Polvo de hierro de alta temperatura
Índice
Visión general
Polvos de hierro a alta temperatura son polvos metálicos especializados fabricados a partir de aleaciones con base de hierro diseñadas para funcionar a temperaturas elevadas superiores a 850°C sin perder rápidamente resistencia. Los polvos de hierro y acero convencionales se oxidan y deterioran más rápidamente por encima de este umbral.
Mediante una cuidadosa adaptación de la química del polvo y los tratamientos de procesado, se mejora la resistencia a las altas temperaturas y al medio ambiente. Entre las principales áreas de aplicación que exigen este tipo de materiales estructurales térmicos extremos se encuentran la automoción, la industria aeroespacial, los equipos de generación de energía y las industrias de procesamiento químico.
Tipos de Polvos de hierro para altas temperaturas
Tipo | Método de producción | Características principales | Aplicaciones (por su rendimiento a altas temperaturas) |
---|---|---|---|
Polvo de hierro carbonilado | Descomposición del vapor de pentacarbonilo de hierro a altas temperaturas | - Alta pureza (>99% Fe) - Morfología esférica de las partículas - Superficie lisa - Control estricto del tamaño - Propiedades magnéticas blandas | - Componentes magnéticos de alto rendimiento (por ejemplo, inductores para aplicaciones de alta frecuencia) - Núcleos magnéticos blandos para transformadores y motores - Absorbedores de microondas - Aplicaciones catalizadoras gracias a su elevada superficie |
Hierro electrolítico en polvo | Electrólisis de soluciones de cloruro de hierro | - Pureza muy elevada (a menudo superior al 99,5% Fe) - Partículas densas y esféricas - Excelente fluidez - Alta compresibilidad | - Núcleos magnéticos blandos para aplicaciones de alta frecuencia, como transformadores e inductores - Componentes electrónicos que requieren gran pureza (por ejemplo, blindaje electromagnético) - Fabricación aditiva de piezas metálicas complejas con forma casi de red - Aplicaciones que aprovechan la buena conductividad eléctrica a temperaturas elevadas |
Polvo de hierro atomizado en agua | El hierro fundido se rompe en finas partículas mediante chorros de agua a alta presión | - Alto índice de producción - Menor coste entre los polvos de hierro de alta temperatura - Contenido de oxígeno relativamente alto - Formas irregulares de las partículas - Amplia distribución granulométrica | - Aplicaciones en las que el coste es una preocupación primordial (por ejemplo, algunos procesos de moldeo por inyección de metales) - Piezas que requieren una buena maquinabilidad después de la sinterización - Soldadura fuerte a alta temperatura debido a la presencia de oxígeno - Aplicaciones que se benefician de un empaquetamiento irregular de las partículas (por ejemplo, algunos medios de filtración). |
Polvo de hierro recocido al vacío | Tratamiento posterior de otros polvos de hierro (a menudo atomizados con agua) mediante recocido en atmósfera de hidrógeno. | - Mejora las propiedades del polvo base (por ejemplo, reduce el contenido de oxígeno, mejora la forma de las partículas) - Propiedades a medida basadas en el polvo de partida | - Aplicaciones que requieren un equilibrio entre coste y rendimiento a altas temperaturas (por ejemplo, algunos componentes magnéticos blandos) - Procesos de fabricación aditiva en los que se necesitan características específicas del polvo - Aplicaciones de soldadura fuerte que exigen un buen rendimiento a temperaturas elevadas |
Métodos de producción de polvos a alta temperatura
Método | Descripción | Ventajas | Desventajas | Materiales típicos producidos |
---|---|---|---|---|
Atomización de gases | El metal fundido se desintegra en finas gotas mediante una corriente de gas inerte a alta velocidad | - Polvos de gran pureza - Morfología esférica de las partículas - Estrecha distribución de tamaños - Buena fluidez - Adecuado para una amplia gama de materiales | - Alto consumo de energía - Relativamente caro en comparación con otros métodos - Posibilidad de formación de óxido en algunos materiales | - Aleaciones de alta temperatura (por ejemplo, superaleaciones de níquel, aluminuros de titanio) - Metales refractarios (por ejemplo, wolframio, molibdeno) - Aceros para herramientas |
Atomización del agua | El metal fundido se fragmenta en gotas mediante chorros de agua a alta presión. | - Alto índice de producción - Bajo coste - Aplicable a una amplia gama de materiales | - Formas irregulares de las partículas - Amplia distribución del tamaño de las partículas - Mayor contenido de oxígeno en comparación con la atomización con gas | - Aceros de baja aleación y hierros - Aceros inoxidables (para algunas aplicaciones) - Polvos para moldeo por inyección de metales (MIM) |
Atomización por plasma | El metal fundido se inyecta en un flujo de plasma de alta temperatura y alta velocidad, lo que provoca una rápida solidificación. | - Polvos ultrafinos (<10 micrómetros) - Partículas esféricas - Distribución de tamaños estrecha - Potencial para producir fases metaestables | - Consumo de energía muy elevado - Capacidad de producción limitada - Proceso complejo y costoso | - Polvos metálicos amorfos - Aleaciones de alto rendimiento para aplicaciones aeroespaciales y de turbinas |
Descomposición del carbonilo | Descomposición térmica de carbonilos metálicos (compuestos metálicos que contienen monóxido de carbono) a altas temperaturas | - Polvos de gran pureza - Morfología esférica de las partículas - Control estricto del tamaño y la morfología de las partículas | - Limitado a unos pocos metales que forman carbonilos estables (p. ej., hierro, níquel) - Proceso complejo y relativamente lento | - Polvos de hierro de gran pureza para aplicaciones magnéticas - Materiales catalizadores |
Electrólisis | Deposición de metal a partir de una sal fundida o una solución acuosa mediante corriente eléctrica. | - Polvos de muy alta pureza - Partículas densas y esféricas - Excelente fluidez | - Velocidad de producción limitada - Coste elevado - Aplicable a una gama limitada de materiales | - Polvo de hierro electrolítico para componentes magnéticos de alto rendimiento - Polvo de cobre para aplicaciones eléctricas |
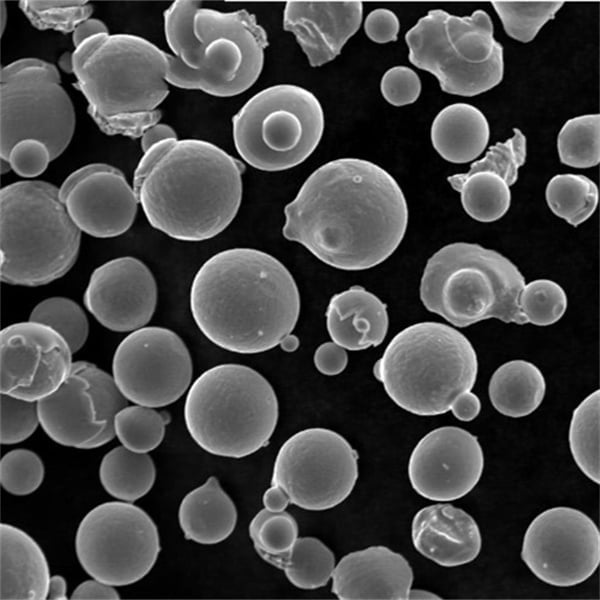
Tipos de aleaciones y composiciones
Existen cuatro categorías principales de polvos especiales de aleaciones de hierro diseñados para un uso prolongado a temperaturas superiores a 850°C:
Polvos de acero inoxidable austenítico
Aleaciones como los aceros inoxidables 316L, 304L y 301L contienen níquel para mantener una estructura cristalina austenítica FCC hasta 1100°C y cromo para la resistencia a la oxidación mediante películas superficiales protectoras de cromo (Cr2O3) a altas temperaturas.
Elemento de aleación | Papel | Peso % Gama |
---|---|---|
Níquel (Ni) | Estabilizador de austenita | 8 – 12% |
Cromo (Cr) | Resistencia a la oxidación | 16 – 18% |
Manganeso (Mn) | Resistencia y refinamiento del grano | Hasta 2% |
Nitrógeno (N) | Fortalecimiento | 0.1 – 0.25% |
Beneficios: Excelente "resistencia en caliente", facilidad de compactación y sinterización, menor coste que las superaleaciones.
Limitaciones: Propenso a la fluencia por encima de 1000°C, no apto para aplicaciones dinámicas con carga.
Aleaciones de hierro con alto contenido en níquel
Las aleaciones de níquel-hierro que contienen entre 25 y 60 wt% de níquel ofrecen la combinación óptima de resistencia a altas temperaturas, tenacidad y resistencia a la corrosión. Las adiciones de níquel ralentizan drásticamente las velocidades de difusión y reducen los cambios microestructurales perjudiciales hasta los 1150 °C.
Otros elementos de aleación clave son:
Elemento de aleación | Papel | Peso % Gama |
---|---|---|
Níquel (Ni) | Fortalecimiento de la solución sólida | 25 – 60% |
Cromo (Cr) | Resistencia a la oxidación | 10 – 25% |
Cobalto (Co) | Mejora las propiedades mecánicas a alta temperatura | 10 – 25% |
Molibdeno (Mo) | Resistencia a la fluencia | 2 – 6% |
Beneficios: Rendimiento mecánico inigualable a 1100°C+, cinética de degradación más lenta. Microestructura térmicamente estable.
Limitaciones: Precios de aleación muy elevados, dificultades de control de la porosidad, que requieren densificación HIP.
Aleaciones de hierro reforzadas por dispersión de óxidos
En las aleaciones reforzadas por dispersión de óxidos, se incrustan partículas muy finas (50-100 nm) de óxido de itrio inerte en la matriz del material. Estos óxidos a escala nanométrica impiden el movimiento de las dislocaciones, manteniendo así la resistencia por encima de los 1.000 °C.
Elemento de aleación | Papel | Peso % Gama |
---|---|---|
Óxido de itrio (Y2O3) | Partículas de nanoóxido que proporcionan estabilidad térmica | 0.25% – 1% |
Cromo (Cr) | Resistencia medioambiental | Hasta 20% |
Aluminio (Al) | Mejora la dispersión del óxido | Hasta 4% |
Beneficios: Excepcional estabilidad microestructural y resistencia a la fluencia en condiciones de funcionamiento de 1100°C+.
Limitaciones: Coste muy elevado, dificultades de transformación - fabricado tradicionalmente mediante aleación mecánica y consolidación.
Aleaciones de aluminuro de hierro (FeAl)
Las aleaciones de aluminuro de hierro con un contenido de aluminio de 10- 40% ofrecen una excelente resistencia a la oxidación y a la sulfuración hasta 900°C mediante la formación de una capa superior protectora duradera de alúmina (Al2O3). El cromo contribuye a la protección de la superficie.
Elemento de aleación | Papel | Peso % Gama |
---|---|---|
Aluminio (Al) | Resistencia a la oxidación | 10 – 40% |
Cromo (Cr) | Mejora la resistencia medioambiental | 5 – 10% |
Carbono, Zr (C, Zr) | Reforzadores de carburo | Hasta 0,5% |
Beneficios: Gran estabilidad medioambiental, densidades inferiores a las de los aceros, facilidad de fabricación en relación con las superaleaciones.
Limitaciones: Pérdida de resistencia por encima de 750°C, escasa resistencia a la fluencia, las tensiones aplicadas aumentan los fenómenos de plaga.
Métodos de producción
Se utilizan técnicas especiales para producir polvos de aleaciones de hierro a alta temperatura con características adecuadas:
Atomización de gases
- El enfriamiento rápido y controlado de la corriente de metal fundido permite la retención de los elementos de aleación en solución en lugar de la formación de precipitados.
Esferoidización del plasma
- Los polvos irregulares procedentes de procesos de atomización con agua se refunden mediante un soplete de plasma y se vuelven a solidificar en polvos esféricos ideales para los métodos de AM.
Múltiples ciclos Sinter-Crush
- Los polvos se compactan repetidamente a altas temperaturas, se trituran y se tamizan para refinar la distribución del polvo, ideal para la procesabilidad MIM.
Aleación mecánica
- El fresado con bolas de polvos metálicos elementales crea distribuciones nanodispersas de partículas y clusters en aleaciones ODS
Refinado de carbonilo
- Produce polvos metálicos de pureza extremadamente alta cuando los métodos de producción de menor coste producen contaminación
Comparación de los métodos de producción
Método | Niveles de pureza | Contenido de oxígeno | Opciones de morfología | Producción (toneladas/año) |
---|---|---|---|---|
Atomización de gases | Moderado | <1000 ppm | Mayormente esférico | Alta >20.000 |
Atomización del agua | Bajo | 2000-4000 ppm | Irregular | Muy alto >50.000 |
Esferoidización del plasma | Medio | 500-2000 ppm | Esférica | Bajo <5.000 |
Aleación mecánica | Alta | <1500 ppm | Formas variables de las partículas | Cientos bajos |
Proceso carbonílico | Extremadamente alto | <200 ppm | Esférico/nodular | Alta >25.000 |
Métodos de caracterización
Varios métodos analíticos son vitales para calificar las aleaciones en polvo de alta temperatura:
Composición química
- Las técnicas espectrográficas y de química húmeda identifican los constituyentes elementales y las cantidades, necesarias para verificar el diseño de las aleaciones.
- Los contenidos de carbono, azufre, oxígeno y nitrógeno muestran una contaminación inducida por el proceso que afecta al rendimiento del material.
Tamaño y morfología de las partículas
- Los analizadores granulométricos por difracción láser determinan la granulometría completa desde tamaños de 10 nm a 3 mm
- Las imágenes SEM visualizan la forma, las características de la superficie, las partículas satélite y la porosidad, lo que resulta útil para evaluar la idoneidad del proceso de fabricación y analizar los defectos.
Cristalografía
- La DRX muestra las fases presentes, los estados de precipitación, el análisis cuantitativo de las propiedades cristalinas
- Evalúa los efectos de la exposición térmica en las fracciones de fase mediante la evolución microestructural
Pruebas de propiedades del polvo
- La flujometría Hall, la densidad aparente y la compresibilidad cuantifican el comportamiento del polvo para facilitar su manipulación y consolidación
Aplicaciones y usos de los polvos de alta temperatura
Área de aplicación | Tipo de polvo (Ejemplos) | Propiedades clave utilizadas | Beneficios |
---|---|---|---|
Fabricación aditiva de metales (AM) | Superaleaciones de níquel atomizadas por gas, aceros inoxidables atomizados por agua | - Morfología esférica para una buena fluidez - Distribución de tamaños estrecha para una deposición uniforme - Rendimiento a alta temperatura para la construcción de piezas funcionales | - Permite la creación de componentes complejos con formas próximas a la red - Propiedades de los materiales adaptadas a aplicaciones específicas - Reducción de los residuos en comparación con la fabricación sustractiva tradicional |
Componentes magnéticos de alto rendimiento | Polvo de hierro carbonílico, polvo de hierro electrolítico | - Alta pureza para bajas pérdidas de energía - Morfología esférica para una buena densidad del núcleo - Propiedades magnéticas blandas para una eficiente transferencia de energía | - Mejora de la eficiencia en transformadores, inductores y motores - Reducción de las temperaturas de funcionamiento y los niveles de ruido - Miniaturización de los dispositivos gracias a un mejor rendimiento magnético |
Soldadura fuerte a alta temperatura | Polvo de hierro atomizado con agua, aleaciones de níquel atomizadas con gas | - Punto de fusión controlado para soldar diferentes materiales - Presencia de óxidos (en algunos polvos) para mejorar la humectación y la unión - Resistencia a altas temperaturas para uniones robustas | - Unión de metales y aleaciones distintos - Creación de juntas resistentes y estancas en entornos difíciles - Aplicaciones en los sectores aeroespacial, de automoción y de generación de energía |
Revestimientos por pulverización térmica | Aleaciones de aluminio atomizadas por agua, superaleaciones de níquel atomizadas por gas | - Amplia gama de puntos de fusión para diversas aplicaciones de recubrimiento - Formas de partículas irregulares para el enclavamiento mecánico - Resistencia a altas temperaturas para proteger los sustratos | - Mayor resistencia al desgaste y a la corrosión - Aislamiento térmico - Restauración de componentes desgastados - Aplicaciones en motores, turbinas e intercambiadores de calor |
Moldeo por inyección de metal (MIM) | Aceros atomizados en agua, polvos prealeados | - Granulometría fina para geometrías de pieza complejas - Buena fluidez para un llenado uniforme del molde - Propiedades del polvo controladas para una precisión dimensional | - Producción rentable de piezas metálicas complejas de forma próxima a la red - Alta resistencia y densidad alcanzables - Aplicaciones en los sectores de automoción, médico y electrónico |
Aplicaciones catalíticas | Polvo de hierro carbonilado, metales de transición atomizados por gas | - Alta superficie para reacciones catalíticas eficaces - Estructura de poros controlada para catálisis selectiva - Morfología de partículas adaptada para mejorar la actividad catalítica | - Control de emisiones en sistemas de escape de automóviles - Reacciones de transformación química - Producción de combustibles limpios y energías renovables |
Especificaciones y grados
Las aleaciones en polvo para alta temperatura deben cumplir unas especificaciones mínimas en cuanto a química, limpieza, características de las partículas y propiedades:
Característica | Descripción | Consideraciones clave |
---|---|---|
Composición del material | Los polvos de alta temperatura se presentan en una gran variedad de materiales, cada uno de ellos con propiedades distintas adecuadas para aplicaciones específicas. Los materiales más comunes son: Aleaciones a base de níquel: Ofrece una excepcional resistencia a la oxidación y a las altas temperaturas, ideal para componentes de motores a reacción, intercambiadores de calor y piezas de turbinas de gas. Aleaciones a base de cobalto: Conocidos por su resistencia al desgaste y estabilidad térmica, se utilizan con frecuencia en herramientas de corte, álabes de turbinas e implantes biomédicos. Aceros inoxidables: Proporciona un equilibrio entre resistencia a la corrosión y rendimiento a altas temperaturas, adecuado para colectores de escape, calderas y equipos de procesamiento de alimentos. Aceros para herramientas: Ofrece una dureza excepcional y resistencia al desgaste a temperaturas elevadas, perfecta para moldes, matrices y punzones. Cerámica refractaria: Ofrece una capacidad de aislamiento térmico superior y se utiliza habitualmente en revestimientos de hornos, crisoles y toberas de cohetes. | La selección del material depende del uso previsto. Hay que tener en cuenta factores como la temperatura máxima de funcionamiento, las propiedades mecánicas deseadas (solidez, resistencia al desgaste), la resistencia a la oxidación y la compatibilidad con el entorno. |
Tamaño y distribución de partículas | El tamaño y la distribución de las partículas de polvo influyen significativamente en el proceso de aplicación y en las características del producto final. Polvos más finos (10-45 micras): Mejora el acabado superficial y produce revestimientos finos y lisos. Adecuado para aplicaciones de deposición por pulverización electrostática y lecho fluidizado. Polvos más gruesos (45-150 micras): Ofrecen mejor fluidez y pueden crear revestimientos más gruesos. Más aplicables para técnicas de prensado y sinterización. | El tamaño de las partículas es crucial para conseguir el espesor de revestimiento y la estética deseados. Una distribución equilibrada garantiza una aplicación eficaz y minimiza los residuos. |
Fluidez | La facilidad con la que fluye el polvo es esencial para una aplicación consistente y un uso eficiente. Los polvos con buena fluidez permiten una alimentación suave en pistolas pulverizadoras y tolvas, minimizando la formación de grumos y los bloqueos. | Una fluidez inadecuada puede provocar incoherencias en la aplicación, recubrimientos desiguales y retrasos en la producción. Los fabricantes suelen utilizar aditivos o ajustar la distribución del tamaño de las partículas para optimizar la fluidez. |
Densidad aparente | Se refiere al peso del polvo por unidad de volumen, lo que influye en factores como los requisitos de almacenamiento, la capacidad de la tolva y el espesor del revestimiento. * Polvos de alta densidad aparente: Ofrecen ventajas en términos de almacenamiento eficiente y potencialmente requieren menos material para lograr un espesor de revestimiento específico. * Polvos de baja densidad aparente: Puede requerir mayores espacios de almacenamiento, pero puede ser más fácil de manejar y crear revestimientos más gruesos con una sola aplicación. | La densidad aparente influye en la manipulación del material, las necesidades de almacenamiento y la eficacia del revestimiento. La selección de la densidad adecuada depende de los requisitos de la aplicación y del equipo disponible. |
Punto de fusión y dilatación térmica | El punto de fusión determina la temperatura máxima utilizable del polvo, mientras que la expansión térmica dicta los cambios dimensionales al calentarlo. * Polvos de alto punto de fusión: Pueden soportar temperaturas extremas, lo que los hace adecuados para aplicaciones exigentes como componentes de motores de cohetes. * Polvos de baja expansión térmica: Minimizan los cambios dimensionales durante los ciclos de calentamiento, cruciales para mantener tolerancias precisas en entornos de alta temperatura. | Comprender estas propiedades es vital para garantizar que el polvo pueda soportar la temperatura de funcionamiento prevista sin comprometer la funcionalidad ni la estabilidad dimensional. |
Resistencia a la corrosión | La capacidad del material en polvo para resistir la degradación por factores ambientales como la oxidación o el ataque químico es fundamental para el rendimiento a largo plazo. Polvos altamente resistentes a la corrosión: Mantienen su integridad en entornos difíciles, ideales para aplicaciones expuestas a productos químicos, alta humedad o niebla salina. Polvos más resistentes a la corrosión: Pueden requerir tratamientos superficiales adicionales o revestimientos protectores para prolongar su vida útil. | La selección de la resistencia a la corrosión depende de las condiciones de exposición previstas. Elegir un polvo muy resistente a la corrosión puede prolongar la vida útil del producto final. |
Análisis de costes de los polvos de alta temperatura
Factor | Descripción | Impacto en el coste |
---|---|---|
Tipo de material | Como ya se ha explicado, los polvos de alta temperatura están disponibles en varios materiales, cada uno con un precio diferente. Aleaciones a base de níquel: Suelen ser los más caros debido a su excepcional rendimiento a altas temperaturas y a sus complejos procesos de fabricación. Aleaciones a base de cobalto: Suelen tener un precio similar al de las aleaciones con base de níquel, pero pueden variar en función del contenido específico de cobalto y de las propiedades deseadas. Aceros inoxidables: Suelen ser más asequibles que las aleaciones a base de níquel o cobalto y ofrecen un equilibrio entre coste y prestaciones. Aceros para herramientas: Su coste puede variar en función de los elementos de aleación específicos y de las propiedades deseadas. Suelen ser más baratos que los basados en níquel o cobalto. Cerámica refractaria: Aunque presentan una excelente resistencia al calor, algunas cerámicas refractarias pueden ser relativamente baratas, sobre todo en el caso de materiales comunes como la alúmina. Sin embargo, las cerámicas más especializadas o de mayor pureza pueden ser bastante más caras. | La selección de materiales influye significativamente en el coste global del proyecto. Evalúe cuidadosamente los requisitos de rendimiento frente a las limitaciones presupuestarias. |
Pureza del polvo | El grado de pureza de un polvo de alta temperatura afecta directamente a sus propiedades y a su precio. Polvos de gran pureza: Ofrecen características de rendimiento superiores, como mayor resistencia, mayor resistencia a la oxidación y mejor comportamiento de sinterización. Sin embargo, tienen un precio elevado debido a los complejos procesos de purificación que conllevan. Polvos de menor pureza: Puede ser suficiente para algunas aplicaciones en las que no es fundamental maximizar el rendimiento. Estos polvos suelen ser más rentables. | Considere el equilibrio entre el rendimiento deseado y la rentabilidad. En algunos casos, una ligera reducción de la pureza puede ser aceptable si se traduce en un importante ahorro de costes. |
Tamaño y distribución de partículas | El tamaño y la distribución de las partículas de polvo pueden influir tanto en el coste del material como en los costes de transformación. Polvos más finos: Generalmente requieren procesos de fabricación más complejos y que consumen más energía, lo que conlleva un mayor coste por unidad de peso. Polvos más gruesos: Aunque su producción es potencialmente menos costosa, pueden requerir pasos de procesamiento adicionales (por ejemplo, molienda) para lograr la distribución de tamaño de partícula deseada para aplicaciones específicas, lo que podría compensar parte de la ventaja inicial en el coste. | Optimizar el tamaño de las partículas para la aplicación elegida puede ayudar a encontrar un equilibrio entre el material y los costes de transformación. |
Cantidad mínima de pedido (MOQ) | Muchos proveedores establecen cantidades mínimas de pedido (MOQ) para los polvos de alta temperatura. Grandes MOQ: Puede acarrear importantes costes iniciales, sobre todo en el caso de los polvos menos utilizados o especializados. MOQs más pequeños: Puede estar disponible a un precio superior debido a la mayor manipulación y administración que conllevan los lotes más pequeños. | Tenga en cuenta los requisitos del proyecto y el potencial de desperdicio. Si no se aprovecha al máximo un MOQ grande, explore proveedores alternativos que ofrezcan cantidades menores o colabore con otros usuarios para compartir un pedido mayor. |
Reputación y ubicación del proveedor | La reputación del proveedor de polvo influye significativamente en el coste y el éxito global del proyecto. Proveedores reputados: Aplique estrictas medidas de control de calidad, que garanticen la homogeneidad de las propiedades del material y minimicen el riesgo de recibir polvos inservibles. Esta fiabilidad puede salir cara. Proveedores menos establecidos: Pueden ofrecer precios más bajos pero carecer de procedimientos rigurosos de control de calidad, lo que puede dar lugar a tasas de rechazo más elevadas o a resultados irregulares. | Evalúe detenidamente las cualificaciones de los proveedores y dé prioridad a una calidad constante frente a unos costes iniciales potencialmente más bajos. |
Plazo de entrega | El tiempo que tarde en entregarse el polvo puede influir en los plazos del proyecto y repercutir potencialmente en los costes. Plazos de entrega más cortos: Puede requerir opciones de envío urgente, que pueden ser más caras. Plazos de entrega más largos: Pueden ser más rentables, pero requieren una planificación y una gestión del inventario cuidadosas para evitar retrasos en la producción. | Evalúe la relación entre el coste y el calendario del proyecto. Si los plazos de entrega son críticos, estudie las opciones de envío urgente o existencias de reserva para mitigar los posibles retrasos. |
Ventajas e inconvenientes de las aleaciones de hierro para altas temperaturas
Característica | Ventaja | Desventaja |
---|---|---|
Relación coste-eficacia | En comparación con otros materiales de alta temperatura, como las superaleaciones a base de níquel o cobalto, las aleaciones a base de hierro ofrecen una importante ventaja económica. El hierro es un elemento fácilmente disponible, por lo que su producción suele ser menos costosa. | Aunque son rentables, las aleaciones de hierro para altas temperaturas no siempre alcanzan el mismo nivel de rendimiento que algunas opciones basadas en níquel o cobalto en términos de temperatura máxima de funcionamiento o propiedades mecánicas específicas. |
Resistencia a la oxidación | Algunas aleaciones de hierro pueden presentar una buena resistencia a la oxidación a temperaturas moderadas (hasta unos 700 °C). Elementos de aleación como el cromo y el aluminio ayudan a formar una capa protectora de óxido que impide la oxidación posterior. | La resistencia a la oxidación de las aleaciones de hierro suele ser inferior a la de las superaleaciones a base de níquel o cobalto, que pueden mantener su integridad a temperaturas mucho más elevadas. Las aleaciones de hierro pueden requerir tratamientos superficiales o revestimientos adicionales para prolongar su vida útil en entornos altamente oxidantes. |
Fuerza y resistencia a la fluencia | Aunque no están a la altura de las mejores, algunas aleaciones de hierro pueden ofrecer una solidez y una resistencia a la fluencia adecuadas a temperaturas elevadas. Elementos de aleación específicos como el molibdeno y el vanadio pueden mejorar estas propiedades, haciéndolas adecuadas para diversas aplicaciones industriales. | La resistencia a altas temperaturas y a la fluencia de las aleaciones de hierro suelen ser inferiores a las de las superaleaciones con base de níquel o cobalto. Para aplicaciones que requieran un rendimiento excepcional a temperaturas extremas, pueden ser necesarias otras opciones de materiales. |
Soldabilidad y mecanizabilidad | Las aleaciones con base de hierro suelen ser más soldables y mecanizables que otros materiales de alta temperatura. Esto facilita la fabricación y reduce los costes generales de procesamiento. | Aunque son soldables y mecanizables, las aleaciones de hierro pueden requerir técnicas de soldadura o procedimientos de mecanizado específicos para evitar comprometer sus propiedades en la unión soldada o introducir tensiones de mecanizado. |
Reciclabilidad | El hierro es uno de los metales más reciclados en todo el mundo. Las aleaciones de hierro de alta temperatura pueden reciclarse al final de su vida útil, lo que minimiza el impacto medioambiental y ofrece cierto grado de sostenibilidad del material. | El proceso de reciclado de aleaciones complejas de hierro puede ser más complicado que el del hierro puro, y factores como los elementos de aleación y los contaminantes superficiales pueden influir en la reciclabilidad. |
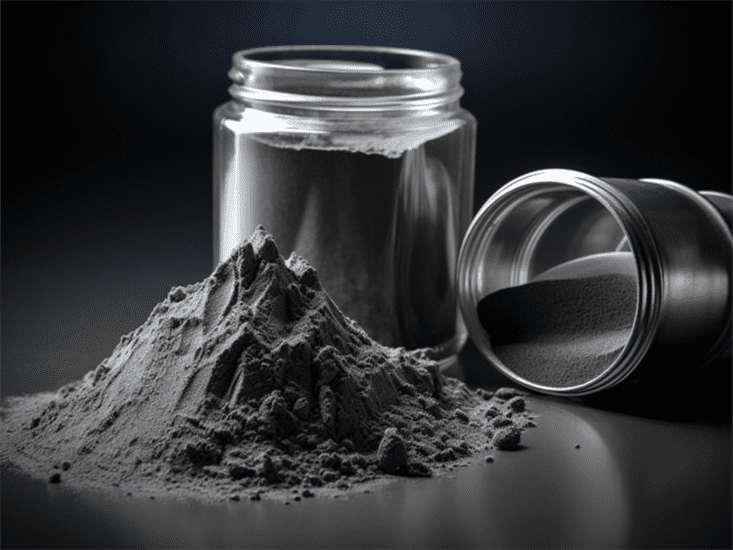
Preguntas frecuentes
P: ¿Cuál es la distribución típica del tamaño de las partículas utilizadas para los polvos de acero inoxidable de alta temperatura en metal AM?
R: En los procesos de fusión de lecho de polvo, como la fusión selectiva por láser (SLM) y la fusión por haz de electrones (EBM), el rango común es de fracciones de tamaño de 15 μm - 45 μm. Las distribuciones más finas pueden mejorar la resolución, pero dificultan la dispersión del polvo durante la deposición de capas y reducen las características de flujo.
P: ¿Qué velocidades de enfriamiento de la atomización con gas conservan las composiciones óptimas del polvo de aleación?
R: Para obtener la mejor combinación de retención química y morfología adecuada del polvo, se utilizan ampliamente velocidades de solidificación entre 1000 y 3000°C por segundo para polvos de acero inoxidable y superaleaciones de alta temperatura.
P: ¿Por qué son perjudiciales los altos niveles de partículas de óxido en las aleaciones de hierro a alta temperatura?
R: Durante el servicio, los óxidos presentes pueden engrosarse y migrar formando poblaciones de óxidos menos protectoras y menos estables, lo que provoca un ataque acelerado de los entornos oxidantes, sulfidizantes, carburantes o clorantes, reduciendo la vida útil de los componentes. En el desarrollo de aleaciones es necesario determinar y controlar cuidadosamente los niveles de oxígeno en función de las temperaturas máximas de exposición y las condiciones de funcionamiento.
P: ¿Qué métodos pueden utilizarse para aumentar la densidad del polvo a >95% teórica?
R: El prensado isostático en caliente suele aplicarse a componentes de acero inoxidable o superaleaciones de alta temperatura tras la fabricación inicial AM o MIM para eliminar los poros residuales, creando un rendimiento del material cercano al de las aleaciones forjadas en los mismos estados de tratamiento térmico reforzado. Las densidades cercanas a las teóricas garantizan la robustez mecánica.
P: ¿Por qué es crítico el control del nitrógeno por debajo de 1000 ppm en aleaciones de cobre de alta resistencia y conductividad?
R: La captación de nitrógeno forma fases de nitruro muy duras y quebradizas que reducen drásticamente la conductividad térmica y eléctrica, lo que reduce la funcionalidad en aplicaciones de gestión térmica y disminuye la conformabilidad y la ductilidad durante la fabricación.
Compartir
MET3DP Technology Co., LTD es un proveedor líder de soluciones de fabricación aditiva con sede en Qingdao, China. Nuestra empresa está especializada en equipos de impresión 3D y polvos metálicos de alto rendimiento para aplicaciones industriales.
Solicite información para obtener el mejor precio y una solución personalizada para su empresa.
Artículos relacionados
Acerca de Met3DP
Actualización reciente
Nuestro producto
CONTACTO
¿Tiene alguna pregunta? ¡Envíenos un mensaje ahora! Atenderemos su solicitud con todo un equipo tras recibir su mensaje.
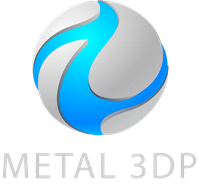
Polvos metálicos para impresión 3D y fabricación aditiva