Princip fungování laserového selektivního tavení (SLM)
Obsah
Představte si svět, kde lze složité kovové díly vykouzlit z práškového lože, vrstvu po vrstvě, s přesností laseru. To není vědecká fikce; je to realita laserového selektivního tavení (SLM), revoluční technologie 3D tisku, která transformuje výrobní prostředí.
Ale jak přesně SLM funguje? Připravte se, protože se chystáme ponořit do fascinujícího světa laserů, kovových prášků a kouzla aditivní výroby.
Odhalení SLM procesu: Podrobný popis krok za krokem
SLM, známé také jako přímé laserové slinování kovů (DMLS), funguje na principu aditivní výroby. Na rozdíl od tradičních subtraktivních metod, jako je obrábění, které odebírají materiál za účelem vytvoření požadovaného tvaru, SLM vytváří objekt vrstvu po vrstvě. Zde je rozpis procesu:
- Digitální design: Prvním krokem je vytvoření 3D modelu požadovaného objektu pomocí počítačového návrhu (CAD). Tento model slouží jako plán pro stroj SLM.
- Příprava práškového lože: Tenká vrstva jemného kovového prášku, obvykle o velikosti 20 až 100 mikronů, se rovnoměrně rozprostře po stavební plošině uvnitř stroje SLM. Materiály používané v SLM mohou zahrnovat slitiny titanu, nerezovou ocel, hliník a dokonce i exotické materiály, jako je Inconel pro vysoce výkonné aplikace.
- Kouzlo laserového paprsku: Vysoce výkonný laserový paprsek skenuje povrch práškového lože podle digitálního návrhu. Laser roztaví částice prášku na specifických místech a spojí je dohromady, čímž vytvoří první vrstvu objektu.
- Vytváření vrstev po vrstvách: Po dokončení první vrstvy se stavební plošina mírně sníží a uloží se čerstvá vrstva prášku. Laserový paprsek pak skenuje tuto novou vrstvu, selektivně taví a spojuje částice prášku, aby vytvořil druhou vrstvu, a tak dále. Tento proces pokračuje vrstvu po vrstvě, dokud není celý objekt vytvořen.
- Podpůrné struktury: Vzhledem k tomu, že se kovové díly mohou v důsledku vysokých teplot deformovat nebo deformovat, SLM často využívá dočasné podpůrné konstrukce. Tyto konstrukce se tisknou společně s hlavním objektem a poskytují podporu během procesu stavby. Po dokončení se podpůrné konstrukce odstraní pomocí různých technik, jako je obrábění, vodní paprsek nebo chemické leptání.
- Následné zpracování: Po dokončení stavby se hotový díl vyjme ze stavební komory a může podstoupit další kroky následného zpracování, jako je tepelné zpracování pro zlepšení mechanických vlastností nebo povrchová úprava pro estetické účely.
Představte si SLM jako sofistikovanou 3D tiskárnu pro kovy. Namísto použití plastového vlákna používá kovový prášek a namísto inkoustové hlavy používá vysoce výkonný laser k selektivnímu tavení a spojování materiálu. Tento přístup vrstva po vrstvě umožňuje vytvářet neuvěřitelně složité geometrie, kterých by bylo obtížné, ne-li nemožné, dosáhnout pomocí tradičních výrobních metod.
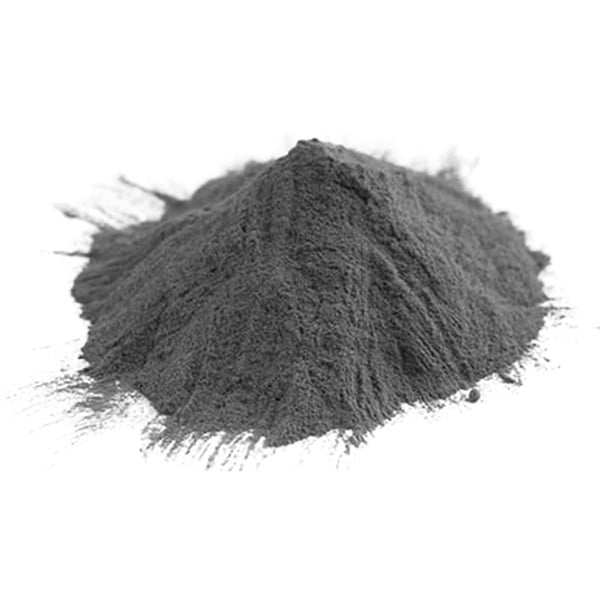
Výhody SLM Proces
SLM nabízí několik přesvědčivých výhod oproti tradičním technikám:
- Svoboda designu: SLM umožňuje vytvářet složité geometrie s vnitřními kanály, mřížkami a dalšími prvky, kterých konvenčními metodami jednoduše nelze dosáhnout. To otevírá svět možností pro lehké, vysoce pevné komponenty v leteckém, automobilovém a lékařském průmyslu.
- Rychlé prototypování: Schopnost vytvářet složité díly přímo z digitálního modelu činí SLM ideální pro rychlé prototypování. To umožňuje konstruktérům rychle a efektivně iterovat návrhy, což snižuje dobu vývoje a náklady.
- Hromadné přizpůsobení: Schopnost SLM vyrábět jedinečné díly na vyžádání je ideální pro hromadnou customizaci. To je zvláště cenné pro odvětví, jako jsou lékařské implantáty, kde je třeba díly přizpůsobit jednotlivým pacientům.
- Účinnost materiálu: SLM je relativně málo odpadní proces. Nepoužitý prášek ze stavební komory lze recyklovat a znovu použít v následných stavbách, čímž se minimalizuje odpad materiálu.
- Odlehčení: Vytvořením složitých vnitřních struktur může SLM vyrábět díly, které jsou výrazně lehčí než tradičně vyráběné komponenty. To je hlavní výhoda pro aplikace, kde je rozhodující snížení hmotnosti, například v letectví a automobilovém průmyslu.
Nevýhody procesu SLM
I když SLM nabízí bohatství výhod, má také některá omezení:
- Vysoká cena: Stroje SLM jsou drahé a samotný proces může být náročný na práci. To může učinit SLM méně nákladově efektivní volbou pro vysokokapacitní výrobní série ve srovnání s tradičními metodami.
- Povrchová úprava: Díly SLM mohou mít drsný povrch v důsledku povahy procesu vrstva po vrstvě. To si může vyžádat další kroky následného zpracování, jako je obrábění pro aplikace vyžadující hladký povrch.
- Omezení materiálu: Ne všechny kovy jsou vhodné pro SLM. Vysoké teploty, které se v SLM vyskytují, mohou způsobit praskání nebo deformaci určitých materiálů. Kromě toho mohou být některé materiály náchylné k zbytkovému napětí uvnitř hotového dílu, což může ovlivnit jeho výkon.
- Omezení velikosti dílů: I když SLM dokáže vytvářet složité geometrie, existují omezení velikosti dílů, které lze vyrobit. Velikost stavební komory stroje určuje maximální rozměry dílů.
- Bezpečnostní hlediska: SLM zahrnuje vysoce výkonné lasery a kovové prášky, které mohou představovat bezpečnostní rizika. Pro ochranu obsluhy před vdechováním prachu a laserovým zářením jsou nezbytné správné ventilační a bezpečnostní protokoly.
Navzdory těmto omezením je SLM rychle se vyvíjející technologie s probíhajícím výzkumem a vývojem, který se těmito výzvami zabývá. Jak technologie dozrává, můžeme očekávat pokroky v kompatibilitě materiálů, kvalitě povrchové úpravy a nákladové efektivitě, což dále rozšíří aplikace SLM ve výrobním prostředí.
Aplikace SLM Proces
Jedinečné schopnosti SLM z něj činí cenný nástroj v různých odvětvích:
- Letectví: SLM se používá k vytváření lehkých, vysoce pevných komponent pro letadla, satelity a kosmické lodě. Schopnost navrhovat složité vnitřní struktury umožňuje díly se zlepšeným výkonem a palivovou účinností.
- Automobilový průmysl: SLM nachází uplatnění při výrobě lehkých komponent pro automobily a motocykly, jako jsou vlastní díly motorů a držáky. To přispívá ke snížení celkové hmotnosti vozidla a zlepšení spotřeby paliva.
- Lékařský: SLM transformuje oblast lékařských implantátů tím, že umožňuje vytváření vlastních protetických pomůcek, zubních implantátů a chirurgických nástrojů se složitými prvky, které dokonale odpovídají anatomii pacienta. Tato úroveň personalizace může výrazně zlepšit výsledky pacientů.
- Spotřební zboží: SLM proniká do výroby špičkového spotřebního zboží, jako jsou šperky, sportovní vybavení a dokonce i hudební nástroje. Schopnost vytvářet jedinečné a složité návrhy otevírá dveře inovativnímu vývoji produktů.
- Nástroje: SLM se používá k vytváření složitých forem a nástrojů pro různá průmyslová odvětví. To umožňuje rychlé prototypování a výrobu přizpůsobených nástrojů, což zkracuje dodací lhůty a snižuje náklady na vývoj.
Potenciální aplikace SLM jsou rozsáhlé a neustále se rozšiřují. Jak se technologie stává dostupnější a nákladově efektivnější, můžeme očekávat, že se objeví ještě více inovativních použití v různých odvětvích.
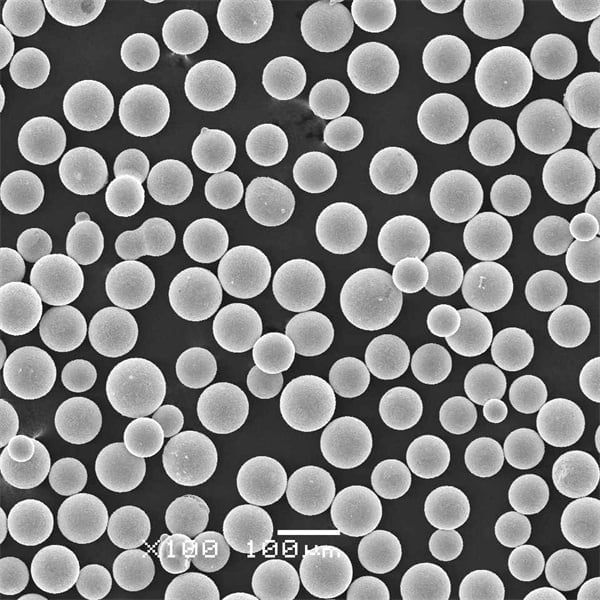
FAQ
Zde je rozpis některých často kladených otázek o SLM:
Otázka | Odpovědět |
---|---|
Jaké materiály lze použít při SLM? | V SLM lze použít širokou škálu kovů, včetně slitin titanu, nerezové oceli, hliníku, Inconelu a dokonce i drahých kovů, jako je zlato a platina. |
Jak silné jsou díly SLM? | Díly SLM mohou být neuvěřitelně pevné, s mechanickými vlastnostmi srovnatelnými s tradičně vyráběnými díly. Pevnost závisí na použitém materiálu a parametrech stavby. |
Jaký je rozdíl mezi SLM a SLS (selektivní laserové slinování)? | SLM se používá specificky pro kovové prášky, zatímco SLS lze použít pro širší škálu materiálů, včetně plastů, keramiky a dokonce i nylonu. SLM navíc plně roztaví částice prášku, zatímco SLS je částečně spojuje. |
Je SLM dobrou volbou pro velkoobjemovou výrobu? | V současné době je SLM vhodnější pro prototypování, nízkoobjemové výrobní série nebo aplikace, kde je prvořadá složitost designu. Jak technologie dozrává, může se však v budoucnu stát nákladově konkurenceschopnější pro velkoobjemovou výrobu. |
Jaké jsou budoucí vyhlídky SLM? | Budoucnost SLM je jasná. S probíhajícím výzkumem a vývojem můžeme očekávat pokroky v kompatibilitě materiálů, kvalitě povrchové úpravy a nákladové efektivitě. To dále rozšíří aplikace SLM a revolučně změní způsob, jakým vyrábíme složité kovové díly. |
Doufám, že toto komplexní vysvětlení poskytuje jasné pochopení principu činnosti, výhod, nevýhod, aplikací a budoucích vyhlídek laserového selektivního tavení (SLM). Tato inovativní technologie 3D tisku má potenciál změnit výrobu v různých odvětvích a nabízí vzrušující možnosti do budoucna.
Sdílet na
MET3DP Technology Co., LTD je předním poskytovatelem řešení aditivní výroby se sídlem v Qingdao v Číně. Naše společnost se specializuje na zařízení pro 3D tisk a vysoce výkonné kovové prášky pro průmyslové aplikace.
Dotaz k získání nejlepší ceny a přizpůsobeného řešení pro vaše podnikání!
Související články
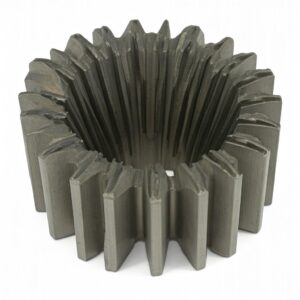
Vysoce výkonné segmenty lopatek trysek: Revoluce v účinnosti turbín díky 3D tisku z kovu
Přečtěte si více "O Met3DP
Nedávná aktualizace
Náš produkt
KONTAKTUJTE NÁS
Nějaké otázky? Pošlete nám zprávu hned teď! Po obdržení vaší zprávy obsloužíme vaši žádost s celým týmem.
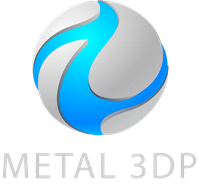
Kovové prášky pro 3D tisk a aditivní výrobu
SPOLEČNOST
PRODUKT
kontaktní informace
- Město Qingdao, Shandong, Čína
- [email protected]
- [email protected]
- +86 19116340731