MIM-productie: een complete gids
Inhoudsopgave
Overzicht van MIM-productie
Metaalspuitgieten (MIM) is een poedermetallurgisch productieproces dat wordt gebruikt om kleine, complexe metalen onderdelen in grote volumes te produceren.
De belangrijkste stappen in MIM zijn onder meer:
- Fijn metaalpoeder mengen met bindmiddel om een grondstof te creëren
- Het injecteren van de grondstof in een mal met behulp van kunststofspuitgieten
- Ontbinden om het bindmiddel te verwijderen, waardoor alleen het metaalpoeder overblijft
- Sinteren om het poeder te verdichten tot een vast metalen onderdeel
MIM combineert de ontwerpflexibiliteit van kunststofspuitgieten met de sterkte en prestaties van bewerkte metalen. Het is een kosteneffectief proces voor de complexe productie van grote hoeveelheden kleine onderdelen.
Hoe MIM-productie werkt
Het MIM-productieproces omvat:
- Formuleren van een grondstof door fijn metaalpoeder te mengen en te pelletiseren met polymeerbindmiddelen
- Het verhitten van de grondstof en het spuitgieten ervan in de gewenste vorm
- Chemisch verwijderen van het bindmiddel door middel van oplosmiddel of thermische ontbinding
- Het sinteren van het ongebonden metaalcomponent in een oven om een volledig dicht onderdeel te produceren
- Optionele secundaire afwerkingsbewerkingen zoals machinaal bewerken, boren, galvaniseren
MIM maakt de economische productie mogelijk van componenten met complexe geometrieën, nauwe toleranties en uitstekende mechanische eigenschappen.
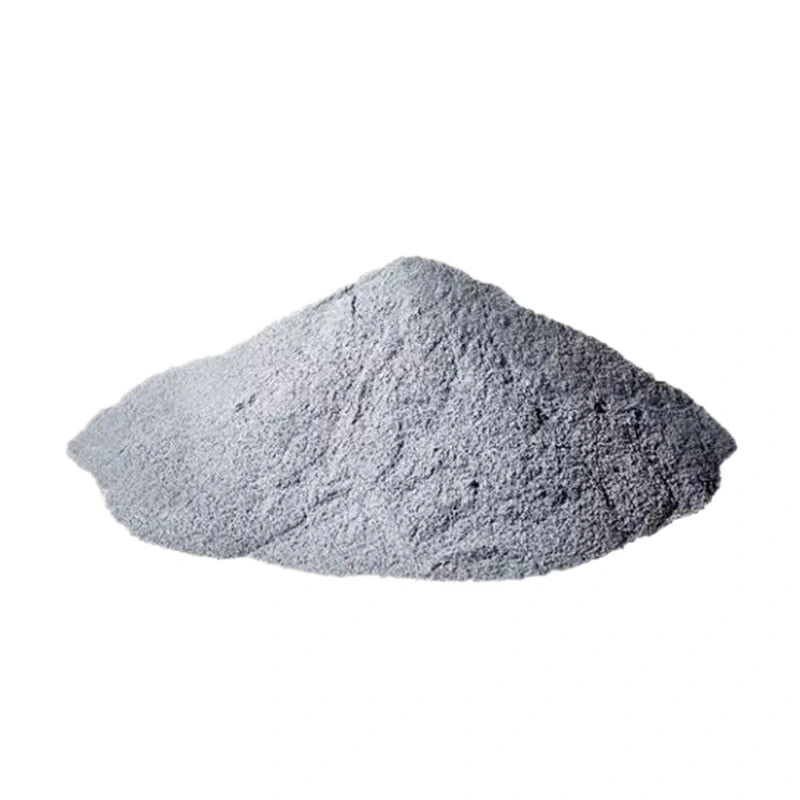
Soorten metalen die in MIM worden gebruikt
Met MIM-technologie kan een breed scala aan metalen worden verwerkt:
- Roestvast staal – 316L, 17-4PH, 410, 420
- Gereedschapsstaal – H13, P20, A2, D2
- Magnetische legeringen – Zachte en harde ferrieten
- Koperlegeringen – Messing, brons
- Laaggelegeerd staal – 4100, 4600
- Superlegeringen – Inconel 625, 718
- Wolfraam zware legeringen
- Titaniumlegeringen – Ti6Al4V, Ti6Al4V ELI
MIM is over het algemeen geschikt voor elk materiaal dat tot hoge dichtheid kan worden gesinterd. Metalen met smeltpunten lager dan 1000°C hebben de voorkeur.
MIM-productieprocesparameters
Kritische procesparameters in MIM zijn onder meer:
Ontwikkeling van grondstoffen:
- Poedermorfologie, grootteverdeling
- Samenstelling bindmiddel
- Poederlading – doorgaans 60-65 vol%
- Mengproces – temperatuur, tijd, atmosfeer
Vormen:
- Matrijsmateriaal – Bij voorkeur P20-gereedschapsstaal
- Injectietemperatuur, druk, snelheid
- Poort ontwerp
- Ontwerp van het koelsysteem
Ontbinding:
- Oplosmiddel, thermische of katalytische ontbinding
- Ontbindingstemperatuur, tijd, atmosfeer
Sinteren:
- Temperatuurprofiel – stappen van ontbinden, sinteren
- Verwarmingssnelheid, sintertijd, atmosfeer
- Sintertemperatuur en -druk
MIM-ontwerp en onderdeeloverwegingen
Het MIM-proces maakt ontwerpvrijheid mogelijk, maar er moeten enkele richtlijnen worden gevolgd:
- Wanddikte: 0,3 – 4 mm bereik mogelijk
- Oppervlakteafwerking: As-sintered is ongeveer Ra 1,5 μm
- Dimensionale toleranties: ±0,5% is standaard, maar ±0,1% haalbaar
- Opgesloten poeder vermijden: Geen volledig afgesloten interne holtes
- Diepgangshoeken: Bij voorkeur > 1° diepgangshoek
- Sinterkrimp: Ongeveer 20% volumetrische krimp
- Vermindering van defecten: royale hoekradii minimaliseren scheuren
Geavanceerde simulatietools maken virtuele optimalisatie van het MIM-proces tijdens het ontwerp mogelijk om vallen en opstaan te verminderen.
Voordelen van MIM-productie
De belangrijkste voordelen van het gebruik van MIM zijn onder meer:
- Complexe geometrieën en nauwe toleranties
- Uitstekende mechanische eigenschappen
- Breed scala aan materiaalopties
- Hoge productieaantallen tegen lage kosten
- Minimaliseert verspilling – bijna netvormproces
- Minder bewerking en afwerking
- Componentintegratie en deelconsolidatie
- Geautomatiseerd proces geschikt voor werking zonder verlichting
- Milieuvriendelijker dan verspanen
- Schaalbaar van prototypes tot volledige productie
De voordelen maken MIM geschikt voor het kosteneffectief vervaardigen van metalen precisiecomponenten in grote volumes in verschillende sectoren.
Beperkingen en uitdagingen van MIM
Enkele beperkingen die verband houden met MIM:
- Beperkte omvang – doorgaans <45 g afgewerkte massa per onderdeel
- Beperkt tot metalen die tot hoge dichtheid kunnen sinteren
- Uitgebreide expertise vereist op het gebied van de formulering van grondstoffen
- Aanloopkosten voor matrijs- en procesontwikkeling
- Rechte delen en scherpe hoeken zijn gevoelig voor scheuren
- Langere doorlooptijd vergeleken met andere processen
- Nabewerking is vaak nodig om de uiteindelijke eigenschappen te bereiken
- Gebrek aan ontwerpvrijheid bij sommige functies, zoals threads
- Secundaire bewerking kan een uitdaging zijn op gesinterde metalen
Met het juiste grondstoffen- en procesontwerp dat is afgestemd op de toepassing, kunnen deze uitdagingen worden overwonnen om het volledige potentieel van MIM-technologie te benutten.
Toepassingen van door MIM vervaardigde onderdelen
MIM vindt wijdverbreid gebruik in de volgende sectoren:
Automobiel: Vergrendel hardware, sensoren, brandstofsysteem en motorcomponenten
Lucht- en ruimtevaart: Waaiers, sproeiers, kleppen, bevestigingsmiddelen
Medisch: Tandimplantaten, scalpelhandvatten, orthopedische instrumenten
Vuurwapens: Triggers, magazijnen, slides, hamers
Horloges: Kasten, armbandschakels, sluitingen en gespen
Elektrisch: Connectoren en leadframes voor betrouwbaarheid
Typische onderdeelgroottes variëren van 0,1 gram tot 110 gram, met de grootste commerciële productievolumes in connectoren, bevestigingsmiddelen, chirurgische instrumenten en orthodontische beugels.
Kostenanalyse van MIM-productie
MIM-productiekosten omvatten:
- Ontwikkeling van grondstoffen – Formulering, mengen, karakterisering
- Vorm fabricage – Vormbewerking met hoge precisie
- MIM-machine – Grote investeringen in kapitaalgoederen
- Operatie – Arbeid, nutsvoorzieningen, verbruiksartikelen
- Secundaire operaties – Ontbinden, sinteren, afwerken
- Materiaalgebruik – Metaalpoeder is goed voor ongeveer 60% van de totale kosten
- Verbruiksartikelen – Meerdere vormholtes om een hoog volume mogelijk te maken
- Productie volume – Instelkosten afgeschreven over het totale volume
- Buy-to-fly-ratio – Slechts 2-4x vergeleken met andere PM-processen
- Ontwerpoptimalisatie – Eenvoudige geometrieën met minimale bewerking
Voor grote productievolumes levert MIM zeer gunstige kosten bij hoge productiesnelheden met uitstekend materiaalgebruik en bijna netvormige mogelijkheden.
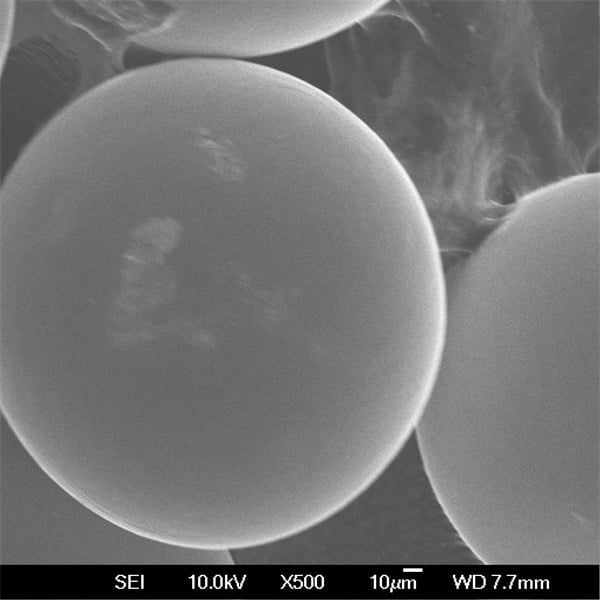
Het selecteren van een MIM-productie Partner
Belangrijke factoren bij het selecteren van een MIM-leverancier:
- Aantoonbare expertise en jarenlange ervaring met MIM
- Materialenportfolio – assortiment roestvrij staal, gereedschapsstaal en superlegeringen
- Kwaliteitscertificeringen – bij voorkeur ISO 9001, ISO 13485
- Secundaire verwerkingsmogelijkheden – bewerking, warmtebehandeling, oppervlakteafwerking
- Strenge procedures voor proces- en productkwaliteitscontrole
- R&D-mogelijkheden voor de formulering van grondstoffen en procesontwikkeling
- Vormstroomsimulatie en andere expertise op het gebied van ontwerpanalyse
- Programmamanagementvaardigheden om klantprojecten te ondersteunen
- Schaalbare capaciteit die kan meegroeien met de productiebehoeften
- Concurrerende prijzen met meerjarige overeenkomsten
- Locatie die nauwe samenwerking en IP-bescherming mogelijk maakt
Het selecteren van een gevestigde MIM-producent met een nichefocus op MIM levert de beste resultaten op, in tegenstelling tot een algemene CNC-metaalbewerkingswerkplaats.
Voor- en nadelen van MIM versus CNC-bewerking
Voordelen van MIM:
- Uitstekende maatnauwkeurigheid en herhaalbaarheid
- Complexe geometrieën die onbereikbaar zijn door machinale bewerking
- Bijna netvorm met minimaal materiaalverlies
- Schaalt efficiënt naar zeer hoge productievolumes
- Geautomatiseerd proces maakt 24/7 werking mogelijk
- Kortere doorlooptijden na installatie
- Aanzienlijk lagere onderdeelkosten bij hoge volumes
- Eigenschappen komen overeen met of overtreffen machinaal bewerkte metalen
Nadelen van MIM:
- Hoge initiële instelkosten voor grondstoffen en schimmels
- Beperkte afmetingen
- Beperkte ontwerpvrijheid in sommige functies
- Lagere initiële productiehoeveelheden zijn inefficiënt
- Uitgebreide expertise vereist op het gebied van de formulering van grondstoffen
- Secundaire afwerkingsbewerkingen kunnen nog steeds nodig zijn
- Langere doorlooptijden en lagere kwaliteit voor eerste prototypes
Voor kleine complexe metalen onderdelen die in zeer grote volumes worden geproduceerd, wordt MIM de meest tijd- en kostenefficiënte productiemethode.
Vergelijking tussen MIM en metaal 3D-printen
Belangrijkste verschillen tussen MIM en 3D-printen:
Parameter | MIM | 3d printen |
---|---|---|
Proces | Bindmiddel spuitgieten + sinteren | Poederbedfusie of binding |
Materialen | Breed scala aan legeringen | Beperkte materiaalopties |
Onderdeelgrootte | < 45 gram | Tot enkele kg |
Nauwkeurigheid | Uitstekend, ±0,5% | Matig, ±1% |
Oppervlakteafwerking | Erg goed | Middelmatig tot arm |
Productieschaal | Van 10.000 tot miljoenen | Prototyping tot middelgrote volumes |
Kosten per onderdeel | Heel laag | Gemiddeld tot hoog |
Secundaire afwerking | Mogelijk vereist | Meestal vereist |
Doorlooptijd | Langer voor procesontwikkeling | Snellere prototypes maar langzamere serieproductie |
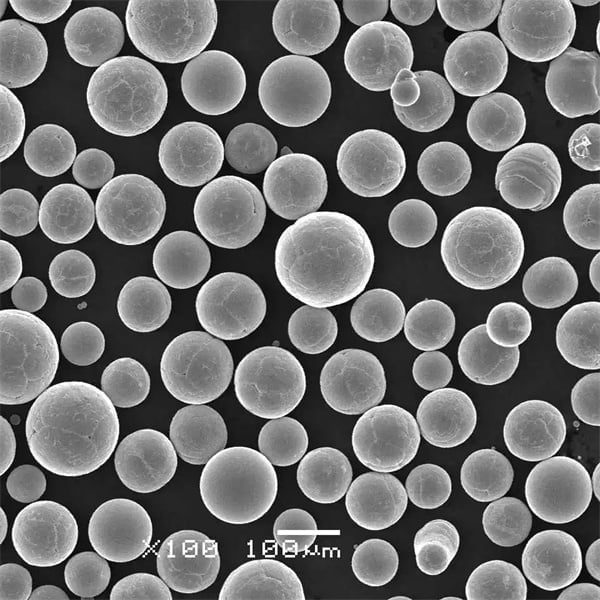
FAQ
Wat is het typische tolerantievermogen voor MIM-productie?
MIM kan op betrouwbare wijze maattoleranties van ±0,5% bereiken met geavanceerde processen die een tolerantie van ±0,1% kunnen bereiken voor kleine precisiecomponenten.
Wat zijn gebruikelijke MIM-grondstofsamenstellingen?
Typische MIM-grondstoffen bestaan uit een belading van metaalpoeder 60-65% met een bindmiddel 35-40% dat polymeren zoals polypropyleen, polyethyleen en polystyreen omvat. Wassen helpen de poederstroom te verbeteren.
Kan MIM onderdelen in meerdere materialen vervaardigen?
Ja, MIM kan composiet- en gegradeerde structuren produceren door verschillende grondstoffen in elke vormholte te spuitgieten of bindmiddelen met verschillende smeltpunten te gebruiken.
Welke vormdeelgrootte kan met MIM worden bereikt?
MIM-vormstukken zijn doorgaans beperkt tot onderdelen die kleiner zijn dan 45 gram in massa en afmetingen van minder dan 50 mm. Grotere of zwaardere componenten zijn moeilijk voldoende te vullen en te verdichten.
Hoe verhoudt MIM zich tot spuitgieten voor kleine metalen componenten?
MIM biedt een hogere maatnauwkeurigheid en materiaalsterkte, maar spuitgieten heeft snellere cyclustijden. MIM is geschikter voor complexe geometrieën, terwijl spuitgieten de voorkeur heeft voor eenvoudigere vormen.
Delen op
MET3DP Technology Co, LTD is een toonaangevende leverancier van additieve productieoplossingen met hoofdkantoor in Qingdao, China. Ons bedrijf is gespecialiseerd in 3D printapparatuur en hoogwaardige metaalpoeders voor industriële toepassingen.
Onderzoek om de beste prijs en een op maat gemaakte oplossing voor uw bedrijf te krijgen!
gerelateerde artikelen
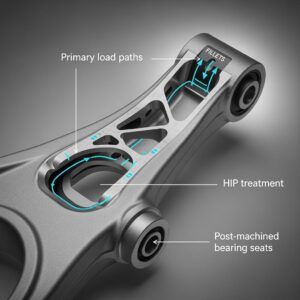
Metal 3D Printing for U.S. Automotive Lightweight Structural Brackets and Suspension Components
Lees verder "Over Met3DP
Recente update
Ons product
NEEM CONTACT MET ONS OP
Nog vragen? Stuur ons nu een bericht! Na ontvangst van uw bericht behandelen wij uw verzoek met een heel team.