Výrobní proces selektivního laserového tavení (sLM)
Obsah
Představte si, že vytváříte složité, vysoce výkonné kovové díly vrstvu po vrstvě s bezkonkurenční konstrukční svobodou a minimálním odpadem. To je kouzlo selektivního laserového tavení (SLM), revoluční technologie 3D tisku, která mění výrobní prostředí. Pojďme se ponořit do fascinujícího světa SLM, prozkoumat jeho složité kroky, rozmanité možnosti kovových prášků a odhalit jeho potenciál.
Přípravné práce pro tiskovou technologii SLM
Než se rozhoří kouzlo laseru, je třeba provést pečlivou přípravu, která vytvoří základ pro úspěšný tisk pomocí SLM.
- 3D model CAD: Cesta začíná pečlivě navrženým 3D modelem počítačem podporovaného designu (CAD). Tento digitální plán definuje přesnou geometrii a rozměry požadovaného kovového dílu.
- Krájení modelu: Specializovaný software pak 3D model rozřeže na mnoho ultratenkých vrstev, obvykle o velikosti 20 až 100 mikrometrů. Každá vrstva slouží jako stavební prvek pro finální díl.
- Výběr kovového prášku: Zásadní je výběr vhodného kovového prášku. Částice prášku musí mít stejnou velikost, kulovitou morfologii a optimální tekutost, aby se zajistilo hladké vytváření vrstev během tisku.
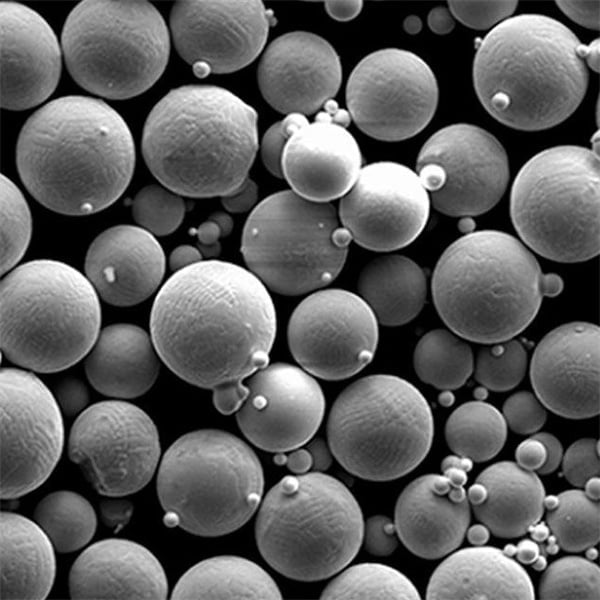
Proces tisku SLMTechnologie tisku
Nyní je scéna připravena k tomu, aby laser mohl utkat své kovové kouzlo:
- Usazování v práškovém loži: Tenká vrstva kovového prášku se pečlivě rozprostře po konstrukční plošině pomocí kotouče pro nanášení nátěru. Tento proces zajišťuje rovnoměrně rozložené a vyrovnané práškové lože pro každou vrstvu.
- Selektivní laserové tavení: Vysoce výkonný laserový paprsek, obvykle vláknový laser, přesně skenuje průřez první vrstvy, jak je definován nařezanými daty 3D modelu. Laser roztaví cílové částice kovového prášku a spojí je dohromady do pevné struktury.
- Stavba po vrstvách: Na nanášečku se nanese další tenká vrstva prášku a laser selektivně roztaví určená místa a spojí je s předchozí vrstvou. Tento proces pečlivě pokračuje a vytváří objekt vrstvu po vrstvě, dokud není celý díl dokončen.
- Generování podpůrných struktur: V některých případech mohou složité geometrie vyžadovat vytvoření dočasných podpůrných konstrukcí, aby se zabránilo deformacím nebo prohýbání během procesu tisku. Tyto podpěry se obvykle tisknou spolu s vlastním dílem a později se ve fázi následného zpracování odstraní.
Následné zpracování technologie tisku SLM
Po vychladnutí laserové magie není vytištěný díl ještě zcela připraven k použití:
- Odstranění z platformy Build: Hotový díl je pečlivě oddělen od stavební plošiny. U choulostivých dílů může jít o obrábění nebo o techniky elektroerozivního obrábění (WEDM).
- Odstranění podpůrné konstrukce: Pokud jsou použity, jsou dočasné podpůrné struktury pečlivě odstraněny pomocí technik, jako je obrábění, mechanické řezání nebo chemické rozpouštění.
- Tepelné zpracování: V závislosti na kovu a požadavcích na použití může být díl podroben tepelnému zpracování, jako je uvolňování napětí nebo žíhání, aby se zlepšily jeho mechanické vlastnosti.
- Povrchová úprava: Povrch vytištěného dílu může vyžadovat další dokončovací postupy, jako je pískování, leštění nebo obrábění, aby bylo dosaženo požadované kvality povrchu a funkčnosti.
Co dokáží kovové prášky SLM's Printing Technology Use?
Všestrannost SLM se projevuje v její kompatibilitě s různými kovovými prášky, z nichž každý nabízí jedinečné vlastnosti a aplikace:
Běžné kovové prášky pro SLM
Kovový prášek | Popis | Vlastnosti | Aplikace |
---|---|---|---|
titan (Ti) | Vysoce biokompatibilní, lehké a odolné proti korozi. | Vynikající poměr pevnosti k hmotnosti, vysoký bod tání | Letecké komponenty, lékařské implantáty, zubní protézy |
Nerezová ocel (316L, 17-4PH) | Široce používané, odolné proti korozi a s dobrými mechanickými vlastnostmi. | Vysoká pevnost, tažnost a odolnost proti opotřebení | Strojní součásti, součásti pro manipulaci s kapalinami, zdravotnické prostředky |
Hliník (AlSi10Mg, AlSi7Mg) | Lehký, dobře odolný proti korozi a nabízí vysokou pevnost ve srovnání s jinými hliníkovými slitinami. | Vynikající poměr pevnosti a hmotnosti, dobrá svařitelnost | Automobilové součástky, letecké díly, výměníky tepla |
Nikl (Inconel 625, Inconel 718) | Odolnost vůči vysokým teplotám, oxidaci a vynikající mechanické vlastnosti. | Vysoká pevnost, odolnost proti tečení a dobrá obrobitelnost | Součásti plynových turbín, zařízení pro chemické zpracování, výměníky tepla |
Kobalt-chrom (CoCrMo) | Biokompatibilní, odolný proti opotřebení a s vysokou pevností. | Vynikající odolnost proti opotřebení, korozi a biokompatibilita | Lékařské implantáty, kloubní náhrady |
Rozšíření obzorů SLM
I když výše uvedené kovové prášky patří k nejčastěji používaným při SLM, potenciál této technologie sahá mnohem dále. Zde je pohled na širší výběr kovových prášků, z nichž každý odemyká jedinečné možnosti:
Kovové prášky pro specializované aplikace:
Kovový prášek | Popis | Vlastnosti | Aplikace |
---|---|---|---|
měď (Cu) | Vysoká vodivost a dobrá tepelná vodivost | Vynikající elektrická vodivost, dobrá tepelná vodivost a vysoká tažnost. | Elektrické komponenty, výměníky tepla, systémy tepelného managementu |
Nástrojová ocel (H13, AISI M2) | Vysoká tvrdost a odolnost proti opotřebení | Výjimečná odolnost proti opotřebení, vysoká pevnost a dobrá houževnatost. | Lisovací formy, formy, řezné nástroje, opotřebitelné díly |
Wolfram (W) | Vysoký bod tání a výjimečná hustota | Velmi vysoký bod tání, vysoká hustota a vynikající tepelná odolnost | Vysokoteplotní aplikace, žáruvzdorné kelímky, stínění rentgenovým zářením |
molybden (Mo) | Vysoký bod tání a dobrá tepelná vodivost | Vysoký bod tání, dobrá tepelná vodivost a dobrá odolnost proti korozi. | vysokoteplotní aplikace, topné prvky, součásti raketových motorů |
tantal (Ta) | Biokompatibilní, odolný proti korozi a s vysokým bodem tání. | Vynikající biokompatibilita, vysoký bod tání a dobrá odolnost proti korozi. | lékařské implantáty, kondenzátory, zařízení pro zpracování chemikálií |
Výběr správného kovového prášku pro SLM
Výběr optimálního kovového prášku pro váš projekt SLM závisí na několika zásadních faktorech:
- Požadované vlastnosti: Pečlivě zvažte základní vlastnosti požadované pro konečný díl, jako je pevnost, hmotnost, odolnost proti korozi a tepelná vodivost.
- Požadavky na přihlášku: Zásadní roli hraje zamýšlené použití dílu. Například lékařské implantáty vyžadují biokompatibilní materiály, jako je titan nebo kobalt-chrom, zatímco vysokoteplotní aplikace mohou upřednostňovat slitiny niklu nebo žáruvzdorné kovy, jako je wolfram.
- Zpracovatelnost: Konkrétní kovové prášky mohou vykazovat různou tekutost, odrazivost laseru a náchylnost k praskání nebo deformaci během procesu SLM. Výběr prášku s optimální zpracovatelností zajistí úspěšný tisk a minimalizuje riziko vzniku vad.
- Náklady: Cena kovových prášků se může výrazně lišit, přičemž některé exotické materiály, jako je tantal nebo iridium, jsou dražší než běžněji používané materiály, jako je nerezová ocel nebo hliník.
Další úvahy o SLM
Zatímco základní principy SLM zůstávají neměnné, úspěch a efektivitu procesu může ovlivnit několik faktorů:
- Parametry stroje: Optimalizace výkonu laseru, rychlosti skenování a vzdálenosti mezi šrafami má zásadní význam pro dosažení požadovaných vlastností materiálu a minimalizaci zbytkových napětí.
- Prostředí pro sestavení: Udržování řízené atmosféry v konstrukční komoře, často za použití inertních plynů, jako je argon, je nezbytné k zabránění oxidace a zajištění stálé kvality materiálu.
- Techniky následného zpracování: Efektivita následného zpracování, jako je tepelné zpracování a povrchová úprava, významně ovlivňuje výkonnost a estetiku výsledného dílu.
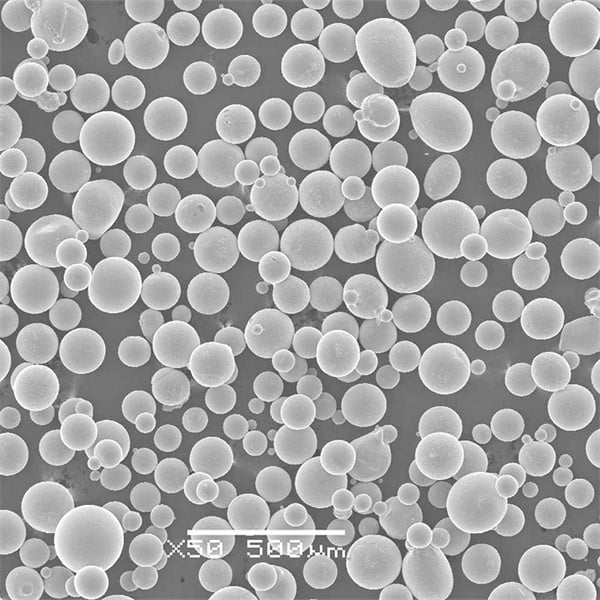
Závěr
Selektivní laserové tavení nabízí bezkonkurenční svobodu při vytváření složitých, vysoce výkonných kovových dílů. Pochopením složitých kroků, prozkoumáním rozmanitých možností kovových prášků a pečlivým zvážením různých faktorů můžete využít sílu SLM odemknout inovativní konstrukční možnosti a způsobit revoluci ve výrobě v různých průmyslových odvětvích.
Nejčastější dotazy
Otázka: Jaké jsou výhody SLM ve srovnání s tradičními výrobními technikami?
Odpověď: SLM nabízí několik výhod oproti tradičním metodám, jako je obrábění, odlévání a kování, včetně:
- Svoboda designu: Umožňuje vytvářet složité geometrie a složité vnitřní prvky, které jsou často nemožné při použití jiných technik.
- Odlehčení: Umožňuje vytvářet lehké díly s vynikajícím poměrem pevnosti a hmotnosti, což je ideální pro aplikace, jako je letectví a doprava.
- Snížení množství odpadu: Minimalizuje plýtvání materiálem v porovnání se subtraktivními výrobními technikami a podporuje efektivní využívání zdrojů.
- Rychlé prototypování: Umožňuje rychlé vytváření prototypů pro iterativní návrh a testování, čímž urychluje proces vývoje.
Otázka: Jaká jsou omezení SLM?
Odpověď: Systém SLM sice nabízí pozoruhodné možnosti, ale má také některá omezení, včetně:
- Náklady: V porovnání s tradičními výrobními metodami může být SLM dražší kvůli vysokým nákladům na kovové prášky a specializované vybavení.
- Drsnost povrchu: Díly vytištěné pomocí SLM mohou mít ve srovnání s obráběnými součástmi mírně drsnější povrch, což vyžaduje další kroky následného zpracování.
- Omezená velikost sestavy: Současné stroje SLM mají omezení týkající se velikosti dílů, které mohou vyrábět, ačkoli se tato omezení neustále vyvíjejí.
Sdílet na
MET3DP Technology Co., LTD je předním poskytovatelem řešení aditivní výroby se sídlem v Qingdao v Číně. Naše společnost se specializuje na zařízení pro 3D tisk a vysoce výkonné kovové prášky pro průmyslové aplikace.
Dotaz k získání nejlepší ceny a přizpůsobeného řešení pro vaše podnikání!
Související články
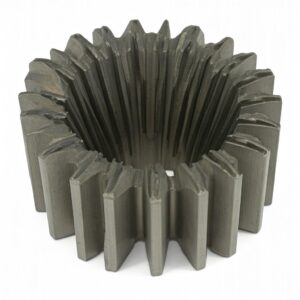
Vysoce výkonné segmenty lopatek trysek: Revoluce v účinnosti turbín díky 3D tisku z kovu
Přečtěte si více "O Met3DP
Nedávná aktualizace
Náš produkt
KONTAKTUJTE NÁS
Nějaké otázky? Pošlete nám zprávu hned teď! Po obdržení vaší zprávy obsloužíme vaši žádost s celým týmem.
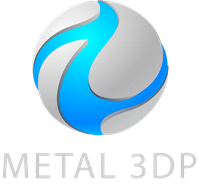
Kovové prášky pro 3D tisk a aditivní výrobu