Proszek do formowania wtryskowego
Spis treści
Proszek nadający się do formowania wtryskowego odnosi się do rodzaju materiału wsadowego stosowanego w formowaniu wtryskowym proszków, przemysłowym procesie produkcji złożonych i precyzyjnych części metalowych. Proszek ten jest mieszaniną drobnych proszków metalowych i spoiw polimerowych, które mogą być formowane wtryskowo w złożone części o kształcie siatki w dużych ilościach.
Zalety stosowania proszku do formowania wtryskowego
Przewaga | Opis | Korzyści |
---|---|---|
Geometrie złożone: IMP pozwala na tworzenie skomplikowanych kształtów z drobnymi elementami, które są trudne lub niemożliwe do osiągnięcia przy użyciu tradycyjnych technik formowania wtryskowego. Ta swoboda projektowania otwiera drzwi dla innowacyjnych komponentów w różnych branżach. | W przeciwieństwie do tradycyjnych materiałów formierskich, takich jak stopione tworzywa sztuczne, IMP wykorzystuje system spoiwa, który utrzymuje cząsteczki proszku razem podczas procesu formowania. Umożliwia to tworzenie części z wewnętrznymi kanałami, podcięciami i innymi złożonymi geometriami. | |
Wydajność materiałowa: IMP promuje produkcję w kształcie zbliżonym do siatki, minimalizując straty materiału w porównaniu z technikami subtraktywnymi, takimi jak obróbka skrawaniem. Jest to szczególnie korzystne w przypadku drogich lub wysokowydajnych materiałów. | Precyzyjna kontrola nad dystrybucją proszku podczas formowania wtryskowego minimalizuje nadmierne zużycie materiału. Dodatkowo, w przeciwieństwie do tradycyjnych procesów, które generują odpady podczas prób, IMP pozwala na szybsze iteracje projektu przy minimalnych stratach materiału. | |
Szeroki wybór materiałów: IMP oferuje szerszy zakres opcji materiałowych w porównaniu do tradycyjnego formowania wtryskowego. Ta wszechstronność pozwala na tworzenie części o specyficznych właściwościach dostosowanych do danego zastosowania. | Oprócz standardowych polimerów stosowanych w formowaniu wtryskowym, IMP może wykorzystywać proszki metali, ceramikę, a nawet materiały kompozytowe. Otwiera to drzwi do tworzenia części o unikalnych kombinacjach wytrzymałości, przewodności lub biokompatybilności. | |
Części o wysokiej wydajności: Możliwość wykorzystania proszków metalowych i ceramicznych w IMP umożliwia produkcję wysokowydajnych części o wyjątkowej wytrzymałości, odporności na ciepło lub zużyciu. | Elementy formowane wtryskowo z metalu (MIM) mogą osiągać właściwości mechaniczne porównywalne z metalami kutymi (luzem), dzięki czemu nadają się do wymagających zastosowań. Podobnie, ceramiczne części IMP oferują doskonałą odporność na zużycie i działanie w wysokich temperaturach. | |
Potencjał produkcji masowej: Początkowo wykorzystywana do prototypowania, technologia IMP dojrzała, aby umożliwić opłacalną masową produkcję złożonych części. | Wysoki stopień automatyzacji osiągalny w procesach IMP pozwala na wydajną produkcję dużych ilości części o stałej jakości. Sprawia to, że jest to realna opcja dla zastosowań wysokonakładowych. | |
Ulepszone wykończenie powierzchni: W porównaniu z tradycyjnymi technikami odlewania metali, IMP może czasami osiągnąć gładsze wykończenie powierzchni końcowych części. | Zastosowanie drobnych proszków i kontrolowanego procesu formowania może zminimalizować niedoskonałości powierzchni, potencjalnie zmniejszając potrzebę obszernych etapów obróbki końcowej, takich jak polerowanie. |
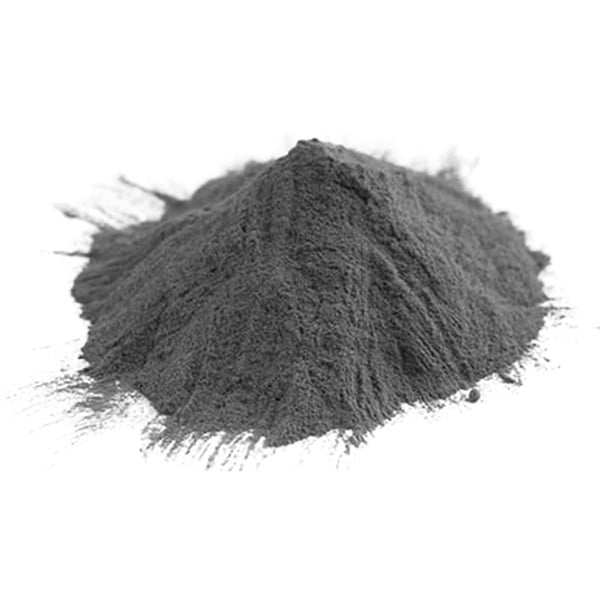
Skład proszku do formowania wtryskowego
Komponent | Opis | Funkcja |
---|---|---|
Proszki bazowe | Stanowią one podstawowy materiał funkcjonalny części końcowej i można je podzielić na trzy główne typy: Proszki metali: Drobno rozdrobnione cząstki metaliczne różnych stopów, takich jak stal nierdzewna, stal narzędziowa lub nadstopy. Proszki ceramiczne: Materiały ceramiczne, takie jak tlenek glinu, tlenek cyrkonu lub azotek krzemu w postaci proszku. Proszki polimerowe: Polimery termoplastyczne powszechnie stosowane w formowaniu wtryskowym, takie jak nylon lub polipropylen. | Wybór proszku bazowego determinuje ostateczne właściwości formowanej części, takie jak wytrzymałość, odporność na zużycie lub właściwości termiczne. |
System segregatorów | Jest to kluczowy składnik, który działa jak tymczasowy klej, utrzymując cząsteczki proszku bazowego razem podczas procesu formowania. System spoiwa zazwyczaj składa się z: Polimer termoplastyczny: Żywica termoplastyczna, która topi się na etapie formowania wtryskowego, umożliwiając płynność i przyczepność do proszku bazowego. * Woski lub dodatki: Mogą one poprawić właściwości płynięcia, zwiększyć wydajność usuwania lepiszcza lub pomóc w dyspersji proszku w spoiwie. | System wiążący zapewnia, że proszek zachowuje się jak materiał formowalny podczas wtrysku i umożliwia tworzenie złożonych kształtów. |
Formatory porów | Są to opcjonalne dodatki, które tworzą tymczasowe pory w formowanej części. Mogą to być: * Materiały organiczne: Wypalają się one podczas usuwania lepiszcza, pozostawiając sieć porów, które ułatwiają usuwanie systemu wiążącego. * Chemiczne środki ługujące: Rozpuszczają się one w określonym rozpuszczalniku podczas etapu przetwarzania końcowego, tworząc kontrolowaną strukturę porów. | Formatory porów umożliwiają tworzenie porowatych struktur w końcowej części, co może być korzystne w przypadku zastosowań takich jak filtry lub implanty kostne. |
Charakterystyka stosowanych proszków metali
Charakterystyka | Opis | Znaczenie w MIM |
---|---|---|
Rozmiar i rozkład cząstek | Rozmiar i rozmieszczenie cząstek proszku metalu znacząco wpływają na następujące aspekty MIM: Wypełnianie form i wytrzymałość zielona: Drobniejsze proszki generalnie oferują lepszą gęstość upakowania i mogą poprawić wypełnienie formy podczas wtrysku. Jednak zbyt drobne cząstki mogą utrudniać płynność i prowadzić do wyzwań podczas przetwarzania. Wąski rozkład wielkości cząstek zapewnia spójne upakowanie i minimalizuje puste przestrzenie w formowanej części, przyczyniając się do dobrej wytrzymałości na zielono (wytrzymałość części przed spiekaniem). Zachowanie podczas spiekania i właściwości końcowe: Rozmiar cząstek wpływa na proces spiekania, w którym cząstki łączą się ze sobą, tworząc stałą strukturę. Proszki o szerszym rozkładzie wielkości mogą prowadzić do niejednorodnego spiekania i potencjalnie wpływać na końcowe właściwości mechaniczne części. | Staranny dobór wielkości i rozkładu cząstek ma kluczowe znaczenie dla uzyskania dobrego wypełnienia formy, wytrzymałości na zimno i optymalnej wydajności końcowego spiekanego elementu. |
Morfologia cząsteczek | Odnosi się to do kształtu cząstek proszku metalu. Idealnie, procesy MIM faworyzują proszki o kulistej lub prawie kulistej morfologii. | Sferyczne cząstki łatwiej przepływają, poprawiając wypełnienie formy i gęstość upakowania. Cząstki o nieregularnym kształcie mogą tworzyć puste przestrzenie i utrudniać przepływ, potencjalnie prowadząc do defektów w formowanej części. |
Gęstość pozorna i kranowa | Właściwości te reprezentują gęstość nasypową proszku w różnych warunkach. Gęstość pozorna: Odnosi się to do gęstości proszku w spoczynku, z uwzględnieniem przestrzeni między cząstkami. Gęstość kranu: Odzwierciedla to gęstszy stan osiągnięty dzięki standardowemu procesowi gwintowania. | Wyższa gęstość upakowania jest ogólnie pożądana w MIM dla efektywnego wykorzystania materiału i dobrej dokładności wymiarowej części końcowej. Przyczynia się również do lepszego upakowania podczas formowania i minimalizuje skurcz podczas spiekania. |
Skład chemiczny | Konkretne pierwiastki lub stopy użyte w proszku metalowym określają ostateczne właściwości spiekanej części. | Wybór składu proszku metalu pozwala na dostosowanie właściwości, takich jak wytrzymałość, odporność na korozję lub odporność na zużycie, aby spełnić określone wymagania aplikacji. MIM może wykorzystywać różne stopy metali, w tym stal nierdzewną, stal narzędziową, a nawet wysokowydajne stopy, takie jak Inconel. |
Płynność | Odnosi się to do łatwości, z jaką proszek przepływa pod wpływem grawitacji lub przyłożonych sił. | Dobra płynność jest niezbędna do równomiernego rozprowadzania proszku podczas formowania wtryskowego. Proszki o słabej płynności mogą prowadzić do niespójności w gęstości upakowania i potencjalnych wad w końcowej części. |
Normy dotyczące proszków metali
Stosowane proszki metali muszą spełniać normy dotyczące składu i ziarna:
Standardowy korpus | Standard | Opis | Znaczenie w IMP |
---|---|---|---|
ASTM International (ASTM) | ASTM B930 - Standardowy przewodnik dotyczący charakterystyki proszków stosowanych do formowania wtryskowego metali (MIM) | Norma ta określa różne metody testowania właściwości proszków metali stosowanych w MIM. | Zapewnia ramy do oceny czynników takich jak rozkład wielkości cząstek, morfologia, płynność i gęstość pozorna. Zapewnia to spójność i kontrolę jakości proszków metali stosowanych w aplikacjach IMP. |
** | ** | * ASTM B783 - Standardowa specyfikacja proszków ze stali nierdzewnej do zastosowań w formowaniu wtryskowym metali (MIM) | Norma ta określa szczegółowe wymagania dotyczące składu chemicznego, rozkładu wielkości cząstek i płynności proszków ze stali nierdzewnej stosowanych w MIM. |
** | ** | * ASTM D4000 - Standardowy system klasyfikacji materiałów z tworzyw sztucznych | Chociaż norma ta nie dotyczy wyłącznie IMP, zapewnia system klasyfikacji dla różnych rodzajów tworzyw sztucznych, w tym tych potencjalnie stosowanych jako spoiwa w surowcach IMP. |
Międzynarodowa Organizacja Normalizacyjna (ISO) | * ISO 3095 - Proszki metaliczne - Oznaczanie natężenia przepływu za pomocą przepływomierza Halla | Niniejszy standard określa metodę pomiaru sypkości proszków metalicznych przy użyciu przepływomierza Halla. | Zapewnia znormalizowane podejście do oceny płynności, krytycznej cechy dla osiągnięcia dobrego wypełnienia formy i stałej jakości części w IMP. |
** | ** | * ISO 4497 - Tworzywa sztuczne - Oznaczanie wskaźnika szybkości płynięcia (MFR) i objętościowego wskaźnika szybkości płynięcia (MVR) tworzyw termoplastycznych | Norma ta określa metodę pomiaru szybkości płynięcia (MFR) materiałów termoplastycznych, która może być istotna dla składnika wiążącego w surowcu IMP. |
Etapy procesu produkcyjnego
Proces produkcyjny składa się z następujących kluczowych etapów:
Krok | Opis | Znaczenie |
---|---|---|
1. Przygotowanie i mieszanie proszku | Proszek bazowy (metalowy, ceramiczny lub polimerowy) jest starannie dobierany i poddawany obróbce wstępnej w oparciu o pożądane właściwości końcowe. Może zawierać dodatki, takie jak substancje tworzące pory lub smary. Proszek jest następnie precyzyjnie ważony i mieszany z systemem wiążącym w celu uzyskania jednorodnego materiału wsadowego. | Ten krok stanowi podstawę dla ostatecznych właściwości części. Staranny dobór i dokładne mieszanie zapewniają spójne zachowanie materiału podczas przetwarzania. |
2. Formowanie wtryskowe | Przygotowany materiał wsadowy IMP jest podgrzewany do stanu półstopionego i wtryskiwany do zamkniętej wnęki formy pod wysokim ciśnieniem. Forma odtwarza pożądany kształt końcowej części. | Ten etap definiuje geometrię części. Stały przepływ i ciśnienie podczas wtrysku mają kluczowe znaczenie dla uzyskania dokładnych wymiarów części i minimalnych defektów. |
3. Debindowanie | Uformowana część, zwana również "zieloną częścią", przechodzi proces usuwania spoiwa w celu usunięcia systemu wiążącego. Można to osiągnąć poprzez: * Odwiązywanie rozpuszczalnikiem: Część jest zanurzana w rozpuszczalniku, który rozpuszcza spoiwo, pozostawiając strukturę proszku. * Odszranianie termiczne: Część jest poddawana kontrolowanemu cyklowi ogrzewania, w którym spoiwo ulega termicznemu rozkładowi i ulatnia się w postaci gazu. | Skuteczne usuwanie wiązań ma kluczowe znaczenie dla osiągnięcia pożądanego kształtu i porowatości bez uszkodzenia delikatnej struktury proszku. |
4. Spiekanie | Część pozbawiona zadziorów jest poddawana działaniu wysokich temperatur w kontrolowanej atmosferze (często pod próżnią lub gazem obojętnym). Proces ten promuje dyfuzję i wiązanie między cząsteczkami proszku, w wyniku czego powstaje stały element o kształcie zbliżonym do siatki. | Spiekanie dyktuje ostateczne właściwości mechaniczne części, takie jak wytrzymałość, gęstość i stabilność wymiarowa. Niezbędna jest precyzyjna kontrola temperatury i zarządzanie atmosferą. |
5. Przetwarzanie końcowe | W zależności od wymagań aplikacji, spiekana część może być poddawana dodatkowym etapom wykańczania, takim jak: * Obróbka skrawaniem lub szlifowanie: W celu uzyskania precyzyjnych tolerancji wymiarowych lub wykończenia powierzchni. * Obróbka cieplna: Aby poprawić określone właściwości mechaniczne, takie jak wytrzymałość lub twardość. * Powłoka lub infiltracja: Aby poprawić właściwości powierzchni, takie jak odporność na zużycie lub odporność na korozję. | Obróbka końcowa może dodatkowo poprawić funkcjonalność i estetykę końcowej części IMP. |
Zastosowania części formowanych wtryskowo
Proszek nadający się do formowania wtryskowego mogą być wykorzystywane do produkcji różnych skomplikowanych i precyzyjnych części w różnych branżach:
Przemysł | Przykłady zastosowań | Korzyści z formowania wtryskowego |
---|---|---|
Motoryzacja | Elementy wnętrza (deski rozdzielcze, panele drzwi, konsole) Części pod maską (osłony wentylatorów, kolektory dolotowe) Komponenty funkcjonalne (koła zębate, zębatki) | Wielkoseryjna produkcja złożonych kształtów o precyzyjnych cechach. Lekkie części zwiększają oszczędność paliwa. Szeroki zakres opcji materiałowych dla różnych potrzeb wydajnościowych (trwałość, odporność na ciepło). |
Elektronika użytkowa | Obudowy elektroniczne (telefony, laptopy, tablety) Złącza i przyciski Komponenty wewnętrzne (wsporniki, koła zębate) | Masowa produkcja skomplikowanych części o wysokiej dokładności wymiarowej. Gładkie wykończenie powierzchni zapewnia estetykę i komfort użytkowania. Różnorodność kolorów i tekstur osiągana poprzez dobór materiałów i technik formowania. |
Urządzenia medyczne | Narzędzia chirurgiczne (uchwyty, rękojeści) Elementy protetyczne (stawy kolanowe, implanty dentystyczne) Jednorazowe elementy medyczne (strzykawki, fiolki) | Sterylizowalne materiały zapewniające higienę i bezpieczeństwo. Materiały biokompatybilne do stosowania w ludzkim ciele (niektóre polimery i stopy metali). Złożone geometrie zapewniające precyzyjną funkcjonalność w zastosowaniach medycznych. |
Przemysł lotniczy i obronny | Elementy samolotów (kanały, części podwozia) Komponenty satelitarne (wsporniki, obudowy) Sprzęt obronny (hełmy, elementy broni) | Lekkie i wytrzymałe materiały do redukcji masy w zastosowaniach lotniczych. Materiały trudnopalne lub żaroodporne spełniające określone wymagania. Wytrzymałe części do pracy w trudnych warunkach i wymagających warunkach operacyjnych. |
Towary konsumpcyjne | Zabawki i gry Urządzenia (obudowy, pokrętła, tarcze) Artykuły sportowe (kaski, części rowerowe) | Ekonomiczna produkcja wysokonakładowych produktów konsumenckich. Szeroka gama kolorów i wykończeń zapewnia atrakcyjność wizualną. Trwałe i funkcjonalne części do codziennego użytku. |
Zalety formowania wtryskowego w produkcji części
Przewaga | Opis | Korzyści |
---|---|---|
Produkcja wielkoseryjna: Formowanie wtryskowe doskonale sprawdza się w wydajnej produkcji dużych ilości identycznych części. Możliwości automatyzacji i szybkie czasy cykli pozwalają na opłacalną produkcję masową. | Jest to szczególnie korzystne w przypadku produktów wymagających milionów sztuk, takich jak elektronika użytkowa lub komponenty motoryzacyjne. Stała jakość i powtarzalność są zapewnione w całym cyklu produkcyjnym. | |
Elastyczność konstrukcji: Formowanie wtryskowe może obejmować szeroki zakres złożoności geometrycznych, w tym skomplikowane kształty, cienkie ścianki i elementy wewnętrzne. Ta swoboda projektowania umożliwia tworzenie funkcjonalnych i innowacyjnych części. | W przeciwieństwie do niektórych metod produkcji subtraktywnej, formowanie wtryskowe nie jest ograniczone geometrią narzędzia. Podcięcia, kanały i inne złożone elementy mogą być bezpośrednio formowane w części. | |
Dokładność wymiarowa i powtarzalność: Precyzyjna kontrola nad projektem formy i parametrami wtrysku pozwala na uzyskanie spójnych i dokładnych wymiarów części przy dużych wolumenach produkcji. | Minimalizuje to potrzebę etapów przetwarzania końcowego w celu korekty wymiarów i zapewnia wymienne części do montażu. Powtarzalność ma kluczowe znaczenie dla utrzymania stałej jakości i funkcjonalności produktu. | |
Szeroki wybór materiałów: W formowaniu wtryskowym można stosować szeroką gamę materiałów, w tym tworzywa termoplastyczne, termoutwardzalne, elastomery, a nawet niektóre stopy metali (poprzez formowanie wtryskowe metali - MIM). | Ta wszechstronność pozwala na wybór optymalnego materiału w oparciu o pożądane właściwości, takie jak wytrzymałość, odporność na ciepło, odporność chemiczna lub elastyczność. | |
Wykończenie powierzchni i estetyka: Formowanie wtryskowe może wytwarzać części o gładkich i wysokiej jakości wykończeniach powierzchni, często eliminując potrzebę obszernych etapów obróbki końcowej, takich jak polerowanie. Ponadto podczas formowania można stosować różne barwniki i tekstury. | Przyczynia się to do atrakcyjności wizualnej i funkcjonalności produktu końcowego. Gładkie powierzchnie mogą mieć zasadnicze znaczenie dla higieny w urządzeniach medycznych lub dla łatwego czyszczenia towarów konsumpcyjnych. | |
Wydajność materiałowa: Formowanie wtryskowe promuje produkcję w kształcie zbliżonym do siatki, minimalizując straty materiału w porównaniu z technikami subtraktywnymi, takimi jak obróbka skrawaniem. Nadmiar materiału, zwany wlewem i prowadnicami, często można poddać recyklingowi i ponownie wykorzystać w kolejnych seriach produkcyjnych. | Jest to korzystne z punktu widzenia kosztów i zrównoważonego rozwoju. Minimalizacja odpadów zmniejsza również wpływ procesu produkcyjnego na środowisko. | |
Potencjał automatyzacji: Proces formowania wtryskowego może być wysoce zautomatyzowany, przy minimalnej interwencji człowieka. Pozwala to uzyskać stałą jakość produkcji i obniżyć koszty pracy. | Automatyzacja jest szczególnie korzystna w przypadku produkcji wielkoseryjnej i zapewnia stałą jakość produktu niezależnie od poziomu umiejętności operatora. |
Ograniczenia procesu produkcyjnego
Istnieją również pewne ograniczenia:
- Waga części ograniczona do < 400 g
- Grubość ścianki > 0,4 mm
- Zespoły potrzebne do złożonych geometrii
- Drogie oprzyrządowanie do form
- Zmiany wymiarów podczas spiekania
Globalni dostawcy materiałów wsadowych
Wiele międzynarodowych firm dostarcza gotowe surowce do formowania wtryskowego:
Firma | Lokalizacja | Materiały |
---|---|---|
BASF | Niemcy | Stal nierdzewna 316L, stopy tytanu |
Sandvik | Szwecja | Stale nierdzewne, stale narzędziowe |
GKN | WIELKA BRYTANIA | Stopy aluminium i magnezu |
Rio Tinto | Australia | Mieszanki wtryskiwane z metalu i ceramiki |
Orientacyjne ceny
Materiał | Zakres cen |
---|---|
Stal nierdzewna | $50-70 za kg |
Stal narzędziowa | $45-65 za kg |
Ciężki stop wolframu | $130-170 za kg |
Ceny zależą od wielkości zamówienia, potrzeb personalizacji i czynników ekonomicznych.
Plusy i minusy korzystania z Proszki do formowania wtryskowego
Zalety | Wady |
---|---|
Skomplikowane i złożone kształty | Ograniczony rozmiar i waga |
Większe tolerancje | Drogie narzędzia i sprzęt |
Precyzyjne wykończenie powierzchni | Zmiany wymiarów podczas spiekania |
Zakres materiałów | Często wymagane jest przetwarzanie końcowe |
Wysoka produkcja, niski koszt w przeliczeniu na część | Kruche materiały mają tendencję do pękania |
Zmniejszona ilość odpadów | Ogranicza wybór materiału |
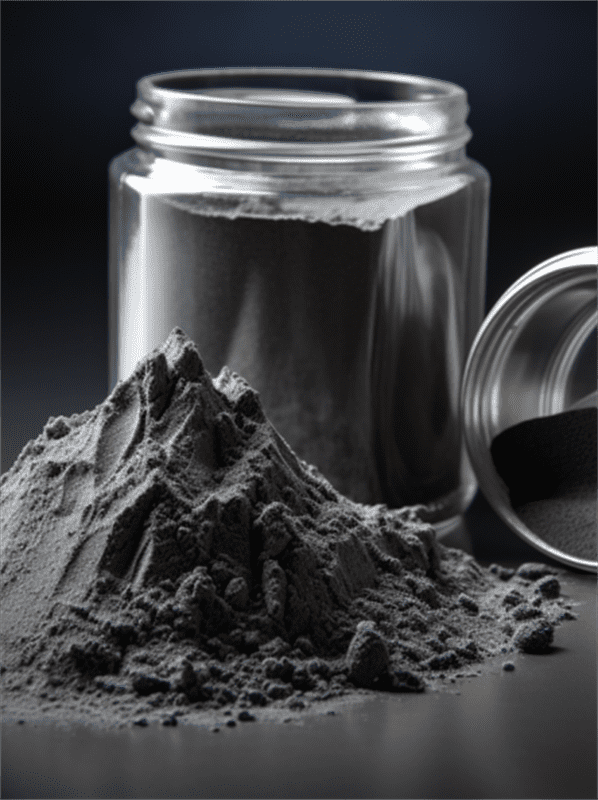
FAQ
P: Jaki jest typowy skład proszków do formowania wtryskowego?
Zawierają 80-90% proszku metalu, 8-20% spoiwa i 1-2% smarów wagowo. Typowe spoiwa to wosk, PP, PE i PEG.
P: Jaki zakres rozmiarów proszków jest używany?
O: Stosowane są proszki o wielkości od 1 do 20 mikronów. Drobniejszy proszek poprawia gęstość, ale może być podatny na aglomerację.
P: Jak duży skurcz występuje podczas spiekania?
O: Podczas spiekania w fazie ciekłej występuje skurcz liniowy części do 20%. Należy uwzględnić to w projekcie narzędzia.
P: Co powoduje pęknięcia w metalowych elementach formowanych wtryskowo?
O: Nierównomierne ogrzewanie w piecach, stosowanie szybkiego chłodzenia po spiekaniu, słabe mieszanie proszków i wybór kruchych stopów.
P: Jakie są dostępne opcje materiałów dla proszków do formowania wtryskowego?
O: Między innymi stale nierdzewne, stale narzędziowe, ciężkie stopy wolframu, stopy miedzi, tytan i stopy tytanu.
Udostępnij
MET3DP Technology Co., LTD jest wiodącym dostawcą rozwiązań w zakresie produkcji addytywnej z siedzibą w Qingdao w Chinach. Nasza firma specjalizuje się w sprzęcie do druku 3D i wysokowydajnych proszkach metali do zastosowań przemysłowych.
Zapytaj o najlepszą cenę i spersonalizowane rozwiązanie dla Twojej firmy!
Powiązane artykuły
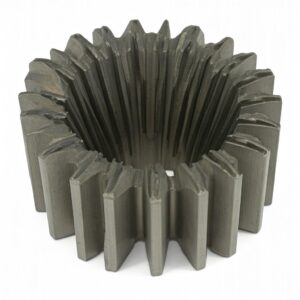
Wysokowydajne segmenty łopatek dysz: Rewolucja w wydajności turbin dzięki drukowi 3D w metalu
Czytaj więcej "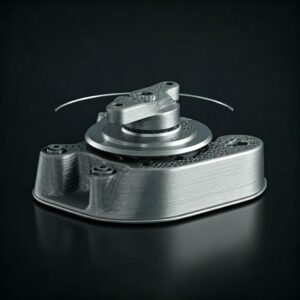
Drukowane w 3D mocowania dla samochodowych czujników radarowych: Precyzja i wydajność
Czytaj więcej "Informacje o Met3DP
Ostatnia aktualizacja
Nasz produkt
KONTAKT
Masz pytania? Wyślij nam wiadomość teraz! Po otrzymaniu wiadomości obsłużymy Twoją prośbę całym zespołem.
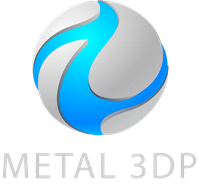
Proszki metali do druku 3D i produkcji addytywnej