3D Printed Aerospace Spars
目次
Introduction – The Critical Role of Spars in Aerospace and the Advent of Metal 3D Printing
In the demanding realm of aerospace engineering, every component plays a crucial role in ensuring the safety, efficiency, and performance of aircraft. Among these critical elements, the spar stands as a fundamental structural member within the wings and control surfaces. Acting as the primary load-bearing beam, the spar withstands bending and shear forces during flight, maintaining the aerodynamic shape and integrity of the aircraft. Traditionally manufactured through subtractive methods like machining from solid billets or assembly of multiple parts, spar production often involves significant material waste and design limitations.
The emergence of メタル 3Dプリンティング, also known as metal additive manufacturing (AM), is revolutionizing the way aerospace components, including spars, are conceived and produced. This advanced manufacturing technique builds parts layer by layer from metal powders, offering unprecedented design freedom, the ability to create complex internal geometries, and the potential for significant weight reduction without compromising structural integrity. For aerospace engineers and procurement managers seeking innovative solutions to enhance aircraft performance and streamline manufacturing processes, metal 3D printing of aerospace spars presents a compelling paradigm shift. Companies like メタル3DPテクノロジー株式会社, headquartered in Qingdao, China, are at the forefront of this revolution, providing industry-leading metal 3D printing equipment and high-performance metal powders tailored for critical aerospace applications. With a commitment to accuracy and reliability, メタル3DP empowers the aerospace industry to push the boundaries of design and manufacturing.
What are Aerospace Spars Used For? Structural Integrity and Beyond
Aerospace spars are the backbone of aircraft wings and control surfaces, serving a multitude of critical functions that directly impact flight safety and performance. Their primary role is to bear the primary flight loads, including bending moments caused by lift and gravity, as well as shear forces generated during maneuvers. The spars ensure the wing maintains its intended aerodynamic profile under various flight conditions, preventing excessive flexing or twisting that could compromise stability.
Beyond structural support, spars also play a vital role in:
- Distributing loads: They transfer forces from the wing skin and ribs to the fuselage, ensuring even distribution and preventing stress concentrations.
- Supporting control surfaces: Spars often extend into ailerons, elevators, and rudders, providing the necessary structural support for these movable surfaces to function effectively.
- Housing internal systems: Depending on the aircraft design, spars can incorporate channels or cavities for routing fuel lines, hydraulic systems, and electrical wiring, contributing to a more integrated and efficient design.
The reliability and integrity of aerospace spars are paramount. Failure of a spar can have catastrophic consequences, underscoring the stringent material and manufacturing requirements for these components. The aerospace industry demands materials with exceptional strength-to-weight ratios, high fatigue resistance, and reliable performance under extreme temperature variations and operational stresses. This is where advanced manufacturing techniques like metal 3D printing, offered by experts such as メタル3DP, become invaluable, enabling the production of complex spar designs with optimized material usage and enhanced performance characteristics. You can learn more about advanced manufacturing solutions on Metal3DP’s website.
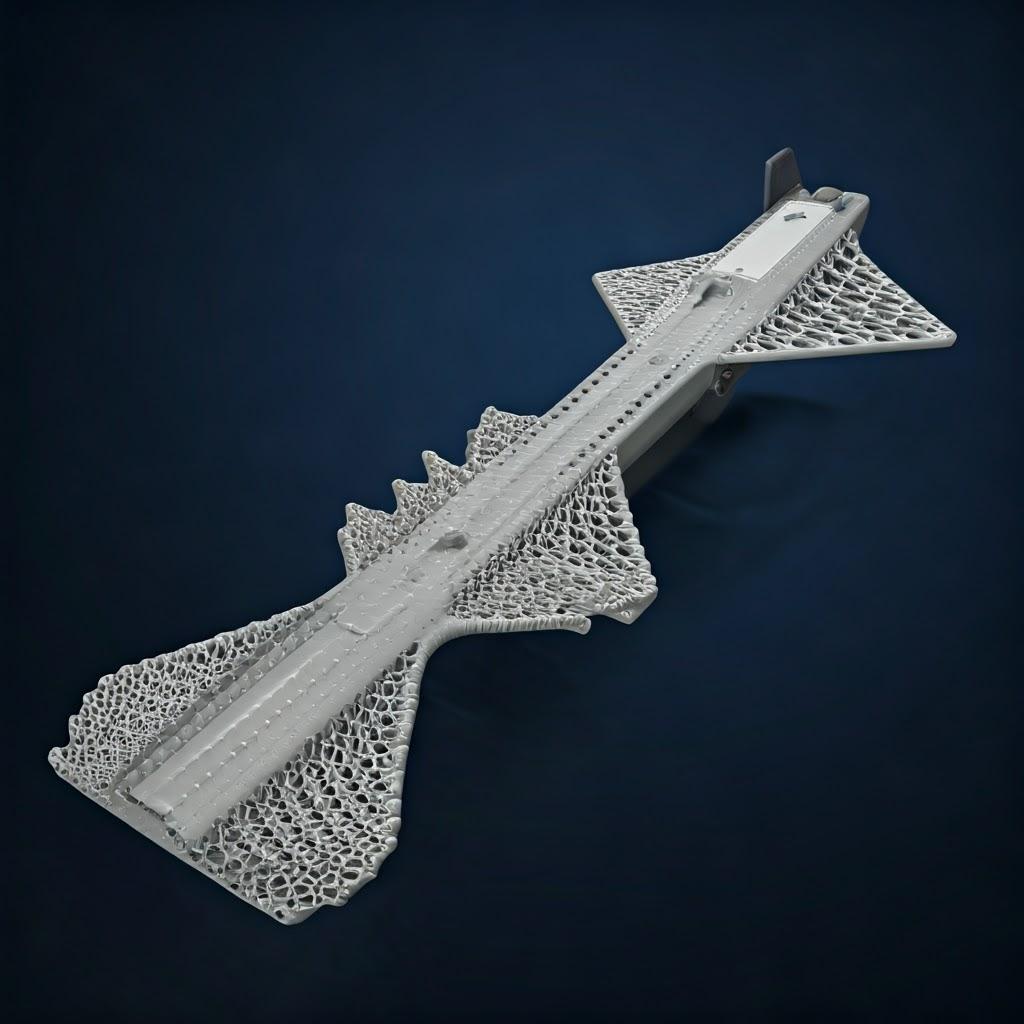
Why Use Metal 3D Printing for Aerospace Spars? Unlocking Design Freedom and Material Efficiency
Adopting metal 3D printing for the production of aerospace spars offers a multitude of compelling advantages over traditional manufacturing methods, making it an increasingly attractive option for the aerospace industry:
- Weight Reduction through Optimized Design: Metal 3D printing enables the creation of complex geometries, including internal lattice structures and topology-optimized designs. These designs strategically place material where it’s needed for strength and remove it from non-critical areas, resulting in significant weight savings compared to conventionally manufactured spars. Reduced weight translates directly to improved fuel efficiency, increased payload capacity, and enhanced aircraft performance.
- デザインの自由と複雑さ: Unlike subtractive manufacturing, which is limited by tool access, metal 3D printing allows for intricate internal features, custom shapes, and consolidated designs. This opens up possibilities for integrating multiple parts into a single 3D-printed spar, reducing assembly time and potential failure points.
- Material Efficiency and Waste Reduction: Traditional spar manufacturing often involves machining away large amounts of material from a solid billet, leading to significant waste. Metal 3D printing, on the other hand, builds parts layer by layer, using only the necessary material. This near-net-shape manufacturing process significantly reduces material waste and lowers overall production costs, particularly for complex geometries.
- Enhanced Performance through Tailored Materials: 次のような企業 メタル3DP offer a range of high-performance metal powders specifically designed for demanding aerospace applications. These materials, combined with the precision of 3D printing, allow for the creation of spars with tailored mechanical properties, such as increased strength, stiffness, and fatigue resistance.
- Faster Prototyping and Reduced Lead Times: Metal 3D printing accelerates the prototyping process, allowing engineers to quickly iterate on designs and test functional prototypes of spars. This rapid prototyping capability, coupled with the potential for on-demand manufacturing, can significantly reduce lead times compared to traditional tooling and machining processes.
- Customization and Part Consolidation: Each aircraft design has unique requirements. Metal 3D printing facilitates the production of customized spars tailored to specific aircraft models without the need for expensive retooling. Furthermore, the ability to consolidate multiple components into a single 3D-printed part can simplify assembly, reduce part count, and improve reliability.
Metal3DP’s expertise in Selective Electron Beam Melting (SEBM) printing methods and advanced metal powders ensures the production of high-quality, high-performance aerospace spars that meet the stringent demands of the industry. Explore the various 印刷方法 提供 メタル3DP to understand how they cater to aerospace requirements.
Recommended Materials for 3D Printed Aerospace Spars and Why They Matter
The selection of the appropriate metal powder is crucial for achieving the desired performance characteristics in 3D printed aerospace spars. メタル3DP offers a portfolio of high-quality metal powders optimized for additive manufacturing, including two standout materials particularly well-suited for spar applications: スカルマロイ そして AlSi10Mg.
Scalmalloy®: This high-performance aluminum alloy is specifically engineered for demanding lightweight applications, making it an excellent choice for aerospace spars. Its key benefits include:
プロパティ | 価値 | Significance for Aerospace Spars |
---|---|---|
高い強度重量比 | 例外的 | Enables significant weight reduction without compromising structural integrity, leading to improved fuel efficiency and performance. |
High Tensile Strength | Up to 520 MPa (annealed) | Provides the necessary resistance to withstand the high loads experienced during flight. |
High Yield Strength | Up to 480 MPa (annealed) | Ensures the spar can withstand significant stress without permanent deformation. |
良好な延性 | Elongation at break up to 15% (annealed) | Offers some flexibility and resistance to fracture under impact loads. |
優れた耐疲労性 | 高い | Crucial for components subjected to cyclic loading during flight, ensuring long service life and reliability. |
良好な耐食性 | グッド | Important for maintaining the structural integrity of the spar in various environmental conditions. |
溶接性 | グッド | Facilitates potential post-processing or joining operations if required. |
Export to Sheets
AlSi10Mg: This aluminum-silicon-magnesium alloy is another popular choice for 3D printed aerospace components due to its excellent balance of properties and processability. Its key advantages include:
プロパティ | 価値 | Significance for Aerospace Spars |
---|---|---|
優れた強度対重量比 | 高い | Offers a good balance of strength and weight, contributing to overall aircraft efficiency. |
High Tensile Strength | Up to 450 MPa (as-built) | Provides sufficient strength for many structural applications within the wing. |
High Yield Strength | Up to 300 MPa (as-built) | Ensures resistance to permanent deformation under load. |
良好な延性 | Elongation at break up to 10% (as-built) | Offers some capacity to deform before fracture. |
良好な熱伝導性 | 高い | Can be beneficial for managing heat within the wing structure. |
Excellent Processability | 素晴らしい | Well-suited for laser powder bed fusion (LPBF) processes, offering good printability and high density. |
良好な耐食性 | グッド | Provides adequate protection against environmental degradation. |
Export to Sheets
Metal3DP’s advanced powder making system ensures that these and other metallic powders exhibit high sphericity and good flowability, critical for achieving dense, high-quality 3D printed parts with superior mechanical properties. Choosing the right powder, like Scalmalloy® or AlSi10Mg from a trusted supplier like メタル3DP, is a fundamental step in realizing the full potential of 3D printed aerospace spars. You can explore Metal3DP’s range of 高品質の金属粉 for various applications. Sources and related content
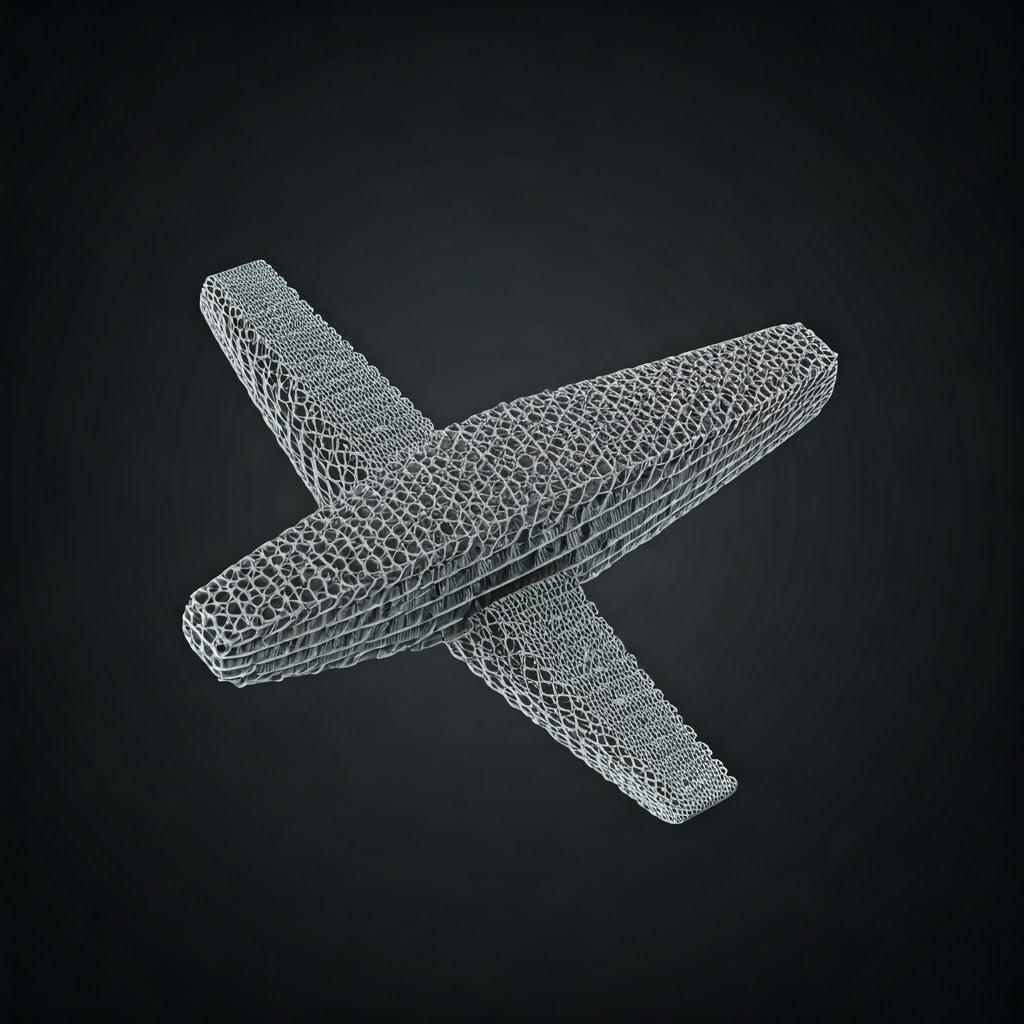
Design Considerations for Additive Manufacturing of Aerospace Spars
Designing aerospace spars for metal 3D printing requires a shift in mindset compared to traditional manufacturing. The layer-by-layer build process offers unique opportunities and necessitates careful consideration of several factors to optimize performance, reduce weight, and ensure successful fabrication.
- Topology Optimization: This computational design approach is particularly powerful for 3D printed spars. By defining the load-bearing requirements and constraints, topology optimization software can generate highly efficient geometries that strategically distribute material only where it’s structurally necessary. This often results in organic, non-intuitive shapes that would be impossible or prohibitively expensive to manufacture using traditional methods, leading to significant weight savings.
- 格子構造: Incorporating internal lattice structures within the spar is another effective way to reduce weight while maintaining or even enhancing stiffness and strength. These intricate, repeating patterns can be tailored to specific load requirements within different sections of the spar. Various lattice types, such as gyroids, honeycombs, and octets, offer different strength-to-weight characteristics.
- パーツの統合: Metal 3D printing allows for the integration of multiple components into a single, monolithic spar. Features like ribs, stiffeners, and mounting brackets can be designed directly into the spar, eliminating the need for separate manufacturing and assembly processes. This reduces part count, simplifies the supply chain, and minimizes potential failure points associated with fasteners.
- Orientation and Support Structures: The orientation of the spar during the 3D printing process significantly impacts surface finish, support structure requirements, and build time. Careful consideration of the part’s orientation can minimize the need for extensive support structures, which require post-processing removal and can affect surface quality. Design features like self-supporting angles (typically 45 degrees or greater) should be incorporated whenever possible.
- Internal Channels and Features: Additive manufacturing enables the creation of complex internal channels within the spar. These channels can be used for various purposes, such as routing wires or hydraulic lines, or even for thermal management by allowing the flow of cooling fluids. Integrating these functionalities directly into the spar design can lead to more compact and efficient systems.
- Wall Thickness and Minimum Feature Size: While 3D printing offers great design freedom, it’s essential to adhere to the minimum feature size and wall thickness capabilities of the chosen printing process and material. Insufficiently thin walls or small features may not print accurately or may lack the required strength. Consulting with Metal3DP’s experts can provide valuable insights into design guidelines for their equipment and materials.
- Stress Concentration Mitigation: Sharp corners and abrupt changes in geometry can lead to stress concentrations under load, potentially compromising the structural integrity of the spar. Designing with smooth transitions, fillets, and radii is crucial to distribute stress effectively and enhance fatigue life.
By thoughtfully addressing these design considerations, engineers can leverage the unique capabilities of metal 3D printing to create high-performance, lightweight aerospace spars that surpass the limitations of traditional manufacturing.
Achieving Precision: Tolerance, Surface Finish, and Dimensional Accuracy in 3D Printed Spars
In the demanding aerospace industry, precision is paramount. Components like spars must adhere to strict tolerance requirements to ensure proper fit, assembly, and performance. Metal 3D printing has evolved significantly, and with the right equipment and process control, it can achieve impressive levels of dimensional accuracy and surface finish suitable for many aerospace applications.
- 寸法精度: The dimensional accuracy achievable with metal 3D printing depends on several factors, including the printing technology (e.g., Selective Laser Melting (SLM), Electron Beam Melting (EBM)), the material used, the size and complexity of the part, and the calibration of the printer. High-end metal 3D printers, such as those offered by メタル3DP, can achieve tolerances in the range of ±0.1 mm or even finer for critical dimensions. Factors influencing accuracy include laser or electron beam spot size, powder bed uniformity, and thermal management during the build process.
- 表面仕上げ: The as-built surface finish of metal 3D printed parts is typically rougher than that achieved by machining. The surface roughness is influenced by the size of the powder particles, the layer thickness, and the presence of partially sintered powder. For aerospace spars, where aerodynamic performance and fatigue life are critical, post-processing techniques are often employed to improve surface finish. These can include:
- Media Blasting: Using abrasive media to remove partially sintered powder and reduce surface roughness.
- 研磨: Mechanical or chemical polishing to achieve smoother surfaces.
- CNC Machining: For critical interfaces or high-tolerance features, selective machining can be used to achieve the required precision and surface finish.
- Factors Affecting Precision: Several parameters during the metal 3D printing process can influence the final dimensional accuracy and surface finish:
- 層の厚さ: Thinner layers generally result in better surface finish but longer build times.
- スキャン戦略: The path the laser or electron beam takes to melt the powder can affect accuracy and surface quality.
- ビルド方向: As mentioned earlier, the orientation of the part on the build platform can impact the surface finish of different areas.
- 素材の特性: The thermal conductivity and melting behavior of the metal powder can influence shrinkage and distortion during the build.
- Quality Control and Inspection: Rigorous quality control measures are essential to ensure that 3D printed aerospace spars meet the required tolerances and surface finish specifications. Techniques such as Coordinate Measuring Machines (CMM), laser scanning, and non-destructive testing (NDT) are used to verify dimensional accuracy and identify any potential defects. メタル3DP adheres to stringent quality control processes to ensure the reliability of their printed parts.
By carefully selecting the printing process, optimizing build parameters, and employing appropriate post-processing techniques, it is possible to achieve the high levels of precision required for critical aerospace components like spars.
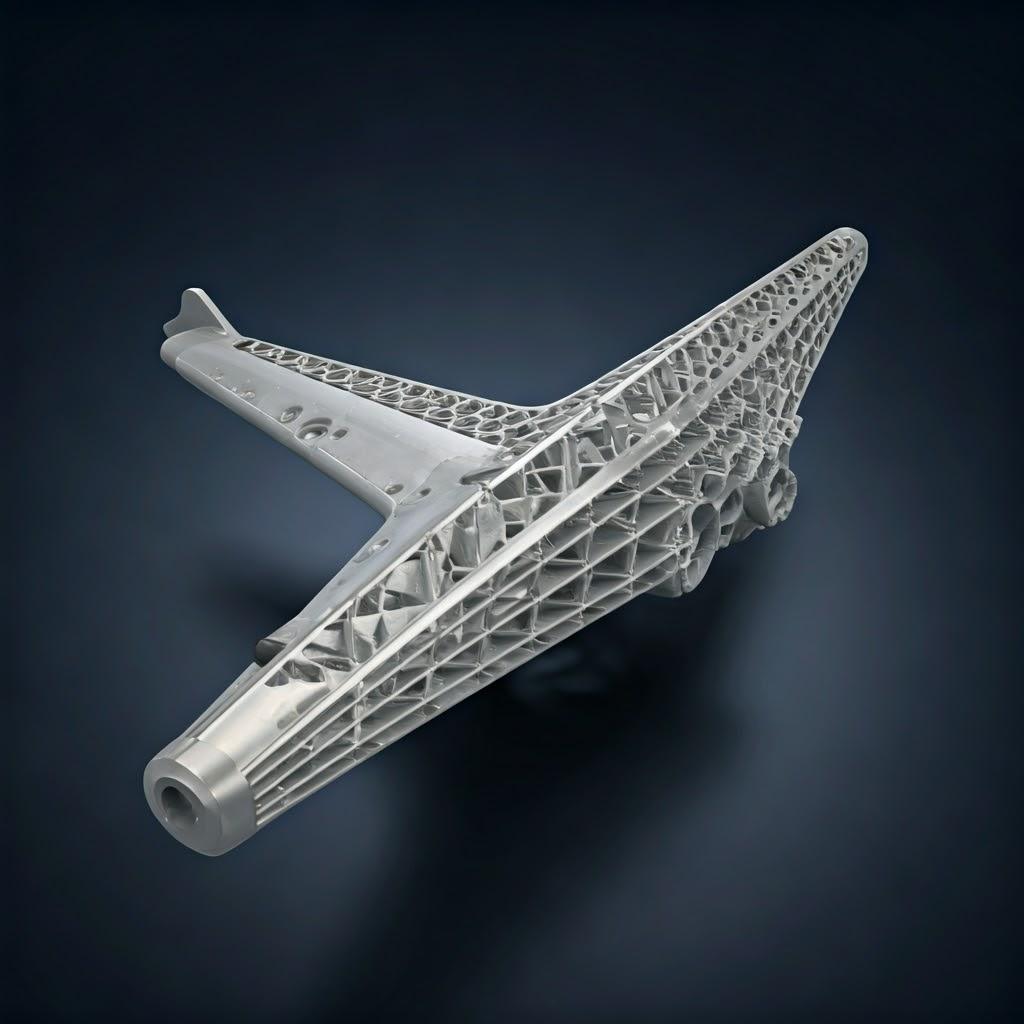
Post-Processing of 3D Printed Aerospace Spars: Ensuring Optimal Performance
While metal 3D printing offers significant advantages in creating complex geometries, post-processing steps are often necessary to achieve the final desired properties, surface finish, and dimensional accuracy for aerospace spars. These steps ensure the component meets the stringent requirements of the aerospace industry.
- Stress Relief Heat Treatment: During the 3D printing process, residual stresses can build up within the part due to rapid heating and cooling cycles. These stresses can lead to distortion or cracking. Stress relief heat treatment involves heating the printed spar to a specific temperature and holding it for a certain period, allowing the internal stresses to dissipate. This step is crucial for ensuring the long-term stability and performance of the spar.
- 支持構造の撤去: Metal 3D printed parts often require support structures to prevent collapse, minimize distortion, and anchor the part to the build platform. These supports need to be carefully removed after the printing process. Depending on the geometry and the type of support used, removal can involve manual cutting, machining, or chemical dissolution. Proper design for manufacturability can minimize the need for extensive support structures.
- 表面処理: As mentioned earlier, the as-built surface finish of 3D printed metal parts may not be suitable for all aerospace applications. Various surface treatment methods can be employed to improve smoothness, corrosion resistance, and other surface properties:
- Media Blasting: Used to remove partially sintered particles and create a more uniform surface texture.
- 研磨: Mechanical (e.g., vibratory finishing, abrasive flow machining) or chemical polishing can achieve smoother surfaces, reducing drag and improving fatigue life.
- コーティング: Applying protective coatings, such as anodizing for aluminum alloys or corrosion-resistant paints, can enhance the durability and performance of the spar in harsh aerospace environments.
- CNC Machining: For critical interfaces that require very tight tolerances or specific surface finishes, selective CNC machining can be performed on the 3D printed spar. This hybrid manufacturing approach leverages the design freedom of 3D printing for the overall shape and the precision of machining for key features.
- 非破壊検査(NDT): To ensure the structural integrity of the 3D printed aerospace spar, various NDT methods are employed to detect any internal flaws or defects that may have occurred during the printing process. Common NDT techniques include:
- Radiographic Testing (X-ray): To identify internal voids or inclusions.
- Ultrasonic Testing: To detect subsurface discontinuities.
- Fluorescent Penetrant Inspection (FPI): To reveal surface cracks or porosity.
- Heat Treatment for Property Enhancement: In addition to stress relief, further heat treatments can be applied to optimize the mechanical properties of the 3D printed material. For example, age hardening can increase the strength and hardness of certain aluminum alloys like Scalmalloy® and AlSi10Mg. The specific heat treatment cycle depends on the alloy and the desired performance characteristics.
By carefully executing these post-processing steps, manufacturers like those partnering with メタル3DP can ensure that 3D printed aerospace spars meet the stringent quality and performance requirements of the aerospace industry.
Common Challenges and How to Avoid Them in 3D Printing Aerospace Spars
While metal 3D printing offers numerous advantages for producing aerospace spars, several challenges can arise during the process. Understanding these potential issues and implementing appropriate strategies to avoid them is crucial for successful and reliable manufacturing.
- Warping and Distortion: Thermal gradients during the printing process can cause internal stresses that lead to warping or distortion of the spar, particularly for large or complex geometries.
- Avoidance: Optimizing part orientation, using support structures strategically, and employing stress relief heat treatments can mitigate warping. Simulation tools can also help predict and compensate for potential distortion. Metal3DP’s expertise in process control helps minimize these issues.
- Residual Stresses: As mentioned earlier, residual stresses can compromise the structural integrity and fatigue life of the printed spar.
- Avoidance: Implementing appropriate stress relief heat treatment cycles is essential. Optimizing the printing parameters, such as laser power and scan speed, can also help reduce residual stress buildup.
- Porosity and Density Issues: Insufficient melting or gas entrapment during the printing process can lead to porosity within the spar, reducing its strength and fatigue resistance.
- Avoidance: Selecting high-quality metal powders with good flowability (like those offered by メタル3DP), optimizing printing parameters, and ensuring a controlled printing environment are crucial for achieving high density. Hot Isostatic Pressing (HIP) is a post-processing technique that can further reduce porosity.
- Support Structure Removal Damage: Removing support structures can sometimes leave surface blemishes or even damage delicate features of the spar.
- Avoidance: Designing self-supporting geometries whenever possible, using optimized support structures with breakaway features, and employing skilled technicians for support removal can minimize this risk.
- Material Consistency and Traceability: Ensuring the consistency and traceability of the metal powder is critical in aerospace applications. Variations in powder composition or particle size distribution can affect the properties of the printed part.
- Avoidance: Working with reputable powder suppliers like メタル3DP, who have robust quality control processes and provide material certifications, is essential. Maintaining detailed records of the powder batch used for each print ensures traceability.
- 表面仕上げの要件: Achieving the smooth surface finishes required for certain aerospace applications can be challenging with as-built 3D printed parts.
- Avoidance: Planning for appropriate post-processing steps, such as media blasting, polishing, or machining, during the design phase is necessary. Selecting the right printing parameters can also influence the initial surface finish.
- Cost and Scalability: While 3D printing offers advantages for complex, low-volume production, the cost per part can be higher than traditional methods for large volumes. Scaling up production can also present challenges.
- Avoidance: Carefully evaluating the total cost of ownership, including material, printing, and post-processing, is crucial. Optimizing designs for efficient printing and exploring strategies for scaling production with experienced partners like メタル3DP can help address these concerns.
By proactively addressing these potential challenges through careful design, process optimization, and collaboration with experienced metal 3D printing service providers, the aerospace industry can successfully leverage the benefits of additive manufacturing for critical components like spars.
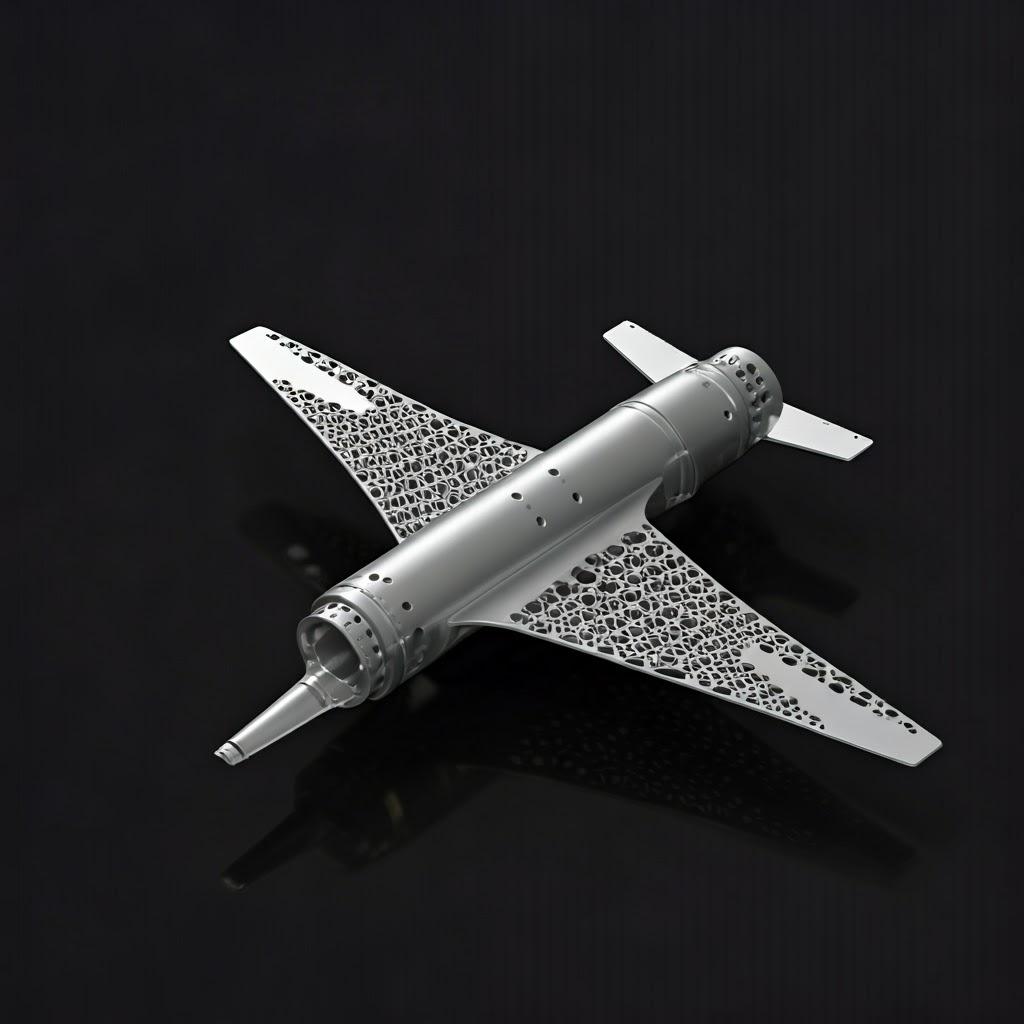
How to Choose the Right Metal 3D Printing Service Provider for Aerospace Components
Selecting the right metal 3D printing service provider is a critical decision for aerospace companies looking to leverage the benefits of additive manufacturing for components like spars. Given the stringent quality and regulatory requirements of the aerospace industry, a thorough evaluation of potential suppliers is essential. Here are key factors to consider:
- Industry Certifications and Standards: Ensure the service provider holds relevant aerospace certifications, such as AS9100. This certification demonstrates their commitment to quality management systems specific to the aerospace industry. Inquire about their adherence to other relevant standards and Nadcap accreditations for processes like heat treatment and non-destructive testing.
- Material Expertise and Range: The provider should have extensive experience working with the specific aerospace-grade materials required for your application, such as Scalmalloy® and AlSi10Mg. Inquire about their material characterization data, process parameters, and expertise in optimizing these materials for additive manufacturing. メタル3DP boasts a comprehensive portfolio of high-performance metal powders tailored for aerospace needs.
- Printing Technology and Capabilities: Understand the types of metal 3D printing technologies the provider utilizes (e.g., SLM, EBM, DED). Ensure they have the equipment and expertise suitable for the size, complexity, and tolerance requirements of your aerospace spars. メタル3DP offers industry-leading print volume, accuracy, and reliability with their printing solutions.
- Design for Additive Manufacturing (DfAM) Support: A knowledgeable service provider should offer support in optimizing your spar design for additive manufacturing. This includes guidance on topology optimization, lattice structures, part consolidation, and orientation for printing. Their expertise in DfAM can significantly impact the performance, weight, and cost-effectiveness of the final component.
- Post-Processing Capabilities: As discussed earlier, post-processing is often crucial for aerospace components. Evaluate the provider’s in-house or partnered capabilities for stress relief heat treatment, support removal, surface finishing (e.g., polishing, coating), and CNC machining. Ensure they have the necessary quality control measures in place for these processes.
- Quality Control and Inspection Procedures: Inquire about the provider’s quality control processes, including dimensional inspection, material testing, and non-destructive testing (NDT). They should have robust procedures in place to ensure that the printed spars meet the required specifications and are free from critical defects.
- Traceability and Documentation: For aerospace components, full material and process traceability is essential. The service provider should have systems in place to track material lots, build parameters, post-processing steps, and inspection results. Comprehensive documentation should be provided with the finished parts.
- Communication and Project Management: Effective communication and project management are crucial for a successful partnership. Assess the provider’s responsiveness, technical support, and ability to manage complex aerospace projects with strict timelines.
- Cost and Lead Times: While quality and expertise are paramount, cost-effectiveness and lead times are also important considerations. Obtain detailed quotes and understand the factors influencing pricing and production timelines. Compare different providers based on overall value.
- Confidentiality and Intellectual Property Protection: Ensure the service provider has robust measures in place to protect your confidential designs and intellectual property.
By carefully evaluating potential metal 3D printing service providers based on these criteria, aerospace companies can establish partnerships that ensure the reliable and high-quality production of critical components like spars. Consider reaching out to メタル3DP to explore their comprehensive additive manufacturing solutions for the aerospace industry.
Cost Factors and Lead Time for 3D Printed Aerospace Spars
Understanding the cost drivers and lead times associated with 3D printed aerospace spars is crucial for effective project planning and budget management. While metal 3D printing can offer long-term cost benefits through weight reduction and design optimization, the initial costs and lead times can vary depending on several factors:
コスト要因:
- 材料費: The cost of the metal powder is a significant factor. Aerospace-grade materials like Scalmalloy® and specialized aluminum alloys can be more expensive than standard metals. The quantity of material used, which is influenced by the part’s volume and the efficiency of the design (e.g., use of lattice structures), will directly impact the material cost.
- 印刷時間: The build time on the metal 3D printer is a major cost driver. Longer print times consume more machine time and energy. Factors influencing print time include the part’s size, complexity, build volume utilization, and layer thickness.
- Pre-processing Costs: This can include design optimization for additive manufacturing (DfAM) services, build file preparation, and material handling.
- Post-processing Costs: As discussed earlier, post-processing steps like stress relief, support removal, surface finishing, machining, and non-destructive testing add to the overall cost. The complexity and extent of these processes will influence the final price.
- Equipment and Overhead Costs: The service provider’s capital investment in metal 3D printers, facility costs, labor, and quality control measures are factored into their pricing.
- Volume and Scalability: The cost per part can decrease with higher production volumes, but metal 3D printing is often most cost-effective for low-to-medium volume production of complex parts. Scaling up production may require additional equipment or build platforms.
- Quality Assurance and Documentation: The stringent quality control and documentation requirements of the aerospace industry can also influence pricing.
Lead Time Factors:
- Design and Engineering: The initial design and optimization phase for 3D printing can take time, especially for complex aerospace components requiring topology optimization and detailed analysis.
- Material Procurement: Lead times for specialized aerospace-grade metal powders can vary depending on availability.
- 印刷時間: As mentioned, the actual build time on the 3D printer is a significant part of the lead time.
- 後処理: The time required for various post-processing steps, such as heat treatment, surface finishing, and NDT, will add to the overall lead time. Complex post-processing requirements can extend the delivery schedule.
- Quality Control and Inspection: Thorough inspection processes can take time to ensure the parts meet the required standards.
- Scheduling and Capacity: The service provider’s current workload and machine availability can impact lead times.
While the initial cost per part for 3D printed aerospace spars might be higher than traditional manufacturing methods for very high volumes, the benefits of weight reduction, design optimization, and faster prototyping can lead to significant long-term cost savings and reduced time-to-market. Collaborating with an experienced provider like メタル3DP can help optimize both cost and lead time through efficient design and streamlined processes. Consider discussing your specific requirements with メタル3DP to get a detailed understanding of the cost and lead time for your aerospace spar application.
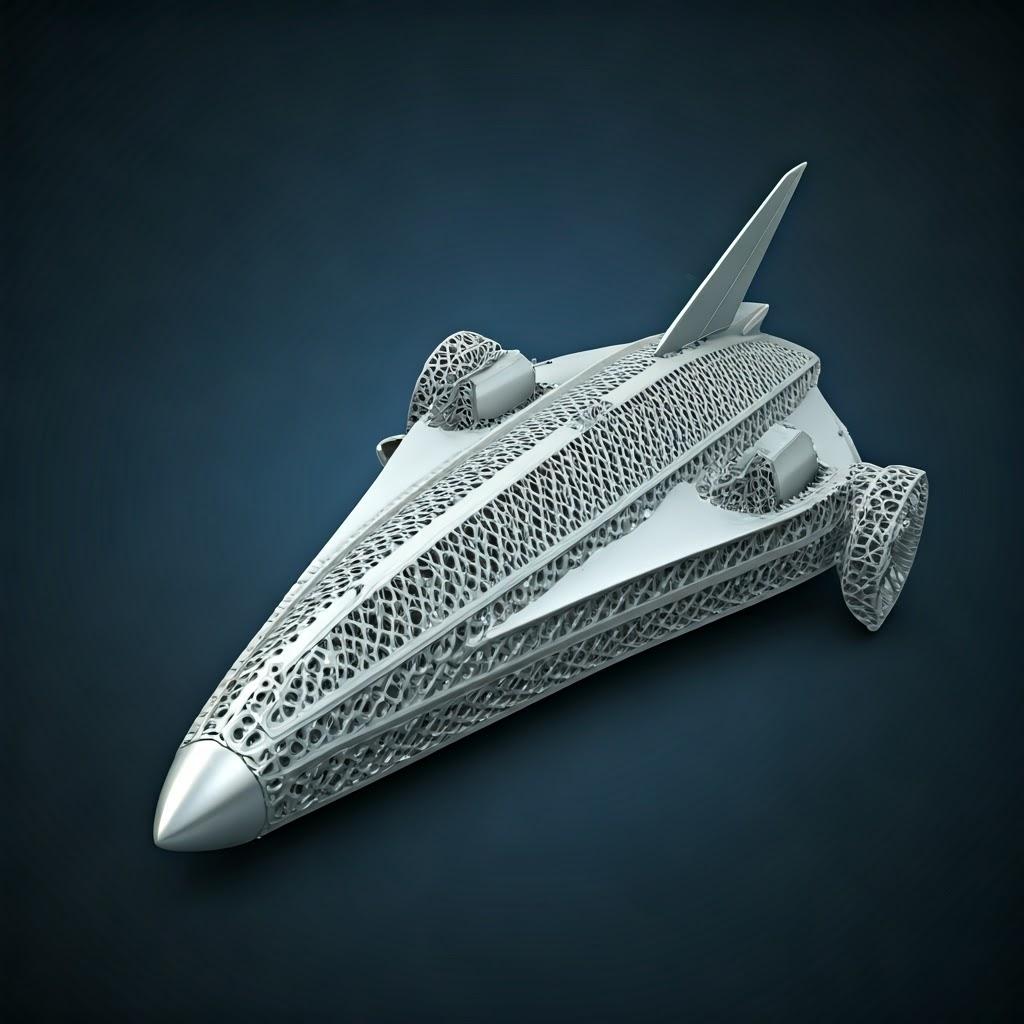
Frequently Asked Questions (FAQ) about 3D Printed Aerospace Spars
Here are some frequently asked questions regarding the use of metal 3D printing for aerospace spars:
- What are the key benefits of using 3D printed spars in aerospace?
- 答え: The primary benefits include significant weight reduction through optimized designs and material usage, enhanced design freedom for complex geometries and part consolidation, faster prototyping and reduced lead times for customized parts, and the ability to utilize high-performance materials tailored for aerospace requirements.
- Are 3D printed metal spars strong and reliable enough for aerospace applications?
- 答え: Yes, when manufactured using high-quality aerospace-grade metal powders (such as Scalmalloy® and AlSi10Mg offered by メタル3DP) and adhering to stringent quality control processes, 3D printed metal spars can meet or exceed the strength and reliability requirements of the aerospace industry. Proper design optimization, post-processing, and non-destructive testing are crucial to ensure structural integrity.
- What design considerations are unique to 3D printing aerospace spars?
- 答え: Unique design considerations include leveraging topology optimization and lattice structures for weight reduction, designing for part consolidation, optimizing build orientation to minimize support structures, incorporating internal channels for various functionalities, and adhering to minimum feature size and wall thickness limitations of the printing process.
- How does the cost of 3D printed spars compare to traditionally manufactured spars?
- 答え: The initial cost per part for 3D printed spars can be higher for very high volumes. However, for low-to-medium volumes, complex geometries, and customized parts, 3D printing can be more cost-effective due to reduced material waste, elimination of tooling costs, and potential for part consolidation. Long-term cost savings can also be realized through weight reduction and improved fuel efficiency.
- What post-processing is typically required for 3D printed aerospace spars?
- 答え: Common post-processing steps include stress relief heat treatment to improve mechanical properties, support structure removal, surface treatment (e.g., media blasting, polishing) to achieve desired surface finish, and non-destructive testing (NDT) to ensure structural integrity. CNC machining may be used for critical interfaces requiring very tight tolerances.
- How do aerospace companies ensure the quality and certification of 3D printed spars?
- 答え: Ensuring quality and certification involves working with service providers who hold relevant aerospace certifications (e.g., AS9100), utilizing certified aerospace-grade materials with full traceability, implementing rigorous quality control and inspection procedures (including NDT), and maintaining comprehensive documentation of the entire manufacturing process.
Conclusion – Embracing the Future of Aerospace Manufacturing with 3D Printed Spars
The integration of metal 3D printing into the aerospace industry represents a significant leap forward in the design and manufacturing of critical structural components like spars. The ability to create lightweight, complex geometries with tailored material properties offers unprecedented opportunities for enhancing aircraft performance, improving fuel efficiency, and streamlining production processes.
次のような企業 メタル3DP are at the forefront of this transformative technology, providing advanced metal 3D printing equipment and a comprehensive range of high-performance metal powders, including Scalmalloy® and AlSi10Mg, specifically designed for demanding aerospace applications. By partnering with experienced service providers and embracing design for additive manufacturing principles, aerospace engineers and procurement managers can unlock the full potential of metal 3D printing for spars and other critical components.
The journey towards widespread adoption of 3D printed aerospace parts requires careful consideration of design, material selection, manufacturing processes, post-processing, and quality assurance. However, the compelling advantages in terms of weight reduction, performance enhancement, and design freedom make metal 3D printing an indispensable tool for the future of aerospace manufacturing. Contact メタル3DP today to explore how their cutting-edge systems and materials can empower your organization’s additive manufacturing goals and drive innovation in the aerospace sector. Visit Metal3DP’s 私たちについて page to learn more about their expertise and commitment to the industry.
シェアする
MET3DP Technology Co., LTDは、中国青島に本社を置く積層造形ソリューションのリーディングプロバイダーです。弊社は3Dプリンティング装置と工業用途の高性能金属粉末を専門としています。