications. Selecting the appropriate powder requires careful consideration of factors like:
- Intended application: The desired properties of the final product will guide the choice of powder composition and characteristics.
- AM process: Different AM technologies may have specific requirements for powder characteristics, such as particle size and flowability.
- Náklady: The cost of the powder can vary depending on the material, processing methods, and desired properties.
Consulting with reputable metal powder suppliers and AM experts is vital for making informed decisions and selecting the optimal powder for your specific needs.
Understanding the Pros and Cons of Plasma-Atomized Kovové prášky
[Table 4: Pros and Cons of Plasma-Atomized Metal Powders]
Klady | Nevýhody |
---|---|
High purity and consistency | Relatively high cost compared to some traditional methods |
Vynikající tekutost a hustota balení | Requires specialized equipment for handling and storage |
Wide range of available materials | May require post-processing steps for specific applications |
Tailorable properties for specific needs | Environmental considerations due to high energy consumption during production |
While plasma atomization offers numerous advantages, it’s essential to be aware of the potential drawbacks associated with this process. Carefully weighing the pros and cons allows you to make informed decisions about the suitability of this technology for your specific application.
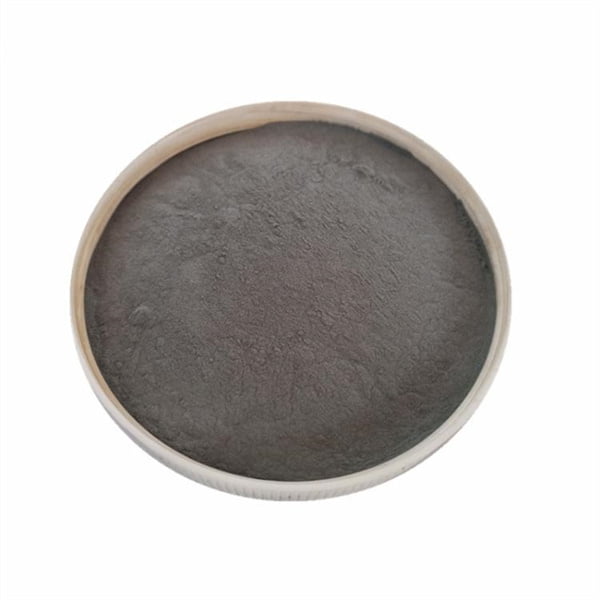
FAQ
[Table 5: Frequently Asked Questions about Plasma-Atomized Metal Powders]
Otázka | Odpovědět |
---|---|
What are the benefits of using plasma-atomized kovové prášky in additive manufacturing? | Plasma-atomized powders offer high purity, consistent morphology, and good flowability, leading to improved quality and printability in AM processes. |
How does the size and distribution of the powder particles impact the final product? | Particle size and distribution significantly affect packing density, surface finish, and mechanical properties of the printed object. |
Can plasma-atomized metal powders be recycled? | Yes, certain types of plasma-atomized metal powders can be recycled, contributing to sustainability and cost reduction. |
What are some emerging trends in plasma atomization technology? | Research is ongoing to develop new techniques for producing even finer powders, exploring alternative feedstock materials, and minimizing the environmental impact of the process. |
By understanding the characteristics, applications, and considerations surrounding plasma-atomized metal powders, you can leverage this technology to unlock its full potential and contribute to advancements in various sectors. As the field of AM continues to evolve, plasma atomization is poised to play a critical role in shaping the future of metal manufacturing.
Sdílet na
MET3DP Technology Co., LTD je předním poskytovatelem řešení aditivní výroby se sídlem v Qingdao v Číně. Naše společnost se specializuje na zařízení pro 3D tisk a vysoce výkonné kovové prášky pro průmyslové aplikace.
Dotaz k získání nejlepší ceny a přizpůsobeného řešení pro vaše podnikání!
Související články
O Met3DP
Nedávná aktualizace
Náš produkt
KONTAKTUJTE NÁS
Nějaké otázky? Pošlete nám zprávu hned teď! Po obdržení vaší zprávy obsloužíme vaši žádost s celým týmem.
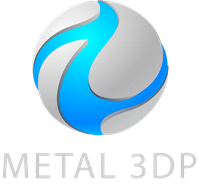
Kovové prášky pro 3D tisk a aditivní výrobu
SPOLEČNOST
PRODUKT
kontaktní informace
- Město Qingdao, Shandong, Čína
- [email protected]
- [email protected]
- +86 19116340731