Lightweight Sensor Gimbals for UAVs via 3D Printing
Spis treści
Introduction: Revolutionizing UAV Performance with Lightweight 3D Printed Sensor Gimbals
The relentless evolution of Unmanned Aerial Vehicle (UAV) technology continues to push the boundaries of what’s possible across diverse sectors, from critical defense operations and intricate infrastructure inspections to precision agriculture and captivating aerial cinematography. At the heart of many advanced UAV capabilities lies the sensor gimbal – a sophisticated electromechanical system responsible for stabilizing and directing cameras, LiDAR scanners, thermal imagers, and other vital sensor payloads. The performance of this gimbal system is paramount; it dictates the quality of data captured, the stability of footage obtained, and ultimately, the operational effectiveness of the entire UAV platform. However, traditional gimbal manufacturing methods often face limitations, particularly concerning weight, design complexity, and production lead times, which can hinder the overall performance and mission endurance of the UAV.
Weight is arguably the most critical currency in aerospace engineering, and UAV design is no exception. Every gram saved on a component translates directly into tangible benefits: longer flight times, increased payload capacity, improved maneuverability, and reduced energy consumption. Sensor gimbals, often positioned far from the UAV’s center of gravity, exert a significant influence on flight dynamics and stability. Consequently, minimizing their mass while maintaining structural integrity and operational precision is a primary objective for UAV designers and manufacturers. This quest for lighter, yet more capable, components has driven the exploration of innovative manufacturing techniques capable of overcoming the constraints of conventional approaches like CNC machining from billet material or complex multi-part assemblies.
Enter metal additive manufacturing (AM), more commonly known as druk 3D z metalu. This transformative technology is rapidly reshaping the landscape of high-performance component production, offering unprecedented solutions for creating lightweight, complex, and highly optimized parts. Unlike subtractive manufacturing, which removes material from a solid block, AM builds parts layer by layer directly from digital models using fine metal powders. This fundamental difference unlocks a new dimension of design freedom, enabling engineers to create intricate geometries, internal lattice structures, and organically shaped components that are perfectly tailored to their functional requirements while shedding unnecessary mass. For UAV sensor gimbals, metal AM presents a compelling opportunity to achieve significant weight reductions (often 20-50% or more compared to traditionally manufactured counterparts) without compromising on stiffness, strength, or the precision needed for stable sensor pointing and control. Furthermore, AM facilitates the consolidation of multiple components into a single, integrated structure, reducing assembly complexity, potential failure points, and overall part count. This paradigm shift empowers engineers to design gimbals that are not just lighter, but smarter and more robust, directly enhancing the mission capabilities of next-generation UAVs. Companies specializing in industrial additive manufacturing solutions, particularly those with deep expertise in high-performance metal powders and advanced printing systems, are becoming crucial partners for UAV manufacturers seeking to leverage this technology for competitive advantage.
Applications Unveiled: Where are Metal 3D Printed Gimbals Taking Flight?
The adoption of metal Drukowane w 3D sensor gimbals is rapidly expanding across a multitude of industries, driven by the tangible performance enhancements they offer. The ability to create highly customized, lightweight, and robust gimbals tailored to specific sensor payloads and operational environments makes them invaluable assets for demanding UAV applications. Let’s delve into the key sectors and specific use cases where these advanced components are making a significant impact:
- Defense and Aerospace: This sector represents a primary driver for advanced UAV technology. Metal AM gimbals are crucial for Intelligence, Surveillance, and Reconnaissance (ISR) missions, where long endurance and stable, high-resolution imaging are critical.
- Przykłady zastosowań: Target acquisition and tracking, border patrol, persistent surveillance, battlefield situational awareness, signals intelligence (SIGINT) payload stabilization.
- Korzyści: Significant weight savings extend mission duration for high-altitude long-endurance (HALE) and medium-altitude long-endurance (MALE) UAVs. The high strength-to-weight ratio of materials like Titanium alloys (e.g., Ti-6Al-4V) ensures durability in harsh operational conditions and under high-g maneuvers. Part consolidation reduces potential points of failure, enhancing system reliability for mission-critical components. The ability to integrate conformal antennas or specific cooling channels directly into the gimbal structure further optimizes performance. Procurement managers in defense prioritize reliability, performance, and secure supply chains, areas where AM offers unique advantages, including the potential for distributed manufacturing.
- Infrastructure Inspection and Asset Management: Maintaining critical infrastructure like power lines, pipelines, bridges, wind turbines, and railway lines requires frequent and detailed inspection, often in hazardous or difficult-to-reach locations. UAVs equipped with specialized sensors mounted on stable gimbals provide a safer, faster, and more cost-effective solution than traditional methods.
- Przykłady zastosowań: Visual and thermal inspection of power grids, structural integrity analysis of bridges and buildings, pipeline leak detection (using methane sensors), wind turbine blade inspection, railway track monitoring.
- Korzyści: Lightweight gimbals allow smaller, more agile UAVs to be deployed, reducing operational costs and complexity. High stability ensures clear imagery and accurate data collection, even in windy conditions. Custom gimbal designs can accommodate multiple sensors (e.g., visual + thermal) simultaneously, improving inspection efficiency. Material choices like AlSi10Mg offer a good balance of weight, strength, and cost for these industrial applications. Wholesale suppliers of inspection services benefit from UAVs with longer flight times and higher data quality enabled by optimized gimbals.
- Mapping and Surveying (Geomatics): Generating accurate topographical maps, 3D models of terrain, and surveying construction sites or mining operations relies heavily on precise data acquisition from aerial platforms. Sensor gimbals ensure that cameras and LiDAR scanners maintain the correct orientation relative to the ground, regardless of UAV movement.
- Przykłady zastosowań: Orthophoto generation, LiDAR point cloud acquisition for digital elevation models (DEMs), volumetric calculations for stockpiles, construction progress monitoring, archaeological site mapping.
- Korzyści: Precise stabilization minimizes data distortion, leading to higher accuracy maps and models. Lightweighting allows for the integration of higher-resolution, heavier sensors without overburdening the UAV. Rapid prototyping enabled by AM allows survey companies to quickly adapt gimbal designs for new sensor packages or specific project requirements.
- Precision Agriculture: UAVs are revolutionizing farming by enabling targeted monitoring and intervention. Gimbals stabilize multispectral or hyperspectral cameras used to assess crop health, soil conditions, and hydration levels.
- Przykłady zastosowań: Crop stress analysis, yield prediction, variable-rate fertilization mapping, irrigation management, plant counting.
- Korzyści: Stable imagery allows for accurate analysis of spectral signatures. Lightweight gimbals maximize flight time, enabling coverage of large agricultural areas in a single flight. Durability ensures reliable operation in dusty or humid farm environments.
- Cinematography and Broadcasting: Professional aerial cinematography demands exceptionally smooth and stable footage. While larger drones often use sophisticated gimbal systems, even smaller production drones benefit significantly from the weight savings and performance offered by optimized, 3D printed gimbal components.
- Przykłady zastosowań: Capturing smooth, cinematic aerial shots for films, documentaries, commercials, and live event broadcasting.
- Korzyści: Reduced vibration and precise stabilization result in higher quality footage. Lighter gimbals improve UAV agility for capturing dynamic shots and extend battery life for longer takes.
- Environmental Monitoring and Research: Scientists use UAVs to monitor wildlife populations, track environmental changes, study atmospheric conditions, and respond to natural disasters. Customized gimbals are often required to house specialized scientific instruments.
- Przykłady zastosowań: Wildlife tracking (thermal/visual), coastal erosion monitoring, atmospheric particulate sampling, post-disaster damage assessment, glacier monitoring.
- Korzyści: AM allows for the creation of highly specific gimbal designs to accommodate unique research sensors. Lightweighting is critical for maximizing endurance in remote or challenging environments. Corrosion-resistant materials like Ti-6Al-4V are beneficial for marine or coastal monitoring applications.
The breadth of these applications underscores the versatility and growing importance of advanced sensor gimbals. Metal additive manufacturing provides the enabling technology to create components that meet the stringent weight, performance, and customization requirements demanded by these diverse and often critical use cases. Distributors and system integrators serving these markets are increasingly looking towards AM suppliers capable of delivering high-quality, reliable gimbal components.
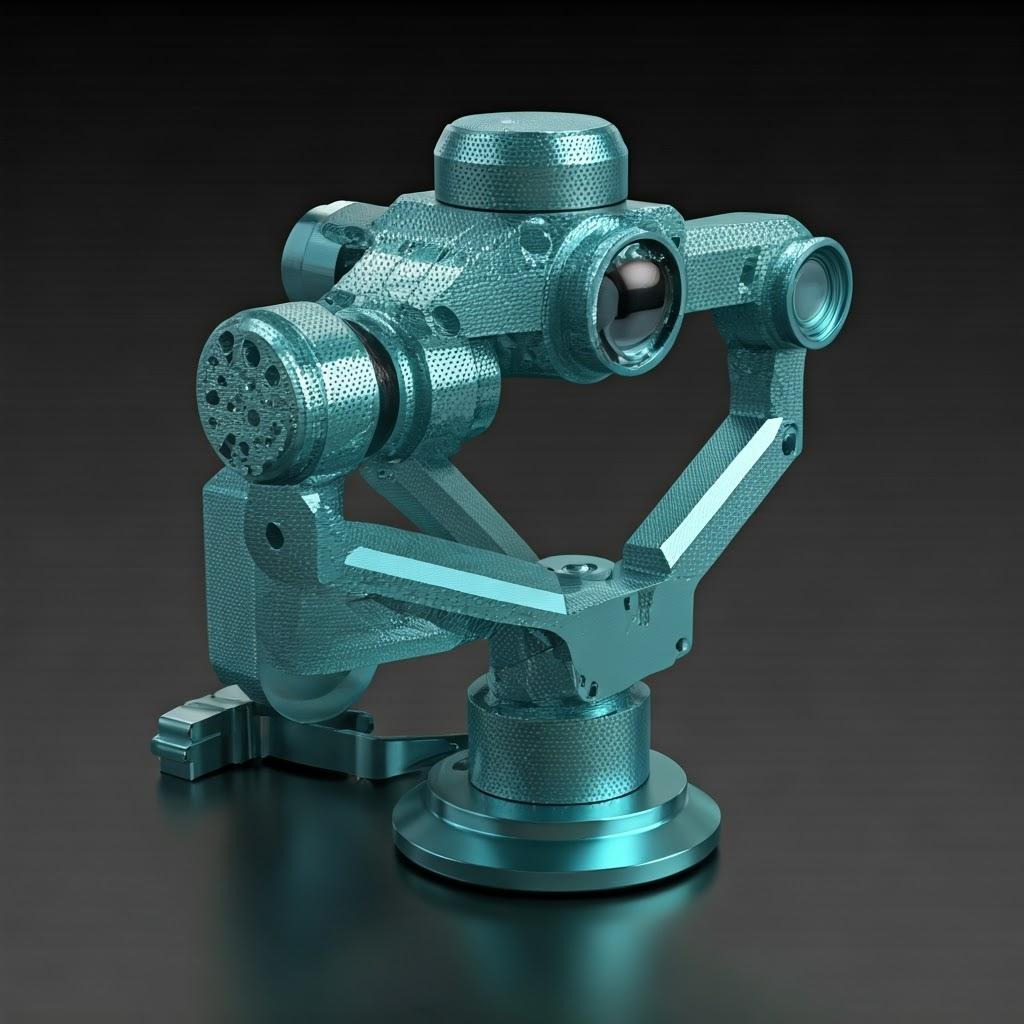
The Additive Advantage: Why Choose Metal 3D Printing for UAV Gimbal Production?
The decision to adopt metal additive manufacturing for UAV gimbal production isn’t merely about embracing a novel technology; it’s a strategic choice driven by a confluence of compelling technical and economic advantages that directly address the limitations of traditional manufacturing methods, primarily CNC machining and casting. While conventional techniques have served the industry well, metal AM offers a paradigm shift, enabling engineers and procurement managers to achieve superior outcomes in terms of performance, efficiency, and design flexibility. Let’s dissect the key benefits that make metal 3D printing a superior choice for manufacturing lightweight, high-performance UAV sensor gimbals:
- Unparalleled Weight Reduction: This is often the most significant driver for adopting AM in aerospace applications.
- Topology Optimization: AM allows for the practical realization of designs generated by topology optimization software. This software mathematically determines the most efficient material distribution to withstand specific load conditions, removing material from non-critical areas and creating organic, load-bearing structures that are incredibly light yet strong. This process can lead to weight savings of 20-50% or even more compared to conventionally designed parts.
- Struktury kratowe: AM makes it possible to integrate complex internal lattice structures within the gimbal’s components. These repeating geometric patterns provide excellent stiffness and structural support with minimal material usage, further contributing to weight reduction without sacrificing rigidity – crucial for maintaining pointing accuracy.
- Material Choice: AM enables the use of advanced lightweight alloys like Aluminum (AlSi10Mg) and Titanium (Ti-6Al-4V) effectively, optimizing the strength-to-weight ratio inherently.
- Revolutionary Design Freedom: AM liberates designers from the constraints imposed by traditional manufacturing processes.
- Geometrie złożone: Features like internal cooling channels for electronics, conformal mounting surfaces, smoothly curved aerodynamic profiles, and intricate internal passageways for wiring can be seamlessly integrated into the design and printed as a single piece. This complexity is often impossible or prohibitively expensive to achieve with subtractive methods.
- Organic Shapes: Engineers can design parts that mimic natural structures, optimized for flow (air or heat) and stress distribution, rather than being limited by the linear movements of cutting tools or the requirements of mold drafts.
- Konsolidacja części: This benefit offers significant downstream advantages.
- Reduced Assembly Time & Cost: Multiple components that would traditionally be manufactured separately and then assembled (often with fasteners like screws and bolts) can be redesigned and printed as a single, monolithic part. This dramatically simplifies the assembly process, saving labor time and cost.
- Improved Reliability: Eliminating fasteners and joints reduces the number of potential failure points (e.g., screws loosening due to vibration), enhancing the overall reliability and structural integrity of the gimbal – a critical factor for aerospace and defense procurement.
- Weight Savings (Indirect): Eliminating fasteners also contributes further to overall weight reduction.
- Szybkie prototypowanie i iteracja: The speed at which designs can be turned into physical metal parts is a game-changer for development cycles.
- Faster Design Validation: Engineers can quickly produce functional metal prototypes to test form, fit, and function, allowing for rapid design iterations and improvements based on real-world testing. This accelerates the development timeline significantly compared to waiting for machined prototypes, which often involve tooling setup and longer lead times.
- Reduced Development Costs: Faster iteration cycles mean less wasted engineering time and quicker convergence on an optimized design, ultimately lowering overall development costs.
- Material Efficiency and Sustainability: AM is inherently less wasteful than traditional subtractive methods.
- Near-Net Shape Production: AM builds parts layer by layer, using only the material needed for the part and its support structures. This contrasts sharply with CNC machining, where a significant portion (often >80-90% for complex aerospace parts) of the initial material block can be machined away as chips (swarf), representing wasted material and energy.
- Powder Reusability: While not infinitely recyclable within a build process due to potential changes in properties, unused metal powder from the build chamber can often be sieved and reused in subsequent builds, further improving material utilization efficiency. Leading powder manufacturers, like Met3dp, focus on powder characteristics that enhance reusability.
- On-Demand Manufacturing and Supply Chain Flexibility: AM enables a more agile and resilient supply chain.
- Zmniejszone zapasy: Parts can be printed as needed, reducing the requirement for large physical inventories of finished goods or spare parts. This is particularly beneficial for high-value, low-volume components like specialized gimbals.
- Distributed Manufacturing: Digital part files can be sent electronically to certified AM service providers located closer to the point of need, potentially reducing shipping times and costs, and mitigating geopolitical supply chain risks.
- Legacy Part Production: AM allows for the recreation of parts for older UAV systems where original tooling may no longer exist, simply requiring a digital model.
Comparison Table: Metal AM vs. Traditional Machining for UAV Gimbals
Cecha | Wytwarzanie przyrostowe metali (AM) | Tradycyjna obróbka CNC |
---|---|---|
Redukcja wagi | Excellent (Topology Opt., Lattices) | Limited (Constrained by subtractive nature) |
Złożoność projektu | Very High (Internal channels, organic shapes) | Moderate to High (Cost increases significantly) |
Konsolidacja części | Excellent (Multiple parts into one) | Limited (Requires assembly) |
Odpady materiałowe | Low (Near-net shape, powder reuse) | High (Significant swarf generation) |
Prototyping Speed | Fast (Direct from CAD) | Slower (Tooling, setup time) |
Wymagane narzędzia | None (Tool-less manufacturing) | Required (Fixtures, cutting tools) |
Ideal Volume | Low to Medium Volume, High Complexity | High Volume, Lower Complexity |
Lead Time (New Part) | Shorter (Especially for complex parts) | Longer (Due to programming, tooling, setup) |
Surface Finish (As-Built) | Rougher (Requires post-processing) | Smoother (Depending on process) |
Dimensional Accuracy (As-Built) | Good (Requires post-processing for tight tol.) | Bardzo dobry |
Export to Sheets
While traditional machining still holds advantages in terms of achievable surface finish and tolerances bez post-processing and potentially lower costs for very simple parts at high volumes, the combined advantages of metal AM, particularly in weight reduction, design freedom, and part consolidation, present an overwhelmingly compelling case for its use in the production of advanced UAV sensor gimbals. For engineers aiming for peak performance and procurement managers seeking reliable, cutting-edge components, metal AM is the definitive manufacturing pathway forward.
Material Matters: Selecting High-Performance Powders like AlSi10Mg & Ti-6Al-4V for Optimal Gimbal Functionality
The success of a metal 3D printed UAV gimbal hinges not only on the design and the printing process but critically on the choice of material. The metal powder used dictates the fundamental properties of the final component – its weight, strength, stiffness, resistance to environmental factors, and thermal behavior. For demanding applications like UAV sensor gimbals, where performance and reliability are non-negotiable, selecting the right high-performance alloy is paramount. Two materials stand out as primary candidates for this application: AlSi10Mg (an aluminum alloy) and Ti-6Al-4V (a titanium alloy). Understanding their distinct characteristics is crucial for engineers and procurement specialists to make informed decisions.
The Importance of Powder Quality:
Before delving into the specific alloys, it’s essential to emphasize the significance of metal powder quality in the additive manufacturing process. The characteristics of the powder directly impact the printing process stability, the density of the final part, and its ultimate mechanical properties. Key powder attributes include:
- Sferyczność: Highly spherical powder particles flow more easily and pack more densely, leading to more uniform layers during printing and reducing the likelihood of voids or porosity in the final part.
- Płynność: Good flowability ensures consistent powder deposition across the build plate, which is critical for achieving dimensional accuracy and consistent material properties.
- Rozkład wielkości cząstek (PSD): A controlled PSD is necessary for achieving high packing density and predictable melting behavior during the laser or electron beam fusion process. Too broad a distribution or excessive fines can lead to issues.
- Czystość: Low levels of impurities and contaminants (like oxygen or nitrogen) are crucial, especially for reactive materials like titanium, to ensure optimal mechanical properties and prevent defects.
Firmy takie jak Met3dp leverage industry-leading powder production technologies, such as Vacuum Induction Melting Gas Atomization (VIGA) and Plasma Rotating Electrode Process (PREP), to manufacture high-quality spherical metal powders. Their advanced systems employ unique nozzle and gas flow designs, ensuring high sphericity, excellent flowability, controlled PSD, and high purity – characteristics essential for producing dense, high-quality metal parts with superior mechanical properties demanded by aerospace and other critical industries. Met3dp’s commitment extends to a wide range of alloys, including not just AlSi10Mg and Ti-6Al-4V, but also specialized materials like TiNi, TiTa, TiAl, TiNbZr, CoCrMo, various stainless steels, and superalloys, catering to diverse AM application needs. Accessing powders with consistent, well-documented quality from reputable suppliers is a cornerstone of successful metal AM.
AlSi10Mg: The Lightweight Workhorse
AlSi10Mg is an aluminum alloy well-known in traditional casting processes, and it has proven to be highly suitable for laser powder bed fusion (LPBF). It offers an excellent combination of low density, good mechanical properties, and favorable thermal conductivity, making it a popular choice for lightweight structural components.
- Kluczowe właściwości:
- Niska gęstość: Approximately 2.67g/cm3, significantly lighter than steels or even titanium. This is its primary advantage for UAV components where weight saving is paramount.
- Dobry stosunek wytrzymałości do wagi: While not as strong as titanium, its very low density results in a competitive strength-to-weight ratio, suitable for many gimbal structures.
- Doskonała przewodność cieplna: Helps dissipate heat generated by gimbal motors or electronics, which can be integrated into the design via internal channels.
- Dobra odporność na korozję: Generally sufficient for typical operating environments, although specific coatings might be considered for marine applications.
- Weldability/Printability: Behaves well during the LPBF process, allowing for relatively fast printing speeds.
- Efektywność kosztowa: Aluminum alloys are generally less expensive than titanium alloys, both in terms of raw material cost and potentially faster printing times.
- Suitability for Gimbals: AlSi10Mg is ideal for gimbal housings, structural frames, and brackets where maximum weight reduction is desired, and the absolute highest strength or temperature resistance is not the primary driver. Its thermal properties are also beneficial for managing heat from integrated electronics.
Ti-6Al-4V (Grade 5): The High-Performance Champion
Ti-6Al-4V, often referred to as Ti64 or Grade 5 Titanium, is the workhorse of the titanium industry, particularly in aerospace. It is renowned for its exceptional combination of high strength, low density (though higher than aluminum), excellent fatigue resistance, and outstanding corrosion resistance, even in harsh environments.
- Kluczowe właściwości:
- Doskonały stosunek wytrzymałości do wagi: Significantly higher than aluminum alloys and many steels. This allows for highly optimized, minimal-mass designs capable of handling substantial loads or vibrations.
- High Strength & Fatigue Resistance: Maintains its strength at moderately elevated temperatures (up to ~300-400°C) and exhibits excellent resistance to fatigue failure, crucial for components subjected to continuous vibration and dynamic loads in UAVs.
- Doskonała odporność na korozję: Forms a stable, passive oxide layer providing outstanding protection against corrosion in most natural and many industrial environments, including saltwater exposure.
- Low Thermal Conductivity: Compared to aluminum, it is more of an insulator. This needs consideration if heat dissipation is a primary design requirement.
- Biokompatybilność: While not relevant for gimbals, its biocompatibility makes it a standard in medical implants.
- Wyższy koszt: Titanium powder is significantly more expensive than aluminum powder, and the printing process can sometimes be slower or require more careful atmospheric control due to its reactivity.
- Suitability for Gimbals: Ti-6Al-4V is the preferred choice for gimbals requiring the absolute highest performance, durability, and strength-to-weight ratio. It’s ideal for highly loaded structural components, critical mounting interfaces, gimbals operating in extreme temperature ranges or corrosive environments (e.g., maritime surveillance UAVs), and defense applications where maximum reliability and robustness are mandated. The higher cost is often justified by the superior performance and longevity in demanding scenarios.
Material Selection Summary Table:
Nieruchomość | AlSi10Mg | Ti-6Al-4V (klasa 5) | Considerations for UAV Gimbals |
---|---|---|---|
Gęstość | Low (~2.67g/cm3) | Moderate (~4.43g/cm3) | AlSi10Mg offers maximum direct weight saving. |
Wytrzymałość do wagi | Dobry | Doskonały | Ti-6Al-4V enables more highly optimized, load-bearing designs. |
Absolute Strength | Umiarkowany | Bardzo wysoka | Ti-6Al-4V for high-load components or extreme durability needs. |
Stiffness (Modulus) | Moderate (~70 GPa) | High (~114 GPa) | Ti-6Al-4V provides greater rigidity, crucial for pointing accuracy. |
Max Service Temp. | Lower (~150-200°C) | Higher (~300-400°C) | Ti-6Al-4V better for high-temperature operational environments. |
Przewodność cieplna | Wysoki | Niski | AlSi10Mg better for heat dissipation; Ti-6Al-4V better insulation. |
Odporność na korozję | Dobry | Doskonały | Ti-6Al-4V essential for marine or chemically harsh environments. |
Możliwość drukowania | Generally Easier/Faster | More Sensitive (Atmosphere control crucial) | Process parameters well-established for both. |
Koszt względny | Niższy | Wyższy | Significant factor; performance requirements justify Ti-6Al-4V cost. |
Typical Post-Processing | Stress Relief, T6 Heat Treatment | Stress Relief, HIP (optional), Annealing | Both require careful thermal post-processing for optimal properties. |
Export to Sheets
Conclusion on Materials:
The choice between AlSi10Mg and Ti-6Al-4V depends heavily on the specific requirements of the UAV gimbal application.
- Wybierz AlSi10Mg when:
- The primary goal is maximum weight reduction at a lower cost.
- Operating temperatures are moderate.
- Absolute strength requirements are not extreme.
- Heat dissipation from integrated components is a benefit.
- Wybierz Ti-6Al-4V when:
- The highest possible strength-to-weight ratio and stiffness are required.
- The gimbal operates in demanding environments (high temperature, corrosive).
- Exceptional fatigue life and durability are critical (e.g., defense applications).
- Cost is secondary to performance and reliability.
Partnering with a knowledgeable AM service provider like Met3dp, which not only supplies high-quality powders but also possesses deep application expertise and state-of-the-art printing equipment, ensures that the chosen material is processed correctly to unlock its full potential, resulting in a UAV sensor gimbal that delivers exceptional performance and reliability in the field. Procurement managers should ensure their suppliers have certified processes for handling and printing these specific aerospace-grade materials.
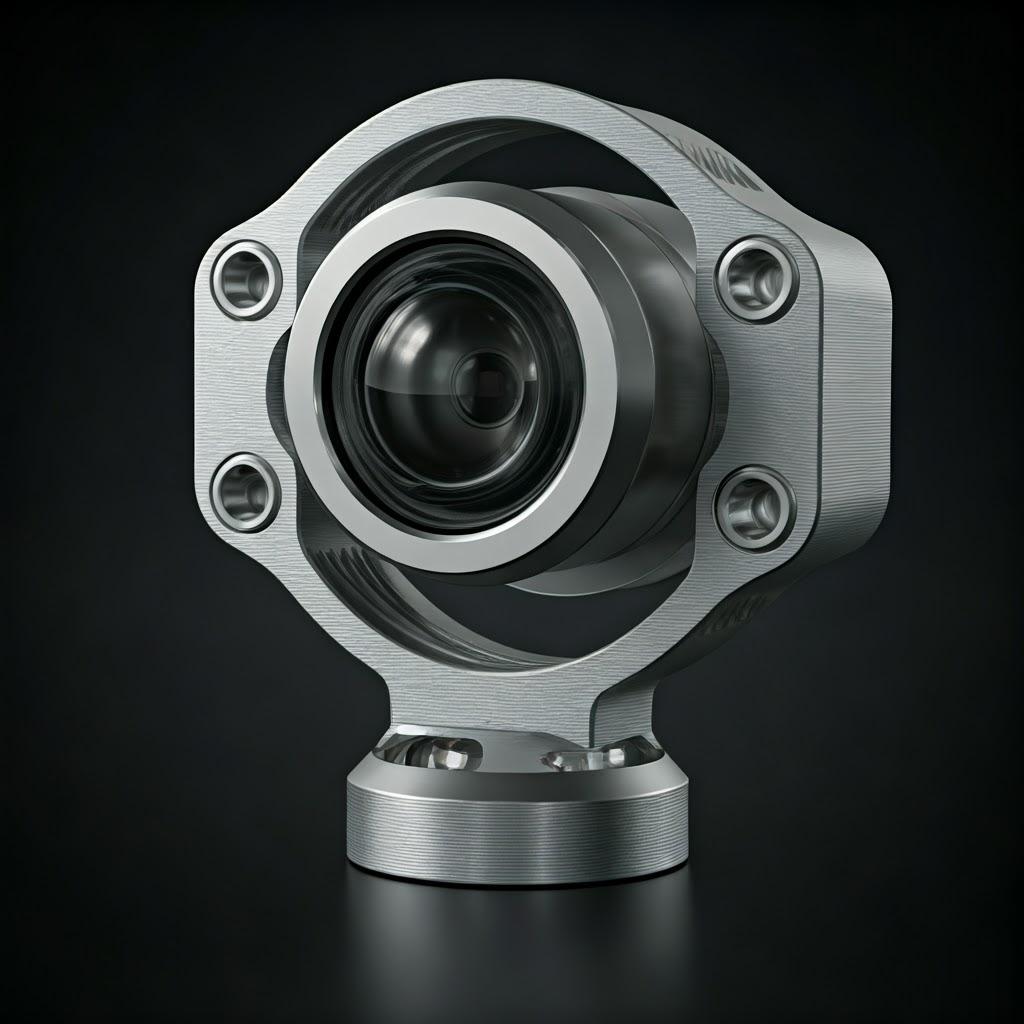
Design for Additive Manufacture (DfAM): Optimizing UAV Gimbal Geometry for 3D Printing Success
Transitioning from traditional manufacturing paradigms to metal additive manufacturing requires more than simply converting an existing CAD file designed for machining into an STL file for printing. To truly harness the transformative potential of AM and achieve the desired outcomes – particularly significant weight reduction and enhanced functionality for UAV gimbals – engineers must embrace Design for Additive Manufacture (DfAM). DfAM is a design philosophy and set of methodologies that specifically leverages the unique capabilities and accounts for the inherent constraints of layer-by-layer fabrication processes. Applying DfAM principles from the outset of the gimbal design process is crucial for optimizing performance, minimizing print time and cost, reducing post-processing efforts, and ensuring the structural integrity and reliability of the final component.
Ignoring DfAM principles often leads to suboptimal results, such as unnecessarily heavy parts, longer print times due to excessive support structures, increased risk of print failures (like warping or cracking), and difficulties during post-processing. For complex systems like sensor gimbals, which involve intricate geometries, moving parts, and integrated electronics, a thoughtful DfAM approach is indispensable.
Core DfAM Principles for Metal AM Gimbals:
- Orientation Optimization: How a part is oriented on the build plate significantly impacts several factors:
- Struktury wsparcia: Orientation determines which features overhang and require support. Minimizing supports reduces print time, material usage, and post-processing effort (support removal can be labor-intensive and potentially damage surfaces). Critical surfaces should ideally be oriented to be self-supporting or require easily removable supports.
- Wykończenie powierzchni: Downward-facing surfaces directly supported by powder tend to have a better finish than upward-facing surfaces or those supported by solid structures. Vertical walls generally have a consistent finish.
- Właściwości mechaniczne: Anisotropy (direction-dependent properties) can exist in AM parts, although it’s often less pronounced in metals compared to polymers, especially after appropriate heat treatment. Orientation might be chosen to align the strongest build direction with the primary load path.
- Zarządzanie temperaturą: Orientation affects heat distribution during the build, influencing residual stress and potential warping.
- Czas budowy: Part height is often the primary driver of build time; orienting the part to minimize its Z-height can speed up the printing process.
- Support Structure Strategy: While minimizing supports is ideal, they are often unavoidable for metal AM due to gravity and thermal stresses.
- Self-Supporting Angles: Designing features with angles typically greater than 45 degrees from the horizontal allows them to be printed without supports (this angle depends on the specific material, machine, and parameters). Incorporating chamfers instead of sharp overhangs is a common strategy.
- Optimized Support Design: When supports are needed, they should be designed for effectiveness during the build (providing stability and heat sinking) but also for ease of removal. Using lighter, tree-like or point/line supports instead of dense blocks can save material and removal time. Access for removal tools must be considered.
- Internal Supports: Supports inside complex internal channels can be extremely difficult or impossible to remove. DfAM focuses on designing internal features to be self-supporting or finding alternative design solutions.
- Thermal Management and Stress Reduction: The rapid heating and cooling inherent in powder bed fusion processes generate significant thermal gradients and residual stresses within the part.
- Gradual Transitions: Avoiding abrupt changes in cross-sectional area helps manage heat flow and reduce stress concentrations. Filleting sharp internal corners is crucial.
- Uniform Wall Thickness: Maintaining consistent wall thicknesses where possible promotes more uniform cooling.
- Stress Relief Features: Incorporating design elements that allow for slight compliance during cooling can sometimes help mitigate stress buildup, although robust thermal post-processing (stress relief cycles) remains essential.
- Simulation: Advanced thermal-mechanical simulation software can predict stress accumulation and distortion, allowing designers to modify the geometry or support strategy proactively.
- Feature Resolution and Minimums: AM processes have limitations on the minimum size of features they can accurately produce.
- Grubość ścianki: There’s a minimum printable wall thickness (typically ~0.4-0.8 mm, depending on the machine and material) below which features may not form reliably.
- Hole Diameter: Small holes (typically < 1 mm) may print undersized or seal over; designing slightly larger or planning for post-drill/reaming is advisable.
- Pin Size: Minimum diameters for pins or rod-like features.
- Gap Size: Minimum clearance required between adjacent features. These parameters should be confirmed with the AM service provider based on their specific equipment, like the systems used at Met3dp, which are known for industry-leading accuracy.
Advanced DfAM Techniques for Gimbals:
- Topology Optimization: As mentioned earlier, this is a cornerstone of lightweighting. Software tools analyze load cases and material properties (AlSi10Mg or Ti-6Al-4V) to sculpt the gimbal structure, removing material where it’s not needed while maintaining required stiffness and strength. The resulting organic, bone-like structures are ideally suited for AM fabrication.
- Struktury kratowe: Replacing solid sections with internal lattice structures (e.g., gyroids, diamond, honeycomb) can further reduce weight while maintaining high stiffness and providing potential benefits like vibration damping. These are virtually impossible to create with traditional methods but straightforward for AM.
- Konsolidacja części: This involves redesigning an assembly of multiple parts into a single, integrated component. For a gimbal, this could mean combining mounting brackets, motor housings, structural arms, and even sensor mounts into one printable piece. Example: A traditional gimbal arm might consist of a machined arm, a separate motor mount bolted on, and potentially a cable clip. Using DfAM, this could be redesigned as a single topology-optimized arm with an integrated motor housing featuring internal cooling channels and built-in conformal channels for routing wiring, all printed as one part. This reduces part count, eliminates fasteners (weight, failure points), and simplifies assembly.
- Function Integration: Embedding functionality directly into the part. This could include:
- Internal Cooling Channels: Designing channels within the gimbal structure to passively or actively cool motors or sensor electronics.
- Conformal Wiring Channels: Creating smooth, internal pathways for electrical wiring, protecting cables and reducing snagging hazards.
- Integrated Fixturing Points: Designing features that aid in post-processing steps like machining or inspection.
Collaborating closely with an experienced AM service provider like Met3dp during the design phase is highly recommended. Their experts understand the nuances of different metody drukowania (like Laser Powder Bed Fusion – LPBF or Selective Electron Beam Melting – SEBM), material behaviors (AlSi10Mg, Ti-6Al-4V), and the specific capabilities of their equipment. They can provide invaluable DfAM guidance, helping engineers optimize gimbal designs for printability, performance, and cost-effectiveness, ensuring the final product fully leverages the additive advantage.
Precision in Flight: Achieving Tight Tolerances, Superior Surface Finish, and Dimensional Accuracy
For a UAV sensor gimbal, precision is not just desirable; it’s fundamental to its function. The gimbal’s primary role is to provide stable pointing accuracy for the sensor payload, compensating for the UAV’s movements and vibrations. This requires components manufactured with tight dimensional tolerances, smooth mating surfaces for bearings and motors, and overall high geometric accuracy to ensure correct assembly and smooth, predictable motion. While metal additive manufacturing offers incredible design freedom, understanding and managing its capabilities regarding tolerances, surface finish, and dimensional accuracy is crucial for producing functional, high-performance gimbals.
Tolerances in Metal AM:
Metal AM processes, such as Laser Powder Bed Fusion (LPBF), which is commonly used for AlSi10Mg and Ti-6Al-4V, can achieve reasonably good dimensional accuracy in the as-built state. However, it’s important to set realistic expectations.
- Typical As-Built Tolerances: Generally, tolerances in the range of ±0.1 mm to ±0.3 mm (or ±0.005 inches per inch) can be expected for well-controlled processes and medium-sized parts. Smaller features might achieve tighter tolerances, while larger parts or those with significant thermal stress challenges might exhibit greater variation. These tolerances are influenced by numerous factors:
- Machine Calibration: Accuracy of the laser/electron beam positioning, layer thickness control, and scanner calibration. Met3dp prides itself on printers delivering industry-leading accuracy and reliability.
- Właściwości materiału: Thermal expansion/contraction coefficients, shrinkage during solidification and cooling.
- Thermal Stresses: Warping and distortion during the build process.
- Part Geometry & Orientation: Complex shapes and orientations can lead to localized overheating or uneven shrinkage.
- Struktury wsparcia: How effectively supports anchor the part and manage heat.
- Charakterystyka proszku: Consistency in powder quality impacts melt pool stability.
- Achieving Tighter Tolerances: For critical features requiring tolerances tighter than what AM can achieve directly (e.g., bearing seats, motor shaft interfaces, precise mounting holes), post-processing machining is typically required. It’s common practice in DfAM to design parts with extra material (machining allowance or “stock”) specifically on these critical surfaces, which is then precision-machined to final tolerances (often achieving ±0.01 mm to ±0.05 mm or better, comparable to conventional machining).
Surface Finish (Roughness):
The surface finish of as-built metal AM parts is inherently rougher than machined surfaces due to the layer-by-layer fusion of powder particles.
- Typical As-Built Surface Roughness (Ra): Values typically range from 6 µm to 25 µm (Ra), depending on:
- Orientation: Upward-facing surfaces are generally rougher than downward-facing or vertical walls due to the way powder particles adhere. Surfaces directly supported by other structures can also show witness marks after support removal.
- Grubość warstwy: Thinner layers generally produce slightly smoother surfaces but increase build time.
- Process Parameters: Laser power, scan speed, beam offset.
- Materiał: Different alloys can exhibit slightly different surface characteristics.
- Poprawa wykończenia powierzchni: For applications requiring smoother surfaces (e.g., reducing friction, improving fatigue life, ensuring proper sealing, aesthetics), various post-processing techniques are employed:
- Abrasive Blasting (Bead/Sand Blasting): Provides a uniform matte finish, effective for removing semi-sintered particles but doesn’t significantly improve Ra value.
- Tumbling/Vibratory Finishing: Uses abrasive media in a tumbling barrel or vibratory bowl to smooth surfaces and round edges, particularly effective for batches of smaller parts.
- Micro-Machining/Polishing: Can achieve very smooth, mirror-like finishes (Ra < 0.1 µm) on specific surfaces through CNC machining, grinding, lapping, or manual polishing.
- Electropolishing: An electrochemical process that removes a thin layer of material, smoothing peaks and valleys, particularly effective on certain alloys like stainless steels, but less common for Al/Ti alloys unless specific requirements dictate it.
For gimbals, critical interfaces will almost certainly require post-machining and potentially polishing to achieve the necessary smoothness and dimensional accuracy for frictionless movement and precise component mating.
Dimensional Accuracy and Geometric Control (GD&T):
Beyond linear tolerances and surface roughness, overall geometric accuracy – encompassing factors like flatness, parallelism, perpendicularity, and position of features (defined by Geometric Dimensioning and Tolerancing – GD&T) – is vital for gimbal assembly and function.
- Wyzwania: Residual stress and thermal distortion during the AM build are the primary challenges to achieving high geometric accuracy in the as-built state, especially for larger or more complex gimbal components.
- Mitigation Strategies:
- Simulation: Predicting distortion to optimize orientation and support strategy.
- Kontrola procesu: Maintaining stable melt pool conditions and build chamber environment.
- Optimized Scan Strategies: Using specific laser scanning patterns (e.g., island scanning) to manage heat input.
- Robust Support Structures: Anchoring the part securely to the build plate.
- Stress Relief Heat Treatment: Crucial post-processing step to relax internal stresses before removing the part from the build plate or machining critical features.
- Post-Machining: Correcting geometric deviations on critical datums and functional surfaces.
Metrology and Inspection:
Verifying that the final gimbal components meet the specified tolerances and geometric requirements is essential.
- Techniques: Coordinate Measuring Machines (CMMs), structured light 3D scanning, and traditional measurement tools are used to inspect parts throughout the manufacturing process (after printing, after heat treatment, after final machining).
- Importance: Rigorous inspection ensures that only conforming parts proceed to assembly, guaranteeing the performance and reliability of the final gimbal system. Reputable AM service providers will have robust quality management systems incorporating these inspection techniques.
In summary, while metal AM offers pathways to create lightweight and complex gimbal geometries, achieving the high precision required for functionality necessitates a combined approach: intelligent DfAM, careful process control during printing, essential thermal post-processing, and targeted post-machining/finishing for critical features. Understanding these capabilities and limitations allows engineers to design effectively and procurement managers to specify requirements accurately when sourcing 3D printed gimbal components.
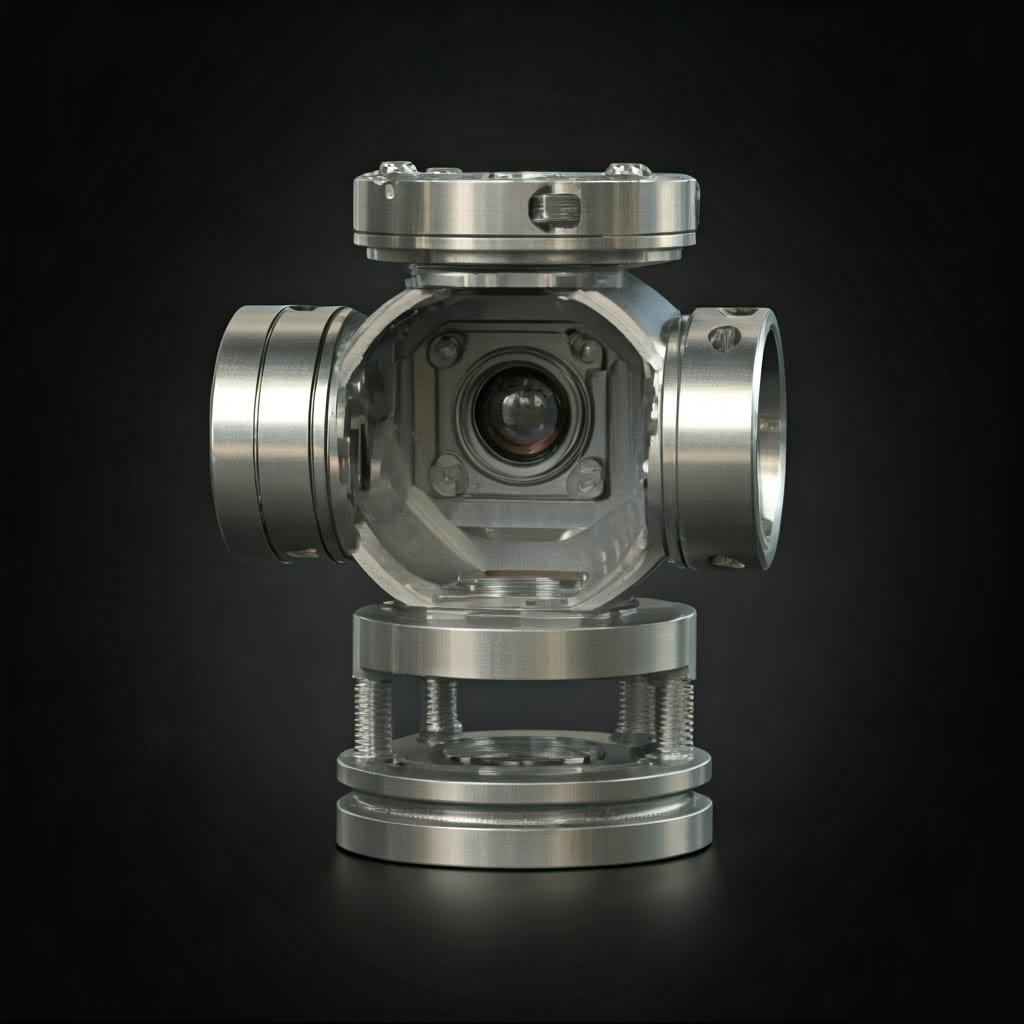
Beyond the Build: Essential Post-Processing Steps for Functional UAV Gimbals
Producing a metal UAV gimbal component doesn’t end when the 3D printer completes the build cycle. The “green” part emerging from the machine requires a series of crucial post-processing steps to transform it from a near-net-shape object into a functional, reliable, and finished component ready for assembly. These steps are not optional extras; they are integral to achieving the desired material properties, dimensional accuracy, surface finish, and overall performance required for demanding applications like UAV sensor stabilization. Understanding this workflow is vital for engineers designing the parts and for procurement managers evaluating potential AM suppliers and accounting for total manufacturing time and cost.
The specific post-processing chain can vary depending on the material (AlSi10Mg vs. Ti-6Al-4V), the complexity of the part, the chosen AM process (LPBF primarily for these materials), and the specific functional requirements. However, a typical workflow includes the following key stages:
- Stress Relief / Heat Treatment: This is often the first critical step, performed while the part may still be attached to the build plate.
- Cel: The rapid heating/cooling cycles during AM create significant internal stresses within the metal. These stresses can cause warping or distortion upon removal from the build plate or during subsequent machining, and they can negatively impact mechanical properties, particularly fatigue life. Stress relief heat treatment involves heating the part to an elevated temperature (below the melting point) and holding it for a specific duration, allowing the microstructure to relax and reduce internal stresses.
- Material Specific Cycles:
- AlSi10Mg: Typically undergoes a stress relief cycle followed by a solution treatment and artificial aging (e.g., T6 heat treatment) to achieve optimal strength through precipitation hardening. The T6 cycle significantly increases the yield strength and ultimate tensile strength compared to the as-built state.
- Ti-6Al-4V: Requires a stress relief cycle (often performed in a vacuum or inert atmosphere furnace to prevent oxidation) at higher temperatures than aluminum. Depending on the application, Hot Isostatic Pressing (HIP) might also be employed. HIP combines high temperature and high pressure to close internal voids/porosity, further improving density and fatigue properties, which is often specified for critical aerospace components. Annealing cycles might also be used to optimize ductility or fracture toughness.
- Importance: Performing stress relief before support removal or significant machining is crucial to prevent distortion as locked-in stresses are released.
- Part Removal from Build Plate: Once thermally stabilized, the part needs to be separated from the build plate.
- Metody: This is typically done using wire EDM (Electrical Discharge Machining), band sawing, or sometimes manual cutting, depending on the part size, geometry, and support structure interface. Care must be taken not to damage the part during this process.
- Usunięcie konstrukcji wsporczej: One of the most labor-intensive post-processing steps, especially for complex geometries with internal supports.
- Metody: Supports are removed using manual tools (pliers, grinders, chisels), CNC machining, or sometimes specialized techniques like electrochemical machining. Access can be challenging, particularly for internal channels designed into gimbals for wiring or cooling.
- DfAM Impact: The effort required here highlights the importance of DfAM principles aimed at minimizing the number and complexity of support structures. Designing for accessibility is key.
- Surface Impact: Support removal often leaves witness marks or rougher areas (“support scars”) on the part surface, which may require further finishing.
- Machining (CNC): Essential for achieving tight tolerances and specific surface finishes on critical features.
- Applications for Gimbals:
- Bearing Seats/Bores: Require precise diameters and smooth finishes for proper bearing fit and function.
- Motor Mount Interfaces: Need accurate dimensions and flatness for correct motor alignment.
- Sensor Mounting Surfaces: Require specific flatness, perpendicularity, or positional accuracy.
- Mating Surfaces: Ensuring precise fit between different gimbal components or the gimbal and the UAV airframe.
- Threaded Holes: Tapping threads for fasteners.
- Proces: Typically involves 3-axis or 5-axis CNC milling or turning. Requires careful fixture design to hold the often complex AM part securely without distortion. The machining allowance specified during DfAM is removed to reach final dimensions.
- Applications for Gimbals:
- Wykończenie powierzchni: Improves surface quality for functional or aesthetic reasons.
- Common Techniques:
- Bead Blasting: Creates a uniform, non-directional matte finish, often used as a standard finish for aesthetic consistency and removing minor blemishes.
- Tumbling/Vibratory Finishing: Smooths surfaces and deburrs edges, good for smaller components.
- Polerowanie: Achieves very smooth, low-Ra finishes on specific surfaces requiring low friction or high aesthetic quality.
- Anodizing (for Aluminum): Provides a hard, wear-resistant, and corrosion-resistant surface layer for AlSi10Mg parts, and allows for coloring.
- Chemical Conversion Coatings (e.g., Chromate for Al, Phosphate for Ti): Improve corrosion resistance and paint adhesion.
- Painting/Powder Coating: For specific color requirements or enhanced environmental protection.
- Common Techniques:
- Czyszczenie: Removing residual powder, machining fluids, blasting media, and other contaminants is crucial before inspection and assembly. Ultrasonic cleaning baths are often used.
- Inspection and Quality Control: Final verification that the part meets all specifications.
- Metody: Dimensional inspection (CMM, 3D scanning), surface finish measurement, visual inspection, and potentially Non-Destructive Testing (NDT) like X-ray or CT scanning to check for internal defects (porosity, cracks), especially for flight-critical components.
Supplier Capability:
The need for this multi-stage post-processing workflow highlights the importance of choosing an AM service provider with comprehensive capabilities. Ideally, the supplier should have in-house or tightly controlled, qualified partners for all necessary steps, from heat treatment and machining to finishing and inspection. This ensures seamless integration, consistent quality control, and often shorter overall lead times compared to managing multiple vendors. Companies like Met3dp, positioning themselves as providers of comprehensive additive manufacturing solutions, understand this integrated workflow and often build relationships or internal capabilities to manage these critical post-processing stages effectively. Procurement managers should inquire about a supplier’s end-to-end capabilities when sourcing complex components like UAV gimbals.
Navigating Challenges: Overcoming Hurdles in Metal 3D Printing for Gimbals
While metal additive manufacturing offers transformative advantages for producing lightweight and complex UAV gimbals, it’s not without its technical challenges. Successfully navigating these potential hurdles requires a deep understanding of the process physics, careful planning during the design phase (DfAM), meticulous process control during printing, and rigorous post-processing and quality assurance. Awareness of these challenges allows engineers and procurement managers to proactively address them and partner effectively with experienced AM service providers.
Common Challenges and Mitigation Strategies:
- Warping and Distortion:
- Cause: Significant temperature gradients between the molten pool and surrounding material lead to expansion and contraction, generating internal stresses. As layers build up, these stresses can accumulate and cause the part to warp or distort, sometimes even detaching from the build plate or supports. This is particularly prevalent in large flat sections or asymmetric designs.
- Mitigation:
- Thermal Simulation: Using software to predict areas of high stress and potential distortion before printing.
- Optimized Orientation & Supports: Orienting the part to minimize large flat surfaces parallel to the build plate and using robust support structures designed to counteract shrinkage forces and provide thermal pathways.
- Build Plate Heating: Preheating the build plate (common in LPBF, essential in EBM) reduces the thermal gradient.
- Optimized Scan Strategies: Employing specific laser scanning patterns (e.g., dividing layers into smaller ‘islands’) helps distribute heat more evenly.
- Ulga w stresie: Performing thermal stress relief immediately after printing and before removing supports is critical.
- Naprężenie szczątkowe:
- Cause: Even if macroscopic warping is controlled, significant residual stresses can remain locked within the printed part. These stresses can compromise the part’s mechanical performance (especially fatigue life) and lead to distortion during subsequent machining when material is removed.
- Mitigation:
- Optymalizacja parametrów procesu: Fine-tuning laser power, scan speed, layer thickness, etc., to minimize stress induction.
- Post-Build Heat Treatment: Stress relief cycles are the primary method for significantly reducing residual stresses to acceptable levels. For Ti-6Al-4V, HIP can also help relieve stress while closing porosity. The effectiveness of these treatments is paramount.
- Porowatość:
- Cause: The presence of small voids or pores within the printed material can degrade mechanical properties (strength, fatigue life) and act as crack initiation sites. Porosity can arise from several sources:
- Gas Porosity: Trapped gas (e.g., Argon used in the build chamber, or dissolved gases in the powder) forming bubbles during solidification.
- Lack-of-Fusion Porosity: Insufficient energy input leading to incomplete melting and bonding between powder particles or successive layers.
- Powder Quality Issues: Entrained gas within powder particles (e.g., from poor atomization) or irregular powder shapes preventing dense packing.
- Mitigation:
- Parameter Optimization: Developing robust process parameters with a sufficiently large processing window to ensure complete fusion. This involves extensive experimentation and characterization by the AM provider.
- Powder Quality Control: Using high-quality, spherical powders with low internal gas content and controlled PSD is crucial. Sourcing from reputable suppliers like Met3dp, who utilize advanced atomization techniques like VIGA and PREP focused on achieving high sphericity and purity, is essential. Regular powder testing and careful handling/recycling protocols are also necessary.
- Prasowanie izostatyczne na gorąco (HIP): Particularly effective for reducing porosity in Ti-6Al-4V for critical applications, although it adds cost and time.
- Cause: The presence of small voids or pores within the printed material can degrade mechanical properties (strength, fatigue life) and act as crack initiation sites. Porosity can arise from several sources:
- Support Removal Difficulties:
- Cause: Supports, especially dense ones or those located in intricate internal channels or hard-to-reach areas, can be challenging, time-consuming, and costly to remove without damaging the part surface.
- Mitigation:
- DfAM: Designing parts to be self-supporting where possible, using optimized support types (e.g., thin-walled, tree-like), and ensuring access for removal tools. Explicitly designing gimbal features like internal channels to avoid the need for internal supports is a key DfAM goal.
- Material Choice: Some support materials or interface layers are designed to be more easily removed (less common in direct metal printing but evolving).
- Skilled Labor: Requires experienced technicians with the right tools and techniques.
- Powder Handling and Safety:
- Cause: Fine metal powders, especially reactive materials like Titanium and Aluminum, can be hazardous if not handled correctly. They pose inhalation risks and can be flammable or explosive under certain conditions (e.g., dust clouds). Maintaining powder purity is also critical.
- Mitigation:
- Controlled Environments: Using appropriate enclosures, ventilation, and inert atmosphere handling systems (especially for Titanium).
- Środki ochrony indywidualnej (PPE): Respirators, conductive clothing, gloves, eye protection.
- Grounding and Spark Prevention: Preventing static discharge.
- Odpowiedni trening: Ensuring personnel are fully trained on safe powder handling, storage, disposal, and emergency procedures.
- Powder Management Systems: Implementing rigorous procedures for powder traceability, sieving, blending, and quality testing to prevent contamination and ensure consistency.
- Quality Assurance and Consistency:
- Cause: Ensuring that every part produced meets the required specifications, build after build, requires robust quality management. Variations in machine performance, powder batches, or environmental conditions can potentially affect part quality.
- Mitigation:
- Process Monitoring: Utilizing in-situ monitoring tools (melt pool monitoring, thermal imaging) to detect anomalies during the build.
- Rigorous QA Procedures: Implementing comprehensive quality management systems (e.g., ISO 9001, AS9100 for aerospace) covering powder management, machine calibration, process validation, post-processing control, and part inspection (dimensional, material testing, NDT).
- Traceability: Maintaining detailed records linking specific parts to powder batches, machine parameters, and post-processing steps.
- Experienced Partner: Collaborating with established AM service providers like Met3dp, who possess decades of collective expertise, industry-leading equipment, and a demonstrated commitment to quality through advanced powder production and printer technology, is arguably the most effective mitigation strategy. Their experience allows them to anticipate and manage these challenges effectively.
Successfully implementing metal AM for high-stakes components like UAV gimbals requires acknowledging and proactively managing these challenges. By leveraging DfAM, partnering with experienced suppliers who prioritize quality control and material science, and implementing rigorous post-processing, manufacturers can reliably produce lightweight, high-performance gimbals that deliver a significant competitive edge.
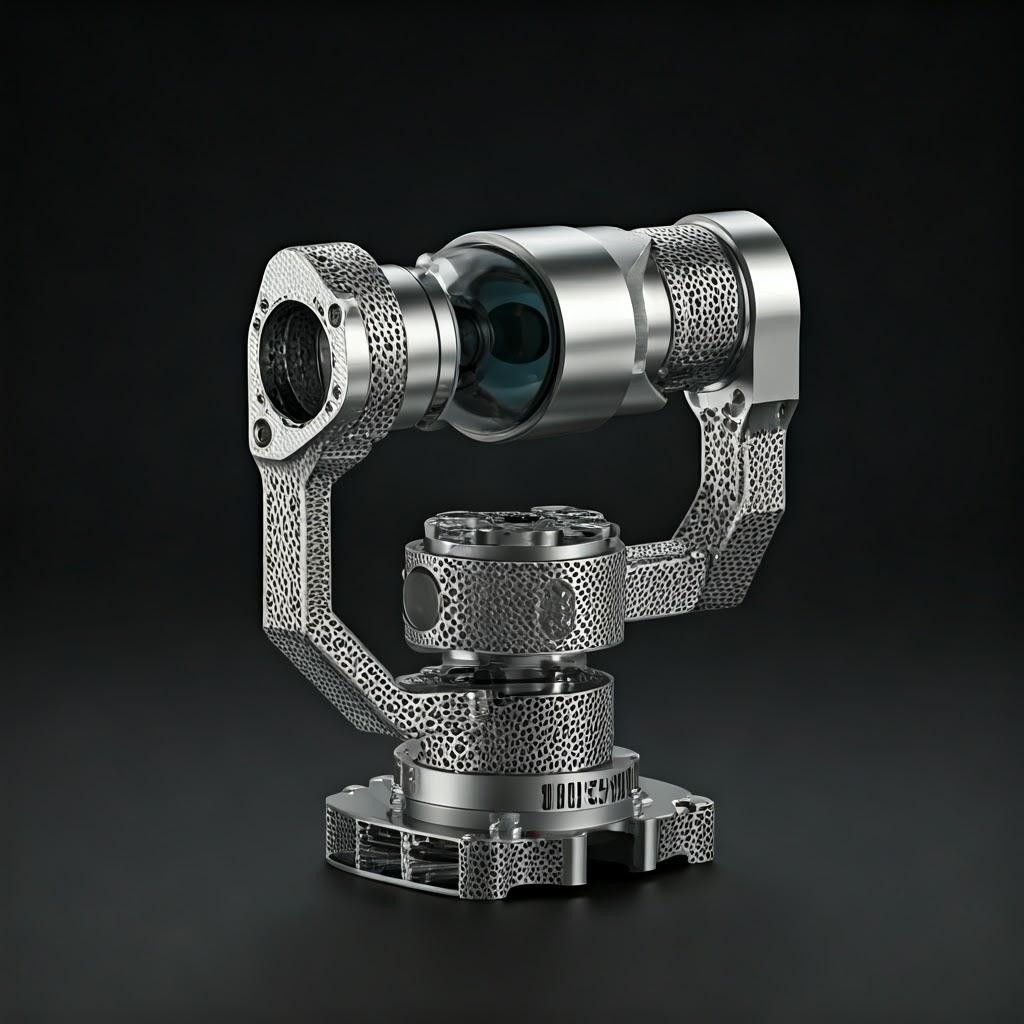
Partnering for Precision: How to Select the Right Metal 3D Printing Service Provider for UAV Components
Choosing the right manufacturing partner is as critical as perfecting the gimbal design itself, especially when dealing with advanced technologies like metal additive manufacturing for demanding applications such as UAV components. The quality, reliability, and performance of the final 3D printed gimbal are directly linked to the expertise, equipment, processes, and quality systems of the service provider you select. Making an informed decision requires careful evaluation based on a set of key criteria tailored to the specific needs of producing high-performance, often flight-critical, metal parts. For engineers and procurement managers navigating the AM landscape, here’s a comprehensive guide on what to look for in a metal 3D printing service provider:
Key Evaluation Criteria:
- Industry Experience and Application Expertise:
- Track Record: Does the provider have demonstrable experience in the aerospace, defense, or UAV sectors? Ask for case studies, examples of similar projects (within confidentiality limits), and references. Understanding the unique demands and standards of these industries is crucial.
- Problem Solving: Can they showcase instances where they helped clients overcome specific challenges related to lightweighting, thermal management, or complex geometries in relevant applications?
- Material Expertise and Certification:
- Specjalizacja: Do they specialize in processing the specific materials required, namely AlSi10Mg and Ti-6Al-4V? This includes certified handling procedures, validated process parameters, and robust powder management (storage, sieving, testing, traceability).
- Jakość materiału: Do they source high-quality powders from reputable manufacturers, or ideally, produce their own high-grade powders? A provider like Met3dp, which employs advanced Gas Atomization and PREP technologies to manufacture its own range of high-sphericity, high-purity metal powders (including AlSi10Mg, Ti-6Al-4V, and specialized alloys like TiNi, TiTa, CoCrMo), offers a distinct advantage in controlling material quality from the source.
- Documentation: Can they provide material certifications and test reports verifying the properties of the printed materials?
- Technology and Equipment:
- Appropriate AM Process: Do they operate the most suitable AM technology, typically Laser Powder Bed Fusion (LPBF/SLM) for the fine features and surface finish often required for gimbals in AlSi10Mg and Ti-6Al-4V? Do they also offer complementary technologies like Electron Beam Melting (SEBM), potentially beneficial for certain Ti-6Al-4V applications?
- Machine Quality and Maintenance: Are their machines from reputable manufacturers? What are their calibration and preventative maintenance schedules? Consistent machine performance is key to part quality. Met3dp utilizes printers delivering industry-leading print volume, accuracy, and reliability, crucial for mission-critical parts.
- Objętość kompilacji: Do their machines have a build volume sufficient for the size of your gimbal components?
- Capacity: Do they have sufficient machine capacity to meet your prototyping and potential production volume requirements within acceptable lead times?
- Quality Management Systems (QMS) and Certifications:
- Essential Certifications: At a minimum, look for ISO 9001 certification, demonstrating a commitment to quality processes.
- Aerospace Standard (Critical): For flight components or defense applications, AS9100 certification is often mandatory. This standard incorporates ISO 9001 requirements but adds stringent criteria specific to the aerospace industry, covering aspects like traceability, risk management, and process control. Working with an AS9100 certified supplier provides a high level of assurance.
- Process Validation: Do they have documented procedures for process validation to ensure repeatability and consistency?
- End-to-End Capabilities (Post-Processing & Inspection):
- Integrated Services: Does the provider offer a comprehensive suite of in-house or tightly managed post-processing services, including stress relief/heat treatment (with certified furnaces and documented cycles for AlSi10Mg T6, Ti-6Al-4V stress relief/annealing/HIP), CNC machining, surface finishing, and cleaning? Managing the entire workflow under one roof or through a single point of contact streamlines the process, improves quality control, and can reduce lead times.
- Metrology and Inspection: What are their inspection capabilities? Do they have CMMs, 3D scanners, surface profilometers, and NDT capabilities (X-ray, CT) if required for critical part verification?
- Technical Support and DfAM Expertise:
- Collaboration: Are their engineers available to collaborate on design optimization (DfAM)? Can they provide expert advice on material selection, orientation strategy, support generation, and tolerance achievement? This collaborative approach is invaluable for maximizing the benefits of AM.
- Simulation Capabilities: Do they offer thermal or structural simulation services to predict and mitigate potential issues like warping or stress concentration?
- Communication, Responsiveness, and Project Management:
- Clear Communication: Is communication clear, professional, and timely? Do they provide regular updates on project status?
- Quoting Process: Is their quoting process transparent and detailed, clearly outlining all included steps and potential variables?
- Project Management: Do they assign a dedicated point of contact for your project?
- Location and Logistics:
- Wysyłka: Consider shipping costs and times, especially for international suppliers. A provider like Met3dp, headquartered in Qingdao, China, serves a global market but logistics need to be factored in.
- Export Controls: Ensure compliance with any relevant export control regulations (e.g., ITAR in the US) if dealing with defense-related components.
Supplier Evaluation Checklist (Example):
Kryteria | Ideal Standard | Notes / Supplier Score |
---|---|---|
Doświadczenie w branży | Proven Aerospace/UAV/Defense Projects | |
Material Expertise (Al/Ti) | Certified Handling, Validated Parameters | |
Jakość proszku | High-Quality Source / In-house Production (e.g., Met3dp) | |
Technology (LPBF/SLM) | State-of-the-Art, Well-Maintained Machines | |
Build Volume & Capacity | Meets Project Needs | |
QMS Certification | ISO 9001 (Minimum), AS9100 (Crucial) | |
Heat Treatment Capability | In-house / Certified Partner (Vacuum/Inert Atm.) | |
CNC Machining Capability | In-house / Certified Partner (Precision) | |
Surface Finishing Capability | Required Options Available (Blasting, Anodizing) | |
Inspection & Metrology | CMM, 3D Scan, NDT (if needed) | |
DfAM Support | Collaborative Engineering Available | |
Communication & Responsiveness | Clear, Timely, Professional | |
Czas realizacji i koszt | Competitive and Transparent | |
References & Case Studies | Available and Relevant |
Export to Sheets
Selecting the right partner is an investment in the success of your project. Thoroughly vetting potential suppliers against these criteria will significantly increase the likelihood of receiving high-quality, reliable 3D printed metal gimbals that meet the demanding requirements of UAV applications. Look for partners like Met3dp who offer a holistic approach, combining advanced material science, cutting-edge printing technology, and deep application expertise.
Understanding the Investment: Key Cost Factors and Lead Time Expectations for 3D Printed Gimbals
While metal additive manufacturing enables the creation of superior, lightweight UAV gimbals, it’s essential for engineers and procurement managers to understand the factors that drive the cost and influence the production lead time. Having realistic expectations allows for accurate budgeting, project planning, and effective comparison between different manufacturing options or service providers. Metal AM costs are typically driven by a combination of material consumption, machine time, labor, and specialized post-processing requirements.
Key Cost Factors:
- Koszt materiałów:
- Powder Price: The cost per kilogram of the metal powder is a primary driver. Ti-6Al-4V powder is significantly more expensive (often 5-10 times or more) than AlSi10Mg powder due to raw material costs and more complex atomization processes.
- Amount Consumed: This includes the material in the final part oraz the material used for support structures. While unused powder can often be recycled, there are handling and testing costs associated with this. DfAM efforts focused on lightweighting and minimizing supports directly reduce material consumption.
- Machine Time:
- Build Preparation: Time taken to slice the CAD model, generate support structures, plan the build layout (nesting multiple parts can reduce per-part machine time), and set up the machine.
- Printing Duration: The actual time the AM machine spends printing the part(s). This is heavily influenced by:
- Part Volume: Larger parts naturally take longer.
- Part Height (Z-axis): Build time is often proportional to the number of layers, so taller parts take longer.
- Part Complexity & Density: Intricate features or dense lattice structures can increase scanning time per layer.
- Support Volume: Printing supports adds to the overall build time.
- Materiał: Some materials may require slower printing parameters for optimal results.
- Machine Depreciation & Overheads: The high capital cost of industrial metal AM machines, maintenance, facility costs, and energy consumption are factored into the hourly machine rate charged by service providers.
- Koszty pracy:
- Setup & Operation: Skilled technicians required for machine setup, build monitoring, and removal.
- Post-Processing Labor: This can be significant, particularly for:
- Usuwanie wsparcia: Manual removal of complex supports requires time and skill.
- Obróbka skrawaniem: Programming and operating CNC machines.
- Wykończenie powierzchni: Manual polishing or preparation for coatings.
- Inspection: Time for CMM programming, scanning, and analysis.
- Koszty przetwarzania końcowego:
- Heat Treatment / HIP: Furnace time, energy consumption, and the cost of using specialized equipment (vacuum furnaces, HIP units) contribute to the cost. HIP is a particularly expensive step often reserved for the most critical Ti-6Al-4V components.
- Obróbka skrawaniem: Costs associated with CNC machine time, tooling, and programming.
- Wykończenie powierzchni: Costs of consumables (blasting media, polishing compounds), equipment usage, and specialized processes like anodizing or coating.
- Quality Assurance & Inspection:
- Standard Inspection: Costs associated with dimensional checks (CMM, scanning).
- Badania nieniszczące (NDT): X-ray or CT scanning, if required for verifying internal integrity, adds significant cost.
- Documentation: Time spent generating compliance reports and traceability documentation, especially for certified parts (e.g., AS9100).
- Non-Recurring Engineering (NRE) Costs (Potentially):
- Design Optimization (DfAM): If significant redesign effort is required by the service provider.
- Simulation: Costs for thermal or structural simulation if performed as part of the service.
Illustrative Cost Breakdown (Example – Highly Variable):
Składnik kosztów | Typical % Range (AlSi10Mg) | Typical % Range (Ti-6Al-4V) | Uwagi |
---|---|---|---|
Materiał | 10-25% | 30-50% | Ti-6Al-4V powder cost dominates. |
Machine Time | 30-50% | 25-40% | Longer builds, but lower % due to Ti cost. |
Labor (Setup/Post-Proc) | 20-40% | 15-30% | Support removal & finishing are key drivers. |
Obróbka cieplna | 5-10% | 5-15% (Higher if HIP needed) | Essential step for both materials. |
Machining/Finishing | 5-15% | 5-15% | Depends heavily on tolerance requirements. |
QA/Inspection | 3-8% | 3-10% (Higher if NDT needed) | Critical for ensuring quality. |
Export to Sheets
Lead Time Expectations:
The total time from order placement to receiving finished parts can vary significantly based on several factors.
- Typical Timeline Components:
- Design Review & Quoting: 1-5 business days.
- Build Preparation & Scheduling: 1-5 business days (depends on machine availability/queue).
- Drukowanie: 1-7+ days (highly dependent on part size, height, complexity, and quantity/nesting).
- Przetwarzanie końcowe:
- Stress Relief/Heat Treatment: 1-3 days (including furnace time and cooling).
- Support Removal/Basic Finishing: 1-3 days.
- CNC Machining: 2-7+ days (depends on complexity and machine shop scheduling).
- Additional Finishing (Anodizing, etc.): 2-5 days.
- Inspection: 1-2 days.
- Wysyłka: 1-7+ days (depends on location and shipping method).
- Factors Influencing Lead Time:
- Częściowa złożoność: More complex parts require longer print and post-processing times.
- Ilość: Larger batches may require multiple builds or longer single builds.
- Printer Queue: Availability of suitable machines at the service provider.
- Wymagania dotyczące przetwarzania końcowego: Extensive machining or specialized finishing significantly extends lead time.
- Dostępność materiałów: Ensuring the specific powder batch is in stock.
- Current Date Considerations: As of Friday, April 25, 2025, global supply chains and specific provider backlogs can influence lead times. Always confirm current estimates with your chosen supplier.
- Indicative Lead Times:
- Simple Prototype (AlSi10Mg, minimal post-processing): 1-2 tygodnie
- Complex Prototype (Ti-6Al-4V, heat treat, basic machining): 2-4 tygodnie
- Small Batch (e.g., 5-10 units, AlSi10Mg, full post-processing): 3-6 tygodni
- Small Batch (e.g., 5-10 units, Ti-6Al-4V, full post-processing + HIP/NDT): 5-8+ weeks
It’s crucial to discuss specific project requirements with potential suppliers to get accurate cost estimates and realistic lead time projections. Transparency from the supplier regarding all cost components and process steps is key to effective project planning and management.
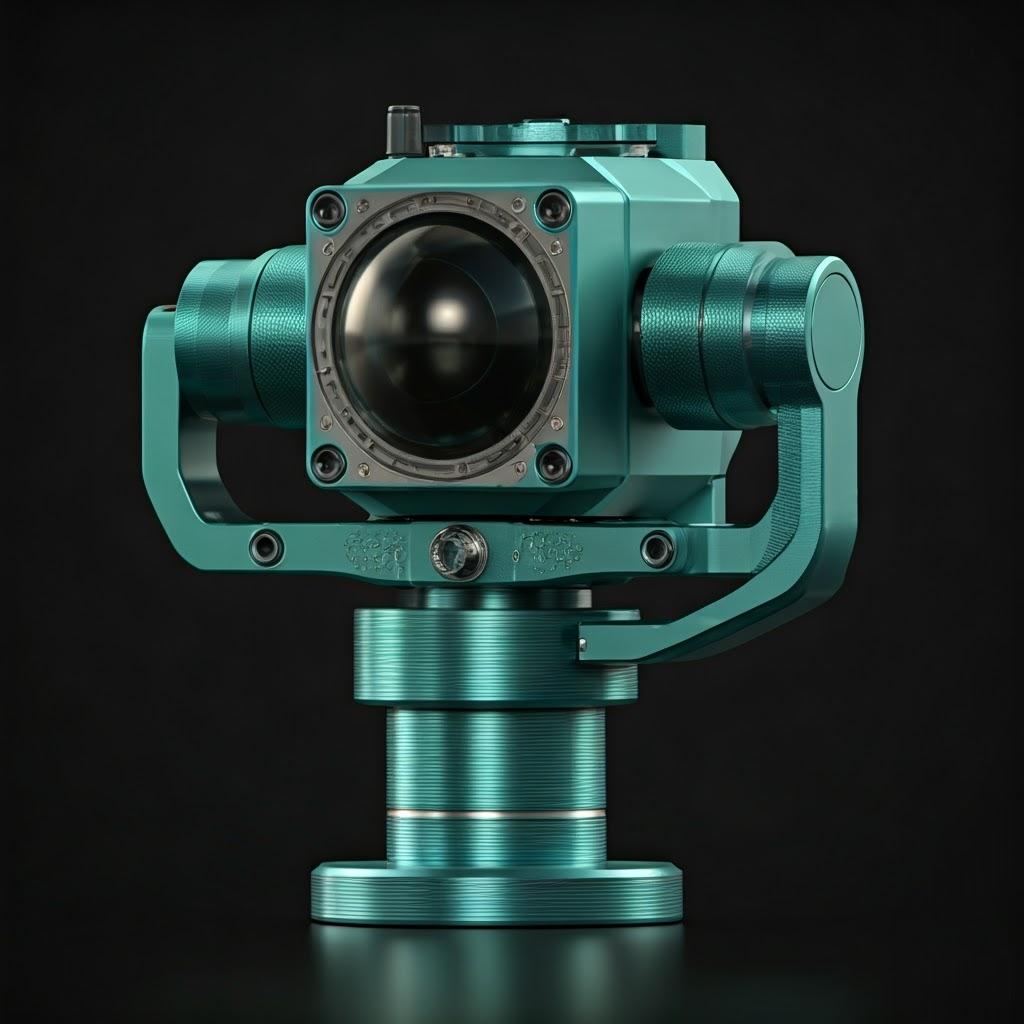
Frequently Asked Questions (FAQ) about 3D Printed UAV Gimbals
As metal additive manufacturing becomes more prevalent in the production of UAV components, engineers, designers, and procurement managers often have questions about its specific application to sensor gimbals. Here are answers to some frequently asked questions:
Q1: How much weight can typically be saved by using metal 3D printing for a UAV gimbal compared to traditional machining?
- A: Significant weight savings are achievable, often ranging from 20% to 50% or even more, compared to traditionally machined components designed for the same function. However, this level of weight reduction is typically not achieved by simply printing an existing design. The key lies in leveraging Design for Additive Manufacture (DfAM) principles, particularly optymalizacja topologii and the integration of lattice structures. Topology optimization software identifies and removes non-essential material based on load paths, creating efficient, organic structures. Lattices replace solid volumes with strong yet lightweight internal frameworks. Without this intentional redesign for AM, the weight savings might be minimal or non-existent. The specific percentage saved depends heavily on the original design, the complexity of the part, the load requirements, and the extent to which DfAM techniques are applied.
Q2: Are 3D printed metal gimbals durable enough for demanding aerospace and defense applications?
- A:Yes, absolutely. When manufactured correctly using appropriate materials like AlSi10Mg or Ti-6Al-4V, coupled with proper DfAM, validated process parameters, and essential post-processing (especially heat treatment like T6 for AlSi10Mg or stress relief/HIP for Ti-6Al-4V), 3D printed metal gimbals exhibit mechanical properties (strength, stiffness, fatigue resistance) that are often comparable or even superior to wrought or cast counterparts.
- Właściwości materiału: Heat-treated Ti-6Al-4V printed via AM offers exceptional strength-to-weight, fatigue life, and corrosion resistance, making it ideal for harsh military and aerospace environments. Heat-treated AlSi10Mg provides excellent performance for its weight class.
- Part Integrity: Proper process control minimizes defects like porosity. For critical applications, techniques like HIP can further enhance density and fatigue performance in Titanium parts.
- Testing & Validation: Like any aerospace component, 3D printed parts undergo rigorous testing and validation (material testing, load testing, environmental testing) to ensure they meet stringent performance and reliability standards (e.g., AS9100). Leading AM providers have experience qualifying parts for such demanding applications.
Q3: What types of sensors (cameras, LiDAR, thermal) can be integrated into these 3D printed gimbals?
- A: Metal 3D printed gimbals are highly versatile and can be designed to accommodate virtually any type of sensor payload typically used on UAVs. The design freedom offered by AM is a major advantage here. Engineers can create:
- Custom Mounts: Precisely tailored mounting interfaces and enclosures for specific sensor models (electro-optical/infrared (EO/IR) cameras, LiDAR units, multispectral/hyperspectral imagers, SIGINT receivers, etc.).
- Multi-Sensor Integration: Complex structures capable of housing and stabilizing multiple sensors simultaneously within a single, compact gimbal unit.
- Integrated Features: Incorporating features like vibration damping elements, specific cable routing channels, or thermal management solutions (heat sinks, cooling channels) directly into the gimbal structure to support the sensor’s operational requirements.
- The ability to rapidly prototype and iterate designs also means gimbals can be quickly adapted for new or upgraded sensor packages.
Q4: How does the performance and cost of a 3D printed metal gimbal compare to one made from carbon fiber composites?
- A: Both 3D printed metals (like Ti-6Al-4V or optimized AlSi10Mg) and carbon fiber composites (CFCs) are used for lightweight, high-performance gimbal structures. The choice between them depends on specific requirements, as they have different strengths and weaknesses: | Feature | 3D Printed Metal (Ti-6Al-4V / AlSi10Mg) | Carbon Fiber Composite (CFC) | Considerations for Gimbals | | :————————- | :———————————————– | :——————————————— | :———————————————————– | | Wytrzymałość do wagi | Excellent (esp. Ti-6Al-4V) | Excellent (Often superior in tension) | Both offer significant lightweighting potential. | | Stiffness-to-Weight | Very Good (Ti-6Al-4V) to Good (AlSi10Mg) | Excellent | CFCs generally offer higher stiffness for the same weight. | | Isotropy | Near-Isotropic (after heat treatment) | Anisotropic (Properties depend on fiber layup) | Metal parts offer more uniform properties in all directions. | | Complexity Potential | Very High (Internal channels, lattices, etc.) | Moderate (Limited by layup/molding processes) | AM excels at highly complex, integrated geometries. | | Odporność na temperaturę| High (Ti-6Al-4V) to Moderate (AlSi10Mg) | Moderate (Limited by resin matrix, ~120-180°C) | Ti-6Al-4V superior for high-temp environments. | | Przewodność cieplna | Low (Ti) to High (Al) | Low (Generally insulating) | AlSi10Mg better for heat dissipation; Ti/CFC are insulators.| | Impact Resistance | Good (Metals are ductile) | Lower (Can be brittle, prone to delamination) | Metals generally handle impacts better. | | Manufacturing Lead Time (Complex Prototype) | Relatively Fast | Slower (Requires mold making, layup, curing) | AM often faster for initial prototypes/low volumes. | | Cost (Complex/Low Vol.) | Can be Competitive/Lower | Higher (Due to tooling and manual labor) | AM cost-effective for complex, low-volume parts. | | **Cost (Simple/High Vol.)**| Higher | Potentially Lower (Once tooling is made) | CFC can be cheaper at very high volumes of simpler shapes. | | Repairability | Difficult to Impossible | Difficult (Specialized composite repair) | Neither is easily field-reparable. | | Joining/Integration | Weldable (Ti), Machinable for interfaces | Requires bonding or fasteners | Integrating metal inserts/features easier with AM. | Wnioski: For highly complex gimbal geometries requiring integrated features, operating in high temperatures, needing isotropic properties, or for rapid prototyping and low-volume production, metal AM often holds an advantage. For applications where maximum stiffness-to-weight is the absolute driver and the geometry is suitable for composite layup techniques, carbon fiber might be preferred, particularly at higher production volumes if tooling costs can be amortized. Often, hybrid approaches combining metal AM components (e.g., for motor mounts or complex joints) with CFC structural elements are also employed.
Conclusion: Elevating UAV Capabilities with Advanced Metal Additive Manufacturing
The landscape of Unmanned Aerial Vehicle technology is one of constant evolution, driven by the pursuit of greater endurance, enhanced payload capacity, improved mission flexibility, and superior data acquisition. In this pursuit, the sensor gimbal stands out as a critical subsystem where innovation yields significant performance dividends. As we’ve explored, metal additive manufacturing, particularly using high-performance alloys like AlSi10Mg and Ti-6Al-4V, represents a paradigm shift in how these vital components are designed and produced.
By unshackling engineers from the constraints of traditional manufacturing, metal AM enables the creation of UAV sensor gimbals that are radically lighter through topology optimization and intricate lattice structures, directly translating to longer flight times and increased payload margins. It allows for unprecedented geometric complexity, facilitating the integration of cooling channels, wiring paths, and conformal mounts, leading to more compact, efficient, and robust designs. The ability to consolidate multiple parts into a single printed component reduces assembly time, minimizes potential failure points, and further contributes to weight savings and reliability. Furthermore, the speed of prototyping inherent in AM accelerates development cycles, allowing UAV manufacturers to innovate and adapt to new sensor technologies more rapidly than ever before.
From demanding defense and aerospace ISR missions requiring the utmost durability of Ti-6Al-4V, to industrial inspection and precision agriculture applications benefiting from the cost-effective lightweighting of AlSi10Mg, metal 3D printing provides tailored solutions. Successfully navigating this advanced manufacturing process requires careful consideration of Design for Additive Manufacture (DfAM) principles, precise control over tolerances and surface finishes through strategic post-processing, and overcoming inherent challenges like residual stress and support removal.
Partnering with the right additive manufacturing expert is paramount. A provider must possess not only state-of-the-art equipment and certified processes but also deep material science knowledge and application-specific expertise.
Met3dp stands as a leader in this field, offering comprehensive rozwiązania w zakresie produkcji addytywnej. With decades of collective expertise, Met3dp provides not only industry-leading SEBM printers recognized for their accuracy and reliability but also manufactures a wide range of high-quality spherical metal powders, including AlSi10Mg and Ti-6Al-4V, using advanced VIGA and PREP technologies. Our integrated approach, spanning cutting-edge systems, premium materials, and dedicated application development services, empowers organizations across aerospace, defense, medical, and industrial sectors to accelerate their adoption of metal AM and achieve next-generation manufacturing goals.
If you are looking to enhance your UAV’s performance with lighter, stronger, and more capable sensor gimbals, the future is additive.
Contact Met3dp today to explore how our advanced metal 3D printing capabilities can power your organization’s innovation and elevate your UAV platform’s potential.
Udostępnij
MET3DP Technology Co., LTD jest wiodącym dostawcą rozwiązań w zakresie produkcji addytywnej z siedzibą w Qingdao w Chinach. Nasza firma specjalizuje się w sprzęcie do druku 3D i wysokowydajnych proszkach metali do zastosowań przemysłowych.
Zapytaj o najlepszą cenę i spersonalizowane rozwiązanie dla Twojej firmy!
Powiązane artykuły
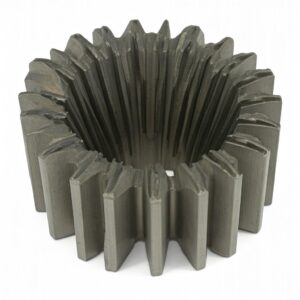
Wysokowydajne segmenty łopatek dysz: Rewolucja w wydajności turbin dzięki drukowi 3D w metalu
Czytaj więcej "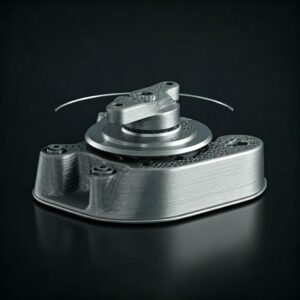
Drukowane w 3D mocowania dla samochodowych czujników radarowych: Precyzja i wydajność
Czytaj więcej "Informacje o Met3DP
Ostatnia aktualizacja
Nasz produkt
KONTAKT
Masz pytania? Wyślij nam wiadomość teraz! Po otrzymaniu wiadomości obsłużymy Twoją prośbę całym zespołem.
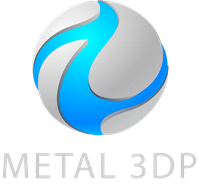
Proszki metali do druku 3D i produkcji addytywnej