3D Printed End Effectors for Robotics
Spis treści
Wprowadzenie
In the rapidly evolving landscape of industrial automation, robotic systems are becoming increasingly sophisticated and adaptable. At the forefront of this evolution lies the crucial role of robotic end effectors – the “hands” of these automated systems that directly interact with workpieces and perform specific tasks. Traditionally manufactured end effectors often face limitations in terms of customization, complexity, and weight, hindering the overall efficiency and versatility of robotic operations. However, the advent of metal 3D printing, also known as metal additive manufacturing, is revolutionizing the creation of these critical components. By offering unprecedented design freedom and material flexibility, metal 3D printing enables the production of highly optimized, lightweight, and application-specific robotic end effectors tailored to the unique demands of industries spanning aerospace, automotive, medical, and beyond. This blog post delves into the transformative impact of metal Drukowanie 3D in this domain, exploring the diverse applications, key advantages, material considerations, and best practices for leveraging this cutting-edge technology to enhance robotic capabilities. At Metal3DP, we are committed to providing industry-leading additive manufacturing solutions, empowering businesses to unlock the full potential of metal 3D printing for their robotic automation needs. Our expertise in high-performance metal powders and advanced printing technologies ensures the delivery of robust and precise end effectors for even the most demanding applications. Learn more about our comprehensive metal 3D printing services.
What are 3D Printed End Effectors Used For?
Metal 3D printed end effectors are finding increasingly diverse and critical applications across a wide spectrum of industries. Their ability to be customized for specific tasks and geometries makes them invaluable for optimizing robotic workflows. Here are some key areas where these additively manufactured components are making a significant impact:
- Aerospace: In the aerospace sector, lightweight yet strong end effectors are crucial for tasks such as:
- Part Handling: Safely and precisely gripping delicate or complex-shaped aerospace components during assembly and inspection.
- Automated Drilling and Fastening: Creating custom tools with integrated features for automated drilling, riveting, and bolting operations on aircraft structures.
- Obróbka powierzchni: Designing specialized grippers or applicators for automated painting, coating, and surface finishing processes.
- Motoryzacja: The automotive industry benefits from the flexibility of 3D printed end effectors in:
- Assembly Line Operations: Developing custom grippers for handling car body panels, engine components, and interior parts with high precision and speed.
- Welding and Bonding: Creating specialized tools with integrated cooling channels or sensors for automated welding, adhesive bonding, and sealing tasks.
- Kontrola jakości: Manufacturing custom probes and fixtures for automated dimensional inspection and quality checks of automotive parts.
- Medyczne: The medical field utilizes 3D printed end effectors for highly specialized applications, including:
- Surgical Robotics: Producing intricate instruments with complex geometries for minimally invasive surgical procedures, offering enhanced dexterity and precision.
- Prosthetics and Orthotics Manufacturing: Creating custom grippers and manipulators for robotic prosthetic arms, tailored to the individual user’s needs and anatomy.
- Laboratory Automation: Designing specialized tools for handling delicate samples, dispensing liquids, and automating laboratory testing processes.
- Produkcja przemysłowa: Across various industrial sectors, metal 3D printed end effectors are employed for:
- Obsługa materiałów: Developing custom grippers for handling a wide range of materials, from raw stock to finished goods, optimizing material flow and reducing damage.
- Machine Tending: Creating specialized tools for loading and unloading parts from CNC machines, injection molding presses, and other manufacturing equipment.
- Inspection and Measurement: Manufacturing custom probes, gauges, and fixtures for automated quality control and dimensional verification.
The ability to rapidly prototype and produce these application-specific end effectors using metal 3D printing significantly reduces lead times and tooling costs compared to traditional manufacturing methods, empowering businesses to optimize their robotic automation processes efficiently.
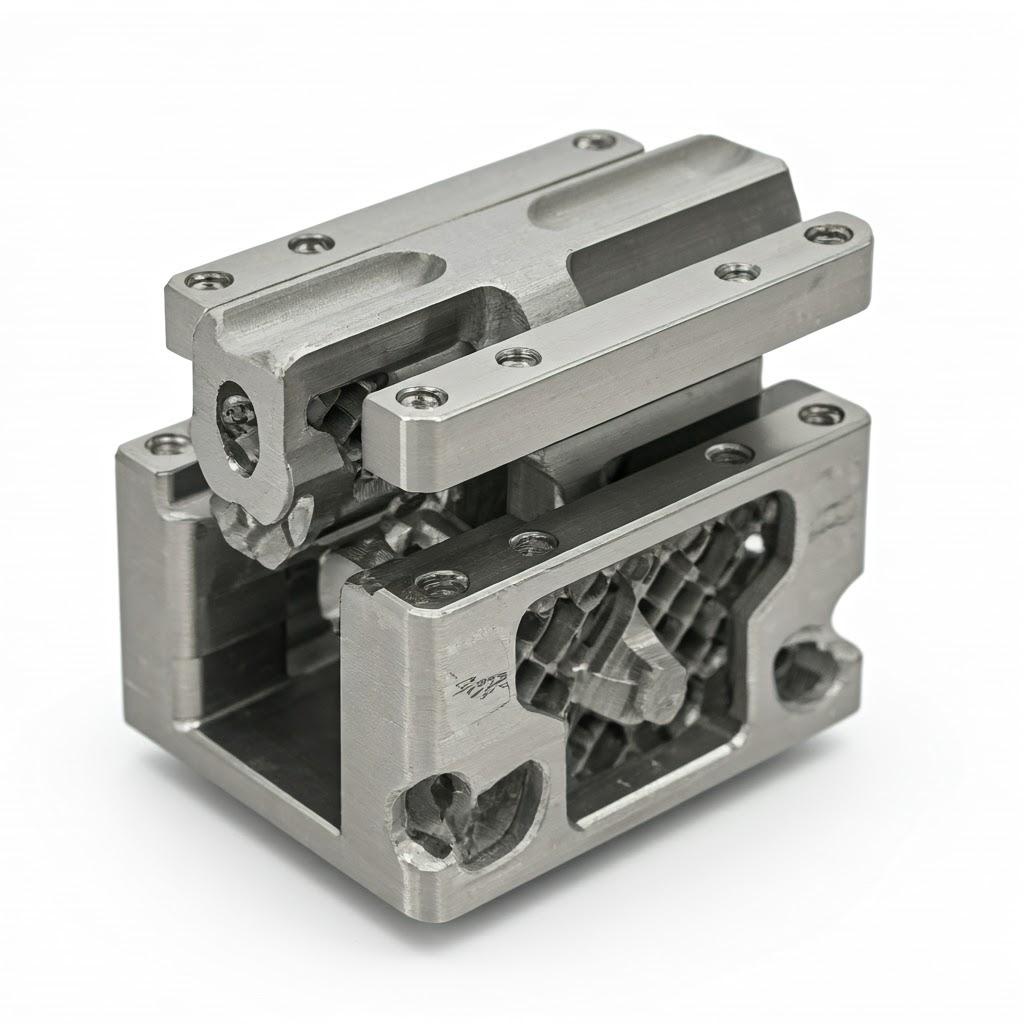
Why Use Metal 3D Printing for Robotic End Effectors?
Opting for metal 3D printing for the production of robotic end effectors offers a multitude of compelling advantages over conventional manufacturing techniques. These benefits directly address the evolving needs of industries seeking enhanced efficiency, flexibility, and performance in their robotic automation systems:
- Swoboda projektowania i złożoność: Metal 3D printing allows for the creation of intricate geometries and internal features that are often impossible or cost-prohibitive to achieve with traditional methods like machining or casting. This design freedom enables the optimization of end effectors for specific tasks, including:
- Lekkość: Creating complex lattice structures and hollow features to reduce the weight of the end effector, leading to lower inertia, faster cycle times, and reduced energy consumption for the robot arm.
- Integracja funkcjonalna: Incorporating multiple functionalities into a single part, such as integrated cooling channels, sensors, or vacuum pathways, simplifying assembly and improving performance.
- Personalizacja: Tailoring the end effector’s shape and features precisely to the workpiece geometry and the specific task requirements, ensuring optimal grip and handling.
- Rapid Prototyping and Reduced Lead Times: Additive manufacturing significantly accelerates the prototyping process. Design iterations can be quickly realized and tested, allowing for faster optimization and time-to-market. Furthermore, the elimination of tooling requirements associated with traditional methods drastically reduces lead times for production, especially for low to medium volumes and highly customized parts.
- Wydajność materiałowa: Metal 3D printing utilizes a layer-by-layer deposition process, allowing for near-net-shape manufacturing. This minimizes material waste compared to subtractive methods like machining, where a significant portion of the raw material is removed. This efficiency can lead to substantial cost savings, especially when working with expensive specialty alloys.
- On-Demand Manufacturing and Flexibility: Metal 3D printing enables the production of end effectors on demand, eliminating the need for large inventories of different tools. This agility is particularly beneficial for industries with fluctuating production needs or those requiring a wide variety of specialized end effectors for different tasks.
- Enhanced Performance and Durability: By selecting the appropriate metal powder and optimizing the design for additive manufacturing, end effectors can be produced with superior mechanical properties, including high strength-to-weight ratios, excellent wear resistance, and improved fatigue life. Materials like 17-4PH stainless steel, offered by Metal3DP, provide a compelling combination of strength, hardness, and corrosion resistance, ideal for demanding robotic applications.
Przy Metal3DP, our advanced metal 3D printing technologies and comprehensive material portfolio empower businesses to leverage these advantages and create high-performance robotic end effectors tailored to their specific needs. Explore our range of high-quality metal powders.
Recommended Materials and Why They Matter
The selection of the appropriate metal powder is paramount to achieving the desired performance characteristics for 3D printed robotic end effectors. Metal3DP offers a range of high-quality metal powders optimized for additive manufacturing, and for robotic end effector applications, two materials stand out: 17-4PH stainless steel and AlSi10Mg aluminum alloy.
1. 17-4PH Stainless Steel:
- Właściwości: 17-4PH is a chromium-nickel-copper precipitation-hardening stainless steel known for its high strength, hardness, and excellent corrosion resistance. It exhibits good fatigue properties and can be heat-treated to achieve various strength levels.
- Why it Matters for Robotic End Effectors:
- Wysoka wytrzymałość i twardość: Enables the creation of robust and durable end effectors capable of withstanding significant loads and wear in demanding industrial environments. This is crucial for gripping, lifting, and manipulating heavy or abrasive workpieces.
- Doskonała odporność na korozję: Ensures the longevity and reliability of the end effector, even in harsh operating conditions where exposure to moisture, chemicals, or other corrosive agents is likely. This is particularly important in industries like chemical processing, food and beverage, and marine applications.
- Good Fatigue Properties: Allows the end effector to withstand repetitive loading and unloading cycles without premature failure, ensuring consistent performance over extended periods. This is critical for high-cycle robotic tasks in automated production lines.
- Versatility in Heat Treatment: The ability to tailor the mechanical properties through various heat treatment processes allows engineers to optimize the material for specific application requirements, balancing strength, ductility, and toughness.
- Zastosowania: Ideal for end effectors requiring high strength and wear resistance, such as grippers for heavy parts, tooling for machining operations, and components operating in corrosive environments.
2. AlSi10Mg Aluminum Alloy:
- Właściwości: AlSi10Mg is a widely used aluminum alloy in additive manufacturing, known for its good strength-to-weight ratio, excellent thermal conductivity, and good corrosion resistance. It exhibits good castability and weldability.
- Why it Matters for Robotic End Effectors:
- Lekkość: The low density of aluminum allows for the creation of significantly lighter end effectors compared to steel alternatives. This reduces the overall weight of the robotic arm, leading to lower inertia, faster acceleration and deceleration, and reduced energy consumption. This is particularly beneficial for high-speed robotic applications and robots with limited payload capacity.
- Dobry stosunek wytrzymałości do wagi: Despite its low density, AlSi10Mg offers sufficient strength for many robotic applications, providing a good balance between weight reduction and structural integrity.
- Doskonała przewodność cieplna: Can be advantageous for end effectors that require heat dissipation, such as those used in welding or high-temperature environments.
- Dobra odporność na korozję: Provides adequate protection against corrosion in many industrial settings.
- Zastosowania: Well-suited for end effectors where weight is a critical factor, such as high-speed pick-and-place grippers, end-of-arm tooling for collaborative robots, and applications in the aerospace and automotive industries where weight reduction is paramount.
Metal3DP offers these high-quality metal powders, processed using advanced techniques to ensure optimal flowability and consistency for superior 3D printing results. Our expertise in material science and additive manufacturing allows us to guide our customers in selecting the ideal powder for their specific robotic end effector application. Contact us to discuss your material requirements. Sources and related content
Design Considerations for Additive Manufacturing
Designing robotic end effectors for metal 3D printing requires a different mindset compared to traditional manufacturing. To fully leverage the capabilities of additive manufacturing, engineers need to consider several key design principles:
- Optymalizacja topologii: This computational method allows for the creation of lightweight structures by strategically removing material from low-stress areas while maintaining structural integrity. For robotic end effectors, topology optimization can lead to significant weight reduction, enabling faster movements and lower energy consumption. Consider incorporating organic, free-form shapes that are characteristic of optimized designs.
- Struktury kratowe: Implementing lattice or mesh-like internal structures can further reduce the weight of the end effector without compromising its strength. These structures offer a high strength-to-weight ratio and can be tailored to specific load-bearing requirements. Different lattice patterns, such as gyroid or cubic, offer varying mechanical properties.
- Integracja funkcjonalna: Metal 3D printing allows for the integration of multiple functionalities into a single part. For end effectors, this could include:
- Integrated Cooling Channels: For applications involving heat generation, such as welding or high-speed machining, internal cooling channels can be designed to dissipate heat effectively.
- Sensor Integration: Embedding channels or housings for sensors (e.g., force sensors, proximity sensors) within the end effector design allows for real-time feedback and improved control.
- Vacuum Pathways: For vacuum-based gripping systems, complex internal channels for vacuum distribution can be directly incorporated into the design, eliminating the need for external tubing.
- Konsolidacja części: Assemblies consisting of multiple components manufactured separately can often be consolidated into a single 3D printed part. This reduces assembly time, minimizes the number of fasteners, and can improve the overall strength and reliability of the end effector.
- Orientation and Support Structures: The orientation of the part during the 3D printing process significantly impacts surface finish, support structure requirements, and build time. Careful consideration of the build orientation and the design of necessary support structures is crucial to minimize post-processing effort and ensure dimensional accuracy. Design features that minimize the need for extensive support, such as self-supporting angles, should be prioritized.
- Grubość ścianek i rozmiar elementów: Metal 3D printing processes have limitations regarding minimum wall thickness and feature size. Designers must adhere to the guidelines provided by the chosen printing technology and material to ensure manufacturability and structural integrity. Collaborating with experienced metal 3D printing service providers like Metal3DP early in the design process can help avoid potential issues. Our team can provide valuable insights into design for additive manufacturing (DfAM) principles.
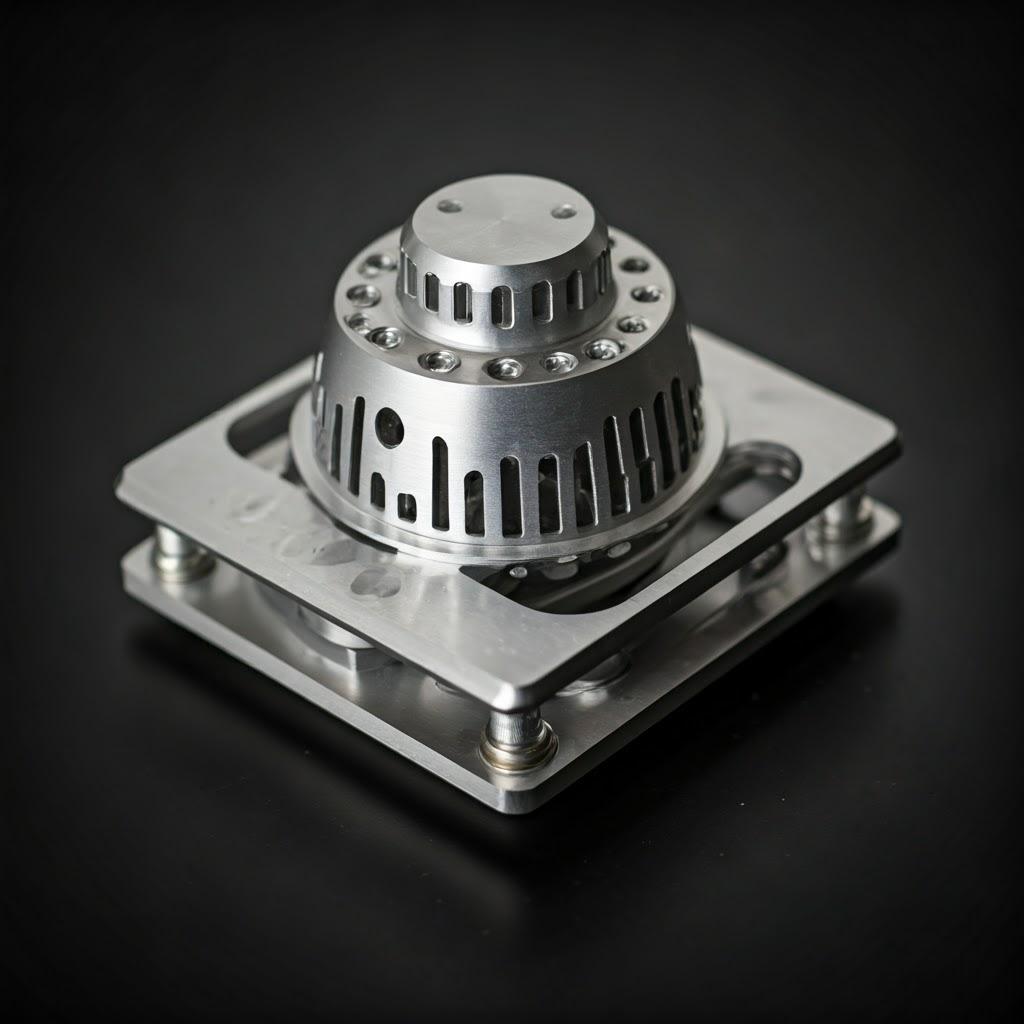
Tolerance, Surface Finish, and Dimensional Accuracy
Achieving the required tolerance, surface finish, and dimensional accuracy is critical for the functional performance of 3D printed robotic end effectors. These aspects are influenced by several factors, including the chosen metal 3D printing technology, the material used, and the post-processing techniques employed.
- Tolerance: Metal 3D printing technologies like Direct Metal Laser Sintering (DMLS) and Selective Laser Melting (SLM) can achieve relatively tight tolerances, typically in the range of ±0.1 to ±0.2 mm for smaller parts. However, larger parts may exhibit greater deviations. Factors affecting tolerance include:
- Machine Accuracy: The inherent accuracy and calibration of the 3D printer.
- Material Shrinkage: Metals undergo thermal expansion and contraction during the printing and cooling process, which can affect final dimensions.
- Orientacja budynku: The orientation of the part on the build platform can influence dimensional accuracy in different axes.
- Wykończenie powierzchni: The as-printed surface finish of metal 3D printed parts is generally rougher compared to machined surfaces, typically ranging from Ra 5-20 µm depending on the technology and material. Factors influencing surface finish include:
- Powder Particle Size: Finer powder particles generally result in smoother surfaces.
- Grubość warstwy: Thinner layers can produce smoother surfaces but increase build time.
- Orientacja budynku: Downward-facing surfaces tend to be rougher due to support structure contact.
- Dokładność wymiarowa: Dimensional accuracy refers to the degree to which the printed part matches the intended design dimensions. While metal 3D printing offers good accuracy, deviations can occur due to the factors mentioned above.
To achieve tighter tolerances and smoother surface finishes for critical features of robotic end effectors, post-processing steps are often necessary. These can include:
- Obróbka CNC: For achieving very tight tolerances and smooth surface finishes on specific functional surfaces, CNC machining can be employed as a secondary operation.
- Grinding and Polishing: These abrasive processes can improve surface finish and dimensional accuracy on external surfaces.
- Powłoka powierzchniowa: Applying coatings can not only improve surface finish but also enhance wear resistance, corrosion resistance, or other functional properties.
Metal3DP understands the importance of achieving the required precision for robotic end effectors. We employ advanced 3D printing equipment and offer a range of post-processing services to meet stringent tolerance and surface finish requirements. Our quality control processes ensure that the final parts meet the specified dimensional accuracy.
Wymagania dotyczące przetwarzania końcowego
While metal 3D printing offers significant advantages in creating complex geometries, post-processing is often a necessary step to achieve the desired functional properties, surface finish, and dimensional accuracy of robotic end effectors. Common post-processing requirements include:
- Usunięcie konstrukcji wsporczej: Metal 3D printing typically requires support structures to prevent warping, sagging, and collapse of overhanging features during the build process. These supports need to be carefully removed after printing. The method of removal can vary depending on the material and support type, ranging from manual removal to machining or chemical dissolution. Designing parts with self-supporting geometries can minimize the need for extensive support structures.
- Obróbka cieplna: To achieve the desired mechanical properties, such as hardness, strength, and ductility, metal 3D printed parts often undergo heat treatment processes. The specific heat treatment cycle depends on the material and the intended application. For example, 17-4PH stainless steel requires specific precipitation hardening treatments to reach its optimal strength.
- Surface Cleaning: After printing and support removal, the surface of the part may have residual powder particles. Various cleaning methods, such as blasting, ultrasonic cleaning, or washing, are used to remove these residues and prepare the surface for further processing or use.
- Ulga w stresie: Internal stresses can build up in metal 3D printed parts during the rapid heating and cooling cycles of the printing process. Stress relief annealing can be performed to reduce these stresses and prevent potential distortion or cracking.
- Wykończenie powierzchni: As mentioned earlier, the as-printed surface finish may not be suitable for all applications. Various surface finishing techniques can be employed to improve smoothness, aesthetics, and functional properties, including:
- Media Blasting: Using abrasive media to create a uniform matte finish.
- Grinding and Polishing: Achieving smoother surfaces with progressively finer abrasives.
- Chemical Etching: Selectively removing surface material to achieve a desired texture or finish.
- Powłoki: Applying protective or functional coatings, such as anti-corrosion coatings, wear-resistant coatings, or aesthetic finishes.
- Obróbka CNC: For critical features requiring very tight tolerances or specific surface finishes, CNC machining can be used as a secondary process to achieve the desired precision.
Metal3DP offers comprehensive post-processing services to ensure that our 3D printed metal parts meet the specific requirements of your robotic end effector applications. Our expertise in heat treatment, surface finishing, and precision machining allows us to deliver functional and high-quality components.
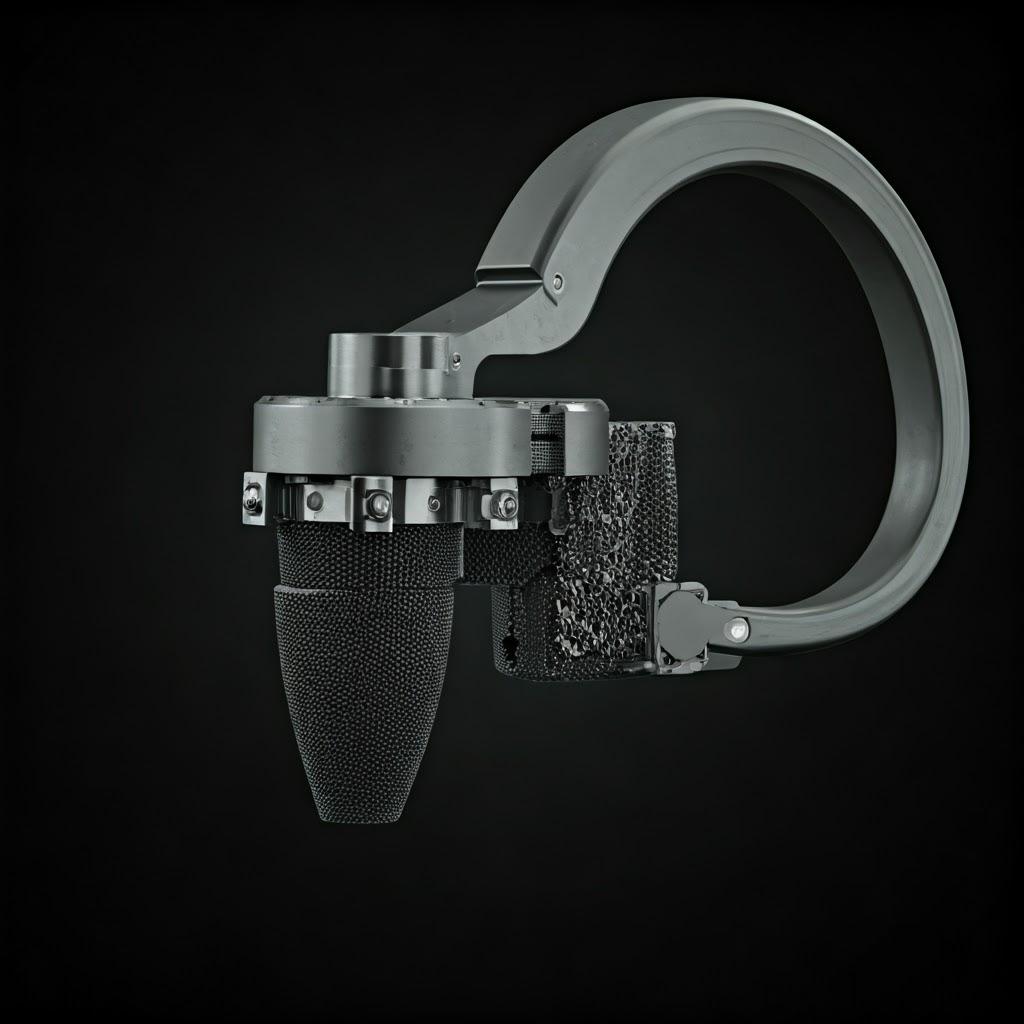
Common Challenges and How to Avoid Them
While metal 3D printing offers numerous advantages, certain challenges can arise during the process. Understanding these potential issues and implementing appropriate strategies can help avoid them and ensure successful outcomes for robotic end effector production:
- Wypaczenia i zniekształcenia: Thermal stresses during the printing process can lead to warping or distortion of the part, especially for large or complex geometries.
- How to Avoid: Optimize part orientation on the build platform, use appropriate support structures to anchor the part, and consider design modifications to reduce stress concentrations. Employing stress relief heat treatments after printing can also mitigate warping.
- Trudności związane z usuwaniem struktury wsparcia: Removing support structures can be challenging for intricate designs or delicate features, potentially damaging the part surface.
- How to Avoid: Design parts with self-supporting angles whenever possible, optimize support structure design for easier removal, and utilize dissolvable support materials when compatible with the chosen metal powder.
- Porosity and Density Issues: Inconsistent melting or insufficient laser power can lead to porosity (internal voids) and reduced density, compromising the mechanical properties of the end effector.
- How to Avoid: Optimize printing parameters such as laser power, scan speed, and layer thickness based on the material and machine. Ensure the metal powder has good flowability and packing density. Metal3DP utilizes high-quality metal powders and optimized printing processes to minimize porosity.
- Chropowatość powierzchni: As-printed surfaces can be too rough for certain applications, affecting fit, function, or aesthetics.
- How to Avoid: Optimize printing parameters for smoother surfaces (e.g., finer powder, thinner layers), and employ appropriate post-processing techniques like media blasting, grinding, or polishing to achieve the desired surface finish.
- Dimensional Inaccuracy: Deviations from the intended dimensions can occur due to material shrinkage, machine calibration issues, or improper build orientation.
- How to Avoid: Calibrate the 3D printer regularly, account for material shrinkage during the design phase, and choose build orientations that minimize dimensional errors in critical areas. Employing post-processing metrology and machining can ensure dimensional accuracy for critical features.
- Wybór materiału: Choosing the wrong metal powder for the application can lead to inadequate strength, wear resistance, or corrosion resistance.
- How to Avoid: Carefully consider the functional requirements of the robotic end effector and select a material with appropriate properties. Consult with material experts at Metal3DP to ensure the chosen powder is suitable for the intended application and printing process.
By understanding these common challenges and implementing preventive measures and appropriate post-processing techniques, manufacturers can effectively leverage metal 3D printing to produce high-quality and reliable robotic end effectors.
How to Choose the Right Metal 3D Printing Service Provider
Selecting the appropriate metal 3D printing service provider is crucial for the successful production of high-quality robotic end effectors. The right partner will possess the expertise, technology, and quality control processes necessary to meet your specific requirements. Here are key factors to consider when evaluating potential suppliers:
- Material Capabilities: Ensure the service provider offers a range of metal powders relevant to your application needs. For robotic end effectors, inquire about their experience with materials like 17-4PH stainless steel and AlSi10Mg, as recommended by Metal3DP. A provider with a diverse material portfolio can cater to various project requirements.
- Technologia i sprzęt: Understand the types of metal 3D printing technologies the provider utilizes (e.g., DMLS, SLM, EBM). Different technologies offer varying levels of precision, surface finish, and build volume. Ensure they have well-maintained and calibrated equipment suitable for producing the size and complexity of your end effectors. You can learn more about different printing methods on our website.
- Design and Engineering Support: A valuable service provider will offer design for additive manufacturing (DfAM) expertise. They should be able to provide guidance on optimizing your end effector design for metal 3D printing, including considerations for lightweighting, functional integration, and manufacturability.
- Post-Processing Services: Inquire about the in-house post-processing capabilities, such as support removal, heat treatment, surface finishing (e.g., machining, polishing, coating), and quality inspection. A provider offering comprehensive post-processing services can streamline the production process and ensure the final parts meet your specifications.
- Quality Assurance and Certifications: Verify if the service provider has robust quality management systems and relevant certifications (e.g., ISO 9001, AS9100 for aerospace). This demonstrates their commitment to quality and consistency.
- Experience and Industry Focus: Look for a provider with a proven track record in metal 3D printing, preferably with experience in your specific industry (e.g., aerospace, automotive, medical). Industry-specific experience can translate to a better understanding of your application requirements and potential challenges.
- Lead Times and Production Capacity: Discuss the typical lead times for similar projects and assess their production capacity to ensure they can meet your volume requirements and delivery schedules.
- Cost Structure and Transparency: Obtain a clear and detailed quotation that outlines all costs involved, including printing, materials, post-processing, and any additional services. Understand their pricing model and ensure transparency in their cost structure.
- Communication and Customer Support: Evaluate the provider’s responsiveness, communication style, and level of customer support. A collaborative partner who is readily available to address your questions and concerns is essential for a smooth and successful project.
Metal3DP is a leading provider of metal additive manufacturing solutions, offering a comprehensive suite of services from high-performance metal powders to advanced 3D printing equipment and application development support. We pride ourselves on our industry-leading print volume, accuracy, and reliability. You can find more information about our company on our about us page.
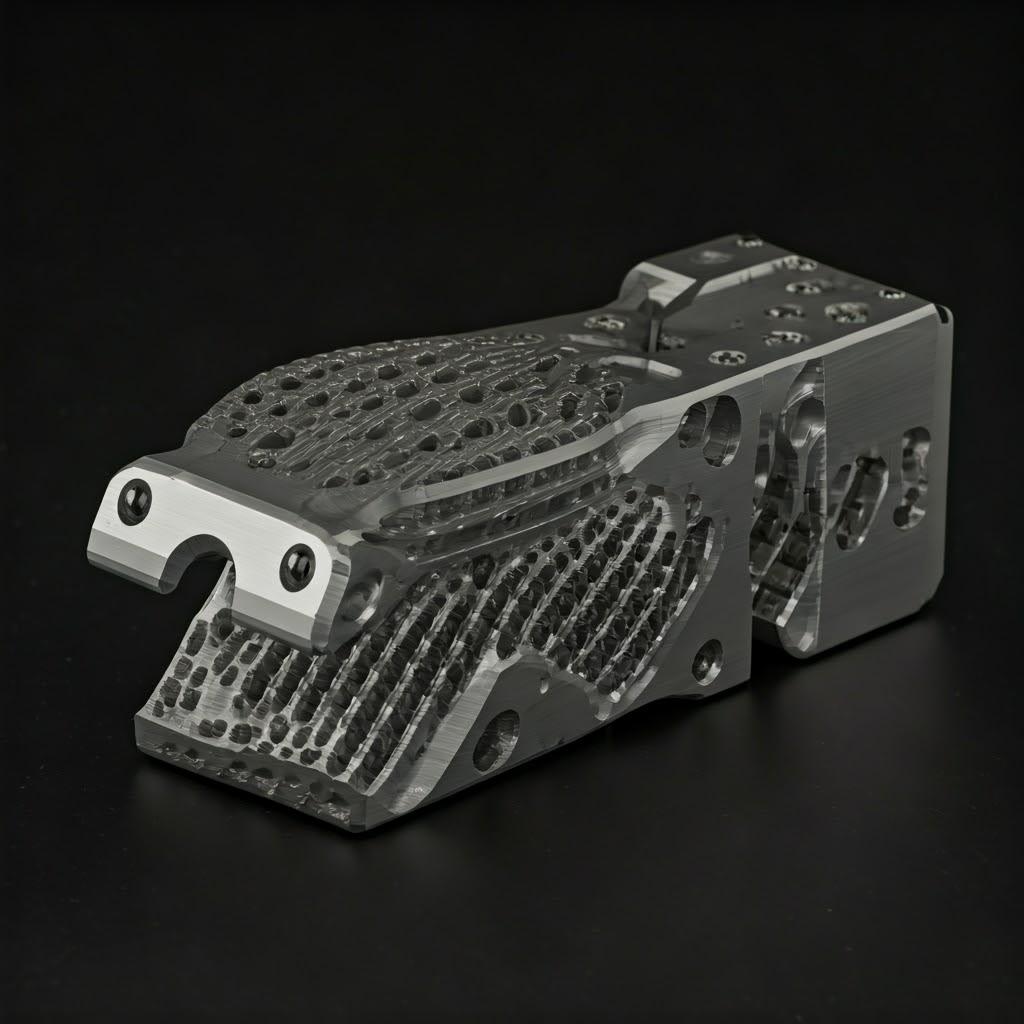
Cost Factors and Lead Time
The cost and lead time for producing robotic end effectors using metal 3D printing are influenced by several factors. Understanding these elements can help you plan your budget and timelines effectively:
Czynniki kosztowe:
- Koszt materiałów: The type and quantity of metal powder used are significant cost drivers. Specialty alloys like titanium or nickel-based superalloys are generally more expensive than standard stainless steels or aluminum alloys. The complexity of the part design, which affects the volume of material required, also plays a role. Metal3DP offers a range of high-quality metal powders at competitive prices.
- Czas budowy: The duration of the 3D printing process directly impacts the cost. Longer build times, often associated with larger parts, higher part density, or finer layer resolutions, increase machine usage and energy consumption costs.
- Koszty przetwarzania końcowego: The extent and complexity of post-processing steps significantly affect the overall cost. Simple support removal will have a lower cost than extensive machining, polishing, or specialized coatings.
- Machine and Operational Costs: Service providers factor in the cost of operating and maintaining their 3D printing equipment, as well as labor costs for design, printing, and post-processing.
- Complexity of Design: Highly complex geometries with intricate internal features or thin walls may require more sophisticated printing strategies and support structures, potentially increasing both build time and material usage.
- Volume of Production: While metal 3D printing is often cost-effective for low to medium volumes and customized parts, the cost per part may decrease with larger production runs due to economies of scale. Consider exploring our product offerings for various production needs.
Czas realizacji:
- Design and Pre-processing: The initial design phase, including optimization for additive manufacturing, and pre-processing steps like build preparation and support generation, contribute to the overall lead time.
- Czas drukowania: The actual duration of the 3D printing process depends on the part size, complexity, material, and chosen printing technology.
- Post-Processing Time: The time required for support removal, heat treatment, surface finishing, and quality inspection varies depending on the specific requirements.
- Shipping and Delivery: The time taken for the finished parts to be shipped to your location needs to be factored into the overall lead time.
It’s important to discuss cost and lead time expectations with your chosen metal 3D printing service provider early in the project. Obtaining a detailed quotation and production timeline will help you make informed decisions and manage your project effectively.
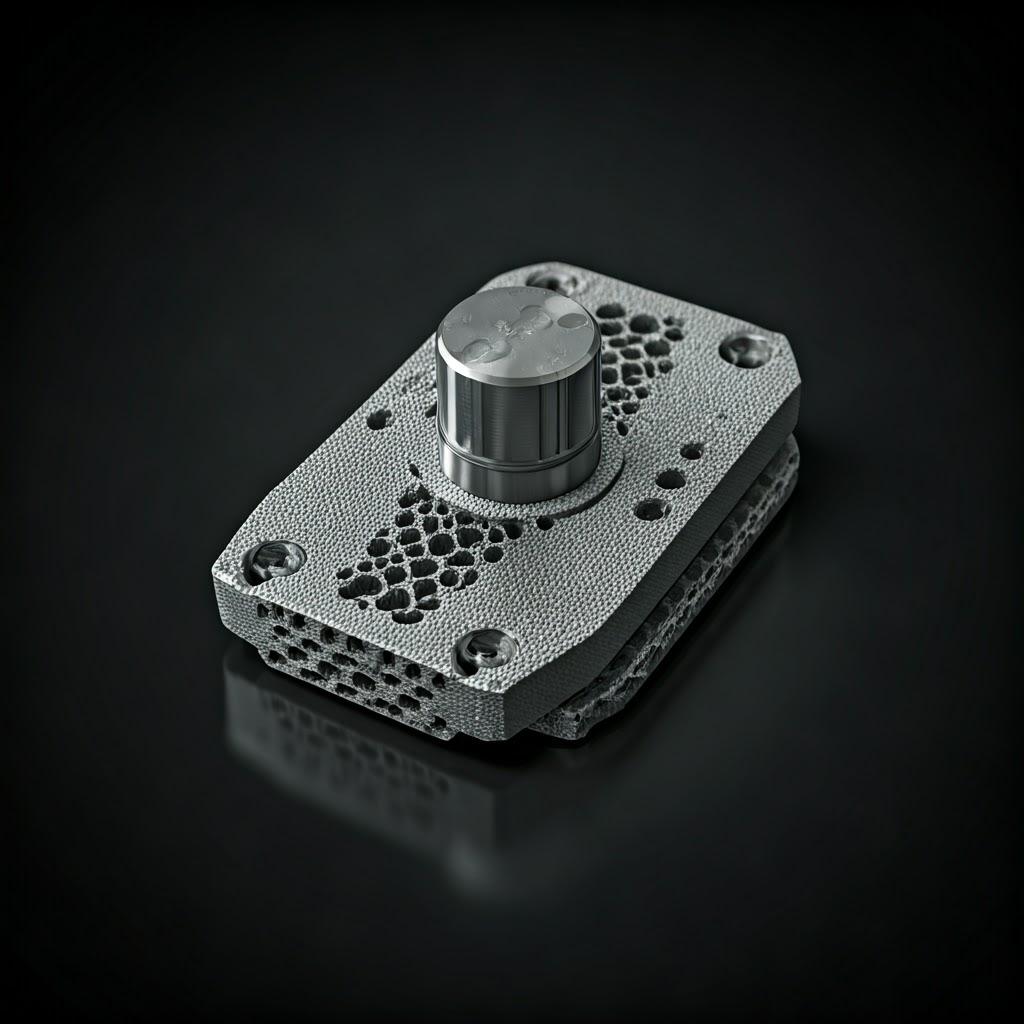
Często zadawane pytania (FAQ)
- What is the typical accuracy achievable with metal 3D printed robotic end effectors?
- Metal 3D printing technologies like DMLS and SLM can typically achieve tolerances in the range of ±0.1 to ±0.2 mm for smaller parts. However, achieving tighter tolerances often requires post-processing steps like CNC machining. The dimensional accuracy also depends on factors like part size, material, and build orientation.
- Can metal 3D printed end effectors be as strong as those manufactured traditionally?
- Yes, metal 3D printed parts, when produced with optimized parameters and appropriate materials and post-processing, can achieve comparable or even superior mechanical properties to traditionally manufactured parts. Materials like 17-4PH stainless steel, offered by Metal3DP, exhibit high strength and hardness suitable for demanding robotic applications.
- What are the limitations of using metal 3D printing for robotic end effectors?
- Some limitations include the initial investment cost for equipment (if you choose in-house production), the as-printed surface finish which may require post-processing, and potential challenges with achieving very tight tolerances on complex geometries without secondary machining. However, advancements in technology and post-processing techniques are continuously addressing these limitations.
- How do I get started with metal 3D printing for my robotic end effector needs?
- The best way to start is to identify your specific application requirements, including the functional needs, material properties, and desired tolerances. Then, contact a reputable metal 3D printing service provider like Metal3DP. Our team can provide guidance on material selection, design optimization, and the overall production process.
Wnioski
Metal 3D printing is revolutionizing the design and manufacturing of robotic end effectors, offering unparalleled opportunities for customization, lightweighting, functional integration, and rapid prototyping. By leveraging the design freedom and material versatility of additive manufacturing, industries across aerospace, automotive, medical, and industrial automation can create high-performance, application-specific tools that enhance the efficiency and capabilities of their robotic systems.
Metal3DP is at the forefront of this transformative technology, providing industry-leading metal powders, advanced 3D printing solutions, and comprehensive application development support. Our commitment to quality, innovation, and customer satisfaction makes us a trusted partner for businesses looking to harness the power of metal additive manufacturing for their robotic end effector needs. Contact Metal3DP today to explore how our capabilities can empower your organization’s additive manufacturing goals and drive the future of your robotic automation.
Udostępnij
MET3DP Technology Co., LTD jest wiodącym dostawcą rozwiązań w zakresie produkcji addytywnej z siedzibą w Qingdao w Chinach. Nasza firma specjalizuje się w sprzęcie do druku 3D i wysokowydajnych proszkach metali do zastosowań przemysłowych.
Zapytaj o najlepszą cenę i spersonalizowane rozwiązanie dla Twojej firmy!
Powiązane artykuły
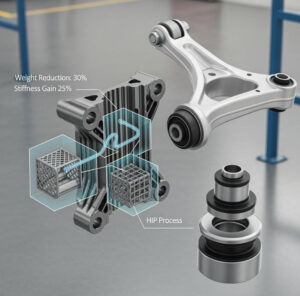
Metal 3D Printed Subframe Connection Mounts and Blocks for EV and Motorsport Chassis
Czytaj więcej "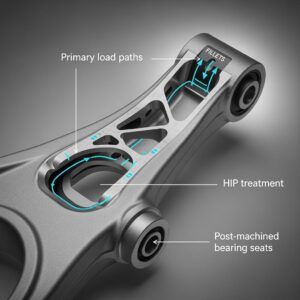
Metal 3D Printing for U.S. Automotive Lightweight Structural Brackets and Suspension Components
Czytaj więcej "Informacje o Met3DP
Ostatnia aktualizacja
Nasz produkt
KONTAKT
Masz pytania? Wyślij nam wiadomość teraz! Po otrzymaniu wiadomości obsłużymy Twoją prośbę całym zespołem.