Metaalpoederproductie
Inhoudsopgave
Overzicht
Metaalpoeders zijn fijne metaaldeeltjes die worden gebruikt als grondstof voor productietechnieken zoals additieve productie, metaalspuitgieten en poedermetallurgisch persen en sinteren. Het produceren van geavanceerde speciale metaalpoeders met precieze controle over de chemie, deeltjesgrootteverdeling, morfologie en microstructuur is cruciaal voor de eigenschappen van afgewerkte componenten.
Er zijn verschillende methoden die gebruikt worden voor grootschalige productie van metaalpoeder uit verschillende legeringssystemen, waaronder:
- Gasverneveling
- Waterverneveling
- Plasma-verneveling
- Elektrode-inductie smeltgasverstuiving
- Proces met roterende elektrode
- Carbonylproces
- Elektrolytisch proces
- Metaalreductieprocessen
Elk proces resulteert in poeders met verschillende eigenschappen die geschikt zijn voor specifieke toepassingen.
Productiemethoden voor metaalpoeder
Methode | Gebruikte metalen | Sleuteleigenschappen | Belangrijkste toepassingen |
---|---|---|---|
Gasverstuiving | Titanium, aluminium, roestvrij staal, gereedschapsstaal, superlegeringen | Bolvormige poeders, matige productiesnelheid | Spuitgieten van metaal, heet isostatisch persen |
Waterverneveling | Laaggelegeerd staal, ijzer, koper | Onregelmatige poedervormen, hoger zuurstofgehalte | Pers- en sinterproces |
Plasma-verneveling | Titaanlegeringen, superlegeringen | Zeer fijne sferische poeders | Additieve productie |
Roterende elektrode | Wolfraam, molybdeen, tantaal | Gecontroleerde korrelstructuur | Filamenten, snijgereedschappen |
Carbonylproces | IJzer, nikkel, kobalt | Ultrafijne zeer zuivere poeders | Elektronische onderdelen, magneten |
Elektrolytisch | Koper, nikkel | Dendritische vlokkenmorfologie | Oppervlaktecoatings |
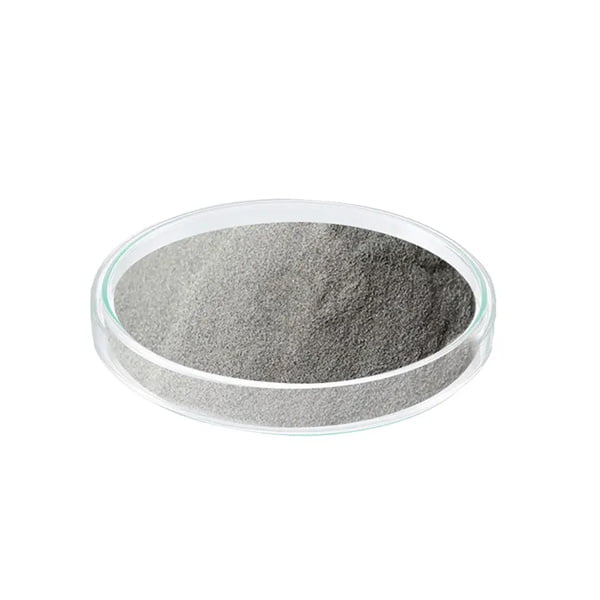
Metaalpoeder Productie methodes
Er zijn verschillende commerciële methoden die worden gebruikt voor het produceren van metaalpoeders uit verschillende legeringssystemen. De keuze van de productiemethode hangt af van factoren zoals:
- Type legeringsmateriaal
- Zuiverheidseisen
- Gewenste poederkenmerken zoals deeltjesgrootte, vorm, korrelstructuur
- Productieschaal in ton per jaar
- Eindtoepassing poeder
Hier zijn enkele van de meest voorkomende industriële processen voor metaalpoederproductie:
Verstuiving van gas
Bij het gasatomisatieproces wordt een stroom gesmolten metaallegering uiteengereten door gasstralen onder hoge druk, meestal stikstof of argon. De metaalstroom valt uiteen in fijne druppeltjes, die stollen tot poederdeeltjes.
Gasvernevelde poeders hebben een bolvorm en een gladde oppervlaktemorfologie. De deeltjesgrootteverdeling kan worden geregeld door de procesparameters aan te passen. Dit is een veelgebruikte techniek voor reactieve materialen zoals titanium, aluminium, magnesiumlegeringen en roestvast staal, gereedschapsstaal en nikkelsuperlegeringen.
Parameter | Beschrijving |
---|---|
Gebruikte metalen | Titaanlegeringen, aluminium, magnesium, roestvrij staal, gereedschapsstaal, superlegeringen |
Deeltjesvorm | Sferische morfologie |
Deeltjesgrootte | 50 - 150 μm typisch |
Puurheid | Hoog, inert gas voorkomt vervuiling |
Zuurstof pick-up | Minimaal vergeleken met verneveling van vloeibaar metaal |
Productieschaal | Tot 10.000 ton per jaar |
Waterverneveling
Bij waterverstuiving wordt de stroom gesmolten metaal geraakt door waterstralen met hoge snelheid. De plotselinge afkoeling veroorzaakt een explosie die het metaal in fijne deeltjes breekt. De poeders hebben een onregelmatige vorm en bevatten een hoger zuurstofgehalte door het contact met water.
Waterverstuiving is een goedkoper proces dat wordt gebruikt voor het produceren van grote hoeveelheden roestvrij staal, gelegeerd staal, ijzer- en koperpoeders voor pers- en sintertoepassingen.
Parameter | Beschrijving |
---|---|
Gebruikte metalen | Koolstofstaal, laaggelegeerd staal, roestvrij staal, koper, ijzerpoeders |
Deeltjesvorm | Onregelmatige morfologie door explosief breken van water |
Deeltjesgrootte | 10 - 300 μm typisch |
Puurheid | Lager, contact met water verhoogt het zuurstofgehalte met 200-500 ppm |
Productieschaal | Zeer hoog, meer dan 50.000 ton per jaar |
Plasmaverstuiving
Bij het plasmaatomisatieproces wordt een plasmatoorts gebruikt om de metaallegering te smelten voordat deze uiteenvalt in fijne druppeltjes door middel van gasstralen. Door de ultrahoge temperaturen kunnen zeer reactieve elementen zoals titaniumaluminiden met succes worden geatomiseerd.
De poeders hebben een zeer sferische vorm en een smalle grootteverdeling die geschikt is voor additieve productiemethoden zoals lasersmelten en smelten met elektronenbundels.
Parameter | Beschrijving |
---|---|
Gebruikte metalen | Titaanlegeringen, nikkelsuperlegeringen, titaanaluminiden |
Deeltjesvorm | Zeer bolvormig |
Deeltjesgrootte | 15 - 45 μm typisch |
Puurheid | Zeer hoge zuiverheid door smelten onder inerte atmosfeer |
Productieschaal | Lager, ongeveer 100 - 1000 ton per jaar |
Roterend Elektrode Proces (REP)
Bij het roterende elektrodeproces wordt een cilindrische metalen elektrode op hoge snelheid rondgedraaid in een geëvacueerde kamer. Het wordt gesmolten met behulp van een elektrische boog en de gesmolten metaaldruppels die door middel van centrifugale krachten worden weggeslingerd, koelen af tot poeders.
REPoeders hebben een korrelstructuur en morfologie die ideaal is voor warme extrusie tot fijne draden en staven voor luchtvaartlegeringen zoals wolfraam, molybdeen, tantaal.
Parameter | Beschrijving |
---|---|
Gebruikte metalen | Wolfraam, molybdeen, tantaal |
Deeltjesvorm | Onregelmatige, gecontroleerde microstructuur |
Deeltjesgrootte | 45 - 150 μm typisch |
Puurheid | Zeer hoog door verwerking onder vacuüm |
Productieschaal | Kleine volumes hoogwaardige poeders |
Elektrode-inductie gasverstuiving (EIGA)
Het EIGA-proces maakt gebruik van inductieverwarming om verbruikbare elektrodepunten te smelten in een inerte gasatmosfeer. De druppels ondergaan secundaire gasverstuiving door argonstralen tot fijne bolvormige poeders.
EIGA maakt zeer hoge zuiverheid van reactieve nikkelsuperlegeringen mogelijk voor kritieke luchtvaartonderdelen door gecontroleerd smelten en minimaliseren van vervuiling.
Parameter | Beschrijving |
---|---|
Gebruikte metalen | Nikkel superlegeringen, titaanaluminiden |
Deeltjesvorm | Bolvormig |
Deeltjesgrootte | 15 - 53 μm typisch |
Puurheid | Extreem hoog, aangepast voor kritieke legeringen |
Productieschaal | R&D/prototyping tot middelgrote volumes |
Carbonylproces
In het carbonylproces wordt metaal omgezet in een vluchtig carbonyl, dat onder gecontroleerde omstandigheden ontleedt tot uniforme, ultrafijne metaaldeeltjes. Deze aanpak is geschikt voor het produceren van zeer zuivere ijzer-, nikkel- en kobaltpoeders.
Parameter | Beschrijving |
---|---|
Gebruikte metalen | IJzer, nikkel, kobalt |
Deeltjesvorm | Bolvormig tot veelvlakkig |
Deeltjesgrootte | 1 - 10 μm typisch |
Puurheid | Extreem hoge 99,9%+ zuiverheid |
Productieschaal | Tot 30.000 ton per jaar |
Andere poederproductiemethoden
Enkele andere technieken die worden gebruikt voor de productie van speciale metaalpoeders zijn:
- Elektrolytisch proces: Gebruikt voor het produceren van onregelmatig gevormde koper- en nikkelpoeders met dendritische morfologie door middel van elektrodepositieproces
- Metaalreductieprocessen: Reductie van metaaloxiden met behulp van waterstof of koolstof om titaan-, zirkonium-, wolfraam- en molybdeenpoeders te produceren
- Mechanisch legeren: Hoge energie kogelmalen om samengestelde en nanogestructureerde legeringen te synthetiseren
Metaalpoeder Specificaties
Kritische kwaliteitsattributen en specificaties die getest worden voor metaalpoeders hangen af van de productiemethode en de eindtoepassing, maar omvatten meestal:
Poederchemie
- Samenstelling van de legering met optische emissie- of röntgenfluorescentiespectroscopie
- Minder belangrijke legeringselementen
- Onzuiverheidselementen zoals zuurstof, stikstof, waterstof
- Verlies bij ontsteking testen bij hoge temperatuur
Deeltjesgrootteverdeling
- Volume gemiddelde deeltjesgrootte
- Distributiebreedtes zoals D10, D50, D90
Karakterisering deeltjesvorm
- Rasterelektronenmicroscopie voor morfologie
- Vormfactoren zoals hoogte-breedteverhouding en vormfactor
Microstructuur
- Aanwezige fasen met röntgendiffractie
- Korrelkarakteristieken van beeldvorming
Poeder eigenschappen
- Schijnbare/tikdichtheid
- Debiet door Hall flowmeter trechtertests
- Samendrukbaarheidsniveaus
De specificatievereisten voor poeders variëren sterk afhankelijk van het eindgebruik in verschillende toepassingen:
Parameter | Metaalspuitgieten (MIM) | Additieve productie | Persen & Sinteren |
---|---|---|---|
Bereik deeltjesgrootte | 3 - 25 μm | 15 - 45 μm | 150 - 300 μm |
Beeldverhouding | 1 - 1,25 voorkeur | <1,5 sferisch | Niet kritisch |
Zuurstofniveaus | <1000 ppm | <500 ppm | 2000 - 4000 ppm |
Schijnbare dichtheid | >2,5 g/cm3 | >2,8 g/cm3 | 2 - 3 g/cm3 |
Debiet van de hal | 15 - 35 s/50g | 25 – 35 s/50g | >12 s/50g |
Karakterisatiemethoden
Er zijn verschillende analysemethoden die gebruikt worden om de eigenschappen van metaalpoeders te karakteriseren die essentieel zijn voor productprestaties:
Deeltjesgrootteanalyse
Laserdiffractiemethoden worden het meest gebruikt om de deeltjesgrootteverdeling te karakteriseren. Bij deze techniek wordt een laserstraal door een gedispergeerd poedermonster gestuurd dat licht verstrooit onder een hoek die afhankelijk is van de deeltjesgrootte. Computeranalyse van het diffractiepatroon levert binnen enkele seconden gedetailleerde statistisch relevante gegevens over de grootteverdeling.
Morfologie en oppervlaktebeeldvorming
Scanning elektronenmicroscopie (SEM) levert beelden met hoge resolutie van de vorm van poederdeeltjes, oppervlaktetopografieën en kenmerken bij een veel hogere vergroting en focusdiepte dan optische microscopie.
SEM-beeldvorming wordt gebruikt om de deeltjesafronding, satellietvorming, oppervlaktegladheid en defecten zoals porositeit te bestuderen.
Meting van dichtheid en vloei-eigenschappen
Er zijn standaardtestmethoden vastgesteld om het bulkgedrag te kwantificeren met behulp van:
- Hall flowmetertrechter om poederdoorstroming door een opening te meten
- Carney trechter om de stroombaarheid te beoordelen aan de hand van de hellingshoek
- Scott volumeter om de tapdichtheid en samendrukbaarheid te bepalen
Deze methoden helpen bij het voorspellen van het gemak van hanteren, mengen, vullen en spreiden tijdens de productie van componenten.
Röntgenmethoden voor samenstelling en kristalstructuur
- Röntgenfluorescentiespectroscopie identificeert en kwantificeert nauwkeurig de elementaire samenstelling van metalen.
- Röntgendiffractie analyseert de aanwezige atomaire rangschikkingen en fasen aan de hand van diffractiepiekpatronen
-
Ti45Nb poeder voor additieve productie
-
TiNb-legeringspoeder
-
TiNbZrSn-legeringspoeder
-
Ti6Al4V poeder titanium gebaseerde metalen poeder voor additieve productie
-
CPTi-poeder
-
TC18-poeder: ontgrendel de kracht van titaniumcarbide
-
TC11-poeder: een uitgebreide gids
-
TC4 ELI-poeder
-
Beste Ti-6Al-4V-poeder (TC4-poeder) voor additieve productie
Toepassingen van metaalpoeders
Enkele belangrijke eindtoepassingen van metaalpoeders zijn:
Additieve productie
Ook bekend als 3D-printtechnieken zoals selective laser melting (SLM), direct metal laser sintering (DMLS) en electron beam melting (EBM) om complexe geometrieën te bouwen van titanium, aluminium, roestvrij staal, superlegering, kobaltchroompoeders.
Metaalspuitgieten (MIM)
Poeders zoals roestvast staal, titaniumlegeringen en gereedschapsstaal worden gecombineerd met een bindmiddel, spuitgegoten en vervolgens gesinterd om kleine, complexe onderdelen in grote volumes tegen lagere kosten te produceren.
Poedermetallurgie Pers en Sinter
Verdichten en sinteren van ijzer-, koper- en gelegeerde staalpoeders tot componenten met een hoog volume, zoals tandwielen, bussen en magneten.
Sollicitatie | Gebruikte metalen | Behoeften voor belangrijk vastgoed |
---|---|---|
Additieve productie | Titaanlegeringen, nikkelsuperlegeringen, aluminium, gereedschapsstaal, roestvrij staal, kobaltchroom | Sferische morfologie Goede stroombaarheid Hoge zuiverheid |
Metaal spuitgieten | Roestvrij staal, titanium, gereedschapsstaal, zware wolfraamlegeringen | Fijn poeder <25 μm Goede dichtheid |
Pers en sinter | IJzer, staal, roestvrij staal, koper | Rendabele poedercoatings |
Er zijn ook nichetoepassingen op gebieden zoals lassen, diamantgereedschappen, elektronica en oppervlaktecoatings die speciale metaalpoeders gebruiken.
Leveranciers en prijzen
Enkele toonaangevende wereldwijde leveranciers van verschillende metaalpoeders zijn:
Bedrijf | Productie methodes | Materialen |
---|---|---|
Sandvik Visarend | Gasverneveling | Titanium, aluminium, nikkellegeringen |
AP&C | Plasma-verneveling | Titaanaluminiden, superlegeringen |
Timmerman technologie | Gas-, waterverneveling | Gereedschapsstaal, roestvrij staal, legeringen |
Hogenäs | Waterverneveling | IJzer, roestvrij staal |
JFE Staal | Waterverneveling | Poeders van roestvrij staal |
Rio Tinto | Aluminium poeder | Carbonylnikkel en -ijzer |
De prijs van metaalpoeders varieert sterk:
- Materiaal en samenstelling van de legering
- Gebruikte productiemethode
- Verwerking om deeltjeseigenschappen te verkrijgen
- Zuiverheidsniveaus en mate van verontreiniging
- Inkoopvolumes - contracten met zeer grote volumes brengen lagere prijzen met zich mee
Typische basisprijzen per kilogram zijn:
Materiaal | Prijsschatting |
---|---|
Roestvrij staal 316L | $12 - $30 per kg |
Aluminium AlSi10Mg | $15 - $45 per kg |
Titaan Ti-6Al-4V | $80 - $220 per kg |
Nikkel superlegering Inconel 718 | $90 - $250 per kg |
Speciale legeringen voor AM | $250 - $1000 per kg |
De prijzen gaan aanzienlijk omhoog voor sterk aangepaste deeltjesgrootteverdelingen, gecontroleerde zuurstof- en stikstofniveaus onder 100 ppm en aankopen van kleine hoeveelheden.
Voordelen en beperkingen van poedermetallurgie
Voordelen van poedermetallurgie
- Mogelijkheid om complexe geometrieën te produceren die niet mogelijk zijn door gieten of machinaal bewerken
- Near-net-shape productie vermindert materiaalverspilling
- Metalen en legeringen met hogere prestaties kunnen worden gebruikt
- Consistente poreusheidsstructuren die niet mogelijk zijn in de metallurgie van ingots
- Componenten kunnen in massa worden aangepast
Beperkingen van poederproductie en -verwerking
- Kapitaalinvestering voor productie- en verwerkingsapparatuur is zeer hoog
- Verhoogd oppervlak maakt het hanteren van pyrofore reactieve poeders riskant
- Om een hoge verdichtingsdichtheid te bereiken, kan een hoge druk nodig zijn.
- Extra processtappen vergeleken met gieten
- Draagbaarheid van AM-machines doordat het poeder LO/NO is
Hier is een snelle vergelijking van poedermetallurgie met het conventionele gietproces:
Parameter | Poeder-Metallurgie | Gieten |
---|---|---|
Complexe vormen | Uitstekend voor gelaagde AM-bouwwerken | Beperkt voor typische gietstukken |
Mechanische eigenschappen | Kan gegoten eigenschappen na het Hete Isostatische Persen benaderen | Voorspelbare eigenschappen |
Cyclustijd | Langzamer proces voor AM-methoden | ✅ Sneller voor volumeproductie |
Dimensionale nauwkeurigheid | Varieert, afhankelijk van nabewerking | Zeer goed voor precisie-inleggietwerk |
Uitrustingskosten | Zeer hoog voor industriële AM-machines | Lagere kapitaalkosten |
Soorten metalen | Voortdurend uitbreidende opties | Breedste selectie |
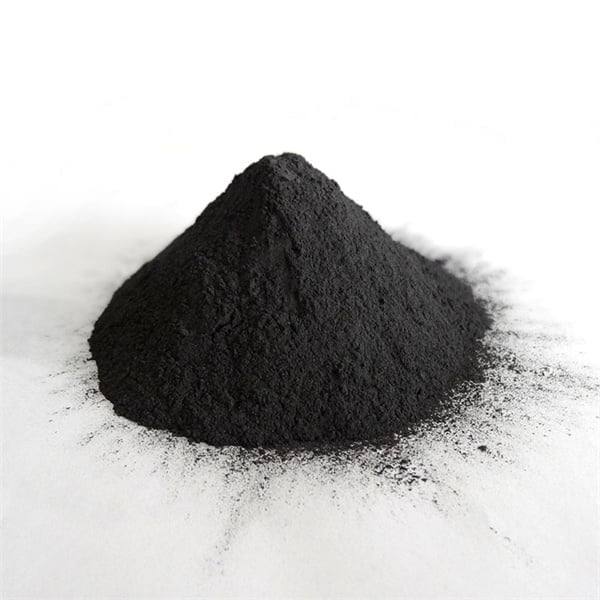
Veelgestelde vragen
V: Wat is de typische deeltjesgrootte die wordt gebruikt in metalen 3D printpoeders?
A: Bij poederbedtechnologieën zoals selectief lasersmelten (SLM) en elektronenbundelsmelten (EBM) is het optimale deeltjesgroottebereik 15-45 micron. Fijnere poeders verbeteren de resolutie, maar kunnen lastig te hanteren en verwerken zijn.
V: Wat bepaalt de morfologie van metaalpoeders met verschillende methoden?
A: Productiefactoren zoals de intensiteit van de afbraakkrachten van de smeltstroom door gasstralen of waterinslagen en de daaropvolgende afkoelsnelheden bepalen de deeltjesvorm. Snellere afkoeling produceert onregelmatige, dendritische deeltjes, terwijl langzamere stolling (bolvormige atomisatie) gladde, ronde structuren mogelijk maakt.
V: Waarom is een hoge zuiverheidsgraad belangrijk voor metaalpoeders in additieve productie?
A: Onzuiverheden kunnen defecten en porositeitsproblemen veroorzaken, de microstructuur van legeringen wijzigen, de dichtheid verminderen en de prestaties onder belastingen en temperaturen beïnvloeden - met negatieve gevolgen voor de mechanische eigenschappen. Streefwaarden voor zuurstof onder 500 ppm en stikstof onder 100 ppm zijn inmiddels gebruikelijk.
V: Hoe worden metaalpoeders veilig behandeld tijdens transport en opslag?
A: Reactieve metaalpoeders worden gepassiveerd om geoxideerde oppervlakken te creëren die het risico op ontvlambaarheid minimaliseren. Poeders worden verzegeld in vaten onder inerte gassen zoals argon in plaats van lucht tijdens transport om ontsteking te voorkomen. Opslagcontainers moeten goed geaard zijn. Personeel draagt speciale persoonlijke beschermingsmiddelen (PPE) tijdens het hanteren.
V: Wat zijn gangbare poederkarakterisatiemethoden?
A: Hall flowmetrie, tapdichtheidstests, pyknometrie, LOI-tests, spectografische analyse, metallografie en deeltjesgrootteverdeling met behulp van laser- of zeeftechnieken zijn van vitaal belang voor het kwantificeren van gedrag, het opbouwen van kwaliteitsprocescontrole voor metaalpoederproductie en het beoordelen van de geschiktheid van batches voor bepaalde toepassingen.
Delen op
MET3DP Technology Co, LTD is een toonaangevende leverancier van additieve productieoplossingen met hoofdkantoor in Qingdao, China. Ons bedrijf is gespecialiseerd in 3D printapparatuur en hoogwaardige metaalpoeders voor industriële toepassingen.
Onderzoek om de beste prijs en een op maat gemaakte oplossing voor uw bedrijf te krijgen!
gerelateerde artikelen
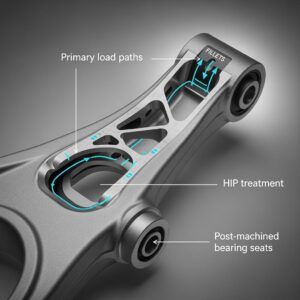
Metal 3D Printing for U.S. Automotive Lightweight Structural Brackets and Suspension Components
Lees verder "Over Met3DP
Recente update
Ons product
NEEM CONTACT MET ONS OP
Nog vragen? Stuur ons nu een bericht! Na ontvangst van uw bericht behandelen wij uw verzoek met een heel team.