Prášek z nástrojové oceli
Obsah
Představte si svět, kde by výroba dokonalého řezného nástroje nebyla omezena tradičními výrobními metodami. Svět, kde lze dosáhnout složitých geometrií a vynikajících vlastností s nesrovnatelnou přesností. Vstupte do fascinující říše prášková nástrojová ocel, revoluční materiál, který mění způsob, jakým navrhujeme a vyrábíme průmyslové řezné nástroje.
Přehled práškové nástrojové oceli
Prášek nástrojové oceli, jak název napovídá, je kovový prášek speciálně vyvinutý pro vytváření vysoce výkonných řezných nástrojů. Na rozdíl od konvenční tvářené nástrojové oceli, která se vyrábí odléváním nebo kováním, využívá prášková nástrojová ocel pečlivý proces známý jako výroba aditiv kovů (MAM) nebo vstřikování kovů (MIM). Tyto techniky zahrnují pečlivé vrstvení jemných částic prášku z nástrojové oceli za účelem vytvoření téměř čistého tvaru, který nabízí výrobcům nástrojů poklad výhod.
Kompoziční chemie Prášek z nástrojové oceli
Složení prášku nástrojové oceli se mění v závislosti na požadovaných vlastnostech hotového nástroje. Některé základní prvky však trvale hrají hlavní roli:
- Železo (Fe): Základ materiálu, poskytující základní strukturu pro nástroj.
- Uhlík (C): Klíčová složka pro tvrdost a odolnost proti opotřebení. Čím vyšší je obsah uhlíku, tím je nástroj tvrdší a odolnější proti opotřebení, ale také méně tažný (flexibilní).
- Legující prvky: Koktejl prvků, jako je chrom (Cr), molybden (Mo), vanad (V), wolfram (W) a nikl (Ni), se strategicky přidává ke zlepšení specifických vlastností. Chrom zvyšuje prokalitelnost, zatímco molybden a vanad zlepšují tvrdost za tepla, což je klíčové pro vysokoteplotní aplikace. Wolfram dále zvyšuje odolnost proti opotřebení a nikl zjemňuje strukturu zrna a zlepšuje houževnatost.
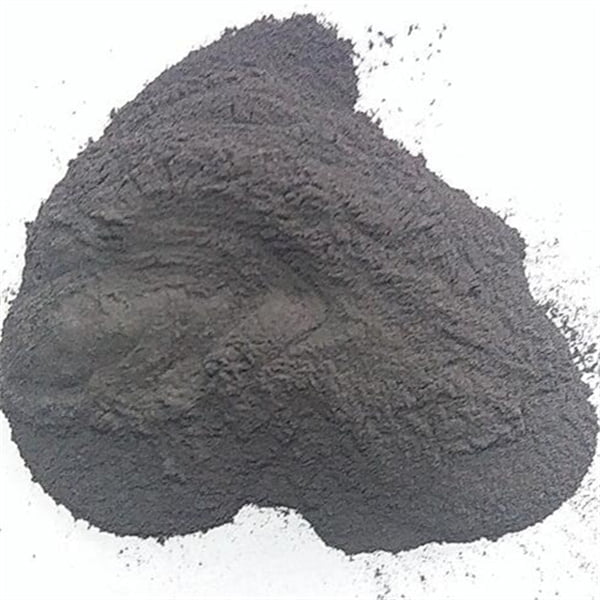
Vlastnosti Prášek z nástrojové oceli
Díky manipulaci se složením a výrobním procesem nabízí prášek nástrojové oceli rozmanité spektrum vlastností:
Vlastnictví | Popis |
---|---|
Tvrdost | Odolnost proti trvalému promáčknutí. Rozhodující pro nástroje, které potřebují řezat houževnaté materiály. |
Odolnost proti opotřebení | Schopnost odolat abrazivnímu opotřebení při dlouhodobém používání. Nezbytné pro nástroje s vysokým třením. |
Houževnatost | Odolnost proti zlomení při nárazu nebo namáhání. Důležité pro nástroje, které jsou vystaveny rázovému zatížení. |
Tvrdost za tepla | Zachovává tvrdost při zvýšených teplotách. Nezbytné pro řezné nástroje používané v aplikacích opracování za tepla. |
Obrobitelnost | Snadnost, s jakou lze materiál tvarovat po počátečním tvářecím procesu. Umožňuje konečné úpravy a přizpůsobení. |
Aplikace práškové nástrojové oceli
Všestrannost práškové nástrojové oceli se promítá do široké škály aplikací v mnoha průmyslových odvětvích:
Průmysl | Příklady použití |
---|---|
Obrábění kovů | Řezné nástroje pro soustružení, frézování, vrtání, závitování a řezání závitů. Zápustky, razidla a formy pro procesy tváření kovů. |
Plasty | Formy a jádra pro vstřikování a vytlačování plastových dílů. |
Dřevoobrábění | Řezné nástroje pro pily, frézky a hoblíky. |
Automobilový průmysl | Zápustky a formy pro součásti motorů, ozubená kola a další automobilové díly. |
Aerospace | Vysoce výkonné řezné nástroje pro obrábění leteckých součástí. |
Lékařský | Chirurgické nástroje a implantáty vyžadující složité geometrie a biokompatibilní vlastnosti. |
Oblíbené stránky Prášek z nástrojové oceli Modely
S rostoucí poptávkou po práškové nástrojové oceli vyvinulo několik předních výrobců řadu inovativních receptur. Zde je letmý pohled na deset oblíbených modelů se zdůrazněním jejich klíčových vlastností:
- Astaloy ČR (Höganäs): Všestranný prášek z nízkolegované oceli nabízející dobrou rovnováhu mezi tvrdostí, odolností proti opotřebení a houževnatostí. Dobře se hodí pro širokou škálu obráběcích aplikací.
- AM301 (Carpenter Additive Powder Products): Vysoce výkonný prášek z molybdenem legované oceli speciálně navržený pro vynikající tvrdost za tepla a odolnost proti opotřebení. Ideální pro řezné nástroje používané v horkém pracovním prostředí.
- D2 (Latrobe Steel Company): Prášek z oceli s vysokým obsahem uhlíku a chromu známý pro svou výjimečnou odolnost proti opotřebení a rozměrovou stabilitu. Ideální pro nástroje, které potřebují udržovat ostré hrany při intenzivním používání.
- H13 (Höganäs): Prášek z chrom-molybdenové oceli nabízející dobrou kombinaci houževnatosti a odolnosti proti opotřebení. Oblíbená volba pro aplikace nástrojů pro práci za studena, jako jsou lisovací raznice.
- Invar 1,2712 (Höganäs): Prášek z nikl-chromové oceli s velmi nízkým koeficientem tepelné roztažnosti. Neocenitelné pro nástroje, které vyžadují minimální rozměrovou změnu s kolísáním teploty.
- M2 (AMETEK SMP): Klasický prášek z rychlořezné oceli obsahující wolfram, molybden a vanad. Proslulý svou tvrdostí za tepla a schopností zvládnout vysoké řezné rychlosti
- Nitrokarburizační stupeň (AMETEK SMP): Tato specializovaná prášková nástrojová ocel prochází povýrobní úpravou zvanou nitrokarburizace, která difunduje dusík a uhlík do povrchové vrstvy. Výsledkem je zvýšená tvrdost povrchu, zlepšená odolnost proti opotřebení a vynikající tribologické vlastnosti (tření a mazání).
- Osprey® 420 (Höganäs): Tato jedinečná prášková nástrojová ocel se může pochlubit strukturou infiltrovanou mědí. Měď působí jako mazivo, snižuje tření a tvorbu tepla při řezání. To se promítá do prodloužené životnosti nástroje a zlepšené kvality povrchu obráběných dílů.
- Sanmac 420 (AP&C Powder Metallurgy): Další inovace, Sanmac 420 je předlegovaná nástrojová ocel v prášku obsahující molybden a kobalt. Tato kombinace nabízí výjimečnou houževnatost a odolnost proti opotřebení, což z ní činí silného kandidáta pro náročné obráběcí aplikace.
- Vanadis 4 (Höganäs): Tato prémiová prášková nástrojová ocel zvedá laťku tím, že obsahuje částice karbidu vanadu. Tyto mikroskopické inkluze výrazně zvyšují odolnost proti opotřebení, díky čemuž je Vanadis 4 ideální pro vysoce výkonné řezné nástroje používané v náročných prostředích.
Srovnávací analýza
I když každá prášková nástrojová ocel nabízí odlišné výhody, výběr té správné závisí na konkrétní aplikaci a požadovaných vlastnostech. Zde je rozpis některých klíčových parametrů, které je třeba vzít v úvahu:
Parametr | Popis | Příklady úvah |
---|---|---|
Tvrdost | Vyšší tvrdost znamená lepší odolnost proti opotřebení při řezání houževnatých materiálů. Příliš tvrdé nástroje však mohou být křehké a náchylné k vylamování. | Pro obrábění titanových slitin může být výhodnější velmi tvrdý prášek nástrojové oceli, jako je D2. |
Houževnatost | Rozhodující pro nástroje, které jsou vystaveny rázovému zatížení nebo vyžadují určitou flexibilitu. Příliš velká křehkost může vést ke zlomení nástroje. | Pro lisovací lis pro tváření za studena by byl přínosem prášek nástrojové oceli s dobrou houževnatostí, jako je H13, aby zvládl dopad lisovacích operací. |
Odolnost proti opotřebení | Nezbytné pro nástroje, které budou široce používány. Zvažte abrazivitu řezaného materiálu a předpokládanou dobu řezání. | Pro obrábění vysoce abrazivních materiálů by byla vhodná rychlořezná ocel jako M2 nebo nitrokarbonizovaná třída. |
Tvrdost za tepla | Stává se kritickým pro nástroje používané při obrábění za tepla nebo pro nástroje, které při řezání generují značné teplo. | Při obrábění dílů při zvýšených teplotách by byla preferovanou volbou prášková nástrojová ocel jako AM301 s vynikající tvrdostí za tepla. |
Obrobitelnost | Vyžaduje-li nástroj povýrobní tvarování nebo vrtání kanálů chladicí kapaliny, je nezbytná dobrá obrobitelnost. | Snazší obrobitelnost může ušetřit čas a prostředky při výrobě nástrojů. Astaloy CR nabízí dobrou rovnováhu mezi tvrdostí a obrobitelností. |
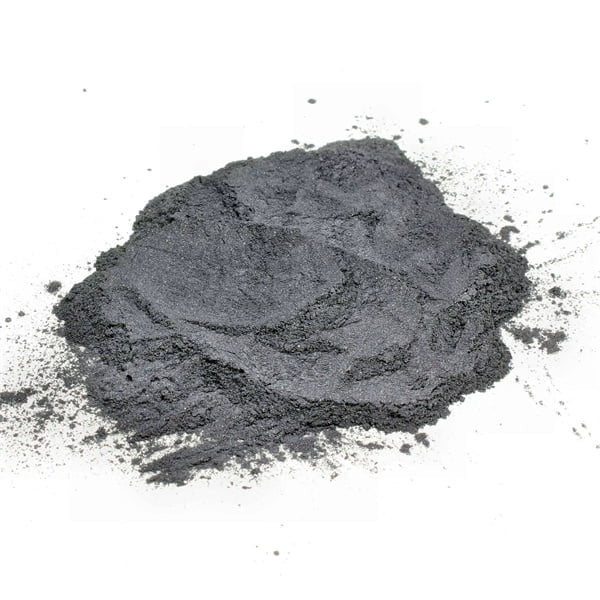
Specifikace, velikosti a normy
Porozumění technickým specifikacím prášková nástrojová ocel je zásadní pro informované rozhodování. Zde je náhled na některé klíčové parametry:
- Chemické složení: Konkrétní procenta železa, uhlíku a legujících prvků budou jasně definována v datovém listu poskytnutém výrobcem.
- Distribuce velikosti částic: Velikost a distribuce částic prášku ovlivňují konečné vlastnosti nástroje. Jemnější prášky obecně vedou k hustším a homogennějším strukturám.
- Zdánlivá hustota: To se týká hmotnosti prášku na jednotku objemu, která ovlivňuje, kolik prášku je potřeba k naplnění formy během výrobního procesu.
- Tekutost: Snadnost, s jakou prášek teče, je rozhodující pro účinné zpracování v technikách MAM nebo MIM.
Normy a certifikace hrají také významnou roli, zajišťují kvalitu a konzistenci práškové nástrojové oceli. Mezi běžné standardy patří:
- ASTM International (ASTM): Stanovuje mezinárodní standardy pro různé materiály, včetně kovových prášků.
- Mezinárodní organizace pro normalizaci (ISO): Vyvíjí a publikuje mezinárodní normy, z nichž některé jsou relevantní pro prášky nástrojové oceli.
- MPIF (Federace kovového prášku): Obchodní sdružení, které stanovuje standardy a podporuje používání kovových prášků v Severní Americe.
Dodavatelé a ceny
Prášek nástrojové oceli je snadno dostupný od mnoha světových a regionálních dodavatelů. Zde je několik faktorů, které je třeba vzít v úvahu při výběru dodavatele:
- Portfolio produktů: Dodavatel by měl nabídnout řadu možností práškové nástrojové oceli, aby vyhovoval vašim specifickým potřebám.
- Technické znalosti: Hledejte dodavatele se silným technickým týmem, který může poskytnout rady a podporu při výběru vhodného prášku z nástrojové oceli.
- Zajištění kvality: Zajistěte, aby dodavatel dodržoval příslušné normy a dodržoval přísné postupy kontroly kvality.
- Ceny a dodací lhůty: Porovnejte ceny od různých dodavatelů a zvažte minimální objednací množství a dodací lhůty.
Výhody a nevýhody práškové nástrojové oceli
I když prášková nástrojová ocel nabízí řadu výhod, je nezbytné uznat její omezení, abychom mohli učinit informované rozhodnutí.
Výhody práškové nástrojové oceli:
- Svoboda designu: Procesy MAM a MIM umožňují vytvářet složité geometrie, které je často obtížné nebo nemožné dosáhnout tradičními výrobními metodami. To otevírá dveře inovativním designům nástrojů se zlepšeným výkonem a funkčností.
- Účinnost materiálu: Prášková nástrojová ocel minimalizuje plýtvání materiálem ve srovnání s konvenčními technikami, jako je obrábění z plných bloků. To znamená úsporu nákladů a snížení dopadu na životní prostředí.
- Rozměrová přesnost: Tvarování téměř čistého tvaru pomocí MAM a MIM umožňuje výjimečnou rozměrovou přesnost a snižuje potřebu rozsáhlého následného zpracování.
- Vylepšené vlastnosti: Řízené vrstvení částic prášku může vést k jednotnější mikrostruktuře a lepším mechanickým vlastnostem ve srovnání s tvářenou nástrojovou ocelí.
- Potenciál pro přizpůsobení: Legovací prvky a výrobní parametry lze upravit tak, aby vznikl prášek nástrojové oceli s vlastnostmi speciálně vhodnými pro konkrétní aplikaci.
Nevýhody práškové nástrojové oceli:
- Vyšší náklady: V současnosti může být prášková nástrojová ocel dražší než běžně vyráběná tvářená nástrojová ocel, zejména pro maloobjemové aplikace.
- Omezený výběr materiálů: Rozmanitost dostupných možností práškové nástrojové oceli nemusí být tak široká jako u jakostí tvářených nástrojových ocelí.
- Složitost procesu: Techniky MAM a MIM vyžadují specializované vybavení a odborné znalosti, což zvyšuje celkové výrobní náklady.
- Možnost vnitřních vad: Nesprávná manipulace s práškem nebo parametry zpracování mohou vést k vnitřním defektům, jako je poréznost, která může ohrozit výkon nástroje.
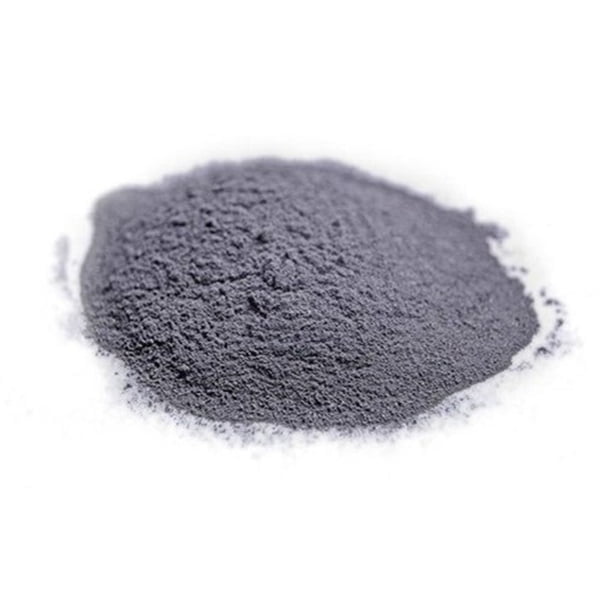
Výzvy pro Prášek z nástrojové oceli
Navzdory omezením pokrok v technologii a výrobních procesech neustále zmenšuje propast mezi práškovou nástrojovou ocelí a konvenčními metodami. Zde jsou některé slibné trendy:
- Snížené výrobní náklady: Jak technologie dospívá a objem výroby se zvyšuje, očekává se, že náklady na práškovou nástrojovou ocel budou klesat, čímž se stane dostupnější pro širší škálu aplikací.
- Rozšíření výběru materiálů: Výrobci neustále vyvíjejí nové složení prášku z nástrojové oceli s jedinečnými vlastnostmi, které uspokojí ještě širší spektrum potřeb.
- Pokročilé techniky zpracování: Inovace v technologiích MAM a MIM vedou ke zlepšení řízení procesu a snížení chybovosti, což zajišťuje konzistentní kvalitu konečného nástroje.
Konečný verdikt: Nástroj pro budoucnost
Prášková nástrojová ocel představuje revoluční přístup k výrobě nástrojů, který nabízí bezkonkurenční svobodu návrhu, výjimečné vlastnosti a snížené plýtvání materiálem. I když existují úvahy o nákladech a omezení, rychlý pokrok v technologii a inherentní výhody materiálu staví práškovou nástrojovou ocel jako výkonný nástroj budoucnosti. Jak se průmysl vyvíjí, očekávejte, že prášek z nástrojové oceli bude hrát stále významnější roli při utváření krajiny řezání a tvarování kovů.
Nejčastější dotazy
Otázka | Odpovědět |
---|---|
Jaké jsou výhody použití práškové nástrojové oceli oproti běžné tvářené nástrojové oceli? | Prášková nástrojová ocel nabízí svobodu návrhu pro složité geometrie, zlepšenou materiálovou efektivitu, výjimečnou rozměrovou přesnost a potenciál pro přizpůsobení vlastností. |
Jaká jsou některá omezení práškové nástrojové oceli? | V současné době může být prášková nástrojová ocel dražší, má omezený výběr materiálu ve srovnání s tvářenou ocelí a vyžaduje složitý výrobní proces s potenciálem vnitřních vad. |
Je prášek nástrojové oceli vhodný pro mou aplikaci? | Zvažte faktory, jako je složitost návrhu, objem výroby, požadované vlastnosti a rozpočet. Prášková nástrojová ocel vyniká pro složité konstrukce, požadavky na vysoký výkon a výrobu šetrnou k životnímu prostředí. |
Kolik stojí prášek z nástrojové oceli? | Cena se liší v závislosti na konkrétním materiálu, množství a dodavateli. Obecně může být pro maloobjemové aplikace dražší než tvářená nástrojová ocel, ale mezera se zmenšuje. |
Kde lze koupit práškovou nástrojovou ocel? | Prášek z nástrojové oceli nabízí řada světových a regionálních dodavatelů. Hledejte dodavatele s rozmanitým produktovým portfoliem, technickou odborností, postupy zajišťování kvality a konkurenceschopnými cenami. |
Sdílet na
MET3DP Technology Co., LTD je předním poskytovatelem řešení aditivní výroby se sídlem v Qingdao v Číně. Naše společnost se specializuje na zařízení pro 3D tisk a vysoce výkonné kovové prášky pro průmyslové aplikace.
Dotaz k získání nejlepší ceny a přizpůsobeného řešení pro vaše podnikání!
Související články
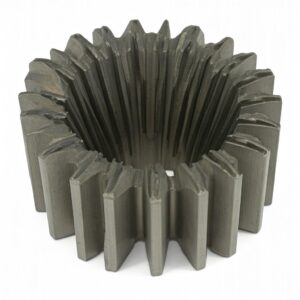
Vysoce výkonné segmenty lopatek trysek: Revoluce v účinnosti turbín díky 3D tisku z kovu
Přečtěte si více "O Met3DP
Nedávná aktualizace
Náš produkt
KONTAKTUJTE NÁS
Nějaké otázky? Pošlete nám zprávu hned teď! Po obdržení vaší zprávy obsloužíme vaši žádost s celým týmem.
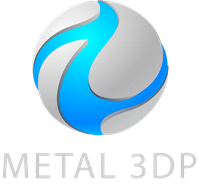
Kovové prášky pro 3D tisk a aditivní výrobu