インコネル3Dプリンティング:利点、種類、用途
目次
インコネル3Dプリンティングの概要
インコネル3Dプリンティングインコネル合金による積層造形とも呼ばれ、3Dプリンティング技術を用いてインコネル金属粉末から部品を製造することを指す。インコネルは、高強度、耐食性、耐熱性で知られるニッケル・クロム基超合金の一種です。インコネル3Dプリンティングの主な特徴は以下の通り:
- 従来の製造では不可能だった複雑で軽量な形状の製造が可能
- 溶製インコネル部品に匹敵する優れた機械的特性と材料性能
- 金型や特別な工具を必要とせず、オンデマンドで部品を印刷できる。
- 小ロット生産におけるリードタイムとコストの削減
- トポロジー最適化によって最適化された形状やデザインを作成する能力
- インコネル3Dプリンティングパーツを使用する幅広い産業には、航空宇宙、自動車、石油・ガス、医療、化学処理などがあります。
インコネル3Dプリントの利点と制限をいくつか挙げてみましょう:
インコネル3Dプリンティングの利点
- 複雑な形状と軽量構造
- カスタマイズされた最適化されたデザイン
- 廃棄物の削減 - 必要な量の材料のみを使用
- リードタイムの短縮、小ロットのコスト削減
- デザインの変更や反復が容易
- アセンブリの統合と部品点数の削減
- 最小発注量なしで部品をオンデマンド購入
インコネル3Dプリンティングの限界
- 大量生産によるコスト上昇
- ステンレス鋼のような他の金属よりも製造速度が遅い。
- ご希望の表面仕上げを得るために、後加工が必要になる場合があります。
- 異方性材料特性
- 規制産業における資格および認証要件
- 3Dプリンティング用インコネル合金グレードの数は限られている
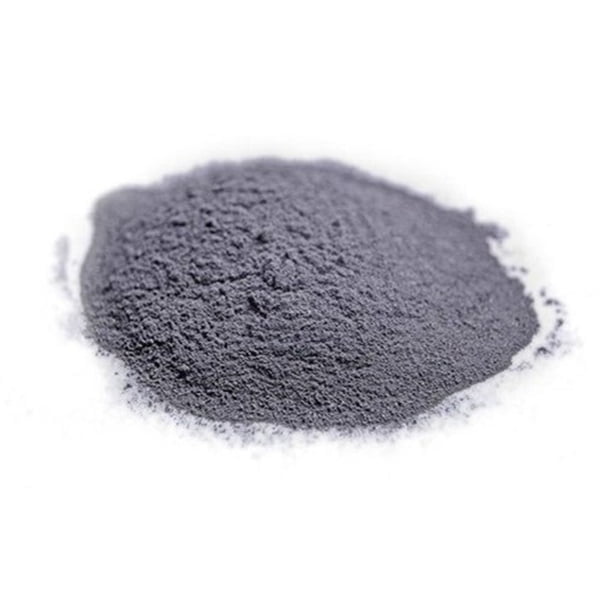
3Dプリンティングに使用されるインコネル合金の種類
いくつかのインコネル超合金グレードが3Dプリンティングプロセス用に開発されています。最も一般的に使用されているインコネル合金は以下の通りです:
インコネル合金 | 主な特徴 |
---|---|
インコネル718 | 700℃までの優れた強度と耐食性。航空宇宙部品に最適。 |
インコネル625 | 優れた耐食性、良好な溶接性、980℃までの強度。化学処理、海洋用途に使用される。 |
インコネル825 | 耐酸化性、耐食性に優れる。石油・ガス部品、発電所に使用される。 |
インコネル939 | 1095℃まで安定した高強度ニッケル合金。ガスタービンエンジン部品に使用される。 |
3Dプリンティングが可能なその他のインコネル合金:
- インコネル X-750
- インコネル909
- インコネル939ER
インコネル3Dプリンティングプロセス
インコネル超合金の印刷には、いくつかの付加製造プロセスが使用されている:
プロセス | 仕組み | メリット | 制限事項 |
---|---|---|---|
パウダーベッドフュージョン - レーザー | レーザーが粉体層を選択的に溶かす | 良好な精度、表面仕上げ | 比較的遅い |
パウダーベッド核融合 - 電子ビーム | 電子ビームが粉末層を溶かす | レーザーより速い造形速度 | 真空チャンバーの要件 |
指向性エネルギー蒸着(DED) | 集束された熱エネルギー源が、成膜中に金属粉末やワイヤー原料を溶かす | 材料の追加による部品の補修やコーティングが可能 | 表面仕上げが粗く、後処理が必要 |
バインダー・ジェット | 液体結合剤が粉末粒子を選択的に結合します | 比較的速く、低コスト | 密度と強度が低く、浸透が必要 |
主要なプロセスパラメータ: レーザー出力、スキャン速度、ハッチ間隔、層厚、造形方向、支持構造、予熱温度、後処理工程。望ましい特性を得るためには、インコネル合金ごとにプロセス・パラメーターを最適化する必要がある。
インコネル3Dプリンティングの用途
積層造形インコネル部品を使用する主な産業とその用途:
産業 | 代表的なアプリケーション |
---|---|
航空宇宙 | タービンブレード、インペラ、燃焼器ライナー、バルブ、ハウジング、ブラケット |
石油・ガス | ダウンホールツール、バルブ、坑口部品、配管継手 |
発電 | 熱交換器、タービンブレード、ケーシング、ファスナー |
自動車 | ターボチャージャーハウジング、エンジンバルブ、排気部品 |
化学処理 | プロセス容器内部、熱交換器部品、バルブ、ポンプ |
メディカル | 歯科インプラント、補綴物、外科器具 |
3Dプリンティングのユニークな機能は、最適化された形状と設計で複雑なインコネル部品を製造するのに適しています。部品の軽量化も可能です。
インコネル3Dプリント部品の仕様
インコネル3Dプリント部品に考慮すべき重要なパラメータと仕様:
パラメータ | 代表的な範囲/値 |
---|---|
寸法精度 | ± 0.1~0.2%または±50μm |
表面粗さ(Ra) | 印刷時:8~15μm <br> 後処理済み:1-4 μm |
多孔性 | レーザーPBF用0.5-2% <br> 5-10% 浸透前のバインダー噴射用 |
壁厚 | 最小0.3~0.5mm |
機械的特性 | 鍛造材の15%以内の強度 <br> 伸び 10-35% |
使用温度 | インコネル718の場合、最高700°C <br> インコネル939の1000℃以上 |
インコネル3Dプリンティングのための重要な設計原則:
- 自立機能の最小肉厚
- 45度以上の傾斜面にはサポートが必要な場合があります。
- 複雑な形状に推奨される余裕のあるフィレット半径
インコネル印刷部品の後処理方法
インコネル部品の一般的な後処理工程:
- ビルドプレートからの取り外し: 切断、ワイヤーEDM
- サポート解除: 機械的除去、熱応力緩和、化学溶解
- ストレス解消になる: 残留応力を除去するため、溶体化温度以下で熱処理を行う。
- 表面仕上げ: 機械加工、研削、研磨、研磨フロー加工、振動仕上げ
- 熱間静水圧プレス(HIP): 熱と静水圧を加えて内部の空隙を塞ぎ、材料特性を向上させる。
後加工は、最終部品の品質と性能を向上させるために非常に重要です。使用される方法は、アプリケーションの要件によって異なります。
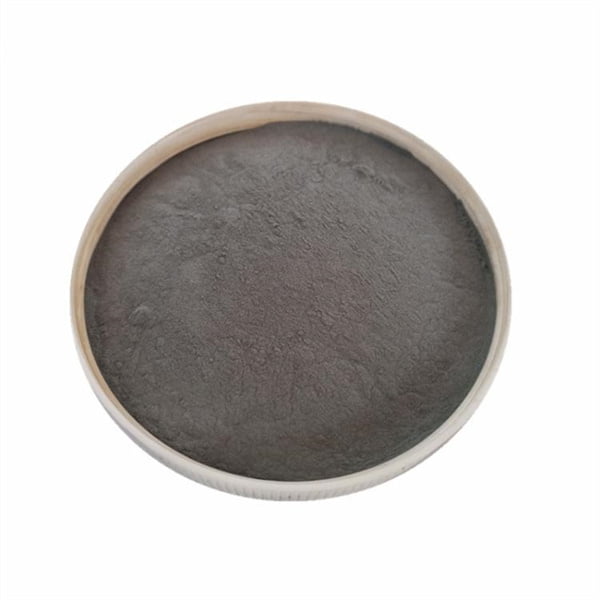
設計原則と推奨事項
インコネル3Dプリント部品を最適化するための主な設計推奨事項:
- 支柱を必要とする張り出しを最小限に抑える
- 支持構造を減らすために部品の向きを変える
- 変形しやすい薄い突起物は避ける
- 応力を緩和するために、余裕のある内部半径を使用する。
- 熱膨張を考慮した設計 - インコネルの熱膨張係数は13 x 10-6 m/m°C。
- 造形方向に基づく異方性材料特性の考慮
- 適切なデータム、公差、後処理用の表面仕上げを設計する。
- 印刷前にCAEツールで造形と熱応力をシミュレーション
トポロジーの最適化を行い、3Dプリント専用にパーツを再設計することで、軽量化、性能向上、コスト削減の面で最大のメリットが得られます。
インコネル3Dプリントサービスのサプライヤー
多くのサービスビューローが、さまざまなプロセスを使用したインコネル3Dプリントサービスを提供しています:
会社概要 | プロセス | インコネル | 対象業界 |
---|---|---|---|
マテリアライズ | レーザーPBF、バインダージェッティング | 718, 625, 800 | 航空宇宙、自動車、一般産業 |
3Dシステムズ | レーザーPBF、DED | 718, 625, 939 | 石油・ガス、航空宇宙、自動車 |
GEアディティブ | レーザーPBF、バインダージェッティング | 718, 625, 800H, 939 | 航空宇宙、石油・ガス、発電 |
ヴォスタルピン | レーザーPBF、DED | 718, 625, 800H | 航空宇宙、石油・ガス、自動車 |
ホーガナス | バインダー・ジェット | 718, 625 | 航空宇宙、自動車、一般産業 |
EOS、Velo3D、SLM Solutions、Renishaw、AddUpなど、多くのプリンターOEMもインコネル印刷サービスを提供しています。レーザーPBFプロセスとDEDプロセスの両方が一般的に利用可能です。
インコネル3Dプリンティングのコスト分析
プロセス | ビルド・レート | 部品サイズ | リードタイム | 部品単価 |
---|---|---|---|---|
レーザーPBF | 5~15cm3/時 | 50 cm3 | 1~2週間 | $250-$1000 |
体外式除細動器 | 25~100cm3/時 | 500 cm3 | 1週間 | $100-$500 |
バインダー・ジェット | 20~50cm3/時 | 1000 cm3 | 1週間 | $50-$200 |
費用についてはお問い合わせください:
- 部品サイズ、形状の複雑さ、生産量
- 材料費 - インコネル粉末は高価
- 設計、後処理工程の労力
- 資格および認定要件
試作品や少量生産の場合、インコネルを3Dプリントすることは、機械加工や鋳造に比べ、非常に費用対効果が高い。DEDは最も経済的なプロセスです。
インコネル3Dプリンティングのベンダーの選び方
インコネル3Dプリントサービスのベンダーを選択する際の主な考慮事項:
- 経験: インコネル合金の取扱年数、取扱業界、ケーススタディ
- 技術力: 提供されるプロセス、印刷されるインコネル・グレード、部品サイズ制限、二次加工
- 品質認証: ISO 9001、AS9100、Nadcap認証が品質管理を実証
- 検証を行う: 材料試験、工程検証、品質チェックの実施
- 後処理: 応力除去、熱間静水圧プレス、機械加工、仕上げサービス
- リードタイム 部品を迅速に納品する能力が不可欠
- クライアントのサポート: AMガイダンス、トポロジー最適化、印刷モニタリング、部品検査のための設計
- コストだ: 印刷費、材料費、人件費、ボリュームディスカウント、証明書
インコネル3Dプリンティングで本格的な生産を開始する前に、複数のベンダーに連絡し、能力を比較し、テストクーポンを要求してサプライヤーを認定します。
インコネル3Dプリンティングの長所と短所
メリット | デメリット |
---|---|
他のプロセスでは不可能な複雑な形状 | 比較的高いインコネル粉末の材料費 |
設計の軽量化と最適化 | 機械加工よりも寸法精度が低く、表面粗さが高い |
部品の統合とアセンブリの削減 | 適格なインコネル鋼種は限られている |
少量生産におけるリードタイムとコストの削減 | 目的の材料特性を得るためには、しばしば後処理が必要である。 |
材料の無駄を最小限に抑える | 異方性材料特性 |
オンデマンド製造、最小注文数量なし | 規制産業における資格および認証要件 |
設計の修正と反復が容易 | 熱応力により部品が歪むことがある。 |
製造業におけるインコネル3Dプリンティングの役割
インコネル3Dプリンティングが製造業で果たす主な役割:
- プロトタイプ製作: 設計検証用インコネル部品の迅速かつ低コストなプロトタイピング
- ブリッジ・ツーリング: プロトタイピングから本格的な製造に移行する際に、金型、固定具、治具を迅速に製作する。
- パーツの統合: 軽量化とコスト削減のためのアセンブリの再設計と部品の統合
- マス・カスタマイゼーション: お客様のご要望に合わせたインコネル部品の提供
- スペアパーツ: バッチ生産と在庫ではなく、必要に応じて交換部品を製造するオンデマンド生産
- サプライチェーンの柔軟性: 拠点間の生産シフトが容易になり、サプライチェーンの混乱が緩和される。
- 短距離走: 少量のインコネル部品を経済的に生産
付加製造のユニークな機能は、複雑なインコネル部品を製造するための従来の製造プロセスを補完する価値あるものです。
インコネル3Dプリンティングの未来
インコネル3Dプリンティングは、以下を原動力に今後数年間で大きく成長すると予想される:
- AMプロセスに最適化された新しいインコネル超合金の開発
- より高いレベルの自動化と再現性を備えた改良型プリンター
- 製造速度の高速化と生産スループットの向上
- 部品サイズの拡張
- AMとサブトラクティブ・プロセスを組み合わせたハイブリッド製造
- 支持構造の最適化を可能にするソフトウェアの強化
- 航空宇宙や医療など規制の厳しい分野での採用が増加
- 工具、金型、治具、固定具などの新興分野での用途
- 部品修理とアフターマーケット・サービスのためのAMの利用
技術がさらに成熟すれば、高性能の金属部品をオンデマンドで製造できるインコネル3Dプリンティングは、より多くの産業で主流になるだろう。
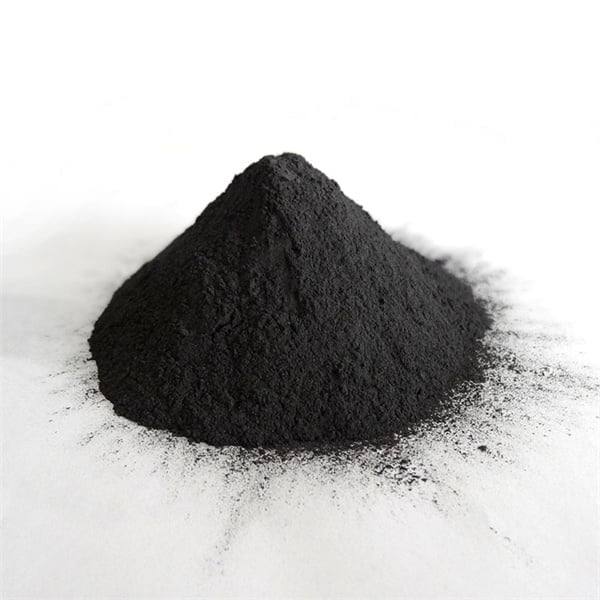
よくあるご質問
Q: 3Dプリンティングで使用されるインコネル合金にはどのような種類がありますか?
A: 3Dプリンティングで使用される最も一般的なインコネル合金は、インコネル718、625、800、939です。それぞれ異なる用途に適した耐熱性、耐食性、耐酸化性を持っています。
Q: 3Dプリントしたインコネルの機械的特性は、鍛造インコネル部品と比べてどうですか?
A: 最適化されたプロセス・パラメーターを使用した場合、3Dプリンティングされたインコネル部品は、溶製材の15%以内の引張強さを示します。しかし、破断伸びの延性は、溶製材の40~50%に対し、AMインコネル部品は10~35%と低い。
Q: インコネル3Dプリント部品にはどのような後処理が施されますか?
A: 一般的な後加工工程には、サポート除去、応力除去熱処理、熱間静水圧プレス(HIP)、機械加工、研削、研磨、その他の仕上げ加工が含まれます。これにより、表面仕上げ、寸法精度、材料特性を向上させることができます。
Q: インコネル3Dプリントには特別な設備やインフラが必要ですか?
A: インコネル合金の印刷には、不活性ガス・チャンバー、高出力レーザーまたは電子ビーム、真空システムを備えた特殊な粉末溶融または指向性エネルギー蒸着プリンターが必要です。また、微細なインコネル粉末の取り扱いには特別な注意と手順が必要です。
Q: インコネル3Dプリンターを使用している産業にはどのような例がありますか?
A: インコネル3Dプリントを使用する主な産業には、航空宇宙、石油・ガス、発電、化学処理、自動車、医療などがあります。タービンブレード、熱交換器部品、バルブ、人工装具などの部品は、一般的にインコネルで3Dプリントされます。
Q: 大きなインコネル部品を3Dプリントすることは可能ですか?
A: サイズの可能性は広がりつつありますが、ほとんどのインコネル3Dプリント・パーツの体積は現在1立方フィート以下です。非常に大きなパーツの場合、指向性エネルギー堆積法(DED)は、粉末床溶融プロセスよりも造形サイズの柔軟性があります。AMとサブトラクティブ・プロセスを組み合わせたハイブリッド製造も、より大きなインコネル部品を可能にします。
Q: インコネル3Dプリントには特別な設計上の配慮が必要ですか?
A: 重要な設計原則には、オーバーハングを最小限に抑えること、熱応力を許容すること、適切な公差と表面仕上げを使用すること、サポートが少なくなるように部品を最適な方向に配置することなどがあります。トポロジーを最適化し、AM用に再設計することで、最大のメリットが得られます。
Q: インコネル3Dプリントの主な利点は何ですか?
A: インコネル3Dプリンティングの主な利点は、鋳造や鍛造では不可能な複雑な形状を製造できること、少量生産のリードタイムとコストを削減できること、最適化された軽量設計、部品の統合、オンデマンド製造が可能なことです。
Q: インコネル3Dプリントのコストは、他の金属AMプロセスと比較してどうですか?
A: インコネル粉末は、ステンレス鋼やチタンなどの他の金属よりも高価です。困難なプリントパラメータと組み合わせることで、インコネル3Dプリントは、鋼やチタン合金のプリントに比べて、パーツあたりのコストが高くなります。
シェアする
MET3DP Technology Co., LTDは、中国青島に本社を置く積層造形ソリューションのリーディングプロバイダーです。弊社は3Dプリンティング装置と工業用途の高性能金属粉末を専門としています。
関連記事
Met3DPについて
最新情報
製品
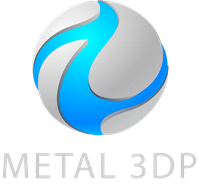
3Dプリンティングと積層造形用金属粉末