3D tištěné konektory nosného kužele rakety
Obsah
Úvod: S kovovými 3D tištěnými konektory nosného kužele rakety je nebe neomezené
V neúnavném úsilí o výzkum vesmíru a technologický pokrok hraje každá součást rakety klíčovou roli. Mezi tyto životně důležité součásti patří konektor nosného kužele rakety slouží jako spojovací prvek, který zajišťuje strukturální integritu a bezproblémovou integraci užitečného zatížení s hlavním tělesem rakety. Tyto konektory, které se tradičně vyráběly konvenčními metodami, nyní procházejí revolucí díky nástupu technologie kov 3D tisk, známý také jako aditivní výroba kovů. Tato špičková technologie nabízí nebývalou volnost při navrhování, možnost optimalizace pro odlehčení a potenciál pro rychlé iterace, což z ní činí stále atraktivnější řešení pro letecký průmysl. Na adrese Metal3DP, stojíme v čele této transformace a poskytujeme pokročilé služby služby kovového 3D tisku a vysoce výkonné kovové prášky které umožňují leteckým inženýrům posouvat hranice možností. Náš závazek špičkový objem, přesnost a spolehlivost tiskuspolu s našimi odbornými znalostmi v oblasti materiálů, jako je např Ti-6Al-4V, nás staví do pozice důvěryhodného partnera pro výrobu kritických komponentů, jako jsou konektory nosných kuželů raket. Prozkoumejte naše schopnosti v oblasti 3D tisk z kovu a zjistíte, jak můžeme přispět k vašemu dalšímu projektu v oblasti letectví a kosmonautiky.
K čemu se používají konektory nosného kužele rakety? Zajištění strukturální integrity v leteckých a kosmických aplikacích
Konektory nosného kužele rakety jsou základními součástmi, které v raketovém systému plní několik důležitých funkcí. Především slouží jako konstrukční rozhraní mezi nosným kuželem, v němž je obvykle umístěno užitečné zatížení, naváděcí systémy a vědecké přístroje, a hlavním tělesem nebo horním stupněm rakety. Jejich robustní konstrukce zajišťuje bezpečné a stabilní spojení, které je schopno odolat obrovským silám a vibracím vznikajícím při startu, výstupu do atmosféry a rozmístění užitečného zatížení.
Zde je přehled jejich klíčových použití:
- Konstrukční spojení: Hlavním úkolem je zajistit pevný a spolehlivý spoj, který účinně přenáší zatížení mezi sestavou nosného kužele a zbytkem konstrukce rakety. To má zásadní význam pro zachování celkové integrity vozidla během letu.
- Integrace užitečného zatížení: Tyto konektory často obsahují prvky pro přesné vyrovnání a bezpečné upevnění užitečného zatížení. To může zahrnovat mechanická rozhraní, elektrická připojení a přístupové body pro integraci a testování.
- Aerodynamická stabilita: Konstrukce konektoru může ovlivnit celkový aerodynamický profil rakety, zajistit plynulé proudění vzduchu a minimalizovat odpor vzduchu. Pro zachování zamýšlených aerodynamických vlastností je nezbytná přesná výroba.
- Události spojené s oddělením: U vícestupňových raket může být nutné v určitých okamžicích mise oddělit nosný kužel nebo části obsahující užitečné zatížení. Konstrukce konektoru musí umožňovat řízené a spolehlivé mechanismy oddělení.
- Ochrana životního prostředí: Konektor může přispět k celkovému utěsnění předního kužele a chránit citlivé vnitřní součásti před nepříznivými podmínkami prostředí, jako jsou extrémní teploty a změny tlaku.
Mezi odvětví, která se ve velké míře spoléhají na vysoce výkonné konektory nosného kužele rakety, patří:
- Letectví: Pro vývoj a vypouštění družic, kosmických lodí a různých typů raket.
- Výzkum vesmíru: Umožňuje mise pro vědecký výzkum, cesty do hlubokého vesmíru a zavádění vesmírné infrastruktury.
- Obrana: Pro vojenské aplikace zahrnující raketové systémy a výšková vozidla.
- Komerční lety do vesmíru: Podpora rostoucího sektoru soukromých společností zabývajících se vesmírnou turistikou, dodávkami nákladu a družicovými konstelacemi.
Poptávka po stále složitějších a lehčích raketových systémech vyžaduje pokročilá výrobní řešení. 3D tisk kovů, který nabízejí odborníci jako např Metal3DP, poskytuje flexibilitu při vytváření složitých konstrukcí konektorů přizpůsobených specifickým požadavkům mise a zajišťuje optimální výkon a spolehlivost. Zjistěte více o našich pokročilých tiskových metod a jak mohou prospět vašim projektům v oblasti letectví a kosmonautiky.
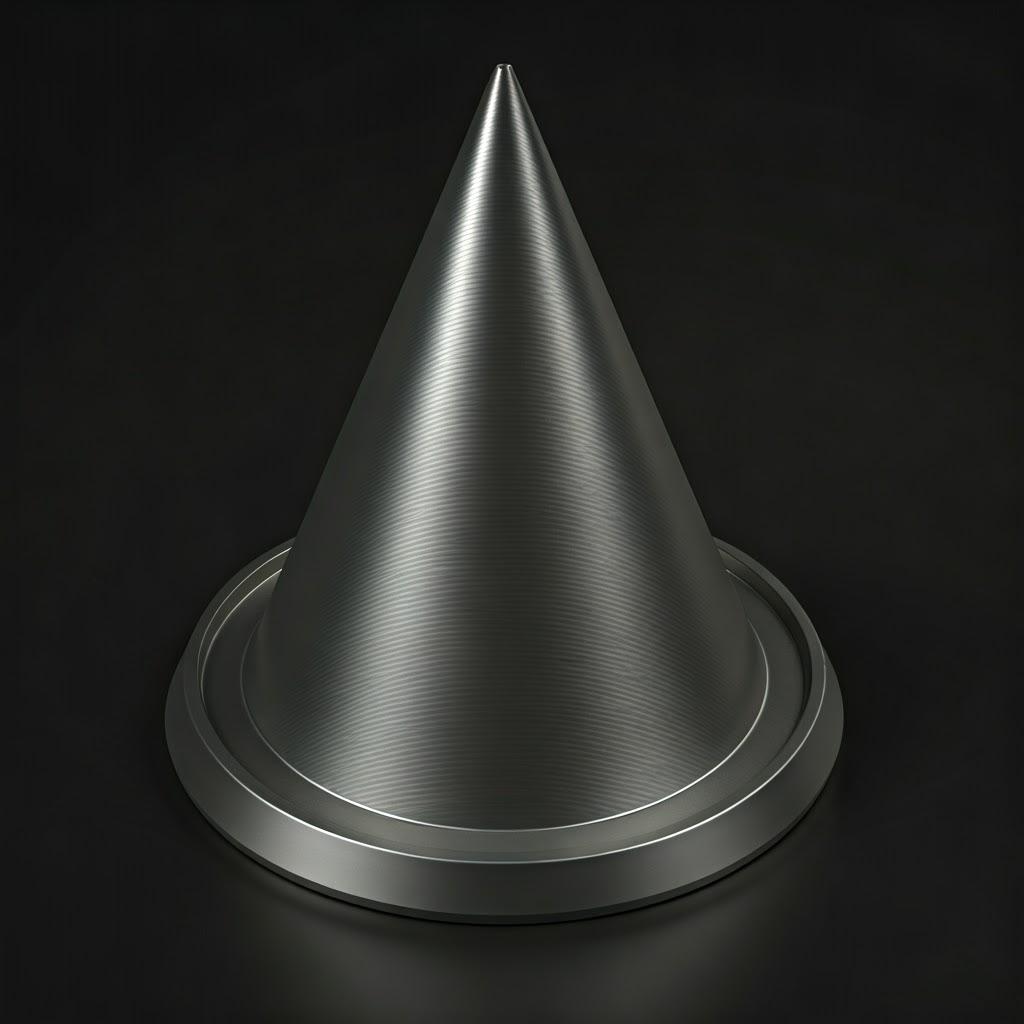
Proč používat kovový 3D tisk pro konektory nosného kužele rakety? Uvolnění svobody designu a výkonu
Přijetí 3D tisk z kovu pro výrobu kuželů nosných částí raket nabízí oproti tradičním výrobním metodám, jako je obrábění nebo odlévání, řadu přesvědčivých výhod. Tyto výhody jsou zvláště významné v náročném leteckém průmyslu, kde jsou rozhodujícími faktory výkon, hmotnost a doba realizace.
Zde jsou hlavní důvody, proč 3D tisk z kovu přináší revoluci ve výrobě těchto důležitých komponent:
- Zvýšená volnost a složitost návrhu: Aditivní výroba umožňuje vytvářet složité geometrie, které tradičními metodami jednoduše nejsou možné nebo nákladově efektivní. Patří sem:
- Optimalizace topologie: Navrhování konektorů s optimalizovaným rozložením materiálu, kdy se materiál umisťuje pouze tam, kde je to nutné pro integritu konstrukce, což vede k výrazné úspoře hmotnosti.
- Mřížové struktury: Začlenění vnitřních mřížových struktur pro další snížení hmotnosti při zachování nebo dokonce zvýšení pevnosti a tuhosti.
- Integrované funkce: Přímý tisk prvků, jako jsou montážní body, kanály pro kabeláž a složité vnitřní chladicí systémy, snižuje potřebu dodatečné montáže a zvyšuje spolehlivost.
- Výrazné snížení hmotnosti: V leteckém průmyslu znamená každý ušetřený kilogram nižší spotřebu paliva a vyšší nosnost. 3D tisk z kovu umožňuje vytvářet lehké a zároveň robustní konektory díky optimalizovanému designu a výběru materiálu.
- Rychlé prototypování a iterace: Aditivní výroba výrazně zkracuje konstrukční a výrobní cyklus. Inženýři mohou rychle vytvářet prototypy, testovat je a opakovat návrhy mnohem rychleji než při použití tradičních metod, což urychluje proces vývoje a zkracuje dobu uvedení na trh.
- Přizpůsobení a výroba na vyžádání: Kovový 3D tisk umožňuje výrobu vysoce přizpůsobených konektorů na míru konkrétním konstrukcím raket a požadavkům mise. Odpadá tak potřeba drahých nástrojů a velkých výrobních sérií, což umožňuje výrobu na vyžádání i malých množství.
- Účinnost materiálu: Aditivní výroba může být materiálově efektivnější než subtraktivní metody, jako je obrábění, protože materiál se přidává pouze tam, kde je to potřeba, což snižuje množství odpadu a související náklady.
- Vyšší výkon a spolehlivost: Optimalizací konstrukce a mikrostruktury materiálu pomocí řízených procesů 3D tisku je možné vyrábět konektory s lepšími mechanickými vlastnostmi, jako je vyšší pevnost, tuhost a odolnost proti únavě, což vede k lepšímu celkovému výkonu a spolehlivosti.
Na Metal3DP, naše služby kovového 3D tisku jsou přizpůsobeny přísným požadavkům leteckého průmyslu. Využíváme pokročilé technologie, jako je selektivní tavení elektronovým svazkem (SEBM), k výrobě vysoce kvalitních, složitých součástí s výjimečnou přesností a vlastnostmi materiálu. Díky našemu závazku k inovacím a kvalitě jsme preferovanou společností dodavatel pro letecké výrobce, kteří hledají špičková řešení.
Doporučené materiály a jejich význam: Ti-6Al-4V a Ti-6Al-4V ELI pro excelenci v leteckém průmyslu
Výběr materiálu je při výrobě konektorů nosného kužele rakety zásadní, protože musí odolávat extrémním podmínkám a poskytovat výjimečnou strukturální integritu. Metal3DP doporučuje Ti-6Al-4V a jeho extra-low intersticiální (ELI) varianta, Ti-6Al-4V ELI, jako ideální kovové prášky pro tuto aplikaci díky svým vynikajícím vlastnostem přizpůsobeným pro letecké a kosmické prostředí.
Zde se podrobně podíváme na to, proč jsou tyto titanové slitiny velmi doporučovány:
Ti-6Al-4V (titan třídy 5): Pracovní kůň v letectví a kosmonautice
- Vysoký poměr pevnosti k hmotnosti: Slitiny titanu jsou známé svou výjimečnou pevností v poměru k hustotě. Ti-6Al-4V nabízí pozoruhodnou rovnováhu mezi vysokou pevností v tahu (přibližně 950 MPa) a nízkou hustotou (přibližně 4,43 g/cm³), což z něj činí ideální materiál pro letecké komponenty citlivé na hmotnost.
- Vynikající odolnost proti korozi: Titan vykazuje vynikající odolnost vůči široké škále korozivních prostředí, včetně slané vody a mnoha chemikálií, což má zásadní význam pro dlouhodobou spolehlivost v leteckých a kosmických aplikacích.
- Dobrá odolnost proti únavě: Při startu a letu rakety dochází ke značnému cyklickému zatížení. Ti-6Al-4V má dobrou únavovou pevnost, která zajišťuje, že konektor vydrží opakované cykly namáhání bez poruchy.
- Výkon při vysokých teplotách: Tato slitina si zachovává své mechanické vlastnosti i při mírně zvýšených teplotách, které se mohou vyskytnout během atmosférického letu.
- Biokompatibilita: Ačkoli je primárně určen pro konstrukční aplikace v raketách, biokompatibilita Ti-6Al-4V je pozoruhodná a důležitá pro potenciální aplikace v kosmických zdravotnických systémech nebo systémech podpory života.
Ti-6Al-4V ELI (titan s velmi nízkou mezerovitostí, třída 23): Zvýšená tažnost a lomová houževnatost
- Vynikající tažnost a houževnatost: Třída ELI Ti-6Al-4V má nižší obsah intersticiálních prvků, jako je kyslík, uhlík, dusík a vodík. Výsledkem je výrazně lepší tažnost a lomová houževnatost ve srovnání se standardním Ti-6Al-4V. To je důležité zejména u součástí, které mohou být zatíženy nárazem nebo vyžadují vysokou odolnost proti šíření trhlin.
- Zvýšená odolnost proti únavě: Nižší obsah intersticiálů také přispívá ke zvýšení únavové životnosti, což z něj činí vynikající volbu pro kritické letecké konstrukce vystavené cyklickému namáhání.
- Vynikající odolnost proti korozi: Podobně jako standardní Ti-6Al-4V nabízí třída ELI výjimečnou odolnost proti korozi.
- Biokompatibilita: Ti-6Al-4V ELI je široce používán v lékařských implantátech díky své vynikající biokompatibilitě a odolnosti proti korozi, což dále zdůrazňuje čistotu a inertnost materiálu.
Proč jsou tyto materiály důležité pro 3D tištěné konektory nosného kužele rakety:
- Odlehčení: Obě slitiny přispívají k výraznému snížení hmotnosti, což je rozhodující faktor pro zlepšení výkonu rakety a snížení nákladů na start.
- Strukturální integrita: Jejich vysoká pevnost a houževnatost zajišťuje, že konektor odolá extrémním silám a vibracím během startu a letu.
- Spolehlivost: Vynikající odolnost těchto titanových slitin proti korozi a únavě zaručuje dlouhodobou spolehlivost v náročných podmínkách leteckého průmyslu.
- Optimalizováno pro aditivní výrobu: Prášky Ti-6Al-4V a Ti-6Al-4V ELI jsou vhodné pro různé procesy 3D tisku z kovů, včetně selektivního laserového tavení (SLM) a tavení elektronovým svazkem (EBM), které Metal3DP využívá k výrobě vysoce kvalitních dílů s konzistentními vlastnostmi. Naše pokročilé systém na výrobu prášku zajišťuje výrobu sférických prášků s vysokou sféricitou a tekutostí, což je nezbytné pro optimální výsledky 3D tisku.
Výběrem Metal3DP jako vaše dodavatel pro služby kovového 3D tisku a využití našich vysoce kvalitních Ti-6Al-4V a Prášky Ti-6Al-4V ELI, můžete dosáhnout vynikajícího výkonu a spolehlivosti konektorů nosného kužele rakety. Kontaktujte nás a zjistěte, jak naše odborné znalosti materiálů a pokročilé výrobní možnosti mohou podpořit vaše inovace v oblasti letectví a kosmonautiky.
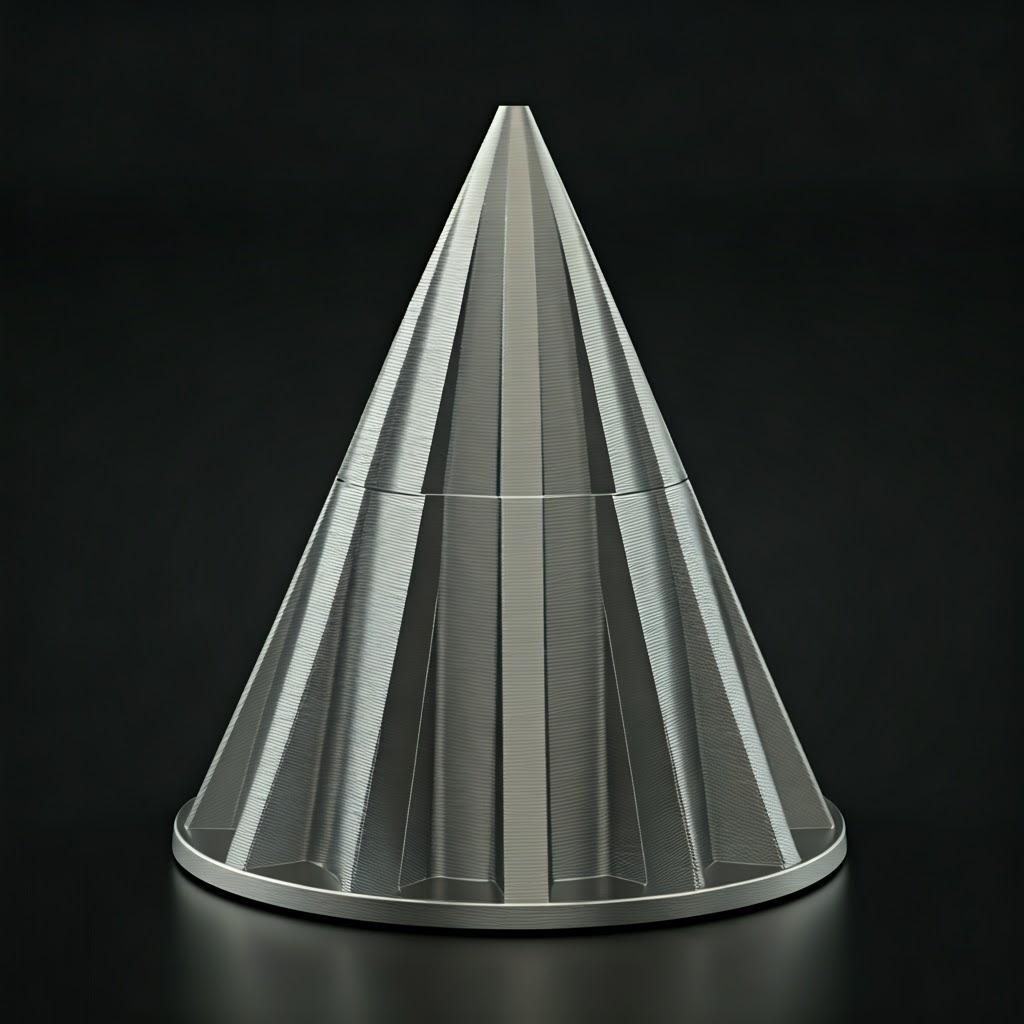
Úvahy o návrhu pro aditivní výrobu: Optimalizace geometrie pro 3D tisk z kovu
Navrhování konektorů nosných kuželů raket pro kovový 3D tisk vyžaduje odlišné myšlení ve srovnání s tradiční výrobou. Pro plné využití možností aditivní výroby a dosažení optimálního výkonu je třeba vzít v úvahu několik klíčových konstrukčních aspektů:
- Optimalizace topologie: Tato výpočetní metoda umožňuje konstruktérům identifikovat a odstranit materiál z málo namáhaných oblastí konstrukce, čímž vznikají lehké, ale konstrukčně pevné součásti. Definováním zatěžovacích stavů a omezení mohou softwarové algoritmy vygenerovat optimalizovanou geometrii, která používá materiál pouze tam, kde je to z konstrukčního hlediska nezbytné. To je významná výhoda 3D tisku, která umožňuje snížit hmotnost bez snížení pevnosti.
- Mřížové struktury: Začlenění vnitřních mřížkových struktur do konektoru může dále snížit hmotnost a v některých případech zvýšit tuhost a absorpci energie. Různé mřížkové vzory, jako jsou gyroidy, voštiny a krychlové struktury, lze přizpůsobit konkrétním požadavkům na zatížení a výrobním procesům.
- Minimalizace podpůrného materiálu: Při 3D tisku z kovu jsou často nutné podpůrné konstrukce, které zabraňují zborcení převisů a odvádějí teplo. Podpěry však zvyšují spotřebu materiálu, dobu tisku a náročnost následného zpracování. Navrhování dílů se samonosnými úhly (obvykle kolem 45 stupňů) a strategická orientace dílu ve stavební komoře mohou minimalizovat potřebu rozsáhlých podpůrných struktur.
- Tloušťka stěny a velikost prvků: Zvažte minimální velikosti prvků a tloušťky stěn, kterých lze dosáhnout pomocí zvoleného procesu 3D tisku z kovu a materiálu. Tenké stěny by mohly být náchylné k deformaci, zatímco velmi malé prvky by nemusely být přesně reprodukovány. Konzultace s Metal3DPmůže poskytnout cenné informace o konstrukčních pravidlech specifických pro naše zařízení a materiály.
- Orientace ve stavební komoře: Orientace konektoru během procesu 3D tisku může významně ovlivnit jeho mechanické vlastnosti, povrchovou úpravu a množství potřebného podpůrného materiálu. V případě kritických leteckých komponentů je nezbytné orientovat díl tak, aby byly směry nejvyššího namáhání v souladu s vrstvami sestavení, a maximalizovat tak pevnost v těchto oblastech.
- Vnitřní kanály a funkce: Aditivní výroba umožňuje vytvářet složité vnitřní kanály pro chlazení, kabeláž nebo přenos tekutin, které lze integrovat přímo do konstrukce konektoru, čímž se sníží počet montážních kroků a zlepší funkčnost.
- Integrace sestavy: Konektor navrhněte s ohledem na jeho integraci s ostatními součástmi rakety. Začlenění prvků, jako jsou zásuvné spoje, vyrovnávací kolíky nebo závitové otvory přímo do 3D tištěného dílu, může zjednodušit proces montáže.
- Úvahy o povrchové úpravě: Povrchová úprava po tisku se u 3D tisku z kovu může lišit v závislosti na procesu a materiálu. Při navrhování prvků je třeba brát tuto skutečnost v úvahu nebo plánovat kroky následného zpracování, aby se dosáhlo požadované drsnosti povrchu pro aerodynamické vlastnosti nebo těsnění.
Pečlivým zvážením těchto konstrukčních zásad a využitím jedinečných možností kovového 3D tisku mohou konstruktéři vytvářet lehčí, pevnější a funkčnější spojovací prvky nosných kuželů raket než ty, které se vyrábějí tradičními metodami. Metal3DPjejí odborné znalosti v oblasti 3D tisk z kovu a naše znalosti požadavků leteckého průmyslu vám pomohou optimalizovat vaše návrhy pro úspěšnou výrobu.
Tolerance, povrchová úprava a rozměrová přesnost: Dosažení přesnosti u 3D tištěných konektorů
V leteckém průmyslu je přesnost nejdůležitější. Konektory kuželů nosné části rakety musí splňovat přísné požadavky na tolerance, aby bylo zajištěno správné uložení, strukturální integrita a aerodynamický výkon. Technologie 3D tisku z kovu dosáhly významného pokroku v dosahování vysoké úrovně přesnosti a kontrolované povrchové úpravy.
- Rozměrová přesnost: Rozměrová přesnost dosažitelná při 3D tisku z kovu závisí na několika faktorech, včetně technologie tisku (např. SLM, EBM), použitého materiálu, geometrie dílu a parametrů sestavení. U pokročilých systémů, jako jsou např Metal3DP, lze u kritických rozměrů dosáhnout tolerance ±0,1 mm nebo ještě větší. Konkrétní požadavky na tolerance je nutné prodiskutovat s vaším dodavatelem poskytovatel služeb 3D tisku kovů abyste měli jistotu, že splní vaše potřeby.
- Faktory ovlivňující přesnost:
- Kalibrace stroje: Pravidelná kalibrace 3D tiskáren je zásadní pro zachování přesnosti.
- Smrštění materiálu: Kovové prášky během tisku tuhnou a chladnou, což vede k předvídatelnému smršťování. Toto smrštění se zohledňuje v konstrukci a parametrech procesu.
- Tepelný management: Pro minimalizaci deformací a zajištění rozměrové přesnosti je zásadní kontrola teploty během procesu sestavování.
- Podpůrné struktury: Umístění a odstranění podpěrných konstrukcí může někdy ovlivnit povrchovou úpravu a rozměrovou přesnost podepřených ploch.
- Povrchová úprava: Povrchová úprava po vytištění při 3D tisku z kovu je obvykle hrubší než při obrábění. Drsnost povrchu (Ra) se může pohybovat od 5 do 20 µm v závislosti na procesu a materiálu. U leteckých aplikací, kde může být vyžadován hladký povrch kvůli aerodynamickým vlastnostem nebo těsnění, se často používají techniky následného zpracování.
- Zlepšení povrchové úpravy:
- Optimalizované parametry sestavení: Nastavení tloušťky vrstvy, výkonu laseru a strategie skenování může ovlivnit kvalitu povrchu.
- Následné zpracování: Techniky, jako je tryskání, leštění a chemické leptání, mohou výrazně zlepšit povrchovou úpravu kovových dílů vytištěných na 3D tiskárně.
- Povlaky: Aplikací specializovaných povlaků lze nejen zlepšit povrchovou úpravu, ale také zvýšit odolnost proti korozi nebo jiné funkční vlastnosti.
- Důležitost pro konektory nosného kužele rakety:
- Přesné přizpůsobení: Těsné tolerance zajišťují správné zarovnání a bezpečné spojení s ostatními součástmi rakety.
- Aerodynamické vlastnosti: Hladká povrchová úprava může minimalizovat odpor vzduchu a zlepšit celkovou aerodynamickou účinnost rakety.
- Těsnění: Přesné rozměry a kontrolovaná povrchová úprava jsou rozhodující pro dosažení účinného utěsnění v tlakovém prostředí.
Metal3DP se snaží dodávat kovové 3D tištěné díly s vysokou rozměrovou přesností a kontrolovanou povrchovou úpravou. Naše pokročilé vybavení a zkušený tým zajišťují, že vaše konektory nosného kužele rakety splňují přísné požadavky leteckého průmyslu. Úzce spolupracujeme s našimi klienty, abychom porozuměli jejich specifickým potřebám a provedli nezbytná opatření k dosažení požadované přesnosti.
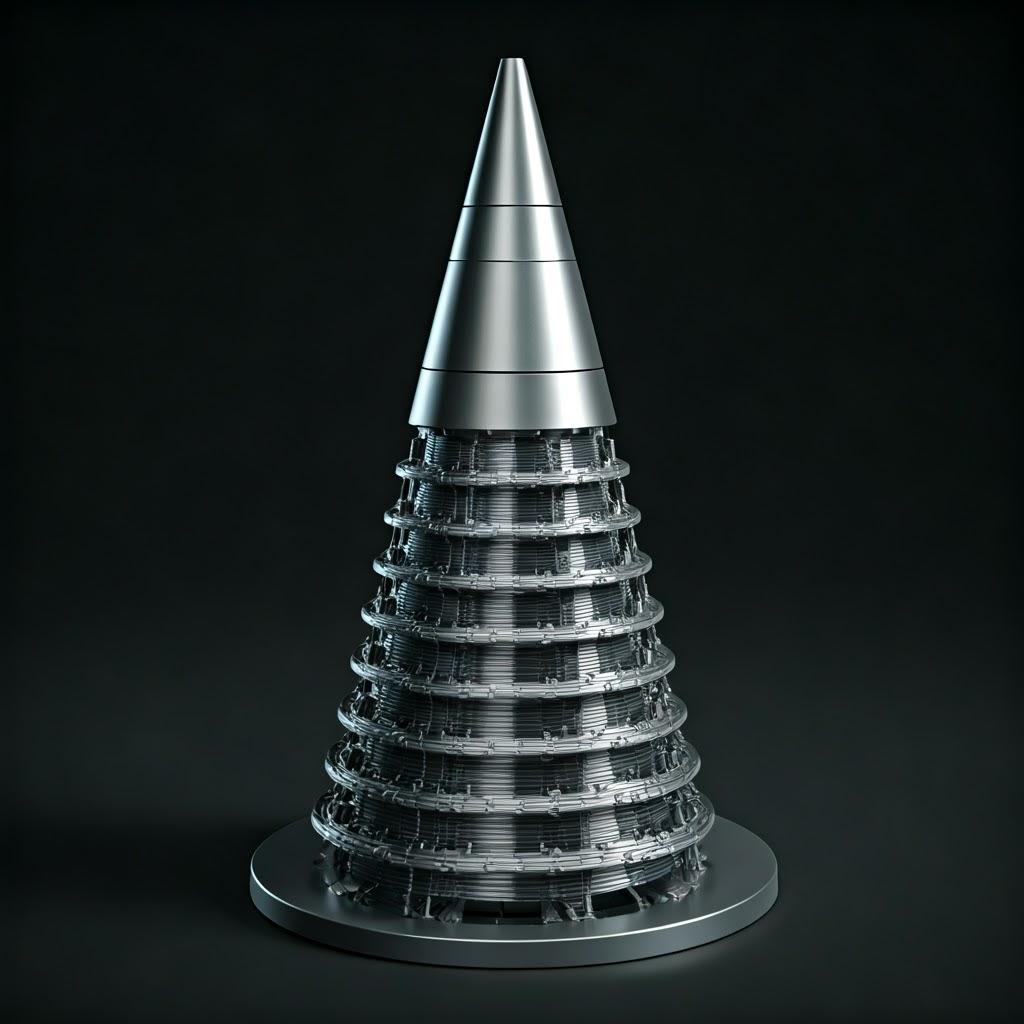
Požadavky na následné zpracování: Zajištění optimálních vlastností a funkčnosti
Ačkoli 3D tisk z kovu nabízí značné výhody při vytváření složitých geometrií, k dosažení konečných požadovaných vlastností, povrchové úpravy a rozměrové přesnosti konektorů nosných kuželů raket jsou často nutné kroky následného zpracování. Tyto kroky zajišťují, že vytištěné díly splňují náročné standardy leteckého průmyslu.
- Tepelné ošetření proti stresu: Procesy 3D tisku kovů zahrnují rychlé cykly zahřívání a ochlazování, které mohou v dílu vyvolat zbytková napětí. Často se provádí tepelné zpracování za účelem snížení těchto vnitřních pnutí, což zabraňuje deformaci a zlepšuje celkové mechanické vlastnosti a rozměrovou stabilitu konektoru. Konkrétní teplota a doba trvání tepelného zpracování závisí na materiálu a procesu tisku.
- Odstranění podpůrné konstrukce: Podpěrné konstrukce, které jsou často nutné při tisku, je třeba opatrně odstranit. To lze provést ručně pomocí nástrojů nebo automatizovanými metodami, jako je obrábění nebo chemické rozpouštění, v závislosti na geometrii a typu použité podpory. Klíčové je zajistit čisté odstranění bez poškození povrchu dílu.
- Povrchová úprava: Pro dosažení požadované povrchové úpravy z důvodu aerodynamických vlastností, těsnění nebo z kosmetických důvodů lze použít různé metody povrchové úpravy:
- Výbuch v médiích: Použití abrazivních médií k odstranění volného prášku a zlepšení rovnoměrnosti povrchu.
- Leštění: Mechanické nebo chemické leštění pro dosažení hladšího povrchu.
- Chemické leptání: Selektivní odstraňování povrchových vrstev za účelem zlepšení hladkosti nebo vytvoření specifických textur.
- CNC obrábění: U kritických prvků, které vyžadují velmi přísné tolerance nebo specifickou povrchovou úpravu, které je obtížné dosáhnout přímo pomocí 3D tisku, může být nutné provést sekundární CNC obrábění. To může zahrnovat obrábění styčných ploch, závitových otvorů nebo zarovnávacích prvků.
- Kontrola kvality: Důsledná kontrola kvality je nezbytná k zajištění toho, aby 3D tištěné konektory splňovaly požadované specifikace. To může zahrnovat:
- Měření rozměrů: Používání souřadnicových měřicích strojů (CMM) nebo jiných přesných měřicích nástrojů k ověření přesnosti rozměrů.
- Nedestruktivní zkoušení (NDT): Techniky, jako je ultrazvukové testování nebo rentgenová kontrola, které odhalují vnitřní vady, jako je pórovitost nebo praskliny.
- Testování materiálů: Ověření mechanických vlastností tištěného materiálu zkouškou v tahu, zkouškou tvrdosti nebo únavovou zkouškou.
- Povlaky a modifikace povrchu: V závislosti na aplikaci mohou být povlaky aplikovány za účelem zvýšení odolnosti proti korozi, odolnosti proti opotřebení nebo jiných funkčních vlastností. Příkladem je eloxování titanových slitin nebo specializované povlaky pro letecký průmysl.
Metal3DP nabízí komplexní služby následného zpracování, aby naše 3D tištěné kovové díly splňovaly nejvyšší standardy kvality a výkonu. Náš zkušený tým rozumí specifickým požadavkům leteckých aplikací a používá vhodné techniky následného zpracování, aby dodal hotвые to-use komponenty. Snažíme se poskytovat bezproblémové výrobní řešení od optimalizace návrhu až po konečnou kontrolu.
Běžné problémy a jak se jim vyhnout: zmírnění rizik při 3D tisku kovů
Přestože 3D tisk z kovu nabízí řadu výhod, existují potenciální problémy, které by měli inženýři a manažeři veřejných zakázek znát. Pochopení těchto problémů a zavedení vhodných strategií může pomoci zmírnit rizika a zajistit úspěšné výsledky.
- Deformace a zkreslení: Tepelné namáhání během tisku může vést k deformaci nebo zkreslení dílu, zejména u velkých nebo složitých geometrií.
- Jak se tomu vyhnout: Optimalizujte orientaci dílu v konstrukční komoře, použijte vhodné podpůrné struktury pro ukotvení dílu a optimalizujte parametry konstrukce, abyste minimalizovali tepelné gradienty. Po tisku je zásadní tepelné zpracování pro uvolnění napětí.
- Odstranění poškození podpůrné konstrukce: Odstranění podpůrných konstrukcí může někdy zanechat povrchové vady nebo dokonce poškodit choulostivé prvky.
- Jak se tomu vyhnout: Navrhujte díly se samonosnými úhly, pokud je to možné, používejte strategicky umístěné a minimálně dimenzované podpěry a používejte vhodné techniky demontáže. Zvažte použití rozpustných podpůrných materiálů, pokud jsou pro zvolený materiál a proces k dispozici.
- Pórovitost a vnitřní vady: Nedůsledné tavení nebo nedostatečná konsolidace prášku může vést ke vzniku pórovitosti nebo jiných vnitřních defektů, které zhoršují mechanické vlastnosti dílu.
- Jak se tomu vyhnout: Optimalizujte parametry sestavování, jako je výkon laseru, rychlost skenování a tloušťka vrstvy. Zajistěte vysokou kvalitu kovové prášky s dobrou tekutostí, jako jsou například ty, které vyrábí Metal3DP's advanced systém na výrobu prášku. Využívejte techniky monitorování v průběhu procesu k odhalení a nápravě potenciálních problémů.
- Zbytková napětí: Jak již bylo zmíněno, během tisku mohou vznikat zbytková napětí, která mohou vést k praskání nebo snížení únavové životnosti.
- Jak se tomu vyhnout: Jako standardní krok po zpracování použijte tepelné zpracování s uvolněním napětí. Optimalizujte pořadí sestavování a parametry tak, abyste minimalizovali nárůst napětí během tisku.
- Problémy s povrchovou úpravou: Dosažení hladkého povrchu přímo při 3D tisku může být náročné.
- Jak se tomu vyhnout: Optimalizujte parametry sestavení pro lepší kvalitu povrchu. Naplánujte vhodné techniky následného zpracování, jako je tryskání, leštění nebo obrábění, abyste dosáhli požadované drsnosti povrchu.
- Variabilita vlastností materiálu: Mechanické vlastnosti 3D tištěných kovových dílů se někdy mohou lišit v závislosti na orientaci sestavení a parametrech procesu.
- Jak se tomu vyhnout: Důkladně charakterizujte vlastnosti materiálu pro specifickou orientaci sestavení a procesní parametry. Optimalizujte proces sestavování, abyste zajistili konzistentní příkon energie a tavení. Proveďte důkladné testování kvality.
- Úvahy o ceně: 3D tisk z kovu může být pro určité aplikace nákladově efektivní, ale počáteční investice do zařízení nebo náklady na specializované materiály a služby mohou být problémem.
- Jak se tomu vyhnout: Pečlivě zhodnoťte celkové náklady na vlastnictví a porovnejte je s tradičními výrobními metodami. Navrhněte aditivní výrobu, abyste optimalizovali využití materiálu a omezili následné zpracování. Zvažte spolupráci se zkušeným poskytovatel služeb 3D tisku kovů jako Metal3DP využít jejich odborné znalosti a vybavení bez velkých počátečních investic.
- Škálovatelnost pro velkoobjemovou výrobu: Zatímco 3D tisk je vynikající pro výrobu prototypů a pro výrobu v malých až středních objemech, jeho rozšíření na velmi velké objemy může představovat problém.
- Jak se tomu vyhnout: Pro velkosériovou výrobu zvažte hybridní výrobní přístupy, které kombinují flexibilitu 3D tisku s efektivitou tradičních výrobních metod pro určité prvky. Konzultujte s Metal3DP prodiskutovat vaše požadavky na objem výroby a prozkoumat nejvhodnější řešení.
Pochopením těchto běžných problémů a zavedením vhodných strategií pro jejich zmírnění mohou letečtí inženýři a manažeři veřejných zakázek efektivně využít výhod kovového 3D tisku pro výrobu vysoce výkonných konektorů nosných kuželů raket. Metal3DPnaše odborné znalosti a komplexní služby jsou navrženy tak, aby našim klientům pomohly zvládnout tyto výzvy a dosáhnout úspěšných výsledků.
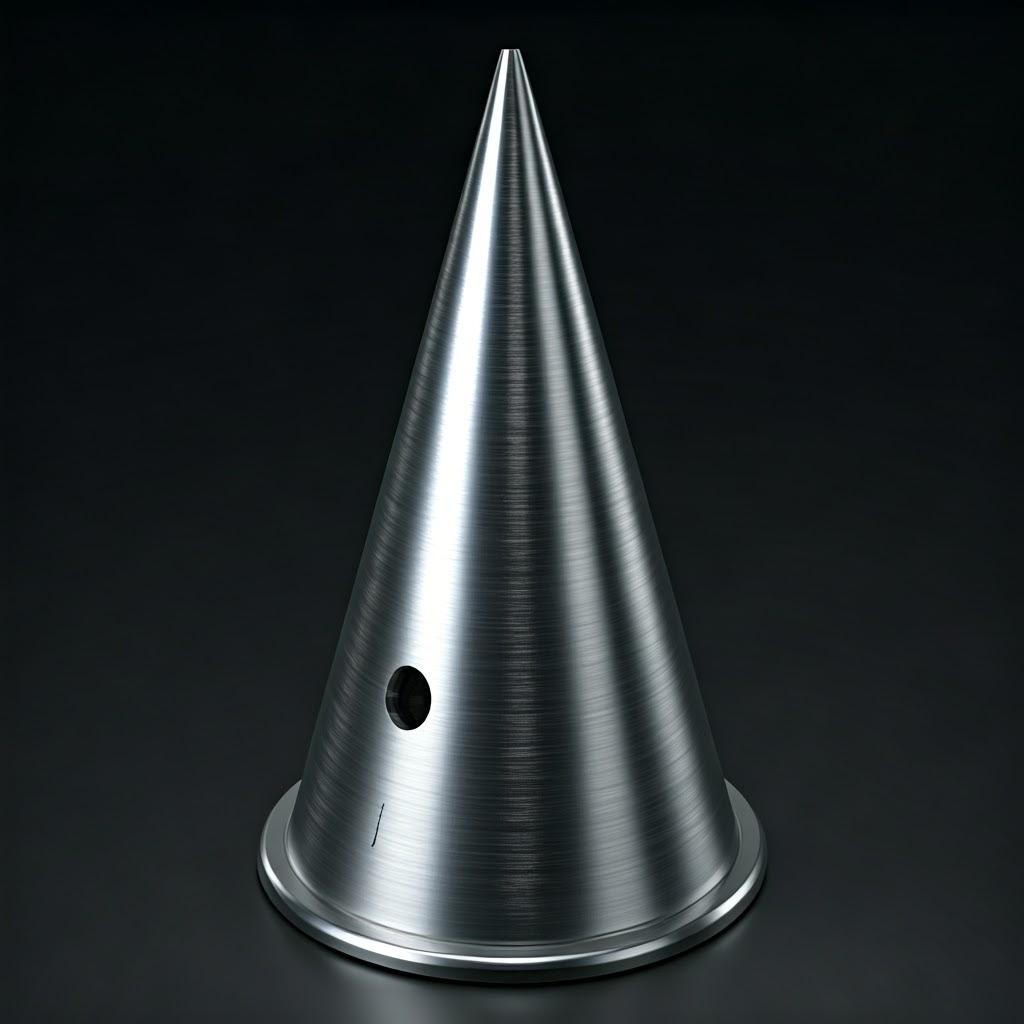
Jak si vybrat správného poskytovatele služeb 3D tisku kovů: Výběr důvěryhodného partnera pro letecké komponenty
Výběr správného poskytovatel služeb 3D tisku kovů je zásadní rozhodnutí, zejména pro náročné aplikace v letectví a kosmonautice, jako jsou například konektory pro nosné kužely raket. Kvalita, spolehlivost a výkonnost těchto součástí přímo ovlivňují úspěch mise. Zde jsou klíčové faktory, které je třeba zvážit při hodnocení potenciálních dodavatelů:
- Zkušenosti a certifikace v letectví a kosmonautice: Hledejte poskytovatele s prokazatelnými zkušenostmi v oblasti leteckého průmyslu. Ověřte si, zda má příslušné certifikáty, jako je AS9100, který prokazuje závazek dodržovat systémy řízení kvality specifické pro letecký průmysl. Metal3DP dodržuje přísné normy kvality a má rozsáhlé zkušenosti s výrobou vysoce výkonných kovových dílů pro letecké a kosmické aplikace.
- Materiálové schopnosti: Ujistěte se, že poskytovatel má zkušenosti s prací s doporučenými materiály, Ti-6Al-4V a Ti-6Al-4V ELIa má odborné znalosti pro zpracování těchto materiálů tak, aby splňovaly specifikace pro letecký průmysl. Měl by také mít hluboké znalosti o vlastnostech materiálů dosažitelných prostřednictvím svých tiskových procesů. Metal3DP nabízí širokou škálu vysoce kvalitních kovové prášky, včetně slitin titanu optimalizovaných pro aditivní výrobu.
- Tiskové technologie a zařízení: Porozumět typům technologií 3D tisku kovů, které poskytovatel používá (např. SLM, EBM). Každá technologie má své silné stránky a omezení, pokud jde o přesnost, povrchovou úpravu, objem sestavení a kompatibilitu materiálů. Metal3DP využívá pokročilé tiskárny SEBM, které jsou známé svým nejlepším objemem tisku, přesností a spolehlivostí. Více informací o našich tiskových metod na našich webových stránkách.
- Optimalizace návrhu a technická podpora: Dobrý poskytovatel služeb by měl nabízet služby optimalizace návrhu, které vám pomohou přizpůsobit návrh konektoru pro aditivní výrobu a maximalizovat jeho výkon a vyrobitelnost. Jeho tým inženýrů by měl mít znalosti v oblastech, jako je optimalizace topologie, strategie odlehčování a výběr materiálů. Metal3DP poskytuje komplexní služby vývoje aplikací a spolupracuje s organizacemi na optimalizaci jejich návrhů pro 3D tisk z kovu.
- Možnosti následného zpracování: Informujte se o nabízených službách následného zpracování, jako je tepelné zpracování s uvolněním napětí, odstranění podpěr, povrchová úprava, CNC obrábění a kontrola kvality. Poskytovatel s komplexními možnostmi následného zpracování může zefektivnit výrobní proces a zajistit, aby finální díl splňoval všechny požadavky. Metal3DP nabízí kompletní sadu služeb následného zpracování a dodává hotové komponenty k použití.
- Kontrola kvality a inspekce: Pro letecké komponenty je nezbytný spolehlivý systém kontroly kvality. Poskytovatel by měl mít zavedené postupy pro kontrolu rozměrů, nedestruktivní testování (NDT) a testování materiálů, aby zajistil, že díly splňují požadované specifikace a normy.
- Dodací lhůty a výrobní kapacita: Diskutujte o dodacích lhůtách pro výrobu prototypů a výrobu, jakož i o schopnosti poskytovatele zvládnout vaše očekávané objemy. Ujistěte se, že jeho harmonogramy jsou v souladu s vaším projektovým plánem.
- Komunikace a zákaznická podpora: Pro hladkou a úspěšnou spolupráci je zásadní efektivní komunikace a pohotová zákaznická podpora. Vyberte si poskytovatele, který je proaktivní, transparentní a ochotný úzce spolupracovat s vaším týmem.
- Struktura nákladů a transparentnost: Porozumět cenovému modelu a všem souvisejícím nákladům, včetně optimalizace designu, tisku, materiálů, následného zpracování a kontroly kvality. Transparentní struktura cen vám pomůže přesně sestavit rozpočet projektu.
- Důvěrnost a ochrana duševního vlastnictví: Ujistěte se, že poskytovatel má přísné zásady a dohody na ochranu vašeho duševního vlastnictví a zachování důvěrnosti vašich návrhů.
Pečlivým vyhodnocením těchto faktorů můžete vybrat poskytovatel služeb 3D tisku kovů která je spolehlivým a schopným partnerem pro výrobu vysoce výkonných konektorů nosné části rakety. Metal3DP se zavázala budovat dlouhodobé partnerství s našimi klienty, nabízet jim nejmodernější systémy, vyspělé technologie a kovové práškya desítky let společných zkušeností v oblasti aditivní výroby kovů. Navštivte naše o nás a dozvíte se více o naší společnosti a našem závazku ke kvalitě.
Nákladové faktory a doba realizace: pochopení ekonomiky 3D tištěných konektorů
Pochopení nákladových faktorů a dodacích lhůt spojených s kovovým 3D tiskem je zásadní pro efektivní plánování projektů a sestavování rozpočtu. Přestože 3D tisk může v určitých scénářích nabídnout nákladové výhody, je důležité zvážit všechny přispívající prvky.
Nákladové faktory:
- Náklady na materiál: Náklady na kovové prášky, jako např. Ti-6Al-4V a Ti-6Al-4V ELI, může být významným faktorem. Speciální slitiny a vysoce výkonné třídy mají často vyšší náklady. K celkovým materiálovým nákladům přispívá také množství materiálu použitého na díl a podpůrné konstrukce.
- Náklady na konstrukci a inženýrské práce: Pokud od poskytovatele služeb požadujete optimalizaci návrhu nebo technickou podporu, budou tyto služby zahrnuty do celkových nákladů. Optimalizace návrhu pro 3D tisk však může často vést k úspoře materiálu a zlepšení výkonu, což může tyto počáteční náklady kompenzovat.
- Náklady na tisk: Náklady na tisk jsou ovlivněny faktory, jako je doba sestavení, využití stroje a spotřeba energie. Složité geometrie nebo velké díly, které vyžadují delší dobu sestavení, mají obecně vyšší náklady na tisk.
- Náklady na následné zpracování: Rozsah požadovaného následného zpracování (např. uvolnění napětí, odstranění podpěr, povrchová úprava, obrábění) ovlivní konečné náklady. Složitější kroky následného zpracování zvýší celkové náklady.
- Náklady na kontrolu kvality a inspekci: Přísné postupy kontroly kvality, včetně kontroly rozměrů a nedestruktivního zkoušení, jsou pro letecké komponenty nezbytné a budou zohledněny v nákladech.
- Náklady na nástroje (oproti tradiční výrobě): Jednou z klíčových výhod 3D tisku je eliminace nebo snížení nákladů na výrobu nástrojů spojených s tradičními metodami, jako je vstřikování nebo odlévání. U nízkých až středních objemů výroby nebo vysoce přizpůsobených dílů to může vést k výrazným úsporám nákladů.
- Úspory z rozsahu: Náklady na jeden díl při 3D tisku se mohou lišit v závislosti na objemu výroby. Zatímco 3D tisk je často nákladově efektivní pro nízké až střední objemy a prototypy, tradiční metody mohou být ekonomičtější pro velmi vysoké výrobní série jednoduchých geometrií. Pokroky v technologii 3D tisku však neustále zlepšují jeho škálovatelnost.
Dodací lhůta:
- Návrh a optimalizace: Počáteční fáze návrhu a optimalizace může trvat různě dlouho v závislosti na složitosti dílu a úrovni požadované technické podpory. Možnosti rychlé iterace 3D tisku však mohou celkový vývojový cyklus výrazně zkrátit ve srovnání s tradičními metodami, které zahrnují zdlouhavé procesy výroby nástrojů.
- Doba tisku: Doba výroby 3D tištěného dílu závisí na jeho velikosti, složitosti a použité technologii tisku. Menší, méně složité díly lze vytisknout relativně rychle, zatímco větší nebo složitější součásti mohou trvat několik hodin nebo dokonce dnů.
- Doba následného zpracování: Čas potřebný pro následné zpracování, jako je tepelné zpracování, odstranění podpěr a povrchová úprava, prodlužuje celkovou dobu výroby. Délku těchto procesů ovlivňuje složitost dílu a požadovaná povrchová úprava.
- Kontrola kvality: Důkladná kontrola kvality může rovněž prodloužit dobu realizace, ale je nezbytná pro zajištění spolehlivosti a výkonnosti leteckých komponent.
- Přeprava a logistika: Je třeba vzít v úvahu také dobu potřebnou k přepravě hotových dílů na místo určení.
Metal3DP se zavazuje poskytovat transparentní rozpis nákladů a reálné dodací lhůty pro naše produkty služby kovového 3D tisku. Úzce spolupracujeme s našimi klienty, abychom porozuměli jejich specifickým požadavkům a nabídli nákladově efektivní řešení bez kompromisů v kvalitě. Kontaktujte nás, abychom s vámi prodiskutovali váš projekt a získali podrobnou cenovou nabídku.
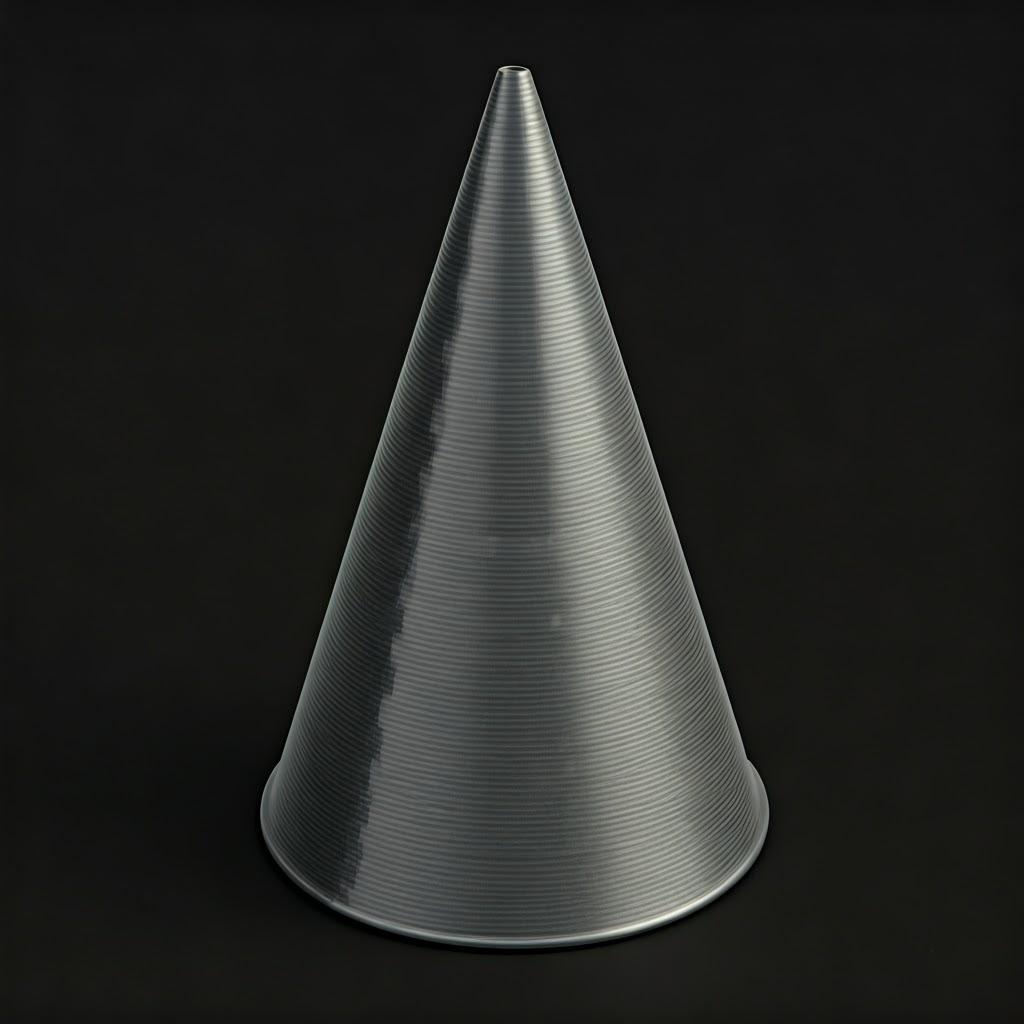
Často kladené otázky (FAQ): Odpovědi na časté dotazy
Zde je několik nejčastějších otázek týkajících se použití kovového 3D tisku pro konektory nosných kuželů raket:
- Otázka: Mohou kovové 3D tištěné konektory splňovat přísné požadavky na pevnost v letectví a kosmonautice?
- A: Ano, při použití vysoce výkonných kovové prášky jako Ti-6Al-4V nebo Ti-6Al-4V ELI a použitím optimalizovaných konstrukčních a tiskových parametrů lze u kovových 3D tištěných konektorů dosáhnout mechanických vlastností, které splňují nebo překračují požadavky mnoha leteckých aplikací. Pro ověření těchto vlastností je nezbytné důkladné testování a kontrola kvality.
- Otázka: Jaká je typická povrchová úprava dosažitelná u kovových 3D tištěných konektorů a je vhodná pro aerodynamické aplikace?
- A: Povrchová úprava po tisku se může lišit v závislosti na tiskovém procesu a materiálu. Obecně je drsnější než obráběné povrchy, ale pro dosažení hladkých povrchů vhodných pro aerodynamické vlastnosti a těsnění lze použít různé techniky následného zpracování, jako je leštění a nátěry.
- Otázka: Je kovový 3D tisk pro výrobu konektorů nosných kuželů raket rentabilní?
- A: Ekonomická efektivita 3D tisku z kovu závisí na faktorech, jako je složitost konstrukce, objem výroby, náklady na materiál a požadavky na následné zpracování. V případě nízkých až středních objemů, vysoce přizpůsobených dílů nebo konstrukcí, které využívají jedinečné možnosti aditivní výroby pro snížení hmotnosti a zvýšení výkonu, může jít o velmi nákladově efektivní řešení ve srovnání s tradičními metodami, které vyžadují nákladné nástroje.
- Otázka: Jaké jsou typické dodací lhůty pro kovové 3D tištěné konektory nosných kuželů raket?
- A: Doba realizace se liší v závislosti na složitosti dílu, použité technologii tisku, požadovaném následném zpracování a vytíženosti poskytovatele služeb. 3D tisk však obecně nabízí rychlejší výrobu prototypů a kratší dodací lhůty pro malé až střední objemy ve srovnání s tradičními výrobními procesy, které zahrnují výrobu nástrojů.
- Otázka: Jak zajistit kvalitu a spolehlivost kovových 3D tištěných leteckých komponent?
- A: Výběr renomovaného poskytovatel služeb 3D tisku kovů se zkušenostmi a certifikacemi v leteckém průmyslu (jako např Metal3DP) s využitím vysoce kvalitních kovové prášky, zavedení důkladných postupů kontroly kvality, včetně kontroly rozměrů a nedestruktivního zkoušení, a dodržování přísných protokolů o zkouškách materiálu jsou zásadní pro zajištění kvality a spolehlivosti kovových 3D tištěných leteckých součástí.
Závěr: Budoucnost letectví a kosmonautiky s kovovými 3D tištěnými konektory
Integrace 3D tisk z kovu do výroby kuželů nosných částí raket představuje pro letecký průmysl významný skok vpřed. Schopnost vytvářet složité, lehké a vysoce výkonné součásti s větší konstrukční svobodou a možností rychlého opakování nabízí nebývalé možnosti inovací a efektivity.
Využitím pokročilých materiálů, jako jsou Ti-6Al-4V a Ti-6Al-4V ELI a spolupráce se zkušenými poskytovatelé služeb kovového 3D tisku jako Metal3DP, mohou letečtí inženýři a manažeři veřejných zakázek otevřít novou éru konstrukčních možností, dosáhnout výrazných úspor hmotnosti, zlepšit strukturální integritu a urychlit vývoj raketových systémů nové generace.
Metal3DP stojí v čele této transformační technologie a poskytuje špičkový objem, přesnost a spolehlivost tisku spolu s komplexní sadou služeb od optimalizace návrhu až po závěrečnou kontrolu. Díky našemu závazku ke kvalitě, inovacím a spolupráci se zákazníky jsme důvěryhodným partnerem pro organizace, které chtějí využít sílu aditivní výroby kovů.
Kontakt Metal3DP a zjistit, jak naše služby kovového 3D tisku a vysoce výkonné kovové prášky může posílit vaše úsilí v oblasti kosmonautiky a pomoci vám dosáhnout nových výšin v oblasti výzkumu vesmíru a technologického pokroku. Navštivte naši produkt na stránce, kde se dozvíte více o naší nabídce materiálů a o tom, jak můžeme podpořit vaše specifické potřeby.
Sdílet na
MET3DP Technology Co., LTD je předním poskytovatelem řešení aditivní výroby se sídlem v Qingdao v Číně. Naše společnost se specializuje na zařízení pro 3D tisk a vysoce výkonné kovové prášky pro průmyslové aplikace.
Dotaz k získání nejlepší ceny a přizpůsobeného řešení pro vaše podnikání!
Související články
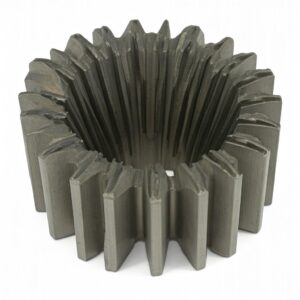
Vysoce výkonné segmenty lopatek trysek: Revoluce v účinnosti turbín díky 3D tisku z kovu
Přečtěte si více "O Met3DP
Nedávná aktualizace
Náš produkt
KONTAKTUJTE NÁS
Nějaké otázky? Pošlete nám zprávu hned teď! Po obdržení vaší zprávy obsloužíme vaši žádost s celým týmem.