ガスタービン用粉末
目次
ジェットエンジンが轟音を立てて回転するそのパワーと効率に驚嘆したことはないだろうか。大陸を横断する飛行機を推進する容赦ない推力や、産業用ガスタービンの驚異的なエネルギー生成は、すべて綿密に設計された部品のシンフォニーのおかげである。しかし、これらの驚異的な機械には秘密の成分が隠されている: ガスタービンエンジニアリングパウダー.これらの微細な金属粒子は、エンジンの心臓部であるタービンのディスクやブレードを作る上で重要な役割を果たしている。
小さな金属宇宙を想像してみてください。ガスタービン・エンジニアリング・パウダーの粒子ひとつひとつは、ガスタービン内の過酷な環境に耐えられるよう特別に設計された、ミクロの戦士です。ここでは、灼熱の温度、莫大な圧力、容赦ない遠心力が組み合わさり、材料の戦場となります。そこで、特別に配合されたこれらのパウダーは、強度、耐熱性、耐疲労性のユニークな組み合わせを提供し、ガスタービン部品の聖なる三位一体となっています。
しかし、ガスタービンのエンジニアリング・パウダーは万能ではありません。熟練したシェフがどの料理にも同じスパイスを使わないように、エンジニアは様々なタイプの粉末を開発してきました。それでは、この魅力的な金属驚異の領域を掘り下げて探ってみよう。
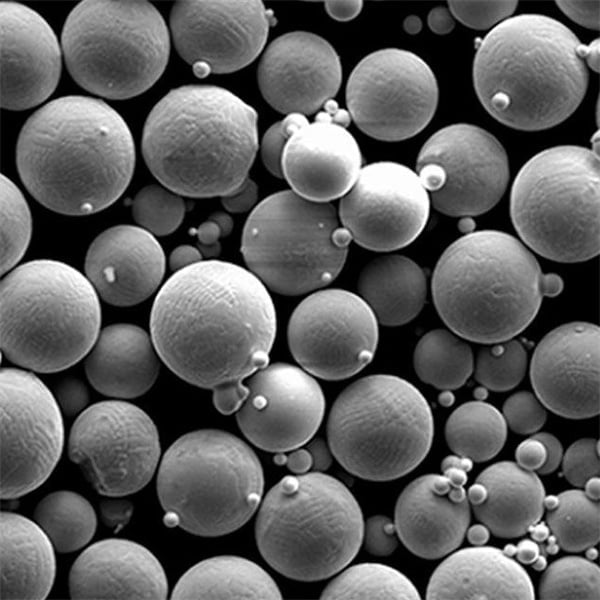
の特徴 ガスタービン用粉末
特徴 | 説明 |
---|---|
素材構成 | 主にニッケル基超合金だが、コバルトや鉄基合金も含むことがある。 |
粒子径と分布 | 充填密度と機械的特性を最適化するために注意深く制御される。通常10ミクロンから150ミクロンの範囲 |
形 | 圧密時に最適なフローとパッキングのための球状 |
流動性 | 積層造形プロセスにおいて重要な役割を果たします。パウダーはスムーズで安定したフローを実現するように設計されています。 |
純度 | 酸素、炭素、硫黄などの不純物の厳格な管理は、最適な性能を発揮するために不可欠である。 |
パワーハウス・パウダーのギャラリー
それでは、ガスタービンエンジニアリングパウダーの世界におけるキーパーソンを紹介しよう:
- IN718 強度、靭性、加工性の優れたバランスで知られる主力素材。様々なガスタービン用途に対応できる万能選手です。
- ルネ41 この高性能合金は、高温での優れた耐クリープ性を誇り、タービンの高温部に最適です。この合金は、灼熱に耐える耐火ファイターのようなものです。
- CMS 247LC このニッケル基超合金は、酸化と高温腐食に対して卓越した耐性を発揮する。高温ガスの容赦ない攻撃から身を守る盾のような存在です。
- 3月-M 247 この強力な素材は、非常に高温で高い強度と耐クリープ性が要求される用途で輝きを放ちます。最も過酷な環境でも活躍する究極のグラディエーターです。
- 午前16時24分: 比較的新しいこの先進的な合金は、3Dプリンティングのような積層造形プロセス用に特別に設計されている。技術に精通した戦士が、最新技術を駆使してパフォーマンスを競い合う姿を想像してみてほしい。
- アストロロイ このコバルト基超合金は、卓越した高温強度と耐酸化性を提供します。極限環境におけるチャンピオンとして、可能性の限界に挑みます。
- DZ 125 この鉄基超合金は、究極の性能が唯一の優先事項ではない用途に、費用対効果の高い選択肢を提供します。価値と性能のバランスの取れた戦略的超合金です。
- SRene 10X: このニッケル基超合金は、低サイクル疲労に対する卓越した耐性を誇り、繰り返し応力サイクルを経験する部品に理想的です。絶え間ない負荷に耐える、疲れ知らずの戦士を想像してみてください。
- PWA 1430 この先進的な合金は、優れた耐クリープ性と高温強度を備えている。材料科学の最新の進歩を備えた最先端の兵士を想像してみてください。
- ルネN5 このニッケル基超合金は、熱疲労やクリープに対する優れた耐性で知られている。様々な温度条件下で優れた性能を発揮する、適応力のある戦士と考えてください。
ガスタービンエンジニアリング粉末の利点
メリット | 説明 | ベネフィット |
---|---|---|
強化された素材特性 | ガスタービンエンジニアリングパウダーは、ガスアトマイズのような綿密に制御されたプロセスによって製造され、非常に優れた純度、粒度分布、球状の形態を持つパウダーを生み出します。これらの精密に設計された粉末は、従来の鋳造部品と比較して、優れた強度、耐クリープ性、耐疲労性、高温性能を持つ部品を製造するために使用することができます。 | これは、ガスタービンエンジンの効率と耐久性の向上につながる。より強い部品は、より高い運転温度と圧力に耐えることができ、燃料効率と出力の向上につながります。さらに、耐クリープ性が向上することで、部品交換が必要になるまでの耐用年数が長くなり、メンテナンスコストの削減にもつながります。 |
デザインの柔軟性 | 3Dプリンティングとしても知られる積層造形(AM)のような粉末ベースの製造技術は、ガスタービン設計の新たな可能性を解き放ちます。金型形状に制限される従来の鋳造法とは異なり、AMでは複雑な内部形状や複雑な格子構造を作成できます。この設計の自由度により、エンジニアは燃費向上のために部品の重量を最適化し、熱管理の改善のために優れた冷却チャネルを持つ部品を作成することができます。 | この柔軟性がガスタービン設計の革新を促進し、性能と効率の限界を押し広げます。コンポーネントを最適化することで、航空機用エンジンの軽量化や、産業用発電のためのコンパクトな設計が可能になります。 |
素材利用 | パウダーベースの製造工程は、従来の鋳造技術に比べて材料の無駄が最小限であることが自慢です。鋳造では、ゲーティングとスプルー除去の工程で材料が大量に失われる。逆にAMでは、未使用のパウダーをリサイクルして再利用できるため、材料の無駄と製造コストを最小限に抑えることができます。 | この利点は、ガスタービン製造における持続可能性を促進する。材料消費量の削減は環境負荷の低減につながり、環境に優しい産業慣行に対する需要の高まりに沿うものです。 |
リードタイムの短縮 | 積層造形は、複雑なガスタービン部品の製造において、リードタイムの点で大きな利点をもたらします。AMでは複雑な金型を作成する必要がないため、従来の鋳造法に比べて納期を短縮できます。この迅速なプロトタイピング能力は、新しいガスタービン設計を効率的に開発・試験するために不可欠です。 | これは、開発サイクルの短縮と、ガスタービンの新技術や改良技術の市場投入までの時間の短縮につながります。この俊敏性は、迅速な技術革新が重要な航空宇宙産業にとって特に有益です。 |
オーダーメイドの素材特性 | 粉末冶金技術は、ガスタービン用途に特化した特性を持つ新しい材料の創出を可能にします。粉末粒子内の元素の組成と分布を精密に制御することで、技術者は強度、延性、耐酸化性を最適に組み合わせた材料を作ることができます。 | このような材料設計への的を絞ったアプローチにより、より高い動作温度と圧力という増え続ける要求に耐えうるガスタービン部品の開発が可能になります。さらに、従来の鋳造法では実現できないような新しい材料の組み合わせを探求する道も開けます。 |
コンフォーマル冷却 | 積層造形では、ガスタービン部品内に複雑な内部冷却流路を形成することができます。これらの流路は、コンポーネントの正確な形状に合わせて設計することができ、最適な熱伝達を確保し、熱勾配を低減します。この精密な冷却戦略により、ホットスポットや熱歪みのリスクが最小限に抑えられ、コンポーネントの性能と寿命が向上します。 | これは、ガスタービンの効率的な運転と信頼性の高い性能につながります。部品の温度を低温に保つことで、材料の劣化や部品の故障のリスクを最小限に抑えることができます。 |
軽量化 | AMが提供する設計の自由度により、内部格子構造を持つより軽量なガスタービン部品の作成が可能になる。これらの複雑な構造は、航空機用ガスタービンにとって極めて重要な要素である重量を最小限に抑えながら、必要な強度を提供します。部品の軽量化は、燃料効率の向上と航空機の航続距離の延長につながります。 | この利点は航空宇宙産業にとって特に重要で、1キログラム節約するごとに大幅な燃料節約とペイロード容量の増加につながる。軽量で高性能な部品を作ることができるのは、ガスタービン用エンジニアリング・パウダーの大きな利点です。 |
のデメリット ガスタービン用粉末
デメリット | 説明 | インパクト |
---|---|---|
高粉体コスト | ガスタービン・エンジニアリング・パウダーは、ガスアトマイズのような複雑でエネルギー集約的なプロセスで製造されることが多い。このため、錬合金のような従来型の材料に比べてキログラムあたりのコストが高くなります。さらに、これらの粉末には厳しい品質管理が要求されるため、割高な価格設定となっています。 | 粉末のコストが高いと、ガスタービン部品の全体的な製造コストが大幅に上昇する可能性がある。これは、特に発電産業におけるコスト重視の用途において、普及の大きな障害となる可能性がある。 |
プロセスの複雑さ | ガスタービン用エンジニアリングパウダーの主な加工技術である積層造形は、従来の鋳造法に比べて比較的新しい技術です。設計の自由度が高い一方で、AMプロセスは複雑な場合があり、効果的に運用するには専門的な知識が必要です。粉末の選択、レーザーパラメータの最適化、後処理技術などの要素はすべて、造形の成功に重要な役割を果たします。 | AMプロセスの複雑さは、特にこの技術の経験が不足している製造業者に課題をもたらす可能性がある。不適切なプロセス制御は、最終的なコンポーネントの気孔、機械的特性の低下、寸法の不正確さなどの欠陥につながる可能性があります。 |
限られたサイズ | 現在のAMマシンでは、製造できる部品のサイズに限界がある。大規模なAMマシンは開発中ですが、まだ普及していません。このため、ガスタービンエンジニアリング用粉末をガスタービンエンジン内の小型部品に適用するには限界がある。 | この制限は、タービン・ディスクや燃焼器ライナーのような大型ガスタービン部品の製造にAMを使用する際の障壁となる可能性がある。そのため、これらの大型で重要な部品については、従来の鋳造法に頼る必要がある。 |
パウダーハンドリング | ガスタービンエンジニアリング粉末は、しばしば水分や酸素の影響を受けやすい。これらの汚染物質は、AMプロセス中の粉末の流動性に悪影響を及ぼし、最終コンポーネント内に酸化物のような欠陥の形成につながる可能性があります。パウダーの品質を維持し汚染を防ぐには、厳格な取り扱い手順と管理された環境が必要です。 | 綿密な取り扱いが要求されるため、製造プロセス全体が複雑化し、コストがかさむ可能性がある。粉体の適切な保管と取り扱いを確実にするために、不活性ガス封入装置や除湿機のような特殊な装置が必要になる場合もある。 |
パート資格 | ガスタービン部品は、厳格な安全・性能規制の対象となる。AMは比較的新しい技術であるため、AMで製造されたコンポーネントをガスタービンで使用するための認定は、困難で時間のかかるプロセスです。AMで製造された部品が、規制機関が要求する厳しい性能と安全基準を満たしていることを証明するには、多くの場合、広範な試験と特性評価が必要です。 | 長い認定プロセスが、ガスタービン・アプリケーションへのAMの採用を妨げる可能性がある。メーカーは、部品認定に伴う不確実性と潜在的な遅れのために、この技術への投資をためらうかもしれない。 |
表面粗さ | AMで製造された部品は、従来の鋳造部品に比べて特徴的な表面粗さを示すことがある。この表面粗さは空力性能に影響を与え、高応力領域での疲労亀裂発生のリスクを高める可能性がある。表面仕上げを改善するために機械加工や研磨のような後処理技術を採用することができますが、これらは製造工程に新たな工程とコストを追加することになります。 | AMコンポーネントの固有の表面粗さは、特定のガスタービン用途、特にコンプレッサーブレードのような空気力学的要求が高い用途では不利になる可能性があります。表面粗さがコンポーネントの性能に与える影響を慎重に考慮することは、設計段階において極めて重要です。 |
限られた材料しか入手できない | ガスタービン・エンジニアリング・パウダーとして現在利用可能な材料の範囲は、従来の製造に使用される錬合金の膨大な選択肢に比べると、まだ開発途上である。このように材料の選択肢が限られているため、特定の用途向けに部品の性能を最適化しようとする技術者にとって、設計の選択肢が制限される可能性があります。 | ガスタービンの性能の限界を押し広げるためには、材料の選択に制約があることが課題となります。極端な運転条件に合わせて特性を調整した新しい粉末組成物の開発は、現在進行中の研究分野である。 |
ガスタービン・エンジニアリング・パウダーの用途
申し込み | 説明 | ベネフィット |
---|---|---|
タービンブレード | タービンブレードの複雑な形状、特に高圧セクションの形状は、ガスタービンエンジニアリングパウダーを使ったAMで容易に製造できる。これらの複雑な内部冷却流路は、熱伝達を最適化し、ブレードの効率を向上させます。さらに、AMはブレードとディスクを単一ユニットとして製造するブリスク設計を可能にし、軽量化と組み立ての簡素化を実現します。 | これは、ガスタービンエンジンの効率と性能の向上につながります。最適化された冷却チャンネルは、ブレード内の熱勾配を最小限に抑え、ホットスポットや熱歪みのリスクを低減します。さらに、ブリスクの設計は軽量化の利点があり、特に航空機用ガスタービンには不可欠です。 |
燃焼器ライナー | AMで複雑な内部形状を作成できることから、ガスタービンエンジニアリング粉末は燃焼器ライナーに適している。これらのライナーは、燃焼器内の燃料混合と火炎安定化において重要な役割を果たします。AMは、燃料と空気の効率的な混合を促進し、汚染物質の排出を最小限に抑える複雑なスワラーとフレームホルダーの設計を可能にします。 | これにより、ガスタービン内の燃焼をよりクリーンで効率的なものにします。スワラーとフレームホルダーの形状を正確に制御することで、燃料と空気の混合を最適化し、燃焼効率の向上とNOxなどの汚染物質の排出削減につながります。 |
熱交換器 | ガスタービンエンジニアリングパウダーが提供する高温性能と設計の柔軟性は、ガスタービン内の熱交換器用途に理想的です。AMは、伝熱面積を最大化する複雑な内部形状を持つ高効率の熱交換器の作成を可能にします。このような高度な熱交換器は、ガスタービンサイクルの全体的な熱効率を向上させることができます。 | これは、ガスタービンの出力向上と燃料節約につながります。熱交換器内に複雑な内部流路を形成できるため、熱伝達が最適化され、サイクル効率の向上と燃料消費量の削減につながります。 |
軽量コンポーネント | AMが提供する設計の自由度は、一部のガスタービンエンジニアリングパウダーの高い強度対重量比と相まって、ガスタービン用の軽量コンポーネントの製造を可能にする。これは特に航空機のガスタービンエンジンにとって有益で、軽量化は燃料効率の向上と航続距離の延長に直結します。コンプレッサーのハウジングや構造用ブラケットなどのコンポーネントは、AMを使用して強度と重量の両方を最適化することができます。 | これは、ガスタービンエンジンを搭載した航空機の大幅な燃料節約と航続距離の延長に貢献する。軽量で高性能な部品を製造できることは、航空機用途にとって大きな利点である。 |
先進の冷却設計 | ガスタービンエンジニアリングパウダーは、ガスタービン部品内に高度な冷却流路を形成することを可能にします。これらの流路は、部品の正確な形状に適合させることができ、最適な熱伝達を確保し、熱勾配を低減します。これにより、ガスタービンの高温・高圧運転が可能になり、全体的な効率と出力が向上します。 | これにより、ガスタービンの性能の限界が押し広げられる。効率的な冷却戦略を可能にすることで、AMはより高い運転温度に耐えられる高度な材料の使用を容易にし、効率と出力の向上につながる。 |
ラピッドプロトタイピング | ガスタービンエンジニアリングパウダーを使用したAMは、設計を迅速に反復できるため、ガスタービンコンポーネントのラピッドプロトタイピングのための貴重なツールとなります。これにより、エンジニアは大規模な生産に着手する前に、新しい設計を迅速にテストして改良することができます。この迅速な開発サイクルにより、ガスタービン技術の革新が加速されます。 | これにより、開発期間が短縮され、新しいガスタービン技術を市場に投入する際のコストが削減されます。新しい設計を素早く試作しテストする能力は、急速に進化する業界で一歩先を行くために極めて重要です。 |
重要部品の修理 | ガスタービンエンジニアリングパウダーは、重要なガスタービン部品の補修に使用できます。AMでは、局所的に材料を堆積させることで、損傷した部分を修復したり、浸食された表面を埋めたりすることができます。これにより、コンポーネントを完全に交換する必要性を最小限に抑え、ダウンタイムとメンテナンスコストを削減します。 | これにより、ガスタービン事業者の稼働時間の向上とメンテナンスコストの削減に貢献します。重要部品の修理が可能なため、耐用年数が延び、高価な交換の必要性がなくなります。 |
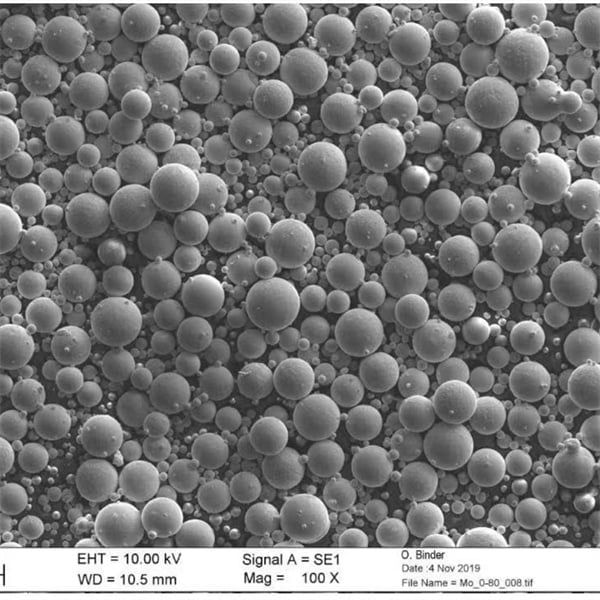
代表的な仕様、サイズ、等級、規格:
特徴 | 説明 |
---|---|
素材構成 | 粉末の種類によって異なる。化学組成は通常、関連規格に概説された厳格な仕様に従って管理される。 |
粒子径と分布 | 通常、10~150ミクロンの範囲であり、特定の範囲は用途と希望する特性によって異なる。粒度分布は、最適な充填密度になるように注意深く制御されます。 |
形 | 圧密工程で最適な流動性とパッキングを実現する球状。 |
流動性 | 積層造形プロセスにおける一貫したスムーズなパウダーフローを保証するために、標準化された試験を用いて測定される。 |
純度 | 酸素、炭素、硫黄などの不純物を厳しく管理することは、最適な性能を発揮するために不可欠である。規制値は関連規格によって定められています。 |
グレード | 特定の合金や製造業者によって、さまざまな粉末等級が利用できる場合がある。これらのグレードは、微量元素の組成や処理パラメーターが異なる場合があります。 |
規格 | ガスタービン・エンジニアリング・パウダーは通常、ASTMインターナショナル(ASTM)やAMSインターナショナル(AMS)などの組織が定めた業界標準に準拠しています。これらの規格は、材料組成、粒子径、その他の重要なパラメータの仕様を定義しています。 |
サプライヤーと価格詳細
インフォメーション | 説明 | 考察 |
---|---|---|
サプライヤー風景 | ガスタービンエンジニアリングパウダーの市場は比較的集中しており、大手企業は限られている。これらの企業は、ガスタービン業界の厳しい要件を満たす高品質の粉末を製造するのに必要な専門知識とインフラを有している。 | 生産工程が複雑で厳格な品質管理が必要なため、新規サプライヤーにとっては参入障壁が高い。これは競争を制限し、価格設定に影響を与える可能性がある。 |
主要サプライヤーの例 | ガスタービンエンジニアリングパウダーの著名なサプライヤーには、以下のようなものがある: | * APEX Powder Company(米国) * Höganäs AB(スウェーデン) * AMETEK SMP(米国) |
価格決定要因 | ガスタービン・エンジニアリング・パウダーの価格は、以下のようないくつかの要因に影響される: | * パウダー素材: エキゾチックな高性能合金は、一般的なニッケル基超合金に比べ、割高になるのが普通です。* パウダーの純度: 純度の高いパウダーは、厳しい品質管理が要求されるため、高値で取引される。* 粒子径と形態: 粒子径がより細かく球状の形態を持つパウダーは、一般的に製造コストが高くなり、コストも高くなる可能性がある。* 注文数量: 大量注文の場合、サプライヤーによっては割引価格が適用される場合があります。 |
その他の考慮事項 | ガスタービン・エンジニアリング・パウダーをAMに使用する場合、パウダーの基本価格以外にも考慮すべきコストがある: | * 最小注文数量: サプライヤーによっては、小規模なプロジェクトやプロトタイピング用途にはハードルとなる最小注文数量を設定している場合があります。* 後処理費用: AMで製造されたガスタービン部品は、熱処理、サポート除去、表面仕上げなどの後処理工程が必要な場合があり、これが製造コスト全体を押し上げる。 |
市場動向 | ガスタービンエンジニアリングパウダー市場は、以下のような要因によって、今後数年間で成長すると予想されている: | * 発電用および航空機推進用のより効率的で強力なガスタービンの需要の増加。* ガスタービン部品の設計の可能性を広げるAM技術の進歩。* 燃料効率と航続距離を向上させるため、航空機の軽量化に注目が集まっている。 |
費用について
ガスタービンエンジニアリングパウダーの具体的な価格情報は、商業上の機密性が高いため、公開されていないことが多いことに注意することが重要です。しかし、これらの粉末は一般的に、従来の選択肢と比較して高価値の材料と考えられています。しかし、そのコストは、性能、設計の柔軟性、材料の利用という点で得られる潜在的なメリットと比較検討する必要があります。
パウダーベースと従来の製造方法の比較
ガスタービン部品の製造に関しては、鋳造や固形ブロックからの機械加工といった伝統的な方法が数十年にわたって主力となってきた。しかし、粉末ベースの技術は、いくつかの利点があるため、大きな支持を集めている:
- 優れた素材特性: 先に述べたように、粉末冶金技術は、従来の鋳造法に比べて優れた強度、耐疲労性、耐クリープ性を達成することができる。これはガスタービンの効率向上と寿命延長につながる。
- 設計の柔軟性: 粉末ベースの積層造形では、従来の機械加工では困難または不可能な複雑な形状を作り出すことができる。これにより、内部冷却チャンネルを備えたコンポーネントや軽量構造など、革新的でより効率的なタービン設計への扉が開かれます。
- 素材利用の改善: パウダーベースのプロセスは、固形ブロックからの機械加工のような従来の方法と比較して、材料の無駄を最小限に抑えることができます。これはコスト削減と環境への影響の低減につながります。
- ニア・ネットシェイプ・マニュファクチャリング: 粉末ベースの積層造形技術は、従来の方法と比較して後処理を最小限に抑え、ニアネットシェイプのコンポーネントを作成することができます。これは、生産時間の短縮とコストの削減につながります。
しかし、伝統的な方法にもそれなりの利点がある:
- 初期費用の削減: 従来の製造プロセスを立ち上げるには、通常、粉末ベースの積層造形装置に比べて初期投資が少なくて済む。
- 確立されたプロセス: 伝統的な製法は何十年も続いており、そのプロセスは確立され、理解されている。そのため、大量生産が可能になり、大量生産部品の製造コストが下がる可能性がある。
- より幅広い素材オプション: 従来の方法は、粉末ベースの方法に比べて、より幅広い種類の材料を扱うことができる。
パウダーベースと従来の製造方法のどちらを選択するかは、以下のようないくつかの要因によって決まる:
- 製造される特定の部品: 複雑な形状や、優れた材料特性を必要とする部品には、粉末を使用する方法が望ましいかもしれない。
- 生産量: 大量生産の場合は、従来の方法の方が費用対効果が高いかもしれない。
- 材料の入手可能性: 特定の合金が粉末状で容易に入手できない場合、伝統的な方法が唯一の選択肢になるかもしれない。
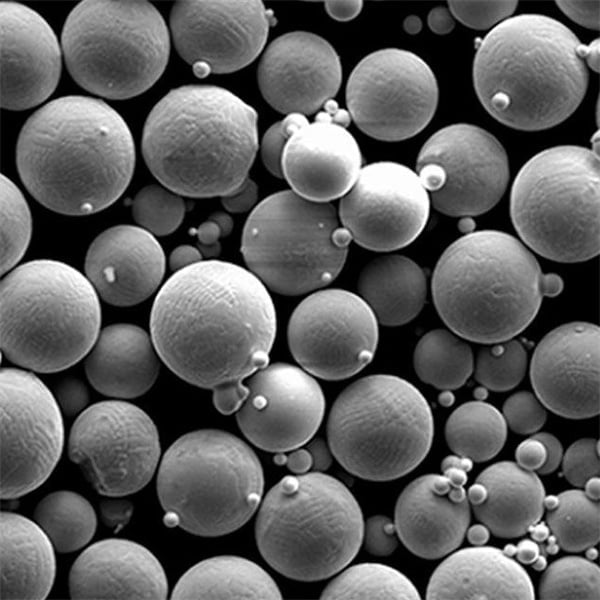
ガスタービン・エンジニアリング・パウダーの未来
ガスタービン用エンジニアリングパウダーの未来は明るい。アディティブ・マニュファクチャリング技術が進歩し続けるにつれて、これらの特殊粉末の需要は伸びると予想されます。注目すべきエキサイティングなトレンドをいくつか紹介しよう:
- 新しい粉末合金の開発: 研究者たちは、ガスタービンのさらなる高効率化と運転温度の向上を目指して、より優れた性能特性を持つ新しい粉末合金の開発に余念がない。
- 粉末製造法の改善: 粉末製造技術の進歩により、高品質のガスタービン・エンジニアリング・パウダーを製造するための、より費用対効果の高い効率的な方法が確立されつつある。
- 粉体仕様の標準化: ガスタービン用エンジニアリングパウダーの使用が普及するにつれ、パウダーの仕様と認証の標準化が進み、一貫した品質と性能が保証されるようになる。
よくあるご質問
質問 | 答え |
---|---|
ガスタービン・エンジニアリング・パウダーを使用する主な利点は何ですか? | ガスタービン・エンジニアリング・パウダーには、材料特性の向上、設計の柔軟性、材料利用の改善、微細構造の制御など、いくつかの利点があります。 |
ガスタービン・エンジニアリング・パウダーを使用するデメリットは何ですか? | 欠点としては、従来の材料に比べてコストが高いこと、工程が複雑であること、厳格な品質管理が必要であることなどが挙げられる。 |
ガスタービン・エンジニアリング・パウダーの典型的な用途は? | これらの粉末は、主にタービン・ディスクやブレード、燃焼器ライナー、ノズル・ガイドベーン、ヒートシールドの製造に使用され、最近では積層造形によってさまざまな航空宇宙、自動車、医療用途に使用されるようになっている。 |
ガスタービン・エンジニアリング・パウダーの価格設定に影響を与える要因は何ですか? | 材料の組成、粒度分布、数量、特定の規格への準拠はすべて、価格設定に影響を与える可能性がある。 |
粉体を使った製造方法は、ガスタービン部品の従来の製造方法と比べてどうなのか? | 粉末ベースの方法は、優れた材料特性、設計の柔軟性、材料利用率の向上を提供するが、初期費用が高く、工程が複雑になる。従来の方法は、より確立されたものであり、より幅広い材料オプションがあるが、設計の複雑さに制限があり、より多くの廃棄物が発生する可能性がある。 |
結論として、ガスタービン・エンジニアリング・パウダーは、ガスタービンの世界で変革的な役割を果たしている。これらの微細な驚異は、性能と効率の限界を押し広げるユニークな特性の組み合わせを提供する。技術が進化し続けるにつれて、このような特殊な粉末の領域でさらにエキサイティングな開発が行われ、よりクリーンで強力かつ効率的なガスタービンの未来への道が開かれることが期待される。
シェアする
MET3DP Technology Co., LTDは、中国青島に本社を置く積層造形ソリューションのリーディングプロバイダーです。弊社は3Dプリンティング装置と工業用途の高性能金属粉末を専門としています。
関連記事
Met3DPについて
最新情報
製品
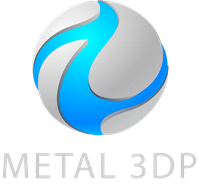
3Dプリンティングと積層造形用金属粉末