Metaalverstuiving: Overzicht, Leveranciers, Voordelen
Inhoudsopgave
Metaalverneveling is een proces waarbij metaal door verneveling van zijn bulkvorm wordt omgezet in fijn metaalpoeder. Het wordt vaak gebruikt bij de productie van metaalpoeders voor verschillende toepassingen in verschillende industrieën. Dit artikel biedt een uitgebreide gids over metaalverneveling, waarin de belangrijkste aspecten gedetailleerd worden behandeld.
Overzicht van metaalverneveling
Metaalverneveling omvat het opbreken van gesmolten metaal in fijne druppeltjes met behulp van een gas- of vloeistofstroom met hoge snelheid. Terwijl de druppeltjes tijdens de vlucht snel stollen, worden fijne bolvormige metaalpoeders gevormd.
Belangrijkste details:
- Wordt gebruikt voor de productie van fijne bolvormige metaalpoeders uit metalen zoals aluminium, koper, ijzer, nikkel enz.
- Op basis van methode ingedeeld in gasverneveling, waterverneveling en centrifugale verneveling
- Poeders variëren van 10 micron tot 250 micron in grootte met een strakke verdeling
- Zorgt voor een snelle stolling van druppels, wat resulteert in fijnkorrelige poeders
- Hoofdzakelijk gebruikt in de metaalpoedermetallurgie en voor de vervaardiging van metaalpoedercomponenten
Vernevelingsmethoden
Methode | Details |
---|---|
Gasverstuiving | Gesmolten metaalstroom uiteengevallen door inerte gasstralen onder hoge druk |
Waterverneveling | Maakt gebruik van waterstralen voor het uiteenvallen van de metaalstroom |
Centrifugale verstuiving | Gesmolten metaal werd op de draaiende schijf gegoten en van de randen geslingerd |
Metaalpoedertoepassingen
Sollicitatie | Details |
---|---|
Poeder-Metallurgie | Pers en sinter poedercompacts om PM-onderdelen te vervaardigen |
Productie van metaaladditieven | Gebruik vernevelde poeders als grondstof voor AM-processen zoals DED, PBF |
Metaal spuitgieten | Poeders mengen met bindmiddel, in mallen injecteren en ontbinden/sinteren |
Thermische spuitcoatings | Spuit vernevelde poeders op oppervlakken met behulp van plasma-/verbrandingsspray |
Solderen | Gebruik vernevelde poedertussenlagen voor hardsoldeerprocessen bij hoge temperaturen |
Lassen | Verstoven metaalpoeders gebruikt als vulmateriaal bij lasprocessen |
Specificaties voor metaalverneveling
Parameter | Typisch bereik |
---|---|
Poedergrootte | 10 tot 250 micron |
Grootteverdeling | Strakke, bolvormige morfologie |
Puurheid | Tot 99,9% |
Schijnbare dichtheid | Ongeveer 40-50% van ware dichtheid |
Oxide-gehalte | <1%, lagere verneveling van inert gas |
Productie snelheid | 10 – 100 kg/uur |
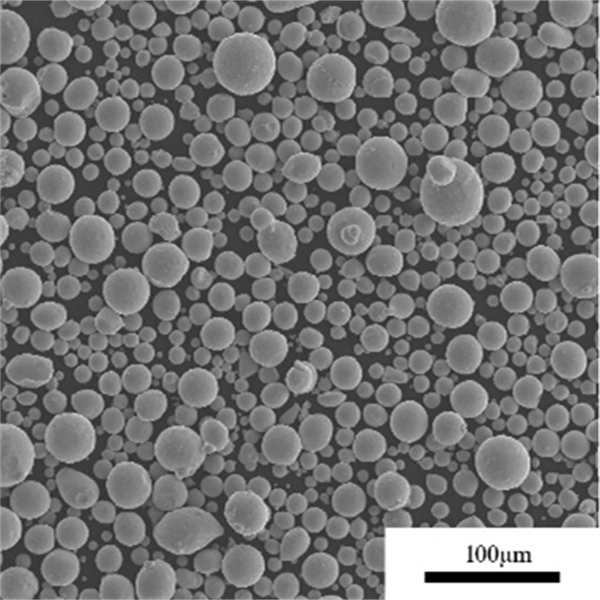
Apparatuur voor metaalverneveling
De belangrijkste apparatuur die betrokken is bij het metaalvernevelingsproces omvat:
Gids voor apparatuur voor metaalverneveling
Apparatuur | Doel |
---|---|
Inductiefornuis | Smelt metaalladingsmateriaal in vloeibare toestand |
Smeltkroes | Houdt gesmolten metaal vast voordat het in de verstuiver wordt gegoten |
Tunisch | Fungeert als reservoir en vergemakkelijkt het gieten van metaal |
Vernevelingsmechanisme | Desintegreert gesmolten metaal in druppeltjes met behulp van een gas-/vloeistofstraal |
Poederopvangsysteem | Verzamelt en scheidt verneveld poeder van transportgas/vloeistof |
Verstuivertypen en kenmerken
Verstuiver | Beginsel | Functies |
---|---|---|
Gasverstuiver | Inerte gasstraal onder hoge druk | Fijner poeder, lagere oxidatie |
Waterverstuiver | Waterstraal met hoge snelheid | Hogere productiesnelheid, grotere deeltjes |
Centrifugale verstuiver | Gesmolten metaal gegoten op draaiende schijf/beker | Compact, eenvoudig te bedienen |
Hulpapparatuur
Categorie | Functie | Beschrijving | Invloed op metaalpoeder |
---|---|---|---|
Grondstofvoorbereiding | Grondstoffen conditioneren en zuiveren | Ontgassingsovens: Verwijder opgeloste gassen zoals waterstof en zuurstof om porositeit in het uiteindelijke poeder te voorkomen. Inductiesmeltovens: Smelten en nauwkeurig regelen van de temperatuur van de metaalgrondstof. Legeringssystemen: Weeg nauwkeurig verschillende metalen af en meng ze om de gewenste uiteindelijke samenstelling van de legering te verkrijgen. | Minimaliseert gasonvolkomenheden in het poeder. Zorgt voor consistente poedereigenschappen. Bereikt de gewenste materiaaleigenschappen van het eindproduct. |
Behandeling en levering van metaal | Gesmolten metaal veilig overbrengen | Kroezen: Vuurvaste houders voor het vasthouden en transporteren van gesmolten metaal. Overhevelvaten (tundishes, pollepels): Geïsoleerde vaten om gesmolten metaal over te brengen van de oven naar de verstuivingskamer. Inert gas doorblaassystemen: Zorg voor een atmosfeer van inert gas om oxidatie en verontreiniging tijdens de metaaloverdracht te voorkomen. | Minimaliseert metaaloxidatie en vervuiling. Handhaaft een consistente metaaltemperatuur voor optimale verstuiving. |
Verstuiving procesbesturing | Nauwkeurige regeling van bedrijfsparameters | Systemen voor debietregeling: Regel de stroomsnelheid van het verstuifmedium (gas of water) voor consistente druppelgrootte en poedermorfologie. Temperatuurregelingssystemen: Bewaak en handhaaf de optimale temperatuur van het gesmolten metaal voor een goede verstuiving. Drukregelsystemen: Regel de druk van het verstuifmedium (bij gasverstuiving) voor efficiënte druppelvorming. | Maakt een consistente poederkwaliteit en verdeling van de deeltjesgrootte mogelijk. Optimaliseert de poederopbrengst. |
Poeder verzamelen en classificeren | Poederdeeltjes scheiden en de grootte ervan bepalen | Cyclonen: Scheid grotere poederdeeltjes uit de gasstroom met behulp van centrifugale kracht. Natte wassers: Vang fijne poederdeeltjes op en koel ze af met een waternevel. Zeven en classificatiesystemen: Poederdeeltjes scheiden in verschillende fracties met behulp van zeven of luchtklassers. | * Zorgt voor de gewenste poedergroottedistributie voor specifieke toepassingen. <br> * Minimaliseert poederverlies. |
Behandeling en opslag van poeder | Metaalpoeder veilig beheren en opslaan | Behandelingssystemen voor inert gas: Zorg voor een inerte atmosfeer tijdens poederoverdracht en opslag om oxidatie en vochtabsorptie te voorkomen. Poederverpakkingssystemen: Verpak het metaalpoeder in luchtdichte verpakkingen voor veilig transport en opslag. Poedersilo's: Grote, gesloten opslagvaten voor metaalpoeder in bulk met gecontroleerde atmosfeer. | Behoudt de poederkwaliteit en voorkomt degradatie. Zorgt voor een veilige en efficiënte poederverwerking. |
Milieubeheersing | Minimaliseer de impact op het milieu | Waterzuiveringssystemen: Behandel en recycle proceswater dat wordt gebruikt bij waterverneveling om afval te minimaliseren en te voldoen aan de milieuwetgeving. Rookafzuigsystemen: Uitlaatgassen van het verstuivingsproces opvangen en filteren om luchtvervuiling tot een minimum te beperken. Geluidsbeheersingssystemen: Verminder het geluid dat wordt gegenereerd tijdens het verstuivingsproces om te voldoen aan de veiligheidsvoorschriften. | Realiseert duurzame metaalpoederproductie. Zorgt voor naleving van milieuregelgeving. |
Veiligheidssystemen | De veiligheid van de operator garanderen | Noodafsluitingssystemen: Stop het verstuivingsproces snel in geval van nood. Explosiebeveiligingssystemen: Voorkom explosies door ophoping van brandbaar gas of metaalstof. Persoonlijke beschermingsmiddelen (PPE): Voorziet operators van geschikte kleding, ademhalingsapparatuur en oogbescherming. | Minimaliseert het risico op ongelukken en verwondingen. Creëert een veilige werkomgeving. |
Ontwerpnormen en installatievereisten
Onderdeel | Ontwerpnormen | Installatievereisten |
---|---|---|
Drukvaten | ASME ketel- en drukvatcode (Sectie VIII Divisie 1) EN 13445 (Europese norm) PD 5500 (Britse norm) | Voldoende ruimte voor het plaatsen van vaartuigen en toegang voor onderhoud. Gecertificeerde hijsogen voor veilig transport en installatie. Ontwerp van funderingen rekening houdend met gewicht, trillingen en mogelijke seismische activiteit. Secundaire insluiting om gemorste of gelekte stoffen op te vangen. |
Leidingen | ASME B31.3 Procesleidingen ANSI B16.5 flenzen en flensfittingen | Buisdiameter en materiaalselectie gebaseerd op drukklasse, temperatuur en compatibiliteit met procesvloeistoffen. Flenskeuze rekening houdend met drukklasse en boutmateriaal. Afgeschuinde leidingen voor een goede afvoer en minimalisering van dode benen. Toegankelijke afsluiters voor isolatie en onderhoud. Hoogwaardige lasprocedures en personeelskwalificaties. |
Smeltende eenheid | Materiaalkeuze voor weerstand tegen hoge temperaturen en compatibiliteit met grondstoffen | Inductiespoeluitlijning en koelsysteem voor efficiënte warmteoverdracht. Selectie van smeltkroesmateriaal en vervangingsschema op basis van grondstof en slijtagekenmerken. Voedingscapaciteit en regelsysteem voor nauwkeurige temperatuurregeling. |
Vernevelingskamer | Selectie van vuurvaste bekleding op basis van bedrijfstemperatuur en procesomstandigheden | Voorziening voor doorspoelen met inert gas om oxidatie te minimaliseren. Ontwerp van een afschriksysteem voor het snel stollen van metaaldruppels. Opvangsysteem voor efficiënte opvang van metaalpoeder. Explosieontlasting om drukopbouw door mogelijke stofexplosies te beperken. |
Sproeiers | ASME MFC-7M Meting van vloeistofstroming door middel van venturibuizen | Regelmatige inspectie en vervanging van spuitdoppen om een consistente verdeling van de deeltjesgrootte te behouden. Uitlijning en positionering van spuitmonden voor optimale verstuivingsefficiëntie. |
Poederbehandelingssysteem | NFPA 654 Norm voor de preventie van stofexplosies in installaties voor productie, verwerking en overslag van bulkgoederen EN 14460 Werkplekatmosfeer - Eisen voor de omgang met brandbaar stof | Inert maken met inert gas van opvang- en overslagvaten voor poeder om explosies te voorkomen. Ontluchtings- en onderdrukkingssystemen voor extra veiligheidsmaatregelen. Afgedichte transfersystemen om het ontstaan van poederstof en vluchtige emissies te minimaliseren. HEPA-filtratie voor luchtzuivering en bescherming van de gezondheid van werknemers. |
Besturingssystemen | IEC 61131 Programmeerbare automatiseringscontrollers (PAC) Programmeertalen NFPA 850 Aanbevolen praktijk voor brandbeveiliging voor elektrische centrales en aanverwante voorzieningen | Real-time bewaking en regeling van procesparameters (temperatuur, druk, debiet). Alarmsystemen voor melding van afwijkingen van bedrijfsparameters. Veiligheidsvergrendelingen om apparatuurstoringen en potentiële gevaren te voorkomen. Redundante besturingssystemen voor kritieke bewerkingen om processtabiliteit te garanderen. |
Leveranciers van metalen verstuivers
Belangrijkste leveranciers
Leverancier | Plaats | Producten |
---|---|---|
PSI | Canada | Gas-, water- en centrifugaalverstuivers |
ALD-vacuümtechnologieën | Duitsland | Gas- en waterverstuivers |
Chinees staal thermo | China | Water- en gasverstuivers |
VTI-vacuümtechnologieën | Groot-Brittannië | Hoogwaardige gasverstuivers |
Prijzen
- Kleine laboratoriumeenheden beginnen rond $100.000
- Productieverstuivers op industriële schaal variëren van $500.000 tot $2.000.000
- Grotere op maat gemaakte systemen kunnen tot $4.000.000 kosten
- Bijkomende kosten voor hulpmiddelen, installatie, verbruiksartikelen
Prijs van metaalverstuivingsapparatuur:
Factor | Beschrijving | Invloed op de prijs |
---|---|---|
Type verstuiving | Er zijn twee hoofdtypen metaalverstuiving: gasverstuiving en waterverstuiving. Bij gasverstuiving wordt een inert gas gebruikt, meestal argon, om het gesmolten metaal in fijne deeltjes te verdelen. Bij waterverstuiving wordt een waterstraal onder hoge druk gebruikt om hetzelfde resultaat te bereiken. | Gasverstuiving is over het algemeen duurder dan waterverstuiving. Dit komt omdat gasverstuivingsapparatuur complexer is en hogere bedrijfskosten vereist. Gasverstuiving kan echter fijnere en meer bolvormige poederdeeltjes produceren, wat wenselijk is voor sommige toepassingen. |
Metaal dat wordt verstoven | De prijs van metaalverstuivingsapparatuur kan ook variëren afhankelijk van het type metaal dat wordt verstoven. Reactieve metalen, zoals titanium en zirkonium, zijn moeilijker te vernevelen dan niet-reactieve metalen, zoals ijzer en koper. Dit komt omdat reactieve metalen kunnen reageren met het vernevelgas of water, wat kan leiden tot problemen met de poederkwaliteit en corrosie van de apparatuur. | De verstuiving van reactieve metalen vereist meestal meer gespecialiseerde apparatuur en hogere bedrijfskosten. Dit kan de prijs van de apparatuur aanzienlijk verhogen. |
Productiecapaciteit | Metaalverstuivingsapparatuur is verkrijgbaar in een breed scala aan productiecapaciteiten, van kleine batchsystemen die een paar kilo poeder per uur kunnen produceren tot grootschalige systemen die meerdere tonnen poeder per uur kunnen produceren. | De prijs van metaalverstuivingsapparatuur neemt toe met de productiecapaciteit. Grotere systemen zijn complexer en vereisen duurdere onderdelen. |
Gewenste poedereigenschappen | De gewenste eigenschappen van het metaalpoeder zijn ook van invloed op de prijs van de verstuivingsapparatuur. Als er bijvoorbeeld een zeer fijn poeder nodig is, dan is er een geavanceerder verstuivingssysteem nodig, dat duurder zal zijn. | Als het poeder moet voldoen aan strenge specificaties voor de deeltjesgrootte, morfologie of andere eigenschappen, dan vereist dit waarschijnlijk extra apparatuur of processtappen, wat de kosten kan verhogen. |
Automatiseringsniveau | Metaalverstuivingsapparatuur kan handmatig, halfautomatisch of volledig geautomatiseerd zijn. Volledig geautomatiseerde systemen zijn het duurst, maar ze bieden ook de hoogste mate van procescontrole en consistentie. | Een hogere mate van automatisering betekent meestal een hoger prijskaartje. Dit kan echter worden gecompenseerd door een hogere productiviteit en lagere arbeidskosten. |
Fabrikant | De prijs van metaalverstuivingsapparatuur kan ook variëren afhankelijk van de fabrikant. Sommige fabrikanten zijn gespecialiseerd in high-end apparatuur voor veeleisende toepassingen, terwijl andere fabrikanten meer eenvoudige apparatuur aanbieden voor minder kritische toepassingen. | Bekende merken met een reputatie van kwaliteit en betrouwbaarheid kunnen een hogere prijs opbrengen. |
Leverancier van verstuivers kiezen
- Reputatie en ervaringsniveau
- Mogelijkheden voor maatwerk en maatbereik
- Productiecapaciteit en doorlooptijden
- Budget beperkingen
- Locatie- en serviceondersteuning
- Eisen aan poederspecificaties
- Aanbod van hulpapparatuur
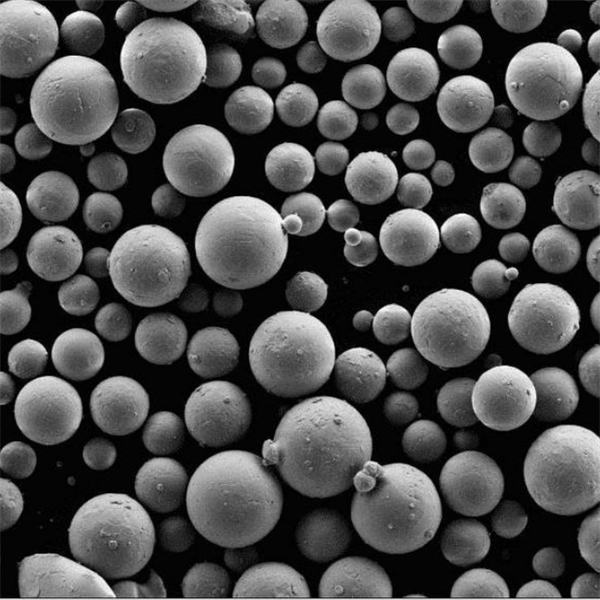
Werking van metalen verstuiver
Typisch atomiseringsproces
Stap | Activiteit |
---|---|
1 | Laad de inductieoven met te verstuiven metaal |
2 | Smelt het metaal volledig en laat het op oververhittingstemperatuur komen |
3 | Start de inerte gasstroom in de verstuiver bij de gewenste druk |
4 | Open de inductieoven en giet het gesmolten metaal in een trechter/kroes |
5 | Laat het metaal in de verstuiver stromen zodat het in poeder uiteenvalt |
6 | Poeder dat door gas naar cycloonafscheiders wordt vervoerd om te worden verzameld |
7 | Zeef poeder om grote deeltjes en fijne deeltjes te verwijderen |
8 | Verpak het uiteindelijke poeder na afkoelen in containers |
Kritieke procesparameters
- Oververhittingstemperatuur van metaal
- Stroomsnelheid gesmolten metaal in verstuiver
- Gas/waterdebiet en druk
- Gietconfiguratie en hoeveelheid metaallading
- Mondstukontwerp en geometrie
- Verzamel- en zeefaanpak
Onderhoudsaspecten
- Inspecteer en vervang versleten spuitmonden, kleppen en voeringen periodiek
- Controleer de gasleidingen en waterstralen op verstoppingen die de doorstroming beïnvloeden
- Bewaak de aandrijving en lagers van de centrifugaalverstuiver
- Schone poederafzetting in leidingen en vaten
- Onderhoud inductieoven, temperatuursensoren etc.
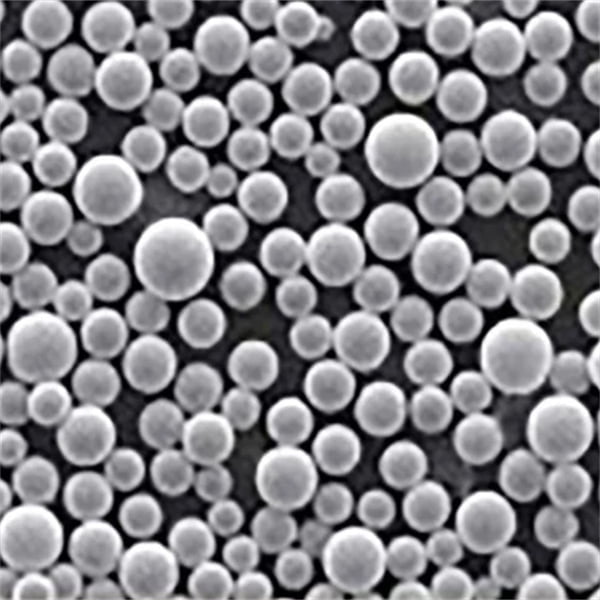
Voordelen en beperkingen
Voordeel | Beschrijving | Beperking | Beschrijving |
---|---|---|---|
Nauwkeurige poederkenmerken | Metaalverstuivingsapparatuur blinkt uit in het produceren van poeders met een strak gecontroleerde deeltjesgrootteverdeling en morfologie. Dit maakt het mogelijk om poeders te maken die specifiek geschikt zijn voor Additive Manufacturing (AM) technieken zoals Selective Laser Melting (SLM) of Electron Beam Melting (EBM). De nauwkeurige controle over de sferische vorm en het smalle bereik van de deeltjesgrootte vertaalt zich naar optimale vloei-eigenschappen voor invoer in AM-machines, wat leidt tot consistente laagvorming en een betere kwaliteit van het eindproduct. | Hoge investerings- en operationele kosten | Het opzetten en gebruiken van metaalverstuivingsapparatuur brengt aanzienlijke investeringen met zich mee. De systemen zijn complex en vereisen gespecialiseerde infrastructuur, geschoold personeel voor bediening en onderhoud en doorlopende kosten voor verbruiksgoederen zoals inerte gassen en reserveonderdelen. |
Hoge productiesnelheden en schaalbaarheid | Moderne verstuivingsapparatuur maakt een continue en geautomatiseerde werking mogelijk, waardoor een hoge poederproductie kan worden behaald. Dit is cruciaal voor AM-toepassingen op industriële schaal waar grote hoeveelheden materiaal nodig zijn. Bovendien maakt het modulaire ontwerp van veel systemen schaalbaarheid mogelijk, wat betekent dat de productiecapaciteit kan worden verhoogd door extra eenheden toe te voegen als de vraag toeneemt. | Beperkte grondstofcompatibiliteit | Hoewel metaalverstuiving een breed scala aan legeringen aankan, kunnen sommige materialen met een hoge dampdruk of reactiviteit problemen opleveren. Het vernevelingsproces kan onzuiverheden introduceren of de chemische samenstelling van het poeder wijzigen, wat de prestaties van het eindproduct beïnvloedt. |
Breed toepasbaar | Metaalverstuivingsapparatuur is een veelzijdige technologie die een groot aantal metalen en legeringen kan verwerken. Dit omvat veelgebruikte materialen in AM zoals titanium, aluminium, nikkel en kobaltlegeringen, maar ook meer exotische opties zoals vuurvaste metalen en hoogwaardige legeringen. | Milieu-overwegingen | Het verstuivingsproces kan afvalproducten en emissies genereren, afhankelijk van de gekozen methode. Waterverstuiving kan bijvoorbeeld leiden tot afvalwater dat metaaloxiden bevat. Verstuiving met inert gas heeft een lagere impact op het milieu, maar vereist nog steeds een verantwoord beheer van uitlaatgassen. |
Hoge poederzuiverheid | Een populaire techniek voor verneveling met inert gas maakt gebruik van een omgeving met inert gas om verontreiniging tijdens het vernevelingsproces te minimaliseren. Dit resulteert in een hoge poederzuiverheid, essentieel voor toepassingen waar materiaaleigenschappen kritisch zijn. | Complexiteit van het proces | Bij verstuiving van metaal zijn er veel parameters die nauwkeurig geregeld moeten worden om de gewenste poedereigenschappen te verkrijgen. Factoren zoals smelttemperatuur, verstuivingsdruk en koelsnelheid hebben allemaal een aanzienlijke invloed op de uiteindelijke poedereigenschappen. Het optimaliseren van deze parameters vereist expertise en voortdurende procesbewaking om een consistente kwaliteit te garanderen. |
Hoe u een metalen verstuiver kiest
Factor | Overweging | Belang | Details |
---|---|---|---|
Metalen compatibiliteit | Materiaal dat je wilt verstuiven | Kritisch | Verschillende verstuivingstechnieken blinken uit met specifieke metalen. Gasverstuiving is ideaal voor reactieve metalen zoals titanium en aluminium, terwijl waterverstuiving goed werkt voor minder reactieve metalen zoals ijzer en koper. |
Deeltjesgrootte en -verdeling | Gewenste grootte en consistentie van metaalpoeder | Hoog belang | De deeltjesgrootte heeft een directe invloed op de eigenschappen van het eindproduct. Een fijner poeder zorgt voor gladdere oppervlakken bij 3D printen, terwijl een grover poeder geschikt kan zijn voor het spuitgieten van metaal. Een uniforme verdeling van de deeltjes zorgt voor consistente materiaaleigenschappen in het hele poederbed. |
Productie volume | Verwachte hoeveelheid benodigd metaalpoeder | Matig Belang | Houd rekening met de capaciteit van de verstuiver om aan je productiebehoeften te voldoen. Een gasverstuiver met een hoog volume kan te veel zijn voor een klein prototype, terwijl een waterverstuiver met een laag volume moeite heeft om de massaproductie bij te houden. |
Operationele kosten | Energieverbruik, onderhoudsvereisten | Matig Belang | Gasverstuiving heeft over het algemeen hogere aanloopkosten, maar lagere bedrijfskosten vanwege de energiezuinigheid. Waterverstuiving heeft vaak lagere aanloopkosten maar hogere bedrijfskosten vanwege het waterverbruik en mogelijke corrosie. |
Veiligheid | Inherente risico's van het verstuivingsproces | Kritisch | Bij zowel gas- als waterverstuiving is er sprake van gesmolten metaal en een omgeving onder druk. Bij gasverstuiving bestaat explosiegevaar door het gebruik van inerte gassen. Waterverstuiving kan brandbaar waterstofgas genereren. Geef prioriteit aan veiligheidsvoorzieningen en houd je aan de juiste veiligheidsprotocollen. |
Automatiseringsniveau | Automatiseringsgraad gewenst in het verstuivingsproces | Verschilt per gebruiker | Een verregaand geautomatiseerd systeem minimaliseert menselijke tussenkomst en vermindert fouten, maar daar zijn hoge kosten aan verbonden. Een handmatig systeem biedt meer controle, maar vereist meer expertise van de operator. |
Toekomstige uitbreidbaarheid | Potentiële noodzaak om verschillende metalen of volumes te verwerken | Overweeg indien nodig | Als je verwacht in de toekomst met verschillende metalen te gaan werken of je productie te verhogen, kies dan een verstuiver die flexibel genoeg is om deze veranderingen aan te kunnen. |
Fabrikant Reputatie | Track record van de verstuiverleverancier | Belangrijk | Onderzoek de ervaring van de fabrikant, de klantenondersteuning en het garantiebeleid. Kies een gerenommeerd bedrijf met een bewezen staat van dienst op het gebied van metaalverstuivingstechnologie. |
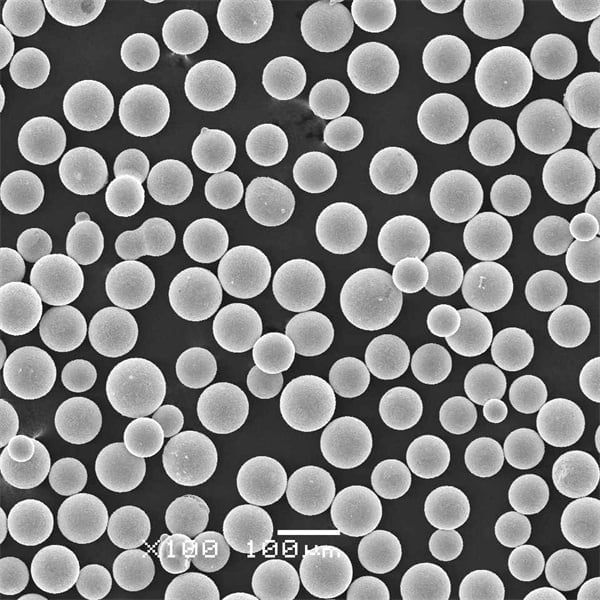
Veelgestelde vragen
Vraag: Wat is het typische groottebereik van verstoven metaalpoeder?
A: Het bereik van de deeltjesgrootte voor de meeste verstuivers bedraagt ongeveer 10 micron tot 250 micron. Gasverstuivers kunnen fijner poeder tot 10 micron produceren, terwijl waterverstuivers grover poeder tot meer dan 100 micron kunnen produceren.
Vraag: Welke metalen kunnen in poedervorm worden verneveld?
A: Gebruikelijke metalen die worden verstoven zijn onder meer aluminium, koper, ijzer, nikkel, kobalt, titanium, tantaal en roestvrij staal. Zelfs legeringen en reactieve metalen zoals magnesium kunnen worden verneveld.
Vraag: Hoe bolvormig zijn de verstoven poeders?
A: Vernevelde poeders hebben een zeer bolvormige morfologie omdat de druppeltjes tijdens de vlucht snel stollen. Er worden sfericiteitsniveaus van 0,9 tot 1 bereikt. Gasverneveling maakt meer bolvormig poeder.
Vraag: Wat is het belangrijkste gebruik van verneveld metaalpoeder?
A: Het primaire gebruik vindt plaats in de poedermetallurgie voor het persen en sinteren van componenten. De fijne poeders zijn ook ideaal voor metaaladditieve productie met behulp van poederbedfusie of gerichte energiedepositie.
Vraag: Hoe wordt de poedergrootteverdeling gecontroleerd bij verneveling?
A: Het ontwerp van het mondstuk, de stroomsnelheid van het gesmolten metaal, de gasdruk en de verstuivingsconfiguratie bepalen de deeltjesgrootteverdeling. Meerdere zeeffasen na de verneveling helpen de verdeling te verkleinen.
Vraag: Vereist metaalverstuiving speciale vaardigheden?
A: Hoewel het een geautomatiseerd proces is, zijn vaardigheden op gebieden als metallurgie, thermisch spuiten en poederverwerking nodig om de verstuiver goed te optimaliseren en te controleren voor een hoogwaardige productie van metaalpoeder.
Vraag: Wat bepaalt de productiesnelheid van een verstuiver?
A: Het metaaldebiet, de gasdruk en de verstuivercapaciteit bepalen de productiesnelheid. Industriële verstuivers kunnen 100 kg/uur poeder maken, terwijl laboratoriumverstuivers slechts enkele kg/uur kunnen maken.
Vraag: Hoe bepaal ik de juiste maat en het juiste type verstuiver?
A: Sleutelfactoren zijn de benodigde hoeveelheid poeder, het budget, de bestaande infrastructuurondersteuning en de gewenste poedereigenschappen. Deze helpen bij het maken van een keuze tussen gas-, water- of centrifugaaltype in de benodigde capaciteit.
Vraag: Produceert metaalverneveling afvalbijproducten?
A: Er is niet veel vast afval nodig, maar er is wel een behandeling van afvalwater/water nodig. Stofafzuiging uit poederverwerkingsruimtes is ook vereist. Een correcte afvoer van gebruikte filters en verbruiksartikelen is vereist.
Conclusie
Metaalverneveling maakt het mogelijk om bulkmetaal om te zetten in fijne bolvormige poeders met behulp van gas-, water- of centrifugale energie. Met een strikte controle van procesparameters kunnen op maat gemaakte poeders met hoge zuiverheid, ideaal voor AM, worden geproduceerd. Deze gids heeft de werking, typen, toepassingen, leveranciers en technische overwegingen voor metaalvernevelingssystemen samengevat. De gestructureerde informatie maakt een eenvoudige vergelijking mogelijk tussen de opties om een geschikte verstuiver te kiezen.
Delen op
MET3DP Technology Co, LTD is een toonaangevende leverancier van additieve productieoplossingen met hoofdkantoor in Qingdao, China. Ons bedrijf is gespecialiseerd in 3D printapparatuur en hoogwaardige metaalpoeders voor industriële toepassingen.
Onderzoek om de beste prijs en een op maat gemaakte oplossing voor uw bedrijf te krijgen!
gerelateerde artikelen
Over Met3DP
Recente update
Ons product
NEEM CONTACT MET ONS OP
Nog vragen? Stuur ons nu een bericht! Na ontvangst van uw bericht behandelen wij uw verzoek met een heel team.
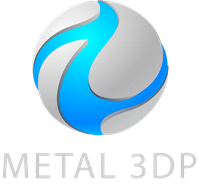
Metaalpoeders voor 3D printen en additieve productie