Optische Bänke für Satelliten: Revolutionierung der Luft- und Raumfahrt mit 3D-Metalldruck
Inhaltsübersicht
Einleitung - Die entscheidende Rolle optischer Satellitenbänke in der modernen Luft- und Raumfahrt
Optische Bänke für Satelliten dienen als stabiles und präzises Fundament für wichtige Instrumente an Bord von Satelliten, einschließlich Teleskopen, Kameras und Spektrometern. Diese komplizierten Strukturen erfordern außergewöhnliche Dimensionsstabilität, geringes Gewicht und Wärmemanagement, um die genaue Erfassung und Analyse von Daten aus dem Weltraum zu gewährleisten. In der anspruchsvollen Umgebung des Orbits, wo Temperaturschwankungen und mechanische Belastungen konstant sind, ist die Integrität der optischen Bank für den Erfolg der Mission von größter Bedeutung. Herkömmliche Fertigungsmethoden stoßen bei diesen hochspezialisierten Komponenten oft an Grenzen, was die Komplexität des Designs, die Materialeffizienz und die Produktionszeiten angeht.
Wozu dienen optische Bänke für Satelliten? - Vielfältige Anwendungen in der Weltraumbeobachtung und Kommunikation
Optische Bänke für Satelliten sind das Rückgrat einer breiten Palette von weltraumgestützten Anwendungen. Sie bieten die stabile Plattform, die für:
- Erdbeobachtung: Unterstützung von hochauflösenden Kameras für Umweltüberwachung, Wettervorhersage und landwirtschaftliche Analysen.
- Weltraumteleskope: Beibehaltung der Ausrichtung von Spiegeln und Linsen für die astronomische Forschung und die Erforschung des Weltraums.
- Kommunikationssatelliten: Sicherstellung der präzisen Positionierung von optischen Transceivern für Laserkommunikation und Datenrelais.
- Fernerkundung: Erleichterung des Betriebs von Spektrometern und anderen Instrumenten für atmosphärische Studien und Ressourcenmanagement.
- Militär und Überwachung: Bereitstellung stabiler Plattformen für Aufklärungs- und Nachrichtengewinnungsinstrumente.
Die spezifischen Anforderungen an eine optische Bank variieren je nach Verwendungszweck, aber die Notwendigkeit eines hohen Verhältnisses von Steifigkeit zu Gewicht, thermischer Stabilität und Maßgenauigkeit bleibt bei all diesen kritischen Verwendungszwecken gleich.
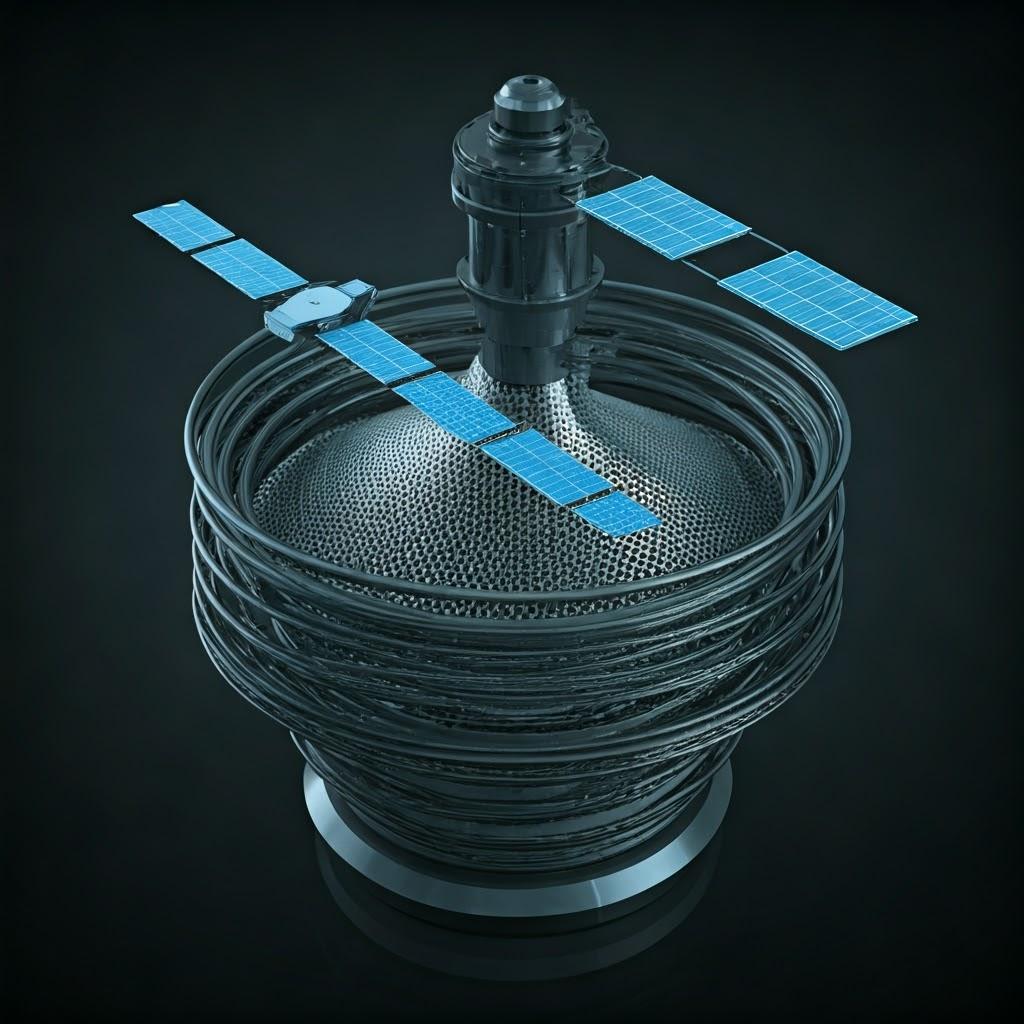
Warum 3D-Metalldruck für optische Bänke für Satelliten verwenden? - Freisetzung von Designfreiheit und Leistungsvorteilen
Metall 3D-Druckauch bekannt als additive Fertigung von Metallen, bietet einen neuen Ansatz für die Herstellung von optischen Bänken für Satelliten und überwindet viele der Einschränkungen, die mit herkömmlichen Fertigungsverfahren verbunden sind. Die Vorteile sind erheblich:
- Gestaltungsfreiheit und Optimierung: Die additive Fertigung ermöglicht die Herstellung komplexer Geometrien und komplizierter interner Strukturen, die mit herkömmlichen Methoden wie der maschinellen Bearbeitung nicht oder nur mit hohem Kostenaufwand zu erreichen sind. Dies ermöglicht es Ingenieuren, ihre Entwürfe im Hinblick auf Gewichtsreduzierung, verbesserte Steifigkeit und integrierte Funktionen wie Kühlkanäle und Montageschnittstellen zu optimieren.
- Gewichtsreduzierung: In der Luft- und Raumfahrtindustrie bedeutet jedes eingesparte Kilogramm eine erhebliche Kostenreduzierung bei den Start- und Betriebskosten. Der 3D-Metalldruck ermöglicht die Herstellung von leichten Gitterstrukturen und topologisch optimierten Designs, wodurch die Gesamtmasse der optischen Bank reduziert wird, ohne ihre strukturelle Integrität zu beeinträchtigen.
- Materialeffizienz: Bei den additiven Fertigungsverfahren werden die Teile Schicht für Schicht aufgebaut, wobei nur das für das endgültige Bauteil benötigte Material verwendet wird. Dadurch wird der Materialabfall im Vergleich zu subtraktiven Verfahren, bei denen erhebliche Mengen an Material aus einem festen Block entfernt werden, drastisch reduziert.
- Schnelle Prototypenherstellung und Produktion: Der 3D-Metalldruck beschleunigt den Design- und Fertigungszyklus. Prototypen können schnell für Tests und Iterationen hergestellt werden, und komplexe Kleinserien können im Vergleich zu herkömmlichen werkzeugabhängigen Verfahren mit kürzeren Vorlaufzeiten gefertigt werden. Diese Flexibilität ist in der schnelllebigen Luft- und Raumfahrtbranche von entscheidender Bedeutung.
- Personalisierung und Komplexität: Jede Satellitenmission kann einzigartige Anforderungen an ihre optische Bank stellen. Der 3D-Metalldruck ermöglicht hochgradig individuelle Konstruktionen, die auf spezifische Instrumentennutzlasten und Missionsprofile zugeschnitten sind, ohne dass teure Umrüstungen erforderlich sind.
- Integrierte Funktionalitäten: Merkmale wie Wärmemanagementkanäle, Kabelführung und Montagepunkte können direkt in das 3D-gedruckte Design der optischen Bank integriert werden, wodurch die Anzahl der separaten Komponenten und Montageschritte reduziert wird. Dies führt zu einer höheren Zuverlässigkeit und einer geringeren Gesamtkomplexität des Systems.
- Verbesserte Leistung: Durch die Auswahl fortschrittlicher Metallpulver und die Optimierung des Designs für die additive Fertigung können optische Bänke ein besseres Verhältnis von Steifigkeit zu Gewicht, thermischer Stabilität und Maßgenauigkeit erreichen, was zu einer verbesserten Leistung der optischen Instrumente des Satelliten führt.
Metal3DP Technology Co. LTD ist ein Vorreiter bei der Bereitstellung dieser fortschrittlichen Lösungen für die additive Fertigung von Metallen. Unsere branchenführenden SEBM-Drucker und Hochleistungsmetallpulver eignen sich ideal für die anspruchsvollen Anforderungen von Luft- und Raumfahrtanwendungen wie optische Bänke für Satelliten. Wir ermöglichen unseren Kunden eine unvergleichliche Designfreiheit und Leistung.
Empfohlene Materialien und warum sie wichtig sind - Scalmalloy® und AlSi10Mg für optimale Leistung
Die Wahl des Materials ist entscheidend für die Leistung einer optischen Bank für Satelliten. Metall3DP bietet eine Reihe von hochwertigen Metallpulvern an, die für die additive Fertigung optimiert sind, darunter zwei außergewöhnliche Legierungen, die für diese Anwendung gut geeignet sind: Scalmalloy® und AlSi10Mg.
- Scalmalloy®: Diese hochfeste Aluminium-Magnesium-Scandium-Legierung wurde speziell für Leichtbauanwendungen entwickelt, ohne dabei an Festigkeit und Steifigkeit einzubüßen. Zu ihren wichtigsten Vorteilen für optische Bänke für Satelliten gehören:
- Außergewöhnliches Verhältnis von Stärke zu Gewicht: Scalmalloy® bietet eine deutlich höhere Festigkeit als herkömmliche Aluminiumlegierungen bei gleichzeitig geringerer Dichte und ist damit ideal für die Reduzierung der Masse kritischer Komponenten in der Luft- und Raumfahrt.
- Hohe Steifigkeit: Der hohe Elastizitätsmodul von Scalmalloy® gewährleistet eine ausgezeichnete Dimensionsstabilität, die für die Aufrechterhaltung der Ausrichtung empfindlicher optischer Instrumente unter wechselnden thermischen und mechanischen Belastungen entscheidend ist.
- Gute Schweißbarkeit und Korrosionsbeständigkeit: Diese Eigenschaften sind wichtig für die Nachbearbeitung und die langfristige Zuverlässigkeit in der rauen Weltraumumgebung.
- Ausgezeichnetes Ermüdungsverhalten: Scalmalloy® kann den zyklischen Belastungen beim Start und bei Orbitalmanövern standhalten.
- AlSi10Mg: Diese Aluminium-Silizium-Magnesium-Legierung ist aufgrund ihrer hervorragenden Verarbeitbarkeit und ihrer guten mechanischen Eigenschaften ein weit verbreitetes Material im 3D-Metalldruck. Seine Vorteile für optische Bänke für Satelliten umfassen:
- Gute Festigkeit und Duktilität: AlSi10Mg bietet ein gutes Gleichgewicht zwischen Festigkeit und Duktilität und eignet sich daher für Bauteile, die mäßigen Belastungen und Vibrationen standhalten müssen.
- Ausgezeichnete Wärmeleitfähigkeit: Diese Eigenschaft ist vorteilhaft für die Steuerung der Wärmeableitung von empfindlichen optischen Instrumenten.
- Gute Korrosionsbeständigkeit: AlSi10Mg weist eine gute Beständigkeit gegen atmosphärische Korrosion auf, was für die lange Lebensdauer von Satellitenkomponenten wichtig ist.
- Kosten-Nutzen-Verhältnis: Im Vergleich zu einigen anderen für die Luft- und Raumfahrt geeigneten Legierungen kann AlSi10Mg für bestimmte Anwendungen eine kostengünstigere Option darstellen.
Metall3DP bietet AlSi10Mg-Pulver an, die sowohl für das Laser- als auch für das Elektronenstrahl-Pulverbettschmelzen optimiert sind und eine hohe Dichte und gleichbleibende Eigenschaften der gedruckten Teile gewährleisten. Unser umfassendes Angebot an hochwertigen Metallpulvern deckt die unterschiedlichsten Anforderungen der Luft- und Raumfahrt ab.
Durch die Nutzung der einzigartigen Eigenschaften von Scalmalloy® und AlSi10Mg mit Metal3DPs mit der fortschrittlichen 3D-Metalldrucktechnologie können Hersteller in der Luft- und Raumfahrt optische Bänke für Satelliten herstellen, die leichter, fester, stabiler und leistungsfähiger sind als solche, die mit herkömmlichen Methoden hergestellt werden. Unser Know-how in der additiven Fertigung von Metall und unser Engagement für branchenführende Lösungen machen Metall3DP ein zuverlässiger Partner für die Luft- und Raumfahrtindustrie. Besuchen Sie unsere Website, um mehr über unsere 3D-Metalldruck-Dienstleistungen zu erfahren: https://met3dp.com/metal-3d-printing/
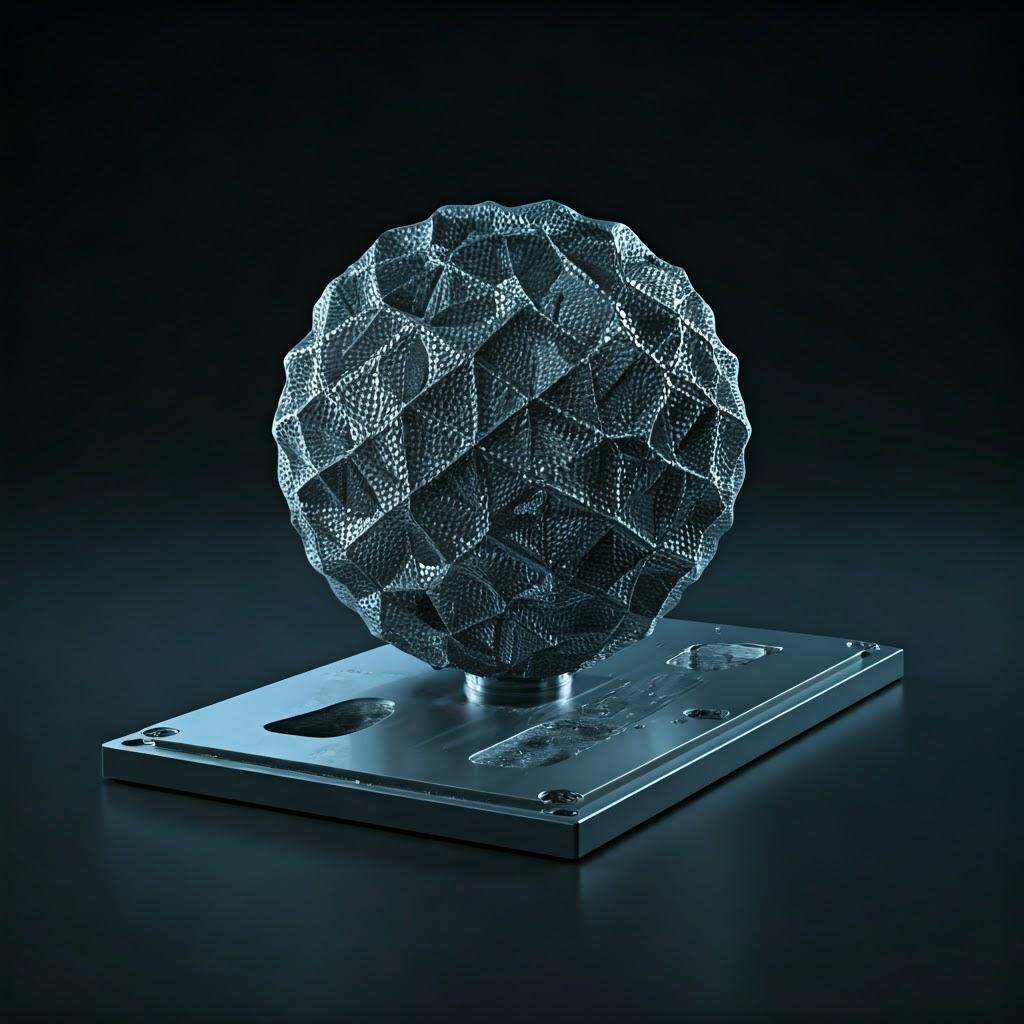
Konstruktionsüberlegungen für die additive Fertigung - Optimierung von Geometrie, Wanddicke und Stützanforderungen
Das Design für die additive Fertigung von Metallen erfordert eine andere Denkweise als die traditionellen subtraktiven Verfahren. Um die Möglichkeiten des 3D-Drucks voll auszuschöpfen und eine optimale Leistung für optische Satellitenbänke zu erzielen, müssen mehrere wichtige Designüberlegungen berücksichtigt werden:
- Topologie-Optimierung: Dieser rechnergestützte Entwurfsansatz ermöglicht es Ingenieuren, die effizienteste Materialverteilung für einen bestimmten Satz von Lasten und Einschränkungen zu ermitteln. Durch die Entfernung von unnötigem Material kann die Topologieoptimierung zu einer erheblichen Gewichtsreduzierung führen, während die strukturelle Steifigkeit beibehalten oder sogar verbessert wird. Der 3D-Metalldruck eignet sich hervorragend für die Realisierung dieser komplexen, organisch anmutenden Geometrien.
- Gitterförmige Strukturen: Die Einbeziehung von Gitterstrukturen in das Design der optischen Bank ist eine weitere effektive Möglichkeit, das Gewicht zu reduzieren, ohne die Steifigkeit zu beeinträchtigen. Diese komplizierten, sich wiederholenden zellularen Strukturen bieten ein hohes Verhältnis von Oberfläche zu Volumen und können auf spezifische Belastungsanforderungen zugeschnitten werden. Die additive Fertigung ist für die Herstellung dieser komplexen Innengeometrien unerlässlich.
- Wandstärke und Riffelung: Die sorgfältige Auswahl der Wandstärke ist entscheidend für das Gleichgewicht zwischen Gewicht und struktureller Integrität. Dünne Wände können das Gewicht reduzieren, sind aber möglicherweise anfällig für Knicken oder Vibrationen. Der Einbau von Rippen und Versteifungselementen kann die Steifigkeit erhöhen, ohne die Masse wesentlich zu erhöhen. der 3D-Druck ermöglicht die präzise Platzierung und Ausrichtung dieser Merkmale.
- Unterstützende Strukturen: Beim 3D-Metalldruck sind häufig Stützstrukturen erforderlich, um eine Verformung des Teils während des Bauprozesses zu verhindern, insbesondere bei überhängenden Merkmalen und komplexen Geometrien. Das Design dieser Stützen sollte den Materialverbrauch minimieren und nach dem Druck leicht zu entfernen sein, ohne die Oberfläche des Teils zu beschädigen. Software-Tools können bei der Optimierung der Support-Generierung helfen.
- Orientierung und Gebäuderichtung: Die Ausrichtung des Teils auf der Bauplattform und die Richtung, in der es gedruckt wird, können die Oberflächengüte, die mechanischen Eigenschaften und den Bedarf an Stützstrukturen erheblich beeinflussen. Die sorgfältige Berücksichtigung dieser Faktoren während der Entwurfsphase kann die Qualität des endgültigen Teils optimieren und die Nachbearbeitungsanforderungen minimieren.
- Integration des Wärmemanagements: Für empfindliche optische Instrumente ist ein wirksames Wärmemanagement von entscheidender Bedeutung. Die additive Fertigung ermöglicht die Integration von Kühlkanälen direkt in das Design der optischen Bank, was eine präzise Temperaturkontrolle und -stabilität ermöglicht. Diese internen Kanäle können komplex sein und für den Flüssigkeitsfluss optimiert werden - eine einzigartige Fähigkeit des 3D-Drucks.
- Feature-Konsolidierung: Der 3D-Metalldruck ermöglicht die Zusammenführung mehrerer Komponenten zu einem einzigen, integrierten Teil. Dadurch verringert sich die Anzahl der Montageschritte, Befestigungselemente und Schnittstellen, was zu höherer Zuverlässigkeit und potenziell geringerem Gesamtgewicht und geringeren Kosten führt. Befestigungselemente, Kabelführungskanäle und Ausrichtungshilfen können direkt in das Design der optischen Bank integriert werden.
Metal3DPs geht über das reine Drucken hinaus. Unsere Anwendungsentwicklungsdienste unterstützen Kunden bei der Optimierung ihrer Designs für die additive Fertigung und stellen sicher, dass sie die Vorteile unserer SEBM-Drucker und Hochleistungsmetallpulver voll ausschöpfen können. Wir arbeiten eng mit den Ingenieuren zusammen, um all diese Designaspekte zu berücksichtigen und die bestmöglichen Ergebnisse für ihre optischen Satellitenbankanwendungen zu erzielen.
Toleranzen, Oberflächengüte und Maßgenauigkeit - Präzision bei 3D-gedruckten Metallkomponenten
Die Leistung von optischen Bänken für Satelliten hängt von ihrer Maßgenauigkeit und Oberflächenqualität ab, um die präzise Ausrichtung und den Betrieb der montierten optischen Instrumente zu gewährleisten. Die 3D-Drucktechnologien für Metall, insbesondere die von Metall3DPkann ein beeindruckendes Maß an Präzision erreichen:
- Maßgenauigkeit: Die Technologie des selektiven Elektronenstrahlschmelzens (SEBM), ein Kernangebot von Metall3DPist für seine hohe Maßhaltigkeit bekannt. Durch die präzise Steuerung des Elektronenstrahls und des Schmelzprozesses kann SEBM Teile mit engen Toleranzen herstellen, die bei kritischen Abmessungen oft innerhalb von ±0,1-0,2 mm liegen. Diese Genauigkeit ist entscheidend für die Gewährleistung der korrekten Passform und Funktion innerhalb des Satellitensystems.
- Oberfläche: Die mit dem 3D-Metalldruck erreichbare Oberflächengüte hängt vom Material, dem Druckverfahren und der verwendeten Schichtdicke ab. Während gedruckte Oberflächen rauer sein können als maschinell bearbeitete Oberflächen, ermöglichen Fortschritte in der Technologie und optimierte Prozessparameter zunehmend glatte Oberflächen. Metall3DP verfeinert kontinuierlich seine Druckverfahren, um die Oberflächenrauheit zu minimieren. Durch Nachbearbeitungstechniken wie Polieren, Bearbeiten und Beschichten kann die Oberflächengüte weiter verbessert werden, um die spezifischen Anforderungen für optische Bänke zu erfüllen.
- Faktoren, die die Genauigkeit beeinflussen: Mehrere Faktoren können die endgültige Maßgenauigkeit und Oberflächengüte eines 3D-gedruckten Metallteils beeinflussen:
- Materialeigenschaften: Verschiedene Metallpulver weisen während des Druckvorgangs unterschiedliche Schrumpfungs- und Wärmeausdehnungseigenschaften auf, was sich auf die endgültigen Abmessungen auswirken kann. Metal3DPs hochwertige Metallpulver werden sorgfältig charakterisiert, um ein konsistentes und vorhersehbares Verhalten zu gewährleisten.
- Druckerkalibrierung und -wartung: Die regelmäßige Kalibrierung und Wartung des 3D-Druckers ist für die Aufrechterhaltung der Genauigkeit unerlässlich. Metal3DPs die branchenführenden Drucker sind auf Zuverlässigkeit und konstante Leistung ausgelegt.
- Parameter aufbauen: Druckparameter wie Schichtdicke, Strahlleistung und Scangeschwindigkeit haben einen erheblichen Einfluss auf die Qualität des Endprodukts. Metal3DPs unsere Erfahrung in der Prozessoptimierung gewährleistet, dass für jedes Material und jede Anwendung die optimalen Parameter verwendet werden.
- Nachbearbeiten: Durch Wärmebehandlung können innere Spannungen abgebaut und die Maßhaltigkeit verbessert werden. Die Präzisionsbearbeitung kann für kritische Oberflächen eingesetzt werden, die sehr enge Toleranzen erfordern.
Metall3DP weiß um die entscheidende Bedeutung von Präzision bei Anwendungen in der Luft- und Raumfahrt. Unsere SEBM-Drucker und optimierten Druckverfahren sind darauf ausgelegt, ein hohes Maß an Maßgenauigkeit und Oberflächenqualität für optische Bänke für Satelliten zu liefern. Wir bieten auch Beratung zu geeigneten Nachbearbeitungstechniken, um auch die anspruchsvollsten Anforderungen zu erfüllen.
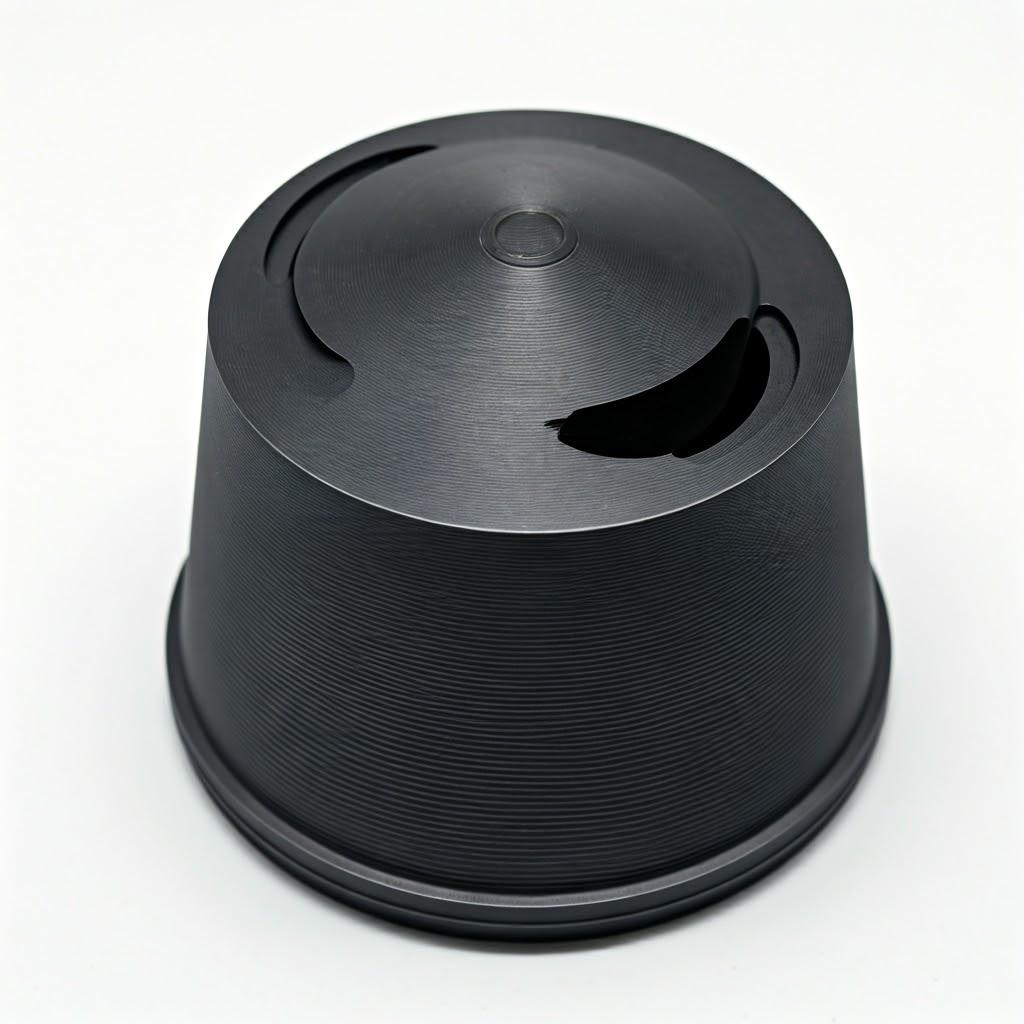
Nachbearbeitungsanforderungen - Veredelung von 3D-gedruckten optischen Bänken aus Metall für Weltraumanwendungen
Der 3D-Metalldruck bietet zwar erhebliche Vorteile bei der Erstellung komplexer Geometrien, doch sind häufig Nachbearbeitungsschritte erforderlich, um die gewünschten endgültigen Eigenschaften und die Oberflächenbeschaffenheit von optischen Satellitenbänken zu erreichen:
- Stressabbau Wärmebehandlung: Dieser Prozess ist entscheidend für die Verringerung der inneren Spannungen, die sich während der schnellen Erwärmungs- und Abkühlungszyklen des 3D-Druckverfahrens aufbauen können. Der Spannungsabbau verbessert die Dimensionsstabilität und verhindert Verformungen oder Risse, was besonders bei großen und komplizierten Strukturen von optischen Bänken wichtig ist.
- Entfernung der Stützstruktur: Stützstrukturen, die für den Druck komplexer Geometrien unerlässlich sind, müssen nach Abschluss des Aufbaus sorgfältig entfernt werden. Die Methode der Entfernung hängt von der Konstruktion der Stützstruktur und dem Material ab. Bei Metallteilen erfolgt dies häufig durch Bearbeiten, Schleifen oder Drahterodieren (Electrical Discharge Machining).
- Oberflächenveredelung: Je nach Anwendung und geforderter Oberflächenqualität für die Montage optischer Instrumente können zusätzliche Schritte der Oberflächenbearbeitung erforderlich sein. Diese können umfassen:
- Media Blasting: Um losen Puder zu entfernen und eine gleichmäßigere Oberflächenstruktur zu erzielen.
- Polieren: Zur Verringerung der Oberflächenrauhigkeit und zur Verbesserung des Reflexionsvermögens, falls erforderlich.
- Spanende Bearbeitung (CNC): Für kritische Schnittstellen und Montageflächen, die sehr enge Toleranzen und glatte Oberflächen erfordern.
- Reinigung und Inspektion: Eine gründliche Reinigung ist unerlässlich, um Pulverreste oder Verunreinigungen zu entfernen. Zerstörungsfreie Prüfverfahren (NDT) wie die Farbeindringprüfung oder die Ultraschallprüfung können eingesetzt werden, um die strukturelle Integrität und die Fehlerfreiheit des gedruckten Teils sicherzustellen.
- Beschichtungen und Oberflächenbehandlungen: Je nach den Anforderungen des Einsatzes und des gewählten Materials können Oberflächenbehandlungen wie Eloxieren (bei Aluminiumlegierungen) oder andere Schutzbeschichtungen zur Verbesserung der Korrosionsbeständigkeit, der thermischen Eigenschaften oder der optischen Leistung vorgenommen werden.
- Montage und Integration: In einigen Fällen kann eine optische Satellitenbank aus mehreren 3D-gedruckten Komponenten bestehen, die zusammengebaut werden müssen. In dieser Phase sind präzise Ausrichtungs- und Befestigungstechniken entscheidend.
Metall3DP bietet umfassende Lösungen, die über den reinen Druckprozess hinausgehen. Wir bieten Beratung und Partnerschaften für verschiedene Nachbearbeitungsschritte an, um sicherzustellen, dass die endgültigen optischen Bänke für Satelliten den strengen Anforderungen von Luft- und Raumfahrtanwendungen entsprechen. Dank unserer Kenntnis der Materialeigenschaften und Verarbeitungstechniken können wir die effektivsten Nachbearbeitungsabläufe für eine optimale Leistung empfehlen.
Häufige Herausforderungen und wie man sie vermeidet - Erfolgreiche Ergebnisse beim 3D-Druck von Metall
Der 3D-Metalldruck bietet zwar zahlreiche Vorteile, aber es gibt auch potenzielle Herausforderungen, die bewältigt werden müssen, um die erfolgreiche Herstellung hochwertiger optischer Bänke für Satelliten sicherzustellen:
- Verformung und Verzerrung: Thermische Spannungen während des Druckvorgangs können insbesondere bei großen oder dünnwandigen Teilen zu Verformungen führen.
- Milderung: Eine optimierte Teileausrichtung, die Verwendung von Stützstrukturen und eine sorgfältige Kontrolle der Fertigungsparameter (z. B. Temperaturprofile) können diese Probleme minimieren. Metal3DPs Die SEBM-Technologie mit ihrer hohen Baukammertemperatur trägt dazu bei, thermische Gradienten und das Risiko von Verformungen zu reduzieren.
- Porosität: Innere Hohlräume oder Porosität können die mechanischen Eigenschaften und die strukturelle Integrität des gedruckten Teils beeinträchtigen.
- Milderung: Die Verwendung hochwertiger Metallpulver mit guter Fließfähigkeit, die Optimierung der Laser- oder Elektronenstrahlparameter und die Gewährleistung einer schützenden Atmosphäre während des Drucks sind entscheidend. Metal3DPs das fortschrittliche Pulverherstellungssystem und die branchenführenden Drucker sind darauf ausgelegt, die Porosität zu minimieren.
- Unterstützung bei der Beseitigung von Schäden: Unsachgemäßes Entfernen von Stützstrukturen kann die Oberfläche des Werkstücks beschädigen.
- Milderung: Die Entwicklung intelligenter Stützstrukturen, die leicht zu entfernen sind, und die Anwendung geeigneter Entfernungstechniken sind von entscheidender Bedeutung. Metall3DP bietet eine Anleitung zu bewährten Praktiken für die Konstruktion und den Abbau von Stützen.
- Eigenspannungen: Wie bereits erwähnt, können Eigenspannungen zu einer Instabilität der Abmessungen und einem möglichen Versagen führen.
- Milderung: Die Spannungsarmglühung ist ein wichtiger Nachbearbeitungsschritt, um dieses Problem zu lösen.
- Oberflächenrauhigkeit: Unbedruckte Oberflächen erfüllen möglicherweise nicht die Anforderungen für alle Anwendungen.
- Milderung: Durch die Optimierung der Herstellungsparameter und den Einsatz geeigneter Nachbearbeitungstechniken wie Bearbeitung oder Polieren kann die gewünschte Oberflächengüte erreicht werden.
- Konsistenz der Materialeigenschaften: Die Gewährleistung gleichbleibender mechanischer Eigenschaften im gesamten gedruckten Teil ist entscheidend für die Zuverlässigkeit.
- Milderung: Die Verwendung von hochwertigen, gut charakterisierten Metallpulvern und die Einhaltung stabiler Druckbedingungen sind von entscheidender Bedeutung. Metal3DPs strenge Qualitätskontrollverfahren gewährleisten die Konsistenz unserer Metallpulver.
Metall3DP verfügt über umfassende Erfahrung bei der Bewältigung dieser Herausforderungen. Unser Know-how im Bereich der additiven Fertigungsverfahren für Metalle in Kombination mit unseren fortschrittlichen SEBM-Druckern und hochwertigen Metallpulvern ermöglicht es uns, zuverlässige und leistungsstarke optische Bänke für Satelliten zu liefern. Wir arbeiten eng mit unseren Kunden zusammen, um potenzielle Probleme vorauszusehen und zu entschärfen und so erfolgreiche Ergebnisse für ihre kritischen Luft- und Raumfahrtanwendungen zu gewährleisten.
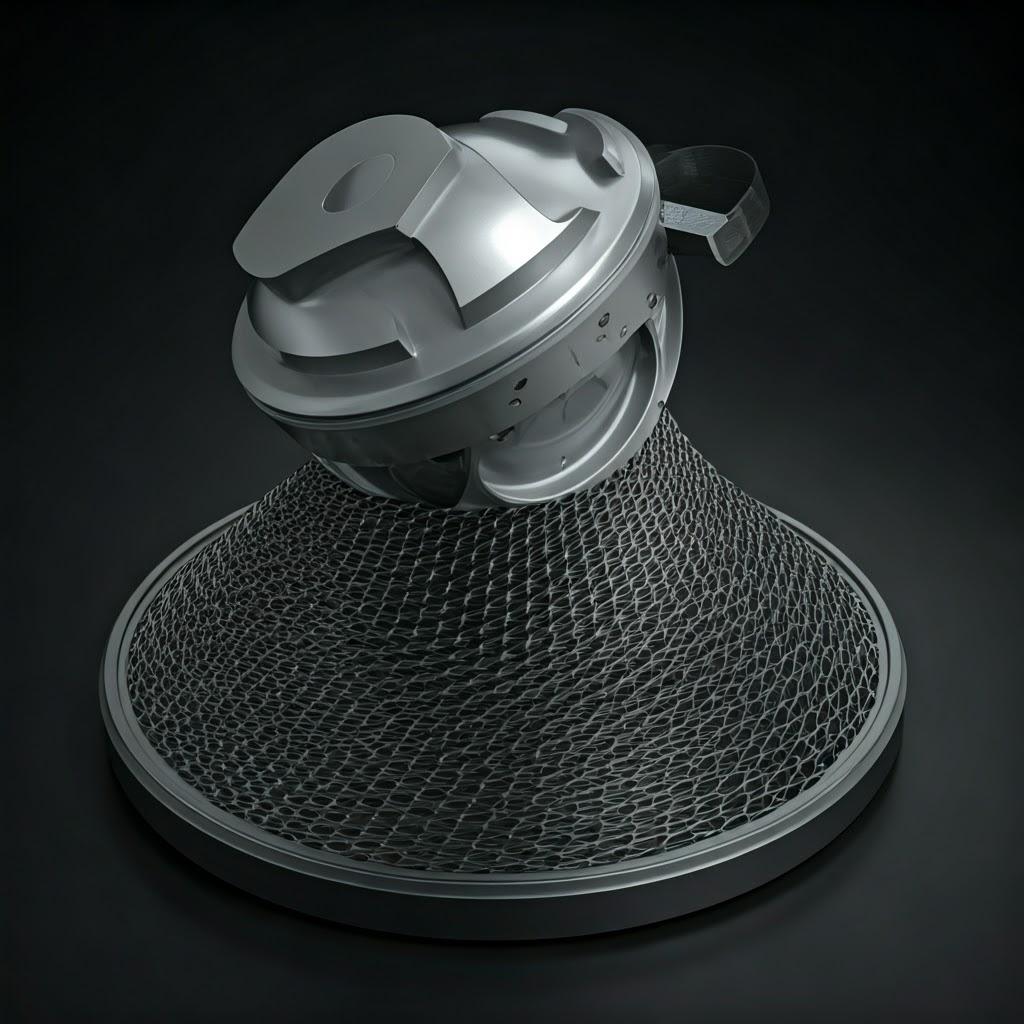
Wie man den richtigen 3D-Druckdienstleister für Metall auswählt - Wichtige Überlegungen für Kunden aus der Luft- und Raumfahrt
Die Auswahl des richtigen 3D-Druckdienstleisters für Metall ist eine wichtige Entscheidung für Luft- und Raumfahrtunternehmen, die optische Bänke für Satelliten herstellen wollen. Die Wahl kann sich erheblich auf die Qualität, die Kosten und die Vorlaufzeit der endgültigen Komponenten auswirken. Hier sind die Schlüsselfaktoren, die bei der Bewertung potenzieller Lieferanten zu berücksichtigen sind:
- Technologie und Ausrüstung: Stellen Sie sicher, dass der Anbieter fortschrittliche 3D-Drucktechnologien aus Metall einsetzt, die für Anwendungen in der Luft- und Raumfahrt geeignet sind. Metal3DPs der Einsatz der SEBM-Technologie (Selective Electron Beam Melting) bietet Vorteile hinsichtlich der Materialeigenschaften und des Bauvolumens, was für größere optische Bankstrukturen entscheidend sein kann. Erkundigen Sie sich nach den von ihnen verwendeten Druckertypen, ihren Bauumfängen und ihrer Erfolgsbilanz bei der Herstellung hochpräziser Teile. Sie können erkunden Metal3DPs druckverfahren hier: https://met3dp.com/printing-methods/
- Materielle Fähigkeiten: Vergewissern Sie sich, dass der Dienstleister eine Reihe von Metallpulvern in Luft- und Raumfahrtqualität anbietet, die für Ihre Anwendung relevant sind, z. B. Scalmalloy® und AlSi10Mg. Erkundigen Sie sich nach der Materialbeschaffung, den Qualitätskontrollverfahren und den Daten zur Materialcharakterisierung. Metall3DP stellt eine breite Palette an hochwertigen Metallpulvern her, die für die additive Fertigung optimiert sind und hervorragende mechanische Eigenschaften aufweisen.
- Qualitätssicherung und Zertifizierungen: Bauteile für die Luft- und Raumfahrt erfordern eine strenge Qualitätskontrolle. Prüfen Sie, ob der Anbieter über einschlägige Zertifizierungen wie AS9100 (Qualitätsmanagementsystem für die Luft- und Raumfahrt) oder ISO 9001 verfügt. Erkundigen Sie sich nach den Prüfverfahren, der Maßgenauigkeit und den Materialprüfverfahren.
- Unterstützung bei Design und Technik: Ein guter Dienstleister sollte Design- und Konstruktionsunterstützung anbieten, um das Design Ihrer optischen Bank für die additive Fertigung zu optimieren. Dazu gehört die Beratung bei der Optimierung der Topologie, der Gitterstrukturen, der Konstruktion der Halterung und der Materialauswahl. Metal3DPs anwendungsentwicklungsdienste bieten dieses entscheidende Fachwissen.
- Nachbearbeitungsmöglichkeiten: Informieren Sie sich über die Nachbearbeitungsmöglichkeiten des Anbieters, einschließlich Wärmebehandlung, Oberflächenveredelung, Bearbeitung und Beschichtung. Vergewissern Sie sich, dass der Anbieter die spezifischen Nachbearbeitungsanforderungen für Ihre Anwendung erfüllen kann.
- Erfahrung und Fachwissen: Beurteilen Sie die Erfahrung des Anbieters in der Zusammenarbeit mit der Luft- und Raumfahrtindustrie und seine Erfolgsbilanz bei der Herstellung ähnlicher Komponenten. Fallstudien und Erfahrungsberichte können wertvolle Erkenntnisse liefern. Metall3DP verfügt über jahrzehntelange Erfahrung in der additiven Fertigung von Metallen und arbeitet mit Unternehmen aus der Luft- und Raumfahrt und anderen anspruchsvollen Bereichen zusammen.
- Vorlaufzeiten und Produktionskapazität: Besprechen Sie die Vorlaufzeiten für die Prototypenerstellung und die Produktion sowie die Kapazität des Unternehmens, die erwarteten Mengen zu bewältigen. Stellen Sie sicher, dass der Zeitplan mit Ihrem Projektplan übereinstimmt.
- Kommunikation und Kundenbetreuung: Eine effektive Kommunikation und ein reaktionsschneller Kundendienst sind für eine reibungslose Zusammenarbeit unerlässlich. Beurteilen Sie die Reaktionsfähigkeit, die technische Kompetenz und die Bereitschaft, Ihre spezifischen Anforderungen zu verstehen.
- Kostenstruktur und Transparenz: Verstehen Sie das Preismodell des Anbieters und sorgen Sie für Transparenz bei der Kostenaufschlüsselung. Erörtern Sie Faktoren, die die Endkosten beeinflussen können.
Wählen Sie Metall3DP als Ihr 3D-Druckdienstleister für Metall bedeutet, dass Sie mit einem Unternehmen zusammenarbeiten, das branchenführende Technologie, hochwertige Materialien, umfassenden Support und ein tiefes Verständnis der anspruchsvollen Anforderungen der Luft- und Raumfahrtindustrie bietet. Wir sind bestrebt, zuverlässige und leistungsstarke Lösungen für Ihre Anforderungen an optische Satellitenbänke zu liefern. Hier erfahren Sie mehr über unser Unternehmen und unser Engagement für Qualität: https://met3dp.com/about-us/
Kostenfaktoren und Vorlaufzeit - Verständnis für die Wirtschaftlichkeit von 3D-gedruckten optischen Bänken
Die Kosten und die Vorlaufzeit für die Herstellung von optischen Bänken für Satelliten mit 3D-Metalldruck werden von mehreren Faktoren beeinflusst. Diese zu verstehen, kann Luft- und Raumfahrtunternehmen helfen, fundierte Entscheidungen zu treffen:
Kostenfaktoren:
- Materialkosten: Die Kosten für das Metallpulver sind ein wichtiger Faktor. Moderne Legierungen wie Scalmalloy® können teurer sein als Standardlegierungen wie AlSi10Mg. Das Volumen des im endgültigen Teil verwendeten Materials und etwaige Stützstrukturen wirken sich ebenfalls auf die Gesamtmaterialkosten aus. Metal3DPs effiziente Druckverfahren und optimierte Designs tragen dazu bei, den Materialabfall zu minimieren.
- Bauzeit: Die Dauer des Druckprozesses hängt von der Größe und Komplexität der optischen Bank, der verwendeten Schichtdicke und der Anzahl der Teile ab, die gleichzeitig auf der Bauplattform gedruckt werden. Längere Bauzeiten führen zu höheren Maschinenbetriebskosten. Metal3DPs sEBM-Hochleistungsdrucker bieten ein branchenweit führendes Bauvolumen, das die effiziente Produktion größerer Teile oder mehrerer kleiner Teile in einem einzigen Bauvorgang ermöglicht.
- Kosten der Vorverarbeitung: Dazu gehören die Designoptimierung für die additive Fertigung, die Bauvorbereitung und alle erforderlichen Simulationen. Die Zusammenarbeit mit erfahrenen Anbietern wie Metall3DP kann dazu beitragen, diese Kosten durch eine effiziente Entwurfs- und Bauplanung zu minimieren.
- Nachbearbeitungskosten: Die Kosten für Nachbearbeitungsschritte wie das Entfernen der Auflage, die Wärmebehandlung, die Oberflächenbearbeitung und die maschinelle Bearbeitung erhöhen die Gesamtkosten. Die Komplexität und erforderliche Präzision dieser Schritte beeinflussen die endgültigen Kosten.
- Arbeitskosten: Dazu gehört das erforderliche Fachwissen für den Maschinenbetrieb, die Bauvorbereitung, die Nachbearbeitung und die Qualitätskontrolle. Die Zusammenarbeit mit einem kompetenten Anbieter wie Metall3DPund unser erfahrenes Team sorgen für eine effiziente und kostengünstige Produktion.
- Werkzeugkosten (im Vergleich zu traditionellen Methoden): Einer der wesentlichen Vorteile des 3D-Drucks sind die minimalen oder gar nicht vorhandenen Werkzeugkosten, insbesondere bei komplexen und kleinen Produktionsserien. Dies kann zu erheblichen Kosteneinsparungen im Vergleich zu herkömmlichen Methoden für optische Bänke für Satelliten führen.
Faktoren für die Vorlaufzeit:
- Entwurfs- und Konstruktionsphase: Die Zeit, die für die Designoptimierung und die Vorbereitung für den 3D-Druck benötigt wird.
- Druckzeit: Die tatsächliche Dauer des Bauprozesses auf dem 3D-Drucker.
- Nachbearbeitungszeit: Die Zeit, die für das Entfernen der Auflage, die Wärmebehandlung, die Oberflächenbearbeitung und andere Nachbearbeitungsschritte benötigt wird.
- Qualitätskontrolle und Inspektion: Die für eine gründliche Inspektion und Prüfung erforderliche Zeit.
- Versand und Logistik: Die Zeit, die für die Lieferung der fertigen Teile benötigt wird.
Metall3DP ist bestrebt, transparente und wettbewerbsfähige Preise für unsere 3D-Metalldruckdienste anzubieten. Wir arbeiten eng mit unseren Kunden zusammen, um ihre spezifischen Anforderungen zu verstehen und den Produktionsprozess zu optimieren, um sowohl die Kosten als auch die Vorlaufzeit für ihre optischen Satellitenbänke zu minimieren. Kontaktieren Sie uns, um Ihr Projekt zu besprechen und ein detailliertes Angebot zu erhalten.
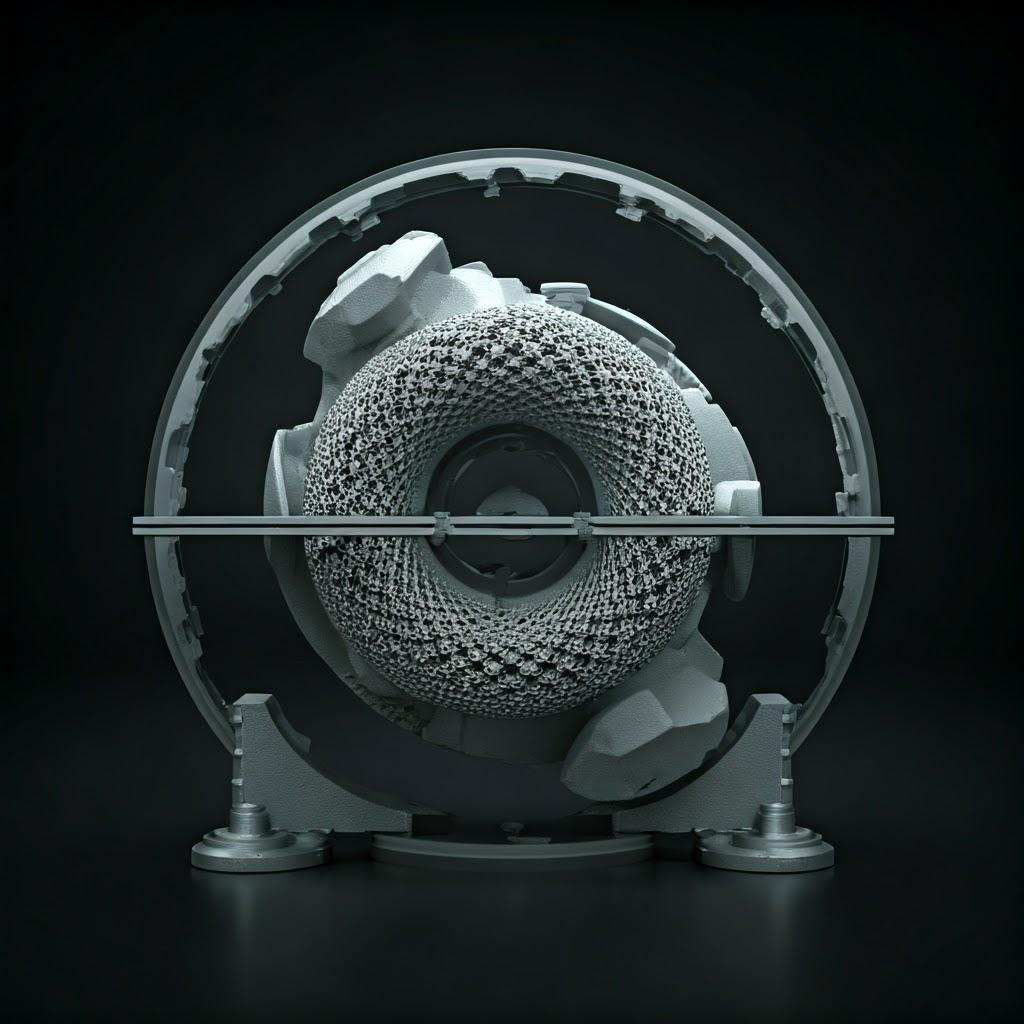
Häufig gestellte Fragen (FAQ)
- Welche typischen Toleranzen sind beim 3D-Metalldruck für optische Bänke für Satelliten zu erreichen?
- Mit fortschrittlichen Technologien wie dem selektiven Elektronenstrahlschmelzen (SEBM), das von Metall3DPbei kritischen Abmessungen sind Toleranzen von ±0,1-0,2 mm möglich. Engere Toleranzen können durch Nachbearbeitung, z. B. durch Präzisionsbearbeitung, erreicht werden.
- Können 3D-gedruckte optische Bänke aus Metall den rauen Bedingungen im Weltraum standhalten?
- Ja, wenn die geeigneten Werkstoffe für die Luft- und Raumfahrt verwendet werden und die Teile richtig konstruiert und nachbearbeitet werden. Werkstoffe wie Scalmalloy® und AlSi10Mg bieten ein hervorragendes Verhältnis von Festigkeit zu Gewicht und Korrosionsbeständigkeit. Durch geeignete Spannungsentlastung und Oberflächenbehandlung wird ihre Eignung für Raumfahrtanwendungen weiter verbessert. Metal3DPs das Know-how bei der Materialauswahl und -verarbeitung gewährleistet die Haltbarkeit der gedruckten Komponenten im Weltraum.
- Wie lang ist die typische Vorlaufzeit für eine kundenspezifische optische Bank für Satelliten, die im 3D-Metalldruck hergestellt wird?
- Die Durchlaufzeiten hängen von der Komplexität des Entwurfs, der Größe des Teils, dem verwendeten Material und den erforderlichen Nachbearbeitungen ab. Im Allgemeinen bietet der 3D-Metalldruck jedoch schnellere Durchlaufzeiten für komplexe Kleinserien im Vergleich zu herkömmlichen, werkzeugabhängigen Verfahren. Metall3DP arbeitet eng mit den Kunden zusammen, um auf der Grundlage ihrer spezifischen Projektanforderungen realistische Vorlaufzeiten zu gewährleisten.
- Ist der 3D-Druck von Metall für die Herstellung von optischen Bänken für Satelliten kostengünstig?
- Bei komplexen Geometrien und geringen bis mittleren Produktionsvolumina kann der 3D-Druck von Metallen sehr kosteneffizient sein, da nur minimale Werkzeuganforderungen bestehen und die Konstruktionen im Hinblick auf Gewichtsreduzierung und Materialeffizienz optimiert werden können. Die Gesamtwirtschaftlichkeit hängt von Faktoren wie der Materialauswahl, der Komplexität des Teils und den Nachbearbeitungsanforderungen ab. Metall3DP bietet wettbewerbsfähige Preise und arbeitet mit den Kunden zusammen, um die Entwürfe im Hinblick auf Kosteneffizienz zu optimieren.
Fazit - Mit 3D-gedruckten optischen Bänken aus Metall in die Zukunft der Luft- und Raumfahrt
Der 3D-Metalldruck revolutioniert das Design und die Herstellung von optischen Bänken für Satelliten und bietet ungeahnte Möglichkeiten zur Gewichtsreduzierung, Designoptimierung und Leistungssteigerung. Unternehmen wie Metall3DPmit unserer fortschrittlichen SEBM-Technologie, hochwertigen Metallpulvern und umfassendem Know-how unterstützen wir die Luft- und Raumfahrtindustrie bei der Entwicklung innovativer und leistungsstarker Komponenten für die nächste Generation von Raumfahrtmissionen. Durch die Nutzung der Designfreiheit, der Materialeffizienz und der schnellen Produktionsmöglichkeiten der additiven Metallfertigung ist die Zukunft der Satellitentechnologie vielversprechender denn je. Kontakt Metall3DP um herauszufinden, wie unsere Fähigkeiten die Ziele Ihres Unternehmens im Bereich der additiven Fertigung unterstützen und Ihre Innovationen in der Luft- und Raumfahrt vorantreiben können. Besuchen Sie unsere Website für weitere Informationen: https://met3dp.com/
Teilen auf
MET3DP Technology Co., LTD ist ein führender Anbieter von additiven Fertigungslösungen mit Hauptsitz in Qingdao, China. Unser Unternehmen ist spezialisiert auf 3D-Druckgeräte und Hochleistungsmetallpulver für industrielle Anwendungen.
Fragen Sie an, um den besten Preis und eine maßgeschneiderte Lösung für Ihr Unternehmen zu erhalten!
Verwandte Artikel
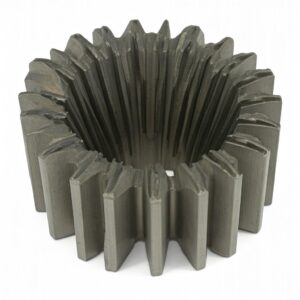
Hochleistungs-Düsenschaufelsegmente: Revolutionierung der Turbineneffizienz mit 3D-Metalldruck
Mehr lesen "Über Met3DP
Aktuelles Update
Unser Produkt
KONTAKT US
Haben Sie Fragen? Senden Sie uns jetzt eine Nachricht! Wir werden Ihre Anfrage mit einem ganzen Team nach Erhalt Ihrer Nachricht bearbeiten.
Holen Sie sich Metal3DP's
Produkt-Broschüre
Erhalten Sie die neuesten Produkte und Preislisten