Jakie proszki metali drukowane w 3D mogą być wykorzystywane w produkcji samolotów?
Spis treści
Świat lotnictwa nieustannie przesuwa granice, poszukując lżejszych, mocniejszych i bardziej paliwooszczędnych samolotów. Wkracza druk 3D, rewolucyjna technologia, która zmienia sposób budowy samolotów. Ale co napędza tę transformację? Odpowiedź tkwi w różnorodności specjalistycznych Proszek metalowy drukowany w 3D, z których każdy ma unikalne właściwości, które sprawiają, że są idealne do konkretnych komponentów samolotów.
Ten kompleksowy przewodnik zagłębia się w fascynujący świat proszków metali do druku 3D stosowanych w produkcji samolotów. Zbadamy różne rodzaje proszków, ich właściwości, zastosowania i czynniki, które sprawiają, że górują nad konkurencją. Zapnij pasy i przygotuj się na
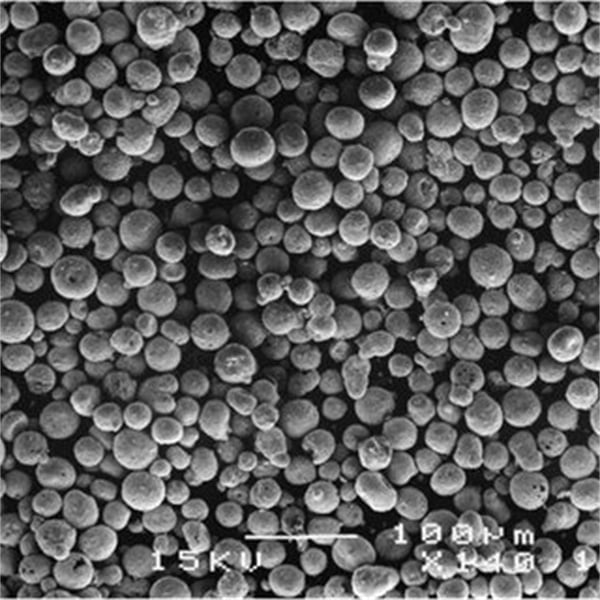
Wgląd w świat Proszki metali drukowane w 3D
Wyobraź sobie budowanie złożonych komponentów samolotów warstwa po warstwie, z niezrównaną precyzją i minimalną ilością odpadów. To magia metalowych proszków do druku 3D. Te drobnoziarniste cząsteczki metalu są podawane do drukarki 3D, gdzie laser lub wiązka elektronów selektywnie je stapia, budując pożądany kształt warstwa po warstwie.
Technologia ta oferuje kilka zalet w porównaniu z tradycyjnymi metodami produkcji, takimi jak obróbka skrawaniem lub odlewanie. Oto kilka kluczowych korzyści:
- Swoboda projektowania: Druk 3D umożliwia tworzenie skomplikowanych geometrii, które byłyby niemożliwe lub niezwykle kosztowne do wykonania przy użyciu konwencjonalnych metod. Pomyśl o lekkich konstrukcjach kratowych dla poprawy efektywności paliwowej lub złożonych kanałach chłodzenia dla bardziej rozgrzanych silników.
- Redukcja wagi: W projektowaniu samolotów liczy się każdy gram. Stosując lekkie proszki metali, takie jak tytan, producenci mogą znacznie zmniejszyć całkowitą masę samolotu, co prowadzi do lepszej efektywności paliwowej i zwiększonej ładowności.
- Zmniejszona ilość odpadów: Tradycyjne metody często generują dużo złomu metalowego. Druk 3D wykorzystuje tylko niezbędny proszek, minimalizując odpady i czyniąc go bardziej zrównoważoną opcją.
- Konsolidacja części: Złożone zespoły można drukować jako pojedyncze komponenty, zmniejszając liczbę części i upraszczając proces produkcji.
Przejdźmy teraz do konkretnych proszków metali, które robią furorę w produkcji samolotów.
Najlepsze proszki metali do produkcji samolotów
Wybór proszku metalu do konkretnego elementu samolotu zależy od kilku czynników, w tym wytrzymałości, wagi, odporności na korozję i temperatury roboczej. Tutaj zbadamy dziesięć najpopularniejszych proszków metali stosowanych w produkcji samolotów, podkreślając ich unikalne właściwości i zastosowania:
1. Proszki ze stopów tytanu (Ti-6Al-4V)
- Skład: Głównie tytan (Ti) z 6% aluminium (Al) i 4% wanadu (V).
- Właściwości: Wysoki stosunek wytrzymałości do masy, doskonała odporność na korozję, dobra biokompatybilność (ważna w zastosowaniach medycznych w samolotach).
- Zastosowania: Elementy podwozia, części kadłuba, mocowania silnika, elementy skrzydeł.
- Specyfikacje: Dostępne w różnych rozmiarach ziaren i mogą być poddawane obróbce końcowej w celu poprawy właściwości mechanicznych.
- Dostawcy: AMPA Material, LPW Powder, EOS GmbH
- Ceny: Stosunkowo drogie w porównaniu z niektórymi innymi proszkami, ale oszczędność wagi i korzyści wydajnościowe często uzasadniają koszty.
- Plusy: Lekkie, mocne, odporne na korozję.
- Wady: Stosunkowo drogie, mogą być trudne do wydrukowania ze względu na wysoką temperaturę topnienia.
2. Proszki ze stopów aluminium (AlSi10Mg)
- Skład: Głównie aluminium (Al) z 10% krzemu (Si) i magnezu (Mg) dla poprawy wytrzymałości i odlewności.
- Właściwości: Doskonała obrabialność, dobry stosunek wytrzymałości do masy, wysoka przewodność cieplna.
- Zastosowania: Wewnętrzne elementy samolotu, wymienniki ciepła, niekrytyczne części konstrukcyjne.
- Specyfikacje: Dostępne w różnych rozmiarach ziaren i mogą być poddawane obróbce cieplnej w celu poprawy właściwości.
- Dostawcy: SLM Solutions, ExOne, Höganäs AB
- Ceny: Bardziej przystępne cenowo w porównaniu z proszkami tytanu.
- Plusy: Lekkie, dobre właściwości termiczne, łatwe do wydrukowania.
- Wady: Niższa wytrzymałość w porównaniu ze stopami tytanu.
3. Proszki ze stali nierdzewnej (316L)
- Skład: Na bazie żelaza (Fe) z chromem (Cr), niklem (Ni), molibdenem (Mo) i innymi pierwiastkami dla odporności na korozję.
- Właściwości: Doskonała odporność na korozję, dobra wytrzymałość i ciągliwość, łatwo dostępna.
- Zastosowania: Przewody, rury, elementy do obsługi płynów, niektóre niekrytyczne części konstrukcyjne.
- Specyfikacje: Dostępne w różnych gatunkach o różnym stopniu odporności na korozję i właściwościach mechanicznych.
- Dostawcy: Carpenter Additive Manufacturing, Oerlikon Metco, Sandvik Additive Manufacturing
- Ceny: Przystępne cenowo w porównaniu z tytanem i niektórymi stopami na bazie niklu.
- Plusy: Łatwo dostępne, dobra odporność na korozję, wszechstronne.
- Wady: Stosunkowo ciężkie w porównaniu ze stopami tytanu, mogą wymagać obróbki końcowej dla optymalnej wytrzymałości.
4. Inconel 625 (IN625)
- Skład: Superstop na bazie niklu (Ni) z chromem (Cr), molibdenem (Mo) i niobem (Nb) dla wytrzymałości w wysokich temperaturach.
- Właściwości: Wyjątkowa wytrzymałość w wysokich temperaturach i odporność na utlenianie, dobra odporność na pełzanie (odporność na odkształcenia pod wpływem naprężeń w wysokich temperaturach).
- Zastosowania: Elementy silników odrzutowych, takie jak komory spalania, łopatki turbin, elementy dopalaczy.
- Specyfikacje: Wymagana rygorystyczna kontrola jakości ze względu na wymagające wymagania dotyczące wydajności.
- Dostawcy: Special Metals Corporation, Haynes International, Aubert & Duval
- Ceny: Drogi ze względu na złożony skład i wysoką wydajność.
- Plusy: Doskonała wydajność w wysokich temperaturach, dobra odporność na pełzanie.
- Wady: Drogi, trudny do wydrukowania ze względu na wysoką temperaturę topnienia.
5. Haynes 282 (UNS N07282)
- Skład: Superstop na bazie niklu (Ni) z chromem (Cr), molibdenem (Mo), wolframem (W) i innymi pierwiastkami dla wyjątkowej wytrzymałości w wysokich temperaturach.
- Właściwości: Najwyższa wytrzymałość w wysokich temperaturach i odporność na utlenianie w porównaniu z Inconel 625, doskonała odporność na pełzanie.
- Zastosowania: Elementy silników gorących, takie jak łopatki i kierownice turbin w zaawansowanych silnikach odrzutowych.
- Specyfikacje: Wymaga skrupulatnego obchodzenia się i rygorystycznej kontroli jakości.
- Dostawcy: Haynes International, Special Metals Corporation, ATI Allegheny Ludlum
- Ceny: Bardzo drogi ze względu na złożony skład i doskonałą wydajność.
- Plusy: Niezrównana wydajność w wysokich temperaturach, doskonała odporność na pełzanie.
- Wady: Niezwykle drogi, bardzo trudny do wydrukowania.
6. Proszki ze stopów aluminium (Scalmalloy)
- Skład: Opatentowany stop aluminium-magnezu-skandu opracowany przez firmę Airbus. Oferuje znaczną poprawę w stosunku do tradycyjnego AlSi10Mg.
- Właściwości: Wyjątkowy stosunek wytrzymałości do masy, przewyższający nawet niektóre stopy tytanu, dobra wytrzymałość i odporność na zmęczenie.
- Zastosowania: Mocno obciążone elementy kadłuba, konstrukcje skrzydeł, potencjalnie elementy kadłuba w przyszłości.
- Specyfikacje: Ograniczona dostępność ze względu na charakter własnościowy, wymagane specyficzne parametry drukowania.
- Dostawcy: Głównie Airbus (za pośrednictwem partnerów, takich jak SLM Solutions)
- Ceny: Potencjalnie droższe niż tradycyjne stopy aluminium ze względu na unikalny skład.
- Plusy: Wyjątkowy stosunek wytrzymałości do masy, dobra wytrzymałość i odporność na zmęczenie.
- Wady: Ograniczona dostępność, wymaga specjalistycznej wiedzy w zakresie drukowania.
7. Stopy miedzi (CuNi2Si)
- Skład: Stop miedzi (Cu) stopiony z niklem (Ni) i krzemem (Si) dla poprawy wytrzymałości i drukowalności.
- Właściwości: Doskonała przewodność cieplna i elektryczna, dobra odporność na korozję, stosunkowo niska temperatura topnienia w porównaniu z innymi opcjami.
- Zastosowania: Wymienniki ciepła, elementy elektryczne, potencjalnie do elementów wymagających wysokiej przewodności cieplnej.
- Specyfikacje: Może wymagać specyficznej obróbki końcowej dla optymalnej przewodności.
- Dostawcy: Höganäs AB, Carpenter Additive Manufacturing, ExOne
- Ceny: Ogólnie przystępne cenowo w porównaniu z wysokowydajnymi stopami.
- Plusy: Doskonała przewodność cieplna i elektryczna, dobra drukowalność.
- Wady: Niższa wytrzymałość w porównaniu z niektórymi innymi opcjami.
8. Proszki ze stopów niklu (Rene 41)
- Skład: Superstop na bazie niklu (Ni) z chromem (Cr), kobaltem (Co), molibdenem (Mo), aluminium (Al) i innymi pierwiastkami dla wydajności w wysokich temperaturach.
- Właściwości: Doskonała wytrzymałość w wysokich temperaturach i odporność na utlenianie, dobra odporność na pełzanie. Często stosowany jako alternatywa dla Inconel 625.
- Zastosowania: Elementy silników odrzutowych, takie jak tarcze i łopatki turbin, części konstrukcyjne wysokotemperaturowe.
- Specyfikacje: Wymaga ścisłej kontroli jakości i może wymagać obróbki końcowej dla optymalnych właściwości.
- Dostawcy: Special Metals Corporation, ATI Allegheny Ludlum, Aubert & Duval
- Ceny: Drogi ze względu na złożony skład i możliwości wysokotemperaturowe.
- Plusy: Doskonała wydajność w wysokich temperaturach, dobra alternatywa dla Inconel 625.
- Wady: Drogi, wymaga starannych procedur drukowania.
9. Proszki ze stopów tytanu (Ti-6Al-4V ELI)
- Skład: Podobne do Ti-6Al-4V, ale z jeszcze niższym poziomem pierwiastków międzywęzłowych, takich jak tlen i azot, dla poprawy spawalności i odporności na zmęczenie.
- Właściwości: Doskonały stosunek wytrzymałości do masy, doskonała spawalność i odporność na zmęczenie w porównaniu ze standardowym Ti-6Al-4V, dobra biokompatybilność.
- Zastosowania: Części lotnicze wymagające wyjątkowej spawalności
- Wady: Nieco niższa wytrzymałość w porównaniu ze standardowym Ti-6Al-4V, może być droższa ze względu na bardziej rygorystyczne wymagania produkcyjne.
10. Stopy chromu kobaltu (CoCr)
- Skład: Stop kobaltu (Co) i chromu (Cr), znany z biokompatybilności i odporności na zużycie.
- Właściwości: Doskonała odporność na zużycie, dobra odporność na korozję, biokompatybilny (stosowany w niektórych implantach medycznych).
- Zastosowania: Elementy podwozia, części odporne na zużycie, potencjalnie do niektórych zastosowań medycznych w lotnictwie (np. protezy dla pilotów).
- Specyfikacje: Może wymagać specyficznych parametrów drukowania dla optymalnej odporności na zużycie.
- Dostawcy: AMPA Material, LPW Powder, EOS GmbH
- Ceny: Ogólnie mieści się w średnim zakresie dla proszków metali.
- Plusy: Doskonała odporność na zużycie, dobra odporność na korozję, biokompatybilny.
- Wady: Może nie być idealny do zastosowań konstrukcyjnych o dużych naprężeniach ze względu na swoje właściwości.
Wybór odpowiedniego proszku metalowego
Jak widać, każdy proszek metalu ma unikalne mocne i słabe strony. Wybór odpowiedniego zależy od kilku czynników specyficznych dla każdego elementu samolotu:
- Wymagania dotyczące wytrzymałości: Mocno obciążone elementy, takie jak podwozie lub łopatki turbin, będą wymagały proszków o wyjątkowej wytrzymałości, takich jak tytan lub super stopy na bazie niklu.
- Względy dotyczące wagi: W przypadku elementów, w których redukcja masy jest najważniejsza, korzystne stają się lekkie opcje, takie jak tytan lub stopy aluminium.
- Temperatury robocze: Elementy narażone na ekstremalne ciepło, takie jak części silników odrzutowych, wymagają proszków o doskonałej wydajności w wysokich temperaturach, takich jak Inconel 625 lub Haynes 282.
- Odporność na korozję: Samoloty działające w trudnych warunkach lub narażone na działanie słonej wody mogą korzystać z proszków o doskonałej odporności na korozję, takich jak stal nierdzewna lub niektóre stopy niklu.
- Możliwość drukowania: Drukowanie niektórych proszków, takich jak stopy tytanu, może być trudne ze względu na ich wysoką temperaturę topnienia. Należy to uwzględnić podczas procesu projektowania i produkcji.
Przyszłość proszków metali do druku 3D w produkcji samolotów
Przyszłość proszków metali do druku 3D w produkcji samolotów jest świetlana. Oto kilka ekscytujących trendów, na które warto zwrócić uwagę:
- Rozwój nowych stopów: Naukowcy nieustannie wprowadzają innowacje, opracowując nowe proszki metali o jeszcze lepszych właściwościach do konkretnych zastosowań. Doprowadzi to do lżejszych, mocniejszych i bardziej odpornych na ciepło komponentów.
- Druk wielomateriałowy: Badane są możliwości drukowania z wielu proszków metali w obrębie tego samego komponentu. Otwiera to drzwi do części o dostosowanych właściwościach w różnych obszarach.
- Niższe koszty proszku: Wraz z dojrzewaniem technologii druku 3D i wzrostem wolumenu produkcji, oczekuje się obniżenia kosztów proszków metali, co sprawi, że technologia ta będzie bardziej dostępna.
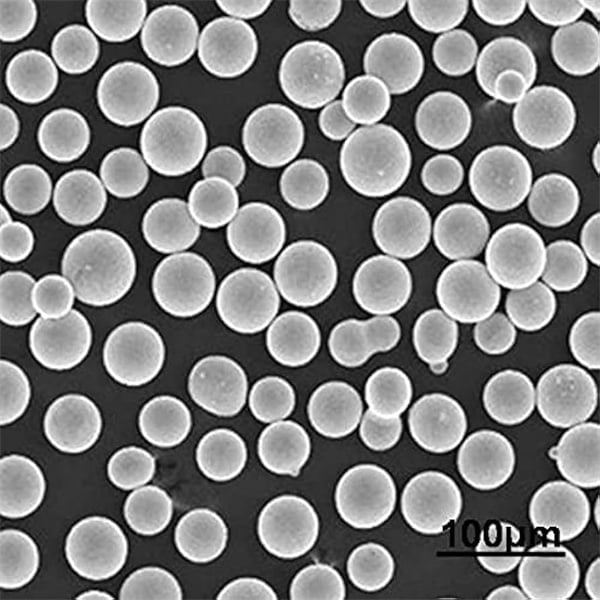
FAQ
P: Jakie są zalety stosowania metalowych proszków do druku 3D w produkcji samolotów?
O: Druk 3D oferuje kilka zalet, w tym swobodę projektowania, redukcję masy, zmniejszenie ilości odpadów i konsolidację części. Przekłada się to na lżejsze, bardziej paliwooszczędne samoloty o potencjalnie niższych kosztach produkcji.
P: Jakie są niektóre z wyzwań związanych z drukowaniem 3D proszków metali?
O: Wyzwania obejmują wysoki koszt niektórych proszków, drukowalność
P: Jakie są perspektywy dla drukowania 3D proszków metali w produkcji samolotów?
Przyszłość rysuje się obiecująco. Dzięki ciągłym badaniom i rozwojowi możemy spodziewać się jeszcze lepszych proszków metali, możliwości druku z wielu materiałów i obniżonych kosztów, co jeszcze bardziej zrewolucjonizuje sposób projektowania i produkcji samolotów.
Udostępnij
MET3DP Technology Co., LTD jest wiodącym dostawcą rozwiązań w zakresie produkcji addytywnej z siedzibą w Qingdao w Chinach. Nasza firma specjalizuje się w sprzęcie do druku 3D i wysokowydajnych proszkach metali do zastosowań przemysłowych.
Zapytaj o najlepszą cenę i spersonalizowane rozwiązanie dla Twojej firmy!
Powiązane artykuły
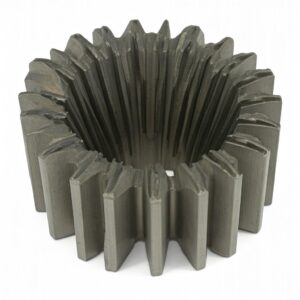
Wysokowydajne segmenty łopatek dysz: Rewolucja w wydajności turbin dzięki drukowi 3D w metalu
Czytaj więcej "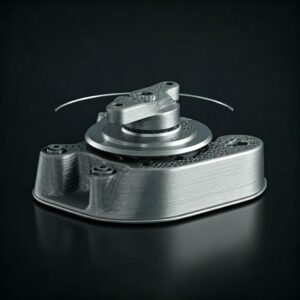
Drukowane w 3D mocowania dla samochodowych czujników radarowych: Precyzja i wydajność
Czytaj więcej "Informacje o Met3DP
Ostatnia aktualizacja
Nasz produkt
KONTAKT
Masz pytania? Wyślij nam wiadomość teraz! Po otrzymaniu wiadomości obsłużymy Twoją prośbę całym zespołem.
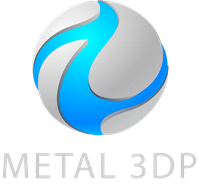
Proszki metali do druku 3D i produkcji addytywnej