3D Printing Dental Implant Abutments
Inhoudsopgave
Introduction: The Growing Role of 3D Printing in Dental Implantology
The landscape of dental implantology is undergoing a significant transformation, driven by advancements in digital technologies and innovative manufacturing processes. Among these, metal 3d printen, also known as metal additive manufacturing, is emerging as a powerful tool for the fabrication of custom dental implant abutments. These critical components serve as the interface between the dental implant fixture embedded in the jawbone and the prosthetic crown, bridge, or denture. The ability to precisely tailor abutments to individual patient needs offers numerous advantages over traditional manufacturing methods, paving the way for improved treatment outcomes, enhanced patient comfort, and streamlined workflows for dental professionals. This blog post will delve into the intricacies of using metal 3D printing for dental implant abutments, exploring its applications, benefits, material considerations, and how businesses can leverage this technology through reliable service providers like Metaal3DP.
What are 3D Printed Dental Implant Abutments Used For? Applications and Benefits for Dental Professionals
3D printed dental implant abutments play a crucial role in restorative dentistry, primarily functioning as a custom-designed connector that bridges the gap between the surgically placed implant and the final prosthetic restoration. Their precise fit ensures optimal load distribution, which is vital for the long-term success and stability of the dental implant. The applications of 3D printed dental implant abutments are diverse and cater to a wide range of clinical scenarios:
- Single Tooth Replacements: Creating abutments that perfectly match the emergence profile of a natural tooth, leading to aesthetically pleasing and functional single-unit restorations.
- Multiple Tooth Restorations: Fabricating abutments for implant-supported bridges, ensuring accurate alignment and support for multi-unit prostheses.
- Full Arch Restorations: Designing custom abutments as part of full-arch implant-supported dentures or fixed hybrid prostheses, providing a stable and comfortable foundation.
- Immediate Loading Protocols: Manufacturing temporary or definitive abutments for immediate placement and loading onto dental implants, reducing treatment time for patients.
- Complex Anatomical Situations: Addressing cases with unique gingival contours or implant angulations where standard, off-the-shelf abutments may compromise aesthetics or function.
The benefits of utilizing 3D printed dental implant abutments extend to both dental professionals and their patients:
- Enhanced Precision and Fit: Additive manufacturing allows for the creation of abutments that are precisely adapted to the patient’s intraoral environment, as determined by digital scans. This accuracy minimizes the risk of ill-fitting restorations and potential complications.
- Improved Aesthetics: Custom-designed abutments can optimize the emergence profile, supporting natural-looking soft tissue contours and enhancing the overall aesthetic outcome, particularly in the anterior region.
- Increased Patient Comfort: A precisely fitting abutment contributes to better prosthetic stability and reduces the likelihood of discomfort or irritation for the patient.
- Streamlined Workflow: Digital design and 3D printing can simplify the restorative process, potentially reducing the number of patient visits and the time required for abutment fabrication.
- Veelzijdigheid van materiaal: Metal 3D printing allows for the use of biocompatible materials like titanium alloys and cobalt-chromium-molybdenum, ensuring the longevity and safety of the restoration. Metaal3DP offers a range of high-quality metal powders suitable for dental applications.
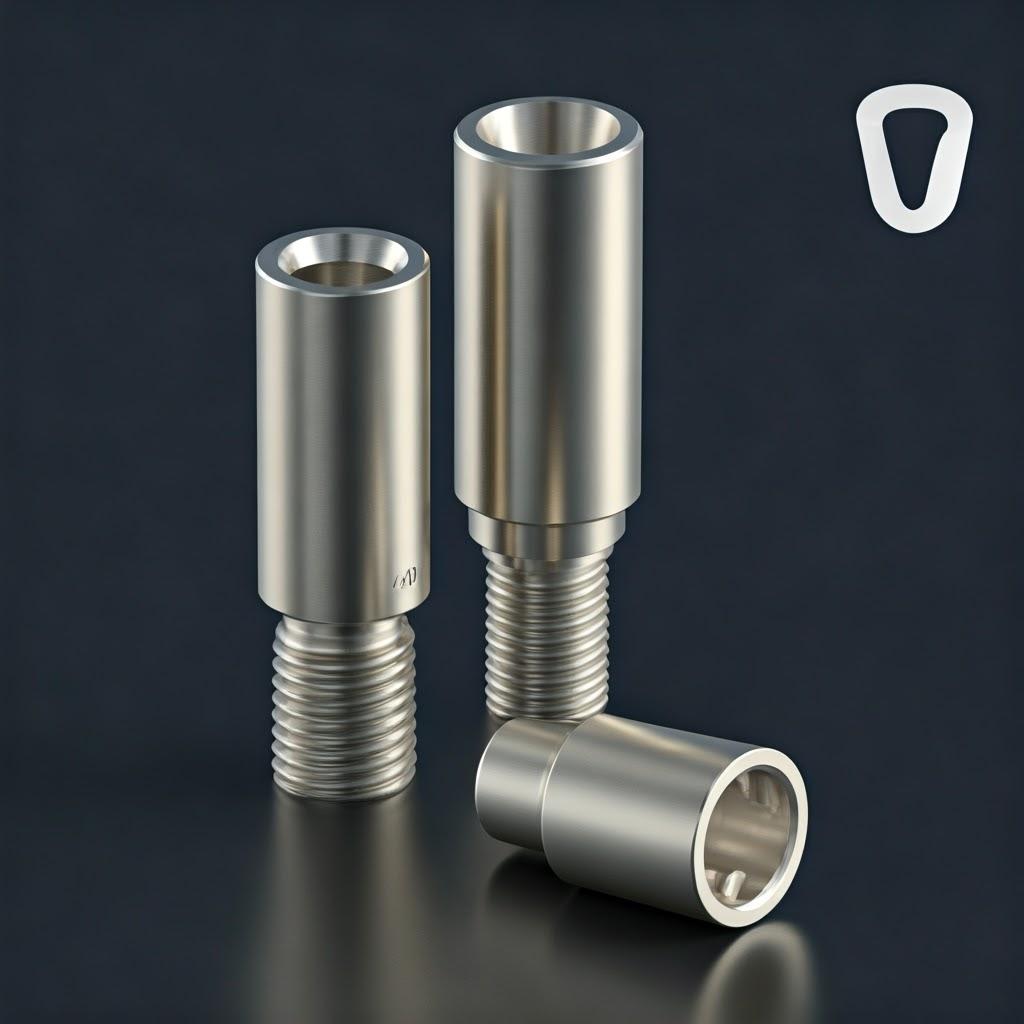
Why Choose Metal 3D Printing for Dental Implant Abutment Manufacturing? Advantages for Suppliers and Wholesale Buyers
For suppliers and wholesale buyers in the dental industry, metal 3D printing presents a compelling alternative to traditional methods of manufacturing dental implant abutments, offering several key advantages:
- Customization and Scalability: Metal 3D printing enables the production of highly customized abutments tailored to individual patient specifications derived from digital scans. This level of personalization is difficult and costly to achieve with conventional subtractive manufacturing. Furthermore, once a design is finalized, it can be easily replicated, allowing for scalable production to meet varying demands.
- Complex Geometries and Design Freedom: Additive manufacturing processes liberate designers from the constraints of traditional machining. Intricate internal structures, optimized emergence profiles, and complex connections can be readily produced, leading to improved functionality and aesthetics. This design freedom can translate to innovative product offerings for suppliers.
- Minder materiaalverspilling: Unlike subtractive methods where material is removed to create the final shape, 3D printing adds material layer by layer. This significantly reduces material waste, leading to potential cost savings for manufacturers and a more sustainable production process. Metal3DP’s advanced powder making system ensures efficient material utilization.
- Faster Prototyping and Production Cycles: The digital workflow of 3D printing allows for rapid prototyping and iteration. Design changes can be implemented quickly, and production can commence without the need for extensive tooling or setup times, potentially shortening lead times for wholesale buyers.
- Productie op aanvraag: Metal 3D printing facilitates on-demand manufacturing, allowing suppliers to produce abutments only when they are needed. This eliminates the need for large inventories of standard abutments, reducing storage costs and the risk of obsolescence.
- Potential for Cost Reduction: While the initial investment in 3D printing equipment may seem significant, the long-term cost benefits, including reduced material waste, lower tooling costs, and the ability to produce complex geometries in a single step, can lead to overall cost reductions for suppliers and potentially more competitive pricing for wholesale buyers.
- Access to Advanced Materials: Metal 3D printing is compatible with a range of high-performance materials, such as CoCrMo and Ti-6Al-4V, which offer excellent biocompatibility, mechanical strength, and corrosion resistance – crucial properties for dental implant abutments.
Recommended Materials for 3D Printed Dental Implant Abutments: Properties and Applications of CoCrMo and Ti-6Al-4V
The selection of appropriate materials is paramount in the 3D printing of dental implant abutments to ensure biocompatibility, mechanical integrity, and long-term clinical success. Two of the most commonly recommended metal powders for this application are Cobalt-Chromium-Molybdenum (CoCrMo) and Titanium-6Aluminum-4Vanadium (Ti-6Al-4V). Metaal3DP offers high-quality powders of both these alloys.
Kobalt-chroom-molybdeen (CoCrMo)
- Eigenschappen:
- Hoge sterkte en hardheid: CoCrMo alloys exhibit excellent mechanical properties, including high yield strength and hardness, making them suitable for load-bearing dental applications.
- Uitstekende corrosiebestendigheid: This alloy demonstrates superior resistance to corrosion in the oral environment, minimizing the risk of degradation and ensuring long-term biocompatibility.
- Good Biocompatibility: CoCrMo alloys are generally well-tolerated by the human body and have a long history of successful use in medical implants.
- High Stiffness (Young’s Modulus): The high stiffness of CoCrMo can provide a rigid connection between the implant and the prosthetic restoration.
- Lower Density than Some Alternatives: While still a metal, CoCrMo often has a lower density compared to some other metallic biomaterials.
- Applications in Dental Implant Abutments: Due to its strength and corrosion resistance, CoCrMo is often preferred for situations where high mechanical loads are anticipated, such as in posterior restorations or for patients with parafunctional habits. It can also be a suitable choice when a rigid connection is desired.
Titanium-6Aluminum-4Vanadium (Ti-6Al-4V)
- Eigenschappen:
- Uitstekende biocompatibiliteit: Titanium alloys are renowned for their exceptional biocompatibility and osseointegration properties, promoting direct bone-to-implant contact.
- Hoge verhouding sterkte/gewicht: Ti-6Al-4V offers a high strength relative to its weight, resulting in lightweight yet durable abutments.
- Goede corrosiebestendigheid: Titanium forms a passive oxide layer that provides excellent resistance to corrosion in the oral environment.
- Lower Stiffness (Young’s Modulus) than CoCrMo: The lower stiffness of titanium can potentially offer a more physiological load transfer to the surrounding bone.
- Well-Established Material in Implantology: Ti-6Al-4V has a long and successful history of use in dental implants and related components.
- Applications in Dental Implant Abutments: Ti-6Al-4V is a versatile material suitable for a wide range of dental implant abutment applications, including anterior and posterior restorations. Its excellent biocompatibility and osseointegration properties make it a preferred choice for many clinicians.
The choice between CoCrMo and Ti-6Al-4V for 3D printed dental implant abutments often depends on the specific clinical requirements, the location of the implant, the patient’s biomechanical factors, and the desired aesthetic outcome. Consulting with a knowledgeable metal 3D printing service provider like Metaal3DP can help dental professionals and procurement managers make informed decisions regarding material selection.
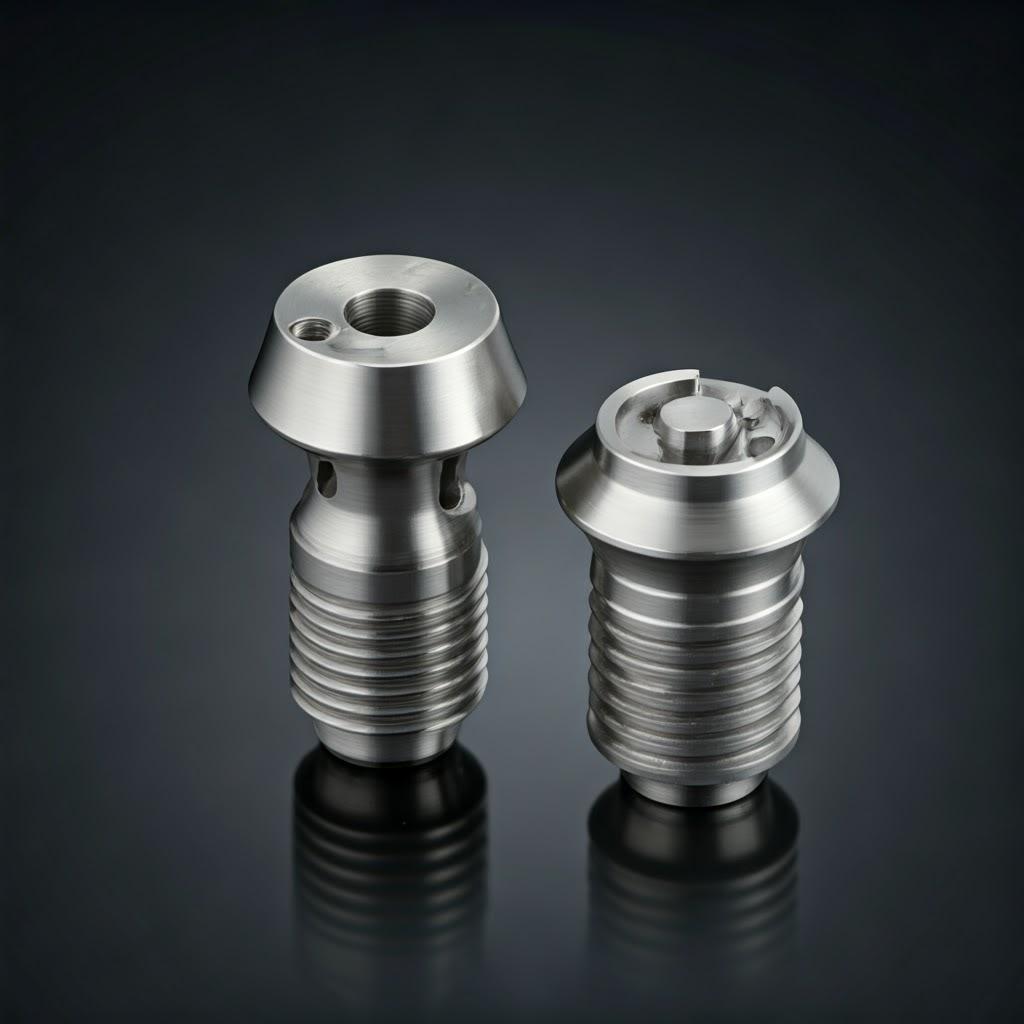
Design Considerations for Optimized 3D Printed Dental Abutments: Ensuring Fit and Functionality
The design phase is critical for achieving successful outcomes with 3D printed dental implant abutments. Optimizing the design for additive manufacturing processes and the specific clinical requirements can significantly impact the fit, functionality, and aesthetics of the final restoration. Several key considerations should be taken into account:
- Emergence Profile: The contour of the abutment as it emerges from the soft tissue is crucial for supporting natural-looking gingival architecture and achieving optimal aesthetics, especially in the anterior region. 3D printing allows for the creation of complex emergence profiles that closely mimic natural tooth contours.
- Margin Design: The location and design of the abutment margin must be carefully planned to ensure a precise fit with the prosthetic crown and to facilitate proper hygiene. Subgingival, equigingival, or supragingival margins can be designed based on the clinical situation.
- Connection to the Implant: The internal connection between the abutment and the dental implant fixture must be designed with high precision to ensure a secure and stable fit. Compatibility with various implant systems and connection types (e.g., internal hex, conical connection) is essential.
- Screw Access Channel: For screw-retained restorations, the angulation and diameter of the screw access channel need to be carefully considered for ease of access during prosthetic placement and removal. The design should minimize aesthetic compromises.
- Material Distribution and Strength: The internal structure and wall thickness of the abutment should be optimized to provide sufficient strength and support for the prosthetic load while minimizing material usage and weight. Finite element analysis (FEA) can be a valuable tool in this optimization process.
- Surface Texture: The surface texture of the abutment, particularly in the transmucosal area, can influence soft tissue attachment and healing. Micro-rough surfaces may promote better integration with the gingiva.
- Integration of Scan Bodies: For digital workflows, the abutment design should be compatible with intraoral scan bodies used for capturing the implant position and orientation. This ensures accurate transfer of information for prosthetic design.
- Design for Manufacturing (DFM): Considerations specific to the metal 3D printing process, such as orientation on the build platform, support structure requirements, and potential for distortion, should be integrated into the design phase to ensure successful and accurate fabrication. Consulting with the experts at Metaal3DP can provide valuable insights into DFM for metal additive manufacturing.
Achieving Precision in 3D Printed Dental Abutments: Tolerance, Surface Finish, and Dimensional Accuracy for Medical Applications
In the highly regulated field of medical devices, particularly dental implants and their components, precision is paramount. 3D printed dental abutments must meet stringent requirements for tolerance, surface finish, and dimensional accuracy to ensure proper fit, functionality, and long-term clinical success.
- Tolerance: Tolerance refers to the allowable variation in the dimensions of a manufactured part. For dental abutments, tight tolerances are crucial for the accuracy of the implant-abutment connection and the abutment-prosthetic crown interface. Metal 3D printing technologies, when properly controlled and calibrated, can achieve impressive dimensional accuracy, often within tens of micrometers. Factors influencing achievable tolerances include the type of 3D printing technology used (e.g., Direct Metal Laser Sintering – DMLS, Selective Laser Melting – SLM), the material being printed, the build parameters, and post-processing steps.
- Afwerking oppervlak: The surface finish of a dental abutment can affect its interaction with both hard and soft tissues. A smooth surface finish in the supragingival area is generally preferred for hygiene, while a slightly rougher surface in the transmucosal region may promote better soft tissue attachment. Metal 3D printed parts typically have a surface roughness that depends on the powder particle size and the laser parameters. Post-processing techniques like polishing or machining can be employed to achieve the desired surface finish.
- Maatnauwkeurigheid: Dimensional accuracy refers to how closely the dimensions of the printed part match the intended design. High dimensional accuracy is essential for the precise fit of the abutment to the implant and the subsequent prosthetic restoration. Factors affecting dimensional accuracy include material shrinkage during solidification, thermal gradients during the printing process, and potential distortion. Careful process control, optimized build orientation, and the use of support structures can help to minimize dimensional inaccuracies.
Metal3DP’s commitment to industry-leading accuracy and reliability ensures that their 3D printing services for dental implant abutments meet the stringent precision requirements of the dental industry.
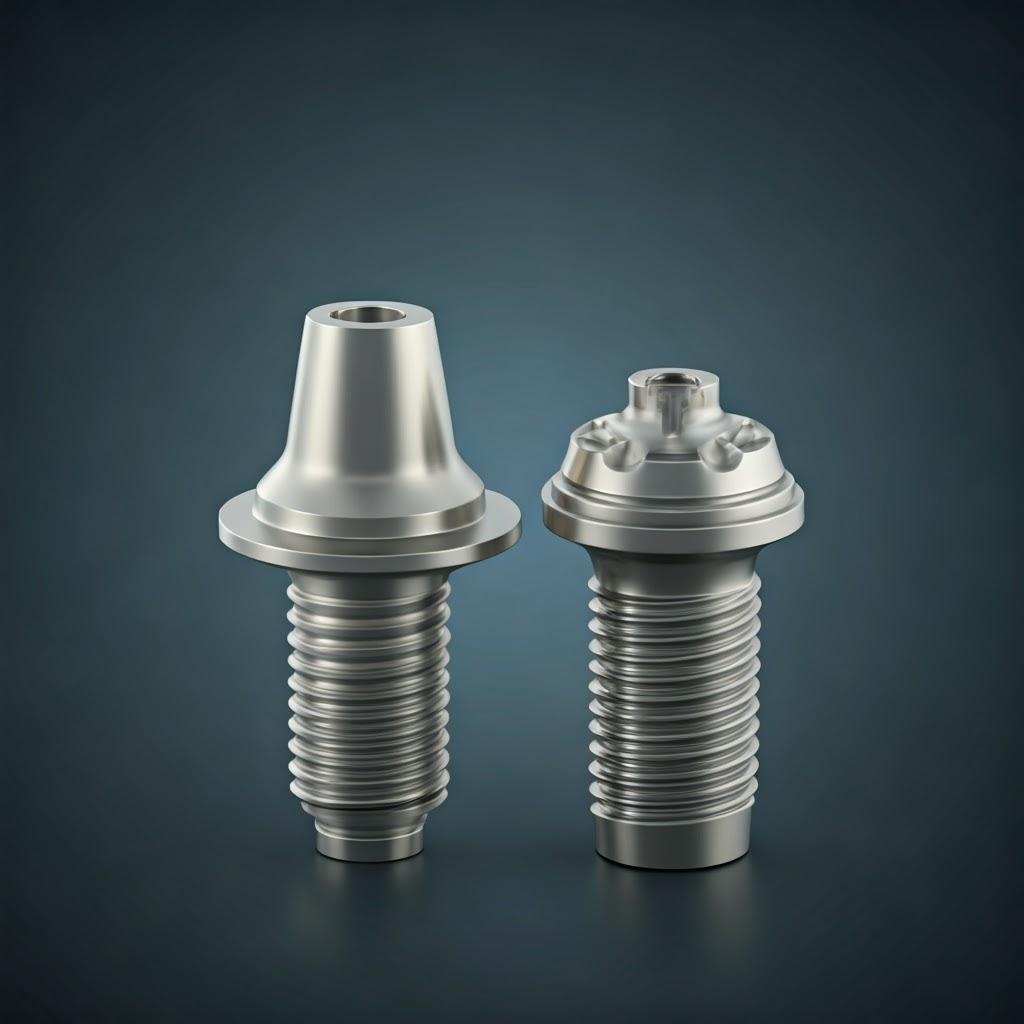
Post-Processing of 3D Printed Dental Implant Abutments: Enhancing Biocompatibility and Aesthetics
While metal 3D printing offers significant advantages in creating complex geometries, post-processing steps are often necessary to achieve the final desired properties, biocompatibility, and aesthetics of dental implant abutments. Common post-processing requirements include:
- Ondersteuning verwijderen: Metal 3D printing typically requires the use of support structures to prevent distortion and ensure the stability of the part during the build process. These supports need to be carefully removed after printing, often using specialized tools or machining techniques.
- Schoonmaken: Residual powder particles may adhere to the surface of the printed abutment and need to be removed through cleaning processes such as ultrasonic cleaning or blasting with inert media.
- Hittebehandeling: Depending on the material and the printing process, heat treatment may be required to relieve internal stresses, optimize the mechanical properties (e.g., hardness, strength), and ensure the desired microstructure of the metal.
- Afwerking oppervlak: To achieve the required surface roughness for different areas of the abutment (e.g., smooth for supragingival, slightly rough for transmucosal), various surface finishing techniques can be employed, including polishing, grinding, blasting, or etching.
- Bewerking: In some cases, high-precision features, such as the implant-abutment connection or the prosthetic interface, may require post-machining to achieve the necessary tight tolerances and surface finish. CNC machining can be used for this purpose.
- Oppervlaktecoating: To enhance biocompatibility, corrosion resistance, or aesthetics, surface coatings may be applied to the 3D printed abutments. For example, titanium abutments may undergo anodization to improve their oxide layer and aesthetic appearance.
- Kwaliteitscontrole en inspectie: Rigorous quality control procedures, including dimensional measurements and surface inspection, are essential to ensure that the final 3D printed dental abutments meet the required specifications and quality standards for medical devices.
Choosing a metal 3D printing service provider like Metaal3DP that offers comprehensive post-processing capabilities and adheres to strict quality control standards is crucial for obtaining high-quality, готовые к использованию dental implant abutments.
Addressing Common Challenges in 3D Printing Dental Abutments: Solutions for Accuracy and Material Properties
While metal 3D printing offers numerous advantages, several challenges can arise during the fabrication of dental implant abutments. Understanding these potential issues and implementing appropriate solutions is essential for achieving consistent and high-quality results. Common challenges include:
- Distortion and Warping: Thermal stresses during the printing process can lead to distortion or warping of the abutment, particularly for complex geometries or thin-walled structures. Optimizing the build orientation, using appropriate support structures, and carefully controlling the printing parameters can mitigate these issues.
- Poreusheid: The presence of pores within the printed material can compromise its mechanical strength and biocompatibility. Optimizing the laser power, scan speed, and powder bed density are crucial for minimizing porosity. Metal3DP’s advanced powder making system contributes to the production of dense, high-quality parts.
- Oppervlakteruwheid: Achieving the desired surface finish directly from the 3D printing process can be challenging. Post-processing techniques like polishing or machining are often necessary to meet the specific requirements for different areas of the abutment.
- Dimensional Inaccuracies: Factors such as material shrinkage and thermal gradients can lead to deviations from the intended dimensions. Precise calibration of the 3D printer, careful material selection, and compensation strategies in the design phase can help to minimize these inaccuracies.
- Support Removal Challenges: Removing support structures from intricate abutment designs can be difficult and may leave surface artifacts. Optimizing support design and placement, as well as employing appropriate removal techniques, are important considerations.
- Material Property Consistency: Ensuring consistent mechanical properties throughout the printed part can be challenging. Careful control of the printing parameters and post-processing heat treatments are essential for achieving uniform material properties.
- Naleving van regelgeving: Medical devices like dental implant abutments are subject to stringent regulatory requirements. Ensuring that the entire manufacturing process, including 3D printing and post-processing, complies with relevant standards (e.g., ISO 13485) is crucial.
By understanding these potential challenges and working with an experienced metal 3D printing service provider like Metaal3DP that has the expertise and quality control systems in place, dental professionals and procurement managers can effectively mitigate these risks and obtain high-quality 3D printed dental implant abutments.
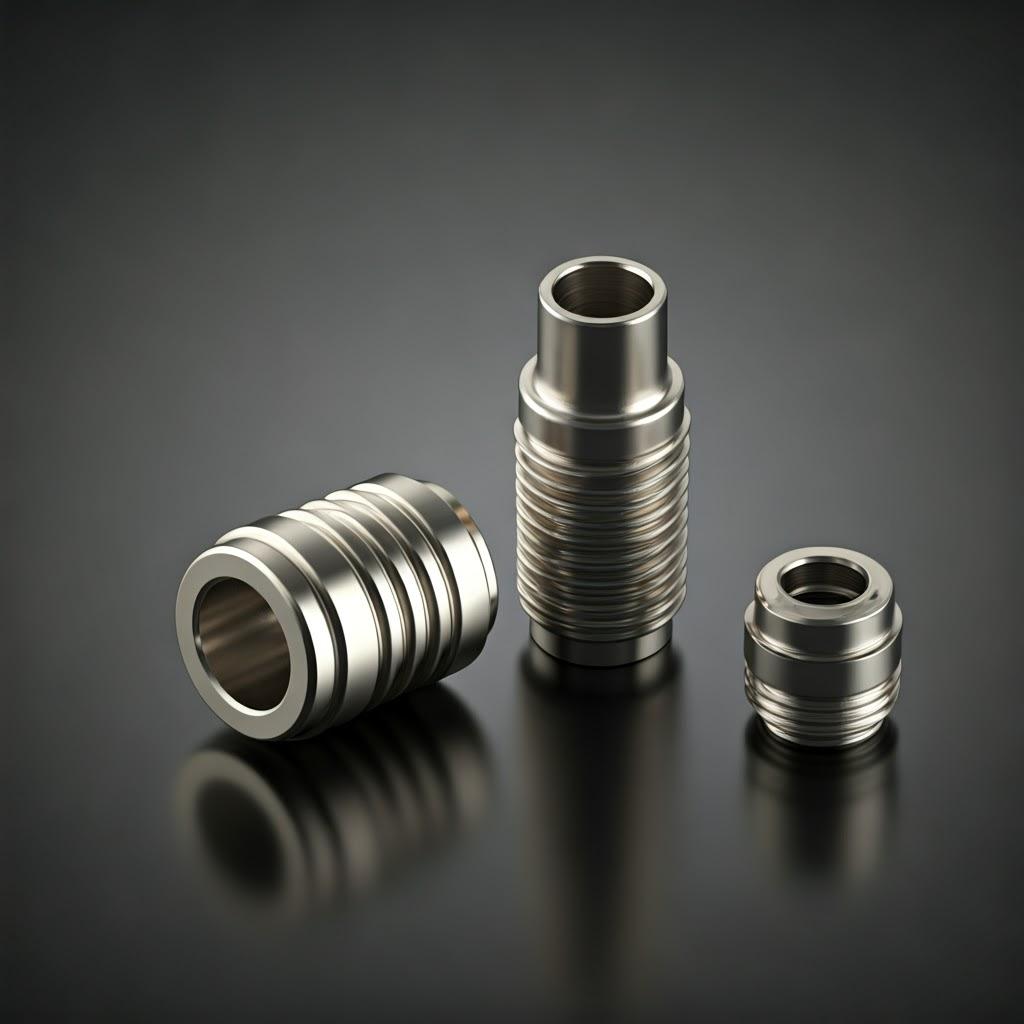
Selecting a Reliable Metal 3D Printing Service for Dental Applications: Key Factors for Procurement Managers
Choosing the right metal 3D printing service provider is a critical decision for dental professionals and procurement managers seeking high-quality dental implant abutments. Several key factors should be carefully evaluated to ensure a successful partnership:
- Material Capabilities: The service provider should offer a range of biocompatible metal powders suitable for dental applications, such as CoCrMo and Ti-6Al-4V. Verify the quality and traceability of their materials. Metaal3DP provides a diverse portfolio of high-quality metal powders.
- Printing Technology and Equipment: Ensure the provider utilizes advanced metal 3D printing technologies (e.g., DMLS, SLM) capable of achieving the required precision, surface finish, and material properties for dental abutments. Their equipment should be well-maintained and regularly calibrated.
- Post-Processing Services: A comprehensive suite of post-processing services, including support removal, cleaning, heat treatment, surface finishing, and potentially machining, is essential to obtain готовые к использованию abutments. Inquire about their capabilities and quality control procedures for each step.
- Quality Management System: The service provider should have a robust quality management system in place, ideally with certifications relevant to medical device manufacturing (e.g., ISO 13485). This ensures adherence to strict quality standards and regulatory requirements.
- Design and Engineering Support: Access to experienced design and engineering teams can be invaluable for optimizing abutment designs for 3D printing, ensuring manufacturability, and addressing any technical challenges.
- Experience in Dental Applications: Prior experience in manufacturing dental components is a significant advantage. A provider with a proven track record in the dental industry will have a better understanding of the specific requirements and challenges involved.
- Turnaround Time and Scalability: Evaluate the provider’s lead times for production and their ability to scale up production to meet your demands, especially for wholesale orders.
- Cost Structure: Understand the pricing model and all associated costs, including design, printing, materials, post-processing, and shipping. Compare quotes from multiple providers to ensure competitive pricing.
- Communication and Customer Support: Effective communication and responsive customer support are crucial for a smooth and efficient collaboration. Assess their responsiveness and willingness to address your questions and concerns.
- Confidentiality and Data Security: For custom designs and patient-specific information, ensure the provider has robust confidentiality agreements and data security protocols in place.
By carefully considering these factors, dental professionals and procurement managers can select a reliable metal 3D printing service provider that meets their specific needs and delivers high-quality dental implant abutments.
Cost-Effectiveness and Lead Times for 3D Printed Dental Implant Abutments: A Comprehensive Overview for Buyers
The cost-effectiveness and lead times associated with 3D printed dental implant abutments are important considerations for dental practices, laboratories, and wholesale buyers. These factors can vary depending on several parameters:
Kostenfactoren:
- Complex ontwerp: More intricate designs may require more design time and computational resources, potentially increasing the initial cost.
- Material Volume: The amount of metal powder used to print the abutment directly impacts the material cost. Optimized designs that minimize material usage can lead to cost savings.
- Bouwtijd: Longer print times on the 3D printer translate to higher machine operating costs. Factors influencing build time include the size and complexity of the part, the number of parts being printed simultaneously, and the layer height used.
- Vereisten voor nabewerking: The extent of post-processing required (e.g., support removal, extensive polishing, machining) will influence the overall cost.
- Hoeveelheid: Similar to traditional manufacturing, the cost per unit for 3D printed abutments can decrease with larger production volumes.
- Service Provider Pricing: Different service providers will have varying pricing structures based on their equipment, expertise, quality systems, and overhead costs. Obtaining quotes from multiple vendors is advisable. Contacteer Metal3DP to explore their pricing options.
Doorlooptijden:
- Design and Pre-processing: The initial design phase and the preparation of the 3D printing build files will contribute to the overall lead time.
- Afdrukken tijd: The actual printing time depends on the size and complexity of the abutment and the number of parts being printed in a single build.
- Post-Processing Time: The time required for post-processing steps such as support removal, cleaning, heat treatment, and surface finishing will add to the total lead time.
- Kwaliteitscontrole en inspectie: Thorough quality checks are necessary before shipment, which can also impact the lead time.
- Shipping Time: The time taken for the finished abutments to be shipped to the customer needs to be factored in.
While the initial cost per unit for highly customized, low-volume 3D printed abutments might be higher than that of standard, mass-produced abutments, the benefits of customization, precision, and potentially faster turnaround times for individual cases can offer significant value. For larger volumes, optimizing designs for 3D printing and working with a capable service provider can lead to cost-competitive solutions with shorter lead times compared to traditional custom manufacturing.
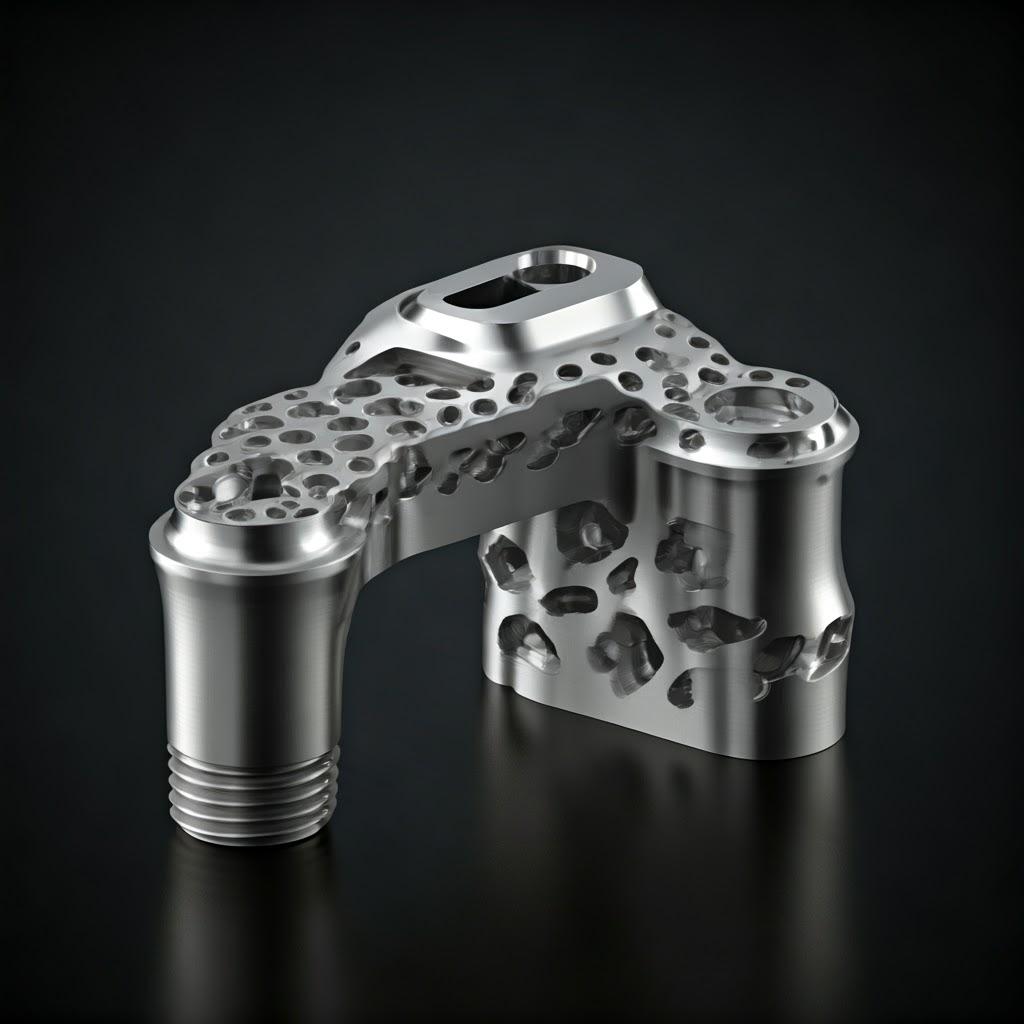
Frequently Asked Questions (FAQ) About 3D Printing Dental Implant Abutments
- Q: Are 3D printed metal dental implant abutments biocompatible?
- A: Yes, when manufactured using biocompatible materials like CoCrMo and Ti-6Al-4V and processed according to medical device standards, 3D printed metal dental implant abutments are biocompatible and safe for intraoral use. Reputable providers like Metaal3DP use certified materials and adhere to strict quality control procedures.
- Q: Can 3D printed abutments be customized to individual patient needs?
- A: Absolutely. The primary advantage of using 3D printing for dental implant abutments is the ability to create highly customized designs based on digital scans of the patient’s oral anatomy. This ensures an optimal fit, emergence profile, and aesthetic outcome.
- Q: What is the typical lifespan of a 3D printed metal dental implant abutment?
- A: When fabricated from high-quality materials and properly designed and placed, 3D printed metal dental implant abutments can have a long lifespan, comparable to traditionally manufactured abutments. The longevity depends on factors such as the material used, the patient’s oral hygiene, and the occlusal forces.
- Q: What kind of prosthetic restorations can be supported by 3D printed abutments?
- A: 3D printed dental implant abutments can support a wide range of prosthetic restorations, including single crowns, multi-unit bridges, and full-arch dentures. The design of the abutment is tailored to the specific type of restoration.
Conclusion: The Future of Dental Implantology with Metal Additive Manufacturing
Metal 3D printing is revolutionizing the field of dental implantology by offering a powerful and versatile method for fabricating custom dental implant abutments. The ability to create highly precise, patient-specific components with biocompatible materials like CoCrMo and Ti-6Al-4V provides significant advantages in terms of fit, aesthetics, and potential for improved treatment outcomes. For dental professionals, laboratories, and wholesale buyers, understanding the benefits, design considerations, material options, and how to choose a reliable service provider like Metaal3DP is crucial for leveraging the full potential of this transformative technology. As the technology continues to advance and become more accessible, metal additive manufacturing will undoubtedly play an increasingly vital role in shaping the future of restorative dentistry and enhancing the quality of care for patients.
Delen op
MET3DP Technology Co, LTD is een toonaangevende leverancier van additieve productieoplossingen met hoofdkantoor in Qingdao, China. Ons bedrijf is gespecialiseerd in 3D printapparatuur en hoogwaardige metaalpoeders voor industriële toepassingen.
Onderzoek om de beste prijs en een op maat gemaakte oplossing voor uw bedrijf te krijgen!
gerelateerde artikelen
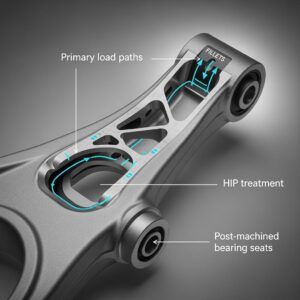
Metal 3D Printing for U.S. Automotive Lightweight Structural Brackets and Suspension Components
Lees verder "Over Met3DP
Recente update
Ons product
NEEM CONTACT MET ONS OP
Nog vragen? Stuur ons nu een bericht! Na ontvangst van uw bericht behandelen wij uw verzoek met een heel team.