Internal Cooling Structures via Metal 3D Printing
Spis treści
Introduction: The Critical Role of Internal Cooling in Aerospace Performance
The relentless pursuit of higher performance, greater efficiency, and improved reliability in the aerospace industry hinges significantly on effective thermal management. As aircraft engines, rocket propulsion systems, and hypersonic vehicles push the boundaries of speed, altitude, and operational duration, the temperatures and thermal stresses experienced by critical components reach unprecedented levels. Internal cooling structures, integrated directly within these high-temperature components, are not merely accessories; they are fundamental enablers of modern aerospace technology. Without sophisticated internal cooling, materials would rapidly degrade, components would fail prematurely, and the desired performance gains would remain unattainable. These intricate networks of channels, passages, and cavities are meticulously designed to extract heat from the hottest sections of components like gas turbine blades, nozzle guide vanes, combustion liners, and rocket engine thrust chambers, maintaining material integrity and ensuring operational safety margins.
The primary objectives of internal cooling in aerospace applications include:
- Preventing Material Overheating: Keeping component temperatures below the material’s creep, oxidation, and melting limits, especially in regions directly exposed to hot gas paths (e.g., turbine inlet temperatures exceeding the melting point of the blade alloys themselves).
- Reducing Thermal Gradients and Stresses: Minimizing temperature differences across a component helps mitigate thermal stresses, which can lead to fatigue cracking and reduced component life. Uniform cooling is key.
- Enhancing Component Lifespan: By controlling temperatures and stresses, internal cooling significantly extends the operational life of critical, high-value parts, reducing maintenance intervals and overall lifecycle costs.
- Improving Engine Efficiency: Higher operating temperatures generally lead to better thermodynamic efficiency (e.g., Carnot efficiency). Effective cooling allows designers to push firing temperatures higher, boosting thrust and reducing fuel consumption, a critical factor for both economic viability and environmental impact.
- Enabling Advanced Designs and Materials: Sophisticated cooling allows the use of advanced materials and complex component geometries that offer performance advantages but might have lower intrinsic temperature resistance compared to older, less efficient designs.
Traditionally, manufacturing these complex internal cooling networks involved intricate casting processes (like investment casting with complex ceramic cores) or elaborate fabrication and joining techniques. While effective to a degree, these methods often impose significant limitations on the complexity, efficiency, and geometric possibilities of the cooling channels. Sharp corners, difficult-to-remove cores, minimum feature sizes, and limitations on channel pathing often constrained cooling designs, preventing engineers from achieving truly optimal thermal management solutions. Furthermore, the multi-step nature of these traditional processes could lead to long lead times, high tooling costs, and potential points of failure at joints or interfaces.
Enter metal additive manufacturing (AM), often referred to as metal Drukowanie 3D. This transformative technology offers a fundamentally different approach to component creation. Instead of subtracting material or casting it into a mold, AM builds parts layer by layer directly from a digital model, typically by fusing fine metal powder using a laser or electron beam. This layer-wise construction unlocks unprecedented design freedom, particularly for internal features. Complex, tortuous cooling channels, optimized lattice structures for enhanced heat transfer, and conformal cooling passages that precisely follow the contours of a part’s hottest regions – geometries previously impossible or prohibitively expensive to manufacture – are now achievable. This capability is revolutionizing the design and production of aerospace components requiring sophisticated thermal management. Companies like Met3dp, specializing in druk 3D z metalu technologies and high-performance powders, are at the forefront of enabling these advancements, providing the tools and materials necessary to realize next-generation aerospace cooling solutions. The ability to directly fabricate parts with highly optimized internal cooling channels not only boosts performance and efficiency but also opens doors for part consolidation, weight reduction, and accelerated development cycles, marking a significant paradigm shift in aerospace engineering and manufacturing.
What are Aerospace Internal Cooling Structures? Applications and Challenges
Aerospace internal cooling structures are engineered features integrated within a component’s volume, specifically designed to manage and dissipate heat generated during operation or absorbed from the surrounding high-temperature environment. Unlike external cooling methods (like film cooling, where cooler air is bled onto the surface), internal cooling focuses on removing heat from within the material itself, often using a coolant fluid (typically compressed air bled from the engine’s compressor stage, or fuel in some rocket applications) flowing through a network of internal passages. The design of these structures is a complex interplay between fluid dynamics, heat transfer principles, material science, and manufacturing constraints. The goal is to maximize heat extraction with minimal coolant usage and minimal impact on the component’s structural integrity.
Key Applications:
The need for internal cooling is most pronounced in the “hot sections” of propulsion systems and high-speed vehicle components:
- Gas Turbine Engine Blades and Vanes: This is perhaps the most critical application. Turbine blades (rotating) and nozzle guide vanes (stationary) operate in extremely hot gas streams exiting the combustor, often at temperatures significantly exceeding the melting point of the superalloys they are made from. Complex internal cooling circuits, often combining serpentine passages, turbulence-promoting ribs (turbulators), and pin-fin arrays, are essential to keep the metal temperature within safe limits, enabling higher turbine inlet temperatures for greater engine efficiency and thrust.
- Combustion Liners and Chambers: The walls of the combustion chamber, where fuel is burned at extremely high temperatures, require robust cooling to prevent structural failure. Internal cooling passages, often arranged in complex patterns, help manage the intense heat flux and maintain the liner’s integrity over thousands of operating hours.
- Rocket Engine Thrust Chambers and Nozzles: Particularly in reusable liquid-propellant rocket engines (LPREs), the combustion chamber and nozzle throat experience extreme heat loads. Regenerative cooling is a common technique where the cryogenic fuel (like liquid hydrogen or methane) flows through intricate internal channels within the chamber/nozzle walls before being injected into the combustion chamber. This cools the structure while simultaneously pre-heating the propellant for better combustion efficiency. The complexity and pressure requirements for these channels are immense.
- Hypersonic Vehicle Components: Leading edges, engine inlets (scramjets), and control surfaces of hypersonic aircraft and missiles experience severe aerodynamic heating. Internal cooling channels, potentially using fuel or dedicated coolants, are critical for survival in these flight regimes.
- Aerospace Heat Exchangers: Compact, high-efficiency heat exchangers are vital for various onboard systems (e.g., environmental control systems (ECS), fuel thermal management, avionics cooling). Internal channels designed for maximum surface area and optimized flow paths are key to their performance, especially where space and weight are critical.
- Electronics and Avionics Cooling: High-power density electronics generate significant heat. While often managed by cold plates, integrating internal cooling channels directly into the chassis or mounting structures using AM can provide more efficient, localized cooling solutions.
Design and Manufacturing Challenges:
Designing and manufacturing these intricate internal structures presents significant challenges, particularly with traditional methods:
- Geometric Complexity: Optimal cooling often requires non-linear, branching, and conformally shaped channels with varying cross-sections, turbulators, and smooth bends to minimize pressure loss. Achieving these with casting (requiring complex ceramic cores) or machining (limited access) is extremely difficult or impossible.
- Feature Size Limitations: Heat transfer is often enhanced by small, intricate features like turbulators or pin fins. Traditional methods struggle to create these features reliably and accurately deep within internal passages.
- Material Constraints: The high-temperature alloys used (e.g., nickel-based superalloys, refractory metals) are often difficult to cast or machine, further complicating the manufacturing process.
- Core Removal (Casting): In investment casting, removing the intricate ceramic cores used to form the internal passages without damaging the thin walls of the component can be a major yield detractor. Residual core material can also block passages.
- Joining and Assembly: Fabricating cooling channels by joining multiple pieces introduces potential leak paths and points of mechanical weakness, which are unacceptable in critical aerospace components.
- Inspection and Quality Control: Verifying the integrity, dimensions, and absence of blockages within deep, complex internal channels is challenging using conventional non-destructive testing (NDT) methods.
- Lead Time and Cost: Tooling for complex castings is expensive and time-consuming. Iterating on designs using traditional methods is slow and costly.
These challenges highlight precisely where metal additive manufacturing offers transformative potential. By building the part layer by layer, AM can create highly complex internal geometries directly, overcoming many limitations of casting and machining, enabling engineers to design cooling structures based on optimal thermal performance rather than being constrained by manufacturing limitations.
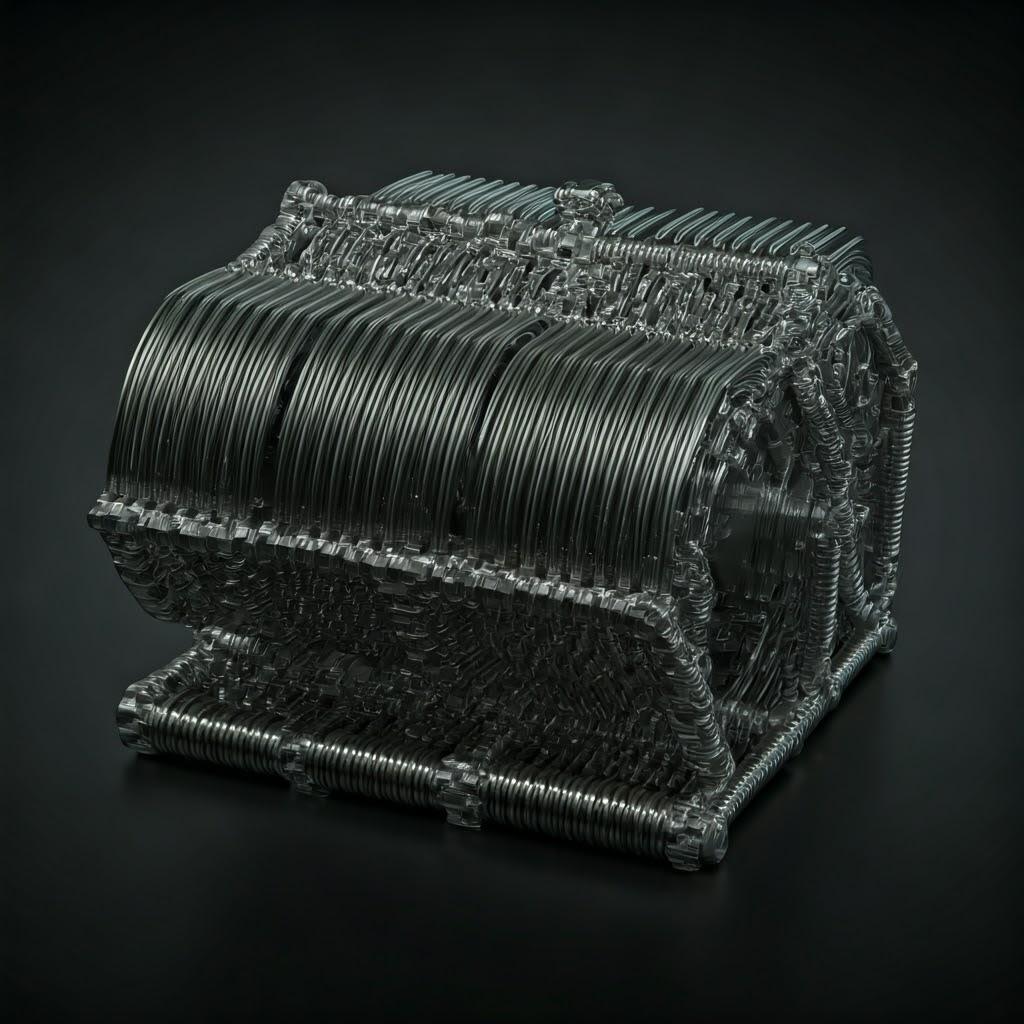
Why Metal 3D Printing for Intricate Internal Cooling Geometries?
The adoption of metal additive manufacturing (AM) for producing aerospace components with internal cooling structures stems from its unique ability to overcome the inherent limitations of traditional manufacturing techniques like investment casting, machining, and fabrication/brazing. AM, particularly powder bed fusion (PBF) methods like Selective Laser Melting (SLM) or Laser Powder Bed Fusion (LPBF) and Electron Beam Melting (EBM) or Electron Beam Powder Bed Fusion (EBPF), offers a compelling suite of advantages for creating parts with complex internal architectures.
Key Advantages of Metal AM for Internal Cooling:
- Unprecedented Design Freedom (Geometric Complexity): This is arguably the most significant advantage. AM liberates designers from the constraints imposed by molds, cores, or tool access.
- Complex Channel Paths: Engineers can design highly tortuous, non-linear cooling paths that closely follow the thermal load profile of the component (conformal cooling). This ensures heat is removed exactly where it’s needed most, improving efficiency and reducing thermal gradients.
- Optimized Cross-Sections: Channel shapes can be varied along their length (e.g., transitioning from circular to elliptical) to optimize flow characteristics and heat transfer coefficients.
- Integrated Features: Intricate heat transfer enhancement features like turbulators, pin fins, trip strips, and complex lattice structures can be directly built into the channels with high fidelity, maximizing thermal performance within a compact volume. These features are often impossible or impractical to create otherwise.
- Konsolidacja części: Components that previously required multiple parts to be manufactured separately and then assembled (e.g., a multi-piece combustion liner with brazed cooling channels) can often be redesigned and printed as a single, monolithic piece.
- Reduced Assembly Time & Cost: Eliminates complex and costly assembly, brazing, or welding steps.
- Improved Reliability: Removes potential failure points associated with joints and interfaces (e.g., braze failures, leaks).
- Redukcja wagi: Eliminates flanges, fasteners, and redundant material needed for joining, contributing to lighter overall systems.
- Lekkość: AM enables advanced lightweighting strategies beyond part consolidation.
- Topology Optimization: Algorithms can be used to remove material from low-stress areas while maintaining structural integrity, creating organically shaped, highly efficient structures. This can be applied to the component’s overall structure, including the walls surrounding the cooling channels.
- Struktury kratowe: Internal voids can be filled with structurally efficient lattice structures instead of solid material, significantly reducing weight while maintaining stiffness and providing potential pathways for secondary cooling or fluid management.
- Accelerated Development and Prototyping: AM allows for rapid iteration on designs without the need for expensive and time-consuming tooling.
- Faster Design Cycles: Engineers can design, print, and test multiple cooling channel configurations much faster than with traditional methods.
- Reduced Prototyping Costs: Eliminates the high cost of creating molds or complex machining setups for prototype parts. This encourages experimentation and optimization.
- Material Capabilities: AM processes are compatible with a wide range of high-performance aerospace alloys required for hot-section components, including nickel-based superalloys (e.g., IN625, IN718, Hastelloy X), titanium alloys (e.g., Ti-6Al-4V), and aluminum alloys (e.g., AlSi10Mg). Companies like Met3dp specialize in producing high-quality, spherical metal powders optimized for AM processes, ensuring the material properties required for demanding aerospace applications. Their advanced gas atomization and PREP technologies yield powders with excellent flowability and high purity, crucial for printing dense, reliable parts.
- Enhanced Cooling Efficiency: The design freedom offered by AM translates directly into more effective cooling.
- Conformal Cooling: Channels can follow the exact 3D contours of the heated surface, maintaining a consistent distance and maximizing heat transfer uniformity.
- Optimized Flow: Complex internal geometries can be designed to induce turbulence or swirl, significantly increasing the convective heat transfer coefficient between the coolant and the channel walls compared to simple smooth channels.
- Increased Surface Area: Features like internal fins or lattices dramatically increase the surface area available for heat exchange within a given volume.
- Supply Chain Advantages: AM can enable distributed manufacturing and on-demand production, potentially reducing reliance on complex global supply chains and long lead times associated with traditional methods like casting.
Comparison Table: AM vs. Traditional Methods for Internal Cooling
Cecha | Wytwarzanie przyrostowe metali (AM) | Odlewanie inwestycyjne | Obróbka skrawaniem | Fabrication/Brazing |
---|---|---|---|---|
Internal Geometry | Highly complex, conformal, integrated features (lattices, turbulators) | Moderate complexity, limited by core creation/removal | Limited by tool access (straight lines, simple curves) | Limited by piece geometry & joining |
Swoboda projektowania | Bardzo wysoka | Umiarkowany | Niski | Low-Moderate |
Konsolidacja części | Excellent potential | Ograniczony | Nie dotyczy | Low potential |
Lekkość | Excellent (topology opt., lattices) | Ograniczony | Limited by subtractive nature | Ograniczony |
Min. Feature Size | Good (depends on process/machine) | Moderate (limited by core fragility) | Moderate (limited by tool size) | Depends on joining method |
Materiały | Wide range (Superalloys, Ti, Al, etc.) | Established for superalloys, Ti, Al | Good for most alloys, but difficult for some | Depends on material compatibility |
Koszt oprzyrządowania | Low (Tool-less) | High (Mold + Core tooling) | Moderate (Fixtures) | Moderate (Fixtures) |
Lead Time (Proto) | Szybko | Powolny | Umiarkowany | Moderate-Slow |
Surface Finish (Internal) | Moderate-Rough (requires post-processing) | Umiarkowanie dobry | Good (where accessible) | Zmienna |
Cost (High Volume) | Potentially higher per part, but system benefits may offset | Generally lower per part | Varies significantly | Varies significantly |
Reliability (Joints) | High (Monolithic) | High (Monolithic) | NIE DOTYCZY | Potential weakness at joints |
Export to Sheets
While AM offers these compelling advantages, it’s crucial to consider factors like surface finish (internal channels printed via PBF tend to have higher roughness), the need for sophisticated post-processing (like HIPing and powder removal), and rigorous quality control. However, for applications where the performance gains enabled by complex internal cooling geometries outweigh these considerations, metal 3D printing provides a powerful and increasingly indispensable manufacturing solution for the aerospace industry.
Material Focus: IN625 and AlSi10Mg for Aerospace Cooling Applications
The choice of material is paramount in designing effective and reliable aerospace components, especially those incorporating internal cooling and operating under demanding conditions. The material must not only withstand the mechanical loads and environmental factors (temperature, corrosion, fatigue) but also be compatible with the chosen manufacturing process – in this case, metal additive manufacturing. For aerospace internal cooling structures, two materials frequently considered, representing different classes of alloys, are Inconel 625 (IN625), a nickel-based superalloy, and Aluminum Silicon Magnesium (AlSi10Mg), a castable aluminum alloy readily adapted for AM. The selection between them, or other potential alloys, depends heavily on the specific application’s temperature requirements, weight constraints, and structural demands.
Inconel 625 (IN625): The High-Temperature Workhorse
IN625 is a nickel-chromium-molybdenum-niobium superalloy renowned for its exceptional combination of high strength, excellent fabricability (including weldability and printability), and outstanding corrosion resistance across a broad range of temperatures, from cryogenic up to approximately 980∘C (1800∘F).
- Key Properties & Benefits for Cooling Applications:
- High-Temperature Strength & Creep Resistance: IN625 maintains significant strength and resists deformation (creep) at elevated temperatures, making it ideal for hot-section components like turbine parts, combustion liners, and exhaust systems where internal cooling is critical for survival.
- Excellent Corrosion and Oxidation Resistance: The high nickel and chromium content provides superb resistance to oxidation and various corrosive media, including hot combustion gases, jet fuel impurities, and sea salt environments (crucial for naval aviation).
- Wytrzymałość zmęczeniowa: Exhibits good resistance to both thermal and mechanical fatigue, essential for components subjected to cyclic loading and temperature fluctuations common in engine operation.
- Dobra drukowność: IN625 is considered one of the more printable nickel superalloys via Laser Powder Bed Fusion (LPBF). While challenges like residual stress exist, established process parameters allow for the creation of dense, high-integrity parts. EBPF can also be used, often resulting in lower residual stresses due to the elevated build chamber temperatures.
- Spawalność: Although AM aims for monolithic parts, good weldability is beneficial for potential repairs or joining AM parts to conventionally manufactured components.
- Why Use IN625 for Internal Cooling Structures?
- Turbine Components: Ideal for internally cooled turbine blades, vanes, shrouds, and heat shields operating in the hottest engine sections.
- Combustors & Exhaust Systems: Suitable for combustion liners, transition ducts, and exhaust nozzles requiring high-temperature strength and corrosion resistance.
- Wymienniki ciepła: Used in high-temperature heat exchangers where operating conditions exceed the capabilities of lighter alloys.
- Rozważania:
- Gęstość: IN625 is relatively dense (approx. 8.44g/cm3), which can be a drawback in weight-sensitive aerospace applications compared to titanium or aluminum alloys.
- Przewodność cieplna: Its thermal conductivity is relatively low compared to aluminum alloys, which needs to be factored into thermal design calculations. While sufficient for many applications, it means temperature gradients within the material itself might be steeper.
- Koszt: Nickel-based superalloys are generally more expensive than aluminum or steel alloys.
Aluminum Silicon Magnesium (AlSi10Mg): The Lightweight Option
AlSi10Mg is a widely used aluminum casting alloy known for its good strength-to-weight ratio, excellent corrosion resistance, and good thermal conductivity. It has become one of the most popular alloys for metal AM, particularly LPBF, due to its favorable printing characteristics.
- Key Properties & Benefits for Cooling Applications:
- Niska gęstość: With a density of approximately 2.67g/cm3, AlSi10Mg offers significant weight savings compared to steels, titanium alloys, and nickel superalloys. This is a major advantage in aerospace where minimizing weight is critical for fuel efficiency and payload capacity.
- Good Thermal Conductivity: Aluminum alloys generally possess high thermal conductivity (significantly higher than IN625 or Ti-6Al-4V). This allows for efficient heat transfer from the component structure to the coolant fluid within the internal channels, potentially enabling more compact or efficient cooling designs for moderate temperature applications.
- Doskonała drukowność: AlSi10Mg is well-understood and relatively easy to process using LPBF, allowing for fine features, thin walls, and complex geometries common in optimized cooling structures. It typically results in near-fully dense parts with good mechanical properties in the as-built and heat-treated states.
- Dobra odporność na korozję: Exhibits good resistance to atmospheric corrosion.
- Niższy koszt: Generally less expensive than nickel or titanium alloys.
- Why Use AlSi10Mg for Internal Cooling Structures?
- Moderate Temperature Applications: Suitable for components where operating temperatures typically do not exceed 150−200∘C (300−390∘F), as its mechanical properties degrade significantly at higher temperatures.
- Wymienniki ciepła: Widely used for lightweight, efficient heat exchangers in environmental control systems (ECS), avionics cooling, and oil/fuel cooling loops.
- Housings and Enclosures: Applicable for cooled electronic enclosures, gearbox housings, or structural components requiring integrated thermal management in moderate temperature zones.
- Cold Section Components: Potentially used in cooler sections of propulsion systems or for components requiring thermal management far from the primary heat source.
- Rozważania:
- Temperature Limitation: The primary limitation is its relatively low melting point and rapid loss of strength at moderately elevated temperatures, restricting its use in hot-section engine components.
- Lower Strength & Fatigue: While possessing a good strength-to-weight ratio, its absolute strength, fatigue endurance, and creep resistance are significantly lower than IN625 or Ti-6Al-4V.
Material Powder Quality: The Met3dp Advantage
Regardless of the alloy chosen, the quality of the metal powder used in the AM process is critical to achieving the desired component properties and integrity, especially for demanding aerospace applications. Poor powder quality (e.g., irregular particle shape, satellites, internal porosity, inconsistent particle size distribution, impurities) can lead to defects in the final part, such as porosity, poor surface finish, and inconsistent mechanical properties.
Met3dp addresses this critical need by leveraging industry-leading powder production technologies:
- Advanced Atomization: Employing state-of-the-art gas atomization (utilizing unique nozzle and gas flow designs) and Plasma Rotating Electrode Process (PREP) technologies, Met3dp produces metallic powders with:
- Wysoka sferyczność: Spherical particles flow easily and pack densely in the powder bed, contributing to uniform layers and reduced porosity in the final part.
- Dobra płynność: Consistent powder flow is essential for reliable recoating (spreading new layers) in PBF machines.
- Low Satellite Content: Minimizing smaller particles attached to larger ones improves packing density and flow.
- Wysoka czystość: Controlled melting and atomization processes minimize oxygen pickup and other contaminants, ensuring optimal material properties.
- Optimized Portfolio: Met3dp manufactures a wide range of high-quality metal powders specifically optimized for laser and electron beam powder bed fusion processes, including IN625 and AlSi10Mg, alongside other innovative alloys like TiNi, TiTa, TiAl, TiNbZr, CoCrMo, various stainless steels, and other superalloys. This ensures customers have access to aerospace-grade materials tailored for AM.
- Ekspertyza: With decades of collective expertise in metal additive manufacturing, Met3dp provides comprehensive solutions, understanding the critical link between powder characteristics and final part quality. They act not just as a powder supplier but as a partner in developing robust AM applications. You can learn more about their commitment and capabilities on their Strona O nas.
Material Selection Summary Table:
Nieruchomość | IN625 | AlSi10Mg | Primary Deciding Factor |
---|---|---|---|
Max Service Temp. | High (~980∘C) | Low (~150−200∘C) | Application Temperature |
Gęstość | High (~8.44g/cm3) | Low (~2.67g/cm3) | Weight Sensitivity |
Strength (High Temp) | Doskonały | Słaby | Application Temperature |
Przewodność cieplna | Moderate/Low | Wysoki | Heat Dissipation Efficiency Needs |
Odporność na korozję | Doskonały | Dobry | Środowisko operacyjne |
Printability (LPBF) | Good (Manageable Challenges) | Doskonały | Manufacturability Ease |
Koszt | Wysoki | Niski/umiarkowany | Ograniczenia budżetowe |
Aplikacje podstawowe | Hot Sections (Turbines, Combustors) | Moderate Temp (Heat Exchangers, Housings) | Overall Performance Requirements |
Export to Sheets
In conclusion, the choice between IN625 and AlSi10Mg for metal 3D printed internal cooling structures is driven primarily by the operating temperature and weight requirements of the specific aerospace application. IN625 offers unparalleled high-temperature performance for demanding hot sections, while AlSi10Mg provides a lightweight, high-thermal-conductivity solution for moderate-temperature components. Partnering with a knowledgeable material supplier like Met3dp ensures access to high-quality powders essential for manufacturing reliable, high-performance aerospace parts using additive manufacturing.
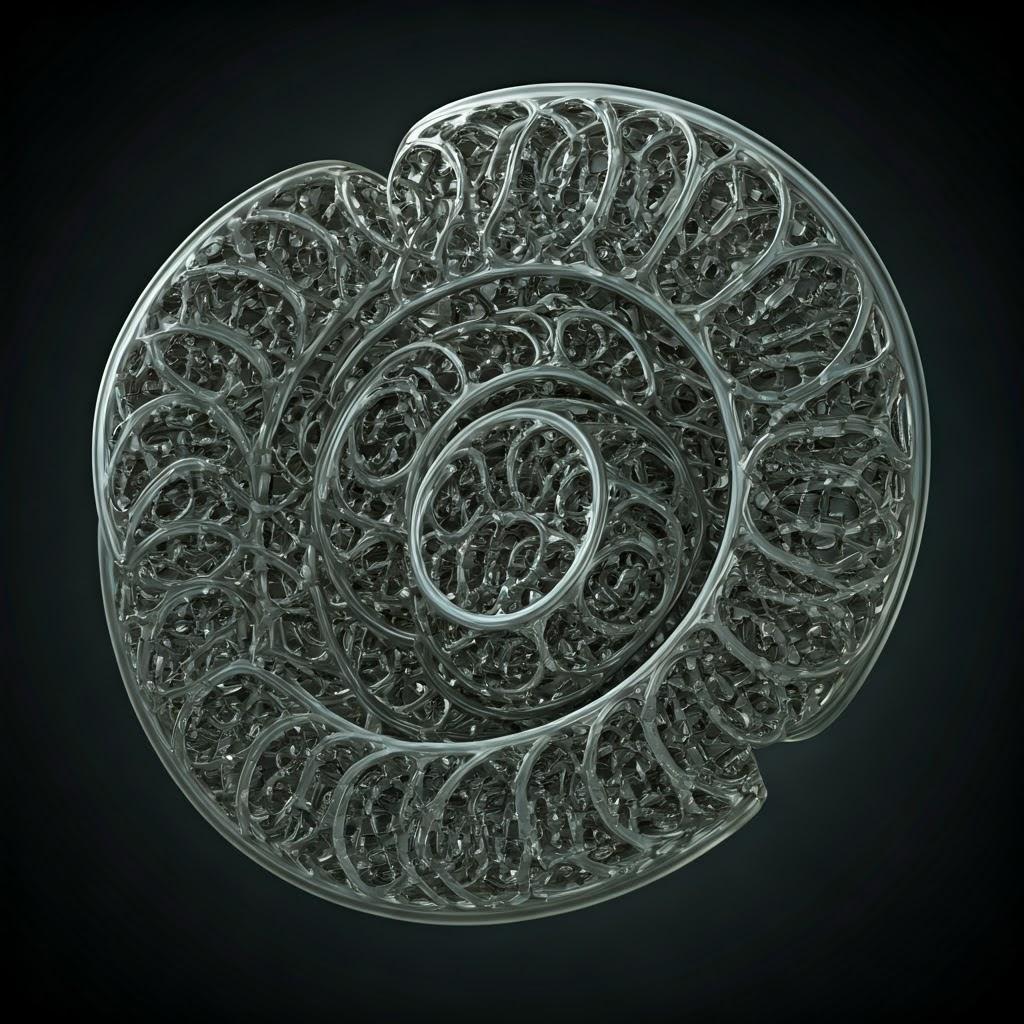
Design Considerations: Optimizing Internal Cooling Channels for Additive Manufacturing
Successfully leveraging metal additive manufacturing for internal cooling structures requires more than simply replicating designs intended for traditional methods. It demands a fundamental shift in design philosophy, embracing Design for Additive Manufacturing (DfAM) principles. DfAM is not just about possibility; it’s about optimality – designing parts that maximize the benefits of AM (complexity, lightweighting, consolidation) while minimizing its inherent challenges (supports, surface finish, residual stress). Optimizing internal cooling channels for AM involves careful consideration of geometry, fluid dynamics, thermal performance, and manufacturability constraints specific to the layer-by-layer process. Procurement managers and engineers must collaborate closely, understanding that upfront design optimization significantly impacts final part quality, cost, and lead time.
Key DfAM Principles for Internal Cooling Channels:
- Self-Supporting Geometries: Powder bed fusion processes require support structures for features overhanging below a certain critical angle (typically around 45 degrees relative to the build plate, though material and parameter dependent). Designing internal channels to be self-supporting is highly desirable to avoid the significant challenge of removing supports from deep within complex passages.
- Strategies:
- Angled Channels: Routing channels at angles steeper than the critical overhang angle.
- Optimized Cross-Sections: Using diamond, teardrop, or hexagonal channel shapes instead of purely circular or horizontal rectangular sections can make them inherently self-supporting.
- Orientacja budynku: Carefully selecting the part’s orientation on the build plate can render many internal features self-supporting. This requires careful analysis, as orientation also affects surface finish, residual stress, and build time.
- Strategies:
- Minimum Feature Sizes and Wall Thickness: AM processes have limitations on the minimum size of features they can reliably produce.
- Channel Diameter: Very small channels (sub-millimeter) can be challenging to print reliably and, more importantly, to clear of unfused powder after printing. Practical minimums often depend on the machine resolution, powder size, and aspect ratio (length vs. diameter), typically in the range of 0.5 mm to 1.0 mm, though smaller is sometimes possible with careful process control.
- Grubość ścianki: Walls separating cooling channels or forming the outer shell of the component must be thick enough to print reliably without distortion or blow-through, and to withstand operational pressures and stresses. Minimum printable wall thickness might be around 0.3−0.5 mm, but structural and thermal requirements usually dictate much thicker walls. DfAM involves ensuring walls are thick enough for function and printability but not unnecessarily thick, adding weight and material cost.
- Designing for Powder Removal: One of the most critical DfAM considerations for internal channels is ensuring that all unfused powder can be completely removed after the build. Trapped powder can block channels, reduce cooling effectiveness, add weight, and potentially become dislodged during operation, causing downstream damage.
- Access Ports: Design inlet and outlet ports strategically placed to allow for effective powder evacuation using compressed air, vibration, and potentially flushing fluids. Consider line-of-sight access where possible.
- Avoid Dead Ends: Eliminate sections of channels where powder can become trapped with no exit path.
- Smooth Transitions: Use fillets and smooth bends instead of sharp corners where powder might accumulate.
- Channel Size & Aspect Ratio: Very long, narrow channels are inherently difficult to clear. Designers may need to balance thermal optimization with powder removal feasibility, potentially increasing channel diameter slightly or adding intermediate clean-out ports if absolutely necessary (though this adds complexity).
- Integrating Heat Transfer Enhancement Features: AM allows for the direct fabrication of complex features within channels to increase turbulence and surface area, boosting heat transfer coefficients (h).
- Turbulators (Ribs): Ribs placed strategically along channel walls disrupt the boundary layer and enhance mixing. DfAM involves optimizing rib shape (angled, V-shaped, broken), height, pitch, and ensuring they are printable without defects.
- Pin Fins: Arrays of small pins spanning the channel can significantly increase surface area but also increase pressure drop. AM allows for optimized pin shapes (elliptical, streamlined) and non-uniform distributions. Printability and powder removal around dense pin fin arrays require careful consideration.
- Struktury kratowe: Filling larger cavities or plenums with optimized lattice structures can provide both structural support and extremely high surface area-to-volume ratios for heat exchange. Selecting the right unit cell type (e.g., gyroid, diamond) and optimizing strut diameter and density is crucial. Met3dp’s expertise in printing complex geometries can be invaluable when incorporating such advanced features.
- Computational Fluid Dynamics (CFD) and Thermal Simulation: Utilizing simulation tools early and often in the design process is essential for optimizing internal cooling channels.
- Flow Distribution: CFD can predict how the coolant distributes through complex channel networks, identifying areas of stagnation or insufficient flow.
- Heat Transfer Prediction: Simulate convective heat transfer coefficients and resulting wall temperatures to ensure the design meets thermal management goals.
- Pressure Drop Analysis: Predict the pressure loss through the cooling circuit, ensuring it aligns with the available coolant pressure budget. Overly complex or rough channels can lead to excessive pressure drop.
- Iterative Optimization: Use simulation results to iteratively refine channel paths, cross-sections, and heat transfer enhancement features before committing to a print.
- Topology Optimization and Generative Design: These advanced design tools can be used to create highly optimized, often organic-looking structures that minimize weight while meeting structural and thermal requirements. They can automatically generate novel cooling channel layouts and integrate them seamlessly with the load-bearing structure of the component, fully exploiting the geometric freedom of AM.
- Support Structure Strategy (If Unavoidable): When self-supporting designs are not feasible, a strategy for internal supports is needed.
- Minimization: Use topology optimization or careful design to minimize the need for internal supports.
- Dostępność: Design supports that are accessible for removal, potentially requiring specific break points or structures designed to be flushed out chemically or mechanically (e.g., via Abrasive Flow Machining).
- Material Choice: Some AM processes or materials allow for easier support removal than others.
By integrating these DfAM principles, engineers can design internal cooling structures that are not only manufacturable via metal AM but are also highly optimized for thermal performance, weight, and reliability. This upfront investment in design pays dividends in reduced post-processing efforts, lower failure rates, and superior component performance. Collaboration with AM experts, like the team at Met3dp, during the design phase can help navigate these complexities and ensure designs are production-ready. Understanding the nuances of different metody drukowania and their specific design rules is crucial for success.
Achievable Precision: Tolerance, Surface Finish, and Dimensional Accuracy in Metal AM
While metal additive manufacturing unlocks unparalleled geometric freedom, it’s crucial for engineers and procurement managers to understand the levels of precision, surface finish, and dimensional accuracy achievable with current technologies, particularly for functional features like internal cooling channels. These factors directly impact component performance (e.g., flow rates, pressure drops, heat transfer) and the need for subsequent post-processing steps. The precision achievable is not a single number but depends on various factors including the specific AM process (LPBF, EBPF), machine calibration, material, part size and geometry, build orientation, and post-processing steps undertaken.
Dimensional Accuracy and Tolerances:
Dimensional accuracy refers to how closely the printed part conforms to the dimensions specified in the CAD model. Tolerances define the permissible range of variation for a given dimension.
- Typical Achievable Tolerances: For metal PBF processes, typical dimensional accuracy is often cited in the range of:
- $ \pm 0.1 $ mm to $ \pm 0.2 $ mm ($ \pm 0.004 $ in to $ \pm 0.008 $ in) for smaller features (e.g., below 100 mm).
- $ \pm 0.1% $ to $ \pm 0.2% $ of the nominal dimension for larger features.
- Factors Influencing Accuracy:
- Machine Calibration: Regular calibration of the laser/electron beam spot size, scanner positioning, and build platform leveling is critical. High-end machines, like those potentially used or supplied by Met3dp, often incorporate advanced calibration and monitoring systems.
- Thermal Effects: Shrinkage during cooling and residual stresses built up during the layer-wise process can cause warping and distortion, affecting final dimensions. Process simulation and optimized support strategies help mitigate this. EBPF, with its high build chamber temperatures, generally experiences lower residual stress and potentially less distortion than LPBF for certain geometries/materials.
- Part Geometry & Size: Large or complex parts are more prone to thermal distortion. Thin walls or cantilevered features may deform more easily.
- Orientacja budynku: The orientation affects how thermal stresses accumulate and how features are sliced, impacting accuracy.
- Właściwości materiału: Different materials have different coefficients of thermal expansion and shrinkage behavior.
- Przetwarzanie końcowe: Stress relief heat treatments can cause minor dimensional changes. Support removal and machining steps obviously alter dimensions in targeted areas.
- Achieving Tighter Tolerances: For critical interfaces, mating surfaces, or features requiring higher precision than achievable “as-built,” post-process CNC machining is typically employed. It’s essential to include sufficient machining allowance (stock) in the AM design for these features.
Surface Finish (Roughness):
Surface finish, often quantified by average roughness (Ra), is a critical characteristic, especially for internal channels. The layer-wise nature of PBF results in surfaces that are inherently rougher than machined or cast surfaces.
- Typical As-Built Surface Roughness:
- LPBF: Often ranges from Ra=6μm to 20μm (240μin to 800μin) or sometimes higher, depending on orientation and parameters. Upward-facing surfaces tend to be smoother than downward-facing (overhang) surfaces or vertical walls which show layer lines.
- EBPF: Tends to produce rougher surfaces than LPBF, potentially in the Ra=20μm to 35μm range or more, due to larger powder particle sizes and higher beam energy causing more melt pool agitation.
- Factors Influencing Surface Roughness:
- Grubość warstwy: Thinner layers generally result in smoother surfaces, especially on angled features, but increase build time.
- Powder Particle Size Distribution (PSD): Finer, more spherical powders (like those produced by Met3dp’s advanced atomization) typically lead to smoother surfaces and better packing density.
- Process Parameters: Laser/electron beam power, scan speed, and strategy significantly impact melt pool stability and resulting surface texture.
- Orientacja budynku: Surfaces parallel to the build plate (upward-facing) are usually the smoothest. Angled surfaces exhibit a “stair-stepping” effect dependent on layer thickness. Vertical walls show distinct layer lines. Downward-facing surfaces (supported or near-supported) are typically the roughest due to contact with partially sintered powder or support structures.
- Impact of Roughness on Internal Channels:
- Increased Pressure Drop: Rougher channel walls increase friction losses, leading to a higher pressure drop for the coolant flow compared to smooth channels. This must be accounted for in the system design.
- Altered Heat Transfer: While roughness can sometimes slightly increase turbulence and heat transfer, it’s often an uncontrolled effect. Predictable heat transfer relies on well-defined geometries. Excessive roughness can also trap contaminants or provide initiation sites for fouling.
- Fatigue Life: High surface roughness can act as stress concentrators, potentially reducing the fatigue life of the component, especially under cyclic loading.
- Poprawa wykończenia powierzchni: If the as-built roughness is unacceptable, post-processing techniques like Abrasive Flow Machining (AFM), chemical polishing, or micro-machining are required (discussed in the next section).
Inspection and Quality Control:
Verifying the dimensional accuracy and internal surface integrity of complex AM parts is crucial, especially for aerospace applications.
- Coordinate Measuring Machines (CMM): Used to verify external dimensions and critical features with high accuracy.
- Optical/Laser Scanning: Provides high-resolution 3D scans of the external surfaces for comparison against the CAD model.
- Computed Tomography (CT) Scanning: The primary method for non-destructively inspecting internal features. CT scanning can:
- Verify the geometry and dimensions of internal channels.
- Detect internal defects like porosity or trapped powder.
- Assess wall thickness variations.
- Provide detailed internal surface analysis (though resolution limits apply).
- Flow Testing: Functional testing by flowing fluid through the cooling channels can verify passage clearance and measure actual pressure drop, comparing it against design predictions.
Summary Table: Precision in Metal AM
Parametr | Typical As-Built Range (PBF) | Key Influencing Factors | Improvement Methods |
---|---|---|---|
Tolerance (Small) | $ \pm 0.1 $ to $ \pm 0.2 $ mm | Machine calibration, thermal effects, orientation | Process optimization, CNC Machining |
Tolerance (Large) | $ \pm 0.1% $ to $ \pm 0.2% $ | Thermal effects, part size, material, supports | Process simulation, Stress relief, CNC Machining |
Surface Roughness (Ra) | $ 6-20 \mu m $ (LPBF), $ 20-35+ \mu m $ (EBPF) | Layer thickness, powder quality, orientation, parameters | Post-processing (AFM, Polishing, etc.) |
Cechy wewnętrzne | Verifiable via CT Scan | Printability limits, powder removal efficiency | DfAM for inspection, Flow testing |
Export to Sheets
Understanding these achievable levels of precision allows engineers to design components appropriately, specifying post-processing steps where necessary, and enables procurement managers to set realistic expectations and quality requirements when sourcing metal AM parts with internal cooling structures. Partnering with experienced providers who maintain tight process control and possess advanced metrology capabilities is essential for mission-critical aerospace components.
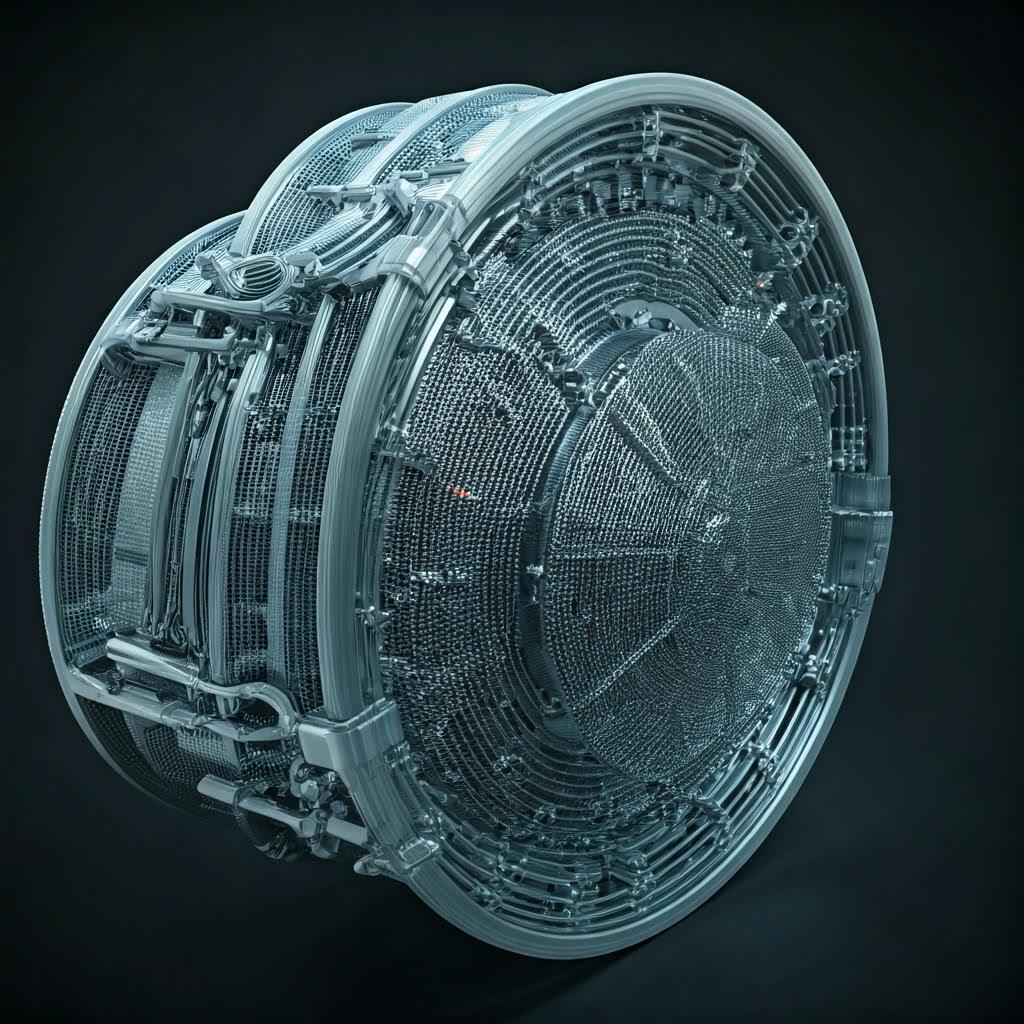
Essential Post-Processing for Aerospace-Grade Cooling Components
Parts produced by metal additive manufacturing, especially those intended for demanding aerospace applications like internally cooled components, rarely come straight out of the printer ready for final use. A series of carefully controlled post-processing steps is almost always required to achieve the necessary material properties, dimensional tolerances, surface finish, and overall integrity demanded by stringent aerospace standards (e.g., AS9100). Omitting or improperly executing these steps can compromise component performance and safety.
Common Post-Processing Steps:
- Ulga w stresie:
- Why: The rapid heating and cooling cycles inherent in PBF processes induce significant residual stresses within the printed part. These stresses can cause distortion (warping) upon removal from the build plate, lead to cracking, and negatively impact mechanical properties, particularly fatigue life.
- How: Typically performed while the part is still attached to the build plate (if possible) in a controlled atmosphere furnace. The part is heated to a specific temperature (below the aging or annealing temperature for the alloy), held for a period, and then slowly cooled. This allows internal stresses to relax without significantly altering the microstructure. Specific cycles depend heavily on the material (e.g., different temperatures for IN625 vs. AlSi10Mg) and part geometry.
- Part Removal from Build Plate:
- Why: The part is fused to a thick metal build plate during printing.
- How: Commonly done using wire Electrical Discharge Machining (EDM) or a bandsaw. Care must be taken not to damage the part, and this step is usually performed po stress relief to prevent distortion upon release.
- Usunięcie konstrukcji wsporczej:
- Why: Support structures are necessary during the build for overhangs and complex features but must be removed afterwards. Internal supports within cooling channels present a significant challenge.
- How:
- Ręczne usuwanie: Supports in accessible areas are often removed manually using pliers, cutters, and grinders. This is labor-intensive and requires skilled technicians.
- CNC Machining: Can be used to remove support connection points precisely.
- Abrasive Flow Machining (AFM): Can sometimes help smooth support remnants in channels but is primarily a finishing process.
- Chemical Etching: In some cases (depending on material compatibility), chemical dissolution might be possible, but it’s less common and requires careful control.
- Design for Removal: The best strategy is often DfAM to minimize or eliminate internal supports or design them for easier breakage and removal.
- Prasowanie izostatyczne na gorąco (HIP):
- Why: Although AM processes aim for high density, microscopic internal voids or pores (like keyhole porosity or lack-of-fusion defects) can sometimes remain. These pores can act as stress concentrators, significantly reducing fatigue life and fracture toughness – unacceptable for critical aerospace parts. HIPing simultaneously applies high temperature and high inert gas pressure (typically Argon) to the part.
- How: The combination of heat (reducing material yield strength) and external pressure collapses internal voids, effectively eliminating porosity and achieving near 100% theoretical density. HIP cycles (temperature, pressure, time) are specific to the alloy (e.g., IN625 HIPing differs significantly from AlSi10Mg) and must be carefully controlled to achieve densification without causing unwanted microstructural changes or part distortion. HIPing is often considered mandatory for Class A aerospace flight hardware produced by AM.
- Heat Treatment (Solution Annealing, Aging):
- Why: Beyond stress relief and HIP, further heat treatments are often required to achieve the desired final microstructure and mechanical properties (e.g., hardness, tensile strength, ductility) specified for the chosen alloy. The as-built microstructure from AM processes is often fine-grained and non-equilibrium, and may not represent the optimal state for the material.
- How: Specific heat treatment cycles (e.g., solution annealing followed by aging for precipitation-hardening alloys like IN625 or certain aluminum alloys) are performed in controlled atmosphere furnaces. These cycles are typically defined by aerospace material specifications (e.g., AMS standards) and must be precisely followed and documented.
- CNC Machining:
- Why: To achieve tight tolerances on critical mating surfaces, sealing faces, bearing bores, or aerodynamic profiles that cannot be met by the as-built AM process. Also used to create features difficult to print accurately (e.g., very fine holes, sharp edges).
- How: Standard multi-axis CNC milling, turning, or grinding operations are used. Requires careful fixture design to hold the complex AM part geometry securely without distortion. Sufficient material stock must be left on features requiring machining during the AM design phase.
- Wykończenie powierzchni:
- Why: The as-built surface roughness of AM parts, particularly internal channels, is often too high for optimal performance (flow efficiency, fatigue life).
- How:
- External Surfaces: Grinding, polishing, bead blasting, tumbling can be used.
- Internal Channels: This is more challenging. Common methods include:
- Abrasive Flow Machining (AFM): Pumping a putty-like abrasive media back and forth through the channels under pressure. The abrasive particles smooth the internal surfaces and round sharp edges. Effective but requires careful media selection and process control.
- Chemical Polishing/Etching: Using chemical solutions to preferentially remove material peaks, thus smoothing the surface. Requires careful control of chemical exposure time and temperature, and material compatibility is key.
- Micro-Machining/Deburring: Specialized long-reach tools might be used for accessible portions of channels.
- Powłoka:
- Why: For applications requiring enhanced thermal protection, wear resistance, or environmental resistance beyond the base material capabilities.
- How: Techniques like Thermal Barrier Coatings (TBCs) – often ceramic coatings applied via plasma spray or EBPVD – are common on turbine components to further reduce metal temperatures. Other wear-resistant or corrosion-resistant coatings may also be applied depending on the application. Surface preparation before coating is critical.
- Inspection and Quality Control:
- Why: Essential throughout the post-processing sequence to ensure each step is performed correctly and to verify the final part meets all specifications.
- How: Includes dimensional checks (CMM, scanning), surface roughness measurements, NDT (CT scanning for internal integrity, FPI/MPI for surface defects), material property verification (tensile testing, hardness testing on sample coupons), and flow testing.
Integrating Post-Processing into the Workflow:
The sequence and necessity of these steps depend on the specific part, material, and application requirements. For a critical aerospace component like an internally cooled turbine blade made from IN625, a likely sequence might be: Stress Relief -> Part Removal -> Support Removal -> HIP -> Solution & Aging Heat Treatment -> CNC Machining (critical features) -> AFM (internal channels) -> TBC Coating -> Final Inspection.
Procurement managers need to ensure that their chosen AM service provider has validated capabilities and certified processes for all required post-processing steps, not just the printing itself. Companies like Met3dp, offering comprehensive solutions, understand the importance of this integrated workflow, from high-quality powder production to final part qualification, ensuring a streamlined and reliable supply chain for aerospace-grade components. Failure to properly manage post-processing can negate the benefits achieved through advanced AM design.
Overcoming Challenges in Printing Complex Internal Geometries
While metal AM enables the creation of highly complex internal cooling channels, the process is not without its challenges. Successfully manufacturing these intricate geometries requires careful control over the entire additive process, from design and material selection to printing parameters and post-processing. Anticipating and mitigating potential issues is key to achieving high yields and reliable components.
Common Challenges and Mitigation Strategies:
- Warping and Distortion:
- Wyzwanie: Uneven heating and cooling during the layer-wise fusion process lead to the buildup of internal residual stresses. These stresses can cause the part to warp or distort, especially thin walls or large flat sections, potentially deviating from the intended geometry or even causing build failures (e.g., collision with the recoater blade).
- Mitigation:
- Thermal Simulation: Using Finite Element Analysis (FEA) to predict stress accumulation and distortion based on scan strategy and geometry before printing.
- Optimized Build Orientation: Selecting an orientation that minimizes large flat surfaces parallel to the build plate and reduces overhangs.
- Support Strategy: Using intelligently designed support structures (solid, lattice, conical) not only anchors the part but also helps conduct heat away, reducing thermal gradients. Support parameters (e.g., tooth size, connection strength) must be optimized.
- Scan Strategy Optimization: Using techniques like island scanning, checkerboard patterns, or adjusting scan vector lengths and rotations can distribute heat more evenly and reduce localized stress peaks.
- Process Parameters: Fine-tuning parameters like laser power, scan speed, and layer thickness can influence the thermal profile.
- Platform Heating (LPBF): Pre-heating the build plate reduces the temperature gradient between the molten pool and the surrounding part/powder.
- High-Temperature Processing (EBPF): EBPF inherently uses high build chamber temperatures (>600∘C), which significantly reduces residual stress during the build compared to typical LPBF.
- Ulga w stresie: Performing a stress relief heat treatment before removing the part from the build plate is crucial.
- Residual Stress Management:
- Wyzwanie: Even if warping is controlled, high residual stresses can remain in the part, negatively impacting fatigue life, fracture toughness, and potentially causing delayed cracking.
- Mitigation:
- All strategies for minimizing warping also help reduce residual stress.
- Post-Build Heat Treatments: Stress relief, HIP, and annealing cycles are critical for reducing residual stresses to acceptable levels. The effectiveness depends on the specific cycle parameters (temperature, time).
- Process Selection: EBPF generally results in lower residual stress than LPBF due to the high process temperature.
- Measurement & Validation: Techniques like X-ray Diffraction (XRD) or contour method can be used to measure residual stresses and validate the effectiveness of mitigation strategies.
- Powder Removal from Internal Channels:
- Wyzwanie: Ensuring complete removal of unfused powder from long, narrow, tortuous internal channels is a major hurdle. Trapped powder adds weight, can obstruct flow, and poses a contamination risk.
- Mitigation:
- DfAM for Powder Removal: Designing channels with adequate diameter, smooth bends, access ports, and avoiding dead ends (as discussed previously).
- Optimized Build Orientation: Orienting the part to facilitate powder drainage via gravity during the build and de-powdering process.
- De-Powdering Procedures: Using controlled vibration tables, compressed air jets (potentially pulsed), and sometimes vacuum systems. Requires careful manipulation of the part.
- Flushing: For some materials/applications, flushing with compatible fluids might aid removal.
- CT Scanning: Essential for verifying complete powder removal. If trapped powder is detected, further cleaning attempts or part rejection may be necessary.
- Porosity Defects:
- Wyzwanie: Small voids within the printed material can arise from gas entrapment (gas porosity, often spherical) or incomplete melting/fusion between layers or scan tracks (lack-of-fusion porosity, often irregular). Porosity severely degrades mechanical properties.
- Mitigation:
- High-Quality Powder: Using powder with high sphericity, good flowability, low internal gas content, and controlled particle size distribution (like Met3dp’s) is fundamental. Low-quality powder is a major source of defects.
- Optimized Process Parameters: Developing and validating robust parameter sets (power, speed, hatch spacing, layer thickness, focus) specific to the material and machine to ensure complete melting and fusion. Requires extensive Design of Experiments (DOE).
- Shielding Gas Control (LPBF): Maintaining a high-purity inert gas atmosphere (e.g., Argon, Nitrogen) with controlled flow is critical to prevent oxidation and remove processing fumes/spatter that can interfere with the melt pool.
- Vacuum Environment (EBPF): EBPF operates under high vacuum, minimizing gas-related porosity.
- Prasowanie izostatyczne na gorąco (HIP): As discussed, HIP is highly effective at closing internal porosity (though it cannot fix surface-connected defects or lack-of-fusion defects related to contamination).
- In-Situ Monitoring: Advanced AM systems incorporate sensors (e.g., thermal cameras, photodiodes) to monitor the melt pool in real-time, potentially detecting anomalies indicative of pore formation.
- Ensuring Channel Integrity and Preventing Blockages:
- Wyzwanie: Besides trapped powder, channels can become blocked or partially constricted due to printing defects like dross formation, delamination, or excessive roughness on downward-facing surfaces within the channel.
- Mitigation:
- Robust Process Parameters & Control: Ensuring stable melting and solidification.
- DfAM: Avoiding designs that push the limits of unsupported overhangs within channels. Using self-supporting shapes where possible.
- Careful Support Design (if needed): Ensuring internal supports don’t inadvertently block channels after removal attempts.
- Flow Testing: Performing functional flow tests to confirm passages are clear and meet pressure drop requirements.
- CT Scanning: Visualizing the entire channel path to identify constrictions or blockages.
Overcoming these challenges requires a combination of robust design practices (DfAM), high-quality materials and equipment, meticulously developed and validated process parameters, comprehensive post-processing, and rigorous quality control. Partnering with an experienced additive manufacturing provider like Met3dp, which combines materials expertise, advanced wyposażenie (like their SEBM printers with industry-leading volume and accuracy), and a deep understanding of process-property relationships, significantly increases the likelihood of successfully producing complex and reliable aerospace components with internal cooling structures.
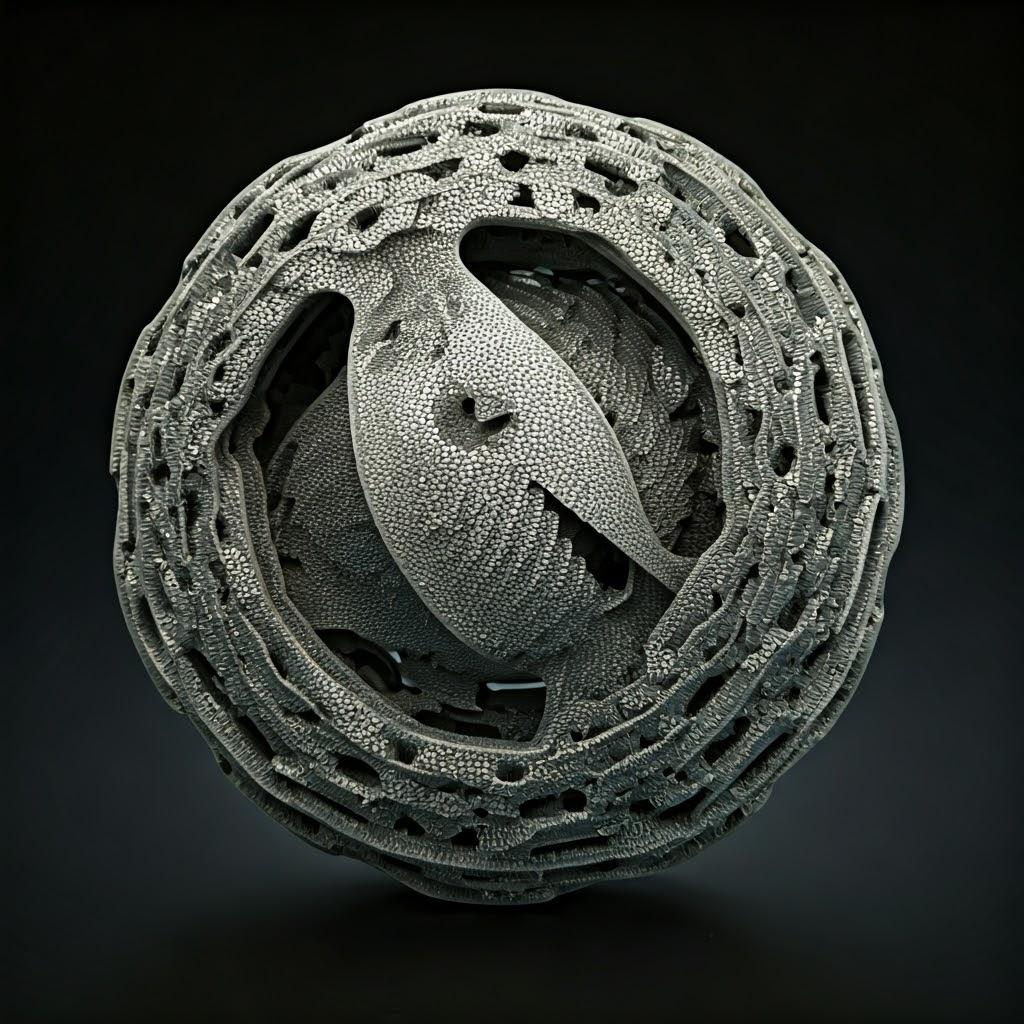
Selecting the Right Metal Additive Manufacturing Partner for Aerospace Components
Choosing a supplier or partner for manufacturing critical aerospace components, such as those with complex internal cooling structures, is a decision with significant implications for quality, reliability, cost, and schedule. The unique nature of additive manufacturing, combined with the stringent requirements of the aerospace industry, necessitates a rigorous evaluation process that goes beyond traditional supplier vetting. Procurement managers and engineering teams must look for partners who demonstrate not only proficiency in printing but also deep expertise across the entire AM value chain, from material science to final part qualification. Selecting the right partner is crucial for mitigating risks and successfully implementing AM for flight-critical applications.
Key Criteria for Evaluating Metal AM Partners:
- Aerospace Certifications and Compliance: This is non-negotiable for flight hardware.
- AS9100 Certification: The internationally recognized Quality Management System (QMS) standard for the aviation, space, and defense industries. Certification demonstrates a provider’s commitment to quality, traceability, and continuous improvement, tailored to aerospace requirements. Lack of AS9100 is typically a disqualifier for critical component manufacturing.
- ITAR Compliance: If dealing with defense-related projects or technical data subject to U.S. export controls, the provider must be registered and compliant with the International Traffic in Arms Regulations.
- Nadcap Accreditation: While AS9100 covers the overall QMS, Nadcap (National Aerospace and Defense Contractors Accreditation Program) provides specific process accreditations for special processes like heat treatment, NDT, welding, and potentially additive manufacturing itself as standards evolve. Accreditation in relevant post-processing areas is highly desirable.
- Proven Aerospace Experience and Expertise:
- Track Record: Look for providers with documented experience in manufacturing aerospace components, particularly using the specified materials (e.g., IN625, AlSi10Mg, Ti-6Al-4V) and geometries (complex internal channels, thin walls). Case studies, references, and part examples are valuable indicators.
- Engineering Support: Does the partner offer robust engineering support? This includes DfAM expertise to help optimize designs for printability and performance, simulation capabilities (thermal, stress, process), and troubleshooting skills. A partner should be able to collaborate effectively with your design team.
- Materials Expertise: Deep understanding of metallurgy, powder characteristics, process-property relationships for aerospace alloys, and powder handling protocols is essential. Providers who manufacture their own high-quality powders, like Met3dp, often possess superior materials expertise and control. Their use of advanced Gas Atomization and PREP technologies ensures powders meet the high sphericity, flowability, and purity standards demanded by aerospace.
- Equipment and Process Capabilities:
- Technology Alignment: Does the provider have the right AM technology (e.g., LPBF, EBPF) best suited for your material and application? Do they have experience with the specific alloy you require?
- Machine Fleet: Assess the number, type, age, and condition of their AM machines. Redundancy provides capacity and reduces risk if one machine is down for maintenance. Look for industry-leading equipment known for accuracy and reliability, aligning with Met3dp’s focus on providing printers with exceptional print volume, accuracy, and reliability for mission-critical parts.
- Process Control & Monitoring: What level of process control and in-situ monitoring do they employ? Documented procedures for machine calibration, parameter control, and environmental monitoring (e.g., oxygen levels in LPBF) are critical for repeatability.
- Powder Management and Traceability:
- Powder Quality Control: How do they verify the quality of incoming powder? What are their procedures for handling, storing, sieving, and recycling powder to prevent contamination and maintain consistency? Full traceability from powder batch to final part is essential.
- Certyfikacja materiałów: Can they provide material test certificates (e.g., chemical composition, Particle Size Distribution) for each powder batch used?
- In-House Post-Processing Capabilities:
- Integrated Workflow: Providers with comprehensive in-house capabilities for key post-processing steps (stress relief, HIP, heat treatment, basic machining, NDT) generally offer better control, potentially faster lead times, and clearer accountability compared to those heavily reliant on outsourcing multiple critical steps.
- Validated Processes: Ensure their post-processing operations (especially heat treatment and HIP) are validated and meet relevant aerospace specifications (e.g., AMS standards).
- Quality Management System (QMS) and Inspection:
- Robust QMS: Beyond AS9100, review their detailed quality manual, procedures for non-conformance management, corrective actions, and process validation.
- Metrology and NDT Capabilities: Do they possess advanced inspection equipment suitable for complex AM parts? This includes CMMs, laser scanners, and crucially, high-resolution CT scanning capabilities for verifying internal channel integrity and detecting subsurface defects. Ensure their inspection procedures are thorough and documented.
- Supply Chain Management and Capacity:
- Skalowalność: Can they handle your prototype volumes as well as potential future production scaling?
- Risk Management: What are their contingency plans for equipment downtime, material shortages, or other disruptions?
- Communication & Project Management: Evaluate their responsiveness, communication protocols, and project management approach.
Why Partner with Met3dp?
Met3dp emerges as a compelling partner by addressing many of these critical criteria. Headquartered in Qingdao, China, they specialize in additive manufacturing solutions tailored for industrial applications across aerospace, medical, automotive, and manufacturing sectors.
- Integrated Solutions: Met3dp provides comprehensive solutions spanning SEBM printers, advanced metal powders manufactured using cutting-edge Gas Atomization and PREP technologies, and application development services. This vertical integration offers greater control over the critical inputs to the AM process.
- Material Excellence: Their focus on producing high-quality spherical metal powders (including IN625, AlSi10Mg, Ti alloys, CoCrMo, and custom alloys) ensures a reliable source of aerospace-grade materials optimized for AM.
- Technology Focus: Their expertise in both equipment (SEBM printers known for accuracy and reliability) and materials provides a strong foundation for producing demanding components.
- Ekspertyza: Decades of collective expertise in metal additive manufacturing enables them to partner with organizations to implement 3D printing effectively and accelerate digital manufacturing transformations.
Selecting a partner like Met3dp, with a strong foundation in materials science, advanced equipment, and a focus on industrial applications, significantly enhances the probability of success when manufacturing complex, mission-critical aerospace components with internal cooling structures.
Understanding Cost Drivers and Lead Times for AM Internal Cooling Structures
While metal additive manufacturing offers significant performance and design advantages for internal cooling structures, it’s essential for procurement managers and engineers to have a realistic understanding of the associated costs and lead times. AM is not always the cheapest or fastest option, particularly compared to traditional methods for simple geometries or extremely high volumes. However, its value often lies in enabling performance levels or complexities that are otherwise unattainable, making a direct cost-per-part comparison sometimes misleading. Understanding the key drivers helps in making informed decisions and managing project budgets and schedules.
Major Cost Drivers in Metal AM:
- Koszt materiałów:
- Powder Price: High-performance aerospace alloys like IN625 or specialized titanium alloys are inherently expensive raw materials. Powder production via gas atomization or PREP is a sophisticated process, adding to the cost. Prices are typically quoted per kilogram. AlSi10Mg is generally less expensive than nickel or titanium alloys.
- Powder Usage: The amount of powder consumed depends not only on the part’s weight but also on the support structures needed and the volume of the build chamber (some powder may not be fully recyclable indefinitely). Efficient nesting of parts on the build plate can improve material utilization.
- Recykling proszków: While unfused powder can often be sieved and reused, there are limits. Recycling strategies, quality control on recycled powder, and refresh rates (mixing virgin and used powder) impact overall material cost and quality consistency. Providers with robust powder management systems, like those emphasized by Met3dp, help optimize material usage.
- Machine Time (Depreciation & Operation):
- Koszt maszyny: Industrial metal AM systems represent a significant capital investment ($500K to >$2M). This cost is amortized over the machine’s operational lifetime and factored into hourly rates.
- Czas budowy: This is often the dominant factor for complex or large parts. Build time is influenced by:
- Part Volume: The amount of material being fused.
- Part Height: The number of layers required (directly impacts time).
- Złożoność: Scan time depends on the intricacy of each layer.
- Nesting Efficiency: How many parts can be printed simultaneously within the build volume.
- Layer Thickness & Parameters: Thinner layers improve resolution but increase build time. Optimized parameters balance speed and quality.
- Koszty operacyjne: Includes energy consumption (lasers/electron beams, heating), inert gas (LPBF), maintenance, and consumables.
- Koszty pracy:
- Pre-Processing: CAD file preparation, build setup, simulation work.
- Machine Operation: Monitoring the build process.
- Przetwarzanie końcowe: This can be highly labor-intensive, including setup, de-powdering, part removal, support removal (often manual), heat treatment cycles, machining setup and operation, surface finishing, and inspection. Skilled labor is required for many of these steps.
- Koszty przetwarzania końcowego:
- Consumables & External Services: Costs associated with furnace time (stress relief, HIP, heat treatment), machining tools, finishing media (AFM), coatings, NDT services (especially CT scanning), and any outsourced processes.
- HIP: Hot Isostatic Pressing is a significant cost addition due to the specialized equipment and long cycle times but is often mandatory for aerospace-grade properties.
- Quality Assurance and Inspection:
- Metrology: Time and equipment cost for CMM, scanning.
- NDT: CT scanning, in particular, can be expensive but is essential for internal feature verification. FPI, MPI also add cost.
- Destructive Testing: Material testing on representative samples/coupons built alongside the parts.
- Documentation: Generating compliance reports and traceability documentation requires labor.
- Non-Recurring Engineering (NRE):
- Initial Design Optimization (DfAM): Adapting or creating designs specifically for AM.
- Process Parameter Development: Especially for new alloys or highly complex geometries, significant effort may be needed to establish optimal, robust printing parameters.
- Fixture Design: Creating custom fixtures for post-processing (machining, inspection).
Lead Time Factors:
Lead time is the total time from order placement to part delivery. For complex AM aerospace parts, it can range from days (for simple prototypes) to many weeks or even months.
- Design & Engineering: Time for DfAM review, simulation, build file preparation.
- Queue Time: The part must wait for an available machine with the correct material loaded. This can be a significant variable depending on the provider’s backlog.
- Czas budowy: As described above, can range from hours to many days depending on size and complexity.
- Przetwarzanie końcowe: This often constitutes a large portion of the total lead time. Stress relief, HIP cycles, heat treatments, machining, finishing, and inspection sequences can cumulatively take days or weeks. Outsourced steps add logistical delays.
- Inspection & Qualification: Thorough inspection and documentation review takes time.
- Wysyłka: Logistics time.
Cost & Lead Time Summary Table:
Czynnik | Kluczowe czynniki napędowe | Wpływ na koszty | Impact on Lead Time | Mitigation / Optimization |
---|---|---|---|---|
Materiał | Alloy type, powder price, part volume, supports, recycling efficiency | Wysoki | Niski | DfAM (lightweighting), efficient nesting, robust powder mgmt. |
Machine Time | Part height/volume/complexity, machine rate, nesting | Wysoki | Wysoki | DfAM (optimize height), nesting, faster parameters (trade-offs) |
Praca | Build prep, supervision, de-powdering, support removal, finishing, inspection | Umiarkowany-wysoki | Umiarkowany | Automation (future), DfAM (reduce supports), efficient workflow |
Przetwarzanie końcowe | HIP, heat treatment, machining complexity, finishing requirements | Umiarkowany-wysoki | Wysoki | DfAM (minimize machining), integrated provider capabilities |
Quality/Inspect | CT scanning, NDT methods, documentation level | Umiarkowany | Umiarkowany | Risk-based inspection plan, efficient reporting |
NRE | Design complexity, new material/process development | Różne | Umiarkowany | Leverage provider expertise, use established parameters |
Queue Time | Provider backlog, machine availability | Niski | Varies (High risk) | Choose provider with capacity, good planning |
Export to Sheets
Understanding these drivers allows for better cost estimation and realistic schedule planning. While AM might appear expensive initially, evaluating the total lifecycle cost, including performance gains, reduced assembly, and potentially longer component life enabled by superior cooling, often reveals a compelling value proposition for aerospace applications.
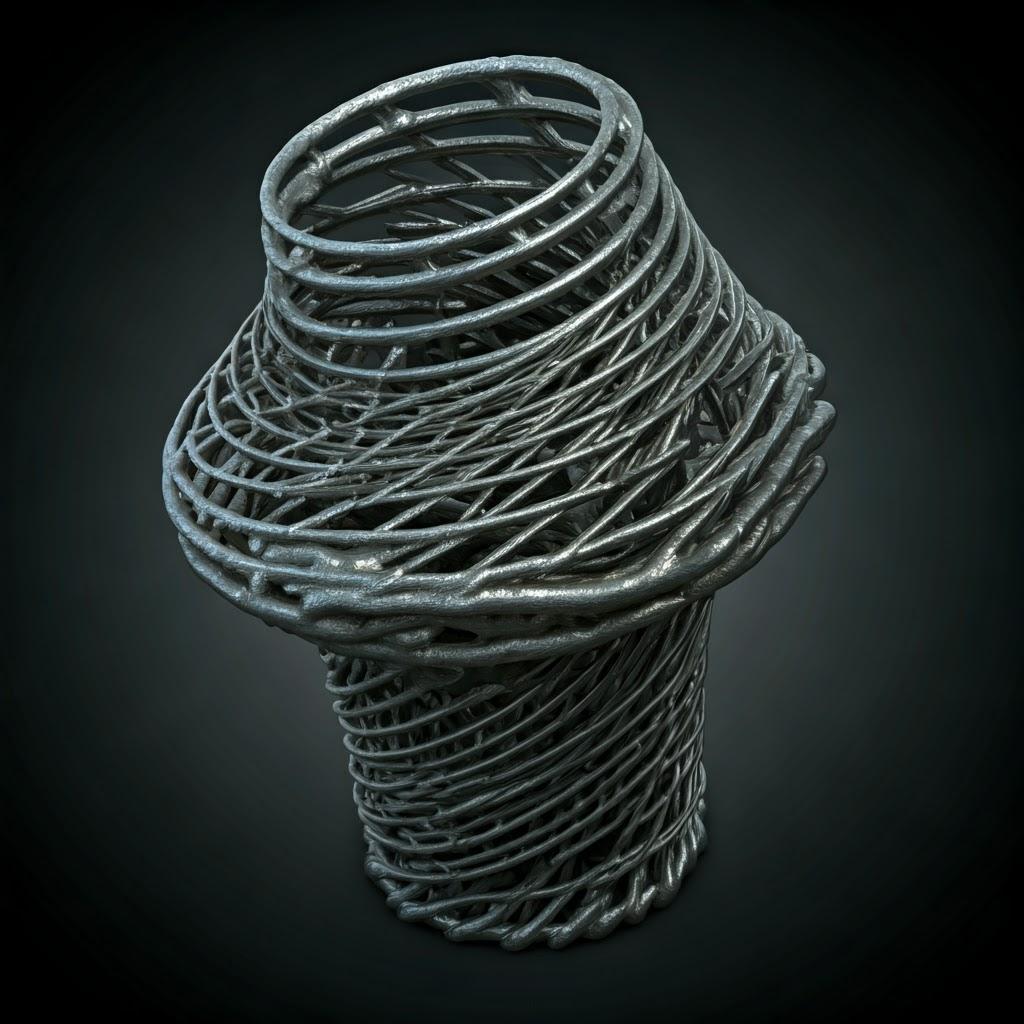
Frequently Asked Questions (FAQ) about Metal 3D Printed Internal Cooling Channels
Here are some common questions engineers and procurement managers ask when considering metal additive manufacturing for components with internal cooling structures:
1. How does the cost of metal AM for internal cooling channels compare to traditional methods like investment casting?
- Odpowiedź: The cost comparison is complex and depends heavily on geometry, material, volume, and quality requirements.
- Prototypes & Low Volumes: AM is often tańszy oraz faster because it avoids high tooling costs (molds, cores) associated with casting.
- Highly Complex Geometries: For internal channel designs impossible or extremely difficult to cast (e.g., conformal channels, integrated lattices, fine turbulators), AM might be the tylko feasible option, making direct cost comparison difficult. The value lies in enabling performance, not just replicating an existing design.
- Moderate Complexity, Higher Volumes: For geometries achievable by casting, investment casting typically becomes bardziej opłacalny on a per-part basis as volumes increase (amortizing tooling costs). However, AM costs are also decreasing with technology maturation.
- Total Value Proposition: Consider factors beyond per-part cost: AM enables part consolidation (reduced assembly cost/time), lightweighting (fuel savings), potentially longer component life (better cooling), and faster design iteration. When these system-level benefits are included, AM can be cost-competitive even at moderate volumes for the right application.
2. How can we be certain that internal cooling channels are completely free of powder and defects after printing?
- Odpowiedź: Ensuring internal channel clearance and integrity is critical and relies on a multi-faceted approach:
- DfAM: Designing channels for effective powder removal (access ports, smooth paths, sufficient diameter) is the first line of defense.
- Controlled De-powdering: Utilizing optimized procedures involving vibration, controlled compressed air, and potentially flushing.
- Badania nieniszczące (NDT): High-resolution industrial Computed Tomography (CT) scanning is the primary method to non-destructively visualize the entire internal channel network. It can detect trapped powder, blockages, significant porosity, cracks, and dimensional deviations within the channels.
- Flow Testing: Performing airflow or liquid flow tests measures the actual pressure drop across the cooling circuit and compares it to design specifications. This provides functional verification that the channels are clear and appropriately sized. Significant deviation indicates a blockage or geometric inconsistency.
- Quality Management: Partnering with an experienced provider like Met3dp, which emphasizes process control and rigorous quality assurance protocols (often compliant with AS9100), provides confidence in the procedures used for printing and cleaning.
3. Can existing component designs originally made for casting be directly printed using metal AM?
- Odpowiedź: While it’s technically possible to print a geometry based on an old casting design, it’s generally not advisable and misses the key benefits of AM.
- Lack of Optimization: Casting designs are inherently constrained by the casting process (draft angles, core limitations, uniform wall thicknesses). Directly printing such a design fails to leverage AM’s geometric freedom for improved cooling efficiency, lightweighting, or part consolidation.
- Potential Printability Issues: Features optimized for casting (e.g., sharp internal corners, features relying on core support) might be difficult or inefficient to print using AM and may require excessive support structures.
- Recommendation: To fully benefit from AM, components should ideally be redesigned lub optimized using DfAM principles. This might involve running topology optimization, redesigning cooling channels to be conformal, integrating heat transfer enhancement features, and consolidating multiple cast parts into a single printed component. Collaborating with AM experts during this redesign phase is highly recommended.
4. What is the expected fatigue life of aerospace components made with AM, especially considering internal channels and potentially rougher surfaces?
- Odpowiedź: The fatigue life of AM components is a critical consideration and depends heavily on the material, process parameters, post-processing (especially HIP and surface finishing), and design.
- Właściwości materiału: After proper post-processing (including HIP to close internal porosity and appropriate heat treatments), AM materials like IN625 and Ti-6Al-4V can achieve fatigue properties comparable or sometimes even przełożony (due to finer microstructures) to wrought or cast counterparts.
- Defect Control: Porosity and surface roughness are key factors that can degrade fatigue life by acting as crack initiation sites. Rigorous process control to minimize defects and effective post-processing (HIP for porosity, surface finishing for roughness) are crucial.
- Wykończenie powierzchni: The higher as-built surface roughness of AM, particularly on internal channel surfaces, can negatively impact fatigue life if not addressed. Post-processing techniques like AFM or chemical polishing can significantly improve the surface finish of internal channels, mitigating this risk.
- Design & Testing: Designs must account for fatigue loading, and extensive testing (using fatigue coupons built with the parts and potentially component-level fatigue testing) is required to validate the fatigue life for critical aerospace applications, following established certification protocols. Partnering with providers who understand these requirements and can produce parts with consistent, documented properties is essential.
Conclusion: The Future of Aerospace Thermal Management with Metal Additive Manufacturing
Metal additive manufacturing is undeniably reshaping the landscape of aerospace engineering, particularly in the critical domain of thermal management. The ability to fabricate components with highly complex, optimized internal cooling structures—geometries previously confined to the realm of imagination—represents a paradigm shift. As we’ve explored, AM technologies like LPBF and EBPF empower engineers to design and produce turbine blades, combustion chambers, rocket nozzles, and heat exchangers that push performance boundaries, enhance efficiency, and improve reliability in ways traditional manufacturing methods simply cannot match.
The advantages are clear: unprecedented design freedom leading to highly efficient conformal cooling channels and integrated heat transfer features; the ability to consolidate multiple parts into monolithic components, reducing weight and eliminating failure-prone joints; and the acceleration of design iteration and prototyping cycles. Materials like the high-temperature stalwart IN625 and the lightweight AlSi10Mg, when processed correctly using high-quality powders, enable the creation of components tailored to specific thermal and structural demands across diverse aerospace applications.
However, harnessing the full potential of AM requires navigating its complexities. Success hinges on embracing Design for Additive Manufacturing (DfAM), meticulously controlling the printing process to ensure dimensional accuracy and minimize defects, implementing essential post-processing steps like HIP and surface finishing, and rigorously verifying component integrity through advanced inspection techniques like CT scanning.
Critically, success also depends on strategic partnerships. Selecting the right metal additive manufacturing partner—one with proven aerospace certifications (AS9100), deep materials and process expertise, robust quality management systems, and comprehensive capabilities spanning the entire workflow—is paramount. Companies like Met3dp, with their focus on high-quality powder production using advanced atomization techniques, industry-leading printing equipment, and a commitment to providing integrated solutions, exemplify the type of partner needed to translate the promise of AM into flight-ready reality.
Looking ahead, the future of aerospace thermal management powered by metal AM appears even brighter. Ongoing advancements in materials science (new alloys), AM processes (faster printing, higher resolution, improved monitoring), simulation tools, and AI-driven generative design will continue to expand the possibilities. As the technology matures and costs potentially decrease, we can expect wider adoption of AM for increasingly critical and complex thermal management solutions, driving the next generation of more efficient, capable, and sustainable aircraft and spacecraft.
For organizations looking to explore how metal additive manufacturing can revolutionize their thermal management challenges and unlock new levels of performance, the journey begins with understanding the technology and engaging with experienced partners. We encourage you to contact Met3dp to explore how their cutting-edge systems, advanced metal powders, and application development services can power your organization’s additive manufacturing goals and help you navigate the exciting future of aerospace manufacturing.
Udostępnij
MET3DP Technology Co., LTD jest wiodącym dostawcą rozwiązań w zakresie produkcji addytywnej z siedzibą w Qingdao w Chinach. Nasza firma specjalizuje się w sprzęcie do druku 3D i wysokowydajnych proszkach metali do zastosowań przemysłowych.
Zapytaj o najlepszą cenę i spersonalizowane rozwiązanie dla Twojej firmy!
Powiązane artykuły
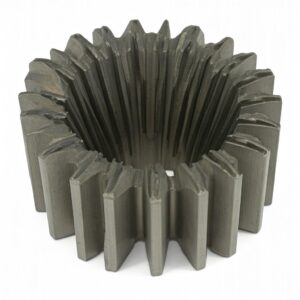
Wysokowydajne segmenty łopatek dysz: Rewolucja w wydajności turbin dzięki drukowi 3D w metalu
Czytaj więcej "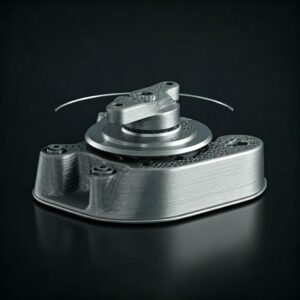
Drukowane w 3D mocowania dla samochodowych czujników radarowych: Precyzja i wydajność
Czytaj więcej "Informacje o Met3DP
Ostatnia aktualizacja
Nasz produkt
KONTAKT
Masz pytania? Wyślij nam wiadomość teraz! Po otrzymaniu wiadomości obsłużymy Twoją prośbę całym zespołem.
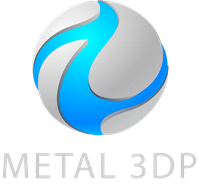
Proszki metali do druku 3D i produkcji addytywnej