Metall-Spritzgießen (MIM)
Inhaltsübersicht
Stellen Sie sich ein Herstellungsverfahren vor, das die Detailgenauigkeit und Designfreiheit des Kunststoffspritzgießens mit der unvergleichlichen Festigkeit und Haltbarkeit von Metall verbindet. Das ist die Magie von Metall-Spritzgießen (MIM), die die Welt der Metallbearbeitung grundlegend verändert.
Was ist Metal Injection Molding (MIM)?
MIM ist eine endkonturnahe Fertigungstechnik, bei der eine einzigartige Mischung aus Metallpulver und einem polymeren Bindemittel verwendet wird. Diese Kombination, die als Feedstock bezeichnet wird, verhält sich ähnlich wie eine formbare Paste. Beim MIM-Verfahren wird dieses Ausgangsmaterial unter hohem Druck strategisch in einen Formhohlraum eingespritzt, wodurch die gewünschte komplizierte Geometrie nachgebildet wird. Im Folgenden wird das MIM-Verfahren in seine wichtigsten Phasen unterteilt:
- Aufbereitung von Rohstoffen: Fein pulverisiertes Metall, in der Regel rostfreier Stahl, Stahllegierungen oder sogar exotische Materialien wie Wolframkarbid, wird sorgfältig mit einem Bindersystem gemischt. Dieses Bindemittel gewährleistet die Fließfähigkeit der Mischung beim Spritzgießen.
- Gießen: Das vorbereitete Ausgangsmaterial wird unter hohem Druck in einen präzise gestalteten Formhohlraum eingespritzt. Auf diese Weise wird die komplizierte, endkonturnahe Form des gewünschten Metallteils nachgebildet.
- Entbinden: Nach dem Gießen muss das Bindemittel vom Formteil entfernt werden. Dieser heikle Prozess, der oft als Entbindern bezeichnet wird, kann je nach gewähltem Bindemittelsystem thermische Techniken (Erhitzen) oder Lösungsmittelentbindern beinhalten.
- Sintern: Das entbinderte Teil, das nun eine zerbrechliche Struktur aus Metallpulver ist, wird einem Hochtemperatursinterprozess in einer kontrollierten Atmosphäre unterzogen. In diesem entscheidenden Schritt verschmelzen die Metallpartikel miteinander und erreichen so die gewünschte Festigkeit und Dichte für das endgültige Bauteil.
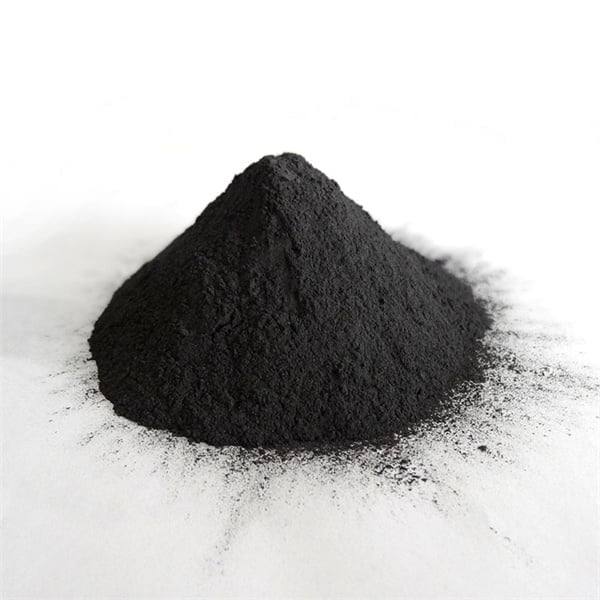
Die Vorteile von Metall-Spritzgießen (MIM)
MIM bietet eine Reihe von überzeugenden Vorteilen, die es zu einem gefragten Verfahren für verschiedene Branchen machen:
- Komplexe Geometrien: Im Gegensatz zu herkömmlichen Bearbeitungsverfahren, die mit komplizierten Formen zu kämpfen haben, eignet sich MIM hervorragend zur Herstellung von Bauteilen mit komplexen Merkmalen, engen Toleranzen und dünnen Wänden. Dies öffnet Türen für innovative Designs, die mit konventionellen Methoden bisher nur schwer oder gar nicht zu realisieren waren.
- Hohe Präzision und Reproduzierbarkeit: MIM nutzt die Präzision des Spritzgießens, was zu äußerst konsistenten Teilen mit minimalen Maßabweichungen führt. Dies führt zu einer zuverlässigen Leistung und einem geringeren Nachbearbeitungsbedarf.
- Massenproduktion: MIM ist ein gut geeignetes Verfahren für die Produktion großer Stückzahlen. Sobald die Form eingerichtet ist, kann MIM eine große Anzahl identischer Teile effizient herstellen, was es ideal für Anwendungen macht, die gleichbleibende Qualität und große Mengen erfordern.
- Vielseitigkeit der Materialien: MIM verfügt über eine breite Palette kompatibler Werkstoffe, von gewöhnlichen rostfreien Stählen und Werkzeugstählen bis hin zu exotischen Optionen wie Titan und Inconel. Dies ermöglicht die Auswahl des optimalen Materials auf der Grundlage der spezifischen Festigkeit, Korrosionsbeständigkeit oder anderer Leistungsanforderungen der jeweiligen Anwendung.
- Kosten-Nutzen-Verhältnis: Im Vergleich zu herkömmlichen Bearbeitungstechniken, insbesondere bei komplexen Geometrien, kann MIM erhebliche Kosteneinsparungen ermöglichen. Durch die Möglichkeit der endkonturnahen Formgebung wird der Materialabfall minimiert und der Bedarf an umfangreichen Bearbeitungsvorgängen verringert.
Anwendungen des Metall-Spritzgießens (MIM)
Die vielfältigen Vorteile von MIM haben es zu einer beliebten Wahl in einem breiten Spektrum von Branchen gemacht. Hier sind einige prominente Beispiele:
- Automobilindustrie: MIM kommt in der Automobilindustrie zum Einsatz, wo komplizierte Bauteile wie Zahnräder, Kettenräder, Ventilkomponenten und Teile des Kraftstoffsystems hergestellt werden, die für ihre Haltbarkeit und Maßgenauigkeit bekannt sind.
- Medizinische Geräte: Da bestimmte MIM-Materialien biokompatibel sind, eignen sie sich hervorragend für medizinische Anwendungen. MIM wird zur Herstellung komplizierter chirurgischer Instrumente, Implantate und Komponenten für verschiedene medizinische Geräte verwendet.
- Unterhaltungselektronik: Die Fähigkeit, kleine, komplexe Teile mit hoher Präzision herzustellen, macht MIM ideal für die Unterhaltungselektronikindustrie. MIM findet Anwendung in Steckverbindern, Gehäusen und internen Komponenten für verschiedene elektronische Geräte.
- Luft- und Raumfahrt & Verteidigung: Die anspruchsvollen Anforderungen der Luft- und Raumfahrt und des Verteidigungssektors sind für MIM gut geeignet. MIM produziert hochfeste, leichte Komponenten für Flugzeuge, Raumfahrzeuge und Waffensysteme.
Über die Vorteile hinaus: Überlegungen zu MIM
MIM bietet zwar eine Fülle von Vorteilen, aber es ist wichtig, einige Faktoren zu berücksichtigen, bevor Sie sich für eine bestimmte Anwendung entscheiden:
- Beschränkungen der Teilegröße: Die maximale Größe der Teile, die mit MIM hergestellt werden können, ist derzeit begrenzt. Teile, die ein bestimmtes Volumen überschreiten, eignen sich möglicherweise besser für herkömmliche Metallbearbeitungsverfahren.
- Materielle Beschränkungen: Obwohl MIM eine breite Palette von Werkstoffen bietet, sind einige exotische oder spezielle Legierungen möglicherweise nicht ohne weiteres verfügbar oder durch MIM nicht kosteneffizient.
- Entwicklungskosten: Die Einrichtung des MIM-Verfahrens für ein neues Bauteil erfordert Vorabinvestitionen in die Werkzeugentwicklung und Prozessoptimierung. Dieser Kostenfaktor muss gegen das potenzielle Produktionsvolumen und die langfristigen Vorteile abgewogen werden.
MIM verstehen: Eine technische Vertiefung
Für diejenigen, die sich für die technischen Feinheiten von MIM interessieren, hier ein genauerer Blick auf einige wichtige Aspekte:
Auswahl der Ausgangsstoffe: Die Auswahl des richtigen Ausgangsmaterials ist entscheidend für den Erfolg von MIM. Hier sind einige wichtige Aspekte zu berücksichtigen:
- Metall-Pulver:
- Partikelgröße und -verteilung: Die Größe und Verteilung des Metallpulvers hat einen erheblichen Einfluss auf die endgültigen Eigenschaften des Teils. Feinere Pulver ermöglichen in der Regel engere Toleranzen und glattere Oberflächen, können aber aufgrund von Problemen mit der Fließfähigkeit auch schwieriger zu verarbeiten sein. Eine ausgewogene Partikelgrößenverteilung wird oft bevorzugt.
- Morphologie des Pulvers: Auch die Form der Metallpartikel spielt eine Rolle. Kugelförmige Pulver neigen dazu, besser zu fließen und sich dichter zu verdichten, was zu einer höheren Festigkeit und Maßgenauigkeit führt.
- Bindemittel-System: Das Bindemittelsystem fungiert als temporärer Klebstoff, der das Metallpulver während des Formens und Entbindens zusammenhält. Verschiedene Bindemittelsysteme bieten unterschiedliche Eigenschaften, wie z. B. thermische Stabilität, Entbinderungsverhalten und Kompatibilität mit dem gewählten Entbinderungsverfahren.
Formenbau für MIM:
MIM-Formen haben Ähnlichkeiten mit Kunststoff-Spritzgießformen, erfordern jedoch besondere Überlegungen zum Verhalten von Metallpulver:
- Tor-Design: Die Konstruktion der Anschnitte, die den Eintritt des Materials in den Formhohlraum bilden, muss einen ordnungsgemäßen Fluss gewährleisten und Turbulenzen, die zu Defekten führen können, minimieren.
- Entlüftung: Entlüftungskanäle sind entscheidend dafür, dass eingeschlossene Luft während der Injektion entweichen kann, um Hohlräume zu vermeiden und eine vollständige Füllung des Teils zu gewährleisten.
- Entwurfswinkel: Entformungsschrägen an den Formwänden sind wichtig, um die leichte Entnahme des Formteils nach dem Abkühlen zu erleichtern.
Entbinderungstechniken bei MIM:
Wie bereits erwähnt, ist das Entbindern der entscheidende Schritt zur Entfernung des Bindemittels aus dem Formteil. Im Folgenden werden die beiden wichtigsten Entbinderungsverfahren beschrieben:
- Thermisches Entbindern: Bei diesem Verfahren wird das Formteil in einer kontrollierten Atmosphäre schrittweise erhitzt. Mit steigender Temperatur zersetzt sich das Bindemittel und hinterlässt die Metallpulverstruktur. Das Erhitzungsprofil muss sorgfältig geplant werden, um eine vollständige Entfernung des Binders zu gewährleisten, ohne die empfindliche Metallstruktur zu beschädigen.
- Lösungsmittel-Entbinderung: Bei dieser Technik wird ein Lösungsmittel verwendet, das das Bindemittelsystem selektiv auflöst. Das Formteil wird in das Lösungsmittel getaucht, wodurch das Bindemittel ausgelaugt wird, während das Metallpulver intakt bleibt. Das Entbindern mit Lösungsmitteln kann schneller sein als das thermische Entbindern, erfordert aber unter Umständen besondere Überlegungen zur Handhabung und Entsorgung des verwendeten Lösungsmittels.
Sintern bei MIM:
Das Sintern ist die letzte Phase des MIM-Prozesses, in der sich das entbinderte Metallpulver in ein festes, funktionales Bauteil verwandelt. Während des Sinterns wird das Teil hohen Temperaturen (in der Regel im Bereich von 1/2 bis 2/3 des Schmelzpunkts des Metalls) in einer kontrollierten Atmosphäre ausgesetzt. Diese hohe Temperatur fördert die Diffusionsbindung zwischen den Metallpartikeln, was zu einer Verdichtung und einer deutlichen Verbesserung der Festigkeit und anderer mechanischer Eigenschaften führt.
Qualitätskontrolle bei MIM:
Die Aufrechterhaltung einer gleichbleibenden Qualität ist bei der MIM-Produktion von größter Bedeutung. Hier sind einige wichtige Maßnahmen zur Qualitätskontrolle:
- Charakterisierung von Rohstoffen: Regelmäßige Prüfungen der Eigenschaften des Ausgangsmaterials, wie z. B. der Größenverteilung des Metallpulvers und des Bindemittelgehalts, gewährleisten ein einheitliches Materialverhalten während der Verarbeitung.
- Prüfung der Abmessungen: Die Abmessungen der Gussteile werden sorgfältig geprüft, um sicherzustellen, dass sie den Konstruktionsspezifikationen entsprechen und enge Toleranzen eingehalten werden.
- Dichtemessung: Die Dichte der gesinterten Teile ist ein entscheidender Indikator für deren Festigkeit und Leistung. Zur Messung der Dichte können verschiedene Verfahren wie das archimedische Prinzip oder die Pyknometrie eingesetzt werden.
- Mikrostrukturanalyse: Die mikroskopische Untersuchung der Mikrostruktur des gesinterten Teils gibt Aufschluss über Korngröße, Porosität und mögliche Defekte.
Die Zukunft der Metall-Spritzgießen
MIM ist eine Technologie, die sich ständig weiterentwickelt, wobei sich die Forschungs- und Entwicklungsarbeiten auf folgende Bereiche konzentrieren:
- Erweiterung der Materialpalette: Die Erforschung neuer Materialien und Bindemittelsysteme, die mit MIM kompatibel sind, erweitert die Anwendungsmöglichkeiten dieses vielseitigen Verfahrens.
- Verbesserte Prozesseffizienz: Die Forschung zielt auf die Optimierung der Entbinderungs- und Sinterungsphasen ab, um die Zykluszeiten zu verkürzen und die Gesamteffizienz der Produktion zu steigern.
- Erweiterte Teilekomplexität: Die Entwicklungen im Formenbau und in der Materialwissenschaft verschieben die Grenzen der durch MIM erreichbaren Teilekomplexität.
Metall-Spritzgießen bietet eine einzigartige Mischung aus Designfreiheit, Materialvielfalt und Kosteneffizienz für eine Vielzahl von Branchen. Da die Technologie immer weiter ausreift, können wir mit noch mehr innovativen Anwendungen und Fortschritten in der spannenden Welt des MIM rechnen.
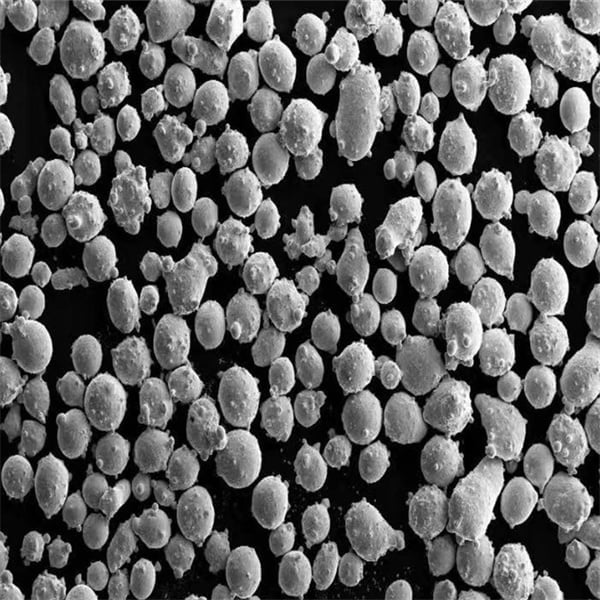
FAQ
Tabelle 1: Häufig gestellte Fragen zum Metall-Spritzgießen (MIM)
Frage | Antwort |
---|---|
Was sind die typischen Größenbeschränkungen für MIM-Teile? | Die maximale Größe von MIM-Teilen ist im Allgemeinen auf einige Kubikzoll begrenzt. Diese Begrenzung ist auf Probleme mit dem Materialfluss und der Gewährleistung einer gleichmäßigen Entbinderung bei größeren Teilen zurückzuführen. |
Kann MIM für das Prototyping verwendet werden? | Ja, MIM kann eine praktikable Option für das Prototyping komplexer Metallteile sein, vor allem wenn ein hohes Maß an Genauigkeit und Treue zum endgültigen Design erforderlich ist. Allerdings müssen die Vorlaufkosten für die Werkzeugentwicklung berücksichtigt werden. |
Was sind die Vorteile von MIM im Vergleich zur herkömmlichen Bearbeitung? | MIM bietet mehrere Vorteile gegenüber der herkömmlichen Bearbeitung, darunter: Fähigkeit zur Herstellung komplexer Geometrien mit engen Toleranzen Größere Gestaltungsfreiheit für komplizierte Merkmale Hohe Präzision und Wiederholbarkeit für konsistente Teile Effizienz der Massenproduktion für große Mengen Reduzierter Materialabfall im Vergleich zu subtraktiven Techniken |
Was sind die Nachteile von MIM im Vergleich zur traditionellen Bearbeitung? | Bei MIM sind auch einige Einschränkungen zu beachten: Begrenzung der Teilegröße im Vergleich zu Techniken wie Gießen oder Schmieden Materialbeschränkungen für bestimmte exotische oder Speziallegierungen Höhere Vorlaufkosten durch die Entwicklung von Formen Die Oberflächenbeschaffenheit entspricht möglicherweise nicht den außergewöhnlich glatten Oberflächen, die durch Polieren oder Schleifen erreicht werden können. |
Welche Faktoren sind bei der Entscheidung zwischen MIM und traditioneller Metallbearbeitung zu berücksichtigen? | Die ideale Wahl hängt von Ihrer spezifischen Anwendung ab. Hier sind einige wichtige Faktoren zu berücksichtigen: Komplexität der Teilegeometrie Anforderungen an das Produktionsvolumen Anforderungen an die Materialauswahl Kostenüberlegungen, einschließlich Vorabinvestitionen und potenzielle Einsparungen Anforderungen an die Oberflächenbeschaffenheit |
Was sind die zukünftigen Trends in der MIM-Technologie? | Die Forschungs- und Entwicklungsanstrengungen im Bereich MIM konzentrieren sich auf die Erweiterung des Materialspektrums, die Verbesserung der Prozesseffizienz für kürzere Zykluszeiten und die Erweiterung der Grenzen der erreichbaren Teilekomplexität. |
Was sind einige typische Anwendungen von MIM? | MIM findet in einer Vielzahl von Branchen Anwendung, unter anderem in der Automobilindustrie: Automobilindustrie (Zahnräder, Kettenräder, Ventilkomponenten) Medizinische Geräte (chirurgische Instrumente, Implantate) Unterhaltungselektronik (Steckverbinder, Gehäuse) Luft- und Raumfahrt & Verteidigung (hochfeste, leichte Komponenten) |
Welche verschiedenen Arten von Rohstoffen werden bei MIM verwendet? | MIM-Ausgangsmaterial besteht in der Regel aus einem Metallpulver (z. B. Edelstahl, Stahllegierungen, Titan), das mit einem polymeren Bindemittelsystem gemischt wird. Die spezifische Art des Metallpulvers und des Bindemittels hängt von den gewünschten Endeigenschaften des Teils ab. |
Welche verschiedenen Entbinderungsverfahren werden bei MIM eingesetzt? | Es gibt zwei grundlegende Entbinderungsverfahren: Thermische Entbinderung: Schrittweises Erhitzen zur Entfernung des Bindemittels. Lösungsmittel-Entbinderung: Verwendung eines Lösungsmittels, um das Bindemittel selektiv aufzulösen. |
Die Wahl des richtigen Verfahrens: MIM vs. Traditionelle Metallbearbeitung
Die Entscheidung zwischen MIM und traditionellen Metallbearbeitungstechniken hängt von verschiedenen anwendungsspezifischen Faktoren ab. Im Folgenden finden Sie einige wichtige Überlegungen, die Ihnen bei Ihrer Wahl helfen können:
- Geometrie des Teils: Wenn Ihr Bauteil komplexe Merkmale, enge Toleranzen und komplizierte Details aufweist, bietet MIM einen erheblichen Vorteil.
- Produktionsvolumen: Für die Produktion hoher Stückzahlen ist MIM aufgrund seiner Effizienz und Wiederholbarkeit eine überzeugende Option.
- Auswahl der Materialien: Stellen Sie sicher, dass das von Ihnen benötigte Material mit MIM kompatibel ist. Wenn Sie eine exotische Legierung benötigen, die im MIM-Verfahren nicht ohne Weiteres erhältlich ist, ist die traditionelle Metallbearbeitung möglicherweise der richtige Weg.
- Kostenüberlegungen: Berücksichtigen Sie die Vorlaufkosten für die Entwicklung von MIM-Formen im Vergleich zum potenziellen Materialabfall und den längeren Produktionszeiten herkömmlicher Techniken für komplexe Teile.
- Anforderungen an die Oberflächenbeschaffenheit: Wenn es auf eine makellose Oberfläche ankommt, sind unter Umständen traditionelle Techniken wie Polieren erforderlich.
Schlussfolgerung
Metal Injection Molding (MIM) ist ein leistungsfähiges und vielseitiges Fertigungsverfahren, das eine einzigartige Kombination aus Designfreiheit, Materialoptionen und Kosteneffizienz für eine breite Palette von Anwendungen bietet. Wenn Sie die Vorteile und Grenzen des Verfahrens kennen und wissen, wie es sich im Vergleich zu herkömmlichen Metallbearbeitungsverfahren verhält, können Sie fundierte Entscheidungen treffen, um MIM für Ihre spezifischen Anforderungen zu nutzen und das Potenzial für innovative und leistungsstarke Metallkomponenten zu erschließen.
Teilen auf
MET3DP Technology Co., LTD ist ein führender Anbieter von additiven Fertigungslösungen mit Hauptsitz in Qingdao, China. Unser Unternehmen ist spezialisiert auf 3D-Druckgeräte und Hochleistungsmetallpulver für industrielle Anwendungen.
Fragen Sie an, um den besten Preis und eine maßgeschneiderte Lösung für Ihr Unternehmen zu erhalten!
Verwandte Artikel
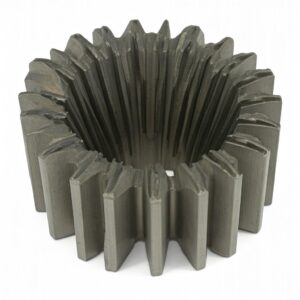
Hochleistungs-Düsenschaufelsegmente: Revolutionierung der Turbineneffizienz mit 3D-Metalldruck
Mehr lesen "Über Met3DP
Aktuelles Update
Unser Produkt
KONTAKT US
Haben Sie Fragen? Senden Sie uns jetzt eine Nachricht! Wir werden Ihre Anfrage mit einem ganzen Team nach Erhalt Ihrer Nachricht bearbeiten.
Holen Sie sich Metal3DP's
Produkt-Broschüre
Erhalten Sie die neuesten Produkte und Preislisten
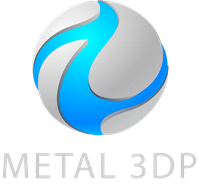
Metallpulver für 3D-Druck und additive Fertigung