Lightweight GPS Antenna Mounts for Drones
Spis treści
Introduction: The Critical Role of Optimized GPS Antenna Mounts in UAV Performance
Unmanned Aerial Vehicles (UAVs), commonly known as drones, have revolutionized industries ranging from aerial surveying and infrastructure inspection to defense reconnaissance and package delivery. Central to their autonomous or remotely piloted operation is the Global Positioning System (GPS), providing critical data for navigation, geo-tagging, and precise positioning. However, the accuracy and reliability of GPS data heavily depend on the quality of the signal received by the antenna. This is where the often-overlooked GPS antenna mount plays a pivotal role.
A UAV GPS antenna mount is far more than just a simple bracket. It is a critical component engineered to securely position the GPS antenna, shield it from electromagnetic interference (EMI), dampen vibrations, and ensure an unobstructed view of the sky for optimal satellite signal reception. In the demanding operational environment of UAVs, factors like weight, durability, structural integrity, and aerodynamic efficiency are paramount. Even slight inaccuracies in GPS data, potentially caused by a poorly designed or failing mount, can lead to navigational errors, mission failure, or even loss of the aircraft.
Traditional manufacturing methods like CNC machining or injection molding often present limitations when creating antenna mounts that meet the stringent requirements of modern UAV designs. Machining complex shapes can be subtractive and wasteful, potentially leaving unnecessary weight, while injection molding requires expensive tooling and may not offer the desired material strength or thermal stability, especially with lightweight metals.
To jest miejsce wytwarzanie przyrostowe metali (AM)lub druk 3D z metalu, emerges as a transformative solution. By building parts layer by layer directly from digital designs using high-performance metal powders, AM enables the creation of highly complex, lightweight, and durable GPS antenna mounts optimized for specific drone platforms and operational needs. Leading providers like Met3dp leverage advanced technologies and materials to deliver superior mounting solutions. Met3dp, headquartered in Qingdao, China, specializes in both state-of-the-art Drukowanie 3D equipment and the high-performance metal powders essential for producing mission-critical UAV components. Our focus on produkcja precyzyjna zapewnia, że UAV components meet the highest standards demanded by aerospace, defense, and industrial clients, guaranteeing GPS signal integrity through optimized design and material selection. We understand the nuances of drone navigation systems and provide components that enhance overall system reliability and performance, making us a trusted UAV component supplier for businesses seeking cutting-edge solutions.
What Are UAV GPS Antenna Mounts Used For? Applications Across Industries
The function of a UAV GPS antenna mount extends beyond simply holding the antenna. Its design directly impacts the drone’s performance, reliability, and the quality of data collected. The primary uses and applications span a diverse range of industries where UAV technology is deployed:
- Secure Antenna Fixation: The most fundamental role is to rigidly secure the GPS antenna to the drone’s airframe, preventing movement or detachment during flight, landing, or high-G maneuvers. This ensures consistent positioning relative to the drone’s inertial measurement unit (IMU) for accurate sensor fusion.
- Vibration Damping: UAVs, particularly multirotor types, generate significant vibrations from motors and propellers. A well-designed metal mount, potentially incorporating specific geometries or utilizing materials with inherent damping properties, can isolate the sensitive GPS antenna from these vibrations, which could otherwise degrade signal quality or damage the antenna electronics.
- Optimized Signal Reception: The mount positions the antenna, typically on the top surface of the UAV, for the clearest possible “view” of the sky, maximizing the number of satellites it can track. The design must avoid obstruction by other drone components and minimize shadowing effects from the airframe itself.
- Electromagnetic Interference (EMI) Shielding: The electronic environment on a UAV is noisy, with signals from motors, electronic speed controllers (ESCs), communication systems, and video transmitters. While the mount itself might not provide extensive shielding (depending on material and design), its placement and integration are critical to keep the GPS antenna away from major EMI sources. Some designs might incorporate specific features or grounding points to mitigate interference.
- Weight Minimization: Every gram saved on a UAV component contributes to longer flight times or increased payload capacity. Metal AM allows for highly optimized, lightweight mount designs that maintain structural integrity, directly addressing this critical requirement.
- Environmental Protection: While the antenna itself usually has environmental sealing, the mount contributes to the overall robustness of the installation, ensuring secure attachment in various weather conditions, including rain, wind, and temperature fluctuations.
Zastosowania przemysłowe:
The need for reliable, high-performance GPS antenna mounts is prevalent across numerous sectors utilizing drone technology:
- Przemysł lotniczy i obronny: Military UAVs performing intelligence, surveillance, and reconnaissance (ISR), target acquisition, or communications relay missions demand the utmost reliability and precision. Antenna mounts must be robust, lightweight, and potentially incorporate specific materials or coatings for signature management or operation in harsh environments. Defense UAV hardware suppliers rely on advanced manufacturing for these critical parts.
- Commercial Surveying and Mapping: Drones used for creating high-resolution maps, topographic surveys, or 3D models require precise GPS data (often RTK or PPK corrected) for geospatial accuracy. The antenna mount’s stability and positioning are crucial for data quality.
- Infrastructure Inspection: UAVs inspecting bridges, power lines, wind turbines, pipelines, and buildings need reliable navigation to operate safely close to structures. Secure and optimally placed GPS antennas are essential for positional awareness. Industrial drone parts manufacturers cater to this growing market.
- Agriculture: Precision agriculture utilizes drones for crop monitoring, yield analysis, and targeted spraying. Accurate GPS data ensures precise application and efficient field coverage, demanding stable antenna mounting.
- Logistics and Delivery: Delivery drones navigating complex urban or suburban environments require highly reliable GPS for route planning and accurate drop-offs. Component failure is not an option.
- Emergency Services and Public Safety: Drones used for search and rescue, situational awareness during incidents, or monitoring events rely heavily on accurate positioning provided by GPS.
- Badania i rozwój: Universities and research institutions developing new drone technologies or applications require customizable and high-performance components, including antenna mounts, often leveraging the flexibility of AM for rapid prototyping.
Dla UAV system integration specialists and commercial drone parts distributors, sourcing high-quality, optimized GPS antenna mounts manufactured using advanced techniques like metal 3D printing is key to delivering reliable and high-performing drone solutions to these diverse industries.
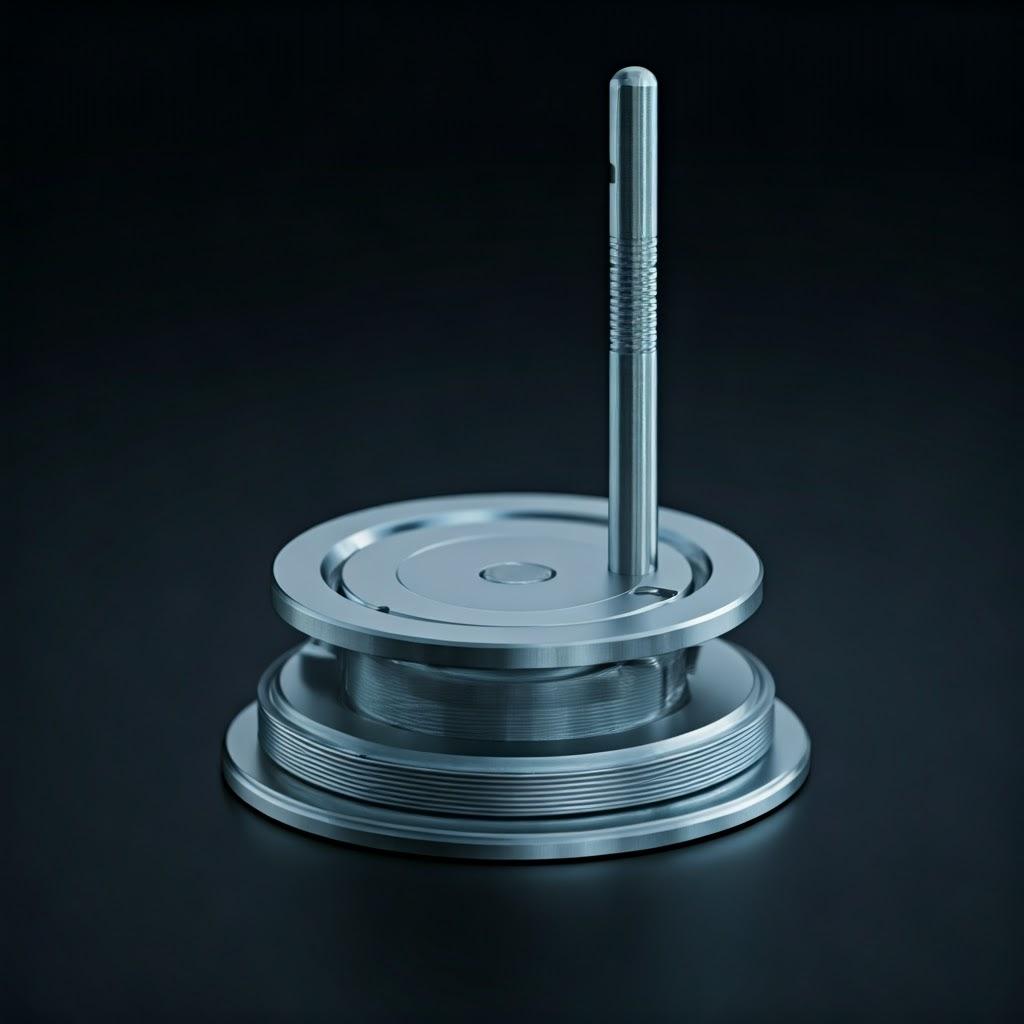
Why Use Metal 3D Printing for UAV GPS Antenna Mounts? Key Advantages Over Traditional Methods
While traditional manufacturing methods have served the industry for years, metal additive manufacturing offers compelling advantages specifically tailored to the challenges of producing high-performance UAV GPS antenna mounts. Comparing AM to conventional techniques like CNC machining and injection molding highlights why it’s rapidly becoming the preferred method for demanding drone applications:
Comparison: Metal AM vs. Traditional Manufacturing for Antenna Mounts
Cecha | Metal Additive Manufacturing (e.g., LPBF/SLM) | CNC Machining (Subtractive) | Injection Molding (Plastics/Composites) |
---|---|---|---|
Złożoność projektu | High (Complex geometries, internal channels, lattices) | Moderate to High (Limited by tool access) | High (Requires complex mold design) |
Lekkość | Excellent (Topology optimization, lattices feasible) | Moderate (Material removal limited by process) | Good (Low-density plastics) but lower strength |
Opcje materiałowe | Growing range of high-performance metals (Al, Ti, Steel, Scalmalloy®) | Wide range of metals, plastics | Primarily thermoplastics, some composites |
Wytrzymałość do wagi | Excellent (Especially with alloys like Scalmalloy®) | Good (Depends on metal chosen) | Lower compared to metals |
Konsolidacja części | High potential (Integrating multiple functions) | Low potential | Low potential |
Koszty oprzyrządowania | None (Direct digital manufacturing) | Low (Fixturing may be needed) | Very High (Mold design & fabrication) |
Lead Time (Proto/Low Vol) | Szybko | Umiarkowany | Very Slow (Due to tooling) |
Waste Material | Low (Powder is largely recyclable) | High (Material removed as chips) | Low (Runner/sprue waste, often regrindable) |
Personalizacja | High (Easy design changes between builds) | Moderate (Requires reprogramming) | Low (Requires mold modification/new mold) |
Ideal Volume | Prototypes, Low-to-Medium Volume, Highly Custom Parts | Prototypes, Low-to-High Volume (Simpler parts) | High Volume |
Export to Sheets
Key Advantages of Metal AM for UAV GPS Antenna Mounts:
- Unmatched Lightweighting Potential: This is arguably the most significant benefit for UAV components. Metal AM enables:
- Topology Optimization: Algorithms determine where material is essential for structural integrity and remove it elsewhere, resulting in organic-looking, highly efficient structures that are impossible to machine conventionally.
- Struktury kratowe: Internal lattice or honeycomb structures can drastically reduce weight while maintaining required stiffness and strength.
- Result: Longer flight endurance, higher payload capacity, or improved maneuverability for the drone.
- Geometric Freedom for Optimized Design: AM removes many constraints of traditional manufacturing. Designers can:
- Create highly complex geometry manufacturing solutions tailored to specific antenna types and drone airframes.
- Integrate features like cable routing channels, mounting points for other sensors, or aerodynamic fairings directly into the mount design (Konsolidacja części).
- Optimize the shape for signal reception and minimal aerodynamic drag.
- Materiały o wysokiej wydajności: Access to advanced metal powders specifically designed for AM, such as:
- Stopy aluminium (AlSi10Mg): Offer a good balance of strength, low weight, and thermal conductivity.
- High-Strength Aluminum (Scalmalloy®): Provides strength comparable to some steels or titanium alloys but at a much lower density, ideal for extreme lightweighting in demanding applications.
- Titanium Alloys (e.g., Ti6Al4V): Offer excellent strength-to-weight, corrosion resistance, and high-temperature performance, suitable for the most demanding aerospace or defense applications.
- Szybkie prototypowanie i iteracja projektu: New mount designs or modifications can be printed and tested in days rather than weeks or months waiting for tooling or complex machining setups. This accelerates the development cycle for new UAV platforms.
- Customization and Low Volume Production: AM is economically viable for producing small batches of niestandardowe części UAV tailored to specific mission requirements or drone models without incurring high tooling costs. This is ideal for specialized platforms or upgrades.
- Zmniejszona ilość odpadów materiałowych: As an additive process, AM uses only the material needed to build the part and its supports. Unused powder can typically be recycled and reused, making it a more sustainable option compared to the significant waste generated by subtractive CNC machining.
- Produkcja na żądanie: Parts can be produced as needed, reducing inventory requirements for drone manufacturers and service providers – a key consideration for B2B procurement.
By leveraging these additive manufacturing benefits, companies like Met3dp can provide GPS antenna mounts that significantly enhance UAV performance and reliability compared to those made with older methods. The ability to produce lightweight drone components with intricate designs makes metal AM vs CNC machining a clear choice for optimization.
Recommended Materials for 3D Printed Antenna Mounts: AlSi10Mg and Scalmalloy® Deep Dive
Choosing the right material is fundamental to achieving the desired performance characteristics for a UAV GPS antenna mount. While various metals can be 3D printed, aluminum alloys are frequently favored for UAV applications due to their inherent low density. Among these, AlSi10Mg and Scalmalloy® stand out as excellent choices, offering distinct advantages depending on the specific requirements. Met3dp possesses deep expertise in processing these advanced materials, utilizing high-quality powders produced via industry-leading gas atomization techniques to ensure optimal part properties. Nasz Wysokiej jakości proszki metali exhibit high sphericity and good flowability, crucial for printing dense, reliable components.
AlSi10Mg: The Versatile Workhorse
AlSi10Mg is one of the most common and well-understood aluminum alloys used in metal additive manufacturing, particularly Laser Powder Bed Fusion (LPBF). It’s essentially an aluminum alloy with silicon (around 10%) and magnesium (trace amounts) as the main alloying elements.
- Kluczowe właściwości:
- Dobry stosunek wytrzymałości do wagi: While not as high as Scalmalloy® or titanium, it offers significantly better strength than typical cast aluminum alloys at a low density (approx. 2.67 g/cm³).
- Doskonałe właściwości termiczne: Good thermal conductivity, which can be beneficial for dissipating any heat generated by antenna electronics, although typically minimal for GPS.
- Dobra odporność na korozję: Suitable for operation in various atmospheric conditions.
- Spawalność: Can be welded if necessary, although AM often allows for part consolidation eliminating this need.
- Przetwarzalność: Well-characterized and relatively easy to process using standard LPBF parameters.
- Efektywność kosztowa: Generally more affordable than higher-performance alloys like Scalmalloy® or titanium.
- Why it Matters for GPS Antenna Mounts:
- Lekka waga: Contributes directly to reducing the overall weight of the UAV.
- Sufficient Strength: Provides ample structural integrity for securing the antenna under typical flight loads and vibrations for many commercial and industrial applications.
- Możliwość drukowania: Allows for the creation of complex, optimized geometries enabled by AM.
- Cost Balance: Offers a good balance between performance and cost, making it ideal for a wide range of drone platforms where extreme performance is not the absolute top priority.
- Met3dp Advantage: Met3dp’s rigorous powder production process ensures consistent AlSi10Mg powder quality, leading to printed parts with reliable mechanical properties and minimal defects. Our expertise in process parameter optimization for AlSi10Mg guarantees parts meet design specifications.
Scalmalloy®: The High-Performance Champion
Scalmalloy® is a patented high-performance aluminum-magnesium-scandium alloy specifically developed for additive manufacturing by APWORKS. It pushes the boundaries of what’s possible with lightweight metal components.
- Kluczowe właściwości:
- Wyjątkowy stosunek wytrzymałości do wagi: This is Scalmalloy®’s defining characteristic. It offers specific strength (strength divided by density) significantly higher than AlSi10Mg and comparable or even superior to some grades of titanium and steel, but at the much lower density of aluminum (approx. 2.66 g/cm³).
- High Ductility and Toughness: Unlike some high-strength materials, Scalmalloy® retains good ductility, meaning it can deform significantly before fracturing, making it more resilient to impacts or unexpected loads.
- Excellent Fatigue Strength: Resists crack initiation and growth under cyclic loading (like vibrations), crucial for long-term durability on a UAV.
- Dobra odporność na korozję: Suitable for demanding environments.
- Designed for AM: Its composition is optimized for weldability during the layer-by-layer fusion process, resulting in dense, crack-free parts.
- Why it Matters for GPS Antenna Mounts:
- Extreme Lightweighting: Enables the design of antenna mounts that are significantly lighter than even optimized AlSi10Mg versions, pushing the limits of flight endurance and payload capacity. Ideal for high-performance drones.
- Najwyższa trwałość: Enhanced fatigue resistance makes it perfect for UAVs subjected to high vibrations or operating in harsh conditions (e.g., defense applications, long-endurance industrial drones).
- High-Stress Applications: Suitable for mounts that may bear additional loads or are part of a more integrated structural element.
- Performance Edge: When absolute minimum weight and maximum strength are critical design drivers, Scalmalloy strength-to-weight provides a distinct advantage.
- Met3dp Advantage: Processing advanced alloys like Scalmalloy® requires precise control over printing parameters and thermal management. Met3dp’s state-of-the-art equipment and deep materials science expertise enable the successful printing of these high-performance AM materials, unlocking their full potential for demanding aerospace aluminum alloy applications, including critical UAV components.
Material Selection Summary:
Cecha | AlSi10Mg | Scalmalloy® |
---|---|---|
Podstawowa korzyść | Versatility, Cost-Effectiveness | Highest Strength-to-Weight, Fatigue Resistance |
Gęstość | ~2.67 g/cm³ | ~2.66 g/cm³ |
Tensile Strength (Typical) | Moderate-High (after heat treatment) | Very High (Comparable to Ti alloys) |
Plastyczność | Dobry | Doskonały |
Wytrzymałość zmęczeniowa | Dobry | Doskonały |
Koszt | Niższy | Wyższy |
Idealne zastosowania | General Commercial/Industrial UAVs, Prototypes | High-Performance UAVs, Defense, Extreme Lightweighting |
Export to Sheets
By offering both AlSi10Mg and potentially Scalmalloy® (or similar high-performance options), service providers like Met3dp give engineers the flexibility to choose the optimal material based on their specific performance requirements, budget constraints, and application demands for their UAV GPS antenna mounts.
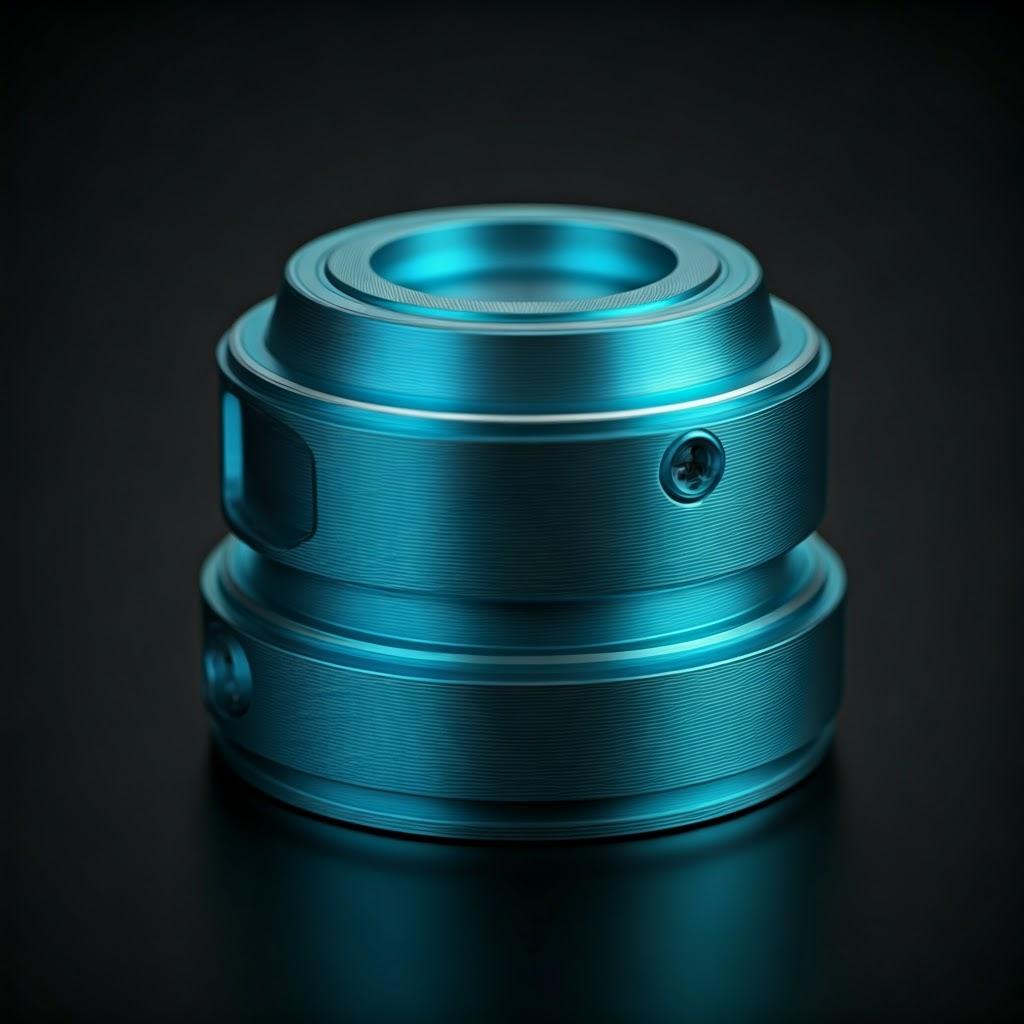
Design Considerations: Optimizing Antenna Mounts for Additive Manufacturing (DfAM)
Successfully leveraging metal 3D printing for UAV GPS antenna mounts goes beyond simply converting an existing design file. To truly harness the benefits of additive manufacturing – particularly lightweighting and performance optimization – requires embracing Projektowanie dla produkcji addytywnej (DfAM) principles. DfAM involves designing parts specifically with the capabilities and constraints of the chosen AM process (like Laser Powder Bed Fusion – LPBF) in mind. For engineers and designers creating antenna mounts, applying DfAM can lead to significant improvements in weight, structural efficiency, and printability. Partnering with an experienced AM provider like Met3dp, who offers application development services, can provide invaluable guidance in implementing these strategies.
Key DfAM strategies for optimizing UAV GPS antenna mounts include:
- Topology Optimization:
- Concept: Utilizing specialized software (e.g., Altair Inspire, nTopology, ANSYS Discovery) to simulate operational loads (vibration, static forces, aerodynamic pressure) on the mount and algorithmically remove material from areas experiencing low stress.
- Goal: Achieve the maximum possible weight reduction while ensuring the part retains the necessary stiffness and strength to perform its function reliably.
- Outcome: Often results in organic, non-intuitive shapes that are highly efficient structurally but difficult or impossible to create using traditional manufacturing. Critical for maximizing UAV parts performance where weight is paramount.
- Lattice Structures & Generative Design:
- Concept: Replacing solid material sections with internal or external lattice structures (e.g., honeycomb, gyroid, truss-based). Generative design tools can automatically create complex, optimized forms based on load cases and constraints.
- Benefits for Mounts:
- Further Lightweighting: Drastically reduces material usage and weight beyond simple topology optimization.
- Vibration Damping: Certain lattice geometries can absorb and dissipate vibrational energy, potentially improving GPS signal stability.
- Enhanced Stiffness-to-Weight: Provides rigidity where needed without the penalty of solid material.
- Rozważania: Requires careful analysis to ensure structural integrity and manufacturability (powder removal, minimum strut size). Lattice structures drone components are a hallmark of advanced AM design.
- Konsolidacja części:
- Concept: Redesigning assemblies of multiple components into a single, monolithic printed part.
- Application for Mounts: Integrating features like mounting brackets, cable routing clips, vibration damping elements, or even parts of the adjacent airframe structure directly into the antenna mount design.
- Zalety: Reduces part count, eliminates fasteners (potential failure points), simplifies assembly, reduces overall weight, and often lowers total cost.
- Build Orientation Strategy:
- Concept: Deciding how the part will be oriented on the build plate within the 3D printer.
- Uderzenie: Significantly affects:
- Support Structure Needs: Minimizing overhangs reduces support material, print time, and post-processing effort.
- Wykończenie powierzchni: Upward-facing and vertical surfaces generally have better finish than downward-facing surfaces requiring support. Critical dimensions might dictate orientation.
- Czas budowy: Part height is a major factor in build duration.
- Właściwości mechaniczne: Anisotropy (direction-dependent properties) can occur in AM parts; orientation might be chosen to align strength with primary load paths.
- Support Structure Minimization and Optimization:
- Concept: Supports are necessary for overhangs typically exceeding 45 degrees from the horizontal, preventing collapse during printing. However, they add print time, material usage, and require removal.
- DfAM Techniques:
- Designing with self-supporting angles (e.g., using chamfers instead of sharp overhangs).
- Employing breakaway or easily removable support structures.
- Considering support placement for ease of access during post-processing.
- Using topology optimization often naturally results in fewer problematic overhangs. The goal is minimizing support structures through clever design.
- Wall Thickness and Feature Size:
- Constraints: LPBF processes have minimum printable wall thicknesses (often 0.4-1.0 mm depending on material, machine, geometry) and feature sizes.
- Design Rules: Ensure walls are sufficiently thick for structural integrity and printability. Avoid overly thin or delicate features that might warp or fail during printing or handling. Lattice strut diameters also have minimums.
- Hole Design:
- Vertical Holes: Generally print accurately without support.
- Horizontal Holes: Often require support or are better designed with a self-supporting “teardrop” or diamond shape to avoid internal supports that are difficult to remove. Minimum printable hole diameters depend on orientation and machine capabilities.
- Filleting and Chamfering:
- Korzyści: Adding fillets (rounded edges) or chamfers (angled edges) at sharp corners can reduce stress concentrations, improving fatigue life. They can also transform steep overhangs into self-supporting angles.
- Powder Escape Holes:
- Necessity: Crucial when designing parts with internal cavities or lattice structures. These allow unfused powder to be removed during post-processing.
- Projekt: Strategically place escape holes (typically ≥ 2-5 mm diameter) considering gravity and vibration-assisted removal techniques. Ensure internal pathways allow powder to flow out.
By thoughtfully applying these DfAM principles, engineers can unlock the full potential of metal AM, creating UAV GPS antenna mounts that are lighter, stronger, more functional, and often more cost-effective in the long run than their conventionally manufactured counterparts.
Achieving Precision: Tolerance, Surface Finish, and Dimensional Accuracy in Metal 3D Printed Mounts
While metal AM offers incredible design freedom, understanding the achievable levels of precision is crucial for ensuring the final antenna mount fits correctly, functions reliably, and meets quality standards. Engineers and procurement managers must consider tolerance, surface finish, and dimensional accuracy when specifying and evaluating 3D printed components. Met3dp prides itself on utilizing equipment known for industry-leading accuracy and reliability, coupled with rigorous process control, to deliver parts meeting demanding specifications.
Tolerance in Metal AM:
- Definicja: Tolerance refers to the permissible range of variation in a dimension of a part.
- Achievable Levels: For typical LPBF processes, general achievable tolerances are often in the range of ±0.1 mm to ±0.2 mm for smaller features, or a percentage of the overall dimension (e.g., ±0.1% to ±0.2%) for larger parts. This often aligns with standards like ISO 2768 Class m (medium) or sometimes Class f (fine) for as-built parts.
- Factors Influencing Tolerance:
- Machine Calibration: Accuracy of the laser system, galvo mirrors, and motion control.
- Właściwości materiału: Shrinkage characteristics during solidification and cooling.
- Thermal Stresses: Internal stresses built up during the process can cause minor distortions.
- Support Strategy: How the part is supported can influence its final geometry.
- Part Size and Geometry: Larger parts or complex geometries may exhibit greater deviation.
- Przetwarzanie końcowe: Heat treatment can cause slight dimensional changes; machining achieves much tighter tolerances.
- Importance for Antenna Mounts: Critical for ensuring proper fit onto the drone airframe, correct alignment of the GPS antenna for optimal reception, and interfacing with fasteners or other components. Mating surfaces and hole diameters often require specific tolerances.
Surface Finish (Surface Roughness):
- Definicja: Surface finish describes the texture and smoothness of a part’s surface, often quantified by the average roughness (Ra).
- As-Built Characteristics: Metal AM parts inherently have a rougher surface finish compared to machined parts due to the layer-by-layer process and partially melted powder particles adhering to the surface. Typical as-built Ra values for LPBF range from 5 µm to 20 µm.
- Factors Influencing Surface Finish:
- Grubość warstwy: Thinner layers generally result in a smoother finish but increase build time.
- Powder Particle Size: Finer powders can lead to smoother surfaces.
- Laser Parameters: Settings like laser power and scan speed influence melt pool dynamics and surface texture.
- Part Orientation: Upward-facing and vertical surfaces tend to be smoother than downward-facing surfaces that required support structures (which leave witness marks upon removal). Low-angle surfaces exhibit more pronounced “stair-stepping.”
- Post-Processing Impact: Surface finish can be significantly improved through various post-processing steps (see next section), such as bead blasting (uniform matte finish), tumbling (smoothing edges), or machining (very smooth, precise surfaces). The required finish depends on the application – functional interfaces may need smoothness, while other areas might be acceptable as-built or bead blasted.
Dokładność wymiarowa:
- Definicja: Dimensional accuracy refers to how closely the final printed part conforms to the dimensions specified in the original CAD model. It encompasses both tolerance deviations and potential geometric distortions like warpage.
- Wyzwania: Achieving high accuracy requires careful control over the entire AM process, compensating for material shrinkage, managing thermal stresses, and ensuring machine calibration. Warpage due to residual stress is a potential concern, especially for large, flat parts or complex geometries.
- Achieving Accuracy: Experienced AM providers use calibrated equipment, optimized process parameters, simulation tools (in some cases) to predict and compensate for distortion, and robust quality control measures. Post-print inspection (e.g., CMM scanning) verifies dimensional accuracy against requirements.
Typical Precision Levels Summary:
Parametr | As-Built (LPBF Typical) | After Bead Blasting | After CNC Machining |
---|---|---|---|
Tolerancja | ±0.1 to ±0.2 mm (or ±0.1-0.2%) | Generally Unchanged | ±0.01 to ±0.05 mm possible |
Surface Finish (Ra) | 5 – 20 µm | 3 – 10 µm (Uniform Matte) | < 1.6 µm (or better) |
Dokładność wymiarowa | Good (Subject to process control) | Generally Unchanged | Very High (On machined features) |
Export to Sheets
Understanding these achievable levels allows designers to specify appropriate tolerances and finishes for different features of the antenna mount, leveraging post-processing where necessary to meet critical requirements for precision drone components. Effective quality control in AM ensures these standards are consistently met.
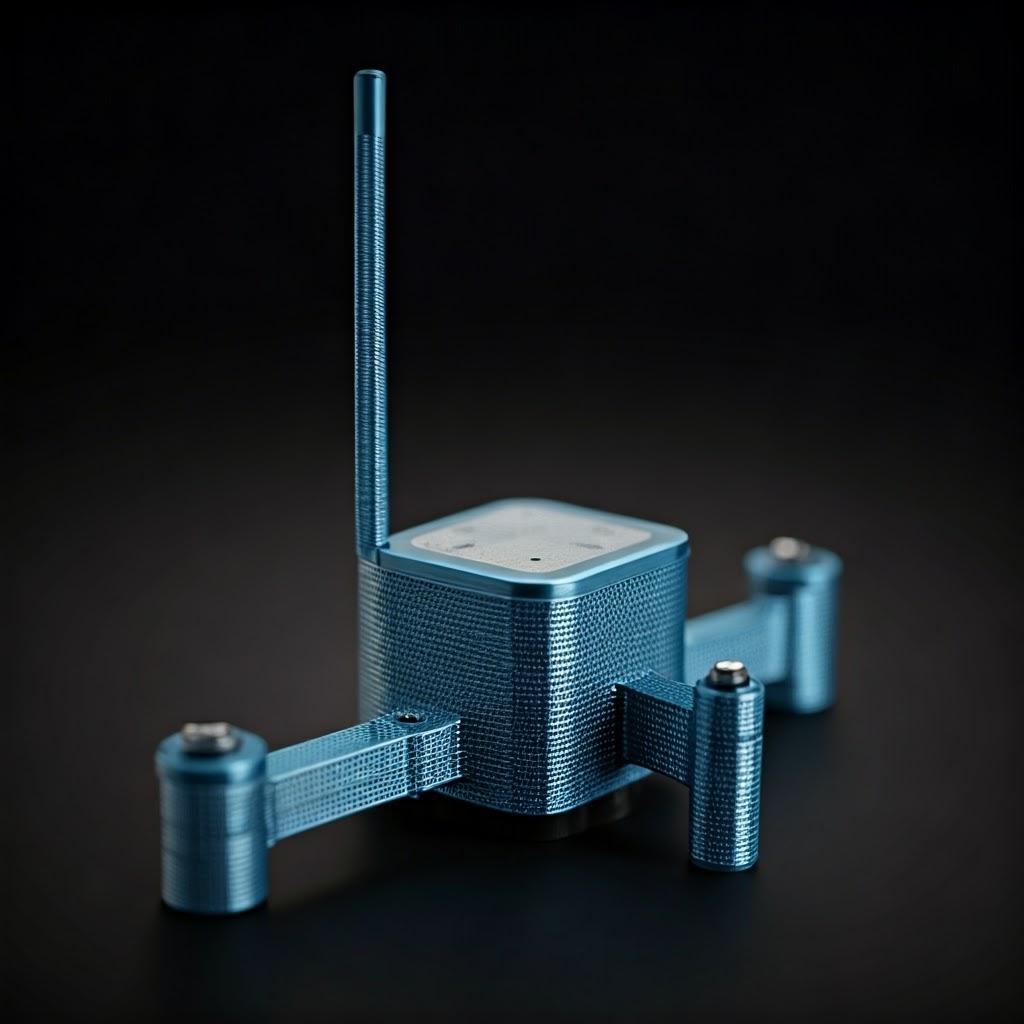
Beyond Printing: Post-Processing Requirements for Optimal Antenna Mount Performance
Producing a high-quality metal 3D printed UAV GPS antenna mount involves more than just the printing process itself. A series of crucial przetwarzanie końcowe steps are typically required to transform the raw printed part into a finished component ready for assembly and deployment. These steps are essential for achieving the desired mechanical properties, dimensional accuracy, surface finish, and overall reliability. Neglecting proper post-processing can compromise the performance and longevity of the mount.
Common post-processing stages for metal AM antenna mounts, particularly those made from aluminum alloys like AlSi10Mg or Scalmalloy®, include:
- Stress Relief / Heat Treatment:
- Cel: This is arguably the most critical post-processing step for load-bearing aluminum AM parts. The rapid heating and cooling cycles during LPBF induce significant internal stresses. Heat treatment relieves these stresses, preventing potential distortion or cracking later. Crucially, it also develops the final desired microstructure and mechanical properties (strength, ductility, hardness) of the alloy.
- Proces: Typically involves heating the part in a controlled atmosphere furnace according to specific time-temperature profiles defined for the alloy (e.g., solution treatment followed by artificial aging, like a T6 temper for AlSi10Mg). Scalmalloy® also requires specific heat treatments to achieve its high strength levels.
- Importance: Ensures the mount possesses the necessary heat treatment aluminum alloys provide in terms of strength and durability to withstand operational loads and vibrations.
- Part Removal from Build Plate:
- Proces: Once the build is complete and cooled, the printed part(s), still attached to the metal build plate via support structures or a solid base layer, must be carefully removed. This is typically done using wire EDM (Electrical Discharge Machining) or a bandsaw.
- Consideration: Care must be taken not to damage the part during removal.
- Usunięcie konstrukcji wsporczej:
- Cel: Removing the temporary support structures required during printing for overhangs and complex features.
- Metody: Can range from manual breaking/clipping for well-designed breakaway supports to more involved methods like CNC machining, grinding, or hand-finishing, especially for supports in intricate areas.
- DfAM Link: The ease and effectiveness of support removal are heavily influenced by the initial design (DfAM principles).
- Powder Removal (Depowdering):
- Cel: Ensuring all residual, unfused metal powder is removed from the part, especially from internal channels, cavities, or lattice structures. Trapped powder adds unnecessary weight and can be a contamination risk.
- Metody: Includes manual brushing, tapping, using compressed air jets, bead blasting (which also serves as a surface finish step), and sometimes ultrasonic cleaning in specialized baths.
- DfAM Link: Designing adequate powder escape holes and clear internal pathways is essential for effective depowdering.
- Surface Treatment / Finishing:
- Cel: To improve surface quality, aesthetics, or prepare the surface for subsequent coatings.
- Common Techniques:
- Abrasive Blasting (Bead, Sand, Grit): Creates a uniform, non-directional matte finish, removes loose powder particles, and can provide minor stress relief to the surface layer. Bead blasting is very common for AM parts.
- Tumbling / Vibratory Finishing: Parts are placed in a tub with media that vibrates or tumbles, smoothing sharp edges, deburring, and providing a more uniform surface finish over time. Good for batches of smaller parts.
- Obróbka CNC: Used selectively on critical features (e.g., mating surfaces, mounting holes, threaded holes) to achieve tight tolerances and very smooth surface finishes that are unattainable with other methods. Crucial for interfaces requiring precision.
- Polerowanie: Can achieve mirror-like finishes but is labor-intensive and typically reserved for aesthetic requirements, less common for functional antenna mounts.
- Coating / Anodizing:
- Cel: To enhance specific properties:
- Odporność na korozję: Essential for UAVs operating in humid, coastal, or marine environments. Anodizing is a common and effective electrochemical process for aluminum alloys, creating a hard, protective oxide layer. Various types (e.g., Type II, Type III hardcoat) offer different levels of protection and wear resistance.
- Odporność na zużycie: Hardcoat anodizing or specialized coatings can improve durability on surfaces subject to rubbing or contact.
- Electrical Insulation/Conductivity: Coatings can be chosen to either insulate or provide specific conductive properties if required by the design.
- Aesthetics/Identification: Anodizing allows for various colors. Coatings can match specific platform requirements (e.g., military color specifications).
- Consideration: The chosen coating process must be compatible with the base alloy and consider the part’s geometry.
- Cel: To enhance specific properties:
The specific combination and sequence of these metal AM post-processing steps depend on the material, design complexity, and functional requirements of the UAV GPS antenna mount. Properly executed surface finishing techniques and heat treatments are vital for ensuring the final component contributes positively to the overall drone component assembly and operational success.
Overcoming Hurdles: Common Challenges in 3D Printing Antenna Mounts and Expert Solutions
While metal additive manufacturing offers substantial advantages for producing UAV GPS antenna mounts, like any advanced manufacturing process, it presents potential challenges. Understanding these hurdles and knowing how experienced providers like Met3dp address them is key to ensuring successful outcomes and high-quality components. Many potential issues can be mitigated or eliminated through a combination of expert process control, high-quality materials, and robust DfAM practices.
Here are some common challenges encountered in metal AM and their solutions:
Common Metal AM Challenges & Solutions for UAV Antenna Mounts
Wyzwanie | Primary Cause(s) | Key Solution(s) Provided by Experienced Providers (e.g., Met3dp) | Keywords |
---|---|---|---|
Warping / Distortion | High thermal gradients during printing, leading to residual stress accumulation. | Optimized part orientation, robust support structure design, process simulation (predictive modeling), effective stress relief heat treatment post-print, build plate heating. | Warping prevention, Residual stress control |
Porosity (Gas / Lack-of-Fusion) | Trapped gas within powder particles, insufficient energy density (LoF), contamination. | Use of high-quality, low-gas powders (Met3dp’s advanced atomization helps), optimized & validated print parameters (laser power, speed, hatch spacing), inert gas atmosphere control (Argon/Nitrogen), potentially Hot Isostatic Pressing (HIP) for critical parts (densification under heat & pressure). | Porosity control metal AM, Dense parts 3D printing |
Cracking (Solidification / Hot Tearing) | Material susceptibility (some alloys), high thermal stresses during cooling phases. | Careful material selection (Scalmalloy® is designed for AM weldability), optimized scan strategies (e.g., island scanning), pre-heating build platform, precise parameter control, appropriate heat treatments. | Metal 3D printing defects, Crack prevention AM |
Support Removal Difficulty / Part Damage | Poor DfAM (inaccessible supports, excessive support density), improper removal technique. | DfAM focus: minimizing overhangs, designing accessible & breakaway supports, using specialized support types (e.g., conical, tree). Careful manual removal or precision machining for removal. | Support removal strategies, DfAM supports |
Incomplete Powder Removal | Complex internal geometries (lattices, channels) without adequate escape paths. | DfAM: Designing sufficient escape holes (≥2-5mm), smooth internal pathways. Thorough cleaning protocols (compressed air, vibration, potentially ultrasonic cleaning). | Powder removal AM, Design for Depowdering |
Surface Roughness / Stair-Stepping | Layer-based nature of AM, low-angle surfaces relative to build plate. | Optimize part orientation (avoid critical surfaces at low angles), use finer layer thickness (trade-off with build time), effective post-processing (bead blasting, tumbling, machining specific surfaces). | Additive manufacturing surface finish, Stair step effect |
Dimensional Inaccuracy | Cumulative effects of shrinkage, thermal stress, minor machine imprecisions. | Rigorous machine calibration, use of compensation factors in build preparation software, process simulation, post-print CMM inspection, targeted CNC machining for critical dimensions. | Dimensional accuracy standards, AM process control |
Export to Sheets
By leveraging deep expertise in materials science, process physics, DfAM, and post-processing, potential metal 3D printing defects can be proactively addressed. Partnering with a knowledgeable provider like Met3dp, who utilizes advanced equipment and high-quality, internally produced powders, significantly reduces the risk associated with these challenges. Effective troubleshooting additive manufacturing relies on this combination of technology, materials science, and practical experience, ensuring the delivery of reliable, high-performance UAV GPS antenna mounts that meet stringent industry requirements.
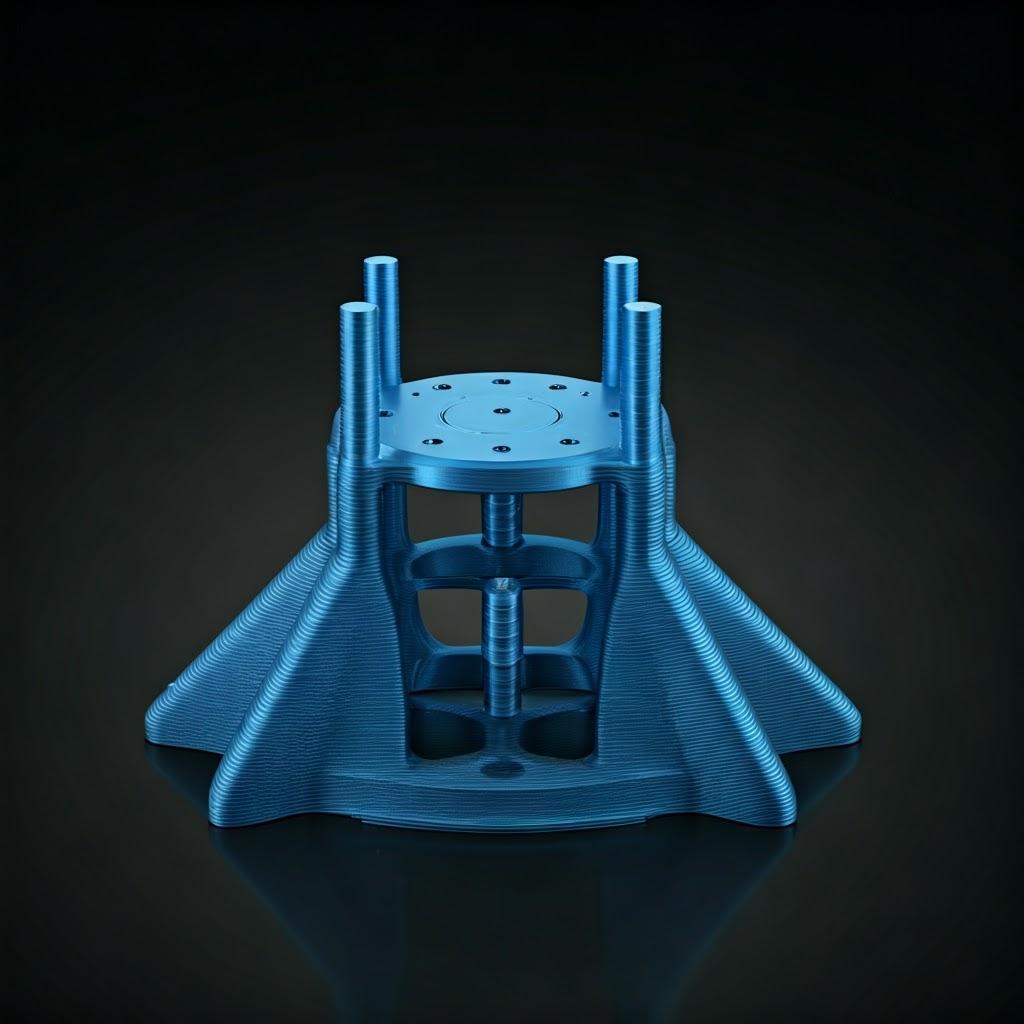
Supplier Selection: How to Choose the Right Metal 3D Printing Service Provider for UAV Components
Selecting the right manufacturing partner is as critical as the design and material choices when producing high-performance UAV GPS antenna mounts. For engineers and procurement managers, navigating the landscape of metal additive manufacturing service providers requires careful evaluation based on technical capabilities, quality assurance, and reliability. Choosing an unsuitable supplier can lead to delays, cost overruns, or components that fail to meet performance specifications. Partnering with a knowledgeable and well-equipped provider like Met3dp ensures access to expertise, advanced technology, and comprehensive support throughout the manufacturing process.
Here are key criteria for evaluating and selecting a metal AM service provider for demanding UAV components:
- Technical Expertise & Engineering Support:
- Assessment: Does the provider employ engineers with deep knowledge of metal AM processes (LPBF specifically for AlSi10Mg/Scalmalloy®), materials science, and DfAM principles? Do they understand the specific requirements of UAV applications (vibration, weight sensitivity, environmental factors)?
- Value: Look for partners who offer design consultation, feasibility studies, and DfAM guidance to optimize your antenna mount for performance and manufacturability. Met3dp’s team brings decades of collective expertise in metal AM.
- Material Capabilities & Quality Control:
- Assessment: Does the supplier offer the specific alloys required (e.g., AlSi10Mg, Scalmalloy®, relevant Ti alloys)? Crucially, what is the source and quality control process for their metal powders? Do they offer traceability?
- Value: Providers like Met3dp, who manufacture their own high-quality metal powders using advanced gas atomization and PREP technologies, offer significant advantages in material consistency, purity, sphericity, and flowability – directly impacting final part quality and mechanical properties. Rigorous incoming powder inspection and batch tracking are essential.
- Equipment & Technology:
- Assessment: What type, make, and model of metal AM printers do they operate? Are the machines well-maintained and calibrated? What is the available build volume?
- Value: State-of-the-art LPBF machines are crucial for processing demanding alloys and achieving tight tolerances. Met3dp utilizes printers delivering industry-leading print volume, accuracy, and reliability, suitable for mission-critical UAV parts.
- Quality Management System (QMS) & Certifications:
- Assessment: Does the provider have a robust QMS? Are they certified to relevant standards? ISO 9001 is a baseline; AS9100 certification is highly desirable (often required) for aerospace and defense supply chains. Inquire about their process controls, inspection procedures (e.g., CMM, non-destructive testing options), and documentation practices.
- Value: Certifications and a strong QMS demonstrate a commitment to quality, repeatability, and process control, vital for UAV component supplier qualification in regulated industries. Aerospace 3D printing certifications provide assurance.
- Post-Processing Capabilities:
- Assessment: Can the provider manage the entire required workflow, including critical post-processing steps like stress relief/heat treatment, precision CNC machining for critical features, surface finishing (blasting, tumbling), and coating/anodizing? Are these services performed in-house or managed through qualified partners?
- Value: A supplier offering comprehensive, end-to-end solutions simplifies the supply chain, ensures process integration, and takes responsibility for the final part quality. Met3dp provides comprehensive solutions spanning printers, powders, and application development, including post-processing coordination.
- Experience & Portfolio (Case Studies):
- Assessment: Can the provider demonstrate successful experience producing similar parts (e.g., lightweight structural components, UAV/aerospace parts, components in AlSi10Mg or Scalmalloy®)? Ask for case studies, examples, or references relevant to your application.
- Value: Proven experience reduces risk and indicates the provider understands the nuances of your specific component type and industry requirements.
- Lead Times & Capacity:
- Assessment: What are their quoted lead times for prototypes versus production runs? Do they have sufficient machine capacity and workforce to meet your project deadlines and potential volume requirements? How transparent are they about scheduling?
- Value: Reliable and predictable lead times are crucial for project planning and meeting market demands. Look for providers with efficient workflow management.
- Customer Service & Communication:
- Assessment: How responsive is the provider to inquiries? Is communication clear, consistent, and technically proficient? Do they provide a dedicated point of contact for project management?
- Value: Strong communication and responsive customer service are essential for a smooth collaboration, especially on complex projects.
Thorough metal AM service bureau evaluation based on these criteria is paramount for successful B2B procurement AM. By prioritizing technical competence, quality assurance, and proven experience, companies can confidently select reliable manufacturers like Met3dp for their critical UAV component needs.
Understanding Investment: Cost Factors and Lead Time for Manufacturing UAV Antenna Mounts
Budget and schedule are critical considerations in any engineering project. Understanding the factors that influence the cost and lead time of metal 3D printed UAV GPS antenna mounts is essential for accurate project planning and procurement decisions. Pricing for additive manufacturing differs from traditional methods, primarily driven by material consumption, machine time, and post-processing complexity rather than tooling amortization.
Key Cost Factors:
- Material Type and Volume:
- Koszt proszku: High-performance alloys like Scalmalloy® are significantly more expensive per kilogram than standard alloys like AlSi10Mg. Titanium alloys are generally more costly than aluminum.
- Objętość: The total volume of the part plus the volume of necessary support structures directly impacts material consumption and cost. Efficient design (DfAM, topology optimization) minimizes material usage.
- Machine Time (Build Time):
- Calculation: This is often the largest cost component, calculated based on an hourly rate for the sophisticated AM machine.
- Influences: Primarily determined by the total height of the build (number of layers), the volume of material being fused in each layer, and the complexity of the laser scanning path. Nesting multiple parts efficiently within a single build can reduce the machine time attributed to each part.
- Design Complexity & Preparation:
- While AM handles complexity well, highly intricate designs might require more sophisticated support strategies or longer slicing/preparation times. If significant DfAM work or engineering support is needed upfront, this adds to the initial cost.
- Support Structure Requirements:
- Materiał: The volume of material used for supports adds to cost.
- Removal Labor: Complex or difficult-to-access supports require more manual labor or machining time for removal, increasing cost.
- Wymagania dotyczące przetwarzania końcowego:
- Uderzenie: Each post-processing step (heat treatment, machining, blasting, tumbling, coating, etc.) adds significant cost due to specialized equipment, energy consumption, and skilled labor. Precision machining of multiple features or advanced coatings can substantially increase the final AM cost per part.
- Koszty pracy:
- Includes engineering review, build preparation, machine operation, part breakout, support removal, finishing, inspection, and quality assurance documentation.
- Quality Assurance & Inspection:
- Standard dimensional checks are typical. More rigorous inspection (e.g., CMM reports for multiple features, non-destructive testing like CT scanning for internal integrity validation) adds cost but may be necessary for critical applications.
- Ilość zamówienia:
- AM avoids high tooling costs, making it ideal for prototypes and low volumes. However, setup costs (build file preparation, machine setup/cleaning) still exist. Modest economies of scale can be achieved with larger batches through optimized build nesting and batch post-processing, but the per-part cost reduction is generally less dramatic than with injection molding.
Key Lead Time Factors:
- Design Review & Build Preparation: Initial file checks, potential DfAM consultation, support generation, slicing, and build layout planning (typically 1-5 business days).
- Machine Queue & Print Time: Waiting for an available machine that matches the material and size requirements. Actual printing can take anywhere from several hours for small parts to multiple days for large parts or full build plates.
- Cooling Time: Controlled cooling of the build chamber post-printing (several hours to overnight).
- Przetwarzanie końcowe: This is often the most variable and potentially longest phase. Heat treatment cycles can take 1-2 days. Support removal and basic finishing might take another day. CNC machining depends on complexity and machine shop queue times (days to weeks). Coating/anodizing often involves external vendors and adds significant time (1-3 weeks is common).
- Inspection & Quality Control: Performing required measurements and completing documentation (1-2 days).
- Wysyłka: Transit time to the customer’s location.
Typical Lead Time Ranges:
- Prototypy: Often 1 to 3 weeks, depending heavily on complexity and post-processing needs.
- Low Volume Production: Typically 3 to 6 weeks, influenced by batch size, machine availability, and extensive post-processing requirements.
Providing a detailed specification (CAD model, material, tolerances, finishes, post-processing) allows providers like Met3dp to deliver accurate quotes for both cost and lead time, enabling informed decisions for UAV component production time and budgeting in your metal 3D printing cost analysis.
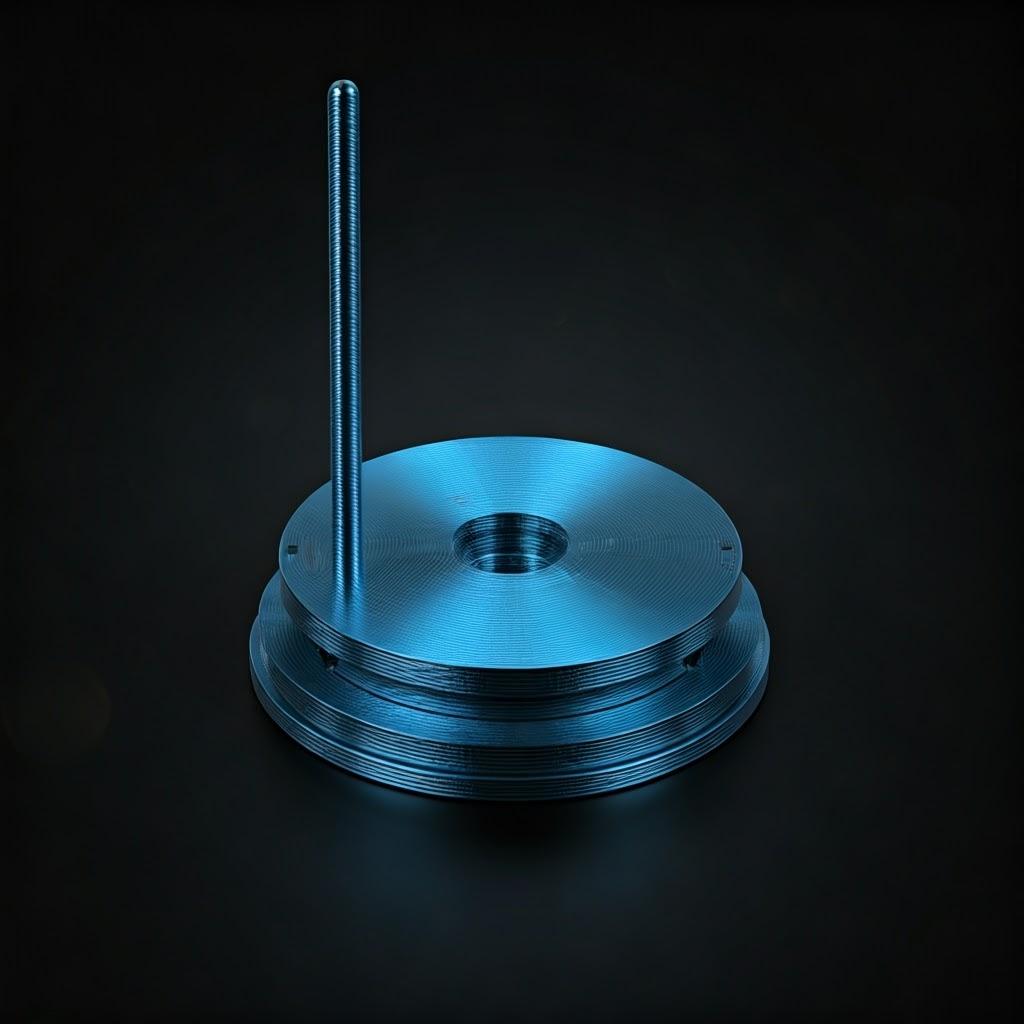
Frequently Asked Questions (FAQ) about 3D Printed UAV GPS Antenna Mounts
Here are answers to some common questions regarding the use of metal additive manufacturing for UAV GPS antenna mounts:
Q1: How much weight can realistically be saved using metal AM for a GPS mount? A: Significant weight savings are achievable, often ranging from 30% to over 60% compared to conventionally machined or molded parts designed for similar strength. The actual reduction depends heavily on the original design, the degree of optimization applied (topology optimization, lattice structures), and the material chosen (e.g., Scalmalloy® enables more aggressive lightweighting than AlSi10Mg). These lightweight mount benefits directly translate to improved drone performance.
Q2: Are 3D printed metal mounts (AlSi10Mg/Scalmalloy®) strong and durable enough for demanding UAV operations? A: Absolutely. When designed correctly, manufactured with quality materials and processes, and subjected to appropriate post-processing (especially heat treatment), metal AM parts made from AlSi10Mg and Scalmalloy® exhibit excellent mechanical properties. They offer high strength, stiffness, and fatigue resistance, making them highly durable and suitable for handling the demanding vibration environments (drone vibration resistance) and operational loads experienced by UAVs. AM material durability is a key advantage.
Q3: What’s the main performance difference between AlSi10Mg and Scalmalloy® for an antenna mount? A: The primary difference lies in the strength-to-weight ratio and fatigue performance. Scalmalloy® offers significantly higher specific strength (strength per unit density) and superior fatigue resistance compared to AlSi10Mg. This allows for designing parts that are either much lighter for the same strength requirement or significantly stronger/more durable at a similar weight. AlSi10Mg provides a very capable and more cost-effective balance of properties suitable for many applications, while Scalmalloy® excels in high-performance or weight-critical scenarios.
Q4: What information does Met3dp need to provide a quote for a 3D printed antenna mount? A: To provide an accurate quote, Met3dp typically requires the following information:
- Model 3D CAD: Preferably in STEP format (though STL is also common).
- Wybór materiału: Specify the desired alloy (e.g., AlSi10Mg, Scalmalloy®, or discuss options).
- Ilość zamówienia: Number of parts required.
- Tolerances: Indicate any critical dimensions and their required tolerances.
- Wykończenie powierzchni: Specify desired finish (e.g., as-built, bead blasted, specific Ra value for machined surfaces).
- Przetwarzanie końcowe: Detail all required steps (e.g., specific heat treatment cycle like T6, specific machining operations, anodizing type/color).
- Application Details (Optional but helpful): Understanding the intended use and load conditions can help Met3dp provide DfAM recommendations if desired. The best first step for getting a quote for 3D printing is to contact Met3dp directly through our website or sales channels to discuss your specific requirements.
Conclusion: Elevating Drone Performance with Advanced Metal 3D Printed Antenna Mounts from Met3dp
The evolution of Unmanned Aerial Vehicles hinges on continuous innovation in component design and manufacturing. As demonstrated, metal additive manufacturing represents a significant leap forward for producing critical components like GPS antenna mounts. By leveraging the power of AM, engineers can overcome the limitations of traditional methods, unlocking unprecedented levels of lightweighting, geometric complexity, and performance optimization.
The ability to utilize advanced aluminum alloys such as the versatile AlSi10Mg and the ultra-high-strength Scalmalloy® allows for the creation of antenna mounts that are not only significantly lighter – contributing to extended flight times and increased payload capacities – but also more durable and reliable, ensuring signal integrity even in high-vibration environments. Techniques like topology optimization and lattice structure integration, enabled by AM, are pushing the boundaries of structural efficiency, directly impacting the performance enhancement drones can achieve.
Metal AM is undeniably shaping the future of drone manufacturing, enabling the production of highly customized, complex, and efficient components that were previously impossible or impractical to create. It facilitates rapid prototyping, accelerates development cycles, and supports the trend towards more integrated and sophisticated UAV designs.
As a leader in metal additive manufacturing solutions, Met3dp stands at the forefront of this technological advancement. With our industry-leading SEBM printers, advanced in-house production of high-quality metal powders using gas atomization and PREP technologies, and comprehensive expertise spanning design, manufacturing, and post-processing, we offer end-to-end solutions for your most demanding UAV component needs. We partner with organizations in aerospace, defense, automotive, medical, and industrial sectors to deliver cutting-edge custom metal components and accelerate their adoption of digital manufacturing.
If you are looking to elevate the performance and reliability of your UAV platforms through optimized, lightweight, and robust GPS antenna mounts or other critical components, we encourage you to explore the possibilities with Met3dp. Contact Met3dp today to discuss how our Met3dp capabilities oraz advanced UAV solutions can power your organization’s additive manufacturing goals and give you a competitive edge.
Udostępnij
MET3DP Technology Co., LTD jest wiodącym dostawcą rozwiązań w zakresie produkcji addytywnej z siedzibą w Qingdao w Chinach. Nasza firma specjalizuje się w sprzęcie do druku 3D i wysokowydajnych proszkach metali do zastosowań przemysłowych.
Zapytaj o najlepszą cenę i spersonalizowane rozwiązanie dla Twojej firmy!
Powiązane artykuły
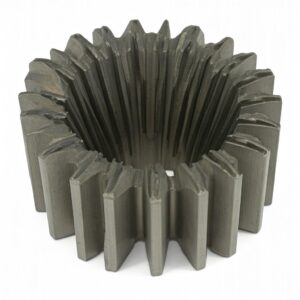
Wysokowydajne segmenty łopatek dysz: Rewolucja w wydajności turbin dzięki drukowi 3D w metalu
Czytaj więcej "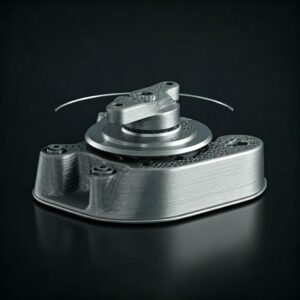
Drukowane w 3D mocowania dla samochodowych czujników radarowych: Precyzja i wydajność
Czytaj więcej "Informacje o Met3DP
Ostatnia aktualizacja
Nasz produkt
KONTAKT
Masz pytania? Wyślij nam wiadomość teraz! Po otrzymaniu wiadomości obsłużymy Twoją prośbę całym zespołem.
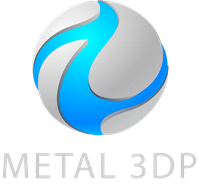
Proszki metali do druku 3D i produkcji addytywnej