3D Printed Pipe Clamps for High-Performance Aircraft Systems
Spis treści
Introduction: Revolutionizing Aerospace Fluid and Wiring Management with 3D Printed Pipe Clamps
The aerospace industry operates at the cutting edge of engineering, demanding components that offer unparalleled performance, reliability, and efficiency. Every gram saved, every component optimized, contributes significantly to fuel economy, payload capacity, and overall aircraft safety. Within the intricate network of aircraft systems – from hydraulic and fuel lines to environmental control systems (ECS) and complex wiring harnesses – seemingly simple components like pipe clamps play a critical, often underestimated, role. Traditionally manufactured through methods like stamping, forging, or machining, these clamps are now undergoing a technological transformation thanks to wytwarzanie przyrostowe metali (AM), commonly known as metal Drukowanie 3D.
This shift towards 3D printed pipe clamps represents more than just a novel manufacturing technique; it’s a strategic move towards creating lighter, stronger, and more customized solutions tailored to the specific, often demanding, requirements of modern aircraft design. Metal 3D printing allows aerospace engineers and procurement managers to rethink component design, enabling part consolidation, complex geometries previously impossible to manufacture, and significantly reduced lead times for both prototyping and production parts. This technology facilitates the creation of highly optimized clamps that perfectly match tube diameters, routing paths, and structural integration points, minimizing weight while maximizing holding strength and vibration resistance. For industries where precision and performance are non-negotiable, embracing advanced manufacturing techniques like those offered by leading providers such as Met3dp is crucial for maintaining a competitive edge and pushing the boundaries of aerospace innovation. The ability to produce high-performance clamps from aerospace-grade materials like Aluminum alloys (e.g., AlSi10Mg) and Titanium alloys (e.g., Ti-6Al-4V) opens up new possibilities for enhancing fluid and wiring management across diverse aircraft platforms.
Core Applications: Where are 3D Printed Pipe Clamps Utilized in Aerospace?
The versatility of metal 3D printing allows for the creation of custom pipe clamps ideally suited for a wide array of applications within an aircraft. These components are essential for securing and organizing the complex networks that keep an aircraft operational. Procurement managers sourcing components for new builds or MRO (Maintenance, Repair, Overhaul) operations are increasingly looking towards AM suppliers for these critical parts.
Key Application Areas:
- Fluid Systems (Hydraulic & Fuel Lines):
- Function: Securely fastening high-pressure hydraulic lines and fuel lines, preventing movement, vibration fatigue, and potential leaks.
- AM Advantage: Custom clamps can be designed to perfectly contour complex tube runs, integrate vibration damping features, or accommodate non-standard diameters found in legacy or highly optimized systems. Lightweighting is crucial here to reduce overall aircraft mass. Titanium clamps offer excellent strength-to-weight and corrosion resistance for aggressive fluids.
- Wiring Harnesses & Cable Management:
- Function: Organizing and securing bundles of electrical wiring, data cables, and fiber optics, protecting them from chafing, vibration, and environmental factors.
- AM Advantage: Additive manufacturing allows for the creation of clamps with integrated strain relief features, multiple channels for segregating different cable types, or complex shapes to fit within tightly constrained spaces in avionics bays or along structural members. Part consolidation can reduce the number of individual fastening components.
- Environmental Control Systems (ECS) Ducting:
- Function: Holding low-pressure air ducts for cabin climate control and avionics cooling in place.
- AM Advantage: Lightweight aluminum alloys like AlSi10Mg are ideal. AM enables the production of clamps with complex organic shapes that minimize airflow disruption around the clamp itself or integrate mounting points for sensors or other components directly onto the clamp body.
- Pitot-Static System Tubing:
- Function: Securing the sensitive tubing connected to pitot tubes and static ports, crucial for accurate airspeed and altitude measurements.
- AM Advantage: High precision and custom fits are paramount. 3D printing can produce clamps that provide secure mounting without distorting the delicate tubing, ensuring system accuracy.
- Oxygen System Lines:
- Function: Fastening oxygen lines for crew and passengers, requiring high reliability and material compatibility.
- AM Advantage: Material selection is critical. Titanium alloys are often preferred for their compatibility and strength. AM allows for optimized designs that ensure secure fastening in critical life-support systems.
- Aerospace MRO & Custom Solutions:
- Function: Replacing obsolete or hard-to-source clamps during maintenance, or creating unique clamping solutions for modifications or upgrades.
- AM Advantage: The ability to produce parts on-demand without tooling significantly reduces lead times for rare or custom clamps, minimizing aircraft downtime. Digital inventories allow for rapid replication of parts as needed.
Procurement managers and engineers seeking reliable aerospace component suppliers for these applications benefit from partnering with companies experienced in metal AM, capable of delivering certified parts that meet stringent aerospace quality standards.
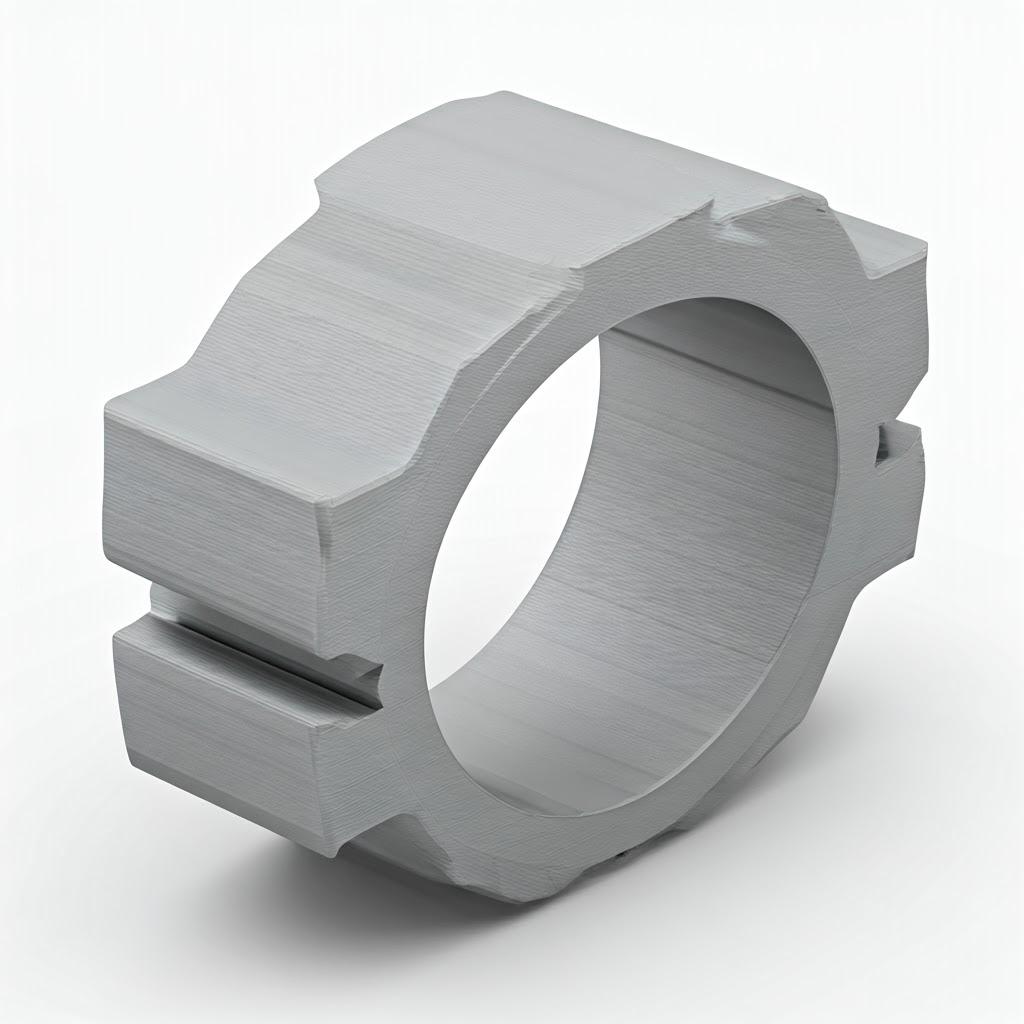
The Additive Advantage: Why Choose Metal 3D Printing for Aerospace Clamps?
While traditional manufacturing methods have served the aerospace industry well, metal 3D printing offers distinct advantages, particularly for components like pipe clamps, driving adoption among engineers and influencing sourcing decisions by procurement teams.
Key Benefits Driving Adoption:
- Significant Weight Reduction:
- How: AM enables topology optimization, removing material from low-stress areas while maintaining structural integrity. Complex, lattice-like internal structures can be created.
- Uderzenie: Reduced clamp weight contributes directly to lower overall aircraft mass, improving fuel efficiency and increasing payload capacity. Even small savings per part accumulate significantly across hundreds or thousands of clamps on an aircraft.
- Konsolidacja części:
- How: Multiple simple components (e.g., a clamp, a bracket, a fastener interface) can often be redesigned and printed as a single, integrated piece.
- Uderzenie: Reduces part count, assembly time, inventory complexity, and potential failure points. Simplifies supply chain management and lowers assembly costs.
- Complex Geometries & Customization:
- How: AM builds parts layer-by-layer, freeing design from the constraints of traditional methods (molding, machining). Highly organic shapes, internal channels, and non-uniform features are possible.
- Uderzenie: Clamps can be perfectly tailored to fit specific tube diameters, complex routing paths around obstacles, or integrate seamlessly with surrounding structures. This level of customization is often impractical or impossible with conventional techniques.
- Rapid Prototyping & Iteration:
- How: Designs can be quickly translated from CAD files to physical prototypes without the need for tooling.
- Uderzenie: Allows engineers to test and refine clamp designs rapidly, accelerating the development cycle for new aircraft systems or modifications. Fit checks and functional tests can be performed much earlier.
- Reduced Lead Times & On-Demand Production:
- How: Eliminates the need for expensive and time-consuming tooling (molds, dies, jigs). Parts can be printed directly from digital files.
- Uderzenie: Crucial for MRO operations needing quick replacements for obsolete parts or for low-volume production runs. Reduces inventory holding costs by enabling an “on-demand” manufacturing model. Supports supply chain resilience by providing an alternative sourcing method.
- Wydajność materiału:
- How: AM processes can utilize high-performance aerospace alloys like Ti-6Al-4V and AlSi10Mg, often achieving material properties comparable or even superior (in certain aspects like grain structure) to wrought or cast equivalents after appropriate post-processing.
- Uderzenie: Ensures clamps meet the demanding strength, temperature resistance, and corrosion resistance requirements of aerospace applications.
Comparison Table: Traditional vs. Additive Manufacturing for Aerospace Clamps
Cecha | Traditional Manufacturing (Machining/Stamping) | Metal 3D Printing (AM) | Advantage for Aerospace Clamps |
---|---|---|---|
Swoboda projektowania | Limited by tooling & process constraints | High (Complex geometries, internal features) | Optimization, Customization, Consolidation |
Waga | Often heavier due to design limitations | Potential for significant weight reduction | Poprawiona wydajność paliwowa |
Lead Time (Proto) | Weeks to Months (Tooling dependent) | Dni | Faster Development |
Lead Time (Prod) | Can be fast for high volume | Scalable, good for low/medium volume | Flexibility, On-Demand Capability |
Koszt oprzyrządowania | Wysoka inwestycja początkowa | Minimal / None | Lower barrier for custom parts |
Odpady materiałowe | High (Subtractive processes) | Low (Additive process) | Cost Savings, Sustainability |
Konsolidacja części | Difficult / Requires assembly | Readily achievable | Reduced Complexity & Assembly Time |
Personalizacja | Costly and time-consuming | Relatively easy | Tailored Solutions, MRO Support |
Export to Sheets
For procurement managers evaluating wholesale pipe clamp suppliers, understanding these AM advantages is key to making informed decisions that leverage technological advancements for better performance and potentially lower total cost of ownership.
Material Selection Deep Dive: AlSi10Mg and Ti-6Al-4V for Demanding Aerospace Environments
The choice of material is paramount in aerospace design, directly impacting component performance, weight, durability, and safety. For 3D printed pipe clamps, two materials stand out due to their excellent balance of properties and proven track record in additive manufacturing: AlSi10Mg (an aluminum alloy) and Ti-6Al-4V (a titanium alloy). Selecting the right material requires understanding the specific application’s demands – temperature exposure, structural load, corrosive environment, and weight targets. Reputable metal powder suppliers, like Met3dp, play a crucial role by providing high-quality, consistent powders essential for reliable 3D printing. Met3dp utilizes advanced gas atomization and Plasma Rotating Electrode Process (PREP) technologies to produce spherical metal powders with high purity, excellent flowability, and controlled particle size distribution – critical factors for achieving dense, high-strength printed parts.
AlSi10Mg (Aluminum-Silicon-Magnesium Alloy): The Lightweight Choice
- Kluczowe właściwości:
- Doskonały stosunek wytrzymałości do wagi.
- Good thermal conductivity.
- Good corrosion resistance in typical atmospheric conditions.
- Relatively easy to print via Laser Powder Bed Fusion (L-PBF).
- Good weldability (relevant for post-processing or assembly).
- Aerospace Clamp Applications: Ideal for applications where weight saving is a primary driver and operating temperatures are moderate (typically below 150°C). Common uses include securing ECS ducting, wiring harnesses in pressurized cabins, and low-pressure fluid lines.
- Why Use It? Significantly lighter than steel or titanium, offering substantial weight savings when used extensively throughout an aircraft. Its good printability allows for complex, thin-walled designs optimized for stiffness and low mass.
- Rozważania: Lower mechanical strength and temperature resistance compared to titanium. Requires appropriate heat treatment (e.g., T6) after printing to achieve optimal mechanical properties.
Ti-6Al-4V (Titanium-Aluminum-Vanadium Alloy): The High-Performance Standard
- Kluczowe właściwości:
- Excellent strength-to-weight ratio (higher absolute strength than AlSi10Mg).
- Outstanding corrosion resistance, even in harsh environments (e.g., exposure to hydraulic fluids, de-icing agents, saltwater).
- Good fatigue strength.
- High operating temperature capability (up to ~400°C).
- Biocompatible (relevant for specific niche applications, though less so for standard clamps).
- Aerospace Clamp Applications: The go-to choice for high-stress applications, securing critical systems, high-temperature zones (near engines), or where exposure to corrosive substances is likely. Used for hydraulic lines, fuel lines, engine components, and structural brackets integrated with clamps.
- Why Use It? Offers superior mechanical performance and environmental resistance compared to aluminum. Its durability and high-temperature capability make it suitable for the most demanding aerospace conditions. While heavier than aluminum, its high strength allows for designs that can still be lighter than comparable steel components.
- Rozważania: More challenging and costly to print compared to AlSi10Mg. Requires careful process control and specific post-processing like stress relief and often Hot Isostatic Pressing (HIP) to minimize internal defects and achieve optimal fatigue properties. Higher material cost.
Material Properties Comparison:
Nieruchomość | AlSi10Mg (Typical, Post-Processed) | Ti-6Al-4V (Typical, Post-Processed) | Jednostka | Uwagi |
---|---|---|---|---|
Gęstość | ~2.67 | ~4.43 | g/cm³ | Significant weight difference |
Ostateczna wytrzymałość na rozciąganie | 300 – 450 | 900 – 1150 | MPa | Ti-6Al-4V is much stronger |
Wytrzymałość na rozciąganie | 200 – 320 | 800 – 1050 | MPa | |
Moduł sprężystości | ~70 | ~110 – 120 | GPa | Titanium is stiffer |
Max Operating Temp. | ~150 | ~400 | °C | Approximate, application-dependent |
Odporność na korozję | Dobry | Doskonały | – | Titanium superior in harsh environments |
Relative Printability | Dobry | Umiarkowany | – | Requires more process control for Titanium |
Koszt względny | Niższy | Wyższy | – | Both material and processing costs |
Export to Sheets
Procurement managers must work closely with engineering teams and AM service providers like Met3dp to select the optimal material based on performance requirements, budget, and certification needs. Ensuring the use of high-quality, aerospace-certified metal powders from reliable suppliers is fundamental to achieving the desired performance and reliability for these critical 3D printed components. Sources and related content
Design for Additive Manufacturing (DfAM): Optimizing Pipe Clamps for 3D Printing Success
Transitioning from traditional manufacturing to additive manufacturing isn’t just about changing the production method; it requires a fundamental shift in design philosophy. Design for Additive Manufacturing (DfAM) principles are crucial for unlocking the full potential of 3D printing for aerospace pipe clamps, ensuring functionality, printability, and cost-effectiveness. Engineers designing these components, and procurement managers sourcing them, should understand that simply replicating a traditionally designed clamp often fails to leverage AM’s unique capabilities and can even introduce printing challenges. Collaboration with experienced AM service providers, who understand the nuances of various metody drukowania, is highly beneficial during the design phase.
Key DfAM Principles for Aerospace Pipe Clamps:
- Topology Optimization:
- Concept: Using specialized software to algorithmically remove material from areas of low stress while ensuring structural integrity under defined load conditions.
- Application for Clamps: Creates highly organic, lightweight structures that efficiently bear clamping forces and resist vibration. This is a primary driver for achieving significant weight savings compared to bulky, conventionally machined clamps. The resulting designs often resemble natural structures, like bone, optimized for strength-to-weight.
- Support Structure Minimization:
- Concept: Designing parts to be self-supporting or require minimal support structures during the layer-by-layer printing process. Overhanging features typically require support below a certain angle (often around 45 degrees).
- Application for Clamps: Orienting the clamp optimally on the build plate can significantly reduce support needs. Designing gradual transitions, using chamfers instead of sharp overhangs, and incorporating built-in support features (that may be part of the final geometry or easily removed) can minimize time-consuming and potentially damaging post-processing steps. Reducing supports also saves material and printing time, lowering costs.
- Feature Integration & Part Consolidation:
- Concept: Combining multiple functions or components into a single, additively manufactured part.
- Application for Clamps: Integrating mounting brackets, vibration damping elements, heat sinks, or even sensor housings directly into the clamp body. This reduces assembly complexity, part count, weight, and potential points of failure. A single complex clamp can replace an assembly of simpler parts.
- Wall Thickness & Feature Size Considerations:
- Concept: Designing features (walls, ribs, pins) within the resolution limits and thermal constraints of the chosen AM process (e.g., L-PBF, EBM). Very thin walls can be difficult to print accurately and may warp, while overly thick sections can accumulate thermal stress.
- Application for Clamps: Ensuring walls are thick enough for structural integrity and printability (typically >0.5mm, process dependent) but avoiding unnecessarily bulky sections. Using hollow structures or internal lattices can reduce mass and thermal stress in thicker areas.
- Orientation Strategy:
- Concept: Deciding how the part will be oriented on the build platform during printing. This impacts support needs, surface finish on different faces, dimensional accuracy, and potentially anisotropic material properties.
- Application for Clamps: Critical clamping surfaces or interfaces might be oriented upwards for better surface finish. Orienting to minimize overhangs reduces support. The orientation can also influence residual stress build-up.
- Hole Design:
- Concept: Small holes printed vertically are generally accurate, while horizontal holes often require support structures or may print slightly out-of-round (often teardrop-shaped if unsupported).
- Application for Clamps: Designing holes slightly undersized if they require high precision, allowing for post-machining to final dimensions. Using self-supporting shapes like diamonds or teardrops for horizontal holes can sometimes eliminate the need for internal supports.
By embracing DfAM, engineers can design pipe clamps that are not only lighter and more functional but also easier and more economical to produce using metal 3D printing. Procurement managers benefit from sourcing parts optimized for the process, leading to potentially lower costs and improved performance metrics.
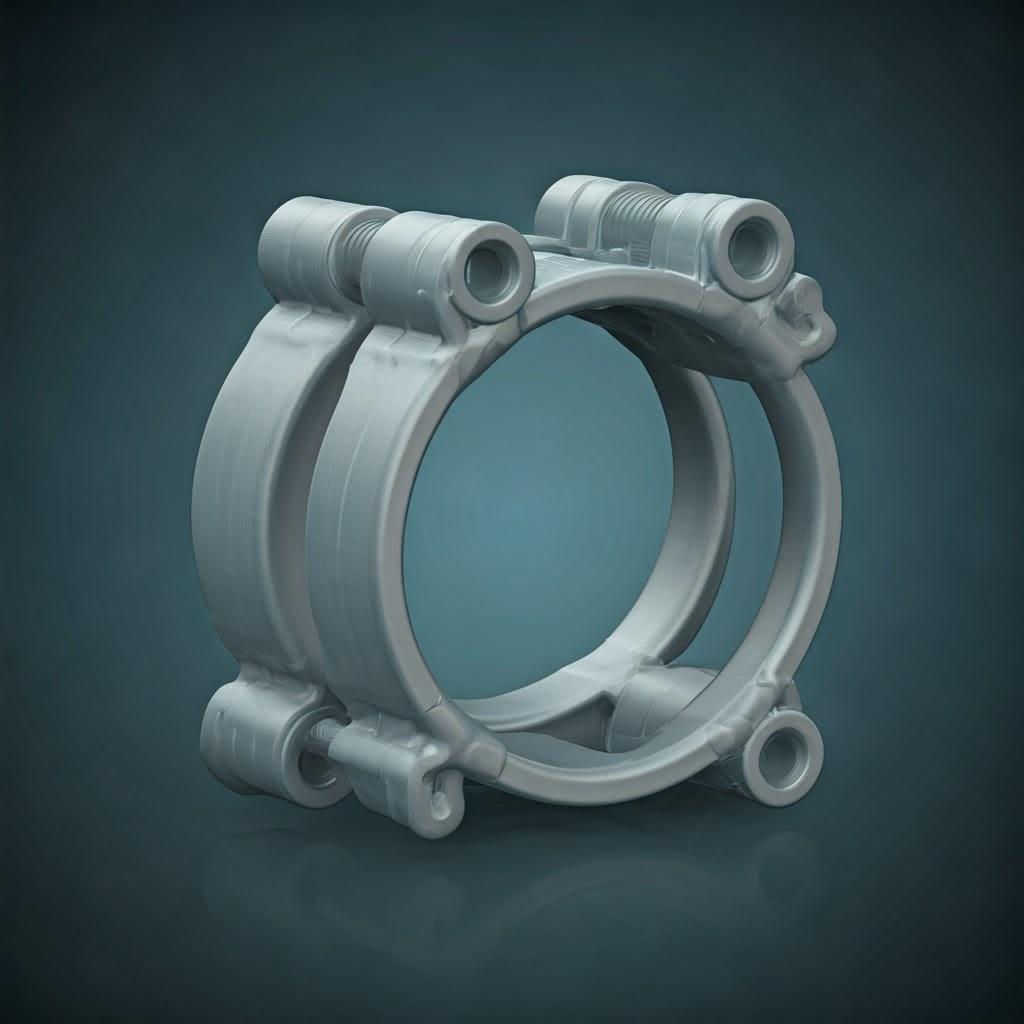
Achieving Precision: Tolerance, Surface Finish, and Dimensional Accuracy in AM Clamps
For aerospace components, precision is non-negotiable. Pipe clamps must securely fasten lines and harnesses without causing damage, often interfacing with other precision components. Understanding the achievable levels of tolerance, surface finish, and dimensional accuracy with metal additive manufacturing is critical for both design engineers and procurement managers evaluating potential suppliers. Companies like Met3dp invest heavily in state-of-the-art equipment and process control to deliver industry-leading accuracy and reliability for mission-critical parts.
Key Aspects of Precision in AM:
- Dokładność wymiarowa: Refers to how closely the final printed part conforms to the nominal dimensions specified in the CAD model.
- Typical Values: For well-controlled processes like Laser Powder Bed Fusion (L-PBF) or Electron Beam Melting (SEBM), typical dimensional accuracy is often in the range of ±0.1 mm to ±0.2 mm, or ±0.1% to ±0.2% of the dimension, whichever is greater. Tighter tolerances are possible on smaller features or with process optimization.
- Influencing Factors: Machine calibration, laser/electron beam spot size, layer thickness, thermal stability during the build, material properties, part geometry, and orientation significantly impact accuracy.
- Tolerances: The permissible range of variation for a given dimension.
- Achievable Tolerances: While standard AM tolerances might be sufficient for some clamp features, critical interfacing dimensions (e.g., the inner diameter that contacts the pipe, mounting hole locations) often require tighter tolerances than achievable “as-printed.” In such cases, features are typically designed slightly oversized or undersized to allow for post-machining (milling, drilling, reaming) to reach blueprint specifications, often achieving tolerances comparable to conventional machining (e.g., ±0.025 mm to ±0.05 mm).
- Surface Finish (Roughness): Describes the texture of the part’s surface, often quantified by the average roughness (Ra).
- As-Printed Values: Metal AM parts inherently have a rougher surface finish compared to machined parts due to the layer-wise fusion of powder particles.
- L-PBF: Typical Ra values range from 6 µm to 15 µm, depending on orientation (upward-facing surfaces are smoother, side walls are rougher) and parameters.
- EBM/SEBM: Generally produces rougher surfaces, often Ra > 20 µm, due to larger powder particles and higher energy input, but can have advantages in reducing residual stress.
- Poprawa wykończenia powierzchni: Post-processing steps like bead blasting, abrasive flow machining, tumbling, electro-polishing, or CNC machining are commonly used to achieve smoother surfaces (e.g., Ra < 3.2 µm or even < 0.8 µm) where required for sealing, fatigue life, or aesthetic reasons.
- As-Printed Values: Metal AM parts inherently have a rougher surface finish compared to machined parts due to the layer-wise fusion of powder particles.
Quality Control & Assurance:
Achieving and verifying precision requires robust quality control throughout the manufacturing process:
- Jakość proszku: Ensuring consistent powder morphology, size distribution, and chemistry.
- Process Monitoring: In-situ monitoring of the melt pool, layer deposition, and thermal conditions during the build.
- Post-Build Inspection: Dimensional verification using CMM (Coordinate Measuring Machines), 3D scanning, or traditional metrology tools.
- Material Testing: Validating mechanical properties through tensile testing on samples printed alongside the parts.
- Badania nieniszczące (NDT): Techniques like CT scanning can be used to inspect internal integrity and detect defects like porosity.
Procurement managers should ensure potential AM suppliers have strong quality management systems (e.g., AS9100 certification for aerospace) and can demonstrate their capability to meet the specified tolerances and surface finish requirements, including necessary post-processing and inspection steps.
Beyond the Print: Essential Post-Processing Steps for Aerospace Pipe Clamps
A common misconception about metal 3D printing is that parts come out of the machine ready for use. Especially in demanding industries like aerospace, extensive post-processing is almost always required to transform the “green” part into a functional, reliable component. These steps are crucial for achieving the desired mechanical properties, dimensional accuracy, surface finish, and overall integrity required for aerospace pipe clamps made from materials like AlSi10Mg or high-performance proszki metali like Ti-6Al-4V.
Common Post-Processing Stages:
- Ulga w stresie:
- Why: The rapid heating and cooling cycles inherent in powder bed fusion create significant internal stresses within the printed part. If not relieved, these stresses can cause warping during removal from the build plate or even premature failure in service.
- How: A thermal cycle (heating the part to a specific temperature below its annealing point and holding it) performed while the part is still attached to the build plate. This is a critical first step for almost all metal AM parts, especially titanium.
- Part Removal:
- Why: Parts are fused or sintered onto a metal build plate during printing.
- How: Typically done using wire EDM (Electrical Discharge Machining) or a bandsaw to carefully separate the printed components from the plate.
- Usunięcie konstrukcji wsporczej:
- Why: Supports are necessary to anchor the part and prevent deformation of overhanging features during printing but are not part of the final component.
- How: Can range from simple manual break-off for easily accessible supports to complex machining (milling, grinding) or EDM for internal or hard-to-reach supports. Careful removal is needed to avoid damaging the part surface. Design (DfAM) plays a huge role in simplifying this step.
- Heat Treatment (Solution Annealing, Aging, HIP):
- Why: To homogenize the microstructure, relieve residual stresses further, and achieve the desired final mechanical properties (strength, ductility, fatigue life).
- How:
- AlSi10Mg: Often requires a solution treatment followed by artificial aging (e.g., T6 temper) to maximize strength.
- Ti-6Al-4V: Typically requires annealing or stress relief cycles. Hot Isostatic Pressing (HIP) is frequently specified for critical aerospace parts. HIP involves applying high pressure and temperature simultaneously to close internal voids/porosity, significantly improving fatigue life and structural integrity.
- Wykończenie powierzchni:
- Why: To improve the as-printed surface roughness for functional requirements (e.g., sealing surfaces, reducing fatigue crack initiation points) or aesthetics.
- How: Typowe metody obejmują:
- Bead Blasting/Sandblasting: Creates a uniform matte finish, removes loose powder.
- Tumbling/Vibratory Finishing: Smoothes surfaces and edges using abrasive media.
- Abrasive Flow Machining (AFM): Forces abrasive putty through internal channels or across surfaces.
- Electropolishing: Electrochemical process to smooth surfaces, often used for corrosion resistance.
- CNC Machining: Used for achieving very smooth surfaces (Ra < 0.8 µm) on specific features.
- Machining for Critical Tolerances:
- Why: To achieve dimensional tolerances tighter than possible with the as-printed process.
- How: Using CNC milling, drilling, reaming, or turning to finish critical interfaces, hole diameters, or mating surfaces to the exact blueprint specifications.
- Cleaning & Inspection:
- Why: To remove any residual powder, machining fluids, or contaminants. Final inspection verifies dimensions and checks for defects.
- How: Ultrasonic cleaning, solvent wiping. Inspection methods include visual, CMM, NDT (CT, X-ray).
Procurement managers must factor the cost and time associated with these essential post-processing steps into their sourcing decisions. Working with a vertically integrated supplier or one with strong partnerships for these services ensures a streamlined workflow and parts that meet all aerospace requirements.
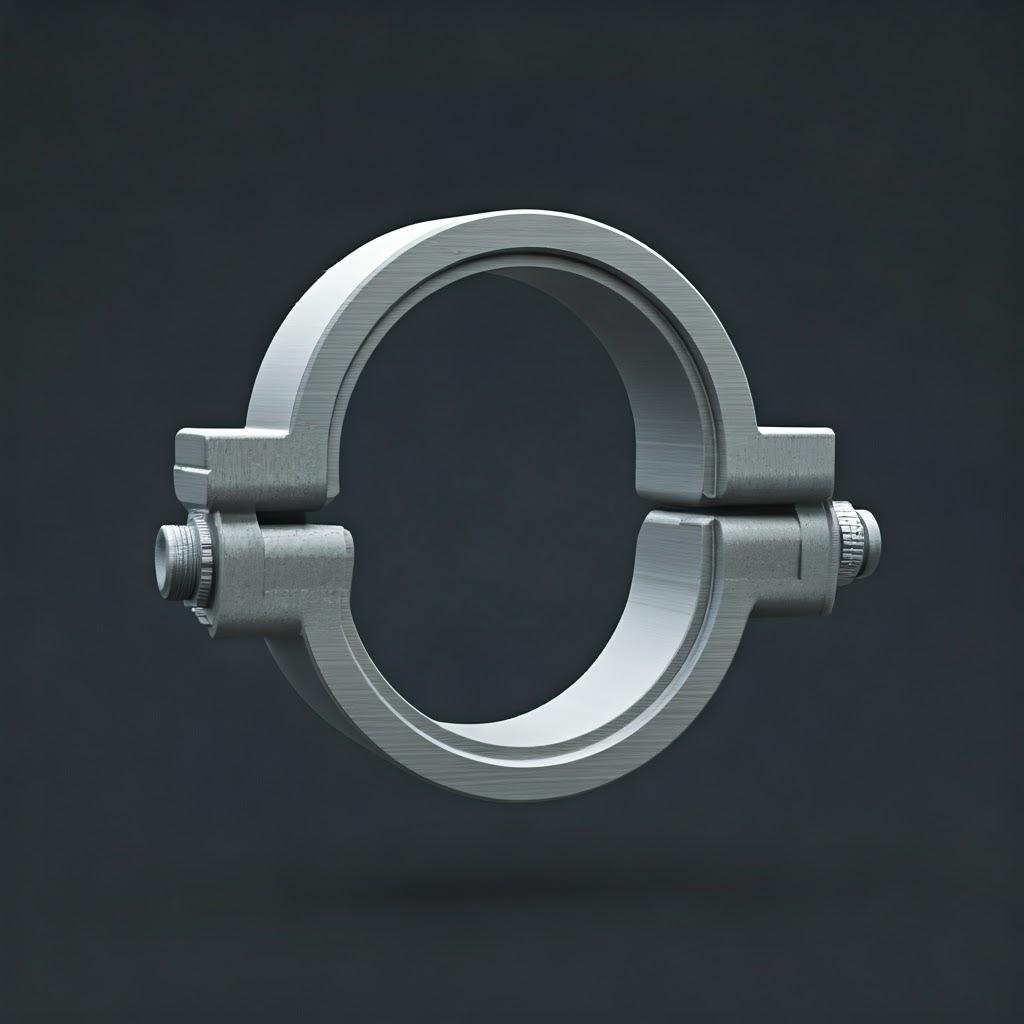
Navigating Challenges: Overcoming Potential Hurdles in 3D Printing Aerospace Clamps
While metal additive manufacturing offers significant advantages, it’s not without its challenges. Successfully producing high-quality, reliable aerospace pipe clamps requires expertise, careful process control, and an understanding of potential pitfalls. Awareness of these challenges allows engineers and procurement teams to work proactively with their AM partners to mitigate risks.
Common Challenges and Mitigation Strategies:
- Warping and Distortion:
- Cause: Uneven heating and cooling during printing lead to internal stresses that can deform the part, especially thin or large flat sections.
- Mitigation:
- DfAM: Designing parts with features that minimize stress concentration, avoiding large flat bases where possible.
- Orientation: Optimizing build orientation to manage thermal gradients.
- Support Strategy: Using appropriate support structures to anchor the part securely to the build plate.
- Process Parameters: Tuning laser/beam power, scan speed, and layer thickness to minimize thermal stress.
- Ulga w stresie: Performing immediate post-build stress relief cycles.
- Naprężenie szczątkowe:
- Cause: Similar to warping, inherent thermal cycles create internal stresses even if the part doesn’t visibly distort. High residual stress can reduce fatigue life and lead to cracking.
- Mitigation:
- Obróbka cieplna: Proper stress relief and annealing cycles are critical, especially for materials like Ti-6Al-4V.
- Kontrola procesu: Techniques like pre-heating the build platform (common in EBM/SEBM and some L-PBF systems) can significantly reduce thermal gradients and residual stress. Met3dp’s SEBM printers, for example, often operate at elevated temperatures beneficial for stress reduction in materials like titanium.
- Strategia skanowania: Using optimized laser/beam scanning patterns (e.g., island scanning) to distribute heat more evenly.
- Porowatość:
- Cause: Small internal voids within the material can arise from trapped gas, incomplete fusion between layers, or powder inconsistencies. Porosity degrades mechanical properties, particularly fatigue strength.
- Mitigation:
- Jakość proszku: Using high-quality, dry, spherical powder with controlled particle size distribution, like those produced by Met3dp’s advanced atomization processes.
- Optymalizacja parametrów procesu: Dialing in energy density (power, speed, hatch spacing) to ensure complete melting and fusion.
- Shielding Gas: Maintaining a high-purity inert gas atmosphere (Argon or Nitrogen) in the build chamber (for L-PBF) to prevent oxidation and gas entrapment.
- HIP: Hot Isostatic Pressing is highly effective at closing internal gas porosity for critical components.
- Support Removal Difficulties:
- Cause: Complex internal channels or delicate features can make removing support structures challenging without damaging the part. Supports made of the same material can be strongly bonded.
- Mitigation:
- DfAM: Designing for minimal support, using self-supporting angles, and optimizing orientation.
- Specialized Tools: Using appropriate tools, potentially including micro-machining or EDM for delicate areas.
- Soluble/Easier-to-Remove Supports: Research is ongoing, but less common for structural metal AM currently.
- Experienced Technicians: Skilled labor is essential for careful manual support removal.
- Chropowatość powierzchni:
- Cause: Inherent nature of layer-wise fusion of powder particles.
- Mitigation: Primarily addressed through post-processing (blasting, polishing, machining) as described previously. Selecting the appropriate AM process (e.g., L-PBF often yields finer finish than EBM) can be a factor if as-built roughness is critical.
- Consistency and Repeatability:
- Cause: Variations in powder batches, machine calibration drift, or slight parameter changes can affect part properties.
- Mitigation:
- Robust Quality Management: Implementing strict process controls, regular machine calibration, and consistent powder management protocols (e.g., sieving, drying).
- Process Monitoring: Using sensors and data logging to track build conditions.
- Standaryzacja: Adhering to industry standards (e.g., SAE AMS specs for AM materials and processes).
Successfully navigating these challenges requires a combination of robust DfAM practices, optimized and validated process parameters, high-quality materials, necessary post-processing, and rigorous quality control. Partnering with an experienced metal AM provider with a deep understanding of materials science and process engineering is key to obtaining reliable, high-performance aerospace clamps.
Supplier Selection Strategy: Choosing the Right Metal AM Partner for Aerospace Components
Selecting the right manufacturing partner is a critical decision for aerospace companies, directly impacting component quality, supply chain reliability, and compliance. When sourcing 3D printed metal pipe clamps, procurement managers and engineers need to evaluate potential suppliers based on criteria specific to both additive manufacturing and the stringent demands of the aerospace industry. Making an informed choice ensures access to technical expertise, consistent quality, and reliable delivery. Considering choosing the right metal 3D printing service provider involves looking beyond just price.
Key Criteria for Evaluating Metal AM Suppliers:
- Aerospace Certifications & Quality Management:
- Requirement: Look for suppliers holding relevant certifications, primarily AS9100, which is the standard for aerospace quality management systems. ISO 9001 is a baseline, but AS9100 demonstrates specific commitment and capability for the aerospace sector.
- Why it Matters: Ensures the provider has robust processes for traceability, process control, risk management, and continuous improvement, mandated by the industry.
- Material Expertise & Handling:
- Requirement: Demonstrated experience printing with the required aerospace-grade materials (e.g., AlSi10Mg, Ti-6Al-4V). Crucially, they must have stringent procedures for powder handling, storage, testing, and traceability to prevent contamination and ensure material consistency.
- Why it Matters: Material properties are fundamental to component performance. Proper powder management, like that employed by Met3dp with its high-quality spherical powders, is essential for achieving desired density, strength, and fatigue life. Ask about their powder sourcing and batch control.
- Technology & Equipment:
- Requirement: Possesses the appropriate AM technology (e.g., Laser Powder Bed Fusion – L-PBF, Selective Electron Beam Melting – SEBM) suitable for the material and application. Evaluate the quality, maintenance, and calibration standards of their printers.
- Why it Matters: Different technologies have different strengths (e.g., SEBM for stress-prone titanium parts, L-PBF for finer features). Suppliers like Met3dp, offering their own advanced SEBM printers known for accuracy and reliability, demonstrate a deep understanding of the technology.
- Post-Processing Capabilities:
- Requirement: Ability to perform or manage the necessary post-processing steps (stress relief, heat treatment/HIP, support removal, machining, surface finishing, NDT). Evaluate whether these are done in-house or through qualified partners.
- Why it Matters: Post-processing is integral to achieving final part specifications. A supplier managing the entire workflow ensures better control, accountability, and potentially shorter lead times.
- Technical Expertise & Engineering Support:
- Requirement: Access to experienced engineers and metallurgists who understand DfAM principles, material science, and the nuances of printing aerospace components. They should be able to provide design feedback and collaborate on optimization.
- Why it Matters: Partnership goes beyond just printing. Expert support can help optimize designs for better performance, reduced cost, and improved printability. Met3dp, with decades of collective expertise, exemplifies this capability.
- Track Record & Experience:
- Requirement: Proven experience manufacturing parts for aerospace or similarly demanding industries. Case studies, references, and examples of past projects are valuable indicators.
- Why it Matters: Demonstrates understanding of industry expectations, quality requirements, and the ability to successfully deliver complex projects.
- Capacity & Scalability:
- Requirement: Sufficient machine capacity to handle prototyping needs as well as potential volume production or wholesale orders. Assess their ability to scale production if required.
- Why it Matters: Ensures timely delivery and the ability to support programs as they transition from development to production phases.
Supplier Evaluation Checklist:
Criterion | Key Questions to Ask | Importance (Aerospace) |
---|---|---|
Certyfikaty | Are you AS9100 certified? Can you provide the certificate? | Krytyczny |
Material Control | How do you manage powder traceability, testing, and handling? What are your sources? | Krytyczny |
Technology Fit | Which AM process (L-PBF/SEBM) do you recommend and why? What are your machine specs? | Wysoki |
Przetwarzanie końcowe | What steps are done in-house vs. outsourced? How do you qualify partners? | Wysoki |
Wsparcie techniczne | Do you offer DfAM support? Who are the technical points of contact? | Wysoki |
Doświadczenie | Can you share examples of similar aerospace parts you’ve produced? | Wysoki |
Quality System | Can you describe your inspection process? What NDT methods do you use? | Krytyczny |
Capacity & Lead Time | What is your typical lead time for this type of part? What is your production capacity? | Średni do wysokiego |
Struktura kosztów | Can you provide a detailed quote? What are the cost drivers? | Średni |
Export to Sheets
Thorough supplier vetting is essential for mitigating risks and ensuring the success of incorporating 3D printed pipe clamps into high-performance aircraft systems.
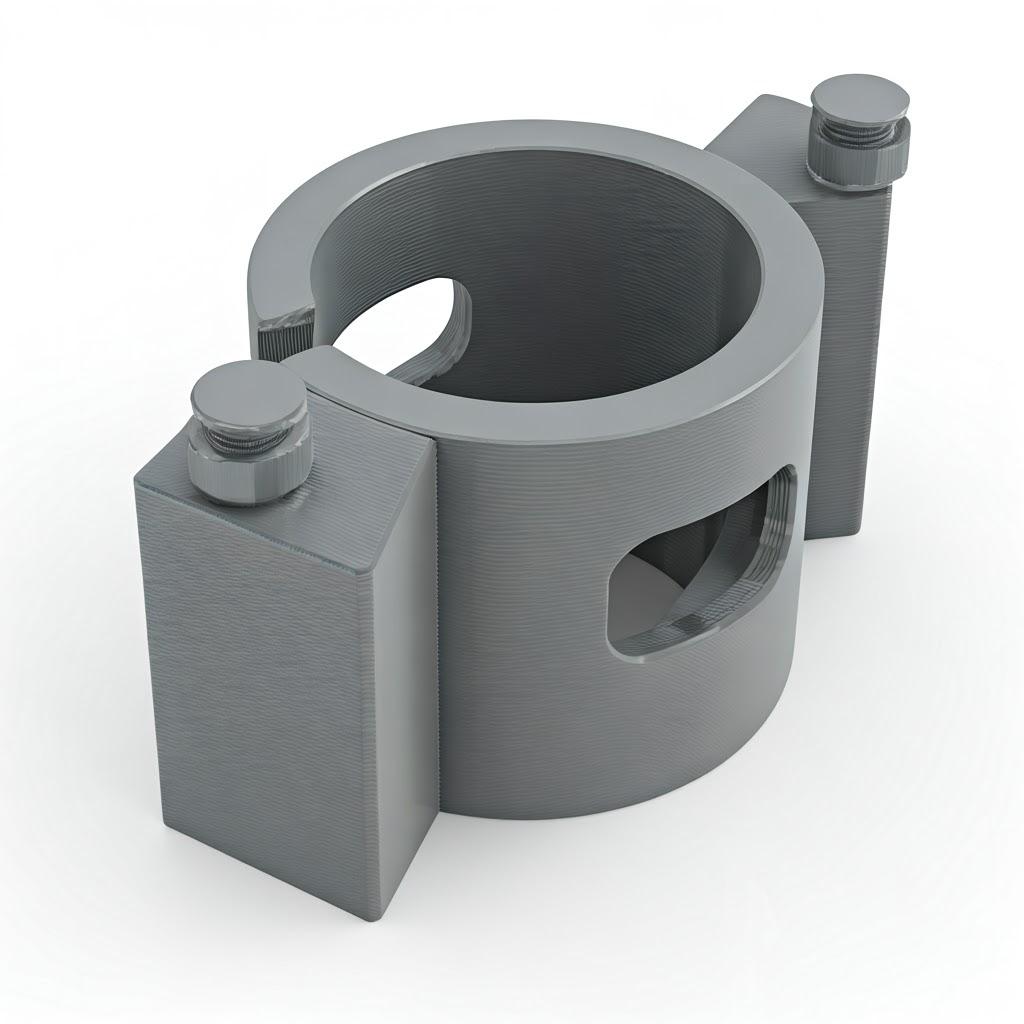
Understanding Investment: Cost Factors and Lead Times for 3D Printed Pipe Clamps
While performance benefits often drive the adoption of AM, understanding the cost structure and typical lead times is crucial for procurement managers and project planning. Pricing for 3D printed metal parts is influenced by a different set of factors compared to traditional manufacturing.
Key Cost Drivers:
- Material Type & Consumption:
- Factor: High-performance aerospace powders like Ti-6Al-4V are significantly more expensive than AlSi10Mg or conventional materials. The total volume of material consumed (including supports) directly impacts cost.
- Uderzenie: Material choice is often the largest single cost component. Efficient design (DfAM, topology optimization) minimizing volume and supports is key.
- Part Complexity & Volume:
- Factor: While AM handles complexity well, highly intricate designs or large solid volumes increase print time. The bounding box size (how much space it takes on the build plate) also matters.
- Uderzenie: Larger parts or those requiring extensive internal supports take longer to print, increasing machine time costs.
- Machine Time:
- Factor: Calculated based on the hours required to print the part(s). This includes setup, the actual layer-by-layer printing, and cooldown.
- Uderzenie: Longer print times tie up expensive machinery, directly adding to the cost. Optimizing orientation and nesting multiple parts on a build plate can improve efficiency for volume production.
- Struktury wsparcia:
- Factor: The amount and complexity of support structures needed. Supports consume material and add significant time/cost to post-processing for removal.
- Uderzenie: Designs minimized for support requirements (DfAM) are inherently more cost-effective.
- Wymagania dotyczące przetwarzania końcowego:
- Factor: The number and type of steps needed after printing (stress relief, heat treatment, HIP, machining, finishing). Labor-intensive steps like manual support removal or high-precision machining add significant cost.
- Uderzenie: Critical aerospace parts often require extensive post-processing (e.g., HIP for titanium), which must be factored in. Specifying only necessary finishing levels helps manage cost.
- Quality Assurance & Inspection:
- Factor: The level of inspection required (standard dimensional checks vs. CMM, NDT like CT scanning).
- Uderzenie: Higher levels of verification and documentation required for critical aerospace components add to the overall cost but are essential for safety and compliance.
- Order Volume (Wholesale Pricing):
- Factor: Printing multiple copies of a part in a single build (nesting) or across consecutive builds allows for economies of scale.
- Uderzenie: Per-part costs generally decrease with higher quantities due to efficiencies in setup, machine utilization, and bulk post-processing. Suppliers may offer wholesale pricing tiers.
Lead Time Estimation:
Lead time is the total duration from order placement to part delivery. It comprises several stages:
- Pre-Processing (1-3 days): Order confirmation, CAD file check, build preparation, scheduling.
- Printing (1-5+ days): Depends heavily on part size, complexity, quantity, and machine availability. Large or complex builds can take several days.
- Post-Processing (2-10+ days): Highly variable based on required steps. Heat treatment cycles (especially HIP) can take multiple days alone. Machining and complex finishing add further time.
- Quality Control & Shipping (1-3 days): Final inspection, documentation, packaging, and transit.
Typical Lead Time Range: For aerospace-grade metal AM parts requiring significant post-processing, lead times of 2 to 4 weeks are common, but this can vary significantly based on the factors above. Rush services may be available at a premium cost. Clear communication with the supplier is key to managing expectations.
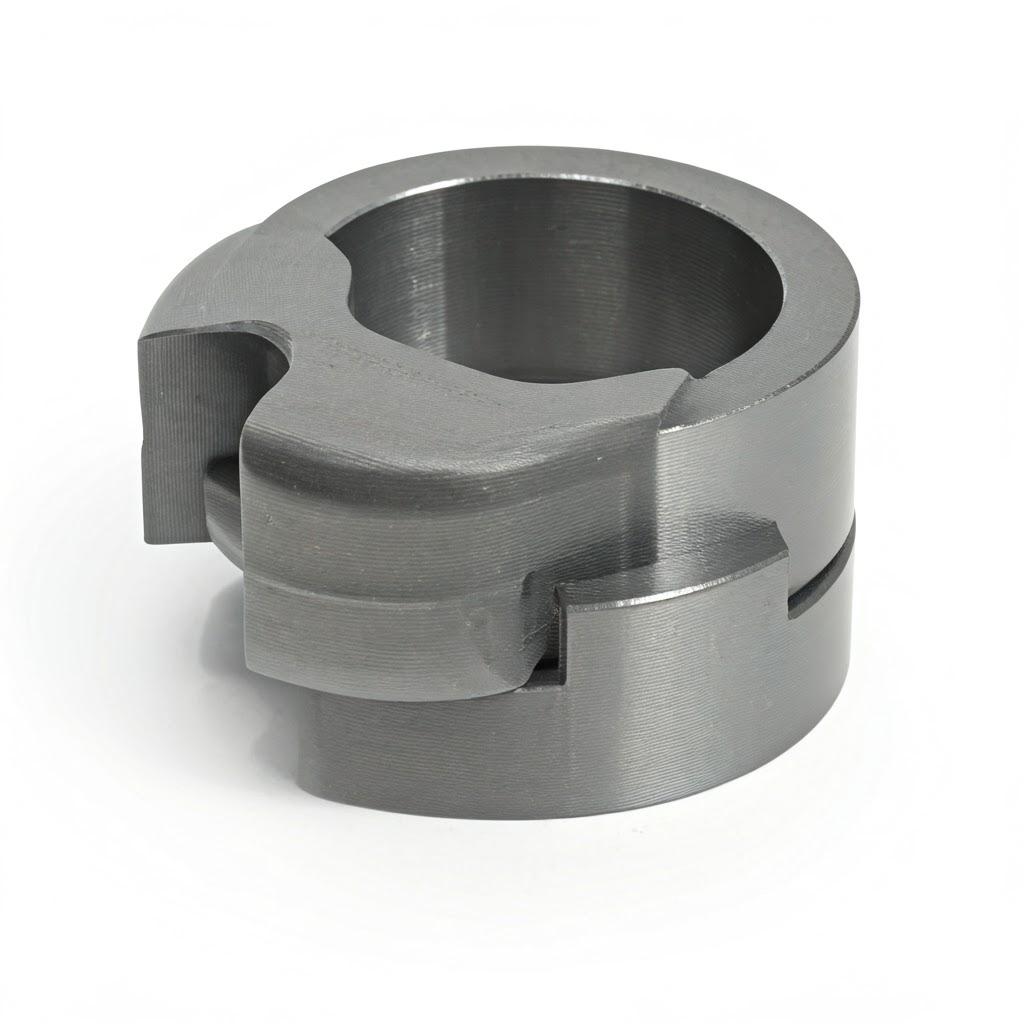
Frequently Asked Questions (FAQ) about 3D Printed Aerospace Pipe Clamps
Here are answers to some common questions engineers and procurement managers have about utilizing metal AM for aerospace pipe clamps:
- Q: Are 3D printed metal clamps as strong and reliable as traditionally manufactured ones?
- A: Yes, when produced using qualified processes, aerospace-grade materials (like Ti-6Al-4V or AlSi10Mg), and appropriate post-processing (including heat treatment and potentially HIP), 3D printed clamps can meet or even exceed the mechanical properties (strength, fatigue life, durability) of cast or machined equivalents. Process validation, material testing, and adherence to aerospace standards are crucial to ensure reliability.
- Q: How does the cost of 3D printed pipe clamps compare to conventionally manufactured ones?
- A: For simple, high-volume clamps, traditional methods like stamping or casting may still be cheaper per part due to established economies of scale. However, AM becomes highly cost-competitive or even advantageous for:
- Złożone geometrie: Where machining would be very difficult or require multiple setups.
- Konsolidacja części: Where one printed part replaces an assembly.
- Lightweight designs: Where topology optimization significantly reduces material usage (especially for expensive materials like titanium).
- Low-to-medium volumes: Where tooling costs for traditional methods are prohibitive.
- Rapid prototyping & MRO: Where speed and avoidance of tooling are paramount.
- A total cost of ownership analysis, considering weight savings and assembly benefits, often favors AM for specialized aerospace clamps.
- A: For simple, high-volume clamps, traditional methods like stamping or casting may still be cheaper per part due to established economies of scale. However, AM becomes highly cost-competitive or even advantageous for:
- Q: What is the process for certifying 3D printed parts for flight?
- A: Certification follows rigorous aerospace protocols (e.g., FAA, EASA guidelines). It typically involves qualifying the specific machine, material batch, AM process parameters, and post-processing steps used. This includes extensive material testing (tensile, fatigue, microstructure analysis) on witness coupons printed alongside the parts, process validation, non-destructive testing (NDT) of the final components, and comprehensive documentation demonstrating compliance with design specifications and airworthiness requirements. Partnering with an AS9100 certified supplier experienced in aerospace qualification is essential.
- Q: Can existing clamp designs be directly 3D printed?
- A: While possible, it’s often not optimal. Directly printing a design created for machining or casting usually fails to leverage AM’s benefits (like lightweighting or consolidation) and may even introduce printing challenges (e.g., requiring excessive support). Redesigning the clamp using DfAM principles is highly recommended to maximize performance, reduce weight, and optimize for printability and cost-effectiveness.
Conclusion: Elevating Aircraft Performance and Efficiency with Additively Manufactured Clamps
The adoption of metal additive manufacturing for components like pipe clamps marks a significant step forward in aerospace engineering and supply chain strategy. By leveraging the unique capabilities of 3D printing – unparalleled design freedom, the potential for drastic weight reduction through topology optimization, and the ability to consolidate multiple parts into a single, complex component – aerospace companies can enhance aircraft performance, improve fuel efficiency, and simplify assembly processes. The use of high-performance materials like AlSi10Mg and Ti-6Al-4V ensures these components meet the rigorous demands of flight environments.
While challenges exist, they are overcome through careful design (DfAM), meticulous process control, essential post-processing, and rigorous quality assurance, often facilitated by partnering with expert providers. Choosing the right AM supplier, one with proven aerospace experience, robust quality systems like AS9100 certification, and deep material and process knowledge, is paramount to success.
Companies like Met3dp are at the forefront of this transformation, providing not only advanced SEBM printing systems known for accuracy and reliability but also high-quality, specialized metal powders manufactured using cutting-edge atomization techniques. Their comprehensive solutions and expertise empower aerospace manufacturers to integrate additive manufacturing effectively. As the technology matures and standardization progresses, 3D printed pipe clamps and similar components will become increasingly integral to building the next generation of lighter, more efficient, and higher-performing aircraft. We invite you to explore how Met3dp’s capabilities can power your organization’s additive manufacturing goals.
Udostępnij
MET3DP Technology Co., LTD jest wiodącym dostawcą rozwiązań w zakresie produkcji addytywnej z siedzibą w Qingdao w Chinach. Nasza firma specjalizuje się w sprzęcie do druku 3D i wysokowydajnych proszkach metali do zastosowań przemysłowych.
Zapytaj o najlepszą cenę i spersonalizowane rozwiązanie dla Twojej firmy!
Powiązane artykuły
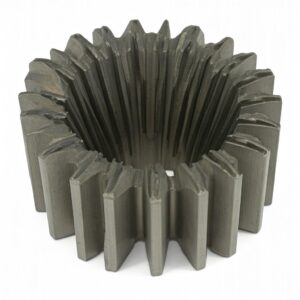
Wysokowydajne segmenty łopatek dysz: Rewolucja w wydajności turbin dzięki drukowi 3D w metalu
Czytaj więcej "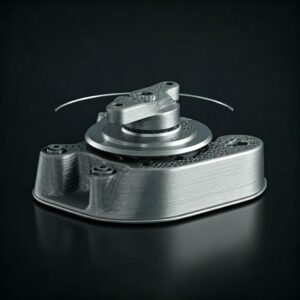
Drukowane w 3D mocowania dla samochodowych czujników radarowych: Precyzja i wydajność
Czytaj więcej "Informacje o Met3DP
Ostatnia aktualizacja
Nasz produkt
KONTAKT
Masz pytania? Wyślij nam wiadomość teraz! Po otrzymaniu wiadomości obsłużymy Twoją prośbę całym zespołem.
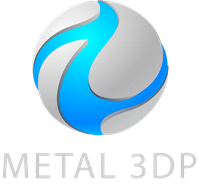
Proszki metali do druku 3D i produkcji addytywnej