Linkage Arms 3D Printed for Dynamic Load Resistance
Spis treści
Introduction: The Critical Role of High-Stress Linkage Arms in Dynamic Systems
Linkage arms are fundamental components in a vast array of mechanical systems, acting as the crucial connectors that transmit force and motion between different parts of an assembly. From the intricate mechanisms within robotic arms to the robust underpinnings of aircraft landing gear and automotive suspensions, these components are ubiquitous. However, their function often places them under severe operational duress, particularly in dynamic systems where loads fluctuate rapidly and unpredictably. These dynamic loads introduce complex challenges, including high cycle fatigue, significant stress concentrations, and vibration-induced wear. Failure in a high-stress linkage arm can have catastrophic consequences, leading to system breakdown, costly repairs, and potential safety hazards.
Traditionally, engineers have relied on methods like casting, forging, or machining from solid billets to produce these critical parts. While effective, these methods often impose limitations on design complexity, can be material-intensive, and may involve long lead times, especially for custom or low-volume production runs. As industries like aerospace, automotive, medical, and industrial manufacturing push the boundaries of performance, efficiency, and lightweighting, the demand for more advanced manufacturing solutions for components like high-stress linkage arms has intensified.
This is where metal additive manufacturing (AM), commonly known as metal Drukowanie 3D, emerges as a transformative technology. Metal AM offers unparalleled design freedom, enabling the creation of highly optimized, complex geometries that are difficult or impossible to achieve through conventional means. It allows for the production of linkage arms with enhanced strength-to-weight ratios, integrated features, and potentially superior fatigue resistance tailored to specific dynamic load conditions. Companies like Met3dp, a leader in metal additive manufacturing solutions, are at forefront of leveraging this technology to produce next-generation, high-performance engineering components. By combining advanced printing technologies like Selective Electron Beam Melting (SEBM) with high-quality, specialized metal powders, Met3dp empowers engineers and procurement managers to rethink how critical components like high-stress linkage arms are designed and manufactured, unlocking new levels of performance and reliability in dynamic systems. This article delves into the specifics of using metal 3D printing for high-stress linkage arms, exploring applications, material choices, design considerations, and the benefits of partnering with an expert provider.
Applications: Where are 3D Printed High-Stress Linkage Arms Used?
The versatility and performance advantages of metal additive manufacturing make it suitable for producing high-stress linkage arms across a diverse spectrum of demanding industries. Procurement managers and engineers seeking reliable component suppliers for challenging applications are increasingly turning to AM providers for custom and series production parts. Here are some key areas where 3D printed linkage arms are making a significant impact:
- Aerospace:
- Zastosowania: Actuation systems (flap linkages, control surface connectors), landing gear components (drag braces, retraction linkages), engine mounts, satellite mechanisms.
- Korzyści: Significant weight reduction is paramount in aerospace. AM allows for topology optimization, creating lightweight yet incredibly strong linkage arms that meet stringent flight certification requirements. Part consolidation reduces assembly complexity and potential failure points. The ability to use high-performance alloys tailored for extreme temperatures and fatigue resistance is critical.
- B2B Focus: Sourcing flight-certified linkage components, reliable aerospace linkage parts suppliers, custom actuation system manufacturing, bulk supply for MRO (Maintenance, Repair, Overhaul).
- Motoryzacja:
- Zastosowania: Suspension systems (control arms, stabilizer bar links), steering linkages, engine and powertrain components, performance vehicle upgrades.
- Korzyści: Enhanced vehicle dynamics through lighter and stiffer suspension components. Rapid prototyping allows for faster design iteration and testing of new suspension geometries. Customization for niche or high-performance vehicles becomes economically viable. Improved fatigue life under constant road-induced vibrations and impacts.
- B2B Focus: Automotive suspension components wholesale, performance parts manufacturing partner, custom steering linkage supplier, rapid prototyping services for automotive OEMs, tier-1 supplier collaboration.
- Robotics and Automation:
- Zastosowania: Robotic arm joints and linkages, end-effector connectors, linkages in automated assembly lines, gripper mechanisms.
- Korzyści: Reduced inertia in robotic arms leads to faster movements, higher precision, and lower energy consumption. Complex geometries can integrate cabling or sensor mounts directly into the linkage arm. High strength is needed to handle payload and repetitive motion stresses. Customization allows tailoring arms for specific tasks or space constraints.
- B2B Focus: Industrial robot component manufacturer, custom robotic arm linkage supplier, automation systems integrator parts sourcing, high-precision linkage procurement.
- Industrial Machinery and Heavy Equipment:
- Zastosowania: Linkages in hydraulic actuators, connectors in construction equipment arms, linkages in manufacturing presses and tooling, components in agricultural machinery.
- Korzyści: High strength and durability are essential for longevity in harsh operating environments. AM enables the creation of replacement parts for legacy equipment where original tooling no longer exists (digital warehousing). Part consolidation can simplify complex assemblies. Ability to use wear-resistant materials extends component life.
- B2B Focus: Heavy equipment parts supplier, industrial machinery linkage manufacturer, custom actuator component production, MRO solutions for industrial equipment, bulk linkage arm orders for OEMs.
- Medyczne:
- Zastosowania: Linkages in surgical robots, prosthetic limbs, external fixation devices, specialized instrumentation.
- Korzyści: Biocompatible materials can be used. High degree of customization for patient-specific devices. Lightweighting improves user comfort for prosthetics. Complex, miniaturized linkages for minimally invasive surgical tools.
- B2B Focus: Medical device component manufacturing, surgical robotics parts supplier, custom prosthetic linkage production, sourcing biocompatible metal AM parts.
Across these diverse fields, metal 3D printing provides a powerful toolset for creating high-stress linkage arms that meet and exceed the demands of dynamic load environments, offering tangible benefits in performance, weight, customization, and often, lead time compared to traditional approaches. Sourcing these advanced components requires partnership with knowledgeable B2B suppliers equipped with the right technology and material expertise.
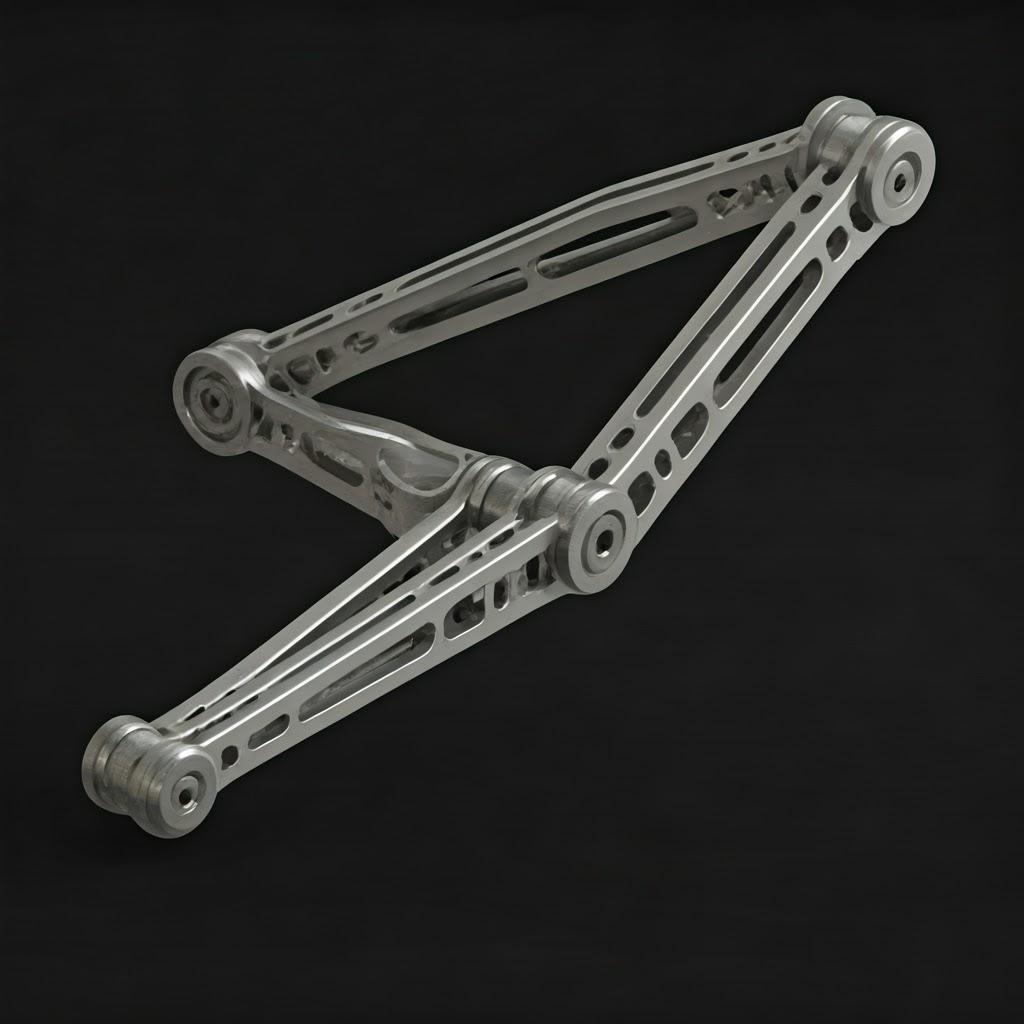
Why Choose Metal 3D Printing for Linkage Arms Subject to Dynamic Loads?
While traditional manufacturing methods have served industries for decades, metal additive manufacturing presents compelling advantages, particularly for components like high-stress linkage arms operating under dynamic loads. Understanding these benefits is crucial for engineers designing next-generation systems and procurement managers seeking optimal sourcing strategies.
Limitations of Traditional Manufacturing for Complex Linkages:
- Casting/Forging: While excellent for high-volume production of simpler shapes, achieving complex internal features or highly optimized geometries is difficult and often requires expensive tooling. Material properties can sometimes be less uniform than desired, and secondary machining is almost always required for precision features.
- CNC Machining: Offers high precision but can be incredibly wasteful, especially when starting from large billets of expensive high-strength materials. Complex geometries, particularly those with deep pockets or internal channels, can lead to long machining times, tool access limitations, and high costs. Design is often constrained by manufacturability limitations (e.g., tool reach, undercuts).
Advantages of Metal Additive Manufacturing (AM):
Cecha | Advantage for High-Stress Linkage Arms | Relevance to B2B Sourcing |
---|---|---|
Swoboda projektowania | Enables complex geometries, topology optimization for ideal load paths, internal cooling channels, and lattice structures for lightweighting. | Access to custom linkage arm production, unique design solutions unavailable elsewhere. |
Topology Optimization | Material is placed only where structurally needed, drastically reducing weight while maintaining or increasing strength and stiffness. | Optimized performance components, competitive advantage through lightweighting (e.g., aerospace, automotive). |
Konsolidacja części | Multiple components of a linkage assembly can potentially be printed as a single, monolithic part. | Reduced assembly time, lower part count, improved reliability, simplified supply chain. |
Szybkie prototypowanie | Quickly iterate designs and produce functional prototypes for testing dynamic load response and fit/form/function validation. | Faster time-to-market for new products, reduced development costs, design risk mitigation. |
Wydajność materiałowa | Additive process uses primarily the material needed for the part, minimizing waste compared to subtractive machining. | Cost savings on expensive high-performance alloys, sustainable manufacturing approach. |
Zwiększona wydajność | Fine control over the printing process can influence microstructure, potentially leading to improved fatigue life and specific material properties. | High-performance linkage components, improved product lifespan and reliability. |
Customization & Low Volume | Economically viable to produce unique or low-volume batches without the high tooling costs of casting or forging. | Supplier for niche applications, custom machinery parts, replacement parts on demand. |
Materiały zaawansowane | Ability to work with specialized alloys (like 17-4PH, M300) optimized for strength, toughness, and corrosion resistance. | Access to components made from materials ideal for extreme operating conditions. |
Export to Sheets
Met3dp leverages advanced druk 3D z metalu technologies, such as Selective Electron Beam Melting (SEBM), known for producing parts with low residual stress and excellent material properties, making it particularly suitable for high-stress applications. By combining these technological capabilities with deep materials science knowledge, Met3dp helps clients unlock the full potential of AM for their critical linkage arm components. Choosing metal AM is not just about adopting a new manufacturing method; it’s about enabling superior design, enhancing performance under demanding dynamic loads, and optimizing the entire product lifecycle from concept to production and procurement.
Material Focus: 17-4PH Stainless Steel and M300 Maraging Steel for Peak Performance
Selecting the right material is paramount for linkage arms subjected to high stress and dynamic loading. The material must possess a combination of high strength, toughness, fatigue resistance, and potentially corrosion resistance, depending on the operating environment. Metal 3D printing offers the ability to work with advanced alloys that meet these demanding criteria. For high-stress linkage arms, two standout candidates often recommended are 17-4PH Precipitation Hardening (PH) Stainless Steel and M300 Maraging Steel.
Stal nierdzewna 17-4PH:
- Przegląd: A martensitic, precipitation-hardening stainless steel offering an excellent combination of high strength, good corrosion resistance (comparable to 304 stainless steel in many environments), good toughness, and weldability. Its properties can be tailored through heat treatment (aging).
- Key Properties (Heat Treated):
- High Yield Strength and Tensile Strength
- Dobra odporność na zmęczenie materiału
- Umiarkowana twardość
- Good Corrosion Resistance, especially against atmospheric corrosion and many chemical environments.
- Operational up to moderate temperatures (around $315^{\circ}$C or $600^{\circ}$F).
- Why it Matters for Linkage Arms: Its balanced properties make it a versatile workhorse. The high strength handles significant loads, while good toughness prevents brittle fracture under impact or dynamic conditions. Corrosion resistance is vital for components exposed to the elements or industrial fluids. Heat treatability allows fine-tuning properties post-printing.
- AM Considerations: 17-4PH is well-established in powder bed fusion processes. Achieving optimal properties requires careful control of print parameters and, critically, appropriate post-print heat treatment (solution annealing followed by aging).
M300 Maraging Steel:
- Przegląd: An ultra-high-strength steel belonging to the maraging family. These steels achieve their exceptional strength through the precipitation of intermetallic compounds during a simple aging heat treatment, rather than relying on carbon like traditional steels. M300 offers superior strength and hardness compared to 17-4PH, coupled with excellent toughness.
- Key Properties (Heat Treated):
- Very High Yield Strength and Tensile Strength (often exceeding 2000 MPa or 290 ksi)
- Wyjątkowa twardość
- Good Toughness and Ductility for its strength level
- Good Dimensional Stability during heat treatment
- Moderate Corrosion Resistance (generally requires protective coating for harsh environments).
- Why it Matters for Linkage Arms: Ideal for the most demanding applications where maximum strength, stiffness, and wear resistance are critical. Suitable for highly loaded joints, aerospace components, or performance racing parts where minimizing size and weight while maximizing load capacity is essential. Its toughness mitigates the risk of fracture despite its ultra-high strength.
- AM Considerations: M300 powder requires precise printing parameters to achieve dense, defect-free parts. The aging heat treatment is relatively simple but crucial for developing the final properties. Due to its lower chromium content compared to stainless steels, corrosion protection might be necessary depending on the application.
Material Comparison for High-Stress Linkage Arms:
Nieruchomość | Stal nierdzewna 17-4PH | M300 Maraging Steel | Selection Guidance |
---|---|---|---|
Siła | Wysoki | Ultra-High | Choose M300 for highest load capacity or minimal size/weight requirements. |
Wytrzymałość | Dobry | Good (for its strength level) | Both offer good resistance to fracture under dynamic loads. |
Twardość | Umiarkowany | Wyjątkowy | M300 offers superior wear resistance. |
Odporność na korozję | Dobry | Moderate (requires protection) | 17-4PH is better for corrosive environments without coating. |
Obróbka cieplna | Solution Anneal + Aging | Starzenie się | Both require heat treatment; M300’s is simpler but dimensional stability is key. |
Koszt | Generally Lower | Generally Higher | Cost-performance trade-off based on application requirements. |
Export to Sheets
Met3dp’s Material Advantage:
The performance of 3D printed parts relies heavily on the quality of the metal powder feedstock. Met3dp utilizes industry-leading powder manufacturing techniques, including Gas Atomization and Plasma Rotating Electrode Process (PREP) technologies. These advanced methods produce metal powders with:
- Wysoka sferyczność: Ensures excellent powder flowability and uniform spreading during the printing process.
- Low Porosity: Contributes to dense, high-integrity final parts.
- Controlled Particle Size Distribution (PSD): Optimized for specific AM processes like SEBM and LPBF, ensuring consistent melting and layer formation.
- Wysoka czystość: Minimizes contaminants that could compromise mechanical properties.
By manufacturing high-quality 17-4PH, M300, and other advanced alloy powders (including Ti-based alloys, CoCrMo, superalloys), Met3dp ensures that the linkage arms printed using their materials possess superior mechanical properties and consistency, critical for reliable performance under dynamic loads. Choosing the right material is a crucial step, and partnering with a provider like Met3dp, who possesses both powder expertise and printing proficiency, ensures the best foundation for high-stress linkage arm production.
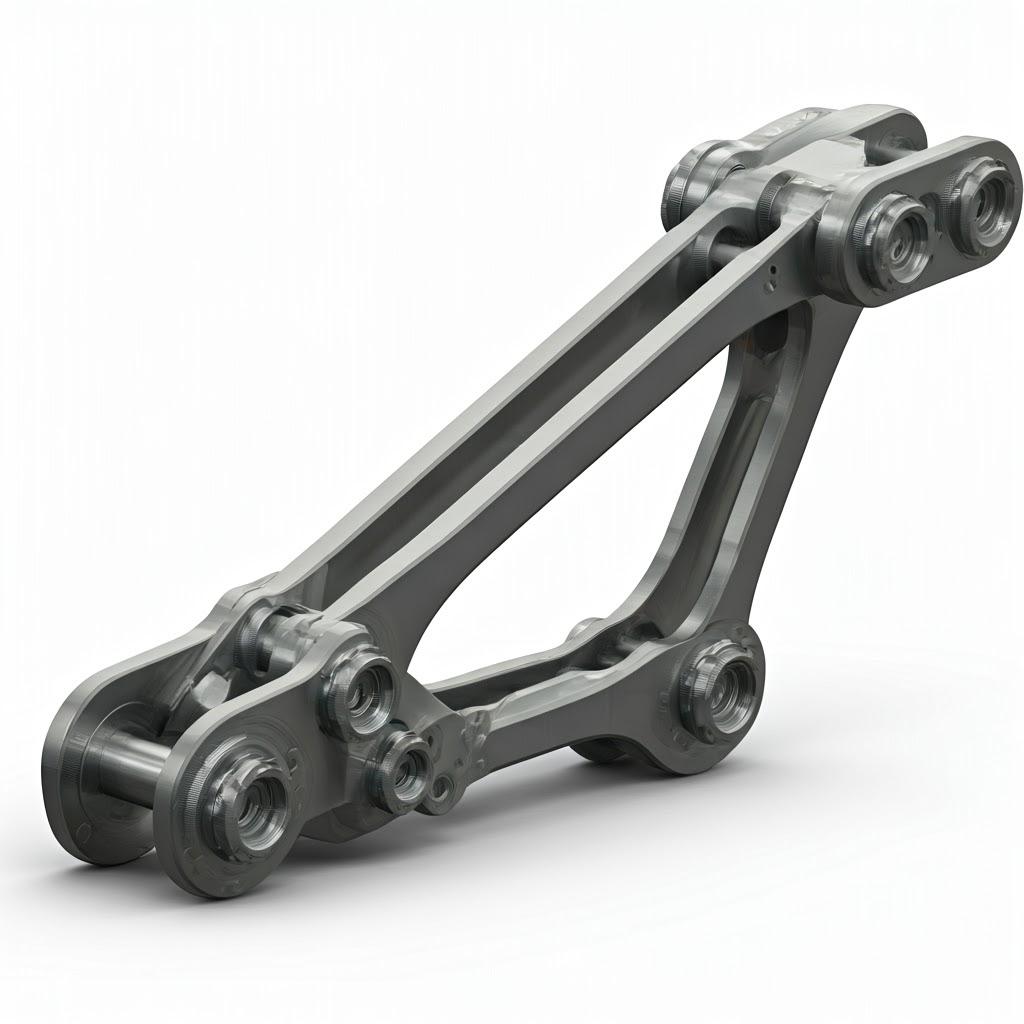
Design for Additive Manufacturing (DfAM): Optimizing Linkage Arms for 3D Printing
Transitioning the production of high-stress linkage arms to metal additive manufacturing isn’t merely a change in fabrication technique; it necessitates a fundamental shift in design philosophy. Simply taking a design intended for machining or casting and sending it to a 3D printer rarely unlocks the full potential of AM. To truly leverage the benefits of enhanced performance, reduced weight, and optimized functionality, engineers must embrace Design for Additive Manufacturing (DfAM). DfAM involves tailoring the component’s geometry specifically for the layer-by-layer build process and the unique capabilities of AM technologies.
Key DfAM Principles for High-Stress Linkage Arms:
- Topology Optimization: This is arguably one of the most powerful tools enabled by AM. Software algorithms analyze the load paths and stress distribution within a defined design space for the linkage arm. Material is then strategically removed from low-stress areas and added along critical load paths, resulting in organic-looking, highly efficient structures that minimize weight while maximizing stiffness and strength. This is ideal for aerospace and automotive applications where weight savings directly impact fuel efficiency and performance.
- Lattice Structures & Internal Geometries: DfAM allows for the incorporation of internal lattice structures within the linkage arm. These can significantly reduce weight and material usage while maintaining structural integrity, or even be designed to absorb specific vibrational frequencies. Furthermore, internal channels for cooling, lubrication, or sensor integration can be designed directly into the part, features often impossible to create with traditional methods.
- Stress Concentration Reduction: Sharp corners and abrupt changes in geometry are notorious stress risers, particularly under dynamic loading, leading to fatigue failure. DfAM encourages the use of smooth fillets, optimized radii, and gradual transitions to distribute stress more evenly throughout the linkage arm, enhancing its fatigue life.
- Support Structure Strategy: Most powder bed fusion processes require support structures to anchor the part to the build plate, manage thermal stresses, and support overhanging features. Effective DfAM involves designing the linkage arm to minimize the need for supports, especially in hard-to-reach areas. This can involve:
- Designing Self-Supporting Angles: Orienting surfaces above a certain angle (typically >45 degrees from the horizontal) can often eliminate the need for direct support underneath.
- Optimizing Part Orientation: The way a linkage arm is oriented on the build platform significantly impacts support requirements, print time, surface finish on different faces, and even mechanical properties due to the anisotropic nature of AM builds. Collaboration with the AM service provider is crucial here.
- Integrating Removable Supports: Designing features that make support structures easier and cleaner to remove post-print saves time and reduces the risk of damaging the part.
- Feature Design for Post-Processing: Consider downstream processes during the design phase. If specific surfaces require high precision (e.g., pin holes, mating faces), adding extra stock material for post-print CNC machining might be necessary. Designing features that aid in workholding for machining or inspection can also streamline production.
- Konsolidacja części: Analyze the entire linkage assembly. Can multiple brackets, connectors, or fasteners be integrated into a single, 3D printed linkage arm? This reduces part count, assembly labor, weight, and potential points of failure – a significant advantage for B2B procurement seeking streamlined logistics and enhanced reliability.
Collaboration is Key:
Successfully implementing DfAM, especially for critical components like high-stress linkage arms, often benefits from close collaboration between the design engineers and the AM service provider. Experienced providers like Met3dp offer DfAM consultation, leveraging their deep understanding of specific metody drukowania, material behaviors (like 17-4PH and M300), and post-processing requirements. This partnership ensures that the final design is not only optimized for performance but also manufacturable, cost-effective, and reliable, meeting the stringent demands of industrial buyers and procurement specialists. Engaging with AM experts early in the design cycle maximizes the benefits achievable through this transformative technology.
Achievable Precision: Tolerance, Surface Finish, and Dimensional Accuracy in Metal AM
For linkage arms to function correctly within a larger mechanical system, precise control over dimensions, tolerances, and surface finish is critical. Mating surfaces, pin diameters, hole locations, and overall geometry must meet specified requirements to ensure proper fit, motion, and load transmission. While metal additive manufacturing offers incredible design freedom, it’s essential to understand the levels of precision achievable and the factors influencing them.
Tolerances in Metal Powder Bed Fusion (PBF):
- General Tolerances: Typical achievable tolerances for metal PBF processes like Selective Laser Melting (SLM) / Laser Powder Bed Fusion (LPBF) and Selective Electron Beam Melting (SEBM) are often in the range of ±0.1 mm to ±0.2 mm (±0.004″ to ±0.008″) for smaller features, or ±0.1% to ±0.2% of the nominal dimension for larger parts. However, this is a general guideline and can vary significantly.
- Factors Influencing Tolerances:
- Machine Accuracy & Calibration: The inherent precision and regular calibration of the AM system are fundamental. Met3dp emphasizes the industry-leading accuracy and reliability of its printers for mission-critical parts.
- Właściwości materiału: Different metal powders exhibit varying shrinkage and thermal behavior during printing and cooling.
- Part Geometry & Size: Larger parts or those with complex internal features are more susceptible to thermal distortion, potentially impacting final tolerances.
- Thermal Stresses: Residual stresses built up during the layer-by-layer melting and solidification can cause warping or distortion if not properly managed through support structures and build strategies.
- Parametry drukowania: Laser/electron beam power, scan speed, layer thickness, and hatching strategy all influence the melt pool dynamics and resulting dimensional accuracy.
- Przetwarzanie końcowe: Heat treatment processes (stress relief, aging) can sometimes cause minor dimensional changes that need to be accounted for.
Surface Finish (Roughness):
- As-Built Surface Finish: The surface finish of parts directly off the AM machine typically has a noticeable roughness (Ra). This is due to the partially melted powder particles adhering to the surface and the layer-wise construction.
- Typical Ra Values (As-Built): Often range from 6 µm to 25 µm (240 µin to 1000 µin), depending on the process (SEBM generally results in rougher surfaces than LPBF), material, orientation (upward-facing and vertical walls are usually smoother than downward-facing surfaces relying on supports), and parameters.
- Achievable Surface Finish: For many functional surfaces on linkage arms (e.g., pin bores, bearing seats, mating faces), the as-built finish is insufficient. Post-processing steps are required to achieve smoother surfaces:
- Bead Blasting/Sand Blasting: Provides a uniform matte finish, improving aesthetics and removing loose powder, but only slightly improves Ra (e.g., 5-15 µm Ra).
- Tumbling/Vibratory Finishing: Can improve Ra significantly for bulk processing of smaller parts (e.g., down to 1-5 µm Ra).
- CNC Machining: Offers the highest precision and smoothest finishes for critical features (capable of <1 µm Ra).
- Polerowanie: Manual or automated polishing can achieve very smooth, mirror-like finishes where required.
Dimensional Accuracy Management:
Achieving the required precision for high-stress linkage arms involves a combination of factors:
- Projekt: Designing critical features with appropriate tolerances and considering potential AM variations. Adding machining allowances where necessary.
- Kontrola procesu: Utilizing well-maintained, high-accuracy machines (like those employed by Met3dp) with optimized and validated parameters for specific materials (17-4PH, M300).
- Simulation: Using process simulation software to predict potential distortion and optimize build orientation and support strategies.
- Przetwarzanie końcowe: Implementing precise post-processing steps, particularly CNC machining for critical-to-function dimensions.
- Kontrola jakości: Employing metrology tools like Coordinate Measuring Machines (CMM), 3D scanning, and traditional gauges to verify dimensional accuracy against specifications.
Procurement managers sourcing high-precision linkage components should engage with AM suppliers who demonstrate a strong understanding of tolerance control, offer necessary post-processing capabilities, and possess robust quality management systems to ensure parts consistently meet engineering requirements.
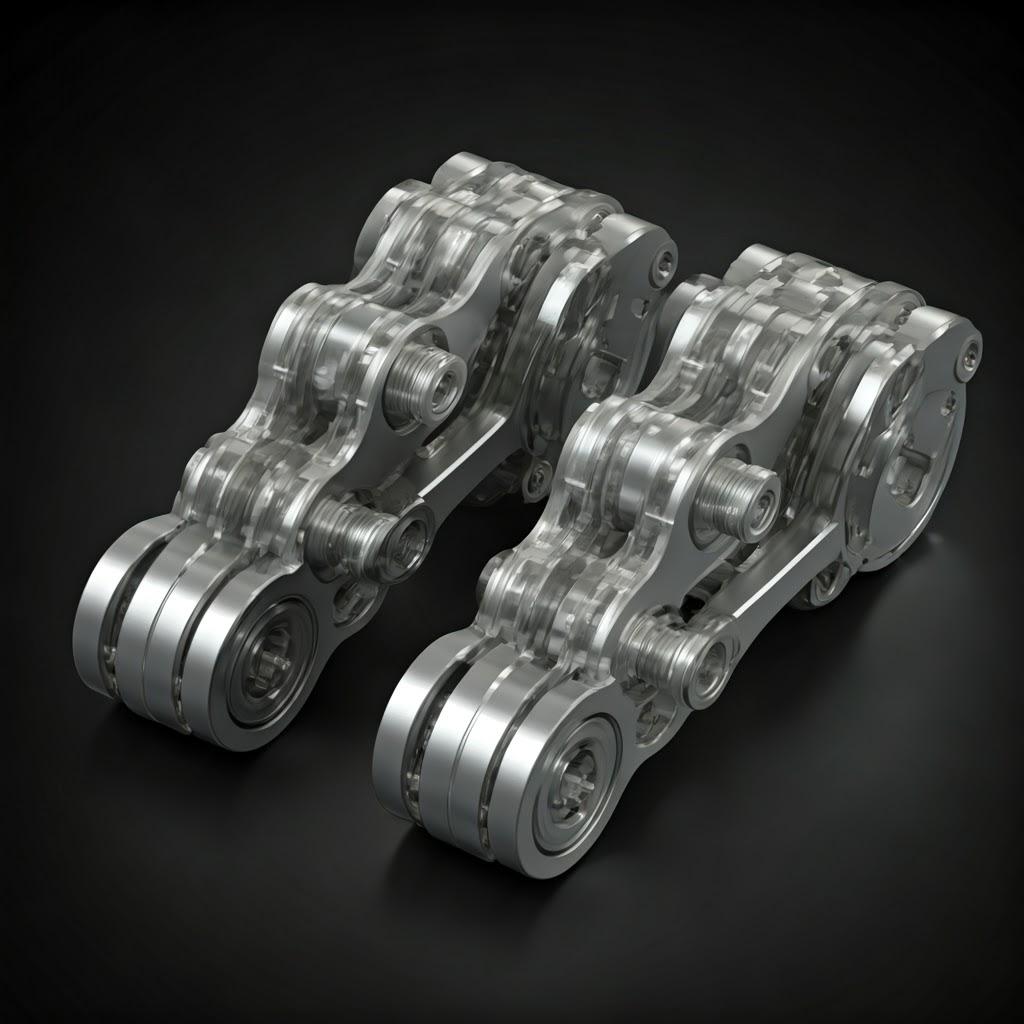
Beyond the Print: Essential Post-Processing Steps for High-Stress Linkage Arms
Producing a high-stress linkage arm using metal additive manufacturing involves more than just the printing process itself. The “green” part that comes off the build plate requires a series of crucial post-processing steps to achieve the final desired dimensions, mechanical properties, and surface finish. These steps are not optional extras; they are integral to ensuring the component’s safety, reliability, and performance, especially when dealing with high-strength materials like 17-4PH and M300 under dynamic loads.
Typical Post-Processing Workflow for AM Linkage Arms:
- Ulga w stresie:
- Cel: To alleviate internal stresses built up during the rapid heating and cooling cycles of the printing process. This minimizes the risk of distortion or cracking when the part is removed from the build plate.
- Method: Typically performed while the part is still attached to the build plate in an inert atmosphere furnace at a specific temperature below the material’s transformation point. Parameters depend on the material and part geometry.
- Part Removal:
- Cel: To separate the printed linkage arm(s) from the build plate.
- Method: Usually done using wire EDM (Electrical Discharge Machining) or a bandsaw. Care must be taken not to damage the parts.
- Usunięcie konstrukcji wsporczej:
- Cel: To remove the temporary structures used during printing.
- Method: Can range from simple manual breakaway for well-designed supports to more laborious cutting, grinding, or CNC machining, especially for supports in complex internal areas. DfAM plays a huge role in simplifying this step.
- Heat Treatment (Crucial for 17-4PH & M300):
- Cel: To develop the final, desired mechanical properties (high strength, hardness, toughness). As-printed parts generally do not possess the optimal properties for high-stress applications.
- Method:
- 17-4PH: Requires a two-step process: Wyżarzanie roztworu (heating to a high temperature to dissolve precipitates, followed by cooling) and then Precipitation Hardening (Aging) (heating to a lower temperature for a specific duration to precipitate strengthening phases). Different aging temperatures (e.g., H900, H1025, H1150) yield different combinations of strength and toughness.
- M300: Requires a simpler Starzenie się process (heating to a specific temperature, typically around 480-500°C, for several hours) to achieve its ultra-high strength through the precipitation of intermetallic compounds. Precise temperature and time control are critical.
- Importance: Skipping or improperly performing heat treatment will result in a linkage arm that fails to meet performance specifications, potentially leading to premature failure under load.
- Hot Isostatic Pressing (HIP) (Optional but Recommended for Critical Parts):
- Cel: To eliminate any residual internal micro-porosity within the printed part, improving fatigue life, ductility, and overall material integrity.
- Method: Subjects the part to high temperature (below melting point) and high isostatic pressure (using an inert gas like Argon) simultaneously. This collapses internal voids.
- Relevance: Often specified for critical aerospace, medical, or high-fatigue applications to ensure maximum material density and performance consistency.
- CNC Machining:
- Cel: To achieve tight tolerances on critical features (e.g., pin/bore diameters, mating surfaces, thread tapping) that cannot be met by the as-built AM process or subsequent heat treatments.
- Method: Using standard CNC milling, turning, or grinding operations. Requires careful fixture design to hold the potentially complex AM part geometry.
- Wykończenie powierzchni:
- Cel: To achieve the desired surface roughness (Ra), improve aesthetics, remove contaminants, or prepare the surface for coating.
- Method: Options include bead blasting, sand blasting, tumbling, polishing, electro-polishing, or applying protective/functional coatings (e.g., paint, plating, passivation for stainless steel).
- Cleaning and Inspection:
- Cel: Final cleaning to remove any machining fluids or debris. Thorough inspection to verify dimensional accuracy, surface finish, and material integrity.
- Method: Dimensional inspection (CMM, scanning), surface finish measurement, visual inspection, and potentially Non-Destructive Testing (NDT) such as dye penetrant testing (DPT) for surface cracks or Computed Tomography (CT) scanning for internal defects.
Understanding this end-to-end workflow is vital for procurement managers and engineers. Partnering with a full-service provider like Met3dp, which possesses expertise across the entire process chain from powder to finished product, ensures that all necessary steps are performed correctly, resulting in a high-quality, reliable high-stress linkage arm ready for its demanding application.
Navigating Potential Hurdles: Common Challenges and Mitigation Strategies
While metal additive manufacturing offers significant advantages for producing high-stress linkage arms, it’s not without its potential challenges. Awareness of these hurdles and the strategies employed by experienced service providers like Met3dp to mitigate them is crucial for ensuring successful outcomes and reliable parts. Procurement managers should inquire about a potential supplier’s approach to managing these common issues.
Challenge 1: Warping and Distortion
- Cause: Uneven heating and cooling during the layer-by-layer build process generate internal stresses. If these stresses exceed the material’s yield strength at elevated temperatures, the part can warp during the build or distort upon removal from the build plate or during post-print heat treatment. This is particularly relevant for large parts or those with significant variations in cross-section.
- Mitigation Strategies:
- Process Simulation: Using software to predict thermal behavior and distortion before printing allows for optimization of part orientation and support structures.
- Optimized Build Parameters: Fine-tuning laser/beam power, scan speed, and scan strategy to manage heat input.
- Robust Support Structures: Designing supports not only for overhangs but also to anchor the part securely and act as heat sinks, counteracting warping forces.
- Optimized Part Orientation: Positioning the linkage arm on the build plate to minimize large, flat surfaces parallel to the recoater and balance thermal mass.
- Controlled Heating/Cooling: Utilizing heated build chambers (common in SEBM) and controlled cool-down cycles.
- Stress Relief Heat Treatment: Performing this step before removing the part from the build plate is critical.
Challenge 2: Residual Stress Management
- Cause: Similar to distortion, residual stresses are inherent due to the rapid solidification process. While some stress is relieved during the build by plastic deformation, significant stress can remain locked within the part. High residual stress can reduce fatigue life, cause distortion during machining, and potentially lead to cracking.
- Mitigation Strategies:
- Zarządzanie temperaturą: Optimized scan strategies (e.g., island scanning) and pre-heating the build environment reduce thermal gradients.
- Stress Relief Cycles: Implementing appropriate post-build heat treatment cycles specifically designed to reduce residual stress without negatively affecting microstructure. SEBM inherently produces parts with lower residual stress compared to LPBF due to the higher process temperatures.
- Rozważania projektowe: Avoiding large bulk masses or abrupt changes in thickness where stress can concentrate.
Challenge 3: Support Removal Difficulties
- Cause: Supports are necessary but add processing time and cost. Removing them, especially from complex internal channels or delicate features of a linkage arm, can be challenging, time-consuming, and risks damaging the part surface.
- Mitigation Strategies:
- DfAM Focus: Designing the part for minimal support reliance (self-supporting angles, optimal orientation).
- Specialized Support Structures: Using support types designed for easier removal (e.g., conical supports, structures with specific break-points).
- Advanced Removal Techniques: Employing electrochemical machining or specialized tools for inaccessible areas.
- Material Choice: Some materials may allow for easier support separation than others.
Challenge 4: Ensuring Material Integrity (Porosity, Microstructure)
- Cause: Achieving fully dense parts with the desired microstructure is critical for high-stress applications. Potential issues include:
- Porowatość: Gas porosity (trapped gas) or lack-of-fusion porosity (incomplete melting between layers/tracks) can act as crack initiation sites, severely reducing fatigue life.
- Undesirable Microstructure: Incorrect print parameters or cooling rates can lead to unfavorable grain structures or phases, compromising strength or toughness.
- Mitigation Strategies:
- High-Quality Powder: Using powders with high sphericity, controlled PSD, and low internal gas content, like those produced by Met3dp’s advanced atomization processes, is fundamental.
- Optimized & Validated Parameters: Rigorously developed and validated process parameters (power, speed, layer thickness, gas flow, vacuum levels for SEBM) specific to the material (17-4PH, M300) and machine.
- Melt Pool Monitoring (Optional): In-situ monitoring systems can detect anomalies during the build.
- Prasowanie izostatyczne na gorąco (HIP): Effective at closing internal porosity post-print.
- Metallurgical Analysis: Cross-sectional analysis and testing to verify density and microstructure meet specifications.
- Robust Quality Management: Implementing stringent quality control throughout the powder handling, printing, and post-processing stages.
By partnering with an experienced additive manufacturing provider like Met3dp, who proactively addresses these challenges through advanced technology (high-quality powders, reliable SEBM/LPBF printers), process simulation, rigorous process control, comprehensive post-processing, and robust quality assurance systems, engineers and procurement managers can confidently source high-stress linkage arms that meet the demanding requirements of their applications.
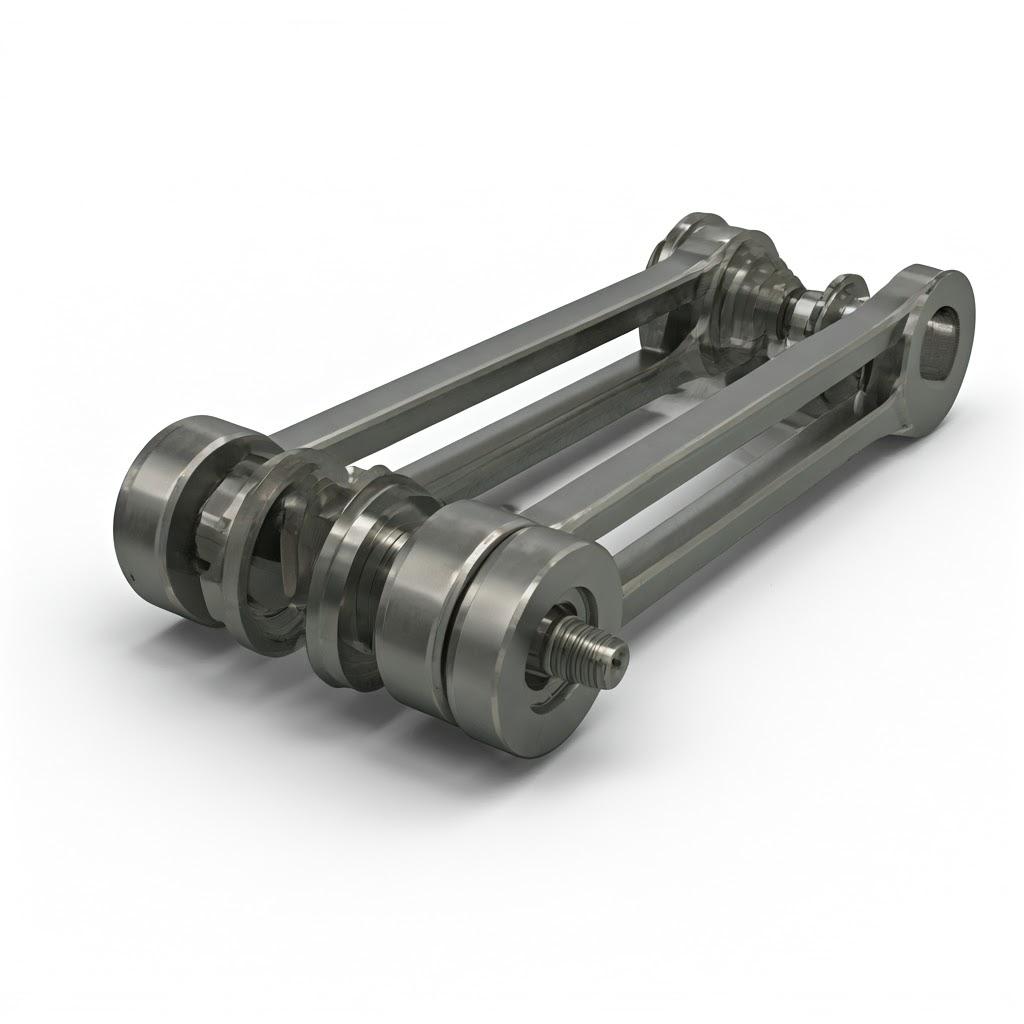
Selecting Your Partner: How to Choose the Right Metal 3D Printing Service Provider
Choosing the right additive manufacturing partner is as critical as the design and material selection, especially when dealing with high-stress components like linkage arms destined for demanding applications. The capabilities, expertise, and quality systems of your chosen supplier will directly impact the performance, reliability, and cost-effectiveness of the final product. For engineers and procurement managers sourcing these parts, particularly for industrial or B2B requirements involving potential bulk orders or critical applications, a thorough evaluation process is essential.
Key Criteria for Evaluating Metal AM Service Providers:
- Certyfikaty jakości: Look for internationally recognized certifications.
- ISO 9001: Demonstrates a commitment to quality management systems – a fundamental requirement.
- AS9100: Specifically for the aerospace industry, indicating stringent quality control for flight-critical components.
- Norma ISO 13485: Relevant if sourcing linkage arms for medical devices.
- Wiedza materiałowa: The provider must have proven experience working with the specific high-performance alloys required, such as 17-4PH and M300 maraging steel. This includes:
- Proper powder handling and storage protocols (especially for reactive materials if applicable).
- Validated print parameters for achieving desired density and microstructure.
- Deep understanding of post-print heat treatment cycles crucial for developing final properties.
- Technology and Equipment: Assess if their technology aligns with your needs.
- Technologia druku: Do they offer the right process (e.g., SEBM for low residual stress and high purity, LPBF for fine features)? Met3dp specializes in advanced SEBM printers and also possesses LPBF capabilities, offering flexibility.
- Możliwości maszyny: Consider build volume (can they accommodate your linkage arm size?), machine accuracy, and condition/maintenance of their equipment. Met3dp prides itself on printers delivering industry-leading print volume, accuracy, and reliability.
- Powder Production: In-house powder production or strong partnerships with quality powder suppliers (like Met3dp’s advanced gas atomization and PREP systems) can be advantageous for quality control and material traceability.
- Technical Expertise and Support: Evaluate the team’s knowledge and willingness to collaborate.
- DfAM Consultation: Can they provide expert advice on optimizing your linkage arm design for additive manufacturing?
- Application Engineering: Do they understand the end-use requirements and challenges of high-stress dynamic systems?
- Problem-Solving: Do they have a track record of overcoming common AM challenges (discussed in Part 2)?
- Track Record and Experience:
- Case Studies/Portfolio: Ask for examples of similar projects involving high-stress components, dynamic load applications, or the specific materials you require.
- Doświadczenie w branży: Have they worked extensively within your industry (aerospace, automotive, industrial)?
- Capacity and Scalability: Can the provider meet your volume requirements, from initial prototypes to potential series or bulk production orders? Discuss their capacity planning and ability to scale output.
- End-to-End Capabilities: Does the provider offer a comprehensive service, including necessary post-processing (heat treatment, HIP, CNC machining, NDT) and quality inspection? Managing multiple vendors adds complexity and risk.
- Location and Logistics: Consider the supplier’s location (Met3dp is headquartered in Qingdao, China) and its implications for shipping times, costs, and communication across time zones. Ensure they have robust logistics for international B2B shipments.
Why Met3dp Stands Out:
Met3dp embodies many qualities of an ideal partner for demanding metal AM projects. With decades of collective expertise, Met3dp provides comprehensive solutions that span from developing and manufacturing high-performance metal powders using industry-leading technologies to operating advanced SEBM printers known for accuracy and reliability. Their focus on innovative alloys like TiNi, TiTa, TiAl, TiNbZr, CoCrMo, stainless steels (including 17-4PH), and superalloys (like M300 precursors) demonstrates deep material science capabilities. Met3dp partners with organizations across aerospace, medical, automotive, and other fields, offering application development services to accelerate digital manufacturing transformations. Their integrated approach, combining cutting-edge systems, advanced materials, and application expertise, makes them a strong choice for B2B customers seeking a reliable supplier for critical, high-stress linkage arms.
Understanding the Investment: Cost Factors and Lead Time for 3D Printed Linkage Arms
While metal 3D printing enables the creation of highly optimized and complex linkage arms, understanding the associated costs and production timelines is essential for project planning and procurement. Unlike traditional mass production methods where tooling costs dominate low volumes, AM costs are driven primarily by material consumption and machine time.
Key Cost Drivers for 3D Printed Linkage Arms:
- Part Design and Complexity:
- Objętość: The sheer amount of material in the final part is a direct cost factor. Topology optimization significantly helps here.
- Złożoność: While AM handles complexity well, intricate designs might require extensive support structures, increasing print time and post-processing effort.
- Materiał pomocniczy: The volume of material used for supports adds to cost and requires time for removal.
- Material Choice:
- High-performance alloys like M300 maraging steel are significantly more expensive per kilogram than materials like 17-4PH stainless steel or standard steels. Powder quality and specialized alloys also impact price.
- Machine Time:
- This is often the most significant cost component. It depends on the part’s height (number of layers), the total area to be scanned per layer, the chosen layer thickness, and the specific machine’s build speed. Larger or taller linkage arms naturally take longer to print.
- Machine amortization, operational costs (energy, gas), and labor are factored into the hourly rate.
- Wymagania dotyczące przetwarzania końcowego:
- Costs increase significantly with the extent of post-processing needed:
- Basic: Stress relief, part/support removal, basic bead blast.
- Pośredni: Adding mandatory heat treatment (aging/solution anneal).
- Zaawansowane: Including HIP, multi-axis CNC machining for tight tolerances, advanced surface finishing (polishing), NDT inspection (CT scanning).
- Costs increase significantly with the extent of post-processing needed:
- Quality Assurance and Inspection:
- The level of required inspection (e.g., basic dimensional checks vs. CMM reports, material certifications, NDT) impacts the final cost. Requirements for aerospace or medical components are typically higher.
- Order Quantity (Volume):
- Setup Costs: There are setup costs associated with preparing each build (loading powder, programming). These costs are amortized over the number of parts in a build.
- Build Packing: Printing multiple linkage arms simultaneously in a single build drastically reduces the cost per part compared to printing one at a time.
- Rabaty ilościowe: For larger B2B or wholesale orders, suppliers like Met3dp can often offer volume discounts based on optimized production planning and material purchasing.
Estimating Lead Times:
Lead time is the duration from order confirmation to part delivery. It’s influenced by several factors:
- Quoting and Design Review: Initial communication, quote generation, and design finalization (including any DfAM iterations). (1-5 days)
- Print Queue: The supplier’s current machine backlog. (Variable: days to weeks)
- Czas drukowania: Actual time the part spends printing on the machine. (Hours to several days, depending on size/complexity/quantity)
- Cooling and Depowdering: Time for the build chamber to cool and for powder removal. (Hours)
- Przetwarzanie końcowe: This can be a significant portion of the lead time, especially if multiple steps like heat treatment, HIP, extensive machining, and finishing are required. (Days to weeks)
- Kontrola jakości: Time for required dimensional and material checks. (Hours to days)
- Wysyłka: Transit time from the supplier (e.g., Qingdao, China) to the customer’s location. (Days to weeks, depending on method and destination)
Typical Lead Time: For a moderately complex high-stress linkage arm requiring heat treatment and some machining, expect lead times ranging from 2 do 6 tygodni, potentially longer for very large parts, complex post-processing, or large batch orders. Prototyping can often be faster. It’s crucial to discuss lead time requirements early with your supplier. Met3dp works with clients to provide realistic timelines based on current capacity and project specifics.
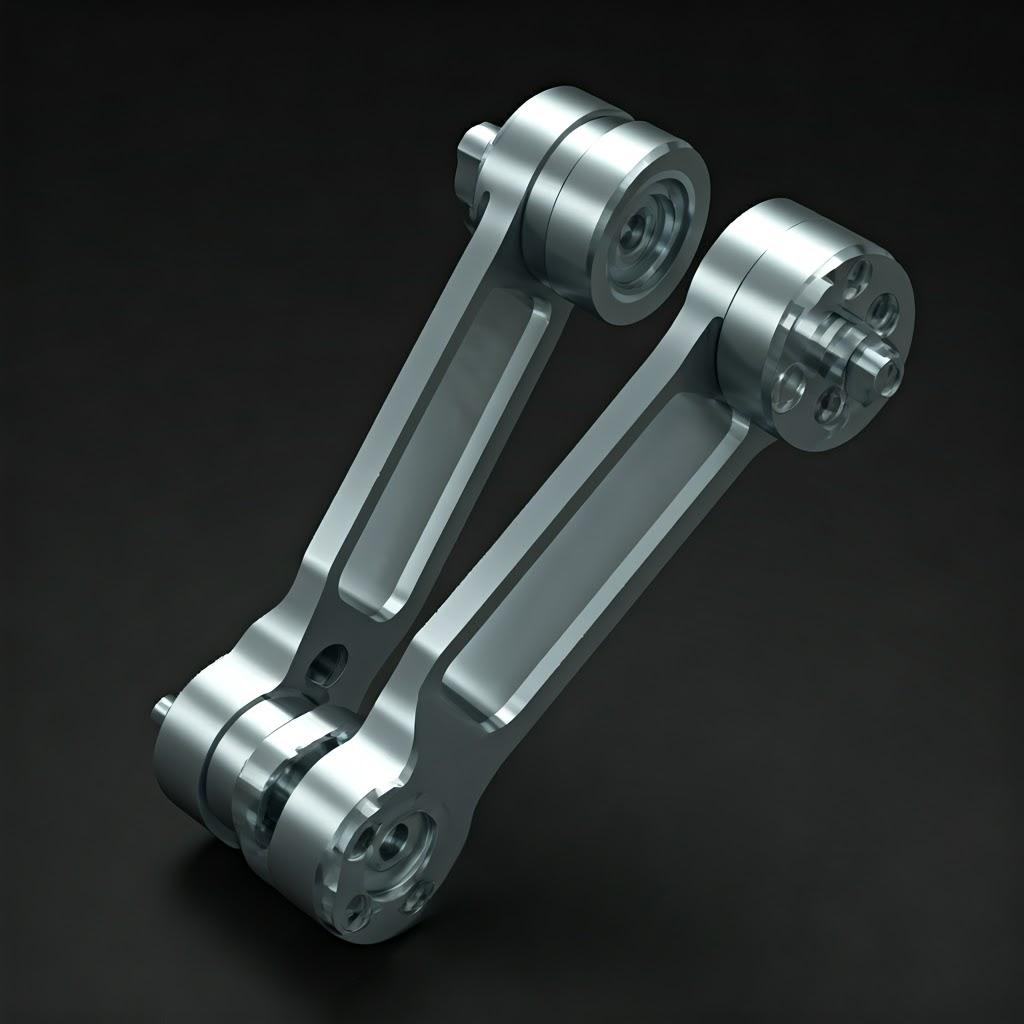
Frequently Asked Questions (FAQ) about 3D Printed High-Stress Linkage Arms
Here are answers to some common questions engineers and procurement managers have when considering metal AM for high-stress linkage arms:
1. How does the strength of 3D printed 17-4PH or M300 compare to traditionally manufactured (e.g., wrought or forged) counterparts?
When printed using optimized parameters and subjected to appropriate post-processing (especially heat treatment and potentially HIP), the mechanical properties (yield strength, tensile strength, hardness) of AM 17-4PH and M300 can be comparable, and sometimes even superior in certain aspects (like yield strength), to wrought specifications. Fatigue properties, critical for dynamic loads, can also be excellent, particularly after HIP treatment eliminates micro-porosity. However, properties can be anisotropic (direction-dependent) in AM parts. It’s essential to work with a provider like Met3dp who understands process control and can provide material data based on standardized testing of their printed materials.
2. What is the typical cost-saving potential compared to traditional CNC machining from billet for a complex linkage arm?
The cost comparison depends heavily on part complexity, material, and volume.
- AM is often more cost-effective when:
- The linkage arm geometry is highly complex or topology-optimized (leading to significant material savings and reduced machining time compared to starting from a large billet).
- Volumes are low to medium (avoiding high tooling costs of casting/forging).
- Rapid prototyping or quick turnaround is needed.
- Part consolidation is possible.
- Traditional machining may be more cost-effective when:
- The geometry is relatively simple and easily machined from standard stock shapes.
- Volumes are very high (allowing economies of scale with dedicated tooling or optimized machining setups).
- The primary cost driver is raw material, and AM doesn’t offer significant buy-to-fly ratio improvements. It’s best to get quotes for both methods for your specific part to make an informed decision.
3. Can complex internal features, like cooling channels or integrated sensor pathways, be reliably built into linkage arms using metal AM?
Yes, this is one of the significant advantages of metal AM. Processes like LPBF and SEBM can create intricate internal channels and void spaces that are impossible to achieve with subtractive manufacturing or casting. This allows for integrated functionality, such as conformal cooling channels to manage heat in high-speed actuation systems or pathways for embedded sensors or wiring, directly within the linkage arm structure. Design considerations for powder removal from these channels are important.
4. What quality certifications and controls does Met3dp employ for manufacturing critical components?
Met3dp implements rigorous quality control throughout its processes, starting with the production of its high-quality metal powders using advanced atomization techniques. Their manufacturing operations adhere to stringent quality management systems (potentially aligned with ISO 9001 principles, though specific certifications should always be confirmed directly based on project requirements). They emphasize the accuracy and reliability of their printing equipment and employ process monitoring and post-print inspection methods (including NDT options) to ensure parts meet dimensional and material specifications required for mission-critical aerospace, medical, and industrial applications. For specific certification details relevant to your project, contacting Met3dp directly is recommended.
5. What is the typical Minimum Order Quantity (MOQ) for custom 3D printed linkage arms?
Unlike traditional manufacturing methods that often require high MOQs due to tooling costs, metal AM is highly flexible. Most service providers, including those catering to B2B clients like Met3dp, can typically accommodate orders ranging from a single prototype to low-volume production runs and larger batch orders. While there’s often no strict MOQ, the cost-per-part is generally lower for larger quantities due to the amortization of setup costs and optimization of build plate capacity. Discussing your specific volume needs (prototype, initial batch, ongoing production) with the supplier will yield the most accurate information on pricing structures.
Conclusion: Revolutionizing High-Stress Components with Met3dp’s Additive Manufacturing
The challenge of designing and manufacturing linkage arms capable of withstanding high stress and dynamic loads has found a powerful ally in metal additive manufacturing. As we’ve explored, leveraging AM technologies like Selective Electron Beam Melting (SEBM) and Laser Powder Bed Fusion (LPBF) allows for the creation of components with unparalleled design freedom, optimized strength-to-weight ratios, and integrated complexity previously unattainable. By utilizing high-performance materials such as 17-4PH stainless steel and M300 maraging steel, engineers can push the boundaries of performance in critical applications across aerospace, automotive, robotics, and industrial sectors.
The journey from digital design to functional, reliable hardware involves careful consideration of DfAM principles, achievable precision, essential post-processing steps like heat treatment, and navigating potential manufacturing challenges. Success hinges not only on the technology itself but significantly on the expertise and capabilities of the chosen manufacturing partner.
Met3dp stands as a leading provider equipped to meet these challenges head-on. Headquartered in Qingdao, China, Met3dp offers a comprehensive suite of additive manufacturing solutions, built upon a foundation of deep materials science expertise, advanced powder production capabilities, and industry-leading SEBM and other AM printing systems. Their focus on producing high-quality spherical metal powders and delivering parts with exceptional accuracy and reliability makes them an ideal partner for organizations seeking to implement next-generation manufacturing for their most demanding components.
Whether you are an engineer seeking to optimize a critical linkage arm design or a procurement manager looking for a reliable B2B supplier for high-performance metal parts, Met3dp offers the expertise and technology to accelerate your goals.
Ready to explore how metal additive manufacturing can enhance your high-stress linkage arms?
Odwiedzać Met3dp.com to learn more about their capabilities or contact their team today to discuss your specific project requirements and unlock the potential of advanced manufacturing.
Udostępnij
MET3DP Technology Co., LTD jest wiodącym dostawcą rozwiązań w zakresie produkcji addytywnej z siedzibą w Qingdao w Chinach. Nasza firma specjalizuje się w sprzęcie do druku 3D i wysokowydajnych proszkach metali do zastosowań przemysłowych.
Zapytaj o najlepszą cenę i spersonalizowane rozwiązanie dla Twojej firmy!
Powiązane artykuły
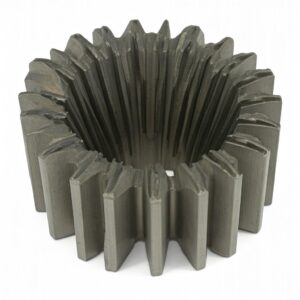
Wysokowydajne segmenty łopatek dysz: Rewolucja w wydajności turbin dzięki drukowi 3D w metalu
Czytaj więcej "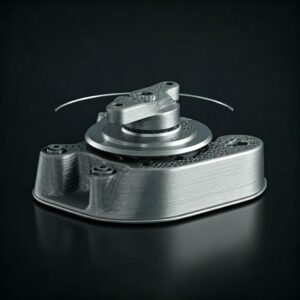
Drukowane w 3D mocowania dla samochodowych czujników radarowych: Precyzja i wydajność
Czytaj więcej "Informacje o Met3DP
Ostatnia aktualizacja
Nasz produkt
KONTAKT
Masz pytania? Wyślij nam wiadomość teraz! Po otrzymaniu wiadomości obsłużymy Twoją prośbę całym zespołem.
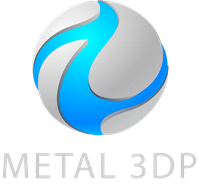
Proszki metali do druku 3D i produkcji addytywnej