Drone Battery Enclosures with 3D Printed Aluminum
Spis treści
Introduction: Revolutionizing Drone Performance with 3D Printed Aluminum Battery Enclosures
The unmanned aerial vehicle (UAV), or drone, has rapidly transitioned from a niche technology to an indispensable tool across countless industries. From aerial surveillance and precision agriculture to package delivery and infrastructure inspection, drones offer unprecedented capabilities. However, their performance – particularly flight time, payload capacity, and durability – is intrinsically linked to the components they carry. Among the most critical of these is the battery enclosure. This component does far more than simply hold the power source; it protects sensitive battery cells from environmental hazards, physical impacts, and thermal fluctuations, while often serving as a structural element within the drone’s airframe.
Traditionally, drone battery enclosures have been manufactured using methods like CNC machining from billet aluminum or plastic injection molding. While effective, these methods present limitations, particularly when optimizing for weight, complex geometries, and rapid design iteration – crucial factors in the competitive drone market. Enter metal additive manufacturing (AM), commonly known as metal Drukowanie 3D. This disruptive technology offers a paradigm shift in how high-performance components like battery enclosures are designed and produced.
By utilizing advanced processes such as Laser Powder Bed Fusion (LPBF), manufacturers can now create drone battery enclosures from high-performance aluminum alloys like AlSi10Mg and Scalmalloy® with designs previously impossible to achieve. Metal AM enables the production of highly optimized, lightweight structures with intricate internal features for cooling, integrated mounting points, and organic shapes that minimize aerodynamic drag. This directly translates to drones that can fly longer, carry more, and withstand harsher operating conditions. For engineers pushing the boundaries of drone capabilities and procurement managers seeking reliable, high-performance component suppliers, understanding the potential of 3D printed aluminum battery enclosures is paramount. Companies specializing in druk 3D z metalu, like Met3dp, are at the forefront, offering not only advanced printing services but also the high-quality metal powders essential for achieving optimal results. This technology is not just an alternative manufacturing method; it’s an enabler of next-generation drone performance.
Applications and Use Cases: Where 3D Printed Aluminum Enclosures Take Flight
The demand for robust, lightweight, and precisely manufactured drone battery enclosures spans a wide array of demanding sectors. The unique advantages offered by 3D printed aluminum alloys like AlSi10Mg and Scalmalloy® make them particularly suitable for applications where performance cannot be compromised. Procurement managers sourcing components for drone fleets and engineers designing UAVs for specific tasks are increasingly turning to AM suppliers for solutions.
Key Industries and Functions:
- Przemysł lotniczy i obronny:
- Zastosowania: Surveillance drones (ISR), tactical UAVs, target drones, research & development platforms.
- Requirements: Extreme lightweighting for maximum endurance and payload, high structural integrity to withstand G-forces and harsh landings, thermal management for high-discharge batteries, resistance to vibration and shock, potential need for specific electromagnetic shielding properties. 3D printed Scalmalloy® is often favored for its exceptional strength-to-weight ratio.
- B2B Focus: Aerospace component manufacturers, defense contractors, government procurement agencies seeking reliable drone parts distributors and qualified AM suppliers.
- Commercial Inspection & Monitoring:
- Zastosowania: Power line inspection, wind turbine blade analysis, bridge and infrastructure assessment, pipeline monitoring, construction site surveying.
- Requirements: Durability for frequent deployment in varying weather conditions, protection against dust and moisture ingress (IP rating), secure battery mounting to prevent disconnects during complex maneuvers, efficient heat dissipation during long flights. 3D printed AlSi10Mg offers a good balance of durability, weight, and thermal properties.
- B2B Focus: Infrastructure companies, energy providers, engineering firms, surveying companies looking for bulk drone component suppliers and custom enclosure manufacturers.
- Agriculture:
- Zastosowania: Crop monitoring, precision spraying, soil analysis, livestock management.
- Requirements: Resistance to dust, chemicals (fertilizers, pesticides), and moisture common in agricultural environments. Lightweight design to maximize flight time over large fields. Secure mounting for easy battery swaps during continuous operation.
- B2B Focus: Agricultural technology providers, large-scale farming operations, drone service providers specializing in agriculture, seeking durable and cost-effective enclosure solutions from wholesale suppliers.
- Logistics & Delivery:
- Zastosowania: Last-mile package delivery, medical supply transport, internal warehouse logistics.
- Requirements: High impact resistance to protect batteries during landing and handling, aerodynamic designs for energy efficiency, features for automated battery swapping systems, consistent quality for large fleet deployment. Both AlSi10Mg and Scalmalloy® can be selected based on specific weight vs. strength trade-offs.
- B2B Focus: Logistics companies, e-commerce giants, medical distributors, warehouse automation specialists searching for scalable manufacturing partners and reliable drone component distributors.
- Mapping & Surveying:
- Zastosowania: Geographic Information System (GIS) data acquisition, terrain modeling, environmental monitoring, archaeological surveying.
- Requirements: Stable platform – enclosure contributes to overall drone rigidity, minimizing vibration affecting sensor data. Lightweighting for extended mapping missions. Protection against environmental factors during remote deployments.
- B2B Focus: Geospatial companies, environmental agencies, research institutions, surveying service providers requiring precision-manufactured components from specialized AM suppliers.
Functional Demands Met by 3D Printed Aluminum:
- Redukcja wagi: Critical for extending flight time and increasing payload capacity across all applications. AM allows for topology optimization and lattice structures impossible with traditional methods.
- Zarządzanie temperaturą: Efficiently dissipating heat generated by high-performance batteries is crucial for safety and longevity. AM enables the integration of complex cooling channels and heat sinks directly into the enclosure design.
- Impact Resistance & Durability: Protecting the battery during rough landings, transport, or in-flight incidents is vital. Aluminum alloys offer superior impact resistance compared to many plastics.
- Environmental Protection: Sealing against dust, moisture, and potentially corrosive elements is essential for reliable operation in diverse environments.
- Design Complexity & Integration: AM allows for consolidating multiple functions into a single part – integrating mounts, connectors, thermal features, and structural supports, reducing assembly time and potential points of failure.
By leveraging the capabilities of metal AM, drone manufacturers and operators can procure battery enclosures specifically tailored to the unique demands of their application, enhancing overall UAV performance, reliability, and mission success. Finding a capable metal additive manufacturing partner who understands these specific industry needs is key.
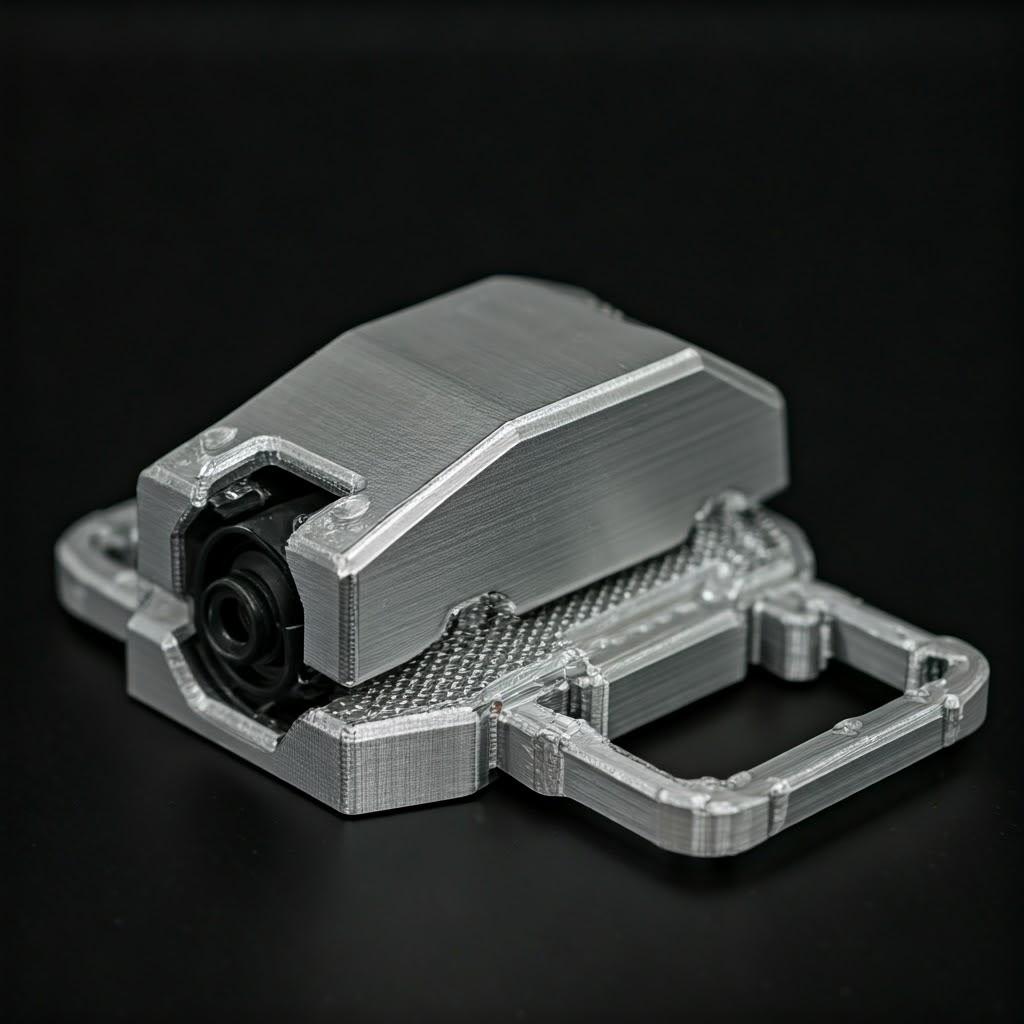
Why Metal 3D Printing for Drone Battery Enclosures? Unlocking Design Freedom and Performance
Choosing the right manufacturing process is as critical as selecting the right material for drone battery enclosures. While traditional methods like CNC machining and injection molding have served the industry well, metal additive manufacturing, particularly Laser Powder Bed Fusion (LPBF), offers compelling advantages that directly address the core challenges of modern drone design: weight, complexity, performance, and speed-to-market. For engineers seeking innovation and procurement managers demanding efficiency and reliability, understanding these benefits is crucial when evaluating drone component suppliers.
Comparison: Metal AM vs. Traditional Methods for Drone Battery Enclosures
Cecha | Metal AM (LPBF – AlSi10Mg/Scalmalloy®) | CNC Machining (Aluminum Block) | Plastic Injection Molding |
---|---|---|---|
Złożoność projektu | Very High (complex internal channels, lattices, organic shapes) | Moderate (limited by tool access, undercuts difficult) | High (but requires complex, expensive tooling) |
Weight Optimization | Excellent (topology optimization, thin walls, lattices feasible) | Good (material removal, but limited by subtractive nature) | Fair (density limited by plastic material, often requires thicker walls for strength) |
Konsolidacja części | High (can integrate mounts, clips, thermal features) | Limited (multiple parts often required) | Moderate (some features can be molded in) |
Właściwości materiału | Excellent (High strength-to-weight – Scalmalloy®, good thermal conductivity – AlSi10Mg) | Excellent (properties of bulk aluminum) | Variable (lower strength, stiffness, thermal conductivity than aluminum) |
Koszt oprzyrządowania | None (Direct digital manufacturing) | Low (fixtures may be needed) | Very High (mold design & fabrication) |
Lead Time (Prototype) | Fast (Days) | Moderate (Days to weeks) | Very Slow (Months for tooling) |
Lead Time (Production) | Moderate (Scalable with machines) | Fast (for established process) | Very Fast (once mold is ready) |
Cost per Part (Low Vol) | Umiarkowany do wysokiego | Wysoki | Extremely High (due to tooling) |
Cost per Part (High Vol) | Umiarkowany | Umiarkowany | Niski |
Odpady materiałowe | Low (powder recyclability) | High (material subtracted) | Low (runners/sprues can be reground) |
Ideal Use Case | Complex, lightweight, high-performance parts, rapid iteration, custom designs | Simpler geometries, established designs, high volume | Very high volume, lower performance requirements, simpler designs |
Export to Sheets
Key Advantages of Metal AM for Drone Battery Enclosures:
- Niezrównana swoboda projektowania: This is perhaps the most significant advantage. LPBF builds parts layer-by-layer, freeing designers from the constraints of traditional manufacturing.
- Geometrie złożone: Create intricate internal cooling channels optimized via computational fluid dynamics (CFD) for superior thermal management.
- Topology Optimization: Utilize software to remove material strategically from low-stress areas, achieving maximum weight reduction while maintaining structural integrity.
- Struktury kratowe: Incorporate internal lattice structures for further weight savings and enhanced impact absorption.
- Konsolidacja części: Integrate mounting brackets, connector housings, wire routing channels, and structural reinforcements directly into the enclosure design, reducing part count, assembly time, and potential failure points. This simplifies the supply chain for drone manufacturers needing fewer individual components.
- Significant Weight Reduction: Flight time is currency in the drone world. Every gram saved extends endurance or increases payload capacity.
- Metal AM allows for wall thicknesses and complex stiffening features (ribs, lattices) that are difficult or impossible to machine.
- High-strength alloys like Scalmalloy® enable even thinner, lighter designs compared to standard aluminum grades used in CNC machining, while maintaining or exceeding strength requirements.
- Szybkie prototypowanie i iteracja: The drone industry evolves rapidly. AM allows designers to quickly move from CAD model to functional metal prototype.
- Test different enclosure designs, thermal strategies, or mounting configurations in days, not weeks or months.
- Accelerate the development cycle and get improved drone models to market faster.
- Supply Chain Optimization & On-Demand Manufacturing:
- Skrócony czas realizacji: For low-to-mid volume production, AM can often deliver finished parts faster than waiting for complex CNC setups or injection mold tooling.
- Digital Inventory: Designs exist as digital files, allowing parts to be printed on-demand, reducing warehousing costs and risks of obsolescence. This is attractive for B2B customers managing diverse drone fleets or requiring spare parts quickly.
- Decentralized Manufacturing: Parts can potentially be printed closer to the point of need, shortening supply lines, a key consideration for global drone operations and distributors.
- Zwiększona wydajność: The combination of optimized designs and advanced materials directly translates to better-performing drones.
- Improved Thermal Management: Prevents battery overheating, enhancing safety and extending battery life.
- Zwiększona wytrzymałość: Robust aluminum enclosures offer superior protection against impacts and environmental factors compared to plastics.
- Optimized Aerodynamics: Smooth, organic shapes possible with AM can contribute to reduced drag.
While CNC machining remains viable for simpler, high-volume enclosure designs, and injection molding excels at mass production of plastic parts, metal additive manufacturing provides a unique combination of design freedom, weight optimization, and performance enhancement crucial for cutting-edge drone battery enclosures. Partnering with an expert AM provider like Met3dp ensures access to the necessary technology, materials, and expertise to fully leverage these advantages.
Material Focus: AlSi10Mg and Scalmalloy® for Optimal Drone Enclosure Performance
The choice of material is fundamental to the success of any engineering component, and drone battery enclosures are no exception. Additive manufacturing unlocks the ability to use advanced metal alloys specifically tailored for demanding applications. For 3D printed drone battery enclosures, two aluminum alloys stand out: AlSi10Mg and Scalmalloy®. Both offer distinct advantages, and understanding their properties is key for engineers and procurement managers selecting the optimal solution for their specific UAV requirements. Sourcing these high-performance powders from reputable suppliers like Met3dp, who utilize advanced gas atomization and PREP technologies for high sphericity and flowability, is crucial for achieving consistent, high-quality prints.
AlSi10Mg: The Versatile Workhorse
AlSi10Mg is one of the most common and well-understood aluminum alloys used in metal additive manufacturing, particularly LPBF. It’s essentially an aluminum alloy with silicon (Si ≈ 10%) and magnesium (Mg < 0.5%) as the primary alloying elements.
- Kluczowe właściwości:
- Dobry stosunek wytrzymałości do wagi: While not as strong as Scalmalloy®, AlSi10Mg offers significantly better strength than most plastics and a good balance for many drone applications.
- Doskonała przewodność cieplna: Aluminum alloys naturally conduct heat well. AlSi10Mg is effective at dissipating heat generated by drone batteries, preventing overheating.
- Dobra odporność na korozję: Offers adequate resistance to environmental factors typically encountered by drones.
- Spawalność: Although less relevant for AM, it indicates good fusion characteristics during the LPBF process.
- Przetwarzalność: It’s relatively easy to process using standard LPBF parameters, making it widely available and often more cost-effective.
- Opcje przetwarzania końcowego: Responds well to standard post-processing steps like heat treatment (T6 condition significantly improves strength and hardness), machining, and surface finishing.
- Ideal Applications:
- General-purpose drone battery enclosures where a good balance of weight, strength, thermal performance, and cost is required.
- Drones for commercial inspection, agriculture, mapping, and some logistics applications.
- Prototypes requiring functional testing with representative material properties.
Scalmalloy®: The High-Performance Champion
Scalmalloy® is a patented high-performance aluminum-magnesium-scandium (Al-Mg-Sc) alloy specifically developed for additive manufacturing by APWORKS. It pushes the boundaries of what’s possible with 3D printed aluminum.
- Kluczowe właściwości:
- Wyjątkowy stosunek wytrzymałości do wagi: This is Scalmalloy®’s defining characteristic. It offers specific strength (strength divided by density) comparable to high-strength titanium alloys, making it ideal for applications where minimizing weight is absolutely critical. Its yield strength can be more than double that of AlSi10Mg in the as-built or heat-treated condition.
- High Ductility and Toughness: Unlike some very high-strength materials, Scalmalloy® retains good ductility, making it resistant to cracking under stress or impact.
- Excellent Fatigue Resistance: Crucial for components subjected to vibration and cyclic loading, common in drone operations.
- Dobra odporność na korozję: Similar or slightly better than AlSi10Mg in many environments.
- Stable Microstructure: Maintains good properties even at moderately elevated temperatures.
- Przetwarzalność: Requires optimized LPBF process parameters specific to the alloy; typically processed by more specialized AM service providers.
- Ideal Applications:
- High-performance drones where minimizing every gram is critical (aerospace, defense, competitive racing drones).
- Enclosures that serve a significant structural function within the airframe.
- Applications requiring maximum durability and resistance to fatigue failure.
- Situations where the higher material and processing cost is justified by significant performance gains.
Material Comparison Table:
Nieruchomość | AlSi10Mg (Typical LPBF, T6 Heat Treated) | Scalmalloy® (Typical LPBF, Heat Treated) | Jednostka | Significance for Drone Enclosures |
---|---|---|---|---|
Gęstość | ~2.67 | ~2.66 | g/cm³ | Similar density, both lightweight compared to steel. |
Wytrzymałość na rozciąganie | ~230 – 300 | ~450 – 520 | MPa | Scalmalloy® is significantly stronger, allowing thinner/lighter designs. |
Ostateczna wytrzymałość na rozciąganie | ~330 – 480 | ~500 – 580 | MPa | Higher strength indicates better resistance to failure under load. |
Wydłużenie przy zerwaniu | ~3 – 10 | ~10 – 18 | % | Scalmalloy® has higher ductility, making it less brittle. |
Wytrzymałość zmęczeniowa | Umiarkowany | Wysoki | – | Scalmalloy® better withstands vibrations and repeated stresses. |
Przewodność cieplna | ~130 – 150 | ~110 – 130 | W/(m-K) | AlSi10Mg slightly better at conducting heat away from the battery. |
Max Service Temp. | ~150 | ~200 | °C | Both suitable for typical battery operating temperatures. |
Koszt względny | Niższy | Wyższy | – | Scalmalloy® powder and processing are generally more expensive. |
Process Maturity | Wysoki | Umiarkowany-wysoki | – | AlSi10Mg parameters are more standardized across machines. |
Export to Sheets
Choosing the Right Material:
The decision between AlSi10Mg and Scalmalloy® depends on a careful analysis of the drone’s specific requirements:
- Prioritize Weight Savings Above All Else? Scalmalloy® is the clear choice, despite the higher cost. This is often the case for high-endurance aerospace or defense UAVs sourced by major contractors.
- Need Good Performance and Thermal Management at a Moderate Cost? AlSi10Mg offers an excellent balance and is suitable for a wide range of commercial drone applications procured by various B2B customers.
- Is Extreme Durability or Fatigue Life Critical? Scalmalloy®’s superior mechanical properties provide an advantage.
- Working with a Specific Budget? AlSi10Mg will generally result in a lower final part cost.
Consulting with an experienced metal AM service provider, such as Met3dp, is highly recommended. Their materials scientists and application engineers can help analyze the specific needs of your drone battery enclosure project, recommend the optimal aluminum alloy, and ensure access to high-quality, contamination-free powders crucial for reliable additive manufacturing. They can provide guidance on sourcing these materials and discuss options for wholesale powder supply or integrated printing services.
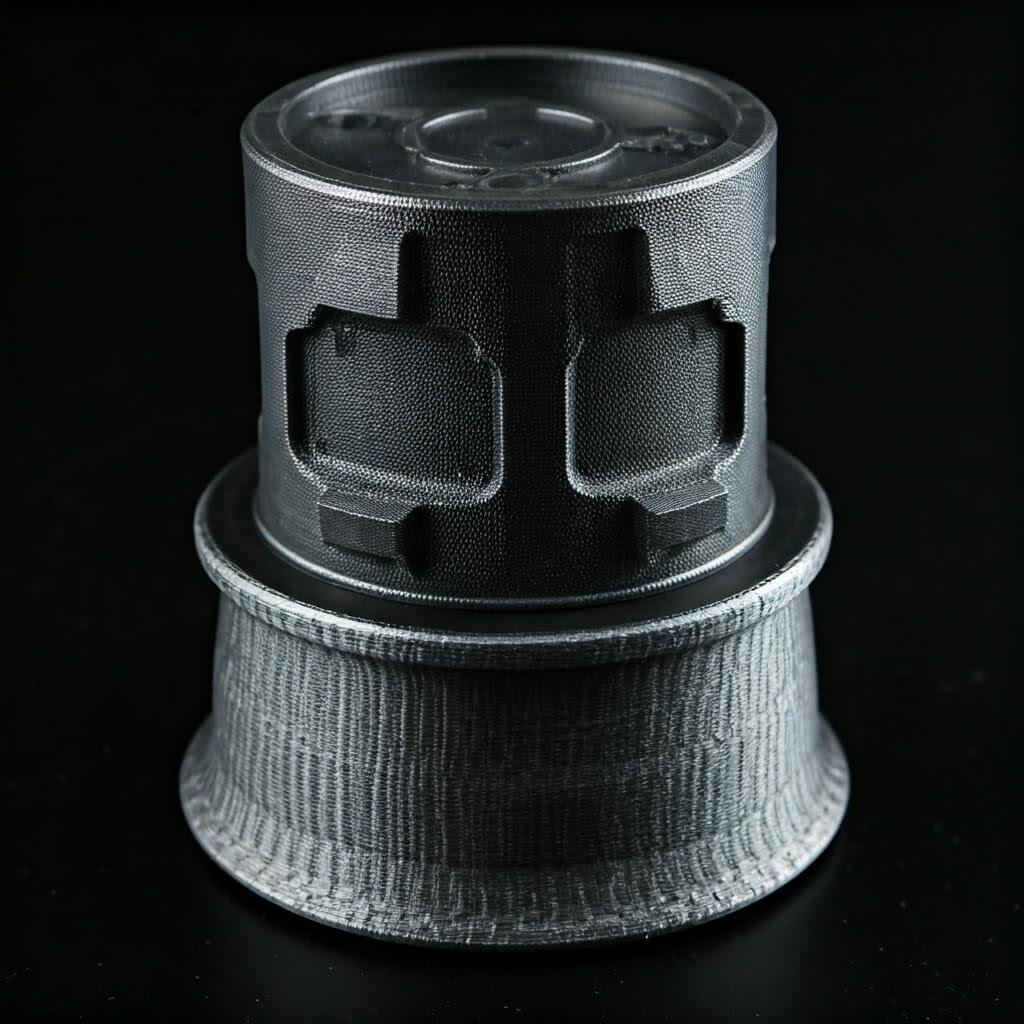
Design for Additive Manufacturing (DfAM): Optimizing Enclosures for 3D Printing Success
Simply replicating a design intended for CNC machining or injection molding rarely unlocks the full potential of metal additive manufacturing. To truly leverage the benefits of 3D printed aluminum for drone battery enclosures – achieving minimum weight, maximum performance, and integrated functionality – engineers must embrace Design for Additive Manufacturing (DfAM) principles. DfAM is not just about making a part printable; it’s about fundamentally rethinking the design to exploit the unique capabilities of layer-by-layer fabrication offered by technologies like Laser Powder Bed Fusion (LPBF). For B2B clients like drone manufacturers and component suppliers, adopting DfAM translates directly into superior products and a competitive edge.
Key DfAM Principles for Drone Battery Enclosures:
- Topology Optimization & Lightweighting:
- Concept: Use software algorithms to analyze the stress distribution within the enclosure under expected load conditions (vibration, impact, structural loads). The software then intelligently removes material from low-stress areas, leaving behind an organic, load-bearing structure that is significantly lighter yet meets all performance requirements.
- Zastosowanie: Transform a standard boxy enclosure into a highly efficient, skeletal structure. This drastically reduces weight, directly improving drone flight time and payload capacity – critical metrics for procurement decisions.
- AM Advantage: Creating these complex, optimized shapes is practically impossible with traditional subtractive methods like CNC machining.
- Struktury kratowe:
- Concept: Incorporate internal, repeating geometric patterns (lattices) within the enclosure’s solid volume or walls. These structures significantly reduce mass while providing tailored stiffness, energy absorption, and facilitating heat dissipation. Different lattice types (e.g., gyroid, diamond, honeycomb) offer varying properties.
- Zastosowanie: Fill sections of the enclosure with lightweight lattices, replace solid walls with lattice-reinforced skins, or create dedicated crumple zones for impact absorption, protecting the sensitive battery cells.
- AM Advantage: LPBF is uniquely suited to creating these intricate, fine-featured internal structures layer by layer.
- Konsolidacja części:
- Concept: Redesign assemblies of multiple components into a single, monolithic printed part.
- Zastosowanie: Integrate battery cell separators, mounting points for the drone frame, housings for connectors (e.g., XT60, AS150), wire routing clips, and even thermal management features (heat sinks, airflow channels) directly into the main enclosure body.
- AM Advantage: Reduces part count, eliminates assembly steps and labor costs, minimizes potential points of failure (fasteners, joints), simplifies inventory management for drone manufacturers, and often results in a lighter, stiffer final assembly. This streamlining is highly attractive to wholesale buyers and distributors looking for efficient solutions.
- Thermal Management Optimization:
- Concept: Design features specifically to enhance heat dissipation from the battery cells.
- Zastosowanie: Incorporate complex, conformal cooling channels within the enclosure walls for liquid cooling (in highly specialized drones) or intricately shaped fins and pins optimized through CFD analysis for passive air cooling. Design thin walls using thermally conductive alloys like AlSi10Mg to facilitate heat transfer to the external airflow.
- AM Advantage: AM allows the creation of internal channels and external features with shapes and complexities that follow the heat path precisely, far exceeding the capabilities of machining or molding.
- Designing for Printability (Minimizing Supports & Overhangs):
- Concept: While AM offers great freedom, practical considerations during the build process must be accounted for. Steeper overhangs (typically >45° from the horizontal) require support structures during printing, which must be removed later.
- Zastosowanie: Orient the part on the build plate strategically. Use chamfers or self-supporting angles (>=45°) instead of sharp horizontal overhangs where possible. Design internal channels with tear-drop or diamond shapes to make them self-supporting. Minimize features requiring extensive internal supports that are difficult or impossible to remove.
- AM Advantage: Although supports are often necessary, clever DfAM can significantly reduce their extent, minimizing post-processing time, material waste, and the risk of surface imperfections where supports were attached. Consulting with AM service providers like Met3dp during the design phase can help optimize orientation and support strategy.
- Feature Integration & Functionality:
- Concept: Think beyond just containment. How can the enclosure add more value?
- Zastosowanie: Design snap-fit features (using AM’s precision), integrated hinges, textured surfaces for grip, embedded channels for sensors, or features that facilitate automated handling or battery swapping.
- AM Advantage: AM’s precision and complexity allow for the seamless integration of fine mechanical and functional features.
DfAM Workflow Considerations:
- Collaboration: Close collaboration between the drone design engineers and the AM service provider’s application engineers is crucial. Experts at facilities like Met3dp can provide invaluable feedback on design feasibility, material selection (AlSi10Mg vs. Scalmalloy®), orientation strategy, and potential cost implications early in the design cycle.
- Software Tools: Utilize CAD software with AM-specific modules, topology optimization tools, and lattice generation capabilities. Simulation tools (FEA, CFD) are vital for validating optimized designs.
- Iterative Process: DfAM is often iterative. Print prototypes, test them, and refine the design based on real-world performance and printability feedback. AM’s speed makes this iteration cycle much faster than traditional methods.
By embracing DfAM principles, engineers can move beyond simple replacement parts and create drone battery enclosures that are lighter, stronger, more thermally efficient, and offer greater integrated functionality, ultimately contributing to superior drone performance and reliability – key selling points for B2B customers in the competitive UAV market.
Achievable Tolerances, Surface Finish, and Dimensional Accuracy in Aluminum AM
While metal additive manufacturing offers unparalleled design freedom, it’s essential for engineers and procurement managers to have realistic expectations regarding the achievable precision, surface finish, and dimensional accuracy of 3D printed aluminum drone battery enclosures. Unlike the mirror finishes and micron-level tolerances often associated with precision CNC machining, LPBF parts have inherent characteristics stemming from the layer-wise fusion process. However, with careful process control and appropriate post-processing, high levels of accuracy suitable for most drone applications can be readily achieved.
Understanding Key Terms:
- Dokładność wymiarowa: How closely the final printed part conforms to the nominal dimensions specified in the CAD model. Often expressed as a tolerance range (e.g., ±0.1 mm).
- Surface Finish (Roughness): The measure of the fine-scale irregularities on the part’s surface. Commonly quantified using the average roughness parameter, Ra (measured in micrometers, µm). A lower Ra value indicates a smoother surface.
- Tolerance: The permissible limit or limits of variation in a physical dimension.
Factors Influencing Precision in LPBF:
- LPBF Process Parameters: Laser power, scan speed, layer thickness (typically 20-60 µm for aluminum), hatch spacing, and scan strategy all influence the melt pool characteristics and solidification, affecting both surface finish and accuracy. Optimized parameters developed by experienced AM providers are crucial.
- Materiał: While both AlSi10Mg and Scalmalloy® can achieve good precision, slight variations might exist due to their different melting behaviors and responses to thermal stress. Met3dp’s expertise with advanced powders like TiNi, TiTa, TiAl, TiNbZr, CoCrMo, and various steels informs their handling of specific aluminum alloys.
- Part Geometry and Size: Larger parts are more susceptible to thermal distortion (warping) during the build, potentially affecting overall dimensional accuracy. Complex geometries with fine features may have localized variations.
- Orientation on Build Plate: The orientation significantly impacts both surface finish and accuracy.
- Upward-facing surfaces: Generally smoother and more accurate.
- Downward-facing surfaces (supported): Tend to be rougher due to support structure contact points. Ra values can be significantly higher.
- Side walls: Show layer lines; roughness depends on the angle relative to the build plate (stair-stepping effect on shallow angles).
- Struktury wsparcia: Where supports touch the part, they leave small marks (“witness marks”) after removal, impacting local surface finish and requiring refinement.
- Thermal Stress: The repeated heating and cooling cycles inherent to LPBF induce residual stresses, which can cause distortion if not managed through proper build strategy and post-process heat treatment (stress relief).
- Machine Calibration: The accuracy and calibration of the LPBF machine itself (galvanometer mirrors, laser focus, recoater system) are fundamental. Providers like Met3dp invest in industry-leading equipment known for accuracy and reliability.
Typical Achievable Values for LPBF Aluminum (AlSi10Mg/Scalmalloy®):
Parametr | Stan powykonawczy | After Post-Processing (Machining/Polishing) | Uwagi |
---|---|---|---|
Dokładność wymiarowa | Typically ±0.1 mm to ±0.3 mm (or ±0.1-0.2% of dimension for larger parts) | Can achieve ±0.01 mm to ±0.05 mm on critical features | Overall accuracy depends heavily on size, geometry, and stress relief. Machining is needed for tight tolerances. |
Chropowatość powierzchni (Ra) | |||
Upward-facing Surfaces | 6 – 15 µm | < 1 µm (polished), 1-6 µm (machined/blasted) | Relatively smooth due to direct laser melting. |
Side Walls | 8 – 20 µm | < 1 µm (polished), 1-6 µm (machined/blasted) | Layer lines visible; roughness increases on shallow-angled walls (“stair-stepping”). |
Downward-facing (Supported) | 15 – 40 µm (or higher) | < 1 µm (polished), 1-6 µm (machined/blasted) | Roughest surface due to support contact; requires significant finishing if smoothness is critical. |
Minimalny rozmiar funkcji | ~0.3 – 0.5 mm | – | Limited by laser spot size and melt pool dynamics. |
Minimalna grubość ścianki | ~0.4 – 1.0 mm | – | Depends on height/aspect ratio; requires careful design to avoid warping or print failure. |
Export to Sheets
Managing Expectations and Achieving Requirements:
- Identify Critical Features: Determine which dimensions and surfaces require the tightest tolerances and smoothest finishes (e.g., mating interfaces, battery contact points, sealing surfaces).
- Design for Post-Processing: If tight tolerances or very smooth finishes are needed, design the part with extra material (“machining stock”) on those specific features to allow for post-process CNC machining or polishing.
- Specify Requirements Clearly: Communicate tolerance and surface finish requirements clearly to the AM service provider using standardized drawing callouts (GD&T – Geometric Dimensioning and Tolerancing).
- Discuss Orientation: Work with the provider to determine the optimal build orientation that balances support needs, surface finish on critical faces, and potential distortion.
- Leverage Post-Processing: Understand that post-processing (machining, bead blasting, tumbling, polishing) is often necessary to achieve the final desired tolerances and surface finish.
While as-built LPBF aluminum parts may not match the precision of meticulously machined components across all surfaces, they offer good baseline accuracy suitable for many functional requirements in drone battery enclosures. By understanding the process capabilities and planning for necessary post-processing steps on critical features, engineers can confidently utilize 3D printed aluminum to create high-performance, reliable enclosures. Partnering with a knowledgeable AM provider ensures access to optimized metody drukowania and realistic guidance on achievable precision.
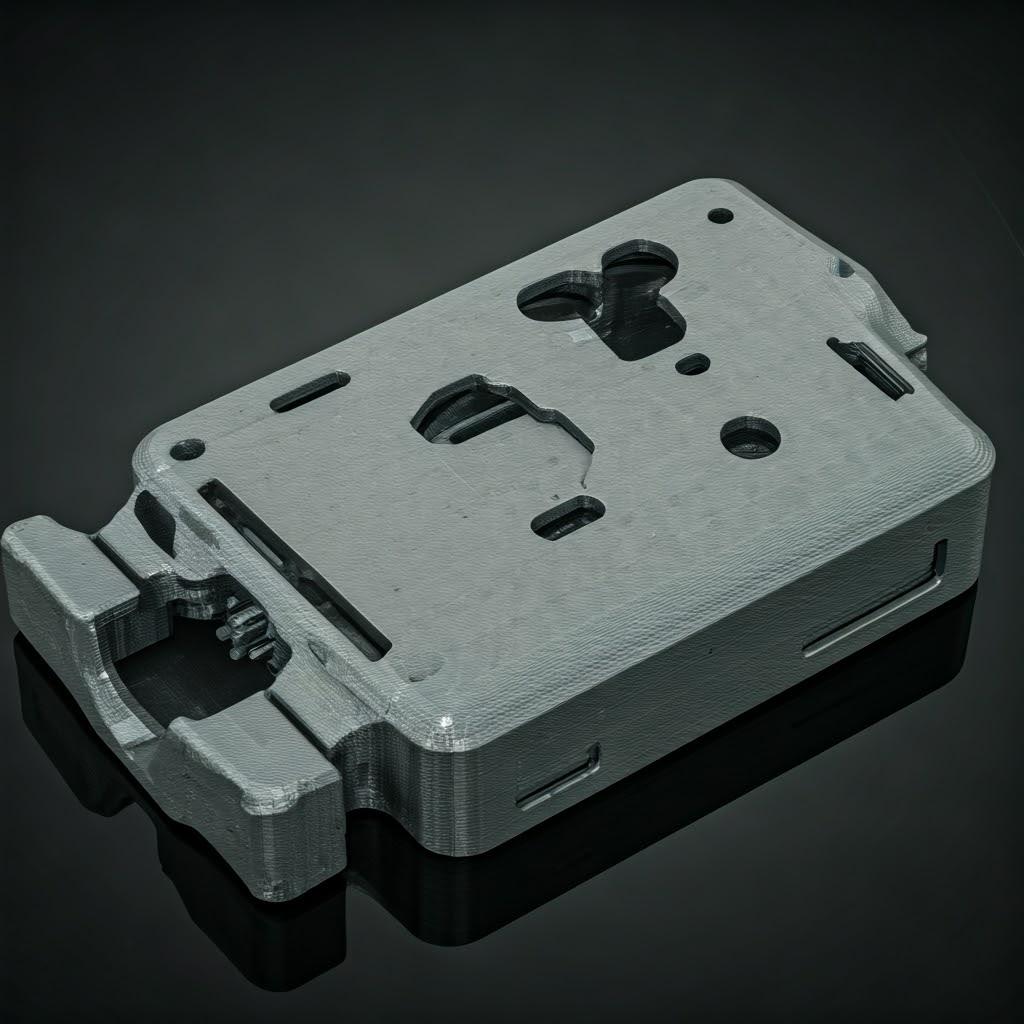
Essential Post-Processing Steps for 3D Printed Drone Battery Enclosures
The journey of a metal 3D printed part doesn’t end when the Laser Powder Bed Fusion (LPBF) machine finishes its build cycle. For drone battery enclosures made from AlSi10Mg or Scalmalloy®, several crucial post-processing steps are typically required to transform the raw printed component into a functional, reliable, and finished product. These steps are essential for relieving internal stresses, removing temporary structures, achieving final dimensional accuracy, improving surface quality, and ensuring the overall integrity of the enclosure. Understanding this workflow is vital for procurement managers factoring in lead times and costs, and for engineers designing parts compatible with these necessary finishing operations.
Common Post-Processing Workflow for LPBF Aluminum Enclosures:
- Powder Removal (Depowdering):
- Cel: To remove the loose, unfused metal powder surrounding the part within the build chamber and from internal channels or cavities.
- Method: Typically involves careful brushing, vacuuming, and compressed air blow-off in a controlled environment (often an inert atmosphere glovebox for reactive powders, though less critical for aluminum). Automated depowdering stations are also used for higher volume production. Thorough removal is critical, especially from internal cooling channels, to ensure functionality and prevent loose powder from interfering with electronics or moving parts later.
- Importance: Recovers valuable unfused powder for recycling; prevents contamination of subsequent processes; ensures clear internal features.
- Stress Relief Heat Treatment:
- Cel: To alleviate the residual internal stresses built up during the rapid heating and cooling cycles of the LPBF process. These stresses can cause warping or distortion after the part is removed from the build plate and can negatively impact mechanical properties.
- Method: The entire build plate with the attached parts is placed in a furnace (often under an inert atmosphere like argon for aluminum to prevent excessive oxidation) and heated to a specific temperature (e.g., around 300°C for AlSi10Mg), held for a set duration (e.g., 1-2 hours), and then slowly cooled. Specific cycles vary based on the alloy and part geometry.
- Importance: Ensures dimensional stability for subsequent steps; prevents delayed distortion; homogenizes the microstructure slightly; critical for maintaining accuracy.
- Part Removal from Build Plate:
- Cel: To separate the printed enclosure(s) from the metal build plate they were fused to during the printing process.
- Method: Commonly done using wire Electrical Discharge Machining (wire EDM) or a bandsaw. Wire EDM offers higher precision and a cleaner cut, minimizing stress on the part, but is slower. Bandsawing is faster but less precise and may require a subsequent facing operation.
- Importance: Frees the individual parts for further processing.
- Usunięcie konstrukcji wsporczej:
- Cel: To remove the temporary support structures that were printed to anchor the part to the build plate and support overhanging features during the build.
- Method: This is often a manual process using pliers, cutters, small grinders, or specialized hand tools. For complex or delicate parts, CNC machining or wire EDM might be used to remove supports more precisely. Care must be taken not to damage the part surface.
- Importance: Reveals the final part geometry; essential for functionality and aesthetics. This step can be labor-intensive, impacting overall cost and lead time.
- CNC Machining (Optional but Common):
- Cel: To achieve tight tolerances, critical flatness, specific surface finishes, or features like threaded holes that are difficult or impossible to print accurately with LPBF alone.
- Method: The 3D printed enclosure is mounted in a CNC milling machine. Critical faces are milled flat, bores are drilled and reamed to precise diameters, threads are tapped, and sealing surfaces are finished.
- Importance: Guarantees precise mating with other drone components; ensures proper sealing (if required); achieves high-quality finishes on specific functional surfaces. Requires careful fixture design to hold the potentially complex AM part.
- Wykończenie powierzchni:
- Cel: To improve the overall surface texture, remove minor imperfections left by supports, enhance aesthetics, and prepare the surface for coatings if needed.
- Method: Several techniques can be used:
- Bead Blasting/Sand Blasting: Propels fine media (glass beads, aluminum oxide) at the surface to create a uniform, matte finish. Effective at blending support witness marks and layer lines.
- Tumbling/Vibratory Finishing: Parts are placed in a tumbler with abrasive media, which smooths edges and surfaces through friction. Good for batch processing but less controlled than blasting or machining.
- Polerowanie: Manual or automated polishing can achieve very smooth, even mirror-like finishes on specific areas, but is labor-intensive.
- Importance: Improves visual appeal; provides a consistent surface texture; can slightly improve fatigue resistance by removing surface notches.
- Anodizing (Optional Coating):
- Cel: To apply a hard, protective, corrosion-resistant oxide layer to the aluminum surface. Can also be used for cosmetic coloring or electrical insulation.
- Method: An electrochemical process where the aluminum part acts as the anode in an electrolyte bath, growing a controlled oxide layer. Different types (Type II, Type III Hardcoat) offer varying thickness and hardness.
- Importance: Significantly enhances durability, wear resistance, and corrosion protection – valuable for drone enclosures exposed to harsh environments.
- Quality Inspection & Validation:
- Cel: To ensure the final enclosure meets all dimensional, material, and functional specifications.
- Method: Includes visual inspection, dimensional checks (calipers, CMM – Coordinate Measuring Machine), surface roughness measurements, potentially CT (Computed Tomography) scanning to check for internal defects (porosity) and verify internal channel clearance, and material property testing if required.
- Importance: Guarantees the part meets the requirements defined by the engineer and procurement agreement; critical for safety and reliability in drone applications.
Each of these steps adds time and cost to the overall production process. Efficient planning, optimized DfAM (to minimize supports), and partnership with a well-equipped AM service provider capable of handling these diverse post-processing operations in-house can significantly streamline the workflow and ensure high-quality, functional drone battery enclosures are delivered reliably.
Navigating Common Challenges in Aluminum AM for Enclosures (and Solutions)
While Laser Powder Bed Fusion of aluminum alloys like AlSi10Mg and Scalmalloy® offers tremendous advantages for producing drone battery enclosures, the process is not without its challenges. Understanding these potential hurdles and the strategies experienced providers use to overcome them is crucial for engineers designing parts and procurement managers selecting suppliers. Forewarned is forearmed, and partnering with a knowledgeable provider like Met3dp, equipped with advanced systems and deep expertise, significantly mitigates these risks.
Common Challenges & Mitigation Strategies:
- Residual Stress, Distortion, and Warping:
- Wyzwanie: The intense, localized heating and rapid cooling inherent in LPBF create significant thermal gradients, leading to internal stresses within the printed part. If not managed, these stresses can cause the part to warp during printing, detach from the build plate, or distort after removal, compromising dimensional accuracy. Aluminum alloys, with their relatively high thermal expansion and conductivity, can be particularly susceptible.
- Solutions:
- Optimized Build Strategy: Careful selection of laser parameters (power, speed, scan strategy) to minimize thermal input and gradients. Utilizing specific scan patterns (e.g., island scanning) can help distribute heat more evenly.
- Robust Support Structures: Well-designed supports anchor the part firmly to the rigid build plate, resisting distortion forces during the build. Support design requires expertise to be effective without being overly difficult to remove.
- Thermal Simulation: Advanced simulation software can predict areas of high stress concentration and potential distortion, allowing for design modifications or optimized orientation before printing.
- Mandatory Stress Relief: Performing a proper stress relief heat treatment cycle immediately after printing and before removing the part from the build plate is non-negotiable for dimensionally critical aluminum parts.
- Appropriate Part Orientation: Orienting the part to minimize large flat surfaces parallel to the build plate and reduce the height can sometimes lessen warping tendencies.
- Support Structure Design and Removal:
- Wyzwanie: Supports are necessary but add complexity. Poorly designed supports can fail during printing, leading to build failure. They also consume extra material and time. Removal can be labor-intensive, time-consuming, and risks damaging the part surface, especially with tough alloys or intricate geometries. Internal supports in channels can be extremely difficult or impossible to remove completely.
- Solutions:
- DfAM for Support Reduction: Designing parts with self-supporting angles (>45°), using internal channels with optimized cross-sections (e.g., diamond, teardrop), and orienting the part strategically can significantly minimize the need for supports.
- Specialized Support Structures: Utilizing support types that are easier to remove (e.g., thin conical contacts, perforated or lattice supports) while still providing necessary anchoring. Software tools often offer advanced support generation options.
- Skilled Technicians: Experienced technicians develop techniques for careful manual removal using appropriate tools.
- Uwagi dotyczące przetwarzania końcowego: Planning for machining or specific surface finishing steps to clean up support witness marks in critical areas.
- Accessibility Planning: Ensuring internal channels requiring supports have access points for removal tools or flushing.
- Achieving Desired Surface Finish:
- Wyzwanie: As-built LPBF surfaces inherently have a degree of roughness due to partially melted powder particles and layer lines. Downward-facing surfaces are particularly rough due to support contact. Achieving a very smooth finish (low Ra) comparable to machining requires additional steps.
- Solutions:
- Optimized Process Parameters: Fine-tuning laser parameters and potentially using smaller layer thicknesses can improve as-built finish, though often at the cost of build speed.
- Contour/Skin Scans: Using specific laser scanning parameters for the outer contours of the part can improve sidewall smoothness.
- Effective Post-Processing: Utilizing appropriate surface finishing techniques like bead blasting (for a uniform matte finish), tumbling (for general smoothing), or CNC machining/polishing (for targeted smoothness on critical surfaces) is essential.
- Orientation Strategy: Prioritize orienting critical surfaces upwards or vertically if possible to achieve the best as-built finish before secondary operations.
- Kontrola porowatości:
- Wyzwanie: Small voids or pores can sometimes form within the printed material due to trapped gas (from powder or shielding gas) or incomplete fusion between layers (Lack-of-Fusion defects). Excessive porosity can compromise mechanical properties (especially fatigue strength) and leak tightness.
- Solutions:
- High-Quality Metal Powder: Using spherical, gas-atomized powders with low internal porosity and controlled particle size distribution, like those produced by Met3dp using their advanced powder making systems, is fundamental. Proper powder handling and storage to prevent moisture absorption are also key.
- Optimized Process Parameters: Developing robust parameter sets (laser power, speed, hatch spacing, focus) specific to the alloy and machine ensures complete melting and fusion. This requires significant process development expertise.
- Inert Atmosphere Control: Maintaining a high-purity inert gas environment (e.g., Argon) in the build chamber prevents oxidation and reduces gas pickup during melting.
- Prasowanie izostatyczne na gorąco (HIP): For critical applications requiring near-zero porosity (common in aerospace), a post-process HIP treatment (high temperature and high pressure) can be used to close internal voids. However, this adds significant cost and lead time.
- Kontrola jakości: Utilizing CT scanning for non-destructive inspection of critical parts to detect and quantify internal porosity.
- Powder Handling and Management:
- Wyzwanie: Metal powders, especially fine ones used in LPBF, require careful handling to ensure operator safety (inhalation risk), prevent contamination (which can affect material properties and print quality), and maintain powder quality (preventing oxidation and moisture). Managing powder traceability and recyclability is also important for cost-effectiveness and quality control.
- Solutions:
- Controlled Environments: Using dedicated powder handling stations, often with integrated sieving and inert atmosphere capabilities.
- Środki ochrony indywidualnej (PPE): Operators must use appropriate respirators, gloves, and safety glasses.
- Zarządzanie cyklem życia proszku: Implementing rigorous procedures for powder receiving, testing, storage, sieving (to remove oversized particles or spatters), blending (recycled with virgin powder), and tracking batch usage.
- Investing in Automation: Automated powder handling systems reduce operator exposure and ensure consistency.
Successfully navigating these challenges requires a combination of robust DfAM practices, advanced printing equipment, high-quality materials, optimized process parameters, diligent post-processing, and rigorous quality control. This underscores the importance of selecting a metal AM partner with proven expertise and a comprehensive understanding of the entire additive manufacturing workflow for demanding applications like drone battery enclosures.
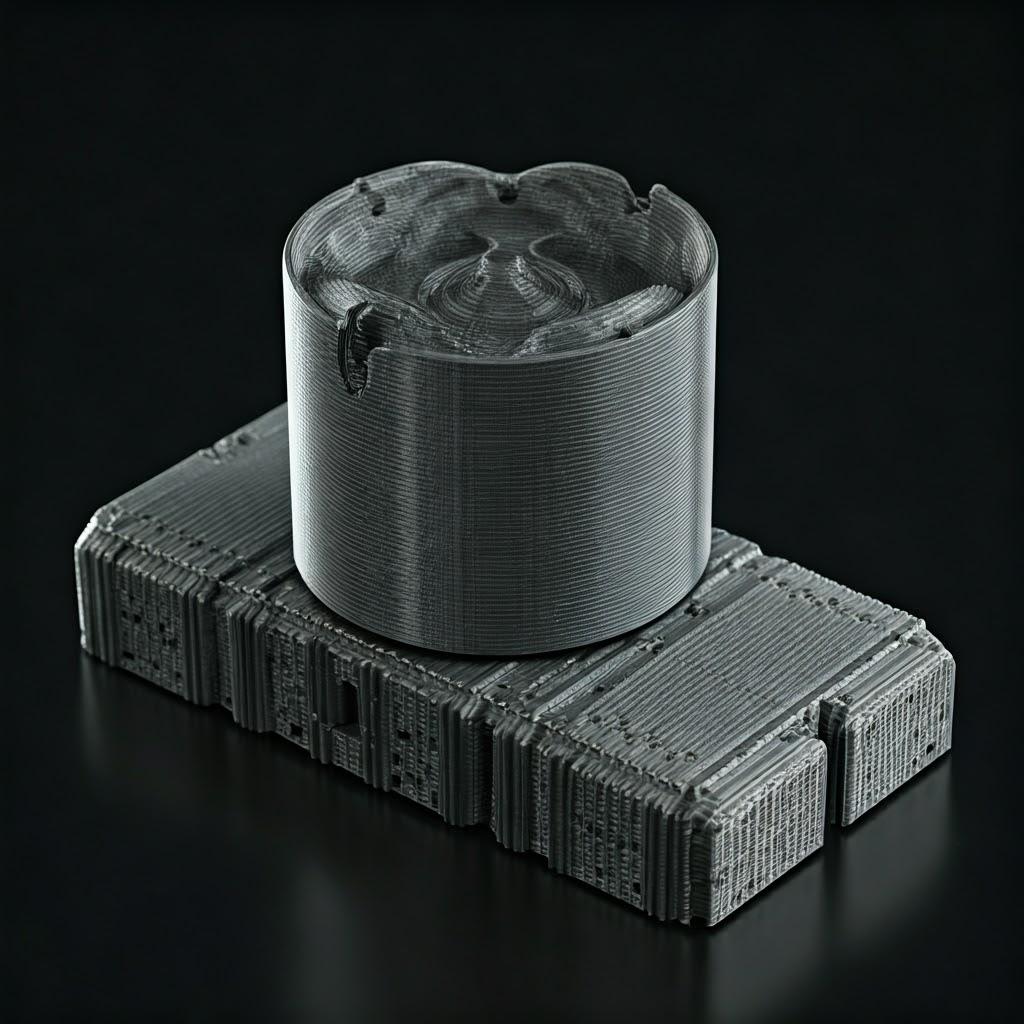
Selecting Your Metal 3D Printing Partner: Criteria for Drone Component Suppliers
Choosing the right additive manufacturing service provider is a critical decision that significantly impacts the quality, reliability, cost, and timely delivery of your 3D printed aluminum drone battery enclosures. The market features a range of suppliers, from small job shops to large, specialized industrial additive manufacturing centers. For procurement managers and engineers sourcing critical drone components, especially those considering wholesale or long-term supply agreements, a thorough vetting process based on objective criteria is essential. Partnering with a provider that aligns with your technical requirements, quality standards, and business goals is key to successfully leveraging AM technology.
Key Criteria for Evaluating Metal AM Service Providers:
- Technical Expertise & Experience:
- Materials Focus: Do they specialize in the required aluminum alloys (AlSi10Mg, Scalmalloy®)? Do they possess deep knowledge of their processing parameters, material properties, and appropriate post-processing? Look for providers like Met3dp, who not only use but also manufacture high-quality metal powders, demonstrating profound materials science expertise across various alloys including aluminum, titanium alloys, superalloys, and more.
- Application Experience: Have they successfully produced similar components, particularly for demanding industries like aerospace, defense, or automotive? Can they showcase case studies or examples relevant to drone applications or complex enclosures?
- Engineering Support: Do they offer Design for Additive Manufacturing (DfAM) support? Can their engineers collaborate with your team to optimize designs for printability, weight reduction, and cost-effectiveness?
- Machine Capabilities & Technology:
- Platform Technology: Do they utilize industrial-grade Laser Powder Bed Fusion (LPBF/SLM) machines known for accuracy and reliability? What is the manufacturer and model of their equipment?
- Objętość kompilacji: Can their machines accommodate the size of your enclosure design? Do they have printers with industry-leading build volumes if larger parts or batch production is required?
- Machine Park: How many machines do they have? A larger machine park generally translates to better capacity, redundancy, and potentially shorter lead times, which is crucial for B2B suppliers needing consistent output.
- Maintenance & Calibration: Do they have rigorous maintenance schedules and calibration procedures to ensure consistent machine performance and part quality?
- Quality Management & Certifications:
- Quality Management System (QMS): Are they certified to relevant quality standards? ISO 9001 is a baseline, but for aerospace and defense applications, AS9100 certification is often required and demonstrates a higher level of process control and traceability.
- Kontrola procesu: What measures do they take to monitor and control the printing process (e.g., melt pool monitoring, inert atmosphere control, laser power checks)?
- Material Traceability: How do they manage powder traceability, handling, storage, and recycling to prevent contamination and ensure consistent material properties?
- Inspection Capabilities: What inspection equipment do they possess in-house (e.g., CMM, optical scanners, CT scanners)? What are their standard quality control procedures for validating part accuracy and integrity?
- Post-Processing Capabilities:
- In-House vs. Outsourced: Can they perform necessary post-processing steps like heat treatment, support removal, CNC machining, bead blasting, and anodizing in-house? In-house capabilities generally lead to better control, shorter lead times, and reduced logistical complexity.
- Ekspertyza: Do they have skilled technicians and the right equipment for each required post-processing step?
- Lead Time & Responsiveness:
- Quoting Turnaround: How quickly do they respond to requests for quotes (RFQs)?
- Stated Lead Times: What are their typical lead times for prototypes and production volumes? Are these realistic and reliable?
- Communication: Are they responsive and communicative throughout the design, production, and delivery process? Good communication is vital for B2B relationships.
- Cost & Value:
- Pricing Structure: Is their pricing transparent and competitive? Understand what is included in the quote (e.g., material, printing, standard post-processing, NDT).
- Volume Pricing: Do they offer discounts for larger batch orders or wholesale agreements?
- Overall Value: Consider the total value proposition, including quality, reliability, support, and speed, not just the lowest price per part. A slightly higher cost from a reputable supplier can prevent expensive failures or delays down the line.
- Company Stability & Reputation:
- Doświadczenie: How long have they been involved in metal additive manufacturing?
- Reputacja: Check for customer testimonials, case studies, and industry reputation. Are they seen as a leader or innovator in the field? Learning about Met3dp reveals decades of collective expertise and a commitment to advancing metal AM.
- Stabilność finansowa: For long-term partnerships or high-volume supply, assess the provider’s stability.
Selecting a partner like Met3dp provides significant advantages. With headquarters in Qingdao, China, they offer a comprehensive solution encompassing industry-leading SEBM (Selective Electron Beam Melting) and LPBF printers known for accuracy and reliability, advanced gas atomization and PREP systems for manufacturing high-performance spherical metal powders (including AlSi10Mg and specialized alloys), and dedicated application development services. Their focus on mission-critical parts for aerospace, medical, and automotive sectors demonstrates their commitment to quality and performance, making them a strong candidate for supplying high-quality 3D printed aluminum drone battery enclosures.
Understanding Cost Drivers and Lead Times for 3D Printed Enclosures
When budgeting for and planning the production of 3D printed aluminum drone battery enclosures, it’s crucial for engineers and procurement managers to understand the factors that influence both the final cost per part and the overall lead time. Metal additive manufacturing involves sophisticated machinery, specialized materials, and multi-step processes, all of which contribute to the final calculation. While AM offers significant advantages in design freedom and speed for certain applications, it’s important to have realistic expectations.
Primary Cost Drivers:
- Material Consumption:
- Part Volume: The actual volume of the final enclosure directly impacts the amount of expensive AlSi10Mg or Scalmalloy® powder consumed. Larger or thicker-walled parts cost more.
- Support Structure Volume: The volume of material used for support structures also adds to the cost. Designs optimized via DfAM to minimize supports are more cost-effective.
- Koszt proszku: Scalmalloy® is generally significantly more expensive per kilogram than AlSi10Mg due to its composition (scandium) and specialized production. The choice of alloy is a major cost factor.
- Machine Time (Build Time):
- Part Height (Z-Height): LPBF builds layer by layer, so the taller the part in its build orientation, the longer the machine runs.
- Part Volume & Density: Larger volumes and denser parts (less internal lattice or optimization) require more laser scanning per layer, increasing build time.
- Number of Parts per Build: Maximizing the number of enclosures printed simultaneously on a single build plate (“nesting”) distributes the machine setup and run time over more parts, reducing the cost per part. This is a key factor for achieving economies of scale in B2B volume orders.
- Machine Hourly Rate: Industrial LPBF machines represent a significant capital investment, and their operating costs (power, gas, maintenance) contribute to an hourly rate charged by the service provider.
- Labor & Engineering:
- File Preparation: Setting up the build file, generating supports, and slicing the model requires engineering time.
- Machine Setup & Teardown: Preparing the machine, loading powder, unloading the build, and initial cleaning requires technician labor.
- Post-Processing Labor: Manual tasks like powder removal, support removal, surface finishing (blasting, polishing), and inspection can be labor-intensive and significantly impact cost, especially for complex parts or high cosmetic requirements. CNC machining setup and runtime also add labor costs.
- DfAM Support: If extensive design consultation or optimization services are utilized, this engineering time will be factored in.
- Post-Processing Complexity:
- Obróbka cieplna: Stress relief is standard, but additional heat treatments (like T6 for AlSi10Mg) add furnace time and cost.
- Support Removal Difficulty: Intricate internal supports or supports on delicate features require more careful, time-consuming removal.
- Machining Requirements: The extent of CNC machining needed for tight tolerances or specific features directly impacts cost (machine time, tooling, programming).
- Wymagania dotyczące wykończenia powierzchni: Achieving very smooth finishes (e.g., polishing) or applying coatings (e.g., anodizing) adds process steps and associated costs.
- Quality Assurance & Inspection:
- Standard QC: Basic dimensional checks and visual inspection are typically included.
- Advanced Inspection: Requiring CMM reports, CT scanning for internal porosity checks, or other non-destructive testing (NDT) adds significant cost but may be necessary for critical applications.
- Wolumen zamówienia:
- Prototypes vs. Production: One-off prototypes are generally more expensive per part than production runs due to setup costs being amortized over a single unit.
- Wielkość partii: As mentioned, printing larger batches simultaneously reduces the per-part cost by optimizing machine utilization. Wholesale buyers and distributors benefit most from higher volume orders.
Typical Lead Time Components:
Lead time refers to the total time from order placement to parts delivery. It’s influenced by several factors:
- Quoting & Order Confirmation: (1-3 days) Initial communication, file analysis, quote generation, and order placement.
- Queue Time: (Variable: 1 day to 2+ weeks) How long before your job can be scheduled onto an available machine. This depends heavily on the service provider’s current workload and machine capacity. High-demand periods or specialized material requests can increase queue times.
- Printing (Build Time): (Hours to several days) Depends on the factors listed under Machine Time cost drivers (part height, volume, nesting). A typical build with multiple enclosures might run for 24-72 hours or more.
- Cooldown & Depowdering: (Several hours to 1 day) Allowing the build chamber to cool sufficiently before safe powder removal.
- Heat Treatment (Stress Relief): (1 day) Includes furnace ramp-up, soak time, and controlled cooling.
- Part Removal & Support Removal: (Hours to days) Depends on part complexity, support density, and removal method (manual vs. EDM/sawing).
- Post-Processing (Machining, Finishing): (Variable: 1 day to 1+ week) Depends entirely on the complexity and number of steps required (e.g., CNC programming/setup/run time, blasting, anodizing lead times).
- Kontrola jakości: (Hours to days) Depends on the level of inspection required (visual, CMM, CT scan).
- Wysyłka: (Variable) Depends on the shipping method chosen and destination.
Estimated Total Lead Times (General Guide):
- Simple Prototypes (Minimal Post-Processing): 5 – 10 working days
- Complex Prototypes/Parts with Machining/Finishing: 2 – 4 tygodnie
- Low-Volume Production Runs: 3 – 6 weeks (depending on batch size and complexity)
It’s crucial to discuss specific lead time requirements with your chosen AM provider early in the process. Factors like material availability, current machine loading, and the complexity of post-processing can all impact the final delivery date. Transparent communication with partners like Met3dp helps set realistic expectations for project timelines.
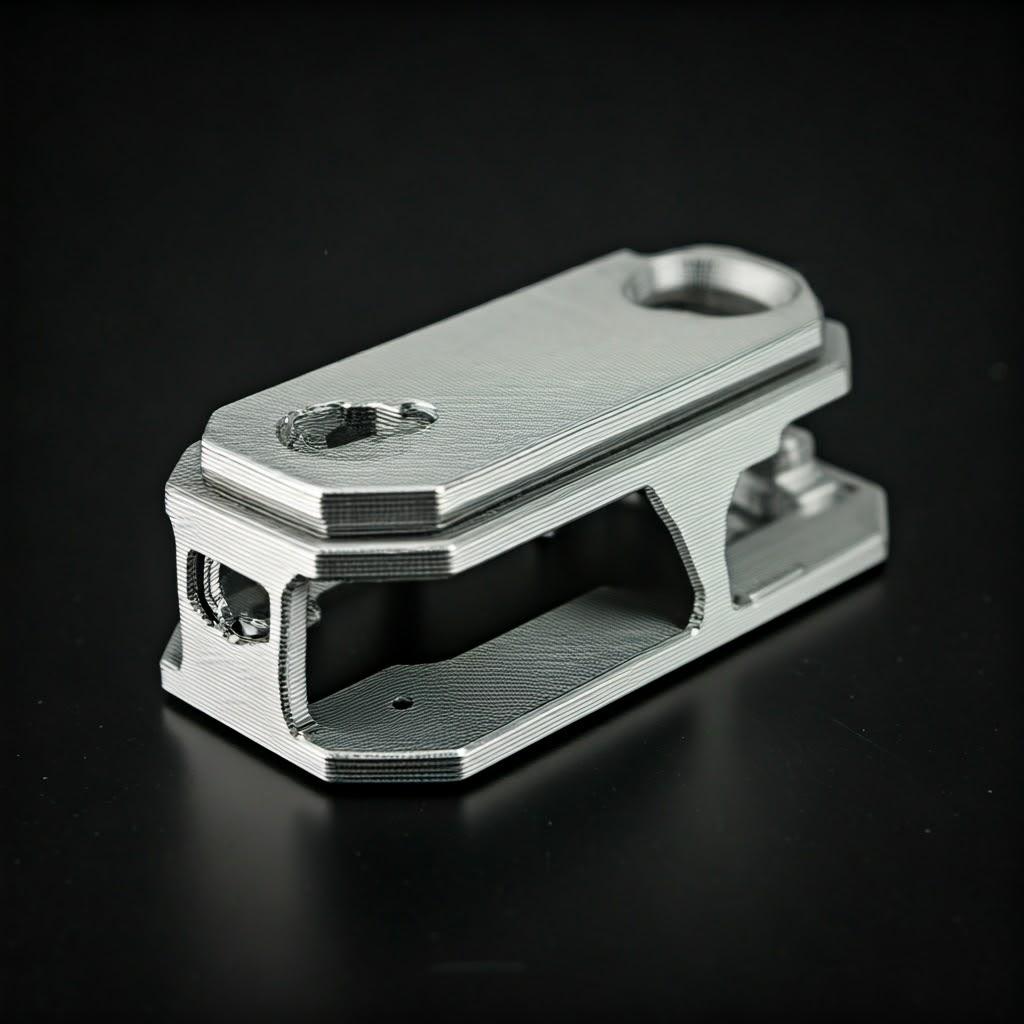
Frequently Asked Questions (FAQ) about 3D Printed Aluminum Drone Battery Enclosures
Here are answers to some common questions engineers and procurement managers have when considering 3D printed aluminum for drone battery enclosures:
1. How does the weight of 3D printed aluminum enclosures (AlSi10Mg/Scalmalloy®) compare to plastic or machined aluminum?
- vs. Plastic (e.g., ABS, Polycarbonate): 3D printed aluminum enclosures will typically be heavier than identically shaped plastic ones, as aluminum’s density (~2.7 g/cm³) is higher than most engineering plastics (1.1-1.4 g/cm³). However, the key advantage of metal AM lies in Projektowanie dla produkcji addytywnej (DfAM). By using topology optimization and lattice structures, engineers can often design aluminum enclosures that meet or exceed the strength and stiffness requirements with significantly less material volume than a comparable plastic design would need. Furthermore, high-strength alloys like Scalmalloy® allow for much thinner walls. The result can be an aluminum enclosure that is competitively lightweight, potentially even lighter than a bulky plastic design built to achieve the same level of durability and impact resistance, while offering superior thermal conductivity and structural integrity.
- vs. Machined Aluminum: When comparing a design optimized for AM (using AlSi10Mg or Scalmalloy®) to the same functional enclosure designed for traditional CNC machining from a block of standard aluminum (e.g., 6061), the 3D printed version can often be made significantly lighter (15-50% or more). This is because AM allows material to be placed only where structurally needed, enabling complex geometries, thin walls, and internal voids/lattices that are impossible or impractical to machine. While the base material density is similar, AM’s design freedom enables far greater weight optimization potential.
2. What is the typical environmental resistance (temperature, moisture, dust) of these enclosures?
- Temperatura: Both AlSi10Mg and Scalmalloy® perform well within the typical operating temperature ranges of drone batteries. AlSi10Mg is generally suitable for continuous service up to around 150°C, while Scalmalloy® retains good properties up to around 200°C. Their excellent thermal conductivity helps dissipate heat generated by the battery. They easily withstand ambient temperatures encountered during drone operation, from cold climates to hot desert environments.
- Moisture & Dust: As solid metal parts, 3D printed aluminum enclosures offer excellent inherent protection against dust and moisture ingress if designed correctly. Achieving a specific Ingress Protection (IP) rating (e.g., IP67 for dust-tight and water immersion resistance) depends on the enclosure design, particularly the sealing mechanisms used for lids, cable glands, and connector interfaces. While the aluminum itself is resistant, achieving a high IP rating requires careful design of mating surfaces (often requiring post-machining for flatness), appropriate gasket selection, and precise assembly. Anodizing can further enhance corrosion resistance against moisture, salt spray, or chemical exposure.
3. Can specific coatings or finishes be applied for enhanced protection or electrical insulation?
Yes, various coatings and finishes can be applied to 3D printed aluminum enclosures to enhance specific properties:
- Anodizing (Type II & Type III Hardcoat): As mentioned, this is a common treatment for aluminum. Type II provides good corrosion resistance and can be dyed various colors for cosmetic purposes. Type III (Hardcoat) creates a much thicker, harder layer (~25-50 µm or more) offering excellent wear resistance, improved corrosion protection, and some dielectric properties (though not a primary insulator).
- Chromate Conversion Coating (Alodine/Chem Film): Provides excellent corrosion resistance and acts as a good primer for paint. Offers some electrical conductivity, which may be needed for grounding/EMI shielding.
- Paint/Powder Coating: Primarily for cosmetic purposes or specific chemical resistance. Requires proper surface preparation (e.g., blasting, conversion coating).
- Electroless Nickel Plating: Provides excellent wear resistance, corrosion protection, and solderability. Can offer good electrical conductivity.
- Specialized Dielectric Coatings: If significant electrical insulation is required (beyond the natural oxide layer or standard anodizing), specialized polymer-based or ceramic-based coatings can be applied via spraying or dipping processes, though compatibility with the complex shapes of AM parts needs consideration.
It’s important to discuss coating requirements with your AM service provider, as surface preparation is key, and some coatings may affect final part tolerances.
Conclusion: Elevate Your Drone Designs with Met3dp’s Aluminum Additive Manufacturing Expertise
The demanding requirements of the drone industry – longer flight times, higher payload capacities, increased durability, and rapid innovation cycles – necessitate advanced manufacturing solutions. For critical components like battery enclosures, metal additive manufacturing using high-performance aluminum alloys like AlSi10Mg and Scalmalloy® offers a transformative approach. As we’ve explored, 3D printing unlocks unparalleled design freedom, enabling engineers to create highly optimized, lightweight, and complex enclosures with integrated thermal management and structural features unattainable through traditional methods.
Leveraging topology optimization, lattice structures, and part consolidation through DfAM principles allows for significant weight reduction without compromising strength or protection. The choice between the versatile AlSi10Mg and the high-strength Scalmalloy® enables tailoring the enclosure to specific performance needs and budgets. While considerations around tolerances, surface finish, post-processing, and potential challenges exist, partnering with an experienced and well-equipped AM provider mitigates these hurdles.
Selecting the right manufacturing partner is paramount. Criteria such as technical expertise, advanced machine capabilities, robust quality management systems (like AS9100), comprehensive post-processing options, and reliable lead times are crucial for ensuring success, particularly for B2B clients requiring consistent quality and supply.
Met3dp stands out as a leader uniquely positioned to meet these demands. With integrated capabilities spanning the development and production of high-quality, spherical metal powders via advanced atomization techniques, the manufacturing of industry-leading metal 3D printers (SEBM and LPBF), and comprehensive application development and printing services, Met3dp offers a complete ecosystem for industrial additive manufacturing. Our decades of collective expertise, particularly in mission-critical components for aerospace, medical, and automotive industries, ensure that we understand the precision and reliability required for drone applications. We invite you to explore how Met3dp’s cutting-edge systems, advanced proszki metali, and application expertise can empower your organization’s additive manufacturing goals and help you create next-generation drone battery enclosures that truly take flight.
Udostępnij
MET3DP Technology Co., LTD jest wiodącym dostawcą rozwiązań w zakresie produkcji addytywnej z siedzibą w Qingdao w Chinach. Nasza firma specjalizuje się w sprzęcie do druku 3D i wysokowydajnych proszkach metali do zastosowań przemysłowych.
Zapytaj o najlepszą cenę i spersonalizowane rozwiązanie dla Twojej firmy!
Powiązane artykuły
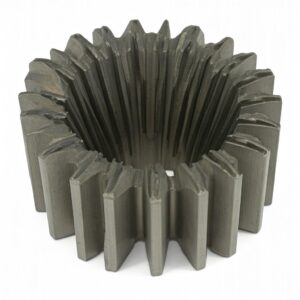
Wysokowydajne segmenty łopatek dysz: Rewolucja w wydajności turbin dzięki drukowi 3D w metalu
Czytaj więcej "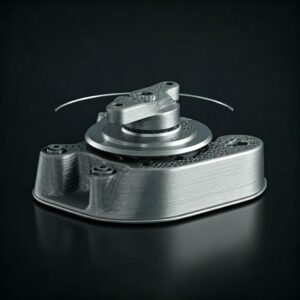
Drukowane w 3D mocowania dla samochodowych czujników radarowych: Precyzja i wydajność
Czytaj więcej "Informacje o Met3DP
Ostatnia aktualizacja
Nasz produkt
KONTAKT
Masz pytania? Wyślij nam wiadomość teraz! Po otrzymaniu wiadomości obsłużymy Twoją prośbę całym zespołem.
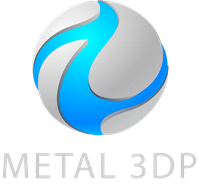
Proszki metali do druku 3D i produkcji addytywnej