Inleiding tot Directed Energy Deposition
Inhoudsopgave
Stel je voor dat je laag voor laag complexe metaalstructuren bouwt, met nauwkeurige controle over materiaaleigenschappen en minimaal afval. Dit is geen sciencefiction; het is de realiteit van Gerichte energiedepositie (DED), een revolutionaire 3D-printtechnologie die het productielandschap verandert.
Directed Energy Deposition, ook bekend onder termen als Laser Engineered Net Shaping (LENS) of Direct Metal Deposition (DMD), is een additief productieproces dat gebruik maakt van een gerichte energiebron, zoals een laser- of elektronenstraal, om metaalgrondstof te smelten en op een substraat te deponeren. Zie het als een hightech laspistool op steroïden, dat ingewikkelde vormen maakt in plaats van alleen maar stukken samen te voegen.
Deze gids duikt diep in de wereld van DED, verkent de functionaliteiten, de verschillende metaalpoeders die worden gebruikt, de toepassingen in verschillende industrieën en de voordelen en beperkingen die deze opwindende technologie definiëren.
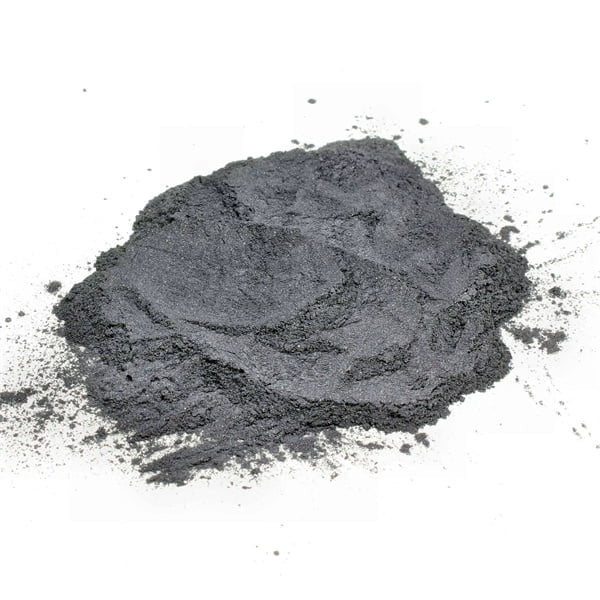
Hoe Gerichte energiedepositie Werken
DED werkt met een synergie van drie belangrijke componenten:
- Energiebron: Het hart van DED ligt in de geconcentreerde energiebron. Lasers en elektronenbundels zijn de meest gebruikte keuzes en bieden verschillende voordelen. Lasers bieden een hoge precisie en controle, maar kunnen beperkt worden door materiaalreflectie. Elektronenbundels daarentegen gaan dieper, bieden een betere penetratie voor dikkere constructies, maar vereisen een vacuümkamer voor gebruik.
- Grondstoffen: De bouwsteen van uw 3D-creatie komt in de vorm van metaalpoeder. DED gebruikt een breed scala aan metaalpoeders, elk met unieke eigenschappen en toepassingen. We zullen later dieper ingaan op de fascinerende wereld van metaalpoeders.
- Leveringssysteem: De magie gebeurt niet zonder een toevoermechanisme. DED maakt gebruik van een mondstuk dat het metaalpoeder in het smeltbad voert dat door de energiebron wordt gecreëerd. Deze nauwkeurige coördinatie zorgt voor een naadloos laag-voor-laag depositieproces.
De hele bewerking wordt gestuurd door computerondersteunde ontwerpsoftware (CAD), die uw digitale blauwdruk vertaalt in precieze instructies voor het DED-systeem. Hierdoor kunnen ingewikkelde geometrieën, holle structuren en vormen worden gemaakt die met traditionele productietechnieken onmogelijk zouden zijn.
Een wereld van metaalpoeders: Brandstof voor DED Creaties
Het succes van DED hangt af van de keuze van het juiste metaalpoeder. Net als bij het kiezen van de perfecte ingrediënten voor een recept, zijn de eigenschappen van het poeder van grote invloed op de eigenschappen van het eindproduct. Hier volgt een blik op tien populaire metaalpoeders die worden gebruikt bij DED:
1. Titaan (Ti): Lichtgewicht, sterk en corrosiebestendig, titanium is een populaire keuze voor de ruimtevaart, medische implantaten en sportartikelen toepassingen. De biocompatibiliteit maakt het ideaal voor protheses en tandheelkundige implantaten.
2. Inconel (nikkel-chroomlegering): Inconel staat bekend om zijn uitzonderlijke sterkte bij hoge temperaturen en weerstand tegen oxidatie en corrosie en vindt toepassingen in straalmotoren, warmtewisselaars en chemische verwerkingsapparatuur.
3. Roestvrij staal (SS): Roestvast staal is een veelzijdige en kosteneffectieve optie en biedt een goede balans tussen sterkte, corrosiebestendigheid en betaalbaarheid. Het wordt veel gebruikt in auto-onderdelen, medische apparatuur en algemene industriële toepassingen.
4. Aluminium (Al): Lichtgewicht en gemakkelijk verkrijgbaar, aluminium is een populaire keuze voor toepassingen waar gewichtsvermindering van cruciaal belang is, zoals ruimtevaartonderdelen en auto-onderdelen.
5. Nikkel (Ni): Nikkel heeft een goede corrosiebestendigheid en elektrische geleidbaarheid en wordt gebruikt in elektronica, chemische verwerkingsapparatuur en zelfs in sommige munttoepassingen.
6. Kobalt-chroom (CoCr): Deze biocompatibele legering heeft een hoge sterkte en slijtvastheid, waardoor het de voorkeur geniet voor orthopedische implantaten en gewrichtsprothesen.
7. Koper (Cu): Koper is een uitstekende geleider van warmte en elektriciteit en vindt toepassingen in koellichamen, elektrische componenten en zelfs voor het maken van ingewikkelde microfluïdische kanalen.
8. Wolfraam (W): Wolfraam staat bekend om zijn ongelooflijk hoge smeltpunt en uitzonderlijke slijtvastheid en wordt gebruikt voor toepassingen als laselektroden, pantserdoorborende projectielen en ovenonderdelen voor hoge temperaturen.
9. Molybdeen (Mo): Net als wolfraam biedt molybdeen sterkte bij hoge temperaturen en vindt het toepassingen in onderdelen voor de ruimtevaart, kernreactoren en gloeidraden voor verlichtingstoepassingen.
10. Hastelloy: Deze familie van op nikkel gebaseerde superlegeringen heeft een uitzonderlijke weerstand tegen een breed scala van corrosieve omgevingen, waardoor ze ideaal zijn voor toepassingen in de chemische verwerkingsindustrie, de olie- en gasindustrie en energieopwekking.
Deze lijst is slechts een tipje van de sluier van het enorme aanbod metaalpoeders dat beschikbaar is voor DED. De keuze van het poeder hangt af van de gewenste eigenschappen van het eindproduct, zoals sterkte, gewicht, corrosiebestendigheid en thermische geleidbaarheid.
Verder dan de basis: Een overzicht van de eigenschappen van metaalpoeders
Eigendom | Beschrijving | Belang bij DED |
---|---|---|
Deeltjesgrootte en -verdeling: | Verwijst naar de grootte en variatie in grootte van de metaalpoederdeeltjes. | Beïnvloedt de vloeibaarheid, verpakkingsdichtheid en oppervlakteafwerking van het eindproduct. Een consistente deeltjesgrootte zorgt voor een soepele afzetting en minimaliseert porositeit. |
Sfericiteit: | De mate waarin een deeltje op een perfecte bol lijkt. | Bolvormige deeltjes stromen gemakkelijker, pakken dichter op en zorgen voor een betere oppervlakteafwerking in vergelijking met onregelmatig gevormde deeltjes. |
Vloeibaarheid: | Het gemak waarmee poeder vloeit. | Essentieel voor een consistente materiaaltoevoer naar het DED-systeem. Een slechte vloeibaarheid kan leiden tot toevoerproblemen en inconsistenties in het eindproduct. |
Schijnbare dichtheid: | De bulkdichtheid van het poeder. | влияет (vliyaniyet) op (op) de hoeveelheid materiaal die nodig is om een onderdeel te maken en kan de productiekosten beïnvloeden. |
Smeltpunt: | De temperatuur waarbij het poeder overgaat van vast naar vloeibaar. | Moet compatibel zijn met de gekozen energiebron om goed smelten en afzetten te garanderen. |
Chemische samenstelling: | De elementaire samenstelling van het poeder. | Bepaalt de uiteindelijke eigenschappen van het geprinte onderdeel, zoals sterkte, corrosiebestendigheid en elektrische geleiding. |
Het juiste poeder kiezen: Een evenwichtsoefening
Het selecteren van het optimale metaalpoeder voor je DED-project vereist een zorgvuldige afweging van verschillende factoren. Hier volgt een overzicht om je te helpen bij deze beslissing:
- Vereisten voor sollicitatie: Het beoogde gebruik van het eindproduct is van het grootste belang. Een onderdeel voor een straalmotor vereist bijvoorbeeld een hittebestendig poeder zoals Inconel, terwijl een medisch implantaat misschien een biocompatibele optie vereist zoals titanium of kobalt-chroom.
- Gewenste eigenschappen: Identificeer de cruciale eigenschappen die je nodig hebt in het afgewerkte onderdeel. Heeft sterkte de hoogste prioriteit? Misschien is corrosiebestendigheid of een lichtgewicht constructie essentieel. Als je deze behoeften begrijpt, kun je de poederselectie sturen.
- Compatibiliteit met DED-systeem: Zorg ervoor dat het gekozen poeder overeenkomt met de mogelijkheden van je DED-machine. Houd rekening met factoren zoals laservermogen of de beschikbaarheid van een vacuümkamer voor DED met elektronenbundels.
- Kosten en beschikbaarheid: Metaalpoeders kunnen aanzienlijk in prijs variëren. Breng je budgettaire beperkingen in evenwicht met de gewenste eigenschappen en onderzoek de beschikbaarheid van het poeder om productievertragingen te vermijden.
Extra overwegingen voor Gerichte energiedepositie
Hoewel metaalpoeders de boventoon voeren in DED, is de toekomst veelbelovend voor het gebruik van andere materialen. Onderzoekers onderzoeken het potentieel van het gebruik van:
- Composieten: Het mengen van metaalpoeders met keramische of polymeerdeeltjes om materialen te creëren met unieke combinaties van eigenschappen, zoals verbeterde slijtvastheid of elektrische geleiding.
- Functioneel Gesorteerde Materialen (FGM's): Geleidelijke overgang tussen verschillende materialen binnen een enkele build om specifieke functionaliteiten te bereiken in verschillende delen van het onderdeel. Stelt u zich een gereedschap voor met een slijtvaste punt dat overgaat in een lichter handvat - allemaal in één keer geprint met DED.
Deze vooruitgang opent spannende mogelijkheden voor DED, waarbij de grenzen van ontwerp en functionaliteit in toekomstige toepassingen worden verlegd.
Toepassingen van Gerichte energiedepositie
De veelzijdigheid van DED komt tot uiting in de diverse toepassingen in tal van industrieën. Hier volgen enkele aansprekende voorbeelden:
- Lucht- en ruimtevaart: DED blinkt uit in het maken van lichtgewicht componenten met hoge sterkte voor vliegtuigen, zoals vleugelribben, landingsgestelonderdelen en zelfs onderdelen voor raketmotoren. Het vermogen om complexe geometrieën te produceren met minimaal afval maakt van DED een game-changer in deze gewichtskritische industrie.
- Medische implantaten: Het vermogen van DED om biocompatibele onderdelen met ingewikkelde ontwerpen te maken, maakt het ideaal voor op maat gemaakte protheses, tandheelkundige implantaten en zelfs schedelimplantaten. Deze technologie personaliseert medische zorg, waardoor de resultaten voor de patiënt en de kwaliteit van leven verbeteren.
- Automobiel: De auto-industrie omarmt DED voor prototyping en de productie van kleine aantallen hoogwaardige onderdelen. Met DED kunnen lichtgewicht onderdelen en complexe interne structuren worden gemaakt waar traditionele productie moeite mee heeft.
- Gereedschap en reparatie: DED biedt een snelle en kosteneffectieve manier om mallen, opspanmiddelen en snijgereedschap te maken en te repareren. Stelt u zich eens voor: een beschadigde matrijs repareren of een op maat gemaakt gereedschap op aanvraag maken - DED maakt het mogelijk.
- Olie en gas: DED vindt toepassingen in het maken van corrosiebestendige onderdelen voor downhole tools en andere apparatuur die wordt gebruikt in de ruwe olie- en gasomgevingen.
- Consumptiegoederen: Van op maat gemaakte brilmonturen tot ontwerpgerichte fietsonderdelen, DED doet zijn intrede op de markt van consumentengoederen en maakt de creatie van unieke en innovatieve producten mogelijk.
Dit zijn maar een paar voorbeelden en naarmate de DED-technologie zich verder ontwikkelt, kunnen we nog meer baanbrekende toepassingen verwachten in verschillende industrieën.
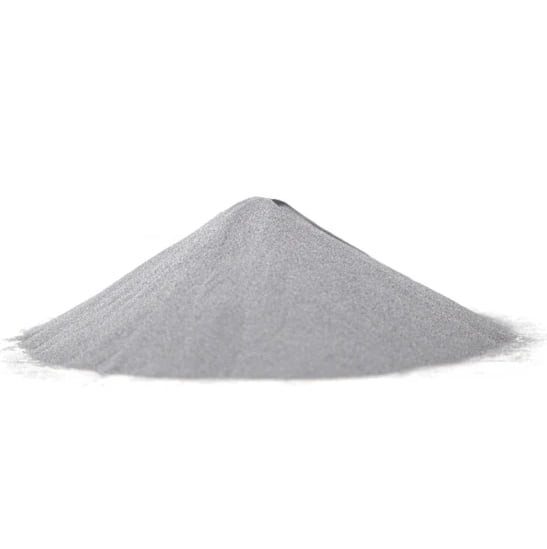
Voordelen en beperkingen van Gerichte energiedepositie
DED kan bogen op een aantal overtuigende voordelen die het een ontwrichtende kracht in de productie maken. Maar zoals elke technologie heeft ook deze zijn eigen beperkingen. Laten we beide kanten van de medaille bekijken.
Voordelen van Directed Energy Deposition:
- Ontwerpvrijheid: Laat uw creativiteit de vrije loop! Met DED kunnen ingewikkelde geometrieën worden gemaakt, zoals dunne wanden, roosters en ondersnijdingen die met traditionele technieken onmogelijk of zeer uitdagend zouden zijn. Dit opent deuren voor lichtgewicht en zeer functionele ontwerpen.
- Materiaalefficiëntie: DED is een bijna-netvormig productieproces, wat betekent dat er minimaal materiaal verloren gaat. Het ongebruikte poeder kan vaak worden gerecycled, waardoor afval en productiekosten tot een minimum worden beperkt.
- Snel prototypen: Het vermogen van DED om snel functionele prototypes te maken, versnelt de productontwikkelingscyclus, waardoor het ontwerp sneller kan worden aangepast en de markt sneller kan worden bereikt.
- Maatwerk: DED blinkt uit in het maken van op maat gemaakte onderdelen, perfect afgestemd op specifieke behoeften. Dit is vooral waardevol in industrieën zoals medische implantaten en luchtvaart.
- Deelconsolidatie: DED kan meerdere componenten combineren tot een enkel stuk, wat ontwerpen vereenvoudigt, assemblagetijd verkort en mogelijk de prestaties van onderdelen verbetert.
- Veelzijdigheid: Een breed scala aan metaalpoeders, en mogelijk andere materialen in de toekomst, verbreedt het toepassingslandschap van DED.
Beperkingen van Gerichte energiedepositie:
- Bouwsnelheid: Vergeleken met traditionele technieken zoals gieten of spuitgieten kan DED langzamer zijn, vooral voor grotere onderdelen. Dit is een doorlopend ontwikkelingsgebied, waarbij het onderzoek zich richt op snellere afzettingssnelheden.
- Oppervlakteruwheid: De laag voor laag aard van DED kan resulteren in een trapsgewijs effect op de oppervlakteafwerking. Nabewerkingstechnieken zoals machinaal bewerken of polijsten kunnen nodig zijn om een gladdere afwerking te verkrijgen.
- Materiaaleigenschappen: Hoewel DED-onderdelen uitstekende mechanische eigenschappen kunnen bereiken, komen ze niet altijd perfect overeen met die van gesmede of gesmede metalen vanwege de inherente aard van het additieve productieproces. Verder onderzoek en ontwikkeling zijn gaande om DED processen te optimaliseren voor verschillende materialen.
- Kosten: DED-systemen kunnen duur zijn en de kosten van metaalpoeders kunnen aanzienlijk variëren. Dit kan de toepassing voor de productie van grote volumes goedkope onderdelen beperken.
- Restspanning: De snelle verwarmings- en koelcycli tijdens DED kunnen restspanning in het onderdeel introduceren. Een goed ontwerp en goede nabewerkingstechnieken kunnen dit probleem beperken.
FAQ
Hier zijn enkele van de meest voorkomende vragen die mensen hebben over DED:
V: Wat zijn de voordelen van DED ten opzichte van andere 3D printtechnologieën zoals FDM (Fused Deposition Modeling)?
A: DED biedt verschillende voordelen ten opzichte van FDM. Ten eerste maakt DED gebruik van metaalpoeders, waardoor functionele metalen onderdelen gemaakt kunnen worden. FDM daarentegen is meestal beperkt tot kunststoffen en andere polymeren. Ten tweede hebben DED onderdelen over het algemeen superieure mechanische eigenschappen in vergelijking met FDM onderdelen. Tot slot biedt DED een grotere ontwerpvrijheid met de mogelijkheid om complexe geometrieën te maken.
V: Kan DED worden gebruikt om metalen onderdelen te repareren?
A: Absoluut! Het vermogen van DED om nauwkeurig materiaal af te zetten maakt het ideaal voor het repareren van beschadigde metalen onderdelen. Dit kan een kosteneffectieve en tijdbesparende oplossing zijn in vergelijking met traditionele vervangingsmethoden.
V: Wat is de toekomst van Directed Energy Deposition?
A: De toekomst van DED is rooskleurig! We kunnen vooruitgang verwachten op verschillende gebieden:
- Snellere bouwsnelheden: Onderzoekers ontwikkelen voortdurend methoden om de depositiesnelheden te verhogen, waardoor DED concurrerender wordt voor productie op grotere schaal.
- Multi-materiaal DED: De mogelijkheid om verschillende metaalpoeders of zelfs metalen en niet-metalen materialen naadloos te combineren binnen een enkele constructie opent opwindende mogelijkheden om onderdelen te maken met op maat gemaakte eigenschappen in verschillende gebieden.
- Standaardisatie: Naarmate de DED-technologie volwassener wordt, zal standaardisatie van processen en materialen een cruciale rol spelen bij het garanderen van kwaliteit en herhaalbaarheid.
- Lagere kosten: Naar verwachting zullen de kosten van DED-systemen en metaalpoeders dalen door de vooruitgang in technologie en de toegenomen toepassing, waardoor DED toegankelijker wordt voor een breder scala aan fabrikanten.
DED heeft een enorm potentieel om een revolutie teweeg te brengen in verschillende industrieën. Het vermogen om complexe, functionele metalen onderdelen te maken met minimaal afval en een grote ontwerpvrijheid maakt het een technologie om in de gaten te houden. Naarmate DED zich verder ontwikkelt, kunnen we nog meer baanbrekende toepassingen verwachten die de toekomst van de productie vormgeven.
Delen op
MET3DP Technology Co, LTD is een toonaangevende leverancier van additieve productieoplossingen met hoofdkantoor in Qingdao, China. Ons bedrijf is gespecialiseerd in 3D printapparatuur en hoogwaardige metaalpoeders voor industriële toepassingen.
Onderzoek om de beste prijs en een op maat gemaakte oplossing voor uw bedrijf te krijgen!
gerelateerde artikelen
Over Met3DP
Recente update
Ons product
NEEM CONTACT MET ONS OP
Nog vragen? Stuur ons nu een bericht! Na ontvangst van uw bericht behandelen wij uw verzoek met een heel team.
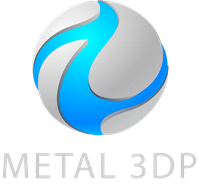
Metaalpoeders voor 3D printen en additieve productie