Lightweight Fairings 3D Printed for Aerospace
Spis treści
Introduction: The Critical Role of Aerospace Fairings and the Additive Manufacturing Revolution
Aerospace engineering relentlessly pursues advancements in performance, efficiency, and safety. Every component, regardless of perceived simplicity, plays a vital role in the intricate symphony of flight. Among these crucial elements are aerospace fairings – structures primarily designed to reduce aerodynamic drag, protect sensitive equipment, and ensure smooth airflow over discontinuities on an aircraft’s exterior. Traditionally manufactured using methods like sheet metal forming, composite layup, or machining from billet, fairings are now prime candidates for the transformative potential of metal additive manufacturing (AM), commonly known as metal Drukowanie 3D. This shift is driven by AM’s unique ability to produce lightweight, complex, and highly optimized parts that were previously difficult or impossible to create.
Fairings are ubiquitous across aircraft, spacecraft, and missiles. They can range from small, simple covers over antennas or joints to large, complex structures enclosing engines, landing gear, or fuselage sections. Their primary function is aerodynamic: by smoothing the transition between different surfaces or covering protruding elements, they minimize drag, which directly translates to fuel savings, increased range, and improved overall performance. Beyond aerodynamics, fairings often serve a protective role, shielding underlying components from environmental factors like moisture, debris, and temperature fluctuations, as well as aerodynamic loads.
The traditional manufacturing approaches for fairings, while mature, present inherent limitations, particularly when addressing the aerospace industry’s escalating demands for weight reduction and design complexity. Sheet metal forming can be limited in the shapes it can produce efficiently, composite layups can be labor-intensive and expensive, especially for complex curves, and subtractive machining generates significant material waste (a critical concern with expensive aerospace alloys).
Enter metal additive manufacturing. Technologies like Laser Powder Bed Fusion (L-PBF) and Electron Beam Melting (EBM) build parts layer by layer directly from digital models using high-performance metal powders. This approach fundamentally changes the design and production paradigm. Engineers are no longer constrained by the limitations of traditional tooling or machining access. Instead, they can leverage sophisticated design tools, such as topology optimization and generative design, to create fairings that are organically shaped, internally complex, and possess an optimal strength-to-weight ratio. This capability is particularly crucial in aerospace, where every gram saved contributes significantly to mission success and operational cost reduction.
Furthermore, metal AM enables part consolidation. Multiple components that previously needed to be manufactured separately and then assembled (introducing potential failure points and added weight from fasteners) can often be integrated into a single, monolithic 3D printed part. This notifes production, reduces assembly time and labor, and can enhance structural integrity.
The materials used in metal AM are also evolving rapidly. High-performance aluminum alloys like AlSi10Mg and specialized aerospace alloys like Scalmalloy® offer exceptional combinations of low density, high strength, and good processability via AM, making them ideal candidates for lightweight structural components like fairings. Companies at the forefront of additive manufacturing, such as Met3dp, are not only advancing printing technologies but also developing and supplying the high-quality, spherical metal powders essential for producing reliable, high-performance aerospace parts. Their expertise spans advanced powder manufacturing techniques, like gas atomization and Plasma Rotating Electrode Process (PREP), ensuring powders meet the stringent requirements for aerospace applications regarding sphericity, flowability, and purity.
This introductory section sets the stage: aerospace fairings are critical components facing increasing demands for performance and weight reduction. Traditional manufacturing methods have limitations, while metal additive manufacturing offers a revolutionary pathway to producing lighter, more complex, and consolidated fairings using advanced materials, ultimately driving innovation across the aerospace sector. The subsequent sections will delve deeper into the specific applications, the compelling advantages of using AM, the recommended materials, and the practical considerations for designing and producing these next-generation components.
What are Aerospace Fairings Used For? Key Functions and Applications
Aerospace fairings, despite often appearing as simple external coverings, perform multiple critical functions essential for flight safety, performance, and efficiency. Understanding these functions highlights why optimizing their design and manufacturing process through technologies like metal 3D printing is so valuable for aerospace manufacturers, suppliers, and procurement managers seeking enhanced component solutions.
Core Functions of Aerospace Fairings:
- Aerodynamic Drag Reduction: This is arguably the primary and most recognized function. Aircraft and spacecraft exteriors inevitably feature junctions, protrusions (like antennas, sensors, or structural joints), and changes in shape that disrupt smooth airflow. These disruptions create turbulence and pressure drag, increasing the overall resistance the vehicle experiences as it moves through the air. Fairings provide smooth, streamlined contours over these discontinuities, minimizing turbulence and significantly reducing parasitic drag.
- Uderzenie: Lower drag leads directly to reduced fuel consumption (for aircraft) or propellant requirements (for launch vehicles), increased range and endurance, higher achievable speeds, and improved aerodynamic stability and control. For aerospace component distributors, offering fairings optimized for drag reduction represents a significant value proposition.
- Protection of Sensitive Components: Many fairings enclose and shield critical systems and structures from the harsh operating environment. This includes:
- Environmental Protection: Shielding components from rain, ice, dust, debris impacts (like bird strikes or runway gravel), UV radiation, and temperature extremes encountered at high altitudes or during atmospheric re-entry.
- Aerodynamic Load Protection: Protecting underlying structures or sensitive equipment (e.g., radar arrays, communication antennas, actuators) from direct exposure to high aerodynamic pressures and forces during flight.
- Zarządzanie temperaturą: Some fairings, particularly in high-speed applications or near engines, may contribute to thermal insulation or help manage heat dissipation.
- Enhancing Structural Integrity and Smoothness: Fairings contribute to the overall structural smoothness and can sometimes play a secondary structural role, particularly at junctions between major components like wings and fuselage, or empennage sections. They ensure load paths are transferred smoothly and prevent stress concentrations at sharp corners or discontinuities.
- Noise Reduction: By smoothing airflow, fairings can also contribute to reducing aerodynamic noise generated by turbulent flow over protrusions or cavities, which is important for passenger comfort in commercial aircraft and for stealth characteristics in military applications.
- Estetyka: While function dictates form in aerospace, fairings contribute significantly to the sleek, streamlined appearance of modern aircraft.
Common Applications Across Aerospace Platforms:
The specific design and location of fairings vary widely depending on the aircraft or spacecraft type and its mission profile. Here are some common examples:
- Wing-to-Fuselage Fairings (Karman Fairings): Large, complex fairings that smooth the airflow at the junction where the wing meets the fuselage. This is a critical area for drag reduction. Their complex, doubly curved shapes make them ideal candidates for the geometric freedom offered by AM.
- Flap Track Fairings: Canoe-shaped fairings located on the underside of wings, housing the mechanisms (tracks and actuators) that extend and retract flaps. They streamline these mechanisms when flaps are retracted.
- Landing Gear Fairings: Covers for wheels, struts, and retraction mechanisms to reduce drag when the landing gear is extended or to seal the wheel wells when retracted.
- Tail Cone Fairings (Aft Body Fairings): Streamline the rearmost part of the fuselage, reducing base drag. May also house auxiliary power units (APUs) or other equipment.
- Engine Pylon Fairings: Smooth the transition between the engine nacelle and the wing or fuselage mounting pylon.
- Antenna and Sensor Fairings (Radomes): Specialized fairings designed to protect communication, navigation, or radar antennas while being transparent to specific electromagnetic frequencies (though metal AM would be used for the supporting structure, not necessarily the RF-transparent element itself, unless integrated).
- Joint and Gap Fairings: Smaller fairings covering structural joints, access panels, or gaps between control surfaces (like ailerons, elevators, rudders) and the main airfoil structure.
- Payload Fairings (Launch Vehicles): Large nose cones that protect the spacecraft payload (e.g., satellites) from aerodynamic forces and heating during atmospheric ascent. While often made of composites, metallic structural elements within or supporting these fairings could benefit from AM.
- Missile Nose Cones and Fin Fairings: Similar aerodynamic and protective functions tailored to the high-speed, high-stress environment of missile flight.
Given this wide range of applications and the constant drive for improved performance and efficiency, the aerospace industry actively seeks advanced manufacturing solutions. Metal 3D printing provides aerospace suppliers and manufacturers the tools to reimagine fairing design, moving beyond traditional constraints to create highly optimized, lightweight, and functionally integrated components tailored to the specific demands of each application. The ability to produce complex geometries efficiently makes AM particularly suitable for parts like Karman fairings or intricately shaped mechanism covers.
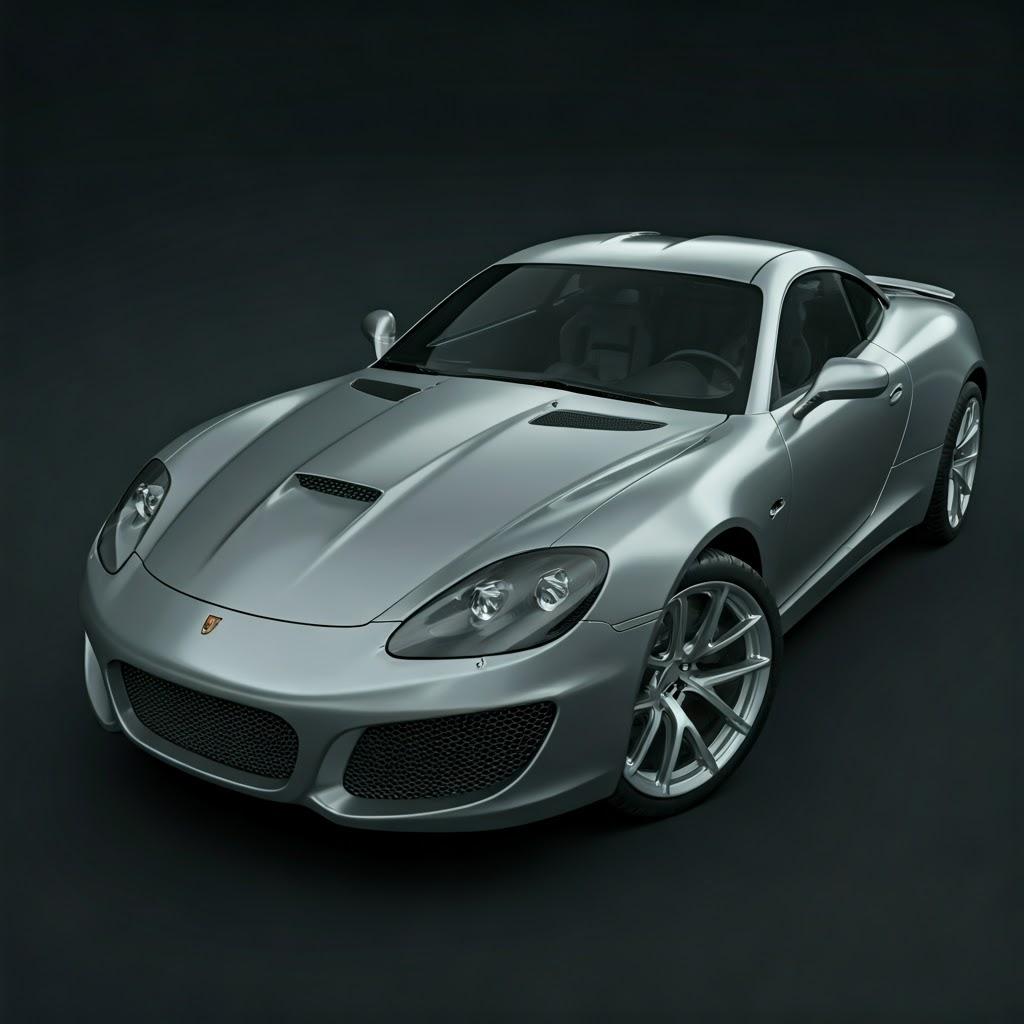
Why Use Metal 3D Printing for Aerospace Fairings? Unlocking Performance and Efficiency
The decision to adopt metal additive manufacturing for producing aerospace fairings stems from a confluence of compelling technical and economic advantages over traditional methods like sheet metal fabrication, composite layup, and CNC machining. For engineers focused on performance optimization and procurement managers evaluating total lifecycle cost and supply chain resilience, metal AM offers significant benefits specifically tailored to the demands of aerospace components.
Key Advantages of Metal AM for Fairings:
- Significant Weight Reduction (Lightweighting): This is often the most critical driver in aerospace. Metal AM enables:
- Topology Optimization: Algorithms remove material from low-stress areas, creating organically shaped, highly efficient structures that maintain strength only where needed. Fairings often have complex load paths, making them ideal for this approach.
- Struktury kratowe: Internal lattice or gyroid structures can replace solid volumes, drastically reducing weight while maintaining required stiffness and structural integrity. This is difficult or impossible with traditional methods.
- Thin Walls & Complex Geometries: AM can produce components with thinner walls and more intricate internal features than casting or machining allows, further minimizing mass.
- Material Choice: Access to high specific strength alloys like Scalmalloy® and AlSi10Mg, which are well-suited for AM processes.
- Uderzenie: Reduced part weight translates directly to lower fuel consumption, increased payload capacity, improved maneuverability, and reduced overall operational costs – key metrics for aircraft manufacturers and operators.
- Swoboda projektowania i złożoność: AM liberates designers from the constraints of traditional manufacturing:
- Complex Curvatures: Fairings often require complex, doubly curved surfaces for optimal aerodynamics (e.g., wing-to-fuselage fillets). AM handles these geometries with ease, requiring no specialized tooling like molds or dies.
- Internal Features: Cooling channels, internal stiffening ribs, integrated mounting points, or embedded sensor housings can be designed directly into the fairing structure without complex assembly steps.
- Konsolidacja części: Multiple simple parts that would traditionally be manufactured separately and joined (e.g., brackets, skin panels, stiffeners) can often be redesigned and printed as a single, monolithic component.
- Uderzenie: Simplifies assembly, reduces part count, eliminates fasteners (reducing weight and potential failure points), improves structural integrity, and enables functionally optimized designs previously unattainable.
- Szybkie prototypowanie i iteracja: The digital nature of AM accelerates the design-test-iterate cycle:
- Prędkość: Moving from a CAD model to a physical metal prototype can take days or weeks, compared to potentially months for tooling development in traditional methods.
- Elastyczność: Design modifications can be implemented quickly in the CAD file and reprinted without costly tooling changes. This allows for rapid aerodynamic testing (e.g., wind tunnel models) and functional validation.
- Uderzenie: Reduces development time and costs, fosters innovation by allowing more design variants to be explored, and enables faster deployment of optimized components. Aerospace engineering teams can iterate designs much more efficiently.
- Zmniejszona ilość odpadów materiałowych: AM is an additive process, building parts layer by layer, using primarily only the material needed for the part and its supports.
- Contrast with Subtractive: CNC machining, especially for complex aerospace parts from billet, can generate substantial material waste (buy-to-fly ratio can be very high). This is particularly costly with expensive aerospace alloys.
- Powder Reusability: While not 100% efficient, unused powder in the build chamber can often be sieved and reused in subsequent builds, improving material utilization. Advanced powder management systems, like those utilized by specialized providers, maximize this benefit.
- Uderzenie: Lowers raw material costs, reduces environmental impact, and improves resource efficiency – increasingly important considerations for sustainable manufacturing initiatives sought by aerospace OEMs and suppliers.
- Supply Chain Optimization and On-Demand Production:
- Digital Inventory: Designs exist as digital files, allowing parts to be printed on demand, closer to the point of need. This reduces the need for large physical inventories of spare parts.
- Skrócenie czasu realizacji: For certain complex or low-volume parts, AM can offer shorter lead times compared to sourcing traditional tooling or complex machined components, especially if tooling needs to be created.
- Tool-less Manufacturing: Eliminates the cost, lead time, and storage requirements associated with traditional molds, dies, and fixtures.
- Uderzenie: Improves supply chain agility, reduces warehousing costs, minimizes downtime for Maintenance, Repair, and Overhaul (MRO) operations by enabling faster access to replacement fairings. This is a key benefit for aerospace MRO providers and airline procurement teams.
- Enhanced Performance through Tailored Materials: AM processes work well with advanced alloys specifically designed for demanding aerospace applications:
- Wysoki stosunek wytrzymałości do wagi: Alloys like Scalmalloy® offer performance exceeding standard aerospace aluminum alloys.
- Good Processability: Materials like AlSi10Mg are well-characterized and reliably processed using L-PBF.
- Potential for Custom Alloys: The layer-wise nature opens possibilities (though still developmental) for functionally graded materials or unique alloy compositions tailored to specific fairing requirements. Companies like Met3dp, with expertise in both printing systems and specialized powder development (including TiNi, TiTa, TiAl, CoCrMo, superalloys), are positioned to leverage these material advancements.
- Uderzenie: Enables fairings that meet or exceed the performance requirements for strength, stiffness, fatigue life, and temperature resistance, often while achieving significant weight savings.
While traditional methods remain viable for simpler or very high-volume fairings, metal 3D printing presents a compelling suite of advantages for complex, performance-critical, or weight-sensitive fairings. It empowers engineers to design better components and offers manufacturers a more agile, efficient, and potentially cost-effective production route, fundamentally changing the approach to aerospace component manufacturing and sourcing.
Recommended Materials for 3D Printed Fairings: AlSi10Mg vs. Scalmalloy®
Choosing the right material is paramount for aerospace components, balancing performance requirements like strength, stiffness, weight, temperature resistance, and corrosion resistance against manufacturability and cost. For metal 3D printed fairings, two aluminum-based alloys stand out due to their excellent properties and processability via Laser Powder Bed Fusion (L-PBF): AlSi10Mg and Scalmalloy®. Understanding their respective characteristics is crucial for engineers designing fairings and for procurement managers sourcing these components from qualified additive manufacturing suppliers.
AlSi10Mg: The Workhorse Aluminum Alloy
AlSi10Mg is one of the most common and well-understood aluminum alloys used in metal AM. It’s essentially an aluminum-silicon-magnesium casting alloy adapted for powder bed fusion processes.
- Skład: Primarily aluminum (Al), with significant additions of Silicon (Si, ~9-11%) and Magnesium (Mg, ~0.2-0.45%), plus minor amounts of other elements like iron (Fe).
- Key Properties & Advantages for Fairings:
- Dobry stosunek wytrzymałości do wagi: While not as high-strength as some aerospace alloys, it offers a respectable balance of strength and low density (~2.67 g/cm³), making it suitable for lightweight structures like fairings where extreme loads aren’t the primary driver.
- Excellent Processability: It is known for its good behavior during L-PBF, exhibiting good melt pool stability and relatively low susceptibility to cracking compared to other high-strength aluminum alloys. This leads to more reliable and repeatable manufacturing.
- Good Thermal Properties: Offers good thermal conductivity, which can be beneficial if the fairing plays a role in heat dissipation.
- Odporność na korozję: Exhibits decent corrosion resistance, suitable for many atmospheric conditions, though surface treatments may still be required depending on the specific application environment.
- Spawalność: Can be welded, which might be relevant if post-print modifications or repairs are needed (though joining AM parts requires careful consideration).
- Cost-Effectiveness & Availability: Generally more widely available and cost-effective than specialized aerospace alloys like Scalmalloy®. Many AM service providers have extensive experience processing AlSi10Mg.
- Rozważania:
- Lower Strength & Fatigue Life: Compared to Scalmalloy® or traditional wrought aerospace aluminum alloys (like 7075 or 2024), AlSi10Mg has lower tensile strength, yield strength, and fatigue performance, especially at elevated temperatures.
- Plastyczność: Can exhibit lower ductility compared to wrought alloys, requiring careful design to avoid stress concentrations.
- Obróbka cieplna: Typically requires heat treatment (e.g., T6 stress relief and aging) after printing to achieve optimal mechanical properties and reduce residual stresses inherent in the PBF process.
- Typical Fairing Applications: Suitable for moderately loaded fairings, access panels, aerodynamic smoothing elements, and components where lightweighting and complex geometry are key drivers, but ultimate strength is not the absolute limiting factor. Ideal for rapid prototyping and cost-sensitive applications.
Scalmalloy®: The High-Performance Aluminum Alloy
Developed specifically for additive manufacturing by APWORKS (an Airbus subsidiary), Scalmalloy® is a patented high-performance aluminum-magnesium-scandium (Al-Mg-Sc) alloy. It pushes the boundaries of what’s achievable with 3D printed aluminum.
- Skład: Aluminum (Al) alloyed with Magnesium (Mg), Scandium (Sc), and Zirconium (Zr). The scandium addition is key to its high performance.
- Key Properties & Advantages for Fairings:
- Exceptional Specific Strength: Offers a significantly higher strength-to-weight ratio than AlSi10Mg and even surpasses the strength of many traditional high-strength wrought aluminum alloys (like 7000 series) in the as-built or heat-treated conditions. Density is similar to other aluminum alloys (~2.67 g/cm³).
- Excellent Ductility & Fatigue Life: Unlike many high-strength AM materials, Scalmalloy® retains good ductility and exhibits excellent fatigue properties, making it suitable for components subjected to cyclic loading – a common scenario for aerospace structures.
- Good Dynamic Load Resistance: Performs well under dynamic and impact loads.
- Odporność na korozję: Offers good corrosion resistance, comparable or superior to AlSi10Mg in many environments.
- Spawalność: Possesses good weldability characteristics.
- Microstructure Stability: The alloy composition provides a stable microstructure, even at moderately elevated temperatures, compared to standard aluminum alloys.
- Rozważania:
- Wyższy koszt: The inclusion of scandium makes Scalmalloy® powder significantly more expensive than AlSi10Mg.
- Processing Expertise: Requires optimized L-PBF process parameters and careful thermal management during printing to achieve its full potential. Working with experienced service providers is crucial.
- Dostępność: While increasingly adopted, it may be less widely available than AlSi10Mg, and fewer providers might have extensive, validated experience with it.
- Obróbka cieplna: Like AlSi10Mg, typically requires post-print heat treatment to optimize properties and relieve stress.
- Typical Fairing Applications: Ideal for highly loaded structural fairings, components requiring maximum weight savings without compromising strength or fatigue life, performance-critical aerodynamic surfaces, and applications replacing traditionally machined high-strength aluminum or even titanium components. Suitable for demanding environments where high fatigue resistance is essential.
Material Selection Summary Table:
Cecha | AlSi10Mg | Scalmalloy® | Why it Matters for Fairings |
---|---|---|---|
Primary Advantage | Cost-effective, Good Processability | High Strength-to-Weight, Excellent Fatigue Life | Balancing budget vs. ultimate performance needs. |
Gęstość | ~2.67 g/cm³ | ~2.67 g/cm³ | Both enable significant lightweighting compared to steel/titanium. |
Wytrzymałość na rozciąganie | Umiarkowany | Very High (often >500 MPa post-treatment) | Ability to handle aerodynamic and structural loads. |
Wytrzymałość na rozciąganie | Umiarkowany | Wysoki | Resistance to permanent deformation under load. |
Plastyczność | Umiarkowany | Good/Excellent | Resistance to fracture, important for damage tolerance. |
Wytrzymałość zmęczeniowa | Umiarkowany | Doskonały | Critical for long service life under cyclic loads (vibration). |
Processability (L-PBF) | Excellent, well-established | Good, but requires optimized parameters | Affects manufacturing reliability, repeatability, and cost. |
Odporność na korozję | Dobry | Good/Excellent | Durability in operational environments. |
Koszt | Niższy | Wyższy | Significant factor in procurement decisions. |
Dostępność | Szeroko dostępny | More Specialized | Impacts supplier choice and potentially lead time. |
Typowe zastosowanie | General purpose lightweighting, prototypes | Performance-critical, high-load, fatigue-sensitive parts | Matching material capability to application demands. |
Export to Sheets
The Role of Powder Quality:
Regardless of the alloy chosen, the quality of the metal powder is fundamental to achieving the desired properties and ensuring part consistency – a non-negotiable aspect of aerospace manufacturing. Factors like:
- Rozkład wielkości cząstek (PSD): Affects powder bed density and melt pool behavior.
- Sferyczność: Ensures good powder flowability for uniform layer spreading.
- Purity & Low Oxygen Content: Minimizes defects like porosity and ensures optimal mechanical properties.
- Batch Consistency: Guarantees repeatable results from build to build.
This is where providers specializing in both AM processes and material science, like Met3dp, add significant value. Their use of advanced powder production techniques like gas atomization and PREP, coupled with rigorous quality control, ensures that the AlSi10Mg, Scalmalloy®, or other specialized powders (like those listed on their product page) used for printing critical components like aerospace fairings meet the demanding specifications required for flight-worthy parts. Choosing a supplier with demonstrated expertise in powder handling and characterization is as important as selecting the right alloy itself.
In conclusion, both AlSi10Mg and Scalmalloy® offer compelling pathways to producing lightweight, complex aerospace fairings via metal 3D printing. AlSi10Mg provides a reliable, cost-effective solution for many applications, while Scalmalloy® delivers superior performance for the most demanding structural and fatigue-critical requirements. The optimal choice depends on a careful analysis of the specific functional requirements, load conditions, budget constraints, and the desired performance targets for the fairing.

Design Considerations for Additively Manufactured Aerospace Fairings
Transitioning from traditional manufacturing methods to metal additive manufacturing (AM) for aerospace fairings is not merely a change in production technique; it requires a fundamental shift in design philosophy. To fully exploit the benefits of AM, engineers must embrace Design for Additive Manufacturing (DfAM) principles. DfAM moves beyond simply replicating existing designs and instead optimizes parts specifically for the layer-by-layer build process, unlocking unprecedented levels of performance, weight reduction, and functional integration. For fairings, which often balance complex aerodynamic shapes with structural requirements and weight sensitivity, DfAM is crucial.
Key DfAM Principles for 3D Printed Fairings:
- Topology Optimization: This is perhaps the most transformative DfAM tool for lightweighting.
- Proces: Software algorithms analyze the load paths and stress distribution within a defined design space (the maximum allowable volume for the fairing). Material is iteratively removed from areas experiencing low stress, leaving behind an optimized, often organic-looking structure that meets performance requirements with minimal mass.
- Application to Fairings: Ideal for reducing the mass of internal ribs, mounting structures, or the overall fairing body while maintaining stiffness and strength to withstand aerodynamic loads and vibration. It can lead to fairings that look radically different from their traditionally manufactured counterparts but perform significantly better in terms of weight.
- Rozważania: Requires accurate definition of load cases, boundary conditions, and manufacturing constraints (e.g., minimum feature size). The resulting complex geometry is often only manufacturable via AM.
- Lattice Structures and Infill Strategies: Replacing solid material sections with internal lattice structures is another powerful lightweighting technique enabled by AM.
- Typy: Various lattice types exist, including strut-based (e.g., cubic, octet-truss) and surface-based or Triply Periodic Minimal Surfaces (TPMS) like gyroids. Each offers different mechanical properties (stiffness, energy absorption, buckling resistance).
- Application to Fairings: Can be used to infill thicker sections of a fairing, providing structural support with significantly less material than a solid fill. Can also be designed for specific vibration damping characteristics or to facilitate airflow/heat transfer if the fairing has secondary thermal functions.
- Rozważania: Requires careful analysis to ensure structural integrity. Must incorporate design features (escape holes) to allow for complete removal of unfused powder after printing. Software tools are needed to generate and validate these complex internal structures.
- Konsolidacja części: AM allows multiple components of an assembly to be redesigned and printed as a single, monolithic part.
- Proces: Analyze existing fairing assemblies (e.g., skin panels, stiffeners, brackets, fasteners). Identify opportunities to integrate these elements into one continuous AM part.
- Application to Fairings: A fairing that previously consisted of a formed skin panel riveted to internal support ribs and mounting brackets could potentially be redesigned as a single print, incorporating optimized internal structures and integrated mounting features.
- Korzyści: Reduces part count, eliminates fasteners (weight savings, removal of potential failure points), simplifies assembly, shortens supply chains, and can improve overall structural efficiency.
- Designing for Self-Support and Minimizing Support Structures: Support structures are often necessary in Powder Bed Fusion (PBF) processes like L-PBF to anchor the part to the build plate, support overhanging features, and manage thermal stresses. However, supports add print time, material consumption, and require post-processing for removal, which can mar surfaces.
- Self-Supporting Angles: Design features with overhang angles typically greater than 45 degrees (relative to the build plate) often require supports. DfAM involves orienting the part optimally on the build plate and modifying geometries (e.g., using chamfers instead of sharp overhangs, designing smooth transitions) to maximize self-supporting regions.
- Sacrificial Features: Designing sacrificial ribs or easily removable internal supports that can be broken away or machined off more easily than dense PBF supports.
- Rozważania: Requires understanding the specific capabilities and limitations of the chosen AM machine and material. Optimal orientation is a balance between minimizing supports, managing thermal stress, achieving desired surface finish, and ensuring optimal mechanical properties (due to anisotropy).
- Minimum Feature Size and Wall Thickness: AM processes have limitations on the smallest features and thinnest walls they can reliably produce.
- Typical Limits (L-PBF): Minimum wall thickness is often in the range of 0.4mm to 1.0mm, depending on the material, machine, and wall height/geometry. Small holes or channels also have minimum diameter limits.
- Application to Fairings: Ensure that thin aerodynamic edges, internal ribs, or lattice struts meet the minimum printable thickness requirements. Overly thin sections may warp or fail to resolve properly during the build.
- Collaboration: Consulting with the AM service provider, like Met3dp, during the design phase is crucial to understand the specific limitations of their equipment and processes for AlSi10Mg or Scalmalloy®.
- Powder Removal Considerations: Unfused powder must be completely removed from the finished part, especially from internal channels or cavities common in optimized or lattice-filled designs.
- Design Strategy: Incorporate strategically placed escape holes or drain channels of sufficient size to allow powder to be evacuated via gravity, vibration, or air/fluid flushing during post-processing.
- Uderzenie: Incomplete powder removal adds weight, can pose safety risks (especially with reactive materials, though less so for Al), and may compromise performance if internal channels are intended for fluid/air flow.
- Incorporating Interfaces and Tolerances: While AM produces near-net-shape parts, surfaces requiring high precision, specific flatness, or tight tolerances (e.g., mating interfaces, mounting points) often need secondary machining.
- Design Strategy: Design these critical features with sufficient extra material (“machining stock” or “machining allowance”) so they can be accurately finished via CNC machining after printing and heat treatment. Clearly define these critical features and tolerances using Geometric Dimensioning and Tolerancing (GD&T) on engineering drawings.
- Rozważania: Adds post-processing steps and cost but ensures functional requirements are met. Design must allow tool access for machining operations.
- Filleting and Stress Reduction: Sharp internal corners can act as stress concentrators, particularly in materials that may have lower ductility than their wrought counterparts.
- Design Strategy: Apply generous fillets or radii to internal corners and transitions to distribute stress more evenly, improving fatigue life and overall structural integrity. This is good practice in general mechanical design but particularly important for AM parts.
Successfully implementing DfAM for aerospace fairings requires a collaborative approach between design engineers and additive manufacturing experts. Leveraging the experience of knowledgeable AM service providers who understand the nuances of materials like AlSi10Mg and Scalmalloy®, machine capabilities, and post-processing requirements is key to translating innovative designs into high-quality, flight-worthy hardware.
Achieving Precision: Tolerance, Surface Finish, and Dimensional Accuracy in 3D Printed Fairings
While metal additive manufacturing offers incredible geometric freedom, understanding and managing the achievable levels of precision – encompassing dimensional accuracy, tolerances, and surface finish – is critical for producing functional aerospace fairings that meet stringent industry requirements. Engineers and procurement managers must have realistic expectations and understand the factors influencing the final part quality.
Dimensional Accuracy and Tolerances:
Metal 3D printing, particularly Laser Powder Bed Fusion (L-PBF), produces near-net-shape parts, but it’s not inherently as precise as high-precision CNC machining across all dimensions.
- Typical Achievable Tolerances: For well-calibrated L-PBF systems and optimized processes using materials like AlSi10Mg or Scalmalloy®, typical achievable dimensional tolerances are often in the range of:
- ±0.1 mm to ±0.2 mm for smaller features (e.g., up to 50-100 mm).
- ±0.1% to ±0.2% of the nominal dimension for larger features.
- Factors Influencing Accuracy:
- Machine Calibration: Regular calibration of the laser scanning system, optics, and build platform leveling is essential.
- Thermal Effects: Residual stresses built up during the heating and cooling cycles can cause warping and distortion, affecting final dimensions. Part orientation, support strategy, and post-build stress relief heat treatment are crucial for mitigating this.
- Part Size and Geometry: Larger parts or those with significant variations in cross-section are generally more prone to distortion.
- Jakość proszku: Consistent particle size distribution and morphology contribute to predictable melt pool behavior and dimensional stability. High-quality powders, like those produced using advanced methods by suppliers such as Met3dp, contribute to process stability.
- Process Parameters: Laser power, scan speed, layer thickness, and hatching strategies significantly impact melt pool dynamics and resulting accuracy.
- Meeting Tight Tolerances: For features requiring tolerances tighter than the standard AM process capability (e.g., critical mounting interfaces, aerodynamic sealing surfaces), secondary machining is typically required. DfAM principles dictate designing these features with machining allowance.
- GD&T: Utilizing Geometric Dimensioning and Tolerancing (GD&T) on engineering drawings is essential to clearly communicate critical dimensions, datums, and required tolerances for both the AM build and any subsequent machining operations.
Surface Finish (Roughness):
The surface finish of L-PBF parts is inherently rougher than machined or polished surfaces due to the layer-wise nature of the process and the partially melted powder particles adhering to the surface.
- Typical As-Built Surface Roughness (Ra):
- Values commonly range from 8 µm to 25 µm (micrometers) Ra (average roughness), depending on the material, parameters, and surface orientation.
- Factors Influencing Surface Finish:
- Orientation: Up-skin surfaces (facing upwards during the build) tend to be smoother than down-skin surfaces (overhanging areas requiring support). Vertical walls typically have intermediate roughness.
- Struktury wsparcia: Areas where support structures were attached will exhibit witness marks and increased roughness after removal, often requiring further finishing.
- Process Parameters: Finer layer thicknesses and optimized contour scanning parameters can improve finish but may increase build time.
- Rozmiar cząstek: The size of the powder particles influences the achievable minimum roughness.
- Poprawa wykończenia powierzchni: If the as-built finish is insufficient for aerodynamic requirements (smoothness) or sealing surfaces, post-processing is necessary. Common methods include:
- Bead Blasting / Sand Blasting: Provides a uniform matte finish, removes loose particles, but only moderately improves Ra.
- Tumbling / Vibratory Finishing: Can smooth surfaces and deburr edges, especially for smaller parts.
- CNC Machining: Provides the best control over surface finish for specific features.
- Polishing: Manual or automated polishing can achieve very smooth, mirror-like finishes but is labor-intensive and costly.
- Chemical Etching/Polishing: Can smooth surfaces but requires careful process control.
Ensuring Consistency and Quality:
Achieving consistent dimensional accuracy and surface finish requires robust process control and quality management systems from the AM service provider.
- Process Monitoring: In-situ monitoring techniques (e.g., melt pool monitoring, thermal imaging) can help detect anomalies during the build.
- Material Control: Strict control over powder quality, storage, handling, and recycling procedures is vital.
- Post-Processing Validation: Ensuring heat treatments are performed correctly and machining operations meet GD&T requirements.
- Inspection: Utilizing advanced metrology tools like 3D scanning (laser or structured light) and Coordinate Measuring Machines (CMM) to verify dimensional accuracy against the CAD model and drawing specifications. Surface roughness measurements are also typically required.
Understanding the capabilities and limitations of metal AM regarding precision is crucial. While it excels at creating complex geometries, achieving the tightest tolerances and smoothest finishes often necessitates integrating post-processing steps into the manufacturing workflow. Partnering with an experienced metal 3D printing service provider who understands these nuances and possesses the necessary quality systems and post-processing capabilities is key to obtaining fairings that meet demanding aerospace specifications.
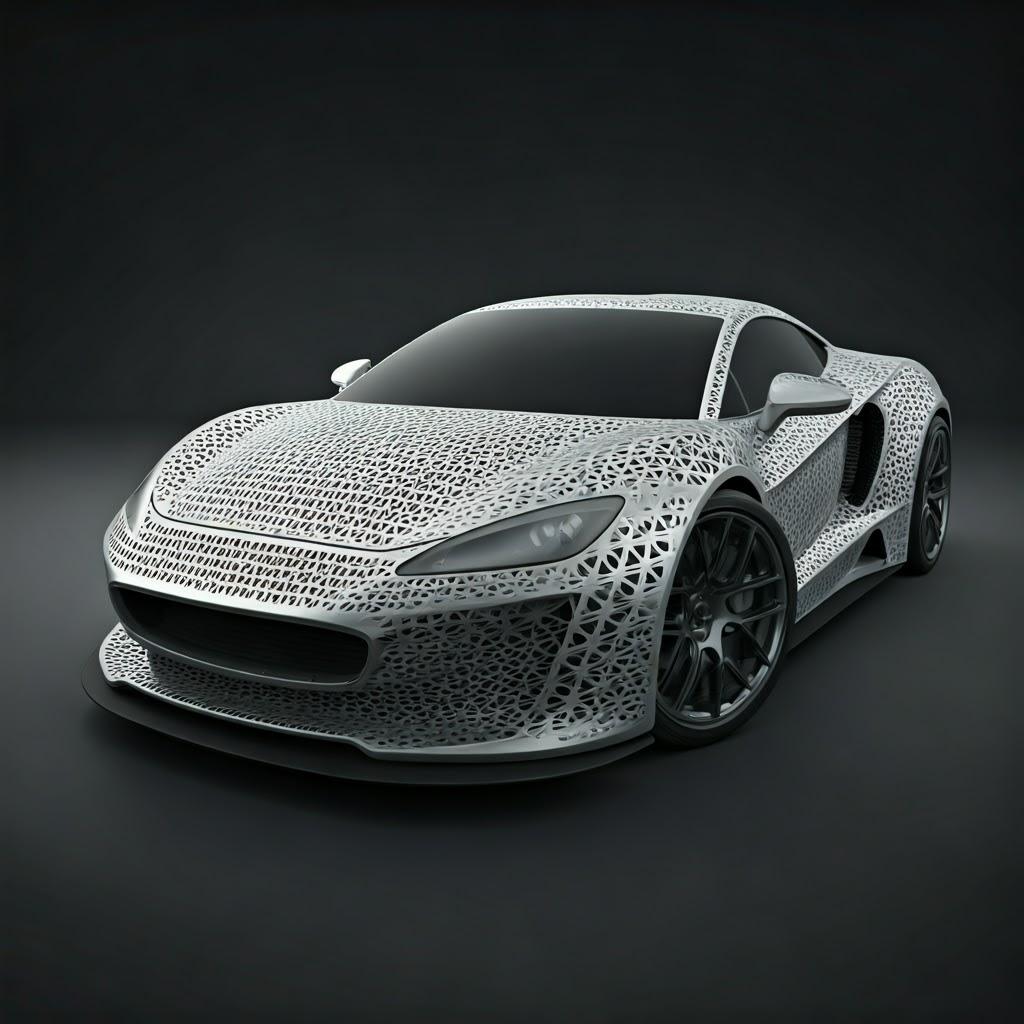
Post-Processing Requirements for Metal 3D Printed Fairings
Producing a metal aerospace fairing doesn’t end when the 3D printer stops. Additive manufacturing, particularly Powder Bed Fusion (PBF), typically requires a series of critical post-processing steps to transform the near-net-shape printed part into a functional, flight-ready component. These steps are essential for relieving internal stresses, removing support structures, achieving required dimensional tolerances and surface finishes, and ensuring the material meets performance specifications. Understanding this workflow is vital for accurate cost estimation, lead time planning, and selecting capable manufacturing partners.
Typical Post-Processing Workflow for L-PBF Aluminum Fairings (AlSi10Mg, Scalmalloy®):
- Depowdering / Powder Removal:
- Objective: Remove all unfused powder from the build chamber and, critically, from the part itself, including internal channels, lattice structures, and cavities.
- Metody: Compressed air blow-off, brushing, vibration, ultrasonic cleaning, sometimes specialized fluid flushing systems. Effective DfAM (incorporating escape holes) is crucial for complete removal from internal features.
- Importance: Residual powder adds weight and can compromise functionality or safety. Thorough depowdering is mandatory.
- Stress Relief Heat Treatment:
- Objective: Reduce the significant internal stresses built up during the rapid heating and cooling cycles inherent in the L-PBF process. These stresses can cause warping, distortion, and reduced mechanical performance if not relieved.
- Proces: The part, often while still attached to the build plate, is heated in a controlled atmosphere furnace to a specific temperature (below the aging temperature for precipitation-hardening alloys like AlSi10Mg/Scalmalloy®), held for a defined period, and then slowly cooled. Exact parameters depend on the alloy and part geometry.
- Importance: Absolutely critical for dimensional stability during subsequent steps (like removal from the build plate) and for the part’s long-term performance. Skipping or improperly performing stress relief can lead to part failure.
- Part Removal from Build Plate:
- Objective: Separate the printed fairing(s) from the metal build plate they were fused to during printing.
- Metody: Typically done using wire EDM (Electrical Discharge Machining), band sawing, or sometimes milling/machining. Care must be taken not to damage the part.
- Rozważania: The interface layer between the part and the plate is usually dense; the chosen method depends on part geometry, material, and available equipment.
- Usunięcie konstrukcji wsporczej:
- Objective: Remove the temporary support structures generated during the build process to anchor overhangs and manage heat.
- Metody: Can range from manual breaking/cutting for easily accessible supports to CNC machining, grinding, or specialized tooling for more intricate or internal supports. This can be labor-intensive.
- Uderzenie: Leaves witness marks or rougher surfaces where supports were attached, often requiring further finishing. DfAM aims to minimize the need for complex supports.
- Solution Treatment and Aging (Precipitation Hardening – e.g., T6 Temper for AlSi10Mg):
- Objective: Develop the final, desired mechanical properties (strength, hardness) for precipitation-hardenable alloys like AlSi10Mg and Scalmalloy®.
- Proces: Involves heating the part to a specific high temperature (solutionizing), holding it to dissolve alloying elements into the aluminum matrix, rapidly quenching (cooling) it, and then aging it at a lower elevated temperature for a set time to precipitate fine hardening particles.
- Importance: Essential for achieving the datasheet properties of these alloys. The exact T6 or other aging cycle parameters are critical and alloy-specific. Must be performed in calibrated furnaces with controlled atmospheres to prevent oxidation.
- (Optional) Hot Isostatic Pressing (HIP):
- Objective: Close internal microporosity (gas pores or lack-of-fusion voids) that might be present after printing, thereby improving fatigue life, ductility, and property consistency.
- Proces: Subjects the part to high pressure (typically 100-200 MPa) and elevated temperature (below melting point) in an inert gas environment (e.g., Argon).
- Zastosowanie: More common for fatigue-critical titanium or superalloy components, but sometimes considered for high-performance aluminum parts like Scalmalloy® in critical applications to ensure maximum density and performance. Adds significant cost and lead time.
- Machining / Finishing of Critical Features:
- Objective: Achieve tight tolerances, specific flatness/parallelism, or required surface finishes on functional interfaces (e.g., mounting points, mating surfaces, sealing edges).
- Metody: CNC milling, turning, grinding. Requires appropriate fixtures to hold the potentially complex AM part.
- Importance: Ensures proper fit, assembly, and function within the larger aircraft structure. Requires designs incorporating machining stock (DfAM).
- Wykończenie powierzchni:
- Objective: Achieve the desired overall surface texture for aerodynamic smoothness, aesthetics, or preparation for coating.
- Metody: As discussed previously: bead blasting (common for a uniform matte finish), tumbling, polishing, etc. The choice depends on the specific requirements for the fairing.
- Czyszczenie:
- Objective: Remove any residual machining fluids, blasting media, or contaminants before final inspection and coating/assembly.
- Metody: Aqueous cleaning, solvent wiping, ultrasonic cleaning.
- Coating / Painting / Anodizing:
- Objective: Provide enhanced corrosion protection, wear resistance, specific surface properties (e.g., emissivity), or desired color/appearance.
- Metody: Anodizing (common for aluminum), chemical conversion coatings (e.g., Alodine), priming and painting, specialized aerospace coatings.
- Importance: Essential for long-term durability in the aerospace operating environment.
- Final Inspection and Quality Assurance:
- Objective: Verify that the finished fairing meets all dimensional, material, and functional specifications defined in the drawings and requirements documentation.
- Metody: Dimensional inspection (CMM, 3D scanning), surface roughness measurement, visual inspection, potentially Non-Destructive Testing (NDT) like dye penetrant testing or CT scanning (especially for critical parts or to verify powder removal from internal channels). Material testing (tensile tests on witness coupons printed alongside the part) is often required for aerospace certification.
Implications for Procurement and Supply Chain:
- Cost and Lead Time: Post-processing often constitutes a significant portion (sometimes >50%) of the total cost and lead time for a metal AM part. Each step adds time and requires specialized equipment and expertise.
- Supplier Capability: It is crucial to select an AM service provider or a network of suppliers capable of performing all necessary post-processing steps to the required aerospace standards (e.g., AS9100 certification). A vertically integrated provider who manages the entire workflow from printing through final inspection can simplify logistics and ensure accountability. Companies with deep roots in manufacturing processes, like Met3dp, understand the importance of these downstream steps.
- DfAM Impact: Clever design leveraging DfAM principles can significantly reduce the burden of post-processing, for example, by minimizing support structures or designing features to be net-shape where possible.
In summary, post-processing is an integral and often complex part of the metal AM workflow for aerospace fairings. Thorough planning, realistic expectations regarding cost and time, and partnering with capable suppliers are essential for success.
Common Challenges in 3D Printing Aerospace Fairings and Mitigation Strategies
While metal 3D printing offers significant advantages for aerospace fairings, it’s not without its challenges. Understanding these potential hurdles and the strategies employed by experienced manufacturers to mitigate them is crucial for successful implementation. These challenges span material science, process control, and design intricacies.
1. Warping, Distortion, and Residual Stress:
- Wyzwanie: The intense, localized heating and rapid cooling inherent in L-PBF create significant thermal gradients, leading to the buildup of internal residual stresses within the part and the potential for warping or distortion, especially in large or geometrically complex fairings. Stresses can compromise dimensional accuracy and even cause cracking.
- Mitigation Strategies:
- Optimized Part Orientation: Orienting the part on the build plate to minimize large flat surfaces parallel to the recoater blade and manage heat distribution.
- Robust Support Structures: Designing effective support structures not only for overhangs but also to anchor the part firmly to the build plate, acting as heat sinks and resisting deformation.
- Optimized Process Parameters: Fine-tuning laser power, scan speed, and scan strategy (e.g., island scanning) to manage heat input and cooling rates.
- Build Plate Heating: Preheating the build plate reduces thermal gradients.
- Stress Relief Heat Treatment: Performing a thermal stress relief cycle immediately after printing (often before removal from the build plate) is essential to relax internal stresses.
- Simulation: Using process simulation software to predict thermal stresses and distortion, allowing for adjustments to orientation or supports before printing.
2. Support Structure Design and Removal:
- Wyzwanie: Fairings often have complex curves and overhangs requiring support. Designing supports that are effective during the build but also easy and clean to remove without damaging the part’s surface can be difficult. Accessing internal supports within complex fairing geometries can be particularly challenging.
- Mitigation Strategies:
- DfAM for Self-Support: Designing features to be self-supporting (e.g., using angles >45°) wherever possible. Using chamfers or optimized fillet shapes instead of sharp overhangs.
- Optimized Support Types: Utilizing specialized support structures (e.g., thin-walled, perforated, tree-like) that provide adequate support with minimal contact points and are easier to remove.
- Orientation Strategy: Balancing support minimization with other factors like surface finish and build time.
- Post-Processing Planning: Ensuring that support removal methods (manual, CNC) are considered during the design phase and that access is available.
- Material Choice: Some support materials or designs are specifically developed for easier removal.
3. Powder Removal from Internal Features:
- Wyzwanie: Lightweight fairings often incorporate internal channels, cavities, or complex lattice structures. Ensuring complete removal of all unfused powder from these intricate internal geometries after printing is critical but can be difficult.
- Mitigation Strategies:
- DfAM for Powder Escape: Designing appropriately sized and located drain/escape holes to allow powder to flow out easily using gravity, vibration, or flushing. Avoiding internal “dead ends” where powder can become trapped.
- Optimized Orientation: Orienting the part to facilitate powder drainage during the build and depowdering process.
- Effective Depowdering Techniques: Utilizing multi-axis vibration tables, compressed air jets, ultrasonic cleaning, or specialized flushing systems.
- Inspection: Using methods like visual inspection (borescopes), weighing the part, or CT scanning (for critical applications) to verify complete powder removal.
4. Porosity Control:
- Wyzwanie: Small voids or pores can sometimes form within the printed material due to trapped gas (gas porosity) or incomplete melting/fusion between layers or scan tracks (lack-of-fusion porosity). Porosity can degrade mechanical properties, particularly fatigue life, which is critical for aerospace components.
- Mitigation Strategies:
- High-Quality Powder: Using powders with controlled sphericity, particle size distribution, and low gas content (especially low oxygen and moisture). This highlights the importance of sourcing from reputable suppliers like Met3dp, who utilize advanced atomization processes (Gas Atomization, PREP).
- Optimized Process Parameters: Developing and validating robust print parameters (laser power, scan speed, layer thickness, hatch spacing, gas flow within the build chamber) specific to the alloy (AlSi10Mg, Scalmalloy®) and machine being used.
- Machine Maintenance & Calibration: Ensuring the AM system is well-maintained, calibrated, and the build chamber atmosphere (inert gas like Argon) is pure.
- (Optional) Hot Isostatic Pressing (HIP): Can be used post-print to close internal pores through high pressure and temperature, achieving near-full density, though it adds cost.
5. Achieving Consistent Material Properties and Microstructure:
- Wyzwanie: Ensuring that the mechanical properties (strength, ductility, fatigue life) and microstructure are consistent throughout the fairing and repeatable from build to build is essential for aerospace certification and reliability. Factors like slight variations in powder batches, machine conditions, or thermal history can influence properties.
- Mitigation Strategies:
- Strict Powder Management: Rigorous quality control of incoming powder, proper storage, handling, and controlled recycling protocols to maintain powder consistency.
- Validated Process Parameters: Using extensively tested and validated parameter sets for the specific alloy and machine combination.
- Process Monitoring & Control: Implementing available in-situ monitoring tools and maintaining tight control over all aspects of the build environment.
- Standardized Post-Processing: Ensuring heat treatment cycles (stress relief, aging) are performed precisely according to specification in calibrated furnaces.
- Witness Coupons: Printing standardized test specimens (witness coupons) alongside the actual fairing during each build. These coupons undergo destructive testing (e.g., tensile tests) to verify that the build achieved the required material properties.
- Supplier Qualification: Working with experienced AM service providers who have robust quality management systems (e.g., AS9100 certified) and a proven track record in aerospace component production.
Overcoming these challenges requires a combination of advanced technology, material science expertise, rigorous process control, and smart design strategies (DfAM). Collaboration between designers, material experts, and manufacturing engineers is key to successfully leveraging metal AM for demanding applications like aerospace fairings.
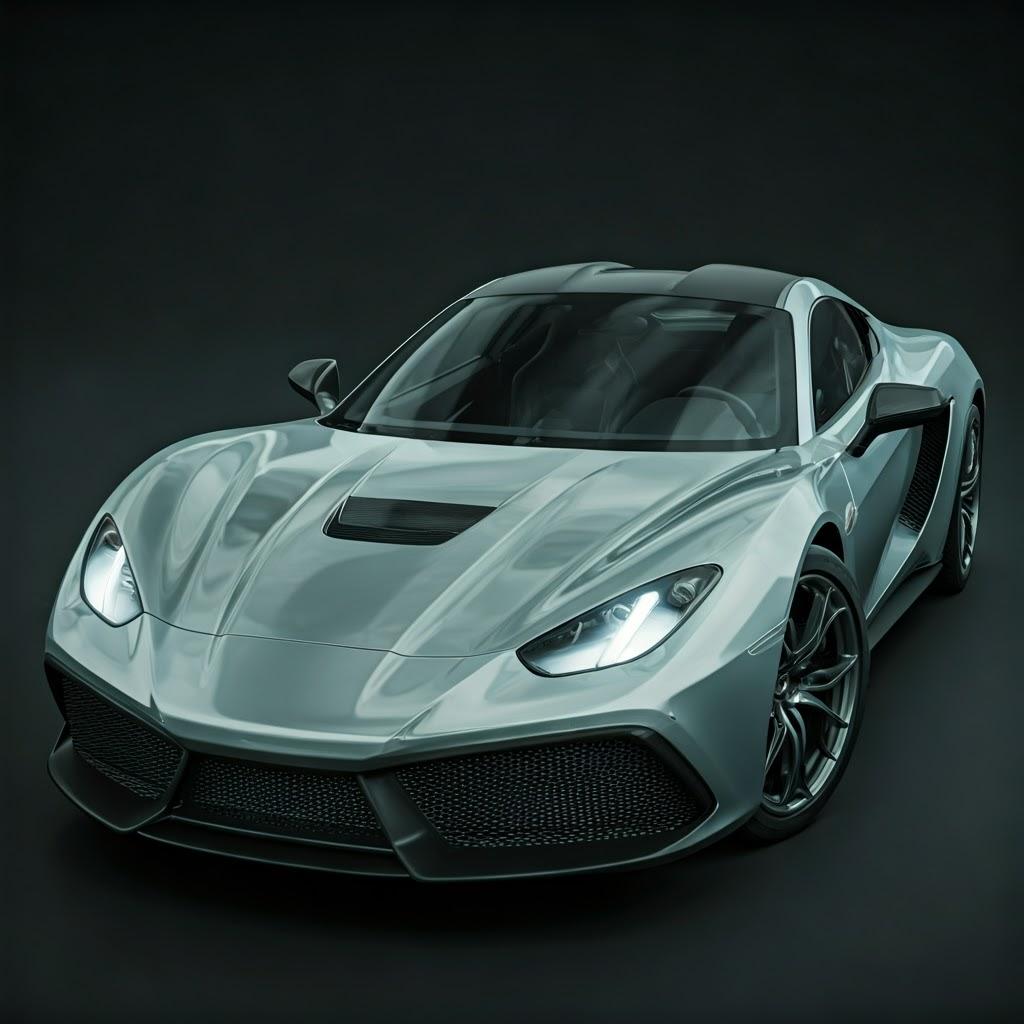
How to Choose the Right Metal 3D Printing Service Provider for Aerospace Fairings
Selecting the right manufacturing partner is arguably as critical as the design and material choices when producing flight-worthy aerospace components like fairings using metal additive manufacturing. The unique demands of the aerospace industry – uncompromising safety standards, rigorous quality control, complex geometries, and advanced materials – necessitate partnering with a service provider possessing specialized expertise and certified capabilities. For procurement managers and engineering teams evaluating potential suppliers for AlSi10Mg or Scalmalloy® fairings, here are key criteria to consider:
Essential Criteria for Selecting an Aerospace AM Supplier:
- Aerospace Certifications (AS9100): This is non-negotiable for flight hardware. AS9100 certification (or equivalent standards like EN9100) demonstrates that the provider operates a robust Quality Management System (QMS) tailored to the stringent requirements of the aerospace, space, and defense industries. It ensures traceability, process control, risk management, and continuous improvement are embedded in their operations. Always verify the certification status and scope.
- Proven Experience with Target Materials & Applications: Look beyond general AM experience. Does the provider have a demonstrated track record printing aerospace components specifically using AlSi10Mg and/or Scalmalloy®? Ask for case studies, examples of similar parts produced, and evidence of validated process parameters for these alloys. Experience translates to understanding material nuances, potential challenges, and effective mitigation strategies.
- Machine Capabilities and Technology:
- Platform Size: Ensure the provider’s L-PBF machines have a build volume sufficient to accommodate the size of your fairing, potentially allowing multiple parts per build for efficiency.
- Machine Quality & Features: Modern, well-maintained machines from reputable manufacturers are crucial. Features like multi-laser systems (for speed), build plate heating, inert atmosphere control, and ideally, in-situ process monitoring capabilities contribute to quality and consistency.
- Redundancy: Does the provider have multiple machines capable of running your part? This provides backup capacity and reduces lead time risks.
- Material Expertise and Handling:
- Powder Sourcing & Quality Control: How do they source their AlSi10Mg or Scalmalloy® powder? Do they perform incoming quality checks? What are their powder handling, storage, and recycling procedures to prevent contamination and ensure consistency? Reputable suppliers often work closely with powder manufacturers or even have in-house expertise, like Met3dp’s focus on advanced powder making systems.
- Material Characterization: Do they have the capability to perform material testing (e.g., tensile tests on witness coupons) to verify batch properties?
- Comprehensive Post-Processing Capabilities: As detailed earlier, post-processing is extensive for aerospace AM parts. An ideal provider will either have in-house capabilities or a well-managed network for all required steps:
- Stress Relief & Heat Treatment (in calibrated, certified furnaces)
- Support Removal & Build Plate Separation (Wire EDM, machining)
- Precision CNC Machining (for critical tolerances)
- Surface Finishing (blasting, polishing, etc.)
- Czyszczenie
- Coating/Anodizing
- Non-Destructive Testing (NDT – e.g., dye penetrant, CT scanning)
- Metrology & Inspection (CMM, 3D scanning)
- Benefit of Integrated Services: Working with a provider offering end-to-end solutions simplifies logistics, project management, and accountability.
- Robust Quality Management System (Beyond Certification):
- Traceability: Full traceability of materials, processes, and personnel involved in manufacturing each part.
- Documentation: Comprehensive documentation packages (material certs, process logs, inspection reports, certificates of conformance).
- Kontrola procesu: Statistical Process Control (SPC) methods, regular machine calibration, and adherence to validated procedures.
- Engineering and DfAM Support: Does the provider offer Design for Additive Manufacturing (DfAM) consultation? Can their engineers collaborate with your team to optimize the fairing design for printability, weight reduction, support minimization, and cost-effectiveness? This collaborative approach often yields the best results.
- Customer Service and Communication: Responsiveness, clear communication, and proactive project management are vital, especially when dealing with complex aerospace projects.
- Capacity and Lead Time: Can the provider meet your required production volumes (from prototypes to potentially series production) within acceptable lead times? Understand their scheduling process and typical turnaround times for similar projects.
- Financial Stability and Reputation: Partnering with a stable, reputable company provides assurance for long-term projects and supply chain reliability. Check references and industry standing.
Supplier Audits and Qualification:
For critical aerospace components, a thorough supplier audit is typically necessary before awarding contracts. This involves visiting the facility, reviewing their QMS documentation, interviewing key personnel, and verifying their equipment and processes firsthand. Building a strong, collaborative relationship based on trust and proven capability is essential for successfully integrating 3D printed fairings into your aerospace platform. Look for partners who position themselves not just as vendors, but as solution providers invested in your success, embodying the kind of comprehensive approach seen in companies with decades of collective expertise in metal additive manufacturing.
Understanding Cost Factors and Lead Times for 3D Printed Aerospace Fairings
While metal additive manufacturing enables the production of highly optimized, lightweight aerospace fairings, understanding the factors that drive cost and lead time is crucial for project planning, budgeting, and making informed sourcing decisions. Both cost and time can vary significantly based on design, material, quality requirements, and the chosen manufacturing partner.
Key Cost Drivers for 3D Printed Fairings:
- Koszt materiałów:
- Alloy Choice: There’s a significant cost difference between standard AM aluminum like AlSi10Mg and high-performance, specialized alloys like Scalmalloy® (due to scandium content). Scalmalloy® powder can be multiple times more expensive.
- Part Volume & Density: The sheer amount of powder required directly impacts cost. Larger or denser fairings consume more material. Topology optimization and lattice structures directly reduce this cost component.
- Support Structure Volume: Material used for supports also adds to the cost, though it’s often less dense than the main part.
- Powder Reuse/Recycling: Efficient powder recycling by the service provider can slightly mitigate costs, but strict aerospace quality control limits the number of reuse cycles.
- Machine Time (Print Time): This is often a primary cost driver.
- Part Height: Build time is strongly correlated with the height of the part in the build chamber, as each layer takes a certain amount of time to process. Optimal orientation considers this.
- Part Volume/Cross-Sectional Area: Larger volumes and wider cross-sections require more laser scanning time per layer.
- Złożoność: Intricate details and extensive support structures can increase scanning time.
- Machine Hourly Rate: AM machines represent significant capital investment, and their operational costs (energy, inert gas, maintenance) contribute to the hourly rate charged by the service provider. Multi-laser machines can reduce print time but may have higher hourly rates.
- Koszty pracy:
- Setup & Teardown: Preparing the build file, setting up the machine, loading powder, and removing the build plate/parts requires skilled labor.
- Depowdering: Manual or semi-automated removal of unfused powder.
- Przetwarzanie końcowe: Support removal, machining, surface finishing, and inspection can be very labor-intensive, especially for complex parts or high finish requirements.
- Koszty przetwarzania końcowego: As discussed, these steps are essential and often significant:
- Obróbka cieplna: Furnace time, energy, controlled atmosphere costs.
- Obróbka skrawaniem: CNC machine time, tooling, programming, and labor.
- Wykończenie: Costs vary greatly depending on the method (blasting is relatively cheap, extensive polishing is expensive).
- NDT & Inspection: Equipment costs, skilled operator time. HIPing, if required, adds substantial cost.
- Quality Assurance and Certification: Aerospace requirements demand rigorous inspection, testing (including witness coupons), and extensive documentation, adding overhead compared to industrial parts.
- Engineering & Setup Fees: Initial file preparation, DfAM consultation, process simulation, and fixture design may incur one-time engineering or setup charges, especially for new designs or prototypes.
- Order Volume (Economies of Scale):
- Prototyping vs. Production: One-off prototypes are typically more expensive per part than series production due to setup costs being amortized over fewer units.
- Nesting: For smaller fairings, printing multiple parts simultaneously in one build (nesting) can significantly reduce the effective machine time cost per part.
- Wholesale/Bulk Pricing: Suppliers may offer volume discounts for larger orders or ongoing production contracts, making AM more cost-effective for established aerospace component distributors or OEMs ordering higher quantities.
Factors Influencing Lead Time:
- Print Time: Directly related to part height and volume, can range from hours to several days for large or complex fairings.
- Machine Availability: Queue times at the service provider depend on their current workload and machine capacity.
- Post-Processing Duration: This often takes longer than the print itself. Heat treatment cycles have fixed durations, complex machining takes time, and finishing/coating processes add days. Support removal can be a bottleneck.
- Quality Assurance & Inspection: Thorough inspection and documentation review add time.
- Shipping & Logistics: Transport time to the final destination.
- Design Complexity & Iteration: If design changes or iterations are required, this adds to the overall project timeline.
Typical Lead Time Range: For a moderately complex aerospace fairing, expect lead times ranging from 1-2 weeks for rapid prototypes (with minimal post-processing) to 4-10 weeks or more for fully qualified, production-ready parts requiring extensive post-processing, machining, and inspection. Lead times for parts requiring specialized processes like HIP or complex coatings will be longer.
Konkurencyjność kosztowa: Metal AM is most cost-competitive for fairings characterized by:
- High geometric complexity.
- Need for significant lightweighting (where weight savings translate to high operational value).
- Part consolidation opportunities.
- Low-to-medium production volumes.
- Rapid prototyping requirements.
For very simple fairings produced in high volumes, traditional methods like sheet metal forming might still be more economical upfront. However, a Total Cost of Ownership (TCO) analysis, considering lifecycle benefits like fuel savings from lightweighting, should be performed.
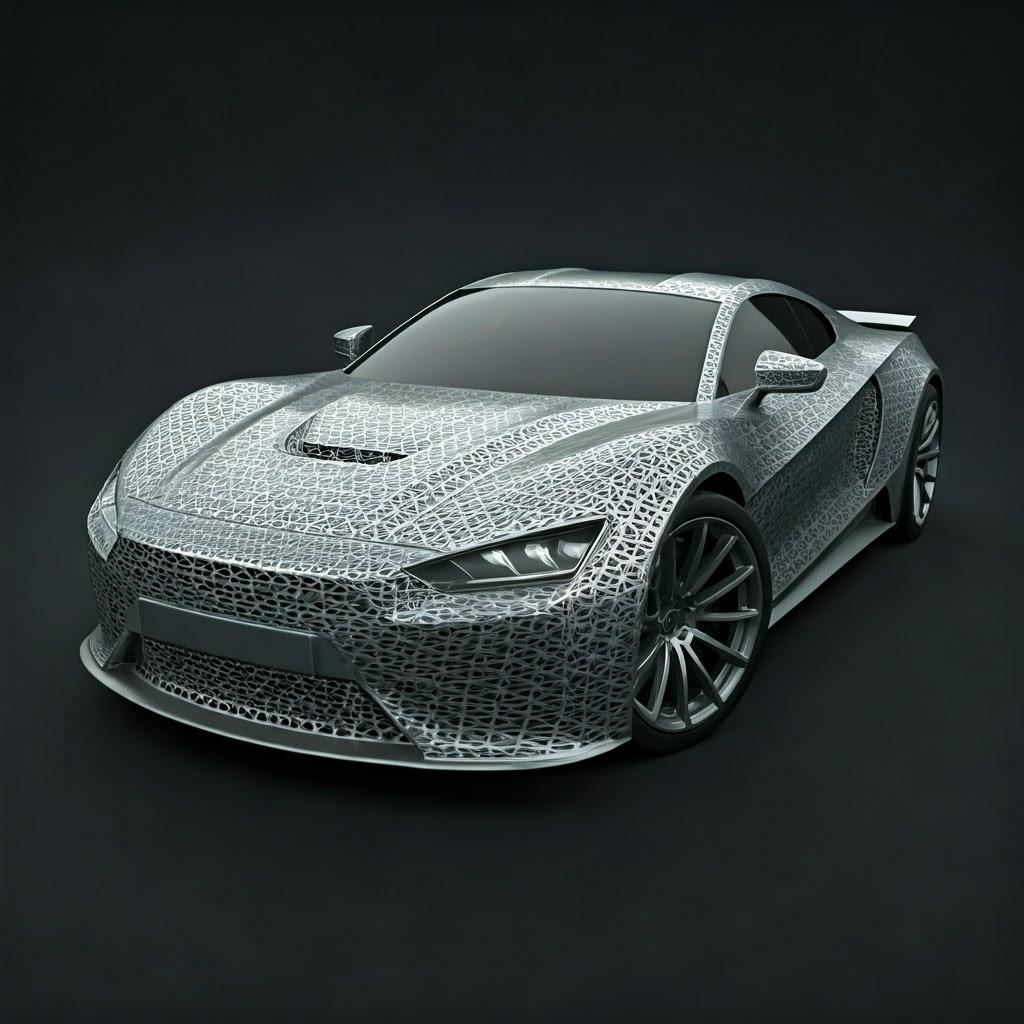
Frequently Asked Questions (FAQ) about 3D Printed Aerospace Fairings
Here are answers to some common questions engineers and procurement managers have about using metal additive manufacturing for aerospace fairings:
- Q1: How does the strength and performance of 3D printed fairings (AlSi10Mg/Scalmalloy®) compare to traditionally manufactured ones (e.g., sheet metal aluminum, composites)?
- A: Performance is highly dependent on the specific alloy and design.
- AlSi10Mg: In its typical heat-treated state (e.g., T6), AlSi10Mg offers strength comparable to mid-range aluminum casting alloys but generally lower strength and fatigue life than high-strength wrought aerospace aluminum (like 7075-T6). Its primary advantage via AM is enabling complex, lightweight designs not feasible otherwise.
- Scalmalloy®: This high-performance AM alloy can meet or exceed the static strength of many traditional high-strength wrought aluminum alloys (like 7000 series) and offers excellent fatigue properties, making it a viable replacement in demanding applications.
- vs. Composites: Composites often offer the highest specific stiffness and strength but can be more susceptible to impact damage and complex/costly to manufacture in intricate shapes compared to AM metals. Metal AM provides good isotropic properties (more uniform strength in all directions compared to layered composites) and damage tolerance.
- Overall: The key benefit of metal AM often lies in achieving significant weight savings through topology optimization and complex geometries while meeting or exceeding the necessary performance requirements for the specific fairing application, especially when using alloys like Scalmalloy®.
- A: Performance is highly dependent on the specific alloy and design.
- Q2: Is metal 3D printing a cost-competitive manufacturing method for aerospace fairings?
- A: It depends. Metal AM is generally most cost-competitive for:
- Geometrie złożone: Parts difficult or impossible to make via traditional methods.
- Low-to-Medium Volumes: Where tooling costs for traditional methods (casting, forming) are prohibitive.
- Konsolidacja części: Replacing multi-part assemblies with a single print reduces assembly labor and fastener costs.
- High-Value Lightweighting: When the operational cost savings (fuel efficiency, payload capacity) from weight reduction outweigh a potentially higher upfront part cost.
- Rapid Prototyping & Development: Faster iteration cycles reduce development costs.
- Dla simple, high-volume fairings, traditional methods like sheet metal forming or stamping are often still more cost-effective per part. A detailed cost analysis comparing AM (including material, machine time, extensive post-processing) with traditional methods, considering the entire lifecycle value, is recommended. Factor in potential wholesale pricing advantages when discussing production volumes with AM suppliers.
- A: It depends. Metal AM is generally most cost-competitive for:
- Q3: What are the main advantages of using Scalmalloy® over the more common AlSi10Mg for a fairing?
- A: The primary advantages of Scalmalloy® are its superior mechanical properties:
- Wyższa wytrzymałość: Significantly higher tensile and yield strength, allowing for thinner walls and further lightweighting for the same load requirements, or handling higher loads.
- Excellent Fatigue Life: Superior resistance to cyclic loading, crucial for components experiencing vibration or fluctuating aerodynamic pressures during flight.
- Dobra ciągliwość: Retains good ductility despite its high strength, offering better damage tolerance.
- Choose Scalmalloy® when the fairing is structurally critical, subjected to high loads or significant fatigue cycles, or when maximizing weight savings is paramount and the higher material cost can be justified by performance gains. AlSi10Mg is suitable for less demanding applications where cost-effectiveness and good processability are primary drivers.
- A: The primary advantages of Scalmalloy® are its superior mechanical properties:
- Q4: What kind of certifications and qualifications are typically required for flight-critical 3D printed fairings?
- A: Requirements are rigorous and multi-layered:
- Supplier Quality System: The manufacturing facility must typically hold AS9100 certification.
- Process Validation: The specific AM process (machine, material batch, parameter set, post-processing steps) used to produce the fairing must be rigorously validated and proven to consistently produce parts meeting specifications. This involves extensive testing.
- Material Specification: The AlSi10Mg or Scalmalloy® powder must meet aerospace material specifications (e.g., AMS standards where applicable).
- Część Kwalifikacje: Each specific fairing design usually requires qualification testing, which may include static load tests, fatigue tests, vibration tests, and detailed NDT inspection, often witnessed or approved by the aircraft manufacturer and potentially regulatory bodies (like FAA or EASA).
- Traceability & Documentation: Full, documented traceability from raw powder batch to finished, inspected part is mandatory.
- A: Requirements are rigorous and multi-layered:
Conclusion: Elevating Aerospace Design with Lightweight 3D Printed Fairings
The journey through the world of 3D printed aerospace fairings reveals a compelling narrative of innovation meeting necessity. Aerospace engineering’s relentless pursuit of lighter, stronger, and more efficient aircraft finds a powerful ally in metal additive manufacturing. By leveraging the capabilities of L-PBF technology and advanced materials like the reliable AlSi10Mg or the high-performance Scalmalloy®, designers and manufacturers can now create fairings that were previously unimaginable.
The advantages are clear and impactful:
- Unprecedented Lightweighting: Topology optimization and lattice structures shed critical kilograms, directly contributing to fuel efficiency and increased payload capacity.
- Geometric Freedom: Complex aerodynamic curves and integrated features are produced with ease, optimizing performance and reducing drag.
- Konsolidacja części: Reducing assembly complexity, minimizing potential failure points, and streamlining supply chains.
- Accelerated Innovation: Rapid prototyping enables faster design iteration and validation, bringing optimized components to aircraft sooner.
However, realizing this potential demands a holistic approach. It requires embracing DfAM principles, carefully selecting the appropriate material, meticulously managing the intricate post-processing workflow, and diligently overcoming inherent manufacturing challenges through robust process control.
Crucially, success hinges on collaboration and expertise. Partnering with the right metal additive manufacturing service provider – one with proven aerospace experience, certified quality systems, deep material knowledge, and comprehensive capabilities spanning design support to final inspection – is paramount. Companies like Met3dp, with their foundation in both advanced metal powder production and industrial 3D printing solutions, represent the type of integrated expertise needed to navigate the complexities of aerospace AM.
Metal 3D printing is no longer a futuristic novelty; it is a present-day enabler of next-generation aerospace design. For aerodynamic fairings, it offers a pathway to enhanced performance, reduced operating costs, and greater design freedom. As the technology continues to mature and material options expand, we can expect metal AM to play an increasingly vital role in shaping the future of flight, making aircraft lighter, faster, and more efficient, one optimized layer at a time. Explore the possibilities and discover how metal additive manufacturing can elevate your aerospace components.
Udostępnij
MET3DP Technology Co., LTD jest wiodącym dostawcą rozwiązań w zakresie produkcji addytywnej z siedzibą w Qingdao w Chinach. Nasza firma specjalizuje się w sprzęcie do druku 3D i wysokowydajnych proszkach metali do zastosowań przemysłowych.
Zapytaj o najlepszą cenę i spersonalizowane rozwiązanie dla Twojej firmy!
Powiązane artykuły
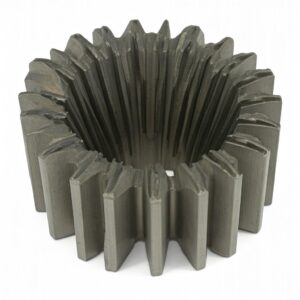
Wysokowydajne segmenty łopatek dysz: Rewolucja w wydajności turbin dzięki drukowi 3D w metalu
Czytaj więcej "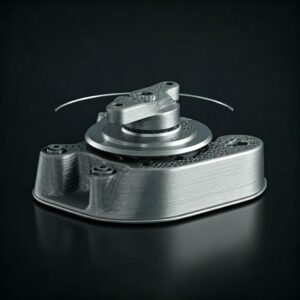
Drukowane w 3D mocowania dla samochodowych czujników radarowych: Precyzja i wydajność
Czytaj więcej "Informacje o Met3DP
Ostatnia aktualizacja
Nasz produkt
KONTAKT
Masz pytania? Wyślij nam wiadomość teraz! Po otrzymaniu wiadomości obsłużymy Twoją prośbę całym zespołem.
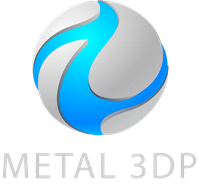
Proszki metali do druku 3D i produkcji addytywnej