inleiding tot selectief lasersmelten (SLM)
Inhoudsopgave
Ik lever graag een informatief en uitgebreid artikel over Selective Laser Melting (SLM), met de gevraagde structuur, SEO-optimalisatie en boeiende verhaalbenadering, terwijl we ons houden aan uw specifieke richtlijnen:
Selectief lasersmelten (SLM)
Stelt u zich eens een wereld voor waarin complexe metalen onderdelen, die voorheen onmogelijk met traditionele technieken te maken waren, laag voor laag met ongelooflijke precisie gemaakt kunnen worden. Deze visionaire sprong wordt werkelijkheid met Selective Laser Melting (SLM), een additieve vervaardiging (AM) proces dat het landschap van metaalproductie verandert.
Wat is SLM?
De kern van SLM, ook bekend als direct metaallasersinteren (DMLS)is een poederbedfusie (PBF) techniek die gebruikmaakt van een krachtige laser om selectief metaalpoederdeeltjes te smelten, waardoor een driedimensionaal object laag voor laag wordt opgebouwd. Deze laag-voor-laag benadering, die lijkt op het bouwen met kleine Legoblokjes, maakt het mogelijk om ingewikkelde geometrieën, holle structuren en interne kenmerken te creëren die onbereikbaar zijn met conventionele methoden zoals gieten of machinaal bewerken.
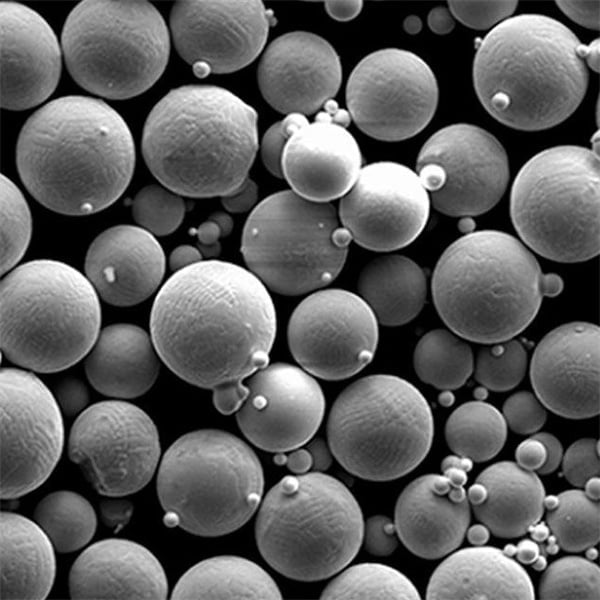
De magie van SLM
- CAD-ontwerp: De reis begint met een CAD-model (Computer Aided Design), waarmee de digitale blauwdruk van het gewenste onderdeel tot leven wordt gewekt.
- Voorbereiding poederbed: Een dunne laag metaalpoeder, zorgvuldig gekozen op basis van zijn eigenschappen en beoogde toepassing, wordt verspreid over een platform in de SLM-machine.
- Lasersmelten: Een krachtige laserstraal, meestal een Yb-vezellaser, scant het poederbed aan de hand van de digitale plak uit het CAD-model. De gerichte energie van de laser smelt precies de aangewezen gebieden, waardoor de metaaldeeltjes samensmelten tot een vaste laag.
- Laag voor laag: Het platform zakt iets naar beneden en er wordt een nieuwe laag poeder afgezet. Deze nauwgezette dans van lasersmelten en poederafzetting gaat door, waarbij het object laag voor laag wordt opgebouwd totdat het compleet is.
- Nabewerking: Zodra het geprinte onderdeel klaar is, wordt de ondersteuningsstructuur verwijderd en afhankelijk van het materiaal en de toepassing kunnen aanvullende behandelingen nodig zijn, zoals warmtebehandeling of oppervlakteafwerking.
Geschikt metaalpoeder voor SLM
Het succes van SLM hangt af van de keuze van het juiste metaalpoeder. Elk materiaal heeft unieke eigenschappen die van invloed zijn op de printbaarheid, mechanische prestaties en kosten. Hier volgt een overzicht van tien veelgebruikte metaalpoeders voor SLM:
Metaalpoeder | Samenstelling | Eigenschappen | Toepassingen |
---|---|---|---|
Roestvrij staal 316L | Fe (66-70%), Cr (16-18%), Ni (10-14%), Mo (2-3%), Si (<1%), Mn (<2%). | Uitstekende corrosiebestendigheid, hoge sterkte, biocompatibel | Ruimtevaartonderdelen, medische implantaten, chemische verwerkingsapparatuur |
Titaan Ti6Al4V | Ti (89-92%), Al (5,5-6,5%), V (3,5-4,5%) | Hoge sterkte-gewichtsverhouding, goede corrosiebestendigheid, biocompatibel | Ruimtevaartonderdelen, medische implantaten, sportartikelen |
Inconel 625 | Ni (58%), Cr (20-23%), Mo (9%), Fe (5%), Mn (2%) | Hoge temperatuursterkte, uitstekende corrosiebestendigheid | Onderdelen van gasturbines, warmtewisselaars, apparatuur voor chemische verwerking |
Aluminium AlSi10Mg | Al (88-92%), Si (9-11%), Mg (0,3-0,6%) | Goede sterkte, lichtgewicht, uitstekende bedrukbaarheid | Auto-onderdelen, ruimtevaartonderdelen, consumentenelektronica |
Koper Cu | Cu (99,9%) | Hoge elektrische geleidbaarheid, goede thermische geleidbaarheid | Warmtewisselaars, elektrische componenten, vloeistofbehandelingssystemen |
Nikkel Ni | Nikkel (99,5%) | Hoge elektrische geleidbaarheid, magnetische eigenschappen | Elektrische componenten, sensoren, katalysatoren |
Kobalt CrCo | Co (60%), Cr (20%), W (15%) | Hoge slijtvastheid, goede weerstand tegen corrosie | Snijgereedschappen, slijtvaste onderdelen, mallen |
Gereedschapstaal | Varieert afhankelijk van het specifieke type | Hoge hardbaarheid, slijtvastheid | Snijgereedschappen, matrijzen, mallen |
Edelmetalen (Goud, Zilver, Platina) | Afhankelijk van het metaal | Hoge waarde, specifieke elektrische eigenschappen | Juwelen, elektronica, medische apparatuur |
-
Ti45Nb poeder voor additieve productie
-
TiNb-legeringspoeder
-
TiNbZrSn-legeringspoeder
-
Ti6Al4V poeder titanium gebaseerde metalen poeder voor additieve productie
-
CPTi-poeder
-
TC18-poeder: ontgrendel de kracht van titaniumcarbide
-
TC11-poeder: een uitgebreide gids
-
TC4 ELI-poeder
-
Beste Ti-6Al-4V-poeder (TC4-poeder) voor additieve productie
de voordelen en beperkingen van SLM
De voordelen van SLM:
- Ontwerpvrijheid: Met SLM kunnen complexe geometrieën, interne kanalen en lichtgewicht structuren worden gemaakt, waardoor de grenzen van de ontwerpmogelijkheden worden verlegd.
- Materiële diversiteit: Een uitgebreide reeks metaalpoeders is geschikt voor diverse toepassingen, waardoor materiaal kan worden geselecteerd op basis van specifieke prestatiebehoeften.
- Minder afval: Vergeleken met traditionele subtractieve productietechnieken minimaliseert SLM materiaalverspilling, wat duurzaamheid bevordert.
De voordelen van SLM (vervolg):
- Flexibele productie: SLM maakt het mogelijk om losse onderdelen of kleine series te maken zonder dure gereedschappen, waardoor on-demand productie en rapid prototyping mogelijk worden.
- Verbeterde functionaliteit: Met SLM kunnen complexe onderdelen in één onderdeel worden geïntegreerd, waardoor de functionaliteit toeneemt en de assemblage minder complex wordt.
De beperkingen van SLM:
- Kosten: SLM-machines en metaalpoeders kunnen duur zijn, waardoor deze technologie minder geschikt is voor productie van grote volumes tegen lage kosten.
- Oppervlakteruwheid: Door de laag voor laag aard van het proces kunnen SLM onderdelen een iets ruwere oppervlakteafwerking vertonen dan sommige traditionele methoden. Technieken voor nabewerking kunnen dit echter tot op zekere hoogte verminderen.
- Materiaaleigenschappen: Hoewel de mechanische eigenschappen van SLM onderdelen over het algemeen goed zijn, komen ze niet altijd perfect overeen met die van traditioneel vervaardigde onderdelen, vooral bij specifieke legeringen. Voortdurend onderzoek en ontwikkeling verbeteren de materiaaleigenschappen van SLM voortdurend.
- Beperkingen in bouwgrootte: De bouwgrootte van SLM-machines is momenteel beperkt in vergelijking met sommige conventionele technieken. Er worden echter steeds grotere machines ontwikkeld.
toepassing van SLM
SLM transformeert gestaag verschillende industrieën en laat zijn sporen na:
Lucht- en ruimtevaart: Het vermogen van SLM om lichtgewicht componenten met hoge sterkte te maken, zorgt voor een revolutie in het ontwerp van vliegtuigen en leidt tot verbeteringen in brandstofefficiëntie en prestatieoptimalisatie.
Auto's: De auto-industrie maakt gebruik van SLM voor prototyping, het maken van lichtgewicht structurele onderdelen en zelfs het produceren van op maat gemaakte onderdelen voor high-performance voertuigen.
Medische hulpmiddelen: SLM speelt een cruciale rol in de ontwikkeling van op maat gemaakte implantaten, prothesen en chirurgische instrumenten, en biedt verbeterde biocompatibiliteit en patiëntspecifieke oplossingen.
Consumptiegoederen: Van gepersonaliseerde sieraden en sportartikelen tot innovatieve consumentenelektronica, SLM maakt de creatie van unieke en functionele producten mogelijk.
De toekomst van SLM: Een blik op de horizon
Naarmate onderzoek en ontwikkeling op het gebied van SLM vorderen, kunnen we nog meer opwindende ontwikkelingen verwachten:
- Geavanceerde materialen: Er wordt voortdurend onderzoek gedaan naar nieuwe metaalpoeders met verbeterde eigenschappen, zoals verbeterde sterkte, hittebestendigheid en biocompatibiliteit.
- Snellere printsnelheden en grotere bouwgroottes: Vooruitgang in lasertechnologie en machineontwerp verleggen de grenzen van printsnelheid en bouwgrootte.
- Lagere kosten: Naarmate de technologie volwassener wordt en meer wordt toegepast, zullen de kosten van SLM-machines en -materialen naar verwachting dalen, waardoor deze technologie toegankelijker wordt.
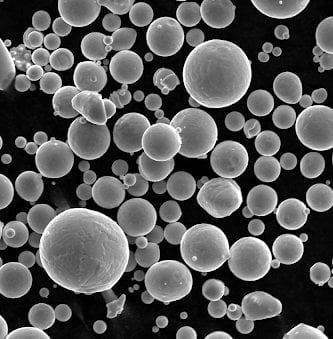
Veelgestelde vragen
V: Wat zijn de typische kosten van SLM?
A: De kosten van SLM kunnen aanzienlijk variëren afhankelijk van verschillende factoren, waaronder:
- Machinekosten: De initiële kosten van de SLM-machine kunnen variëren van honderdduizenden tot miljoenen dollars.
- Materiaalkosten: De kosten van metaalpoeders kunnen variëren afhankelijk van het specifieke materiaal en de eigenschappen ervan.
- Deelcomplexiteit: De complexiteit van het onderdeelontwerp kan een aanzienlijke invloed hebben op de printtijd en het materiaalgebruik, wat de totale kosten beïnvloedt.
- Vereisten voor nabewerking: Extra behandelingen zoals warmtebehandeling of oppervlakteafwerking kunnen de uiteindelijke kosten verhogen.
Een algemene schatting is dat de kosten per kilogram van SLM-geprinte onderdelen kunnen variëren van enkele honderden dollars tot tienduizenden dollars.
V: Wat zijn de sterkste materialen die met SLM geprint kunnen worden?
A: Met SLM kunnen verschillende materialen met hoge sterkte worden geprint, waaronder:
- Inconel 625: Deze superlegering op basis van nikkel-chroom heeft een uitstekende sterkte bij hoge temperaturen en wordt vaak gebruikt in veeleisende toepassingen zoals onderdelen voor gasturbines.
- Titaan Ti6Al4V: Dit werkpaardmateriaal biedt een hoge sterkte-gewichtsverhouding en een goede corrosiebestendigheid, waardoor het populair is voor ruimtevaart en medische toepassingen.
- Gereedschapsstaal: Met SLM kunnen verschillende soorten gereedschapsstaal worden geprint, bekend om hun superieure slijtvastheid en hardheid, ideaal voor snijgereedschappen en matrijzen.
Het is belangrijk om te overleggen met SLM-experts om te bepalen welk materiaal het meest geschikt is voor uw specifieke toepassing op basis van de vereiste sterkte, andere eigenschappen en budgettaire overwegingen.
V: Hoe is de oppervlakteruwheid van SLM onderdelen in vergelijking met traditioneel vervaardigde onderdelen?
A: Door het laagje-voor-laagje karakter van het proces kunnen SLM onderdelen een iets ruwere oppervlakteafwerking hebben dan onderdelen die geproduceerd zijn met technieken als machinaal bewerken of gieten. Nabewerkingstechnieken zoals zandstralen, polijsten of machinaal bewerken kunnen de oppervlakteafwerking echter aanzienlijk verbeteren en de gewenste gladheid bereiken.
V: Is SLM een milieuvriendelijk productieproces?
A: Vergeleken met traditionele subtractieve productietechnieken die veel materiaalafval genereren, biedt SLM een duurzamer alternatief. Het maakt bijna-net-vorm productie mogelijk, waardoor materiaalafval wordt geminimaliseerd. Bovendien kan de mogelijkheid om onderdelen op aanvraag te produceren helpen om de behoefte aan transport te verminderen.
Conclusie
Selective Laser Melting (SLM) is een krachtig bewijs van het menselijk vernuft, verlegt de grenzen van metaalbewerking en ontsluit een nieuw tijdperk van ontwerp- en productiemogelijkheden. Naarmate de technologie zich verder ontwikkelt, kunnen we nog meer transformatieve toepassingen verwachten in diverse industrieën. Of het nu gaat om het revolutioneren van de manier waarop we vliegtuigen bouwen, het maken van levensveranderende medische implantaten of het bevorderen van innovatie in consumentengoederen, SLM is klaar om een onuitwisbare stempel op de toekomst te drukken.
Delen op
MET3DP Technology Co, LTD is een toonaangevende leverancier van additieve productieoplossingen met hoofdkantoor in Qingdao, China. Ons bedrijf is gespecialiseerd in 3D printapparatuur en hoogwaardige metaalpoeders voor industriële toepassingen.
Onderzoek om de beste prijs en een op maat gemaakte oplossing voor uw bedrijf te krijgen!
gerelateerde artikelen
Over Met3DP
Recente update
Ons product
NEEM CONTACT MET ONS OP
Nog vragen? Stuur ons nu een bericht! Na ontvangst van uw bericht behandelen wij uw verzoek met een heel team.
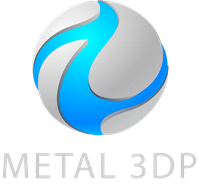
Metaalpoeders voor 3D printen en additieve productie