Jet Turbine Blade Roots: Revolutionizing Aerospace Manufacturing with Metal 3D Printing
目次
Introduction to Jet Turbine Blade Roots
Jet turbine blades stand as critical components within aircraft engines, enduring extreme conditions of temperature, pressure, and rotational forces. The root of these blades, the attachment point to the turbine disk, is paramount for ensuring the structural integrity and operational efficiency of the entire engine. Traditionally manufactured through subtractive methods, the production of these complex geometries often involves significant material waste and lengthy lead times. However, the advent of metal 3D printing, also known as metal additive manufacturing, presents a transformative approach to fabricating jet turbine blade roots with enhanced design freedom, reduced material usage, and faster production cycles. This blog post delves into the advantages of employing metal 3Dプリンティング for jet turbine blade roots, the recommended materials, design considerations, and how メタル3DP is at the forefront of this technological revolution, offering industry-leading solutions for aerospace and beyond.
What are Jet Turbine Blade Roots Used For?
The primary function of a jet turbine blade root is to securely fasten the airfoil of the turbine blade to the rotating turbine disk or rotor within a gas turbine engine. These roots must withstand immense centrifugal forces generated by the high rotational speeds, as well as thermal stresses arising from the extreme operating temperatures. The intricate design of the root, often featuring complex interlocking geometries such as fir-tree or dovetail shapes, ensures a robust mechanical connection that prevents blade detachment during operation. Beyond secure attachment, the root design also plays a crucial role in:
- Load Transfer: Efficiently distributing the operational loads from the airfoil to the turbine disk, minimizing stress concentrations.
- Vibration Damping: Contributing to the overall stability of the turbine assembly by damping vibrations.
- Sealing: In some designs, the root incorporates features that aid in sealing the gaps between adjacent blades, preventing hot gas leakage and maintaining engine efficiency.
- Cooling Integration: Providing pathways or features for integrating cooling channels that extend into the airfoil, crucial for managing the extreme temperatures.
These critical functions underscore the importance of precise manufacturing and the use of high-performance materials for jet turbine blade roots, making metal 3D printing an increasingly attractive alternative to conventional manufacturing methods.
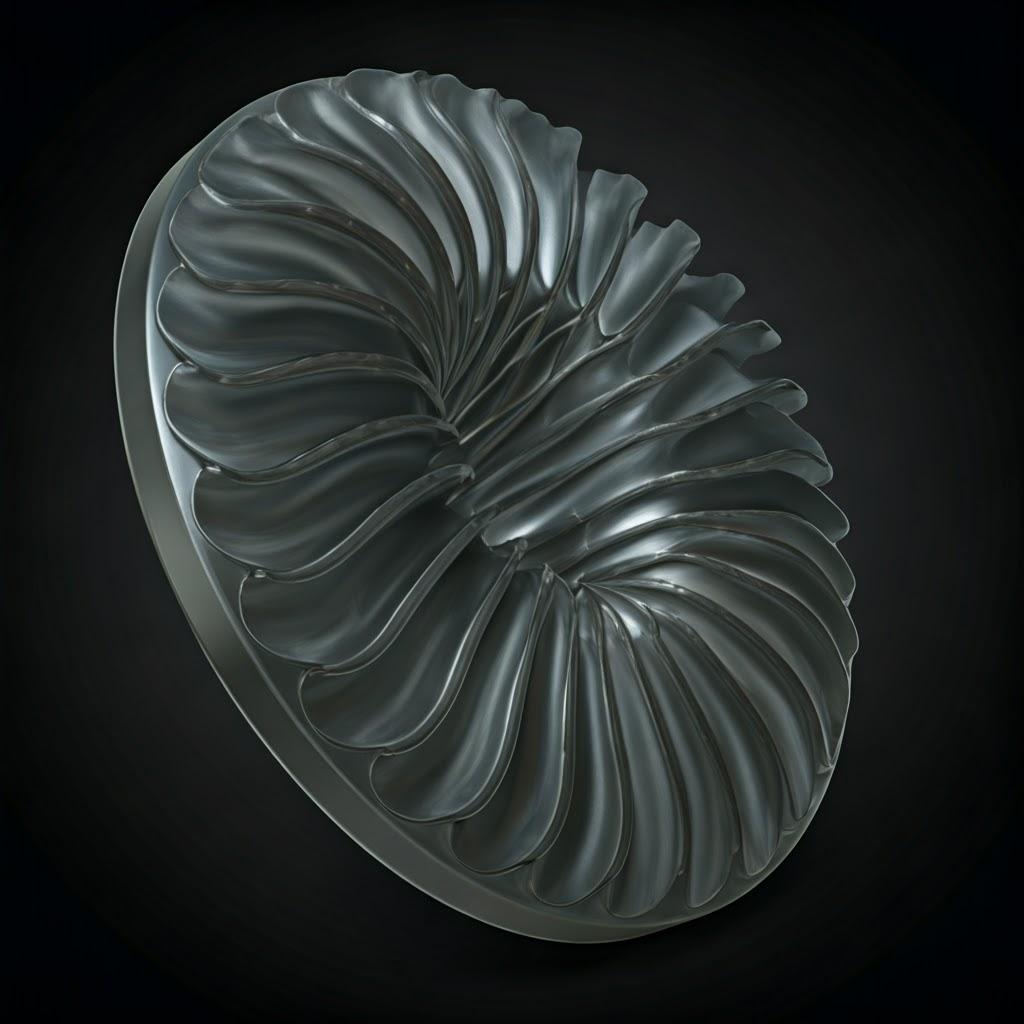
Why Use Metal 3D Printing for Jet Turbine Blade Roots?
Opting for metal 3D printing for the fabrication of jet turbine blade roots offers a multitude of compelling advantages over traditional manufacturing techniques like casting, forging, and machining:
- デザインの自由と複雑さ: Additive manufacturing अनलॉक्स unparalleled design freedom, enabling the creation of intricate root geometries that are optimized for stress distribution, weight reduction, and cooling integration. Features like internal cooling channels with complex lattices, which are difficult or impossible to achieve with conventional methods, can be readily incorporated.
- 材料効率: Metal 3D printing utilizes a layer-by-layer deposition process, significantly reducing material waste compared to subtractive methods where a substantial portion of the raw material is removed. This is particularly crucial when working with expensive, high-performance alloys commonly used in turbine applications.
- リードタイムの短縮: 3D printing can drastically shorten production lead times. The elimination of tooling requirements, such as molds and dies, and the ability to produce parts on-demand accelerate the manufacturing process from design to final component. メタル3DP‘s advanced printing technology further enhances this efficiency.
- Customization and Prototyping: Metal 3D printing is ideal for producing customized blade roots for specific engine designs or for rapid prototyping and iteration. Engineers can quickly modify designs and produce prototypes to test performance characteristics before committing to mass production.
- パフォーマンスの向上: By optimizing the root design through additive manufacturing, it’s possible to enhance the overall performance and lifespan of the turbine blades. Improved cooling designs can lead to lower operating temperatures and increased efficiency.
- 部品の統合: In some cases, metal 3D printing allows for the consolidation of multiple components into a single, integrated part, reducing the number of joints and fasteners, thereby improving reliability and potentially reducing weight.
メタル3DP‘s commitment to innovation in metal additive manufacturing positions us as a trusted partner for aerospace companies seeking to leverage these benefits for their jet turbine blade root production.
Recommended Materials and Why They Matter
The selection of the appropriate metal powder is paramount for ensuring the performance and reliability of 3D printed jet turbine blade roots. These components operate in extremely demanding environments, necessitating materials with exceptional high-temperature strength, creep resistance, oxidation resistance, and fatigue properties. メタル3DP offers a range of high-performance metal powders specifically optimized for such applications, including:
- IN738LC: This nickel-based superalloy is renowned for its excellent high-temperature strength and creep resistance up to approximately 950°C. Its optimized composition also offers good thermal fatigue and oxidation resistance, making it a prime candidate for hot section components in gas turbines. The balanced properties and processability of IN738LC make it suitable for long-term service in demanding aerospace applications. You can explore our range of high-quality metal powders, including IN738LC, on our 製品ページ.
- Haynes 282: Developed for high-temperature structural applications, Haynes 282 is another nickel-based superalloy exhibiting exceptional creep strength in the temperature range of 650-930°C. It surpasses other commercial alloys in creep strength and approaches the performance of R-41 alloy without compromising weldability and fabricability. Its superior oxidation resistance and thermal stability make it ideal for critical gas turbine components. To learn more about our advanced powder making system that ensures the quality of powders like Haynes 282, visit our advanced powder making system.
The choice between these and other suitable alloys depends on the specific operating conditions and performance requirements of the jet turbine engine. メタル3DP‘s team of experts provides comprehensive material consultation services to help customers select the optimal powder for their specific application needs. Our decades of collective expertise in metal additive manufacturing ensure that you receive the best guidance for your project. You can read more about our company’s background and expertise on our 会社概要ページ.
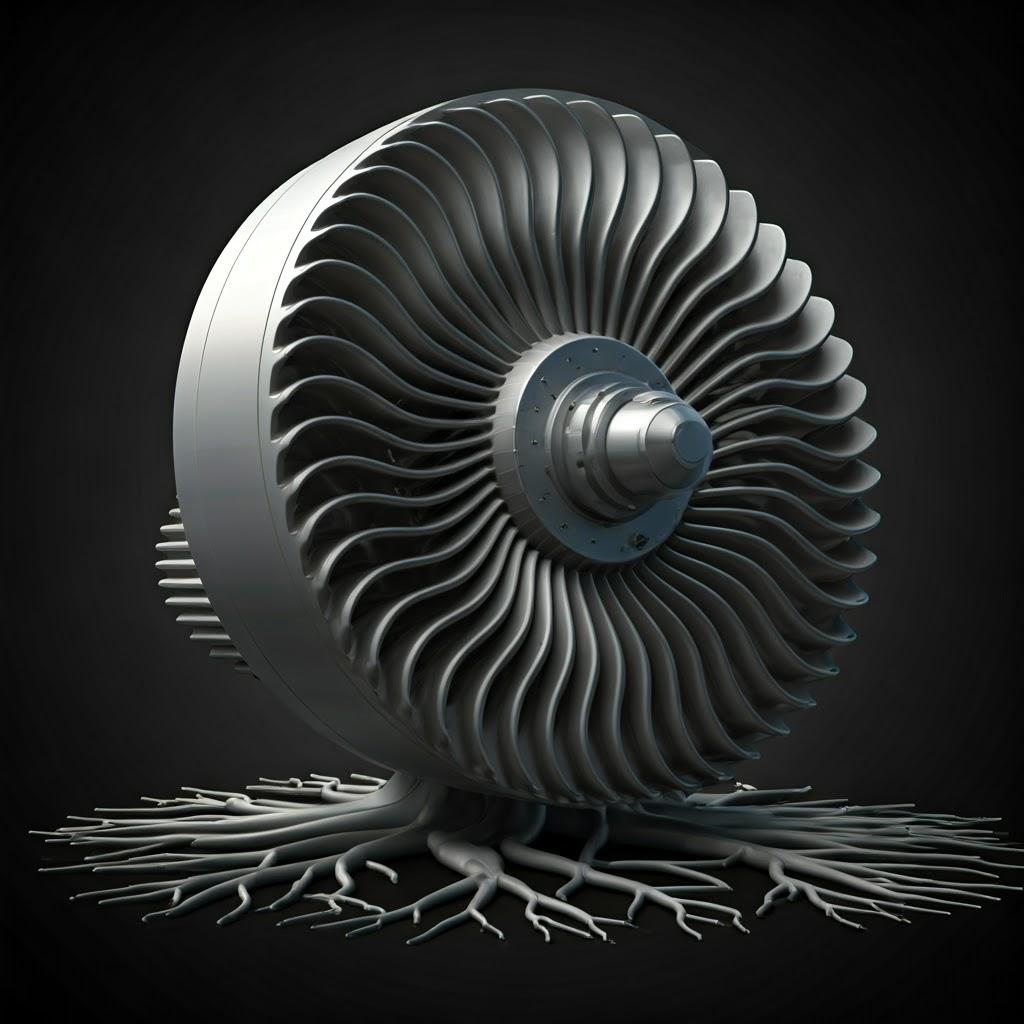
Design Considerations for Additive Manufacturing of Jet Turbine Blade Roots
Designing jet turbine blade roots for metal 3D printing necessitates a shift in mindset compared to traditional manufacturing. The layer-by-layer build process offers unique opportunities and constraints that engineers must consider to optimize the part for performance, manufacturability, and cost-effectiveness. Key design considerations include:
- Topology Optimization: Metal AM allows for the creation of complex, organic shapes that can be optimized for weight reduction while maintaining structural integrity. By strategically removing material from low-stress areas, engineers can design lighter blade roots without compromising their ability to withstand operational loads.
- Internal Cooling Channels: One of the most significant advantages of 3D printing is the ability to integrate intricate internal cooling channels directly into the blade root. These channels, often with complex geometries like lattices or conformal designs, enable more efficient heat dissipation, crucial for extending the lifespan of turbine blades operating at high temperatures.
- サポート体制: Overhanging features and complex geometries often require support structures during the printing process to prevent collapse and ensure dimensional accuracy. Careful consideration of support placement, type, and removal strategy is essential to minimize material waste, reduce post-processing effort, and maintain the surface finish of critical areas.
- Orientation and Build Direction: The orientation of the part on the build platform and the direction in which it is printed can significantly impact its mechanical properties, surface finish, and the need for support structures. Optimizing the build orientation is crucial for achieving the desired performance characteristics in critical stress areas of the blade root.
- Feature Size and Resolution: Metal 3D printing processes have limitations in terms of the minimum feature size and achievable resolution. Designers must be mindful of these limitations when incorporating fine details or intricate features into the blade root design. Consulting with メタル3DP‘s experts can provide valuable insights into the capabilities and limitations of our printing technologies.
- Wall Thickness and Ribs: Achieving optimal strength-to-weight ratios often involves careful consideration of wall thicknesses and the incorporation of stiffening ribs. 3D printing allows for the creation of thin-walled structures reinforced by internal or external ribs, providing strength without excessive weight.
By thoughtfully addressing these design considerations, engineers can fully leverage the capabilities of metal 3D printing to create high-performance, efficient, and cost-effective jet turbine blade roots.
Tolerance, Surface Finish, and Dimensional Accuracy in 3D Printed Blade Roots
Achieving the required levels of tolerance, surface finish, and dimensional accuracy is paramount for the functional integration and performance of jet turbine blade roots. Metal 3D printing technologies have made significant strides in these areas, offering capabilities that meet the stringent demands of the aerospace industry.
- Tolerance: The achievable tolerance in metal 3D printing depends on the specific printing technology, material, and part geometry. Selective Laser Melting (SLM) and Electron Beam Melting (EBM), the primary technologies employed by メタル3DP for high-performance applications, can achieve tolerances in the range of ±0.05 mm to ±0.1 mm for critical dimensions. Post-processing techniques like CNC machining can further refine tolerances when necessary.
- 表面仕上げ: The as-printed surface finish in metal 3D printing is typically rougher than that achieved by traditional machining processes. The surface roughness is influenced by factors such as powder particle size, layer thickness, and build orientation. For critical surfaces of jet turbine blade roots, post-processing methods like polishing, grit blasting, or chemical etching are often employed to achieve the required smoothness and ensure proper aerodynamic performance and fatigue life.
- 寸法精度: Dimensional accuracy refers to the degree to which the printed part matches the intended design dimensions. Factors affecting dimensional accuracy include material shrinkage during solidification, thermal gradients during the build process, and the accuracy of the printing equipment. メタル3DP‘s state-of-the-art printers are calibrated and controlled to minimize these deviations, ensuring high dimensional accuracy. Furthermore, advanced simulation tools can predict and compensate for potential distortions.
メタル3DP is committed to delivering jet turbine blade roots that meet the most demanding specifications for tolerance, surface finish, and dimensional accuracy. Our expertise in both printing and post-processing ensures that the final components adhere to the stringent quality standards of the aerospace industry. You can learn more about the precision and reliability of our printing methods on our 印刷方法ページ.
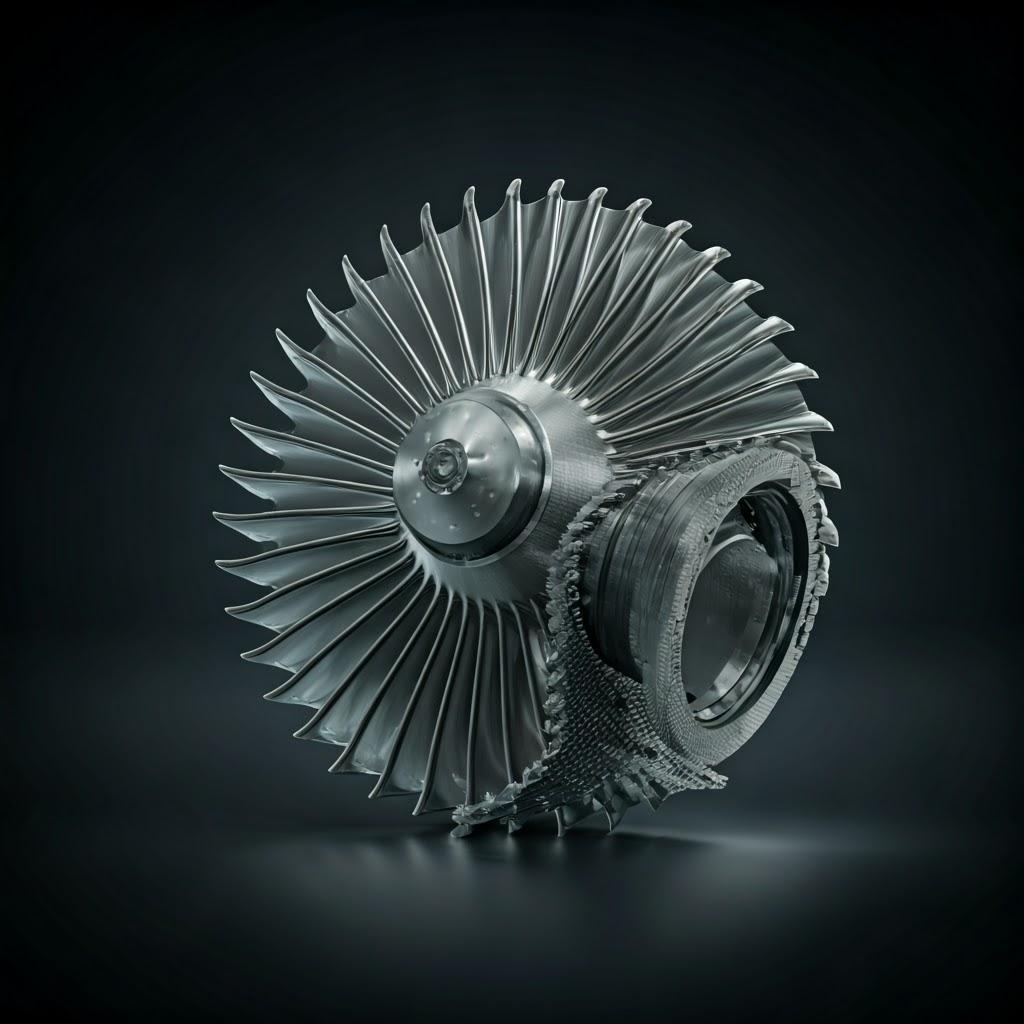
Post-Processing Requirements for 3D Printed Turbine Blade Roots
While metal 3D printing offers significant advantages in creating complex geometries, post-processing is often a necessary step to achieve the final desired properties and surface finish for jet turbine blade roots. Common post-processing requirements include:
- サポートの取り外し: Support structures, essential for printing overhanging features, must be carefully removed after the build process. This can involve manual methods, machining, or chemical dissolution, depending on the support material and part geometry.
- Stress Relief Heat Treatment: To alleviate residual stresses that may have built up during the rapid heating and cooling cycles of the 3D printing process, a stress relief heat treatment is often performed. This improves the mechanical properties and dimensional stability of the component.
- 熱間静水圧プレス(HIP): For critical aerospace applications, Hot Isostatic Pressing (HIP) may be employed to eliminate internal porosity and further densify the material, enhancing its fatigue life and high-temperature performance.
- CNC Machining: In cases where very tight tolerances or specific surface finishes are required on critical features, CNC machining can be used as a secondary operation to achieve the desired precision.
- 表面仕上げ: As mentioned earlier, surface finishing techniques such as polishing, grit blasting, or coating may be applied to improve the surface roughness, enhance corrosion resistance, or provide specific functional properties.
- 非破壊検査(NDT): To ensure the integrity and quality of the 3D printed blade roots, various non-destructive testing methods, such as dye penetrant inspection, ultrasonic testing, or X-ray radiography, may be employed to detect any internal flaws or surface defects.
メタル3DP offers comprehensive post-processing services to ensure that 3D printed jet turbine blade roots meet the stringent requirements of aerospace applications. Our expertise in heat treatment, surface finishing, and NDT guarantees the quality and reliability of the final components.
Common Challenges and How to Avoid Them in 3D Printing Blade Roots
While metal 3D printing offers numerous advantages, several challenges can arise during the fabrication of complex parts like jet turbine blade roots. Understanding these challenges and implementing appropriate strategies to avoid them is crucial for successful outcomes.
- Warping and Distortion: Thermal stresses during the printing process can lead to warping or distortion of the part, particularly for large or complex geometries. Optimizing build orientation, employing appropriate support structures, and carefully controlling the printing parameters can mitigate these issues. Simulation tools can also help predict and compensate for potential distortions.
- 多孔性: Internal porosity within the printed part can compromise its mechanical properties. Ensuring the use of high-quality metal powders, optimizing laser or electron beam parameters, and employing post-processing techniques like HIP can minimize or eliminate porosity. メタル3DP‘s advanced powder making system ensures the high quality and density of our metal powders, contributing to the production of dense, high-performance parts.
- Support Structure Removal Damage: Improper removal of support structures can damage the surface of the part, especially intricate features. Careful design of support structures and the use of appropriate removal techniques are essential.
- Residual Stresses: As mentioned earlier, residual stresses can affect the dimensional stability and fatigue life of the printed part. Implementing stress relief heat treatments is crucial for mitigating these stresses.
- Surface Finish Issues: Achieving the desired surface finish on complex geometries can be challenging. Optimizing build parameters and employing appropriate post-processing techniques are necessary to meet surface roughness requirements.
- Material Property Variability: Inconsistent material properties throughout the printed part can be a concern. Careful control of the printing process, including laser power, scan speed, and powder bed temperature, is essential for ensuring uniform material properties.
メタル3DP‘s extensive experience and deep understanding of metal additive manufacturing processes enable us to effectively address these challenges and deliver high-quality, reliable jet turbine blade roots. Our team of experts works closely with customers to optimize designs and printing parameters, ensuring successful outcomes.
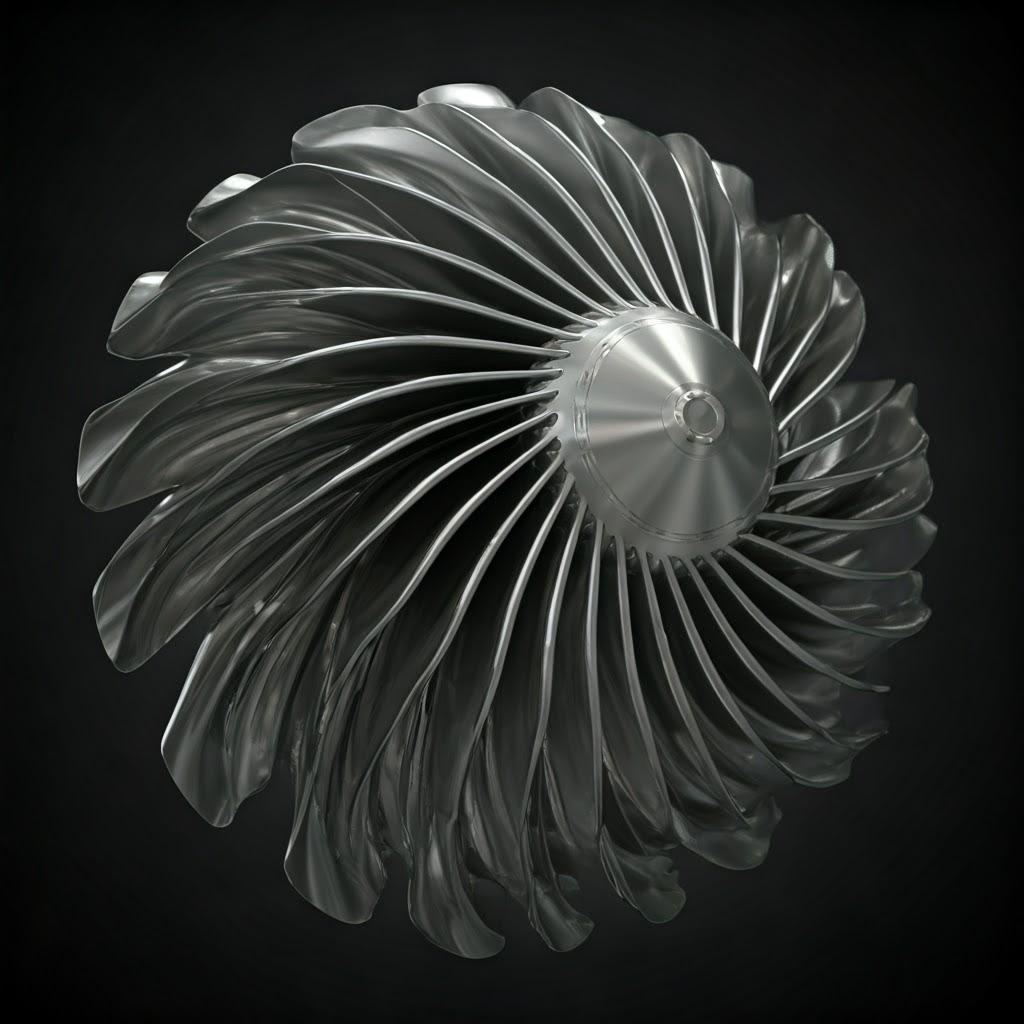
How to Choose the Right Metal 3D Printing Service Provider for Jet Turbine Blade Roots
Selecting the appropriate metal 3D printing service provider is a critical decision that can significantly impact the quality, cost, and lead time of your jet turbine blade roots. Consider the following factors when evaluating potential partners:
- Material Capabilities: Ensure the provider has experience working with the specific high-performance alloys required for turbine applications, such as IN738LC and Haynes 282. Verify their expertise in processing these materials to achieve the desired mechanical properties and microstructures. メタル3DP boasts extensive experience with a wide range of high-performance metal powders optimized for demanding applications.
- 印刷技術: Different metal 3D printing technologies (e.g., SLM, EBM) offer varying levels of precision, build volume, and material compatibility. Choose a provider whose technology aligns with the specific requirements of your blade root design in terms of complexity, size, and desired tolerances. Our company specializes in SEBM printers, known for their accuracy and reliability for mission-critical parts. You can explore our capabilities further on our 金属 3D プリント ページ.
- Quality Assurance and Certifications: Verify that the provider has robust quality control processes in place, including material traceability, in-process monitoring, and post-processing inspection. Relevant certifications, such as AS9100 for aerospace applications, demonstrate a commitment to quality and reliability.
- Post-Processing Services: Determine if the provider offers the necessary post-processing services, such as support removal, heat treatment, surface finishing, and non-destructive testing, required for your application. A comprehensive service offering can streamline the production process and ensure the final part meets your specifications. メタル3DP provides comprehensive solutions spanning printing and application development services.
- Design Optimization Expertise: A knowledgeable service provider can offer valuable insights into designing for additive manufacturing, helping you optimize your blade root geometry for performance, manufacturability, and cost-effectiveness.
- Experience and Track Record: Evaluate the provider’s experience in producing similar components for the aerospace or related industries. Review case studies and testimonials to gauge their expertise and reliability.
- Communication and Support: Effective communication and responsive customer support are essential for a smooth and successful project. Choose a provider that is proactive, transparent, and readily available to address your questions and concerns.
By carefully considering these factors, you can select a metal 3D printing service provider like メタル3DP that can reliably deliver high-quality jet turbine blade roots that meet your specific requirements.
Cost Factors and Lead Time for 3D Printed Blade Roots
The cost and lead time for producing jet turbine blade roots using metal 3D printing are influenced by several factors:
- 材料費: The cost of the metal powder, particularly high-performance alloys like IN738LC and Haynes 282, is a significant factor. Material waste is generally lower in 3D printing compared to subtractive methods, which can help offset some of these costs.
- ビルドタイム: The time it takes to print a blade root depends on its size, complexity, and the chosen printing technology. Longer build times translate to higher machine operating costs.
- 後処理費用: The extent of post-processing required (e.g., support removal, heat treatment, machining, surface finishing) will impact the overall cost and lead time. Complex post-processing steps will add to both.
- デザインの複雑さ: Intricate designs that require extensive support structures or careful orientation may increase both the printing time and post-processing effort, thus affecting cost and lead time.
- 生産量: While 3D printing is often advantageous for low to medium production volumes and customization, the cost per part may decrease with larger production runs due to economies of scale in material procurement and process optimization.
- Service Provider Costs: Different service providers have varying pricing structures based on their equipment, expertise, and overhead costs. Obtaining quotes from multiple reputable providers like メタル3DP is essential for cost comparison.
Lead times for 3D printed jet turbine blade roots can vary from a few days to several weeks, depending on the complexity of the part, the chosen materials, the required post-processing, and the service provider’s current workload. Metal 3D printing can often offer shorter lead times compared to traditional tooling-dependent methods, especially for complex geometries and low to medium volumes. Contact メタル3DP to explore how our capabilities can power your organization’s additive manufacturing goals and to get a customized cost and lead time estimate for your specific requirements.
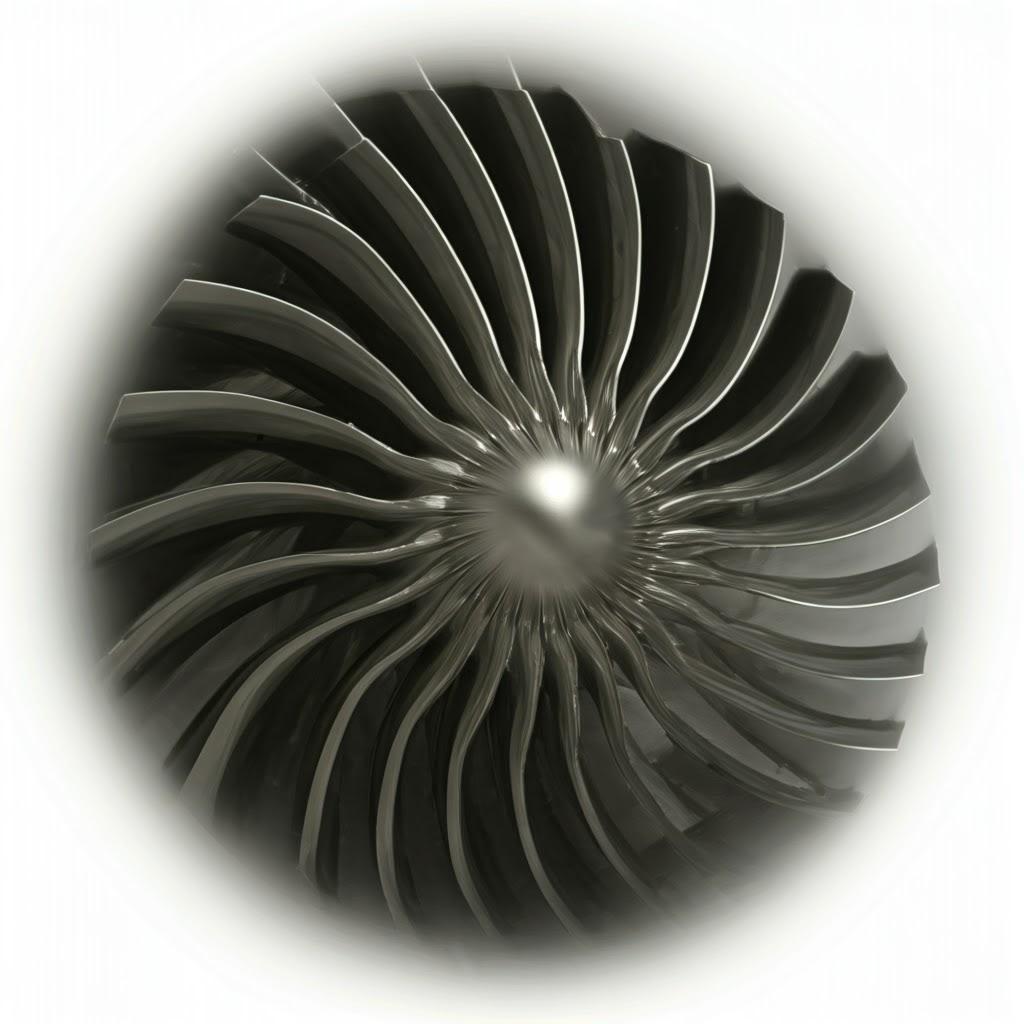
よくある質問(FAQ)
- What are the typical tolerances achievable for 3D printed jet turbine blade roots?
- Using technologies like SLM and EBM, tolerances of ±0.05 mm to ±0.1 mm are achievable for critical dimensions. Post-processing like CNC machining can further refine these tolerances when necessary.
- Is metal 3D printing cost-effective for mass production of turbine blade roots?
- Metal 3D printing is particularly cost-effective for low to medium production volumes, complex geometries, and customized designs. For very high volumes, traditional manufacturing methods may still be more economical, but the advantages of design freedom and reduced lead times often make 3D printing a compelling option even for larger production runs.
- What non-destructive testing methods are used to ensure the quality of 3D printed turbine blade roots?
- Common NDT methods include dye penetrant inspection to detect surface cracks, ultrasonic testing to identify internal flaws, and X-ray radiography to reveal porosity or inclusions within the part.
Conclusion: Embracing the Future of Jet Turbine Blade Root Manufacturing with Metal 3D Printing
Metal 3D printing is revolutionizing the manufacturing of jet turbine blade roots, offering unprecedented design freedom, material efficiency, and reduced lead times. By leveraging advanced materials like IN738LC and Haynes 282 and optimizing designs for additive manufacturing, engineers can create high-performance components with enhanced cooling capabilities and improved structural integrity. メタル3DP stands at the forefront of this technological advancement, providing industry-leading metal 3D printing equipment, high-quality metal powders, and comprehensive application development services. Our commitment to innovation and quality makes us a trusted partner for aerospace companies seeking to embrace the future of digital manufacturing. Contact メタル3DP today to explore how our capabilities can empower your organization’s additive manufacturing journey.
シェアする
MET3DP Technology Co., LTDは、中国青島に本社を置く積層造形ソリューションのリーディングプロバイダーです。弊社は3Dプリンティング装置と工業用途の高性能金属粉末を専門としています。