Jet Turbine Disk Segments 3D Printed in Superalloys
Spis treści
Introduction: Revolutionizing Aerospace with 3D Printed Jet Turbine Disk Segments
The relentless pursuit of higher performance, greater efficiency, and unwavering safety defines the aerospace industry. At the heart of modern flight lies the jet engine, a marvel of engineering operating under conditions that push materials to their absolute limits. Within this intricate machinery, components like turbine disks and their constituent segments function as critical linchpins, enduring extreme temperatures and colossal stresses to harness energy and generate thrust. Traditionally, manufacturing these vital parts has involved complex, time-consuming, and often wasteful processes like forging and machining from large billets of exotic superalloys. However, a technological revolution is reshaping the landscape of aerospace manufacturing: Wytwarzanie przyrostowe metali (AM), more commonly known as metal Drukowanie 3D.
Metal AM represents a fundamental shift from subtractive methods (removing material) to additive ones (building layer by layer from metal powder). This paradigm shift unlocks unprecedented possibilities for designing and producing components previously deemed impossible or prohibitively expensive to make. For critical parts like jet turbine disk segments, AM offers a powerful toolkit to enhance performance, reduce weight, shorten development cycles, and optimize the entire manufacturing value chain. Imagine turbine components with intricate internal cooling channels perfectly conforming to the part’s surface, or structures algorithmically optimized to bear specific loads with minimal material usage – these are the realities enabled by additive manufacturing.
The true potential of AM in this demanding application is realized when combined with advanced materials specifically engineered for extreme environments. Nadstopy na bazie niklu, such as the renowned IN738LC (Inconel 738 Low Carbon) and the high-performance Haynes 282, stand out as materials of choice. These alloys possess exceptional high-temperature strength, creep resistance, and durability, making them indispensable for the punishing conditions inside a jet engine’s hot section. Additive manufacturing provides a viable, and often superior, pathway to transform these sophisticated superalloy powders into functional, flight-ready hardware.
Navigating this advanced manufacturing frontier requires deep expertise, cutting-edge technology, and high-quality materials. This is where Met3dp emerges as a pivotal partner for the aerospace industry. As a leading provider of comprehensive additive manufacturing solutions, headquartered in Qingdao, China, Met3dp specializes in both state-of-the-art metal 3D printing equipment and the high-performance metal powders essential for industrial applications. Our integrated approach ensures that engineers and procurement managers in aerospace have access not only to industry-leading print volume, accuracy, and reliability for mission-critical parts but also to the meticulously produced superalloy powders required to achieve superior mechanical properties and component integrity. We understand the unique challenges and stringent requirements of aerospace manufacturing and are dedicated to empowering organizations to leverage the transformative power of AM. This post will delve into the specifics of using metal 3D printing, particularly with IN738LC and Haynes 282 superalloys, to manufacture robust and optimized jet turbine disk segments, exploring the functions, benefits, material considerations, and processes involved.
The Critical Function of Jet Turbine Disk Segments
To appreciate the significance of applying additive manufacturing to jet turbine disk segments, one must first understand their incredibly demanding role within the engine’s architecture. The turbine section is the powerhouse of the jet engine, responsible for extracting energy from the high-temperature, high-pressure gas stream exiting the combustor. This extracted energy drives the compressor at the front of the engine and, in turbofan engines, the large fan that generates most of the thrust. The turbine typically consists of multiple stages, each comprising a set of stationary vanes and a rotating disk assembly with blades attached.
The turbine disk, often manufactured in segments for various design and manufacturing reasons, serves several critical functions:
- Blade Retention: Its primary role is to securely hold the numerous turbine blades, which are airfoil shapes that interact with the hot gas flow. The disk segments must feature precisely engineered slots or “firtrees” into which the blade roots are inserted, ensuring they remain firmly attached despite enormous centrifugal forces.
- Torque Transmission: As the hot gas impinges on the turbine blades, it forces the entire disk assembly to rotate at incredibly high speeds – often reaching tens of thousands of revolutions per minute (RPM). The disk must efficiently transmit this rotational torque along the engine shaft to power the compressor and fan.
- Structural Integrity: The disk segments form the backbone of the rotating turbine assembly. They must withstand not only the centrifugal loads from their own mass and the attached blades but also significant thermal stresses arising from steep temperature gradients between the hot rim (near the gas path) and the cooler bore (center).
The operating environment within the high-pressure turbine section is arguably the most hostile in the entire engine:
- Ekstremalne temperatury: Gas temperatures can exceed 1400circC or even higher in advanced engines, although the metal surface temperatures are typically managed (through cooling) to peaks around 850circC to 1100circC, depending on the stage and alloy limits. This is well into the regime where conventional metals lose their strength.
- Colossal Centrifugal Forces: At high rotational speeds, the stresses generated, particularly at the disk bore and blade attachment points, can reach hundreds of megapascals (MPa). The disk material must resist immediate fracture (yield strength) and long-term deformation (creep).
- Aggressive Atmosphere: The combustion gases are not only hot but also chemically reactive, containing oxygen and potentially corrosive species (like sulfur from fuel, or salts ingested from marine environments) that can attack the material surface (oxidation and hot corrosion).
- Complex Loading Cycles: Every flight involves engine start-up, varying thrust levels, and shutdown, imposing cyclic thermal and mechanical loads. This necessitates high resistance to Low Cycle Fatigue (LCF), driven primarily by engine cycles, and High Cycle Fatigue (HCF), induced by aerodynamic vibrations.
Failure of a turbine disk segment would be catastrophic, potentially leading to blade release, uncontained engine failure, and loss of the aircraft. Therefore, the material properties required are exceptionally demanding:
- High-Temperature Tensile Strength: To withstand instantaneous loads without yielding or fracturing.
- Odporność na pełzanie: To prevent gradual, time-dependent deformation under sustained stress at high temperatures, which could cause blades to loosen or interfere with stationary parts.
- Fatigue Resistance (LCF & HCF): To endure millions of loading cycles throughout the engine’s operational life without crack initiation and propagation.
- Oxidation and Hot Corrosion Resistance: To maintain surface integrity and load-bearing capability over thousands of flight hours.
- Wytrzymałość na złamania: To resist rapid crack propagation should a flaw or defect be present.
Traditionally, manufacturing turbine disks from superalloys involves complex forging operations followed by extensive and costly machining to achieve the final intricate shape, especially the firtree slots for the blades. These processes can be slow, generate significant material waste (poor buy-to-fly ratio), and inherently limit the geometric complexity achievable, potentially constraining optimal design for performance and cooling. This demanding application, with its critical safety implications and traditional manufacturing challenges, makes it a prime candidate for the disruptive potential of metal additive manufacturing.

Why Metal 3D Printing for Turbine Disk Segments?
Given the critical nature and harsh operating environment of jet turbine disk segments, coupled with the challenges of traditional manufacturing, metal additive manufacturing presents a compelling value proposition for aerospace engineers and procurement managers. The advantages extend beyond mere fabrication, enabling genuine performance enhancements and process efficiencies that redefine how these vital components are conceived and produced. Let’s explore the key benefits in detail:
1. Unprecedented Design Freedom (DfAM – Design for Additive Manufacturing): This is perhaps the most transformative advantage of AM. Unlike subtractive methods constrained by tool access and machining paths, AM builds parts layer by layer, liberating designers to create highly complex and optimized geometries.
- Complex Internal Cooling Channels: Turbine disks, especially in the high-pressure stages, require cooling to survive the extreme gas temperatures. AM allows the integration of intricate, conformal cooling channels directly within the disk structure, following the contours where cooling is most needed. These channels can have complex cross-sections and paths impossible to create via drilling or casting. Uderzenie: More effective cooling allows for higher turbine entry temperatures (boosting engine thermal efficiency and thrust) or enables the disk to run cooler, significantly extending its operational life and improving reliability.
- Topology Optimization: Using specialized software, designers can define load cases and boundary conditions for the turbine disk segment and allow algorithms to iteratively remove material from non-critical areas. This results in organic-looking, highly efficient structures that possess the required stiffness and strength but with significantly reduced mass. Uderzenie: Weight savings in rotating components like turbine disks are particularly valuable, reducing inertial loads, improving engine responsiveness, and contributing to overall aircraft fuel efficiency. Weight reductions of 10-30% are often achievable for appropriately redesigned components.
- Konsolidacja części: AM enables the integration of multiple functions or separate components into a single, monolithic printed part. For instance, features for attaching seals or other adjacent hardware, which might normally be separate pieces requiring assembly (bolting, welding), could potentially be grown directly as part of the disk segment. Uderzenie: Reduces part count, eliminates joints (which can be potential failure points or sources of fretting), simplifies assembly processes, lowers inventory complexity, and potentially reduces overall weight and cost.
2. Significant Lead Time Reduction: Traditional manufacturing routes for superalloy turbine disks involve long lead times, often spanning many months or even years, especially considering the procurement of specialized forgings and the creation of complex tooling and machining setups.
- Rapid Prototyping & Iteration: AM allows design concepts to be physically realized in days or weeks rather than months. Engineers can rapidly prototype different design variations (e.g., testing various cooling channel configurations or topology-optimized structures), perform functional tests, and iterate towards an optimal solution much faster.
- Tooling Elimination: AM is a ‘tool-less’ manufacturing process. It bypasses the need for expensive and time-consuming forging dies, casting molds, or specialized machining fixtures. This drastically cuts the upfront time and cost associated with introducing new designs or modifying existing ones.
- On-Demand Production & Spares: AM offers the potential for producing parts, including spares for maintenance, repair, and overhaul (MRO), on demand. This can reduce the need for large physical inventories, minimizing warehousing costs and mitigating issues of part obsolescence.
3. Enhanced Material Efficiency (Improved Buy-to-Fly Ratio): Manufacturing complex components like turbine disks from expensive superalloys using traditional subtractive methods is notoriously wasteful.
- Near-Net-Shape Manufacturing: AM builds parts additively, depositing material only where it is needed. This results in components that are very close to their final dimensions (“near-net shape”), requiring significantly less finish machining compared to starting with a large forging or billet.
- Zmniejszona ilość odpadów materiałowych: The “buy-to-fly” ratio (the weight of raw material purchased divided by the weight of the final component) is a key metric in aerospace. Forgings for complex superalloy parts can have buy-to-fly ratios of 10:1, 15:1, or even higher, meaning 90% or more of the expensive material is machined away. With AM, this ratio can be dramatically reduced, often to figures closer to 1.5:1 or 2:1. Uderzenie: Given the high cost of aerospace-grade superalloys like IN738LC and Haynes 282, this translates directly into substantial cost savings on raw materials.
- Powder Reuse: Unfused powder in the build chamber during Powder Bed Fusion processes can typically be sieved and reused in subsequent builds (subject to quality control), further improving material utilization.
4. Leveraging Advanced AM Technologies (e.g., SEBM): Powder Bed Fusion (PBF) techniques are well-suited for producing dense, high-resolution metal parts. Selektywne topienie wiązką elektronów (SEBM), a technology where Met3dp possesses significant expertise and offers industry-leading equipment, presents particular advantages for processing challenging superalloys:
- High Processing Temperatures: SEBM operates with significantly higher powder bed preheating temperatures (often several hundred degrees Celsius) compared to Laser PBF (L-PBF). This elevated temperature reduces the thermal gradients during melting and solidification, significantly mitigating the risk of solidification cracking and reducing residual stresses in the as-built part. This is particularly beneficial for crack-sensitive alloys like IN738LC.
- Środowisko próżniowe: The process occurs under a high vacuum, which prevents oxidation or contamination of the reactive elements (like Al, Ti) present in nickel-based superalloys, ensuring material purity and optimal properties.
- Potentially Higher Productivity: Electron beams can typically scan faster and use higher power levels than lasers, potentially leading to faster build rates for bulky or less intricate geometries, although L-PBF often offers finer feature resolution.
By embracing metal 3D printing, aerospace companies can move beyond the constraints of traditional manufacturing, unlocking performance improvements, accelerating innovation cycles, and achieving significant cost and material efficiencies in the production of critical components like jet turbine disk segments. Met3dp stands ready with the technology, materials, and expertise to facilitate this transition.
Superalloy Selection: IN738LC and Haynes 282 for Extreme Environments
The ability of jet turbine disk segments to withstand their operational environment hinges critically on the material they are made from. For the demanding high-temperature, high-stress conditions found in the turbine hot section, Nadstopy na bazie niklu are the undisputed champions. These remarkable materials retain significant strength, creep resistance, and environmental stability at temperatures where steels or titanium alloys would fail rapidly. Their performance stems from a carefully engineered microstructure, primarily a Nickel-based face-centered cubic (FCC) matrix (gamma) strengthened by finely dispersed intermetallic precipitates (gamma′). Two prominent superalloys often considered for these applications, and processable via Additive Manufacturing, are IN738LC and Haynes 282. Understanding their specific attributes is crucial for selecting the right material and optimizing the AM process.
Deep Dive: IN738LC (Low Carbon Inconel 738)
IN738LC is a precipitation-hardenable nickel-based superalloy that has been a workhorse material for turbine components, particularly blades and vanes, for decades. Its reputation is built on a strong combination of high-temperature strength and excellent hot corrosion resistance.
- Composition & Microstructure: IN738LC derives its properties from a complex blend of alloying elements dissolved in the nickel matrix. Key elements include:
- Chrom (Cr): ~16% – Primarily responsible for oxidation and hot corrosion resistance by forming a protective chromium oxide (Cr$_2$O$_3$) scale.
- Kobalt (Co): ~8.5% – Enhances solid solution strengthening and raises the gamma′ solvus temperature (the temperature at which the strengthening precipitates dissolve).
- Molybdenum (Mo), Tungsten (W): ~1.75% & ~2.6% – Contribute significantly to solid solution strengthening of the gamma matrix.
- Aluminum (Al), Titanium (Ti), Niobium (Nb), Tantalum (Ta): ~3.4%, ~3.4%, ~0.9%, ~1.75% – These are crucial “gamma prime formers.” They combine with Nickel to precipitate the ordered L1$_2$ intermetallic phase gamma′ (nominally Ni$_3$(Al,Ti,Nb,Ta)). The high volume fraction (~40-50%) and stability of these fine gamma′ precipitates impede dislocation movement, providing the alloy’s exceptional high-temperature strength and creep resistance.
- Carbon (C), Boron (B), Zirconium (Zr): Low levels (~0.1% C, ~0.01% B, ~0.05% Zr) – Segregate to grain boundaries, forming carbides (like MC, M$_2_3$C$_6$) and modifying grain boundary structure to improve creep rupture life and ductility. The “LC” designation signifies a lower carbon content (~0.09-0.13%) compared to the original IN738C (~0.15-0.20%), which slightly improves castability, weldability, and potentially AM processability by reducing susceptibility to cracking during solidification and heat treatment.
- Kluczowe właściwości:
- Wytrzymałość na wysokie temperatury: Maintains excellent tensile and yield strength up to approximately 980circC (1800circF).
- Odporność na pełzanie: Exhibits good resistance to time-dependent deformation under load at temperatures up to 950circC (1740circF).
- Hot Corrosion Resistance: Considered one of the best among common superalloys for resistance to both high-temperature (Type I) and low-temperature (Type II) hot corrosion, primarily due to its high Chromium content. This is critical in environments where fuel impurities (sulfur) or ingested salts (in marine or coastal operations) are present.
- Odporność na utlenianie: Good resistance to oxidation in air up to high temperatures.
- AM Considerations: While widely used in casting, processing IN738LC via AM (especially L-PBF) can be challenging. It is known to be susceptible to solidification cracking (due to its wide freezing range and segregation of certain elements) and strain-age cracking during post-print heat treatment (due to the precipitation kinetics of gamma′). Strategies to mitigate this include:
- Careful optimization of AM process parameters (laser/beam power, scan speed, layer thickness, scan strategy).
- Utilizing processes with significant preheating, such as SEBM, which reduces thermal gradients.
- Developing specific post-build heat treatment cycles involving slow heating rates through critical temperature ranges and appropriate solutioning and aging steps to achieve the desired microstructure and mechanical properties without inducing cracking.
Deep Dive: Haynes 282
Haynes 282 is a newer generation, precipitation-strengthened nickel-based superalloy specifically developed to offer an exceptional combination of creep strength, thermal stability, good fabricability, and weldability – addressing some of the limitations of older alloys.
- Composition & Microstructure: Haynes 282 also relies on gamma′ precipitation for its strength but with a different balance of alloying elements compared to IN738LC:
- Nikiel (Ni): ~57% (Base)
- Chrom (Cr): ~19.5% – Provides excellent oxidation resistance and contributes to solid solution strength.
- Kobalt (Co): ~10% – Enhances solid solution strength and raises the gamma′ solvus temperature.
- Molibden (Mo): ~8.5% – Major contributor to solid solution strengthening.
- Titanium (Ti), Aluminum (Al): ~2.1%, ~1.5% – The primary gamma′ formers (Ni$_3$(Al,Ti)). The specific ratio and amounts are optimized for creep strength and stability. Note the absence of significant Nb or Ta compared to IN738LC.
- Boron (B), Carbon (C): Similar roles to IN738LC in grain boundary strengthening.
- The alloy is designed to have slower gamma′ precipitation kinetics compared to alloys like Waspaloy, which contributes significantly to its improved fabricability and resistance to strain-age cracking during welding and heat treatment.
- Kluczowe właściwości:
- Outstanding Creep Strength: This is the hallmark of Haynes 282. It offers significantly better creep resistance than alloys like Waspaloy, R’41, and often exceeds IN738LC, particularly in the intermediate temperature range of 650circC to 900circC (1200circF to 1650circF).
- Excellent Fabricability: Due to its slower precipitation kinetics, it exhibits better resistance to strain-age cracking, making it easier to form, machine, and crucially, weld (important for potential AM part repairs or joining operations).
- Good Thermal Stability: Resists the formation of detrimental topological close-packed (TCP) phases (like sigma phase) during long-term high-temperature exposure, which can embrittle other superalloys.
- Good Fatigue Properties: Exhibits favorable LCF and HCF resistance.
- Very Good Oxidation Resistance: Comparable to other high-Cr superalloys.
- AM Suitability: Generally considered more amenable to additive manufacturing (both L-PBF and SEBM) than IN738LC or Waspaloy due to its improved resistance to cracking. However, like all superalloys, it still demands precise control over AM process parameters and tailored post-processing heat treatments (typically a solution anneal followed by a two-step aging process) to develop the optimal microstructure and achieve the full potential of its mechanical properties.
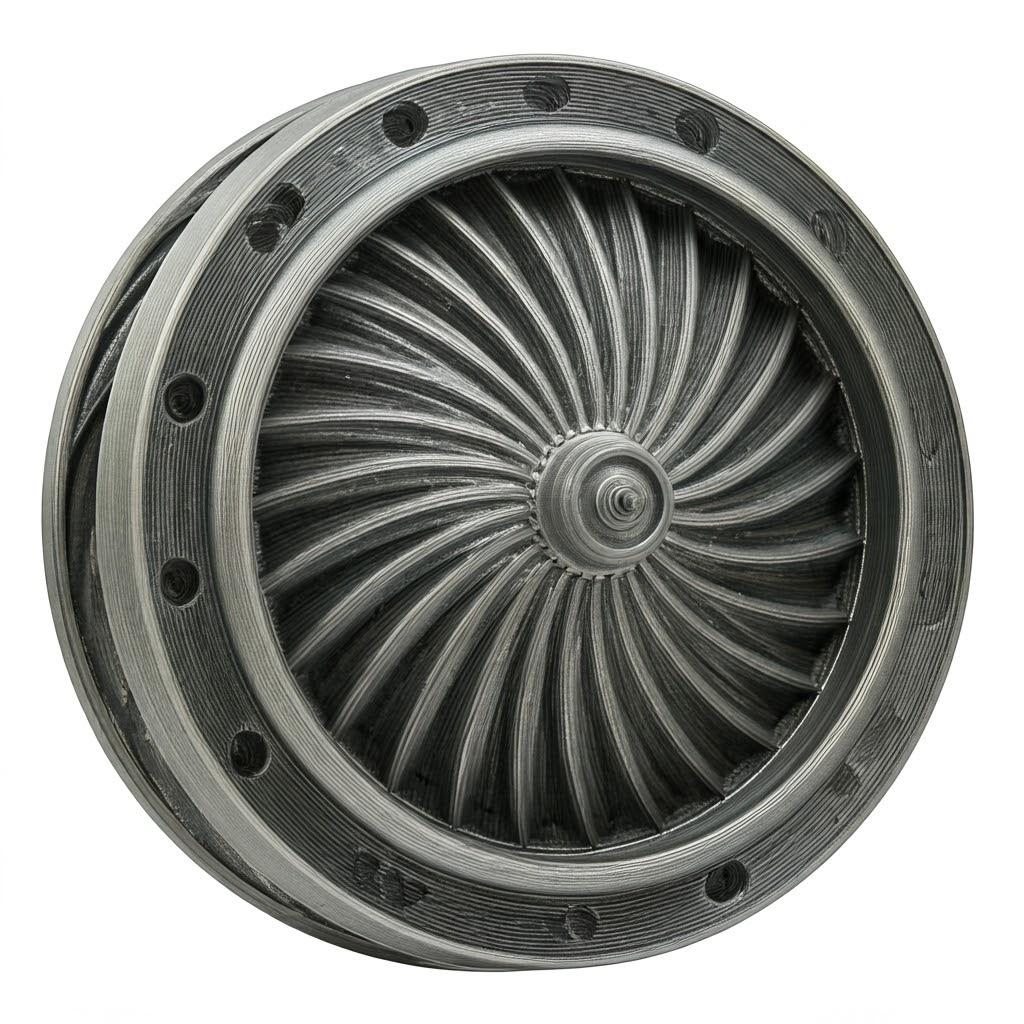
Met3dp’s High-Quality Superalloy Powders:
The success of manufacturing turbine disk segments using AM fundamentally relies on the quality of the starting metal powder. Defects or inconsistencies in the powder can translate directly into flaws within the final part, compromising its integrity – an unacceptable outcome for safety-critical aerospace components. Met3dp leverages industry-leading powder manufacturing technologies to produce IN738LC, Haynes 282, and other advanced superalloy powders optimized for AM processes like SEBM and L-PBF.
- Advanced Atomization: We employ cutting-edge Atomizacja gazowa (GA) oraz Proces plazmowej elektrody rotacyjnej (PREP) technologie.
- Atomizacja gazu: Uses high-pressure inert gas (like Argon or Nitrogen) jets to break up a stream of molten superalloy into fine droplets, which solidify into spherical powder particles. Our GA equipment utilizes unique nozzle and gas flow designs to achieve high yields of powder with excellent sphericity and flowability.
- PREP: Involves rotating a consumable electrode bar of the desired alloy at high speed within a controlled atmosphere. A plasma torch melts the tip of the electrode, and centrifugal force ejects molten droplets that solidify in flight into highly spherical powders with very few internal pores or satellites (smaller particles attached to larger ones). PREP is particularly known for producing extremely clean and spherical powders ideal for demanding applications.
- Kontrola jakości: Every batch of Met3dp superalloy powder undergoes rigorous quality control checks, including:
- Chemical Composition Analysis (ensuring it meets aerospace specifications).
- Particle Size Distribution (PSD) analysis (using laser diffraction to ensure the powder suits the specific AM machine and desired layer thickness).
- Morphology Assessment (using Scanning Electron Microscopy – SEM to verify high sphericity and low satellite content).
- Flowability Testing (e.g., Hall Flowmeter) and Apparent/Tap Density measurements (critical for uniform powder bed spreading).
- Gas Content Analysis (controlling Oxygen and Nitrogen levels).
This meticulous approach to powder production ensures that Met3dp provides aerospace manufacturers with consistently high-quality, reliable superalloy powders – the essential foundation for building mission-critical components like jet turbine disk segments using additive manufacturing.
Comparative Overview:
Cecha | IN738LC | Haynes 282 |
---|---|---|
Primary Strengths | Excellent Hot Corrosion Resistance, Good Creep Str. | Outstanding Creep Strength, Excellent Fabricability |
Typical Max Use Temp | ~980°C (1800circF) | ~900°C (1650circF) (Excels in 650-900°C range) |
Key Strengthening | High vol% gamma′ (Ni$_3$(Al,Ti,Nb,Ta)) | Optimized gamma′ (Ni$_3$(Al,Ti)), Solid Solution |
AM Processability | More challenging (cracking potential) | Generally better (slower kinetics, less cracking) |
Weldability/Repair | Fair (LC version improves it) | Good to Excellent |
Typowe zastosowania | Turbine Blades, Vanes, Disks (Legacy/Current) | Combustors, Turb. Casings, Rings, Seals, Disks (Newer) |
Met3dp Powder | Available (GA/PREP, Optimized for AM) | Available (GA/PREP, Optimized for AM) |
Export to Sheets
Choosing between IN738LC and Haynes 282 for a 3D printed turbine disk segment depends on the specific design requirements, operating temperature profile, expected lifetime, and manufacturing considerations. Haynes 282 might be preferred for new designs targeting the highest creep performance and easier manufacturability, while IN738LC remains a viable option where its specific corrosion resistance profile is critical or for replacing existing components made from this alloy. Met3dp can provide both high-quality powders and the application expertise to help make the right selection.
Optimizing Design for Additive Manufacturing (DfAM) of Turbine Disk Segments</h1>
Transitioning the production of critical components like jet turbine disk segments to additive manufacturing is not merely about replicating existing designs using a new method. True value realization comes from fundamentally rethinking the component’s architecture through the lens of Projektowanie dla produkcji addytywnej (DfAM). DfAM empowers engineers to move beyond the limitations imposed by traditional forging and machining, actively exploiting the unique capabilities of AM to create parts that are lighter, stronger, more efficient, and potentially longer-lasting. For turbine disk segments operating under extreme conditions, applying DfAM principles can yield substantial performance and lifecycle benefits.
Leveraging Geometric Complexity: AM’s layer-by-layer approach removes many of the geometric constraints of subtractive manufacturing. This freedom can be strategically employed in turbine disk design:
- Konforemne kanały chłodzące: Efficiently managing the intense heat loads at the turbine disk rim and near blade attachments is paramount for component durability and engine performance. Traditional methods often rely on drilled cooling holes, which are typically straight and limited in placement. AM enables the creation of highly complex, conformal cooling channels that precisely follow the 3D contours of the component’s hottest regions. These channels can possess optimized cross-sectional shapes (e.g., elliptical or teardrop instead of circular) to maximize heat transfer surface area while minimizing aerodynamic disruption or pressure loss of the cooling air. Imagine intricate networks of micro-channels running just beneath the surface of the firtree slots or the disk rim, extracting heat far more effectively than conventional methods. Computational Fluid Dynamics (CFD) simulations become essential DfAM tools here, allowing engineers to model fluid flow and heat transfer within these complex channel designs, iteratively refining the geometry for optimal cooling effectiveness before committing to a print. The payoff is significant: either enabling higher turbine operating temperatures for improved engine efficiency and thrust, or substantially reducing metal temperatures for the same operating conditions, leading to vastly improved creep life and thermal fatigue resistance.
- Optimized Blade Attachments: The firtree or dovetail slots that hold the turbine blades are areas of extremely high stress concentration. While traditional machining produces these features with high precision, AM offers possibilities to further optimize their design. For instance, subtle variations in the firtree profile, incorporating smoothly blended radii or localized reinforcement impossible to machine conventionally, could potentially reduce peak stresses and enhance fatigue life. AM might even enable entirely novel, more efficient load-bearing attachment concepts that depart from traditional slot designs.
- Integrated Features & Part Consolidation: Turbine disk segments often interface with other components like seals, retaining plates, or sensor mounts. DfAM encourages designers to explore integrating these adjacent features directly into the AM build. Sealing surfaces with specific labyrinth patterns, brackets for instrumentation, or even flow guides could be grown as a monolithic part of the disk segment. This consolidation reduces the number of individual parts, eliminates fasteners and joints (which are potential failure points and add weight/complexity), streamlines the assembly process, and reduces the overall bill of materials (BOM) and associated logistical overhead.
Topology Optimization for Lightweighting: Rotating mass is a critical concern in jet engine design. Topology optimization is a powerful computational DfAM technique that helps create the lightest possible structure that still meets all performance requirements.
- The Process: Engineers define the “design space” (the maximum allowable volume for the disk segment), specify the loads it must withstand (centrifugal forces, thermal loads, vibrational inputs), define material properties (e.g., for IN738LC or Haynes 282), and set performance constraints (e.g., maximum allowable stress or deflection). Topology optimization software then uses algorithms (like SIMP or BESO) to iteratively remove material from areas experiencing low stress, leaving behind an optimized, often organic-looking load-bearing structure.
- Application to Turbine Disks: For a turbine disk segment, this might result in significant material removal from the web connecting the rim to the bore, potentially creating intricate lattice structures or smoothly varying thicknesses. The rim and bore areas, being critical for blade attachment and shaft interface, would typically remain more solid.
- Validation: It is absolutely critical that topology-optimized designs are rigorously validated using Finite Element Analysis (FEA) to ensure they can withstand all static, dynamic, and thermal loads encountered during engine operation, including worst-case scenarios and fatigue analysis. The weight savings achievable (potentially 10-30% or more for redesigned components) directly translates to lower rotational inertia, improved engine responsiveness, and reduced fuel consumption over the aircraft’s lifetime.
Support Structure Strategy: In Powder Bed Fusion (PBF) processes like SEBM and L-PBF, support structures are often necessary for:
- Supporting overhanging features (typically angles below ~45 degrees from the horizontal plane).
- Anchoring the part firmly to the build plate to prevent warping due to thermal stresses.
- Conducting heat away from the melt zone to control cooling rates and reduce stress.
However, supports add time and cost to the process (material usage, build time, removal effort) and can negatively impact the surface finish where they attach. Effective DfAM for turbine disk segments involves minimizing the need for supports and designing them for easy removal:
- Orientacja budynku: Selecting the optimal orientation on the build plate is crucial. This involves balancing factors like minimizing overhangs, reducing build height (which impacts time), managing thermal stresses, and considering potential anisotropy.
- Designing Self-Supporting Features: Where possible, modifying designs to use angles greater than 45 degrees, or incorporating chamfers and fillets instead of sharp overhangs.
- Support Design: Using support types (e.g., lattice, conical, tree-like) that use minimal material and have easily breakable contact points. Designing sacrificial layers or features specifically intended for support attachment and later machining away.
- Removal Considerations: Superalloys are tough materials, making support removal challenging. Designing for clear tool access for manual or automated removal is essential. Poorly designed supports in inaccessible areas can be extremely difficult or impossible to remove without damaging the part.
Adhering to AM Design Rules: Designers must also respect the inherent possibilities and limitations of the chosen AM process (SEBM or L-PBF):
- Minimum Wall Thickness / Feature Size: Dictated by beam/laser spot size, powder characteristics, and process stability (e.g., typically 0.3-0.5mm might be a practical lower limit for robust features).
- Hole/Channel Diameter: Minimum achievable size for internal channels without powder becoming trapped or sintering shut.
- Rozdzielczość: The level of fine detail that can be accurately reproduced.
- Smooth Transitions: Avoiding sharp corners and abrupt changes in cross-section helps reduce stress concentrations.
- Anizotropia: Recognizing that AM parts, especially those with columnar grain structures, can exhibit different mechanical properties in the build direction (Z) versus the transverse directions (X, Y), and orienting the part or designing features to account for this if necessary.
The Role of Software and Expertise: Successfully implementing DfAM for critical components relies heavily on advanced software tools for CAD, topology optimization, CFD, FEA, and AM process simulation (predicting thermal behavior, residual stress, potential defects). Equally important is the expertise of engineers who understand both the functional requirements of the turbine disk and the nuances of the AM process. Met3dp offers not just printing services and materials but also application development support, helping customers leverage DfAM principles to unlock the full potential of additive manufacturing for their demanding aerospace components.
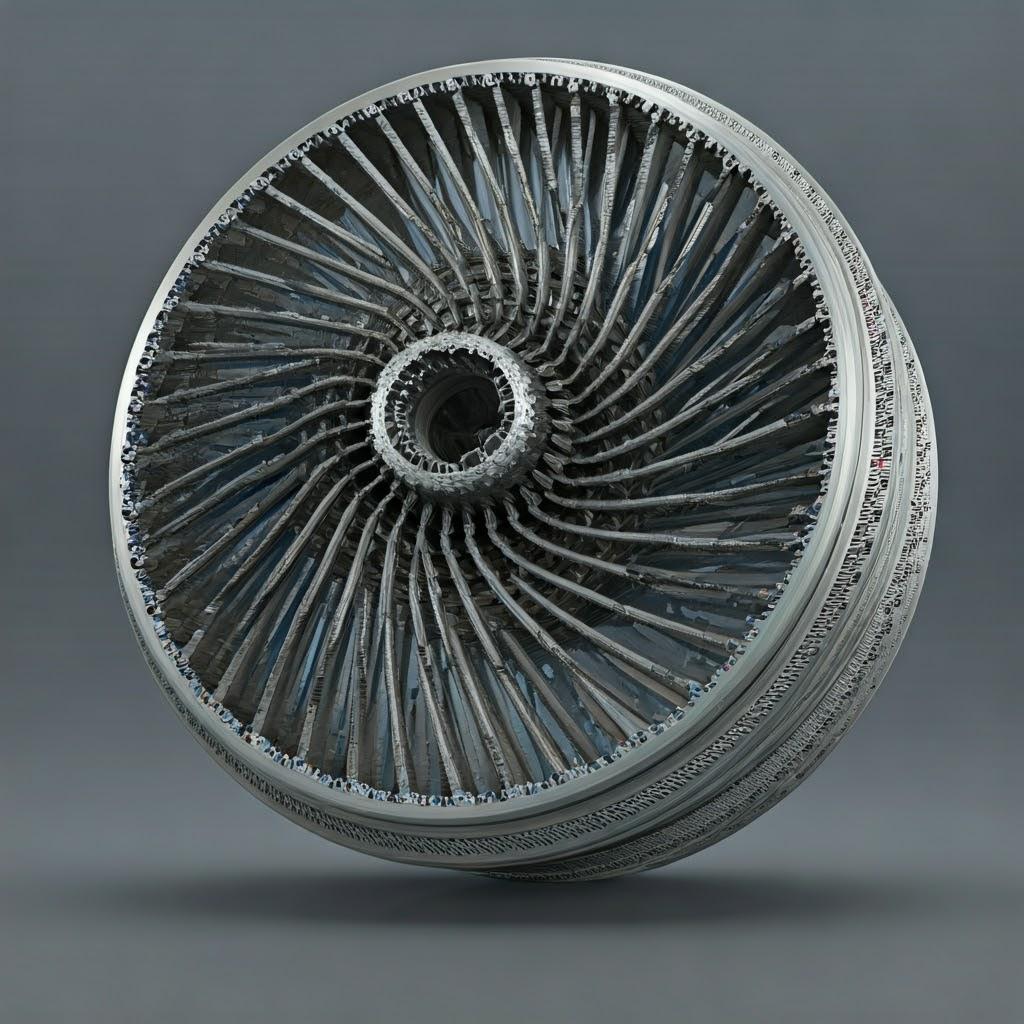
Achieving Precision: Tolerance, Surface Finish, and Dimensional Accuracy in 3D Printed Segments
While additive manufacturing offers unparalleled design freedom, achieving the extreme precision demanded by aerospace components like turbine disk segments requires a clear understanding of the technology’s capabilities and limitations, particularly regarding tolerances, surface finish, and overall dimensional accuracy. While AM parts, especially those made via PBF processes like SEBM and L-PBF, can be highly accurate, they typically do not achieve the ultra-fine tolerances and finishes of high-precision machining in their as-built state. Post-processing steps are almost always integral to meeting the final specifications for these critical parts.
Tolerances in Metal AM: Tolerance refers to the permissible variation in a dimension. In AM:
- Typical As-Built Tolerances: For well-controlled SEBM and L-PBF processes using superalloys like IN738LC or Haynes 282, general achievable tolerances might range from approximately pm0.1 mm to pm0.3 mm for smaller features, or perhaps pm0.1 to pm0.2 for larger dimensions. Met3dp’s industry-leading printers are engineered for high accuracy and repeatability within these typical ranges. However, these are general guidelines, and specific achievable tolerances depend heavily on:
- Machine Calibration & Condition: Regular calibration and maintenance are crucial.
- Process Parameters: Beam/laser power, scan speed, layer thickness, focus control.
- Thermal Factors: Stability of the build chamber temperature, effectiveness of preheating (SEBM advantage), residual stress management.
- Part Geometry & Size: Larger parts or those with complex internal features are more prone to thermal distortion.
- Orientacja budynku: Affects support needs, thermal history, and potential directional inaccuracies.
- Jakość proszku: Consistent particle size and morphology contribute to stable melting and layer formation.
- Critical vs. Non-Critical Tolerances: It’s vital to differentiate. While general form tolerances might be acceptable as-built for some areas, critical interfacing dimensions – such as the complex profile of firtree slots, the flatness and parallelism of mating faces between segments, or the precise diameter of the bore – almost invariably require post-machining (CNC milling, grinding, EDM) to achieve the necessary micron-level precision specified by aerospace GD&T (Geometric Dimensioning and Tolerancing) requirements.
Surface Finish (Roughness): Surface finish, typically quantified by the average roughness (Ra), is another key characteristic influenced by the AM process.
- As-Built Surface Roughness:
- L-PBF: Generally produces smoother surfaces, often in the range of Ra 10-20 µm (micrometers).
- SEBM: Due to typically larger powder particles and higher energy input, as-built surfaces are rougher, often Ra 20-40 µm.
- Influencing Factors: Layer thickness (thicker layers = rougher surface), powder particle size distribution, melt pool stability, and importantly, the angle of the surface relative to the build plate. Inclined or curved surfaces exhibit a characteristic “stair-stepping” effect inherent to the layered manufacturing process, which increases roughness. Top-facing horizontal surfaces tend to be rougher than vertical walls.
- Wymagania dotyczące wykończenia powierzchni: Different areas of a turbine disk segment have vastly different finish requirements. Aerodynamic surfaces might need polishing for efficiency, mating faces require extreme flatness and smoothness (sub-micron Ra) for proper sealing and load transfer, while the surfaces within firtree slots need a specific, carefully controlled finish to optimize fatigue life (often achieved via shot peening after machining).
- Post-Processing for Finish: As-built surfaces are rarely acceptable for functional requirements. Post-processing methods like CNC machining, grinding, polishing, abrasive flow machining (AFM) for internal channels, and shot peening are employed to achieve the required final surface characteristics. Shot peening is particularly important for fatigue-critical areas as it introduces beneficial compressive residual stresses alongside modifying the surface texture.
Dokładność wymiarowa: This refers to how closely the final part conforms to the intended geometry specified in the CAD model. Deviations arise from several sources:
- Thermal Shrinkage and Distortion: As the part heats and cools during the build, thermal expansion and contraction occur. Residual stresses locked into the part can cause warping or distortion, especially after removal from the build plate and during subsequent heat treatments. Complex geometries or parts with large variations in cross-section are more susceptible. Advanced AM simulation software can predict these effects to some extent, allowing for compensated (pre-deformed) build files to counteract anticipated distortion.
- Support Structure Effects: The presence and subsequent removal of support structures can leave witness marks or slightly affect local geometry.
- Post-Processing Stack-up: Each post-processing step (heat treatment, HIP, machining) has its own associated tolerances. HIP, for example, causes predictable volumetric shrinkage as internal porosity is closed. Machining operations must account for the variability of the as-built AM part when establishing datums and machining paths.
Metrology and Inspection – The Non-Negotiable Step: Given the safety-critical nature of turbine disk segments, rigorous inspection is paramount.
- Techniques:
- Coordinate Measuring Machines (CMM): Touch probes used to measure discrete points and verify critical dimensions, geometric tolerances (flatness, parallelism, position), and complex profiles against the CAD model with high accuracy.
- Non-Contact 3D Scanning: Laser line scanners or structured light systems capture millions of points across the part’s entire surface, creating a dense point cloud that can be compared to the original CAD data (often shown as a color map highlighting deviations). This is excellent for verifying overall shape and detecting unexpected warping or distortion.
- Planning: A detailed metrology plan, defining critical dimensions, datums, measurement techniques, and acceptance criteria, must be established early in the process, often in collaboration between the designer and the AM service provider like Met3dp.
Ensuring Consistency and Repeatability: For production applications, it’s not enough to produce one accurate part; every part must meet specifications reliably. Met3dp achieves this through:
- Kontrola procesu: Strict adherence to qualified process parameters for each machine/material combination. Real-time monitoring where available.
- Machine Calibration & Maintenance: Regular schedules to ensure machine accuracy.
- Consistent Powder Quality: Rigorous incoming inspection and controlled handling/recycling of Met3dp’s high-quality metal powders.
- Robust Quality Management System (QMS): Procedures compliant with aerospace standards (like AS9100) covering all stages of production and inspection.
In summary, while AM requires careful management and often post-processing to meet the stringent precision requirements of aerospace turbine components, partnering with an experienced provider like Met3dp ensures that tolerances, surface finish, and dimensional accuracy are proactively addressed through optimized processes, meticulous control, and comprehensive inspection.
Essential Post-Processing Steps for 3D Printed Turbine Disk Segments
Producing a jet turbine disk segment using metal additive manufacturing doesn’t end when the printer stops. The as-built part, while geometrically complex, is far from being flight-ready. A series of crucial post-processing steps are required to relieve internal stresses, remove support structures, achieve the final required dimensions and surface finish, ensure material integrity by eliminating internal defects, and develop the optimal microstructure for demanding high-temperature mechanical performance. For safety-critical aerospace components like turbine disks made from superalloys such as IN738LC or Haynes 282, this post-processing workflow is not optional; it’s an integral and meticulously controlled part of the manufacturing process.
Here’s a breakdown of the typical post-processing sequence:
1. Stress Relief (SR):
- Cel: This is typically the very first step, performed while the part is still attached to the build plate. The rapid heating and cooling inherent in PBF processes generate significant internal residual stresses within the component. If the part were removed from the build plate without this step, these stresses could cause immediate and potentially severe warping, distortion, or even cracking.
- Proces: The entire build plate with the attached part(s) is placed inside a furnace with a controlled inert atmosphere (usually Argon or vacuum to prevent oxidation). The assembly is heated slowly to a specific stress relief temperature (which is below the aging temperature for the superalloy, typically in the range of 650°C – 950°C depending on the alloy and specifics), held for a defined period (soaking time), and then cooled down slowly and uniformly. This allows internal stresses to relax through microscopic plastic deformation without altering the primary microstructure significantly.
2. Part Removal from Build Plate:
- Cel: To separate the stress-relieved part(s) from the metal build plate they were printed on.
- Proces: This is commonly done using Wire Electrical Discharge Machining (Wire EDM), which uses a thin, electrically charged wire to precisely cut through the base of the part or any support interface layer. Sawing or abrasive waterjet cutting may also be used in some cases. Care must be taken to avoid damaging the part itself during this operation.
3. Support Structure Removal:
- Cel: To remove the temporary structures that were printed to support overhangs and anchor the part during the build.
- Proces: This can be one of the most labor-intensive steps, depending on the complexity and accessibility of the supports. Methods include:
- Ręczne usuwanie: Using pliers, cutters, grinders, or specialized tools to break or cut away accessible supports. Requires skill to avoid damaging the part surface.
- CNC Machining: Milling or grinding away support structures, especially useful for robust or partially inaccessible supports.
- EDM: Can be used for intricate or hard-to-reach internal supports.
- Wyzwania: Supports made from high-strength superalloys are inherently difficult to remove. Internal channels or complex geometries can make access extremely challenging. This underscores the importance of DfAM principles to minimize support requirements and design them for easier removal (e.g., with specific break-off points or weakened interfaces). Residual support material or damage caused during removal must be addressed in subsequent finishing steps.
4. Heat Treatment (Solutioning & Aging) and Hot Isostatic Pressing (HIP):
- Cel: This multi-stage thermal processing is arguably the most critical post-processing phase for achieving the required material properties and integrity for aerospace applications.
- Prasowanie izostatyczne na gorąco (HIP): This process is considered mandatory for almost all critical AM aerospace components, especially rotating parts. The part is placed in a specialized pressure vessel and subjected simultaneously to high temperature (typically close to the alloy’s solution annealing temperature, e.g., 1120circC−1200circC) and high inert gas pressure (typically Argon at 100-200 MPa or 15-30 ksi) for several hours. The combination of heat and pressure effectively collapses and diffusion-bonds any internal microporosity (gas pores, small lack-of-fusion voids) remaining from the AM process, driving the part towards full theoretical density (>99.9%). This significantly improves mechanical properties, particularly fatigue life, ductility, and fracture toughness, by eliminating internal defect initiation sites. HIP also helps to homogenize the microstructure.
- Wyżarzanie roztworu: This heat treatment step (which can sometimes be combined with the HIP cycle, or performed separately before or after) involves heating the alloy to a high temperature (e.g., around 1120circC for IN738LC, 1150circC for Haynes 282) to dissolve the existing gamma′ precipitates and potentially other phases into the solid solution gamma matrix, and to homogenize the chemical composition. It’s often followed by a controlled cooling or quenching step.
- Leczenie starzenia się: After solutioning, the part undergoes one or more lower-temperature aging heat treatments (e.g., typically in the range of 760circC−980circC for varying times) . This carefully controlled process allows the strengthening gamma′ phase to re-precipitate with the desired fine size, morphology (shape), and uniform distribution within the gamma matrix. The specific aging cycle (temperatures and times) is critical for achieving the target mechanical properties (high-temperature strength, creep resistance, fatigue life) and is alloy-specific (IN738LC and Haynes 282 require different aging cycles).
- Kontrola: All heat treatments must be performed in precisely controlled vacuum or inert atmosphere furnaces to prevent oxidation, with accurate temperature monitoring and recording according to aerospace specifications.
5. CNC Machining:
- Cel: To achieve the final, precise dimensions, tolerances, and surface finishes on critical features that cannot be met by the as-built AM process, even after HIP and heat treatment. This includes features like the firtree slots, mating surfaces between segments, the bore interface, and sealing features.
- Proces: Utilizes multi-axis CNC milling, turning, or grinding machines. Requires careful planning for workholding (fixturing) due to the often complex, near-net shape of the AM part. Machining nickel-based superalloys is inherently challenging due to their high strength, high work-hardening rate, and poor thermal conductivity, requiring specific cutting tools, speeds, feeds, and coolants.
6. Surface Finishing:
- Cel: To achieve the final required surface texture and properties on specific areas.
- Proces:
- Grinding/Polishing: For achieving very smooth surfaces (low Ra) on mating faces or aerodynamic profiles.
- Śrutowanie: Critically important for enhancing fatigue life. Small spherical media (shot) are propelled at high velocity onto the component surface. Each impact creates a small indentation, yielding the surface layer and inducing beneficial compressive residual stresses. This compressive layer resists crack initiation and propagation under cyclic loading, significantly improving fatigue performance, especially in high-stress areas like firtree slots. The process parameters (shot size, material, velocity, coverage) must be tightly controlled.
- Abrasive Flow Machining (AFM) or Electrochemical Polishing (ECP): May be used to smooth internal passages or hard-to-reach areas.
7. Non-Destructive Testing (NDT):
- Cel: To verify the internal and external integrity of the finished part without damaging it, ensuring it is free from critical defects. This is a mandatory quality gate for flight hardware.
- Proces: NDT is often performed at multiple stages (e.g., post-HIP, post-machining). Common methods include:
- X-ray Radiography and Computed Tomography (CT): Detect internal flaws like porosity, inclusions, cracks, and lack of fusion. CT scanning provides a full 3D reconstruction, allowing detailed analysis of the internal structure and detection of subtle defects.
- Fluorescent Penetrant Inspection (FPI): A sensitive method to detect surface-breaking defects (cracks, porosity). A fluorescent dye penetrates any surface openings and is then made visible under UV light.
- Ultrasonic Testing (UT): Uses high-frequency sound waves to detect internal flaws. Can be challenging on complex AM geometries.
- Eddy Current Testing: Can detect surface and near-surface flaws and variations in material properties.
- Standardy: All NDT must be performed by certified technicians according to stringent aerospace standards (e.g., ASTM, NAS) and customer-specific requirements.
Met3dp manages this entire complex post-processing chain, leveraging in-house capabilities and a network of qualified, aerospace-certified partners for specialized processes like HIP, heat treatment, and NDT. This ensures a seamless workflow from digital design to a fully qualified, flight-ready turbine disk segment.
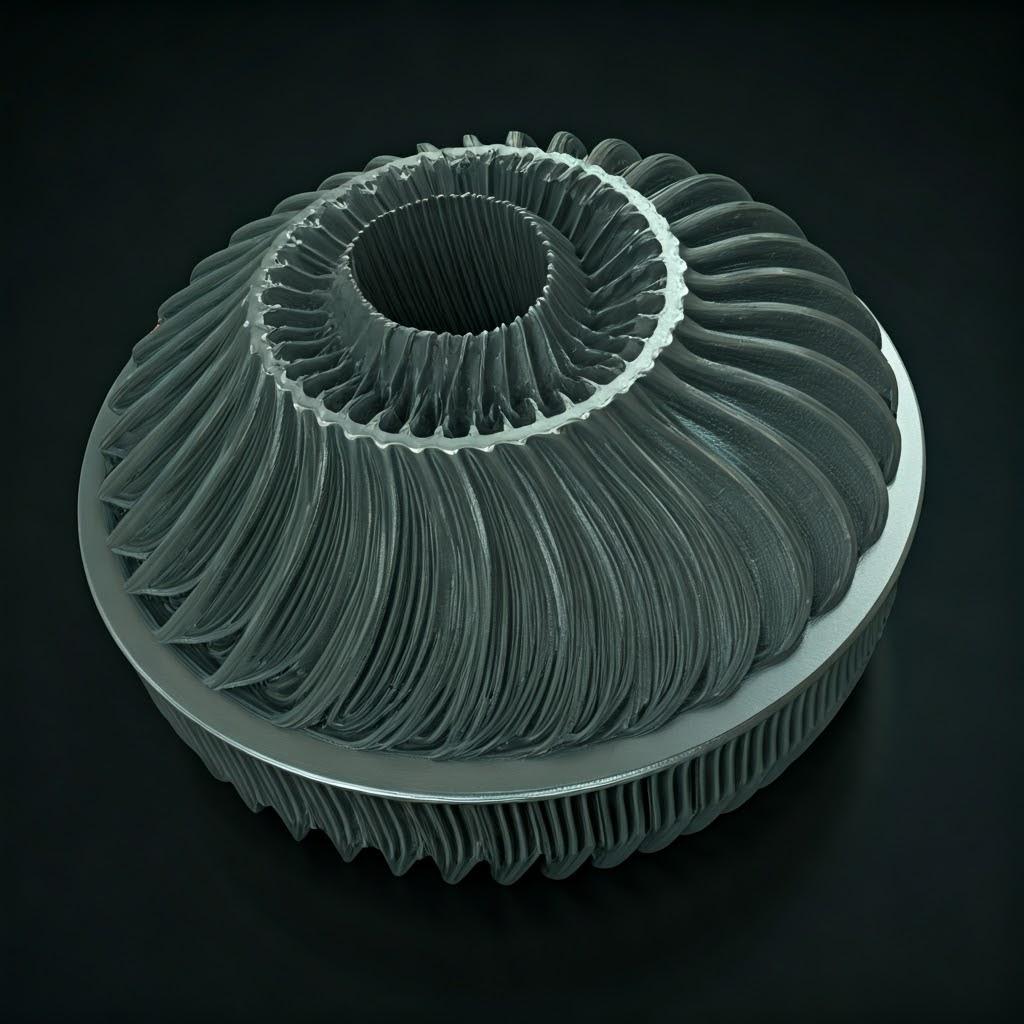
Navigating Challenges in AM for Turbine Disks: Warping, Residual Stress, and Quality Assurance
While the benefits of using additive manufacturing for complex superalloy components like jet turbine disk segments are substantial, the path from design to validated part is not without its technical hurdles. The extreme processing conditions, the challenging nature of the materials themselves, and the uncompromising quality demands of the aerospace industry necessitate a deep understanding of potential issues and robust strategies to mitigate them. Successfully navigating these challenges requires a combination of advanced technology, process expertise, simulation tools, and rigorous quality control – capabilities that experienced providers like Met3dp bring to the table.
Residual Stress and Warping: This remains one of the most significant challenges in metal PBF.
- The Root Cause: The localized, intense heating from the electron beam or laser, followed by rapid cooling and solidification, creates steep thermal gradients ($\Delta$T) across the part and between layers. This leads to differential thermal expansion and contraction, resulting in locked-in residual stresses. These stresses can easily exceed the material’s yield strength at elevated temperatures.
- Manifestations: If not properly managed, residual stresses can cause:
- Warping/Distortion: Bending or twisting of the part during the build, or significant shape changes upon removal from the build plate.
- Cracking: Hot cracking (during solidification) or cold cracking (after cooling or during heat treatment), especially in crack-sensitive alloys like IN738LC.
- Delamination: Separation of layers or detachment from support structures.
- Reduced Performance: High tensile residual stresses can decrease fatigue life and fracture toughness.
- Mitigation Strategies Employed by Met3dp:
- Process Simulation: Utilizing FEA-based simulation tools before printing to predict thermal history, stress accumulation, and potential distortion hotspots. This allows for adjustments to geometry (e.g., adding stiffening features to be removed later, pre-deforming the CAD model to compensate for expected warp) or build layout.
- Optimized Scan Strategies: Employing sophisticated beam/laser scanning patterns (e.g., island scanning where the layer is divided into small squares scanned randomly, sector-based scanning, rotating scan vectors between layers) helps to distribute heat more uniformly, reduce the length of continuous melt tracks, and lower peak stresses.
- Parameter Optimization: Fine-tuning process parameters (beam/laser power, scan speed, layer thickness, focus) within a validated process window specific to the alloy (IN738LC or Haynes 282) and machine.
- High Preheat Temperatures (SEBM Advantage): Met3dp’s expertise in Selektywne topienie wiązką elektronów (SEBM) is a key advantage here. The ability of SEBM to maintain high powder bed preheating temperatures (e.g., 600°C – 1000°C) significantly reduces the $\Delta$T during processing, drastically lowering residual stresses compared to typical L-PBF processes. This makes SEBM particularly well-suited for large, complex parts and crack-prone superalloys.
- Intelligent Support Structure Design: Designing supports not just for overhangs but also to act as effective heat sinks and anchors against warping forces.
- Mandatory Post-Build Stress Relief: As detailed previously, this thermal cycle is crucial for relaxing stresses before part removal.
Kontrola porowatości: Internal pores are detrimental defects that act as stress concentrators, severely compromising the mechanical integrity (especially fatigue strength) of critical rotating components. Achieving near-full density is paramount.
- Types and Origins:
- Gas Porosity: Caused by gas trapped within the powder particles (e.g., Argon from atomization) or dissolved gas in the melt pool coming out of solution during solidification. Can also result from contamination in the build chamber atmosphere.
- Lack-of-Fusion Porosity: Irregularly shaped voids caused by insufficient energy input to completely melt the powder or fuse adjacent melt tracks/layers. Often found between scan tracks or layers.
- Keyhole Porosity: Caused by excessive energy density, leading to deep melt pool penetration and metal vaporization. The collapsing vapor depression can trap gas, forming spherical pores often found at the bottom of the melt pool.
- Mitigation Strategies Employed by Met3dp:
- Premium Powder Quality: Using high-purity, gas-atomized (GA) or PREP-produced powders with low internal gas content, controlled spherical morphology, and optimized PSD, sourced from Met3dp’s advanced powder production facilities. Strict powder handling protocols prevent moisture absorption and contamination.
- Rigorous Parameter Development: Establishing stable process windows (optimal combinations of power, speed, hatch spacing, etc.) through extensive testing (coupon analysis, density measurements) to ensure complete fusion without inducing keyholing.
- Controlled Build Atmosphere: Utilizing high vacuum (SEBM) or high-purity inert gas flow (L-PBF) to minimize contamination from the environment.
- Prasowanie izostatyczne na gorąco (HIP): The definitive step to eliminate any remaining microporosity. HIP effectively closes gas pores and diffusion-bonds lack-of-fusion defects, guaranteeing maximum density.
Microstructural Control: The final mechanical properties of the superalloy component are intrinsically linked to its microstructure – grain size, shape, orientation, and the precise characteristics of the strengthening gamma′ precipitates.
- AM Microstructure: The rapid solidification inherent in PBF often leads to fine, columnar grains growing epitaxially layer upon layer, oriented along the thermal gradient (typically parallel to the build direction). This can result in anisotropic mechanical properties (different strength/ductility in Z vs. X/Y directions).
- Challenges & Goals: Controlling grain structure (achieving fine, equiaxed grains for isotropy is often desirable), ensuring homogeneity, preventing the formation of detrimental phases (like brittle TCP phases during prolonged exposure at certain temperatures), and achieving the optimal size, shape, and distribution of gamma′ precipitates through post-AM heat treatments are key challenges.
- Mitigation Strategies:
- Kontrola procesu: Scan strategies and parameters can influence grain morphology to some extent.
- Post-Processing Heat Treatments: Carefully designed solutioning, HIP, and aging cycles are paramount for homogenizing the as-built structure, potentially inducing recrystallization for finer, more equiaxed grains (depending on alloy and processing), and developing the crucial gamma′ microstructure. Met3dp possesses the metallurgical expertise to define and execute these critical heat treatments for IN738LC and Haynes 282.
- Alloy Design/Modification: Ongoing research explores minor alloying adjustments or seeding techniques to promote desirable microstructures during the AM build itself.
Quality Assurance & Certification – The Overarching Requirement: For flight-critical hardware, quality cannot be inspected w; it must be built w and rigorously verified. Meeting aerospace standards like AS9100 is non-negotiable.
- Wyzwanie: Ensuring that every single manufactured turbine disk segment is free from defects and meets all material property and dimensional specifications requires a comprehensive, multi-faceted quality system.
- Met3dp’s Integrated Quality Approach:
- Certified QMS: Operating under an AS9100-compliant (or equivalent) Quality Management System.
- Process Validation & Control: Locking down qualified machine/material/process parameter combinations (Fixed Process Control). Utilizing statistical process control (SPC) methods.
- Full Traceability: Maintaining meticulous records tracking powder batches, machine usage, process logs, post-processing steps, and inspection results for each individual part (digital thread).
- In-Process Monitoring (Advancing Tech): Exploring and implementing tools like melt pool monitoring (using photodiodes or cameras) and thermal imaging during the build to detect anomalies in real-time, providing early warnings of potential issues.
- Comprehensive NDT: Employing a suite of NDT methods (CT, FPI, UT etc.) as appropriate at defined stages.
- Mechanical Testing: Performing destructive testing (tensile, creep, fatigue) on representative samples built alongside the components or cut from witness coupons to verify material properties meet specifications.
- Detailed Documentation: Providing complete documentation packages (Certificate of Conformance, material certs, inspection reports) with each delivered part.
By systematically addressing these potential challenges through advanced technology like SEBM printing methods, process expertise, rigorous quality control, and a commitment to continuous improvement, Met3dp provides the reliability and assurance required to successfully implement additive manufacturing for demanding applications like superalloy jet turbine disk segments.
Choosing Your Partner: Selecting the Right Metal AM Service Provider for Aerospace Components
The decision to adopt additive manufacturing for flight-critical components like jet turbine disk segments carries significant implications. Selecting the right manufacturing partner is paramount and extends far beyond a simple transactional relationship. For engineers and procurement managers in the demanding aerospace sector, choosing a metal AM service provider requires a rigorous evaluation process focused on capability, quality, reliability, and expertise. This partnership is fundamental to successfully navigating the complexities of AM adoption, ensuring component integrity, and meeting stringent industry regulations.
Here are key criteria to consider when evaluating potential B2B suppliers for aerospace additive manufacturing:
- Aerospace Expertise & Proven Track Record:
- Demonstrated Experience: Look for providers with tangible experience in producing components for the aerospace industry, ideally including hot-section engine parts or similar high-stress, high-temperature applications. Ask for relevant (potentially anonymized) case studies or examples.
- Industry Knowledge: The provider must understand aerospace materials specifications (AMS, ASTM), quality clauses (flow-downs from prime contractors), and the general requirements of aerospace qualification processes (like Production Part Approval Process – PPAP, or First Article Inspection – FAI per AS9102).
- Material Specialization: Deep knowledge of processing the specific superalloys required (IN738LC, Haynes 282) is crucial, including their metallurgy, response to AM processing, and required post-processing nuances.
- Technological Capabilities & Equipment:
- Appropriate Technology: Does the provider offer the most suitable AM technology for your specific part and material? For complex superalloy turbine parts prone to residual stress, providers offering Selektywne topienie wiązką elektronów (SEBM), like Met3dp, present a significant advantage due to high preheat capabilities. Access to high-resolution Laser Powder Bed Fusion (L-PBF) might be needed for finer features. Met3dp offers industry-leading SEBM and L-PBF printers, providing flexibility.
- Build Volume & Condition: Ensure the machines have adequate build volume for your component size and are well-maintained and calibrated to ensure accuracy and repeatability. Inquire about their process monitoring and control capabilities.
- Material Portfolio & Quality Control:
- Certified Materials: Verify the provider can source or supply the required IN738LC or Haynes 282 powder certified to relevant aerospace specifications.
- Powder Management: Critically evaluate their procedures for incoming powder inspection, qualification, handling, storage (controlled environment), traceability (batch tracking), and recycling/rejuvenation protocols. Contaminated or degraded powder directly compromises part quality. Met3dp’s in-house powder production provides a distinct advantage in controlling quality from the source.
- End-to-End Process Control & Post-Processing:
- Integrated Workflow: Producing a flight-ready part requires seamless management of the entire process chain: DfAM consultation -> Printing -> Stress Relief -> Part Removal -> Support Removal -> HIP -> Heat Treatment -> Precision Machining -> Surface Finishing -> NDT -> Final Inspection.
- Capability Management: Assess whether the provider has strong in-house capabilities for these critical post-processing steps or utilizes a tightly controlled network of qualified, preferably Nadcap-accredited, subcontractors. Clear evidence of quality oversight and integration across the entire supply chain is essential.
- Quality Management System (QMS) & Certifications:
- AS9100 Certification: This certification (or equivalent, like EN 9100) is the internationally recognized standard for aerospace quality management systems. It should be considered a minimum requirement for suppliers of flight hardware, demonstrating robust processes for documentation, configuration management, process control, corrective actions, and continuous improvement. While Met3dp champions industry best practices, confirm the certification status relevant to your needs.
- Nadcap Accreditation: For special processes like heat treating, NDT, materials testing, or HIP, Nadcap accreditation of the facility performing the work (whether in-house or subcontracted) provides additional assurance of process control and compliance.
- Engineering & Application Support:
- Expertise Access: Does the provider offer access to engineers skilled in DfAM, AM process simulation, materials science, and ideally, turbomachinery or your specific application area?
- Collaboration: Look for a partner willing to collaborate proactively on optimizing the design for manufacturability and performance, troubleshooting issues, and developing tailored process parameters.
- Capacity, Scalability & Lead Time Reliability:
- Volume Capability: Can the provider handle your required volumes, from initial prototypes through potential low-rate or full-rate production?
- Reliable Scheduling: Do they have robust production planning and scheduling systems to provide realistic and reliable lead time estimates and meet delivery commitments?
- Future Growth: Assess their plans and capabilities to scale production capacity if your demand increases.
- Transparency, Communication & Partnership Focus:
- Open Communication: Look for clear, proactive communication channels and regular project updates.
- Transparent Quoting: While cost is a factor, for critical aerospace parts, value derived from quality, reliability, and expertise often outweighs chasing the lowest price. Ensure the quoting process is detailed and transparent.
- Long-Term View: Seek a supplier interested in building a long-term strategic partnership rather than just fulfilling short-term orders.
Met3dp positions itself as a strong contender across these criteria. Our integrated model, encompassing advanced powder manufacturing and industry-leading SEBM/L-PBF printing systems, combined with deep materials and processing expertise, provides a robust foundation. We are committed to meeting the stringent quality demands of the aerospace industry and collaborating closely with clients to deliver optimized, reliable components. When selecting your AM partner for critical applications like turbine disk segments, a thorough evaluation against these points will help ensure a successful outcome.
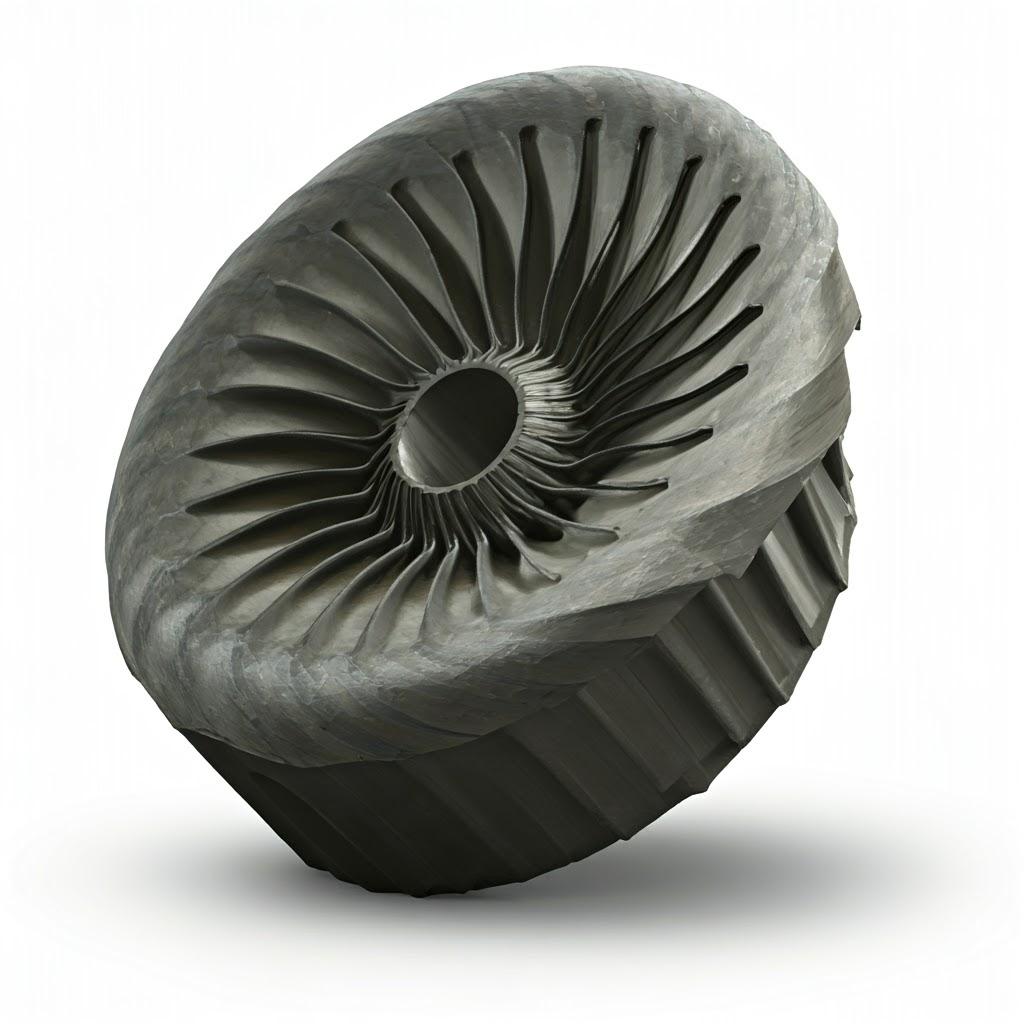
Understanding Cost Drivers and Lead Times for 3D Printed Turbine Disk Segments
Additive manufacturing of complex components from advanced superalloys like IN738LC and Haynes 282 represents a significant technological capability, but it’s essential for engineers and procurement managers to have a realistic understanding of the associated costs and lead times. While AM can offer compelling value propositions through design optimization, reduced buy-to-fly ratios, and potentially faster development cycles, it is not typically the “cheapest” manufacturing method on a per-part basis, especially compared to mature, high-volume traditional processes (if applicable). The focus should be on the Total Cost of Ownership (TCO) and the value derived from AM’s unique advantages.
Key Cost Drivers:
Several factors significantly influence the final cost of a 3D printed turbine disk segment:
- Koszt materiałów:
- Powder Price: Aerospace-grade nickel-based superalloy powders are intrinsically expensive, with prices often ranging from $50-$200+ per kilogram, depending on the specific alloy, quality level (e.g., purity, sphericity requirements for PREP powder), and quantity ordered.
- Powder Consumption: The total cost depends on the volume of the part itself, the volume of support structures required, and unavoidable losses during handling and processing. While unfused powder can often be recycled, this requires careful management and quality control, adding some process cost. The significantly improved buy-to-fly ratio compared to forging/machining remains a major cost advantage, however.
- AM Machine Time:
- Hourly Rate: This is often the largest single cost component. AM machines represent significant capital investment and have substantial operating costs (energy, inert gas/vacuum, maintenance). Hourly rates vary based on machine type (SEBM vs. L-PBF), size, age, and the provider’s pricing model.
- Build Time Drivers:
- Build Height (Z-axis): Print time is most strongly correlated with the height of the build, as each layer takes a finite amount of time to deposit and fuse. Printing taller parts takes proportionally longer.
- Part Volume/Complexity: The amount of material to be melted per layer (related to cross-sectional area) affects the time required for scanning/melting. Highly complex geometries might require slower scan speeds for accuracy.
- Nesting Efficiency: For production runs, efficiently packing multiple parts onto a single build plate (especially minimizing overall Z-height) is critical for reducing the per-part machine time cost.
- Struktury wsparcia:
- Direct Costs: Consume expensive superalloy powder and add to the print time.
- Indirect Costs: Removal is often labor-intensive and time-consuming, potentially requiring dedicated machining operations, adding significantly to the overall cost. Effective DfAM to minimize supports directly impacts final cost.
- Praca:
- Includes skilled operator time for machine setup, build monitoring, powder handling, part removal and cleaning, support removal, basic finishing, inspection tasks, and quality documentation.
- Post-Processing Costs (Can be very significant):
- Stress Relief / Heat Treatment: Costs include furnace time, energy consumption, inert gas/vacuum usage, and labor. Specialized furnaces are required.
- Prasowanie izostatyczne na gorąco (HIP): HIP is a high-cost process due to the specialized equipment, long cycle times (often 8-24 hours including heat-up/cool-down), high pressures, and controlled atmospheres. Costs are often per cycle, making full utilization of the HIP vessel important for economics.
- CNC Machining: Precision machining of tough superalloys is slow, requires specialized tooling with significant wear, and demands skilled machinists and programmers. Costs depend heavily on the amount of material to remove, the complexity of features (e.g., firtree slots), and the required tolerances/finishes.
- Badania nieniszczące (NDT): Specialized equipment (industrial CT scanners, FPI lines, UT systems) and certified NDT technicians represent significant costs. The level of inspection required (e.g., 100% CT scanning) heavily influences this cost component.
- Quality Assurance & Certification:
- Includes the overhead costs of maintaining an aerospace-certified QMS (e.g., AS9100), performing process validation, material testing (destructive tests on samples), and generating comprehensive documentation packages (often required per part).
- Non-Recurring Engineering (NRE):
- For new component designs, there are often upfront costs associated with DfAM optimization, AM process simulation, development and validation of specific process parameters, and initial qualification builds/testing. These costs are typically amortized over the production volume.
- Wolumen zamówienia:
- Significant per-part cost reductions are achievable at higher volumes due to amortization of NRE, optimized machine utilization through nesting, bulk material purchasing discounts, and streamlined post-processing workflows.
Estimating Lead Times:
Lead time – the duration from order placement to part delivery – is another critical factor. It’s influenced by many of the same factors as cost, particularly build time and the complexity of post-processing. A typical (highly variable) timeline for a qualified, first-article superalloy turbine disk segment might look like this:
- Phase 1: Pre-Processing (1-2 weeks):
- Order confirmation, final design review/freeze.
- AM build simulation (optional but recommended).
- Build file preparation, nesting, scheduling.
- Phase 2: Additive Manufacturing (Printing) (3 days – 2+ weeks):
- Machine setup, powder loading.
- Actual print time (highly dependent on build height, volume, nesting).
- Build cool-down.
- Phase 3: Post-Processing (3 – 8+ weeks):
- Stress Relief (on build plate): ~1 day.
- Part Removal (EDM/Saw): ~1 day.
- Support Removal & Basic Cleaning: 1-3 days (variable).
- HIP & Heat Treatment (Solution/Aging): 1-3 weeks (cycle times + furnace scheduling/logistics).
- CNC Machining: 1-4 weeks (highly dependent on complexity).
- Surface Finishing (Peening, Polishing): 2-5 days.
- NDT & Final Inspection: 3-7 days.
- Total Estimated Lead Time: Summing these ranges suggests typical lead times for a first article or prototype part can range from 6 to 12 weeks, and potentially longer for highly complex components or during initial process qualification phases.
Once a process is fully qualified and stable, lead times for subsequent production parts can often be shorter and more predictable, especially if parts can be built and processed in batches.
Getting Accurate Quotes: Given the number of variables, obtaining accurate cost and lead time estimates requires detailed information about the specific component (CAD model, material, tolerances, quality requirements) and the expected order volume. Working closely with an experienced AM provider like Met3dp is essential. We can analyze your specific needs, leverage our expertise in processing IN738LC and Haynes 282, and provide comprehensive quotes that reflect the true scope of work required to deliver flight-ready hardware. Understanding how DfAM choices influence support structures, print time, and machining requirements is also key to managing cost and lead time effectively.
Często zadawane pytania (FAQ)
Here are answers to some common questions regarding the 3D printing of jet turbine disk segments using superalloys like IN738LC and Haynes 282:
Q1: Are 3D printed turbine disk segments as strong and reliable as forged ones?
A: The ultimate goal of using additive manufacturing for these critical components is to achieve performance (strength, fatigue life, creep resistance, reliability) that is equivalent to or potentially better than conventionally manufactured (e.g., forged) counterparts. As-printed AM parts possess a different microstructure (often fine, columnar grains) compared to wrought materials. Therefore, comprehensive post-processing, particularly Prasowanie izostatyczne na gorąco (HIP) to close internal porosity and optimized obróbka cieplna (solutioning and aging) to develop the desired strengthening phases (like gamma′), is absolutely essential. When processed correctly, AM superalloys like IN738LC and Haynes 282 can achieve near-full density and exhibit excellent mechanical properties that meet or exceed typical specifications for forged materials. Furthermore, DfAM enables designs (e.g., topology-optimized structures, conformal cooling) that can reduce stress concentrations or operating temperatures, potentially leading to improved fatigue life or creep resistance compared to traditional designs. However, equivalence or superiority is not automatic; it must be rigorously demonstrated through extensive material characterization, component testing (including fatigue and creep tests under representative conditions), and formal qualification programs dictated by aerospace certification authorities and engine manufacturers.
Q2: What certifications are needed to supply 3D printed parts for jet engines?
A: Supplying flight-critical hardware for jet engines involves meeting some of the most stringent certification requirements across any industry. Key certifications and approvals typically include:
- AS9100 (or EN 9100): This is the fundamental Quality Management System standard for the Aviation, Space, and Defense industries. Certification demonstrates that the supplier has robust systems for process control, traceability, configuration management, risk management, and continuous improvement. It is generally considered a prerequisite.
- Nadcap Accreditations: Nadcap (National Aerospace and Defense Contractors Accreditation Program) provides industry-managed accreditation for special processes. Depending on the scope of work performed by the AM supplier and its subcontractors, Nadcap accreditation may be required for processes like Heat Treating, Materials Testing Laboratory, Non-Destructive Testing (NDT), and potentially Welding (if applicable). HIP facilities typically also hold relevant quality certifications.
- OEM-Specific Approvals: Major engine manufacturers (e.g., GE Aerospace, Rolls-Royce, Pratt & Whitney, Safran Aircraft Engines) have their own specific requirements, approved supplier lists, and material/process specifications. Suppliers must typically undergo audits and qualification processes defined by the specific customer before being approved to supply parts for their engines.
- Part/Process Qualification: Beyond system certifications, the specific part, material (e.g., IN738LC powder batch), AM process (machine, parameters), and post-processing steps must usually undergo a formal qualification process, often involving First Article Inspection Reports (FAIR) according to AS9102, process capability demonstrations, and extensive testing.
Q3: Can existing turbine disk segment designs be directly 3D printed?
A: While it might be technically feasible to take a CAD model of a legacy turbine disk segment (originally designed for forging and machining) and simply print it, this approach is generally not recommended and fails to capture the primary benefits of AM.
- Missed Optimization: Directly replicating a design intended for traditional manufacturing ignores the opportunities for lightweighting via topology optimization, performance enhancement through conformal cooling channels, or part consolidation – key value drivers for adopting AM.
- Manufacturability Issues: Legacy designs might incorporate features optimized for machining access (e.g., sharp internal corners, specific draft angles) that are suboptimal or challenging for the AM process, potentially leading to increased need for support structures, higher residual stresses, or difficulties in post-processing.
- Performance Differences: The material properties and residual stress state of an AM part can differ from its forged counterpart, even with identical geometry. Simply printing the old shape doesn’t guarantee identical performance or lifespan.
- Best Practice: Existing designs should ideally undergo a Projektowanie dla produkcji addytywnej (DfAM) review. This involves analyzing the part’s function and loads, then potentially redesigning or optimizing it specifically for the capabilities and constraints of the chosen AM process (e.g., SEBM or L-PBF) to maximize performance gains, ensure printability, and manage costs effectively.
Q4: What is the typical lifespan of a 3D printed superalloy turbine segment compared to traditional ones?
A: The aerospace industry mandates extremely high levels of reliability and durability. When introducing an AM component to replace a traditionally manufactured one, the engineering goal is invariably to achieve at least an equivalent operational lifespan, with the potential for life extension being a significant driver for AM adoption. Component life in the turbine hot section is often limited by creep deformation, low-cycle fatigue (LCF) from engine cycles, high-cycle fatigue (HCF) from vibrations, or oxidation/corrosion damage accumulation. AM, coupled with DfAM, offers potential pathways to extend life:
- Improved cooling (via conformal channels) can lower metal temperatures, drastically slowing creep rates and thermal fatigue damage.
- Topology optimization can reduce peak stresses in critical areas, improving fatigue life.
- Potentially optimized microstructures achievable through AM + post-processing could enhance intrinsic material resistance. However, predicting and validating the lifespan of AM components requires sophisticated lifing models adapted for AM material characteristics (e.g., potential anisotropy, specific defect populations) and extensive, engine-relevant testing (cyclic spin pit tests, thermal-mechanical fatigue tests, engine endurance tests). Any claims of extended life must be rigorously substantiated through this demanding certification process.
Q5: How does Met3dp ensure the quality of its IN738LC and Haynes 282 powders?
A: Met3dp recognizes that premium powder quality is the bedrock of reliable additive manufacturing for critical applications. Our quality assurance strategy for aerospace-grade superalloy powders like IN738LC and Haynes 282 is comprehensive:
- Advanced Production Technology: We utilize state-of-the-art Atomizacja gazowa (GA) equipment featuring optimized nozzle designs for high sphericity and yield, alongside the Proces plazmowej elektrody rotacyjnej (PREP), renowned for producing exceptionally clean, spherical powders with minimal satellites, ideal for the most demanding applications.
- Strict Raw Material Control: We begin with high-purity elemental or master alloy input materials, sourced from qualified suppliers with accompanying certifications.
- Controlled Atomization Parameters: Key parameters like melt temperature, gas pressure/flow (GA), electrode rotation speed (PREP), and cooling rates are tightly controlled to achieve the target Particle Size Distribution (PSD) and morphology while minimizing contamination.
- Post-Atomization Classification: Powders are carefully sieved and classified into specific PSD ranges tailored for optimal performance in different AM machine types (SEBM, L-PBF) and layer thicknesses. Blending ensures batch homogeneity.
- Rigorous Lot Testing & Certification: Every production batch undergoes extensive Quality Control testing before release, including:
- Skład chemiczny: Verified using methods like ICP-OES or XRF to ensure compliance with AMS or customer specifications.
- Rozkład wielkości cząstek: Measured accurately using laser diffraction (e.g., Malvern Mastersizer).
- Morfologia: Assessed via Scanning Electron Microscopy (SEM) for sphericity, satellite levels, and internal porosity.
- Płynność: Measured using standardized tests like Hall Flowmeter (ASTM B213).
- Gęstość: Apparent density (ASTM B212) and Tap density (ASTM B527) are measured.
- Gas Content: Oxygen and Nitrogen levels measured (e.g., LECO analysis).
- Controlled Environment: Powder handling, sieving, blending, and packaging are performed in controlled environments (e.g., inert gas glove boxes) to prevent atmospheric contamination and moisture pickup. Vacuum packaging is standard.
- Documentation: Each batch is shipped with a detailed Certificate of Analysis (CoA) providing full traceability and confirming compliance with all specified parameters.
This meticulous focus on powder production and quality control ensures that Met3dp customers receive consistently high-quality, reliable superalloy powders tailored for success in their critical aerospace AM applications.
Conclusion: The Future is Additive – Advancing Jet Engine Technology with Met3dp
The landscape of aerospace manufacturing is undergoing a profound transformation, and metal additive manufacturing sits at the epicenter of this revolution. For highly stressed, high-temperature components like jet turbine disk segments, AM is moving beyond prototyping and niche applications to become a viable, value-adding production technology. It represents a fundamental shift, enabling engineers to break free from the shackles of traditional manufacturing constraints and unlock new levels of performance, efficiency, and design innovation.
Throughout this discussion, we’ve explored how AM, particularly when paired with advanced nickel-based superalloys like IN738LC and Haynes 282, offers compelling advantages:
- Niezrównana swoboda projektowania: Enabling complex geometries like conformal cooling channels and topology-optimized structures that enhance thermal management, reduce weight, and improve mechanical integrity.
- Accelerated Development: Facilitating rapid design iteration and potentially shortening lead times compared to processes reliant on dedicated tooling like forging.
- Wydajność materiałowa: Significantly improving the buy-to-fly ratio for expensive superalloys, reducing waste and material costs.
- Pathways to Enhanced Performance: Offering the potential for lighter, more efficient, and more durable components that contribute directly to the next generation of aircraft propulsion systems – engines that fly further, faster, cleaner, and more reliably.
However, realizing these benefits in the demanding, safety-critical world of aerospace requires more than just a 3D printer. It demands deep expertise in materials science, process optimization, rigorous quality control, and a holistic understanding of the entire manufacturing workflow, from initial design concept to fully qualified and certified hardware.
To jest miejsce Met3dp stands as a leader and key enabler. We provide comprehensive, integrated additive manufacturing solutions specifically tailored to the needs of industries like aerospace. Our unique value proposition combines:
- Cutting-Edge AM Systems: Offering industry-leading drukarki 3D do metalu, including advanced Selective Electron Beam Melting (SEBM) technology ideally suited for processing challenging superalloys with reduced residual stress.
- Premium Metal Powders: Leveraging our in-house expertise and advanced Gas Atomization and PREP technology to produce high-quality, aerospace-grade IN738LC, Haynes 282, and other critical alloy powders optimized for AM.
- End-to-End Expertise: Possessing the knowledge and capabilities to support customers throughout the entire journey – from DfAM consultation and process simulation to printing, critical post-processing (including HIP, heat treatment, machining management), and stringent quality assurance protocols.
We are committed to partnering with aerospace engineers, designers, and procurement managers who are ready to harness the transformative power of additive manufacturing. Whether you are exploring AM for the first time, seeking to qualify a specific component, or looking for a reliable partner for series production, Met3dp has the technology, materials, and expertise to help you achieve your goals.
The future of jet engine technology is undeniably additive. Let Met3dp be your trusted partner in navigating this exciting frontier. We invite you to explore our capabilities further on our website and contact us today to discuss your specific requirements for 3D printed turbine disk segments or other demanding aerospace applications. Let’s build the future of flight, together.
Udostępnij
MET3DP Technology Co., LTD jest wiodącym dostawcą rozwiązań w zakresie produkcji addytywnej z siedzibą w Qingdao w Chinach. Nasza firma specjalizuje się w sprzęcie do druku 3D i wysokowydajnych proszkach metali do zastosowań przemysłowych.
Zapytaj o najlepszą cenę i spersonalizowane rozwiązanie dla Twojej firmy!
Powiązane artykuły
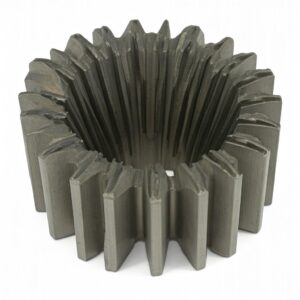
Wysokowydajne segmenty łopatek dysz: Rewolucja w wydajności turbin dzięki drukowi 3D w metalu
Czytaj więcej "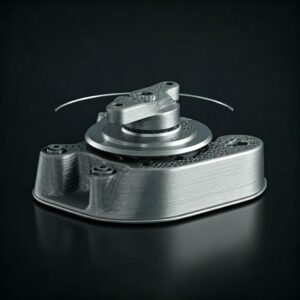
Drukowane w 3D mocowania dla samochodowych czujników radarowych: Precyzja i wydajność
Czytaj więcej "Informacje o Met3DP
Ostatnia aktualizacja
Nasz produkt
KONTAKT
Masz pytania? Wyślij nam wiadomość teraz! Po otrzymaniu wiadomości obsłużymy Twoją prośbę całym zespołem.
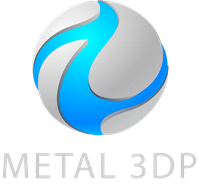
Proszki metali do druku 3D i produkcji addytywnej