3D tištěné struktury pro redistribuci tepla ve vesmírných systémech
Obsah
Úvod: Revoluce v tepelném managementu satelitů pomocí 3D tisku kovů
Nepřátelské prostředí vesmíru představuje pro konstrukci a provoz kosmických lodí jedinečné a obrovské výzvy. Mimo ochrannou přikrývku zemské atmosféry jsou družice vystaveny extrémním tepelným cyklům, kdy se střídá intenzivní teplo přímého slunečního záření a mrazivý chlad hlubokého vesmírného stínu. K tomu se přidává vesmírné vakuum, které vylučuje možnost konvekčního chlazení - hlavního mechanismu, na který se spoléháme při pozemském odvádění tepla pomocí proudění vzduchu nebo kapalin. Jako schůdné metody zvládání tepelné zátěže generované vlastními elektronickými součástmi družice a absorbované z vnějších zdrojů tak zůstává pouze kondukce (přenos tepla skrze materiály) a radiace (vyzařování tepla prostřednictvím elektromagnetických vln). Efektivní tepelné řízení není jen otázkou pohodlí, ale má zásadní význam. Citlivé elektronické komponenty, optické užitečné zatížení, pohonné systémy a dokonce i konstrukční prvky mají specifické rozsahy provozních teplot. Překročení těchto limitů může vést ke snížení výkonu, zkrácení životnosti, poruchám nebo katastrofickému selhání, což může ohrozit mise v hodnotě mnoha milionů nebo dokonce miliard dolarů. Manažeři veřejných zakázek a letečtí inženýři proto neustále hledají inovativní řešení, která by zvýšila tepelná regulace satelitů a zajistit úspěch mise v těchto náročných podmínkách vesmírné systémy.
Tepelný management v družicích se tradičně opírá o kombinaci pasivních a aktivních technik. Pasivní metody zahrnují nasazení tepelných přikrývek (vícevrstvá izolace nebo MLI), použití specializovaných povrchových nátěrů se specifickými absorpčními a emisními vlastnostmi a využití tepelných trubek a radiátorů vyrobených z běžných materiálů, jako jsou slitiny hliníku a mědi. Aktivní systémy mohou zahrnovat žaluzie, čerpané kapalinové smyčky nebo kryogenní chladiče, což zvyšuje složitost, hmotnost a spotřebu energie. Tyto tradiční přístupy jsou sice účinné, ale často se potýkají s omezeními, zejména s tím, jak se satelity stávají výkonnějšími, miniaturizovanými a vybavenými elektronikou s vysokou hustotou, která generuje značné tepelné toky. Výroba složitých geometrií tepelných trubek nebo optimalizace konstrukce žeber chladičů pomocí konvenčních metod, jako je CNC obrábění, pájení nebo odlévání, může být složitá, časově náročná, nákladná a často vede ke vzniku těžších komponent, než je žádoucí. Sestavování více dílů také přináší tepelný odpor na rozhraních a potenciální místa poruch.
Toto je místo výroba aditiv kovů (AM), běžně známý jako kov 3D tisk, se stává transformativní technologií. Tím, že se komponenty vytvářejí vrstvu po vrstvě přímo z kovového prášku pomocí zdrojů energie, jako jsou lasery nebo elektronové paprsky, uvolňuje AM nebývalou konstrukční svobodu. Umožňuje inženýrům vytvářet vysoce komplexní, optimalizované konstrukce 3D tištěné satelitní komponenty speciálně navržené pro vynikající redistribuci tepla. Představte si složité vnitřní kanály napodobující biologické cévní systémy, mřížkové struktury s velkou plochou při minimální hmotnosti nebo chladiče dokonale přizpůsobené tvaru komponent, které mají chladit. Jedná se o geometrie, které je často nemožné nebo neúnosně drahé vyrobit subtraktivními výrobními technikami.
3D tisk z kovu umožňuje vytvářet nové zesilovače tepelného toku a struktury pro redistribuci tepla - součásti speciálně navržené tak, aby účinně shromažďovaly odpadní teplo z kritických oblastí (jako jsou procesory, zesilovače nebo baterie) a účinně jej odváděly k povrchu zářiče, odkud může být bezpečně vyzářeno do vesmíru. Tyto struktury mohou být samostatnými součástmi nebo mohou být integrovány přímo do primární konstrukce družice, což vede k multifunkčním konstrukcím, které šetří hmotnost a objem - dvě vzácné komodity v konstrukci kosmických lodí. Možnost sloučit více dílů do jediné tištěné součásti dále snižuje složitost montáže, minimalizuje tepelný odpor kontaktů a zvyšuje celkovou spolehlivost. Kromě toho AM usnadňuje použití pokročilých materiálů, včetně slitin s vysokou tepelnou vodivostí, které jsou pro tyto aplikace speciálně optimalizovány.
Firmy jako Met3dp stojí v čele této revoluce a poskytují nejen pokročilé technologie, ale také 3D tisk z kovu služby, ale také vývoj a výrobu vysoce výkonných kovových prášků, které jsou klíčové pro dosažení požadovaných tepelných a mechanických vlastností v těchto náročných leteckých aplikacích. Díky odborným znalostem v procesech, jako je selektivní tavení elektronovým svazkem (SEBM), a pokročilým technikám výroby prášků, jako je plynová atomizace, umožňuje společnost Met3dp leteckým inženýrům a výrobcům plně využít potenciál aditivní výroby pro novou generaci tepelná regulace satelitů. Integrace aditivní výroba kovů do pracovního postupu návrhu a výroby nabízí změnu paradigmatu, která přesahuje postupná zlepšení a směřuje k zásadně novým způsobům řízení tepla v konstrukci vesmírné systémy, což v konečném důsledku zvyšuje výkonnost družic, prodlužuje jejich provozní životnost a umožňuje realizovat ambicióznější mise. Tento posun vyžaduje hluboké pochopení možností technologie, vlastností materiálů a konstrukčních principů, takže pro úspěšnou realizaci je nezbytná spolupráce se zkušenými partnery.
Aplikace: Kde se ve vesmírných systémech využívají 3D tištěné zesilovače tepelného toku?
Všestrannost aditivní výroby kovů umožňuje vytvářet řešení tepelného managementu na míru specifickým potřebám různých vesmírných misí a satelitních architektur. Díky schopnosti optimalizovat geometrii pro tepelný výkon při současné minimalizaci hmotnosti jsou 3D tištěné zesilovače tepelného toku obzvláště atraktivní v širokém spektru aplikací v rámci vesmírné systémy. Tyto komponenty rychle přecházejí od výzkumných konceptů k letově ověřenému hardwaru, což přináší hmatatelné výhody pro výrobce družic a pro uživatele dodavatelé leteckých komponentů.
Zde je několik klíčových oblastí, ve kterých 3D tištěné struktury pro redistribuci tepla mají významný dopad:
- Vylepšené chlazení pro výkonnou elektroniku: Moderní družice, zejména ty pro komunikaci, dálkový průzkum a zpracování dat, obsahují stále výkonnější elektronické komponenty. Polní programovatelná hradlová pole (FPGA), aplikačně specifické integrované obvody (ASIC), výkonné zesilovače (SSPA) a procesory generují v koncentrovaných oblastech značné množství odpadního tepla. Tradiční chladiče nebo tepelné pásky mohou mít potíže s efektivním řízením těchto vysokých tepelných toků nebo mohou způsobovat nepřijatelné hmotnostní ztráty.
- 3D tisk z kovu umožňuje navrhovat vysoce optimalizované chladiče se složitou geometrií žeber, vnitřními mikrokanálky nebo integrovanými strukturami tepelných trubic (jako jsou oscilační tepelné trubice nebo parní komory) přímo spojené se zdrojem tepla.
- Tyto stránky 3D tištěné satelitní komponenty mohou být konformně tvarovány tak, aby se přizpůsobily nepravidelným povrchům elektronických obalů a minimalizovaly tepelný odpor rozhraní.
- Pomocí materiálů, jako je měď, chrom, zirkon (CuCrZr), které jsou známé svou vynikající tepelnou vodivostí, může společnost AM vyrábět rozvaděče tepla, které rychle odvádějí teplo z horkých míst, čímž zabraňují přehřátí a zajišťují spolehlivý provoz. Pro aplikace, kde je nejdůležitější hmotnost, nabízejí slitiny hliníku a křemíku s hořčíkem (AlSi10Mg) dobrou rovnováhu mezi tepelným výkonem a nízkou hustotou.
- Manažeři veřejných zakázek, kteří hledají chlazení satelitní elektroniky řešení mohou využít AM k získání vysoce výkonných komponent na zakázku, které předčí hotové varianty.
- Integrované konstrukční a tepelné komponenty: Jednou z nejpřesvědčivějších výhod AM je možnost vytvářet multifunkční komponenty. Namísto oddělených konstrukčních podpěr a tepelných cest mohou konstruktéři navrhovat díly, které slouží oběma účelům současně.
- Například montážní držáky elektronických skříněk nebo přístrojů užitečného zatížení mohou být navrženy s integrovanými kanály nebo optimalizovanými topologiemi, které odvádějí teplo z namontované součásti směrem k hlavním chladicím panelům družice.
- Tento část konsolidace satelit tento přístup výrazně snižuje počet dílů, dobu montáže, hmotnost spojovacích prvků a potenciální místa tepelných nebo mechanických poruch.
- Software pro optimalizaci topologie ve spojení s volností konstrukce AM umožňuje inženýrům strategicky odstraňovat materiál z konstrukčních prvků, přičemž nosné cesty zůstávají nedotčené a ve zbývající konstrukci se vytvářejí účinné tepelné kanály. To vede k významným odlehčování v letectví a kosmonautice možnosti bez snížení výkonu.
- Pokročilé tepelné trubky a parní komory: Tepelné trubice jsou vysoce účinná pasivní zařízení pro přenos tepla na větší vzdálenosti s minimálním poklesem teploty. Tradiční tepelné trubice mají obvykle jednoduchou válcovou nebo zploštělou geometrii.
- Technologie AM umožňuje výrobu složitých geometrií tepelných trubek, jako jsou zakřivené nebo rozvětvené trubky, které se mohou pohybovat kolem jiných součástí v těsném prostoru satelitního šasi.
- Umožňuje integraci knotové struktury (zodpovědné za kapilární působení) přímo do stěny tepelné trubice během procesu tisku, což potenciálně zvyšuje výkon a spolehlivost ve srovnání s vkládáním běžných knotových materiálů.
- Ploché parní komory, které šíří teplo po povrchu, lze vytisknout se složitými vnitřními podpůrnými strukturami a optimalizovanými cestami proudění par, což zvyšuje jejich schopnost šířit teplo pro aplikace, jako je chlazení velkých elektronických desek nebo propojení s.. panely chladiče.
- Optimalizované panely a pláty chladiče: Radiátory jsou nezbytné pro odvod odpadního tepla do prostoru. Jejich účinnost závisí na ploše povrchu, emisivitě povrchu a účinnosti rozvodu tepla po sálavém povrchu.
- AM umožňuje vytvářet chladičové panely s velmi složitou geometrií žeber (např. mřížkové struktury, kolíčková žebra, fraktální konstrukce), které maximalizují plochu pro vyzařování a zároveň minimalizují hmotnost.
- Tepelné pásky nebo spoje, které přenášejí teplo z vnitřních součástí do chladiče, lze vytisknout s optimalizovanými průřezy a případně integrovat přímo do samotného panelu chladiče, čímž se zvýší účinnost přenosu tepla.
- Pro Tepelný management CubeSat, kde jsou hmotnost a objem extrémně omezené, mohou být miniaturizované, vysoce výkonné zářiče umožněné technologií AM klíčové pro realizovatelnost mise.
- Komponenty pro kryogenní systémy: Některé specializované vesmírné mise vyžadují kryogenní chlazení citlivých detektorů nebo přístrojů.
- Pomocí AM lze vytvářet složité výměníky tepla, součásti kryochladičů nebo tepelné pásy navržené pro efektivní provoz při velmi nízkých teplotách s využitím materiálů vhodných pro kryogenní prostředí.
Přijetí 3D tištěné zesilovače tepelného toku zahrnuje různé třídy družic, od malých CubeSatů a SmallSatů, kde je nejdůležitější úspora hmotnosti a objemu, až po velké geostacionární komunikační družice a složité mise pozorování Země nebo vědecké mise vyžadující sofistikovanou tepelnou kontrolu. Jak uvádí letecké a kosmické inženýrství firmy a výroba satelitů společnosti získají více zkušeností a důvěry v technologii, která je poháněna spolehlivými dodavatelé leteckých komponentů jako je Met3dp, který nabízí vysoce kvalitní materiály a tiskové procesy, se rozsah aplikací stále rozšiřuje a posunuje hranice vesmírné technologie.
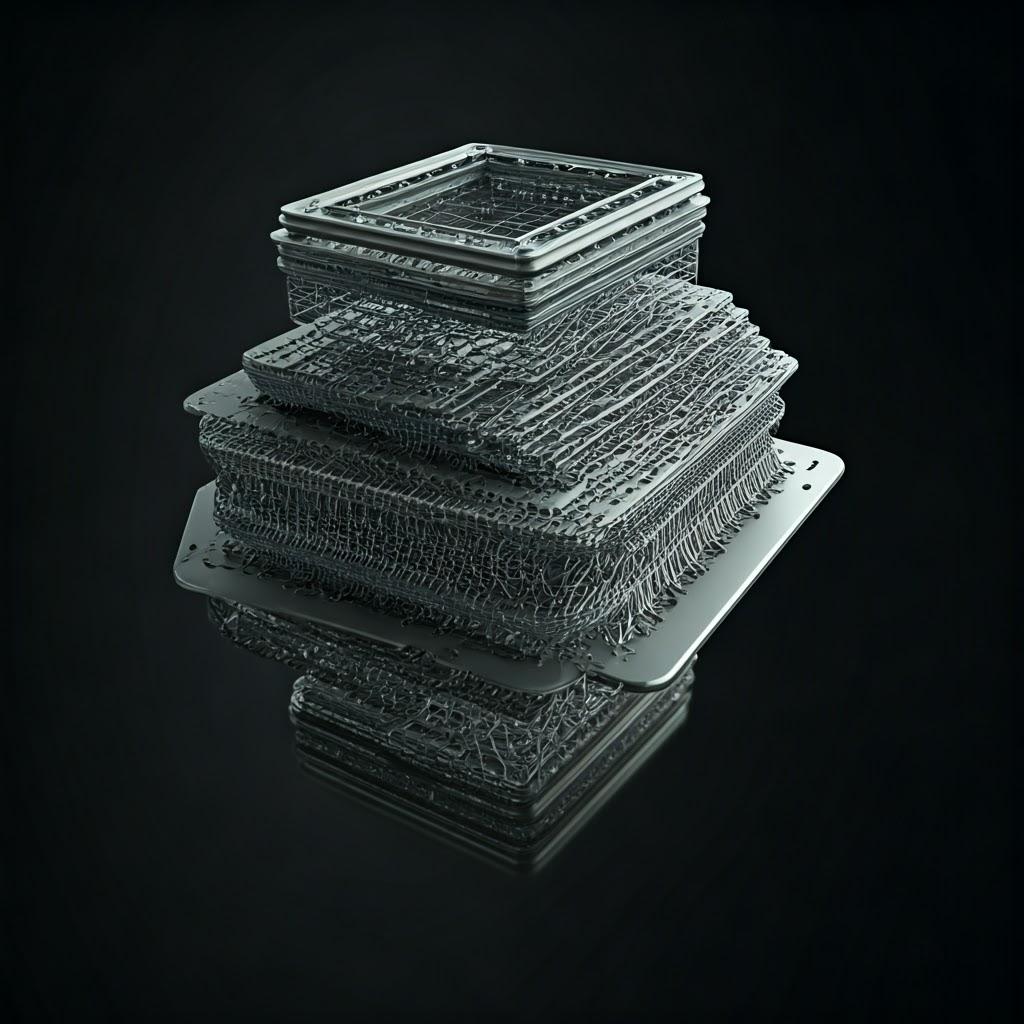
Proč 3D tisk z kovu pro konstrukce pro redistribuci tepla ze satelitů?
Rozhodnutí přijmout aditivní výroba kovů pro kritické součásti, jako jsou satelitní zesilovače tepelného toku, vyplývá ze souběhu přesvědčivých výhod oproti tradičním výrobním metodám. Zatímco zavedené techniky, jako je CNC obrábění, odlévání, pájení a tváření plechů, dobře sloužily leteckému průmyslu po celá desetiletí, často přinášejí značná omezení, pokud jde o vytváření vysoce optimalizovaných, komplexních geometrií, které jsou vyžadovány pro řešení tepelného managementu nové generace. Inženýři a specialisté na zadávání zakázek, kteří posuzují možnosti výroby pro satelitní komponenty se stále častěji obracejí na AM díky výhodám, které přímo řeší jedinečné výzvy, jež přináší vesmírné systémy.
Zde je rozpis důvodů 3D tisk z kovu nabízí pro tyto aplikace vynikající přístup:
- Bezkonkurenční volnost designu (geometrická složitost): To je pravděpodobně nejvýznamnější výhoda. AM vytváří díly vrstvu po vrstvě, což konstruktéry osvobozuje od omezení daných subtraktivními metodami (odebírání materiálu) nebo technikami lisování/odlévání.
- Optimalizované vnitřní kanály: Inženýři mohou navrhovat složité vnitřní kanály a sítě v chladiči nebo výměníku tepla, přesně řídit proudění kapaliny (v aktivních systémech) nebo maximalizovat vodivé cesty a povrch v pasivních zařízeních. To umožňuje vytvářet konstrukce, které věrně napodobují vysoce účinné přírodní struktury, jako jsou cévní sítě.
- Mřížové struktury: Lze vytvořit lehké, ale pevné mřížkové nebo topologicky optimalizované struktury, které maximalizují plochu pro odvod tepla (např. v chladičích nebo chladičích) a zároveň minimalizují spotřebu materiálu a hmotnost.
- Konformní chlazení: Chladiče a rozptylovače tepla lze navrhnout tak, aby se dokonale přizpůsobily zakřiveným nebo nepravidelným povrchům elektronických součástek nebo satelitních struktur, minimalizovaly tepelný odpor rozhraní a maximalizovaly účinnost přenosu tepla.
- Integrované funkce: Montážní body, přípojky pro kapaliny, pouzdra senzorů a další prvky lze během tisku integrovat přímo do tepelné součásti.
- DfAM (Design for Additive Manufacturing): Využití DfAM principy umožňují konstruktérům plně využít těchto geometrických možností, což vede ke komponentům, které jsou zásadně vhodnější pro jejich úkol tepelného managementu.
- Konsolidace částí: Tradiční tepelné sestavy často zahrnují několik jednotlivých komponent (např. základní desky, žebra, tepelné trubky, držáky), které je třeba vyrobit samostatně a poté je spojit, obvykle pájením, pájením nebo mechanickým upevněním.
- AM umožňuje spojit více funkčních prvků do jediného monolitického tištěného dílu. Například montážní držák může mít integrované tepelné pásky a chladič.
- Výhody konsolidace částí Satelit:
- Snížená hmotnost: Eliminuje spojovací prvky, rozhraní a překrývající se materiál.
- Zvýšená spolehlivost: Méně spojů znamená méně potenciálních cest úniku (u kapalinových systémů) nebo míst mechanických/tepelných poruch.
- Nižší náklady na montáž & Čas: Zjednodušuje proces integrace satelitů.
- Vylepšený tepelný výkon: Eliminuje tepelný odpor spojů a rozhraní.
- Efektivita materiálu a odlehčení: Letecké a kosmické aplikace kladou důraz na minimalizaci hmotnosti vzhledem k vysokým nákladům na vynesení užitečného nákladu na oběžnou dráhu (často desítky tisíc dolarů za kilogram).
- Tvorba téměř čistého tvaru: Při AM se vyrábějí díly s rozměry blízkými jejich konečným rozměrům, přičemž se používá pouze materiál nezbytný pro samotnou součást a potřebné podpůrné konstrukce (které jsou často minimalizovány díky návrhu). To je v ostrém kontrastu se subtraktivní výrobou (např. CNC obráběním), kdy se značná část výchozího polotovaru materiálu odřeže a stane se odpadem. Tím se zlepšuje poměr “buy-to-fly”, což je kritický ukazatel při dodavatel leteckých komponentů řetězy.
- Optimalizace topologie: V kombinaci s volností návrhu umožňuje AM praktické použití algoritmů optimalizace topologie. Tyto nástroje matematicky určují nejefektivnější rozložení materiálu v definovaném konstrukčním prostoru tak, aby byly splněny konkrétní požadavky na vlastnosti (např. tuhost, tepelná vodivost) při daném zatížení, což vede k vysoce organicky vypadajícím, lehkým konstrukcím, které nelze vyrobit konvenčním způsobem. To je klíčovým faktorem pro odlehčování v letectví a kosmonautice komponenty.
- Rychlé prototypování a zrychlený vývoj: The vesmírný hardware vývojový cyklus je notoricky známý jako dlouhý a nákladný. AM nabízí významné výhody pro urychlení tohoto procesu.
- Rychlá iterace: Nové iterace konstrukce tepelných součástí lze vytisknout a otestovat během několika dnů nebo týdnů, zatímco u tradičních nástrojů a výrobních zařízení jsou to často měsíce. To umožňuje inženýrům rychle ověřovat tepelné modely, zkoumat různé konstrukční koncepty a mnohem rychleji dospět k optimálnímu řešení.
- Eliminace nástrojů: AM obvykle nevyžaduje nákladné a časově náročné vytváření forem, zápustek nebo přípravků spojených s odléváním, kováním nebo složitým obráběním. To výrazně snižuje počáteční náklady a dobu realizace, zejména u nízkoobjemových sérií typických pro satelitní hardware.
- Výroba na vyžádání: Díly lze tisknout podle potřeby, což usnadňuje agilní vývoj a v budoucnu může podpořit koncepty, jako je výroba ve vesmíru.
- Flexibilita materiálu: Tento příspěvek se zaměřuje na AlSi10Mg a CuCrZr, ale procesy AM jsou kompatibilní s rostoucím počtem kovů a slitin důležitých pro letecký průmysl, včetně různých titanových slitin, niklových superslitin a nerezových ocelí. To umožňuje konstruktérům vybrat optimální materiál na základě specifických tepelných, strukturálních a environmentálních požadavků aplikace. Přístup k vysoce kvalitním práškům, jako jsou prášky vyráběné společností Met3dp s využitím pokročilých technologií rozprašování plynu techniky, je zásadní pro dosažení konzistentních a spolehlivých vlastností materiálu v konečném tištěném dílu.
Souhrnně lze říci, že srovnání 3D tisk z kovu vs CNC obrábění a jiných tradičních metod odhaluje přesvědčivé důvody pro použití AM pro satelitní struktury redistribuce tepla. Schopnost vytvářet vysoce komplexní, lehké a konsolidované díly optimalizované z hlediska tepelného výkonu spolu se zrychlenými vývojovými cykly poskytuje výrobcům satelitů a poskytovatelům tepelných řešení na náročném leteckém trhu významnou konkurenční výhodu. Spolupráce se znalými metal AM poskytovatelé služeb zajišťují přístup k odborným znalostem v oblasti konstrukce, materiálů a řízení procesů, které jsou nezbytné pro plné využití těchto výhod.
Doporučené materiály: AlSi10Mg a CuCrZr pro optimální tepelný výkon
Výběr správného materiálu je při navrhování jakékoli satelitní součásti prvořadý, ale u zařízení pro zvýšení tepelného toku, kde jsou tepelné vlastnosti hlavním faktorem výkonu a jsou vyváženy přísnými požadavky na hmotnost a konstrukci, nabývá na významu. Pro 3D tištěné struktury tepelného managementu družic se jako hlavní kandidáti objevily dva kovové prášky, které nabízejí odlišné výhody v závislosti na konkrétních potřebách aplikace: Hliník, křemík, hořčík (AlSi10Mg) a měď, chrom, zirkon (CuCrZr). Porozumění jejich vlastnostem a důvodům, proč jsou upřednostňovány v kovové prášky pro letectví a kosmonautiku výběr je pro inženýry a manažery veřejných zakázek zásadní.
Hliník křemík hořčík (AlSi10Mg): Lehký univerzální materiál
AlSi10Mg je jednou z nejpoužívanějších hliníkových slitin při aditivní výrobě kovů, zejména při laserové práškové fúzi (L-PBF). Je to v podstatě slitina hliníkového odlitku upravená pro procesy AM.
- Klíčové vlastnosti a výhody:
- Nízká hustota: S hustotou přibližně 2,67 g/cm³ je výrazně lehčí než slitiny mědi, oceli nebo titanu, a proto je velmi atraktivní pro odlehčování v letectví a kosmonautice komponenty, u nichž je rozhodující hmotnost.
- Dobrá tepelná vodivost: Přestože AlSi10Mg nemá tak vysokou tepelnou vodivost jako čistý hliník nebo měď, nabízí dobrou tepelnou vodivost (obvykle v rozmezí 100-130 W/m-K po vhodném tepelném zpracování), která je dostatečná pro mnoho aplikací chladičů a rozvaděčů tepla.
- Dobrý poměr pevnosti a hmotnosti: Vykazuje dobré mechanické vlastnosti, včetně slušné pevnosti v tahu a tvrdosti, zejména po odlehčení od napětí nebo tepelném zpracování podobném T6. Díky tomu mohou součásti vyrobené z AlSi10Mg plnit jak konstrukční, tak tepelné funkce.
- Vynikající zpracovatelnost: AlSi10Mg je známý svým relativně dobrým chováním během procesu L-PBF, což umožňuje spolehlivý tisk složitých geometrií s jemnými rysy.
- Odolnost proti korozi: Nabízí dobrou odolnost proti korozi.
- Typické aplikace: Ideální pro aplikace, kde je třeba najít rovnováhu mezi nízkou hmotností, přiměřeným tepelným výkonem a strukturální integritou. Mezi příklady patří:
- Integrované konstrukční konzoly s tepelnými cestami.
- Větší a složitější chladiče, u nichž je úspora hmotnosti ve srovnání s mědí značná.
- Panely chladiče s optimalizovanou strukturou žeber.
- Pouzdra pro elektroniku vyžadující mírný odvod tepla.
Měď, chrom, zirkon (CuCrZr): Šampion ve vysoké vodivosti
CuCrZr (typicky UNS C18150) je srážením kalitelná slitina mědi známá pro svou výjimečnou kombinaci vysoké tepelné a elektrické vodivosti a dobré mechanické pevnosti, která se poměrně dobře udržuje při zvýšených teplotách.
- Klíčové vlastnosti a výhody:
- Vynikající tepelná vodivost: To je výjimečná funkce. Tepelná vodivost CuCrZr je velmi vysoká, po vhodném tepelném zpracování (stárnutí) často přesahuje 300 W/m-K. Tato hodnota je výrazně vyšší než u AlSi10Mg a blíží se hodnotě čisté mědi, takže je ideální pro řízení vysokých tepelných toků.
- Vysoká elektrická vodivost: Má také vynikající elektrickou vodivost, což může být výhodné v některých integrovaných aplikacích.
- Dobrá odolnost při vysokých teplotách: Ve srovnání s čistou mědí nebo některými slitinami hliníku si lépe zachovává pevnost při zvýšených teplotách.
- Dobrá odolnost proti opotřebení: Nabízí přiměřenou odolnost proti opotřebení.
- Typické aplikace: Používá se především tam, kde je absolutní prioritou maximální přenos tepla, a to i za cenu vyšší hustoty ve srovnání s hliníkem. Příklady zahrnují:
- Vysoce výkonné chladiče pro hustě osazenou výkonnou elektroniku (např. zesilovače, procesory).
- Rozptylovače tepla určené k rychlému odvádění tepla z lokálních horkých míst.
- Součásti v tepelných trubkách nebo parních komorách, které vyžadují maximální tepelnou propustnost.
- Indukční cívky nebo součásti vyžadující tepelnou i elektrickou vodivost.
Srovnání a úvahy o vesmírných aplikacích:
Volba mezi AlSi10Mg a CuCrZr často zahrnuje kompromisy:
Vlastnictví | AlSi10Mg (typický, tepelně zpracovaný) | CuCrZr (typický, tepelně zpracovaný) | Tradiční Al 6061-T6 | Tradiční měď (ETP) | Poznámky |
---|---|---|---|---|---|
Hustota (g/cm³) | ~2.67 | ~8.89 | ~2.70 | ~8.96 | CuCrZr má 3x větší hustotu než AlSi10Mg. |
Tepelná vodivost (W/m-K) | ~100 – 130 | ~300 – 320 | ~167 | ~390 – 400 | CuCrZr nabízí výrazně vyšší K. |
Pevnost v tahu (MPa) | ~300 – 450 | ~450 – 550 | ~310 | ~220 (žíhaný) | Oba materiály AM mají dobrou pevnost. |
Koeficient tepelné roztažnosti (CTE) (µm/m-°C) | ~21 – 22 | ~17 – 18 | ~23 | ~17 | Důležité pro tepelné namáhání & rozhraní. |
Relativní náklady | Mírný | Vyšší | Dolní | Mírný | Prášky AM zvyšují náklady. |
Možnost tisku | Obecně dobré | Náročnější | N/A | N/A | Vliv odrazivosti/vodivosti na proces AM. |
Export do archů
Proč právě tyto prášky pro vesmír?
Kromě základních tepelných a mechanických vlastností musí materiály určené do vesmíru splňovat i další kritéria:
- Zplodiny: Materiály musí mít ve vakuovém prostředí nízké odplyňovací vlastnosti, aby nedošlo ke kontaminaci citlivých optických povrchů nebo elektroniky. AlSi10Mg i CuCrZr mohou při správném zpracování a čištění splňovat typické požadavky na prostor.
- Odolnost proti záření: I když jsou kovy obecně méně náchylné k poškození zářením než polymery, je třeba zvážit dlouhodobé účinky v prostředí kosmického záření, i když jsou pro tyto slitiny obvykle méně kritické než pro elektroniku.
- Spolehlivost procesu: Konzistentní a předvídatelné vlastnosti materiálů jsou pro kritický hardware zásadní. To do značné míry závisí na kvalitě vstupních práškových surovin.
Úloha Met3dp’ v oblasti materiálové excelence:
Dosažení výše uvedených optimálních vlastností u hotového 3D tištěného dílu závisí především na kvalitě a konzistenci použitého kovového prášku. Společnost Met3dp se specializuje na výrobu vysoce kvalitní kovové prášky optimalizované pro aditivní výrobní procesy, jako je L-PBF a SEBM. S využitím pokročilých technik, jako je vakuum rozprašování plynu a plazmovým procesem s rotační elektrodou (PREP) vyrábí Met3dp prášky s:
- Vysoká sféricita: Zajišťuje dobrou tekutost prášku a husté uložení v loži prášku, což vede k vyšší hustotě dílů s menším počtem dutin.
- Nízká pórovitost: Minimalizuje vnitřní pórovitost prášku pro lepší integritu finálního dílu.
- Řízená distribuce velikosti částic (PSD): Optimalizovaný PSD pro konkrétní stroje a procesy AM, který zajišťuje konzistentní tavení a tvorbu vrstev.
- Vysoká čistota: Minimalizace nečistot, které by mohly negativně ovlivnit mechanické nebo tepelné vlastnosti.
Použitím vysoce kvalitních prášků AlSi10Mg a CuCrZr od renomované společnosti kovové prášky pro letectví a kosmonautiku dodavatele, jako je Met3dp, mohou mít výrobci satelitů větší jistotu, že dosáhnou požadovaného výkonu, spolehlivosti a konzistence, které jsou vyžadovány pro náročné systémy výběr satelitního materiálu v aplikacích tepelného managementu. Konzultace s odborníky na materiály a AM je klíčem k optimální volbě pro každý jedinečný požadavek mise.
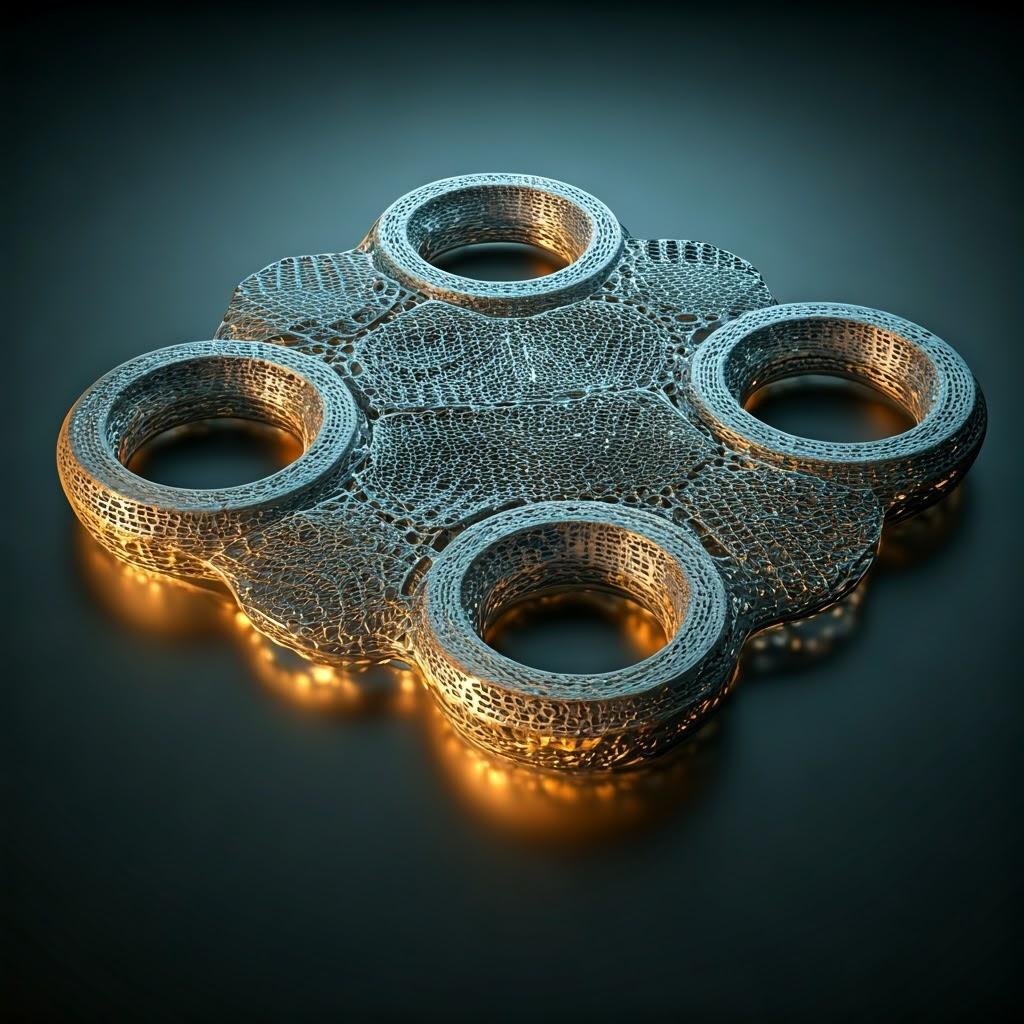
Úvahy o návrhu aditivně vyráběných zařízení pro zvýšení tepelného toku
Skutečná síla aditivní výroby kovů spočívá ve schopnosti převádět složité návrhy zaměřené na výkon do fyzické reality. Pouhá replikace návrhu určeného pro tradiční výrobu však často nedokáže využít plný potenciál AM a může dokonce vést k neoptimálním výsledkům nebo výrobním potížím. Navrhování úspěšných 3D tištěných zesilovačů tepelného toku pro vesmírné systémy vyžaduje přijetí Design pro aditivní výrobu (DfAM) zásady. Tento přístup zohledňuje jedinečné možnosti a omezení stavebního procesu po vrstvách již od koncepční fáze, čímž zajišťuje současnou optimalizaci tepelných vlastností, strukturální integrity a vyrobitelnosti. Inženýři navrhující satelitní komponenty, zejména tepelného hardwaru, musí přemýšlet jinak, pokud je zvolenou výrobní cestou AM.
Zde jsou klíčové informace Tepelný management DfAM úvahy o satelitních zesilovačích tepla:
- Využití geometrické volnosti pro tepelný výkon:
- Optimalizované vnitřní kanály: Na rozdíl od vrtání nebo odlévání umožňuje technologie AM vytvářet hladce zakřivené vnitřní kanály s proměnlivým průřezem, které minimalizují tlakovou ztrátu (u systémů založených na kapalině) nebo maximalizují konvekční plochu. Kanály mohou sledovat složité dráhy, aby se přímo zaměřily na konkrétní zdroje tepla. Tenké, konformní kanály mohou účinně šířit teplo po povrchu.
- Pokročilé geometrie ploutví: Překročte rámec jednoduchých lisovaných ploutví. AM umožňuje vytvářet složité struktury ploutví, jako jsou kolíkové ploutve, kuželovité ploutve, vlnité ploutve nebo ploutve na bázi mřížky (např. gyroidy, osmičkové příhradoviny). Tyto struktury mohou významně zvýšit poměr plochy k objemu a zlepšit odvod tepla konvekcí (pokud je to použitelné při pozemních zkouškách nebo ve specifických prostředích) nebo vyzařováním a současně snížit hmotnost. Zejména příhradové konstrukce nabízejí vynikající poměr tuhosti a hmotnosti spolu se zvýšenou plochou.
- Maximalizace plochy: Techniky, jako je přidání texturovaných povrchů nebo začlenění mikroelementů do kanálů nebo na vnější povrchy, mohou dále zlepšit přenos tepla, ačkoli jejich dopad a praktická využitelnost do značné míry závisí na konkrétním mechanismu přenosu tepla (vedení, sálání) a okolním prostředí (vakuum).
- Konformní design: Navrhněte chladiče, rozptylovače nebo studené desky tak, aby dokonale odpovídaly obrysům součástí, které vytvářejí teplo (např. zakřivené povrchy desek plošných spojů, nerovinné obaly zařízení). Tím se minimalizuje tloušťka materiálu tepelného rozhraní (TIM) a kontaktní odpor, což vede k účinnějšímu přenosu tepla ve srovnání s plochými chladiči na nerovinných površích.
- Minimální rozměry prvků a tloušťka stěn: Procesy AM, jako je například laserová fúze v práškovém loži (L-PBF), mají omezení týkající se nejmenších prvků a nejtenčích stěn, které mohou spolehlivě vyrobit.
- Typické limity: V závislosti na stroji, materiálu (AlSi10Mg a CuCrZr mají různé vlastnosti zpracování) a použitých parametrech se minimální tloušťky stěn mohou pohybovat od 0,3 mm do 0,8 mm a minimální rozměry prvků (jako jsou průměry kanálků nebo tloušťky vzpěr v mřížkách) se často pohybují v podobném rozmezí. Překročení těchto limitů může vést k neúplnému vytvoření, špatné povrchové úpravě nebo strukturálním slabinám.
- Dodržování pravidel návrhu: Návrháři musí pracovat v rámci stanovených Pravidla návrhu L-PBF poskytované poskytovatelem služeb AM (jako je Met3dp). Tato pravidla, založená na empirických datech a znalostech procesu, určují dosažitelné velikosti prvků, poměry stran pro nepodporované stěny nebo převisy a minimální průměry otvorů. Zásadní je včasná konzultace s výrobním partnerem.
- Strategie podpůrné struktury: Součásti AM se vytvářejí vrstvu po vrstvě a převislé prvky nebo povrchy orientované pod určitým úhlem (obvykle 45 stupňů od vodorovné roviny sestavení) vyžadují během tisku dočasné podpůrné struktury. Tyto podpěry zabraňují deformaci v důsledku tepelného namáhání, ukotvují díl k sestavovací desce a zajišťují geometrickou přesnost.
- Minimalizujte podporu: Pokud je to možné, navrhujte díly se samonosnými úhly, abyste omezili potřebu podpěr, které spotřebovávají další materiál, prodlužují dobu tisku a vyžadují následné zpracování pro odstranění.
- Návrh na odstranění: Pokud jsou podpěry nevyhnutelné, navrhněte je tak, aby byly snadno přístupné a odstranitelné bez poškození povrchu finálního dílu. Vyvarujte se umisťování podpěr na kritické funkční povrchy nebo do složitých vnitřních kanálů, kde je jejich odstranění obtížné nebo nemožné. Zvažte místa odlomení nebo prvky, které usnadňují čisté oddělení.
- Vliv na povrchovou úpravu: Povrchy, na kterých jsou připevněny podpěry, mají po odstranění zpravidla drsnější povrch ve srovnání se samonosnými nebo nahoru směřujícími povrchy. To je třeba vzít v úvahu, pokud je povrchová úprava v těchto oblastech kritická. S dodavatelem by se mohly prozkoumat specializované podpůrné strategie (např. snadno odstranitelné nebo rozpustné podpěry, i když v kovovém AM jsou méně běžné).
- Optimalizace topologie a odlehčení: Tato výpočetní konstrukční technika je pro AM ideální.
- Proces: Inženýři definují návrhový prostor, aplikují očekávané tepelné a konstrukční zatížení, stanoví výkonnostní cíle (např. maximální teplotu, minimální tuhost) a specifikují omezení (např. ochranné zóny, výrobní omezení). Software pak iterativně odstraňuje materiál z nekritických oblastí, čímž vzniká optimalizovaná, často organicky vypadající konstrukce, která splňuje požadavky s minimální hmotností.
- Použití: Široce používané pro optimalizace topologie v letectví a kosmonautice konzol a konstrukčních prvků, je stejně výkonný i pro tepelné komponenty. Dokáže určit nejefektivnější cesty pro vedení tepla a zároveň zajistit, aby součást odolala provoznímu namáhání (např. vibracím při startu). Výsledné složité geometrie jsou často vyrobitelné pouze pomocí AM.
- Integrace funkcí: Snižte počet dílů a složitost montáže integrací prvků přímo do návrhu AM.
- Montážní rozhraní: Navrhněte otvory pro šrouby, nástavce, polohovací čepy nebo složité styčné plochy přímo do tepelného zesilovače. Zajistěte, aby tolerance a povrchová úprava splňovaly požadavky na montáž (případně vyžadovaly dodatečné opracování).
- Kapalinové konektory: U kapalinou chlazených systémů nebo tepelných trubek integrujte závitové porty, trubkové přípojky nebo přípojky rozdělovače.
- Pouzdro senzoru: Osazení míst nebo držáků pro teplotní čidla (termistory, termočlánky) pro sledování tepelného výkonu.
- Tepelné modelování a simulace: Vzhledem ke složitým geometriím, které AM umožňuje, je přesné tepelné modelování a simulace ve fázi návrhu ještě důležitější.
- Předpověď výkonu: Použijte nástroje pro analýzu konečných prvků (FEA) nebo výpočetní dynamiku tekutin (CFD) k předpovědi rozložení teplot, cest tepelného toku, tlakových ztrát (pokud je to vhodné) a celkového tepelného odporu navržené součásti za provozních podmínek.
- Iterace návrhu: Simulace umožňuje rychlou virtuální iteraci a optimalizaci rozvržení kanálů, návrhů žeber a volby materiálů před se zavázat k nákladným a časově náročným fyzickým prototypům. Ověřte různé Tepelný management DfAM strategie z výpočetního hlediska.
- Korelace: Tepelné zkoušky po výrobě by měly být použity k ověření a zpřesnění simulačních modelů pro budoucí návrhy.
Úspěšné konstrukce satelitních komponentů použití AM vyžaduje spolupráci mezi konstruktéry, tepelnými specialisty a odborníky na výrobu. Spolupráce se zkušenými poskytovateli AM služeb, jako je Met3dp, na počátku návrhového cyklu umožňuje přístup k zásadním výrobním poznatkům, odborným znalostem materiálů a poradenství v oblasti Pravidla návrhu L-PBF, čímž se zajistí, že konečný 3D tištěná struktura pro redistribuci tepla je nejen inovativní, ale také vyrobitelný, spolehlivý a optimálně funguje v náročném prostředí vesmírné systémy.
Dosažitelná tolerance, povrchová úprava a rozměrová přesnost
Zatímco aditivní výroba kovů otevírá neuvěřitelnou svobodu designu, je pro inženýry a manažery nákupu, kteří zajišťují dodávky, zásadní, aby 3D tištěné satelitní komponenty mít realistická očekávání ohledně dosažitelné úrovně přesnosti. Tolerance, povrchová úprava a rozměrová přesnost jsou rozhodujícími faktory, zejména u součástí, které musí přesně spolupracovat s ostatními částmi družicové sestavy nebo splňovat přísná výkonnostní kritéria. Klíčem k úspěšné realizaci je pochopení možností a omezení procesů, jako je laserová fúze v práškovém loži (L-PBF) pro materiály, jako jsou AlSi10Mg a CuCrZr.
Tolerance v kovovém AM:
- Obecné dosažitelné tolerance: Typická rozměrová přesnost kovových dílů L-PBF se zpravidla pohybuje v rozmezí ±0,1 mm až ±0,2 mm u menších rozměrů (např. do 100 mm) nebo ±0,1 % až ±0,2 % u větších rozměrů. Tyto hodnoty mohou být ovlivněny několika faktory:
- Velikost a geometrie dílu: Větší díly nebo složité geometrie s tenkými stěnami nebo převisy mohou vykazovat větší odchylky v důsledku nahromaděného tepelného napětí a možných deformací během sestavování.
- Materiál: Různé materiály se při intenzivních, lokalizovaných cyklech ohřevu a chlazení L-PBF chovají různě. AlSi10Mg a CuCrZr mají odlišné tepelné vlastnosti, které ovlivňují vznik zbytkového napětí a potenciální deformace.
- Kalibrace stroje: Přesnost a kalibrace konkrétního stroje AM hraje významnou roli. Špičkové průmyslové stroje, jako jsou ty, které používají poskytovatelé zaměřující se na kvalitu, jako je Met3dp, obecně nabízejí lepší přesnost a opakovatelnost.
- Orientace na stavbu: Orientace dílu na konstrukční plošině ovlivňuje tepelný průběh, požadavky na podporu a potenciální anizotropie smrštění, což má vliv na konečné rozměry.
- Následné zpracování: Tepelné zpracování s uvolněním napětí může způsobit drobné rozměrové změny, se kterými je třeba počítat.
- Normy ISO: Dosažitelné tolerance se často vztahují k obecným tolerančním normám, jako je ISO 2768 (střední ‘m’ nebo hrubá ‘c’ třída). Dosažení přísnějších tolerancí (např. ISO 2768-fine ‘f’) však obvykle vyžaduje sekundární obráběcí operace.
- Kritické rozměry: U rozhraní, montážních otvorů nebo prvků vyžadujících vysokou přesnost je běžnou praxí navrhnout AM díl mírně naddimenzovaný (přidáním obráběcího materiálu) a poté použít CNC obrábění v následném kroku zpracování k dosažení požadovaných těsných tolerancí (např. až ±0,01 mm nebo více, v závislosti na prvku).
Povrchová úprava (drsnost):
Povrchová úprava kovových dílů AM je ze své podstaty drsnější než povrchová úprava dosažená běžným obráběním nebo leštěním.
- Typická drsnost (Ra) ve stavu po dokončení: Drsnost povrchu (hodnota Ra) se obvykle pohybuje v rozmezí od 5 µm do 25 µm (mikrometrů) v závislosti na:
- Orientace: Povrchy směřující vzhůru a svislé stěny mají obecně nejlepší povrchovou úpravu. Povrchy směřující dolů (podepřené povrchy) bývají nejdrsnější v důsledku interakce s podpůrnými konstrukcemi. Šikmé povrchy se nacházejí někde uprostřed.
- Tloušťka vrstvy: Tenčí vrstvy obecně vedou k hladšímu povrchu, ale prodlužují dobu výstavby a zvyšují náklady. Typické tloušťky vrstev se pohybují od 20 µm do 60 µm.
- Parametry procesu: Výkon laseru, rychlost skenování a vzdálenost mezi šrafami ovlivňují vlastnosti taveniny a výslednou strukturu povrchu.
- Kvalita prášku: Rozložení velikosti a sféricita kovového prášku (například vysoce kvalitních prášků z pokročilé atomizace Met3dp’) může ovlivnit hustotu práškového lože a stabilitu taveniny, což má vliv na konečnou kvalitu povrchu.
- Zlepšení povrchové úpravy: Pokud je požadován hladší povrch z důvodu tepelného kontaktu, proudění kapalin, těsnění nebo z estetických důvodů, lze použít různé techniky následného zpracování:
- Tryskání kuličkami/pískování: Poskytuje rovnoměrný matný povrch, obvykle mírně zlepšuje Ra a odstraňuje částečně roztavené částice.
- Třískové/vibrační dokončování: Dokáže vyhladit vnější povrchy a odjehlit hrany, což je obzvláště účinné pro dávky menších dílů.
- Elektrolytické/chemické leštění: Lze dosáhnout velmi hladkého, zrcadlového povrchu, ale může mírně zaoblit ostré hrany. Účinnost se liší podle materiálu.
- CNC obrábění/broušení: Nabízí přesnou kontrolu nad povrchovou úpravou specifických oblastí.
- Mikroobrábění/laserové leštění: Pokročilé techniky pro dosažení velmi vysoké kvality povrchu na cílových plochách.
Rozměrová přesnost a ověřování:
Zajištění konečného 3D tištěná struktura pro redistribuci tepla splňuje všechny rozměrové specifikace, je rozhodující pro jeho funkci a integraci do družice.
- Důležitost: Správné rozměry zajišťují správné spojení s párovacími součástmi, přesné vyrovnání tepelných rozhraní a správné průtokové cesty ve vnitřních kanálech. Odchylky mohou vést k problémům při montáži, snížení tepelného výkonu nebo dokonce ke konstrukčním problémům.
- Metrologie a kontrola: Renomovaný služby 3D tisku pro letecký průmysl používat přísné postupy kontroly kvality a inspekce. Mezi běžné postupy patří:
- Souřadnicové měřicí stroje (CMM): Poskytuje vysoce přesná 3D měření kritických prvků a celkové geometrie.
- 3D skenování (laserem nebo strukturovaným světlem): Zachycení celé geometrie dílu, což umožňuje porovnání s původním modelem CAD a identifikaci odchylek na celém povrchu (tepelné mapování).
- Tradiční metrologické nástroje: Třmeny, mikrometry, výškoměry pro měření specifických prvků.
- Nedestruktivní zkoušení (NDT): Techniky, jako je rentgenové nebo CT skenování, lze použít nejen ke kontrole přesnosti vnitřních rozměrů (např. průměrů kanálků), ale také ke kontrole vnitřních vad, jako je pórovitost.
- Systémy řízení kvality: Hledejte dodavatele s robustním systémem řízení kvality (QMS), případně certifikovaným podle norem, jako je ISO 9001 nebo, v ideálním případě pro letecký průmysl, AS9100. To zajišťuje zdokumentované procesy pro kontrolu kvality, sledovatelnost a neustálé zlepšování. Například společnost Met3dp zdůrazňuje svůj závazek dodržovat špičkový objem, přesnost a spolehlivost tisku, podpořený přísnými protokoly kvality, které jsou nezbytné pro kritické úkoly satelitní komponenty.
Závěrem lze říci, že konstruktéři by měli využívat volnost designu AM, ale zároveň musí navrhovat s ohledem na dosažitelné výsledky tolerance 3D tisku kovů a povrchová úprava L-PBF na paměti. Na výkresech jasně specifikujte kritické tolerance a včas projednejte požadavky s dodavatelem AM. Naplánujte nezbytné kroky následného zpracování, jako je obrábění, v případech, kdy je přesnost podle konstrukce nedostatečná. Spolupráce s poskytovatelem se zkušenostmi v oblasti kontrola kvality v letectví a kosmonautice a vybavený pokročilou metrologií zajišťuje, že finální tepelný zesilovač splňuje náročné požadavky vesmírné systémy.
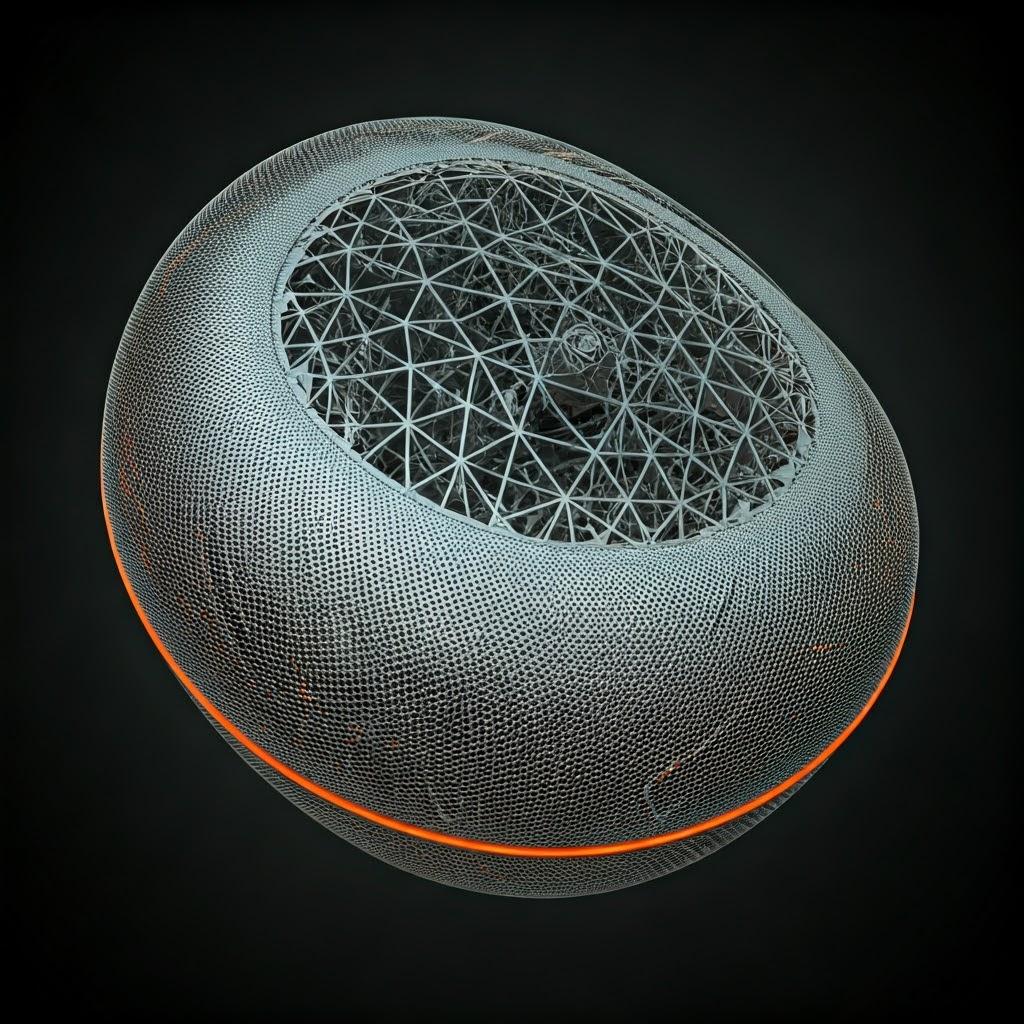
Požadavky na následné zpracování 3D tištěných tepelných komponentů
Výroba satelitního zesilovače tepelného toku pomocí aditivní výroby kovů nekončí, když díl sjede z konstrukční desky. K přeměně sestavené součásti na funkční kus hardwaru připravený k letu je obvykle zapotřebí řada nezbytných kroků následného zpracování. Tyto kroky jsou klíčové pro uvolnění vnitřních pnutí, dosažení požadovaných vlastností materiálu (včetně optimální tepelné vodivosti), odstranění dočasných podpůrných struktur, splnění rozměrových a povrchových specifikací a zajištění čistoty součásti a její připravenosti k integraci. Pochopení těchto požadavky na následné zpracování má zásadní význam pro plánování projektu, odhad nákladů a zajištění toho, aby výsledná součást splňovala přísné požadavky na vesmírné systémy.
Zde je přehled běžných kroků následného zpracování dílů AM vyrobených z AlSi10Mg a CuCrZr:
- Úleva od stresu / tepelné ošetření: Jedná se pravděpodobně o jeden z nejdůležitějších kroků, zejména u kovových dílů AM. Rychlé cykly zahřívání a ochlazování, které jsou vlastní L-PBF, vytvářejí v tištěné součásti značná zbytková napětí.
- Účel:
- Snížení zbytkového napětí: Vysoké vnitřní pnutí může způsobit deformaci během sestavování nebo po něm (zejména po vyjmutí ze sestavovací desky) a může negativně ovlivnit mechanické vlastnosti a únavovou životnost dílu. Tepelné zpracování s odlehčením od napětí tato vnitřní pnutí výrazně snižuje.
- Optimalizace mikrostruktury & Vlastnosti: U slitin, jako jsou AlSi10Mg a CuCrZr, jsou pro dosažení požadované mikrostruktury a následně optimální rovnováhy mechanických vlastností (pevnost, tažnost) a, což je důležité, nezbytné specifické cykly tepelného zpracování, tepelná vodivost. Mikrostruktura ve stavu, v jakém je postavena, je často nerovnovážná a nemusí vykazovat nejlepší tepelné vlastnosti.
- Proces: Specifická teplota, čas a atmosféra (např. vakuum, argon) pro tepelné zpracování AlSi10Mg a následné zpracování CuCrZr AM dílů závisí na slitině a cílových vlastnostech. AlSi10Mg často prochází cyklem uvolňování napětí, po němž případně následuje úprava podobná roztokům T6 a stárnutí pro zvýšení pevnosti. CuCrZr obvykle vyžaduje úpravu roztokem a následné stárnutí, aby se dosáhlo vysoké vodivosti a pevnosti díky precipitačnímu kalení.
- Úvahy: Tepelné zpracování může způsobit drobné rozměrové změny (smrštění nebo nárůst), které je třeba předvídat nebo kompenzovat, případně provést hrubé obrábění před tepelným zpracováním a konečné obrábění po něm.
- Účel:
- Vyjmutí dílu ze stavební desky: Součástka se nejprve nataví na kovovou konstrukční desku. Oddělení se obvykle provádí pomocí:
- Drátové elektroerozivní obrábění (EDM): Nabízí přesný řez s minimální silou působící na díl, ideální pro jemné struktury.
- Řezání/pásové řezání: Běžnější a rychlejší metoda pro robustní díly.
- Obrábění: Odfrézování základny dílu od desky.
- Odstranění podpůrné konstrukce: Jak bylo uvedeno v části o návrhu, často jsou nutné dočasné podpěry.
- Metody: Podpěry se často odstraňují ručně pomocí kleští, brusek nebo ručního nářadí. U složitých nebo vnitřních podpěr může být nutné CNC obrábění nebo případně elektroerozivní obrábění.
- Výzvy: To může být pracné a vyžaduje to pečlivé provedení, aby nedošlo k poškození povrchu dílu. Obtížný přístup k vnitřním podpěrám zdůrazňuje důležitost DfAM a výzvy k odstranění podpory zmírnění dopadů prostřednictvím návrhu. Místa, kde byly připevněny podpěry, mají obvykle drsnější povrch.
- Povrchová úprava: V závislosti na požadavcích aplikace lze po odstranění podpěr použít různé povrchové úpravy.
- Čištění/odprašování: Důkladné odstranění veškerého volného nebo částečně spečeného prášku, často pomocí stlačeného vzduchu, tryskání kuličkami nebo čištění ultrazvukem. To je rozhodující pro prevenci kontaminace v vesmírné systémy.
- Tryskání kuličkami / pískování: Vytváří rovnoměrnou, matnou povrchovou úpravu, odstraňuje drobné nedokonalosti a může pomoci uzavřít pórovitost v blízkosti povrchu. Různá média (skleněné kuličky, keramika, oxid hlinitý) vytvářejí různé povrchové úpravy.
- Obrábění / vibrační úprava: K vyhlazení vnějších povrchů a hran se používá brusné médium v rotujícím nebo vibrujícím bubnu. Nejvhodnější pro dávky menších, robustních dílů.
- Leštění (ruční nebo automatické): Pro dosažení velmi hladkých povrchů (nízké Ra), které jsou vyžadovány pro specifická rozhraní nebo někdy z estetických důvodů. Elektrolytické leštění může být účinné pro některé slitiny, jako je CuCrZr, a poskytuje jasný, hladký povrch.
- Obrábění: Jak je popsáno níže, používá se k dosažení hladkých a rovných povrchů na kritických místech.
- CNC obrábění: Často jsou nezbytné pro dosažení úzkých tolerancí a specifických povrchových úprav kritických prvků.
- Aplikace: Obrábění styčných ploch, rozhraní, těsnicích drážek, ložiskových otvorů, závitových otvorů nebo jakýchkoli prvků vyžadujících přesnost přesahující možnosti AM. Dosažení CNC obrábění 3D dílů přesnost je běžnou praxí.
- Úvahy: Vyžaduje pečlivou konstrukci upínacích přípravků, které udrží potenciálně složitý AM díl bez deformace. U prvků, které vyžadují obrábění, musí být součástí návrhu AM i obráběcí materiál.
- Termoregulační nátěry: Tepelné řízení družic do značné míry závisí na radiačních vlastnostech povrchu (pohltivost a emisivita). Specializované stránky tepelně regulační povlaky satelit jsou často vyžadovány aplikace.
- Účel: Přizpůsobení způsobu, jakým zesilovač tepla absorbuje sluneční záření a vyzařuje odpadní teplo do vesmíru.
- Typy: Mezi běžné povlaky patří specializované barvy (např. bílé barvy jako AZ-93, černé barvy jako Z-306), eloxování (zejména u hliníkových slitin jako AlSi10Mg, které mohou být obarveny na černo nebo ponechány čiré) nebo nanášení povlaků (např. postříbřený teflon, optické sluneční reflektory – OSR, které se však obvykle používají spíše na panely chladičů než na složité chladiče).
- Příprava povrchu: Účinnost a přilnavost těchto nátěrů závisí v rozhodující míře na správné přípravě povrchu (čištění, případně specifické profily drsnosti).
- Čištění a kontrola: Konečné čištění je pro vesmírný hardware nejdůležitější, aby splňoval přísné požadavky na odplyňování a kontrolu kontaminace.
- Postupy čištění: Může zahrnovat vícestupňové procesy s použitím specifických rozpouštědel, ultrazvukových lázní a čistých prostor podle stanovených pravidel normy pro čištění v letectví a kosmonautice.
- Závěrečná kontrola: Zahrnuje ověřování rozměrů (souřadnicový měřicí přístroj, skenování), kontrolu povrchové úpravy, vizuální kontrolu a případně NDT (např. CT skenování pro kontrolu vnitřní integrity) podle požadavků projektových specifikací.
Rozsah a pořadí těchto kroků následného zpracování závisí do značné míry na konkrétním návrhu, materiálu a požadavcích na použití. Významně se podílejí na celkových nákladech a době realizace výroby komponent AM. Proto je třeba porozumět a plánovat požadavky na následné zpracování je pro úspěšnou implementaci aditivní výroba kovů pro náročné aplikace, jako jsou satelitní zařízení pro zvýšení tepelného toku. Spolupráce s poskytovatelem komplexních služeb, jako je Met3dp, který nabízí odborné znalosti v celém pracovním procesu od prášku až po hotový díl, včetně nezbytného následného zpracování, zefektivňuje výrobní proces a zajišťuje, že komponenty splňují všechny specifikace. Můžete si prohlédnout různé tiskových metod a souvisejících důsledků následného zpracování na webových stránkách Met3dp.
Běžné problémy při 3D tisku s tepelnými zesilovači a strategie pro jejich zmírnění
Ačkoli aditivní výroba kovů nabízí významné výhody při vytváření složitých tepelných součástí družic, není tento proces bez problémů. Pochopení potenciálních problémů a zavedení účinných strategií jejich zmírnění během návrhu, simulace, tisku a následného zpracování je zásadní pro zajištění výroby vysoce kvalitních a spolehlivých dílů. Uvědomění si těchto problémů vady kovu AM a překážek pomáhá inženýrům a manažerům nákupu stanovit realistická očekávání a spolupracovat s poskytovateli služeb AM na jejich překonání.
Zde jsou uvedeny některé běžné problémy, se kterými se setkáváme při 3D tisku zesilovačů tepelného toku z AlSi10Mg a CuCrZr, spolu s přístupy k jejich zmírnění:
- Zbytkové napětí a deformace:
- Výzva: Rychlý, lokalizovaný ohřev a ochlazování, které jsou pro L-PBF typické, vytvářejí významné tepelné gradienty, což vede ke vzniku vnitřních zbytkových napětí v dílu a nosných konstrukcích. Pokud tato napětí překročí mez kluzu materiálu při zvýšených teplotách, mohou způsobit deformaci (pokřivení) během sestavování, odtržení od podpěr nebo prasknutí. K deformaci může dojít i po vyjmutí dílu z konstrukční desky, pokud nejsou napětí dostatečně odstraněna.
- Strategie zmírnění dopadů:
- Optimalizovaná orientace dílu: Orientaci dílu na konstrukční plošině tak, aby se minimalizovaly velké rovné plochy rovnoběžné se zařízením pro nanášení nátěru, omezily se převisy a řídilo se rozložení tepelné hmoty, lze zmírnit namáhání.
- Robustní podpůrné struktury: Návrh dostatečných a dobře umístěných podpěrných konstrukcí má zásadní význam pro pevné ukotvení dílu ke stavební desce a odolnost proti deformačním silám. Simulace metodou konečných prvků může pomoci optimalizovat umístění a návrh podpěr.
- Optimalizace parametrů procesu: Přesné nastavení výkonu laseru, rychlosti skenování a strategie skenování (např. šachovnicové vzory) může pomoci zvládnout tepelné gradienty. Výhodné je použití pokročilých systémů s přesným řízením procesu.
- Vytápění platformy: Předehřátí stavební platformy snižuje tepelný gradient mezi roztaveným materiálem a okolním prostředím, čímž se snižuje zbytkové napětí (častější u EBM, ale používá se i u některých systémů L-PBF).
- Povinná úleva od stresu: Provedení cyklu tepelného zpracování bezprostředně po tisku a před vyjmutí dílu z konstrukční desky je nejefektivnějším způsobem, jak zmírnění zbytkového napětí.
- Pórovitost:
- Výzva: Přítomnost malých dutin nebo pórů v tištěném materiálu může negativně ovlivnit mechanické vlastnosti (zejména únavovou pevnost) i tepelnou vodivost. Pórovitost může vzniknout v důsledku zachycení plynu (např. rozpuštěných plynů v prášku nebo stínícím plynu) nebo neúplného spojení mezi vrstvami nebo skenovacími stopami (nedostatečná pórovitost spojení).
- Strategie zmírnění dopadů:
- Vysoce kvalitní prášek: Použití vysoce čistých, sférických kovových prášků s nízkou vnitřní pórovitostí a řízenou distribucí velikosti částic, jako jsou prášky vyráběné pokročilou atomizací Met3dp, je základem pro kontrola pórovitosti 3D tisku. Nekvalitní prášek je častým zdrojem závad. Viz Met3dp’s produkt na stránce s příklady vysoce kvalitních prášků.
- Optimalizované parametry procesu: Vývoj a použití ověřených parametrů procesu (výkon laseru, rychlost, vzdálenost šrafování, tloušťka vrstvy) specifických pro daný materiál (AlSi10Mg a CuCrZr se chovají odlišně) a stroj je zásadní pro zajištění úplného roztavení a tavení.
- Kontrola inertní atmosféry: Udržování vysoce čisté atmosféry inertního plynu (např. argonu, dusíku) v konstrukční komoře minimalizuje oxidaci a zachycování plynu během tavení.
- Izostatické lisování za tepla (HIP): U kritických aplikací vyžadujících maximální hustotu (>99,9 %) lze použít následné zpracování HIP k uzavření vnitřních pórů pomocí vysokého tlaku a teploty. To však zvyšuje náklady a dobu realizace a může ovlivnit rozměry.
- NDT inspekce: CT vyšetření může nedestruktivně odhalit vnitřní pórovitost.
- Problémy s odstraněním podpůrné konstrukce:
- Výzva: Ačkoli je to nezbytné, odstranění podpůrných konstrukcí může být obtížné a časově náročné, zejména ze složitých vnitřních kanálů nebo choulostivých prvků. Nesprávné odstranění může poškodit povrch dílu nebo zanechat zbytky, které brání funkci (např. zablokování kanálků). Tyto výzvy k odstranění podpory jsou častým úzkým místem.
- Strategie zmírnění dopadů:
- DfAM pro snížení podpory: Navrhněte díly tak, aby byly co nejvíce samonosné (s použitím úhlů > 45 stupňů).
- Optimalizovaný design podpory: Používejte typy podpěr, které se snadněji odstraňují (např. tenčí kontaktní body, perforované konstrukce). Simulační nástroje mohou pomoci optimalizovat umístění podpěr z hlediska stability i odstranitelnosti.
- Plánování přístupu: Zajistěte dostatečný fyzický přístup pro nástroje, aby se během fáze návrhu dostaly k podpůrným konstrukcím. Vyhněte se vnitřním podpěrám v kanálech, pokud to není nezbytně nutné a pokud nejsou navrženy pro splachování nebo rozpouštění (u kovů vzácné).
- Odborné znalosti v oblasti následného zpracování: K pečlivému odstranění podpěry jsou zapotřebí kvalifikovaní technici s vhodným nářadím.
- Dosažení požadované tepelné vodivosti:
- Výzva: finále tepelná vodivost dílů AM může být někdy nižší než teoretické maximum pro kovanou nebo litou slitinu. To může být způsobeno faktory, jako je zbytková pórovitost, nerovnovážné mikrostruktury ve stavu po výrobě nebo nečistoty.
- Strategie zmírnění dopadů:
- Maximalizujte hustotu: Zavedení strategií pro kontrolu pórovitosti (vysoce kvalitní prášek, optimalizované parametry, případně HIP).
- Optimalizované tepelné zpracování: Pro vytvoření rovnovážné mikrostruktury, která maximalizuje tepelnou vodivost, je zejména v případě CuCrZr nezbytné použít správné odlehčení napětí a tepelné zpracování stárnutím/rozpouštěním.
- Certifikace materiálů & Testování: Získání prášku s certifikovaným chemickým složením a případné provedení testů tepelné vodivosti na vzorových kuponech vytištěných s finálními parametry dílu může ověřit výkonnost.
- Manipulace s práškem a jeho opětovné použití:
- Výzva: Kovové prášky mohou v průběhu času degradovat v důsledku manipulace a působení atmosféry (oxidace, absorpce vlhkosti). Opětovné použití nespékaného prášku z předchozích staveb je běžnou praxí, která zlepšuje ekonomiku, ale musí se provádět opatrně, aby se zachovala kvalita. Nesprávné správa prášku aditivní výroba může vést k nekonzistentní kvalitě dílů.
- Strategie zmírnění dopadů:
- Kontrolované prostředí: Prášky skladujte a manipulujte s nimi v kontrolovaném prostředí s nízkou vlhkostí.
- Prosévání a analýza: Znovu použitý prášek prosejte, abyste odstranili případné aglomeráty nebo nečistoty. Pravidelně analyzujte znovu použitý prášek (např. chemický složení, distribuce velikosti částic, tekutost), abyste zajistili, že zůstane v souladu se specifikací.
- Strategie míchání: Zavedení jasné strategie pro míchání původních a opakovaně použitých šarží prášku.
- Kvalita dodavatele: Spolehnutí se na dodavatele, jako je Met3dp, kteří udržují přísnou kontrolu kvality výroby prášku, zajišťuje vysoce kvalitní výchozí materiál.
Řešení těchto problémů vyžaduje kombinaci pečlivého návrhu, simulace procesu, vysoce kvalitních materiálů, přesné kontroly procesu během tisku, pečlivého následného zpracování a přísné kontroly kvality. Spolupráce mezi konstruktéry a zkušenými dodavateli AM je klíčem k překonání těchto potenciálních úskalí a k úspěšné výrobě robustních a spolehlivých zařízení pro zvýšení tepelného toku pro kritická zařízení tepelné řízení satelitů aplikace.
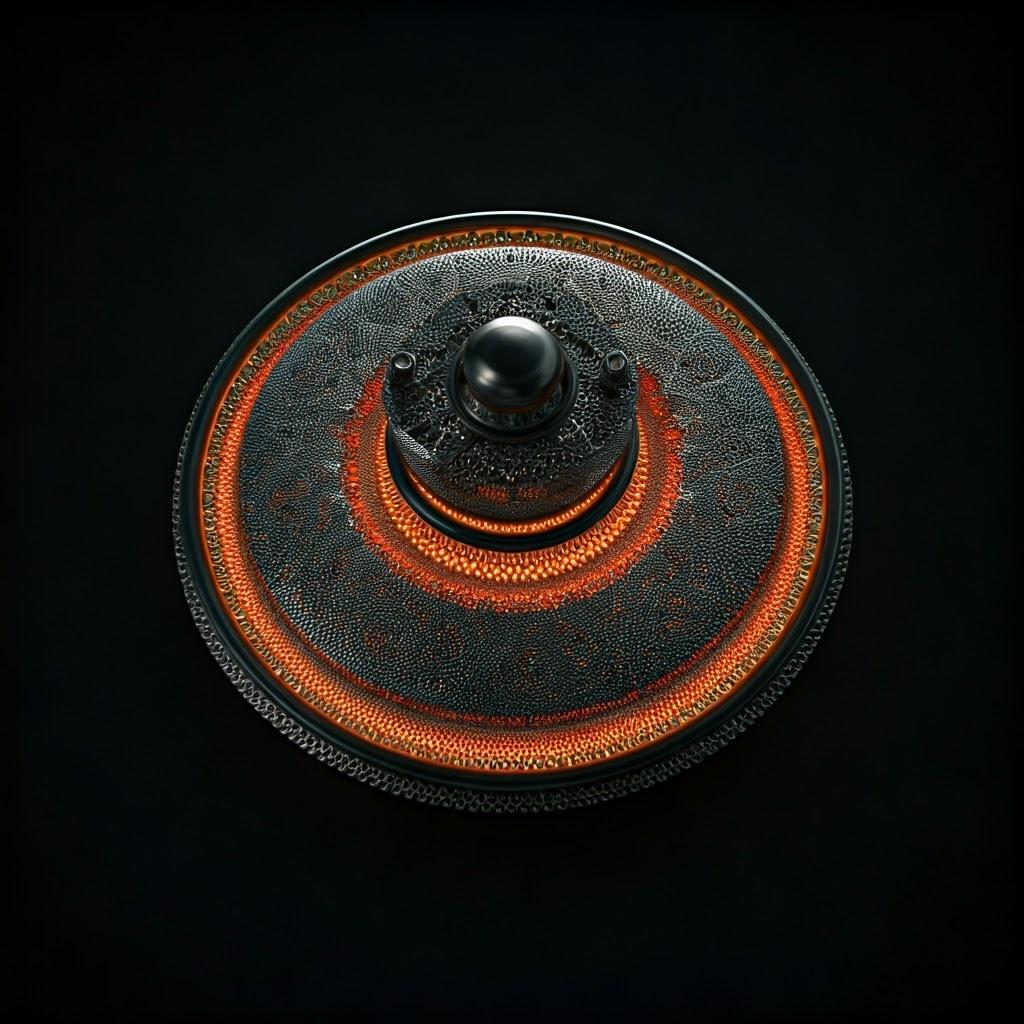
Výběr správného poskytovatele služeb 3D tisku kovů pro letecké komponenty
Výběr vhodného výrobního partnera je zásadním rozhodnutím při pořizování vysoce výkonných komponent, jako jsou satelitní zesilovače tepelného toku vyráběné aditivní výrobou kovů. Letecký a kosmický průmysl vyžaduje výjimečnou kvalitu, spolehlivost a sledovatelnost a ne všichni poskytovatelé AM služeb mají potřebné odborné znalosti, vybavení a certifikace, aby tyto přísné požadavky splnili. Manažeři nákupu a inženýrské týmy musí provést důkladnou hloubkovou kontrolu, aby identifikovali dodavatele schopného důsledně dodávat hardware připravený k letu. Správná volba zajistí přístup ke špičkovým technologiím, odborným znalostem materiálů a řízení procesů, které jsou nezbytné pro úspěch mise v náročných podmínkách vesmírné systémy.
Zde jsou klíčová kritéria, která je třeba vzít v úvahu při hodnocení potenciálu služby 3D tisku pro letecký průmysl partnery:
- Zkušenosti a certifikace v letectví a kosmonautice:
- Osvědčené výsledky: Hledejte dodavatele s prokazatelnými zkušenostmi s výrobou komponentů pro letecký a obranný průmysl. Požádejte o případové studie, reference nebo příklady podobných projektů (s výhradou dohod o důvěrnosti). Klíčové je porozumět specifickým výzvám a očekáváním kvality v tomto odvětví.
- Příslušné certifikáty: Certifikace AS9100 je mezinárodně uznávaný standard systému řízení kvality (QMS) pro letecký, kosmický a obranný průmysl. Aditivní výroba s certifikací AS9100 poskytovatelé prokazují závazek k přísné kontrole procesů, sledovatelnosti, řízení rizik a neustálému zlepšování v souladu s požadavky leteckého průmyslu. Zatímco norma ISO 9001 je dobrým základem, norma AS9100 poskytuje vyšší úroveň zabezpečení specifickou pro toto odvětví. V závislosti na požadovaných krocích následného zpracování mohou být relevantní i další certifikace související s konkrétními procesy (např. Nadcap pro tepelné zpracování nebo NDT).
- Odborné znalosti materiálů a portfolio:
- Specializace na příslušné slitiny: Ujistěte se, že dodavatel má ověřené a validované postupy pro konkrétní požadované materiály, jako jsou AlSi10Mg a CuCrZr pro tepelné aplikace. Nehledejte pouze seznam materiálů, ale ptejte se na úroveň jejich zkušeností, vyvinuté sady parametrů, typické dosažené vlastnosti (mechanické a tepelné) a znalost leteckých specifikací pro tyto slitiny.
- Kontrola kvality prášku: Informujte se o jejich protokolech pro získávání a správu prášku. Pocházejí od renomovaných dodavatelů? Jaké jsou jejich postupy pro manipulaci s práškem, skladování, testování (chemie, PSD, tekutost) a opakované použití, aby byla zajištěna konzistence a zabránilo se kontaminaci? Společnosti jako Met3dp, které vyrábějí vlastní vysoce kvalitní kovové prášky pomocí pokročilého rozprašování plynu a technologie PREP nabízejí výhodu díky vertikální integraci a přímé kontrole nad tímto kritickým vstupním materiálem. Tím je zajištěna sledovatelnost již od zdroje surovin.
- Schopnosti vývoje materiálů: Pro špičkové aplikace mohou být cennými partnery poskytovatelé se schopnostmi výzkumu a vývoje a zkušenostmi s kvalifikací nových nebo specializovaných slitin (jako jsou TiNi, TiTa, TiAl, TiNbZr, CoCrMo uvedené v portfoliu společnosti Met3dp).
- Schopnosti a technologie zařízení:
- Vhodná technologie AM: Pro kovové díly s vysokým rozlišením, jako jsou tepelné zesilovače, se běžně používá laserová fúze v práškovém loži (L-PBF). Někteří poskytovatelé mohou nabízet také tavení elektronovým svazkem (EBM), které má u některých materiálů, jako jsou slitiny titanu, výhody (menší zbytkové napětí), ale obvykle vytváří drsnější povrchy. Informujte se o konkrétních strojích, které poskytovatel provozuje (výrobce, model, stáří, stav údržby).
- Vytváření objemu a kapacity: Ujistěte se, že stroje poskytovatele’mají dostatečně velkou konstrukční plochu pro rozměry vašich součástí a dostatečnou kapacitu pro splnění požadovaných dodacích lhůt, ať už pro prototypy nebo potenciální výrobní objemy.
- Monitorování a řízení procesu: Pokročilé systémy AM zahrnují možnosti monitorování in-situ (např. monitorování bazénu taveniny, termální zobrazování). Poskytovatelé využívající tyto nástroje vykazují vyšší úroveň kontroly procesu a zajištění kvality. Ptejte se na jejich metodiky validace procesu a vývoje parametrů.
- Komplexní možnosti následného zpracování:
- Vlastní vs. partnerské služby: Jak již bylo řečeno, následné zpracování je velmi důležité. Zjistěte, které kroky (odlehčení/tepelné zpracování, odstranění podpěr, obrábění, povrchová úprava, lakování, čištění) poskytovatel provádí ve vlastní režii a které externě. Vlastní kapacity obecně nabízejí lepší kontrolu nad dodacími lhůtami, kvalitou a komunikací.
- Odbornost v požadovaných krocích: Ujistěte se, že poskytovatel (nebo jeho kvalifikovaní partneři) má specifické odborné znalosti v oblasti následného zpracování potřebného pro zvolený materiál a aplikaci (např. vakuové tepelné zpracování pro letecké slitiny, přesné CNC obrábění pro přísné tolerance, použití specifických materiálů pro obrábění, které se používají v letectví a kosmonautice) tepelně regulační povlaky satelit normy).
- Robustní systém řízení kvality (QMS) a inspekce:
- Dokumentace a sledovatelnost: Letectví a kosmonautika vyžaduje pečlivou dokumentaci. Systém řízení jakosti poskytovatele by měl zajistit úplnou sledovatelnost materiálů (šarží prášku), parametrů procesu, činností obsluhy, kroků po zpracování a výsledků kontroly každého dílu.
- Metrologické vybavení: Ověřte si, že mají k dispozici potřebné kalibrované kontrolní vybavení (souřadnicové měřicí stroje, 3D skenery, profilometry, zařízení NDT, jako jsou CT skenery, pokud je to nutné), aby bylo možné ověřit, že díly splňují všechny požadavky na rozměry, povrchovou úpravu a vnitřní integritu.
- Podávání zpráv: Porozumět úrovni podrobností uváděných ve zprávách o kvalitě a certifikátech shody.
- Technická podpora a technické znalosti:
- Konzultace DfAM: Ideální partner funguje více než jen jako tisková kancelář. Hledejte poskytovatele, kteří nabízejí konzultační služby v oblasti designu pro aditivní výrobu (DfAM). Jejich inženýři vám mohou poskytnout cennou zpětnou vazbu k vašemu návrhu a optimalizovat jej z hlediska tisknutelnosti, tepelného výkonu, nákladové efektivity a minimalizace podpory.
- Řešení problémů: Zkušení poskytovatelé mohou pomoci vyřešit problémy související s konstrukcí, výběrem materiálu nebo výrobními problémy.
- Umístění, komunikace a logistika:
- Blízkost: Blízkost sice není vždy rozhodujícím faktorem, ale může zjednodušit logistiku, usnadnit návštěvy/audity na místě a případně zkrátit dobu přepravy.
- Reakce a komunikace: Zhodnoťte reakce poskytovatele na dotazy, srozumitelnost komunikace a přístup k řízení projektu. Zásadní je silný pracovní vztah.
Proč uvažovat o Met3dp?
Společnost Met3dp se sídlem v čínském městě Čching-tao se prezentuje jako přední poskytovatel komplexních řešení aditivní výroby, což odpovídá mnoha z těchto kritických kritérií výběru. Mezi klíčové silné stránky patří:
- Integrovaná řešení: Nabídka obou špičkový objem, přesnost a spolehlivost tisku v jejich 3D tisk z kovu zařízení (včetně tiskáren SEBM) a vysoce výkonných tiskáren Met3dp kovové prášky.
- Pokročilá výroba prášků: Využití nejmodernějších technologií plynové atomizace a PREP zajišťuje vysoce kvalitní sférické prášky, které jsou klíčové pro náročné aplikace.
- Portfolio materiálů: Odborné znalosti v celé řadě materiálů včetně standardních leteckých slitin a inovativních složení.
- Desítky let zkušeností: Společné zkušenosti v oblasti AM kovů poskytují silný základ pro technickou podporu a vývoj aplikací.
- Závazek ke kvalitě: Důraz na přesnost, spolehlivost a umožnění výroby kritických dílů pro průmyslová odvětví, jako je letectví a kosmonautika.
Pečlivým vyhodnocením potenciálních dodavatelů podle těchto kritérií, zaměřením se na potřeby specifické pro letecký průmysl a zohledněním integrovaných schopností nabízených společnostmi, jako je Met3dp, mohou organizace s jistotou vybrat hodnocení dodavatelů AM kovů partnera schopného dodávat vysoce kvalitní a spolehlivé zesilovače tepelného toku družic, které přispívají k celkovému úspěchu mise.
Nákladové faktory a doba realizace 3D tištěných satelitních tepelných zesilovačů
Aditivní výroba kovů umožňuje vytvářet vysoce optimalizované a složité satelitní komponenty, ale pro efektivní plánování projektů, sestavování rozpočtů a zadávání zakázek je nezbytné pochopit související strukturu nákladů a typické doby realizace. Jak náklady na 3D tisk kovů a doba realizace se mohou výrazně lišit od tradičních výrobních metod a jsou ovlivněny mnoha faktory specifickými pro proces AM a samotnou součást. Klíčem k řízení očekávání je sdělit jasné požadavky a získat podrobné nabídky od kvalifikovaných dodavatelů.
Klíčové faktory nákladů na satelitní zesilovače tepla AM:
- Objem a složitost části:
- Spotřeba materiálu: Samotný objem dílu přímo ovlivňuje množství spotřebovaného drahého, vysoce kvalitního kovového prášku (např. AlSi10Mg, CuCrZr). To je často hlavním faktorem ovlivňujícím náklady.
- Geometrická složitost: Ačkoli AM vyniká složitostí, velmi složité konstrukce s jemnými prvky, tenkými stěnami nebo rozsáhlými vnitřními kanály mohou prodloužit dobu tisku a potenciálně vést k vyšší míře poruch během tisku nebo následného zpracování, což má vliv na náklady. Konstrukce vyžadující rozsáhlé podpůrné struktury rovněž zvyšují spotřebu materiálu a dobu tisku.
- Čas sestavení (strojový čas):
- Výška dílu (Z-výška): Vzhledem k tomu, že AM vytváří vrstvu po vrstvě, je výška dílu v orientaci sestavení hlavním faktorem určujícím celkovou dobu tisku. Vyšší díly se tisknou déle.
- Část Objem & Hustota: Objemově větší díly vyžadují více skenování laserovým/elektronovým paprskem na vrstvu.
- Počet dílů na sestavení: Náklady na strojní čas lze amortizovat, pokud lze více dílů (vašich nebo jiných zákazníků’) efektivně vnořit na jednu konstrukční platformu. Tisk na vyžádání pro jednotlivé složité prototypy bude mít vyšší náklady na strojní čas na díl ve srovnání s malou sérií.
- Tloušťka vrstvy: Tenčí vrstvy zlepšují kvalitu povrchu, ale výrazně prodlužují počet vrstev, a tím i dobu výroby.
- Typ materiálu:
- Náklady na prášek: Náklady na práškové suroviny se u jednotlivých slitin výrazně liší. Prášky pro letectví a kosmonautiku, jako je CuCrZr nebo specializované titanové slitiny, jsou obecně dražší než běžnější AlSi10Mg nebo nerezové oceli kvůli nákladům na suroviny a složitosti zpracování. Kvalita (sféricita, čistota, kontrola PSD) požadovaná pro letecké a kosmické aplikace si rovněž žádá vyšší cenu.
- Obtížnost zpracování: Některé materiály (např. vysoce reflexní slitiny mědi) je náročnější spolehlivě zpracovat pomocí L-PBF, což může vyžadovat specializované vybavení nebo parametry, které mohou ovlivnit náklady.
- Požadavky na podpůrnou strukturu:
- Objem: Podpory spotřebovávají materiál a zvyšují celkový objem tisku, čímž prodlužují dobu tisku.
- Úsilí o odstranění: Složité nebo obtížně přístupné podpěry výrazně zvyšují pracnost a náklady spojené s následným zpracováním. Návrhy optimalizované pro minimalizaci podpěr (DfAM) mohou přinést značné úspory nákladů.
- Intenzita následného zpracování:
- Tepelné zpracování: Potřebné cykly (odlehčování, stárnutí atd.) prodlužují čas, využívají specializované zařízení (vakuové pece) a spotřebovávají energii.
- Obrábění: Rozsah CNC obrábění potřebného pro tolerance nebo prvky významně ovlivňuje náklady (čas stroje, nástroje, programování, nastavení).
- Povrchová úprava: Kroky, jako je tryskání, leštění nebo nanášení povlaku, zvyšují náklady na pracovní sílu a potenciálně i na specializované zpracování.
- Čištění & amp; Kontrola: Rigorózní kontrola kvality v letectví a kosmonautice požadavky, včetně detailní kontroly (CMM, NDT) a dokumentace, výrazně zvyšují konečné náklady ve srovnání s méně kritickými průmyslovými díly.
- Požadavky na kvalitu a kvalifikaci:
- Testování: Destruktivní zkoušení zkušebních kuponů (na mechanické nebo tepelné vlastnosti) nebo rozsáhlé nedestruktivní zkoušení konečného dílu zvyšuje náklady.
- Dokumentace: Vytvoření komplexních balíčků dokumentace sledovatelnosti a kvality, které jsou vyžadovány pro letový hardware, vyžaduje čas a zdroje.
- Kvalifikace procesu: Pokud je pro novou součást nebo dodavatele vyžadována specifická kvalifikace procesu nebo validace, je třeba tyto počáteční náklady zohlednit.
- Objem objednávky (množství):
- Úspory z rozsahu: Ačkoli se AM často propaguje pro malosériovou výrobu, určité úspory z rozsahu se stále uplatňují. Náklady na zřízení (příprava konstrukce, programování) lze amortizovat ve větších sériích. Optimalizované vnořování na konstrukčních deskách se stává efektivnějším. Snížení nákladů na jeden díl je však obecně méně dramatické než u tradičních technik hromadné výroby, jako je odlévání nebo vstřikování.
Porozumění modelům kótování:
Poskytovatelé mohou používat různé modely pro ceny aditivní výroby:
- Náklady na jeden díl: Pevná cena za každou úspěšně vyrobenou a zkontrolovanou součást.
- Náklady na sestavení: Cena za obsazení stavební plošiny bez ohledu na úspěch a následné zpracování. Běžnější v prostředí výzkumu a vývoje.
- Čas a materiál: Účtování podle skutečně spotřebovaného času stroje a materiálu. Méně obvyklé pro výrobní díly.
Je velmi důležité získat podrobné nabídky, ve kterých bude uvedeno, co je zahrnuto (materiál, tisk, standardní následné zpracování, kontrola) a co může být navíc (složité obrábění, specializované povlaky, rozsáhlé NDT, kvalifikační úsilí). Vyžádejte si Nabídka 3D tisku B2B od kvalifikovaných dodavatelů, jako je Met3dp, a poskytnutí jasného 3D modelu a technického výkresu se všemi požadavky je nejlepší způsob, jak získat přesnou cenu.
Faktory doby realizace:
Doba dodání satelitního hardwaru pro komponenty AM ovlivňují:
- Složitost návrhu: Tisk a následné zpracování složitých dílů trvá déle.
- Tisková fronta: Dostupnost a počet nevyřízených zakázek poskytovatele služeb. Za urgentní objednávky mohou být účtovány poplatky za urychlení.
- Doba výstavby: Jak již bylo řečeno, řídí se především výškou a objemem dílů. Může se pohybovat od hodin až po několik dní nebo dokonce týdnů u velmi velkých/komplexních konstrukcí.
- Kroky následného zpracování: Každý krok (tepelné zpracování, obrábění, dokončovací práce, kontrola) je časově náročný. Cykly tepelného zpracování mohou trvat hodiny až dny, složité obrábění může trvat dny. Úzkým místem může být odstranění podpory.
- Testování a kvalifikace: Pokud je třeba provést rozsáhlé testování nebo kvalifikaci, je to časově náročné.
- Doprava: Logistická doba potřebná k dopravě dílu od dodavatele do vašeho zařízení.
Typické dodací lhůty:
- Prototypy: Jednoduché prototypy mohou být dodány za 1-3 týdny.
- Složité prototypy/malý objem: Díly, které vyžadují rozsáhlé následné zpracování nebo jsou vyrobeny z náročných materiálů, mohou trvat 4-8 týdnů nebo déle.
- Výrobní díly: Závisí do značné míry na objemu, složitosti a požadované kvalifikaci/dokumentaci, což se může protáhnout až na několik měsíců u počátečních výrobních sérií vyžadujících stabilizaci procesu a úplnou kvalifikaci.
Nákladová efektivita vs. tradiční metody:
AM je v porovnání s tradičními metodami (jako je CNC obrábění z polotovaru) nákladově nejefektivnější ve scénářích, které zahrnují:
- Vysoká geometrická složitost: Tam, kde by obrábění bylo velmi obtížné nebo nemožné.
- Výroba v malém až středním objemu: Pokud jsou náklady na nástroje pro odlévání/lisování neúnosné.
- Konsolidace částí: Úspory při montáži a vyšší spolehlivost kompenzují vyšší náklady na jeden díl AM.
- Odlehčení: Pokud hodnota úspory hmotnosti (zejména snížení nákladů na start) převáží nad příplatkem za výrobní náklady.
- Rychlé prototypování: Tam, kde je rychlost nejdůležitější.
Pro jednoduché geometrie vyráběné ve velkých objemech jsou tradiční metody často ekonomičtější. U složitých a optimalizovaných konstrukcí potřebných pro pokročilé zesilovače tepelného toku družic však AM často nabízí nejlepší kombinaci výkonu, doby realizace a celkové hodnoty, zejména při zohlednění celkového životního cyklu a dopadu na misi.
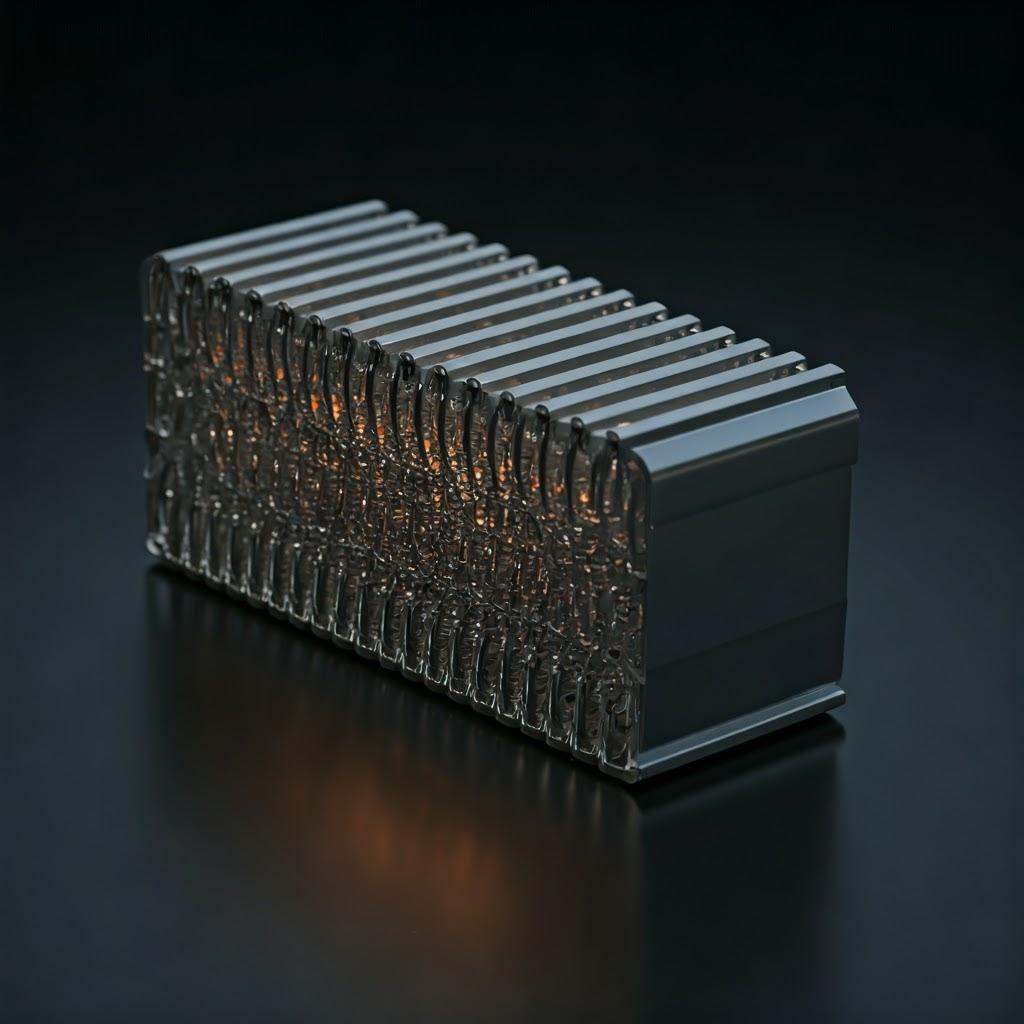
Často kladené otázky (FAQ)
Zde jsou odpovědi na některé časté otázky týkající se 3D tištěných satelitních zesilovačů tepelného toku s použitím AlSi10Mg a CuCrZr:
Otázka 1: Jaká je typická tepelná vodivost dosažitelná pro 3D tisk AlSi10Mg a CuCrZr?
- A1: Dosažitelná tepelná vodivost do značné míry závisí na slitině, parametrech tiskového procesu, výsledné hustotě dílu a především na tepelném zpracování po tisku.
- AlSi10Mg: Ve stavu, v jakém se nachází, může být tepelná vodivost relativně nízká (např. 90-110 W/m-K). Po vhodném odlehčení napětí a případném tepelném zpracování podobném T6 (optimalizovaném pro tepelné vlastnosti, které se mohou mírně lišit od zpracování optimalizovaného pouze pro pevnost) se tepelná vodivost obvykle výrazně zvýší a dosáhne hodnot v rozmezí od 100-130 W/m-K, někdy i vyšší v závislosti na konkrétním procesu a ošetření. Rozhodující je dosažení >99,5% hustoty.
- CuCrZr: Tato slitina se opírá o precipitační kalení prostřednictvím tepelného zpracování (rozpuštění a stárnutí), aby bylo dosaženo vysoké pevnosti a vysoké vodivosti. V základním stavu je vodivost nižší. Po optimalizovaném tepelném zpracování lze u CuCrZr vytištěného pomocí L-PBF dosáhnout vynikající tepelné vodivosti, obvykle v rozsahu 300-320 W/m-Ka blíží se hodnotám blízkým tvářené slitině C18150. Opět je rozhodující dosažení téměř plné hustoty a použití správného tepelného zpracování ověřeného pro proces AM. Je nezbytné prodiskutovat cílové požadavky na tepelnou vodivost s dodavatelem AM, protože by měl mít k dispozici údaje založené na svých validovaných procesech a tepelném zpracování pro tyto specifické procesy kovové prášky pro letectví a kosmonautiku.
Otázka 2: Jaká je hmotnost 3D tištěných tepelných posilovačů ve srovnání s tradičně vyráběnými?
- A2: 3D tisk kovů nabízí významný potenciál pro odlehčování v letectví a kosmonautice složek, včetně tepelných posilovačů, ve srovnání s tradičními metodami, a to především dvěma mechanismy:
- Optimalizace topologie a složité geometrie: AM umožňuje vytvářet vysoce optimalizované tvary (jako jsou mřížkové struktury nebo topologicky optimalizované konstrukce), které umisťují materiál pouze tam, kde je to potřeba pro podporu konstrukce nebo tepelnou funkci. To může výrazně snížit objem a hmotnost v porovnání s odvozením výroby z pevného bloku nebo sestavením jednodušších tvarů. Chladič navržený podle principů DfAM může mít často stejný nebo lepší tepelný výkon a zároveň být o 20-50 % lehčí (v některých případech i více) než tradičně navržený a vyrobený protějšek.
- Konsolidace částí: Díky integraci více funkcí (např. konstrukce, tepelné cesty, montáže) do jediného tištěného dílu eliminuje AM potřebu spojovacích prvků, držáků a materiálů rozhraní, což dále snižuje celkovou hmotnost sestavy.
- Výběr materiálu: CuCrZr je sice hustý, ale schopnost vytvářet vysoce účinné a složité struktury znamená, že ve srovnání s jednoduššími a objemnějšími měděnými součástmi vyrobenými tradičním způsobem může být zapotřebí menší objem materiálu. Při použití AlSi10Mg může přirozená nízká hustota v kombinaci s optimalizací topologie vést k extrémně lehkým tepelným řešením. Proto jsou 3D tištěné tepelné zesilovače často výrazně lehčí než tradičně vyráběné ekvivalenty nabízející podobný tepelný výkon.
Otázka 3: Jsou kovové díly vytištěné 3D tiskem vhodné do vakua a radiačního prostředí ve vesmíru?
- A3: Ano, kovové součásti vyrobené aditivní výrobou ze slitin jako AlSi10Mg a CuCrZr jsou obecně vhodné pro kosmické prostředí, pokud jsou řádně zpracovány a vyčištěny.
- Kompatibilita s vakuem: Kovy mají ze své podstaty velmi nízký tlak par a při správném čištění za účelem odstranění organických zbytků a kontaminantů vykazují nízkou míru odplyňování, která je slučitelná s požadavky na vesmírné vakuum (obvykle definované normami jako NASA-STD-6016 nebo ECSS-Q-ST-70-02C). Zajištění vysoké hustoty (>99,5 %) minimalizuje virtuální úniky z vnitřní pórovitosti. Zásadní význam mají důkladné postupy čištění po zpracování.
- Odolnost proti záření: Kovové slitiny jsou obecně odolné vůči typům a úrovním záření, které se vyskytují na většině oběžných drah Země (protony, elektrony, gama záření). Na rozdíl od polymerů nebo některých elektronických součástek nejsou strukturní a tepelné vlastnosti slitin AlSi10Mg a CuCrZr výrazně zhoršeny typickými dávkami kosmického záření během běžné životnosti mise. Stínicí účinky samotného kovu rovněž poskytují určitou ochranu vnitřním součástem.
- Tepelné cyklování: Velké výkyvy teplot ve vesmíru vyžadují materiály se stabilními vlastnostmi v celém provozním rozsahu a odolností proti tepelné únavě. Zatímco zbytkové napětí z AM vyžaduje pečlivé řízení (prostřednictvím tepelného zpracování), základní kovy samy o sobě dobře zvládají tepelné cykly. Důležitým faktorem při návrhu je soulad koeficientu tepelné roztažnosti (CTE) se styčnými součástmi.
Otázka 4: Jaké certifikáty kvality bych měl hledat u dodavatele leteckých dílů?
- A4: Při výběru hodnocení dodavatelů AM kovů partnerem pro kritické letecké komponenty, specifické certifikace kvality poskytují záruku robustních procesů a kontrol:
- AS9100: Jedná se o zlatý standard QMS pro letecký průmysl. Certifikace podle AS9100 znamená, že dodavatel zavedl přísné kontroly pro řízení konfigurace, sledovatelnost, řízení rizik, validaci procesů a prevenci vad specifických pro požadavky leteckého průmyslu. Pro letecký hardware je vysoce doporučován.
- ISO 9001: Obecná certifikace QMS, která tvoří základ pro AS9100. Je sice dobrá, ale postrádá specifické zaměření na letecký průmysl jako AS9100.
- Nadcap: Zatímco AS9100 se vztahuje na celý systém, Nadcap poskytuje akreditaci pro konkrétní speciální procesy. Pokud vaše součást vyžaduje kritické následné zpracování, jako je tepelné zpracování, svařování nebo nedestruktivní testování prováděné poskytovatelem AM nebo jeho subdodavateli, vyhledejte příslušné akreditace Nadcap pro tyto specifické procesy.
- Registrace ITAR (pokud je to relevantní): U projektů souvisejících s obranou, které podléhají americkým předpisům o mezinárodním obchodu se zbraněmi, se ujistěte, že je poskytovatel registrován a splňuje požadavky ITAR.
- Specifická schválení zákazníků: Významní výrobci OEM v leteckém průmyslu mají často vlastní postupy a požadavky na schvalování dodavatelů, které mohou jít nad rámec standardních certifikací.
Otázka 5: Zvládne Met3dp výrobu prototypů i sériovou výrobu těchto komponent?
- A5: Na základě uvedených schopností společnosti Met3dp se zdá, že je schopna podporovat obě fáze. Zdůrazňují:
- Špičkový objem, přesnost a spolehlivost tisku: Navrhuje zařízení vhodné pro opakovatelnou výrobu.
- Komplexní řešení: Tiskárny, pokročilé kovové prášky a vývoj aplikací zahrnují podporu v celém životním cyklu výrobku od konceptu až po výrobu.
- Partnerský přístup: Ochota spolupracovat s organizacemi při zavádění 3D tisku a urychlení transformace digitální výroby naznačuje připravenost na trvalé výrobní vztahy.
- Odborné znalosti: Desítky let společných zkušeností jim umožňují podporovat počáteční DfAM pro prototypy až po optimalizaci procesů pro výrobu ve velkém měřítku. Ačkoli konkrétní údaje o kapacitě by vyžadovaly přímý dotaz, jejich zaměření na průmyslové aplikace v leteckém, zdravotnickém a automobilovém průmyslu naznačuje, že jsou vybaveni pro zvládnutí požadavků na kvalitu a potenciálně i objemů potřebných pro sériovou výrobu kritických komponentů, které přesahují rámec jednorázových prototypů. Projednání konkrétních požadavků na objem a plánů výroby přímo s Met3dp by objasnilo jejich kapacitu a možnosti škálování pro váš projekt.
Závěr: Zlepšení úspěchu vesmírných misí pomocí pokročilé aditivní výroby
Neustálá snaha o vyšší výkon, vyšší účinnost a vyšší spolehlivost satelitní technologie vyžaduje neustálé inovace v každém aspektu konstrukce kosmických lodí, zejména v kritických oblastech, jako je tepelný management. Jak jsme již prozkoumali, aditivní výroba kovů představuje změnu paradigmatu a nabízí bezprecedentní možnosti řešení složitých problémů s odváděním tepla v drsném prostředí vesmíru. Využitím konstrukční svobody, která je vlastní AM, mohou inženýři vytvářet 3D tištěné struktury pro redistribuci tepla s použitím pokročilých materiálů, jako je AlSi10Mg a CuCrZr, které překonávají běžně vyráběné komponenty z hlediska tepelné účinnosti, hmotnosti a integrace.
Schopnost vyrábět vysoce komplexní vnitřní kanály, topologicky optimalizované geometrie, konformní povrchy a integrované multifunkční komponenty umožňuje významně vylepšit tepelná regulace satelitů. To se přímo promítá do hmatatelných výhod: elektronické komponenty mohou spolehlivě pracovat při vyšších výkonech, citlivé přístroje si udržují stabilní provozní teplotu a celkovou hmotnost družic lze snížit, což uvolní kapacitu pro větší užitečné zatížení nebo umožní vypouštění na menších a levnějších nosičích. Výhody přesahují výkonnost; AM usnadňuje část konsolidace satelit konstrukce, čímž se snižuje složitost montáže a potenciální poruchovost a zároveň se rychlé prototypování vesmírného hardwaru zrychlují vývojové cykly a umožňují rychlejší iteraci a ověřování nových tepelných řešení.
Materiály jako lehký AlSi10Mg poskytují vynikající tepelný výkon tam, kde je nejdůležitější hmotnost, zatímco vysoce vodivá CuCrZr řeší extrémní tepelné toky. Klíč k využití plného potenciálu těchto materiálů spočívá ve využití vysoce kvalitních, speciálně navržených materiálů kovové prášky pro letectví a kosmonautiku a partnerství s odbornými poskytovateli AM, kteří mají ověřené procesy, přísnou kontrolu kvality a komplexní možnosti následného zpracování. Z Tepelný management DfAM konzultace, přes pečlivou kontrolu a dokončovací práce, celý výrobní řetězec musí být přizpůsoben náročným normám leteckého průmyslu.
Výběr správného výrobního partnera, který má prokazatelné zkušenosti v leteckém průmyslu, příslušné certifikace, jako je AS9100, hluboké znalosti materiálů a pokročilé technologické schopnosti, má zásadní význam. Společnosti jako Met3dp, které nabízejí komplexní řešení od pokročilý systém výroby prášku technologie poskytující vynikající Met3dp kovové prášky k nejmodernějším tiskovým zařízením a odborným znalostem v oblasti aplikací, umožňují budoucnost tepelného managementu satelitů. Jejich závazek k přesnosti, spolehlivosti a partnerství pomáhá organizacím zvládnout složitost zavádění AM pro kritické aplikace.
Závěrem lze říci, že AM kovů již není jen nástrojem pro výrobu prototypů, ale vyspělou výrobní technologií, která je hnací silou aditivní výroba inovace v letectví a kosmonautice. U satelitních zařízení pro zvýšení tepelného toku a redistribučních struktur nabízí přesvědčivou hodnotu, protože umožňuje lehčí, účinnější a spolehlivější řešení tepelného managementu, která přímo přispívají k lepšímu využití tepla úspěch vesmírné mise. Vzhledem k tomu, že se tato technologie dále vyvíjí, její úloha v umožnění nové generace vesmírné systémy bude jen růst. Doporučujeme inženýrům a manažerům veřejných zakázek, kteří čelí tepelným výzvám při navrhování družic, aby prozkoumali možnosti, které nabízí aditivní výroba kovů, a navázali spolupráci se znalými partnery, aby se inovativní koncepty proměnily v realitu připravenou k letu. Navštivte Domovská stránka Met3dp a dozvíte se více o jejich komplexních řešeních a o tom, jak mohou podpořit cíle vaší organizace v oblasti aditivní výroby.
Sdílet na
MET3DP Technology Co., LTD je předním poskytovatelem řešení aditivní výroby se sídlem v Qingdao v Číně. Naše společnost se specializuje na zařízení pro 3D tisk a vysoce výkonné kovové prášky pro průmyslové aplikace.
Dotaz k získání nejlepší ceny a přizpůsobeného řešení pro vaše podnikání!
Související články
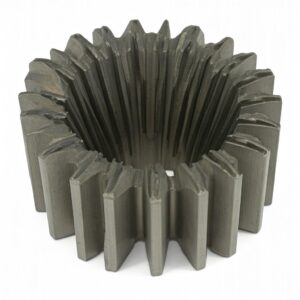
Vysoce výkonné segmenty lopatek trysek: Revoluce v účinnosti turbín díky 3D tisku z kovu
Přečtěte si více "O Met3DP
Nedávná aktualizace
Náš produkt
KONTAKTUJTE NÁS
Nějaké otázky? Pošlete nám zprávu hned teď! Po obdržení vaší zprávy obsloužíme vaši žádost s celým týmem.
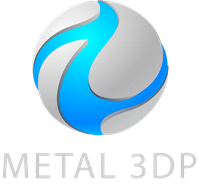
Kovové prášky pro 3D tisk a aditivní výrobu