die Anwendung von DMLS in der Luft- und Raumfahrt
Inhaltsübersicht
Stellen Sie sich vor, Sie könnten komplizierte Flugzeugteile mit unvergleichlicher Designfreiheit herstellen, das Gewicht reduzieren und gleichzeitig die Leistung steigern - das ist die Magie des Direkten Metall-Laser-Sinterns (DMLS) in der Luft- und Raumfahrtindustrie. Diese revolutionäre 3D-Drucktechnologie verändert in rasantem Tempo die Art und Weise, wie wir Komponenten in Flugzeugen, Satelliten und darüber hinaus entwerfen, herstellen und nutzen. Schnallen Sie sich an, wenn wir in die faszinierende Welt des DMLS in der Luft- und Raumfahrt eintauchen und seine Anwendungen, die spezifischen Metallpulver, die es verwendet, und die aufregende Zukunft, die es verspricht, untersuchen.
DMLS: Ein 3D-Druck-Kraftpaket für die Luft- und Raumfahrt
DMLS, auch bekannt als Direct Metal Laser Melting (DMLS®), ist ein additives Fertigungsverfahren, bei dem ein Hochleistungslaser verwendet wird, um Metallpulverpartikel selektiv Schicht für Schicht zu schmelzen und so ein 3D-Objekt aus einem computergestützten Designmodell (CAD) aufzubauen. Im Gegensatz zu herkömmlichen subtraktiven Fertigungsverfahren wie der maschinellen Bearbeitung entstehen beim DMLS die Teile von Grund auf, was für Anwendungen in der Luft- und Raumfahrt eine Fülle von Vorteilen bietet:
- Unerreichte Designfreiheit: DMLS sprengt die Grenzen herkömmlicher Verfahren. Stellen Sie sich interne Gitterstrukturen zur Gewichtsreduzierung, komplexe Kühlkanäle zur Verbesserung der Motoreffizienz oder Teile mit bisher unmöglichen Geometrien vor - mit DMLS ist all das möglich.
- Leichtgewichtige Fähigkeiten: In der Luft- und Raumfahrt zählt jedes Gramm. DMLS ermöglicht es Ingenieuren, komplizierte, leichte Komponenten zu entwerfen, die das Gesamtgewicht von Flugzeugen erheblich reduzieren, was zu einer höheren Treibstoffeffizienz und längeren Flugstrecken führt.
- Rapid Prototyping und Iteration: Die Möglichkeit, komplexe Teile schnell und direkt aus CAD-Modellen zu fertigen, ermöglicht ein schnelles Prototyping und eine schnelle Design-Iteration. Dies beschleunigt den Entwicklungsprozess und verkürzt die Markteinführungszeit für neue Luft- und Raumfahrttechnologien.
- Weniger Abfall und Materialeinsparungen: Beim DMLS wird nur das benötigte Metallpulver verwendet, so dass im Vergleich zu herkömmlichen Verfahren, bei denen viel Ausschuss anfällt, nur wenig Abfall anfällt. Dies führt zu Kosteneinsparungen und einem umweltfreundlicheren Herstellungsprozess.
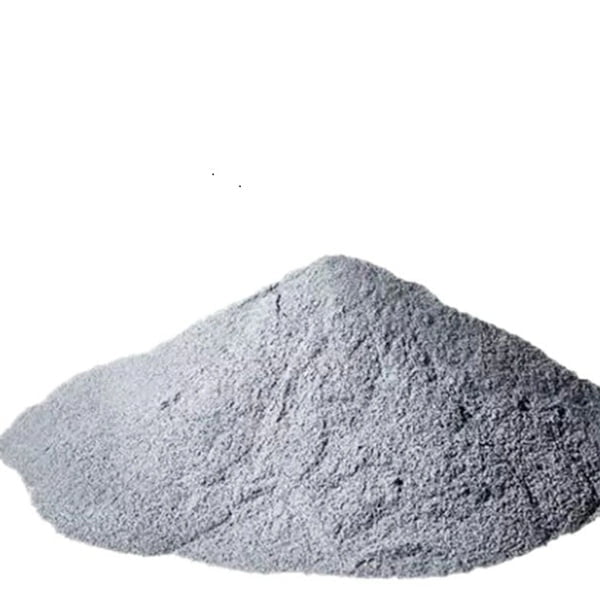
DMLS in Aktion: Ein Schaufenster der Anwendungen
DMLS ist nicht nur theoretisch, sondern revolutioniert die Luft- und Raumfahrt in realen Anwendungen:
- Flugzeugtriebwerke: Komplexe Motorkomponenten wie Brennkammern, Kraftstoffeinspritzdüsen und leichte Turbinenschaufeln mit komplizierten internen Kühlkanälen werden zunehmend mit DMLS hergestellt, was zu einer verbesserten Kraftstoffeffizienz und Motorleistung führt.
- Strukturen der Flugzeugzelle: DMLS ermöglicht die Herstellung von leichten, hochfesten Flugzeugkomponenten wie Halterungen, Rippen und Beschlägen und trägt so zu einer allgemeinen Gewichtsreduzierung und verbesserten Leistung des Flugzeugs bei.
- Satelliten und Raumfahrzeuge: Die Fähigkeit, komplizierte Teile mit einem hohen Verhältnis von Festigkeit zu Gewicht herzustellen, macht DMLS ideal für Satellitenstrukturen, ausfahrbare Mechanismen und sogar Antriebskomponenten, die den Weg für leichtere, effizientere Raumfahrzeuge ebnen.
- Unbemannte Luftfahrzeuge (UAVs): DMLS eignet sich perfekt für das Rapid Prototyping und die Produktion von leichten, kundenspezifischen Komponenten für Drohnen und fördert so die Innovation in der schnell wachsenden Drohnenindustrie.
Das Arsenal an Metallpulvern
Der Erfolg von DMLS hängt von den verwendeten Metallpulvern ab. Hier erhalten Sie einen Einblick in einige der Top-Kandidaten, von denen jeder seine einzigartigen Eigenschaften hat:
Metallpulver | Beschreibung | Eigenschaften | Anwendungen in der Luft- und Raumfahrt |
---|---|---|---|
Titan-Legierungen (Ti-6Al-4V, Ti-6Al-4V ELI): | Das Arbeitspferd des DMLS für die Luft- und Raumfahrt, das ein ausgezeichnetes Verhältnis von Festigkeit zu Gewicht, hohe Korrosionsbeständigkeit und Biokompatibilität (nützlich für Lebenserhaltungssysteme in Raumfahrzeugen) bietet. | Ausgezeichnete mechanische Eigenschaften, gute Schweißbarkeit, biokompatibel. | Turbinenschaufeln, Komponenten von Flugzeugen, Strukturen von Raumfahrzeugen. |
Inconel 625: | Eine Hochleistungs-Nickel-Chrom-Superlegierung, die für ihre außergewöhnliche Hochtemperaturfestigkeit und Oxidationsbeständigkeit bekannt ist. | Außergewöhnliche Hochtemperaturleistung, gute Korrosionsbeständigkeit. | Triebwerksbrennkammern, Heißteilkomponenten, Hochtemperaturanwendungen in der Luft- und Raumfahrt. |
Aluminium-Legierungen (AlSi10Mg, Scalmalloy): | Aufgrund ihres ausgewogenen Verhältnisses von Festigkeit, Gewicht und Druckbarkeit werden Aluminiumlegierungen zunehmend im DMLS-Verfahren für die Luft- und Raumfahrt eingesetzt, insbesondere für unkritische Komponenten. | Leicht, gut bedruckbar, mit gewissen Einschränkungen bei der Festigkeit. | Leichte Flugwerkskomponenten, Gehäuse, unkritische Teile. |
Rostfreier Stahl (316L): | Eine vielseitige und kostengünstige Option, die sich durch gute Korrosionsbeständigkeit und Bearbeitbarkeit auszeichnet. | Gute Korrosionsbeständigkeit, Bearbeitbarkeit, mäßige Festigkeit. | Gehäuse, Rohrleitungen, nicht kritische Komponenten, die Korrosionsbeständigkeit erfordern. |
Kobalt-Chrom (CoCr): | Eine biokompatible Legierung mit hervorragender Verschleißfestigkeit, die eine wertvolle Option für bestimmte Anwendungen in der Luft- und Raumfahrt darstellt. | Hohe Verschleißfestigkeit, biokompatibel, gute Festigkeit. | Fahrwerkskomponenten, spezifische Verschleißanwendungen. |
Kupferlegierungen (CuNi) (Fortsetzung): | Aufgrund ihrer hohen thermischen und elektrischen Leitfähigkeit finden Kupferlegierungen in der Luft- und Raumfahrt Nischenanwendungen für Wärmetauscher und elektrische Komponenten. | Leitfähigkeit, gute elektrische Leitfähigkeit. | Wärmetauscher, elektrische Komponenten in Raumfahrzeugen. |
Molybdän (Mo): | Ein Refraktärmetall, das für seine außergewöhnliche Hochtemperaturfestigkeit und gute Wärmeleitfähigkeit bekannt ist. | Ausgezeichnete Hochtemperaturleistung, gute Wärmeleitfähigkeit. | Feuerfeste Komponenten für Raketentriebwerke, Hitzeschilde. |
Tantal (Ta): | Ein weiteres hochschmelzendes Metall mit einem sehr hohen Schmelzpunkt und ausgezeichneter Korrosionsbeständigkeit. | Ultrahoher Schmelzpunkt, gute Korrosionsbeständigkeit. | Tiegel für den Umgang mit geschmolzenem Metall, spezielle Hochtemperaturanwendungen. |
Nickellegierungen (Rene 41, Inconel 718): | Eine Familie von Hochleistungs-Nickellegierungen, die eine Kombination aus Festigkeit, Hochtemperaturleistung und guter Oxidationsbeständigkeit bieten. | Ausgezeichnete mechanische Eigenschaften, gute Hochtemperaturleistung. | Turbinenschaufeln, Scheiben und andere Hochtemperaturbauteile in Düsentriebwerken. |
Die Wahl des richtigen Metallpulvers
Auswahl des optimalen Metallpulvers für eine DMLS Die Bewerbung ist wie die Arbeit eines Heiratsvermittlers - sie erfordert eine sorgfältige Abwägung verschiedener Faktoren:
- Erforderliche Eigenschaften: Die spezifischen Anforderungen des Bauteils bestimmen die Wahl des Pulvers. Hochtemperatur-Triebwerksteile erfordern Pulver wie Inconel 625 oder Rene 41, während für leichte Flugwerkskomponenten möglicherweise Aluminiumlegierungen verwendet werden.
- Druckbarkeit: Nicht alle Metallpulver sind in Bezug auf die Druckfähigkeit gleich. Faktoren wie Partikelgröße, Form und Fließfähigkeit beeinflussen den Erfolg des DMLS-Prozesses erheblich.
- Kosten: Metallpulver sind sehr unterschiedlich im Preis. Titanlegierungen sind in der Regel teurer als beispielsweise rostfreier Stahl. Es muss ein Gleichgewicht zwischen Kosten und Leistungsanforderungen gefunden werden.
Vorteile und Beschränkungen von DMLS
DMLS bietet zwar eine Fülle von Vorteilen, ist aber nicht uneingeschränkt anwendbar:
Vorteile:
- Unerreichte Designfreiheit: DMLS erschließt bisher unvorstellbare Designmöglichkeiten und fördert Innovation und Leistungssteigerung.
- Gewichtsreduzierung: Die Fähigkeit, komplizierte, leichte Strukturen zu schaffen, führt in der Luft- und Raumfahrt zu einer erheblichen Gewichtsreduzierung.
- Rapid Prototyping und Iteration: DMLS beschleunigt den Entwicklungsprozess, indem es ein schnelles Prototyping und Designänderungen ermöglicht.
- Weniger Abfall: DMLS minimiert den Materialabfall im Vergleich zu herkömmlichen Verfahren und fördert die Nachhaltigkeit.
Beschränkungen:
- Materialverfügbarkeit: Die Auswahl an leicht verfügbaren Metallpulvern für das DMLS ist im Vergleich zu den traditionellen Fertigungsmaterialien noch in der Entwicklung begriffen.
- Oberfläche: DMLS-Teile können im Vergleich zu maschinell gefertigten Bauteilen eine rauere Oberfläche aufweisen, was möglicherweise zusätzliche Nachbearbeitungsschritte erfordert.
- Beschränkungen der Teilegröße: Die derzeitigen DMLS-Maschinen sind bei der Größe der Teile, die sie herstellen können, begrenzt.
- Kosten: DMLS bietet zwar langfristige Vorteile, aber die Anschaffungskosten für DMLS-Maschinen und Metallpulver können bei bestimmten Anwendungen höher sein als bei herkömmlichen Verfahren.
Die Zukunft von DMLS in der Luft- und Raumfahrt: Aufbruch zu neuen Höhen
Die Zukunft von DMLS in der Luft- und Raumfahrt ist geradezu berauschend. Mit den Fortschritten der Technologie können wir erwarten:
- Entwicklung von neuen Metallpulvern: Das Angebot an leicht erhältlichen Metallpulvern, die speziell für DMLS-Anwendungen entwickelt wurden, wird sich weiter vergrößern und die Grenzen des Machbaren erweitern.
- Größere Bauvolumina: DMLS-Maschinen mit größeren Bauräumen werden immer häufiger zum Einsatz kommen und die Herstellung noch größerer und komplexerer Bauteile für die Luft- und Raumfahrt ermöglichen.
- Verbesserte Oberflächengüte: Fortschritte in der DMLS-Technologie werden zu glatteren Oberflächen führen, so dass möglicherweise weniger umfangreiche Nachbearbeitungen erforderlich sind.
- Geringere Kosten: In dem Maße, wie die DMLS-Technologie reift und sich durchsetzt, werden die Gesamtkosten für DMLS-Maschinen und Metallpulver wahrscheinlich sinken, so dass die Technologie für eine breitere Palette von Luft- und Raumfahrtanwendungen zugänglicher wird.
DMLS ist nicht nur eine Fertigungstechnologie, sondern auch ein Katalysator für Innovationen in der Luft- und Raumfahrt. Indem DMLS Designfreiheit eröffnet, Gewicht reduziert und Entwicklungszyklen beschleunigt, treibt es uns in Richtung einer Zukunft mit leichteren, effizienteren und leistungsfähigeren Flugzeugen, Satelliten und Raumfahrzeugen. Der Himmel ist wirklich die Grenze für DMLS in der Luft- und Raumfahrt!
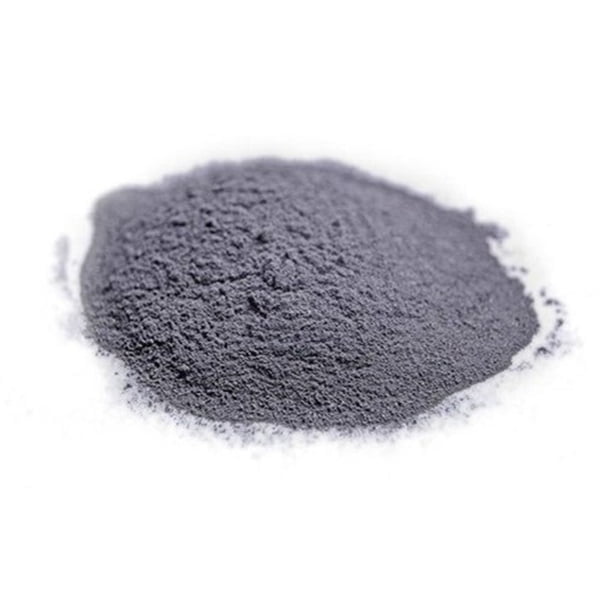
FAQ
F: Welche Vorteile bietet der Einsatz von DMLS für Anwendungen in der Luft- und Raumfahrt?
A: DMLS bietet zahlreiche Vorteile, wie z. B. unübertroffene Designfreiheit, Leichtbauweise, schnelles Prototyping und weniger Abfall im Vergleich zu herkömmlichen Fertigungsmethoden.
F: Was sind einige der Einschränkungen von DMLS?
A: Zu den Einschränkungen gehören die derzeitige Auswahl an leicht verfügbaren Metallpulvern, mögliche Probleme mit der Oberflächenbeschaffenheit, die begrenzte Größe der Teile und die höheren Anschaffungskosten im Vergleich zu einigen traditionellen Verfahren.
F: Was sind einige der zukünftigen Trends für DMLS in der Luft- und Raumfahrt?
A: Die Zukunft von DMLS in der Luft- und Raumfahrt ist unglaublich vielversprechend. Wir können mit Fortschritten in mehreren Schlüsselbereichen rechnen:
Entwicklung von neuen Metallpulvern: Die Hersteller von Metallpulvern arbeiten ständig an Innovationen und formulieren neue Pulver mit überlegenen Eigenschaften, die speziell auf das DMLS zugeschnitten sind. Dies wird die Konstruktionsmöglichkeiten noch erweitern und die Herstellung von Bauteilen mit einem noch besseren Verhältnis von Festigkeit zu Gewicht, verbesserter Hochtemperaturleistung und erhöhter Korrosionsbeständigkeit ermöglichen. Stellen Sie sich vor, dass exotische Legierungen die Grenzen des derzeit Möglichen verschieben, die Leistung von Triebwerken revolutionieren und zur Entwicklung von Luft- und Raumfahrzeugen der nächsten Generation führen.
Größere Bauvolumina: Die derzeitigen DMLS-Maschinen sind in der Größe der Teile, die sie herstellen können, begrenzt. Die Zukunft wird jedoch von Maschinen mit größeren Bauräumen geprägt sein. Dies wird ein entscheidender Faktor sein, denn damit können ganze Flugzeugteile, große Raketentriebwerkskomponenten und sogar komplette Satellitenstrukturen direkt mit einem 3D-Drucker hergestellt werden. Dies eröffnet die Möglichkeit, die Anzahl der Teile und die Komplexität der Montage erheblich zu reduzieren, was zu leichteren, effizienteren Raumfahrzeugen führt.
Verbesserte Oberflächengüte: DMLS-Teile bieten zwar eine außergewöhnliche Funktionalität, aber ihre Oberflächenbeschaffenheit kann im Vergleich zu traditionell bearbeiteten Bauteilen rauher sein. Dies kann manchmal zusätzliche Nachbearbeitungsschritte wie Polieren oder maschinelle Bearbeitung erforderlich machen. Fortschritte in der DMLS-Technologie führen jedoch zu glatteren Oberflächen direkt aus dem Druckprozess. Dies verringert nicht nur den Nachbearbeitungsbedarf, sondern kann auch die Leistung bestimmter Bauteile verbessern, indem glattere Luftströmungswege geschaffen oder die Reibung verringert wird.
Geringere Kosten: Da die DMLS-Technologie immer ausgereifter wird und die Akzeptanz zunimmt, dürften die Gesamtkosten für DMLS-Maschinen und Metallpulver sinken. Dadurch wird DMLS für eine breitere Palette von Anwendungen in der Luft- und Raumfahrt zu einer praktikablen Option, nicht nur für hochwertige, leistungsrelevante Komponenten. Diese Demokratisierung des DMLS hat das Potenzial, die Innovation in der gesamten Luft- und Raumfahrtindustrie zu beschleunigen.
Fazit
DMLS ist nicht nur eine Fertigungstechnologie, sondern eine Revolution in der Luft- und Raumfahrtindustrie. DMLS ermöglicht Designfreiheit, reduziert das Gewicht, beschleunigt die Entwicklungszyklen und fördert die Nachhaltigkeit. Damit treibt DMLS uns in Richtung einer Zukunft mit leichteren, effizienteren und leistungsfähigeren Fluggeräten. Mit der Weiterentwicklung der DMLS-Technologie sind die Möglichkeiten wirklich grenzenlos. Die Zukunft der Luft- und Raumfahrt wird zweifelsohne von DMLS geprägt, und der Himmel ist wahrlich nicht die Grenze - er ist erst der Anfang!
Teilen auf
MET3DP Technology Co., LTD ist ein führender Anbieter von additiven Fertigungslösungen mit Hauptsitz in Qingdao, China. Unser Unternehmen ist spezialisiert auf 3D-Druckgeräte und Hochleistungsmetallpulver für industrielle Anwendungen.
Fragen Sie an, um den besten Preis und eine maßgeschneiderte Lösung für Ihr Unternehmen zu erhalten!
Verwandte Artikel
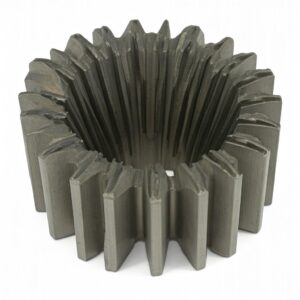
Hochleistungs-Düsenschaufelsegmente: Revolutionierung der Turbineneffizienz mit 3D-Metalldruck
Mehr lesen "Über Met3DP
Aktuelles Update
Unser Produkt
KONTAKT US
Haben Sie Fragen? Senden Sie uns jetzt eine Nachricht! Wir werden Ihre Anfrage mit einem ganzen Team nach Erhalt Ihrer Nachricht bearbeiten.
Holen Sie sich Metal3DP's
Produkt-Broschüre
Erhalten Sie die neuesten Produkte und Preislisten
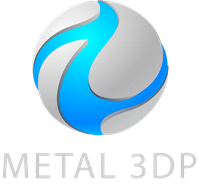
Metallpulver für 3D-Druck und additive Fertigung