Wprowadzenie do ukierunkowanego osadzania energii
Spis treści
Wyobraź sobie budowanie złożonych struktur metalowych warstwa po warstwie, z precyzyjną kontrolą właściwości materiału i minimalną ilością odpadów. To nie jest science fiction; to rzeczywistość Ukierunkowane osadzanie energii (DED), rewolucyjnej technologii druku 3D, która zmienia krajobraz produkcji.
Directed Energy Deposition, znane również pod takimi nazwami jak Laser Engineered Net Shaping (LENS) lub Direct Metal Deposition (DMD), to proces produkcji addytywnej, który wykorzystuje skoncentrowane źródło energii, takie jak laser lub wiązka elektronów, do topienia i osadzania metalowego materiału wsadowego na podłożu. Przypomina to zaawansowany technologicznie pistolet spawalniczy na sterydach, budujący skomplikowane kształty zamiast łączenia elementów.
Niniejszy przewodnik zagłębia się w świat DED, badając jego funkcje, różnorodne proszki metali, które wykorzystuje, jego zastosowania w różnych branżach oraz zalety i ograniczenia, które definiują tę ekscytującą technologię.
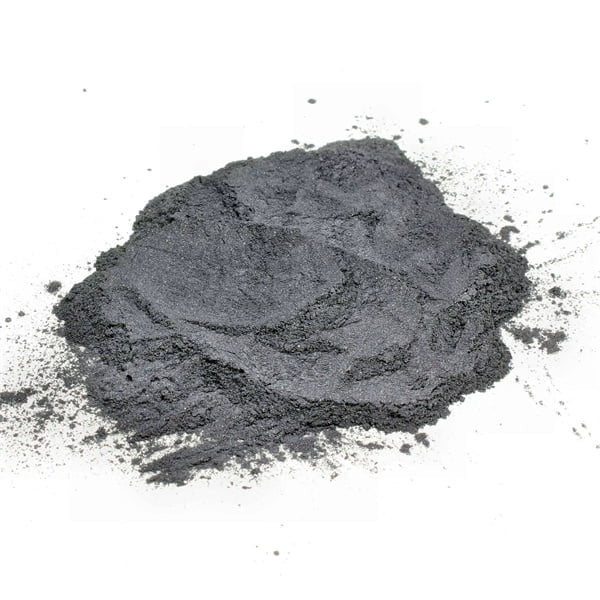
Jak Ukierunkowane osadzanie energii Prace
DED działa w oparciu o synergię trzech kluczowych elementów:
- Źródło energii: Sercem DED jest skoncentrowane źródło energii. Najczęściej wybierane są lasery i wiązki elektronów, oferujące różne zalety. Lasery zapewniają wysoką precyzję i kontrolę, ale mogą być ograniczone przez odbicie materiału. Z drugiej strony, wiązki elektronów sięgają głębiej, oferując lepszą penetrację dla grubszych konstrukcji, ale wymagają komory próżniowej do działania.
- Materiał wsadowy: Budulcem do tworzenia 3D jest proszek metalowy. DED wykorzystuje szeroką gamę proszków metali, z których każdy ma unikalne właściwości i zastosowania. Zagłębimy się w fascynujący świat proszków metali w dedykowanej sekcji później.
- System dostarczania: Magia nie dzieje się bez mechanizmu dostarczania. DED wykorzystuje dyszę, która podaje metalowy proszek do roztopionego basenu utworzonego przez źródło energii. Ta precyzyjna koordynacja zapewnia płynny proces osadzania warstwa po warstwie.
Cała operacja jest koordynowana przez oprogramowanie do projektowania wspomaganego komputerowo (CAD), które przekłada cyfrowy plan na precyzyjne instrukcje dla systemu DED. Pozwala to na tworzenie skomplikowanych geometrii, pustych struktur i funkcji, które byłyby niemożliwe przy użyciu tradycyjnych technik produkcyjnych.
Świat proszków metali: Napędzanie DED Kreacje
Sukces DED zależy od wyboru odpowiedniego proszku metalowego. Podobnie jak w przypadku wyboru idealnych składników do przepisu, właściwości proszku znacząco wpływają na charakterystykę produktu końcowego. Poniżej przedstawiamy dziesięć popularnych proszków metali stosowanych w DED:
1. Tytan (Ti): Lekki, wytrzymały i odporny na korozję tytan jest popularnym wyborem dla przemysłu lotniczego, implantów medycznych i zastosowań sportowych. Jego biokompatybilność sprawia, że idealnie nadaje się do protetyki i implantów dentystycznych.
2. Inconel (stop niklowo-chromowy): Znany z wyjątkowej wytrzymałości w wysokich temperaturach oraz odporności na utlenianie i korozję, Inconel znajduje zastosowanie w silnikach odrzutowych, wymiennikach ciepła i urządzeniach do przetwarzania chemicznego.
3. Stal nierdzewna (SS): Wszechstronna i ekonomiczna stal nierdzewna oferuje dobrą równowagę między wytrzymałością, odpornością na korozję i przystępną ceną. Jest szeroko stosowana w częściach samochodowych, urządzeniach medycznych i ogólnych zastosowaniach przemysłowych.
4. Aluminium (Al): Lekkie i łatwo dostępne aluminium jest popularnym wyborem do zastosowań, w których redukcja masy ma kluczowe znaczenie, takich jak komponenty lotnicze i części samochodowe.
5. Nikiel (Ni): Oferując dobrą odporność na korozję i przewodność elektryczną, nikiel znajduje zastosowanie w elektronice, sprzęcie do przetwarzania chemicznego, a nawet w niektórych zastosowaniach związanych z monetami.
6. Chrom kobaltowy (CoCr): Ten biokompatybilny stop charakteryzuje się wysoką wytrzymałością i odpornością na zużycie, co czyni go preferowanym wyborem w przypadku implantów ortopedycznych i protez stawów.
7. Miedź (Cu): Jako doskonały przewodnik ciepła i elektryczności, miedź znajduje zastosowanie w radiatorach, komponentach elektrycznych, a nawet do tworzenia skomplikowanych kanałów mikroprzepływowych.
8. Wolfram (W): Znany ze swojej niezwykle wysokiej temperatury topnienia i wyjątkowej odporności na zużycie, wolfram jest wykorzystywany w takich zastosowaniach jak elektrody spawalnicze, pociski przeciwpancerne i elementy pieców wysokotemperaturowych.
9. Molibden (Mo): Podobnie jak wolfram, molibden oferuje wytrzymałość w wysokich temperaturach i znajduje zastosowanie w komponentach lotniczych, reaktorach jądrowych i żarnikach do zastosowań oświetleniowych.
10. Hastelloy: Ta rodzina superstopów na bazie niklu charakteryzuje się wyjątkową odpornością na szeroki zakres środowisk korozyjnych, dzięki czemu idealnie nadaje się do zastosowań w przetwórstwie chemicznym, przemyśle naftowym i gazowym oraz energetyce.
Lista ta stanowi zaledwie zarys ogromnej gamy proszków metali dostępnych dla DED. Wybór proszku zależy od pożądanych właściwości produktu końcowego, takich jak wytrzymałość, waga, odporność na korozję i przewodność cieplna.
Więcej niż podstawy: Podział właściwości proszków metali
Nieruchomość | Opis | Znaczenie w DED |
---|---|---|
Rozmiar i rozkład cząstek: | Odnosi się do wielkości i zmienności wielkości cząstek proszku metalu. | Wpływa na płynność, gęstość upakowania i wykończenie powierzchni produktu końcowego. Stały rozmiar cząstek zapewnia płynne osadzanie i minimalizuje porowatość. |
Sferyczność: | Stopień, w jakim cząstka przypomina idealną kulę. | Sferyczne cząstki łatwiej przepływają, są gęściej upakowane i zapewniają lepsze wykończenie powierzchni w porównaniu do cząstek o nieregularnych kształtach. |
Płynność: | Łatwość, z jaką przepływa proszek. | Krytyczne dla spójnego podawania materiału do systemu DED. Słaba płynność może prowadzić do problemów z podawaniem i niespójności w produkcie końcowym. |
Gęstość pozorna: | Gęstość nasypowa proszku. | W zależności od ilości materiału wymaganego do zbudowania części, może to mieć wpływ na koszty produkcji. |
Temperatura topnienia: | Temperatura, w której proszek przechodzi ze stanu stałego w ciekły. | Musi być kompatybilny z wybranym źródłem energii, aby zapewnić prawidłowe topienie i osadzanie. |
Skład chemiczny: | Skład pierwiastkowy proszku. | Decyduje o ostatecznych właściwościach drukowanej części, takich jak wytrzymałość, odporność na korozję i przewodność elektryczna. |
Wybór odpowiedniego proszku: Równowaga
Wybór optymalnego proszku metalicznego do projektu DED wymaga starannego rozważenia kilku czynników. Oto zestawienie, które pomoże w podjęciu tej decyzji:
- Wymagania dotyczące aplikacji: Przeznaczenie produktu końcowego jest najważniejsze. Na przykład komponent silnika odrzutowego będzie wymagał proszku odpornego na wysokie temperatury, takiego jak Inconel, podczas gdy implant medyczny może wymagać opcji biokompatybilnej, takiej jak tytan lub kobalt-chrom.
- Pożądane właściwości: Zidentyfikuj kluczowe cechy, których potrzebujesz w gotowej części. Czy wytrzymałość ma najwyższy priorytet? Być może niezbędna jest odporność na korozję lub lekka konstrukcja. Zrozumienie tych potrzeb pomoże w wyborze proszku.
- Kompatybilność z systemem DED: Upewnij się, że wybrany proszek jest zgodny z możliwościami urządzenia DED. Należy wziąć pod uwagę takie czynniki, jak moc lasera lub dostępność komory próżniowej do DED z wiązką elektronów.
- Koszt i dostępność: Proszki metali mogą znacznie różnić się ceną. Zrównoważ ograniczenia budżetowe z pożądanymi właściwościami i sprawdź dostępność proszku, aby uniknąć opóźnień w produkcji.
Dodatkowe uwagi dotyczące Ukierunkowane osadzanie energii
Podczas gdy proszki metali królują w DED, przyszłość obiecuje włączenie innych materiałów. Naukowcy badają potencjał ich wykorzystania:
- Kompozyty: Mieszanie proszków metali z cząstkami ceramicznymi lub polimerowymi w celu stworzenia materiałów o unikalnych kombinacjach właściwości, takich jak zwiększona odporność na zużycie lub przewodność elektryczna.
- Funkcjonalnie stopniowane materiały (FGM): Stopniowe przechodzenie między różnymi materiałami w ramach jednej kompilacji w celu uzyskania określonych funkcji w różnych regionach części. Wyobraźmy sobie narzędzie z odporną na zużycie końcówką, przechodzące w lżejszy uchwyt - wszystko to wydrukowane w jednym cyklu za pomocą DED.
Te postępy otwierają ekscytujące możliwości dla DED, przesuwając granice projektowania i funkcjonalności w przyszłych zastosowaniach.
Zastosowania Ukierunkowane osadzanie energii
Wszechstronność DED przejawia się w różnorodności zastosowań w wielu branżach. Oto kilka przekonujących przykładów:
- Aerospace: DED przoduje w tworzeniu lekkich komponentów o wysokiej wytrzymałości dla samolotów, takich jak żebra skrzydeł, części podwozia, a nawet elementy silników rakietowych. Zdolność do wytwarzania złożonych geometrii przy minimalnej ilości odpadów sprawia, że DED zmienia zasady gry w tej branży, w której waga ma kluczowe znaczenie.
- Implanty medyczne: Zdolność DED do tworzenia biokompatybilnych części o skomplikowanych wzorach sprawia, że jest to idealne rozwiązanie dla niestandardowych protez, implantów dentystycznych, a nawet implantów czaszkowych. Technologia ta personalizuje opiekę medyczną, poprawiając wyniki i jakość życia pacjentów.
- Motoryzacja: Przemysł motoryzacyjny wykorzystuje technologię DED do prototypowania i niskonakładowej produkcji wysokowydajnych części. DED pozwala na tworzenie lekkich komponentów i złożonych struktur wewnętrznych, z którymi tradycyjna produkcja może mieć trudności.
- Oprzyrządowanie i naprawa: DED oferuje szybki i ekonomiczny sposób tworzenia i naprawy przyrządów, uchwytów i narzędzi skrawających. Wyobraź sobie naprawę uszkodzonej formy lub stworzenie niestandardowego narzędzia na żądanie - DED sprawia, że jest to możliwe.
- Ropa i gaz: DED znajduje zastosowanie w tworzeniu odpornych na korozję komponentów do narzędzi wiertniczych i innego sprzętu używanego w trudnych warunkach naftowych i gazowych.
- Dobra konsumpcyjne: Od spersonalizowanych oprawek okularów po zaprojektowane komponenty rowerowe, DED wkracza na rynek dóbr konsumpcyjnych, umożliwiając tworzenie unikalnych i innowacyjnych produktów.
To tylko kilka przykładów, a w miarę dojrzewania technologii DED możemy spodziewać się jeszcze bardziej przełomowych zastosowań w różnych branżach.
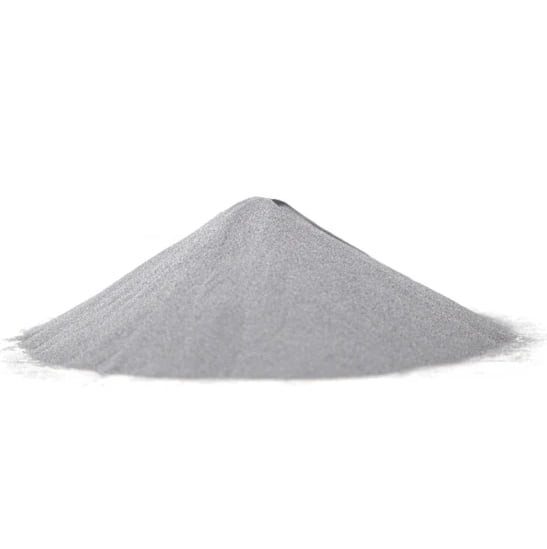
Zalety i ograniczenia Ukierunkowane osadzanie energii
Technologia DED ma wiele zalet, które czynią ją przełomową siłą w produkcji. Ale jak każda technologia, ma swoje ograniczenia. Przyjrzyjmy się obu stronom medalu.
Zalety bezpośredniego osadzania energii:
- Swoboda projektowania: Uwolnij swoją kreatywność! DED pozwala na tworzenie skomplikowanych geometrii, w tym cienkich ścianek, kratownic i podcięć, które byłyby niemożliwe lub bardzo trudne w przypadku tradycyjnych technik. Otwiera to drzwi dla lekkich i wysoce funkcjonalnych projektów.
- Wydajność materiałowa: DED jest procesem produkcyjnym o kształcie zbliżonym do siatki, co oznacza, że minimalna ilość materiału jest marnowana. Niewykorzystany proszek można często poddać recyklingowi, minimalizując ilość odpadów i koszty produkcji.
- Szybkie prototypowanie: Zdolność DED do szybkiego tworzenia funkcjonalnych prototypów przyspiesza cykl rozwoju produktu, umożliwiając szybsze iteracje projektu i skrócenie czasu wprowadzenia produktu na rynek.
- Personalizacja: DED wyróżnia się w tworzeniu niestandardowych części, idealnie dopasowanych do konkretnych potrzeb. Jest to szczególnie cenne w branżach takich jak implanty medyczne i lotnictwo.
- Konsolidacja części: DED może łączyć wiele komponentów w jeden element, upraszczając projekty, skracając czas montażu i potencjalnie poprawiając wydajność części.
- Wszechstronność: Szeroka gama proszków metali i potencjalnie innych materiałów w przyszłości poszerza zakres zastosowań DED.
Ograniczenia Ukierunkowane osadzanie energii:
- Szybkość budowania: W porównaniu z tradycyjnymi technikami, takimi jak odlewanie lub formowanie wtryskowe, DED może być wolniejsze, szczególnie w przypadku większych części. Jest to ciągle rozwijany obszar, w którym badania koncentrują się na szybszym osadzaniu.
- Chropowatość powierzchni: Warstwowy charakter DED może skutkować schodkowym efektem wykończenia powierzchni. Aby uzyskać gładsze wykończenie, konieczne może być zastosowanie technik obróbki końcowej, takich jak obróbka skrawaniem lub polerowanie.
- Właściwości materiału: Chociaż części DED mogą osiągać doskonałe właściwości mechaniczne, nie zawsze mogą idealnie odpowiadać właściwościom kutych lub kutych metali ze względu na nieodłączny charakter procesu wytwarzania przyrostowego. Trwają dalsze badania i rozwój w celu optymalizacji procesów DED dla różnych materiałów.
- Koszt: Systemy DED mogą być drogie, a koszt proszków metali może się znacznie różnić. Może to ograniczać ich zastosowanie w produkcji wielkoseryjnej tanich części.
- Naprężenie szczątkowe: Szybkie cykle nagrzewania i chłodzenia podczas DED mogą wprowadzać naprężenia szczątkowe do części. Odpowiednie techniki projektowania i obróbki końcowej mogą pomóc złagodzić ten problem.
FAQ
Oto niektóre z najczęściej zadawanych pytań dotyczących DED:
P: Jakie są zalety DED w porównaniu z innymi technologiami druku 3D, takimi jak FDM (Fused Deposition Modeling)?
DED oferuje kilka zalet w porównaniu do FDM. Po pierwsze, DED wykorzystuje proszki metali, umożliwiając tworzenie funkcjonalnych części metalowych. FDM, z drugiej strony, jest zazwyczaj ograniczony do tworzyw sztucznych i innych polimerów. Po drugie, części DED mają zazwyczaj lepsze właściwości mechaniczne w porównaniu do części FDM. Wreszcie, DED pozwala na większą swobodę projektowania dzięki możliwości tworzenia złożonych geometrii.
P: Czy DED może być używany do naprawy części metalowych?
O: Absolutnie! Zdolność DED do precyzyjnego osadzania materiału sprawia, że jest to idealne rozwiązanie do naprawy uszkodzonych elementów metalowych. Może to być opłacalne i oszczędzające czas rozwiązanie w porównaniu do tradycyjnych metod wymiany.
P: Jaka jest przyszłość Directed Energy Deposition?
O: Przyszłość DED rysuje się w jasnych barwach! Możemy spodziewać się postępów w kilku obszarach:
- Większa szybkość kompilacji: Naukowcy stale opracowują metody zwiększania szybkości osadzania, dzięki czemu DED staje się bardziej konkurencyjny dla produkcji na większą skalę.
- Multi-Material DED: Zdolność do płynnego łączenia różnych proszków metali, a nawet materiałów metalowych i niemetalowych w ramach jednej konstrukcji otwiera ekscytujące możliwości tworzenia części o właściwościach dostosowanych do różnych regionów.
- Standaryzacja: W miarę dojrzewania technologii DED, standaryzacja procesów i materiałów będzie odgrywać kluczową rolę w zapewnianiu jakości i powtarzalności.
- Niższe koszty: Oczekuje się, że wraz z postępem technologicznym i wzrostem popularności, koszt systemów DED i proszków metali spadnie, dzięki czemu DED będzie bardziej dostępny dla szerszego grona producentów.
DED ma ogromny potencjał, aby zrewolucjonizować różne branże. Jego zdolność do tworzenia złożonych, funkcjonalnych części metalowych przy minimalnej ilości odpadów i dużej swobodzie projektowania sprawia, że jest to technologia, którą należy obserwować. W miarę rozwoju DED możemy spodziewać się jeszcze bardziej przełomowych zastosowań, kształtujących przyszłość produkcji.
Udostępnij
MET3DP Technology Co., LTD jest wiodącym dostawcą rozwiązań w zakresie produkcji addytywnej z siedzibą w Qingdao w Chinach. Nasza firma specjalizuje się w sprzęcie do druku 3D i wysokowydajnych proszkach metali do zastosowań przemysłowych.
Zapytaj o najlepszą cenę i spersonalizowane rozwiązanie dla Twojej firmy!
Powiązane artykuły
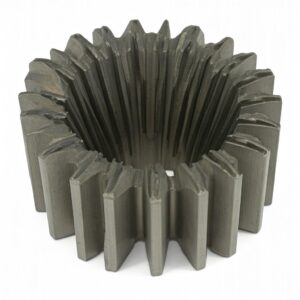
Wysokowydajne segmenty łopatek dysz: Rewolucja w wydajności turbin dzięki drukowi 3D w metalu
Czytaj więcej "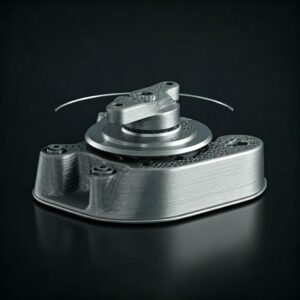
Drukowane w 3D mocowania dla samochodowych czujników radarowych: Precyzja i wydajność
Czytaj więcej "Informacje o Met3DP
Ostatnia aktualizacja
Nasz produkt
KONTAKT
Masz pytania? Wyślij nam wiadomość teraz! Po otrzymaniu wiadomości obsłużymy Twoją prośbę całym zespołem.
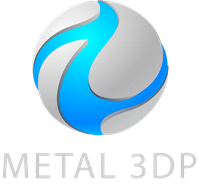
Proszki metali do druku 3D i produkcji addytywnej