Precision Robotic Linkages 3D Printed in Aluminum
Spis treści
Introduction – The Critical Role of Precision Linkages in Robotics
In the dynamic and rapidly evolving field of robotics, precision is paramount. Every component within a robotic system plays a crucial role in its overall performance, accuracy, and reliability. Among these components, linkages stand out as essential elements that directly influence the robot’s range of motion, dexterity, and the precision with which it can execute tasks. From industrial automation and medical surgery to aerospace assembly and logistics, the demand for high-performance robotic systems with intricate movements is constantly increasing. This necessitates the use of manufacturing techniques that can deliver components with exceptional accuracy and tailored properties. Metal Drukowanie 3D, also known as metal additive manufacturing, has emerged as a transformative technology offering unprecedented design freedom and the ability to produce complex geometries with high precision, making it an ideal solution for creating advanced robotic arm linkages. At Metal3DP, we understand the critical nature of these components and are dedicated to providing cutting-edge metal additive manufacturing solutions that meet the demanding requirements of the robotics industry. Our expertise in druk 3D z metalu and our range of high-performance metal powders enable the production of robotic linkages that offer superior performance and reliability.
What are Precision Robotic Linkages and Their Key Functions?
Precision robotic linkages are rigid or semi-rigid mechanical structures that connect different parts of a robotic arm or system, enabling controlled movement and force transmission. These linkages are fundamental to the robot’s kinematics, determining its reach, workspace, and the accuracy of its end-effector movements. Their key functions include:
- Enabling Degrees of Freedom: Linkages are designed to provide specific axes of rotation or linear movement, allowing the robot to perform a variety of tasks. The configuration and length of these linkages dictate the robot’s overall dexterity.
- Force and Torque Transmission: They act as conduits for transferring power from actuators (motors or cylinders) to the end-effector, ensuring that the robot can exert the necessary force or torque for its intended application.
- Maintaining Positional Accuracy: In high-precision robotics, the rigidity and dimensional accuracy of the linkages are critical for ensuring that the end-effector reaches the desired coordinates with minimal error. Any deformation or backlash in the linkages can significantly impact the robot’s accuracy.
- Supporting Structural Integrity: Linkages often form part of the robot’s structural framework, providing support and stability to other components. They must be able to withstand the dynamic loads and stresses encountered during operation.
The specific design and requirements of robotic linkages vary widely depending on the application. For instance, linkages in surgical robots demand extremely high precision and lightweight materials, while those in heavy industrial robots may prioritize strength and durability. Industries such as aerospace, automotive, medical, and industrial manufacturing rely heavily on the precise and reliable performance of these critical components. Metal3DP oferuje zaawansowane metody drukowania capable of producing intricate and high-performing robotic linkages tailored to these diverse industry needs.
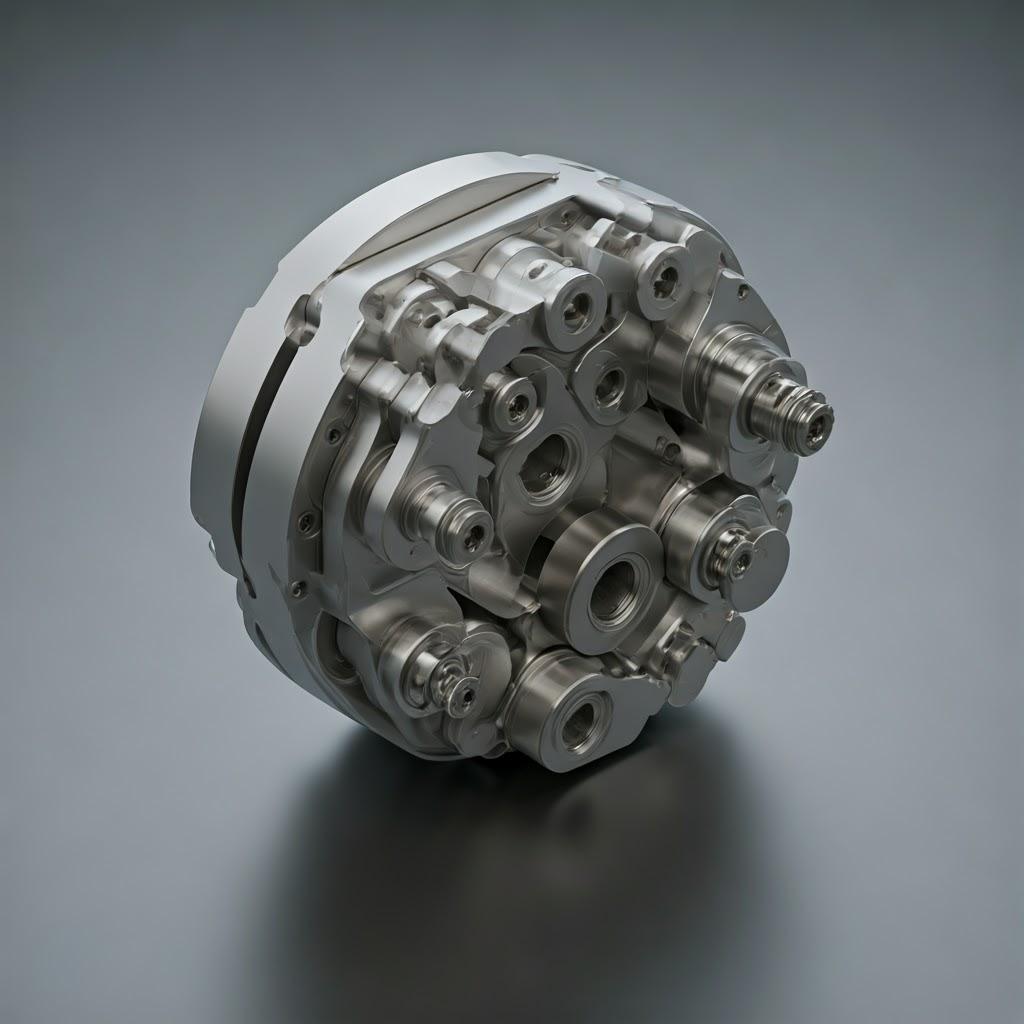
Why Choose Metal 3D Printing for Manufacturing Robotic Arm Linkages?
Traditional manufacturing methods, such as machining or casting, often present limitations when it comes to producing complex robotic linkages with optimized designs and material properties. Metal 3D printing offers several compelling advantages that make it an increasingly preferred choice for manufacturing these critical components:
- Swoboda projektowania i złożoność: Additive manufacturing allows for the creation of intricate geometries that are difficult or impossible to achieve with traditional methods. This enables engineers to design linkages with optimized weight-to-strength ratios, internal channels for cooling or cable routing, and consolidated parts, reducing the need for assembly.
- Optymalizacja materiałów: Metal 3D printing supports a wide range of high-performance materials, including aluminum alloys like AlSi10Mg and A6061, which offer excellent strength-to-weight ratios, crucial for robotic applications where minimizing inertia is vital. Metal3DP provides a variety of Wysokiej jakości proszki metali specifically optimized for additive manufacturing processes.
- Customization and Rapid Prototyping: 3D printing allows for the rapid production of prototypes and customized linkages with minimal tooling costs. This is particularly beneficial for iterative design processes and for producing small batches or unique components for specialized robotic systems.
- Zwiększona wydajność: By tailoring the design and material selection, metal 3D printing can lead to robotic linkages with improved stiffness, reduced weight, and enhanced durability, ultimately contributing to better overall robot performance and efficiency.
- Zmniejszona ilość odpadów: Additive manufacturing processes are generally more material-efficient compared to subtractive methods like machining, as material is only deposited where needed, leading to less waste and potentially lower manufacturing costs for complex parts.
Drukowanie 3D z metalu is revolutionizing the way robotic linkages are designed and manufactured, offering a pathway to creating more efficient, precise, and customized robotic systems across various industries.
Aluminum Alloys for 3D Printing Robotic Linkages: AlSi10Mg and A6061
When it comes to selecting the right material for 3D printing precision robotic linkages, aluminum alloys stand out due to their excellent combination of properties, including lightweight nature, high strength-to-weight ratio, good thermal conductivity, and corrosion resistance. Metal3DP offers two particularly well-suited aluminum alloys for this application: AlSi10Mg and A6061.
AlSi10Mg:
- Skład: Primarily composed of aluminum, silicon (Si), and magnesium (Mg). The addition of silicon improves its castability and flowability during the 3D printing process, resulting in dense and intricate parts. Magnesium enhances its strength and hardness through precipitation hardening.
- Kluczowe właściwości:
- Wysoki stosunek wytrzymałości do wagi
- Doskonała przewodność cieplna
- Dobra odporność na korozję
- High density and low porosity when processed correctly
- Good fatigue strength
- Benefits for Robotic Linkages: The lightweight nature of AlSi10Mg reduces the inertia of the robotic arm, allowing for faster and more energy-efficient movements. Its high strength ensures the structural integrity of the linkages under operational loads.
A6061:
- Skład: A precipitation-hardening aluminum alloy containing magnesium and silicon as its major alloying elements. It is known for its high strength, good weldability, and excellent corrosion resistance.
- Kluczowe właściwości:
- Very high strength-to-weight ratio (can be further enhanced through heat treatment)
- Dobra obrabialność
- Doskonała odporność na korozję
- Good fatigue strength
- Benefits for Robotic Linkages: A6061 offers even higher strength than AlSi10Mg, making it ideal for applications where the robotic arm linkages are subjected to significant stresses. Its good machinability allows for post-processing to achieve very tight tolerances and surface finishes.
The choice between AlSi10Mg and A6061 depends on the specific requirements of the robotic application. AlSi10Mg is often preferred for its excellent printability and good overall properties, while A6061 is chosen when maximum strength is a critical factor. Metal3DP‘s expertise in druk 3D z metalu ensures that both these alloys can be processed to achieve the high levels of precision and performance required for demanding robotic applications.
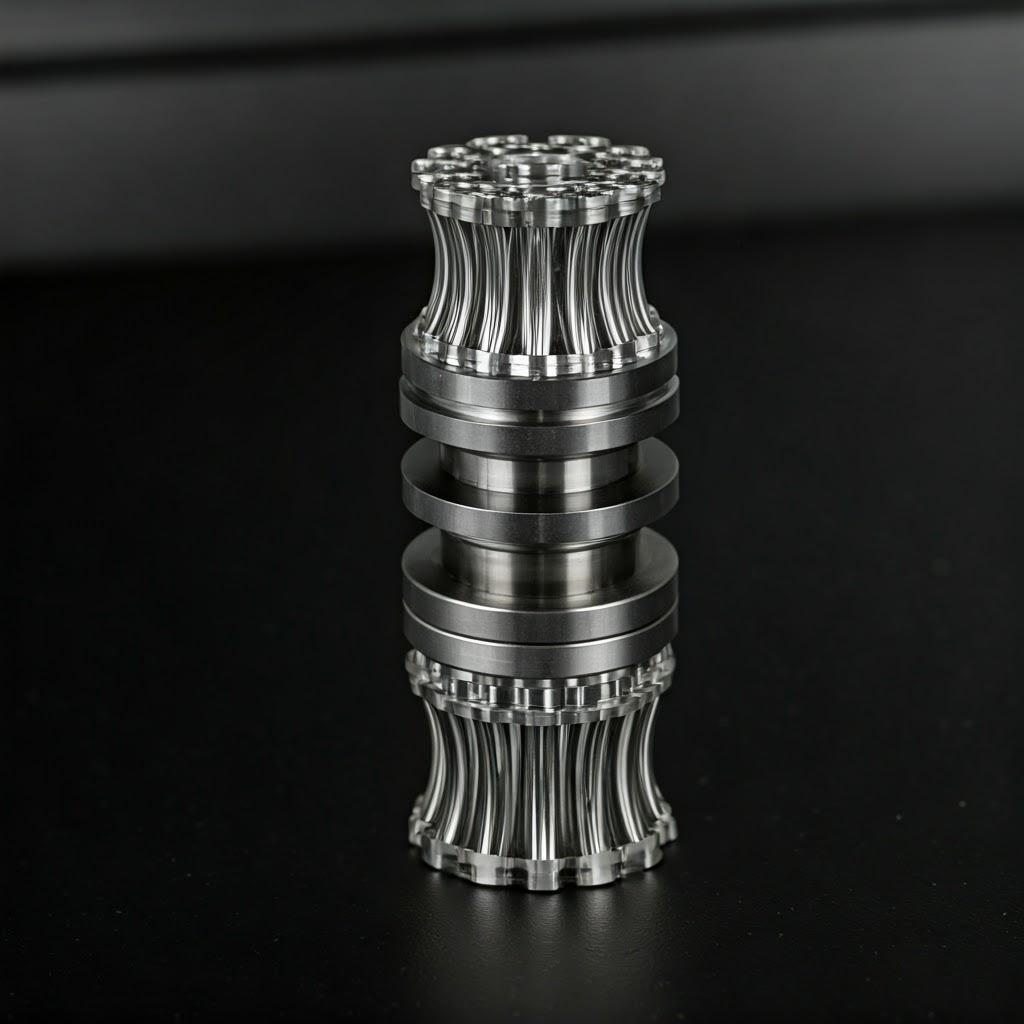
Design Optimization Strategies for Additively Manufactured Robotic Linkages
The unique capabilities of metal 3D printing open up a realm of possibilities for optimizing the design of robotic linkages beyond the constraints of traditional manufacturing. By strategically leveraging additive manufacturing techniques, engineers can create components that are lighter, stronger, and more functional. Here are some key design optimization strategies for additively manufactured robotic linkages:
- Optymalizacja topologii: This computational method identifies the most efficient material distribution for a given set of loads and constraints. By removing unnecessary material, topology optimization can lead to significant weight reduction in robotic linkages without compromising their structural integrity. This is crucial for minimizing inertia and improving the dynamic performance of the robot.
- Struktury kratowe: Incorporating lattice structures within the interior of the linkages can provide high stiffness-to-weight ratios. These intricate, repeating patterns offer excellent support while significantly reducing the overall mass of the component. Different lattice designs can be tailored to specific load-bearing requirements.
- Konsolidacja części: Metal 3D printing allows for the integration of multiple components into a single, seamless part. This reduces the need for fasteners and assembly processes, leading to improved accuracy, reduced weight, and increased reliability of the robotic arm. Features such as internal channels for cable routing or cooling can also be integrated directly into the linkage design.
- Customized Geometries: Additive manufacturing enables the creation of complex and organic shapes that can be optimized for specific kinematic requirements or to fit within tight spatial constraints within the robotic system. This design freedom can lead to more compact and efficient robotic arm designs.
- Surface Texture Optimization: The surface finish of critical mating surfaces on the linkages can be directly controlled during the 3D printing process or through post-processing. Optimizing these textures can improve wear resistance, reduce friction, and enhance the overall performance and lifespan of the robotic joint.
Przy Metal3DP, our team of experienced engineers can assist you in leveraging these design optimization strategies to create high-performance robotic linkages tailored to your specific application requirements. Our advanced druk 3D z metalu technologies and material expertise ensure that your designs are translated into functional and reliable components.
Achieving Tight Tolerances and Superior Surface Finish in 3D Printed Linkages
Precision is paramount in robotics, and the dimensional accuracy and surface finish of the linkages directly impact the overall performance and reliability of the robotic system. Metal 3D printing, when executed with expertise and the right equipment, can achieve remarkably tight tolerances and good surface finishes. Here’s what users can typically expect:
- Dokładność wymiarowa: Depending on the 3D printing technology and material used, tolerances in the range of ±0.1 mm or even finer can be achieved for critical dimensions. Factors such as part orientation during printing, material shrinkage, and the calibration of the 3D printer influence the final accuracy. Metal3DP‘s industry-leading print volume, accuracy and reliability ensure that our printed parts meet stringent dimensional requirements.
- Wykończenie powierzchni: The as-printed surface finish in metal 3D printing is typically rougher than that achieved by machining. However, significant advancements in printing technologies and post-processing techniques allow for substantial improvements. Selective Laser Melting (SLM) and Electron Beam Melting (EBM), the technologies employed by Metal3DP, can produce parts with relatively good surface finishes.
- Post-Processing for Enhanced Precision: To achieve even tighter tolerances and smoother surface finishes, post-processing steps such as CNC machining, grinding, and polishing are often employed. These subtractive methods can refine critical surfaces to meet demanding specifications for robotic joints and interfaces.
- Design for Accuracy: Incorporating design features that minimize warpage and distortion during the printing process is crucial for achieving high accuracy. This includes optimizing part orientation, adding support structures strategically, and considering the thermal behavior of the material.
Metal3DP understands the importance of precision in robotic applications. We combine our advanced metody drukowania with meticulous process control and access to various post-processing techniques to deliver aluminum robotic linkages that meet your exact tolerance and surface finish requirements.
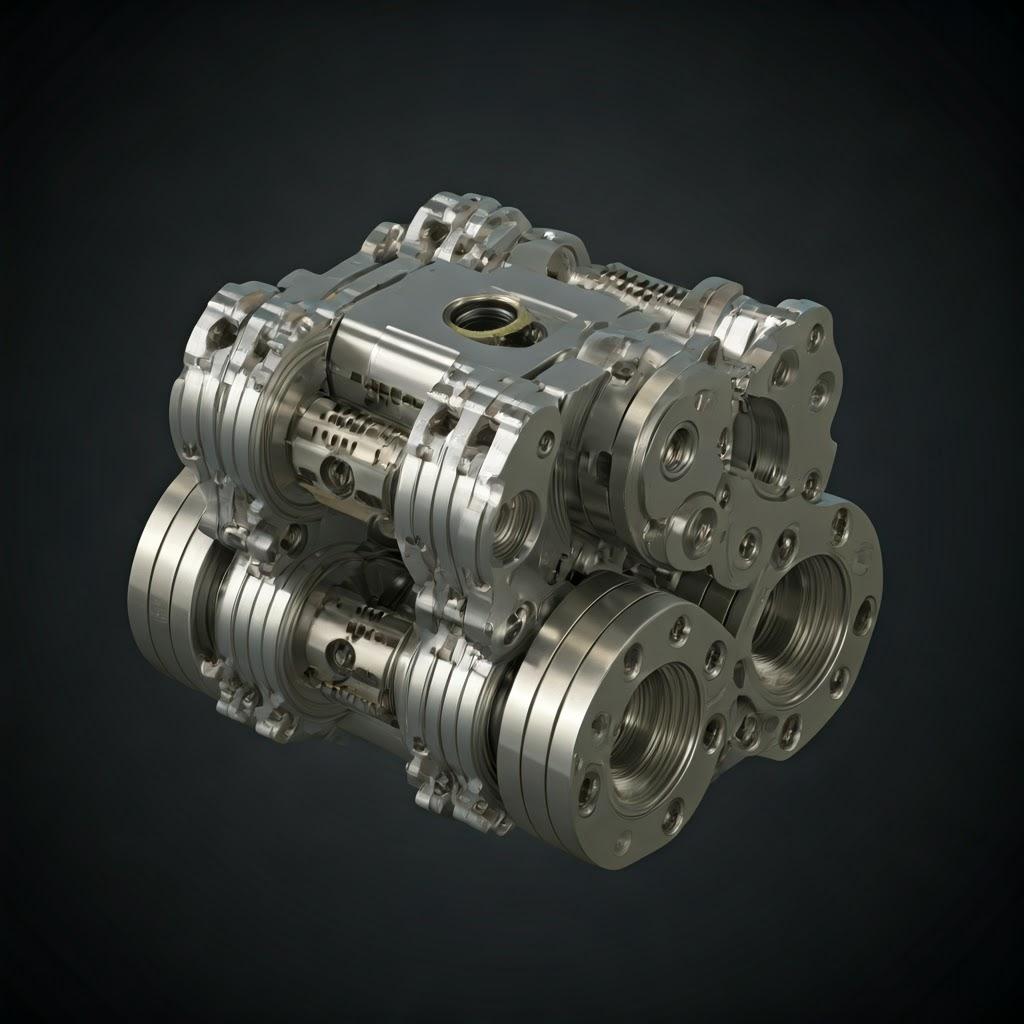
Essential Post-Processing Techniques for Aluminum Robotic Arm Components
While metal 3D printing offers significant advantages in creating complex geometries, post-processing is often necessary to achieve the final desired properties, surface finish, and dimensional accuracy for aluminum robotic arm components. Common post-processing techniques include:
- Usuwanie wsparcia: Metal 3D printed parts often require support structures to prevent collapse or distortion during the printing process. These supports need to be carefully removed after printing, typically through machining, grinding, or wire EDM (Electrical Discharge Machining).
- Obróbka cieplna: To optimize the mechanical properties of the aluminum alloys, such as strength and hardness, heat treatment processes are often applied. For AlSi10Mg, this might involve stress relieving or annealing. For A6061, solution heat treatment followed by aging can significantly enhance its strength. Metal3DP has the expertise to apply the appropriate heat treatment cycles to ensure optimal material properties.
- Obróbka CNC: For critical surfaces that require very tight tolerances and smooth finishes, CNC machining is a common post-processing step. This subtractive process can refine features such as holes, threads, and mating surfaces to precise specifications.
- Wykończenie powierzchni: Depending on the application requirements, various surface finishing techniques can be employed to improve aesthetics, corrosion resistance, or wear properties. These can include polishing, sandblasting, anodizing, or coating.
- Inspection and Quality Control: Rigorous inspection processes, including dimensional measurements and non-destructive testing, are essential to ensure that the final robotic linkages meet the required quality standards.
Metal3DP offers comprehensive post-processing services to ensure that your 3D printed aluminum robotic linkages achieve the desired mechanical properties, dimensional accuracy, and surface finish. Our integrated approach streamlines the manufacturing process and ensures high-quality, ready-to-use components.
Overcoming Common Challenges in 3D Printing Aluminum Robotic Linkages
While metal 3D printing offers numerous advantages, there are also potential challenges that need to be addressed to ensure successful fabrication of high-quality aluminum robotic linkages:
- Wypaczenia i zniekształcenia: Thermal stresses during the printing process can lead to warping or distortion of the part, especially for complex geometries or thin-walled structures. Careful design optimization, proper part orientation, and optimized process parameters are crucial to minimize these issues.
- Support Removal Difficulties: Intricate support structures can be challenging to remove without damaging the part’s surface. Designing self-supporting geometries where possible and using appropriate support removal techniques are important considerations.
- Porosity and Density: Achieving high density and minimizing porosity are critical for ensuring the mechanical strength and fatigue resistance of the linkages. Optimized printing parameters, high-quality metal powders from suppliers like Metal3DP, and proper post-processing can help mitigate these issues. Our company employs wiodące w branży technologie atomizacji gazu i PREP to produce high-quality powders that contribute to dense, high-performance parts.
- Chropowatość powierzchni: As-printed surface roughness may not be suitable for all applications, particularly for mating surfaces requiring smooth movement. Post-processing techniques like machining or polishing are often necessary.
- Material Property Consistency: Ensuring consistent material properties throughout the printed part is crucial for reliable performance. This requires precise control over the printing process and the use of high-quality, consistent metal powders. Metal3DP manufactures a wide range of high-quality metal powders optimized for laser and electron beam powder bed fusion, ensuring consistent and reliable material properties.
By understanding these potential challenges and implementing appropriate design strategies, process controls, and post-processing techniques, it is possible to overcome them and successfully leverage metal 3D printing for the production of high-performance aluminum robotic linkages. Metal3DP‘s expertise and comprehensive solutions are geared towards helping our clients navigate these challenges and achieve their additive manufacturing goals.
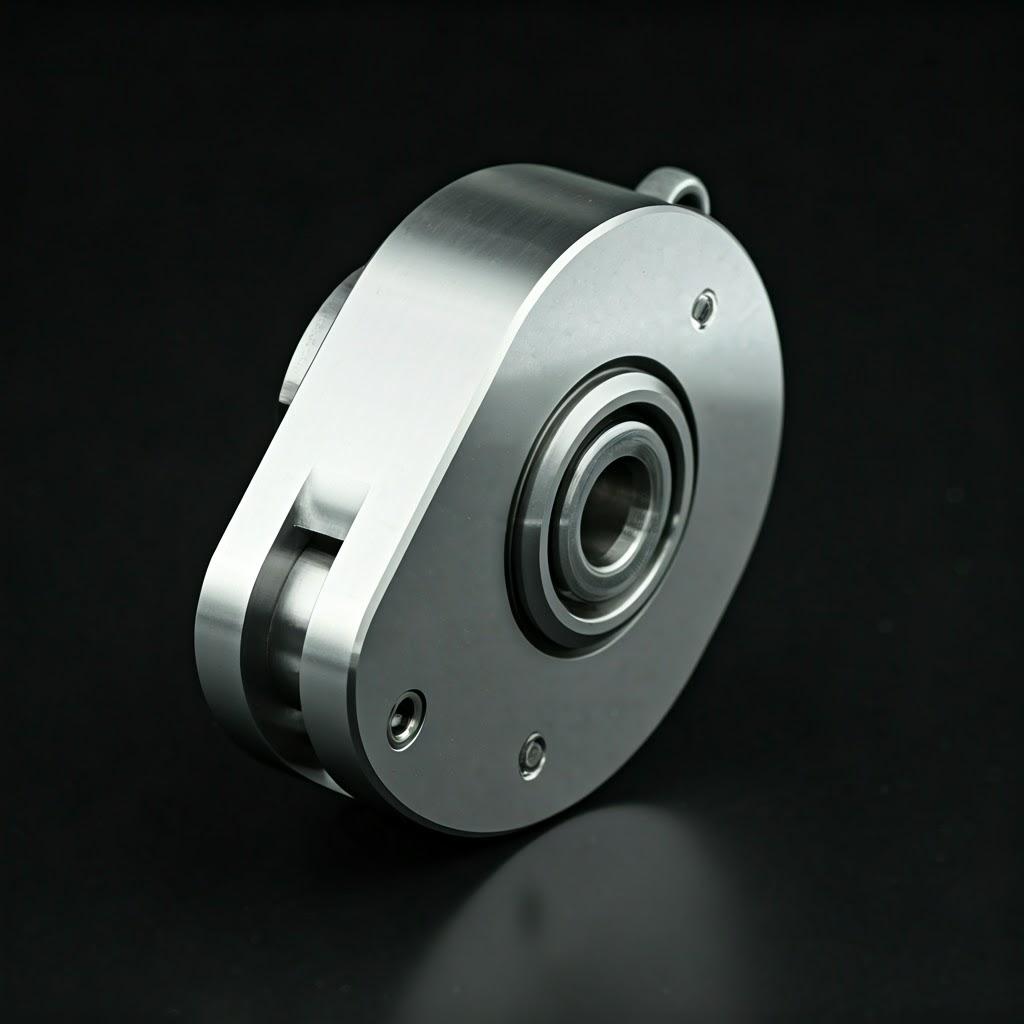
Selecting a Reliable Metal 3D Printing Service Provider for Robotic Parts
Choosing the right metal 3D printing service provider is a critical decision that can significantly impact the quality, cost, and lead time of your robotic linkages. Here are some key factors to consider when evaluating potential suppliers:
- Material Capabilities: Ensure the provider has experience working with the specific aluminum alloys required for your application (e.g., AlSi10Mg, A6061) and can demonstrate expertise in achieving the desired mechanical properties. Metal3DP offers a portfolio of innovative alloys, including these aluminum grades, specifically optimized for additive manufacturing.
- Technologia i sprzęt: Understand the types of metal 3D printing technologies the provider uses (e.g., SLM, DMLS, EBM). Each technology has its own strengths and limitations in terms of accuracy, surface finish, and build volume. Metal3DP utilizes advanced SEBM printers known for their accuracy and reliability. You can learn more about our metody drukowania on our website.
- Quality Assurance and Certifications: Inquire about the provider’s quality management system and any relevant certifications (e.g., ISO 9001, AS9100 for aerospace). Robust quality control processes are essential for ensuring the reliability and performance of critical robotic components.
- Design and Engineering Support: A good service provider should offer design consultation and optimization services to help you leverage the full potential of metal 3D printing. Metal3DP provides comprehensive solutions spanning equipment, powders, and application development services.
- Możliwości obróbki końcowej: Determine if the provider offers the necessary post-processing services, such as support removal, heat treatment, CNC machining, and surface finishing, to meet your specific requirements.
- Experience and Expertise: Look for a provider with a proven track record in manufacturing parts for demanding industries like aerospace, automotive, medical, or industrial manufacturing, as these often have stringent requirements similar to robotics. Metal3DP has decades of collective expertise in metal additive manufacturing and partners with organizations to implement 3D printing solutions. You can find more information about our company on our o nas strona.
- Lead Times and Production Capacity: Discuss the expected lead times for your project and ensure the provider has the capacity to meet your production volumes, both for prototyping and serial manufacturing.
- Cost Structure and Transparency: Understand the pricing model and all associated costs, including printing, materials, and post-processing. A transparent and competitive pricing structure is essential.
By carefully evaluating these factors, you can select a reliable metal 3D printing service provider like Metal3DP that can deliver high-quality aluminum robotic linkages that meet your specific technical and business needs.
Understanding the Cost and Lead Time for 3D Printed Robotic Linkages
The cost and lead time for manufacturing robotic linkages using metal 3D printing are influenced by several factors:
- Part Complexity and Volume: More complex geometries and larger build volumes generally lead to higher costs and longer printing times. However, metal 3D printing can be cost-effective for low to medium volumes of complex parts compared to traditional methods that may require expensive tooling.
- Material Selection and Consumption: The type and amount of metal powder used directly impact the cost. Alloys like A6061 might be more expensive than AlSi10Mg. Optimizing part design to minimize material usage is crucial for cost efficiency. You can explore our range of product offerings on our website.
- Printing Parameters and Build Time: The chosen printing parameters and the overall build time on the 3D printer affect the cost. Longer build times consume more machine time and energy.
- Wymagania dotyczące przetwarzania końcowego: The extent of post-processing required (e.g., support removal, heat treatment, machining, finishing) significantly influences both the cost and the lead time. Complex post-processing workflows will add to the overall duration and expense.
- Service Provider Factors: The pricing structure, overhead costs, and expertise of the metal 3D printing service provider will also play a role in the final cost. Providers with advanced equipment and comprehensive services may have different pricing models.
- Czas realizacji: Lead times can vary depending on the complexity of the part, the production schedule of the service provider, the availability of materials, and the required post-processing steps. Prototyping may have shorter lead times compared to large-scale production runs.
It’s essential to discuss these factors in detail with your chosen metal 3D printing service provider to get an accurate estimate of both the cost and the lead time for your specific robotic linkage project. Metal3DP is committed to providing transparent and competitive pricing while adhering to efficient production schedules.
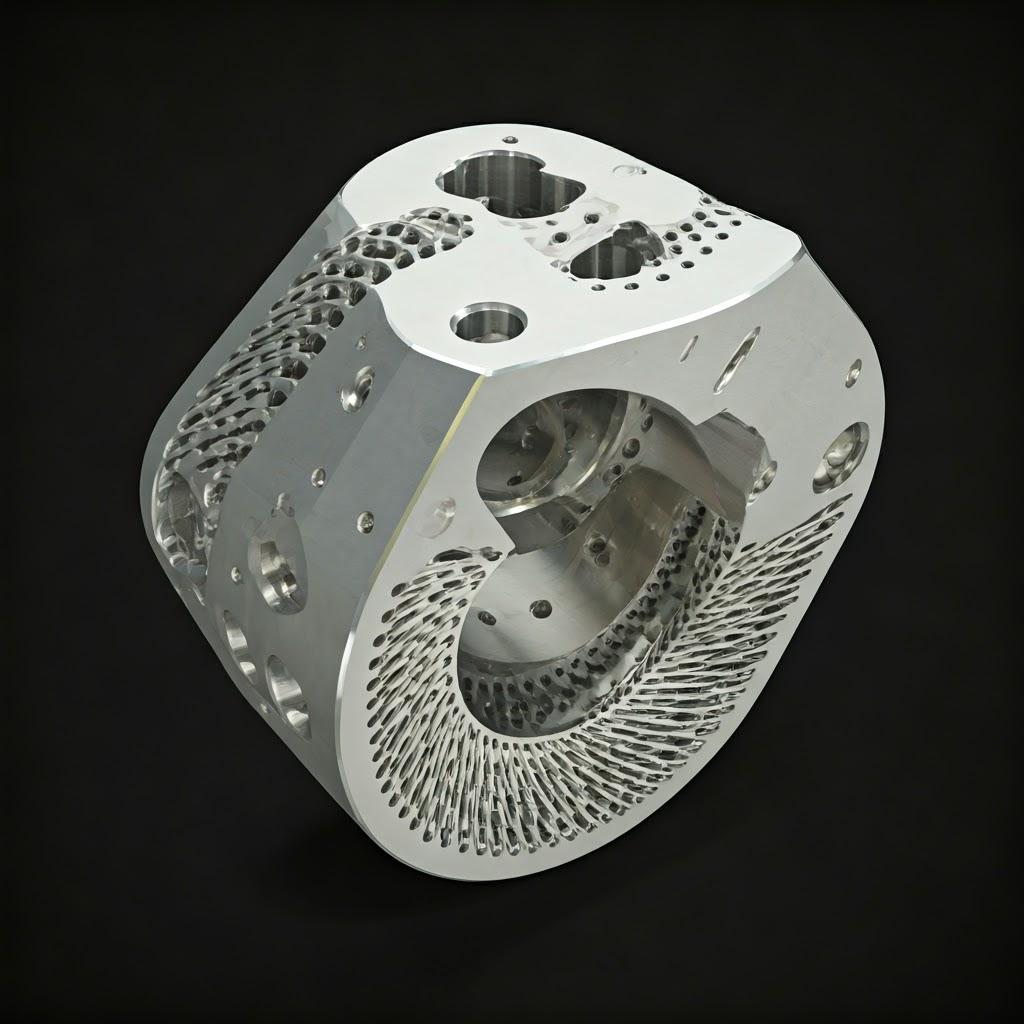
Często zadawane pytania (FAQ)
- What are the typical tolerances achievable with 3D printed aluminum robotic linkages? Depending on the design, material, and post-processing, tolerances of ±0.1 mm or even finer can be achieved on critical dimensions. For very high precision requirements, post-processing like CNC machining can further refine these tolerances.
- Is metal 3D printing cost-effective for producing robotic linkages? Metal 3D printing can be highly cost-effective, especially for complex geometries, low to medium production volumes, and customized designs where traditional tooling costs can be significant. Factors like material usage and post-processing requirements will influence the final cost.
- What are the advantages of using aluminum alloys like AlSi10Mg and A6061 for robotic linkages? These aluminum alloys offer an excellent strength-to-weight ratio, which is crucial for minimizing inertia and improving the dynamic performance of robotic arms. They also exhibit good thermal conductivity and corrosion resistance, contributing to the durability and reliability of the linkages.
- What kind of post-processing is typically required for 3D printed aluminum robotic parts? Common post-processing steps include support removal, heat treatment to optimize mechanical properties, CNC machining for tight tolerances, and surface finishing to improve aesthetics or functionality.
- How do I ensure the quality and reliability of 3D printed metal robotic linkages? Choosing a reputable metal 3D printing service provider with robust quality control processes, experience in demanding industries, and expertise in material science and additive manufacturing is crucial. Reviewing their certifications and material testing procedures is also recommended.
Conclusion – Enhancing Robotic Performance with Metal 3D Printing
Metal 3D printing has emerged as a powerful manufacturing technology for producing high-performance robotic arm linkages. The ability to create complex, optimized designs using lightweight yet strong aluminum alloys like AlSi10Mg and A6061 offers significant advantages in terms of precision, efficiency, and customization. By leveraging design optimization strategies, achieving tight tolerances through advanced printing and post-processing techniques, and carefully selecting a reliable service provider like Metal3DP, engineers and procurement managers in aerospace, automotive, medical, and industrial manufacturing can unlock new possibilities for enhancing the performance and capabilities of their robotic systems. Metal3DP‘s commitment to providing cutting-edge druk 3D z metalu solutions, including advanced equipment and high-quality metal powders, positions us as a trusted partner in driving innovation and accelerating the adoption of additive manufacturing in the robotics industry. Contact Metal3DP today to explore how our capabilities can power your organization’s additive manufacturing goals.
Udostępnij
MET3DP Technology Co., LTD jest wiodącym dostawcą rozwiązań w zakresie produkcji addytywnej z siedzibą w Qingdao w Chinach. Nasza firma specjalizuje się w sprzęcie do druku 3D i wysokowydajnych proszkach metali do zastosowań przemysłowych.
Zapytaj o najlepszą cenę i spersonalizowane rozwiązanie dla Twojej firmy!
Powiązane artykuły
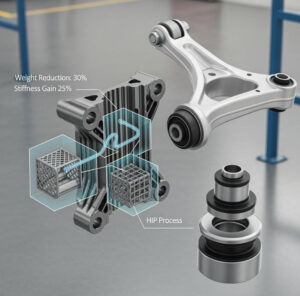
Metal 3D Printed Subframe Connection Mounts and Blocks for EV and Motorsport Chassis
Czytaj więcej "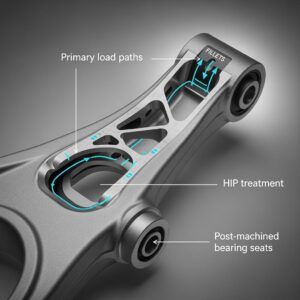
Metal 3D Printing for U.S. Automotive Lightweight Structural Brackets and Suspension Components
Czytaj więcej "Informacje o Met3DP
Ostatnia aktualizacja
Nasz produkt
KONTAKT
Masz pytania? Wyślij nam wiadomość teraz! Po otrzymaniu wiadomości obsłużymy Twoją prośbę całym zespołem.