Zařízení na výrobu prášku
Obsah
Prášky jsou všude kolem nás a hrají zásadní roli v bezpočtu průmyslových odvětví. Od život zachraňujících léků, které přijímáme, až po make-up, který zlepšuje náš vzhled, tyto jemné částice jsou neviditelnými stavebními kameny našeho moderního světa. Ale jak přesně tyto materiály vznikají? Vstupte do fascinující říše zařízení na výrobu prášku, neopěvovaní hrdinové, kteří přeměňují suroviny na mikroskopické zázraky, které utvářejí naše životy.
Různé typy zařízení na výrobu prášku
Svět zařízení na výrobu prášku je překvapivě rozmanitý, přičemž každý stroj je pečlivě navržen tak, aby zpracovával specifické materiály a dosahoval požadované velikosti částic a vlastností. Zde je pohled na některé z nejběžnějších typů:
- mlýnky: Představte si vysoce výkonný mixér na steroidech. Brusky využívají rotující nože nebo kotouče k drcení materiálů pouhou silou. Přemýšlejte o kávové sedlině nebo koření – mlýnky jsou tahouny pro tyto každodenní prášky.
- Drtiče: U tvrdších materiálů, které vyžadují tvrdší přístup, přicházejí na řadu drtiče. Tyto stroje využívají výkonné čelisti nebo kladiva k rozbití hrubé suroviny na menší kousky. Představte si mohutné drtiče kamenů nebo dokonce hmoždíř a paličky – všechny patří do rodiny drtičů.
- mlýny: Mlýny posouvají mletí na zcela novou úroveň a dosahují ultra jemných velikostí částic. Kuličkové mlýny například používají rotující buben naplněný mlecím médiem (jako jsou kuličky nebo oblázky), které omílají a rozdrtí materiál na jemný prášek. Vzpomeňte si na mastek, který nás udržuje chladnými – kulové mlýny jsou pravděpodobně tajnou zbraní za jeho hedvábnou texturou.
- Mikronizéry: Jak název napovídá, mikronizéry jsou nejlepšími umělci ve světě výroby prášku. Tyto stroje využívají techniky, jako je tryskové mletí ve fluidním loži nebo tryskové mletí vzduchem, aby se dosáhlo neuvěřitelně jemných a jednotných velikostí částic. Představte si pigmenty používané ve vašich oblíbených barvách – mikronizéry zajišťují jejich konzistentní barvu a hladkou aplikaci.
- Vzduchové klasifikátory: Ne všichni hrdinové nosí pláštěnky – někteří mají podobu vzduchových třídičů. Tyto chytré stroje pracují ve spojení s mlýnky nebo mlýny a oddělují částice na základě jejich velikosti pomocí přesně řízených proudů vzduchu. Představte si kuchaře, který prosévá mouku – vzduchové třídiče plní podobnou funkci, ale s mnohem větší přesností a automatizací.
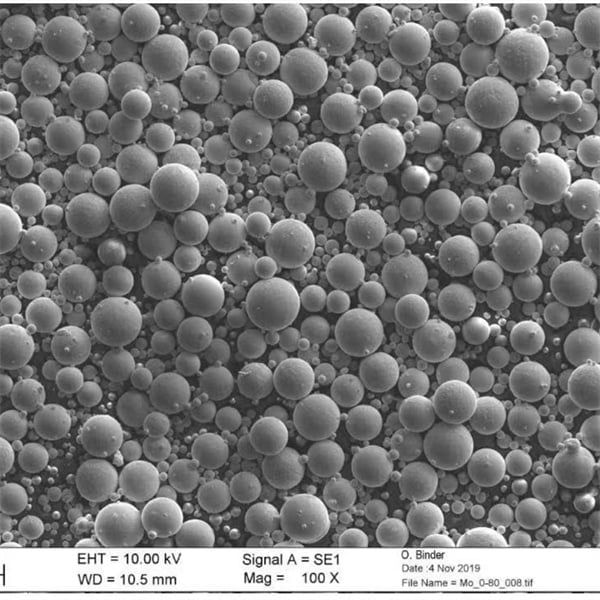
Složení, vlastnosti a vlastnosti prášků vyrobených různými zařízeními
Typ zařízení | Kompoziční dopad | Vliv na majetek | Charakteristický dopad |
---|---|---|---|
Brusky | Omezený dopad | Distribuce velikosti částic může být široká | Prášky mohou mít širší rozsah tvarů a velikostí částic |
Drtiče | Omezený dopad (může zanést určitou kontaminaci z drtivých médií) | Podobně jako u mlýnků | Podobně jako u mlýnků |
Mills | Může způsobit kontaminaci z brusného média | Může dosáhnout velmi jemných velikostí částic s užší distribucí velikosti | Prášky mají tendenci být jednotnější ve tvaru a velikosti |
Mikronizéry | Omezený dopad | Dokáže dosáhnout extrémně jemných a jednotných velikostí částic | Prášky mají velmi vysoký stupeň jednotnosti velikosti a tvaru |
Vzduchové klasifikátory | Žádný dopad (separační technika) | Umožňuje přesnou kontrolu distribuce velikosti částic | Prášky lze upravit tak, aby měly konkrétní rozsahy velikostí pro optimální výkon v různých aplikacích |
Aplikace Zařízení na výrobu prášku
Aplikace zařízení na výrobu prášku jsou tak rozsáhlé jako lidská vynalézavost sama. Zde je jen několik příkladů:
- potravinářský průmysl: Od moučkového cukru a kakaa pro naše dezerty až po koření a kávovou sedlinu, mlýnky a mlýnky jsou páteří práškových surovin potravinářského průmyslu.
- Farmaceutický průmysl: Mikronizery hrají klíčovou roli při vytváření život zachraňujících léků. Přesným řízením velikosti částic zajišťují rovnoměrnou distribuci a absorpci léčiv v našem těle.
- Kosmetický průmysl: Pudry jsou základní složkou make-upu, pigmentů a produktů péče o pleť. Vzduchové třídiče a mikronizéry pomáhají dosáhnout hladkých textur a konzistentních barev, které od těchto produktů očekáváme.
- Chemický průmysl: Široká škála chemikálií, od pigmentů pro barvy až po katalyzátory pro průmyslové procesy, se vyrábí v práškové formě. Zařízení na výrobu prášku umožňuje přesnou kontrolu velikosti částic a vlastností, které jsou klíčové pro optimální chemické reakce.
- Aditivní výroba (3D tisk): Rostoucí oblast 3D tisku spoléhá na specializované zařízení na výrobu prášku k vytvoření jemných kovových nebo plastových prášků používaných v procesu tisku.
Různé typy zařízení na výrobu prášku
Modely kovových práškových výrobců: Odhalení elektráren
Nyní se pojďme ponořit hlouběji do světa zařízení na výrobu kovového prášku. Zde je deset konkrétních modelů, každý se svými přednostmi a aplikacemi:
- Vysokoenergetický kulový mlýn: Tato bruska využívá rotační válcovou komoru naplněnou kuličkami (nebo mlecími médii) vyrobenými z materiálu tvrdšího než cílový kov. Jak se komora otáčí, kuličky narážejí na kovovou surovinu a rozmělňují ji na jemný prášek. Vysokoenergetické kulové mlýny jsou známé svou všestranností, zpracovávají širokou škálu kovů a dosahují širokého spektra velikostí částic. Jsou ideální pro výrobu prášků pro aplikace, jako je vstřikování kovů (MIM) a výroba aditiv.
- Attritor Mill: Představte si vysokorychlostní třepačku barev v průmyslovém měřítku. Attritorové mlýny využívají rotační hřídel s míchadly, které míchají kovovou surovinu spolu s mlecím médiem (často keramickými kuličkami) v komoře. Intenzivní střihové působení rozbíjí kovové částice, což má za následek jemnější a jednotnější prášek ve srovnání s kulovými mlýny. Attritorové mlýny jsou vhodné pro výrobu kovových prášků pro aplikace, jako je pájení natvrdo a tepelné stříkání, kde je rozhodující úzká distribuce velikosti částic.
- Tryskový mlýn: Tryskové mlýny využívající technologicky vyspělý přístup využívají tlakový proud plynu k pohánění částic kovové suroviny proti sobě při vysokých rychlostech. Tento proces kolizního mletí vytváří velmi jemný a jednotný prášek. Tryskové mlýny vynikají ve výrobě vysoce čistých kovových prášků pro aplikace, jako je elektronika a letectví, kde je zásadní přesná velikost částic a minimální kontaminace.
- Tryskový mlýn s fluidním ložem: Tento inovativní mlýn kombinuje principy fluidizace a tryskového mletí. Kovová surovina je suspendována v turbulentním proudu vzduchu v komoře a poté soustředěný proud plynu dále rozkládá částice. Tato technika minimalizuje kontakt mezi částicemi, snižuje kontaminaci a dosahuje výjimečně jemných a jednotných prášků. Tryskové mlýny s fluidním ložem jsou zvláště cenné pro výrobu kovových prášků pro aplikace, jako je pyrotechnika a farmacie, kde je prvořadá čistota a přesná velikost částic.
- Kryogenní mletí: Tento ultranízkoteplotní přístup posouvá výrobu kovového prášku na zcela novou úroveň. Kovová surovina nejprve zkřehne vystavením extrémně nízkým teplotám (často za použití kapalného dusíku). Poté se drtí na prášek pomocí konvenčních mlecích technik, jako je kulové frézování nebo tryskové frézování. Kryogenní mletí minimalizuje tvorbu tepla během procesu, což může být škodlivé pro určité kovy citlivé na teplotu. Tato metoda je zvláště užitečná pro výrobu kovových prášků pro aplikace, jako jsou supravodiče a magnetické slitiny, kde je kritické zachování vlastností materiálu.
Výhody a omezení Zařízení na výrobu prášku
výhody:
- Všestrannost: Zařízení na výrobu prášku dokáže zpracovat širokou škálu materiálů, od měkkých léčiv až po houževnaté kovy.
- Ovladatelnost: Různé stroje nabízejí přesnou kontrolu nad velikostí částic, distribucí velikosti a dalšími vlastnostmi prášku.
- Škálovatelnost: Zařízení je k dispozici v různých velikostech pro potřeby malých výzkumných laboratoří nebo velké průmyslové výroby.
- Efektivita: Moderní zařízení na výrobu prášku je vysoce efektivní, minimalizuje odpad a maximalizuje výrobní výkon.
Omezení:
- Náklady: Pokročilá zařízení, zejména mikronizéry a tryskové mlýny, mohou být nákladnou investicí.
- Složitost: Obsluha některých strojů vyžaduje specializované školení a odborné znalosti.
- Kontaminace: Některá mlecí média nebo procesy mletí mohou do prášku vnést nežádoucí kontaminaci.
- Generování tepla: Proces broušení může generovat teplo a potenciálně měnit vlastnosti některých materiálů citlivých na teplotu.
Výběr správného vybavení: Balancing Act
Výběr nejvhodnějšího zařízení na výrobu prášku závisí na několika faktorech:
- Vlastnosti materiálu: Druh kovu a jeho tvrdost výrazně ovlivňují výběr zařízení.
- Požadovaná velikost a distribuce částic: Požadovaná jemnost a jednotnost prášku určuje potřebnou technologii mletí.
- Objem výroby: Rozsah vašeho provozu – od výzkumné laboratoře po plnohodnotné výrobní zařízení – určuje velikost a kapacitu zařízení.
- Rozpočet: Náklady na zařízení je třeba započítat do celkové ekonomiky výroby.
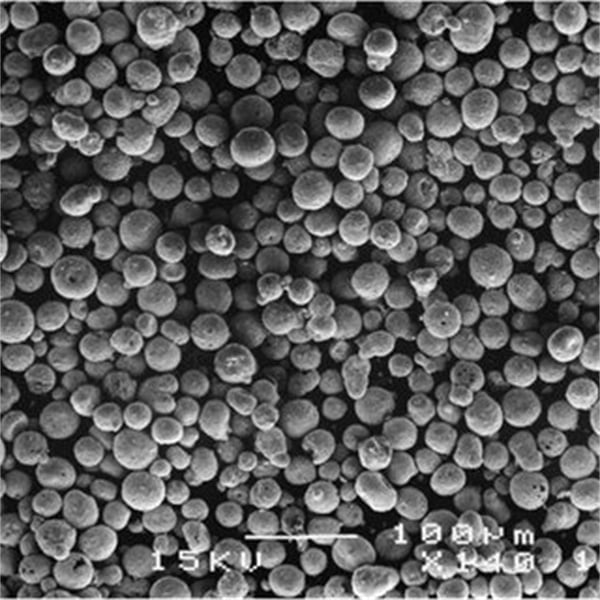
FAQ
Jaký je rozdíl mezi drtičem a mlýnkem?
Drtiče se obvykle používají k rozmělňování velkých kusů materiálu na menší, hrubší kusy. Na druhé straně mlýnky berou tyto menší kousky a rozdrtí je na mnohem jemnější prášek.
Jak mohu ovládat velikost částic prášku?
Při určování konečné velikosti částic hraje roli typ použitého zařízení, výběr mlecího média a parametry procesu, jako je doba a rychlost mletí. Vzduchové třídiče mohou dále zušlechťovat prášek oddělováním částic na základě velikosti.
Jaké zařízení na výrobu prášku existuje?
Typ zařízení, které potřebujete, závisí na materiálu, se kterým pracujete, a požadovaných vlastnostech konečného prášku. Zde jsou dvě hlavní kategorie:
- Brusné zařízení: Tato kategorie rozkládá větší materiály na jemnější částice. Příklady zahrnují kladivové mlýny, kulové mlýny a tryskové mlýny s fluidním ložem.
- Atomizační zařízení: Tato kategorie vytváří prášek z roztavených materiálů. Příklady zahrnují atomizéry taveniny, sprejové sušárny a plazmové atomizéry.
Jaké důležité faktory je třeba vzít v úvahu při výběru zařízení na výrobu prášku?
- Vlastnosti materiálu: Tvrdost, drobivost a obsah vlhkosti vašeho materiálu ovlivní typ vybavení, které potřebujete.
- Požadovaná velikost částic a distribuce: Jak jemný potřebujete, aby byl prášek? Jak konzistentní by měly být velikosti částic?
- Výrobní kapacita: Kolik prášku potřebujete vyrobit za hodinu nebo den?
- Rozpočet: Zařízení na výrobu prášku se může pohybovat v ceně od několika tisíc dolarů až po miliony dolarů.
Existují různé typy strojů na plnění prášku?
Ano, existují dva hlavní typy strojů na plnění prášku:
- Plničky šneků: Tyto stroje používají šroubový mechanismus pro přesné měření a dávkování prášku do nádob. Jsou všestranné a zvládnou širokou škálu typů prášků.
- Objemová plniva: Tyto stroje používají k plnění nádob kelímek nebo jiný systém založený na objemu. Jsou méně přesné než šnekové plničky, ale mohou být vhodné pro některé aplikace.
Jaká bezpečnostní opatření bych měl dodržovat při práci se zařízením na výrobu prášku?
- Používejte vhodné osobní ochranné prostředky (OOP), jako jsou ochranné brýle, maska proti prachu a ochrana sluchu.
- Buďte si vědomi možnosti výbuchu, zejména při práci s hořlavými prášky.
- Zajistěte řádné větrání, aby se zabránilo usazování prachu.
- Dodržujte všechny bezpečnostní pokyny a postupy uvedené v návodu k zařízení.
Sdílet na
MET3DP Technology Co., LTD je předním poskytovatelem řešení aditivní výroby se sídlem v Qingdao v Číně. Naše společnost se specializuje na zařízení pro 3D tisk a vysoce výkonné kovové prášky pro průmyslové aplikace.
Dotaz k získání nejlepší ceny a přizpůsobeného řešení pro vaše podnikání!
Související články
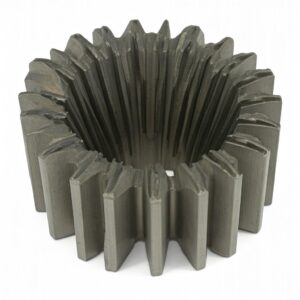
Vysoce výkonné segmenty lopatek trysek: Revoluce v účinnosti turbín díky 3D tisku z kovu
Přečtěte si více "O Met3DP
Nedávná aktualizace
Náš produkt
KONTAKTUJTE NÁS
Nějaké otázky? Pošlete nám zprávu hned teď! Po obdržení vaší zprávy obsloužíme vaši žádost s celým týmem.
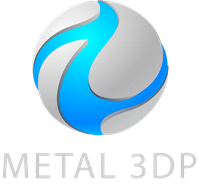
Kovové prášky pro 3D tisk a aditivní výrobu