Marine Heat Exchangers via Metal 3D Printing.
Spis treści
The maritime industry operates under some of the most demanding conditions on Earth. Components must withstand constant vibration, corrosive saltwater environments, extreme temperature fluctuations, and immense pressure, all while delivering unwavering reliability. Among the most critical components ensuring the smooth operation of any vessel are heat exchangers. These devices are fundamental to managing thermal loads across various onboard systems, from main propulsion engines to auxiliary machinery and climate control. Traditionally, manufacturing these vital parts involved complex processes like casting, brazing, and welding – methods often constrained by design limitations and long lead times. However, the advent of wytwarzanie przyrostowe metali (AM), or metal Drukowanie 3D, is ushering in a new era for marine heat exchanger design, production, and performance. This technology offers unprecedented opportunities to create highly optimized, complex, and efficient heat exchangers tailored specifically for the rigorous demands of marine applications. For procurement managers, marine engineers, and MRO suppliers, understanding the potential of metal AM is becoming increasingly crucial for maintaining a competitive edge and enhancing operational efficiency.
Introduction to Metal 3D Printed Marine Heat Exchangers
A marine heat exchanger is a device designed to transfer thermal energy between two or more fluids (typically liquids or gases) within a ship’s systems, without allowing the fluids to mix directly. Their primary function is to regulate temperature, either by cooling down essential machinery or by heating specific processes or spaces. Common types include shell-and-tube, plate, and plate-fin heat exchangers, each tailored for different applications based on factors like pressure, temperature, fluid types, and space constraints.
Why do they matter so much in maritime operations?
- Engine Cooling: Preventing overheating in main propulsion engines and auxiliary generators, which is critical for reliability and longevity.
- Lubrication Oil Cooling: Maintaining optimal viscosity for lubricating oils.
- HVAC Systems: Enabling heating and air conditioning for crew comfort and sensitive equipment.
- Cargo Temperature Control: Ensuring refrigerated or heated cargo maintains its required temperature.
- Hydraulic Systems: Cooling hydraulic fluids to prevent degradation and ensure proper function.
- Waste Heat Recovery: Capturing heat from exhaust gases or cooling systems to improve overall vessel energy efficiency.
Given their vital role, the performance and reliability of marine heat exchangers directly impact a vessel’s operational safety, fuel efficiency, and maintenance costs. Failure can lead to catastrophic engine damage, mission compromise, or costly downtime.
Enter Metal Additive Manufacturing:
Metal 3D printing builds components layer by layer directly from a digital CAD model using high-performance metal powders. This contrasts sharply with subtractive methods (like machining) or traditional forming/joining techniques. For marine heat exchangers, AM offers transformative potential:
- Bezprecedensowa swoboda projektowania: Engineers are no longer bound by the limitations of traditional manufacturing. Complex internal channels, optimized fin structures (like Triply Periodic Minimal Surfaces – TPMS), and integrated manifolds can be designed to maximize thermal efficiency and minimize pressure drop within a compact footprint.
- Konsolidacja części: Multiple components of a traditional heat exchanger assembly (e.g., tubes, shells, baffles, end caps) can potentially be printed as a single, monolithic part. This reduces potential leak paths, simplifies assembly, lowers part count, and can decrease overall weight.
- Optymalizacja materiałów: AM allows for the use of advanced alloys specifically chosen for their superior thermal conductivity, corrosion resistance in saltwater, or high-temperature strength – properties essential for demanding marine environments. Companies like Met3dp specialize in producing high-purity, spherical proszki metali ideal for these applications.
- Rapid Prototyping and On-Demand Production: New designs can be prototyped and tested quickly. Furthermore, spare parts can be printed on-demand, significantly reducing the need for large physical inventories and shortening lead times for critical replacements, a key benefit for MRO suppliers and fleet operators.
By leveraging these advantages, metal 3D printing enables the creation of marine heat exchangers that are lighter, more compact, more efficient, and potentially more reliable than their conventionally manufactured counterparts.
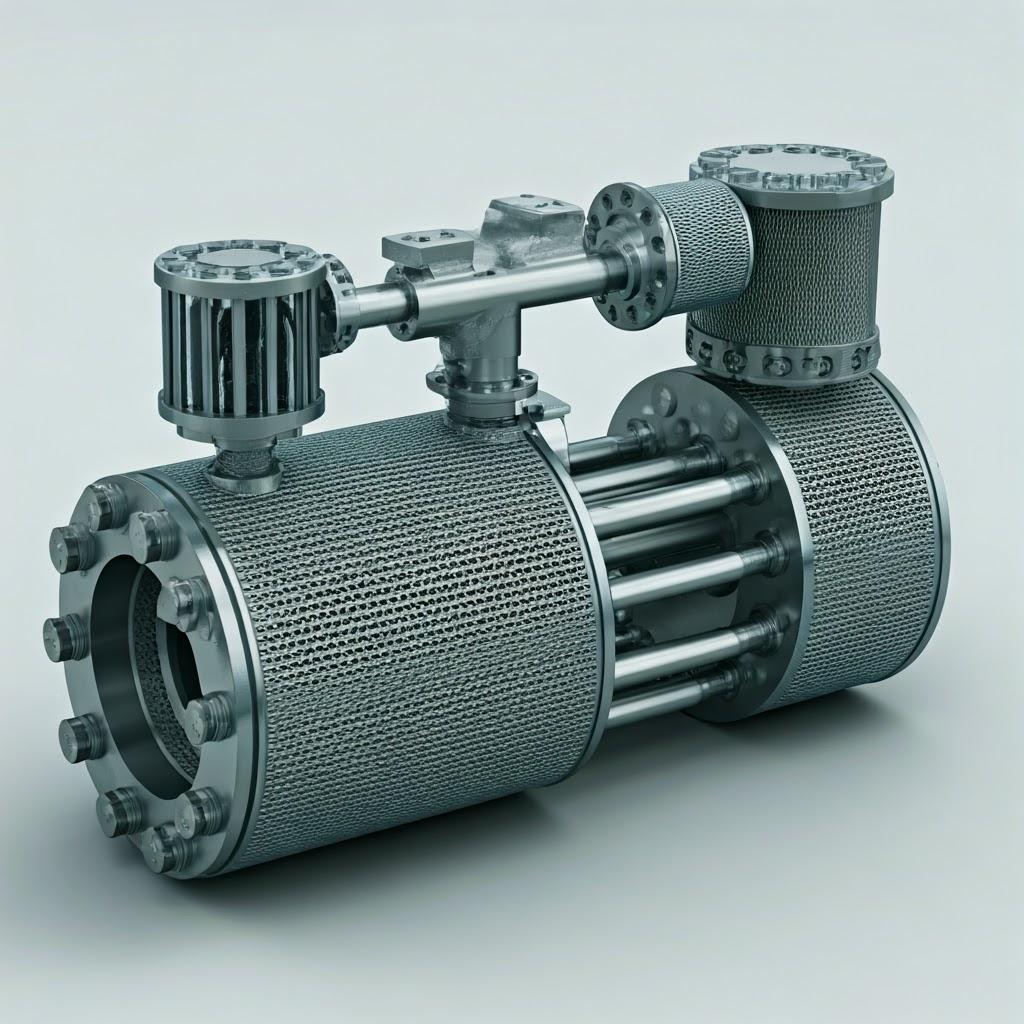
Applications and Use Cases for AM Marine Heat Exchangers
The versatility of metal additive manufacturing opens up a wide range of applications for 3D printed heat exchangers across the maritime sector. The ability to customize designs and utilize specialized materials makes AM particularly suitable for niche, high-performance, or challenging installations.
Key Functional Applications within Ship Systems:
- Engine Jacket Water Cooling: High-performance, compact coolers designed for main engines and generators, potentially using materials like CuCrZr for maximum heat dissipation or IN625 for longevity in harsh conditions.
- Lube Oil Coolers: Optimized designs to efficiently cool lubricating oils, critical for engine health. AM allows for complex internal structures that enhance turbulence and heat transfer.
- Charge Air Coolers: Intercoolers and aftercoolers for turbocharged engines, where efficiency directly impacts engine power and fuel consumption. AM can create intricate fin designs impossible with traditional methods.
- Hydraulic Oil Coolers: Compact and robust coolers for stabilizing hydraulic fluid temperatures in systems operating winches, cranes, steering gear, or stabilizers.
- Fuel Coolers/Heaters: Temperature regulation for fuel conditioning systems, particularly important for vessels using varying fuel types or operating in extreme climates.
- HVAC&R Chillers/Condensers: Components for onboard air conditioning and refrigeration plants, where efficiency gains translate to significant energy savings. AM enables compact designs ideal for space-constrained marine environments.
- Steam Condensers: For steam propulsion systems or waste heat recovery units, often requiring high-temperature and corrosion-resistant materials like IN625.
- LNG Vaporizers: Specialized heat exchangers used on LNG carriers or LNG-fueled vessels, demanding materials suitable for cryogenic temperatures and stringent safety standards.
Use Cases Across Different Vessel Types:
Vessel Type | Specific AM Heat Exchanger Applications & Benefits | Target B2B Audience |
---|---|---|
Commercial Shipping | Compact, efficient engine/oil coolers for space savings; high-corrosion resistance (316L, IN625) for longevity; on-demand spares for reduced downtime. | Ship Owners, Fleet Managers, MRO Suppliers, Wholesalers |
Naval Vessels | High-performance, weight-optimized coolers; reduced acoustic signature designs; rapid deployment of custom solutions; enhanced survivability (IN625). | Defense Contractors, Naval Procurement, Shipyards |
Offshore Platforms | Robust, corrosion-resistant (IN625) units for harsh environments; specialized process coolers; compact designs for platform integration. | Oil & Gas Operators, Platform Engineers, EPC Contractors |
Luxury Yachts | Highly customized, compact HVAC and engine cooling solutions; minimized noise and vibration; aesthetic integration possibilities. | Yacht Builders, Design Firms, Owner Representatives |
Research Vessels | Specialized cooling for scientific equipment; high-reliability systems for remote operations; custom designs for unique experimental setups. | Research Institutions, Ship Operators |
Ferries & Cruise Ships | High-efficiency HVAC components for passenger comfort & energy savings; reliable engine cooling for demanding schedules. | Ferry Operators, Cruise Lines, Maintenance Providers |
Eksport do arkuszy
OEM vs. MRO Scenarios:
- Original Equipment Manufacturing (OEM): AM enables naval architects and shipbuilders to integrate highly optimized heat exchangers from the initial design phase. This allows for performance maximization, space saving, and potential weight reduction integrated seamlessly into the vessel’s systems. B2B suppliers working with shipyards can offer innovative AM solutions.
- Maintenance, Repair, and Overhaul (MRO): For existing vessels, AM offers a powerful solution for replacing obsolete or hard-to-source heat exchangers. Spare parts can be produced on-demand, potentially with improved designs or materials compared to the original. This drastically reduces lead times compared to traditional sourcing, minimizing vessel downtime. MRO providers and wholesale distributors can leverage AM for responsive part supply. Digital inventories (CAD files) replace physical stock, offering flexibility for global fleet support.
Why Choose Metal Additive Manufacturing for Marine Heat Exchangers?
While traditional manufacturing methods have served the maritime industry for decades, they inherently come with limitations, particularly when dealing with the complex geometries required for optimal thermal performance. Metal AM provides compelling advantages that address these constraints, offering significant benefits for engineers, procurement specialists, and ship operators focused on performance, efficiency, and lifecycle cost.
Comparison: Metal AM vs. Traditional Methods
Cecha | Wytwarzanie przyrostowe metali (AM) | Traditional Methods (Casting, Brazing, Welding, Machining) | Marine Industry Implications |
---|---|---|---|
Złożoność projektu | Virtually unlimited; enables intricate internal channels, TPMS, lattices | Limited by tooling, casting molds, machining access, joining methods | AM allows designs optimized purely for thermal/fluid dynamics, leading to higher efficiency and compactness. |
Konsolidacja części | High potential; multiple parts printable as one unit | Low potential; assemblies require multiple components and joints | Fewer joints mean reduced leak paths, simplified assembly, potentially lower weight, and increased reliability. |
Opcje materiałowe | Growing range of advanced alloys (IN625, CuCrZr, Ti alloys) | Established but sometimes limited for complex shapes (e.g., casting) | AM enables use of ideal materials for corrosion, temperature, and conductivity, matched precisely to the application. |
Lead Time (Prototyping) | Very Fast (days/weeks) | Slow (weeks/months, requires tooling) | Rapid design iteration and testing accelerates development cycles for new vessel designs or system upgrades. |
Lead Time (Production) | Moderate; suitable for low-to-medium volumes, on-demand spares | Can be fast for high volumes (mass production), slow for custom parts | AM excels at producing spares quickly, reducing MRO downtime. Scalability is improving for serial production. |
Koszty oprzyrządowania | Brak | High (molds, dies, fixtures) | Eliminates significant upfront investment, making custom or low-volume production economically viable. |
Redukcja wagi | Significant potential through topology optimization & complex shapes | Limited potential; often relies on material selection | Lower weight contributes to fuel efficiency and improved vessel stability. |
Waste Material | Minimal (powder is recyclable) | Significant (machining chips, casting runners/risers) | More sustainable manufacturing process. |
Eksport do arkuszy
Key Advantages Driving Adoption:
- Enhanced Thermal Performance: AM enables the creation of internal structures – such as gyroids, lattice networks, or optimized fin arrays – that dramatically increase the surface area available for heat transfer within a given volume. This leads to more effective cooling or heating, potentially allowing for smaller, lighter heat exchangers that achieve the same or better performance than larger traditional units. This is a major driver for B2B customers seeking efficiency gains.
- Compactness and Weight Savings: By consolidating parts and optimizing topology (removing unnecessary material while maintaining structural integrity), AM can produce heat exchangers that are significantly lighter and smaller. This is invaluable in marine applications where space is at a premium and weight reduction contributes to fuel economy and cargo capacity.
- Improved Fluid Dynamics: Complex channel geometries achievable with AM can be designed to promote turbulence exactly where needed, enhancing heat transfer while simultaneously optimizing flow paths to minimize pressure drop. This delicate balance is difficult to achieve with traditional manufacturing constraints.
- Supply Chain Resilience & On-Demand Spares: The ability to print parts locally or regionally based on digital files transforms the spare parts supply chain. Vessel operators and MRO providers are less reliant on complex global supply chains and long lead times for critical components. A digital inventory allows for “just-in-time” manufacturing of spares, minimizing costly downtime. Companies like Met3dp, with expertise in both procesy wytwarzania przyrostowego and materials, can be key partners in establishing such digital supply chains.
- Customization and Retrofitting: AM is ideal for creating bespoke heat exchanger solutions tailored to specific vessel requirements or for retrofitting improved designs into existing systems where off-the-shelf components may not fit or perform optimally.
- Reduced Leak Potential: Printing multi-part assemblies as a single monolithic component eliminates potential leak points associated with traditional joints (brazed, welded, gasketed). This enhances reliability, particularly crucial for systems operating under high pressure or handling hazardous fluids.
For procurement managers evaluating long-term value and operational efficiency, and for engineers pushing the boundaries of thermal management, the strategic advantages offered by metal additive manufacturing for marine heat exchangers are becoming increasingly compelling.
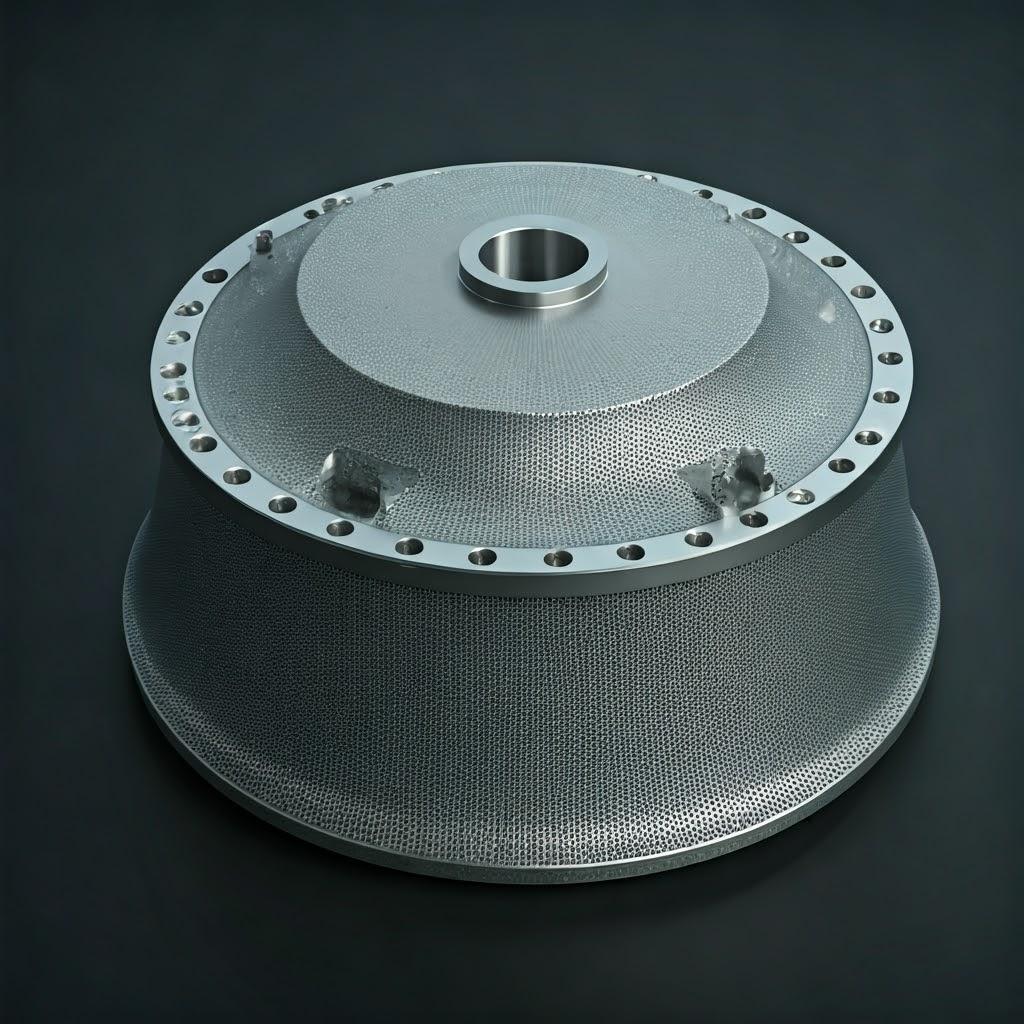
Recommended Metal Powders for 3D Printed Heat Exchangers (CuCrZr, IN625, 316L)
The choice of material is paramount to the success of any marine heat exchanger, especially one produced via additive manufacturing. The powder characteristics directly influence the printability, final part density, mechanical properties, and ultimately, the performance and lifespan of the component in the harsh marine environment. Met3dp, leveraging its advanced gas atomization and PREP technologies, produces high-sphericity, high-flowability metal powders optimized for AM processes like Selective Electron Beam Melting (SEBM) and Laser Powder Bed Fusion (LPBF). Here’s an analysis of the recommended powders for marine heat exchangers:
1. CuCrZr (Copper Chromium Zirconium)
- Kluczowe właściwości:
- Doskonała przewodność cieplna: Significantly higher than steels or nickel alloys, making it ideal for applications where rapid heat dissipation is the primary goal.
- Good Mechanical Strength (for a copper alloy): Precipitation hardening provides better strength and hardness compared to pure copper, especially at slightly elevated temperatures.
- Dobra odporność na korozję: Offers reasonable resistance in freshwater and mildly corrosive environments, but less so than stainless steels or nickel alloys in aggressive saltwater.
- Dobra drukowność: Generally processes well in LPBF systems, although requires careful parameter optimization due to high reflectivity and conductivity.
- Why it Matters for Marine Heat Exchangers:
- Primarily chosen for applications demanding the highest possible thermal efficiency in a compact space, such as high-performance engine coolers or electronics cooling.
- Its strength allows for relatively thin walls, further enhancing heat transfer.
- Rozważania:
- Lower corrosion resistance compared to IN625 or 316L, potentially requiring protective coatings or careful application selection (e.g., closed-loop freshwater systems).
- Higher material cost compared to 316L.
- Requires specialized AM parameter sets due to copper’s optical and thermal properties.
2. IN625 (Inconel 625 – Nickel Chromium Superalloy)
- Kluczowe właściwości:
- Wyjątkowa odporność na korozję: Outstanding resistance to a wide range of corrosive media, including saltwater, crevice corrosion, pitting, and acidic environments. This is its primary advantage in marine applications.
- High Strength at Elevated Temperatures: Maintains excellent mechanical properties up to high temperatures (e.g., 650°C and beyond).
- Excellent Weldability and Fabricability (in wrought form): Translates to good processability in AM, resulting in dense, strong parts.
- Dobra wytrzymałość zmęczeniowa: Important for components subjected to cyclic loading and vibration onboard ships.
- Why it Matters for Marine Heat Exchangers:
- The go-to choice for maximum durability and longevity in direct saltwater cooling applications or when handling corrosive fluids.
- Suitable for high-temperature applications like exhaust gas heat recovery or steam condensers.
- Ideal for critical systems where reliability and minimal maintenance are paramount (e.g., naval applications, offshore platforms).
- Rozważania:
- Lower thermal conductivity compared to CuCrZr or even 316L (approx. 10-11 W/m·K). Design must compensate through increased surface area (enabled by AM).
- Higher material cost and density compared to stainless steel.
3. 316L Stainless Steel (Austenitic Stainless Steel)
- Kluczowe właściwości:
- Dobra odporność na korozję: Offers good resistance to general corrosion, pitting, and creville corrosion in many marine environments, though less robust than IN625 in highly aggressive conditions. The ‘L’ denotes low carbon content, improving weldability and reducing sensitization risk.
- Good Mechanical Properties: Provides a good balance of strength, ductility, and toughness at ambient and moderately elevated temperatures.
- Doskonała drukowność: One of the most common and well-understood materials for metal AM, readily processed with high density.
- Opłacalność: Significantly lower material cost compared to IN625 or CuCrZr.
- Good Availability: Widely available from numerous powder suppliers, including specialist providers like Met3dp known for high-quality spherical powders.
- Why it Matters for Marine Heat Exchangers:
- A versatile and cost-effective workhorse material suitable for a wide range of standard marine heat exchanger applications (e.g., freshwater cooling, hydraulic oil cooling, some HVAC components) where extreme corrosion or temperature is not the primary concern.
- Often used for prototyping or less critical applications before potentially upgrading to IN625 if needed.
- Its ease of printing makes it suitable for complex geometries aiming for improved thermal performance over traditional stainless steel designs.
- Rozważania:
- Thermal conductivity is moderate (approx. 15 W/m·K), better than IN625 but much lower than CuCrZr.
- Susceptible to chloride stress corrosion cracking at higher temperatures and chloride concentrations.
Material Selection Summary Table:
Materiał | Primary Advantage | Key Disadvantage(s) | Typical Marine Applications | Koszt względny | Przewodność cieplna (W/m-K) |
---|---|---|---|---|---|
CuCrZr | Highest Thermal Conductivity | Lower Corrosion Resistance, Higher Cost | High-efficiency coolers (engine, electronics), where heat flux is critical | Wysoki | ~300+ |
IN625 | Exceptional Corrosion & Temp. Resistance | Lower Thermal Conductivity, Highest Cost | Saltwater coolers, exhaust gas recovery, high-temp/pressure systems, critical components | Najwyższy | ~11 |
316L | Cost-Effective, Good All-Round | Moderate Thermal Conductivity & Corrosion Res. | General purpose cooling (freshwater, oil), HVAC, non-critical systems, prototypes | Najniższy | ~15 |
Eksport do arkuszy
Met3dp’s Role in Material Excellence:
Choosing the right alloy is only part of the equation. The quality of the metal powder itself is critical for successful additive manufacturing. Met3dp utilizes industry-leading Gas Atomization and Plasma Rotating Electrode Process (PREP) technologies. This allows for the production of metal powders with:
- Wysoka sferyczność: Ensures good powder flowability and uniform spreading during the printing process.
- Low Porosity: Minimizes internal defects in the final part.
- Kontrolowany rozkład wielkości cząstek (PSD): Optimized for specific AM processes (LPBF, SEBM) to achieve high density and good surface finish.
- Wysoka czystość: Reduces contaminants that could compromise material properties.
By controlling these factors, Met3dp provides powders like IN625, 316L, and potentially specialized copper alloys that enable customers to reliably print dense, high-performance marine heat exchangers with superior mechanical properties and corrosion resistance, meeting the stringent demands of the maritime industry. Their expertise ensures that B2B clients, from wholesale distributors to end-users, receive materials optimized for additive manufacturing success.
Design Optimization Strategies for Additively Manufactured Heat Exchangers
One of the most profound impacts of metal additive manufacturing (AM) on marine heat exchanger development lies in the realm of design. Freed from the constraints of traditional manufacturing processes, engineers can employ Projektowanie dla produkcji addytywnej (DfAM) principles to create components optimized for thermal performance, fluid dynamics, weight, and integration. Simply replicating a traditionally designed heat exchanger using AM often misses the technology’s true potential. Instead, a ground-up DfAM approach is necessary to unlock significant performance gains, crucial for B2B customers seeking competitive advantages in efficiency and reliability.
Key DfAM Strategies for Heat Exchangers:
- Maximizing Surface Area-to-Volume Ratio: Heat transfer is fundamentally linked to surface area. AM excels at creating complex internal geometries that vastly increase this area within a given volume.
- Triply Periodic Minimal Surfaces (TPMS): Structures like Gyroids, Schwarz-P, or Diamond surfaces offer very high surface area, promote fluid mixing (turbulence), and are self-supporting to some extent, reducing the need for complex internal supports during printing. They represent a paradigm shift from traditional tube-and-shell or fin designs.
- Struktury kratowe: Stochastic or strut-based lattices can also be used to create highly porous structures with large surface areas, functioning like intricate metal foams tailored for heat exchange.
- Optimized Fin Geometries: Instead of simple extruded fins, AM allows for curved, variable-thickness, or organically shaped fins precisely placed to optimize flow and heat transfer.
- Optimizing Fluid Flow Paths: AM enables the design of smooth, curved channels that minimize pressure drop compared to the abrupt turns often required in traditionally fabricated assemblies.
- Flow Channel Shaping: Channels can be shaped to maintain desired flow velocities, manage turbulence, and ensure even distribution across the heat exchange surfaces. Computational Fluid Dynamics (CFD) simulations become powerful tools when coupled with the design freedom of AM.
- Integrated Manifolds: Inlet and outlet manifolds can be seamlessly integrated into the heat exchanger body, reducing the need for separate components and optimizing flow distribution from the start.
- Konsolidacja części: This is a cornerstone of DfAM.
- Reducing Components: Printing what was previously an assembly of tubes, baffles, shells, and end caps as a single, monolithic part drastically reduces potential leak points (brazed/welded joints, gaskets).
- Simplifying Assembly: Eliminates complex assembly steps, reducing labor costs and potential for errors.
- Improving Structural Integrity: A single printed part can often be stronger and more robust than a comparable assembly.
- Designing for Manufacturability (AM Specifics):
- Struktury wsparcia: While TPMS and some organic shapes minimize internal supports, external supports and some internal ones might still be necessary depending on the geometry and AM process (e.g., LPBF often requires more supports than SEBM for certain overhangs). Designs must allow access for support removal, especially from internal channels.
- Usuwanie proszku: Complex internal channels must include pathways or strategically placed drainage holes for removing unfused metal powder after printing. Trapped powder can add weight, impede flow, and potentially contaminate the system.
- Minimalna grubość ścianki: Designs must adhere to the minimum printable wall thickness for the chosen material and AM process to ensure structural integrity and prevent print failures. Met3dp’s experience can guide customers on achievable limits with their advanced equipment.
- Orientacja: The orientation of the part on the build plate affects support needs, surface finish on different faces, and potentially residual stress. Designing with an optimal build orientation in mind is crucial.
- Thermal Management During Printing: Large thermal gradients can cause stress and distortion. Design features like variable thickness or filleted corners can help manage heat flow during the build process.
Example DfAM Application:
Consider a traditional shell-and-tube oil cooler. Using DfAM and AM:
- The shell, tubes, baffles, and end caps could be printed as one part.
- The internal tubes could be replaced with a highly efficient TPMS structure (e.g., Gyroid).
- The inlet/outlet ports could be smoothly integrated with optimized flow paths.
- Topology optimization could remove unnecessary material from the outer casing, reducing weight.
The resulting AM heat exchanger could be smaller, lighter, leak-proof by design, and offer significantly higher cooling efficiency compared to its traditional counterpart. Engaging with AM experts, such as the team at Met3dp, early in the design phase is crucial to fully leverage these DfAM possibilities.
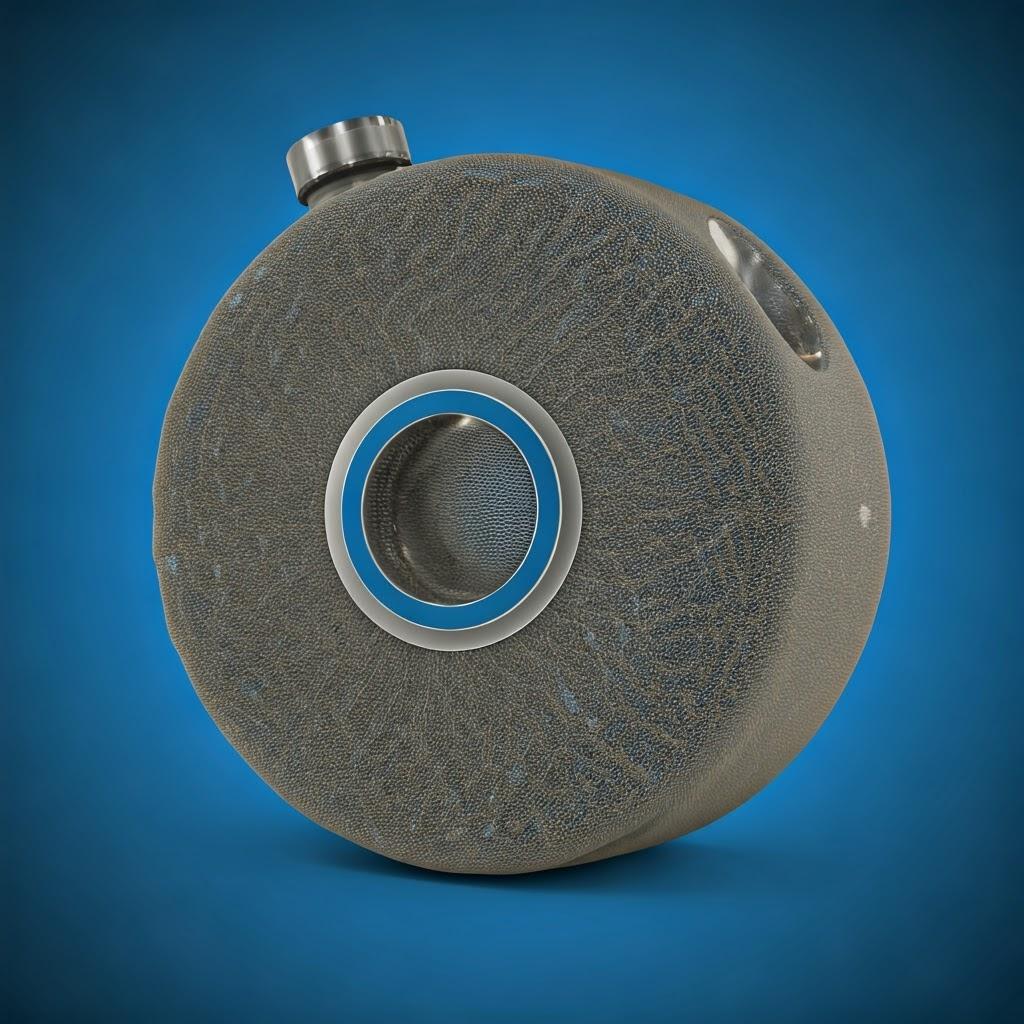
Osiągalne tolerancje, wykończenie powierzchni i dokładność wymiarowa
While metal AM offers incredible design freedom, it’s essential for engineers and procurement managers to have realistic expectations regarding the achievable precision of 3D printed marine heat exchangers. Tolerances, surface finish, and overall dimensional accuracy are influenced by the specific AM process used (e.g., LPBF, SEBM), the material, part size and geometry, print parameters, and post-processing steps.
Understanding Key Terms:
- Tolerance: The permissible limit or limits of variation in a physical dimension of a part. Often expressed as a range (e.g., ±0.1 mm).
- Wykończenie powierzchni (chropowatość powierzchni): Measures the fine-scale irregularities on a part’s surface. Commonly quantified by Ra (average roughness), typically in micrometers (µm). A lower Ra value indicates a smoother surface.
- Dokładność wymiarowa: How closely the printed part conforms to the dimensions specified in the original CAD model.
Typical Values for Metal AM Processes:
Cecha | Laser Powder Bed Fusion (LPBF/SLM) | Selektywne topienie wiązką elektronów (SEBM) | Uwagi |
---|---|---|---|
Dokładność wymiarowa | Typically ±0.1% to ±0.2% (min. ±0.1-0.2 mm) | Typically ±0.2% to ±0.4% (min. ±0.2-0.4 mm) | Can vary significantly with part size, geometry, material, and parameter optimization. Larger parts generally have larger absolute deviations. |
As-Printed Ra (Sides) | ~6 – 15 µm | ~20 – 40 µm | LPBF generally produces smoother side walls due to smaller powder particles and layer heights. |
As-Printed Ra (Top) | ~10 – 20 µm | ~30 – 50 µm | Top surfaces are often rougher due to the last layers of powder fusion. |
As-Printed Ra (Overhangs) | Can be significantly higher (>20 µm for LPBF, >50 µm for SEBM) | Can be significantly higher (>20 µm for LPBF, >50 µm for SEBM) | Down-facing surfaces and supported areas tend to be rougher. |
Minimalny rozmiar funkcji | ~0.2 – 0.4 mm | ~0.4 – 0.8 mm | Relates to wall thickness, hole diameter, channel width achievable. |
Eksport do arkuszy
Factors Influencing Precision:
- AM Technology: As noted, LPBF generally offers slightly better accuracy and surface finish than SEBM in the as-printed state, primarily due to finer powder and smaller melt pools. However, SEBM often requires fewer supports and can process certain materials more effectively with less residual stress. Met3dp provides solutions utilizing various leading metody drukowania to best suit application needs.
- Materiał: Different metal powders behave differently during melting and solidification, affecting shrinkage, warping, and achievable feature definition.
- Geometria i rozmiar części: Large, complex parts are more prone to distortion and deviation due to accumulated thermal stress.
- Parametry drukowania: Layer thickness, laser/beam power, scan speed, and other parameters directly impact the outcome. Experienced providers like Met3dp fine-tune parameters for optimal results.
- Strategia wsparcia: Supports can influence surface finish where they attach and may slightly affect local accuracy upon removal.
- Przetwarzanie końcowe: Crucially, post-processing steps like CNC machining are often required to achieve tight tolerances on critical features (e.g., sealing faces, connection ports, mounting points). Surface finishing processes (polishing, electropolishing) can significantly improve Ra values.
What to Expect for Marine Heat Exchangers:
- As-Printed State: Sufficient for many internal heat transfer surfaces where high geometric precision isn’t paramount, but surface roughness will influence fluid dynamics and potentially fouling.
- Critical Interfaces: Flanges, O-ring grooves, threaded ports, and mounting surfaces will almost certainly require post-machining to meet the tight tolerances required for leak-proof connections and proper assembly within the ship’s systems. Tolerances in the range of ±0.05 mm or tighter might be required for sealing faces, achievable only through machining.
- Wykończenie powierzchni: While as-printed finishes might suffice internally, external surfaces or easily accessible internal channels may be polished or electropolished to improve cleanability, reduce fouling potential, or enhance corrosion resistance. Ra values below 1 µm are achievable with these methods.
It is vital to specify required tolerances and surface finishes clearly on engineering drawings, indicating which features are critical and require post-processing. Discussing these requirements early with your AM service provider ensures the final part meets the necessary specifications for reliable marine operation. Met3dp prides itself on delivering industry-leading accuracy and reliability, understanding the critical nature of components destined for aerospace, medical, and marine applications.
Essential Post-Processing Steps for Marine Heat Exchangers
A metal 3D printed part, upon removal from the printer, is rarely ready for immediate deployment, especially for demanding applications like marine heat exchangers. A series of essential post-processing steps are required to transform the as-printed component into a functional, reliable, and safe piece of equipment. These steps are critical for achieving the desired mechanical properties, dimensional accuracy, surface quality, and overall integrity needed to withstand the rigors of the marine environment. Procurement managers and engineers must factor these processes into project timelines and cost analyses.
Common Post-Processing Workflow:
- Usuwanie proszku: The first step after the build is complete and the part has cooled is removing it from the build plate and thoroughly cleaning off any residual, unfused metal powder. This is especially critical for heat exchangers with complex internal channels. Techniques include compressed air blowing, brushing, vibration, and sometimes specialized chemical or flow-based methods for intricate internal geometries. Incomplete powder removal can lead to contamination, blockages, and added weight.
- Stress Relief / Heat Treatment: Due to the rapid heating and cooling inherent in AM processes, significant internal stresses can build up within the printed part.
- Ulga w stresie: A heat treatment cycle performed at a moderate temperature (below the material’s annealing or aging temperature) to relax these internal stresses, reducing the risk of distortion or cracking during subsequent steps (like support removal or machining) or in service. This is almost always necessary.
- Prasowanie izostatyczne na gorąco (HIP): This process involves subjecting the part to high temperature (but below melting point) and high isostatic pressure (typically using an inert gas like Argon) simultaneously. HIP is highly effective at closing internal microporosity, significantly improving fatigue life, ductility, and impact strength. It’s often specified for critical components to achieve near 100% density and enhance overall material integrity.
- Solution Annealing / Aging: Depending on the alloy (e.g., IN625, CuCrZr), specific heat treatments may be required to achieve the desired final material microstructure and mechanical properties (e.g., strength, hardness).
- Usunięcie konstrukcji wsporczej: Supports required during the printing process must be carefully removed. This can be done manually (using pliers, grinders, cutting tools) or through machining (milling, wire EDM). Care must be taken not to damage the part surface. Access for support removal should be considered during the DfAM phase.
- Machining of Critical Features: As discussed previously, AM tolerances are often insufficient for sealing surfaces, flanges, bearing interfaces, or threaded connections. CNC machining (milling, turning, grinding) is used to bring these critical features within the required tight tolerances and achieve specific surface finishes.
- Wykończenie powierzchni: Depending on the requirements, various surface treatments can be applied:
- Grinding/Sanding: Manual or automated processes to remove support witness marks and improve general surface smoothness.
- Wykończenie bębnowe/wibracyjne: Using abrasive media in a tumbling barrel or vibratory bowl to deburr edges and achieve a more uniform, smoother surface finish, especially on external surfaces.
- Blasting: Using abrasive media (e.g., glass beads, ceramic beads, aluminum oxide) propelled by compressed air to clean the surface, remove oxides, and create a uniform matte finish.
- Polishing/Electropolishing: Used to achieve very smooth, reflective surfaces (low Ra). Electropolishing can be particularly effective for smoothing complex internal channels (if accessible) and improving corrosion resistance by removing the outer surface layer and creating a chromium-rich passive film on stainless steels and nickel alloys.
- Czyszczenie: Thorough cleaning is essential to remove any machining fluids, polishing compounds, blasting media, or other contaminants before inspection and deployment.
- Inspection and Testing: Non-destructive testing (NDT) methods like visual inspection, dimensional analysis (CMM or scanning), dye penetrant testing (DPT), or X-ray/CT scanning may be employed to verify part integrity and check for internal defects. Crucially for heat exchangers, pressure testing (hydrostatic or pneumatic) is performed to ensure leak-tight integrity under operational pressures. Certification documentation often requires proof of successful pressure testing.
- Powłoka (opcjonalnie): In some cases, specialized coatings (e.g., ceramic, polymer, passivation treatments) might be applied to further enhance corrosion resistance, reduce fouling, or improve thermal properties, although selecting inherently resistant materials like IN625 often mitigates this need.
The extent and combination of these post-processing steps depend heavily on the specific application, material, design complexity, and required certifications. Partnering with a full-service provider experienced in both printing and post-processing is vital for ensuring marine heat exchangers meet all performance and safety standards.
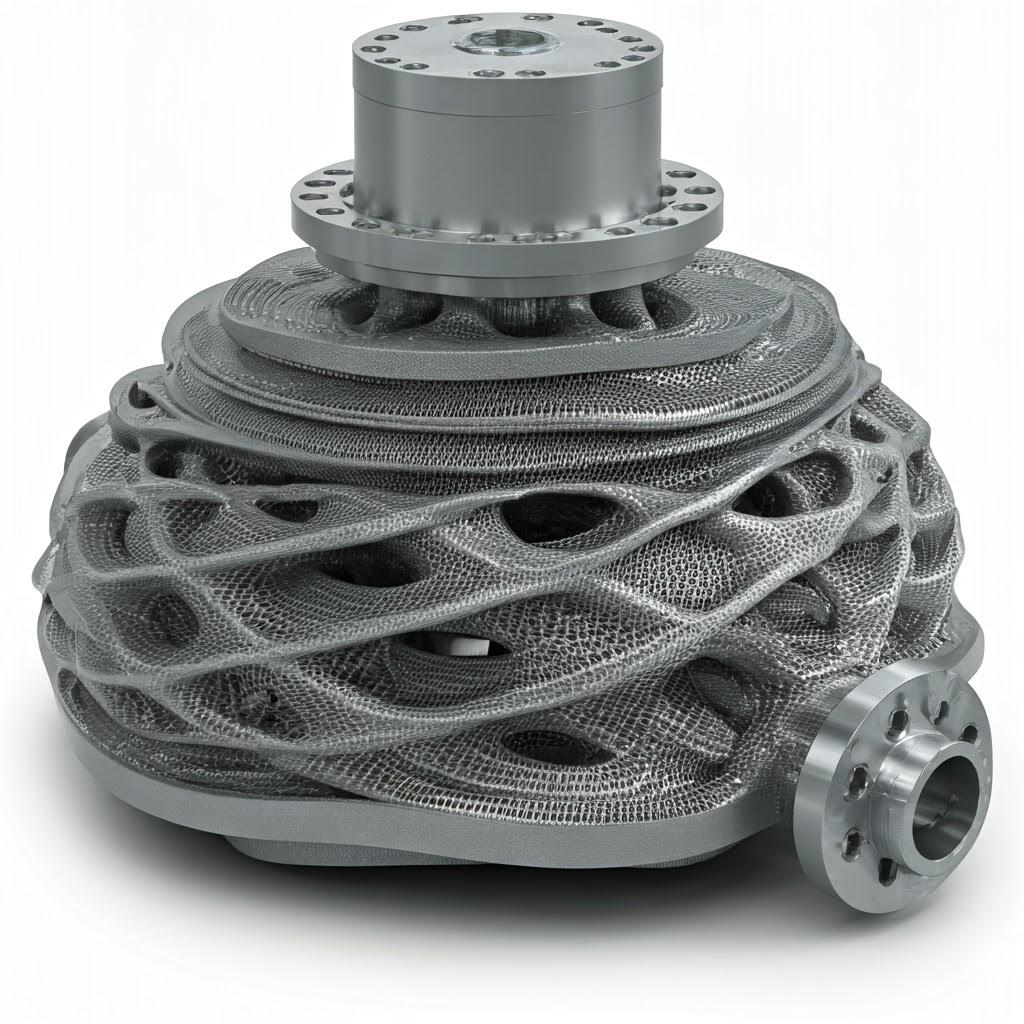
Overcoming Common Challenges in 3D Printing Marine Heat Exchangers
While metal AM offers significant advantages, producing high-quality, reliable marine heat exchangers using this technology is not without its challenges. Understanding these potential hurdles and implementing effective mitigation strategies is key to successful adoption. Experienced AM providers, like Met3dp, leverage their deep understanding of materials science, process control, and post-processing techniques to navigate these complexities.
Key Challenges and Mitigation Strategies:
- Residual Stress, Distortion, and Warping:
- Wyzwanie: The rapid heating/cooling cycles inherent in AM generate internal stresses. If not managed, these stresses can cause parts to warp during printing, detach from the build plate, distort after removal, or even crack.
- Łagodzenie:
- Zoptymalizowane parametry drukowania: Careful control of laser/beam power, scan strategy (e.g., island scanning), and pre-heating (especially in SEBM) helps minimize thermal gradients.
- Struktury wsparcia: Properly designed supports anchor the part to the build plate and counteract warping forces.
- Thermal Simulation: Using simulation software during the design phase to predict stress accumulation and modify geometry accordingly.
- Stress Relief Heat Treatment: Essential post-processing step to relax internal stresses before support removal or machining.
- DfAM: Designing parts with features that inherently reduce stress concentration (e.g., fillets, variable thickness).
- Support Removal from Complex Internal Geometries:
- Wyzwanie: Heat exchangers often feature intricate internal channels or structures (like TPMS) where traditional support structures would be extremely difficult or impossible to remove mechanically after printing.
- Łagodzenie:
- DfAM for Self-Supporting Designs: Prioritizing designs like TPMS or optimizing channel shapes and overhang angles to be self-supporting or require minimal internal supports.
- Soluble or Easily Breakable Supports: Research into specialized support materials or structures designed for easier removal (less common in metal AM currently).
- Wybór procesu: SEBM often requires fewer supports than LPBF due to the higher chamber temperature and powder sintering.
- Access Ports: Designing specific access points for tool insertion or flow-based removal techniques if supports are unavoidable internally.
- Complete Powder Removal from Internal Channels:
- Wyzwanie: Ensuring all unfused powder is removed from narrow, tortuous internal passages is critical. Trapped powder can impede flow, reduce thermal performance, add weight, and act as a contaminant.
- Łagodzenie:
- DfAM for Drainage: Designing channels with smooth pathways and strategically placed drainage/access holes (which may be sealed later).
- Thorough Cleaning Procedures: Utilizing optimized combinations of vibration, compressed air, ultrasonic cleaning, and potentially fluid flushing cycles.
- Inspekcja: Using methods like endoscopy or CT scanning to verify complete powder removal in critical applications.
- Ensuring Leak-Proof Integrity:
- Wyzwanie: Micro-porosity or micro-cracks, if present, can compromise the pressure-holding capability and lead to leaks between fluid circuits or to the environment. Part consolidation helps, but material quality and print process control are key.
- Łagodzenie:
- Wysokiej jakości proszek: Using powders with low internal porosity and optimized PSD, like those produced by Met3dp’s advanced atomization systems.
- Zoptymalizowane parametry drukowania: Ensuring sufficient energy density for full melting and fusion between layers to achieve >99.5% density.
- Prasowanie izostatyczne na gorąco (HIP): Highly effective at closing internal pores and ensuring maximum density and integrity. Often mandated for critical pressure-bearing components.
- Rigorous Pressure Testing: Implementing hydrostatic or pneumatic leak testing protocols (often exceeding operational pressures) as a standard quality control step.
- Meeting Stringent Marine Certification Standards:
- Wyzwanie: Marine components, especially pressure equipment, must often meet standards set by classification societies (e.g., DNV, ABS, Lloyd’s Register). Proving the reliability, material properties, and process control of AM parts requires thorough documentation and potentially specific testing protocols.
- Łagodzenie:
- Process Control & Quality Management: Implementing robust quality management systems (e.g., ISO 9001) covering powder handling, printing processes, post-processing, and inspection.
- Material Property Validation: Extensive testing of printed material samples (tensile, fatigue, corrosion) to demonstrate equivalence or superiority to traditional material standards.
- Identyfikowalność: Maintaining full traceability from powder batch to final part.
- Collaboration with Classification Societies: Engaging early with societies to understand requirements and develop qualification programs for AM components. Partnering with experienced providers who understand these requirements is crucial.
- Surface Roughness Effects:
- Wyzwanie: The inherent surface roughness of AM parts, especially internal channels, can increase pressure drop and potentially promote fouling or scaling compared to smooth drawn tubes.
- Łagodzenie:
- Design Compensation: Potentially designing slightly larger channel diameters to account for roughness effects.
- Wykończenie powierzchni: Employing techniques like abrasive flow machining, chemical polishing, or electropolishing where feasible to smooth internal surfaces.
- Wybór materiału: Choosing materials less prone to specific types of fouling in the operating environment.
Successfully navigating these challenges requires a combination of thoughtful design, meticulous process control, appropriate post-processing, and rigorous quality assurance. Working with a knowledgeable dostawcy usług druku 3D z metalu is essential for B2B customers aiming to reliably implement AM for demanding marine heat exchanger applications.
Selecting the Right Metal AM Service Provider for Marine Components
Choosing the right additive manufacturing partner is as critical as the design and material selection for ensuring the success of your 3D printed marine heat exchanger project. The specialized nature of marine applications – involving corrosive environments, high reliability requirements, and stringent regulations – necessitates partnering with a provider possessing specific expertise and capabilities. For procurement managers, engineers, and wholesale distributors sourcing AM services, careful evaluation based on the following criteria is essential:
Key Evaluation Criteria for AM Suppliers:
- Proven Industry Experience:
- Marine & Related Expertise: Does the provider have demonstrable experience producing parts for the marine, offshore, aerospace, or other demanding industries with similar environmental challenges and quality expectations? Case studies or references are valuable.
- Heat Exchanger Experience: Have they successfully printed heat exchangers or components with complex internal fluid channels before? Understanding the specific challenges (powder removal, leak testing) is crucial.
- Material Expertise and Portfolio:
- Relevant Alloy Capability: Does the provider routinely process the specific alloys required for your application (e.g., IN625, 316L, CuCrZr)? Do they source high-quality, traceable powders?
- Material Data & Support: Can they provide material datasheets for their printed materials? Do they have materials scientists or application engineers who can advise on material selection and expected performance? Met3dp, for instance, not only manufactures high-performance powders but also possesses deep expertise in their application.
- Technologia i sprzęt:
- Appropriate AM Process: Do they operate the best-suited AM technology (LPBF, SEBM) for your part’s geometry, material, and requirements?
- Machine Quality & Maintenance: Are their printers industrial-grade, well-maintained, and calibrated to ensure consistent, high-quality output? Met3dp utilizes industry-leading equipment known for accuracy and reliability.
- Objętość kompilacji: Can their machines accommodate the size of your heat exchanger?
- In-House Post-Processing Capabilities:
- Comprehensive Services: Does the provider offer critical post-processing steps in-house (or through trusted partners), such as heat treatment (including HIP if required), CNC machining, support removal, surface finishing, and cleaning? Managing the entire workflow under one roof or through a coordinated system improves quality control and lead time.
- Specialized Equipment: Do they have the necessary furnaces, CNC machines, polishing equipment, and cleaning facilities?
- Quality Management and Certifications:
- Robust QMS: Is the provider certified to quality standards like ISO 9001? This indicates established processes for quality control, traceability, and continuous improvement.
- Industry-Specific Certifications: While specific AM marine certifications are evolving, experience with aerospace (AS9100) or medical (ISO 13485) certifications often indicates a high level of process control applicable to marine requirements. Ask about their familiarity with classification society (DNV, ABS, etc.) requirements.
- Inspection & Testing: What are their standard inspection procedures? Do they have CMM capabilities, NDT methods, and importantly, pressure testing facilities suitable for heat exchangers?
- Wsparcie inżynieryjne i DfAM:
- Podejście oparte na współpracy: Are they willing to work closely with your engineering team to optimize the design for additive manufacturing (DfAM)? Providers who offer design consultation can significantly improve the final product’s performance and manufacturability.
- Capacity and Lead Time:
- Zdolność produkcyjna: Can they handle your required production volume, whether it’s prototypes, small series, or on-demand spares for wholesale distribution?
- Quoted Lead Times: Are their quoted lead times realistic, encompassing printing, post-processing, inspection, and shipping?
Why Partner with Met3dp?
Met3dp stands out as a comprehensive solutions provider in metal additive manufacturing. Headquartered in Qingdao, China, the company brings together:
- Advanced Printer Technology: Offering SEBM systems known for industry-leading print volume, accuracy, and reliability, ideal for mission-critical parts.
- Wysokiej jakości proszki metali: Manufacturing a wide range of powders (including superalloys like IN625, stainless steels like 316L, and potentially custom alloys like CuCrZr) using advanced atomization techniques for superior part quality.
- Decades of Collective Expertise: A team with deep knowledge spanning AM processes, materials science, and application development.
- Zintegrowane rozwiązania: Providing services from powder production and printer systems to application support and potentially finished part production through partners, ensuring a seamless workflow.
Choosing a supplier isn’t just about finding the lowest price; it’s about finding a reliable partner committed to quality and equipped to handle the specific demands of marine applications.
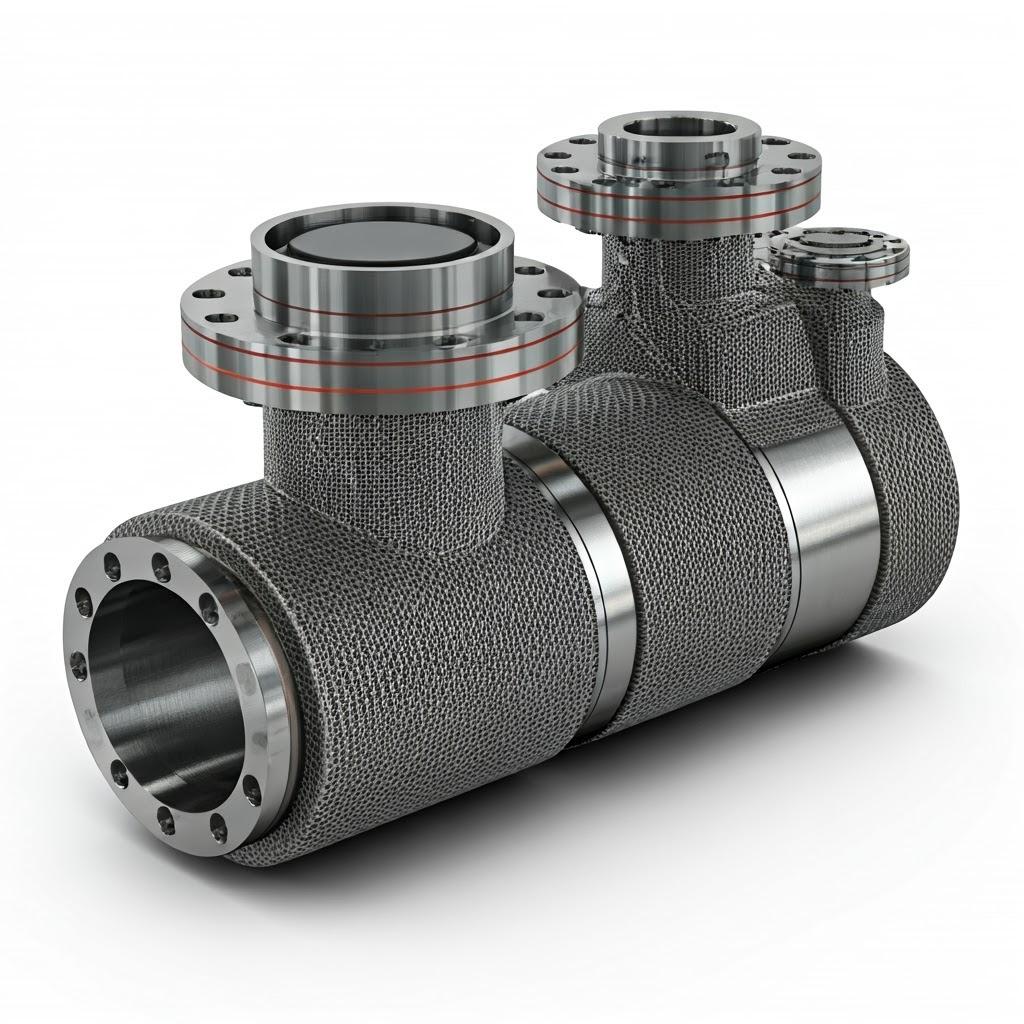
Cost Analysis and Lead Time Factors for 3D Printed Heat Exchangers
Understanding the factors that influence the cost and production timeline of metal 3D printed heat exchangers is crucial for budgeting, project planning, and comparing AM to traditional manufacturing methods. Both cost and lead time can vary significantly based on several interconnected variables.
Key Cost Drivers:
- Rodzaj i zużycie materiału:
- Koszt proszku: High-performance alloys like IN625 or specialized copper alloys (CuCrZr) are significantly more expensive per kilogram than standard materials like 316L stainless steel.
- Objętość i gęstość części: The sheer amount of material required directly impacts cost. DfAM techniques like topology optimization can help reduce material usage without compromising performance.
- Struktury wsparcia: Material used for support structures adds to the overall consumption, although unused powder is largely recyclable, improving overall material utilization compared to subtractive methods.
- Part Design Complexity and Size:
- Czas budowy: Larger or more complex parts take longer to print, increasing machine time costs. Intricate internal features or very thin walls can slow down the printing process.
- Data Preparation: Highly complex geometries may require more time for slicing, support generation, and build simulation.
- AM Machine Time:
- Hourly Rate: AM machines represent significant capital investment, and their operational time is a major cost component. Factors like layer thickness, scan speed, and the number of parts nested onto a build plate influence this.
- Wymagania dotyczące przetwarzania końcowego:
- Obróbka cieplna: Standard stress relief is common; more advanced cycles like HIP add significant cost but may be necessary for critical parts.
- Usuwanie wsparcia: Complex internal supports requiring manual or specialized removal methods increase labor costs.
- Obróbka skrawaniem: The extent of CNC machining needed for critical tolerances is a major factor. More features requiring tight tolerances mean higher machining costs.
- Wykończenie powierzchni: Processes like polishing or electropolishing add cost based on the surface area treated and required finish level.
- Inspection, Testing, and Certification:
- NDT Methods: Basic visual and dimensional checks are standard. Advanced NDT (CT scanning, DPT) adds cost.
- Pressure Testing: Required for heat exchangers, the cost depends on the pressure level, duration, and documentation requirements.
- Certyfikacja: Costs associated with generating documentation packages for classification societies.
- Ilość zamówienia:
- Korzyści skali: While AM has no tooling costs, some economies of scale exist. Setting up a build, data preparation, and post-processing workflows become more efficient with larger batches. Wholesale buyers or those ordering multiple units may see a lower per-part price compared to single prototypes.
Typical Lead Time Factors:
Lead time is the duration from order placement (with a finalized design) to shipment of the finished part.
- Design Finalization & Data Prep: 1-5 days (depending on complexity and readiness).
- Czas oczekiwania: Waiting for machine availability: Highly variable (days to weeks, depending on provider’s backlog).
- Czas drukowania: Few hours to several days (or even > week for very large/complex parts).
- Cooling & Powder Removal: ~1 day.
- Obróbka cieplna: 1-3 days (including furnace time and cooling).
- Support Removal & Machining: 1-5 days (highly dependent on complexity).
- Wykończenie powierzchni & Czyszczenie: 1-3 days.
- Inspection & Testing: 1-2 days.
- Wysyłka: Dependent on location and method.
Overall Lead Time: For a moderately complex marine heat exchanger, a typical lead time might range from 2 do 6 tygodni. This can be significantly faster than sourcing traditionally manufactured custom replacements, which might take months, especially for obsolete parts. However, it’s crucial to get specific quotes from providers based on the actual design.
FAQ: Metal 3D Printing for Marine Heat Exchangers
Here are answers to some frequently asked questions regarding the use of metal AM for marine heat exchangers:
- How does the corrosion resistance of AM IN625 or 316L compare to traditional wrought materials in saltwater?
- When printed using optimized parameters and high-quality powder (achieving near full density), AM IN625 and 316L exhibit corrosion resistance largely comparable to their wrought counterparts in typical marine environments. Post-processing steps like HIP can further enhance properties by eliminating potential micro-porosity. Surface finish can play a role; smoother surfaces (achieved via polishing or electropolishing) generally offer slightly better resistance. However, specific testing in the target environment is always recommended for critical applications.
- What pressure ratings can 3D printed heat exchangers typically withstand?
- The achievable pressure rating depends entirely on the design (wall thickness, channel geometry), material properties (yield strength, tensile strength), and the quality of the print (density, defect levels). With proper design, material selection (like IN625 or 316L), optimized printing, and potentially HIP treatment, AM heat exchangers can be designed to meet typical marine system pressure requirements, often ranging from a few bar up to tens or even hundreds of bar for specific high-pressure hydraulic or gas systems. Rigorous pressure testing as part of the quality assurance process is essential to validate the design rating.
- Is it feasible to use metal AM to retrofit or replace an existing, traditionally manufactured heat exchanger?
- Yes, this is a significant advantage of AM. If an existing heat exchanger fails and is obsolete or has long lead times, AM offers a path to replacement. Reverse engineering (3D scanning the old part) can create a CAD model. DfAM principles can then be applied to potentially improve the design (e.g., enhance efficiency, consolidate parts) before printing a replacement, often using a more robust material like IN625. This provides a rapid solution for MRO scenarios, minimizing vessel downtime.
- Can metal 3D printed marine components be certified by classification societies like DNV or ABS?
- The framework for certifying AM marine components is actively developing. Classification societies are establishing guidelines and requirements. Certification typically involves qualifying the specific manufacturing process, the material, the post-processing steps, and the final part through rigorous testing and documentation. It is achievable, but requires close collaboration between the end-user, the AM service provider, and the classification society from the outset. Providers experienced with stringent quality management systems and material testing are better positioned to navigate this process.
Conclusion: The Future of Marine Heat Exchangers with Metal AM
The maritime industry is navigating towards greater efficiency, enhanced reliability, and more resilient supply chains. Metal additive manufacturing stands at the forefront of this evolution, offering a transformative approach to producing critical components like marine heat exchangers. By unshackling design engineers from traditional manufacturing constraints, AM enables the creation of heat exchangers that are:
- More Thermally Efficient: Utilizing complex geometries like TPMS and optimized flow paths to maximize heat transfer in smaller, lighter packages.
- More Reliable: Consolidating parts to eliminate potential leak points and utilizing advanced, corrosion-resistant materials like IN625.
- Highly Customized: Tailored precisely to specific vessel requirements or retrofitted into existing systems.
- Available On-Demand: Revolutionizing MRO and spare parts logistics, reducing downtime and inventory costs through digital inventories.
While challenges remain, particularly concerning standardization and scaling for high-volume production, the advantages are compelling. The successful implementation hinges on embracing DfAM principles, selecting the appropriate high-performance materials, performing necessary post-processing, and ensuring rigorous quality control.
Critically, partnering with an experienced and capable metal AM provider is paramount. Companies like Met3dp, offering comprehensive solutions encompassing advanced printing technologies, high-quality powder manufacturing, and deep application expertise, are instrumental in helping the marine industry harness the full potential of additive manufacturing.
As the technology continues to mature and gain wider acceptance, metal 3D printed heat exchangers are set to become increasingly prevalent, contributing significantly to the performance, efficiency, and sustainability of future maritime operations. Explore how Met3dp’s cutting-edge systems and powders can power your organization’s additive manufacturing goals by visiting https://met3dp.com/.
Udostępnij
MET3DP Technology Co., LTD jest wiodącym dostawcą rozwiązań w zakresie produkcji addytywnej z siedzibą w Qingdao w Chinach. Nasza firma specjalizuje się w sprzęcie do druku 3D i wysokowydajnych proszkach metali do zastosowań przemysłowych.
Zapytaj o najlepszą cenę i spersonalizowane rozwiązanie dla Twojej firmy!
Powiązane artykuły
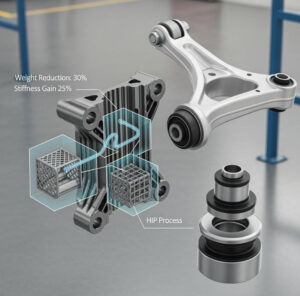
Metal 3D Printed Subframe Connection Mounts and Blocks for EV and Motorsport Chassis
Czytaj więcej "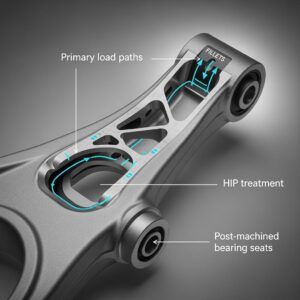
Metal 3D Printing for U.S. Automotive Lightweight Structural Brackets and Suspension Components
Czytaj więcej "Informacje o Met3DP
Ostatnia aktualizacja
Nasz produkt
KONTAKT
Masz pytania? Wyślij nam wiadomość teraz! Po otrzymaniu wiadomości obsłużymy Twoją prośbę całym zespołem.