Electric Motor Stator Housings using metal 3D printing
目次
Introduction – The Critical Role of Electric Motor Stator Housings in Modern EVs
The electric vehicle (EV) revolution is reshaping the automotive landscape, demanding innovation in every component, including the often-unsung hero: the electric motor stator housing. This critical component serves as the backbone of the electric motor, providing structural support for the stator core and windings, facilitating heat dissipation, and ensuring the overall integrity and performance of the powertrain. As the demand for high-performance, lightweight, and efficient EVs continues to surge, traditional manufacturing methods for stator housings are increasingly facing limitations in terms of design flexibility, material optimization, and production scalability. This is where metal 3Dプリンティング, also known as metal additive manufacturing, emerges as a transformative solution, offering unprecedented opportunities to engineer and produce electric motor stator housings with enhanced functionalities and tailored properties. At メタル3DP, we understand the pivotal role of these components and are at the forefront of providing advanced metal 3D printing solutions to meet the evolving needs of the electric vehicle industry. Our commitment to industry-leading print volume, accuracy, and reliability ensures that mission-critical EV components, like stator housings, are manufactured to the highest standards.
What are Electric Motor Stator Housings Used For? – Applications Across the EV Landscape
Electric motor stator housings are integral to the functionality and longevity of electric powertrains across a diverse range of EV applications. Their primary functions include:
- Structural Support: The housing provides a rigid framework that securely holds the stator laminations and copper windings in precise alignment. This structural integrity is crucial for maintaining the air gap between the stator and rotor, which directly impacts the motor’s efficiency and torque output.
- Heat Dissipation: Electric motors generate significant heat during operation. The stator housing often incorporates design features, such as cooling channels or fins, to facilitate efficient heat transfer away from the motor’s active components, preventing overheating and ensuring optimal performance and lifespan.
- 電磁シールド: The metallic nature of the housing can provide a degree of electromagnetic shielding, containing the electromagnetic fields generated by the motor and preventing interference with other sensitive electronic systems within the vehicle.
- Protection: The housing acts as a protective barrier against environmental factors such as dust, moisture, and debris, safeguarding the delicate internal components of the electric motor.
- Mounting Interface: The stator housing typically includes features for mounting the motor to the vehicle’s chassis or transmission, ensuring secure and stable integration within the powertrain system.
The applications of electric motor stator housings extend across the entire spectrum of electric mobility, including:
- Battery Electric Vehicles (BEVs): From compact city cars to high-performance SUVs, stator housings are essential components in the primary propulsion motors of all battery-powered electric vehicles.
- Plug-in Hybrid Electric Vehicles (PHEVs): PHEVs utilize both an internal combustion engine and one or more electric motors. Stator housings are critical in the electric motor(s) that contribute to the vehicle’s hybrid powertrain.
- Electric Buses and Trucks: Larger electric vehicles for public transportation and logistics rely on robust and efficient electric motors with precisely engineered stator housings to deliver the necessary power and torque.
- Electric Motorcycles and Scooters: The growing market for electric two-wheelers also incorporates electric motors with stator housings designed for specific size, weight, and performance requirements.
- Specialty Electric Vehicles: Beyond mainstream automotive, electric motors with stator housings find applications in material handling equipment, agricultural machinery, and other specialized electric vehicles.
で メタル3DP, our advanced metal 3D printing processes enable the production of complex stator housing geometries tailored to the specific demands of each application, offering enhanced performance and integration capabilities.
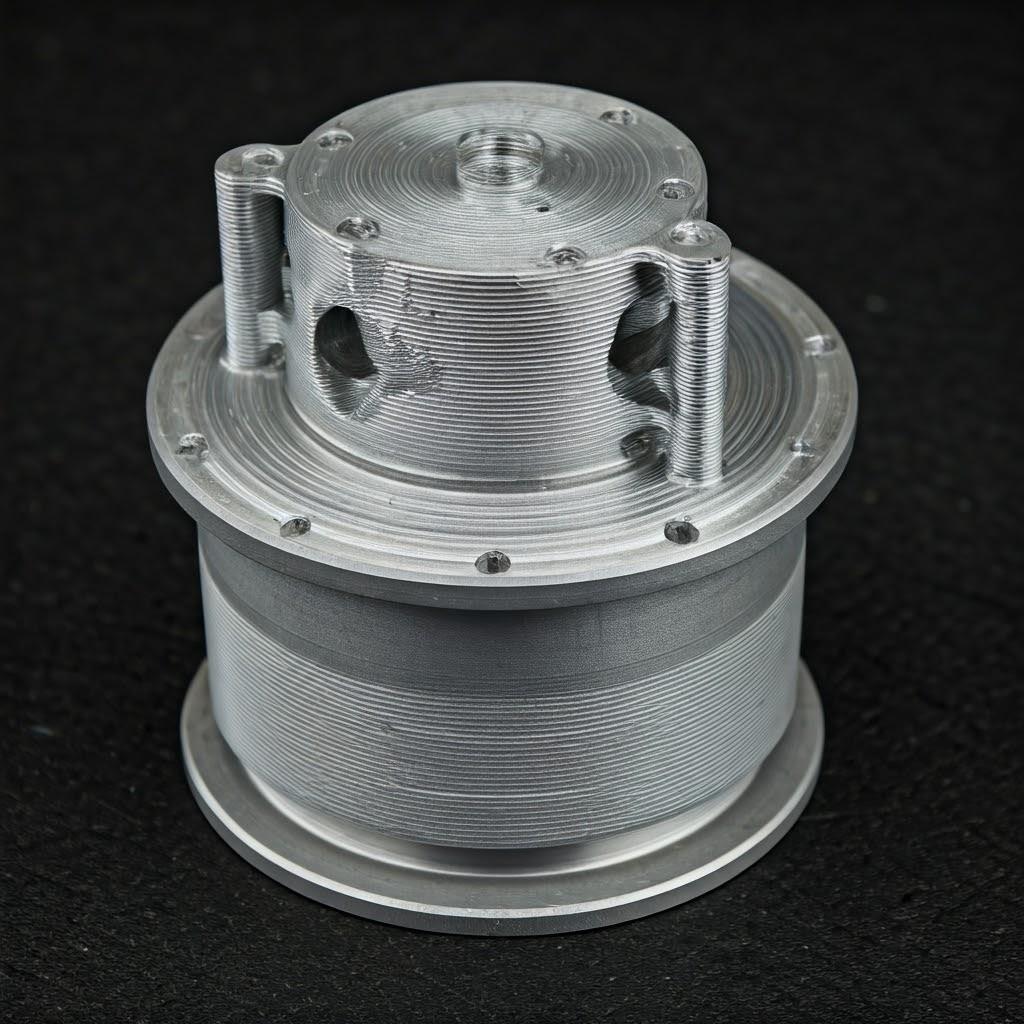
Why Use Metal 3D Printing for Electric Motor Stator Housings? – Advantages Over Traditional Manufacturing
Adopting metal 3D printing for the production of electric motor stator housings offers a compelling array of advantages compared to conventional manufacturing methods such as casting, machining, or stamping:
- デザインの自由と複雑さ: Metal 3D printing allows for the creation of intricate geometries and internal features that are difficult or impossible to achieve with traditional methods. This includes optimized cooling channels, integrated mounting features, and lightweight lattice structures, leading to improved performance and reduced weight. Our industry-leading print volume at メタル3DP enables the production of larger and more complex stator housings as single parts, minimizing assembly requirements.
- 素材の最適化: Metal 3D printing provides the flexibility to utilize a wide range of high-performance metal powders, such as AlSi10Mg and 17-4PH, which offer specific properties tailored to the demands of EV motor applications. Furthermore, additive manufacturing minimizes material waste as material is only deposited where needed. メタル3DP manufactures a comprehensive portfolio of high-quality metal powders, ensuring optimal material selection for stator housings.
- 軽量化: The ability to create complex internal structures and optimize material distribution allows for the production of lighter stator housings without compromising structural integrity. Reduced weight contributes to improved vehicle efficiency and range, crucial factors in the EV market.
- ラピッドプロトタイピングと反復: Metal 3D printing significantly accelerates the prototyping process, allowing engineers to quickly iterate on designs and test different configurations. This faster design cycle reduces development time and costs.
- Customization and Low-Volume Production: Additive manufacturing is particularly advantageous for producing customized stator housings for specific motor designs or for low-volume production runs, where traditional tooling costs can be prohibitive.
- Integrated Functionality: Features such as cooling channels, sensor integration points, and mounting interfaces can be directly incorporated into the design and 3D printed as part of the stator housing, reducing the need for secondary operations and assembly.
- パフォーマンスの向上: Optimized designs enabled by 3D printing can lead to enhanced heat dissipation, improved structural rigidity, and potentially reduced electromagnetic noise, contributing to overall motor performance and efficiency.
By leveraging metal 3D printing, EV manufacturers can overcome the limitations of traditional manufacturing and unlock new possibilities in the design and production of high-performance electric motor stator housings. Metal3DPへのお問い合わせ to explore how our advanced additive manufacturing capabilities can power your organization’s EV manufacturing goals.
Recommended Materials and Why They Matter – AlSi10Mg and 17-4PH for Optimal Performance
The choice of material for electric motor stator housings is critical for ensuring optimal performance, durability, and reliability. Metal 3D printing offers the flexibility to utilize advanced metal powders tailored to these demanding applications. で メタル3DP, we recommend and offer high-quality powders such as AlSi10Mg and 17-4PH for the additive manufacturing of EV stator housings, each possessing unique properties that cater to specific performance requirements. Our advanced powder making system ensures the production of metallic spheres with high sphericity and good flowability, essential for consistent and high-quality 3D printing.
AlSi10Mg:
- 構成: An aluminum alloy containing silicon (Si) and magnesium (Mg).
- Key Properties and Benefits:
- 優れた熱伝導性: Aluminum alloys, including AlSi10Mg, exhibit high thermal conductivity, which is crucial for efficient heat dissipation in electric motors. This helps to maintain optimal operating temperatures and prolong the motor’s lifespan.
- 軽量だ: Aluminum is significantly lighter than steel, contributing to overall weight reduction in the vehicle, which in turn improves energy efficiency and range.
- 優れた強度対重量比: AlSi10Mg offers a good balance of strength and weight, providing the necessary structural integrity for the stator housing while minimizing mass.
- 耐食性: Aluminum alloys generally possess good corrosion resistance, which is important for the long-term reliability of the motor in various environmental conditions.
- 良好な印刷性: AlSi10Mg is a well-established material for powder bed fusion processes like Selective Laser Melting (SLM), offering good printability and consistent results.
17-4PHステンレス鋼:
- 構成: A martensitic precipitation-hardening stainless steel containing chromium (Cr), nickel (Ni), and copper (Cu).
- Key Properties and Benefits:
- 高い強度と硬度: 17-4PH offers exceptional strength and hardness after heat treatment, making it suitable for applications requiring high structural integrity and resistance to mechanical stress.
- 良好な耐食性: As a stainless steel, 17-4PH provides excellent resistance to corrosion in a wide range of environments.
- Good Fatigue Strength: This material exhibits good fatigue strength, which is important for components subjected to cyclic loading during motor operation.
- Moderate Thermal Conductivity: While not as high as aluminum alloys, 17-4PH still offers adequate thermal conductivity for many stator housing applications.
- 優れた耐摩耗性: The high hardness of 17-4PH contributes to good wear resistance, which can be beneficial for mounting interfaces or other areas subject to friction.
The selection between AlSi10Mg and 17-4PH depends on the specific performance requirements of the electric motor and the overall vehicle design. For applications where lightweighting and thermal management are paramount, AlSi10Mg is often the preferred choice. In cases where high strength and corrosion resistance are critical, 17-4PH provides an excellent solution. メタル3DP offers both of these high-quality metal powders, along with our expertise in material selection and application development, to help our customers achieve optimal results in their 3D printed EV stator housings.
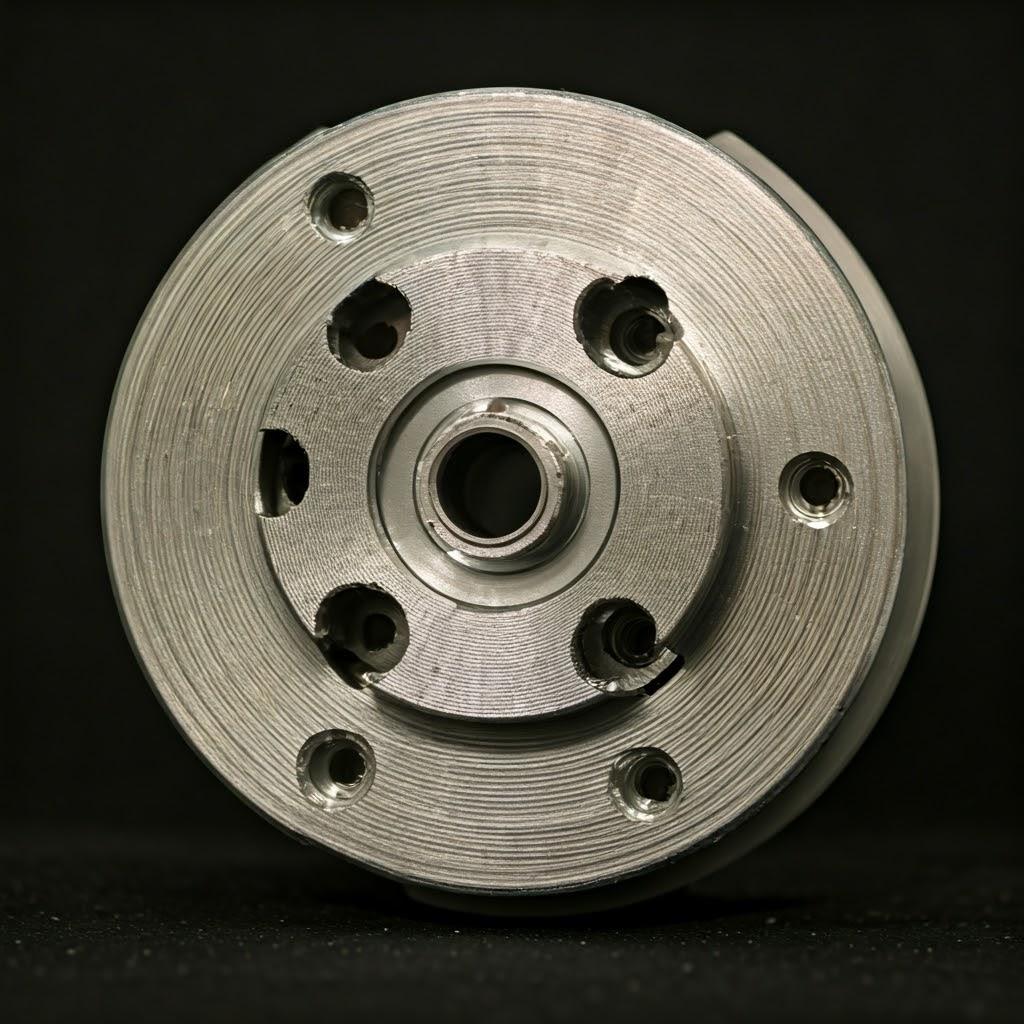
Design Considerations for Additive Manufacturing of Stator Housings – Optimizing for 3D Printing
Designing electric motor stator housings for metal 3D printing requires a shift in mindset compared to traditional manufacturing approaches. To fully leverage the capabilities of additive manufacturing and achieve optimal performance, several key design considerations must be taken into account:
- Topology Optimization: Metal 3D printing enables the creation of complex, organic shapes. Topology optimization software can be used to identify the most efficient material distribution based on applied loads and boundary conditions, resulting in lightweight yet structurally sound housings. This can lead to significant material savings and improved performance.
- 格子構造: Incorporating lattice structures within the non-critical areas of the stator housing can further reduce weight without compromising stiffness. These intricate internal networks provide excellent strength-to-weight ratios and can also enhance heat transfer through increased surface area.
- Integrated Cooling Channels: One of the significant advantages of 3D printing is the ability to design and fabricate internal cooling channels with complex geometries that closely follow the heat-generating components. This allows for more efficient and targeted cooling compared to traditional drilled channels, leading to improved motor performance and longevity.
- Wall Thickness and Ribbing: Careful consideration of wall thickness is crucial to balance weight, strength, and printability. Incorporating ribs and stiffeners in strategic locations can enhance the structural rigidity of thin-walled sections without adding excessive weight.
- Support Structure Optimization: Support structures are often necessary in metal 3D printing to prevent part deformation during the build process. Designing with self-supporting angles and minimizing the need for extensive supports is essential for reducing material waste, post-processing time, and surface finish issues.
- Feature Integration: Additive manufacturing allows for the integration of multiple functionalities into a single part. Features such as mounting bosses, sensor housings, and wire routing channels can be directly incorporated into the stator housing design, reducing the need for separate components and assembly steps.
- Surface Finish Considerations: The as-printed surface finish of metal 3D printed parts can vary depending on the material and printing process. Designing with this in mind and planning for any necessary post-processing steps, such as machining or polishing, is important for achieving the required surface quality and dimensional accuracy.
- Assembly Interfaces: When the stator housing is part of a larger assembly, designing precise and robust interfaces for connection with other components is crucial. 3D printing allows for the creation of complex interlocking features and precise mating surfaces.
By embracing these design principles, engineers can fully exploit the potential of metal 3D printing to create innovative and high-performance electric motor stator housings. メタル3DP‘s expertise in design for additive manufacturing ensures that our customers can optimize their components for both functionality and efficient production.
Tolerance, Surface Finish, and Dimensional Accuracy in 3D Printed Stator Housings
Achieving the required tolerance, surface finish, and dimensional accuracy is paramount for the functional performance and integration of electric motor stator housings. Metal 3D printing technologies have advanced significantly in their ability to produce parts with tight specifications. However, understanding the capabilities and limitations of different processes and materials is crucial.
- 寸法精度: The dimensional accuracy achievable with metal 3D printing depends on factors such as the printing technology (e.g., SLM, DMLS, EBM), the material used, part geometry, and build orientation. Generally, tolerances in the range of ±0.1 to ±0.05 mm can be achieved for critical dimensions. It’s important to design with these tolerances in mind and to identify critical features that may require post-processing for tighter accuracy.
- 表面仕上げ: The as-printed surface finish in metal 3D printing typically ranges from rough to moderately smooth, depending on the powder particle size and layer thickness. Selective Laser Melting (SLM) and Direct Metal Laser Sintering (DMLS) generally produce finer surface finishes compared to Electron Beam Melting (EBM). For applications requiring smoother surfaces, post-processing techniques such as machining, grinding, polishing, or surface coating can be employed.
- Factors Affecting Accuracy and Finish:
- 層の厚さ: Thinner layers generally result in better surface finish and higher accuracy but increase build time.
- 粉末の粒子径と分布: Finer, more uniform powder particles contribute to a smoother surface and higher resolution. メタル3DP‘s advanced powder making system ensures high sphericity and good flowability, leading to improved print quality.
- ビルド方向: The orientation of the part during printing can significantly impact dimensional accuracy and surface finish, particularly for overhanging surfaces.
- サポート体制: The placement and removal of support structures can affect the surface finish of the supported areas. Careful design and support optimization are essential.
- Machine Calibration and Maintenance: Properly calibrated and maintained 3D printing equipment is crucial for consistent accuracy and repeatability. メタル3DP‘s commitment to accuracy and reliability in our printers ensures high-quality output.
To ensure that 3D printed stator housings meet the required specifications, it’s essential to:
- Design with Manufacturing in Mind (DFM): Consider the capabilities and limitations of the chosen 3D printing process during the design phase.
- Specify Tolerances Clearly: Clearly define the critical dimensions and their required tolerances in the design documentation.
- Choose the Right Printing Process and Material: Select the appropriate technology and material based on the performance requirements and desired accuracy and surface finish.
- Plan for Post-Processing: If necessary, incorporate post-processing steps into the manufacturing workflow to achieve the required surface finish and dimensional accuracy.
- Utilize Metrology and Inspection: Employ appropriate measurement techniques to verify that the printed parts meet the specified tolerances and surface finish requirements.
メタル3DP works closely with our customers to understand their specific requirements for tolerance, surface finish, and dimensional accuracy, and we leverage our expertise and advanced printing technologies to deliver high-quality metal 3D printed stator housings that meet these critical specifications.
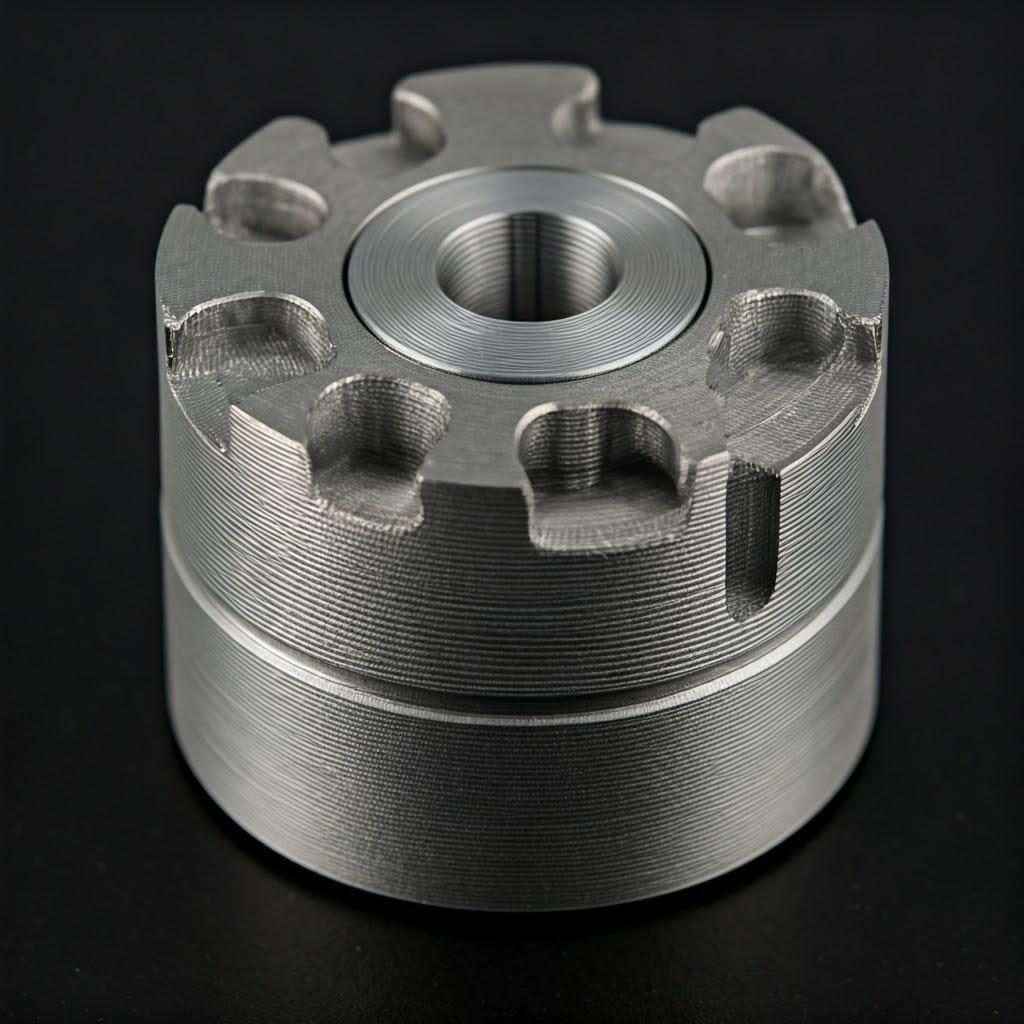
Post-Processing Requirements for Metal 3D Printed EV Stator Housings
While metal 3D printing offers significant advantages in terms of design freedom and complexity, post-processing is often required to achieve the final functional part with the desired properties and finish. The specific post-processing steps for electric motor stator housings can vary depending on the material, printing process, and application requirements.
- サポートの取り外し: In most metal 3D printing processes, support structures are necessary to prevent deformation during the build. These supports need to be carefully removed after printing. Techniques include manual removal, machining, wire EDM, or chemical dissolution, depending on the support material and part geometry.
- 熱処理: To achieve the desired mechanical properties, such as strength and hardness, metal 3D printed parts often undergo heat treatment. The specific heat treatment cycle depends on the material. For example, 17-4PH stainless steel requires precipitation hardening to reach its optimal strength.
- ストレス解消: Residual stresses can build up during the 3D printing process. Stress relief annealing can be performed to reduce these stresses and prevent potential warping or cracking.
- 表面仕上げ: As mentioned earlier, the as-printed surface finish may not be suitable for all applications. Common surface finishing techniques include:
- Machining (CNC): Precision machining can be used to achieve tight tolerances and smooth surface finishes on critical mating surfaces or features.
- Grinding and Polishing: These processes can improve surface smoothness and remove any remaining support marks.
- ショットピーニング: This surface treatment can enhance fatigue resistance by introducing compressive stresses on the surface.
- 表面コーティング: Coatings, such as anodizing for aluminum or passivation for stainless steel, can be applied to improve corrosion resistance, wear resistance, or electrical insulation properties.
- Joining and Assembly: In some cases, a stator housing may consist of multiple 3D printed components that need to be joined together using methods like welding, brazing, or mechanical fastening.
- Inspection and Quality Control: Thorough inspection using techniques such as coordinate measuring machines (CMM), non-destructive testing (NDT), and surface roughness measurement is essential to ensure that the final part meets the required dimensional accuracy, surface finish, and material integrity specifications.
Planning for post-processing early in the design phase is crucial for optimizing the overall manufacturing workflow and minimizing costs. Selecting the appropriate post-processing techniques and ensuring their availability are important considerations when choosing a metal 3D printing service provider. メタル3DP offers comprehensive solutions that include not only advanced metal 3D printing but also access to necessary post-processing capabilities to deliver fully functional and high-quality electric motor stator housings.
Common Challenges and How to Avoid Them in 3D Printing Stator Housings
While metal 3D printing offers numerous advantages, there are also potential challenges that need to be addressed to ensure successful production of electric motor stator housings. Understanding these challenges and implementing appropriate strategies to avoid them is crucial.
- Warping and Distortion: Thermal gradients during the printing process can lead to residual stresses and subsequent warping or distortion of the part, especially for complex geometries or large parts.
- How to Avoid: Optimize part orientation, use appropriate support structures, control the build chamber temperature, and consider stress relief heat treatment.
- Porosity and Density Issues: Incomplete fusion of powder particles can result in porosity within the printed part, which can negatively impact its mechanical properties and performance.
- How to Avoid: Optimize printing parameters such as laser power, scan speed, and layer thickness; ensure high-quality metal powders with good flowability (as provided by メタル3DP); and consider Hot Isostatic Pressing (HIP) for densification.
- Surface Finish Issues: Achieving a smooth surface finish directly from the 3D printer can be challenging. Rough surfaces may require extensive post-processing.
- How to Avoid: Optimize build orientation to minimize stepped surfaces, use finer powder particles, reduce layer thickness, and plan for appropriate surface finishing techniques.
- 支持構造の撤去: Removing support structures can be time-consuming and may leave surface marks, especially on intricate geometries.
- How to Avoid: Design parts with self-supporting angles where possible, optimize support placement and type, and utilize dissolvable support materials if available for the chosen material.
- Dimensional Inaccuracy: Deviations from the intended dimensions can occur due to shrinkage, thermal expansion, or machine calibration issues.
- How to Avoid: Calibrate and maintain the 3D printer regularly, compensate for material shrinkage in the design phase, and use appropriate build parameters.
- Material Property Variability: The mechanical properties of 3D printed parts can sometimes vary depending on the build orientation and processing parameters.
- How to Avoid: Establish robust process control, optimize build parameters for consistent properties, and conduct thorough material testing and qualification.
- コストを考慮する: While 3D printing can be cost-effective for low-volume production and complex designs, the cost per part can be higher for large volumes compared to traditional methods.
- How to Avoid: Optimize part design for efficient printing, minimize material usage and build time, and carefully evaluate the overall manufacturing costs, including post-processing.
By proactively addressing these potential challenges through careful design, optimized process parameters, and appropriate post-processing, manufacturers can successfully leverage metal 3D printing to produce high-quality electric motor stator housings. メタル3DP‘s expertise in metal additive manufacturing and our understanding of these challenges enable us to provide solutions and guidance to our customers for successful outcomes.
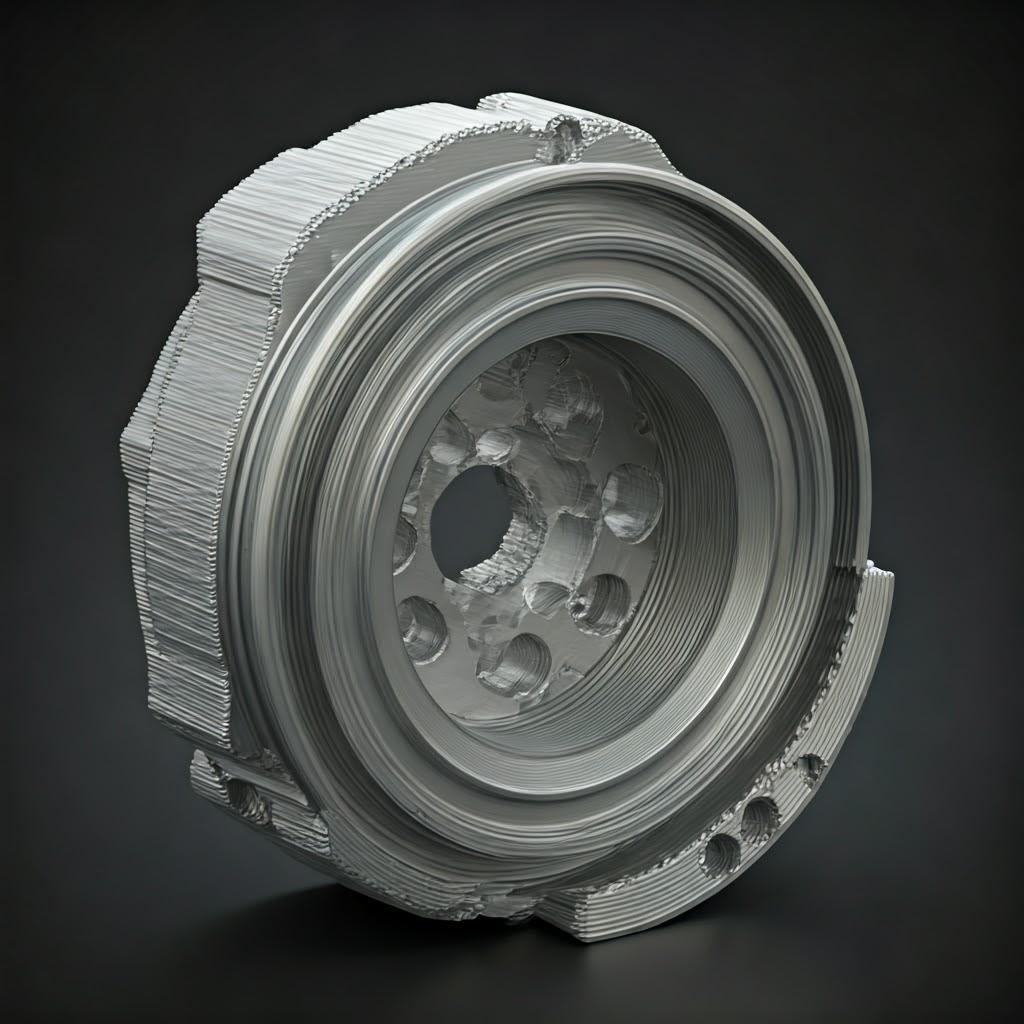
How to Choose the Right Metal 3D Printing Service Provider for EV Components
Selecting the right metal 3D printing service provider is a critical decision for EV manufacturers looking to leverage the benefits of additive manufacturing for components like stator housings. A reliable and experienced partner can significantly impact the quality, cost-effectiveness, and timely delivery of these crucial parts. Here are key factors to consider when evaluating potential service providers:
- Material Capabilities: Ensure the provider has experience working with the recommended materials for EV stator housings, such as AlSi10Mg and 17-4PH, and possesses the necessary material certifications and quality control processes. メタル3DP offers a wide range of high-quality metal powders optimized for various applications.
- Printing Technology and Equipment: Understand the types of metal 3D printing technologies the provider utilizes (e.g., SLM, DMLS, EBM) and their fleet of printers. Industry-leading print volume, accuracy, and reliability are crucial for consistent production. メタル3DP‘s printers are designed to deliver just that for mission-critical parts.
- Industry Experience and Expertise: Look for a provider with a proven track record in serving the automotive, aerospace, medical, or industrial manufacturing sectors, ideally with specific experience in EV components. Their understanding of industry-specific requirements and quality standards is invaluable.
- Design for Additive Manufacturing (DfAM) Support: A strong service provider should offer expertise in DfAM, helping you optimize your stator housing designs for 3D printing to enhance performance, reduce weight, and improve manufacturability. メタル3DP provides comprehensive solutions spanning application development services.
- Post-Processing Capabilities: Determine if the provider offers the necessary post-processing services, such as support removal, heat treatment, surface finishing (machining, polishing, coating), and inspection, to deliver a finished part that meets your specifications.
- Quality Assurance and Certifications: Inquire about the provider’s quality management system, certifications (e.g., ISO 9001, AS9100 for aerospace), and inspection processes to ensure the highest quality standards are met.
- Scalability and Production Capacity: Assess the provider’s ability to handle your current and future production volumes, including their capacity for scaling up as your needs evolve.
- Lead Times and Delivery: Understand the provider’s typical lead times for similar projects and their logistics capabilities to ensure timely delivery of parts.
- Communication and Customer Support: Evaluate the provider’s responsiveness, communication processes, and technical support to ensure a smooth and collaborative partnership.
- コスト競争力: While not the sole factor, cost is an important consideration. Obtain detailed quotes and compare pricing structures, taking into account material costs, printing time, post-processing, and any additional services.
By carefully evaluating these factors, you can select a metal 3D printing service provider that aligns with your specific needs and can reliably deliver high-quality electric motor stator housings. Metal3DPへのお問い合わせ to explore how our capabilities can power your organization’s additive manufacturing goals.
Cost Factors and Lead Time for 3D Printed Electric Motor Stator Housings
Understanding the cost factors and lead times associated with metal 3D printing electric motor stator housings is essential for effective project planning and budgeting. These can vary depending on several parameters:
コスト要因:
- 材料費: The price of the metal powder (e.g., AlSi10Mg, 17-4PH) is a significant factor. Specialized alloys or smaller batch orders can result in higher material costs. メタル3DP manufactures a wide range of high-quality metal powders.
- ビルドタイム: The duration of the printing process directly impacts the cost. Longer build times, influenced by part size, complexity, and layer thickness, increase machine usage and energy consumption costs.
- 後処理費用: The extent and complexity of required post-processing steps (support removal, heat treatment, surface finishing, inspection) contribute to the overall cost.
- Machine Depreciation and Overhead: Service providers factor in the cost of their equipment, maintenance, and operational overhead.
- デザインの最適化: Complex designs requiring significant DfAM effort may incur higher upfront costs.
- Volume and Batch Size: While 3D printing is often cost-effective for low to medium volumes, larger production runs might benefit from economies of scale with traditional manufacturing methods. However, for complex geometries or customized parts, 3D printing can remain competitive even at higher volumes.
リードタイム:
- Design and Engineering: The initial design phase, including optimization for 3D printing, can take varying amounts of time depending on the complexity.
- ビルドタイム: As mentioned earlier, the printing duration is a key component of the lead time.
- Post-Processing Time: Each post-processing step adds to the overall lead time. Simple support removal might take hours, while complex machining or coating processes can take days.
- Quality Control and Inspection: Thorough inspection processes also contribute to the lead time.
- Shipping and Logistics: The time required for packaging and shipping the finished parts needs to be considered.
Generally, metal 3D printing can offer shorter lead times for prototypes and low-volume production compared to traditional tooling-dependent methods. However, for high-volume production, the lead time might be influenced by the number of available printers and the build time per part.
When requesting quotes from metal 3D printing service providers, it’s crucial to provide detailed specifications, including material requirements, tolerances, surface finish, and desired quantities, to get an accurate estimate of both cost and lead time. Factors like part orientation and the need for support structures can also influence these aspects. By understanding these factors, EV manufacturers can make informed decisions about integrating metal 3D printing into their supply chain.
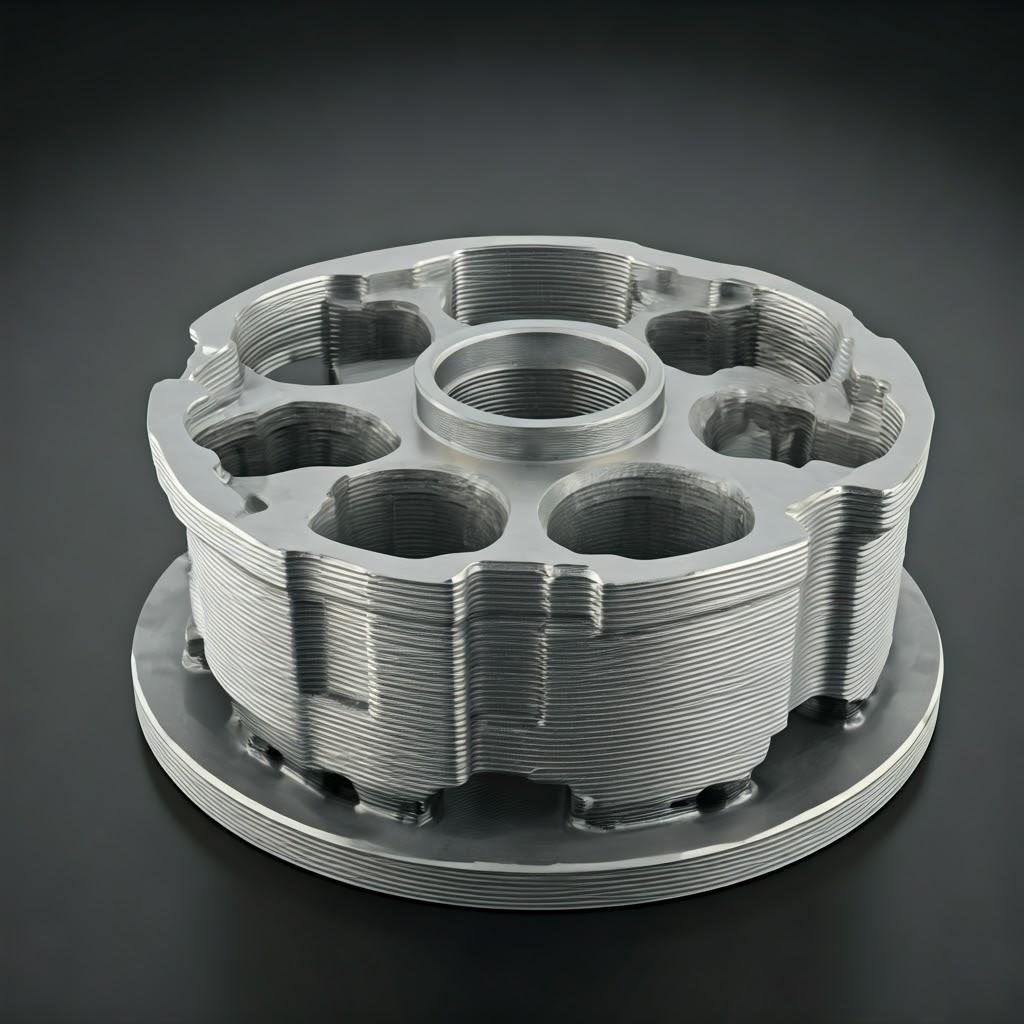
Frequently Asked Questions (FAQ) – Addressing Common Inquiries about 3D Printed Stator Housings
- Q: Can metal 3D printed stator housings achieve the same performance as traditionally manufactured ones?
- A: Yes, often they can exceed the performance of traditionally manufactured housings. Metal 3D printing allows for optimized designs, lightweighting, and tailored material properties that can lead to improved heat dissipation, structural integrity, and overall motor efficiency. The key is proper design for additive manufacturing and material selection, areas where メタル3DP provides significant expertise.
- Q: What is the typical lifespan of a 3D printed metal stator housing in an EV application?
- A: The lifespan depends on factors such as the material used, operating conditions, and post-processing treatments. With appropriate material selection (like AlSi10Mg or 17-4PH offered by メタル3DP) and proper design and post-processing, 3D printed metal stator housings can achieve comparable or even longer lifespans than traditionally manufactured components.
- Q: Is metal 3D printing cost-effective for mass production of EV stator housings?
- A: The cost-effectiveness for mass production depends on the complexity of the design and the specific requirements. While traditional methods might be more economical for very high volumes of simple designs, metal 3D printing can be competitive for complex geometries, customized parts, and medium production volumes, offering advantages in terms of design flexibility and reduced tooling costs. We at メタル3DP can help evaluate the cost-effectiveness for your specific production needs.
Conclusion – Embracing Metal 3D Printing for Next-Generation EV Motor Stator Housings
The electric vehicle industry demands continuous innovation in powertrain technology, and the electric motor stator housing plays a pivotal role in achieving higher performance, efficiency, and reliability. Metal 3D printing stands as a transformative manufacturing approach, offering unparalleled design freedom, material optimization, and the potential for integrated functionality. By leveraging advanced materials like AlSi10Mg and 17-4PH and embracing design principles tailored for additive manufacturing, EV manufacturers can create next-generation stator housings that push the boundaries of what’s possible.
メタル3DP is committed to providing cutting-edge metal additive manufacturing solutions, from high-performance metal powders to industry-leading printing equipment and application development expertise. Our focus on accuracy, reliability, and innovation makes us a trusted partner for organizations looking to accelerate their digital manufacturing transformations in the EV sector and beyond. Embrace the future of manufacturing with metal 3D printing and unlock the full potential of your electric vehicle designs. https://met3dp.com/metal-3d-printing/
シェアする
MET3DP Technology Co., LTDは、中国青島に本社を置く積層造形ソリューションのリーディングプロバイダーです。弊社は3Dプリンティング装置と工業用途の高性能金属粉末を専門としています。