3D Printing Hydraulic Valve Blocks for Fluid Control
Spis treści
Introduction to 3D Printed Hydraulic Valve Blocks
In the realm of fluid power, hydraulic valve blocks serve as critical components, orchestrating the flow of hydraulic fluid to control the movement and force of machinery. Traditionally manufactured through subtractive methods like machining, these blocks are now undergoing a transformative shift with the advent of metal 3D printing, also known as metal additive manufacturing. This innovative technology offers unprecedented design freedom, the ability to create complex internal channels, and the potential for significant performance enhancements. At Metal3DP, we are at the forefront of this revolution, providing cutting-edge metal Drukowanie 3D solutions that empower industries to reimagine hydraulic system design and functionality. Our expertise in both advanced metal powders and high-performance printing equipment ensures the production of hydraulic valve blocks that meet the most demanding specifications.
Understanding the Applications of Hydraulic Valve Blocks
Hydraulic valve blocks are indispensable across a diverse range of industries, each with specific requirements and operational demands. Their primary function is to direct hydraulic fluid to various actuators, such as cylinders and motors, thereby controlling the motion and power of machinery.
- Aerospace: In aerospace applications, hydraulic valve blocks are crucial for controlling flight surfaces, landing gear, and actuation systems. The need for lightweight yet robust components makes metal 3D printing an ideal manufacturing solution.
- Motoryzacja: Within the automotive sector, these blocks are integral to power steering systems, braking mechanisms, and transmission control. The ability to optimize designs for space efficiency and performance is a key advantage of 3D printing.
- Medyczne: Medical equipment, such as surgical robots and patient positioning systems, relies on precise hydraulic control. Metal 3D printing enables the creation of compact and intricate valve blocks tailored to specific medical device requirements.
- Produkcja przemysłowa: Across various industrial applications, including construction equipment, agricultural machinery, and manufacturing robots, hydraulic valve blocks are essential for controlling heavy-duty operations. The durability and customizability offered by metal 3D printing are highly beneficial in these demanding environments.
Metal3DP understands the unique needs of each industry and offers tailored metal 3D printing services to produce hydraulic valve blocks that meet stringent performance and reliability standards. Our range of high-quality metal powders and advanced printing technologies allows us to cater to the specific demands of aerospace, automotive, medical, and industrial manufacturing sectors. You can explore our metal 3D printing capabilities further on our website.
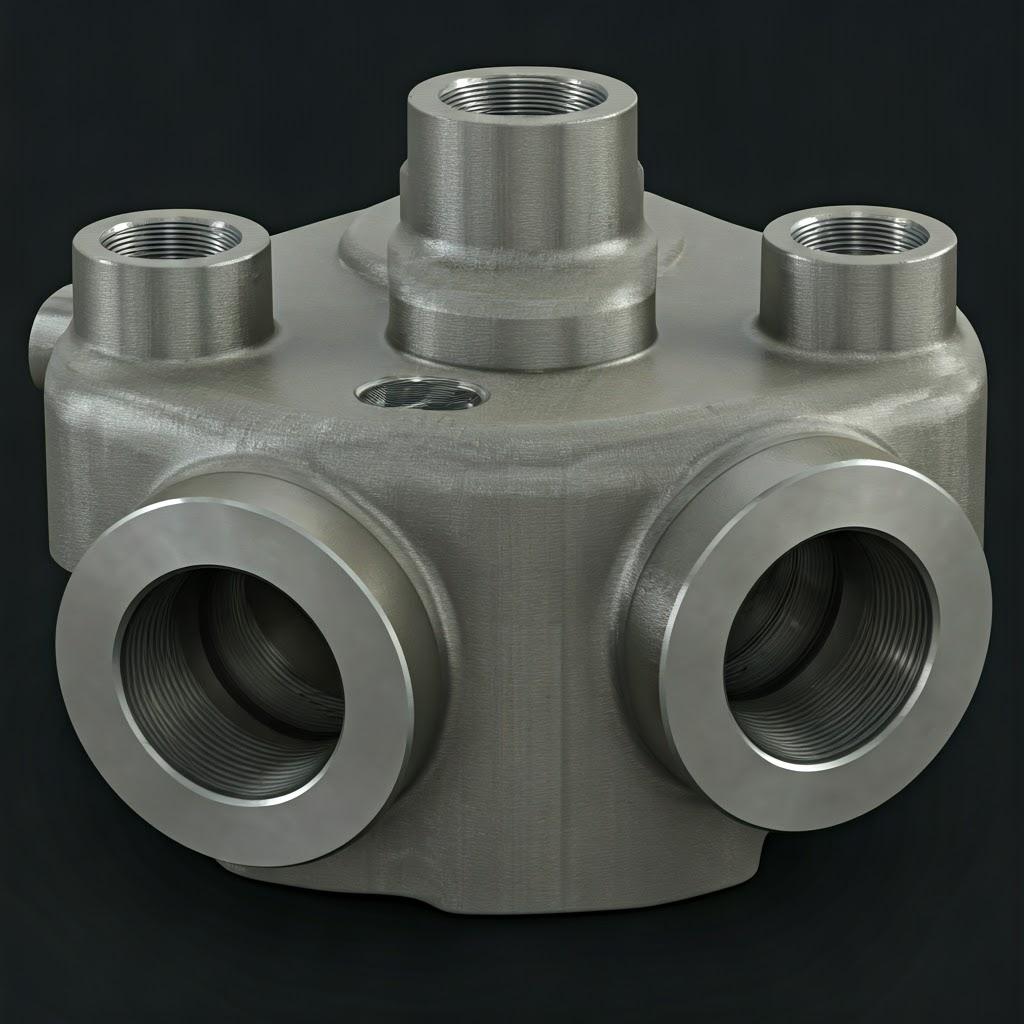
Advantages of Metal 3D Printing for Hydraulic Valve Blocks
Opting for metal 3D printing over traditional manufacturing methods for hydraulic valve blocks presents a multitude of compelling advantages:
- Swoboda projektowania i złożoność: Additive manufacturing liberates engineers from the constraints of traditional machining, enabling the creation of intricate internal geometries, optimized flow paths, and integrated functionalities within the valve block. This can lead to improved hydraulic efficiency and reduced system complexity.
- Redukcja wagi: By optimizing designs and utilizing advanced materials, metal 3D printing can produce lighter hydraulic valve blocks without compromising structural integrity. This is particularly beneficial in weight-sensitive applications like aerospace and automotive.
- Zredukowany montaż: Integrating multiple components into a single 3D-printed part eliminates the need for assembly, reducing manufacturing time, costs, and potential failure points.
- Szybkie prototypowanie i iteracja: Metal 3D printing facilitates rapid prototyping, allowing for quick design iterations and testing. This accelerates the development cycle and enables faster time-to-market.
- Personalizacja i produkcja na żądanie: Additive manufacturing enables the production of customized hydraulic valve blocks in small to medium volumes, catering to specific application requirements without the need for expensive tooling.
- Wydajność materiałowa: Metal 3D printing can significantly reduce material waste compared to subtractive methods, as material is only added where needed.
Metal3DP‘s commitment to innovation in metal additive manufacturing empowers our clients to leverage these advantages. Our industry-leading print volume and accuracy allow for the production of complex hydraulic valve blocks with exceptional quality. Discover more about our metal 3D printing services.
Material Selection: 316L, IN625, and AlSi10Mg for Hydraulic Valve Blocks
The choice of metal powder is paramount in determining the final properties and performance of a 3D-printed hydraulic valve block. Metal3DP offers a range of high-quality metal powders, including 316L stainless steel, Inconel 625 (IN625), and Aluminum Silicon Magnesium (AlSi10Mg), each possessing unique characteristics that make them suitable for specific hydraulic applications.
- Stal nierdzewna 316L: This austenitic stainless steel is renowned for its excellent corrosion resistance, high strength, and good ductility. It is a versatile material suitable for a wide range of hydraulic applications, particularly those involving exposure to corrosive fluids or environments. | Property | Value | | :—————- | :————————————- | | Tensile Strength | ~550-650 MPa | | Yield Strength | ~200-300 MPa | | Elongation at Break | ~40-50% | | Corrosion Resistance | Excellent | | Applications | General hydraulic systems, marine, chemical processing |
- IN625 (Inconel 625): This nickel-chromium superalloy exhibits exceptional high-temperature strength, creep resistance, and corrosion resistance, even in harsh environments. It is ideal for hydraulic systems operating under high pressures and extreme temperatures. | Property | Value | | :—————- | :————————————- | | Tensile Strength | ~830-1140 MPa | | Yield Strength | ~410-760 MPa | | Elongation at Break | ~30-55% | | Corrosion Resistance | Excellent, high-temperature corrosion resistance | | Applications | High-pressure hydraulics, aerospace, chemical processing |
- AlSi10Mg (Aluminum Silicon Magnesium): This aluminum alloy offers a good strength-to-weight ratio and excellent thermal conductivity. It is well-suited for hydraulic applications where weight reduction is critical, such as in automotive and aerospace industries. | Property | Value | | :—————- | :————————————- | | Tensile Strength | ~350-450 MPa | | Yield Strength | ~250-300 MPa | | Elongation at Break | ~5-10% | | Corrosion Resistance | Good | | Applications | Lightweight hydraulic systems, automotive, aerospace |
Metal3DP‘s advanced powder making system ensures that our 316L, IN625, and AlSi10Mg powders possess high sphericity and good flowability, crucial for achieving dense, high-quality 3D-printed hydraulic valve blocks with superior mechanical properties. Learn more about our high-quality metal powders.
Design Optimization for Additive Manufacturing of Valve Blocks
Designing hydraulic valve blocks for metal 3D printing requires a shift in mindset compared to traditional manufacturing. The layer-by-layer additive process offers unique opportunities for optimization, enabling the creation of geometries that enhance performance and reduce material usage.
- Internal Channel Design: One of the most significant advantages of metal 3D printing is the ability to create complex internal channels with optimized flow paths. Sharp corners and abrupt changes in direction can be replaced with smooth curves and gradual transitions, minimizing pressure drops and improving hydraulic efficiency. Consider incorporating lattice structures within non-critical areas to reduce weight without sacrificing structural integrity.
- Optymalizacja topologii: Utilize topology optimization software to identify and remove material from low-stress regions of the valve block. This can lead to significant weight reductions and improved material efficiency while maintaining the required structural performance.
- Integration of Features: Metal 3D printing allows for the integration of multiple components into a single part. For hydraulic valve blocks, this could include integrating mounting features, sensor housings, or even simplified valve elements directly into the main block. This reduces the need for assembly and potential leak points.
- Wall Thickness and Support Structures: Carefully consider wall thicknesses to ensure structural integrity under operating pressures while minimizing material usage and print time. Design for minimal support structures to reduce post-processing effort and improve surface finish. Consider self-supporting angles where possible.
- Orientation and Build Strategy: The orientation of the part during the printing process can significantly impact surface finish, dimensional accuracy, and the need for support structures. Optimize the build orientation to minimize overhangs and critical surface roughness.
Przy Metal3DP, our application development services provide expert guidance on designing for metal additive manufacturing. We work closely with our clients to optimize their hydraulic valve block designs for performance, manufacturability, and cost-effectiveness. Our team leverages years of experience to help you unlock the full potential of metal 3D printing.
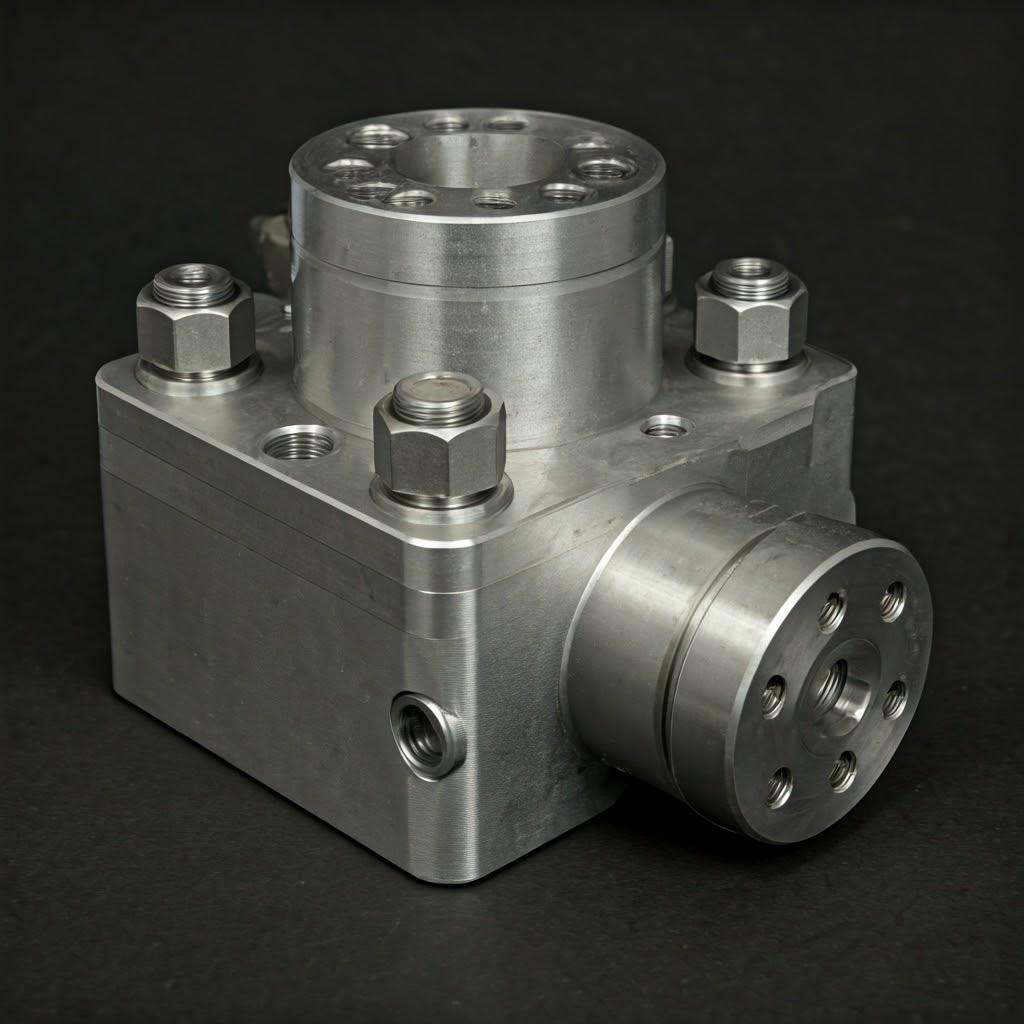
Achieving Precision: Tolerance, Surface Finish, and Dimensional Accuracy in 3D Printed Valves
The precision achievable with metal 3D printing has advanced significantly, making it a viable option for demanding hydraulic applications. However, understanding the factors influencing tolerance, surface finish, and dimensional accuracy is crucial for successful outcomes.
- Tolerance: Metal 3D printing processes can achieve tolerances ranging from ±0.1 mm to ±0.05 mm or even tighter in specific cases and with post-processing. Factors influencing tolerance include the printing technology used (e.g., SLM, DMLS, EBM), material properties, part geometry, and build orientation.
- Wykończenie powierzchni: The as-printed surface finish in metal 3D printing typically ranges from Ra 5-20 µm, depending on the powder size, layer thickness, and build orientation. For hydraulic applications requiring smoother surfaces to minimize friction and wear, post-processing techniques like machining, polishing, or abrasive flow machining can be employed.
- Dokładność wymiarowa: Achieving high dimensional accuracy requires careful calibration of the 3D printer, optimized process parameters, and consideration of material shrinkage during solidification. Simulation tools can help predict and compensate for potential deviations.
Metal3DP‘s state-of-the-art SEBM printers are engineered for industry-leading accuracy and reliability. Our expertise in process control and material science ensures that we can produce hydraulic valve blocks with tight tolerances and consistent dimensional accuracy. We also offer a range of post-processing services to meet specific surface finish requirements.
Post-Processing Techniques for Hydraulic Valve Blocks
While metal 3D printing offers near-net-shape manufacturing, post-processing steps are often necessary to achieve the final desired properties and finish for hydraulic valve blocks.
- Usuwanie wsparcia: Support structures, essential for printing complex geometries, need to be carefully removed after the build. This can involve manual breaking, machining, or chemical dissolution, depending on the support material and part geometry.
- Obróbka cieplna: Heat treatment processes, such as stress relieving, annealing, or hardening, are often applied to improve the mechanical properties of the 3D-printed metal, such as strength, hardness, and ductility. The specific heat treatment cycle depends on the material and application requirements.
- Obróbka CNC: For critical surfaces requiring very tight tolerances or specific features that are difficult to achieve directly through 3D printing, CNC machining can be used as a secondary process. This is common for sealing surfaces and threaded holes in hydraulic valve blocks.
- Wykończenie powierzchni: Techniques like polishing, grinding, shot peening, and abrasive flow machining can be used to improve the surface finish of the hydraulic valve block, reducing friction, wear, and the risk of leakage.
- Coating and Surface Treatments: Depending on the application environment, coatings such as hard chrome plating, nickel plating, or anodizing may be applied to enhance corrosion resistance, wear resistance, or other surface properties.
- Pressure Testing: After post-processing, hydraulic valve blocks typically undergo rigorous pressure testing to ensure they can withstand the operating pressures without leakage or failure.
Metal3DP provides comprehensive solutions that include not only high-quality 3D printing but also a range of post-processing services tailored to the specific needs of hydraulic valve blocks. Our experienced team ensures that all post-processing steps are performed to the highest standards, resulting in functional and reliable components. You can find more information about our product offerings on our website.
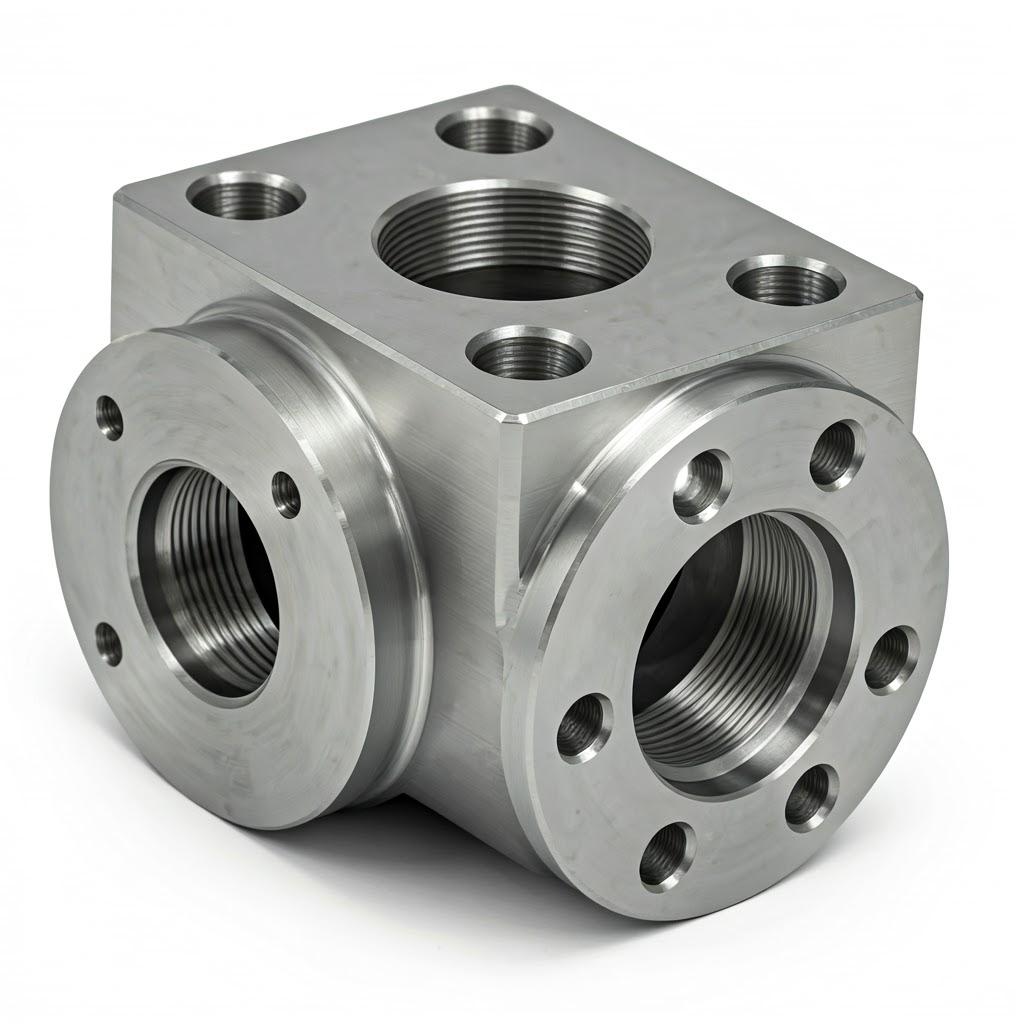
Overcoming Common Challenges in Metal 3D Printing of Valves
While metal 3D printing offers numerous advantages, there are also potential challenges that need to be addressed to ensure successful fabrication of hydraulic valve blocks.
- Wypaczenia i zniekształcenia: Thermal stresses during the printing process can lead to warping or distortion of the part, particularly for large or complex geometries. Optimizing the build orientation, using support structures, and controlling the printing parameters can mitigate these issues.
- Support Removal Damage: Improper removal of support structures can damage the surface of the part. Careful design of support structures and the use of appropriate removal techniques are essential.
- Porowatość: Internal porosity can compromise the mechanical strength and leak-tightness of hydraulic components. Optimizing printing parameters, material selection, and powder quality are crucial for minimizing porosity. Metal3DP‘s high-quality metal powders, produced using advanced gas atomization and PREP technologies, are designed to minimize porosity.
- Chropowatość powierzchni: The as-printed surface roughness may not be suitable for all hydraulic sealing applications. Post-processing techniques are often required to achieve the desired surface finish.
- Rozważania dotyczące kosztów: While metal 3D printing can be cost-effective for certain applications, the initial investment in equipment and materials, as well as the cost of post-processing, needs to be carefully considered.
Metal3DP has decades of collective expertise in metal additive manufacturing, enabling us to effectively address these common challenges. Our comprehensive solutions, spanning advanced printers, high-quality powders, and application development services, are designed to help our partners overcome these hurdles and successfully implement 3D printing for their hydraulic valve block needs.
Selecting a Reliable Metal 3D Printing Service Provider
Choosing the right metal 3D printing service provider is crucial for obtaining high-quality hydraulic valve blocks that meet your specific requirements. Here are key factors to consider when evaluating potential suppliers:
- Material Capabilities: Ensure the provider offers the specific metal powders required for your application (e.g., 316L, IN625, AlSi10Mg) and has experience processing these materials for hydraulic components. Metal3DP boasts a wide range of high-quality metal powders optimized for various applications.
- Printing Technology and Equipment: Understand the printing technologies and equipment the provider utilizes. Different technologies (e.g., SLM, DMLS, EBM) offer varying levels of precision, build volume, and material compatibility. Metal3DP employs industry-leading SEBM printers known for their accuracy and reliability. You can learn more about our printing methods on our website.
- Quality Control and Certifications: Inquire about the provider’s quality control processes, including material testing, dimensional inspection, and non-destructive testing. Relevant certifications (e.g., ISO 9001, AS9100 for aerospace) indicate a commitment to quality.
- Design and Engineering Support: A reliable provider should offer design and engineering support to optimize your hydraulic valve block for additive manufacturing, including material selection, design for AM, and simulation services. Metal3DP provides comprehensive application development services to assist you throughout the design and production process.
- Możliwości obróbki końcowej: Determine if the provider offers the necessary post-processing services, such as support removal, heat treatment, CNC machining, and surface finishing, to meet your final part specifications. Metal3DP offers a range of post-processing services to deliver готовые к использованию hydraulic valve blocks.
- Lead Times and Production Capacity: Evaluate the provider’s lead times and production capacity to ensure they can meet your project timelines and volume requirements.
- Communication and Customer Support: Clear and responsive communication is essential for a successful partnership. Assess the provider’s responsiveness and willingness to understand your specific needs.
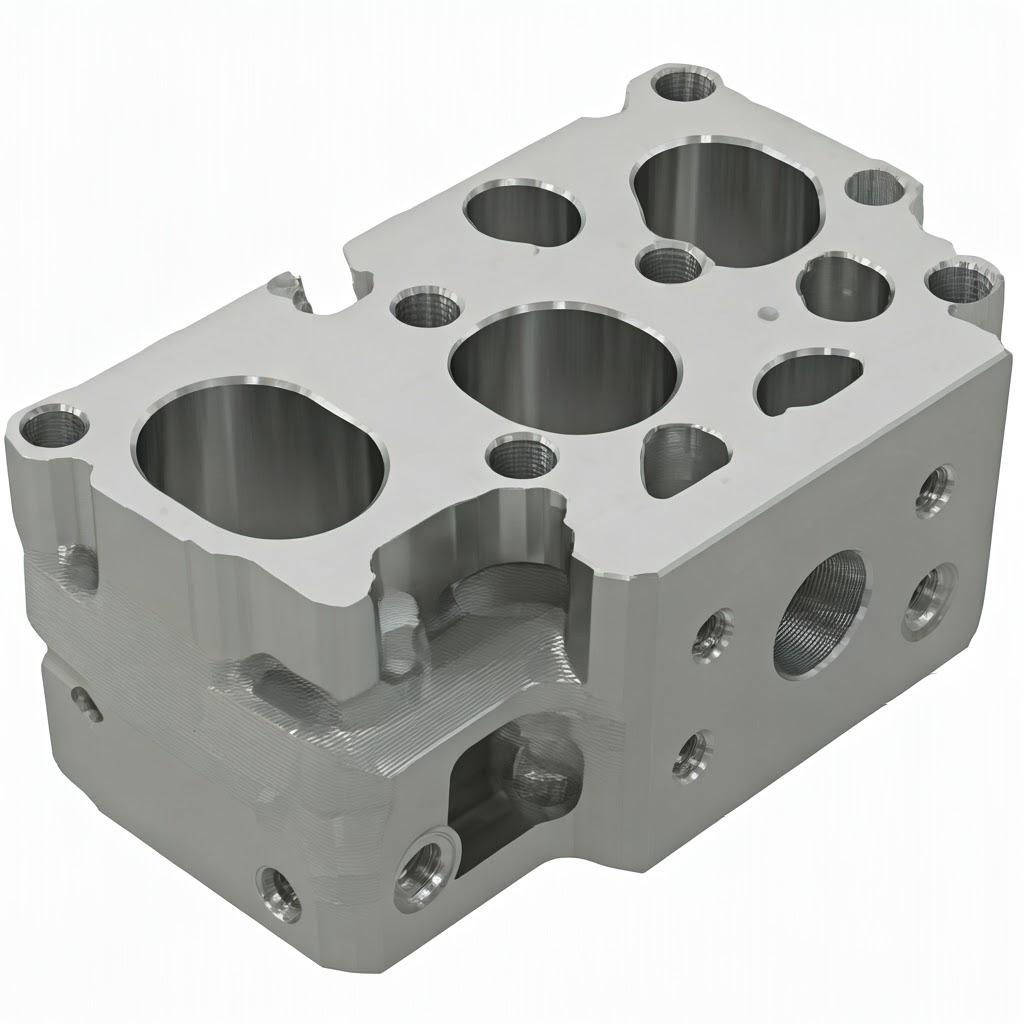
Cost Analysis and Lead Time for 3D Printed Hydraulic Valve Blocks
The cost and lead time for metal 3D printed hydraulic valve blocks are influenced by several factors:
- Koszty materiałowe: The type and quantity of metal powder used significantly impact the overall cost. Alloys like IN625 are typically more expensive than stainless steel or aluminum alloys.
- Build Volume and Complexity: Larger and more complex parts require more material and longer print times, increasing costs.
- Struktury wsparcia: The volume and complexity of support structures affect material usage and post-processing time, influencing the final cost.
- Wymagania dotyczące przetwarzania końcowego: Additional post-processing steps, such as CNC machining, specialized surface finishes, or coatings, will add to the overall cost and lead time.
- Wielkość produkcji: While 3D printing can be cost-effective for low to medium volumes and customized parts, higher volumes may benefit from economies of scale with traditional manufacturing methods.
- Machine Time and Labor: The duration of the printing process and the labor involved in pre-processing, printing, and post-processing contribute to the overall cost.
- Service Provider’s Pricing Structure: Different service providers have varying pricing models based on factors like machine hourly rates, material markups, and labor costs.
Lead times can vary depending on the complexity of the part, the material availability, the service provider’s capacity, and the required post-processing. It’s essential to discuss lead times upfront with your chosen provider. Metal3DP is committed to providing transparent cost estimates and realistic lead times for your metal 3D printing projects. Contact us to explore how our capabilities can power your organization’s additive manufacturing goals.
Często zadawane pytania (FAQ)
- Q: Can metal 3D printed hydraulic valve blocks withstand high pressures?
- A: Yes, when the design is optimized for pressure loads, the correct material is selected, and proper post-processing is performed (including heat treatment and pressure testing), metal 3D printed hydraulic valve blocks can withstand high operating pressures. Materials like 316L and IN625 are well-suited for high-pressure applications.
- Q: What is the typical turnaround time for a 3D printed hydraulic valve block prototype?
- A: The turnaround time for a prototype can vary depending on the complexity and size of the part, as well as the service provider’s current workload. Typically, it can range from a few days to a couple of weeks. Metal3DP strives to provide efficient turnaround times for prototypes to accelerate your development process.
- Q: Is metal 3D printing cost-effective for mass production of hydraulic valve blocks?
- A: Metal 3D printing is generally most cost-effective for low to medium volumes, complex geometries, and customized parts. For very high production volumes, traditional manufacturing methods may offer better economies of scale. However, the benefits of design freedom and reduced assembly can still make 3D printing a competitive option in many cases.
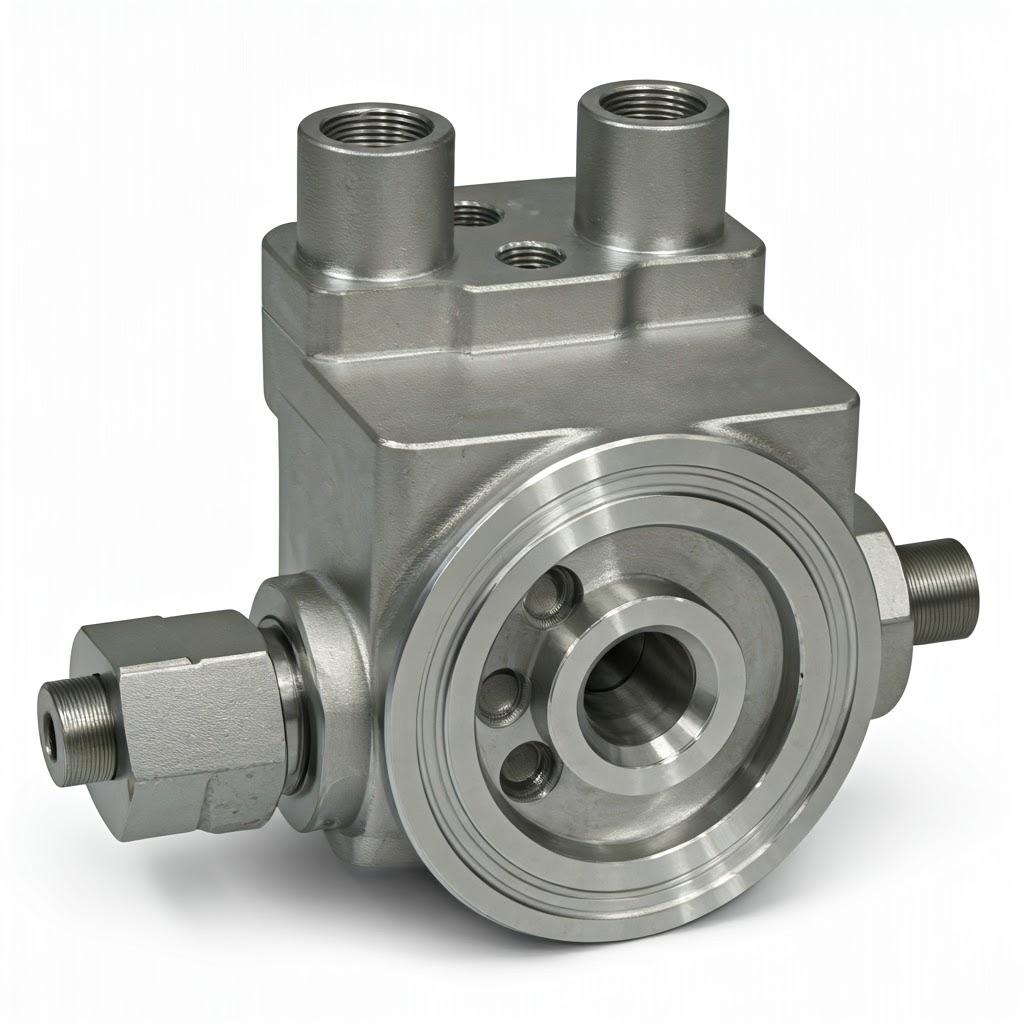
Conclusion: The Future of Hydraulic Valve Blocks with Metal 3D Printing
Metal 3D printing is revolutionizing the design and manufacturing of hydraulic valve blocks, offering unprecedented opportunities for enhanced performance, weight reduction, and design complexity. As industries like aerospace, automotive, medical, and industrial manufacturing continue to demand more efficient and customized hydraulic systems, the role of metal additive manufacturing will only become more significant.
Metal3DP is proud to be a leading provider of metal 3D printing solutions, offering advanced equipment, high-quality metal powders, and comprehensive application development services. Our commitment to innovation and quality empowers our clients to harness the full potential of metal additive manufacturing for their hydraulic valve block needs, driving progress and enabling the next generation of fluid power systems. We invite you to explore the possibilities of metal 3D printing with Metal3DP and discover how our expertise can help you achieve your manufacturing goals. Visit our about us page to learn more about our company and our commitment to advancing metal additive manufacturing.
Udostępnij
MET3DP Technology Co., LTD jest wiodącym dostawcą rozwiązań w zakresie produkcji addytywnej z siedzibą w Qingdao w Chinach. Nasza firma specjalizuje się w sprzęcie do druku 3D i wysokowydajnych proszkach metali do zastosowań przemysłowych.
Zapytaj o najlepszą cenę i spersonalizowane rozwiązanie dla Twojej firmy!
Powiązane artykuły
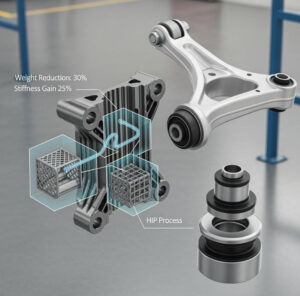
Metal 3D Printed Subframe Connection Mounts and Blocks for EV and Motorsport Chassis
Czytaj więcej "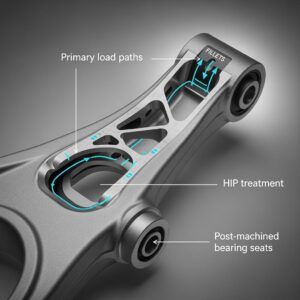
Metal 3D Printing for U.S. Automotive Lightweight Structural Brackets and Suspension Components
Czytaj więcej "Informacje o Met3DP
Ostatnia aktualizacja
Nasz produkt
KONTAKT
Masz pytania? Wyślij nam wiadomość teraz! Po otrzymaniu wiadomości obsłużymy Twoją prośbę całym zespołem.