Additive Manufacturing of Battery Thermal Management Plates
Spis treści
Revolutionizing EV Performance: Additive Manufacturing of Battery Thermal Management Plates
The relentless drive towards electrification in the automotive industry is pushing the boundaries of battery technology. Electric vehicles (EVs) are no longer niche products; they represent the future of personal and commercial transportation. Central to this transformation is the lithium-ion battery pack, the powerhouse that dictates an EV’s range, performance, and lifespan. However, these sophisticated energy storage systems generate significant heat during charging and discharging cycles, particularly under demanding conditions like fast charging or high-performance driving. Uncontrolled heat is the enemy of battery health, leading to accelerated degradation, reduced efficiency, safety risks (thermal runaway), and ultimately, a compromised driving experience. To jest miejsce Battery Thermal Management Systems (BTMS) play a critical, non-negotiable role. Within the BTMS, the battery cooling plate (also known as a cold plate or heat exchanger) is a cornerstone component, responsible for efficiently dissipating waste heat and maintaining the battery cells within their optimal operating temperature window, typically between 15∘C and 35∘C.
Traditionally, these cooling plates have been manufactured using methods like stamping, brazing, extrusion, or casting, often involving multiple components assembled together. While effective to a degree, these conventional techniques face limitations, especially when dealing with the increasing power densities and complex packaging constraints of modern EV battery packs. Achieving uniform temperature distribution across hundreds or thousands of individual cells packed into intricate architectures becomes a significant engineering challenge. Traditional manufacturing methods often struggle to create the highly complex internal channel geometries needed for optimal coolant flow and maximum heat transfer surface area within the limited space available. This can lead to compromises in cooling efficiency, increased system weight, and limitations on battery pack design flexibility. Furthermore, the tooling costs and lead times associated with traditional methods can hinder rapid prototyping and design iteration, slowing down the development cycle for new EV models. Procurement managers and engineers involved in sourcing EV battery cooling solutions are constantly seeking innovations that offer superior performance, reduced weight, and faster development timelines.
Wchodzić Produkcja addytywna (AM), commonly known as Drukowanie 3D. Specifically, metal AM processes like Laser Powder Bed Fusion (LPBF), which includes Selective Laser Melting (SLM) and Direct Metal Laser Sintering (DMLS), are emerging as a disruptive force in the design and production of systemy zarządzania temperaturą. Metal AM allows for the layer-by-layer construction of components directly from 3D CAD data using high-performance metal powders. This approach fundamentally unshackles designers from the constraints of traditional manufacturing. It enables the creation of cooling plates with incredibly complex internal structures, such as intricate lattice networks or biomimetic channels that mimic natural cooling systems, maximizing surface area and optimizing coolant flow for unparalleled thermal performance. This design freedom translates directly into more efficient heat dissipation, better temperature uniformity across the battery pack, and the potential for significant lightweighting – a crucial factor in extending EV range. Companies specializing in druk 3D z metalu, like Met3dp, leverage advanced powder metallurgy and printing technologies to realize these complex designs with high precision and material integrity, offering automotive OEMs and suppliers a powerful tool to enhance EV battery performance, safety, and longevity. The ability to rapidly iterate designs and produce customized cooling solutions without the need for expensive tooling makes AM particularly attractive for both niche high-performance applications and, increasingly, for mainstream EV development and production. As the industry demands ever-higher battery performance and faster charging, the role of additive manufacturing in producing next-generation battery thermal management plates is set to grow exponentially.
Core Functions & Applications: Where are 3D Printed Cooling Plates Making an Impact?
The primary purpose of any battery cooling plate, whether traditionally manufactured or 3D printed, is effective thermal management. This encompasses several core functions crucial for the optimal operation and longevity of an EV battery pack:
- Heat Dissipation: This is the most fundamental role. During operation (charging and discharging), battery cells generate heat due to internal resistance and electrochemical reactions. The cooling plate, typically using a circulating liquid coolant (like a water-glycol mixture), absorbs this heat from the cells or modules and transports it away to a radiator or chiller where it can be rejected to the ambient environment. Efficient heat dissipation prevents cells from exceeding their safe upper-temperature limits, mitigating risks of accelerated degradation, capacity loss, and thermal runaway.
- Temperature Uniformity: Simply removing heat isn’t enough; ensuring all cells within the pack operate at similar temperatures is equally vital. Temperature gradients across the pack can cause cells to age at different rates, leading to imbalances, reduced overall pack capacity, and shortened lifespan. 3D printed cooling plates excel here, as their design freedom allows for intricate channel routing that can be tailored to deliver consistent cooling across the entire battery module or pack, minimizing cell-to-cell temperature variations (ΔT).
- Pre-heating/Warm-up (in some systems): In cold climates, battery performance can be significantly reduced. Some BTMS designs incorporate heating elements or circulate warm coolant through the plates to bring the battery pack up to its optimal operating temperature more quickly, improving cold-start performance and charging efficiency. AM allows for the integration of heating functions potentially within the same complex plate structure.
- Structural Support: Depending on the battery pack architecture, the cooling plate can sometimes serve a secondary role as a structural component, contributing to the rigidity and mechanical integrity of the battery module or pack assembly. AM allows for optimizing the plate’s design for both thermal performance and structural requirements simultaneously.
The unique advantages offered by metal additive manufacturing are driving the adoption of 3D printed cooling plates across a growing range of applications, particularly where performance, weight, and design complexity are key considerations. Key impact areas include:
- High-Performance Electric Vehicles: Motorsport (Formula E, electric racing series), hypercars, and premium sports EVs demand maximum power output and rapid energy deployment, generating extreme heat loads. AM enables the creation of highly optimized, lightweight cooling plates with complex internal geometries (like TPMS or intricate fin structures) capable of handling these intense thermal challenges, providing a competitive edge. Weight reduction is paramount in racing, and AM delivers.
- Aerospace and Electric Aviation: Emerging electric vertical take-off and landing (eVTOL) aircraft and electric conventional take-off and landing (eCTOL) planes rely heavily on battery power. Stringent requirements for weight reduction, high reliability, and efficient thermal management under varying atmospheric conditions make AM an ideal solution for producing bespoke, high-performance battery cooling systems. Aerospace thermal solutions providers are increasingly exploring AM.
- EV Prototyping and Niche Vehicles: During the development phase of new EVs, AM allows engineers to rapidly prototype and test different cooling plate designs without investing in expensive tooling. This accelerates the design iteration cycle and allows for fine-tuning thermal performance early on. It’s also highly suitable for low-volume production runs of specialized EVs, such as electric buses, trucks, or custom vehicles. Automotive thermal solutions procurement teams can leverage AM for faster development cycles.
- Battery Energy Storage Systems (BESS): Large-scale BESS installations, used for grid stabilization or renewable energy storage, also require effective thermal management to ensure safety and longevity. While cost is often a primary driver here, the design flexibility of AM can be advantageous for optimizing cooling in densely packed containerized solutions or unique installation footprints. Finding a reliable BESS cooling manufacturer capable of advanced solutions is key.
- Industrial Equipment Electrification: As heavy machinery, mining equipment, and other industrial applications electrify, they require robust battery systems capable of operating in harsh environments. Custom-designed, high-performance 3D printed cooling plates can provide the necessary thermal management for these demanding applications.
Essentially, any application demanding superior thermal performance, minimal weight, complex packaging integration, or rapid design customization for its battery system is a prime candidate for leveraging the power of 3D printed cooling plates. The technology is rapidly moving from a prototyping tool to a viable solution for specialized series production, driven by the continuous improvements in AM processes, materials, and cost-effectiveness offered by innovative metal 3D printing powder suppliers and service providers.
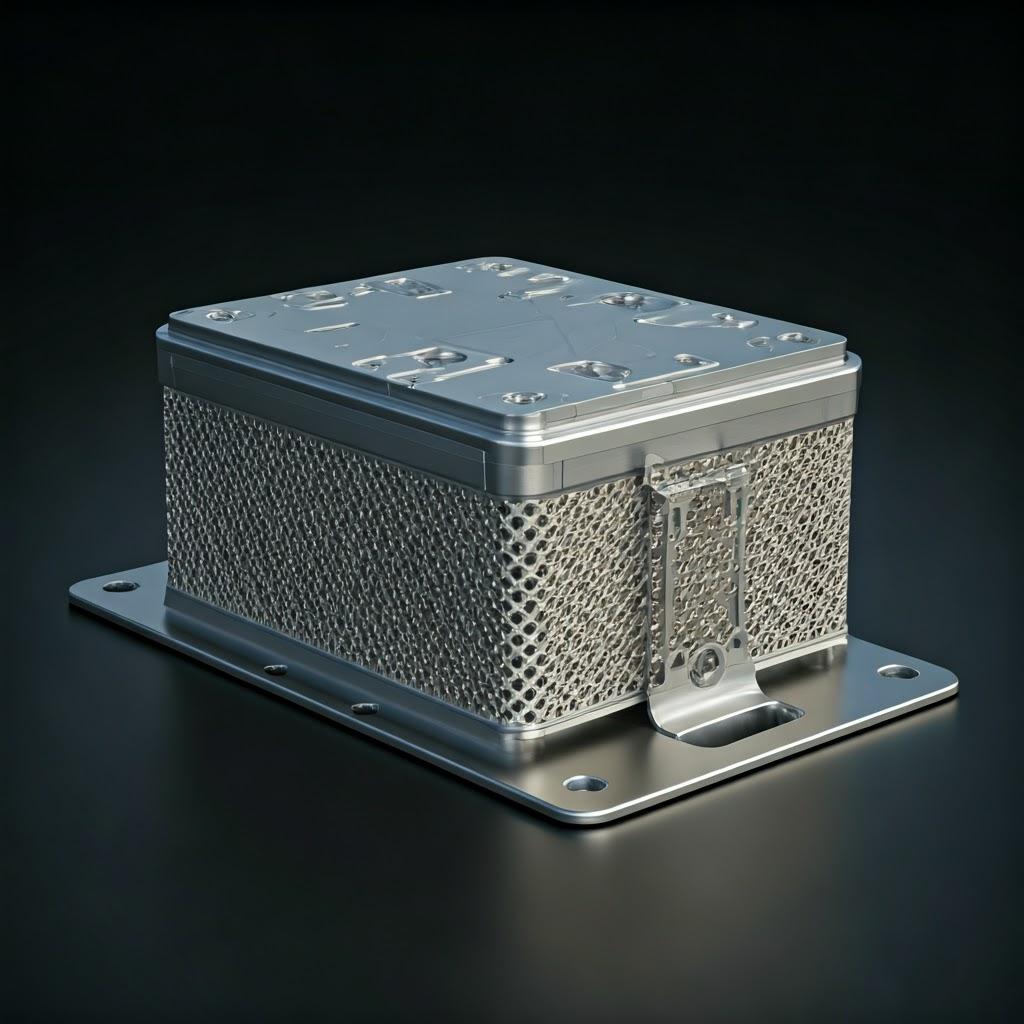
The Additive Advantage: Why Choose Metal 3D Printing for Battery Cooling Plates?
While traditional manufacturing methods like brazing aluminum sheets or casting have served the automotive industry for decades, they present inherent limitations when applied to the increasingly complex demands of modern EV battery cooling. Metal additive manufacturing, particularly Laser Powder Bed Fusion (LPBF), offers a paradigm shift, providing distinct advantages that directly address these limitations and unlock new levels of performance and design possibilities. For engineers and procurement managers evaluating automotive thermal management solutions, understanding these benefits is crucial for making informed sourcing decisions.
Key Advantages of Metal AM for Cooling Plates:
- Unparalleled Design Freedom & Geometric Complexity: This is arguably the most significant advantage. AM builds parts layer by layer, freeing designers from the constraints imposed by casting molds, stamping dies, or CNC machining access. This enables:
- Highly Optimized Internal Channels: Creation of intricate, non-linear flow paths, variable channel cross-sections, and features like Triply Periodic Minimal Surfaces (TPMS) or complex fin structures. These maximize the heat transfer surface area within a given volume, leading to superior cooling efficiency and temperature uniformity (ΔT minimization).
- Conformal Cooling: Channels can be designed to follow the exact contours of the battery cells or modules, ensuring intimate thermal contact and minimizing thermal resistance.
- Integrated Features: Mounting points, brackets, sensor housings, inlet/outlet ports can be directly integrated into the cooling plate design, reducing part count, assembly steps, and potential leak points.
- Potencjał lekkości: AM allows for topology optimization and the use of complex internal lattice structures, removing material from non-critical areas without compromising structural integrity or thermal performance. This results in significantly lighter cooling plates compared to traditional solid or multi-part designs. Reducing weight is paramount in EVs to maximize range and performance. Lightweight automotive components suppliers are increasingly turning to AM.
- Konsolidacja części: Complex assemblies traditionally made from multiple brazed, welded, or bolted components can often be redesigned and printed as a single, monolithic part. This simplifies the supply chain, reduces assembly time and cost, eliminates potential leak paths associated with joints, and improves overall reliability.
- Rapid Prototyping and Accelerated Development: AM eliminates the need for expensive and time-consuming tooling (e.g., casting molds, stamping dies). Design modifications can be implemented quickly in CAD and new prototypes printed within days, not weeks or months. This allows engineering teams to iterate designs rapidly, perform physical testing earlier, and significantly shorten the overall product development lifecycle for new battery packs and EV models.
- Customization and Low-Volume Production: AM is economically viable for producing customized cooling plates tailored to specific battery module dimensions, performance requirements, or vehicle platforms, even in low volumes. This is ideal for niche vehicles, motorsport applications, or early-stage production ramps before committing to mass production tooling.
- Improved Thermal Efficiency: The ability to create highly complex internal geometries directly translates to improved heat transfer coefficients. Optimized flow paths minimize pressure drop while maximizing turbulence and surface area contact with the coolant, leading to more effective heat removal compared to simpler channel designs common in traditional manufacturing.
- Elastyczność materiału: While traditional methods are often tied to specific formable or castable alloys, AM processes like LPBF can work with a wider range of high-performance alloys optimized for thermal conductivity and strength, including specialized aluminum (like AlSi10Mg) and copper alloys (like CuCrZr), enabling performance beyond standard materials.
Comparative Overview: AM vs. Traditional Methods for Cooling Plates
Cecha | Metal Additive Manufacturing (LPBF) | Traditional Methods (Brazing, Casting, Stamping) |
---|---|---|
Złożoność projektu | Very High (Complex internal channels, lattices, TPMS) | Moderate to Low (Limited by tooling, assembly) |
Internal Channels | Highly optimized, conformal, complex paths possible | Simpler geometries, often linear or layered |
Lekkość | Excellent (Topology optimization, lattices) | Limited (Often solid or requires complex assembly) |
Konsolidacja części | High potential (Multiple parts into one) | Low (Often requires assembly of multiple pieces) |
Wymagane narzędzia | None (Direct digital manufacturing) | Yes (Molds, dies, fixtures – expensive & time-consuming) |
Prototyping Speed | Very Fast (Days) | Slow (Weeks to Months) |
Personalizacja | High & Cost-Effective at low volumes | Difficult & Expensive at low volumes |
Thermal Efficiency | Potentially Higher (Optimized surface area/flow) | Generally Lower (Design constraints limit optimization) |
Potential Leak Points | Minimized (Monolithic structure) | Higher (Joints, seals, brazing/welding points) |
Opcje materiałowe | Growing range of specialized AM powders (Al, Cu alloys) | Often limited to standard formable/castable alloys |
Cost (Low Volume) | Konkurencyjny | Very High (Tooling amortization) |
Cost (High Volume) | Currently Higher (Can be competitive for high value) | Lower (Economy of scale) |
Export to Sheets
While the cost per part for AM can still be higher than traditional methods at very high volumes, the system-level benefits – improved performance, reduced weight, faster development, enhanced reliability, and simplified logistics – often provide a compelling value proposition, particularly for performance-critical applications. As AM technology matures, printing speeds increase, and material costs decrease, the economic equation is continually shifting, making additive manufacturing vs traditional methods a critical evaluation for forward-thinking companies seeking a competitive edge in the demanding EV market. Partnering with an experienced AM provider like Met3dp, which possesses deep expertise in materials, process optimization, and post-processing, is key to successfully leveraging these advantages.
Material Matters: Selecting AlSi10Mg and CuCrZr Powders for Optimal Thermal Performance
Choosing the right material is fundamental to the success of any engineering component, and 3D printed battery cooling plates are no exception. The material must possess a specific combination of properties to ensure efficient heat transfer, structural integrity, durability, and compatibility with the battery system environment (including the coolant). For metal additive manufacturing of thermal management components, two materials stand out as leading candidates: AlSi10Mg (an aluminum-silicon-magnesium alloy) oraz CuCrZr (a copper-chromium-zirconium alloy). Understanding their respective strengths and weaknesses is crucial for selecting the optimal powder for a specific application.
AlSi10Mg: The Versatile Workhorse
AlSi10Mg is one of the most widely used aluminum alloys in additive manufacturing, particularly via Laser Powder Bed Fusion (LPBF). It’s essentially a casting alloy adapted for AM, known for its excellent processability, good strength-to-weight ratio, and respectable thermal properties.
- Key Properties & Advantages:
- Good Thermal Conductivity: While not as high as pure aluminum or copper alloys, AlSi10Mg offers thermal conductivity significantly better than steels or titanium alloys (typically around 120−150W/(m⋅K) after appropriate heat treatment), sufficient for many EV cooling applications.
- Excellent Processability: It prints relatively easily with LPBF, allowing for fine features and complex geometries with good dimensional accuracy and surface finish.
- Dobra wytrzymałość i twardość: Especially after heat treatment (typically T6 PHT – Precipitation Hardening Treatment), AlSi10Mg exhibits good mechanical properties suitable for structural components.
- Lekka waga: As an aluminum alloy, it offers low density (approx. 2.67g/cm3), contributing significantly to overall weight reduction of the battery pack – a critical factor for EV range.
- Odporność na korozję: Offers decent corrosion resistance, particularly important for handling common coolants like water-glycol mixtures.
- Efektywność kosztowa: Compared to copper alloys, AlSi10Mg powder is generally more affordable, making it an attractive option for balancing performance and cost.
- Rozważania:
- Requires post-print heat treatment (stress relief and T6) to achieve optimal mechanical properties and thermal stability.
- Thermal conductivity is good, but significantly lower than copper alloys, potentially limiting performance in extremely high heat flux applications.
CuCrZr: The High-Performance Conductor
When maximum thermal performance is paramount, copper alloys are the go-to choice due to their exceptional thermal conductivity. CuCrZr is a precipitation-hardenable copper alloy specifically developed to offer a compelling combination of high thermal and electrical conductivity, good strength, and resistance to softening at elevated temperatures.
- Key Properties & Advantages:
- Doskonała przewodność cieplna: This is the standout feature. CuCrZr boasts thermal conductivity typically in the range of 300−340W/(m⋅K), more than double that of AlSi10Mg. This allows for significantly more efficient heat dissipation, enabling smaller or more effective cooling plate designs.
- Wysoka przewodność elektryczna: Also exhibits excellent electrical conductivity, although less critical for cooling plates, it’s indicative of its electron mobility which relates to thermal transport.
- Dobra wytrzymałość i twardość: Achieves good mechanical strength, especially after heat treatment, comparable to some steels, while retaining high conductivity.
- Resistance to Softening: Maintains its strength well at moderately elevated temperatures, important for durability within a battery pack environment.
- Rozważania:
- Higher Density: Copper alloys are significantly denser than aluminum (CuCrZr density approx. 8.9g/cm3), which can counteract lightweighting efforts if not carefully managed through design optimization (e.g., thinner walls, complex lattices enabled by AM).
- More Challenging to Print: Copper’s high reflectivity and thermal conductivity make it more challenging to process reliably using LPBF compared to aluminum or steel. It requires higher laser power, careful parameter optimization, and often specific machine modifications to manage heat buildup and ensure dense, defect-free parts. Overcoming these challenges requires significant process expertise.
- Wyższy koszt materiałów: Copper alloy powders are generally more expensive than aluminum alloy powders.
- Potential Corrosion: Depending on the coolant chemistry and operating environment, specific corrosion protection measures might be needed, although CuCrZr generally offers reasonable corrosion resistance.
Material Properties Comparison (Typical Values after Appropriate Heat Treatment)
Nieruchomość | AlSi10Mg (T6 Heat Treated) | CuCrZr (Heat Treated) | Jednostka | Importance for Cooling Plates |
---|---|---|---|---|
Przewodność cieplna | 120−150 | 300−340 | W/(m⋅K) | Bardzo wysoka |
Gęstość | ≈2.67 | ≈8.9 | g/cm3 | High (for Lightweighting) |
Wytrzymałość na rozciąganie | 230−280 | 350−450 | MPa | Moderate (Structural Integrity) |
Ostateczna wytrzymałość na rozciąganie | 330−400 | 450−550 | MPa | Umiarkowany |
Wydłużenie przy zerwaniu | 3−10 | 10−20 | % | Moderate (Ductility) |
Processability (LPBF) | Dobry | Wyzwanie | – | High (Manufacturability) |
Koszt względny | Niższy | Wyższy | – | High (Economics) |
Export to Sheets
The Critical Role of Powder Quality
Regardless of the chosen alloy, the quality of the metal powder used in the AM process is paramount to achieving high-quality, reliable cooling plates. Key powder characteristics include:
- Sferyczność: Highly spherical powder particles ensure good flowability within the printer’s recoating mechanism and contribute to dense, uniform packing of the powder bed. This minimizes porosity in the final part.
- Rozkład wielkości cząstek (PSD): A controlled PSD is crucial for achieving high packing density and predictable melting behavior. Fines can affect flowability, while excessively large particles may not melt completely.
- Czystość: Low levels of impurities and contaminants (like oxygen or nitrogen) are essential for achieving the desired mechanical properties and preventing defects in the printed part.
- Płynność: Good flowability ensures consistent powder deposition across the build platform layer after layer, critical for process stability and part quality.
Firmy takie jak Met3dp specjalizujemy się w produkcji Wysokiej jakości proszki metali specifically optimized for additive manufacturing processes. Utilizing advanced techniques like Vacuum Induction Melting Gas Atomization (VIGA) oraz Proces plazmowej elektrody rotacyjnej (PREP), Met3dp ensures its AlSi10Mg, CuCrZr, and other powders (see full product range) meet stringent requirements for sphericity, PSD, purity, and flowability. Their rigorous quality control ensures that the powders delivered enable customers to 3D print dense, high-performance cooling plates with superior material properties and reliability. Partnering with a metal 3D printing powder supplier that understands the nuances of powder production and its impact on the final part properties, like Met3dp, is a critical step in successfully implementing AM for demanding applications like EV battery thermal management.
Selection Guidance:
- Wybierz AlSi10Mg when:
- Weight reduction is a primary driver.
- Good thermal performance is sufficient, but not extreme.
- Cost is a significant factor.
- Faster prototyping and easier printing are desired.
- Wybierz CuCrZr when:
- Maximum thermal conductivity and heat dissipation are absolutely critical (high power density batteries, extreme performance).
- Higher component weight can be tolerated or offset by design optimization.
- Budget allows for higher material and processing costs.
- Partnering with an AM provider experienced in processing copper alloys is possible.
Ultimately, the choice involves a trade-off analysis based on the specific requirements of the EV battery pack and vehicle platform, considering thermal loads, weight targets, cost constraints, and production volume. Simulation tools like Computational Fluid Dynamics (CFD) are often used in conjunction with material properties to predict performance and guide the optimal selection and design.
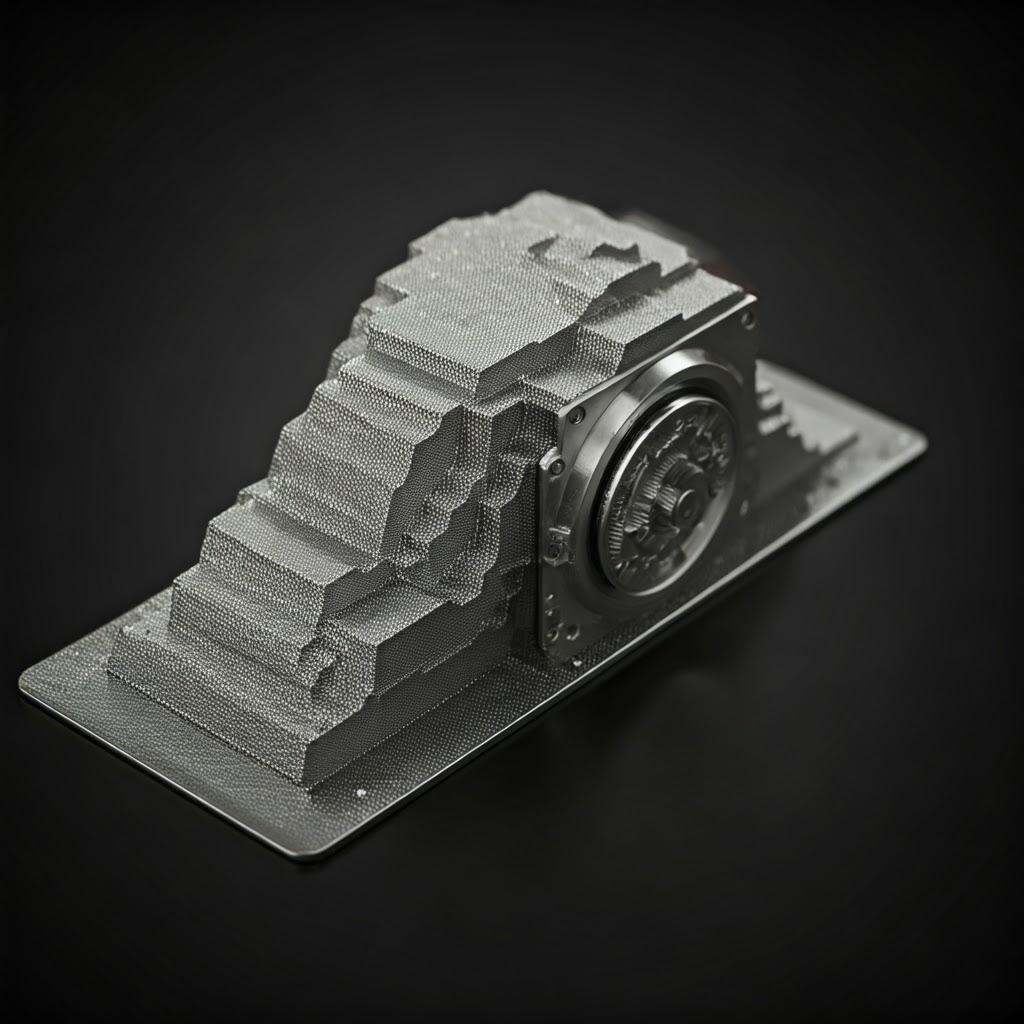
Design for Additive Manufacturing (DfAM): Optimizing Cooling Plate Geometry
Simply replicating a design intended for traditional manufacturing using additive manufacturing rarely unlocks the full potential of the technology. To truly harness the benefits of metal 3D printing for battery cooling plates – enhanced thermal performance, lightweighting, and part consolidation – engineers must embrace Projektowanie dla produkcji addytywnej (DfAM) principles. DfAM is not just a suggestion; it’s a fundamental shift in mindset, considering the unique capabilities and constraints of the layer-by-layer building process right from the conceptual design stage. For procurement managers, understanding that a design optimized for AM may look significantly different from its traditionally manufactured counterpart is key to evaluating proposals and potential performance gains from additive manufacturing design guidelines.
Optimizing a battery cooling plate using DfAM involves several key considerations:
- Leveraging Geometric Freedom for Thermal Performance:
- Complex Internal Channels: This is where AM truly shines. Instead of simple drilled or routed channels, designers can create:
- Biomimetic Structures: Mimicking natural forms like veins in a leaf or vascular networks to optimize fluid flow and heat transfer.
- Variable Cross-Sections: Tailoring the channel diameter or shape along its length to control coolant velocity and pressure drop, ensuring uniform heat extraction.
- Turbulators & Fins: Integrating complex internal features like micro-fins or turbulators directly into the channel walls to enhance turbulence and increase the heat transfer coefficient without significantly increasing pressure drop.
- Triply Periodic Minimal Surfaces (TPMS): Mathematically defined, highly complex lattice structures (e.g., Gyroid, Schwarz-P) offer an enormous surface area-to-volume ratio. Filling internal cavities with TPMS structures can dramatically increase heat transfer capabilities, creating highly efficient, compact heat exchangers. Designing and simulating these requires specialized software and expertise.
- Conformal Cooling: Designing channels that precisely follow the 3D contours of the battery cells or modules they are cooling. This minimizes the thermal interface distance and maximizes contact area, leading to more direct and efficient heat removal compared to flat plates cooling cylindrical or prismatic cells.
- Complex Internal Channels: This is where AM truly shines. Instead of simple drilled or routed channels, designers can create:
- Lightweighting Strategies:
- Topology Optimization: Using software tools to analyze the stress distribution under expected thermal and mechanical loads, allowing material to be removed from low-stress regions. This results in organic-looking, highly efficient structures that meet performance requirements with minimum mass.
- Internal Lattices: Replacing solid sections of the cooling plate (where high thermal conductivity isn’t the primary driver, e.g., structural supports or casings) with internal lattice structures. These significantly reduce weight while maintaining necessary stiffness and strength. The type of lattice (e.g., honeycomb, strut-based) can be chosen based on the specific load case.
- Thin Walls: AM allows for the creation of much thinner walls than traditional casting or machining might permit, provided the design considers printability and pressure requirements. Minimum wall thicknesses achievable depend on the material (AlSi10Mg vs. CuCrZr), printer capabilities, and orientation, but are often in the range of 0.4−0.8mm.
- Part Consolidation and Feature Integration:
- Reducing Assembly: Identify opportunities to combine multiple components (e.g., inlet/outlet manifolds, mounting brackets, flow distributors) into a single printable part. This eliminates assembly steps, potential leak points at joints, and simplifies the supply chain.
- Embedded Sensors: Potential to design integrated channels or cavities for embedding temperature or pressure sensors directly within the cooling plate structure for enhanced monitoring.
- Optimized Ports: Designing inlet and outlet ports with smooth transitions and flow-friendly geometries to minimize pressure losses.
- Printability Considerations (LPBF Specific):
- Struktury wsparcia: AM parts often require support structures to anchor them to the build plate, support overhanging features, and manage thermal stress during printing. DfAM aims to minimize the need for supports, especially in hard-to-reach internal channels.
- Self-Supporting Angles: Designing overhangs typically below a certain angle (often around 45∘ from the horizontal, though material and parameter dependent) to be self-supporting, reducing or eliminating the need for supports that must be removed later.
- Orientation Optimization: Choosing the optimal build orientation to minimize overhangs, reduce print time, optimize surface finish on critical faces, and manage residual stress.
- Minimalny rozmiar funkcji: Understanding the printer’s resolution and the minimum printable feature size (e.g., hole diameter, channel width) is crucial.
- Powder Removal: Designing internal channels with sufficient diameter and smooth pathways to facilitate easy removal of unfused powder after printing. Avoid creating inescapable powder traps.
- Thermal Management During Build: Very thin or large, flat sections can be prone to warping. DfAM involves considering thermal gradients during the build and potentially adding sacrificial features or optimizing geometry to mitigate distortion.
- Struktury wsparcia: AM parts often require support structures to anchor them to the build plate, support overhanging features, and manage thermal stress during printing. DfAM aims to minimize the need for supports, especially in hard-to-reach internal channels.
- Simulation-Driven Design:
- Computational Fluid Dynamics (CFD): Essential for simulating coolant flow through complex internal channels, predicting pressure drop, identifying potential stagnation zones, and quantifying heat transfer efficiency. CFD allows designers to iterate virtually and optimize channel geometry before committing to a physical print.
- Thermal Analysis (FEA): Simulating temperature distribution across the cooling plate and battery cells under various operating conditions to verify thermal performance and identify potential hot spots.
- Structural Analysis (FEA): Ensuring the optimized, lightweight design can withstand mechanical loads (vibration, mounting stresses) and internal coolant pressure without failure.
Successfully implementing DfAM for battery cooling plates requires a collaborative approach between design engineers, thermal engineers, and AM process experts. Engaging with a knowledgeable metal AM service provider like Met3dp early in the design process is highly beneficial. Met3dp’s team possesses deep expertise in the nuances of LPBF metody drukowania for materials like AlSi10Mg and CuCrZr and can provide invaluable DfAM guidance. They can help optimize designs for printability, thermal performance, and cost-effectiveness, ensuring that the final product fully leverages the transformative potential of additive manufacturing. Investing time in DfAM is not an extra step; it is the pathway to creating superior optimized cooling channel designs and next-generation thermal management solutions.
Precision Engineering: Understanding Tolerance, Surface Finish, and Accuracy in AM Cooling Plates
While additive manufacturing offers unprecedented design freedom, it’s crucial for engineers and procurement managers to have realistic expectations regarding the achievable dimensional accuracy, tolerances, and surface finish of 3D printed metal parts, including battery cooling plates. These characteristics are influenced by the AM process itself (LPBF), the material used (AlSi10Mg, CuCrZr), printer calibration, build orientation, part geometry, and significantly, the post-processing steps employed. Understanding these factors is vital for ensuring proper fit, function, and sealing performance of the cooling plate within the battery pack assembly.
Dimensional Accuracy and Tolerances:
- As-Built Accuracy: Metal LPBF processes typically achieve dimensional accuracy in the range of ±0.1mm to ±0.2mm for smaller features, or around ±0.1%−0.2% of the nominal dimension for larger parts. However, factors like thermal shrinkage, warping, and residual stress can influence these values. Complex geometries and unsupported features might exhibit larger deviations.
- General Tolerances: For as-built parts without specific tolerancing callouts, general tolerances comparable to ISO 2768-m (medium) might be achievable for some features, but it’s often safer to assume tolerances closer to ISO 2768-c (coarse) for non-critical dimensions, especially on larger parts. Achieving tighter tolerances consistently across the entire part usually requires post-machining.
- Critical Tolerances: Dimensions critical for interfacing with other components (e.g., mounting surfaces, sealing faces, port connections) almost always require post-machining (CNC milling or turning) to achieve the necessary precision. Through machining, tolerances equivalent to ISO 2768-f (fine) or even tighter, depending on the specific requirement, can be reliably achieved. It is essential to clearly define these critical features and their required tolerances on engineering drawings.
- Influence of Design: Complex internal channels or very thin walls inherent in optimized cooling plate designs can be challenging to measure accurately and may exhibit slightly larger variations than simpler solid geometries. DfAM practices that minimize warping and residual stress contribute positively to overall accuracy.
Surface Finish (Roughness):
- As-Built Surface Roughness (Ra): The surface finish of as-built LPBF parts is inherently rougher than machined surfaces due to the layer-by-layer fusion process and partially melted powder particles adhering to the surface.
- Typical Ra Values: For AlSi10Mg and CuCrZr printed via LPBF, typical as-built Ra values range from 6μm to 20μm (240μin to 800μin), depending heavily on:
- Orientation: Surfaces parallel to the build plate (up-facing) tend to be smoother than vertical walls, while down-facing surfaces (supported) are typically the roughest due to support structure contact points.
- Grubość warstwy: Thinner layers generally result in a smoother finish but increase print time.
- Laser Parameters: Beam spot size, scan speed, and energy density influence melt pool dynamics and surface texture.
- Charakterystyka proszku: Particle size distribution can also play a role.
- Internal Channels: The surface finish inside complex internal channels is particularly difficult to control and measure and tends to be on the rougher end of the scale. While this roughness can sometimes enhance turbulence and heat transfer, it also increases pressure drop.
- Typical Ra Values: For AlSi10Mg and CuCrZr printed via LPBF, typical as-built Ra values range from 6μm to 20μm (240μin to 800μin), depending heavily on:
- Post-Processed Surface Finish: If a smoother surface finish is required (e.g., for sealing surfaces, improved flow characteristics, or aesthetics), various post-processing techniques can be employed:
- CNC Machining: Provides excellent surface finish (Ra $ < 1.6 , \mu m$ easily achievable, down to 0.4μm or better with fine machining/grinding). Typically used for critical interface surfaces.
- Abrasive Flow Machining (AFM) / Extrude Hone: Forces abrasive media through internal channels to smooth surfaces and remove partially sintered particles. Effective for improving internal finish.
- Chemical Polishing/Etching: Can provide uniform smoothing but requires careful control and material compatibility checks.
- Micro-machining / Laser Polishing: Emerging techniques for targeted surface refinement.
- Tumbling/Vibratory Finishing: Can improve external surface finish and deburr edges, but less effective on internal channels and may round sharp features.
Achieving Precision and Reliability:
- Kontrola procesu: Partnering with an AM service provider like Met3dp, which emphasizes rigorous process control, machine calibration, and optimized parameter sets for specific materials like AlSi10Mg and CuCrZr, is crucial for achieving consistent dimensional accuracy and minimizing defects.
- Quality Management Systems: Look for suppliers with robust quality management systems (e.g., ISO 9001 certified) to ensure traceability, process repeatability, and adherence to specifications. Certifications relevant to the automotive industry (like IATF 16949) are a significant advantage, indicating a commitment to quality and process control suitable for demanding applications.
- Metrology and Inspection: Comprehensive inspection is vital. This includes:
- Kontrola wymiarów: Using Coordinate Measuring Machines (CMMs), 3D scanning, or traditional metrology tools to verify critical dimensions against the drawing specifications.
- Pomiar chropowatości powierzchni: Using profilometers to check surface finish on critical areas.
- Leak Testing: This is non-negotiable for cooling plates. Parts must undergo rigorous leak testing (e.g., pressure decay testing, helium leak testing) to ensure complete integrity and prevent coolant leaks within the battery pack. Test parameters (pressure, duration, acceptable leak rate) should be clearly specified.
- Badania nieniszczące (NDT): Techniques like X-ray or CT scanning may be employed, especially during process qualification or for highly critical parts, to detect internal defects like porosity or incomplete powder removal.
In summary, while AM provides geometric freedom, achieving high precision comparable to traditional machining requires careful planning, DfAM implementation, optimized process control, and targeted post-processing. Defining critical tolerances and surface finish requirements clearly on drawings, and collaborating with an experienced AM provider capable of delivering verifiable metal 3D printing tolerance and quality, ensures that the final 3D printed battery cooling plates meet the demanding functional requirements of precision engineering services for the EV industry.
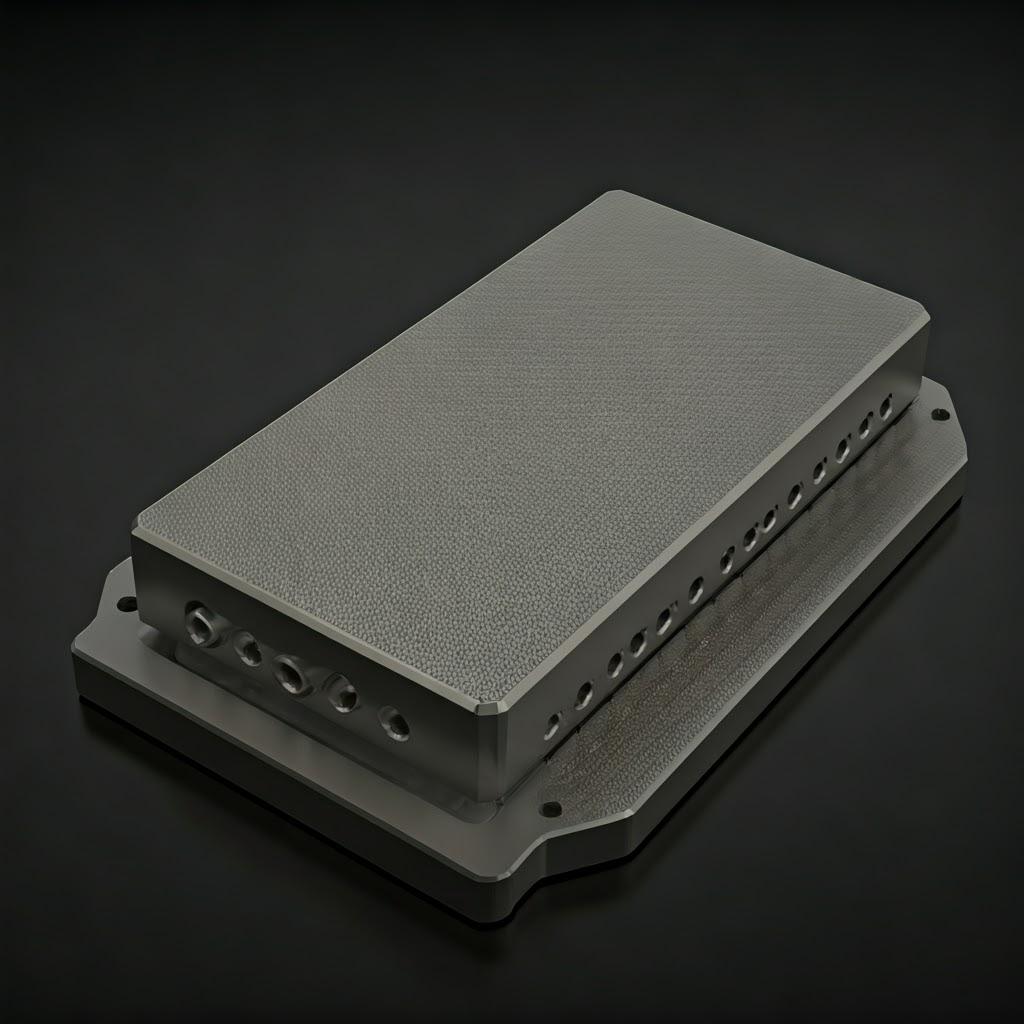
Beyond the Print: Essential Post-Processing Steps for Battery Cooling Plates
The journey of a 3D printed metal battery cooling plate doesn’t end when the printer stops. The “as-built” part, fresh off the build plate, requires a series of essential post-processing steps to transform it from a near-net-shape component into a functional, reliable, and finished product ready for integration into an EV battery pack. These steps are critical for achieving the desired mechanical properties, dimensional accuracy, surface finish, and ensuring leak-proof performance. Understanding this workflow is vital for engineers specifying requirements and procurement managers accounting for total cost and lead time.
The typical post-processing workflow for LPBF-printed AlSi10Mg or CuCrZr cooling plates involves several stages:
- Stress Relief / Heat Treatment: This is often one of the first and most critical steps.
- Why it’s needed: The rapid heating and cooling cycles inherent in the LPBF process create significant internal residual stresses within the printed part. These stresses can lead to distortion (warping) after removal from the build plate, reduced fatigue life, and potentially even cracking.
- Proces:
- Ulga w stresie: Parts are typically heated to a specific temperature (below the aging temperature) while still attached to the build plate, held for a period, and then slowly cooled. This relaxes the internal stresses without significantly altering the microstructure. Specific temperatures and times depend on the alloy (e.g., ≈300∘C for AlSi10Mg).
- Solution Annealing & Aging (e.g., T6 for AlSi10Mg): For alloys like AlSi10Mg, a full precipitation hardening heat treatment (T6) is usually required to achieve optimal mechanical properties (strength, hardness). This involves solutionizing at a high temperature, quenching rapidly, and then artificially aging at a lower temperature. CuCrZr also requires specific heat treatment cycles to achieve its desired combination of strength and conductivity.
- Importance: Właściwy heat treatment AlSi10Mg and CuCrZr is non-negotiable for ensuring dimensional stability and achieving the material properties specified in the design. This step requires accurately controlled furnaces and established metallurgical knowledge.
- Part Removal from Build Plate:
- Method: The printed part(s) are typically separated from the metal build plate using wire EDM (Electrical Discharge Machining) or a bandsaw. Care must be taken to avoid damaging the part during this process.
- Usunięcie konstrukcji wsporczej:
- Why Supports Exist: As mentioned in DfAM, supports anchor the part, prevent overhangs from collapsing, and help conduct heat away during printing.
- Removal: This is often a manual process, involving breaking, cutting, or grinding away the support structures. Access can be difficult, especially for internal supports within complex channel geometries. For delicate features or hard-to-reach areas, CNC machining or EDM might be used for precise removal.
- Wyzwania: Support removal can be labor-intensive and costly. Poorly designed supports or aggressive removal techniques can damage the part surface. Minimizing supports through DfAM is highly beneficial.
- Powder Removal (Depowdering):
- Wyzwanie: Unfused metal powder gets trapped within the internal channels and complex features of the cooling plate during printing. Removing this completely is critical for function (preventing blockages) and safety.
- Metody: Various techniques are used, often in combination:
- Compressed Air / Inert Gas Blowing: Initial removal of loose powder.
- Vibration / Tumbling: Shaking or tumbling the part to dislodge trapped powder.
- Manual Brushing/Vacuuming: For accessible areas.
- Liquid Flushing / Ultrasonic Cleaning: Using solvents or specialized cleaning solutions, sometimes with ultrasonic agitation, to flush out fine powder particles.
- Verification: Often verified through weighing the part, visual inspection (borescope for internal channels), or sometimes CT scanning to ensure channels are clear.
- CNC Machining:
- Cel: To achieve tight tolerances, critical flatness, and specific surface finishes on interfacing surfaces.
- Zastosowania: Machining sealing faces for O-rings or gaskets, creating precisely located mounting holes, finishing inlet/outlet port connections, achieving overall flatness requirements for mounting against battery modules.
- Rozważania: Requires careful fixture design to hold the potentially complex AM part geometry securely without distortion. CNC machining 3D prints is a standard step for functional metal AM parts.
- Surface Finishing & Smoothing:
- Cel: To improve surface roughness beyond the as-built state, if required for fluid dynamics (reducing pressure drop in channels), sealing, or aesthetics.
- Metody: As discussed previously (AFM, tumbling, polishing, etc.), selected based on the specific requirements and geometry (internal vs. external surfaces). Surface finishing services may be specialized operations.
- Cleaning & Inspection:
- Czyszczenie: Thorough final cleaning to remove any machining fluids, abrasive media, fingerprints, or other contaminants before final inspection and packaging.
- Inspection: Comprehensive quality checks are performed:
- Weryfikacja wymiarowa: Measuring critical features (CMM, scanning).
- Visual Inspection: Checking for surface defects, incomplete support removal.
- Leak Testing: Crucial pressure testing to guarantee the integrity of the cooling channels. This is a pass/fail gate for cooling plates.
- Material Property Verification (Optional): Testing witness coupons printed alongside the part for tensile strength, hardness, etc., especially during process validation.
The extent and sequence of these post-processing metal AM parts steps depend heavily on the application requirements, material choice, and part complexity. It’s essential for procurement teams to recognize that post-processing contributes significantly to the final cost and lead time of a 3D printed component. Working with a full-service AM provider like Met3dp, which possesses in-house or tightly managed external capabilities for all necessary post-processing stages, ensures a streamlined workflow and guarantees that the final cooling plate meets all specifications. Their integrated approach, combining powder expertise, advanced printing, and comprehensive post-processing, delivers application-ready components optimized for the demanding automotive sector.
Navigating Challenges: Overcoming Hurdles in 3D Printing Thermal Management Plates
While metal additive manufacturing offers compelling advantages for producing advanced battery cooling plates, the technology is not without its challenges. Engineers, designers, and procurement managers should be aware of potential hurdles to set realistic expectations and work proactively with their AM partners to mitigate risks. Successfully navigating these challenges is key to realizing the full benefits of AM for thermal management.
Here are some common metal 3D printing challenges encountered when producing cooling plates and strategies to overcome them:
- Warping and Distortion:
- Cause: Intense localized heating from the laser/electron beam followed by rapid cooling leads to significant thermal gradients and induces residual stress. As layers build up, this stress can cause the part to warp or distort, especially in large, flat sections or thin features common in cooling plates.
- Mitigation:
- Optimized Support Structures: Well-designed supports anchor the part firmly to the build plate and help conduct heat away more evenly.
- Orientacja budynku: Strategic orientation can minimize large flat areas parallel to the build plate and reduce stress concentration.
- Process Simulation: Using simulation software to predict thermal behavior and stress accumulation allows for adjustments to the build strategy (e.g., scan pattern, laser parameters) or part geometry before printing.
- Appropriate Heat Treatment: Post-build stress relief heat treatment is crucial for relaxing internal stresses and stabilizing the part’s geometry.
- Robust Machine Platform: Using high-quality AM systems with stable thermal management, like those potentially offered or utilized by partners like Met3dp, contributes to process stability.
- Residual Stress Management:
- Uderzenie: Beyond causing distortion, high residual stress can negatively impact a part’s mechanical properties, particularly fatigue life, and can even lead to cracking during printing or post-processing.
- Mitigation:
- Optimized Print Parameters: Fine-tuning laser power, scan speed, layer thickness, and scan strategy can influence the thermal cycles and reduce stress buildup. Requires significant process expertise.
- Obróbka cieplna: As mentioned, stress relief and subsequent aging treatments are essential for residual stress control AM.
- Design Modifications: Incorporating features like stress-relieving grooves or avoiding sharp internal corners can help manage stress concentrations.
- Wybór materiału: Some alloys may be inherently more prone to stress buildup than others.
- Usunięcie konstrukcji wsporczej:
- Wyzwanie: Removing supports, especially dense or internally located ones within complex cooling channels, can be time-consuming, costly, and risks damaging the part surface. Incomplete removal can impede fluid flow or break off later, causing contamination.
- Mitigation:
- DfAM for Support Reduction: Prioritizing self-supporting angles and clever orientation during the design phase is the most effective strategy.
- Optimized Support Design: Using specialized software to generate supports that are strong enough during the build but easier to remove (e.g., specific geometries, perforation points).
- Advanced Removal Techniques: Employing methods like CNC machining or electrochemical machining for difficult-to-access supports, although this adds cost.
- Careful Manual Removal & Inspection: Skilled technicians and thorough inspection are needed.
- Powder Removal from Internal Channels:
- Wyzwanie: Ensuring all unfused powder is removed from intricate, potentially long and narrow internal cooling channels is critical for functionality and preventing downstream contamination.
- Mitigation:
- DfAM Considerations: Designing channels with adequate diameters, smooth bends (avoiding sharp corners), and potentially multiple access ports aids powder removal. Avoid creating dead-end zones.
- Effective Depowdering Processes: Utilizing optimized combinations of vibration, gas flow, solvent flushing, and ultrasonic cleaning specifically tailored to the part geometry and powder type.
- Verification Methods: Borescope inspection, airflow testing, weight checks, or CT scanning to confirm channels are clear.
- Porosity Defects:
- Cause: Small voids or pores within the printed material can arise from gas entrapment during melting, incomplete fusion between layers, or powder quality issues (e.g., hollow powder particles, contaminants).
- Uderzenie: Porosity reduces material density, degrades mechanical properties (especially fatigue strength), and can create potential leak paths in a cooling plate.
- Mitigation:
- Optimized Print Parameters: Careful control over laser power, scan speed, hatch spacing, and focus ensures complete melting and fusion.
- High-Quality Powder: Using powders with high sphericity, controlled PSD, and low gas content (like those produced using advanced atomization by Met3dp) is crucial. Proper powder handling and storage are also important.
- Process Environment Control: Maintaining a high-purity inert gas atmosphere (Argon or Nitrogen) in the build chamber prevents oxidation and gas pickup.
- Prasowanie izostatyczne na gorąco (HIP): A post-processing step involving high temperature and pressure can close internal pores but adds significant cost and may not be necessary for all cooling plate applications unless extreme reliability is demanded. Addressing porosity defects LPBF through process optimization is usually preferred.
- Achieving Leak-Proof Integrity:
- Wyzwanie: Ensuring the final cooling plate is 100% leak-proof under operating pressures is paramount. Defects like micro-cracks or interconnected porosity can compromise sealing.
- Mitigation:
- Robust Process Control: Minimizing defects like porosity and cracks through optimized printing and heat treatment.
- Appropriate Design: Ensuring sufficient wall thickness, proper sealing features (e.g., O-ring grooves machined post-print).
- Rigorous Leak Testing: Implementing standardized leak testing protocols (e.g., pressure decay) on 100% of parts as a final quality gate.
- Scalability and Cost-Effectiveness:
- Wyzwanie: While ideal for prototyping and low volumes, scaling AM production for thousands or tens of thousands of cooling plates per year presents economic and logistical challenges compared to established high-volume traditional methods. Print times, machine utilization, and post-processing labor can drive costs.
- Mitigation:
- Design Optimization for Production: Simplifying designs where extreme complexity isn’t needed, nesting multiple parts efficiently on the build plate.
- Automatyzacja: Increasing automation in post-processing steps (e.g., robotic support removal, automated inspection).
- Process Improvements: Ongoing advancements in AM technology leading to faster print speeds and larger build envelopes.
- Strategic Sourcing: Working with large-scale AM providers who have invested in capacity and process efficiency.
- Hybrid Approaches: Considering AM for complex core sections combined with traditional manufacturing for simpler outer casings.
Overcoming these challenges requires deep technical expertise in materials science, AM process physics, DfAM, and post-processing. Partnering with an experienced and knowledgeable additive manufacturing provider is therefore essential. Met3dp, with its foundation in both advanced produkcja proszków metali and AM solutions, possesses the integrated expertise to help customers navigate these complexities, optimize designs, control processes, and ultimately deliver high-quality, reliable 3D printed battery cooling plates. Their focus on industrial applications means they understand the rigorous demands of the automotive sector.
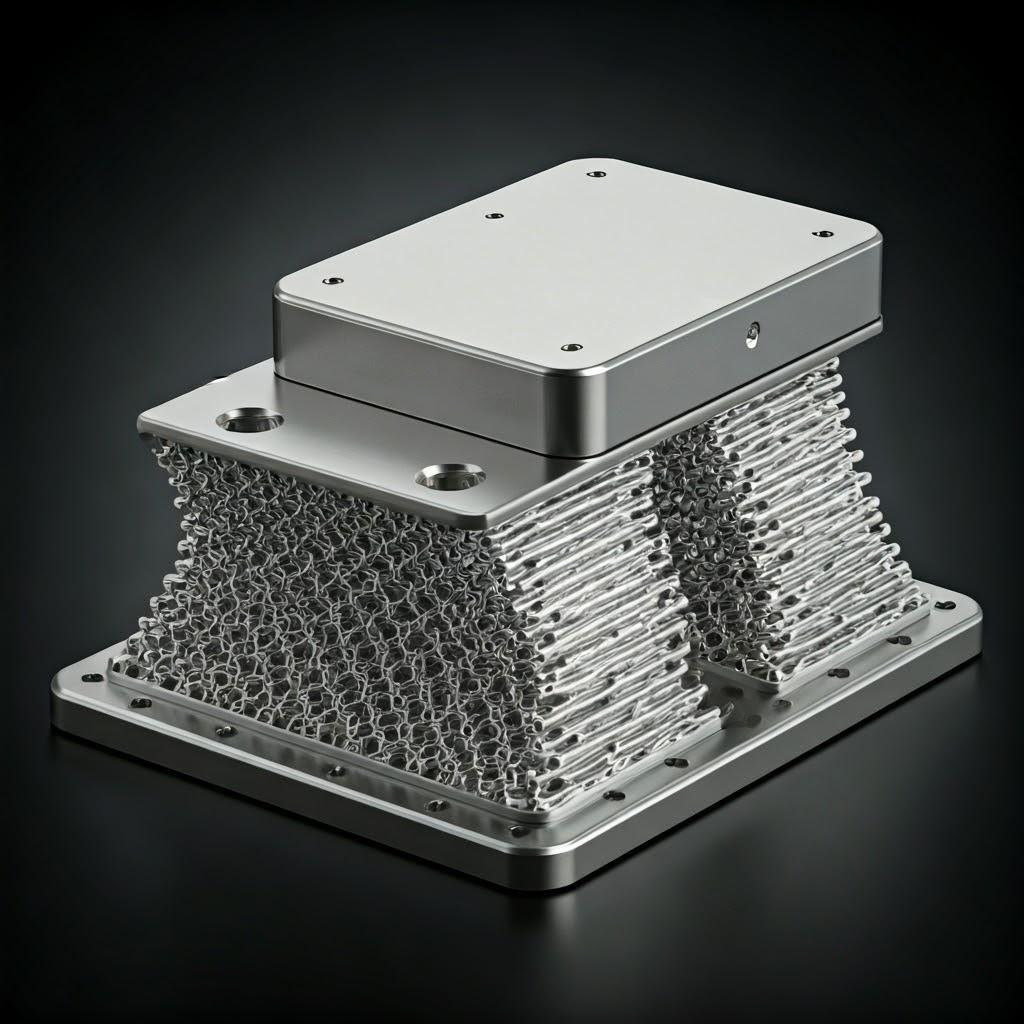
Partnering for Success: How to Select the Right Metal AM Service Provider for Cooling Plates
Choosing the right additive manufacturing partner is as critical as optimizing the design or selecting the appropriate material. The success of your 3D printed battery cooling plate project hinges on the capabilities, expertise, and reliability of your chosen service provider. For procurement managers and engineering leads navigating the metal AM service provider selection process, evaluating potential partners based on a comprehensive set of criteria is essential. This ensures not only the quality of the final part but also a smooth development and production experience.
Here’s a breakdown of key factors to consider when evaluating potential automotive 3D printing suppliers for complex thermal management components:
- Demonstrated Technical Expertise:
- DfAM & Simulation Support: Does the provider offer expert guidance on Design for Additive Manufacturing? Can they assist with topology optimization, lattice structure generation, or complex channel design? Do they have simulation capabilities (CFD, thermal FEA) to validate designs before printing, potentially saving costly iterations?
- Materials Science Knowledge: Do they possess deep understanding of the chosen materials (AlSi10Mg, CuCrZr), including their behavior during the LPBF process, required heat treatments, and resulting properties? Can they advise on material selection trade-offs?
- Optymalizacja procesów: Can they demonstrate expertise in optimizing print parameters (laser power, speed, scan strategy) specifically for your chosen material and geometry to achieve desired density, surface finish, and mechanical properties while minimizing defects?
- Machine Capability and Capacity:
- Technology Suitability: Do they utilize state-of-the-art LPBF machines suitable for processing aluminum and copper alloys effectively? Are the machines well-maintained and calibrated?
- Objętość kompilacji: Can their machines accommodate the size of your cooling plate design? Consider both current needs and potential future scaling.
- Capacity & Scalability: Do they have sufficient machine capacity to meet your prototyping and potential low-to-mid volume production needs? Can they handle fluctuations in demand or urgent requests? What are their plans for capacity expansion?
- Material Quality Control & Sourcing:
- Jakość proszku: How do they ensure the quality of the metal powder used? Do they conduct incoming powder inspection (chemistry, PSD, morphology)? Proper powder handling and storage protocols are critical to prevent contamination and moisture pickup.
- Powder Sourcing & Traceability: Do they source powders from reputable suppliers with strong quality control, or do they, like Met3dp, possess in-house powder production capabilities using advanced methods like VIGA or PREP? In-house production, as detailed on their Strona O nas, can offer greater control over quality and potentially tailored powder characteristics. Full traceability of powder batches used for your parts is essential.
- Comprehensive Post-Processing Capabilities:
- Integrated Services: Does the provider offer a full suite of required post-processing steps in-house or through tightly controlled, qualified partners? This includes stress relief/heat treatment (with proper furnace controls and metallurgical knowledge), support removal, precision CNC machining, powder removal, surface finishing, cleaning, and crucially, leak testing.
- Expertise in Finishing: Do they have proven methods for finishing internal channels (like AFM) if required? Can they achieve the specified tolerances and surface finishes on critical machined features?
- Quality Management Systems and Certifications:
- Baseline Certification: ISO 9001 certification is a minimum requirement, indicating a documented quality management system.
- Industry-Specific Certifications: For automotive applications, IATF 16949 certification is highly desirable, demonstrating adherence to stringent automotive quality standards. AS9100 (aerospace) also signifies a mature quality system. Ask for proof of certifications.
- Metrology & Inspection: Do they have calibrated metrology equipment (CMM, scanners, profilometers) and documented inspection procedures? Can they provide detailed inspection reports? What are their leak testing protocols and equipment?
- Proven Track Record and Relevant Experience:
- Case Studies & References: Can they provide examples of similar projects they have successfully completed, particularly in thermal management, heat exchangers, or the automotive/EV sector? Client testimonials or references can be valuable.
- Problem-Solving Ability: Discuss potential challenges (warping, porosity, support removal) and gauge their experience and methodologies for overcoming them.
- Project Management and Communication:
- Clear Communication: Is there a dedicated point of contact? Are they responsive to inquiries and providing regular project updates?
- Wsparcie techniczne: Is knowledgeable technical support readily available to discuss design revisions, material choices, or process details?
- Documentation & Reporting: Do they provide comprehensive documentation, including material certifications, process parameters (if required), inspection reports, and traceability records?
- Location, Logistics, and Supply Chain:
- Shipping & Handling: Evaluate their capabilities for securely packaging and shipping potentially delicate, high-value components.
- Geographic Location: While global providers are common, consider the implications of location on shipping times, costs, and ease of communication (time zones). Met3dp, headquartered in Qingdao, China, operates as a global supplier with experience serving international clients.
- Odporność łańcucha dostaw: Discuss their risk mitigation strategies regarding material supply, machine downtime, or other potential disruptions.
Wybór certified additive manufacturing partner is a strategic decision. It’s not just about finding the lowest price, but about finding a supplier who acts as an extension of your engineering team, bringing expertise, quality, and reliability to the table. Companies like Met3dp, which combine foundational expertise in metal powder production with advanced additive manufacturing solutions and a focus on industrial applications, represent the type of integrated partner capable of handling the complex requirements of 3D printed EV battery cooling plates. Conducting thorough due diligence using these criteria will significantly increase the likelihood of a successful project outcome and a high-performance final product.
Understanding the Investment: Cost Factors and Lead Times for AM Cooling Plates
One of the primary considerations for both engineers and procurement managers evaluating additive manufacturing for battery cooling plates is the associated cost and lead time. While AM offers significant performance and design benefits, understanding the key drivers behind the price and production schedule is crucial for budgeting, project planning, and making informed comparisons with traditional manufacturing methods, especially when seeking wholesale 3D printing quotes for larger quantities.
Key Cost Drivers for 3D Printed Cooling Plates:
- Part Design & Geometry:
- Material Volume: The sheer volume of material in the part (including support structures) is a direct cost driver. Larger or thicker parts consume more expensive metal powder. DfAM techniques like topology optimization and lattice structures are key to minimizing volume while maintaining performance.
- Częściowa złożoność: Highly intricate designs with complex internal channels or fine features often require longer print times and potentially more complex support structures and post-processing (e.g., powder removal, internal finishing), increasing cost.
- Bounding Box / Build Height: The overall dimensions, particularly the height in the build orientation, significantly impact the print time (number of layers) and how many parts can fit onto a single build plate (machine utilization). Taller parts take longer to print.
- Material Choice:
- Koszt proszku: The raw material cost varies significantly between alloys. High-performance copper alloys like CuCrZr are substantially more expensive per kilogram than common aluminum alloys like AlSi10Mg.
- Możliwość drukowania: Materials that are more challenging to print (like copper alloys) may require specialized machine parameters, potentially slower print speeds, or higher scrap rates during process optimization, indirectly affecting cost.
- Proces wytwarzania przyrostowego:
- Machine Time: This is often a major cost component. It’s determined by the print duration, which depends on part volume, height, layer thickness, laser parameters (scan speed), and the number of parts nested on the build plate. Machine hourly rates vary based on the printer’s capital cost, maintenance, and operational expenses.
- Struktury wsparcia: The volume of material used for supports adds to material cost. Furthermore, the time and labor required for support removal contribute significantly to post-processing costs. Designs minimizing supports are more cost-effective.
- Wymagania dotyczące przetwarzania końcowego:
- Obróbka cieplna: Costs associated with furnace time, energy consumption, and inert atmosphere (if required) for stress relief and aging cycles.
- Obróbka skrawaniem: The extent of CNC machining needed for critical tolerances and surfaces directly impacts cost (machine time, programming, fixturing, labor).
- Wykończenie powierzchni: Specific finishing steps like AFM for internal channels or polishing add cost based on the process time and complexity.
- Powder Removal & Cleaning: Labor and equipment time for ensuring complete powder removal, especially from complex internal geometries.
- Leak Testing: Equipment and labor time for performing and documenting mandatory leak tests.
- Quality Assurance & Inspection:
- Level of Inspection: The required level of dimensional inspection (e.g., 100% CMM vs. sample inspection), NDT (if specified), and documentation detail impacts labor and equipment costs.
- Certyfikaty: Costs associated with maintaining quality certifications (ISO 9001, IATF 16949) are factored into overheads.
- Order Volume & Setup:
- Setup Costs: Initial costs for build preparation (file processing, slicing, support generation) are amortized over the number of parts in a batch. Larger batches generally have a lower per-part setup cost.
- Economy of Scale: While AM doesn’t have tooling costs like casting, there are still economies of scale related to machine utilization, bulk powder purchasing, and optimized post-processing workflows for larger volumes. This makes the cost per part 3D printing generally decrease with quantity, although often less dramatically than with traditional mass production methods.
Typical Lead Time Components:
The total time from order placement to receiving finished parts involves multiple stages:
- Quoting & Order Confirmation (1-5 days): Initial review of requirements, potential DfAM feedback, quote generation, and order processing.
- Build Preparation (1-3 days): Final design checks, CAD file processing, slicing, support strategy finalization, and build layout planning (nesting).
- Printing (1-7+ days): Actual machine time. Highly variable based on part size/height, complexity, material, and number of parts per build. A single large cooling plate or a full plate of smaller ones can take several days.
- Cooldown & Depowdering (0.5-2 days): Allowing the build chamber and parts to cool safely, removing parts from the build plate, and initial bulk powder removal.
- Post-Processing (3-15+ days): This is often the longest and most variable phase. Heat treatment cycles take time (furnace time + cooling). Support removal, CNC machining (depending on complexity and queue times), surface finishing, cleaning, and inspection all add up. Complex parts requiring multiple steps will have longer post-processing times.
- Quality Control & Shipping Prep (1-3 days): Final inspection, documentation compilation, packaging.
- Shipping (Variable): Depends on location and shipping method.
Indicative Total Lead Times:
- Prototypes (Single part or small batch): Typically 1 to 4 weeks.
- Low-Volume Production (Small series): Typically 4 to 8 weeks or more, depending on complexity and quantity.
It is crucial to get specific quotes and lead time estimates from potential suppliers based on your final part design, material, specifications, and required quantity. Clearly defining all requirements upfront, including tolerances, surface finishes, heat treatment, and testing protocols, allows suppliers like Met3dp to provide accurate additive manufacturing pricing factors and realistic delivery schedules for your lead time metal AM potrzeby.
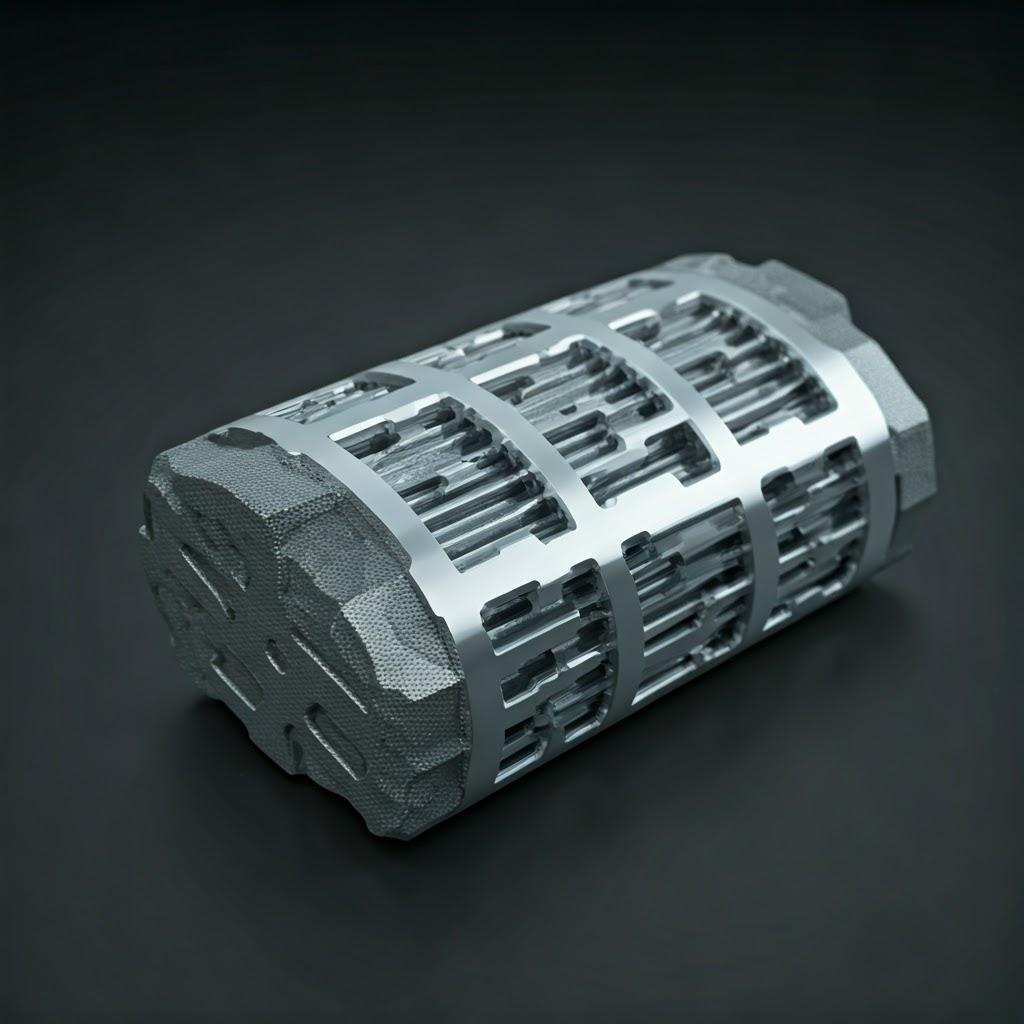
Frequently Asked Questions (FAQ) about 3D Printed EV Battery Cooling Plates
Engineers and procurement managers exploring additive manufacturing for battery thermal management often have specific questions. Here are answers to some frequently asked questions:
Q1: How does the thermal performance of 3D printed cooling plates compare to traditionally manufactured ones (e.g., brazed aluminum)?
A: 3D printed cooling plates, when properly designed using DfAM principles, can often offer Doskonała wydajność termiczna compared to traditional counterparts. The key reasons are:
- Optimized Geometries: AM allows for complex internal channel designs (e.g., TPMS, micro-fins, conformal channels) that maximize heat transfer surface area and optimize coolant flow, leading to higher heat transfer coefficients and better temperature uniformity (ΔT) across the battery cells. Traditional methods are limited to simpler channel geometries.
- Wybór materiału: While traditional methods often use standard aluminum alloys, AM allows for the use of optimized materials like AlSi10Mg or even high-conductivity CuCrZr. Using CuCrZr (≈320W/(m⋅K)) can provide significantly better heat dissipation than standard brazed aluminum alloys (typically 150−180W/(m⋅K)).
- Konsolidacja części: Eliminating thermal resistance associated with joints or brazing layers in multi-part traditional assemblies can improve heat flow.
However, achieving this superior performance depends heavily on leveraging DfAM. Simply printing a design made for brazing might not yield significant benefits and could even perform worse if not optimized for the AM process (e.g., due to rougher internal surfaces increasing pressure drop if flow isn’t managed). Performance should always be validated through CFD simulation and physical testing.
Q2: What is the typical production volume where AM becomes cost-competitive for cooling plates compared to traditional methods like brazing or casting?
A: This is a complex question with no single answer, as the “crossover point” depends heavily on several factors:
- Częściowa złożoność: For very complex designs that are difficult or impossible to make traditionally, AM might be cost-effective even at relatively low volumes due to the value of the achieved performance or function.
- Materiał: Using expensive materials like CuCrZr in AM will shift the crossover point to lower volumes compared to using AlSi10Mg.
- Traditional Method Tooling Costs: Methods like die casting involve very high upfront tooling costs. AM avoids this, making it highly competitive for prototypes and low volumes (typically up to hundreds or perhaps low thousands of parts per year). Brazing may have lower tooling costs than casting but higher assembly labor.
- Level of Optimization (Lightweighting/Performance): If AM enables significant lightweighting (reducing material cost and improving vehicle range) or performance gains (allowing for smaller/cheaper battery packs), the system-level cost benefits can justify a higher component price at larger volumes.
- AM Process Maturity & Speed: As AM print speeds increase and machine costs decrease, the crossover point is continually moving towards higher volumes.
General Guideline:
- Prototyping & Very Low Volume (1s – 100s): AM is almost always more cost-effective due to the absence of tooling.
- Low to Mid Volume (100s – few 1000s per year): Often competitive, especially for complex designs or where AM benefits (performance, weight) add significant value.
- High Volume (10,000s+ per year): Traditional methods like casting or high-volume brazing/stamping are typically more cost-effective for the component itself, unless the complexity or performance enabled by AM provides overwhelming system-level benefits or is simply unachievable otherwise.
A detailed cost analysis comparing optimized AM designs with optimized traditional designs, including tooling amortization and system-level value, is needed for specific cases.
Q3: Can you guarantee leak-proof performance for 3D printed cooling plates?
A: Reputable metal AM service providers puszka deliver leak-proof cooling plates, but it requires rigorous process control and mandatory testing. It’s not an inherent property but an outcome of quality manufacturing.
- Kontrola procesu: Achieving fully dense parts with minimal porosity is critical. This relies on optimized print parameters, high-quality powder, and a stable printing environment.
- Projekt: Ensuring sufficient wall thickness and properly designed sealing interfaces (often requiring post-machining) is crucial.
- Obróbka cieplna: Proper stress relief is important to prevent delayed cracking.
- 100% Leak Testing: This is the ultimate guarantee. Every cooling plate must undergo leak testing (e.g., pressure decay testing with air or helium leak testing for stricter requirements) at specified pressures (typically exceeding maximum operating pressure by a safety factor). Parts that fail the test must be scrapped or potentially repaired/sealed if feasible and permitted by specifications (though scrapping is safer).
Suppliers like Met3dp, focused on industrial quality, understand the criticality of leak-free performance for applications like battery cooling and implement the necessary process controls and testing protocols to ensure parts meet stringent requirements. Guarantees are typically tied to passing specific, agreed-upon leak test parameters.
Q4: What information is needed to get an accurate quote for a 3D printed cooling plate from a supplier like Met3dp?
A: To provide an accurate quote and assess manufacturability, suppliers typically need the following information:
- Model 3D CAD: In a standard format like STEP (.stp, .step) or IGES (.igs, .iges). Native CAD files might also be acceptable. The model should represent the final desired geometry.
- 2D Engineering Drawing (if available): Essential for defining critical dimensions, tolerances (especially for machined features), surface finish requirements (Ra values for specific surfaces), material specifications, heat treatment requirements, and any specific testing protocols (like leak test parameters).
- Material Specification: Clearly state the desired alloy (e.g., AlSi10Mg, CuCrZr) and any specific standard it must conform to.
- Heat Treatment Requirements: Specify the required heat treatment condition (e.g., Stress Relieved, T6 condition for AlSi10Mg).
- Ilość: Number of parts required (for prototypes, low-volume batches, or estimated annual volume).
- Critical Features & Requirements: Highlight any particularly critical features, tolerances, or functional requirements (e.g., specific internal channel cleanliness, pressure rating).
- Testing & Inspection Requirements: Detail any specific NDT, enhanced dimensional inspection, or specific leak test parameters (pressure, duration, max leak rate).
- Desired Lead Time: Indicate your required delivery timeframe, if critical.
Providing comprehensive information upfront allows the AM service provider to give a more accurate quote, identify potential DfAM opportunities or manufacturing challenges early, and ultimately deliver parts that meet your exact specifications.
Conclusion: Driving the Future of EV Thermal Management with Additive Manufacturing
The electric vehicle revolution is demanding continuous innovation in battery technology, and effective thermal management lies at the heart of unlocking greater performance, faster charging, enhanced safety, and longer battery life. While traditional manufacturing methods have served well, they are increasingly challenged by the complex requirements of modern, high-power-density battery packs. Metal additive manufacturing, specifically Laser Powder Bed Fusion, has emerged as a powerful enabler, offering a transformative approach to designing and producing advanced thermal management solutions like battery cooling plates.
We’ve explored how AM unshackles designers, allowing the creation of cooling plates with intricate internal geometries – conformal channels, TPMS structures, integrated fins – that were previously impossible to manufacture. This translates directly into tangible benefits:
- Superior Thermal Performance: Maximizing heat dissipation and achieving exceptional temperature uniformity across battery modules.
- Significant Lightweighting: Reducing component mass through topology optimization and lattice structures, contributing to extended vehicle range.
- Accelerated Innovation: Enabling rapid prototyping and design iteration without the constraints of traditional tooling.
- Zwiększona niezawodność: Consolidating multiple parts into a single, monolithic structure, minimizing potential leak points.
The journey involves careful material selection, with AlSi10Mg offering a versatile balance of properties and cost, while CuCrZr provides ultimate thermal conductivity for the most demanding applications. Success hinges on embracing Design for Additive Manufacturing (DfAM) principles, understanding achievable precision, implementing necessary post-processing steps like heat treatment and machining, and navigating potential challenges through expert process control.
Choosing the right manufacturing partner is paramount. Look for providers with demonstrated technical expertise, robust quality systems, comprehensive capabilities from design support through post-processing and testing, and experience with relevant materials and applications. Companies like Met3dp, with their integrated capabilities spanning high-quality metal powder production and advanced additive manufacturing solutions, represent the ideal partners to navigate the complexities and unlock the full potential of AM.
The future of EV cooling is intrinsically linked with advancements in manufacturing technology. Additive manufacturing is no longer just a prototyping tool; it is a competitive manufacturing solution enabling next-generation battery performance. As the automotive industry continues its push towards electrification, the adoption of additive manufacturing automotive trends like 3D printed cooling plates will only accelerate.
Ready to explore how additive manufacturing can revolutionize your battery thermal management strategy?
Contact the experts at Met3dp today to discuss your project requirements, leverage their DfAM expertise, and discover how their cutting-edge metal AM solutions can help you design and produce high-performance, lightweight, and reliable battery cooling plates for your electric vehicles. Partner with Met3dp to drive the future of electric mobility.
Udostępnij
MET3DP Technology Co., LTD jest wiodącym dostawcą rozwiązań w zakresie produkcji addytywnej z siedzibą w Qingdao w Chinach. Nasza firma specjalizuje się w sprzęcie do druku 3D i wysokowydajnych proszkach metali do zastosowań przemysłowych.
Zapytaj o najlepszą cenę i spersonalizowane rozwiązanie dla Twojej firmy!
Powiązane artykuły
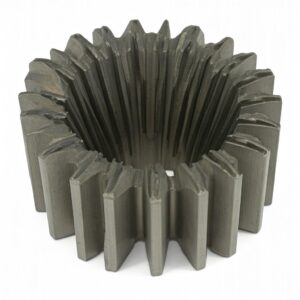
Wysokowydajne segmenty łopatek dysz: Rewolucja w wydajności turbin dzięki drukowi 3D w metalu
Czytaj więcej "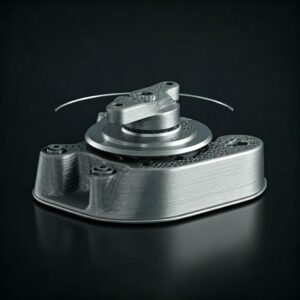
Drukowane w 3D mocowania dla samochodowych czujników radarowych: Precyzja i wydajność
Czytaj więcej "Informacje o Met3DP
Ostatnia aktualizacja
Nasz produkt
KONTAKT
Masz pytania? Wyślij nam wiadomość teraz! Po otrzymaniu wiadomości obsłużymy Twoją prośbę całym zespołem.
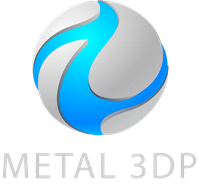
Proszki metali do druku 3D i produkcji addytywnej