Inconel 600 Polvo
Índice
El Inconel 600 es un material de ingeniería estándar para aplicaciones de alta temperatura de hasta 1100°C. Esta guía cubre Inconel 600 polvo composiciones, propiedades, métodos de fabricación, aplicaciones, especificaciones, precios, comparaciones y preguntas frecuentes a la hora de considerar esta aleación de níquel, cromo y hierro.
Composición típica del polvo de Inconel 600
Elemento | Peso % |
---|---|
Níquel | 72% min |
Cromo | 14-17% |
Hierro | 6-10% |
Carbono | 0,15% máx. |
Manganeso | 1% máx |
Azufre | 0,015% máx |
Silicio | 0,5% máx |
Cobre | 0,5% máx |
El níquel-cromo equilibra la resistencia a altas temperaturas con la fabricabilidad. El bajo contenido de carbono minimiza la precipitación de carburos nocivos durante exposiciones superiores a 550 °C.
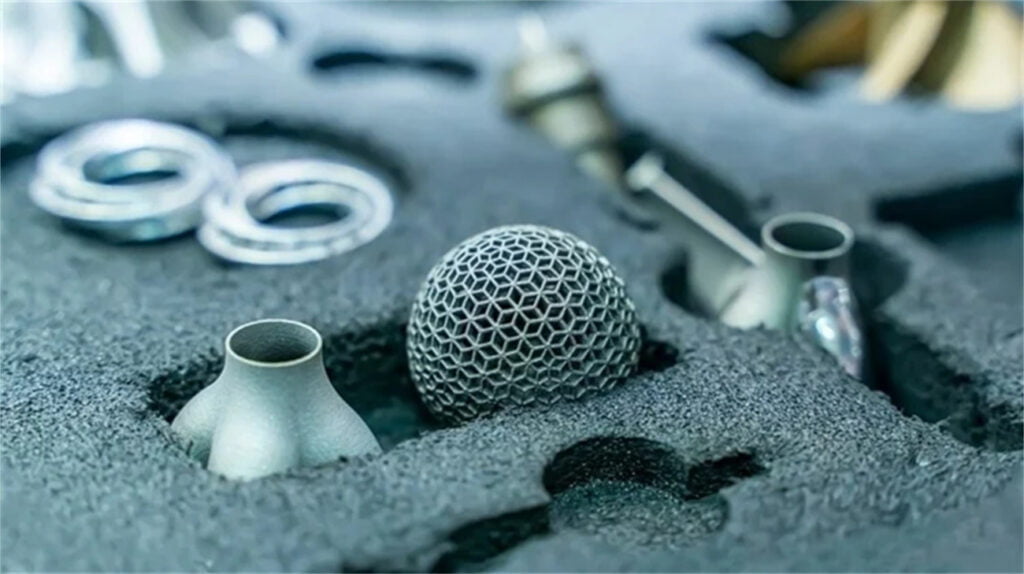
Propiedades y características clave
Propiedad | Descripción | Beneficio |
---|---|---|
Resistencia a altas temperaturas | El polvo de Inconel 600 conserva su impresionante resistencia incluso a temperaturas abrasadoras que alcanzan los 1093 °C (2000 °F). Esta resistencia lo convierte en el material perfecto para piezas expuestas a un calor extremo, como las que se encuentran en motores de turbinas de gas y cámaras de combustión. | El polvo de Inconel 600 permite crear componentes que pueden funcionar a la perfección en entornos en los que otros materiales sucumbirían a la debilidad inducida por el calor. |
Excepcional resistencia a la corrosión | El polvo de Inconel 600 presenta una resistencia superior a diversos agentes corrosivos, como ácidos, álcalis e iones cloruro. Permanece estable y sin manchas tanto en entornos oxidantes como reductores, por lo que es ideal para su uso en equipos de procesamiento químico, componentes marinos y centrales nucleares. | Esta propiedad garantiza que el polvo de Inconel 600 pueda resistir los duros ataques químicos, salvaguardando la integridad estructural de los componentes en aplicaciones exigentes. |
Excelente formabilidad | A diferencia de algunas superaleaciones, el polvo de Inconel 600 presenta una buena ductilidad, lo que permite moldearlo y darle forma mediante técnicas convencionales de metalurgia. Esta característica simplifica el proceso de fabricación de piezas complejas. | La forjabilidad del polvo de Inconel 600 reduce la necesidad de métodos de fabricación especializados, agilizando la producción y reduciendo los costes generales. |
Soldabilidad | El polvo de Inconel 600 ofrece una soldabilidad excepcional, lo que permite crear uniones fuertes y fiables entre materiales similares o distintos. Esta propiedad es crucial para fabricar estructuras complejas a partir de múltiples componentes. | La capacidad de soldar polvo de Inconel 600 sin costuras facilita la construcción de componentes robustos y fiables para diversas aplicaciones. |
Buena resistencia a la fatiga | El polvo de Inconel 600 demuestra una notable resistencia a la fatiga, que es el debilitamiento de un material debido a ciclos de tensión repetidos. Esta característica garantiza que los componentes puedan soportar una exposición prolongada a cargas fluctuantes sin sucumbir al fallo. | La resistencia a la fatiga del polvo de Inconel 600 lo hace adecuado para aplicaciones que implican vibraciones constantes o tensiones cíclicas, como los álabes de las turbinas y las piezas de los motores a reacción. |
Resistencia a la oxidación | El polvo de Inconel 600 presenta una resistencia excepcional a la oxidación, un proceso en el que un material reacciona con el oxígeno a altas temperaturas. Esta propiedad permite que los componentes mantengan su integridad estructural y su rendimiento en entornos con temperaturas elevadas y presencia de oxígeno. | La resistencia a la oxidación del polvo de Inconel 600 evita que los componentes se degraden y se vuelvan quebradizos en entornos propensos a la oxidación a altas temperaturas. |
Biocompatibilidad | El polvo de Inconel 600 demuestra una buena biocompatibilidad, lo que significa que presenta riesgos mínimos para la salud cuando se utiliza en contacto con tejidos humanos. Esta característica lo convierte en un material viable para determinados implantes y dispositivos médicos. | Aunque no es su función principal, la biocompatibilidad del polvo de Inconel 600 abre las puertas a su posible uso en aplicaciones médicas. |
Compatibilidad de la fabricación aditiva | El polvo de Inconel 600 es especialmente adecuado para técnicas de fabricación aditiva como la fusión de lecho de polvo por láser. La morfología esférica de las partículas del polvo optimiza el flujo y facilita la construcción precisa capa por capa durante el proceso de impresión. | La compatibilidad del polvo de Inconel 600 con la fabricación aditiva permite crear componentes complejos e intrincados con una libertad de diseño excepcional. |
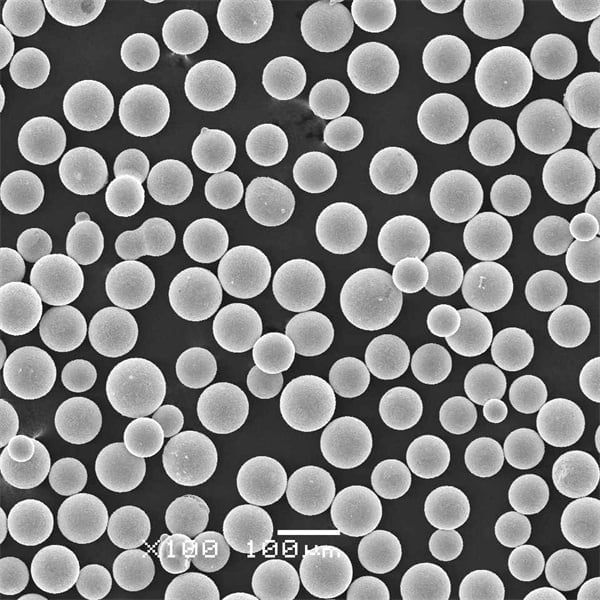
Aplicaciones de Inconel 600 Polvo
Industria | Aplicación | Propiedades clave utilizadas | Consideraciones adicionales |
---|---|---|---|
Aeroespacial | * Componentes de postcombustión * Conductos de escape * Cubiertas de turbina | * Resistencia a altas temperaturas: Resiste temperaturas extremas que superan los 1100 °C, lo que resulta crucial para soportar el intenso calor generado por los motores a reacción. * Resistencia a la oxidación: Mantiene la integridad estructural en entornos ricos en oxígeno durante el vuelo. * Resistencia a la fluencia: Resiste la deformación bajo esfuerzos prolongados a altas temperaturas, garantizando la longevidad de los componentes. | * Tolerancias estrictas y geometrías complejas: La buena soldabilidad del polvo de Inconel 600 permite fabricar piezas complejas cumpliendo las estrictas normas aeroespaciales. * Reducción de peso: La fabricación aditiva con polvo de Inconel 600 permite diseñar componentes ligeros, lo que mejora la eficiencia del combustible. |
Procesado químico | * Intercambiadores de calor * Recipientes de reacción * Equipos de tratamiento de productos químicos agresivos | * Resistencia a la corrosión: Muestra una resistencia excepcional a una amplia gama de productos químicos corrosivos, garantizando la contención de los medios de proceso y la integridad de los componentes. * Resistencia a altas temperaturas: soporta las altas temperaturas de funcionamiento que se dan en las reacciones químicas. * Buena fabricabilidad: El polvo de Inconel 600 permite la creación de formas complejas necesarias para equipos especializados de procesamiento químico. | * Acabado superficial: El acabado superficial de los componentes de Inconel 600 impresos en 3D puede requerir un tratamiento posterior para obtener una compatibilidad química óptima en función de la aplicación específica. |
Petróleo y gas | * Herramientas de fondo de pozo * Líneas de control de cabeza de pozo * Equipos submarinos | * Resistencia a altas temperaturas: Soporta las temperaturas abrasadoras que se dan en los entornos de pozos profundos. * Resistencia a la presión: Mantiene la integridad estructural bajo la inmensa presión ejercida por el petróleo y el gas a grandes profundidades. * Resistencia a la corrosión: Resiste los efectos corrosivos de los fluidos de fondo de pozo, incluidas las salmueras y el gas ácido. | * Tensión residual: Minimizar la tensión residual después de la impresión 3D es crucial para los componentes de fondo de pozo para garantizar que puedan soportar las exigentes condiciones de servicio. * Ensayos no destructivos: Los ensayos no destructivos rigurosos son esenciales para identificar cualquier posible defecto en los componentes de Inconel 600 impresos en 3D para aplicaciones de petróleo y gas. |
Generación de energía | * Componentes de turbinas de gas * Intercambiadores de calor * Tuberías de alta temperatura | * Resistencia a altas temperaturas y a la fluencia: Garantiza que los componentes puedan soportar las temperaturas extremas y la tensión constante presentes en el funcionamiento de las turbinas de gas. * Resistencia a la oxidación: Mantiene la integridad estructural en entornos de alta temperatura y ricos en oxígeno. * Soldabilidad: Permite la unión fiable de componentes de Inconel 600 impresos en 3D con piezas de fabricación tradicional. | * Estricto control de calidad: es necesario aplicar estrictas medidas de control de calidad en todo el proceso de impresión 3D para garantizar que los componentes cumplen los exigentes requisitos de las aplicaciones de generación de energía. |
Control de la contaminación | * Componentes de gasificación del carbón * Recuperadores de gases de escape * Sistemas de tratamiento de gases de combustión | * Resistencia a altas temperaturas y a la oxidación: Crucial para soportar las altas temperaturas y los entornos hostiles que se encuentran en los procesos de gasificación del carbón. * Resistencia a la corrosión: Permite que los componentes resistan los efectos corrosivos de los gases de combustión ácidos y otros contaminantes. * Fabricabilidad: Permite la creación de geometrías complejas necesarias para un equipo eficaz de control de la contaminación. | * Características del polvo: Las características específicas del polvo de Inconel 600, como el tamaño y la distribución de las partículas, pueden influir en la imprimibilidad y las propiedades finales de los componentes fabricados. |
Inconel 600 Polvo Especificaciones
Propiedad | Especificación | Valor típico | Importancia en la fabricación aditiva |
---|---|---|---|
Composición química (wt%) | * Níquel (Ni) + Cobalto (Co) * Cromo (Cr) * Hierro (Fe) * Niobio + Tántalo (Nb+Ta) * Carbono (C) * Silicio (Si) * Fósforo (P) * Azufre (S) * Aluminio (Al) * Manganeso (Mn) * Cobre (Cu) * Titanio (Ti) | * ≥ 72 * 14.0 - 17.0 * 6.0 - 10.0 * ≤ 1.00 * ≤ 0.15 * ≤ 0.50 * ≤ 0.040 * ≤ 0.015 * ≤ 0.35 * ≤ 1.00 * ≤ 0.50 * ≤ 0.50 | * El equilibrio específico de los elementos determina las propiedades mecánicas, la resistencia a la corrosión y el comportamiento a altas temperaturas del producto final. * El estricto cumplimiento de estas especificaciones garantiza un rendimiento constante y fiable en la fabricación aditiva. |
Distribución del tamaño de las partículas | * D10 * D50 * D90 | * Varía en función de la aplicación * Rango típico: 15-150 μm | * La distribución del tamaño de las partículas influye significativamente en la fluidez del polvo, la densidad de empaquetamiento y la capacidad de impresión. * Se prefiere una distribución más estrecha con un tamaño medio de partícula (D50) optimizado para el proceso específico de fabricación aditiva. |
Morfología de las partículas | * Esfericidad * Morfología de la superficie * Partículas satélites | * Alta esfericidad * Superficie lisa * Partículas satélites mínimas | * Las partículas esféricas mejoran la fluidez del polvo, la densidad de empaquetamiento y la absorción del láser durante el proceso de fabricación aditiva. * Una superficie lisa minimiza los defectos y mejora el acabado superficial del componente final. * Unas partículas satélite mínimas (partículas pequeñas adheridas a otras más grandes) garantizan un flujo uniforme del material y evitan la obstrucción de las boquillas. |
Densidad aparente | 4,0 - 4,5 g/cm³ | * La densidad aparente influye en la manipulación del polvo, la eficacia del empaquetado y el uso del material en el proceso de fabricación aditiva. * Una mayor densidad aparente permite un mejor empaquetado y reduce el tiempo de impresión. | |
Fluidez | Medido mediante técnicas como Hall Flow Rate | * Una buena fluidez es esencial para la deposición uniforme del polvo y la formación de capas consistentes durante la fabricación aditiva. * Las características del polvo, como la distribución del tamaño de las partículas y la morfología, influyen significativamente en la fluidez. | |
Contenido de humedad | ≤ 0,2 wt% | * Una humedad excesiva puede provocar salpicaduras, porosidad y debilitamiento de las propiedades mecánicas del componente final. * Un bajo contenido de humedad garantiza una impresión suave y piezas de alta calidad. | |
Contenido de oxígeno | ≤ 0,5 wt% | * Un alto contenido de oxígeno puede provocar la formación de óxido, lo que afecta negativamente a las propiedades mecánicas del material y a su rendimiento a altas temperaturas. * Un bajo contenido de oxígeno es crucial para mantener las propiedades deseadas del Inconel 600 en el producto final. | |
Análisis químico | Realizada mediante técnicas como la fluorescencia de rayos X (XRF) o la espectrometría de emisión óptica (OES). | * El análisis químico verifica el cumplimiento de la composición especificada y garantiza la coherencia de las propiedades del material. * Los análisis periódicos a lo largo del proceso de producción de polvo son esenciales para el control de calidad. |
Proveedores mundiales y gama de precios
Empresa | Tiempo de espera | Precio/kg |
---|---|---|
Sandvik Osprey | 10-14 semanas | $50-$150 |
TLS Técnica | 16 semanas | $60-$180 |
Atlantic Equipment | 12 semanas | $45-$130 |
Precios para cantidades superiores a 100 kg. Es posible una reducción significativa de los costes por encima de los 500 kg mediante negociaciones.
Análisis comparativo
Característica | Descripción | Beneficio | Consideración |
---|---|---|---|
Composición química | El polvo de Inconel 600 tiene una composición primaria de níquel (alrededor de 70%), cromo (alrededor de 15%) y hierro (alrededor de 8%). También están presentes pequeñas cantidades de elementos como manganeso, cobre y silicio. | Esta composición ofrece una convincente combinación de propiedades: excelente resistencia a la oxidación y la corrosión a altas temperaturas, buena resistencia mecánica a temperaturas elevadas y una deseable fabricabilidad. | El equilibrio específico de los elementos puede ser ajustado por algunos fabricantes para conseguir ligeras variaciones en las propiedades para aplicaciones especializadas. |
Métodos de producción de polvo | Dos métodos principales dominan la producción de polvo de Inconel 600: la atomización con gas y la atomización con agua. La atomización con gas consiste en dispersar el metal fundido en una corriente de gas inerte a alta velocidad, creando partículas finas y esféricas que se solidifican rápidamente. La atomización con agua utiliza un principio similar, pero con una corriente de agua en lugar de gas. | La atomización con gas suele producir polvos con una distribución del tamaño de las partículas más ajustada, mayor fluidez y menor contenido de oxígeno, lo que se traduce en una mayor calidad del producto final. Los polvos atomizados con agua pueden ser una opción más rentable, pero pueden requerir un procesamiento adicional para algunas aplicaciones. | La elección de uno u otro método depende de las características deseadas del polvo y de los requisitos específicos de la aplicación. |
Tamaño y distribución de partículas | El polvo de Inconel 600 está disponible en una amplia gama de tamaños de partícula, normalmente entre 15 y 150 micras. La distribución de estos tamaños de partícula en el lecho de polvo es crucial para el éxito de los procesos de fabricación aditiva (AM), como la fusión por haz de láser (LBM) y la fusión por haz de electrones (EBM). | Una gama de tamaños de partícula bien distribuida favorece una densidad de empaquetamiento óptima, una buena fluidez y una interacción eficaz del láser o del haz de electrones durante la fusión. Esto se traduce en construcciones de alta calidad con defectos mínimos. | Los fabricantes de polvo de Inconel 600 proporcionan datos detallados sobre la distribución del tamaño de las partículas para garantizar la compatibilidad con los equipos de AM y los parámetros de proceso específicos. |
Fluidez | La fluidez se refiere a la facilidad con la que el polvo se mueve bajo su propio peso. Es un factor crítico para la deposición uniforme de capas en los procesos de AM. | Una buena fluidez permite una distribución uniforme del polvo y minimiza el riesgo de variaciones en la densidad de las capas. Esto se traduce en una mejora de la precisión dimensional y las propiedades mecánicas de la pieza impresa final. | Los fabricantes de polvo emplean técnicas como la modificación de la superficie o la adición de agentes de flujo para mejorar la fluidez. También puede utilizarse el precalentamiento del lecho de polvo para mejorar las características de fluidez. |
Esfericidad y morfología | Lo ideal es que las partículas de polvo de Inconel 600 tengan forma esférica y superficie lisa. Esta morfología favorece una buena densidad de empaquetamiento y minimiza los huecos entre partículas, lo que da lugar a piezas impresas más densas y resistentes. | Las partículas muy esféricas también tienden a fluir mejor y mejoran la eficacia del acoplamiento láser durante la fusión. | Los polvos con formas irregulares o defectos superficiales pueden provocar incoherencias en la densidad de empaquetado y posibles deficiencias en el producto final. |
Densidad aparente y de toma | La densidad aparente es la relación entre la masa de un polvo y su volumen total, incluidos los huecos entre partículas. La densidad aparente se mide tras una rutina de golpeo normalizada que compacta el lecho de polvo. | La densidad aparente proporciona una medida básica de la voluminosidad del polvo, mientras que la densidad de extracción refleja la densidad de empaquetamiento máxima alcanzable. La diferencia entre estos valores indica la porosidad del lecho de polvo. | En general, se prefiere una mayor densidad de macho para las aplicaciones de AM, ya que se traduce en piezas finales más densas y resistentes. |
PREGUNTAS FRECUENTES
¿Por qué se prefiere Inconel 600 para fijaciones de alta temperatura?
Sus características de fácil conformado y unión facilitan la fabricación de tuercas y tornillos, a diferencia de los grados altamente aleados que requieren un procesamiento especial. La buena resistencia a la fluencia por encima de 550 °C es adecuada para aplicaciones de turbocompresores.
¿Qué rango de tamaño de partícula funciona mejor para la fusión de lecho de polvo por láser?
Alrededor de 25 a 45 micras son óptimas para equilibrar el acabado superficial, la resolución y la velocidad de fabricación. Los polvos demasiado gruesos perjudican la densidad y la precisión. Verifique la distribución de tamaños para una fluidez adecuada.
¿Qué parámetros del proceso son los más importantes a la hora de imprimir piezas de Inconel 600?
Densidad de energía, control del precalentamiento, parámetros de distribución del polvo que garantizan una fusión densa sin exceso de oxidación ni tensiones residuales que provoquen grietas durante las fases de construcción y tratamiento térmico.
¿Qué tratamientos térmicos se aplican a Inconel 600 de fabricación aditiva?
El envejecimiento con alivio de tensiones, similar al proceso de forjado, ayuda a obtener propiedades constantes: normalmente se especifican 1050-1120 °F durante 1-3 horas. Los tratamientos por precipitación son menos comunes.
¿Cómo se recicla el polvo usado de Inconel 600?
Los sistemas de recuperación filtran, tamizan y mezclan alrededor de 20-30% de polvo reutilizado con material fresco de forma continua. Controle los niveles de oxígeno y los límites de las fracciones reutilizadas para evitar problemas de contaminación.
Conclusión
En resumen, el polvo de Inconel 600 ofrece una combinación óptima de conformabilidad, soldabilidad y resistencia al calor esencial para la fabricación de componentes en sectores exigentes mediante fabricación aditiva u otras técnicas pulvimetalúrgicas.
Compartir
MET3DP Technology Co., LTD es un proveedor líder de soluciones de fabricación aditiva con sede en Qingdao, China. Nuestra empresa está especializada en equipos de impresión 3D y polvos metálicos de alto rendimiento para aplicaciones industriales.
Solicite información para obtener el mejor precio y una solución personalizada para su empresa.
Artículos relacionados
Acerca de Met3DP
Actualización reciente
Nuestro producto
CONTACTO
¿Tiene alguna pregunta? ¡Envíenos un mensaje ahora! Atenderemos su solicitud con todo un equipo tras recibir su mensaje.
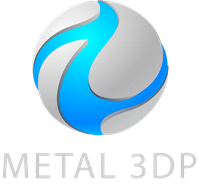
Polvos metálicos para impresión 3D y fabricación aditiva