Opmerkingen over MIM-technologie
Inhoudsopgave
Spuitgieten van metaal (MIM) is een revolutionair productieproces dat de kloof overbrugt tussen traditionele metaalbewerking en kunststof spuitgieten. Stel je voor dat je ingewikkelde, bijna netvormige metalen onderdelen maakt met de snelheid en kosteneffectiviteit van kunststof spuitgieten - dat is de magie van MIM. Maar voordat we dieper ingaan, lichten we eerst de essentie toe.
Wat is MIM en hoe werkt het?
Zie MIM als een culinair avontuur. Je begint met een fijngemalen metaal, zoals het meel in je favoriete koekjesrecept. Dit metaalpoeder is het hoofdingrediënt en de specifieke eigenschappen ervan bepalen de eigenschappen van het uiteindelijke onderdeel. We zullen later verschillende metaalpoeders onderzoeken. Vervolgens wordt er een bindmiddel, vergelijkbaar met de natte ingrediënten in je deeg, doorheen gemengd. Dit bindmiddel houdt de metaaldeeltjes bij elkaar tijdens het vormproces.
Het resulterende mengsel, dat grondstof wordt genoemd, wordt dan onder hoge druk in een vormholte geïnjecteerd, net zoals je koekjesdeeg door een spuitzak perst. Eenmaal afgekoeld heb je een "groen" deel, dat breekbaar is en nog steeds het bindmiddel bevat. Hier gaat de analogie een beetje mank. Het groene deel ondergaat een ontbindingsproces, waarbij het bindmiddel zorgvuldig wordt verwijderd door een combinatie van warmte en vaak een chemisch oplosmiddel. Stel je voor dat je voorzichtig de chocoladeschilfers uit je koekjesdeeg haalt en alleen de meelstructuur achterlaat.
Ten slotte gaat het onderdeel naar de sinterfase. Zie dit als het bakken van je "gedeblindeerde" deeg. Hoge temperaturen zorgen ervoor dat de metaaldeeltjes zich aan elkaar hechten, waardoor een bijna netvormig metalen onderdeel met een hoge dichtheid ontstaat.
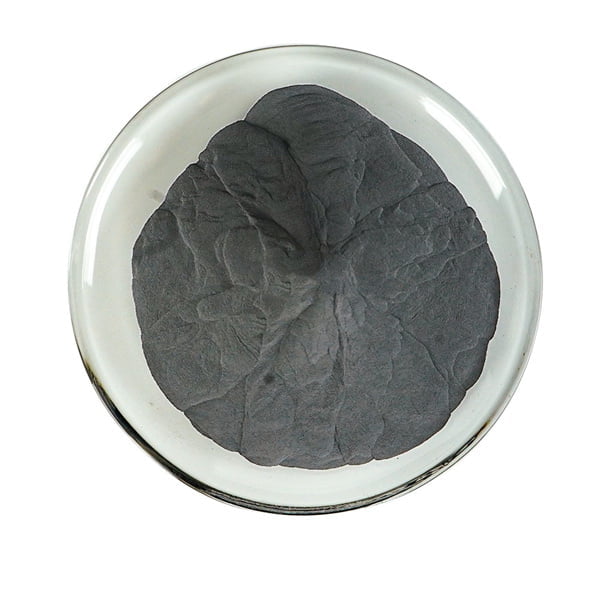
Onthulling van de allure van MIM: Een blik op de voordelen
MIM heeft een fascinerende reeks voordelen die het een aantrekkelijke keuze maken voor verschillende industrieën. Hier zijn enkele belangrijke voordelen die je misschien wel overtuigen:
- Complexe geometrieën: In tegenstelling tot traditionele bewerking blinkt MIM uit in het produceren van ingewikkelde vormen met krappe toleranties. Stelt u zich eens voor: tandwielen met kwetsbare tanden of ingewikkelde medische implantaten - MIM verwerkt deze geometrieën met gemak en bespaart op dure nabewerking.
- Hoge productiesnelheden: MIM blinkt uit in de productie van grote volumes. Vergeleken met het machinaal bewerken van elk onderdeel afzonderlijk, verhoogt het snelle spuitgietproces van MIM de productiesnelheid aanzienlijk, wat zich vertaalt in snellere doorlooptijden en mogelijk lagere kosten.
- Veelzijdigheid van materiaal: MIM is niet beperkt tot één metaal. Er kan een breed scala aan metaalpoeders worden gebruikt, elk met unieke eigenschappen. Dit maakt het mogelijk om de sterkte, corrosiebestendigheid en andere eigenschappen van het onderdeel af te stemmen op specifieke toepassingsbehoeften.
- Maatnauwkeurigheid: MIM-onderdelen hebben een indrukwekkende maatnauwkeurigheid, waardoor uitgebreide nabewerking niet nodig is. Dit leidt tot een consistente productkwaliteit en minder productieafval.
- Kosteneffectiviteit: Voor de productie van grote aantallen complexe onderdelen kan MIM een kosteneffectief alternatief zijn voor traditionele machinale bewerking. De verminderde noodzaak voor machinale bewerking en de minimale materiaalverspilling dragen bij aan de economische aantrekkingskracht.
Metaalpoeders voor MIM
Laten we ons nu eens verdiepen in de wereld van metaalpoeders, het hart en de ziel van MIM. Het specifieke poeder dat gekozen wordt, heeft een grote invloed op de eigenschappen van het uiteindelijke onderdeel. Hier volgt een blik op enkele populaire opties:
Poeders van roestvrij staal:
- 316L: Het meest gebruikte MIM roestvast staal met een uitstekende corrosiebestendigheid en biocompatibiliteit, waardoor het ideaal is voor medische implantaten en voedselverwerkende apparatuur.
- 17-4PH: Een precipitatiehardend roestvrij staal met hoge sterkte, perfect voor toepassingen die uitzonderlijke mechanische sterkte vereisen, zoals onderdelen voor de ruimtevaart.
Poeders van laaggelegeerd staal:
- 46XX-serie: Deze veelzijdige laaggelegeerde staalsoorten bieden een goede balans tussen sterkte, taaiheid en betaalbaarheid, waardoor ze geschikt zijn voor de auto-industrie en algemene technische toepassingen.
Poeders voor gereedschapsstaal:
- H13: Dit hooggelegeerde gereedschapsstaal heeft een uitstekende slijtvastheid, waardoor het ideaal is voor matrijzen en stempels die worden gebruikt bij metaalvormprocessen.
Poeders voor legeringen op basis van nikkel:
- Inconel 625: Deze hoogwaardige superlegering op basis van nikkel biedt uitzonderlijke weerstand tegen hoge temperaturen en corrosie, waardoor het perfect is voor veeleisende toepassingen zoals straalmotoren en chemische verwerkingsapparatuur.
Andere metaalpoeders:
MIM is niet beperkt tot deze opties. Andere materialen zoals koper, titanium en wolfraam kunnen ook worden gebruikt, waardoor de potentiële toepassingen van deze veelzijdige technologie worden uitgebreid.
Factoren die de materiaalselectie beïnvloeden
Het juiste metaalpoeder kiezen voor je MIM project vereist een zorgvuldige afweging van verschillende factoren:
- Gewenste eigenschappen: Wat zijn de kritieke eigenschappen voor uw onderdeel? Sterkte, corrosiebestendigheid, hittetolerantie - elk metaalpoeder biedt een unieke mix van eigenschappen.
- Complexiteit van geometrie: Sommige poeders vloeien beter dan andere, wat invloed heeft op de mogelijkheid om ingewikkelde vormen te maken.
- Kostenoverwegingen: De materiaalkosten kunnen aanzienlijk variëren.
- Onderdeelgrootte: De grootte van de poederdeeltjes kan de minimaal haalbare vormgrootte in het uiteindelijke onderdeel beïnvloeden.
- Vereisten voor nabewerking: Sommige metaalpoeders vereisen extra behandelingen na het sinteren, zoals infiltratie voor verbeterde sterkte of warmtebehandeling voor verbeterde mechanische eigenschappen. Deze extra stappen kunnen de totale kosten en productietijd beïnvloeden.
de toepassingen van MIM-technologie
De diverse mogelijkheden van MIM hebben deuren geopend voor de toepassing ervan in een groot aantal industrieën. Hier volgen enkele prominente voorbeelden:
- Medische hulpmiddelen: Het vermogen van MIM om ingewikkelde, biocompatibele onderdelen te maken, maakt het ideaal voor de productie van medische implantaten zoals gewrichtsprothesen, stents en chirurgische instrumenten.
- Ruimtevaart en defensie: De hoge sterkte-gewichtsverhouding en hittebestendigheid van sommige MIM-materialen maken ze geschikt voor luchtvaartonderdelen, zoals turbinebladen en motoronderdelen. Bovendien kunnen met MIM complexe vuurwapenonderdelen met nauwe toleranties worden gemaakt.
- Automobiel: MIM vindt zijn plaats in automobieltoepassingen zoals tandwielen, transmissieonderdelen en onderdelen van het brandstofsysteem omdat het ingewikkelde vormen kan maken met een hoge productiesnelheid.
- Consumentenelektronica: Kleine, complexe onderdelen die worden gebruikt in elektronische apparaten, zoals connectoren en behuizingen, kunnen efficiënt worden geproduceerd met MIM.
- Telecommunicatie: MIM wordt gebruikt om ingewikkelde onderdelen voor telecommunicatieapparatuur te maken omdat het nauwe toleranties en maatnauwkeurigheid kan bereiken.
Voordelen en beperkingen van MIM
Hoewel MIM over een indrukwekkende reeks voordelen beschikt, is het essentieel om de beperkingen te erkennen om weloverwogen beslissingen te kunnen nemen. Hier volgt een evenwichtig perspectief:
Voordelen:
- Complexe geometrieën: Zoals eerder besproken blinkt MIM uit in het produceren van ingewikkelde vormen, waardoor er minder complexe nabewerking nodig is.
- Hoge productiesnelheden: Voor massaproductie biedt MIM aanzienlijke voordelen in termen van snelheid en efficiëntie vergeleken met traditionele bewerkingsmethoden.
- Veelzijdigheid van materiaal: Dankzij de mogelijkheid om een breed scala aan metaalpoeders te gebruiken, kunnen onderdelen worden aangepast aan specifieke toepassingsbehoeften.
- Maatnauwkeurigheid: MIM-onderdelen bereiken een indrukwekkende maatnauwkeurigheid, waardoor uitgebreide nabewerking niet nodig is.
Beperkingen:
- Beperkingen in onderdeelgrootte: Er zijn beperkingen aan de maximale grootte van onderdelen die geproduceerd kunnen worden met MIM. Zeer grote of omvangrijke onderdelen zijn mogelijk niet geschikt voor dit proces.
- Afwerking oppervlak: MIM-onderdelen hebben meestal een ruwere oppervlakteafwerking dan machinaal bewerkte onderdelen. Dit kan extra nabewerkingsprocessen noodzakelijk maken, afhankelijk van de toepassingseisen.
- Materiaaleigenschappen: Hoewel er verschillende metaalpoeders bestaan, kunnen sommige eigenschappen die via traditionele processen kunnen worden bereikt, niet volledig worden gerepliceerd met MIM. Het bereiken van de allerhoogste sterktes in sommige metalen kan bijvoorbeeld een uitdaging zijn met MIM.
- Ontwikkelingskosten: Het opzetten van een MIM-productielijn kan aanzienlijke aanloopkosten met zich meebrengen. Dit kan een overweging zijn voor projecten met lagere productievolumes.
Selecteren MIM voor uw project
MIM is een krachtig hulpmiddel voor het vervaardigen van complexe metalen onderdelen. Maar om te bepalen of MIM de juiste keuze is voor jouw project, moet je de volgende factoren in overweging nemen:
- Deel Complexiteit: Als je onderdeel ingewikkelde vormen met krappe toleranties moet hebben, kan MIM een uitstekende optie zijn.
- Productievolume: Voor massaproductie kan MIM aanzienlijke kosten- en tijdbesparingen opleveren ten opzichte van traditionele machinale bewerking.
- Materiaalvereisten: Evalueer de kritieke eigenschappen die nodig zijn voor je onderdeel en zorg ervoor dat het gekozen metaalpoeder deze eigenschappen kan leveren.
- Projectbudget: Overweeg de kostenimplicaties van MIM, inclusief potentiële ontwikkelingskosten vooraf en vereisten voor nabewerking.
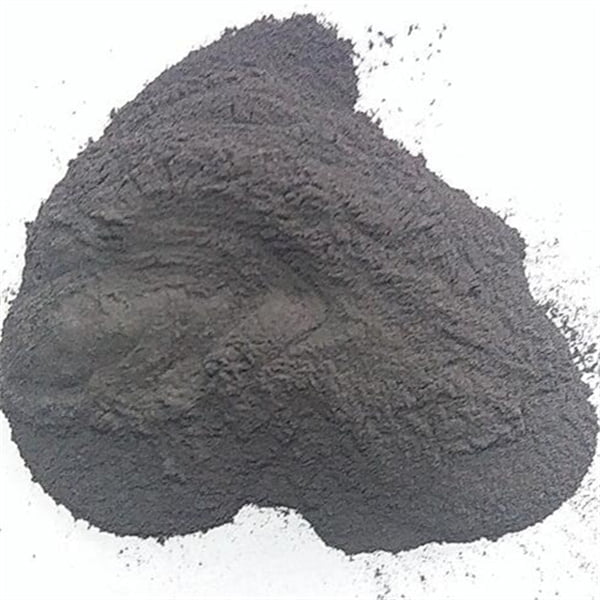
FAQ
V: Wat zijn de voordelen van MIM ten opzichte van traditionele bewerking?
MIM biedt verschillende voordelen, zoals de mogelijkheid om complexe geometrieën te produceren, hoge productiesnelheden en veelzijdigheid van materialen. Bovendien kan MIM een goede maatnauwkeurigheid bereiken, waardoor mogelijk uitgebreide nabewerking minder nodig is.
V: Wat zijn de beperkingen van MIM?
Er zijn beperkingen aan de maximale onderdeelgrootte die haalbaar is met MIM. Bovendien hebben MIM-onderdelen meestal een ruwere oppervlakteafwerking dan machinaal bewerkte onderdelen. De materiaaleigenschappen die met MIM haalbaar zijn, kunnen ook iets afwijken van die van traditionele processen.
V: Welke soorten metaalpoeders kunnen worden gebruikt in MIM?
Bij MIM kan een breed scala aan metaalpoeders worden gebruikt, waaronder roestvast staal, laaggelegeerd staal, gereedschapsstaal en legeringen op nikkelbasis. Het specifieke poeder dat gekozen wordt, heeft een grote invloed op de eigenschappen van het uiteindelijke onderdeel.
V: Is MIM geschikt voor de productie van kleine aantallen?
Hoewel MIM een goede optie kan zijn voor de productie van grote volumes, kunnen de ontwikkelingskosten vooraf zwaarder wegen dan de voordelen voor projecten met kleine volumes. Traditionele bewerking kan in zulke gevallen geschikter zijn.
De toekomst van MIM-technologie:
De MIM-technologie ontwikkelt zich voortdurend, met vooruitgang in materialen, verwerkingstechnieken en ontwerpsoftware. Hier zijn enkele spannende mogelijkheden aan de horizon:
- Nieuwe metaalpoeders: De ontwikkeling van nieuwe metaalpoeders met verbeterde eigenschappen zoals hogere sterkte, betere corrosiebestendigheid of zelfs de mogelijkheid om functionele onderdelen te printen zal de toepassingen van MIM uitbreiden.
- Integratie van additieve productie: Het combineren van MIM met additieve productietechnieken zoals 3D-printen is veelbelovend voor het maken van nog complexere geometrieën en het mogelijk personaliseren van onderdelen.
- Verbeteringen op het gebied van duurzaamheid: Het verminderen van afval en het minimaliseren van energieverbruik tijdens het MIM-proces zijn doorlopende onderzoeksgebieden. Duurzame praktijken zullen in de toekomst steeds belangrijker worden.
Conclusie
MIM-technologie biedt een overtuigende oplossing voor de productie van complexe, bijna netvormige metalen onderdelen met een hoge productie-efficiëntie. Als u de mogelijkheden, beperkingen en ontwerpoverwegingen begrijpt, kunt u weloverwogen beslissingen nemen over de geschiktheid voor uw project. Naarmate de MIM-technologie zich verder ontwikkelt, zal deze een nog belangrijkere rol gaan spelen in het vormgeven van de toekomst van metaalproductie.
Delen op
MET3DP Technology Co, LTD is een toonaangevende leverancier van additieve productieoplossingen met hoofdkantoor in Qingdao, China. Ons bedrijf is gespecialiseerd in 3D printapparatuur en hoogwaardige metaalpoeders voor industriële toepassingen.
Onderzoek om de beste prijs en een op maat gemaakte oplossing voor uw bedrijf te krijgen!
gerelateerde artikelen
Over Met3DP
Recente update
Ons product
NEEM CONTACT MET ONS OP
Nog vragen? Stuur ons nu een bericht! Na ontvangst van uw bericht behandelen wij uw verzoek met een heel team.
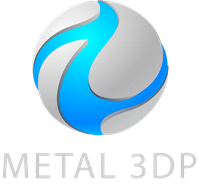
Metaalpoeders voor 3D printen en additieve productie