Powder Bed Fusion
Spis treści
Przegląd
Synteza złoża proszku to proces produkcji addytywnej, który wykorzystuje energię cieplną do selektywnego łączenia obszarów złoża proszku warstwa po warstwie w celu tworzenia części. Jest to obecnie jedna z najczęściej wykorzystywanych technologii druku 3D z metalu w zastosowaniach produkcyjnych.
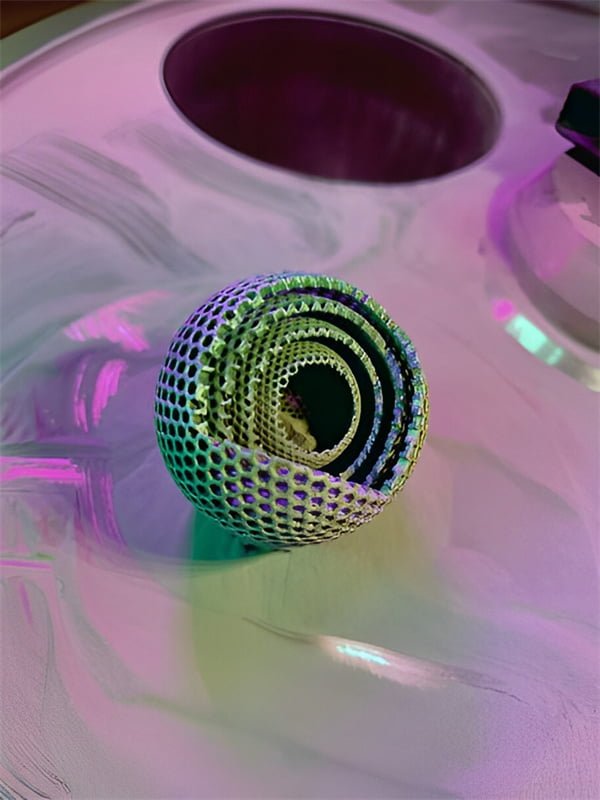
Kilka kluczowych szczegółów dotyczących fuzji w złożu proszkowym:
- Należy do rodziny fotopolimeryzacji kadziowej w produkcji dodatków.
- Źródło energii cieplnej, takie jak laser lub wiązka elektronów, jest wykorzystywane do topienia i stapiania proszku materiału.
- Stosowane proszki to zazwyczaj metale, takie jak stal nierdzewna, tytan, aluminium, stopy niklu i kobaltowo-chromowe. W niektórych procesach można również stosować polimery i ceramikę.
- Fuzja w złożu proszkowym może tworzyć w pełni zwarte części metalowe o właściwościach mechanicznych porównywalnych z tradycyjną produkcją.
- Umożliwia ona tworzenie złożonych geometrii, co nie jest możliwe w przypadku konwencjonalnych technik subtraktywnych.
- Zastosowania obejmują lotnictwo, medycynę, stomatologię, motoryzację i ogólne zastosowania przemysłowe.
- Popularne technologie łoża proszkowego obejmują selektywne topienie laserowe (SLM), bezpośrednie spiekanie laserowe metali (DMLS), topienie wiązką elektronów (EBM) i rozpylanie spoiwa.
Procesy fuzji w złożu proszkowym
Istnieje kilka różnych technologii fuzji w złożu proszkowym, które zostały opracowane. Główne z nich to:
Proces | Opis |
---|---|
Selektywne topienie laserowe (SLM) | Wykorzystuje laser o dużej mocy do pełnego stopienia i stopienia proszku metalicznego w łożu. |
Bezpośrednie spiekanie laserowe metali (DMLS) | Podobne do SLM, ale ukierunkowane na spiekanie proszków, a nie pełne topienie. |
Topienie wiązką elektronów (EBM) | Wykorzystuje wiązkę elektronów jako źródło energii do stopienia proszku. Odbywa się to w próżni. |
Multi Jet Fusion (MJF) | Drukowanie atramentowe środka utrwalającego na złożu proszku polimerowego przed spiekaniem za pomocą źródła energii. |
Binder Jetting | Płynny środek wiążący selektywnie osadzany w celu związania materiału proszkowego, a następnie spiekania. |
Selektywne topienie laserowe (SLM) jest obecnie najczęściej stosowaną technologią stapiania w złożu proszkowym. Laser o dużej mocy (np. światłowodowy, CO2, YAG) jest skupiany na złożu proszku w celu utworzenia jeziorka stopu i stopienia materiału. Złoże proszku obniża się po każdej warstwie i rozprowadzany jest na nim nowy proszek. SLM wykorzystuje pełne topienie, dzięki czemu można budować w pełni gęste części. Powszechnie stosowane są materiały takie jak stal nierdzewna, tytan, aluminium, Inconel.
Bezpośrednie spiekanie laserowe metali (DMLS) działa podobnie, ale ma na celu tylko częściowe stopienie proszku w celu utworzenia szyjek między cząstkami w celu wytworzenia stałej części. DMLS ma niższe wymagania dotyczące mocy lasera w porównaniu do SLM.
Topienie wiązką elektronów (EBM) wykorzystuje wiązkę elektronów jako źródło energii skupionej w próżni w celu stopienia proszków metalicznych warstwa po warstwie. EBM pozwala na wyższe tempo produkcji niż procesy oparte na laserze, ponieważ wiązka może skanować szybciej. EBM jest najczęściej używany ze stopami tytanu w zastosowaniach lotniczych.
Fuzja wielostrumieniowa (MJF) wykorzystuje głowice do druku atramentowego do selektywnego osadzania środka utrwalającego na złożu proszku polimerowego, który jest następnie spiekany przez źródło energii. MJF umożliwia szybkie spiekanie tworzyw termoplastycznych.
Rozpylanie spoiwa Najpierw nakłada płynny środek wiążący w wybranych obszarach, aby związać materiał proszkowy, a następnie spieka w celu zagęszczenia części. Może być stosowana z metalami, ceramiką i polimerami.
Materiały do fuzji w złożu proszkowym
W produkcji addytywnej metodą fuzji w złożu proszkowym można stosować szereg materiałów. Najpopularniejsze z nich to:
Materiał | Procesy | Zastosowania |
---|---|---|
Stal nierdzewna | SLM, DMLS, strumieniowanie spoiwa | Implanty medyczne, oprzyrządowanie, inżynieria ogólna |
Stopy tytanu | SLM, EBM | Implanty lotnicze i medyczne |
Stopy aluminium | SLM, EBM | Lekkość w przemyśle motoryzacyjnym i lotniczym |
Nadstopy niklu | SLM, EBM | Łopatki turbin, dysze rakietowe do pracy w ekstremalnych warunkach |
Kobalt-chrom | SLM, DMLS | Implanty dentystyczne i protetyka |
Polimery | MJF, Binder jetting | Prototypowanie i końcowe części z tworzyw sztucznych |
Ceramika | Rozpylanie spoiwa | Implanty medyczne, lotnictwo i kosmonautyka |
Najczęściej używane są stale nierdzewnektóre oferują dobrą odporność na korozję i właściwości mechaniczne. Stopy tytanu takie jak Ti6Al4V są popularne w przemyśle lotniczym ze względu na oszczędność masy w porównaniu ze stalą i stopami niklu. Stopy aluminium umożliwiają produkcję lekkich części dla przemysłu motoryzacyjnego i lotniczego.
Nadstopy niklu takie jak Inconel, są stosowane w wysokotemperaturowych łopatkach turbin i dyszach rakiet. Stopy kobaltowo-chromowe są biokompatybilne i szeroko stosowane w uzupełnieniach dentystycznych. Polimery takie jak nylony, PEEK i poliamidy mogą być spiekane na części z tworzyw sztucznych. Ceramika takie jak tlenek cyrkonu i tlenek glinu mają zastosowanie w implantach medycznych.
Rozkład wielkości cząstek, płynność, gęstość upakowania i temperatura topnienia to kluczowe właściwości materiału proszkowego, które określają przetwarzalność i końcowe właściwości części.
Zastosowania fuzji w złożu proszkowym
Produkcja addytywna w technologii fuzji w złożu proszkowym jest wykorzystywana w przemyśle lotniczym, medycznym, dentystycznym, motoryzacyjnym i inżynierii ogólnej. Typowe zastosowania obejmują:
Przemysł | Zastosowania |
---|---|
Lotnictwo i kosmonautyka | Łopatki turbin, dysze rakietowe, profile lotnicze, satelity, drony |
Medyczny | Implanty ortopedyczne i dentystyczne, protetyka, narzędzia chirurgiczne |
Motoryzacja | Lekkie prototypy, niestandardowe oprzyrządowanie |
Przemysłowy | Oprzyrządowanie metalowe, sprzęt górniczy, transport cieczy |
Architektura | Elementy dekoracyjne, fasady, oświetlenie, meble |
W lotnictwoFuzja w złożu proszkowym jest idealna dla jednorazowych komponentów, takich jak satelity i UAV. Jest stosowana do produkcji lekkich części ze stopów tytanu i niklu, w tym turbin, dysz i płatowców.
Dla medycznySpersonalizowane tytanowe i kobaltowo-chromowe implanty i protezy są głównym obszarem zastosowań. Umożliwia również spersonalizowane narzędzia chirurgiczne.
W motoryzacjaŁoże proszkowe jest wykorzystywane do produkcji lekkich prototypów oraz niestandardowych narzędzi i osprzętu, takiego jak przyrządy. Dla przemysłowy sprzęt, umożliwia specjalistyczne oprzyrządowanie, przyrządy i metalowe części końcowe.
W architekturaFuzja proszkowa umożliwia tworzenie unikalnych geometrii elementów dekoracyjnych i funkcjonalnych w budynkach i meblach.
Zalety fuzji w złożu proszkowym
Niektóre kluczowe zalety technologii fuzji w złożu proszkowym obejmują:
- Złożone geometrie - Możliwe są skomplikowane elementy wewnętrzne i siatki.
- Personalizacja - Części mogą być dostosowane do indywidualnych zastosowań.
- Lekkość - zmniejszenie wagi komponentów poprzez optymalizację projektów.
- Konsolidacja - łączenie zespołów w pojedyncze części.
- Wysoka wytrzymałość - W pełni zwarte metale porównywalne z wytrzymałością materiałów kutych.
- Krótszy czas realizacji - szybka realizacja od pliku cyfrowego do części.
- Masowa personalizacja - łącząc ekonomię skali z personalizacją części.
- Zrównoważony rozwój - mniej odpadów w porównaniu z procesami subtraktywnymi.
Zdolność do produkcji gęstych części metalowych o niestandardowych, złożonych geometriach sprawia, że spajanie w złożu proszkowym jest idealne dla lekkich, wysokowydajnych komponentów w różnych branżach. Technologia ta umożliwia konsolidację zespołów w pojedyncze części, zmniejszając koszty produkcji i zapasów. Zastosowanie produkcji addytywnej skutkuje również znacznie mniejszą ilością odpadów materiałowych niż tradycyjne metody subtraktywne, takie jak obróbka CNC.
Ograniczenia fuzji w złożu proszkowym
Niektóre z obecnych ograniczeń obejmują:
- Ograniczenia rozmiaru - Objętości kompilacji są zazwyczaj mniejsze niż 1 metr sześcienny.
- Wykończenie powierzchni - efekt schodkowy wymagający przetwarzania końcowego.
- Szybkość budowania - wolniej niż metody produkcji wielkoseryjnej.
- Właściwości anizotropowe - kierunkowe zmiany właściwości materiału.
- Standardy - brak kodów i specyfikacji kwalifikujących się części.
- Oprogramowanie - zasady projektowania i złożoność przygotowania plików.
- Koszty - koszty sprzętu i materiałów są nadal stosunkowo wysokie.
Maksymalny rozmiar komponentu jest ograniczony przez objętość roboczą maszyn, która jest coraz większa, ale nadal zwykle mniejsza niż 1 metr sześcienny. Proces "warstwa po warstwie" może skutkować słabym wykończeniem powierzchni, które wymaga wygładzania i polerowania.
Ogólne prędkości produkcji są wolniejsze w porównaniu z technologiami produkcji wielkoseryjnej, takimi jak formowanie wtryskowe. Części mogą również wykazywać właściwości anizotropowe w zależności od orientacji wydruku. Brak standardów i specyfikacji dotyczących kwalifikacji drukowanych części jest również ograniczeniem w branżach podlegających ścisłym regulacjom, takich jak lotnictwo i medycyna. Projektowanie optymalnych części i wstępne przetwarzanie plików wymaga zaawansowanej wiedzy w zakresie oprogramowania.
Koszty systemu i materiałów są nadal stosunkowo wysokie w porównaniu do tradycyjnej produkcji. Jednak wraz ze wzrostem popularności tej technologii koszty maleją, a wiele zastosowań może uzasadnić koszty ze względu na wydajność części, dostosowanie i elastyczność projektu.
Przetwarzanie końcowe
Post-processing odnosi się do kroków wymaganych po zakończeniu procesu kompilacji w celu uzyskania gotowej części:
- Usuwanie proszku - Części są oddzielane od nieroztopionego proszku za pomocą szczotek.
- Obsługuje usuwanie - Konstrukcje wsporcze są odcinane, a powierzchnia czyszczona.
- Wykończenie powierzchni - Szlifowanie, piaskowanie, śrutowanie w celu poprawy
Parametry procesu
Istnieje kilka kluczowych parametrów procesu, które można dostosować w celu optymalizacji właściwości, wydajności i produktywności podczas stapiania w złożu proszkowym:
Parametr | Typowy zakres | Efekt |
---|---|---|
Moc lasera | 50-500W | Szybkość topnienia, rozmiar basenu topnienia, głębokość penetracji |
Prędkość skanowania | 100-10 000 mm/s | Szybkość krzepnięcia, szybkość chłodzenia, mikrostruktura |
Rozstaw włazów | 50-200 μm | Nakładające się ścieżki, gęstość, siła wiązania |
Grubość warstwy | 20-100 μm | Rozdzielczość, chropowatość powierzchni, czas budowy |
Strategia skanowania | Wyspy, paski, szachownica | Naprężenia szczątkowe, odkształcenia, anizotropia |
Atmosfera procesu | Próżnia, gaz obojętny | Utlenianie, zanieczyszczenie, porowatość |
Moc lasera wpływa na energię wejściową, szybkość topienia, wymiary basenu topnienia i głębokość penetracji. Prędkość skanowania kontroluje szybkość krzepnięcia i chłodzenia, co wpływa na morfologię ziaren i powstawanie defektów.
Rozstaw włazów ustawia odstępy między ścieżkami skanowania i wpływa na nakładanie się, zagęszczanie i łączenie między warstwami. Grubość warstwy określa rozdzielczość, chropowatość powierzchni i całkowity czas budowy.
Strategia skanowania (wzorce skanowania) wpływa na naprężenia szczątkowe, odkształcenia i właściwości anizotropowe w zależności od kierunku drukowania. Atmosfera procesu określa poziomy utlenienia i zanieczyszczenia.
Recykling proszków
- Nieroztarty proszek można zebrać i przesiać w celu usunięcia dużych cząstek.
- Ponowne użycie zazwyczaj do 20 cykli
- Znaczne obniżenie kosztów proszku
- Świeży proszek dodany w celu uzupełnienia i utrzymania składu chemicznego
- Właściwości monitorowane pod kątem progów ponownego użycia
Procesy fuzji w złożu proszkowym ponownie wykorzystują niestopiony proszek do dodatkowych kompilacji. Po usunięciu proszku, luźny proszek jest zbierany, przesiewany w celu usunięcia dużych cząstek i mieszany ze świeżym proszkiem przed ponownym użyciem.
Typowe wskaźniki ponownego użycia wynoszą do 20 cykli w zależności od materiału, zmian wielkości cząstek i poziomów zanieczyszczenia. Recykling ten znacznie poprawia wydajność materiałową i obniża ogólne koszty części. Współczynnik ponownego użycia proszku i jego właściwości są monitorowane w celu określenia szybkości odświeżania.
Kontrola jakości
Niektóre kluczowe środki kontroli jakości stosowane w przypadku fuzji w złożu proszkowym obejmują:
- Analiza chemiczna proszków
- Analiza rozkładu wielkości cząstek
- Śledzenie ponownego użycia proszku
- Monitorowanie puli stopu
- Kontrola geometrii części
- Testowanie właściwości mechanicznych
- Badania nieniszczące (np. rentgenowskie)
- Skanowanie CT w celu wykrycia wad wewnętrznych
- Pomiar chropowatości powierzchni
Skład chemiczny proszku wejściowego i rozkład wielkości cząstek są analizowane w celu zapewnienia wysokiej jakości. Śledzone są wskaźniki odświeżania proszku. Systemy monitorowania w trakcie procesu, takie jak monitorowanie puli stopu, wykrywają defekty podczas produkcji.
Wydrukowane części są mierzone pod kątem tolerancji geometrycznych. Testy mechaniczne oceniają właściwości w oparciu o parametry procesu i orientację wydruku. Skanowanie nieniszczące i tomografia komputerowa identyfikują wady wewnętrzne. Oceniane jest wykończenie powierzchni. Wszystkie dane są analizowane w celu kalibracji i optymalizacji procesów.
Analiza kosztów
Typowe koszty części do stapiania w złożu proszkowym zależą od:
- Amortyzacja maszyny
- Koszty materiałów
- Praca przy przetwarzaniu wstępnym i końcowym
- Czas budowy i zużycie energii
- Ilość proszku wielokrotnego użytku
- Współczynnik kupna do lotu
Koszty sprzętu maszynowego są amortyzowane przez przewidywany okres użytkowania w oparciu o zużycie. Koszty materiałów są obliczane na podstawie ilości części i współczynnika zakupu do lotu. Robocizna obejmuje przygotowanie plików, konfigurację, usuwanie naddatku i etapy wykańczania.
Zużycie energii zależy od czasu budowy i poziomu mocy. Proszek wielokrotnego użytku obniża ogólne koszty materiałów. Współczynniki zakupu do lotu od 3:1 do 20:1 są powszechne w przypadku części o wysokiej wartości.
Dostawcy
Niektórzy z głównych dostawców systemów fuzji w złożu proszkowym to:
Dostawca | Kluczowa technologia |
---|---|
EOS | DMLS (bezpośrednie spiekanie laserowe metalu) |
3D Systems | DMP (bezpośredni druk na metalu) |
GE Additive | DMLM (bezpośrednie topienie laserowe metalu) |
Trumpf | Drukarki 3D TruPrint do metalu |
Sisma | Laserowe systemy stapiania metali |
AddUp | Drukarki 3D do metalu FormUp |
EOS oraz 3D Systems byli pionierami w dziedzinie fuzji w złożu proszkowym i pozostają liderami do dziś. GE Additive przejęła Concept Laser i Arcam EBM, aby oferować zarówno technologie laserowe, jak i wiązki elektronów. Trumpf oraz Sisma dostarcza również przemysłowe systemy SLM. AddUp to spółka joint venture pomiędzy Michelin i Fives, koncentrująca się na produkcji dodatków metalowych.
Istnieje również wielu dostawców materiałów do syntezy w złożu proszkowym, w tym Carpenter, Sandvik, Praxair, LPW Technology i AP&C.
Porównanie kosztów
Proces | Koszt sprzętu | Koszt materiałów | Prędkość |
---|---|---|---|
Fuzja złoża proszkowego | $100K - $1M+ | $100-500/kg | 5-100 cm3/godz. |
Obróbka CNC | $50K - $500K | $5-50/kg | 50-500 cm3/godz. |
Formowanie wtryskowe | $100K - $1M+ | $2-5/kg | 100-1000 cm3/godz. |
Systemy ze złożem proszkowym charakteryzują się wysokimi kosztami sprzętu, od $100,000 dla drukarek przemysłowych do ponad $1 miliona dla dużych systemów produkcyjnych. Ceny materiałów wahają się od $100-500/kg. Prędkości produkcji wahają się od 5-100 cm3/godz. w zależności od technologii.
Obróbka CNC ma niższe koszty sprzętu, zaczynające się od około $50,000. Koszty materiałów metalowych są niższe i wynoszą $5-50/kg. Prędkości wynoszą 50-500 cm3/godz.
Systemy formowania wtryskowego również kosztują ponad $100,000. Jednak tworzywo sztuczne jest bardzo tanie i kosztuje $2-5/kg. Prędkości wynoszą 100-1000 cm3/godz.
Tak więc stapianie w łożu proszkowym jest opłacalne tylko w przypadku części metalowych o mniejszej objętości i wysokiej wartości, gdzie wydajność zasługuje na wyższe koszty.
Fuzja w złożu proszkowym a rozpylanie spoiwa
Powder Bed Fusion | Binder Jetting | |
---|---|---|
Materiały | Metale, polimery, ceramika | Metale, polimery, ceramika |
Gęstość | W pełni zwarte części | Części porowate, wymagana infiltracja |
Dokładność | Średni, ±0,1% z przetwarzaniem końcowym | Średni, ±0,2% |
Wykończenie powierzchni | Umiarkowany, wymaga wykończenia | Pozostaje uczciwa, warstwowa tekstura |
Prędkość | Powolny, zależy od źródła energii | Szybki, niezależny od źródła energii |
Zastosowania | Części metalowe do użytku końcowego | Oprzyrządowanie, wzory odlewnicze, prototypy |
- Stapianie w łożu proszkowym może wytwarzać w pełni zwarte części, podczas gdy części wtryskiwane spoiwem są porowate i wymagają infiltracji.
- Dokładność wtryskiwania spoiwa jest umiarkowana, podczas gdy stapianie w łożu proszkowym może osiągnąć wyższą dokładność dzięki obróbce końcowej.
- Wykończenie powierzchni metodą stapiania w łożu proszkowym wymaga wykończenia, podczas gdy binder jetting ma warstwowe, teksturowane wykończenie.
- Prędkości wytwarzania spoiwa są znacznie szybsze niż w przypadku procesów proszkowych ograniczonych przez źródło energii.
- Złoże proszkowe jest częściej stosowane w przypadku części końcowych, podczas gdy wtryskiwanie spoiwa jest lepsze w przypadku narzędzi, odlewów i modeli koncepcyjnych.
Fuzja w złożu proszkowym a osadzanie z wykorzystaniem ukierunkowanej energii
Powder Bed Fusion | DED | |
---|---|---|
Materiały | Głównie metale | Metale, polimery |
Geometria | Włączona złożoność | Średnia złożoność |
Dokładność | Średni do wysokiego | Średni |
Wykończenie powierzchni | Umiarkowany, wymaga wykończenia | Szorstki, bardziej wykończeniowy |
Skalowalność | Małe i średnie części | Średnie i duże części |
Szybkość osadzania | Niski, zależy od szybkości skanowania | Wysoka, zwiększona przy większych dyszach |
- Fuzja w złożu proszkowym jest stosowana głównie z metalami, podczas gdy DED może wykorzystywać metale i polimery.
- Fuzja w złożu proszkowym pozwala na większą złożoność niż DED, która ma pewne ograniczenia geometryczne.
- Dokładność jest wyższa w przypadku stapiania w złożu proszkowym. Dokładność DED jest średnia.
- DED tworzy szorstkie powierzchnie wymagające więcej wykończenia ze względu na dodatkowe kulki.
- Fuzja w łożu proszkowym buduje mniejsze części, podczas gdy DED wykonuje średnie i duże kształty zbliżone do siatki.
- DED ma znacznie wyższe szybkości osadzania ze względu na metodę rozdmuchiwania proszku.
Tak więc synteza w łożu proszkowym generalnie wytwarza mniejsze, złożone geometrie przy umiarkowanych prędkościach. DED tworzy większe proste kształty znacznie szybciej, ale wymaga więcej pracy wykończeniowej.
Przyszłość fuzji w złożu proszkowym
Niektóre obszary przyszłego rozwoju fuzji w złożu proszkowym obejmują:
- Większe objętości zabudowy do kilku metrów sześciennych
- Szybsze metody skanowania w celu zwiększenia prędkości kompilacji
- Rozszerzające się materiały, takie jak stopy wysokotemperaturowe, MMC, polimery
- Produkcja hybrydowa łącząca syntezę w złożu proszkowym i CNC
- Zautomatyzowany depowdering i postprocessing
- Zaawansowane monitorowanie i kontrola w czasie rzeczywistym
- Bardziej rygorystyczne procedury kwalifikacji i certyfikacji
Większe platformy konstrukcyjne umożliwią produkcję większych części lub zwiększenie wydajności produkcji. Nowe, szybsze technologie skanowania mogą drastycznie zwiększyć prędkość produkcji. Opcje materiałowe będą się nadal rozszerzać, zwłaszcza w zakresie wysokowydajnych stopów.
Udostępnij
MET3DP Technology Co., LTD jest wiodącym dostawcą rozwiązań w zakresie produkcji addytywnej z siedzibą w Qingdao w Chinach. Nasza firma specjalizuje się w sprzęcie do druku 3D i wysokowydajnych proszkach metali do zastosowań przemysłowych.
Zapytaj o najlepszą cenę i spersonalizowane rozwiązanie dla Twojej firmy!
Powiązane artykuły
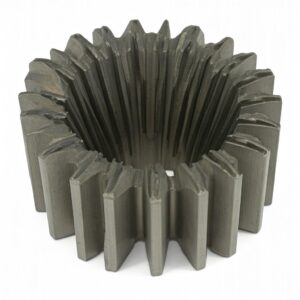
Wysokowydajne segmenty łopatek dysz: Rewolucja w wydajności turbin dzięki drukowi 3D w metalu
Czytaj więcej "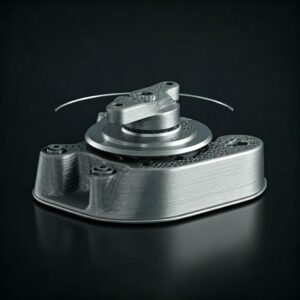
Drukowane w 3D mocowania dla samochodowych czujników radarowych: Precyzja i wydajność
Czytaj więcej "Informacje o Met3DP
Ostatnia aktualizacja
Nasz produkt
KONTAKT
Masz pytania? Wyślij nam wiadomość teraz! Po otrzymaniu wiadomości obsłużymy Twoją prośbę całym zespołem.
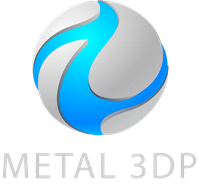
Proszki metali do druku 3D i produkcji addytywnej