Materiales refractarios en polvo
Índice
Polvo refractario Los materiales refractarios representan una clase especializada de materiales inorgánicos no metálicos que presentan una resistencia al calor extremadamente alta y se utilizan en industrias exigentes. Esta completa guía sirve a los profesionales técnicos y a los compradores para comprender todas las características clave de los polvos refractarios: composición típica, datos de propiedades críticas, procesos de fabricación, aplicaciones, especificaciones y proveedores.
Visión general de los materiales refractarios en polvo
Los polvos refractarios comprenden materiales no metálicos inertes finamente divididos que demuestran una estabilidad térmica excepcional, conservando la resistencia y la forma a temperaturas elevadas superiores a 1000°C. Las principales subclases son los óxidos, carburos, nitruros y cerámicas.
Atributos críticos:
- Resistencia al calor superior a 1000°C
- Resiste el choque térmico
- Resiste la corrosión
- Alto punto de fusión
- Mantener la integridad estructural
Sus excepcionales capacidades potencian el rendimiento en hornos, calderas, hornos, reactores y otros entornos térmicos extremos en los que los materiales tradicionales fallan rápidamente.
Composición típica
Material | Papel | Gama Wt% |
---|---|---|
Alúmina | Propiedades térmicas | 40-100% |
Sílice | Vincular la matriz | 0-60% |
Magnesia | Resistir al deterioro | 0-20% |
Grafito | Aumentar la resistencia al choque térmico | 0-15% |
Equilibrar los componentes clave permite optimizar características como la capacidad calorífica, el aislamiento, la resistencia a la erosión, el punto de fusión y el coste.
Principales tipos de polvos refractarios
Tipo | Descripción |
---|---|
Fundido | Pureza extrema, soporta más de 1800°C |
Sinterizado | Prensado/cocción de polvo, menor coste |
Carburo de silicio | Cerámica de alta conductividad térmica |
Cromita | Resiste la penetración de escoria y metal |
Zirconia | Resistencia al choque térmico |
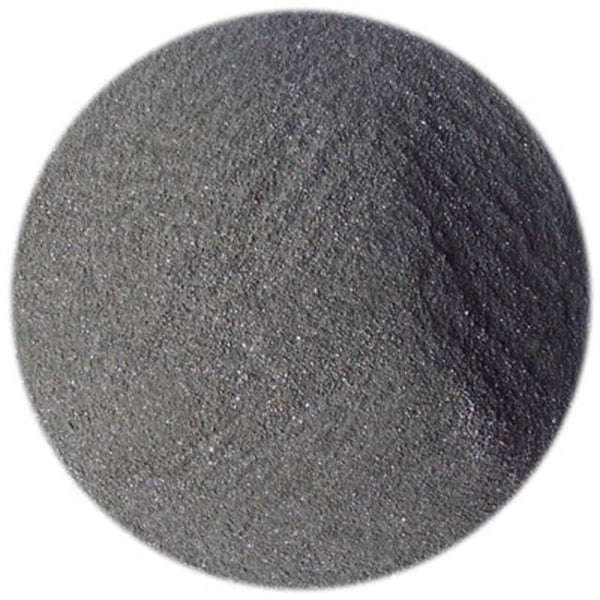
Polvo refractario Materiales Procesos de fabricación
Beneficio | Descripción | Impacto |
---|---|---|
Piezas de alta densidad con forma casi de red | La EBM crea piezas con una densidad superior al 99,5% de la densidad teórica del polvo metálico utilizado. Esto elimina la porosidad (pequeñas bolsas de aire) habitual en otros métodos de fabricación aditiva, lo que da lugar a piezas con una solidez, resistencia a la fatiga y precisión dimensional excepcionales. | Esto permite crear componentes metálicos funcionales para aplicaciones exigentes en los sectores aeroespacial (álabes de turbinas, carcasas de motores), médico (implantes dentales, prótesis) y automovilístico (piezas ligeras de alto rendimiento). |
Propiedades mecánicas superiores | El entorno de alto vacío y el preciso proceso de fusión en EBM minimizan la oxidación y la contaminación, preservando las propiedades inherentes del polvo metálico. Esto se traduce en piezas con una excelente resistencia a la tracción, resistencia a la fluencia (capacidad de soportar la deformación bajo tensión a altas temperaturas) y tenacidad a la fractura. | Las piezas producidas con EBM pueden soportar cargas importantes, funcionar eficazmente a temperaturas elevadas y resistir la propagación de grietas, lo que las hace ideales para aplicaciones que requieren durabilidad e integridad estructural en entornos difíciles. |
Procesado de metales refractarios y reactivos | A diferencia de los métodos de fabricación tradicionales, limitados por los altos puntos de fusión y la reactividad, la EBM destaca en el procesamiento de materiales difíciles como las aleaciones de titanio, tántalo e Inconel. El entorno de vacío evita la oxidación y permite un control preciso del proceso de fusión, lo que garantiza el éxito de la fabricación. | Esto amplía las posibilidades de diseño para sectores como el aeroespacial y el biomédico, en los que los componentes requieren una excepcional relación resistencia-peso, biocompatibilidad (compatibilidad con tejidos vivos) y rendimiento a altas temperaturas. |
Libertad de diseño para geometrías complejas | El enfoque capa por capa de EBM permite crear intrincadas características internas, canales y estructuras reticulares imposibles con las técnicas convencionales. Esta flexibilidad de diseño optimiza la distribución del peso, mejora la transferencia de calor y permite crear componentes con una funcionalidad superior. | Esta ventaja revoluciona el diseño de productos en industrias como la aeroespacial, donde los componentes ligeros y de alta resistencia con complejos canales de refrigeración son cruciales para la eficiencia de los motores. También permite crear implantes médicos personalizados que se adaptan perfectamente a la anatomía del paciente. |
Estructuras de apoyo mínimas | Debido a la gran resistencia inherente de las piezas producidas con EBM, se necesitan estructuras de soporte mínimas durante el proceso de fabricación. Esto reduce el tiempo de procesamiento posterior y el desperdicio de material, así como el riesgo de que la estructura de soporte dañe el componente final. | Esto se traduce en tiempos de producción más rápidos, costes generales más bajos y la posibilidad de crear geometrías complejas que serían difíciles o imposibles de conseguir con los métodos tradicionales. |
Reducción del desperdicio de material | La EBM es un proceso de fabricación aditiva, lo que significa que el material se añade capa a capa para crear la forma deseada. Esto minimiza el desperdicio de material en comparación con técnicas sustractivas como el mecanizado, en las que se retira una parte significativa de la materia prima para conseguir la forma final. | Esta ventaja fomenta la sostenibilidad y reduce los costes de producción al maximizar la utilización del material. Además, el polvo no utilizado de la cámara de fabricación puede reutilizarse para fabricaciones posteriores, lo que minimiza aún más los residuos. |
Propiedades de los materiales refractarios en polvo
Propiedad | Valor típico |
---|---|
Punto de fusión | Más de 1600°C |
Densidad | 2 - 6 g/cm3 |
Resistencia a la compresión | 20 - 100 MPa |
Resistencia a la flexión | 10 - 60 MPa |
Resistencia a la fractura | 2 - 10 MPa-m^1/2 |
Conductividad térmica | 20 - 100 W/m-K |
Resistividad eléctrica | 10^8 - 10^13 Ohm-cm |
Temperatura máxima de servicio | 1200°C - 2000°C |
El equilibrio entre requisitos como el punto de fusión, la capacidad calorífica, la resistencia al choque térmico, el valor aislante, la inercia química y el coste determina la selección.
Aplicaciones de los materiales refractarios en polvo
Industria | Aplicación | Material | Propiedades utilizadas |
---|---|---|---|
Aeroespacial | * Álabes de turbina * Toberas de cohetes * Escudos térmicos | * Tungsteno * Tantalio * Rhenium | * Altos puntos de fusión (>3000°C) * Excelente resistencia mecánica a altas temperaturas * Resistencia superior a la oxidación |
Automoción | * Electrodos de bujía * Válvulas de escape * Componentes del turbocompresor | * Tungsteno * Molibdeno * Aleaciones de níquel | * Alta conductividad eléctrica * Resistencia al desgaste * Resistencia al choque térmico |
Electrónica | * Resistencias de alta temperatura * Condensadores * Contactos eléctricos | * Tungsteno * Molibdeno * Plata | * Puntos de fusión elevados * Baja resistividad * Resistencia a la erosión del arco |
Energía | * Revestimientos para hornos de centrales eléctricas * Reactores de sales fundidas | * Carburo de silicio * Alúmina * Zirconia | * Excelente conductividad térmica * Alta estabilidad química * Resistencia a las sales fundidas |
Médico | * Prótesis de cadera y rodilla * Implantes dentales * Blindaje contra la radiación | * Aleaciones de titanio * Tantalio * Tungsteno | * Biocompatibilidad * Alta relación resistencia/peso * Opacidad de los rayos X |
Procesado químico | * Reactores para entornos químicos agresivos * Tuberías de alta temperatura * Intercambiadores de calor | * Tantalio * Zirconio * Aleaciones de níquel | * Resistencia a la corrosión * Alta resistencia a temperaturas elevadas * Excelente formabilidad |
Herramientas | * Herramientas de corte para materiales de alta resistencia * Matrices para conformado de metales * Moldes para vidrio y cerámica | * Carburo de tungsteno * Nitruro de boro * Polvos de diamante | * Dureza excepcional * Alta resistencia al desgaste * Baja expansión térmica |
Fabricación aditiva | * Impresión 3D de componentes metálicos complejos * Reparación de piezas desgastadas o dañadas | * Polvos Inconel * Aleaciones de cromo-cobalto * Polvos de titanio | * Alta fluidez del polvo para una impresión precisa * Excelentes propiedades de sinterización * Microestructuras a medida para aplicaciones específicas |
Especificaciones y grados
Propiedad | Descripción | Consideraciones clave para la selección |
---|---|---|
Composición química | Los componentes básicos del polvo, normalmente óxidos metálicos, carburos, nitruros o cerámicas. | * Óxido dominante: La alúmina (Al2O3) ofrece una excelente resistencia a altas temperaturas pero una menor resistencia al choque térmico. La sílice (SiO2) ofrece buena resistencia química pero menor refractariedad. La magnesia (MgO) es excelente para resistir el ataque de la escoria, pero se hidrata con facilidad. * Aditivos secundarios: La calcia (CaO) mejora la resistencia a la escoria, mientras que el cromo (Cr2O3) mejora la resistencia al desgaste. * Pureza: Una mayor pureza suele traducirse en un mejor rendimiento, pero puede suponer un aumento del coste. |
Distribución del tamaño de las partículas | La variedad y dispersión de tamaños de partículas individuales dentro del polvo. | * Tamaño medio de las partículas: Los polvos más finos ofrecen una densidad de empaquetamiento y una superficie de adhesión superiores, pero pueden ser más susceptibles a la aglomeración y dificultar las características de flujo. * Distribución del tamaño de las partículas: Una distribución estrecha garantiza un envasado homogéneo y minimiza la segregación durante el procesado. Las distribuciones más amplias pueden ser beneficiosas para rellenar huecos y mejorar la eficacia del envasado. * Aplicaciones específicas: Los procesos como la impresión 3D suelen requerir un control más estricto del tamaño para conseguir un flujo y una imprimibilidad óptimos. |
Morfología de las partículas | La forma de las partículas individuales. | * Forma: Las partículas esféricas suelen empaquetarse con más eficacia, mientras que las angulares pueden crear un efecto de enclavamiento mecánico para mejorar la resistencia. * Superficie: Los polvos con mayor superficie ofrecen un mejor potencial de adhesión, pero también pueden aumentar la reactividad. * Control morfológico: Ciertas aplicaciones pueden dar prioridad a formas específicas, como las plaquetas para mejorar la conductividad térmica. |
Densidad aparente | Masa de polvo por unidad de volumen en estado suelto, sin compactar. | * Eficiencia de embalaje: Una mayor densidad aparente indica una mayor eficacia del envasado y puede reducir el uso de material. * Fluidez: Los polvos con menor densidad aparente suelen presentar mejores características de fluidez para facilitar su manipulación y procesamiento. * Fuerza Verde: La densidad aparente puede influir en la resistencia en verde (precocción) de los componentes conformados. |
Densidad aparente | La masa de polvo por unidad de volumen tras someterse a un procedimiento normalizado de golpeteo o vibración. | * Eficacia de compactación: La densidad aparente refleja la capacidad de compactación del polvo, lo que influye en la densidad y las propiedades del producto final. * Porosidad: Una menor densidad aparente indica una mayor porosidad, que puede influir en las propiedades de aislamiento térmico pero puede disminuir la resistencia mecánica. * Manipulación de materiales: La densidad aparente afecta a la cantidad de polvo que puede almacenarse o transportarse eficazmente en un volumen determinado. |
Peso específico | Relación entre la densidad de un material y la densidad del agua. | * Selección de refractarios: Los materiales de alto peso específico suelen ofrecer una mayor resistencia al calor, pero su peso puede ser mayor. * Rentabilidad: Los materiales más ligeros y con menor peso específico pueden ser más rentables de transportar y manipular. |
Refractariedad | La temperatura máxima que puede soportar un material sin fundirse o perder su integridad estructural. | * Requisitos de la solicitud: El polvo refractario debe superar la temperatura de funcionamiento prevista en la aplicación final. * Entorno químico: Ciertas atmósferas pueden afectar a la refractariedad. Por ejemplo, los ambientes reductores pueden degradar algunos óxidos. |
Conductividad térmica | La capacidad del material para conducir el calor. | * Gestión de la transferencia de calor: Una conductividad térmica elevada puede ser beneficiosa para aplicaciones que requieren una transferencia de calor eficaz, como los intercambiadores de calor. * Aislamiento térmico: La baja conductividad térmica es deseable para aplicaciones que necesitan retener el calor, como los revestimientos de hornos. |
Expansión térmica | La expansión de un material al calentarse. | * Resistencia al choque térmico: Los materiales con menor dilatación térmica suelen ser más resistentes al agrietamiento y al desconchado debidos a los cambios bruscos de temperatura. * Estabilidad dimensional: La adaptación del coeficiente de dilatación térmica del polvo refractario al material del sustrato minimiza el desarrollo de tensiones durante los ciclos térmicos. |
Resistencia química | La capacidad del material para resistir el ataque de productos químicos corrosivos y metales o escorias fundidos. | * Agentes agresivos específicos: La selección debe tener en cuenta los tipos de productos químicos que el refractario encontrará en la aplicación. * Acidez/Alcalinidad: Los ambientes ácidos o básicos pueden degradar determinados materiales refractarios. |
Otras características de rendimiento | Propiedades adicionales en función de la aplicación específica, como resistencia a la erosión, conductividad eléctrica o resistencia al desgaste. | * Centrarse en las necesidades: Identifique los factores de rendimiento críticos para el caso de uso previsto y elija un polvo que destaque en esas áreas. * Contrapartidas: A menudo, habrá compensaciones entre varias propiedades. Seleccionar el material óptimo implica priorizar las características más relevantes. |
Polvo refractario Proveedores de materiales
Empresa | Ubicación |
---|---|
Saint-Gobain | Global |
RHI Magnesita | Brasil, Austria, China |
Krosaki Harima | Japón |
Vesubio | Europa, Estados Unidos |
Morgan Materiales Avanzados | Reino Unido, Estados Unidos |
Estimación de precios
Grado | Precio por kg |
---|---|
Alúmina tabular | $10-30 |
Carburo de silicio | $50-150 |
Zirconia | $100-500 |
Otros | $20-100 |
Las economías de escala influyen en los costes: las composiciones personalizadas y los estrictos requisitos de calidad exigen primas.
Pros y contras
Pros | Contras |
---|---|
Resistencia al calor inigualable: Los polvos refractarios presentan una estabilidad térmica excepcional, soportando temperaturas superiores a 1500°C (2732°F) sin fundirse ni degradarse. Esto los hace ideales para revestir hornos, reactores y otras aplicaciones de alta temperatura en las que los materiales tradicionales sucumbirían rápidamente. | Fragilidad y desconchamiento: Debido a su estructura rígida, los polvos refractarios pueden ser susceptibles de agrietarse y desconcharse, especialmente bajo fluctuaciones rápidas de temperatura (choque térmico). Este desconchamiento puede comprometer la integridad del revestimiento y exigir su reparación o sustitución. |
Rendimiento a medida: Seleccionando y mezclando cuidadosamente distintos tipos de polvo refractario (por ejemplo, alúmina, circonio, magnesia), los ingenieros pueden crear fórmulas de materiales personalizadas con propiedades específicas. Esto permite optimizar factores como la resistencia al calor, la compatibilidad química y la resistencia al desgaste para satisfacer con precisión las exigencias de la aplicación. | Instalación compleja: A diferencia de los ladrillos o formas preformados, los polvos refractarios requieren un proceso de instalación más complejo. A menudo se emplean técnicas como el colado, el gunitado o el vibrocolado, que requieren equipos especializados y mano de obra cualificada para conseguir un revestimiento denso y uniforme. |
Versatilidad en forma y función: Los polvos refractarios ofrecen una flexibilidad de diseño superior a la de los componentes prefabricados. Su capacidad para moldearse en formas intrincadas permite crear complejos revestimientos de hornos, crisoles y otros elementos refractarios a medida. | Consideraciones de costos: Las materias primas y las técnicas de procesamiento que intervienen en la producción de polvos refractarios de alto rendimiento pueden traducirse en un mayor coste inicial en comparación con algunos materiales refractarios convencionales. |
Ventaja de la ligereza: Los polvos refractarios contribuyen a una reducción significativa del peso en comparación con los revestimientos de ladrillo tradicionales. Esto resulta especialmente beneficioso en aplicaciones en las que un menor peso se traduce en una mayor eficiencia energética, una menor carga estructural y una manipulación más sencilla durante la instalación. | Riesgos potenciales para la salud: Ciertas composiciones de polvo refractario, en particular las que contienen sílice o cromita, pueden plantear riesgos para la salud si se inhalan. La aplicación de protocolos de seguridad adecuados y el uso de equipos de protección individual (EPI) apropiados son cruciales durante la manipulación y la instalación. |
Propiedades refractarias mejoradas: Mediante la incorporación de aditivos específicos o la utilización de técnicas de fabricación avanzadas, los polvos refractarios pueden diseñarse para que presenten propiedades superiores a la resistencia térmica básica. Esto puede incluir una mayor resistencia al choque térmico, una mayor resistencia química a los metales fundidos o escorias, e incluso capacidades de autocuración para prolongar la vida útil. | Impacto medioambiental: Dependiendo de la composición específica y de los métodos de producción, algunos polvos refractarios pueden plantear problemas medioambientales relacionados con su extracción, procesamiento o eliminación. La selección de materias primas respetuosas con el medio ambiente y las prácticas de reciclaje responsables son factores importantes a tener en cuenta. |
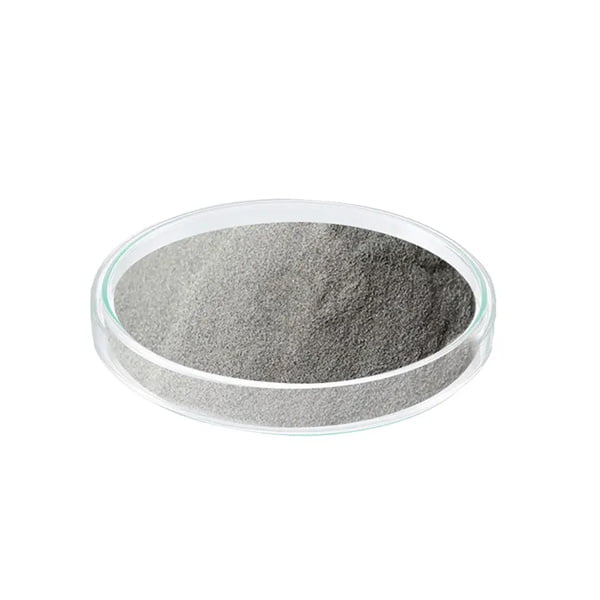
Preguntas frecuentes
P: ¿Cuál es la diferencia entre polvos refractarios y ladrillos refractarios?
R: Los ladrillos son construcciones consolidadas preformadas, mientras que los polvos representan materias primas que permiten la fabricación de componentes refractarios especiales mediante prensado/cocción o métodos avanzados de fabricación aditiva.
P: ¿Pueden imprimirse en 3D todos los polvos refractarios con tecnología AM?
R: Sí, la impresión por chorro de aglutinante y deposición de energía dirigida ha demostrado ser compatible con la mayoría de las calidades de alúmina, circonio y carburo de silicio termorresistentes para geometrías refractarias antes imposibles.
P: ¿Qué polvo refractario ofrece la temperatura de servicio más elevada?
R: Los grados de mullita fundida y circonio de pureza ultra alta resisten con fiabilidad más de 2000°C para las aplicaciones más exigentes en hornos, aeroespaciales y nucleares, donde las alternativas se funden o descomponen.
P: ¿Cuál es la diferencia entre materiales refractarios sintéticos y naturales?
R: Las materias primas naturales, como la bauxita, la magnesita y la arcilla, deben procesarse exhaustivamente para obtener polvos controlados con precisión para lograr la uniformidad mejorada y la resistencia térmica extrema que permiten las fórmulas sintéticas.
Conclusión
El objetivo de esta guía es proporcionar una referencia global sobre polvos refractarios, materiales especiales que superan las limitaciones de los metales y aleaciones ordinarios en los entornos industriales más calientes y agresivos gracias a su excepcional resistencia al calor. Póngase en contacto con un experto del sector para hablar de cómo adaptar los grados refractarios avanzados a sus necesidades específicas de procesamiento extremo. Las posibilidades van mucho más allá.
Compartir
MET3DP Technology Co., LTD es un proveedor líder de soluciones de fabricación aditiva con sede en Qingdao, China. Nuestra empresa está especializada en equipos de impresión 3D y polvos metálicos de alto rendimiento para aplicaciones industriales.
Solicite información para obtener el mejor precio y una solución personalizada para su empresa.
Artículos relacionados
Acerca de Met3DP
Actualización reciente
Nuestro producto
CONTACTO
¿Tiene alguna pregunta? ¡Envíenos un mensaje ahora! Atenderemos su solicitud con todo un equipo tras recibir su mensaje.
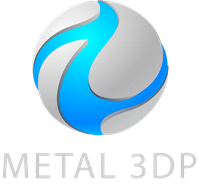
Polvos metálicos para impresión 3D y fabricación aditiva