3D Printed Drone Motor Mounts: Revolutionizing UAV Manufacturing
Inhaltsübersicht
The drone industry is experiencing exponential growth, with applications spanning from aerial photography and surveillance to package delivery and industrial inspections. A critical component in the performance and reliability of any unmanned aerial vehicle (UAV) is the motor mount. These seemingly simple parts are responsible for securely attaching the motors to the drone frame, ensuring stability, minimizing vibrations, and contributing to overall flight efficiency. Traditionally manufactured motor mounts often face limitations in terms of design complexity, weight optimization, and material performance. This is where the transformative power of metal 3D-Druck, also known as metal additive manufacturing, comes into play, offering engineers and procurement managers unprecedented opportunities to innovate and enhance their drone designs.
What are 3D Printed Drone Motor Mounts Used For?
3D printed drone motor mounts serve as the crucial interface between the drone’s motors and its frame. Their primary functions include:
- Secure Motor Attachment: Providing a robust and reliable connection point for the motors, ensuring they remain firmly in place during flight maneuvers and under varying loads.
- Schwingungsdämpfung: Minimizing the transmission of motor-induced vibrations to the airframe, which can negatively impact flight stability, sensor accuracy, and the lifespan of other electronic components. Optimized designs achievable through 3D printing can significantly improve vibration damping.
- Optimierung des Gewichts: Enabling the creation of lightweight yet strong structures with internal lattices and optimized geometries, directly contributing to increased flight time and payload capacity – critical factors in the competitive drone market.
- Customization and Integration: Facilitating the design of motor mounts tailored to specific motor sizes, frame geometries, and application requirements. Features such as integrated wire routing or sensor mounts can be incorporated directly into the design.
- Rapid Prototyping und Iteration: Allowing for quick design modifications and the production of functional prototypes, accelerating the development cycle for new drone models.
These versatile components find applications across a wide spectrum of drone types and industries, including:
- Commercial Drones: Used for photography, videography, surveying, and mapping.
- Industrial Drones: Employed in infrastructure inspection, agricultural monitoring, and construction.
- Logistics and Delivery Drones: Designed for efficient and rapid transportation of goods.
- Surveillance and Security Drones: Utilized for monitoring, law enforcement, and defense applications.
- Racing Drones: Where lightweight and robust motor mounts are essential for agility and performance.
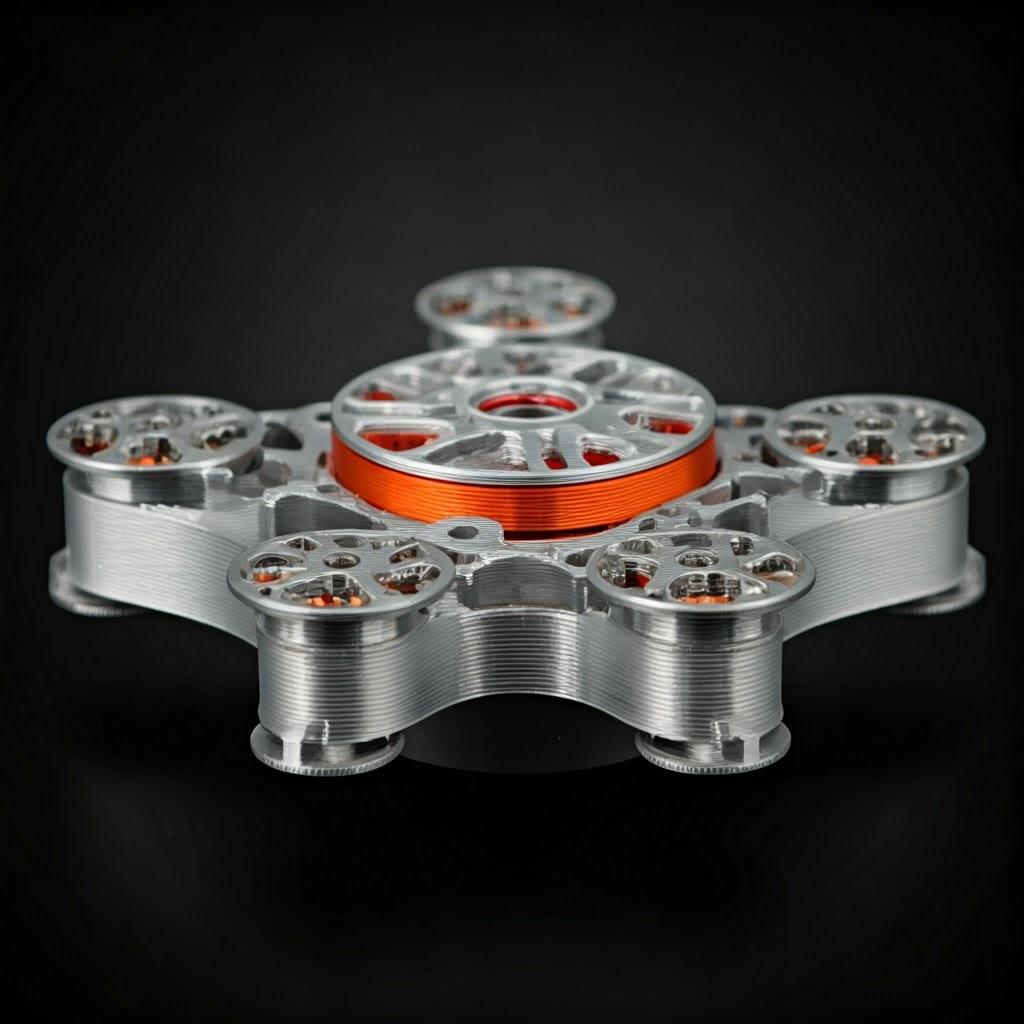
Why Use Metal 3D Printing for Drone Motor Mounts?
Opting for metal 3D printing for the production of drone motor mounts offers numerous advantages over traditional manufacturing methods such as CNC machining or die casting:
- Gestaltungsfreiheit und Komplexität: Additive manufacturing allows for the creation of intricate geometries, including internal lattices, conformal cooling channels (if needed for motor heat dissipation), and organic shapes that are difficult or impossible to achieve with subtractive methods. This design freedom enables significant weight reduction and improved structural performance.
- Gewichtsreduzierung: By employing topology optimization and lattice structures, metal 3D printing facilitates the creation of significantly lighter parts without compromising strength or stiffness. This is paramount in drone design, where every gram saved translates to longer flight times and increased efficiency.
- Materialeffizienz: Additive manufacturing processes build parts layer by layer, minimizing material waste compared to subtractive methods where material is removed from a solid block. This can lead to significant cost savings, especially when working with expensive specialty alloys.
- Schnelles Prototyping und individuelle Anpassung: Metal 3D printing enables the fast production of prototypes, allowing for rapid design iteration and testing. Furthermore, it facilitates the cost-effective production of customized motor mounts tailored to specific drone configurations or low-volume production runs.
- Verbesserte Leistung: The ability to choose high-performance metal powders, like those offered by Metall3DP (learn more about their 3D-Druck von Metall capabilities), allows for the creation of motor mounts with superior strength-to-weight ratios, excellent thermal conductivity, and high durability, crucial for demanding drone applications.
- Integration of Features: 3D printing allows for the integration of multiple functionalities into a single part, such as wire conduits or mounting features for sensors, reducing the number of components and assembly steps. Metal3DPs expertise in application development services can help in realizing such integrated designs.
Recommended Materials and Why They Matter
The selection of the appropriate metal powder is critical to achieving the desired performance characteristics for 3D printed drone motor mounts. Metall3DP offers a range of high-quality metal powders optimized for additive manufacturing, including:
- AlSi10Mg: This aluminum alloy is a popular choice for aerospace and automotive applications due to its excellent strength-to-weight ratio, good thermal conductivity, and high ductility. Key benefits for drone motor mounts include:
- Leichtes Gewicht: Minimizing the overall weight of the drone, leading to longer flight times and improved maneuverability.
- Hohe Festigkeit: Providing a robust and durable connection for the motors, capable of withstanding flight stresses.
- Good Thermal Management: Dissipating heat generated by the motors, preventing overheating and ensuring optimal performance.
- Excellent Processability: Well-suited for laser powder bed fusion (LPBF) processes, offering good surface finish and dimensional accuracy. Metal3DPs advanced powder making system ensures the high sphericity and flowability of AlSi10Mg powder, crucial for consistent printing.
- Scalmalloy®: This high-performance aluminum-magnesium-scandium alloy offers exceptional strength-to-weight ratio, even surpassing conventional aluminum alloys. Its key advantages for demanding drone applications include:
- Ultra-Lightweight: Significantly reducing the weight of the motor mount, maximizing flight efficiency and payload capacity.
- Sehr hohe Festigkeit: Providing superior structural integrity, crucial for high-performance drones and challenging operating conditions.
- Excellent Fatigue Resistance: Ensuring the longevity and reliability of the motor mount under cyclic loading during flight.
- Gute Korrosionsbeständigkeit: Enhancing the durability of the component in various environmental conditions. Metall3DP offers high-quality Scalmalloy® powder, enabling customers to 3D print dense, high-quality parts with superior mechanical properties.
By leveraging the advanced metal powders offered by Metall3DP and the design flexibility of metal 3D printing, drone manufacturers can achieve significant improvements in the performance, efficiency, and reliability of their UAVs. Stay tuned for Part 2, where we will delve into design considerations for additive manufacturing, tolerance and surface finish, post-processing requirements, and common challenges in 3D printing drone motor mounts.
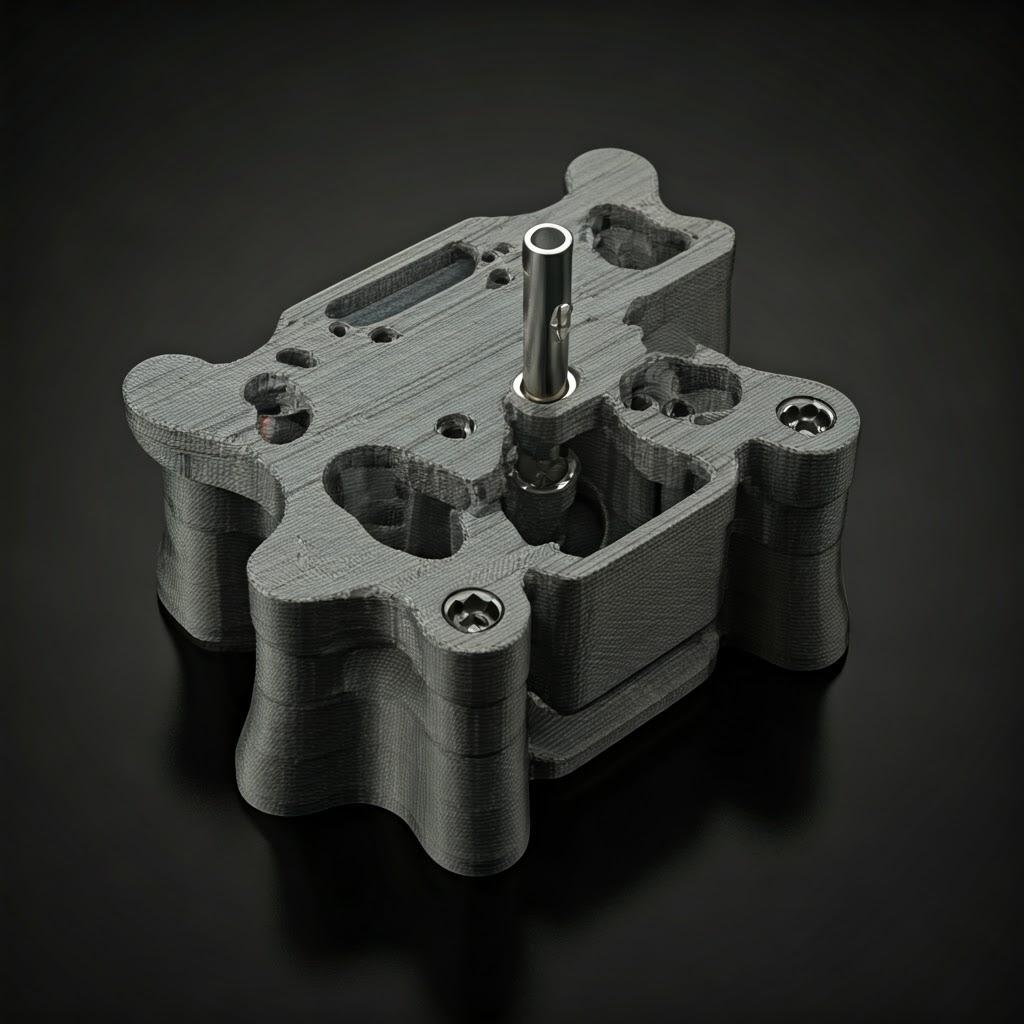
Design Considerations for Additive Manufacturing of Drone Motor Mounts
Designing for metal 3D printing requires a different mindset compared to traditional manufacturing. To fully leverage the capabilities of additive manufacturing and achieve optimal performance for drone motor mounts, several design considerations are crucial:
- Topologie-Optimierung: This computational method helps to identify and remove material in non-critical areas while maintaining the structural integrity of the part. By defining the load-bearing requirements and constraints, engineers can generate lightweight designs with optimized material distribution. This is particularly beneficial for drone motor mounts where minimizing weight is paramount. Software tools can automatically generate complex, organic-looking structures that would be impossible to manufacture using conventional methods.
- Gitterförmige Strukturen: Incorporating lattice structures, such as gyroids, honeycombs, or cubic lattices, within the interior of the motor mount can significantly reduce weight without sacrificing stiffness or strength. The density and cell size of the lattice can be tailored to specific load requirements. Metal3DPs expertise can assist in determining the optimal lattice design for your application.
- Orientation and Support Structures: The orientation of the part during the printing process can impact surface finish, support material requirements, and overall build time. Careful consideration of the build orientation is necessary to minimize the need for extensive post-processing and ensure critical surfaces meet the required specifications. Support structures are often required to prevent collapse or distortion during printing, especially for overhanging features. Designing with self-supporting angles and minimizing overhangs can reduce the amount of support material needed.
- Wall Thickness and Ribs: Maintaining a consistent and appropriate wall thickness is essential for structural integrity. Thin walls can be prone to buckling, while excessively thick walls add unnecessary weight. Incorporating ribs or gussets can provide additional reinforcement to thinner sections without significantly increasing weight.
- Merkmal Integration: Additive manufacturing allows for the integration of multiple features into a single part. For drone motor mounts, this could include integrated wire routing channels, mounting points for sensors or lights, or even cooling features. Consolidating parts reduces assembly time and potential failure points. Metal3DPs application development services can help explore and implement such integrated designs.
- Tolerances and Fit: Account for the tolerances achievable with the chosen metal 3D printing process. Design interfaces with other drone components, such as the motor and the frame, with appropriate clearances or interference fits to ensure proper assembly and functionality.
Tolerance, Surface Finish, and Dimensional Accuracy of 3D Printed Motor Mounts
The tolerance, surface finish, and dimensional accuracy achievable with metal 3D printing have significantly improved over time. However, they are still influenced by several factors, including the chosen printing technology (e.g., LPBF, DED), the material, the part geometry, and the post-processing steps.
- Verträglichkeit: Typical tolerances for metal 3D printed parts range from ±0.1 mm to ±0.05 mm, depending on the process and part size. Critical functional interfaces of the drone motor mount that require precise fitment with the motor or the drone frame should be designed with these tolerances in mind. For very tight tolerances, post-machining operations may be necessary. Metal3DPs industry-leading accuracy ensures that your printed parts meet stringent requirements.
- Oberfläche: The surface finish of as-printed metal parts is typically rougher than that achieved by machining. The surface roughness (Ra) can range from 5 to 20 µm for LPBF processes. For drone motor mounts, the surface finish might not be critical for structural performance but can impact aerodynamic properties or aesthetics in some applications. Post-processing techniques like polishing or media blasting can be used to improve the surface finish if required.
- Maßgenauigkeit: Dimensional accuracy refers to the degree to which the printed part matches the intended CAD model. While metal 3D printing offers good dimensional accuracy, factors like material shrinkage during solidification and thermal stresses can introduce slight deviations. Careful process parameter optimization and build orientation planning can minimize these inaccuracies. Metal3DPs commitment to industry-leading reliability ensures consistent dimensional accuracy in the manufactured parts.
Merkmal | Typical Range for LPBF | Impact on Drone Motor Mounts | Minderungsstrategien |
---|---|---|---|
Toleranz | ±0.05−0.1 mm | Affects fit with motor and frame; can impact vibration damping and structural integrity. | Design with appropriate clearances/fits; consider post-machining for critical interfaces. |
Oberflächenrauhigkeit (Ra) | 5 - 20 µm | May affect aerodynamics or aesthetics; generally not critical for structural performance. | Specify post-processing (e.g., polishing, blasting) if smoother finish is required. |
Maßgenauigkeit | ±0.1−0.3% | Can impact overall assembly and functionality. | Optimize build orientation; consider material shrinkage during design. |
In Blätter exportieren
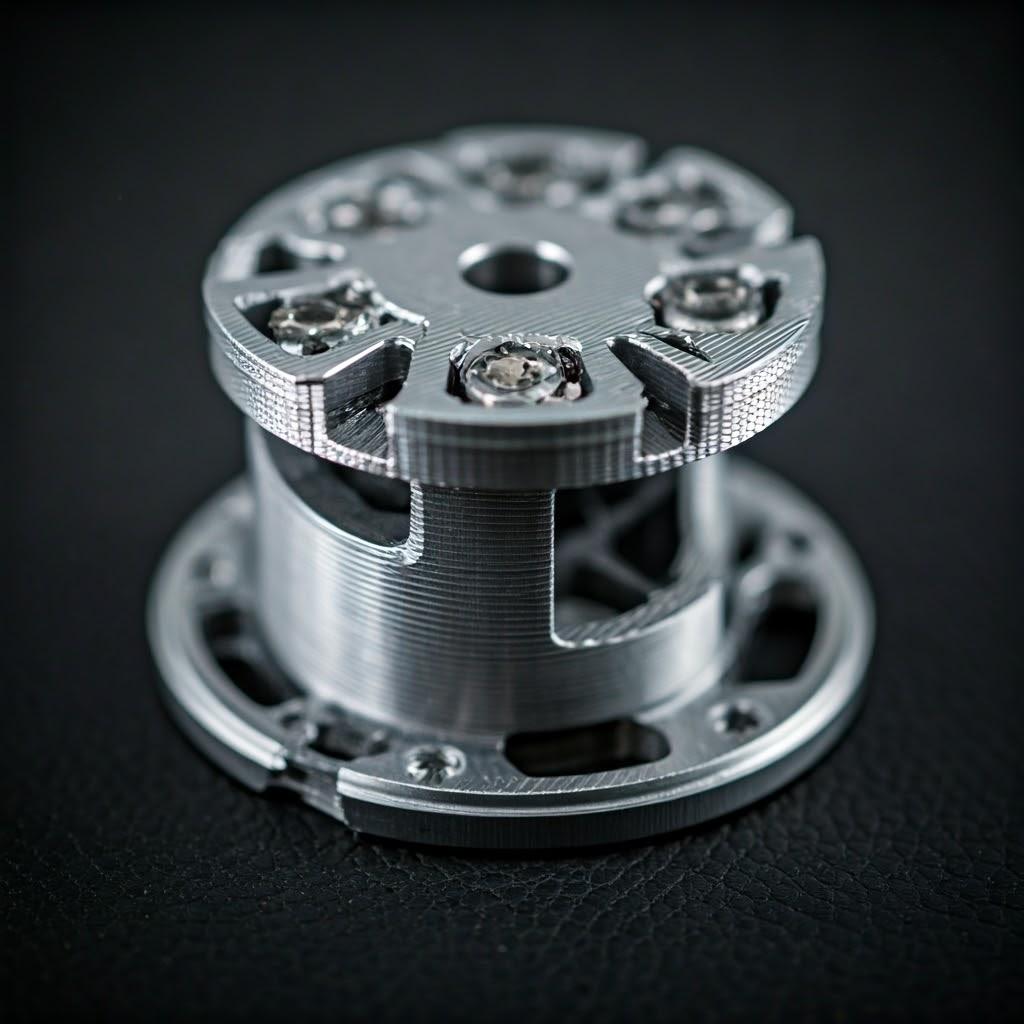
Post-Processing Requirements for Metal 3D Printed Motor Mounts
While metal 3D printing offers near-net-shape manufacturing, some post-processing steps are often required to achieve the final desired properties and finish for drone motor mounts:
- Unterstützung bei der Entfernung: Support structures used during the printing process need to be removed. This can be done manually using tools or through automated methods like machining or chemical dissolution, depending on the material and support type. Careful design to minimize support structures, as discussed earlier, can simplify this step.
- Stressabbau Wärmebehandlung: To alleviate residual stresses that can build up during the rapid heating and cooling cycles of the printing process, a stress relief heat treatment is often performed. This improves the mechanical properties and dimensional stability of the part. Metal3DPs comprehensive solutions include guidance on appropriate heat treatment procedures.
- Heiß-Isostatisches Pressen (HIP): For critical applications requiring maximum density and mechanical performance, Hot Isostatic Pressing (HIP) can be employed. This process involves subjecting the printed part to high pressure and temperature in an inert atmosphere, effectively eliminating internal porosity and improving material homogeneity.
- Oberflächenveredelung: Depending on the application requirements, various surface finishing techniques can be applied, including:
- Media Blasting: To remove loose powder and improve surface uniformity.
- Polieren: To achieve a smoother surface finish for aesthetic or functional reasons.
- Beschichtung: To enhance corrosion resistance, wear resistance, or other specific properties.
- CNC-Bearbeitung: For features requiring very tight tolerances or specific surface finishes that cannot be directly achieved through 3D printing, secondary CNC machining operations may be necessary. This is often used for critical mounting holes or interfaces.
Common Challenges and How to Avoid Them in 3D Printing Drone Motor Mounts
While metal 3D printing offers numerous advantages, several challenges can arise during the process. Understanding these potential issues and implementing preventative measures is crucial for successful production of drone motor mounts:
- Verformung und Verzerrung: Thermal stresses during the printing process can lead to warping or distortion of the part, especially for large or complex geometries.
- How to Avoid: Optimize build orientation, use appropriate support structures, and carefully control process parameters. Stress relief heat treatment after printing can also mitigate warping.
- Unterstützung bei der Beseitigung von Schwierigkeiten: Intricately designed supports or supports fused to the part can be challenging to remove without damaging the component.
- How to Avoid: Design for minimal support structures, utilize breakaway supports, or consider soluble support materials if available for the chosen material and printing process.
- Porosität: Internal voids or pores can compromise the mechanical strength and fatigue resistance of the printed part.
- How to Avoid: Optimize printing parameters such as laser power, scan speed, and layer thickness. Ensure high-quality metal powder with good flowability, such as those offered by Metall3DP. Consider HIP for critical applications requiring maximum density.
- Surface Finish Issues: Achieving a smooth surface finish directly from the printing process can be challenging.
- How to Avoid: Optimize build orientation to minimize stepped surfaces. Utilize finer powder particles. Plan for post-processing steps like media blasting or polishing if a smoother finish is required.
- Dimensional Inaccuracies: Deviations from the intended dimensions can occur due to material shrinkage or process variations.
- How to Avoid: Calibrate the 3D printer regularly. Optimize process parameters for the chosen material. Account for material shrinkage during the design phase. Consider using build platform preheating.
By understanding these design considerations, post-processing requirements, and potential challenges, engineers and procurement managers can effectively leverage metal 3D printing to produce high-performance drone motor mounts. Metal3DPs expertise in metal AM equipment and materials can provide valuable support in navigating these aspects and ensuring successful outcomes.
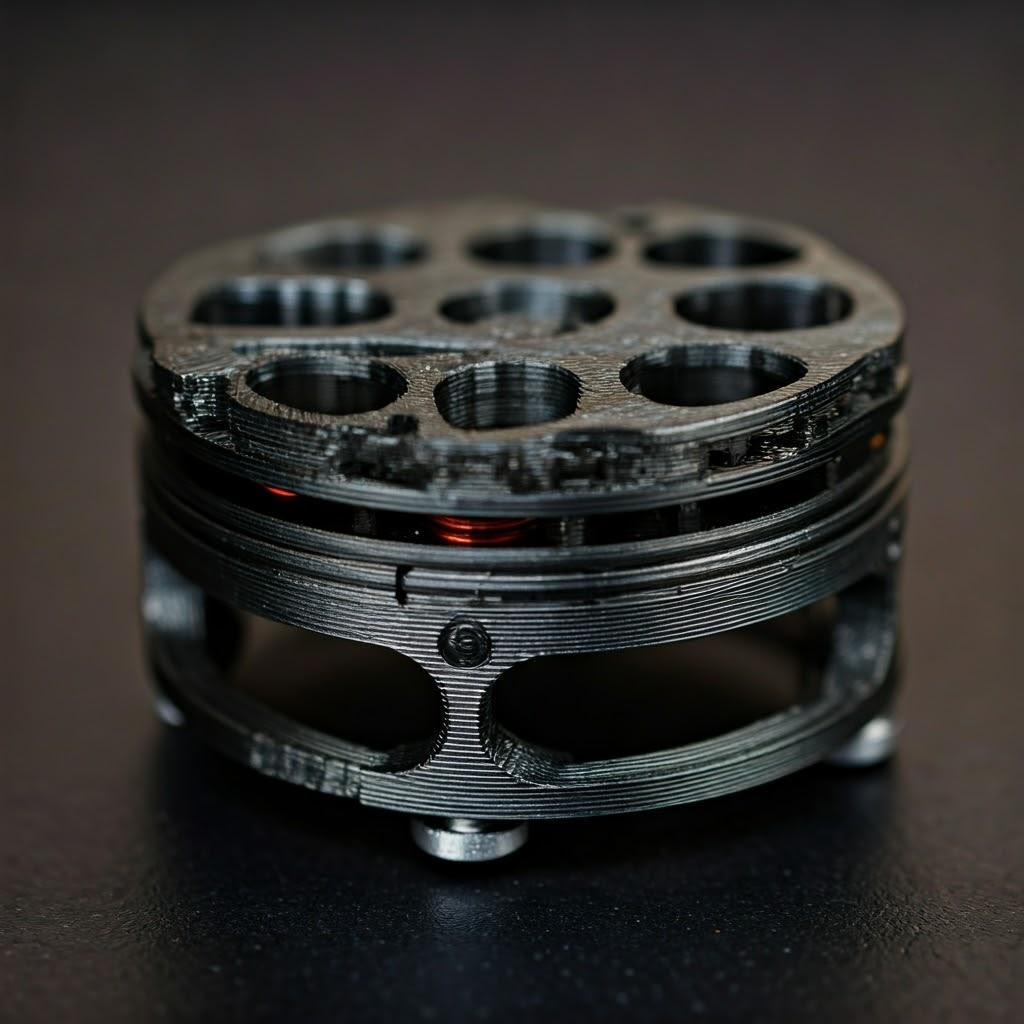
How to Choose the Right Metal 3D Printing Service Provider for Drone Motor Mounts
Selecting the appropriate metal 3D printing service provider is a critical decision that can significantly impact the quality, cost, and lead time of your drone motor mounts. Here are key factors to consider when evaluating potential suppliers:
- Material Capabilities: Ensure the service provider has experience processing the specific metal powders required for your application (e.g., AlSi10Mg, Scalmalloy®). Verify their material certifications and the quality control measures they have in place. Metall3DP itself is a leading provider of high-performance metal powders, giving them inherent expertise in material selection and processing.
- Printing Technology and Equipment: Understand the types of metal 3D printing technologies the provider utilizes (e.g., LPBF, DED). The choice of technology can influence the achievable tolerance, surface finish, and build volume. Inquire about the specifications and maintenance of their equipment. Metall3DP offers industry-leading SEBM printers known for their print volume, accuracy, and reliability. You can learn more about their Druckverfahren on their website.
- Quality Assurance and Certifications: Check if the provider has relevant quality management certifications (e.g., ISO 9001, AS9100 for aerospace). Inquire about their inspection processes, dimensional accuracy reports, and material traceability.
- Design and Engineering Support: Assess whether the provider offers design optimization services for additive manufacturing. Experienced engineers can help refine your motor mount design for improved printability, weight reduction, and performance. Metall3DP provides comprehensive solutions spanning equipment, powders, and application development services.
- Post-Processing Services: Determine if the provider offers the necessary post-processing services, such as support removal, heat treatment, surface finishing, and CNC machining. A comprehensive service offering can streamline the production process.
- Experience and Expertise: Look for a provider with a proven track record in metal 3D printing, ideally with experience in the aerospace, automotive, medical, or industrial manufacturing sectors – industries where drone technology is prevalent.
- Communication and Customer Support: Evaluate the responsiveness and clarity of their communication. A reliable provider should be readily available to answer your questions and provide updates on your project.
- Vorlaufzeiten: Inquire about their typical lead times for similar projects, from design finalization to shipment of the finished parts. Understand their production capacity and how it might affect delivery schedules.
Cost Factors and Lead Time for 3D Printed Drone Motor Mounts
The cost of metal 3D printed drone motor mounts is influenced by several factors:
- Materialkosten: The price of the metal powder is a significant contributor to the overall cost. Specialty alloys like Scalmalloy® are typically more expensive than standard aluminum alloys like AlSi10Mg. The quantity of material used per part also plays a role.
- Bauzeit: The duration of the printing process directly impacts the cost. Longer build times, often associated with larger parts or higher part counts per build, increase machine operating costs.
- Nachbearbeitungskosten: The extent and complexity of required post-processing steps (e.g., support removal, heat treatment, machining, surface finishing) will add to the final cost.
- Arbeitskosten: Engineering time for design optimization, print setup, and post-processing all contribute to the overall cost.
- Machine Depreciation and Overhead: The service provider’s operational costs, including machine maintenance and depreciation, are factored into their pricing.
- Auftragsvolumen: Generally, higher production volumes can lead to lower per-part costs due to economies of scale. However, metal 3D printing often remains cost-competitive for low-to-medium volume production and highly customized parts.
Lead times for metal 3D printed drone motor mounts can vary depending on factors such as:
- Teil Komplexität und Größe: More intricate or larger parts may require longer print times.
- Materialverfügbarkeit: The availability of the chosen metal powder can impact the start of production. Metall3DP manufactures a wide range of high-quality metal powders, potentially offering shorter lead times for projects utilizing their materials.
- Service Provider’s Capacity: The current workload and the number of available machines at the service provider’s facility will influence lead times.
- Nachbearbeitungsanforderungen: Extensive post-processing can add to the overall lead time.
- Shipping Time: The time required for shipping the finished parts to your location needs to be considered.
It’s crucial to discuss both cost and lead time expectations with potential service providers early in the process to ensure they align with your project requirements and budget. Getting detailed quotes that break down material, printing, and post-processing costs will provide transparency. You can explore Metal3DPs product offerings on their Produktseite.
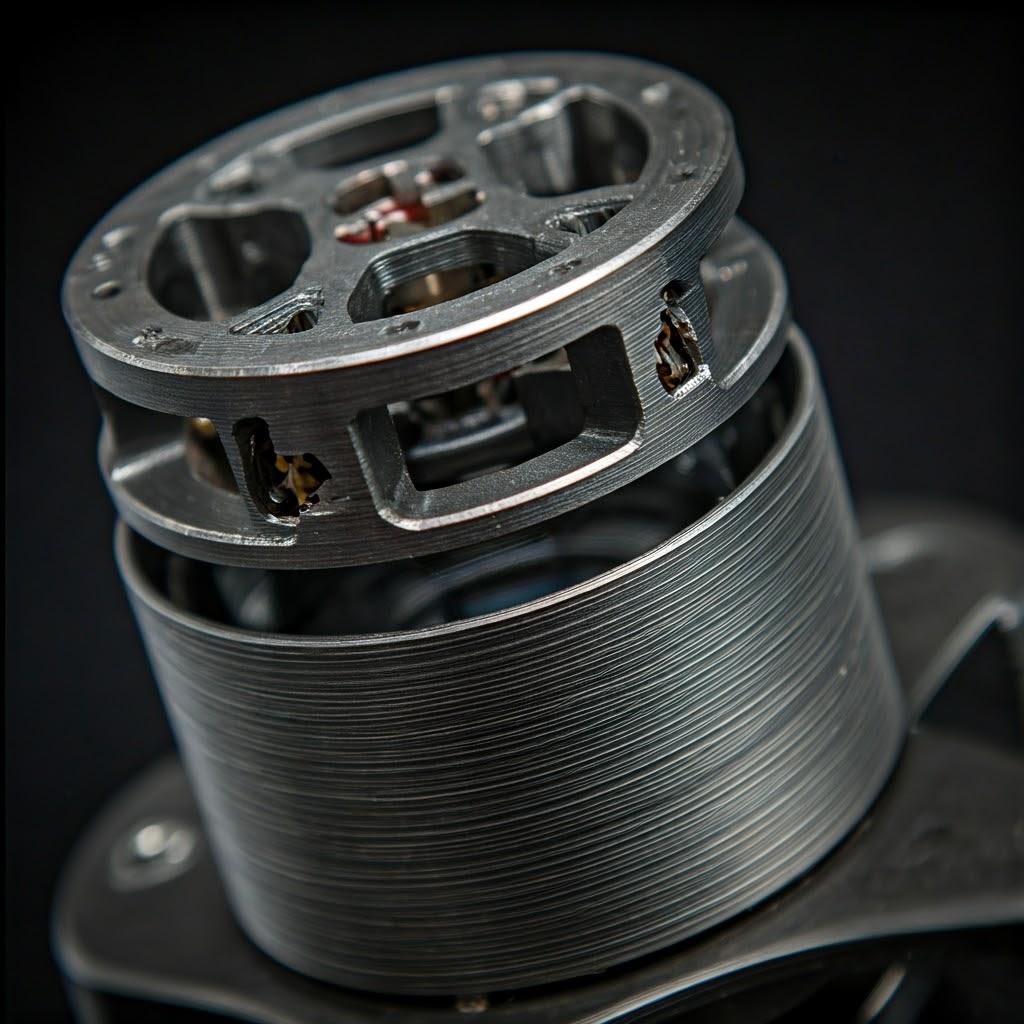
Häufig gestellte Fragen (FAQ)
- Q: Can metal 3D printed drone motor mounts be as strong as traditionally manufactured ones?
- A: Yes, when the appropriate metal powder and printing parameters are used, metal 3D printed parts can achieve comparable or even superior strength-to-weight ratios compared to traditionally manufactured parts. Alloys like Scalmalloy®, offered by Metall3DP, demonstrate exceptional mechanical properties. Post-processing treatments like HIP can further enhance the density and strength of 3D printed components.
- Q: What is the typical lifespan of a metal 3D printed drone motor mount?
- A: The lifespan depends on the material used, the operating conditions of the drone, and the design of the motor mount. High-quality metal powders and optimized designs can result in durable parts with a long service life. Proper post-processing and surface treatments can also enhance their resistance to wear and corrosion.
- Q: Is metal 3D printing cost-effective for producing drone motor mounts in large quantities?
- A: While metal 3D printing excels in producing complex geometries and customized parts in low to medium volumes, for very high volumes, traditional manufacturing methods like die casting might be more cost-effective. However, the advantages of design flexibility, lightweighting, and rapid iteration offered by 3D printing can still make it a compelling option even for moderate production runs, especially when considering the total cost of ownership and potential performance benefits.
Schlussfolgerung
Metal 3D printing offers a transformative approach to the manufacturing of drone motor mounts, providing engineers and procurement managers with unprecedented opportunities for design innovation, weight optimization, and performance enhancement. By leveraging advanced materials like AlSi10Mg and Scalmalloy® from providers like Metall3DP, manufacturers can create lighter, stronger, and more efficient drones for a wide range of applications. Understanding the design considerations, post-processing requirements, and how to choose the right service provider are crucial steps in harnessing the full potential of metal additive manufacturing. As a leader in metal AM equipment and materials, Metall3DP is well-positioned to partner with organizations looking to implement 3D printing and accelerate their digital manufacturing transformations. Contact Metall3DP through their website (https://met3dp.com/) to explore how their capabilities can power your organization’s additive manufacturing goals.
Teilen auf
MET3DP Technology Co., LTD ist ein führender Anbieter von additiven Fertigungslösungen mit Hauptsitz in Qingdao, China. Unser Unternehmen ist spezialisiert auf 3D-Druckgeräte und Hochleistungsmetallpulver für industrielle Anwendungen.
Fragen Sie an, um den besten Preis und eine maßgeschneiderte Lösung für Ihr Unternehmen zu erhalten!
Verwandte Artikel
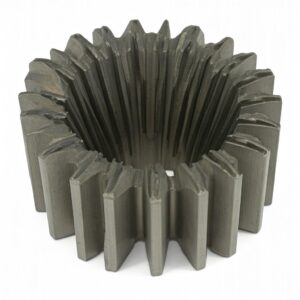
Hochleistungs-Düsenschaufelsegmente: Revolutionierung der Turbineneffizienz mit 3D-Metalldruck
Mehr lesen "Über Met3DP
Aktuelles Update
Unser Produkt
KONTAKT US
Haben Sie Fragen? Senden Sie uns jetzt eine Nachricht! Wir werden Ihre Anfrage mit einem ganzen Team nach Erhalt Ihrer Nachricht bearbeiten.
Holen Sie sich Metal3DP's
Produkt-Broschüre
Erhalten Sie die neuesten Produkte und Preislisten
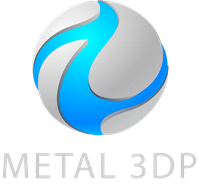
Metallpulver für 3D-Druck und additive Fertigung
UNTERNEHMEN
PRODUKT
cONTACT INFO
- Qingdao Stadt, Shandong, China
- [email protected]
- [email protected]
- +86 19116340731