Přehled kovových prášků MIM
Obsah
mim kovový prášek je univerzální výrobní proces, který umožňuje vyrábět malé kovové díly složitých tvarů ve velkých objemech za použití kovových prášků a plastových pojiv. Tento průvodce nabízí podrobný přehled prášků MIM zahrnující jejich složení, klíčové vlastnosti, použití v různých průmyslových odvětvích, běžné druhy a specifikace, hlavní světové dodavatele s cenovými ukazateli.
Přehled kovových prášků MIM
Prášky MIM jsou kovové prášky kulovitého tvaru speciálně vyvinuté pro proces vstřikování kovů. Vykazují vynikající tokové a obalové vlastnosti ve vstřikovací formě pro dosažení vysoké pevnosti v zeleném stavu před odstraněním pojiva a finálním spékáním dílu.
Klíčové vlastnosti požadované pro kovové prášky používané v technologii MIM:
- Kontrolovaná velikost částic a distribuce velikosti
- Vysoká čistota s nižším obsahem kyslíku a dusíku
- Dobrý tok prášku a vysoká hustota balení
- Mísitelnost a kompatibilita se systémy pojiv
- Kulovitost, nízká pórovitost, málo satelitů a hladká morfologie povrchu
Výsledkem těchto přísných vlastností jsou vysoce kvalitní koncové kovové díly, které kombinují složitost plastových dílů a vysoký výkon obráběných kovových dílů.
Mezi nejběžnější slitiny MIM patří nerezová ocel, nízkolegovaná a nástrojová ocel, magnetické slitiny, těžké slitiny wolframu a slitiny titanu a titanu.
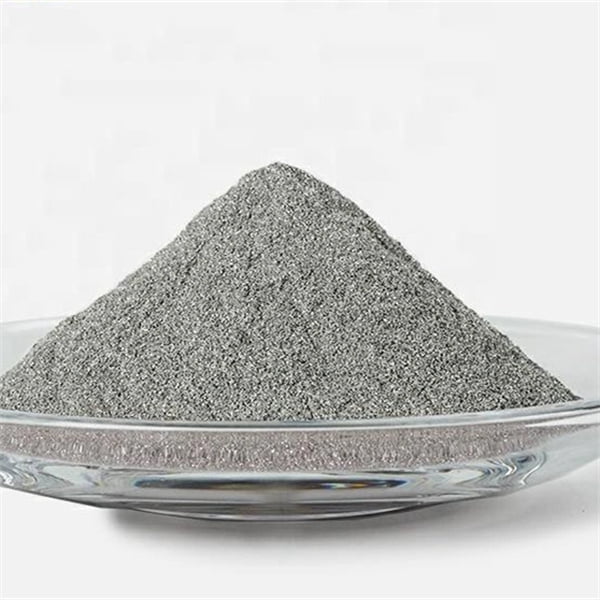
Složení klíčových kovových prášků MIM
MIM je vhodný pro celou řadu materiálů včetně nerezových ocelí, slitinových ocelí, magnetických slitin, titanu, wolframu atd., které jsou optimalizací složení přizpůsobeny konkrétním aplikacím.
Typické složení kovových prášků MIM
Typ slitiny | Klíčové legující prvky |
---|---|
Nerezová ocel | Fe + 17-20% Cr + 8-12% Ni + menší příměsi Mo, Mn, Si |
Nízkolegovaná ocel | Fe + Cr + Mo + Mn + Ni + C |
Nástrojová ocel | Fe + Cr + W + Mo + V + C |
Soft Magnetic | Fe + Ni + Mo , Fe + Cr + Si + Nb + Cu + Ti , Fe + Cr + Co + Mo + Al |
Kobalt Chrome | Co + Cr + Mo + méně významné prvky |
Těžká slitina wolframu | W + Ni + Fe , W + Ni + Cu |
Třída titanu 1-4 | Ti + stopy C, Fe, O, N a H |
Výrobci prášků přizpůsobují poměr klíčových legujících prvků ve spojení s distribucí velikosti částic a výběrem pojiva, aby splnili požadavky na výkon výrobků MIM v této rozmanité škále materiálů od nerezové oceli po slitiny titanu a wolframu.
Klíčové vlastnosti a aplikace prášků MIM
Charakteristiky a typické aplikace napříč kategoriemi slitin MIM:
Typ slitiny | Charakteristika | Aplikace |
---|---|---|
Nerezová ocel | Vysoká pevnost, odolnost proti opotřebení a korozi, biokompatibilita | Zdravotnické prostředky, příbory, ruční nářadí, ventily, vodovodní armatury |
Nízkolegovaná ocel | Tepelně zpracovatelné, velmi vysoká pevnost, odolnost proti opotřebení | Automobilový průmysl, střelné zbraně, ozubená kola, nástrojové destičky |
Nástrojová ocel | Velmi vysoká tvrdost + odolnost proti opotřebení, reakce na tepelné zpracování | Děrovací nástroje, razníky, průmyslové nože, chirurgické nástroje |
Soft Magnetic | Vysoká magnetická permeabilita, nízké ztráty v jádře | Magnetické senzory, díly elektromotorů, relé, magnetické stínění |
Kobalt Chrome | Biokompatibilní, odolnost proti opotřebení + korozi, vysoká tuhost | Ortopedické + zubní implantáty, protetika |
Těžká slitina wolframu | Velmi vysoká hustota, tlumení vibrací | Protizávaží, radiační stínění, vyvažování rotoru |
Titanové slitiny | Nízká hustota, odolnost proti korozi, biokompatibilní | Letectví a kosmonautika, lékařské implantáty, sportovní zboží |
MIM rozšiřuje svobodu konstrukce a rozsah použití všech těchto pokročilých kovových slitin na malé rozměry součástí s nižšími náklady na výrobu čistého tvaru ve srovnání s alternativami, jako je přesné obrábění.
Vstřikování kovů Parametry procesu
Pro dosažení optimálního výkonu technologie MIM je třeba optimalizovat parametry vstupní suroviny a podmínky procesu:
Klíčové fáze a proměnné procesu vstřikování kovů
Fáze | Procesní podmínky |
---|---|
Příprava surovin | Vlastnosti prášku, složení pojiva, proces míchání, podmínky peletizace |
Vstřikování | Teplota formy, tlakové profily, rychlost vstřikování, rychlost chlazení |
Debinding | Rozpouštědlo, tepelné profily, podmínky katalýzy |
Spékání | Atmosféra, teplota, doba zdržení |
Charakteristiky prášku, jako je distribuce velikosti částic, morfologie a čistota, určují mechanické vlastnosti, zatímco pojiva zajišťují potřebnou viskozitu a snadné odstraňování.
Interakce mezi kovovými částicemi, polymery, rozpouštědly a tepelnými gradienty ovlivňují konečné vlastnosti. Po stanovení receptury zajišťuje automatizace konzistenci.
Úloha vlastností prášku při optimalizaci výkonu MIM
Parametr prášku | Dopad na proces a výrobky MIM |
---|---|
Distribuce velikosti částic | Pevnost zeleného dílu a hustota spékání |
Morfologie prášku | Míchání kovových pojiv, balení a tok prášku |
Povrchové hladiny oxidů | Vady jako zbytkový uhlík ovlivňující čistotu |
Satelitní částice | Opotřebení formy ovlivňující životnost nástroje a kvalitu povrchu |
Výrobci prášků proto navrhují aspekty, jako je rozsah velikostí, poměry tvarů, čistota atd., na základě funkčnosti konečného dílu.
Specifikace a kontrolní normy pro prášky MIM
Aby se zajistila vhodnost vstupní suroviny pro proces vstřikování kovů, existují různé národní a mezinárodní specifikace zahrnující limity složení, distribuci velikosti částic, prahové hodnoty nečistot, balení atd.
Klíčové normy ukládající kontrolu kvality a konzistence prášku:
Standard | Účel |
---|---|
ISO 13330 | Určuje distribuci velikosti částic od jemných po hrubé frakce. |
ASTM B215 | Zahrnuje standardní příručku pro odběr vzorků kovových prášků |
MPIF 04 | Zkušební metody pro stanovení hustoty výstřiků, průtoku a stlačitelnosti |
ASTM E345 | Definuje metody chemické analýzy složení prášku |
ASTM B809 | Zabývá se doporučeným balením a přepravou kovových prášků. |
Certifikované prášky připravené pro MIM, podpořené statistickou kontrolou kvality, zajišťují spolehlivý a opakovaný výkon a zkracují dobu kvalifikace. Důsledné vedení záznamů podporuje analýzu vad.
Požadavky na distribuci velikosti částic pro prášky MIM
Rozložení velikosti částic přizpůsobené právě pro proces MIM vede ke konzistentní hustotě balení po miliony vstřikovacích cyklů. Tím se minimalizuje opotřebení formy, zamezuje se vzniku vad zelených dílů a optimalizuje se mechanická integrita spékání.
Typické specifikace distribuce velikosti částic prášků optimalizovaných MIM
Velikost částic (μm) | Nerezová ocel 316L | Nerezová ocel 17-4PH | Nástrojová ocel H13 |
---|---|---|---|
Méně než 5 μm | ≤ 7% | ≤ 6% | ≤ 3% |
5 μm až 15 μm | 10-35% | 15-38% | 35-40% |
15 μm až 45 μm | Zůstatek | Zůstatek | Zůstatek |
Větší než 45 μm | ≤ 7% | ≤ 10% | ≤ 5% |
Střední velikostní rozsah zajišťuje hladký povlak pojiva, nabalování a homogenitu směsi potřebnou pro vysokou hustotu spékání. Minimální jemné částice snižují opotřebení formy, zatímco omezená nadměrná velikost zabraňuje problémům se segregací.
Globální dodavatelé kovových prášků pro MIM
Vzhledem ke zrychlujícímu se růstu průmyslu MIM v důsledku poptávky v automobilovém průmyslu, zdravotnictví a spotřební elektronice patří mezi hlavní světové dodavatele prášků MIM na míru:
Přední výrobci a poskytovatelé přizpůsobených Kovové prášky MIM
Společnost | Umístění centrály |
---|---|
Sandvik Osprey | Neath, Spojené království |
Höganäs | Švédsko |
AMETEK | Spojené státy |
BASF | Německo |
Kovové prášky Rio Tinto | Sorel-Tracy, Kanada |
Jilin Ferroalloys | Čína |
Japonsko Nový kov | Japonsko |
Výroba kovových prášků | Spojené království |
Tito zavedení výrobci kovových prášků mají potřebné odborné znalosti a kontrolní mechanismy v oblasti dezoxidace, atomizace inertním plynem, prosévání, míchání a sférického žíhání, které jsou nezbytné pro suroviny kompatibilní s MIM.
Kromě těchto velkých hráčů nabízí mnoho menších regionálních podniků lehké slitiny, nástrojové oceli atd., ale globální logistika dodávek je omezená.
Globální výrobní kapacita a poptávka po prášcích MIM
Rychle rostoucí využití MIM pro malé přesné součástky v různých aplikacích zvyšuje výrobní kapacitu.
Odhady velikosti globálního trhu se vstřikováním kovových prášků:
- Současná velikost trhu v roce 2022: ~120 000 tun
- Předpokládaná velikost trhu do roku 2027: více než 160 000 tun
- CAGR pro poptávku po prášku v letech 2022-2027: ~6%
MIM proniká na nová území díky růstu poptávky po MIM komponentech využívajících všechny druhy kovů - od drahého zlata, stříbra, platiny až po měď, hliník, hořčík a jejich slitiny, kromě běžných nerezových ocelí, nástrojových ocelí, těžkých slitin wolframu atd.
Cenové trendy a nákladové modely pro kovové prášky MIM
Ceny prášků MIM závisí na složení, úrovni shody kvality, výrobní technologii používané výrobcem prášku a objemu nákupu.
Typická cenová rozpětí pro prášky optimalizované pro MIM:
Materiál | Cena za kg (USD/kg) |
---|---|
Nerezová ocel | 5 – 15 |
Nástrojová ocel | 15 – 30 |
Kobalt Chrome | 50 – 80 |
Titanium Ti64 | 100 – 200 |
Inconel | 150 – 300 |
Obecně platí, že nástrojové oceli, titanové třídy a superslitiny mají vyšší ceny kvůli vlastním nákladům na suroviny a pokročilým technikám výroby prášku, jako je atomizace inertním plynem.
Prášky s vysokou čistotou certifikované pro lékařství a kosmonautiku a s možností sledování šarží vyžadují prémiovou ~30% nad průmyslovou kvalitu. Velcí odběratelé OEM využívají až 20% slevy ze středních cen.
Možnosti úspory nákladů v životním cyklu prášku MIM:
Fáze | Příležitost k úspoře |
---|---|
Kvalifikace | Rychlejší schvalování pomocí zavedených prášků připravených pro MIM |
Zadávání veřejných zakázek | Smluvní velkoobchodní ceny od předních výrobců |
Inventura | Dodávky Just-in-time zabraňují hromadění zásob |
Operace | Opětovné použití získaného prášku po testování složení a distribuce velikosti částic |
Zlepšení procesů dále snižují náklady na díly MIM, takže konstrukce s vysokou složitostí jsou ekonomicky výhodné.
Srovnávací analýza MIM s konkurenčními možnostmi výroby kovů
Proces MIM konkuruje metodám přesného obrábění při výrobě malých složitých kovových dílů.
MIM versus alternativní výrobní technologie - srovnávací analýza
Parametry | Vstřikování kovů (MIM) | Přesné CNC obrábění | Investiční odlévání |
---|---|---|---|
Náklady na zřízení | Vysoká pro plísně | Nižší jako aditivní proces | Střední díky voskovým nástrojům |
Doba realizace | Dlouhé díky konstrukci formy | Rychlejší přechod od CAD k obrábění | Střední kvůli nástrojům |
Geometrická svoboda | Vysoký pro tvarování složitých tvarů | Omezené díky subtraktivnímu přístupu | Schopnosti střední složitosti |
Snížení hmotnosti | Umožňuje odlehčení pomocí optimalizace | Obtížné odstraňování přebytečného materiálu | Do jisté míry možné |
Konzistence částí | Extrémně vysoká | Záleží na dovednostech obsluhy | Poměrně vysoká po zralosti procesu |
Nákladový profil | Úsporné nad 10000-50000 jednotkových objemů | Levnější pod 10000 jednotek | Ideální jsou nízké a střední objemy |
Vertikální škálovatelnost | Velká kapacita prostřednictvím vysokotlakých vstřikovacích strojů | Omezeno velikostí obráběcího stroje | Omezeno kapacitou autoklávu |
MIM poskytuje ve své třídě nejlepší konstrukční flexibilitu v kombinaci s velmi vysokými objemy a snížením hmotnosti za cenu, která je nesrovnatelná s obráběním nebo odléváním, což vede k rychlejšímu zavádění v segmentech automobilového průmyslu, zdravotnictví, spotřební elektroniky a průmyslu.
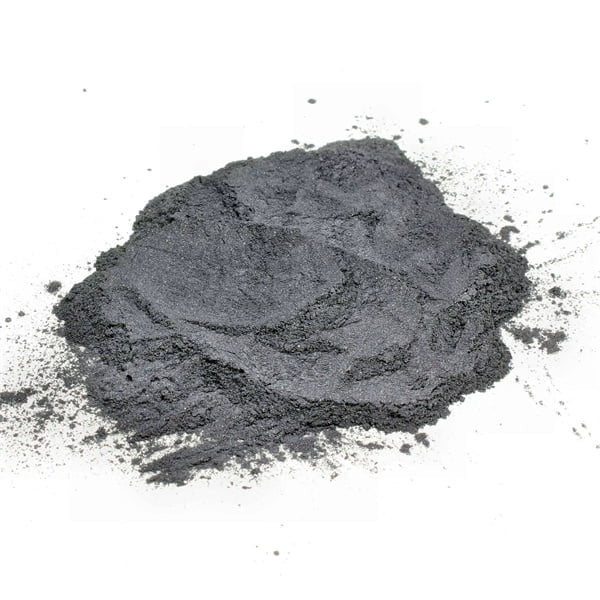
Nejčastější dotazy
Otázka: Jaký kovový prášek se nejčastěji používá při MIM?
Odpověď: Prášek z nerezové oceli 316L je díky optimální kombinaci pevnosti, odolnosti proti korozi, biologické snášenlivosti, ekologické stabilitě a ceně základem pro přibližně 50% veškerého objemu průmyslu MIM.
Otázka: Čím se řídí vlastnosti dílů MIM?
Odpověď: Charakteristiky prášku, jako je distribuce velikosti částic, geometrie a čistota, mají rozhodující vliv na mechanické vlastnosti a kvalitu konečného dílu. Tyto vlastnosti vstupních surovin v kombinaci s proměnnými procesu určují specifikace konečných MIM součástí.
Otázka: Jsou komponenty MIM stejně pevné jako kované kovy?
Odpověď: Správně formulované a zpracované díly dosahují pevnosti >95% kovaného materiálu. HIP (izostatické lisování za tepla) může odstranit vnitřní dutiny a dále zlepšit únavovou odolnost a tvrdost povrchu.
Otázka: Co ovlivňuje ceny prášků MIM?
Odpověď: Ceny závisí na složení (např. drahé kovy jsou dražší), požadovaných úrovních kvality, výrobní technologii používané výrobci prášků a objemech nákupu od výrobců dílů MIM.
Otázka: Může MIM umožnit výrobu lehkých komponent?
Odpověď: Ano, MIM umožňuje výrazné odlehčení díky optimalizaci topologie, která není možná při subtraktivních metodách obrábění, protože umožňuje vyztužení pouze podél cest zatížení. To vede k rychlejšímu přijetí mobility.
Sdílet na
MET3DP Technology Co., LTD je předním poskytovatelem řešení aditivní výroby se sídlem v Qingdao v Číně. Naše společnost se specializuje na zařízení pro 3D tisk a vysoce výkonné kovové prášky pro průmyslové aplikace.
Dotaz k získání nejlepší ceny a přizpůsobeného řešení pro vaše podnikání!
Související články
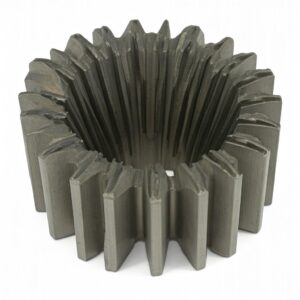
Vysoce výkonné segmenty lopatek trysek: Revoluce v účinnosti turbín díky 3D tisku z kovu
Přečtěte si více "O Met3DP
Nedávná aktualizace
Náš produkt
KONTAKTUJTE NÁS
Nějaké otázky? Pošlete nám zprávu hned teď! Po obdržení vaší zprávy obsloužíme vaši žádost s celým týmem.
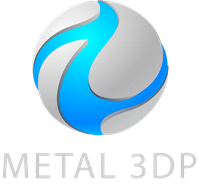
Kovové prášky pro 3D tisk a aditivní výrobu