3D Printing Metal Powder in 2025
Inhoudsopgave
3d printen metal powder is revolutionizing manufacturing across industries like aerospace, medical, and automotive. This advanced additive manufacturing technology allows complex metal parts to be created directly from 3D CAD data by selectively melting layers of fine metallic powder.
Deze uitgebreide gids onderzoekt alle aspecten van 3D-printen met metaalpoeder om u te helpen de technologie en toepassingen te begrijpen.
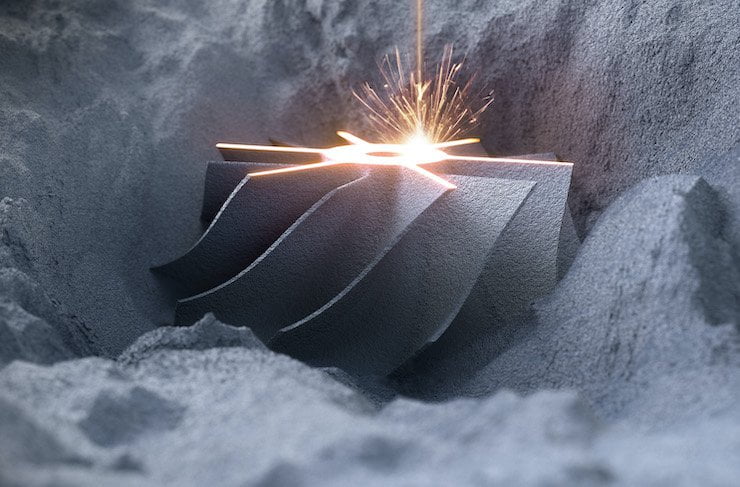
Overview of 3D Printing Metal powder
Metaal 3D-printen, ook bekend als Direct Metal Laser Sintering (DMLS) of Selective Laser Melting (SLM), is een additief productieproces waarbij gebruik wordt gemaakt van een krachtige laser om fijn metaalpoeder samen te smelten tot solide 3D-objecten.
Een 3D-printer bouwt metalen onderdelen laag voor laag op uit poedervormige metalen materialen zoals aluminium, titanium, nikkellegeringen en roestvrij staal. De technologie biedt ongeëvenaarde ontwerpvrijheid en indrukwekkende materiaaleigenschappen die ongeëvenaard zijn door traditionele productie.
Key Details About 3D Printing Metal Powder:
Parameter | Details |
---|---|
Technologie | Poederbedfusieproces met behulp van laser om metaalpoeder selectief te smelten |
Materialen | Aluminium, titanium, nikkel, roestvrij staal, kobalt-chroom, edele metalen |
Hardware | 3D-printer met krachtige laser, poederbed en harksysteem |
Proces | Verspreid een dunne laag poeder, smelt selectief met laser, voeg lagen toe om onderdelen te bouwen |
Eigenschappen | Zeer sterk, gelijkmatig verdeeld materiaal, complexe interne geometrie |
Toepassingen | Lucht- en ruimtevaart, medische implantaten, auto's, gereedschappen, sieraden |
Voordelen | Ontwerpvrijheid, gewichtsvermindering, consolidatie van onderdelen, snelle prototyping |
Beperkingen | Hoge apparatuurkosten, beperkte omvang, nabewerking vereist |
Deze additieve productiemethode levert talloze voordelen op ten opzichte van traditionele subtractieve technieken zoals CNC-bewerking, zoals grotere ontwerpvrijheid, consolidatie van onderdelen, snelle prototyping en aanzienlijke gewichtsvermindering. De mogelijkheid om complexe metalen componenten in 3D te printen maakt belangrijke innovaties in alle sectoren mogelijk.
Types of 3D Printing Metal Powder
3D printing metal powders are essential materials in additive manufacturing, offering unique properties for various industries like aerospace, automotive, medical, and energy. Below is an overview of the major categories of 3D printing metal powders and their common types, presented in a table format for clarity.
Verwante producten
1. Titanium Alloys
Titanium powders are lightweight, strong, and corrosion-resistant, making them ideal for aerospace and medical applications.
Type | Beschrijving | Toepassingen |
---|---|---|
Ti6Al4V (graad 5) | High strength-to-weight ratio, widely used titanium alloy. | Ruimtevaart, automobielindustrie, medische implantaten |
Ti6Al4V ELI | Purified version of Grade 5, extra-low interstitials for biocompatibility. | Medische implantaten, protheses |
Puur titanium | Grades 1-4, excellent corrosion resistance and biocompatibility. | Chemical processing, medical implants |
2. Stainless Steels
Stainless steel powders are durable, corrosion-resistant, and widely used for structural and functional parts.
Type | Beschrijving | Toepassingen |
---|---|---|
316L roestvrij staal | Excellent corrosion resistance and mechanical properties. | Medical tools, food processing, marine |
17-4PH roestvast staal | Precipitation-hardened steel with high strength and wear resistance. | Aerospace, automotive, industrial tools |
304 roestvrij staal | Cost-effective, moderate corrosion resistance. | Consumer goods, structural components |
3. Aluminum Alloys
Aluminum powders are lightweight and have excellent thermal conductivity, ideal for aerospace and automotive uses.
Type | Beschrijving | Toepassingen |
---|---|---|
AlSi10Mg | Good mechanical properties and heat resistance. | Aerospace, automotive, industrial parts |
AlSi12 | High thermal conductivity, good wear resistance. | Heat exchangers, lightweight parts |
Aluminium 7075 | High strength and low weight, suitable for heavy-duty applications. | Aerospace, structural components |
4. Nickel-Based Alloys
Nickel alloys excel in extreme environments, offering high-temperature and corrosion resistance.
Type | Beschrijving | Toepassingen |
---|---|---|
Inconel 718 | High strength and oxidation resistance, suitable for extreme conditions. | Turbine blades, jet engines, energy sector |
Inconel 625 | Exceptional resistance to harsh environments, including marine. | Scheepvaart, chemische verwerking |
Hastelloy X | Outstanding heat and chemical resistance. | Aerospace, high-temperature environments |
5. Cobalt-Chromium Alloys
Cobalt-chromium powders are highly wear-resistant and biocompatible, perfect for medical and dental applications.
Type | Beschrijving | Toepassingen |
---|---|---|
CoCrMo | Combines strength, wear resistance, and biocompatibility. | Tandheelkundige implantaten, orthopedische hulpmiddelen |
CoCrW | High hardness and heat resistance, suitable for demanding applications. | Turbine blades, high-wear parts |
6. Tool Steels
Tool steels are known for their hardness and wear resistance, commonly used in manufacturing tools and molds.
Type | Beschrijving | Toepassingen |
---|---|---|
H13 Gereedschapsstaal | Heat-resistant steel, ideal for tooling and molds. | Spuitgieten, spuitgieten |
Maragingstaal | Excellent strength and toughness, suitable for high-stress parts. | Ruimtevaart, gereedschap |
7. Precious Metals
Precious metals are used in luxury goods, jewelry, and electronics for their aesthetic and conductive properties.
Type | Beschrijving | Toepassingen |
---|---|---|
Goud (Au) | High value and corrosion resistance, used in decorative applications. | Jewelry, electronics |
Zilver (Ag) | Uitzonderlijk thermisch en elektrisch geleidingsvermogen. | Electronics, conductive components |
Platina (Pt) | High durability and resistance, used in high-end applications. | Jewelry, catalytic converters |
8. Copper Alloys
Copper-based powders offer outstanding thermal and electrical conductivity for specialized applications.
Type | Beschrijving | Toepassingen |
---|---|---|
Zuiver Koper | Excellent conductivity, suitable for electrical applications. | Elektronica, warmtewisselaars |
Koperlegeringen | Enhanced mechanical properties with good conductivity (e.g., CuCrZr). | Electrical components, tooling |
3D Printing metal powder Processes
Er zijn verschillende vergelijkbare poederbedfusietechnologieën die worden gebruikt voor 3D-printen van metaal:
Metaalpoederbedfusieprocessen
Proces | Details |
---|---|
Direct metaallasersinteren (DMLS) | Maakt gebruik van laser om metaalpoeder selectief te smelten in een atmosfeer van inert gas |
Selectief lasersmelten (SLM) | Zeer vergelijkbaar met DMLS, smelt poeder volledig in vaste delen |
Elektronenbundelsmelten (EBM) | Gebruikt elektronenstraal in plaats van laser voor hogere bouwsnelheden |
Selectief lasersinteren (SLS) | Sinters verpoederen tot een vast onderdeel zonder volledig te smelten |
Direct metaallasersmelten (DMLM) | Een andere term voor DMLS-proces |
LaserCUSING | Proces ontwikkeld door Concept Laser |
LASFORM | Proces door DMG MORI |
De meest gebruikte technologieën zijn DMLS en SLM. Beiden maken gebruik van een krachtige ytterbium-vezellaser om het metaalpoeder volledig te smelten en samen te smelten om 3D-objecten uit CAD-gegevens te laten groeien.
Het belangrijkste verschil tussen SLM en DMLS is dat SLM streeft naar volledig smeltende en dichte onderdelen, terwijl DMLS onderdelen kan produceren met enige porositeit tussen poederdeeltjes. De termen worden echter vaak door elkaar gebruikt.
Elektronenbundelsmelten (EBM) maakt gebruik van een warmtebron met elektronenbundels in plaats van een laser, waardoor hogere bouwsnelheden mogelijk zijn. Maar EBM kan alleen worden gebruikt met geleidende materialen zoals titanium- en nikkellegeringen.
Selectief lasersinteren (SLS) gebruikt lagere temperaturen om het poeder tot vaste delen te smelten zonder het volledige smeltpunt te bereiken. Dit levert meer poreuze metalen onderdelen op.
Metalen materialen voor 3D-printen met poederbed
Een reeks metalen en legeringen kan worden verwerkt tot fijne poeders voor gebruik in 3D-printtechnologieën met poederbedfusie:
Metalen voor 3D-printen met poederbed
Materiaal | Details | Toepassingen |
---|---|---|
Titanium | Hoge sterkte-gewichtsverhouding, biocompatibel | Lucht- en ruimtevaart, medische implantaten |
Aluminium | Lichtgewicht, hoge sterkte | Automobiel, ruimtevaart |
Nikkellegeringen | Corrosiebestendigheid, hoge sterkte | Lucht- en ruimtevaart, maritiem |
Roestvrij staal | Corrosiebestendigheid, hoge hardheid | Industrieel gereedschap, mallen |
Kobalt-Chroom | Biocompatibel, draagt goed | Tandheelkundige, medische implantaten |
Edelmetalen | Sieraden, duurzaamheid | Sieraden, luxe goederen |
Gereedschapsstaal | Hittebestendigheid, hardheid | Metaalvormen, spuitgietmatrijzen |
Gelegeerde staalsoorten | Hoge sterkte, slagvastheid | Industriële slijtagedelen |
De meest gebruikte metalen zijn titaniumlegeringen en aluminium vanwege hun hoge sterkte-gewichtsverhouding. Inerte nikkellegeringen zoals Inconel zijn populair in ruimtevaarttoepassingen. Roestvast staal- en gereedschapsstaalpoeders creëren duurzame metalen onderdelen met uitstekende hardheid en slijtvastheid.
Edelmetalen zoals goud, zilver en platina maken het direct 3D-printen van sieraden en luxe artikelen mogelijk. Op maat gemaakte medische implantaten maken vaak gebruik van biocompatibele legeringen zoals titanium of kobaltchroom.
Metaalpoeders voor AM worden geproduceerd door gas- of waterverneveling tot precieze deeltjesgroottes die optimaal zijn afgestemd op de resolutie van poederbedprinten.
Toepassingen van 3D-printen met metaalpoederbed
Metaaladditieve productie maakt de productie mogelijk van complexe, lichtgewicht onderdelen in de lucht- en ruimtevaart-, medische, tandheelkundige, automobiel- en industriële sectoren.
Industrietoepassingen van 3D-printen met metaalpoederbed:
Industrie | Toepassingen | Voordelen |
---|---|---|
Lucht- en ruimtevaart | Vliegtuigonderdelen, turbines, raketonderdelen | Gewichtsreductie, geoptimaliseerde geometrie |
Medisch | Orthopedische implantaten, chirurgische instrumenten | Biocompatibel, gepersonaliseerd |
Automobiel | Lichtgewicht onderdelen, aangepaste gereedschappen | Snellere ontwikkeling, consolidatie |
Industrieel | Spuitgietmatrijzen, mallen, armaturen | Geoptimaliseerde conformele koeling |
Juwelen | Ringen, hangers, horloges | Unieke geometrieën, goud/zilver |
Tandheelkundig | Kronen, bruggen, aligners | Op maat gemaakt, snelle productie |
In de lucht- en ruimtevaart wordt metaal AM gebruikt om lichtere structurele componenten van vliegtuigen te vervaardigen, zoals titaniumbeugels en roestvrijstalen landingsgestelonderdelen met geoptimaliseerde sterkte-gewichtseigenschappen.
De technologie is ideaal voor op maat gemaakte medische implantaten, zoals heupgewrichten, die aansluiten bij de anatomie van de patiënt en de belasting beter verdelen. Metaalprinten stroomlijnt de automobielproductie door middel van consolidatie van onderdelen en geoptimaliseerde lichtgewichtontwerpen.
Voor industrieën zoals spuitgieten verhogen 3D-geprinte conforme koelkanalen in gereedschappen de productiviteit aanzienlijk. Juweliers maken gebruik van het proces voor unieke sieradencreaties in edele metalen.
Voordelen van 3D-printen met metaalpoederbed
Van prototypes tot productieonderdelen voor eindgebruik, metaal-AM biedt aanzienlijke voordelen ten opzichte van conventionele fabricageprocessen zoals machinale bewerking of metaalgieten:
Belangrijkste voordelen van 3D-printen met metaalpoederbed
- Ontwerpvrijheid – Creëer complexe organische vormen en interne roosters die onmogelijk zijn met subtractieve methoden
- Sneller proces – Additief proces zonder gereedschap, weinig afval – ga rechtstreeks van CAD naar metalen onderdeel
- Gewichtsreductie – Optimaliseer de topologie voor lichtere, sterkere metalen componenten
- Consolidatie van onderdelen – Combineer assemblages tot één 3D-geprint onderdeel om productiestappen te verminderen
- Snelle prototyping – Test ontwerpen van metalen onderdelen snel tijdens de ontwikkeling
- Aangepaste onderdelen – Pas medische implantaten en andere metalen onderdelen eenvoudig aan
- Hoge sterkte – As-printed metalen onderdelen concurreren met traditionele methoden zoals gieten
- Verminder de voorraad – Print on-demand metalen reserveonderdelen, geen pre-productie
- Afvalvermindering – Het additieve proces heeft materiaalverspilling onder de 5%
De geoptimaliseerde eigenschappen van metalen AM-onderdelen, zoals conformele koelkanalen in mallen of complexe roosterstructuren in implantaten, zijn onmogelijk te produceren door middel van frees- of gietprocessen.
Het 3D-printen van complexe of op maat gemaakte metalen onderdelen rechtstreeks vanuit CAD-gegevens minimaliseert ook productiestappen ten opzichte van subtractieve methoden die uitgebreide gereedschappen, bewerkingen en assemblage vereisen. Er zijn enorme tijd- en kostenbesparingen, waardoor het ideaal is voor productie in kleine volumes.
Beperkingen en uitdagingen bij het printen van metaalpoederbedden
Ondanks de vele voordelen zijn er enkele beperkingen waarmee u rekening moet houden bij het gebruik van 3D-printen met metaalpoederbed:
Beperkingen van 3D-printen met metaalpoederbed
- Hoge machinekosten – Metaal 3D-printers beginnen rond de $100.000. Grote systemen overschrijden $1M
- Beperkte onderdeelgrootte – Bouw momenteel volumes van minder dan 500 mm x 500 mm x 500 mm
- Nabewerking – Extra arbeid voor het verwijderen van steunen en oppervlakteafwerking
- Anisotroop materiaal – Mechanische eigenschappen variëren afhankelijk van de bouworiëntatie
- Normen nodig – Voor de lucht- en ruimtevaart en de medische sector, zonder poeder- en procesnormen
- Beperkte materiaalopties – Er zijn minder legeringen beschikbaar dan gieten of MIM-poedermetallurgie
- Porositeitsproblemen – Het proces kan kleine interne holtes creëren, afhankelijk van de parameters
- Beheer van ongebruikte poeders – Behandeling van metaalpoeder, vereisten voor recycling
De beperkingen van de printerkosten en de bouwgrootte kunnen de adoptie van metaal-AM beperken tot relatief lage productievolumes. Ondersteuningsconstructies en overhangende delen van bouwplaten vereisen ook nabewerking, zoals machinale bewerking.
Er is sprake van een voortdurende ontwikkeling van industriestandaarden voor materialen, processen en poederverwerking, nu de adoptie zich verspreidt naar sterk gereguleerde sectoren. Momenteel is slechts een subset van metaallegeringen beschikbaar als geoptimaliseerde voorgelegeerde poeders voor AM.
Anisotrope materiaaleigenschappen, waarbij de sterkte varieert tussen de bouwrichtingen X/Y en Z, vereisen ontwerp- en procescompensatie. Interne holtes of porositeitsproblemen moeten ook worden beperkt door de ideale verwerkingsparameters in te stellen.
Metaalpoederbed 3D-printproces
Het 3D-printproces met poederbedfusie voor metalen omvat het verspreiden van dunne lagen metaalpoeder en het selectief smelten ervan om onderdelen op te bouwen:
Metaalpoederbed Fusion 3D-printproces:
Stap | Beschrijving |
---|---|
1. 3D-model | CAD-model is 3D in lagen gesneden |
2. Verdeel poeder | De machine verspreidt een dunne laag (~20-100 μm) metaalpoeder |
3. Lasersmelten | De krachtige laser smelt selectief poeder om de laag te smelten |
4. Onderbed | Bouwplaat omlaag, nieuwe laag poeder erop |
5. Herhaal de stappen | Stappen 2-4 worden herhaald totdat het volledige onderdeel is opgebouwd |
6. Onderdeel verwijderen | Niet-gefuseerd poeder ondersteunt een deel en wordt vervolgens verwijderd |
7. Postproces | Extra reiniging en oppervlakteafwerking |
Het proces begint met een 3D CAD-model, meestal in STL-formaat, dat wordt verwerkt door slicersoftware. Hierdoor wordt het model in lagen verdeeld, waardoor in feite 2D-profielen voor elke laag worden gemaakt, en er worden bouwinstructies voor de printer gegenereerd.
De printer verspreidt met behulp van een wipersysteem een dunne laag metaalpoeder over het poederbed. De laserstraal gaat vervolgens over de laag en smelt het metaalpoeder selectief volgens het profiel van die laag.
De krachtige laser smelt metaaldeeltjes volledig samen tot een gestolde laag. De bouwplaat gaat vervolgens omlaag, waardoor de volgende laag vers poeder over de vorige laag kan worden verspreid. Het proces herhaalt zich totdat het volledige 3D-object van onder naar boven is opgebouwd.
Elk ongesinterd poeder fungeert als ondersteuning tijdens de opbouw. Na het printen wordt dit eenvoudigweg weggeborsteld, zodat het voltooide metalen onderdeel zichtbaar wordt. Vaak volgt er enige bewerking of oppervlakteafwerking om de 3D-geprinte oppervlakken glad te maken.
Powder Bed Fusion-printerhardware
Gespecialiseerde 3D-printsystemen voor metaal maken gebruik van poederbedfusietechnologie om metaalpoeders te verwerken. De kerncomponenten omvatten:
Onderdelen van de Powder Bed Fusion-printer:
Onderdeel | Beschrijving |
---|---|
Lasersysteem | Krachtige fiberlaser ~100-400W voor het smelten van metaalpoeder |
Poeder bed | Metaalpoeder verspreidt zich in dunne lagen over dit beweegbare bed |
Poederdispenser | Doseert en verspreidt poeder soepel over het bed |
Poeder collectie | Verzamelt overtollig poeder om opnieuw te gebruiken |
Inerte gasstroom | Afgedichte kamer gevuld met argon of stikstof |
Bouw plaat | Zakt naarmate er lagen bovenop worden gedrukt |
Optisch systeem | Focust en stuurt de laserstraal over het poederbed |
Controle systeem | Bestuurt laser, optiek, poederbed in coördinatie |
Er is een krachtige ytterbiumvezellaser nodig om de metaalpoeders volledig te smelten en samen te smelten tot dichte delen. De dichtheid en focus van de laserenergie moeten strak worden gecontroleerd om ideale smeltbaden en binding te bereiken.
De laser focust tot op ongeveer 10 micron op het poederbed om de geometrie van elke opeenvolgende laag te bepalen. Galvospiegeloptiek stuurt de laser nauwkeurig over het bed.
Het metaalpoeder wordt door een harksysteem uit cartridges gedoseerd en gelijkmatig over het printgebied verspreid met een dikte van ongeveer 20-100 micron. Poeder wordt aan de voorkant van het systeem afgegeven en het overtollige poeder wordt aan de achterkant opgevangen.
Een inert gas zoals argon of stikstof vult de bouwkamer om oxidatie van reactieve metalen zoals aluminium of titanium te voorkomen. Het hele systeem wordt bestuurd door gespecialiseerde software die de laser, het poederbed en andere actuatoren integreert.
Poederbedfusieprocesparameters
Het optimaliseren van de verschillende procesparameters die betrokken zijn bij poederbedfusie is van cruciaal belang voor het produceren van hoogwaardige metalen onderdelen:
Belangrijke poederbedfusieprocesparameters:
Parameter | Typisch bereik | Effect op onderdeelkwaliteit |
---|---|---|
Laserkracht | 100-400W | Beïnvloedt de grootte van het smeltbad, regelt de hechting |
Grootte van de straal | ~50-100 μm | De scherpstelpuntgrootte heeft invloed op de resolutie en precisie |
Scansnelheid | Tot 10.000 mm/s | Sneller scannen heeft invloed op de thermische gradiënten |
Hatch-afstand | ~50-200 μm | Afstand tussen scansporen, verdichting |
Laag hoogte | 20-100 μm | Dunnere lagen verbeteren de resolutie en oppervlakteafwerking |
Poeder laag | 20-50 μm | Uniformiteit en dikte van de poederlaag |
Bouwplaat temp | 60-200°C | Voorverwarmen vermindert spanningen en krullen |
Het laservermogen moet hoog genoeg zijn (doorgaans 100 W tot 400 W) om de metaalpoederdeeltjes volledig samen te smelten tot een vast onderdeel. Maar te veel kracht kan sleutelgateffecten veroorzaken.
Sneller scannen van de laser verhoogt de productiesnelheid, maar kan meer restspanningen en materiaalanisotropie veroorzaken. De arceringsafstand bepaalt de afstand tussen aangrenzende scansporen.
Dunnere poederlagen van ongeveer 20-50 micron verbeteren de resolutie, fijne details en oppervlakteafwerking. Het voorverwarmen van de bouwplaat helpt ook om spanningen te verminderen.
Parameteroptimalisatie is specifiek voor het poedermateriaal, de laseroptiek, de inerte gasstroom en andere onderling afhankelijke factoren. Om de ideale instellingen te kunnen instellen, is fijnafstemming nodig.
Nabewerkingsstappen voor metalen AM-onderdelen
Na het printen van complexe metalen onderdelen met behulp van poederbedfusie is doorgaans aanvullende nabewerking vereist:
Algemene nabewerkingsstappen voor metalen AM-onderdelen:
- Verwijderen van ondersteuningen – Verwijder ongesinterde poederondersteuningen door middel van trillingen, stralen, enz.
- Thermische spanningsverlichting – Onthard onderdelen om interne spanningen tijdens het proces te verlichten
- Oppervlaktebewerking – Traditionele methoden om oppervlakken glad te maken, zoals frezen, draaien en slijpen
- Heet isostatisch persen – Past hoge hitte en druk toe om de materiaaldichtheid te verbeteren
- Warmtebehandelingen – Pas de microstructuur aan met behulp van gecontroleerde verwarmings- en koelcycli
- Oppervlakteafwerking – Breng coatings aan, polijst afwerkingen voor de gewenste oppervlakte-eigenschappen
Steunpoeder wordt voorzichtig verwijderd met behulp van een combinatie van trillen, stralen met kralen of lucht en vacuümzuigen. Dit poeder kan vaak worden gezeefd en hergebruikt.
Gloeiwarmtebehandelingen helpen de spanningen te verlichten die worden veroorzaakt door de intense plaatselijke verwarming tijdens het lasersmelten. Extra oppervlaktebewerking verbetert de maatnauwkeurigheid en oppervlakteafwerking.
Sommige toepassingen profiteren van heet isostatisch persen om onderdelen verder te verdichten door een hoge uniforme gasdruk toe te passen bij verhoogde temperaturen. Dit minimaliseert eventuele porositeit in geprinte onderdelen.
Gewenste materiaalmicrostructuren en -eigenschappen kunnen worden bereikt door middel van oplossen, veroudering of andere warmtebehandelingen die op maat zijn gemaakt voor de legering. Extra oppervlakteafwerkingsstappen zoals polijsten en coatings zorgen voor de vereiste oppervlaktekarakteristieken.
Industriële metaalpoeders voor additieve productie
Er zijn gespecialiseerde metaalpoeders ontwikkeld om ideale eigenschappen te bieden, zoals stroming, pakkingsdichtheid en laserabsorptie, wanneer ze worden verwerkt tijdens 3D-printen met poederbedfusie:
Metaalpoedereigenschappen en productiemethoden
Poeder eigendom | Typische specificatie | Productie methode |
---|---|---|
Maatbereik | 15-45 µm | Gasverneveling met inert gas |
Morfologie | Bolvormig | Zorgt voor een goede poederstroom en pakking |
Onzuiverheden | <100 ppm O2 | Behoudt de mechanische eigenschappen van de legering |
Schijnbare dichtheid | Tot 80% materiaaldichtheid | Geeft poederverpakking en verspreiding aan |
Stroomsnelheid | Hall-debietmeter >15s/50g | Zorg voor een soepele poederverspreiding tijdens het printen |
Nauwkeurige deeltjesgrootteverdelingen tussen ongeveer 15-45 micron zijn vereist voor afdrukken met hoge resolutie, goede oppervlakteafwerking en adequate vloei-eigenschappen. Bolvormige poedermorfologieën maken een soepele aanvoer en verspreiding van het poeder over het bed mogelijk.
Chemische zuiverheid is van cruciaal belang om de beoogde prestaties van het gedrukte materiaal te bereiken. Elke oxidatie of verontreiniging kan de sterkte en ductiliteit verminderen.
De stroomsnelheden worden getest volgens de ASTM B213-standaard met behulp van een Hall-stroommetertrechter. Voor consistente poederlagen is een goede schijnbare poederdichtheid van meer dan ongeveer 4 g/cc nodig.
Gas- en waterverneveling zijn gebruikelijke technieken om bolvormige metaalpoeders te produceren die voldoen aan de eisen voor additieve productie. Poeders worden gezeefd om uniforme deeltjesgroottes te garanderen.
Een 3D-printservice met metaalpoederbed kiezen
Het selecteren van de juiste AM-serviceprovider voor metaal is de sleutel tot het verkrijgen van gedrukte onderdelen van hoge kwaliteit. Hier zijn factoren waarmee u rekening moet houden:
Hoe u een 3D-printservice voor metaal kunt evalueren en selecteren
- Ervaring – Zoek naar jarenlange ervaring specifiek met metal AM om expertise te evalueren
- Materialen – Zorg ervoor dat de leverancier de benodigde metalen aanbiedt, zoals titanium, gereedschapsstaal en edele metalen
- Onderdeelgrootte – Kies service met bouwvolume dat past bij de vereiste onderdeelafmetingen
- Kwaliteitsprocessen – Moeten in alle fasen strikte kwaliteitscontroleprotocollen volgen
- Nabewerking – Kijk of de leverancier secundaire afwerking kan aanbieden, zoals CNC-bewerking
- Expertise in toepassingen – Belangrijk voor sterk gereguleerde sectoren zoals de lucht- en ruimtevaart en de medische sector
- Certificeringen – Zoek naar ISO- en branchespecifieke certificeringen voor processen
- Klantenservice – Responsief technisch ondersteuningsteam dat cruciaal is voor ontwerp en toepassingsadvies
- Levertijden – Begrijp de typische doorlooptijden en opties voor spoedbestellingen
- Prijzen – Houd rekening met de complexiteit van materiaal en geometrie, nabewerking en volume
- NDA/IP-bescherming – Uw eigen ontwerpgegevens moeten contractueel worden beschermd
Ontwerprichtlijnen voor metalen AM-onderdelen
Om de voordelen van metaaladditieve productie ten volle te benutten, moeten ontwerpen de DfAM-principes (Design for Additive Manufacturing) volgen:
Belangrijke Metal AM-ontwerprichtlijnen:
- Optimaliseer voor gewichtsvermindering met roosterstructuren
- Consolideer samenstellingen in afzonderlijke, complexe onderdelen
- Ontwerp interne functies zoals conforme koelkanalen
- Gebruik organische, vrije vormen die niet mogelijk zijn bij machinale bewerking
- Minimaliseer overhangen en ontwerp schuine steunen
- Oriënteer om de hoogte van het onderdeel te verkleinen en grote vlakke gebieden te vermijden
- Ontwerp gaten met schroefdraad om problemen met het verwijderen van de ondersteuning te voorkomen
- Zorg voor extra dikte op dunne wanden die gevoelig zijn voor porositeit
- Compenseer anisotrope materiaaleigenschappen in verschillende richtingen
- Ontwerp gecontroleerde porositeit in oppervlakken wanneer dit nuttig is
Complexe roosterstructuren met dunnere elementen kunnen het gewicht verminderen terwijl de sterkte behouden blijft wanneer ze in 3D worden geprint. Het consolideren van assemblages in afzonderlijke onderdelen is een groot voordeel ten opzichte van conventionele productie.
Koelkanalen en andere nuttige interne holtes hoeven niet langer te worden geboord en kunnen optimale organische paden volgen. Uitsteeksels die gevoelig zijn voor doorzakken kunnen worden vermeden door middel van schuine roosters of schuine ontwerpen.
De oriëntatie van de onderdelen moet gericht zijn op het minimaliseren van de Z-hoogte tijdens het afdrukken om restspanningen te verminderen. Dunne wanden die gevoelig zijn voor porositeit hebben mogelijk extra dikte nodig om de dichtheden van het doelmateriaal te bereiken.
Kostenmodellering en economie van Metal AM
Bepalen of metaaladditief economisch haalbaar is, hangt af van het beoordelen van alle kosten:
Kostenfactoren voor metaalpoederbed AM:
- Afschrijving van machines – Spreid hoge printerkosten over de levensduur
- Materiaalkosten – Poedermetalen kunnen variëren van $100-$500/kg
- Arbeid – Arbeid van de operator, ontwerp, nabewerking
- Energieverbruik – Lasers met hoog vermogen en andere systemen vereisen aanzienlijke elektriciteit
- Productiesnelheid – Printvolume per uur op basis van parameters, machinelimieten
- Nabewerking – Bewerkings- en afwerkingsstappen zorgen voor stilstand en kosten
- Facilitaire kosten – Benodigde poederhandlingsystemen, inert gas, ruimte
- Kwaliteitscontrole – Testen van onderdelen tijdens productie en proceskwalificatie
- Veiligheid en naleving – Voor gereguleerde toepassingen is de documentatie uitgebreid
De hoge kosten van metaalprinters betekenen dat het machinegebruik gedurende de hele levensduur moet worden geëvalueerd voor een optimaal gebruik door hogere productievolumes. De materiaalkosten zijn ook aanzienlijk, vooral voor exotische legeringen.
Er moet rekening worden gehouden met alle arbeid: operators, ingenieurs, ontwerpers, kwaliteitstechnici. Het energieverbruik is hoog. Stilstand na de verwerking verlaagt de productiesnelheid.
Voor lucht- en ruimtevaart- en medische toepassingen zijn de nalevingskosten zoals documentatie en kwaliteitssystemen omvangrijk. Zorgvuldige kostenmodellering bepaalt wanneer metaal-AM kosteneffectief is.
Trends en toekomst van de productie van metaaladditieven
Metaalpoederbedfusie kent een snelle ontwikkeling en acceptatie:
Toekomstige trends voor 3D-printen met metaalpoederbed:
- Grotere bouwvolumes – Behuizingen van meer dan 500 mm in blokjes in ontwikkeling
- Hogere bouwsnelheden – Verbeterde scanstrategieën en multi-lasersystemen
- Nieuwe materiaalopties – Meer legeringen zoals aluminium F357 en M300 maragingstaal
- Hybride productie – Gecombineerd printen, frezen en inspectie in één systeem
- Geautomatiseerde poederverwerking – Gesloten recyclingsystemen voor poederbeheer
- Nieuwe toepassingen – Uitbreiding naar de olie- en gas- en elektronicasector
- Dalende systeemkosten – Industrialisatie zal de printerkosten in de loop van de tijd verlagen
- Verbeterde materiaaleigenschappen – Door procesverfijningen en HIP-verdichting
- Uitgebreide metallurgie – Verbeterde karakterisering van microstructuren en eigenschappen
- Industriestandaarden – Voor processen en materiaalkwaliteit in de lucht- en ruimtevaart en de medische sector
Grotere bouwvolumes zullen complexere productie in grotere volumes mogelijk maken. Multi-laser optische systemen kunnen de bouwsnelheid dramatisch verhogen.
Gesloten poederverwerkingssystemen automatiseren recycling en hergebruik en verbeteren tegelijkertijd de kwaliteit en veiligheid. Jaarlijks worden er nieuwe exotische legeringsopties geïntroduceerd. Hybride productie combineert additieve en subtractieve processen voor volledige in-situ bewerking.
Dalende kosten naarmate de technologie volwassener wordt, zullen de toepassingen blijven uitbreiden. Verder materiaalonderzoek en benchmarking zullen de verwerkte legeringen uitbreiden en de materiaalprestaties verbeteren. Uitgebreid werk aan industriestandaarden heeft tot doel de adoptie in de lucht- en ruimtevaart-, medische en automobielsector te versnellen.
Conclusie
Deze gids behandelt de belangrijkste aspecten van 3D-printen met metaalpoederbedfusie, van het printproces en de materialen tot toepassingen, voordelen, beperkingen en trends.
Additieve productie met metalen maakt disruptieve innovaties in alle sectoren mogelijk dankzij de unieke mogelijkheden ervan. De technologie maakt gewichtsvermindering, consolidatie van onderdelen, ontwerpvrijheid, snelle prototyping en op maat gemaakte productie van metalen onderdelen mogelijk.
Ondanks beperkingen op het gebied van printerkosten, bouwgroottebeperkingen, nabewerking en materiaalopties, versnelt de adoptie van metaal-AM voor een groeiend aantal bedrijfskritische toepassingen in de lucht- en ruimtevaart-, medische, automobiel- en industriële sectoren.
Voortdurende procesverfijningen, nieuwe materialen, grotere bouwvolumes, hybride systemen, geautomatiseerde poederverwerking en dalende kosten zullen het toegenomen gebruik van 3D-printen van metaal voor productieonderdelen voor eindgebruik stimuleren. Deze gids behandelt de huidige staat en het traject van deze transformatieve productietechnologie.
Veelgestelde vragen over 3D-printen met metaalpoeder
Hier vindt u antwoorden op enkele veelgestelde vragen over additieve productie van metaalpoederbedfusie:
Vraag: Welke materialen kunnen 3D-geprint worden met behulp van metaalpoederbedfusie?
A: Veel voorkomende legeringen zijn titanium, aluminium, nikkel, roestvrij staal, gereedschapsstaal, kobaltchroom, edele metalen zoals goud en zilver, en koper. Nieuwe legeringen zijn voortdurend in ontwikkeling.
Vraag: Welke industrieën gebruiken tegenwoordig metaal-AM?
A: Luchtvaart-, medische, tandheelkundige, automobiel-, olie- en gas-, industriële machines en sieraden zijn de belangrijkste gebruikers van metaal-AM. De technologie is ideaal voor complexe onderdelen met een laag volume.
Vraag: Hoe nauwkeurig is 3D-printen met metaalpoederbed?
A: De dimensionale nauwkeurigheid kan oplopen tot ±0,1-0,2%, met fijnere resoluties rond ±50μm mogelijk op basis van parameters en nabewerking.
Vraag: Zijn er voor metaal AM speciale voorzieningen nodig?
A: Er is tijdens het printen een atmosfeer van inert gas nodig, meestal argon. Poederbehandelingssystemen met ontluchting en zeven worden ook aanbevolen. Er zijn verder geen bijzondere voorzieningen nodig.
Vraag: Welke factoren beïnvloeden de oppervlakteafwerking?
A: Laaghoogte, laserparameters, poedergrootteverdeling en nabewerking zoals polijsten hebben allemaal invloed op de oppervlakteafwerking. Ra-waarden onder 10 μm zijn mogelijk.
Vraag: Wat bepaalt de mechanische eigenschappen?
A: De samenstelling van de legering, de kwaliteit en morfologie van het poeder, procesparameters, warmtebehandelingen en HIP hebben allemaal invloed op de uiteindelijke eigenschappen van het geprinte metalen onderdeel.
Vraag: Hoe duur is het printen van metaalpoederbedden?
A: Printersystemen variëren van $100.000 tot meer dan $1.000.000. De materiaalkosten variëren per legering, doorgaans van $100-$500/kg. De exploitatiekosten zijn ook hoog.
Vraag: Hoe lang duurt het afdrukken voor een middelgroot onderdeel?
A: De bouwsnelheid bedraagt doorgaans 5-20 cm3/uur, afhankelijk van de geometrie van het onderdeel, het materiaal, de parameters en het printermodel. Een onderdeel ter grootte van een schoenendoos kan 5-15 uur duren.
Vraag: Welke onderdelen kan een metaalprinter maken?
A: De huidige maximale bouwvolumes zijn ongeveer 500 x 500 x 500 mm, maar grotere systemen zijn in ontwikkeling. Grotere delen kunnen in veelvouden worden gesegmenteerd.
Vraag: Welke nabewerking is vereist na metal AM?
A: Ondersteuning verwijderen, spanning verlichten, machinaal bewerken, boren, oppervlakteafwerking, warmtebehandelingen en soms heet isostatisch persen.
Delen op
MET3DP Technology Co, LTD is een toonaangevende leverancier van additieve productieoplossingen met hoofdkantoor in Qingdao, China. Ons bedrijf is gespecialiseerd in 3D printapparatuur en hoogwaardige metaalpoeders voor industriële toepassingen.
Onderzoek om de beste prijs en een op maat gemaakte oplossing voor uw bedrijf te krijgen!
gerelateerde artikelen
Over Met3DP
Recente update
Ons product
NEEM CONTACT MET ONS OP
Nog vragen? Stuur ons nu een bericht! Na ontvangst van uw bericht behandelen wij uw verzoek met een heel team.