Polvos de impresión 3D
Índice
La impresión 3D, también conocida como fabricación aditiva (AM), utiliza polvos especializados para construir componentes tridimensionales con métodos de estratificación sucesivos. Esta guía es una referencia exhaustiva sobre los polvos para impresión 3D: tipos, características, especificaciones, métodos de fabricación, principales proveedores y precios, aplicaciones en distintos sectores, comparaciones con alternativas, preguntas frecuentes y mucho más.
Visión general de Polvos de impresión 3D
Los polvos de impresión 3D son materias primas que permiten la fabricación aditiva de piezas en plataformas de plástico, metal y cerámica. Rasgos clave:
- Estado: Polvos particulados ultrafinos
- Rango de tamaño: normalmente entre 10 y 150 micras
- Morfología: Más a menudo forma de partícula esférica.
- Composición: Polímero, aleación de metal, cerámica, mezclas de arenisca.
- Propiedades clave: Distribución de tamaño de partículas diseñada, fluidez, densidad del paquete y microestructura.
Al aprovechar el estricto control de las propiedades físicas del polvo y las interacciones con los procesos de impresión térmica/cinética, los polvos de impresión 3D facilitan geometrías de piezas intrincadas y gradientes de composición de materiales que no se podrían lograr de otra manera.
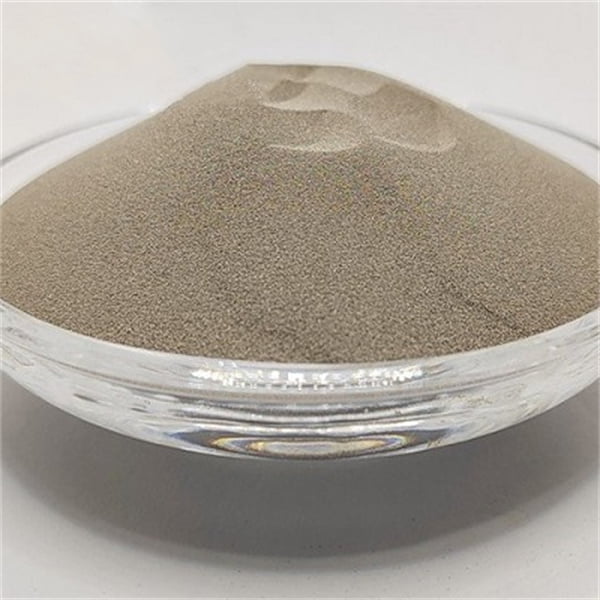
Tipos de polvos de impresión 3D
Categoría | Materiales | Método de impresión |
---|---|---|
Plásticos | Nailones, ABS, TPU, PEKK, PEEK… | Sinterizado selectivo por láser (SLS) |
Metales | Inoxidables, aceros para herramientas, titanio y aleaciones, superaleaciones… | Sinterizado directo de metales por láser (DMLS) |
Cerámica | Alúmina, circonio, carburo de silicio. | Chorro de aglutinante, modelado por deposición fundida |
Compuestos | Mezclas de metal/plástico, mezclas de arenisca | Fusión por chorro múltiple (MJF), deposición de metal ligado |
Biocompatible | PEEK, PLGA, TCP… | Fusión selectiva por láser (SLM) |
Cuadro 1: Principales categorías, materiales y plataformas de impresión asociadas para polvos de impresión 3D comerciales
Los polvos poliméricos, metálicos, cerámicos y compuestos respaldan la producción de piezas de uso final en los mercados aeroespacial, automotriz, médico, dental e industrial.
Métodos de fabricación
Método | Descripción | Idoneidad del material | Ventajas | Desventajas |
---|---|---|---|---|
Atomización | Este término general abarca varias técnicas que descomponen el metal fundido en partículas finas. El metal fundido se fuerza a través de una boquilla hacia una corriente de agua o gas a alta presión, solidificando rápidamente las gotas en partículas esféricas. | Metales (hierro, aluminio, aleaciones de titanio) | – Alta tasa de producción – Tamaño y forma de partículas consistentes – Buena fluidez del polvo | – Requiere un alto aporte de energía – Potencial de formación de óxido en las partículas – Limitado a ciertos materiales |
Atomización de gases | El método de atomización más común, que utiliza un gas inerte (normalmente nitrógeno) para romper el metal fundido. | Similar a la atomización, pero generalmente con mejor calidad de superficie y control más estricto sobre el tamaño de las partículas. | – Calidad de polvo superior en comparación con otros métodos de atomización – Adecuado para metales reactivos | Similar a la atomización, pero con mayor costo de equipo. |
Atomización del agua | Utiliza un chorro de agua a alta presión para fragmentar el metal fundido. Más rentable que la atomización con gas pero produce partículas menos esféricas. | Algunos metales (hierro, cobre) y algunos polímeros. | – Menor costo que la atomización con gas – Muy adecuado para materiales insensibles a la humedad | – Menor calidad del polvo (formas irregulares) – Puede no ser ideal para aplicaciones de alto rendimiento |
Atomización por plasma | Un arco eléctrico calienta el material de alimentación (alambre metálico o polvo) hasta un estado fundido. Luego, el metal fundido se expulsa a través de una boquilla y se atomiza mediante un soplete de plasma. | Amplia gama de materiales (metales, aleaciones, cerámicas) | – Puede manejar materiales de alto punto de fusión – Adecuado para crear polvos compuestos | – Proceso complejo y de alto costo – Requiere estrictas medidas de seguridad |
Pulverización Mecánica | Un proceso físico que muele o muele material a granel hasta obtener un polvo fino. | Materiales frágiles (cerámica, algunos polímeros) | – Configuración más simple y de menor costo en comparación con otros métodos | – Control limitado sobre el tamaño y la morfología de las partículas – Puede introducir impurezas durante la molienda |
Deposición química en fase vapor (CVD) | Un proceso químico en el que los precursores gaseosos reaccionan para formar un depósito sólido sobre una partícula de semilla. | Metales, cerámicas y algunos materiales avanzados. | – Alta pureza y control preciso sobre la composición de las partículas – Puede crear geometrías complejas | – Proceso lento con tasa de producción limitada – Alta inversión de capital |
Atomización electrolítica | Se utiliza una celda electrolítica para descomponer un ánodo metálico en iones. Luego, los iones se combinan con los electrones en el cátodo para formar partículas metálicas. | Metales | – Proceso respetuoso con el medio ambiente (evita altas temperaturas) – Adecuado para materiales sensibles a la humedad | – Tasa de producción más baja que los métodos de atomización – Limitado a ciertos electrolitos y materiales de ánodo |
Esferoidización | Un proceso adicional utilizado para mejorar la forma de polvos de forma irregular producidos por otros métodos. Implica tratamiento térmico o procesos químicos para fomentar la aglomeración de partículas en esferas. | La mayoría de los tipos de polvo (metales, polímeros, cerámicas) | – Mejora la fluidez del polvo y la densidad de empaquetamiento – Mejora la imprimibilidad | – Agrega un paso de procesamiento adicional – Puede que no sea necesario para todas las aplicaciones |
Propiedades de Polvos de impresión 3D
Propiedad | Descripción | Importancia para la impresión 3D | Ejemplos y consideraciones |
---|---|---|---|
Tamaño y distribución de partículas | Se refiere a la variación en el tamaño de las partículas de polvo individuales y la distribución general en diferentes rangos de tamaño. Medido en micrómetros (μm). | Desempeña un papel crucial en la imprimibilidad, la resolución y la densidad de la pieza final. – Demasiado grande: dificultad para la fluidez, distribución desigual y posibilidad de defectos de rastrillado. – Demasiado pequeña: El aumento de la superficie puede provocar apelmazamiento y empaquetamiento deficiente, lo que afecta la resistencia. | – SLS (Sinterización selectiva por láser): Generalmente prefiere polvos más finos (20-80 µm) para características detalladas. – MJF (Fusión Multi Jet): Se pueden utilizar partículas ligeramente más grandes (50-100 µm) debido a la capacidad de la tecnología de inyección de tinta para superar las limitaciones de flujo. – Polvos metálicos: La distribución estrecha (rango estrecho) es ideal para una buena densidad de empaquetamiento y una porosidad mínima en la pieza final. |
Morfología de las partículas | La forma de las partículas de polvo individuales. | Afecta el buen empaquetamiento de las partículas, la fluidez y el acabado superficial de la pieza final. – Esférico: Ofrezca la mejor densidad de empaquetamiento y fluidez, lo que genera piezas fuertes y uniformes. – Formas irregulares: Puede crear espacios e inconsistencias, lo que podría afectar la resistencia y la calidad de la superficie. | – Polvos plásticos: Generalmente esférico o casi esférico para una imprimibilidad óptima. – Polvos metálicos: Puede variar según el metal y el método de producción. Se prefieren las morfologías esféricas, pero se pueden lograr mediante técnicas de posprocesamiento como la atomización. |
Fluidez | La facilidad con la que el polvo fluye por su propio peso o con una fuerza cortante mínima. | Es fundamental para la deposición constante del material y la formación uniforme de capas durante la impresión. – Buena fluidez: Garantiza una distribución suave y minimiza el riesgo de defectos de capa. – Poca fluidez: Puede provocar una deposición desigual, inconsistencias y posibles problemas de impresión. | – Polvos con una estrecha distribución del tamaño de partículas. tienden a fluir mejor debido a una menor interferencia del tamaño de las partículas. – Aditivos y tratamientos superficiales. Se puede utilizar para mejorar la fluidez al reducir la fricción entre partículas. |
Densidad de embalaje | La medida de cuán estrechamente se pueden empaquetar las partículas de polvo. Expresado como porcentaje del volumen total ocupado por el polvo. | Afecta la densidad final, la resistencia y la precisión dimensional de la pieza impresa. – Alta densidad de embalaje: Conduce a piezas más densas con propiedades mecánicas y precisión dimensional mejoradas. – Baja densidad de embalaje: Da como resultado piezas con mayor porosidad, potencialmente más débiles y menos precisas dimensionalmente. | – Forma de las partículas juega un papel importante. Las partículas esféricas se empaquetan de manera más eficiente que las formas irregulares. – Procesos como Binder Jetting puede beneficiarse de densidades de empaque ligeramente más bajas para permitir una infiltración adecuada del aglutinante. |
Sinterabilidad | La capacidad de las partículas de polvo para fusionarse o unirse durante el proceso de impresión 3D, generalmente mediante calor o energía láser. | Esencial para conseguir piezas impresas resistentes y funcionales. – Buena sinterabilidad: Permite una fuerte unión entre partículas, lo que da lugar a piezas robustas y funcionales. – Mala sinterabilidad: Puede provocar uniones débiles y posibles fallas de las piezas bajo estrés. | – Composición del material: Los metales generalmente tienen buena sinterabilidad debido a su capacidad inherente para formar enlaces fuertes a altas temperaturas. – Polvos de polímero a menudo requieren aditivos específicos o pasos de posprocesamiento (por ejemplo, hornos de sinterización) para mejorar la unión. |
Composición química | La composición elemental del material en polvo. | Determina las propiedades finales de la pieza impresa, como resistencia, resistencia al calor y biocompatibilidad. – Selección de materiales es crucial en función de la aplicación deseada y los requisitos funcionales. – Los polvos se pueden mezclar para lograr propiedades específicas (por ejemplo, combinar metales para mejorar la relación resistencia-peso). | – Polvos metálicos Puede variar desde metales puros como el titanio hasta aleaciones complejas con propiedades personalizadas. – Polvos de polímero puede incluir nailon, poliamidas y materiales biocompatibles para aplicaciones médicas. |
Propiedades térmicas | El comportamiento del material en polvo bajo temperaturas variables, incluido el punto de fusión, la conductividad térmica y el coeficiente de expansión térmica. | Factores de impacto como estabilidad dimensional, deformación y distorsión por calor durante la impresión y el posprocesamiento. – Calefacción controlada es fundamental para evitar superar los límites térmicos del material y provocar defectos en las piezas. – Propiedades térmicas coincidentes del polvo y la plataforma de construcción Minimiza la deformación y garantiza la precisión dimensional. | – Polvos metálicos a menudo tienen puntos de fusión altos y requieren un control preciso de la temperatura durante procesos basados en láser como SLM (fusión selectiva por láser). – Polvos de polímero puede ablandarse o derretirse a temperaturas más bajas, |
Especificaciones del polvo de impresión 3D
Propiedad | Descripción | Impacto en la imprimibilidad y la calidad de las piezas | Ejemplos de materiales |
---|---|---|---|
Tamaño y distribución de partículas | Se refiere a los diámetros de partículas individuales y la variación dentro del polvo. Medido en micras (μm). | Los polvos finos (< 50 µm) ofrecen alta resolución y acabado superficial, pero pueden resultar difíciles de fluir y pueden requerir un manejo especial. Los polvos más gruesos (> 100 µm) mejoran la fluidez pero pueden limitar los detalles y aumentar la rugosidad de la superficie. Una distribución de tamaño estrecha garantiza un comportamiento de embalaje e impresión consistente. | Polímeros: Nailon (15-75 µm), Polipropileno (40-100 µm) |
Morfología de las partículas | La forma de las partículas de polvo individuales. | Las partículas esféricas fluyen libremente y se empaquetan de manera eficiente, lo que conduce a una buena imprimibilidad. Las formas irregulares pueden mejorar la unión entre partículas, pero pueden causar problemas de flujo y requerir técnicas de impresión específicas. | Polímeros: Normalmente esférico debido a los procesos de fabricación. |
Densidad aparente y densidad de empaquetadura | La densidad aparente es el peso del polvo por unidad de volumen en su estado suelto y vertido. La densidad de empaquetadura es la densidad máxima que se puede lograr después de golpear o vibrar. | La densidad aparente afecta el flujo y la manipulación del polvo. La densidad del embalaje influye en la densidad final de la pieza impresa y en sus propiedades mecánicas. Una mayor densidad de empaquetamiento generalmente conduce a piezas más resistentes. | Polímeros: Densidad aparente (0,3-0,8 g/cm³), Densidad de embalaje (0,5-0,9 g/cm³) |
Fluidez | La facilidad con la que el polvo fluye por gravedad o con mínima agitación. | Una buena fluidez es crucial para una distribución uniforme del polvo durante la impresión. Una fluidez deficiente puede provocar inconsistencias en las capas y defectos de impresión. | Polímeros: Normalmente fluyen libremente debido a su morfología esférica. Se pueden utilizar aditivos para mejorar la fluidez. |
Contenido de humedad | La cantidad de vapor de agua atrapada dentro de las partículas de polvo. | El exceso de humedad puede causar problemas durante la impresión, como explosiones de vapor o un comportamiento de fusión inconsistente. La mayoría de los polvos requieren un estricto control de la humedad. | Polímeros: Por lo general, un contenido de humedad muy bajo (<0,1 wt%) para evitar la hidrólisis y garantizar un comportamiento de impresión constante. |
Composición química y pureza | La composición elemental del polvo y la presencia de impurezas. | La composición química determina las propiedades finales de la pieza impresa. Las impurezas pueden afectar la imprimibilidad, el rendimiento mecánico y la calidad de la superficie. | Polímeros: Se utiliza material de alta pureza para garantizar propiedades e imprimibilidad consistentes. |
Propiedades térmicas | Punto de fusión, temperatura de transición vítrea (Tg) de polímeros y conductividad térmica. | Las propiedades térmicas influyen en los parámetros del proceso de impresión y en la microestructura final de la pieza impresa. | Polímeros: El punto de fusión y la Tg son cruciales para configurar parámetros de impresión como la potencia del láser o la temperatura de la cama. |
Proveedores de polvos de impresión 3D
Material | Aplicaciones clave | Proveedores representativos | Consideraciones |
---|---|---|---|
Polvos de polímero | – Creación de prototipos – Piezas funcionales – Dispositivos médicos – Bienes de consumo | * Poliamida (nylon): BASF, Evonik, Arkema * Ácido poliláctico (PLA): NatureWorks, ExxonMobil Química, DuPont * Polipropileno (PP): Real DSM, SABIC, Repsol | * El tamaño y la distribución de las partículas afectan la imprimibilidad y las propiedades finales de la pieza. * Las propiedades de los materiales, como la resistencia al calor, la flexibilidad y la biocompatibilidad, varían. *Considerar la compatibilidad química con las técnicas de posprocesamiento. |
Polvos metálicos | – Componentes aeroespaciales – Piezas de automoción – Implantes médicos – Herramientas y matrices | * Aleaciones de titanio: AP Powder Company, Höganäs, Aditivo GE * Acero inoxidable: Fabricación aditiva de carpintero, Soluciones SLM, EOS GmbH * Aleaciones de aluminio: Rio Tinto Alcan, Fabricación DLP, Exone | * La morfología (forma) del polvo afecta la fluidez y la densidad de empaquetamiento. * El tamaño de grano influye en las propiedades mecánicas de la pieza final. * Los protocolos de seguridad son cruciales al manipular polvos metálicos reactivos. |
Polvos compuestos | – Estructuras ligeras con alta resistencia – Componentes conductores – Implantes biocompatibles con propiedades mejoradas | * Compuestos de polímero-metal: Tecnología LPW, Markforged, Metal de escritorio * Compuestos Cerámico-Metal: Sandvik Hyperion, perfeccionador de extrusión, Plasma Technik * Compuestos de polímero y fibra de carbono: Stratasys, escritorio metálico, Henkel | * La selección depende de la combinación deseada de propiedades (resistencia, conductividad, biocompatibilidad). * La interfaz entre diferentes materiales requiere una cuidadosa consideración para un rendimiento óptimo. * Es posible que sea necesario ajustar los parámetros de impresión en comparación con los polvos de un solo material. |
Aplicaciones de Polvos de impresión 3D
Los polvos de impresión facilitan de manera única geometrías de piezas complejas y personalizadas en todas las industrias:
Industria | Componentes de ejemplo | Beneficios |
---|---|---|
Aeroespacial | Palas de turbinas, toberas de cohetes, chasis de vehículos aéreos no tripulados | Reducción de peso, aumento de rendimiento. |
Médico | Implantes y prótesis adaptados al paciente | Talla personalizada, biocompatibilidad. |
Automoción | Intercambiadores de calor, elementos de chasis ligeros. | Consolidación de piezas, eficiencia. |
Industrial | Herramientas de producción personalizadas, plantillas | Plazos de desarrollo más cortos |
Cuadro 5: Principales sectores de casos de uso que aprovechan las capacidades del polvo de impresión 3D
La capacidad de iterar rápidamente diseños e imprimir tiradas cortas de forma económica permite la innovación de piezas de uso final.
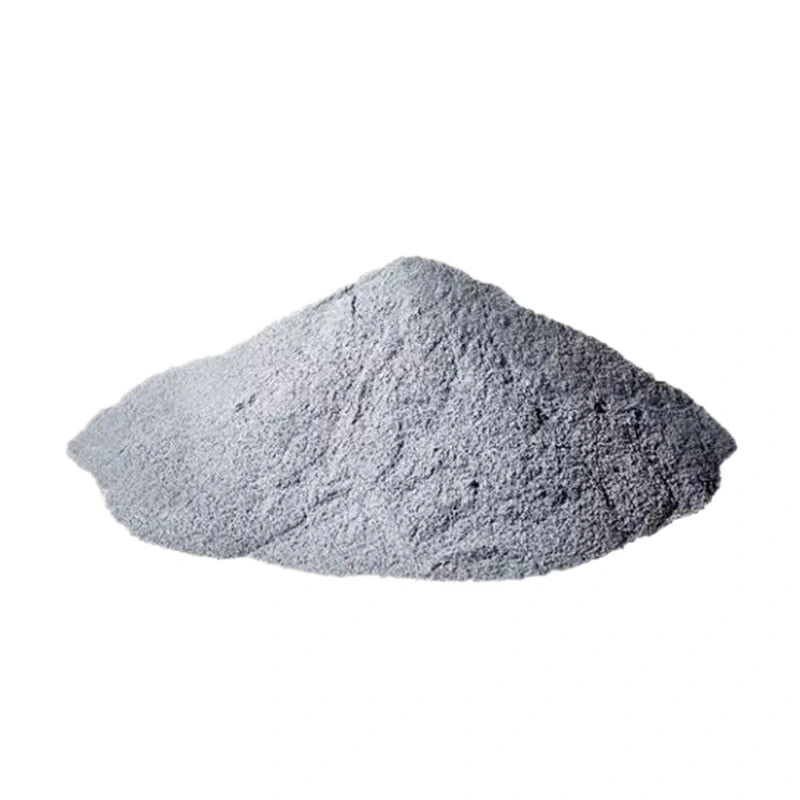
Pros y contras de la impresión 3D a base de polvo
Pros | Contras |
---|---|
Alta precisión y resolución | Manejo y seguridad del polvo |
Amplia gama de materiales | Tamaño de construcción limitado |
Estructuras de apoyo mínimas | Requisitos de postprocesamiento |
Tasas de producción rápidas | Inversión inicial elevada |
Preguntas frecuentes
P: ¿Qué rango de tamaño de partículas funciona mejor para los polvos metálicos de impresión 3D?
R: 10-45 micrones facilitan un buen empaque y esparcimiento y, al mismo tiempo, evitan desafíos con polvos ultrafinos en la manipulación de polvos. La mayoría de las aleaciones funcionan bien con una distribución de 30 ± 15 μm.
P: ¿Qué proceso de impresión 3D de polvo de polímero ofrece el mejor rendimiento mecánico?
R: La sinterización selectiva por láser (SLS) permite una fusión excelente y una producción de características finas, creando piezas de plástico de alto rendimiento que rivalizan o superan los procesos de moldeo por inyección.
P: ¿Cuánto tiempo puede durar almacenado el polvo de impresión 3D sin usar?
R: Se mantienen sellados con desecante contra la humedad en un ambiente fresco y seco; los polvos mantienen las características de flujo durante al menos 12 meses. Incluso los polvos abiertos duran más de 6 meses antes de una degradación notable.
P: ¿La calidad del polvo de partida influye significativamente en las propiedades de las piezas impresas?
R: Sí, la pureza química del polvo más un control adecuado de las características del polvo determinan en gran medida las propiedades mecánicas, la estética, la precisión dimensional y la confiabilidad del rendimiento de la pieza final.
Compartir
MET3DP Technology Co., LTD es un proveedor líder de soluciones de fabricación aditiva con sede en Qingdao, China. Nuestra empresa está especializada en equipos de impresión 3D y polvos metálicos de alto rendimiento para aplicaciones industriales.
Solicite información para obtener el mejor precio y una solución personalizada para su empresa.
Artículos relacionados
Acerca de Met3DP
Actualización reciente
Nuestro producto
CONTACTO
¿Tiene alguna pregunta? ¡Envíenos un mensaje ahora! Atenderemos su solicitud con todo un equipo tras recibir su mensaje.
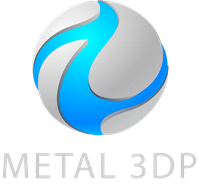
Polvos metálicos para impresión 3D y fabricación aditiva